Discover Cost-Saving Tips from Top Hammer Mill Suppliers (2025)
Introduction: Navigating the Global Market for hammer mill supplier
In the intricate landscape of global commerce, sourcing a reliable hammer mill supplier poses a significant challenge for international B2B buyers, particularly those from Africa, South America, the Middle East, and Europe. The diversity of available products, coupled with varying quality standards and regional regulations, can make the procurement process daunting. This guide aims to demystify the complexities of selecting the right hammer mill supplier by providing a comprehensive overview of types, applications, and industry-specific considerations that impact purchasing decisions.
From understanding the different types of hammer mills—such as industrial-grade models versus those suitable for small-scale operations—to exploring their applications across various sectors like agriculture, food processing, and recycling, this guide covers critical aspects that influence effective sourcing. Additionally, we delve into strategies for vetting suppliers, ensuring compliance with international standards, and evaluating total cost of ownership, enabling buyers to make informed choices.
By equipping B2B buyers with actionable insights and practical tools, this guide empowers them to navigate the global market confidently. Whether you are operating in the bustling markets of Poland or the emerging economies of Africa, our insights will help you identify reputable suppliers and optimize your procurement process, ensuring that you secure the best products at competitive prices. Embrace the opportunity to enhance your operational efficiency and profitability through informed sourcing of hammer mills.
Understanding hammer mill supplier Types and Variations
Type Name | Key Distinguishing Features | Primary B2B Applications | Brief Pros & Cons for Buyers |
---|---|---|---|
Industrial Hammer Mill | High throughput, robust construction | Large-scale manufacturing, agriculture | Pros: Efficient for bulk processing; Cons: Higher initial cost. |
Laboratory Hammer Mill | Smaller size, precise output | R&D, small batch production | Pros: Ideal for testing; Cons: Limited capacity. |
Mobile Hammer Mill | Portable design, flexible applications | On-site processing, construction sites | Pros: Versatile and convenient; Cons: May sacrifice power. |
Feed Hammer Mill | Specialized for animal feed production | Livestock feed processing | Pros: Optimized for feed; Cons: Less adaptable for other uses. |
Grain Hammer Mill | Designed for grain milling | Grain processing, flour production | Pros: High efficiency for grains; Cons: Not suitable for other materials. |
What are the Characteristics of Industrial Hammer Mills?
Industrial hammer mills are designed for high throughput and durability, making them ideal for large-scale manufacturing processes. These mills often feature heavy-duty construction materials and powerful motors that allow them to handle significant volumes of materials, including grains, wood, and various industrial products. When considering an industrial hammer mill, B2B buyers should evaluate the machine’s capacity, energy efficiency, and maintenance requirements, as these factors can significantly impact operational costs and productivity.
How Do Laboratory Hammer Mills Differ from Other Types?
Laboratory hammer mills are specifically designed for research and development purposes, offering precise milling capabilities for small batches. These machines are typically more compact and equipped with advanced controls to allow for fine-tuning of particle size and output. Buyers in the pharmaceutical, food, and chemical industries should consider the mill’s ability to produce consistent results and its compatibility with various materials, as this will influence the effectiveness of product development and testing processes.
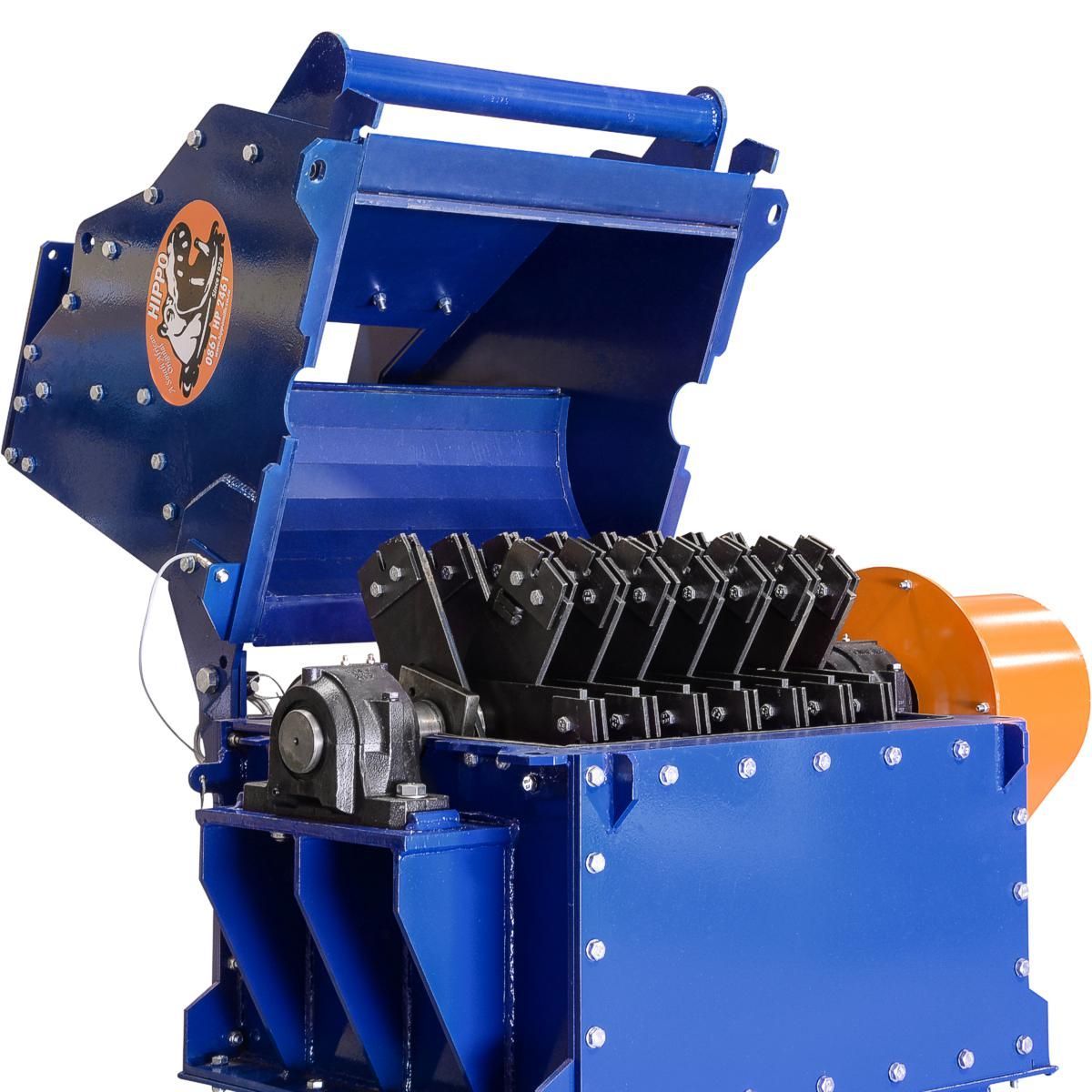
A stock image related to hammer mill supplier.
What Makes Mobile Hammer Mills a Flexible Option?
Mobile hammer mills are designed for portability, allowing them to be easily transported to various job sites. This flexibility makes them particularly useful for on-site processing in industries such as construction and agriculture. While they provide significant advantages in terms of convenience and adaptability, buyers should be mindful of potential trade-offs in power and throughput. Assessing the specific needs of the application and the types of materials to be processed is crucial when choosing a mobile hammer mill.
Why Choose a Feed Hammer Mill for Livestock Operations?
Feed hammer mills are tailored for the production of animal feed, optimizing particle size and consistency for livestock nutrition. These mills often incorporate features that enhance efficiency in processing grains and other feed ingredients. For B2B buyers in the agriculture sector, understanding the specific requirements for animal feed production is essential. Considerations should include the mill’s capacity, ease of maintenance, and ability to produce various feed formulations to meet the nutritional needs of different livestock.
How Do Grain Hammer Mills Optimize Grain Processing?
Grain hammer mills are specifically engineered for the efficient milling of grains, making them indispensable in flour production and grain processing operations. These mills typically feature specialized screens and hammers that maximize output while minimizing waste. When selecting a grain hammer mill, buyers should focus on the machine’s milling efficiency, ease of cleaning, and adaptability to different grain types. Understanding these factors can help ensure that the mill meets production demands while maintaining quality standards.
Related Video: Hosokawa Hammer Mill Demonstration
Key Industrial Applications of hammer mill supplier
Industry/Sector | Specific Application of hammer mill supplier | Value/Benefit for the Business | Key Sourcing Considerations for this Application |
---|---|---|---|
Agriculture | Feed Production | Efficient grinding of grains and feed materials, improving animal nutrition and growth rates. | Sourcing for durability and capacity to handle various grain types. |
Food Processing | Spice and Herb Grinding | Consistent particle size for flavor extraction, ensuring quality and compliance with safety standards. | Certification for food safety and hygiene standards. |
Biomass Energy | Wood Pellet Production | Effective size reduction of biomass for energy generation, enhancing combustion efficiency. | Equipment size and power requirements for specific biomass types. |
Pharmaceutical Manufacturing | Powder Milling for Active Ingredients | Precise milling for uniformity and bioavailability of drugs, ensuring therapeutic efficacy. | Compliance with GMP standards and ability to handle sensitive materials. |
Mining and Minerals | Ore Processing | Reduction of ore size for improved extraction processes, enhancing recovery rates. | Capacity to handle abrasive materials and ensure operational efficiency. |
How is Hammer Mill Supplier Used in Agriculture Feed Production?
In the agriculture sector, hammer mills are extensively utilized for feed production. They efficiently grind grains and other feed materials to a uniform particle size, which is crucial for optimal animal nutrition. This process not only enhances the digestibility of the feed but also promotes better growth rates in livestock. For international buyers, especially from Africa and South America, sourcing hammer mills that can handle diverse grain types and have robust construction is essential. Durability and maintenance support are key considerations to ensure long-term operation in often challenging environments.
What Role Does Hammer Mill Supplier Play in Food Processing for Spices?
In food processing, particularly in spice and herb grinding, hammer mills are vital for achieving consistent particle sizes that enhance flavor extraction. This uniformity is crucial for maintaining quality and meeting safety standards in food production. Buyers in Europe and the Middle East should prioritize suppliers that comply with food safety certifications, ensuring that the equipment meets stringent hygiene requirements. Additionally, the ability to customize the milling process for different spices can provide a competitive edge in the market.
How Does Hammer Mill Supplier Facilitate Biomass Energy Production?
For the biomass energy sector, hammer mills are instrumental in wood pellet production. They reduce the size of biomass materials, such as wood chips and agricultural residues, to prepare them for energy generation. This size reduction is essential for enhancing the combustion efficiency of the pellets. Buyers from regions like Africa and South America should consider the power requirements and capacity of the hammer mills to ensure they can handle the specific types of biomass available locally. Additionally, energy efficiency and operational costs are critical factors in sourcing decisions.
Why is Hammer Mill Supplier Important in Pharmaceutical Manufacturing?
In pharmaceutical manufacturing, hammer mills are used for milling active ingredients into fine powders. This process is critical for ensuring uniformity and bioavailability, which directly impacts the therapeutic efficacy of medications. International buyers, particularly from Europe, need to ensure that the suppliers comply with Good Manufacturing Practices (GMP) and can handle sensitive materials without contamination. The ability to provide precise milling solutions tailored to specific pharmaceutical needs is a significant advantage for suppliers in this sector.
How Do Hammer Mill Suppliers Contribute to Mining and Minerals Processing?
In the mining and minerals industry, hammer mills are employed for ore processing, where they reduce the size of ore to facilitate improved extraction processes. This size reduction is crucial for maximizing recovery rates of valuable minerals. Buyers from regions rich in mineral resources, such as Africa and South America, should focus on sourcing hammer mills that can withstand abrasive materials and provide reliable operational efficiency. Additionally, considerations around maintenance and parts availability are vital to minimize downtime and maintain productivity.
Related Video: Bühler Multimpact™ Hammer Mill Technology
3 Common User Pain Points for ‘hammer mill supplier’ & Their Solutions
Scenario 1: Inefficient Material Processing and High Downtime
The Problem: For many international B2B buyers, particularly those in the agricultural and recycling sectors, a common pain point is the inefficiency of their current hammer mill systems. Buyers often report frequent breakdowns and maintenance issues that lead to significant downtime. This not only affects production schedules but also results in lost revenue and increased operational costs. For instance, a company in South Africa relying on a hammer mill for maize processing might experience delays due to wear and tear, leading to a backlog in orders and customer dissatisfaction.
The Solution: To combat inefficiency, buyers should prioritize sourcing hammer mills that are designed for durability and ease of maintenance. When evaluating suppliers, inquire about the materials used in the construction of the mills and whether they offer extended warranties. Additionally, consider suppliers that provide comprehensive training on proper operation and maintenance practices. Implementing a preventive maintenance schedule can also drastically reduce downtime. Buyers should keep spare parts on hand or establish a reliable supply chain for quick replacements. This proactive approach not only minimizes disruptions but also enhances overall production efficiency.
Scenario 2: Difficulty in Sourcing the Right Hammer Mill for Specific Needs
The Problem: Another significant challenge faced by B2B buyers is identifying the right hammer mill that meets their specific processing requirements. For instance, a company in Turkey might need a hammer mill tailored for fine particle size reduction of specific materials, such as plastics or grains. The broad range of options available can be overwhelming, leading to confusion and the risk of investing in equipment that does not meet operational needs.
The Solution: To effectively source the right hammer mill, buyers should conduct a thorough needs assessment before engaging with suppliers. This assessment should include the types of materials to be processed, desired particle size, and expected production volume. Buyers should then communicate these specifications clearly to potential suppliers. Requesting detailed product catalogs and performance data can help in comparing different models. Furthermore, consider engaging in pilot testing with suppliers who offer trial periods or demo units. This hands-on experience can provide invaluable insights into the equipment’s performance and suitability for specific applications, reducing the risk of misinvestment.
Scenario 3: Navigating Import Regulations and Compliance Issues
The Problem: For international buyers, especially from regions like Africa and South America, navigating import regulations and compliance issues can be a daunting task when procuring hammer mills. Each country has its own set of regulations concerning machinery imports, which can lead to delays, additional costs, and even legal complications. For example, a buyer in Brazil might face unexpected tariffs or documentation requirements that complicate the import process.
The Solution: To mitigate these challenges, buyers should familiarize themselves with the regulatory landscape of their home country before initiating a purchase. Engaging a local consultant who specializes in import regulations can provide critical insights and guidance. Additionally, work closely with the hammer mill supplier to ensure they provide all necessary documentation, such as compliance certificates and import permits. Requesting detailed shipping information and timelines can also help in anticipating potential delays. Establishing a strong communication channel with the supplier can facilitate a smoother process, ultimately leading to timely delivery and compliance with all regulations.
Strategic Material Selection Guide for hammer mill supplier
When selecting materials for hammer mills, international B2B buyers must consider various factors that influence performance, durability, and cost-effectiveness. Below is an analysis of common materials used in hammer mill manufacturing, focusing on their properties, advantages, disadvantages, and specific considerations for buyers from Africa, South America, the Middle East, and Europe.
What Are the Key Properties of Carbon Steel in Hammer Mills?
Carbon steel is a widely used material in hammer mill construction due to its excellent strength-to-weight ratio. Its properties include high tensile strength and good wear resistance, making it suitable for handling various materials. However, carbon steel has limited corrosion resistance, which can be a concern in humid or corrosive environments.
Pros & Cons:
– Pros: High durability, cost-effective, and easy to machine.
– Cons: Prone to rusting if not properly coated, requiring additional maintenance.
Impact on Application:
Carbon steel is compatible with a wide range of agricultural and industrial materials, making it a versatile choice for many applications. However, its susceptibility to corrosion may limit its use in specific environments.
Considerations for International Buyers:
Buyers should ensure compliance with international standards such as ASTM A36 or DIN 17100. Additionally, consider the local climate and environmental conditions when selecting carbon steel for hammer mills.
How Does Stainless Steel Enhance Performance in Hammer Mills?
Stainless steel is known for its exceptional corrosion resistance and hygiene properties, making it ideal for applications where cleanliness is crucial, such as food processing. The material can withstand high temperatures and pressures, ensuring reliable performance.
Pros & Cons:
– Pros: Excellent durability, corrosion resistance, and low maintenance.
– Cons: Higher cost compared to carbon steel and more complex manufacturing processes.
Impact on Application:
Stainless steel is particularly suitable for applications involving abrasive materials or where sanitation is critical. Its resistance to corrosion ensures longevity and reliability in harsh environments.
Considerations for International Buyers:
Buyers should look for compliance with standards like ASTM A240 or JIS G4303. Additionally, they should consider the availability of stainless steel grades, such as 304 or 316, which may vary by region.
What Role Does Alloy Steel Play in Hammer Mill Construction?
Alloy steel combines various elements to enhance specific properties, such as toughness and wear resistance. This material is particularly effective in high-stress applications, where standard carbon steel may fail.
Pros & Cons:
– Pros: Superior wear resistance and toughness, making it suitable for heavy-duty applications.
– Cons: Higher manufacturing complexity and cost.
Impact on Application:
Alloy steel is ideal for processing hard materials or in environments with high wear rates. Its enhanced properties ensure that hammer mills maintain performance over time.
Considerations for International Buyers:
Buyers should ensure that alloy steel grades meet relevant standards, such as ASTM A514 or DIN 1.7225. Understanding local supply chains for alloy steel is also crucial for timely procurement.
How Does Cast Iron Compare for Hammer Mill Applications?
Cast iron is another common material used in hammer mills, particularly for the housing and base components. It offers good wear resistance and vibration dampening properties, making it a stable choice for heavy machinery.
Pros & Cons:
– Pros: Excellent vibration absorption and wear resistance.
– Cons: Brittle nature can lead to cracking under high stress.
Impact on Application:
Cast iron is suitable for applications where stability and noise reduction are essential. However, its brittleness may limit its use in high-impact scenarios.
Considerations for International Buyers:
Buyers should verify that the cast iron meets standards such as ASTM A48. They should also consider the logistics of sourcing cast iron components, particularly in regions where it may be less readily available.
Summary Table of Material Selection for Hammer Mills
Material | Typical Use Case for hammer mill supplier | Key Advantage | Key Disadvantage/Limitation | Relative Cost (Low/Med/High) |
---|---|---|---|---|
Carbon Steel | General-purpose milling | High durability and cost-effective | Prone to rusting | Low |
Stainless Steel | Food processing and sanitary applications | Excellent corrosion resistance | Higher cost and complexity | High |
Alloy Steel | Heavy-duty applications | Superior wear resistance | Higher manufacturing complexity | Medium |
Cast Iron | Base and housing components | Good vibration dampening | Brittle nature can lead to cracking | Medium |
This strategic material selection guide provides valuable insights for international B2B buyers, helping them make informed decisions that align with their specific operational needs and regional considerations.
In-depth Look: Manufacturing Processes and Quality Assurance for hammer mill supplier
What Are the Key Manufacturing Processes for Hammer Mills?
When considering a hammer mill supplier, it’s crucial to understand the manufacturing processes that ensure the quality and reliability of the equipment. The typical manufacturing process for hammer mills can be broken down into several main stages: material preparation, forming, assembly, and finishing.
1. Material Preparation: What Materials Are Used in Hammer Mill Manufacturing?
The first stage involves selecting high-quality raw materials, which typically include carbon steel or stainless steel. Suppliers often source these materials from reputable vendors to guarantee their durability and performance. The materials must undergo rigorous testing to ensure they meet specified standards, especially for heavy-duty applications.
2. Forming: How Are Hammer Mills Shaped and Constructed?
Once the materials are prepared, the forming process begins. This stage involves techniques such as cutting, machining, and welding. Advanced methods like laser cutting and CNC machining are commonly used to achieve precise dimensions and shapes. The forming stage is critical, as any inaccuracies can lead to inefficiencies in operation and increased wear over time.
3. Assembly: What Does the Assembly Process Entail?
The assembly process is where the various components, such as the hammers, screen, and casing, are brought together. Skilled technicians perform this task, ensuring that all parts fit together correctly. During this stage, suppliers may also incorporate safety features and user-friendly designs, which are increasingly important for international buyers.
4. Finishing: How Is the Final Product Prepared for Market?
The final stage of manufacturing is finishing, which includes surface treatments like powder coating or galvanizing to enhance corrosion resistance. This is particularly vital for buyers in humid or coastal regions, where equipment is susceptible to rust and wear. Quality assurance measures are implemented throughout the finishing process to ensure the final product meets all specifications.
What Quality Assurance Measures Should B2B Buyers Consider?
Quality assurance (QA) is a critical aspect of hammer mill manufacturing, as it ensures that the final product meets international standards and customer expectations. Understanding the relevant quality assurance practices can help B2B buyers make informed purchasing decisions.
Relevant International Standards: Which Certifications Should Hammer Mill Suppliers Have?
For international B2B buyers, it’s essential to verify that suppliers adhere to recognized quality standards. ISO 9001 is the most widely adopted quality management standard, ensuring consistent quality and continuous improvement. Additionally, industry-specific certifications like CE marking (for compliance with EU regulations) and API certification (for equipment used in the petroleum industry) can be significant indicators of quality.
QC Checkpoints: What Are the Key Quality Control Stages?
Quality control typically involves several checkpoints throughout the manufacturing process:
- Incoming Quality Control (IQC): This is the first stage where raw materials are inspected for quality before they enter the production process.
- In-Process Quality Control (IPQC): During manufacturing, regular checks ensure that the components are being produced according to specifications.
- Final Quality Control (FQC): After assembly, the finished hammer mills undergo a thorough inspection and testing phase before they are shipped.
Each of these checkpoints is vital for ensuring that the final product performs reliably in the field.
Common Testing Methods: How Are Hammer Mills Tested for Quality?
Testing methods for hammer mills can vary but generally include:
- Performance Testing: Assessing the mill’s efficiency and capacity under various operating conditions.
- Durability Testing: Simulating prolonged use to evaluate wear and tear on components.
- Safety Testing: Ensuring that the equipment meets safety standards to protect users.
B2B buyers should inquire about the specific testing methods used by their suppliers to ensure that they meet their operational needs.
How Can B2B Buyers Verify Supplier Quality Control?
Verifying a supplier’s quality control measures is crucial for international buyers. Here are some actionable steps to ensure quality:
1. Conduct Supplier Audits: What Should B2B Buyers Look For?
Regular audits are essential to assess a supplier’s compliance with quality standards. Buyers should look for documentation of quality procedures, certifications, and evidence of testing and inspection processes. An on-site audit can provide valuable insights into the supplier’s manufacturing capabilities and quality assurance practices.
2. Request Quality Reports: How Can Documentation Help?
Buyers should request detailed quality reports from suppliers, which outline the results of inspections, tests, and any corrective actions taken. This documentation can provide assurance that the supplier maintains high standards throughout the manufacturing process.
3. Engage Third-Party Inspectors: Why Is This Important?
Utilizing third-party inspection services can provide an unbiased assessment of a supplier’s quality control measures. These inspectors can verify compliance with international standards and provide a report that can be crucial for buyers, especially in regions like Africa and South America, where local regulations may differ significantly.
What Are the Quality Control Nuances for International B2B Buyers?
Understanding the specific quality control nuances for international transactions is vital for B2B buyers from Africa, South America, the Middle East, and Europe. These regions may have different regulatory requirements, which can affect product compliance and quality assurance.
Regional Compliance: How Do Regulations Vary?
Buyers should be aware that compliance regulations can differ significantly across regions. For example, European buyers must ensure CE compliance, while buyers in the Middle East may require certifications that align with local standards. Understanding these nuances can help buyers avoid costly mistakes and ensure that their equipment is compliant with local laws.
Cultural Considerations: How Do Business Practices Affect Quality Assurance?
Cultural differences can also play a role in quality assurance practices. For instance, some regions may prioritize personal relationships and trust in supplier dealings, while others may emphasize formal contracts and documentation. Buyers should adapt their approach based on the cultural context of their suppliers.
Conclusion: Why Is Understanding Manufacturing and Quality Assurance Crucial for B2B Buyers?
In conclusion, a comprehensive understanding of the manufacturing processes and quality assurance measures for hammer mills is essential for B2B buyers. By focusing on these aspects, buyers can ensure they choose reliable suppliers that meet their operational needs, ultimately leading to more successful business outcomes.
Practical Sourcing Guide: A Step-by-Step Checklist for ‘hammer mill supplier’
In the quest for sourcing a reliable hammer mill supplier, international B2B buyers must navigate a multitude of factors to ensure they make informed decisions. This checklist serves as a practical guide to streamline the sourcing process, enabling buyers from regions such as Africa, South America, the Middle East, and Europe to find the best suppliers for their specific needs.
Step 1: Define Your Technical Specifications
Before reaching out to potential suppliers, it’s essential to clearly outline your technical requirements. Consider factors such as the desired capacity, power consumption, and material to be processed. Defining these specifications will help you communicate effectively with suppliers and ensure that the hammer mills they offer meet your operational needs.
Step 2: Conduct Market Research on Suppliers
Thorough market research is vital to identify reputable hammer mill suppliers. Utilize industry reports, online directories, and trade shows to gather a list of potential candidates. Pay attention to suppliers that have established a presence in your region, as they may better understand local market demands and regulations.
Step 3: ✅ Verify Supplier Certifications
Ensure that the suppliers you are considering possess relevant industry certifications. Certifications such as ISO 9001 for quality management or CE marking for compliance with European standards are indicators of a supplier’s commitment to quality. This step is crucial as it can affect both product reliability and safety in your operations.
Step 4: Evaluate Supplier Experience and Reputation
Assessing a supplier’s experience in the hammer mill industry is essential. Look for suppliers that have been in business for several years and have a track record of serving clients in your sector. Check online reviews, testimonials, and case studies to gauge their reputation. Engaging with past clients can provide insights into the supplier’s reliability and service quality.
Step 5: Request Detailed Quotations
Once you have shortlisted potential suppliers, request detailed quotations that include pricing, terms of delivery, and warranty information. A comprehensive quotation allows for better comparison and negotiation. Ensure that the pricing includes all potential costs, such as shipping, customs duties, and installation.
Step 6: Understand After-Sales Support and Service
After-sales support is a critical aspect of your supplier relationship. Inquire about the level of technical support they offer, including installation, maintenance, and spare parts availability. A supplier with robust after-sales service can significantly reduce downtime and improve the longevity of your hammer mill.
Step 7: Negotiate Terms and Conditions
Finally, engage in negotiations to secure favorable terms. Discuss payment terms, delivery schedules, and warranty conditions. Clear agreements on these terms will help prevent misunderstandings and ensure a smooth procurement process.
By following this checklist, B2B buyers can enhance their sourcing strategy for hammer mills, ensuring that they partner with suppliers who meet their technical requirements, offer competitive pricing, and provide excellent support throughout the product lifecycle.
Comprehensive Cost and Pricing Analysis for hammer mill supplier Sourcing
What Are the Key Cost Components in Hammer Mill Supplier Pricing?
When sourcing hammer mills, understanding the cost structure is essential for international B2B buyers. The primary cost components include:
-
Materials: The choice of raw materials significantly impacts the overall cost. High-quality steel, for instance, enhances durability but increases expenses. Buyers should consider sourcing from local suppliers to reduce material costs.
-
Labor: Labor costs vary by region and can influence the price of manufacturing hammer mills. Countries with lower labor costs may offer more competitive pricing, but it’s crucial to assess the skill level and training of the workforce involved in production.
-
Manufacturing Overhead: This includes utilities, rent, and other operational costs that contribute to the final price. Buyers should inquire about the supplier’s production efficiency, as lower overhead can lead to reduced pricing.
-
Tooling: The initial setup for manufacturing hammer mills can be costly, particularly if custom tooling is required. Buyers should discuss tooling costs upfront, especially when considering customization.
-
Quality Control (QC): Effective QC processes ensure product reliability but can add to the cost. Suppliers with robust QC measures might charge more, yet they provide assurance of quality, which can save costs in the long run.
-
Logistics: Shipping and handling costs can vary widely based on distance and shipping method. Buyers should evaluate their logistics options and consider local suppliers to minimize these expenses.
-
Margin: Finally, suppliers will include their profit margins in the pricing. Understanding the standard margins in the industry can provide leverage during negotiations.
How Do Price Influencers Affect Hammer Mill Sourcing?
Several factors can influence the pricing of hammer mills, particularly for international buyers:
-
Volume and Minimum Order Quantity (MOQ): Larger orders can lead to significant discounts. Buyers should assess their needs to negotiate favorable pricing based on volume.
-
Specifications and Customization: Custom features can drive up costs. It’s essential to balance specific requirements with budget constraints, ensuring that customization aligns with operational needs without unnecessary expense.
-
Materials and Quality Certifications: Premium materials and certifications (like ISO or CE) enhance product reliability but come at a higher price. Buyers should weigh the benefits of certified products against budget limitations.
-
Supplier Factors: The supplier’s reputation, experience, and location can influence pricing. Established suppliers might charge more due to their reliability and service quality, which can justify the cost.
-
Incoterms: Understanding Incoterms (International Commercial Terms) is crucial for pricing. Different terms can affect the total cost, including who bears responsibility for shipping and insurance, impacting overall budgeting.
What Are Effective Buyer Tips for Hammer Mill Sourcing?
To navigate the complexities of hammer mill pricing, international buyers can employ several strategies:
-
Negotiate Wisely: Leverage volume and long-term relationships to negotiate better terms. Don’t hesitate to ask for discounts or additional services, such as extended warranties.
-
Focus on Cost-Efficiency: Analyze not just the initial purchase price but the Total Cost of Ownership (TCO). Consider maintenance, operational efficiency, and potential downtime when evaluating options.
-
Understand Pricing Nuances: Be aware of regional pricing variances. For instance, suppliers in Europe may have different pricing strategies compared to those in Africa or South America due to local market conditions.
-
Research and Benchmark: Conduct thorough research on market prices for hammer mills. Benchmarking against competitors can provide insights into fair pricing and help in negotiations.
-
Request Transparent Pricing: Ask suppliers for a detailed breakdown of costs to understand the pricing structure. This transparency can help identify areas for potential savings.
Conclusion
In conclusion, a comprehensive understanding of cost components, price influencers, and effective negotiation strategies is vital for international B2B buyers sourcing hammer mills. By considering these factors, buyers from Africa, South America, the Middle East, and Europe can make informed decisions that align with their operational needs and budget constraints. It is advisable to seek indicative prices and be prepared for variations based on specific requirements and market conditions.
Alternatives Analysis: Comparing hammer mill supplier With Other Solutions
Understanding the Importance of Alternative Solutions in Hammer Mill Procurement
When considering the procurement of a hammer mill, it’s essential for B2B buyers to evaluate alternative solutions that can achieve similar objectives. This comparison not only helps in identifying the most cost-effective and efficient option but also ensures that the specific needs of different markets, such as Africa, South America, the Middle East, and Europe, are met. In this section, we will compare hammer mills with two viable alternatives: Roller Mills and Pin Mills.
Comparison Table of Hammer Mill Supplier and Alternatives
Comparison Aspect | Hammer Mill Supplier | Roller Mill | Pin Mill |
---|---|---|---|
Performance | High throughput, versatile | Efficient for fine grinding | Excellent for fine to ultra-fine grinding |
Cost | Moderate to high | Generally lower than hammer mills | Higher initial investment |
Ease of Implementation | Requires skilled labor | Easier to operate | Requires specialized training |
Maintenance | Moderate maintenance needs | Lower maintenance frequency | Higher maintenance due to complexity |
Best Use Case | Grain and biomass processing | Flour milling, feed production | Pharmaceuticals, food, and chemical industries |
What Are the Advantages and Disadvantages of Roller Mills?
Roller Mills are an alternative that many B2B buyers consider due to their efficiency in producing fine particles. They work by compressing material between two cylindrical rollers, which can be adjusted to achieve the desired particle size. The primary advantage of roller mills is their ability to produce uniform particle sizes, which is crucial in industries like flour milling. Additionally, they typically have lower operational costs and require less energy compared to hammer mills. However, they may not be as versatile when it comes to handling different types of materials and require specific adjustments to optimize performance for various applications.
How Do Pin Mills Compare to Hammer Mills?
Pin Mills utilize high-speed rotating discs with pins to grind materials into fine particles, making them suitable for industries that require ultra-fine milling, such as pharmaceuticals and food processing. The significant advantage of pin mills is their ability to produce very fine particles with a narrow particle size distribution. However, this comes at a higher cost both in terms of initial investment and maintenance. The complexity of their design may also necessitate specialized training for operators, which could be a barrier for some businesses in emerging markets.
How to Choose the Right Solution for Your Needs
In conclusion, selecting the right milling solution involves a careful analysis of your specific requirements, including the type of material to be processed, desired particle size, budget constraints, and operational capabilities. Hammer mills offer versatility and high throughput, making them suitable for various applications. In contrast, roller mills and pin mills present unique advantages for specific industries. Buyers should assess their operational context and long-term goals to determine which milling technology aligns best with their business needs. By doing so, they can ensure not only cost-effectiveness but also operational efficiency and product quality.
Essential Technical Properties and Trade Terminology for hammer mill supplier
What Are the Key Technical Properties of Hammer Mills?
When selecting a hammer mill supplier, understanding the essential technical properties is critical for ensuring optimal performance and reliability. Below are several key specifications that international B2B buyers should consider:
1. Material Grade
The material used for constructing the hammer mill significantly impacts its durability and performance. High-quality steel alloys are commonly employed, as they provide resistance to wear and tear, especially in high-volume operations. Buyers should prioritize suppliers who use industry-standard materials that comply with international specifications to ensure longevity and efficiency.
2. Tolerance Levels
Tolerance refers to the allowable deviation from a specified dimension, which is crucial for ensuring that all components fit and operate seamlessly together. In hammer mills, precise tolerances can affect the efficiency of the grinding process. Buyers should inquire about the tolerance levels a supplier adheres to, as tighter tolerances often correlate with higher-quality machinery, leading to reduced maintenance costs and downtime.
3. Capacity
The capacity of a hammer mill is typically measured in tons per hour (TPH) and indicates how much material the mill can process within a given timeframe. For businesses scaling their operations, understanding capacity requirements is vital. Buyers should evaluate their production needs and ensure the hammer mill’s capacity aligns with their operational goals to avoid bottlenecks in the production line.
4. Power Consumption
Power consumption is an essential consideration for cost management and environmental impact. Hammer mills can vary in energy efficiency, with some models designed to reduce electricity usage while maintaining performance. International buyers should assess the energy consumption ratings provided by suppliers, as this can significantly influence operational costs over time.
5. Noise Levels
Noise pollution can be a concern in many industrial settings. Hammer mills can generate significant noise, which may necessitate additional soundproofing measures. Buyers should inquire about the noise levels of different models and consider suppliers that offer quieter options, especially if machinery will be used in populated areas or enclosed spaces.
What Are Common Trade Terms Related to Hammer Mill Suppliers?
Familiarity with industry jargon and trade terminology is essential for effective communication and negotiation with suppliers. Here are several key terms that international B2B buyers should understand:
1. OEM (Original Equipment Manufacturer)
An OEM is a company that produces parts and equipment that may be marketed by another manufacturer. Understanding whether a supplier is an OEM can be crucial for quality assurance, as OEMs often adhere to stringent manufacturing standards. Buyers should consider sourcing from OEMs to ensure they receive reliable and high-quality products.
2. MOQ (Minimum Order Quantity)
MOQ refers to the smallest quantity of a product that a supplier is willing to sell. Understanding MOQ is vital for budgeting and inventory management. International buyers should negotiate MOQs that align with their purchasing capabilities to avoid overstocking or the need for frequent reorders.
3. RFQ (Request for Quotation)
An RFQ is a formal document requesting price quotes from suppliers for specific products or services. When dealing with hammer mill suppliers, submitting an RFQ can help buyers compare prices, terms, and conditions across different vendors. A well-prepared RFQ can streamline the procurement process and lead to more favorable terms.
4. Incoterms (International Commercial Terms)
Incoterms are a set of predefined commercial terms published by the International Chamber of Commerce (ICC) that define the responsibilities of buyers and sellers in international transactions. Familiarity with these terms helps buyers understand shipping costs, risks, and responsibilities. Common Incoterms include FOB (Free On Board) and CIF (Cost, Insurance, and Freight), which clarify who pays for transportation and insurance.
5. Lead Time
Lead time is the duration between placing an order and receiving the goods. Understanding lead times is crucial for project planning and inventory management. Buyers should inquire about a supplier’s lead times to ensure they align with their production schedules and minimize delays.
By grasping these technical properties and trade terms, international B2B buyers can make informed decisions when selecting a hammer mill supplier, ultimately leading to more efficient operations and better investment outcomes.
Navigating Market Dynamics and Sourcing Trends in the hammer mill supplier Sector
What Are the Current Market Dynamics and Key Trends in the Hammer Mill Supplier Sector?
The hammer mill supplier sector is experiencing significant evolution driven by several global factors. A surge in demand for eco-friendly and sustainable materials is reshaping market dynamics, particularly in regions like Africa and South America, where agricultural processing is vital. The increase in biomass energy production is also a key driver, as hammer mills play a crucial role in reducing raw materials into suitable sizes for various applications.
Emerging technologies are transforming the way hammer mills are manufactured and utilized. Automation and IoT integration are enhancing operational efficiencies, allowing buyers to monitor performance remotely and optimize production processes. Furthermore, the rise of e-commerce platforms has made it easier for international buyers, especially in Europe and the Middle East, to source hammer mills directly from manufacturers. This shift is accompanied by an increase in competitive pricing and transparency in the supply chain, enabling buyers to make informed decisions.
International B2B buyers should also be aware of the growing trend towards customization. Suppliers are increasingly offering tailor-made solutions that cater to specific requirements, allowing businesses to maximize productivity and minimize waste. Understanding these market dynamics is essential for B2B buyers looking to stay ahead in a competitive landscape.
How Is Sustainability and Ethical Sourcing Changing the Hammer Mill Supplier Landscape?
Sustainability is becoming a cornerstone of the hammer mill supplier industry, with a growing emphasis on minimizing environmental impact. Many suppliers are adopting sustainable practices in their manufacturing processes, such as using recycled materials and reducing energy consumption. Buyers from Africa and South America, who often prioritize sustainable solutions in their sourcing strategies, will find that partnering with suppliers committed to green practices can enhance their brand reputation and compliance with international standards.
Ethical sourcing is equally critical, particularly in regions where supply chains can be complex and opaque. B2B buyers should prioritize suppliers that demonstrate a commitment to ethical labor practices and fair trade principles. Certifications such as ISO 14001 (Environmental Management) and FSC (Forest Stewardship Council) are increasingly important, as they provide assurance that suppliers adhere to rigorous environmental and ethical standards.
By focusing on sustainability and ethical sourcing, international buyers can not only contribute to environmental conservation but also foster long-term partnerships with suppliers who share similar values. This alignment is crucial in today’s market, where consumers are becoming more conscious of the ethical implications of their purchases.
What Is the Brief Evolution and History of the Hammer Mill Supplier Sector?
The hammer mill has a rich history that dates back to the early 19th century, originally designed for agricultural uses such as grinding grain. Over the years, the technology has evolved significantly, with advancements in material science and engineering leading to more efficient and versatile machines.
In recent decades, the hammer mill supplier sector has expanded to include a variety of applications, from biomass processing to recycling and manufacturing. This evolution has been driven by increased industrial demand and the need for more sustainable processing solutions. As a result, today’s hammer mills are not only more efficient but are also integrated with technology that allows for real-time monitoring and data collection, marking a significant shift from their traditional roots.
Understanding this historical context can provide international B2B buyers with insights into how the sector has adapted to meet changing market needs and can guide them in making informed sourcing decisions.
Frequently Asked Questions (FAQs) for B2B Buyers of hammer mill supplier
-
How do I solve issues with sourcing hammer mills from international suppliers?
To address sourcing challenges, start by clearly defining your requirements, including specifications, capacity, and intended application of the hammer mill. Research potential suppliers through trade directories, industry associations, and online marketplaces. Reach out for quotes and sample products to evaluate quality. Establish clear communication channels and consider using third-party inspection services to ensure product quality before shipping. Building relationships with suppliers can also help mitigate future sourcing issues. -
What is the best hammer mill for processing agricultural materials?
The optimal hammer mill for agricultural materials depends on the type of feedstock you intend to process. For instance, a heavy-duty hammer mill with adjustable screen sizes is ideal for grains, while a fine-grinding mill may be better for fibrous materials like straw or hay. Look for features such as high throughput, energy efficiency, and easy maintenance. Additionally, consider the supplier’s expertise in agricultural applications, as they can provide tailored solutions for your specific needs. -
How do I evaluate the reliability of a hammer mill supplier?
To assess supplier reliability, check their industry reputation through online reviews, testimonials, and case studies. Request references from previous clients, particularly those in your region, to gauge their experiences. Evaluate the supplier’s certifications, quality control processes, and after-sales support. A reliable supplier should also offer warranties on their products and demonstrate a commitment to customer satisfaction through responsive communication and problem resolution. -
What customization options are available when sourcing hammer mills?
Most manufacturers offer customization options to cater to specific industry needs. This may include alterations in size, capacity, motor type, and additional features like dust collection systems or different screen configurations. Communicate your requirements clearly during initial discussions and request detailed specifications. Some suppliers may also provide engineering support to help optimize the design for your operational needs, ensuring that the hammer mill performs efficiently in your application. -
What are the common minimum order quantities (MOQs) for hammer mills?
Minimum order quantities can vary significantly among suppliers. Typically, established manufacturers might have MOQs ranging from one unit for custom orders to several units for standard models. It’s essential to discuss MOQs upfront to align with your procurement strategy, especially if you’re a smaller business. Some suppliers may also offer flexibility in MOQs based on your purchasing history or potential for future orders, so it’s worth negotiating. -
What payment terms should I expect when buying from international hammer mill suppliers?
Payment terms can vary widely based on the supplier’s policies and the buyer’s location. Common terms include a deposit upfront (usually 30-50%) with the balance paid before shipping or upon delivery. For larger orders, suppliers may offer letter of credit options or payment via escrow services for added security. Always clarify payment methods, currency, and any potential fees for international transactions to avoid misunderstandings and ensure a smooth procurement process. -
How do I ensure quality assurance when purchasing hammer mills?
To ensure quality assurance, request documentation that outlines the supplier’s quality control processes, including certifications like ISO 9001. Consider conducting a factory visit or arranging for third-party inspections to verify the manufacturing standards and product quality before shipment. Additionally, inquire about warranties and return policies to safeguard your investment. Establishing a clear quality agreement outlining your expectations can further protect your interests. -
What logistics considerations should I keep in mind when importing hammer mills?
When importing hammer mills, consider the logistics of shipping, including freight costs, shipping times, and customs regulations in your country. Engage with a freight forwarder who understands the specifics of importing machinery to navigate import duties and ensure compliance with local regulations. Additionally, factor in the need for specialized handling during transport, as hammer mills can be bulky and heavy. Planning for these logistics early can help streamline the entire procurement process.
Important Disclaimer & Terms of Use
⚠️ Important Disclaimer
The information provided in this guide, including content regarding manufacturers, technical specifications, and market analysis, is for informational and educational purposes only. It does not constitute professional procurement advice, financial advice, or legal advice.
While we have made every effort to ensure the accuracy and timeliness of the information, we are not responsible for any errors, omissions, or outdated information. Market conditions, company details, and technical standards are subject to change.
B2B buyers must conduct their own independent and thorough due diligence before making any purchasing decisions. This includes contacting suppliers directly, verifying certifications, requesting samples, and seeking professional consultation. The risk of relying on any information in this guide is borne solely by the reader.
Strategic Sourcing Conclusion and Outlook for hammer mill supplier
What Are the Key Takeaways for International B2B Buyers of Hammer Mills?
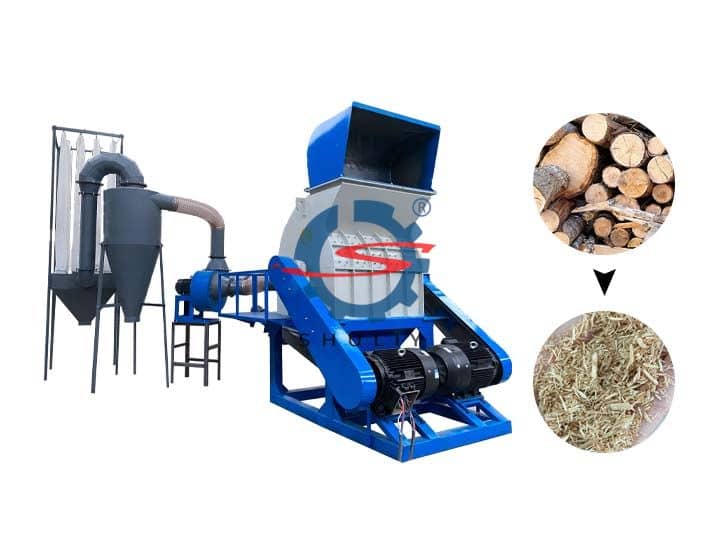
A stock image related to hammer mill supplier.
In conclusion, strategic sourcing for hammer mills presents a multitude of opportunities for international B2B buyers, particularly in regions such as Africa, South America, the Middle East, and Europe. The importance of establishing strong supplier relationships cannot be overstated; it leads to better pricing, improved product quality, and enhanced supply chain resilience. Buyers should prioritize suppliers who demonstrate a commitment to innovation and sustainability, as these factors increasingly influence market competitiveness.
How Can Buyers Prepare for Future Trends in Hammer Mill Sourcing?
Looking ahead, buyers should be proactive in adapting to emerging trends such as digital transformation and automation within the manufacturing sector. Leveraging technology can streamline procurement processes and facilitate better communication with suppliers. Additionally, understanding local regulations and market conditions in your respective regions will be crucial for informed decision-making.
What Is the Next Step for International B2B Buyers?
As you navigate your sourcing strategies, consider conducting thorough market research and engaging with multiple suppliers to identify the best fit for your operational needs. By embracing a strategic approach to sourcing hammer mills, you position your business for long-term success and competitiveness. Take action today—evaluate your current suppliers and explore new partnerships that align with your business objectives.