Discover Cost-Saving Tips from a Welded Wire Mesh Manufacturer (2025)
Introduction: Navigating the Global Market for welded wire mesh manufacturer
In an increasingly interconnected world, sourcing reliable welded wire mesh manufacturers presents a significant challenge for international B2B buyers. With diverse applications ranging from construction to agriculture, understanding the nuances of this market is crucial for making informed purchasing decisions. This guide serves as a comprehensive resource, diving deep into various types of welded wire mesh, their specific applications, and the essential considerations for supplier vetting.
As a B2B buyer from regions like Africa, South America, the Middle East, or Europe, you face unique challenges, including fluctuating prices, varying quality standards, and the need for timely deliveries. Our guide empowers you to navigate these complexities by providing actionable insights on cost structures, quality control measures, and logistical considerations that can significantly impact your sourcing strategy.
Furthermore, we will explore how to assess potential suppliers effectively, ensuring you partner with manufacturers that not only meet your specifications but also align with your business values. By the end of this guide, you will be equipped with the knowledge and tools necessary to make strategic purchasing decisions, enhancing your supply chain efficiency and product quality. Whether you’re looking to procure for large-scale projects or niche applications, understanding the global market landscape for welded wire mesh is your first step towards success.
Understanding welded wire mesh manufacturer Types and Variations
Type Name | Key Distinguishing Features | Primary B2B Applications | Brief Pros & Cons for Buyers |
---|---|---|---|
Standard Welded Wire Mesh | Uniform wire spacing, typically galvanized | Fencing, concrete reinforcement | Pros: Cost-effective, versatile. Cons: Limited strength for heavy-duty applications. |
Heavy-Duty Welded Wire Mesh | Thicker wire gauge, higher tensile strength | Industrial applications, heavy fencing | Pros: Superior durability, withstands heavy loads. Cons: Higher cost, may be overkill for light applications. |
Stainless Steel Welded Wire Mesh | Corrosion-resistant, aesthetically pleasing | Food processing, chemical industries | Pros: Long lifespan, hygienic. Cons: Expensive compared to carbon steel options. |
Electro-Fused Welded Wire Mesh | Welded at high temperatures for stronger joints | Agricultural applications, security | Pros: Enhanced joint strength, suitable for varied environments. Cons: Limited to specific wire types. |
Plastic Coated Welded Wire Mesh | Coated with PVC for added protection | Landscaping, animal enclosures | Pros: Weather-resistant, visually appealing. Cons: Coating can wear off over time. |
What Are the Characteristics of Standard Welded Wire Mesh?
Standard welded wire mesh is characterized by its uniform spacing and is often galvanized to prevent rust and corrosion. This type is widely used in fencing and concrete reinforcement due to its cost-effectiveness and versatility. When purchasing, B2B buyers should consider the specific spacing and gauge required for their projects, as these factors will affect both strength and application suitability.
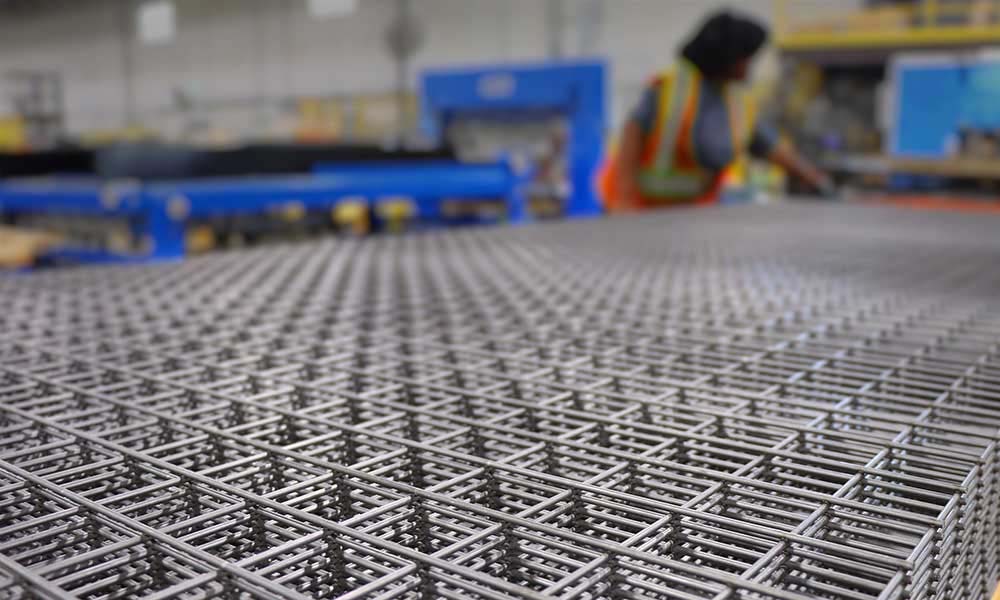
A stock image related to welded wire mesh manufacturer.
How Does Heavy-Duty Welded Wire Mesh Stand Out?
Heavy-duty welded wire mesh features a thicker wire gauge that provides higher tensile strength, making it ideal for industrial applications and heavy fencing. This type is suited for environments where durability and load-bearing capacity are critical. Buyers should evaluate the specific load requirements and potential environmental factors, such as exposure to chemicals or extreme weather, before making a purchase.
Why Choose Stainless Steel Welded Wire Mesh?
Stainless steel welded wire mesh is known for its corrosion resistance and aesthetic appeal, making it a popular choice in food processing and chemical industries. Its hygienic properties ensure compliance with health standards, which is crucial for B2B buyers in these sectors. However, the higher cost may be a consideration, and buyers should weigh the long-term benefits against initial investment.
What Are the Benefits of Electro-Fused Welded Wire Mesh?
Electro-fused welded wire mesh is produced by welding wires at high temperatures, resulting in stronger joints. This type is particularly useful in agricultural applications and for security purposes. B2B buyers should consider the specific environmental conditions in which the mesh will be used, as this can influence the choice of wire type and gauge. The enhanced joint strength can be a significant advantage for demanding applications.
How Does Plastic Coated Welded Wire Mesh Enhance Durability?
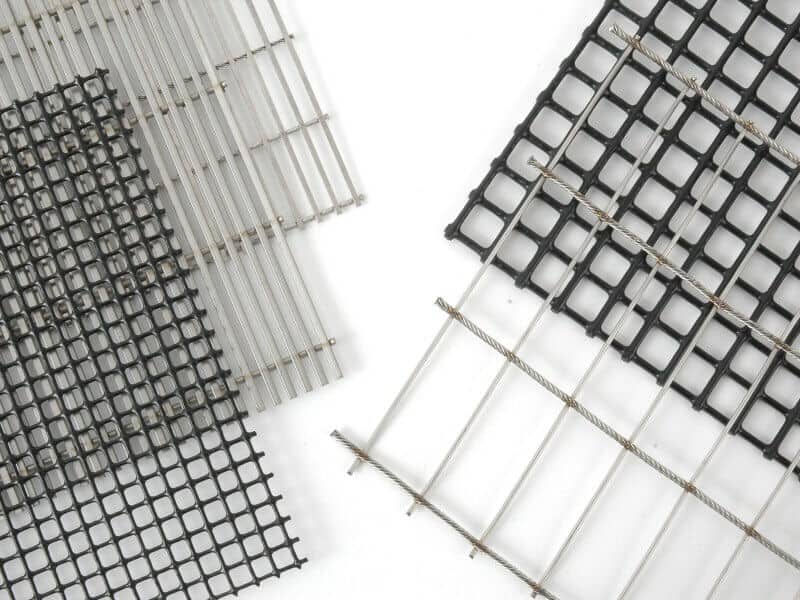
A stock image related to welded wire mesh manufacturer.
Plastic coated welded wire mesh features a protective PVC coating that enhances weather resistance and visual appeal, making it ideal for landscaping and animal enclosures. While it offers great aesthetic value and protection, buyers should be aware that the coating can wear off over time, potentially exposing the wire to corrosion. It’s essential for B2B buyers to assess the expected lifespan and maintenance needs of this type when making purchasing decisions.
Related Video: Welded wire mesh fabrication process for concrete reinforcement
Key Industrial Applications of welded wire mesh manufacturer
Industry/Sector | Specific Application of welded wire mesh manufacturer | Value/Benefit for the Business | Key Sourcing Considerations for this Application |
---|---|---|---|
Construction | Reinforcement in concrete structures | Increases structural integrity and load-bearing capacity | Ensure compliance with local building codes and standards |
Agriculture | Animal enclosures and fencing | Protects livestock and crops from predators | Assess durability against environmental factors and pests |
Transportation | Highway and railway safety barriers | Enhances safety by preventing unauthorized access | Evaluate corrosion resistance based on regional climate |
Mining | Support in underground operations | Improves safety and operational efficiency | Consider mesh size and strength for specific geological conditions |
Industrial Manufacturing | Storage racks and containment solutions | Optimizes space utilization and safety | Verify custom sizes and load ratings based on application needs |
How is Welded Wire Mesh Used in Construction?
In the construction industry, welded wire mesh is primarily used for reinforcing concrete structures such as slabs, walls, and pavements. By integrating welded wire mesh, businesses can significantly enhance the structural integrity and load-bearing capacity of their projects. This application addresses common challenges like cracking and settling, which can lead to costly repairs. For international buyers, particularly in regions like Africa and South America, it’s crucial to ensure that the mesh complies with local building codes and standards to avoid legal and safety issues.
What Role Does Welded Wire Mesh Play in Agriculture?
Welded wire mesh finds extensive use in agriculture for creating secure animal enclosures and fencing solutions. This application is vital for protecting livestock from predators and safeguarding crops from damage. By using welded wire mesh, agricultural businesses can reduce losses and improve animal welfare. International buyers should assess the durability of the mesh against environmental factors such as UV exposure and pest resistance, especially in diverse climates found in the Middle East and Europe.
How is Welded Wire Mesh Essential for Transportation Safety?
In the transportation sector, welded wire mesh is utilized for constructing safety barriers along highways and railways. These barriers are crucial for preventing unauthorized access and enhancing public safety. The use of welded wire mesh in these applications not only minimizes accident risks but also ensures compliance with safety regulations. Buyers in Europe and Africa should evaluate the corrosion resistance of the mesh, as varying climates can impact longevity and effectiveness.
In What Ways Does Welded Wire Mesh Support Mining Operations?
Welded wire mesh serves a critical role in the mining industry, particularly for providing support in underground operations. It enhances safety by preventing collapses and improving operational efficiency. Businesses in the mining sector must consider the appropriate mesh size and strength to withstand specific geological conditions. International buyers, especially from regions with diverse mining environments like South America and the Middle East, should prioritize sourcing high-quality materials that meet their operational needs.
How is Welded Wire Mesh Utilized in Industrial Manufacturing?
In industrial manufacturing, welded wire mesh is often employed for creating storage racks and containment solutions. This application helps optimize space utilization while ensuring safety in warehouses and production areas. By using welded wire mesh, businesses can improve organization and accessibility of materials. Buyers should verify custom sizes and load ratings based on their specific application needs, particularly in fast-paced manufacturing environments across Europe and Africa.
Related Video: Woven vs. Welded Wire Mesh: Picking the Right Solution
3 Common User Pain Points for ‘welded wire mesh manufacturer’ & Their Solutions
Scenario 1: Sourcing Quality Welded Wire Mesh Products
The Problem: B2B buyers, particularly in regions such as Africa and South America, often struggle to identify reliable suppliers that offer high-quality welded wire mesh. With a market flooded by numerous manufacturers, distinguishing between those that provide durable, corrosion-resistant products and those that compromise on quality can be daunting. This uncertainty can lead to project delays, increased costs, and ultimately, unsatisfied customers.
The Solution: To mitigate this challenge, buyers should begin by conducting thorough market research. Utilize platforms such as industry trade shows, online marketplaces, and supplier directories to compile a list of potential manufacturers. Once you have a shortlist, request samples and specifications for the welded wire mesh products you are considering. Evaluate these samples against your project requirements, focusing on material composition, wire diameter, and welding quality. Additionally, inquire about the manufacturer’s certifications and quality assurance processes to ensure compliance with international standards. By establishing clear criteria and systematically assessing potential suppliers, you can confidently select a manufacturer that meets your quality expectations.
Scenario 2: Understanding Technical Specifications and Applications
The Problem: Many buyers are often overwhelmed by the technical specifications associated with welded wire mesh products. Different projects may require specific types of mesh, such as varying gauge sizes, mesh openings, and materials. Without a clear understanding of these specifications, buyers can easily make misinformed decisions that lead to inadequate performance or safety risks in their applications.
The Solution: To effectively navigate the technical landscape of welded wire mesh, buyers should invest time in understanding the key specifications and their implications for different applications. Collaborate with technical experts or consult with the manufacturer’s engineering team to clarify your project’s requirements. Create a checklist of essential specifications, including wire gauge, mesh size, and coating options, tailored to your intended use—whether it be for construction, agriculture, or security fencing. Furthermore, leverage online resources, such as technical datasheets and educational webinars offered by manufacturers, to deepen your understanding. This proactive approach will enable you to make informed choices that align with your project’s needs.
Scenario 3: Managing Logistics and Delivery Timelines
The Problem: International B2B buyers often face challenges related to logistics, including shipping delays, customs clearance issues, and unexpected costs. These factors can significantly impact project timelines, leading to frustration and potential losses. For buyers in regions like the Middle East and Europe, where timely delivery is critical for construction and infrastructure projects, these logistical hurdles can be particularly detrimental.
The Solution: To address logistical challenges, buyers should establish a clear communication channel with their welded wire mesh manufacturers regarding shipping terms and timelines. Discuss options for expedited shipping and consider utilizing freight forwarding services that specialize in international logistics. Additionally, it’s advisable to establish a buffer in your project timeline to accommodate potential delays. Regularly track your shipments and maintain open lines of communication with your logistics provider to swiftly address any issues that arise. By proactively managing logistics and setting realistic expectations, you can minimize disruptions and keep your projects on schedule, ensuring smooth operations and client satisfaction.
Strategic Material Selection Guide for welded wire mesh manufacturer
When selecting materials for welded wire mesh, international B2B buyers must consider various factors that influence product performance, durability, and cost-effectiveness. Below is an analysis of four common materials used in the production of welded wire mesh, focusing on their properties, advantages, disadvantages, and implications for specific markets.
What Are the Key Properties of Mild Steel in Welded Wire Mesh?
Mild steel is the most commonly used material for welded wire mesh due to its balance of strength, ductility, and cost. It typically offers a temperature rating of up to 300°C and has good weldability, making it suitable for various applications. However, mild steel is prone to corrosion, which can significantly affect its longevity in harsh environments.
Pros & Cons:
– Pros: Cost-effective, readily available, and easy to work with. Ideal for general applications such as fencing and concrete reinforcement.
– Cons: Limited corrosion resistance, requiring protective coatings for outdoor use.
Impact on Application:
Mild steel is suitable for applications in construction and agriculture but may not perform well in coastal areas or regions with high humidity without additional protective measures.
Considerations for International Buyers:
Buyers from Africa and South America should ensure compliance with local standards, such as ASTM A615 for reinforcing bars, while European buyers may refer to EN 10080 standards.
How Does Stainless Steel Enhance the Performance of Welded Wire Mesh?
Stainless steel is known for its excellent corrosion resistance and durability, making it a preferred choice for applications in aggressive environments. It can withstand temperatures up to 800°C and is available in various grades, such as 304 and 316, which offer varying levels of resistance to corrosion and oxidation.
Pros & Cons:
– Pros: Exceptional longevity and low maintenance costs, making it ideal for outdoor and industrial applications.
– Cons: Higher initial cost and more complex manufacturing processes compared to mild steel.
Impact on Application:
Stainless steel welded wire mesh is particularly suitable for food processing, chemical plants, and marine applications, where corrosion resistance is critical.
Considerations for International Buyers:
Buyers in the Middle East and Europe should verify compliance with standards like ASTM A313 and EN 10088 for stainless steel products. Understanding local market preferences for specific grades can also enhance procurement decisions.
What Are the Benefits of Galvanized Steel in Welded Wire Mesh?
Galvanized steel is mild steel that has been coated with zinc to enhance its corrosion resistance. This material can withstand temperatures similar to mild steel and is often used in outdoor settings.
Pros & Cons:
– Pros: Cost-effective solution with improved durability compared to untreated mild steel. The zinc coating protects against rust and extends service life.
– Cons: The coating can wear off over time, especially in abrasive environments, leading to potential corrosion issues.
Impact on Application:
Galvanized welded wire mesh is commonly used in construction, agriculture, and landscaping, where exposure to moisture is a concern.
Considerations for International Buyers:
Buyers in regions like Africa and South America should ensure that the galvanized mesh complies with local standards, such as ASTM A123 for zinc coatings, to ensure quality and performance.
Why Choose PVC-Coated Wire Mesh for Specific Applications?
PVC-coated welded wire mesh is made by coating galvanized steel with a layer of PVC, enhancing its corrosion resistance and aesthetic appeal. This material performs well in temperatures up to 60°C and is available in various colors.
Pros & Cons:
– Pros: Excellent corrosion resistance, attractive appearance, and reduced maintenance needs. Ideal for decorative and protective applications.
– Cons: Higher cost compared to uncoated options and potential for wear over time in harsh environments.
Impact on Application:
PVC-coated wire mesh is ideal for residential fencing, garden applications, and animal enclosures, where appearance and corrosion resistance are priorities.
Considerations for International Buyers:
Buyers in Europe and the Middle East should check for compliance with standards such as ASTM D638 for plastic materials and ensure that the coating thickness meets local requirements.
Summary Table of Material Selection for Welded Wire Mesh
Material | Typical Use Case for welded wire mesh manufacturer | Key Advantage | Key Disadvantage/Limitation | Relative Cost (Low/Med/High) |
---|---|---|---|---|
Mild Steel | Fencing, concrete reinforcement | Cost-effective and versatile | Prone to corrosion | Low |
Stainless Steel | Food processing, chemical plants | Exceptional corrosion resistance | Higher initial cost | High |
Galvanized Steel | Outdoor construction, landscaping | Improved durability | Coating can wear off | Medium |
PVC-Coated Wire | Residential fencing, garden applications | Attractive and low maintenance | Higher cost than uncoated options | Medium |
This strategic material selection guide provides a comprehensive overview for international B2B buyers, enabling informed decisions that align with both application requirements and regional standards.
In-depth Look: Manufacturing Processes and Quality Assurance for welded wire mesh manufacturer
What Are the Main Stages of the Manufacturing Process for Welded Wire Mesh?
The manufacturing process of welded wire mesh involves several critical stages that ensure the product’s durability and reliability. Understanding these processes is essential for international B2B buyers who seek high-quality products.
-
Material Preparation: The process begins with the selection of raw materials, typically high-quality steel wires. These wires are sourced based on specific mechanical properties such as tensile strength and ductility. The wires are then cleaned to remove any impurities, which is crucial for ensuring proper welding and adhesion.
-
Forming: Once the wires are prepared, they are fed into a mesh-making machine. This equipment arranges the wires in a predetermined grid pattern. The spacing between the wires can vary based on customer specifications. Advanced automated systems often enhance precision, reducing human error and increasing output efficiency.
-
Assembly and Welding: The next step is the welding process, where the intersecting wires are joined together at their points of contact. This is typically done using electric resistance welding, which provides strong and consistent welds. For buyers, understanding the welding technique is vital, as it directly affects the mesh’s structural integrity.
-
Finishing: After welding, the mesh undergoes finishing processes, which may include galvanization or coating to enhance corrosion resistance. This is particularly important for applications in harsh environments, such as those found in Africa and the Middle East. Buyers should inquire about the types of finishes available and their respective benefits.
How Do Quality Assurance Practices Impact Welded Wire Mesh Production?
Quality assurance (QA) is integral to the manufacturing process, ensuring that the final products meet both industry standards and customer expectations. For international B2B buyers, it is crucial to understand the quality control mechanisms in place.
-
International Standards Compliance: Many welded wire mesh manufacturers adhere to international quality standards, such as ISO 9001, which outlines requirements for an effective quality management system. Compliance with these standards indicates that the manufacturer has established robust processes to ensure product quality.
-
Industry-Specific Certifications: Depending on the application, additional certifications may be relevant. For instance, the CE marking is essential for products sold within the European Economic Area, indicating compliance with health, safety, and environmental protection standards. Buyers from Europe should prioritize suppliers with these certifications.
-
Quality Control Checkpoints: A comprehensive quality control process involves several checkpoints:
– Incoming Quality Control (IQC): This stage assesses the quality of raw materials before they enter production.
– In-Process Quality Control (IPQC): During manufacturing, ongoing inspections are conducted to ensure that the welding and assembly processes meet specified criteria.
– Final Quality Control (FQC): After production, the finished products are thoroughly inspected and tested to ensure they meet quality standards. -
Testing Methods: Common testing methods include tensile strength testing, weld integrity testing, and corrosion resistance assessments. These tests help verify that the welded wire mesh will perform as expected in real-world applications.
How Can B2B Buyers Verify Supplier Quality Control Measures?
For B2B buyers, especially those operating across borders, it is essential to have confidence in the quality control measures of their suppliers. Here are several strategies to verify supplier QC:
-
Supplier Audits: Conducting audits is one of the most effective ways to assess a manufacturer’s quality control processes. Buyers can either perform these audits themselves or hire third-party inspection firms to evaluate the supplier’s facilities, processes, and compliance with international standards.
-
Requesting Quality Reports: Buyers should ask suppliers for detailed quality reports that outline the results of various tests and inspections. These reports should include data on IQC, IPQC, and FQC stages, providing insight into the manufacturer’s commitment to quality.
-
Third-Party Inspections: Utilizing third-party inspection services can add an additional layer of assurance. These independent entities can conduct random inspections and testing, providing unbiased evaluations of the product quality.
-
Certifications and Documentation: Always request copies of relevant certifications and documentation from suppliers. This includes ISO certifications, CE markings, and any other industry-specific standards. These documents serve as proof of the manufacturer’s adherence to quality assurance practices.
What Are the Nuances of Quality Control and Certification for International Buyers?
Understanding the nuances of quality control and certification is particularly important for international B2B buyers. Here are key considerations:
-
Regional Standards Variability: Quality standards can vary significantly between regions. For example, while ISO 9001 is globally recognized, certain countries in Africa or South America may have additional local regulations or standards that must be met. Buyers should familiarize themselves with these regional requirements.
-
Cultural Considerations: Different cultures may have varying approaches to quality assurance and business practices. Establishing clear communication and expectations regarding quality can help bridge these gaps and foster successful supplier relationships.
-
Supply Chain Transparency: Buyers should prioritize suppliers who are transparent about their supply chain processes. This includes sharing information on sourcing, production methods, and quality control measures. Transparency builds trust and helps mitigate risks associated with quality issues.
-
Long-Term Partnerships: Establishing long-term relationships with manufacturers can lead to improved quality and service over time. Buyers should consider suppliers that demonstrate a commitment to continuous improvement and innovation in their manufacturing processes.
Conclusion: Making Informed Decisions in the Welded Wire Mesh Market
For international B2B buyers, understanding the manufacturing processes and quality assurance practices of welded wire mesh manufacturers is crucial. By focusing on the key stages of production, verifying quality control measures, and considering regional nuances, buyers can make informed decisions that ensure they procure high-quality products tailored to their specific needs. Building strong partnerships with reliable manufacturers will ultimately enhance operational efficiency and product performance in diverse applications.
Practical Sourcing Guide: A Step-by-Step Checklist for ‘welded wire mesh manufacturer’
In the competitive landscape of sourcing welded wire mesh, B2B buyers must navigate various considerations to ensure they partner with reliable manufacturers. This step-by-step checklist aims to provide practical insights for international buyers, particularly from Africa, South America, the Middle East, and Europe, to effectively procure welded wire mesh products.
Step 1: Define Your Technical Specifications
Before you start reaching out to manufacturers, clarify your technical requirements. This includes the gauge of wire, mesh size, coating type (e.g., galvanized or PVC), and application (e.g., construction, agriculture). Having well-defined specifications ensures that you receive accurate quotes and products that meet your specific needs.
Step 2: Research Potential Manufacturers
Conduct comprehensive research to identify potential manufacturers. Utilize online directories, trade shows, and industry associations to compile a list of candidates. Look for manufacturers with a proven track record, positive reviews, and extensive experience in welded wire mesh production, as these factors often correlate with product quality.
Step 3: ✅ Verify Supplier Certifications
It’s essential to confirm that the manufacturers possess relevant certifications, such as ISO 9001 or CE marking, which reflect adherence to international quality standards. Certifications not only ensure product reliability but also demonstrate the manufacturer’s commitment to quality control processes. Request copies of these certifications during your evaluation.
Step 4: Evaluate Manufacturing Capabilities
Assess the manufacturing capabilities of your shortlisted suppliers. Inquire about their production capacity, technology, and quality control measures. Understanding their capabilities will help you determine if they can meet your order volumes and delivery timelines, especially for large-scale projects.
Step 5: Request Samples for Quality Assessment
Before finalizing your supplier, request product samples. This step is crucial for assessing the quality of the welded wire mesh firsthand. Examine the sample for factors like durability, finish, and compliance with your specifications. A hands-on quality check can reveal potential issues that may not be apparent in product descriptions or specifications.
Step 6: Negotiate Pricing and Payment Terms
Once you’ve identified a suitable manufacturer, engage in negotiations regarding pricing and payment terms. Be clear about your budget and look for transparent pricing structures. Consider discussing payment options such as letters of credit or escrow services, which can provide security for both parties, especially in cross-border transactions.
Step 7: Establish Clear Communication Channels
Effective communication is vital for a successful partnership. Ensure that the manufacturer has a dedicated point of contact and that communication channels are well-defined. Regular updates on order status, production timelines, and shipping information can prevent misunderstandings and foster a smoother procurement process.
By following these steps, B2B buyers can confidently navigate the sourcing process for welded wire mesh manufacturers, ensuring they select a partner that meets their quality and delivery expectations.
Comprehensive Cost and Pricing Analysis for welded wire mesh manufacturer Sourcing
What Are the Key Cost Components in Welded Wire Mesh Manufacturing?
Understanding the cost structure of welded wire mesh manufacturing is crucial for international B2B buyers seeking to optimize their sourcing strategy. The primary cost components include:
-
Materials: The type and quality of steel wire used significantly impact costs. Galvanized wire, for instance, offers corrosion resistance but at a higher price than plain steel. Buyers should assess material specifications based on their application needs.
-
Labor: Labor costs can vary widely based on the manufacturing location. Regions with lower labor costs, such as parts of Africa and South America, might offer competitive pricing, but this may come with trade-offs in quality or reliability.
-
Manufacturing Overhead: This encompasses all indirect costs related to production, including utilities, rent, and equipment maintenance. Efficient operations can help minimize these expenses, affecting the final price of the welded wire mesh.
-
Tooling: Initial tooling costs can be significant, especially for custom designs. Buyers should inquire about the tooling lifespan and whether these costs are amortized over large orders.
-
Quality Control (QC): Ensuring product quality through rigorous QC processes adds to the overall cost. Certifications like ISO can enhance the product’s marketability but may increase the price.
-
Logistics: Transportation and handling costs are critical, especially for international shipments. Factors such as distance, shipping method, and Incoterms can influence overall logistics expenses.
-
Margin: Manufacturers typically add a profit margin to cover risks and ensure sustainability. This margin can vary based on supplier reputation and market demand.
What Influences Pricing for Welded Wire Mesh Products?
Several factors influence the pricing of welded wire mesh products, which buyers should consider when negotiating:
-
Volume/MOQ: Pricing often benefits from economies of scale. Higher order volumes typically lead to lower per-unit costs. Buyers should discuss minimum order quantities (MOQs) to maximize cost savings.
-
Specifications and Customization: Custom specifications can significantly increase costs. Buyers should determine whether standard products meet their needs to avoid unnecessary expenses.
-
Materials and Quality Certifications: Premium materials or certifications can raise prices. It’s essential to balance quality with budget constraints to ensure a suitable procurement strategy.
-
Supplier Factors: The supplier’s reputation, production capacity, and experience can affect pricing. Established suppliers may charge more but offer greater reliability.
-
Incoterms: Understanding the implications of Incoterms on shipping and risk management is vital. Terms like FOB (Free on Board) or CIF (Cost, Insurance, and Freight) can impact overall costs and responsibilities.
How Can Buyers Optimize Costs When Sourcing Welded Wire Mesh?
To ensure cost-efficiency and value in sourcing welded wire mesh, international B2B buyers should consider the following strategies:
-
Negotiate Terms: Engage suppliers in discussions about pricing structures, payment terms, and potential discounts for bulk orders. A transparent negotiation process can yield better deals.
-
Evaluate Total Cost of Ownership (TCO): Beyond the initial purchase price, consider the TCO, which includes maintenance, logistics, and potential future costs. This holistic view helps in making informed decisions.
-
Understand Regional Pricing Nuances: Pricing may vary significantly across regions. Buyers from Africa and South America, for instance, may find different cost structures compared to those in Europe or the Middle East. Researching local market conditions can lead to better sourcing decisions.
-
Leverage Technology: Utilize digital platforms and tools for comparing suppliers and prices. This can streamline the sourcing process and uncover competitive offers.
-
Build Strong Relationships: Establishing long-term relationships with suppliers can lead to better pricing, improved service, and enhanced collaboration.
Disclaimer on Indicative Prices
Prices for welded wire mesh can fluctuate based on market conditions, currency exchange rates, and geopolitical factors. Therefore, it is essential to obtain updated quotes directly from manufacturers to ensure accurate budgeting and planning.
Alternatives Analysis: Comparing welded wire mesh manufacturer With Other Solutions
In the ever-evolving landscape of construction and industrial applications, buyers often seek alternatives to standard solutions like welded wire mesh. Understanding these alternatives can provide valuable insights for B2B buyers looking to optimize their procurement strategies. This section compares welded wire mesh manufacturing with other viable solutions, helping international buyers make informed decisions that best suit their specific needs.
Comparison Aspect | Welded Wire Mesh Manufacturer | Steel Reinforcement Bars | Plastic Mesh Solutions |
---|---|---|---|
Performance | High tensile strength, ideal for concrete reinforcement and fencing. | Strong load-bearing capacity, widely used in construction. | Lightweight, suitable for temporary barriers and agricultural use. |
Cost | Moderate initial investment with long-term durability benefits. | Generally lower upfront costs but may require more material. | Low-cost option but less durable over time. |
Ease of Implementation | Requires skilled labor for installation, but relatively straightforward. | Familiar installation methods, widely practiced in the industry. | Easy to install, often DIY-friendly. |
Maintenance | Low maintenance, resistant to corrosion when galvanized. | Requires periodic inspections and may need rust protection. | Minimal maintenance but may degrade faster under UV exposure. |
Best Use Case | Ideal for industrial, commercial, and residential construction projects. | Best for heavy-load applications, such as structural supports. | Suitable for agricultural fencing and temporary structures. |
What Are the Advantages and Disadvantages of Using Steel Reinforcement Bars?
Steel reinforcement bars (rebar) are a common alternative to welded wire mesh in construction. The primary advantage of rebar is its strong load-bearing capacity, making it ideal for heavy-duty applications like bridges and high-rise buildings. However, while rebar may be less expensive initially, it often requires more material to achieve the same structural integrity as welded wire mesh. This can lead to higher overall costs in larger projects. Additionally, installation can be more complex, necessitating skilled labor and careful planning to ensure proper placement.
How Do Plastic Mesh Solutions Compare to Welded Wire Mesh?
Plastic mesh solutions serve as a lightweight and cost-effective alternative, particularly for applications such as agricultural fencing or temporary barriers. The advantages of plastic mesh include easy installation, often allowing for DIY projects, and a lower initial investment. However, these solutions typically lack the tensile strength and durability of welded wire mesh. They may degrade over time due to UV exposure and are not suitable for heavy-load applications. Therefore, while they can be a practical choice for certain scenarios, they may not provide the long-term benefits associated with welded wire mesh.
How Can B2B Buyers Choose the Right Solution for Their Needs?
When selecting between welded wire mesh and its alternatives, B2B buyers should consider several factors: the specific application, budget constraints, and the expected lifespan of the material. For heavy-duty construction projects requiring structural integrity, welded wire mesh or steel reinforcement bars may be the best choice. Conversely, for agricultural uses or temporary setups, plastic mesh might be sufficient. Ultimately, the decision should align with the project’s demands and the buyer’s long-term goals, ensuring that the selected solution delivers optimal performance and value.
Essential Technical Properties and Trade Terminology for welded wire mesh manufacturer
What Are the Key Technical Properties of Welded Wire Mesh?
Understanding the technical properties of welded wire mesh is crucial for international B2B buyers to ensure they select the right product for their specific applications. Here are the critical specifications to consider:
1. Material Grade
The material grade of welded wire mesh typically refers to the type of steel used in its production. Common grades include low carbon steel, stainless steel, and galvanized steel. Each grade has distinct characteristics, such as strength, corrosion resistance, and flexibility. For example, stainless steel offers superior durability and is ideal for environments exposed to moisture, making it a preferred choice in coastal regions. Buyers should assess their project requirements against the material grade to ensure longevity and performance.
2. Wire Diameter
Wire diameter is a significant factor in determining the strength and load-bearing capacity of welded wire mesh. It is usually measured in millimeters or inches. A thicker wire diameter generally indicates a stronger mesh, suitable for heavy-duty applications such as fencing or concrete reinforcement. Buyers must evaluate the intended use to select a wire diameter that balances strength and cost-effectiveness.
3. Mesh Opening Size
The mesh opening size refers to the distance between the intersecting wires in the mesh. This specification affects the wire mesh’s ability to retain or release materials, such as soil or aggregate in construction applications. Smaller openings are often chosen for applications requiring filtration, while larger openings may be used in fencing or other structural uses. Understanding the required mesh opening is vital for ensuring the product meets specific application needs.
4. Tolerance Levels
Tolerance levels indicate the permissible deviation from specified dimensions during manufacturing. These are essential for ensuring that the welded wire mesh fits seamlessly into its intended application, especially in projects requiring precise measurements. For international buyers, understanding tolerance levels can help prevent costly adjustments or project delays due to misalignment or sizing issues.
5. Coating Options
Coating options, such as galvanization or PVC coating, enhance the durability and corrosion resistance of welded wire mesh. Galvanized wire mesh is coated with zinc to protect against rust, making it suitable for outdoor use. In contrast, PVC-coated mesh offers additional protection and aesthetic appeal, often used in residential fencing. Buyers should evaluate their environmental conditions and aesthetic preferences when selecting coating options.
What Are Common Trade Terminology and Jargon in the Welded Wire Mesh Industry?
Familiarizing yourself with industry terminology can streamline communication and decision-making processes. Here are some essential terms:
1. OEM (Original Equipment Manufacturer)
An OEM refers to a company that produces components or products that are used in another company’s end products. In the context of welded wire mesh, buyers may work with OEMs to source custom mesh solutions tailored to specific project requirements. Understanding OEM relationships can enhance supply chain efficiency and product customization.
2. MOQ (Minimum Order Quantity)
MOQ is the smallest quantity of a product that a supplier is willing to sell. For welded wire mesh, MOQs can vary significantly based on the manufacturer and the product type. Buyers should be aware of MOQs to plan their budgets and inventory effectively, especially when dealing with large-scale projects.
3. RFQ (Request for Quotation)
An RFQ is a document sent to suppliers requesting pricing and other relevant information for specific products. For international buyers, submitting an RFQ can facilitate competitive pricing and ensure that all suppliers understand the exact specifications needed for welded wire mesh.
4. Incoterms
Incoterms, or International Commercial Terms, are a set of predefined commercial terms published by the International Chamber of Commerce (ICC). They define the responsibilities of buyers and sellers in international transactions. Understanding Incoterms is essential for international B2B buyers to clarify shipping responsibilities, risk management, and costs associated with the delivery of welded wire mesh.
5. Lead Time
Lead time refers to the time it takes from placing an order to receiving the product. In the welded wire mesh industry, lead times can vary based on factors such as order size, manufacturing capabilities, and shipping logistics. Buyers should inquire about lead times to ensure project timelines are met, preventing delays in construction or manufacturing processes.
By grasping these technical properties and trade terms, international B2B buyers can make informed decisions when sourcing welded wire mesh, ultimately leading to successful procurement and project execution.
Navigating Market Dynamics and Sourcing Trends in the welded wire mesh manufacturer Sector
What Are the Key Market Trends Impacting Welded Wire Mesh Manufacturers?
The welded wire mesh manufacturing sector is experiencing dynamic shifts driven by several global factors. Increased construction activities, particularly in emerging markets across Africa, South America, and the Middle East, are fueling demand for durable and versatile materials. The rise in infrastructure projects, including residential buildings, roadways, and industrial facilities, is a primary driver, with significant investments being made in these regions. For B2B buyers, understanding local market conditions and regional economic policies can facilitate better sourcing decisions.
Additionally, technological advancements are reshaping the sourcing landscape. Automation and robotics in manufacturing processes are enhancing production efficiency and reducing costs. B2B buyers should look for manufacturers that leverage these technologies to ensure they receive high-quality products at competitive prices. Furthermore, the integration of Industry 4.0 solutions allows for improved supply chain visibility and predictive analytics, enabling buyers to make informed purchasing decisions.
Another trend is the increasing focus on customization. As industries seek unique solutions, manufacturers are adapting their offerings to meet specific buyer needs. International buyers, particularly those from regions like Europe and the Middle East, should prioritize suppliers that can provide tailored products, ensuring their projects achieve optimal results.
How Is Sustainability Influencing Sourcing Decisions for Welded Wire Mesh?
Sustainability has become a critical consideration in the sourcing process for welded wire mesh manufacturers. The environmental impact of production methods and materials is under scrutiny, prompting buyers to demand more sustainable practices. This includes sourcing materials that have lower carbon footprints and minimizing waste throughout the manufacturing process.
Ethical sourcing is equally important. Buyers are increasingly favoring suppliers who demonstrate a commitment to responsible labor practices and transparent supply chains. Certifications such as ISO 14001 for environmental management and Fair Trade certifications can serve as indicators of a manufacturer’s commitment to sustainable practices. By prioritizing suppliers with these credentials, international B2B buyers can align their purchases with corporate social responsibility goals and appeal to environmentally conscious consumers.
Moreover, the use of recycled materials in welded wire mesh production is gaining traction. Manufacturers who incorporate recycled steel not only reduce their environmental impact but also often benefit from lower material costs. B2B buyers should explore suppliers who are adopting these practices, as it can lead to cost savings while supporting sustainability initiatives.
How Has the Welded Wire Mesh Manufacturing Sector Evolved Over Time?
The evolution of the welded wire mesh manufacturing sector reflects broader industrial trends and technological advancements. Initially, the industry was characterized by manual processes, which limited production capacity and consistency. However, with the advent of electric welding technology in the mid-20th century, manufacturers began to produce stronger and more uniform mesh products.
In recent decades, globalization has also played a significant role in the sector’s development. Manufacturers are now able to source raw materials from various regions, allowing for competitive pricing and enhanced product offerings. The rise of digital technologies and e-commerce platforms has further transformed how buyers interact with suppliers, making it easier to compare products and services across borders.
As the market continues to evolve, B2B buyers must stay informed about innovations and shifts in production practices to make strategic sourcing decisions that align with their business goals.
Frequently Asked Questions (FAQs) for B2B Buyers of welded wire mesh manufacturer
-
How do I determine the right specifications for welded wire mesh?
When sourcing welded wire mesh, consider the application requirements, including the intended use, environmental conditions, and load-bearing capacity. Specifications such as wire diameter, mesh opening size, and coating type (e.g., galvanized or PVC) are crucial. Collaborate closely with your manufacturer to align your needs with their capabilities, ensuring the product meets industry standards and local regulations. Additionally, gathering insights from local construction codes in your region can provide guidance on necessary specifications. -
What is the best method to vet a welded wire mesh manufacturer?
To effectively vet a welded wire mesh manufacturer, assess their production capacity, quality control processes, and compliance with international standards such as ISO certifications. Request samples of their products to evaluate quality firsthand. Engage with past clients for testimonials and reviews, and explore their experience in serving clients from your region. Conducting a factory visit, if feasible, can provide further assurance of their operational standards and commitment to quality. -
What customization options are available for welded wire mesh products?
Most manufacturers offer various customization options for welded wire mesh, including dimensions, wire gauge, and mesh patterns. Some may also provide specialized coatings for enhanced durability in specific environments, such as corrosion-resistant finishes for coastal areas. Discuss your requirements with potential suppliers to explore available customization options. Ensure that the manufacturer can accommodate your needs without compromising quality or lead times. -
What are the typical minimum order quantities (MOQs) for welded wire mesh?
Minimum order quantities can vary significantly between manufacturers, typically ranging from a few hundred to several thousand square meters, depending on the product and supplier. Smaller manufacturers may offer lower MOQs to accommodate smaller projects, while larger manufacturers might require higher volumes to optimize production efficiency. Clarifying MOQs early in the negotiation process can help you plan your project budget and timelines effectively. -
What payment terms should I expect when sourcing from a welded wire mesh manufacturer?
Payment terms can differ based on the manufacturer’s policies and your negotiation skills. Common arrangements include a deposit upon order confirmation, with the balance due before shipping or upon delivery. Some manufacturers may offer financing options or extended payment terms for large orders. It’s essential to establish clear payment terms upfront to avoid potential disputes and ensure a smooth transaction process. -
How can I ensure quality assurance in welded wire mesh products?
To ensure quality assurance, inquire about the manufacturer’s quality control processes, including in-house testing and third-party inspections. Request documentation of compliance with relevant quality standards. Consider implementing your quality checks upon receiving the goods, such as sampling and testing for tensile strength and corrosion resistance. Building a strong relationship with your supplier can also facilitate better communication about quality expectations. -
What logistics considerations should I keep in mind when importing welded wire mesh?
Logistics is a critical aspect of importing welded wire mesh. Consider factors like shipping methods, lead times, and customs regulations in your country. Choose a reliable freight forwarder familiar with handling construction materials to navigate potential challenges. Additionally, factor in costs related to duties, taxes, and insurance to avoid unexpected expenses. Clear communication with your manufacturer regarding packaging and shipping can also streamline the process. -
What are the common applications for welded wire mesh in different industries?
Welded wire mesh is widely used across various industries, including construction for reinforcement in concrete, agriculture for fencing and animal enclosures, and manufacturing for shelving and storage solutions. In the construction sector, it provides structural integrity and support. In agriculture, it serves as a protective barrier. Understanding the specific applications relevant to your industry can guide your sourcing decisions and help you choose the right specifications for your projects.
Important Disclaimer & Terms of Use
⚠️ Important Disclaimer
The information provided in this guide, including content regarding manufacturers, technical specifications, and market analysis, is for informational and educational purposes only. It does not constitute professional procurement advice, financial advice, or legal advice.
While we have made every effort to ensure the accuracy and timeliness of the information, we are not responsible for any errors, omissions, or outdated information. Market conditions, company details, and technical standards are subject to change.
B2B buyers must conduct their own independent and thorough due diligence before making any purchasing decisions. This includes contacting suppliers directly, verifying certifications, requesting samples, and seeking professional consultation. The risk of relying on any information in this guide is borne solely by the reader.
Strategic Sourcing Conclusion and Outlook for welded wire mesh manufacturer
In the evolving landscape of the welded wire mesh industry, strategic sourcing emerges as a critical factor for international B2B buyers. By prioritizing quality, reliability, and cost-effectiveness, companies can significantly enhance their supply chain resilience. Buyers should consider local and global suppliers who can meet diverse regulatory standards and offer competitive pricing without compromising on quality. Establishing long-term relationships with manufacturers not only fosters trust but also provides insights into market trends and innovations.
How can international buyers leverage strategic sourcing for better outcomes? It’s essential to engage in thorough market research and supplier evaluation. This approach allows buyers from Africa, South America, the Middle East, and Europe to identify the best manufacturers that align with their specific needs. Additionally, embracing digital tools for communication and transaction can streamline processes and reduce lead times.
Looking ahead, the demand for welded wire mesh is poised to grow across various sectors, including construction and agriculture. International B2B buyers are encouraged to remain proactive, adapting to changes in market dynamics while seeking sustainable and innovative solutions from reliable manufacturers. By doing so, they can not only secure their supply chains but also contribute to the industry’s advancement.