Discover Cost-Saving Tips from Top Luggage Manufacturers (2025)
Introduction: Navigating the Global Market for luggage manufacturer
Navigating the global market for luggage manufacturers can be a daunting task for international B2B buyers, particularly those from regions like Africa, South America, the Middle East, and Europe. With diverse consumer needs and varying quality standards, sourcing high-quality luggage that meets both functional and aesthetic demands is essential. This guide aims to simplify the procurement process by providing comprehensive insights into the types of luggage available, their applications, and the key factors to consider when vetting suppliers.
From hard-shell suitcases to soft-sided travel bags, understanding the range of products is crucial for making informed purchasing decisions. This guide will delve into the specific needs of different markets, offering actionable tips on supplier evaluation, cost considerations, and logistics management. By addressing these critical areas, we empower B2B buyers to navigate the complexities of international trade effectively.
In this resource, you will find detailed information tailored to various markets, ensuring that your sourcing strategy is both efficient and effective. Whether you are a retailer seeking to expand your product line or a distributor looking for reliable manufacturers, this guide will equip you with the knowledge necessary to make strategic decisions that align with your business goals. Prepare to embark on a journey that will enhance your understanding of the global luggage market, ultimately leading to successful partnerships and increased profitability.
Understanding luggage manufacturer Types and Variations
Type Name | Key Distinguishing Features | Primary B2B Applications | Brief Pros & Cons for Buyers |
---|---|---|---|
Hard-Shell Luggage Manufacturers | Rigid outer casing, often made from polycarbonate or ABS | Durable travel solutions, retail sales | Pros: High protection, weather-resistant. Cons: Heavier and less flexible than soft-shell. |
Soft-Shell Luggage Manufacturers | Flexible materials like nylon or polyester | Casual and business travel, promotional use | Pros: Lightweight, expandable. Cons: Less protection against impacts. |
Custom Luggage Manufacturers | Tailored designs, branding options | Corporate gifts, promotional products | Pros: Brand visibility, unique designs. Cons: Higher costs and longer lead times. |
Eco-Friendly Luggage Manufacturers | Sustainable materials and production processes | Green branding, eco-conscious consumers | Pros: Attracts eco-conscious buyers. Cons: Potentially higher price points. |
Specialty Luggage Manufacturers | Focus on niche markets (e.g., sports, luxury) | Targeted marketing, specialized retail | Pros: Tailored solutions for specific needs. Cons: Limited general appeal. |
What Are the Characteristics of Hard-Shell Luggage Manufacturers?
Hard-shell luggage manufacturers produce cases with a rigid outer shell, typically crafted from durable materials like polycarbonate or ABS. This type of luggage is ideal for international shipping and travel as it offers superior protection against impacts and adverse weather conditions. B2B buyers should consider the weight and storage efficiency, as hard-shell cases can be bulkier compared to their soft-shell counterparts. When sourcing, ensure to evaluate the manufacturer’s reputation for quality and durability.
How Do Soft-Shell Luggage Manufacturers Differ?
Soft-shell luggage manufacturers focus on creating flexible bags made from materials like nylon or polyester. These products are often lighter and can be expanded to accommodate additional items, making them suitable for casual and business travel. B2B buyers should consider the balance between weight and durability when selecting soft-shell luggage. Additionally, the ability to customize designs and branding can enhance promotional efforts, making them an attractive option for businesses looking to market their products.
What Are the Benefits of Custom Luggage Manufacturers?
Custom luggage manufacturers specialize in creating tailored designs that align with specific branding requirements. This type of luggage is particularly valuable for companies looking to use products as corporate gifts or promotional items. While custom luggage can enhance brand visibility, B2B buyers should be aware of the potential for higher costs and longer lead times. It’s crucial to communicate clear specifications and expectations with the manufacturer to ensure that the final product meets branding needs.
Why Choose Eco-Friendly Luggage Manufacturers?
Eco-friendly luggage manufacturers prioritize sustainable materials and production processes, appealing to businesses that wish to enhance their green branding. These products often attract eco-conscious consumers, making them a strategic choice for companies looking to differentiate themselves in a competitive market. However, B2B buyers should consider the potential for higher price points associated with eco-friendly products. It is essential to assess the manufacturer’s commitment to sustainability and the quality of materials used.
What Niche Markets Do Specialty Luggage Manufacturers Target?
Specialty luggage manufacturers cater to niche markets, such as sports enthusiasts or luxury travelers. By focusing on specific consumer needs, these manufacturers can create highly tailored products that resonate with targeted audiences. B2B buyers should evaluate whether these specialized products align with their marketing strategies and customer demographics. While these items may not appeal to the general market, their unique features can provide significant advantages in targeted retail environments.
Key Industrial Applications of luggage manufacturer
Industry/Sector | Specific Application of luggage manufacturer | Value/Benefit for the Business | Key Sourcing Considerations for this Application |
---|---|---|---|
Travel and Tourism | Production of durable luggage for hotels and travel agencies | Enhances guest experience and brand image | Quality materials, customization options, lead times |
Retail | Wholesale luggage for retail stores | Expands product offering and increases sales | Competitive pricing, inventory management, supplier reliability |
Corporate and Business | Branded corporate travel bags for employee use | Strengthens corporate identity and morale | Customization capabilities, bulk order discounts, delivery timelines |
Event Management | Luggage solutions for event organizers | Streamlines logistics and improves attendee experience | Custom branding, durability for transport, eco-friendly options |
E-commerce | Dropshipping luggage products for online retailers | Reduces inventory costs and improves cash flow | Supplier reliability, shipping times, product quality |
How is Luggage Manufacturing Applied in the Travel and Tourism Sector?
In the travel and tourism industry, luggage manufacturers produce durable and stylish luggage for hotels and travel agencies. This application enhances the guest experience by providing high-quality travel solutions that reflect the establishment’s brand image. International B2B buyers must consider sourcing luggage made from robust materials that can withstand various travel conditions while also offering customization options to align with their branding. Lead times are critical in this sector, as timely delivery ensures that businesses can meet customer demands during peak travel seasons.
What Role Does Luggage Manufacturing Play in Retail?
Retail stores benefit significantly from wholesale luggage supply as it allows them to expand their product offerings. This application not only increases sales but also attracts a broader customer base looking for reliable travel solutions. Buyers in this sector should focus on competitive pricing and effective inventory management to optimize their supply chain. Additionally, establishing a relationship with reliable suppliers ensures consistent product availability and quality, which is essential for maintaining customer trust and satisfaction.
How Can Corporate Entities Leverage Luggage Manufacturing?
Corporate and business sectors utilize luggage manufacturers to create branded travel bags for employees. This not only enhances corporate identity but also boosts employee morale by providing them with quality travel gear. For international B2B buyers, customization capabilities are crucial, as they allow businesses to imprint their logos and messages on the products. Bulk order discounts and timely delivery are other key considerations that can significantly impact the overall cost-effectiveness of the procurement process.
Why is Luggage Manufacturing Important for Event Management?
Event organizers often require specialized luggage solutions to facilitate logistics and improve attendee experiences. Manufacturers can provide custom-branded luggage that promotes the event and serves practical purposes, such as transporting materials and personal items. Buyers should prioritize durability, as the luggage needs to withstand the rigors of transport. Eco-friendly options are also gaining traction, appealing to environmentally conscious consumers and businesses alike.
How Does E-commerce Benefit from Luggage Manufacturing?
E-commerce platforms often engage in dropshipping luggage products, allowing them to offer a wide range of items without the burden of holding inventory. This model significantly reduces costs and improves cash flow for online retailers. For B2B buyers in this sector, ensuring supplier reliability is paramount, as it directly affects shipping times and product quality. Additionally, selecting manufacturers who provide high-quality products will enhance customer satisfaction and encourage repeat business.
Related Video: 25 Amazing Uses for IBC Totes
3 Common User Pain Points for ‘luggage manufacturer’ & Their Solutions
Scenario 1: Challenges in Sourcing High-Quality Luggage at Competitive Prices
The Problem:
B2B buyers often struggle to find reliable luggage manufacturers that provide high-quality products at competitive prices. This is particularly true for buyers from emerging markets in Africa and South America, where the supply chain can be inconsistent. Buyers may face issues such as fluctuating prices, subpar materials, or manufacturers unable to meet their specifications, leading to delays and dissatisfaction among their customer base.
The Solution:
To navigate this challenge, B2B buyers should establish strong relationships with multiple manufacturers, allowing them to compare quality and pricing effectively. Utilize platforms like Alibaba or industry-specific trade shows to identify reputable manufacturers with positive reviews. It’s essential to request samples before committing to large orders. Additionally, consider negotiating long-term contracts that lock in prices and ensure product quality. Engage in thorough communication about specifications and quality control measures, which can help mitigate risks associated with sourcing.
Scenario 2: Managing Lead Times and Order Fulfillment Issues
The Problem:
Another common pain point for B2B buyers is managing lead times for orders. Manufacturers in different regions may have varying production schedules, causing delays that can impact inventory and sales. This is especially critical for buyers in Europe and the Middle East, where quick turnaround times can be crucial during peak travel seasons or holiday sales.
The Solution:
To address lead time issues, buyers should implement a robust inventory management system that allows for accurate forecasting and demand planning. Establishing a buffer stock can also help mitigate the impact of delays. Buyers should communicate directly with manufacturers about lead times and potential bottlenecks in the production process. It’s advisable to discuss and agree upon clear timelines and penalties for delays in contracts. Additionally, consider diversifying suppliers across different regions to ensure a backup option in case of unforeseen circumstances.
Scenario 3: Difficulty in Customization and Brand Differentiation
The Problem:
B2B buyers often find it challenging to get customized luggage that aligns with their brand identity. Manufacturers may have limitations on the types of customization they can offer, leading to generic products that fail to stand out in a competitive market. This is particularly a concern for businesses looking to appeal to niche markets in Africa and South America, where brand loyalty can be influenced by unique product offerings.
The Solution:
To overcome customization challenges, buyers should clearly outline their specific branding requirements during the initial stages of communication with manufacturers. Engage manufacturers who specialize in custom luggage solutions and have experience working with brands. It’s beneficial to create a detailed design brief that includes colors, materials, and features that reflect your brand’s identity. Leverage technology by using 3D modeling software to visualize the product before production, ensuring that the final product meets expectations. Building a long-term partnership with a manufacturer that understands your brand can facilitate smoother customization processes in the future.
By addressing these common pain points through strategic sourcing, effective communication, and a focus on customization, B2B buyers can enhance their purchasing experience and improve their product offerings in the competitive luggage market.
Strategic Material Selection Guide for luggage manufacturer
What Are the Key Materials Used in Luggage Manufacturing?
When selecting materials for luggage manufacturing, it’s crucial to consider their properties, advantages, and limitations. Here, we analyze four common materials: Polycarbonate, Nylon, Polyester, and Leather. Each material presents unique characteristics that can significantly impact product performance and market suitability.
How Does Polycarbonate Perform in Luggage Manufacturing?
Key Properties: Polycarbonate is a thermoplastic known for its high impact resistance and lightweight nature. It can withstand significant pressure and temperature variations, making it suitable for both checked and carry-on luggage.
Pros & Cons: The primary advantage of polycarbonate is its durability; it is resistant to cracks and can endure rough handling during travel. However, it tends to be more expensive than other materials, which can increase the final product’s cost. Additionally, while it offers excellent protection, its manufacturing process can be complex, requiring specialized equipment.
Impact on Application: Polycarbonate is ideal for hard-shell suitcases, providing a robust barrier against external impacts. It is compatible with various media, including water and dirt, making it easier to clean.
Considerations for International Buyers: Buyers from regions like Africa and South America should ensure compliance with international safety standards, such as ASTM and ISO, which may affect the choice of polycarbonate for specific markets. Additionally, understanding local preferences for durability and design aesthetics is essential.
What Are the Benefits of Using Nylon in Luggage?
Key Properties: Nylon is a synthetic fabric known for its strength, elasticity, and resistance to abrasion. It can handle varying temperatures and is generally resistant to mold and mildew.
Pros & Cons: The major advantage of nylon is its lightweight nature, which helps reduce overall luggage weight. It is also relatively affordable, making it a popular choice for budget-conscious manufacturers. However, nylon is less durable than polycarbonate and can wear out over time, especially with frequent use.
Impact on Application: Nylon is commonly used in soft-sided luggage, backpacks, and travel accessories. Its flexibility allows for easy storage and packing, while its water-resistant properties help protect contents from moisture.
Considerations for International Buyers: When sourcing nylon luggage, buyers should verify compliance with local regulations regarding synthetic materials. In Europe, for instance, REACH compliance is crucial, while buyers in the Middle East may prioritize UV resistance due to harsh climates.
Why Choose Polyester for Luggage Manufacturing?
Key Properties: Polyester is another synthetic fabric that offers good resistance to stretching and shrinking. It is also quick-drying and resistant to fading, making it suitable for various environmental conditions.
Pros & Cons: Polyester is often more affordable than nylon and polycarbonate, making it an attractive option for manufacturers aiming to produce cost-effective luggage. However, it is generally heavier than nylon and may not offer the same level of durability, especially in high-stress applications.
Impact on Application: Polyester is frequently used in both soft-sided luggage and as a lining material in hard-shell cases. It provides a good balance of durability and affordability, making it suitable for entry-level products.
Considerations for International Buyers: Buyers should be aware of the varying quality standards for polyester in different regions. For example, South American buyers may prefer higher denier polyester for increased durability, while European markets may have specific environmental standards for textile manufacturing.
What Are the Advantages of Leather in Luggage Manufacturing?
Key Properties: Leather is a natural material known for its aesthetic appeal and durability. It can withstand various temperatures and is resistant to water when treated properly.
Pros & Cons: The primary advantage of leather is its premium look and feel, which can elevate a product’s status in the market. However, it is significantly more expensive than synthetic options and requires more maintenance to preserve its quality. Additionally, leather can be heavy, which may not appeal to all consumers.
Impact on Application: Leather is often used in high-end luggage and travel accessories, appealing to luxury markets. Its compatibility with various media, including oils and moisture, can enhance the product’s longevity if properly cared for.
Considerations for International Buyers: Buyers should consider the ethical sourcing of leather, as this can influence consumer perception, particularly in Europe and North America. Compliance with regulations regarding animal products is also critical in many markets.
Summary Table of Material Selection for Luggage Manufacturing
Material | Typical Use Case for luggage manufacturer | Key Advantage | Key Disadvantage/Limitation | Relative Cost (Low/Med/High) |
---|---|---|---|---|
Polycarbonate | Hard-shell suitcases | High impact resistance | Higher manufacturing cost | High |
Nylon | Soft-sided luggage, backpacks | Lightweight and flexible | Less durable over time | Medium |
Polyester | Soft-sided luggage, linings | Cost-effective | Heavier than nylon | Low |
Leather | High-end luggage and accessories | Premium aesthetic | Expensive and requires maintenance | High |
This strategic material selection guide provides international B2B buyers with critical insights into the materials used in luggage manufacturing, helping them make informed decisions based on product performance, market preferences, and compliance requirements.
In-depth Look: Manufacturing Processes and Quality Assurance for luggage manufacturer
What Are the Main Stages in Luggage Manufacturing Processes?
Manufacturing luggage involves a systematic approach that encompasses several key stages, each critical to ensuring the final product meets quality standards and customer expectations. For B2B buyers, understanding these stages can help in evaluating potential suppliers and ensuring the durability and functionality of the products they source.
Material Preparation: Sourcing High-Quality Inputs
The first step in the luggage manufacturing process is material preparation. Manufacturers typically source materials such as polyester, nylon, leather, and various types of plastics. The choice of material significantly impacts the durability, weight, and aesthetics of the luggage.
B2B buyers should ensure that suppliers provide detailed specifications about the materials used, including their origin and compliance with environmental standards. Sustainable sourcing is increasingly becoming important, especially for buyers in Europe and the Middle East, where eco-conscious products are in demand.
Forming: Shaping the Product with Precision
Once materials are prepared, the next step is forming. This involves cutting the materials into specific shapes and sizes needed for the luggage components. Various techniques such as die-cutting, laser cutting, and CNC machining may be used to achieve precision.
For buyers, it’s essential to inquire about the machinery and technology used in the forming process. Advanced technology can lead to more precise cuts and less material waste, ultimately affecting pricing and sustainability.
Assembly: Bringing Components Together
The assembly stage is where individual components—such as zippers, handles, wheels, and the outer shell—are brought together. This process may involve stitching, welding, and riveting. Quality assembly is crucial as it impacts the overall strength and functionality of the luggage.
B2B buyers should look for manufacturers that utilize skilled labor and have a well-defined assembly line process. Quality control during assembly is vital; thus, understanding the workforce’s training and experience can provide insights into the potential quality of the finished product.
Finishing: Final Touches for Quality Assurance
The final stage in the manufacturing process is finishing, where luggage is polished, inspected, and packed. This stage may also include adding branding elements such as logos or labels.
Buyers should check if manufacturers follow a specific finishing standard, as this can influence the product’s marketability. Moreover, ensuring that manufacturers are equipped with modern finishing techniques can enhance the product’s aesthetic appeal and durability.
How Is Quality Assurance Implemented in Luggage Manufacturing?
Quality assurance (QA) is a critical component in luggage manufacturing, ensuring that the products meet both international standards and buyer specifications. For international B2B buyers, understanding the QA processes of potential suppliers can significantly affect their purchasing decisions.
What International Standards Should B2B Buyers Look For?
Manufacturers often adhere to international quality standards such as ISO 9001, which focuses on effective quality management systems. Additionally, certifications like CE marking (Common European Mark) and API (American Petroleum Institute) standards may be relevant, particularly for specialized luggage products.
Buyers should request documentation of these certifications to verify compliance. This can provide assurance that the manufacturer maintains high-quality production processes and adheres to safety regulations.
What Are the Key Quality Control Checkpoints?
Quality control in luggage manufacturing typically involves several checkpoints throughout the production process:
-
Incoming Quality Control (IQC): This stage involves inspecting raw materials upon arrival to ensure they meet specified standards.
-
In-Process Quality Control (IPQC): During the manufacturing process, ongoing inspections ensure that each stage adheres to quality standards, helping to catch defects early.
-
Final Quality Control (FQC): This final inspection occurs before packaging, assessing the finished product against quality benchmarks.
B2B buyers should ask suppliers about their quality control processes and the specific metrics used to evaluate product quality at each checkpoint.
What Common Testing Methods Are Used in Luggage Quality Assurance?
Testing methods can vary based on the materials and intended use of the luggage. Common testing methods include:
- Durability Testing: Assessing how well the luggage withstands wear and tear.
- Water Resistance Testing: Evaluating the material’s ability to repel water.
- Zipper and Handle Strength Testing: Ensuring that these components can withstand the forces they will encounter during use.
For buyers, understanding these tests and their relevance to their target markets can help them make informed sourcing decisions.
How Can B2B Buyers Verify Supplier Quality Control?
To ensure that a potential supplier meets quality standards, B2B buyers should consider the following verification methods:
- Audits: Conducting or requesting third-party audits can provide insights into the manufacturer’s processes and compliance with quality standards.
- Quality Reports: Suppliers should provide documentation detailing their quality assurance processes, including test results and compliance with standards.
- Third-Party Inspections: Hiring independent inspection agencies can offer unbiased assessments of product quality before shipment.
In regions such as Africa and South America, where manufacturing standards may vary, these measures can help mitigate risks associated with sourcing.
What Are the Quality Control Nuances for International B2B Buyers?
International B2B buyers face unique challenges, such as differing quality standards and regulations across regions. For example, compliance with EU regulations may differ significantly from standards in the Middle East or Africa.
Buyers should familiarize themselves with local regulations and standards in their target markets. Engaging with manufacturers who understand these nuances and can provide compliant products can facilitate smoother transactions and enhance market entry.
In summary, understanding the manufacturing processes and quality assurance measures in luggage production is essential for international B2B buyers. By focusing on materials, processes, and quality standards, buyers can make informed decisions that ensure the durability and appeal of the luggage they procure.
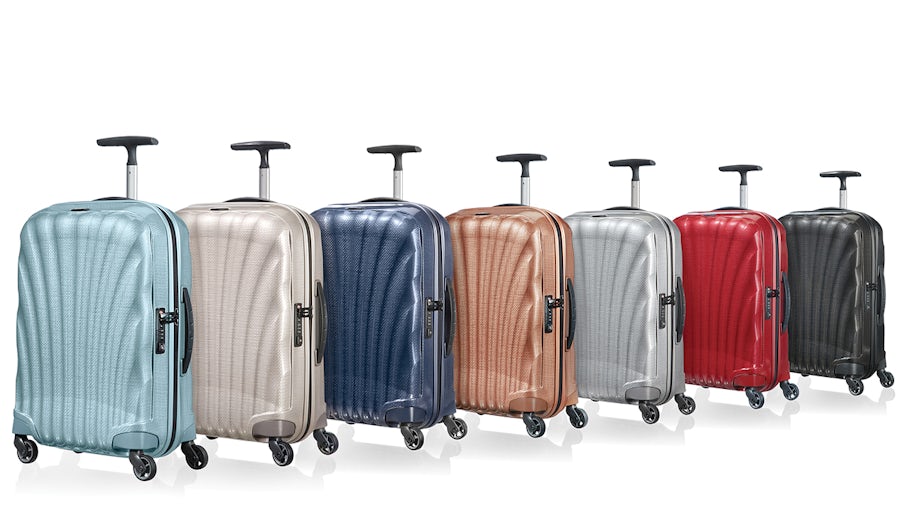
A stock image related to luggage manufacturer.
Practical Sourcing Guide: A Step-by-Step Checklist for ‘luggage manufacturer’
In the competitive landscape of the luggage manufacturing industry, international B2B buyers must adopt a structured approach to sourcing. This guide provides a step-by-step checklist designed to streamline the procurement process, ensuring that buyers from Africa, South America, the Middle East, and Europe make informed decisions when selecting luggage manufacturers.
Step 1: Define Your Technical Specifications
Establishing clear technical specifications is critical for aligning with potential suppliers. Consider the materials, dimensions, and design features that meet your target market’s needs. This clarity will help you communicate effectively with manufacturers and ensure that the products meet quality expectations.
- Material Requirements: Identify whether you need durable materials such as polycarbonate, nylon, or leather.
- Design Features: Consider additional functionalities like expandability, weight, and wheel type.
Step 2: Research and Identify Potential Suppliers
Conduct thorough market research to identify reputable luggage manufacturers. Utilize online directories, industry associations, and trade shows to compile a list of potential suppliers, focusing on those with a strong track record in your target regions.
- Local vs. International Suppliers: Assess the benefits of local suppliers, such as reduced shipping costs and shorter lead times, against international options that may offer lower prices.
- Supplier Reviews and Ratings: Look for feedback from other B2B buyers to gauge reliability and product quality.
Step 3: Evaluate Supplier Capabilities
Before committing to a supplier, it’s crucial to assess their manufacturing capabilities. Request detailed company profiles, including production capacity, technology used, and workforce expertise.
- Production Capacity: Ensure the manufacturer can meet your order volume without compromising quality.
- Technology and Innovation: Investigate if they use modern manufacturing techniques that can enhance product durability and design.
Step 4: Verify Supplier Certifications and Compliance
Confirm that potential suppliers comply with industry standards and certifications relevant to luggage manufacturing. This step is vital for ensuring product quality and safety.
- Quality Certifications: Look for ISO certifications or compliance with international safety standards.
- Environmental Compliance: Verify if the manufacturer follows sustainable practices, which can be a selling point in many markets.
Step 5: Request Samples and Conduct Quality Checks
Before placing a bulk order, request samples to evaluate the quality of the luggage. Conduct thorough inspections to ensure that the samples meet your specifications.
- Quality Assessment: Check for durability, stitching quality, and overall finish.
- User Testing: If possible, have potential customers test the samples to gather feedback on design and functionality.
Step 6: Negotiate Terms and Conditions
Once you have shortlisted potential suppliers, engage in negotiations to establish favorable terms and conditions. This includes pricing, payment terms, lead times, and warranty policies.
- Transparent Pricing: Ensure that all costs are outlined to avoid hidden fees.
- Flexible Payment Options: Discuss payment terms that suit both parties, particularly for large orders.
Step 7: Establish Clear Communication Channels
Effective communication is paramount throughout the sourcing process. Ensure that you and your supplier have established clear channels for ongoing dialogue regarding order status, changes, and issues.
- Regular Updates: Set expectations for updates on production and shipping timelines.
- Point of Contact: Designate a specific representative from both sides to streamline communication.
By following this checklist, international B2B buyers can enhance their sourcing efficiency and establish fruitful partnerships with luggage manufacturers, driving success in their business endeavors.
Comprehensive Cost and Pricing Analysis for luggage manufacturer Sourcing
What Are the Key Cost Components in Luggage Manufacturing?
When sourcing luggage from manufacturers, understanding the cost structure is essential for international B2B buyers. The primary components of costs include:
-
Materials: The type of materials used significantly affects the overall cost. Common materials include polyester, nylon, leather, and various plastics. High-quality materials can enhance durability and appeal but will increase the price.
-
Labor: Labor costs vary by region and can be a major factor in the total cost. Countries with lower labor costs, such as Vietnam or certain regions in Africa, may offer more competitive pricing.
-
Manufacturing Overhead: This encompasses costs related to facility maintenance, utilities, and other operational expenses. A manufacturer’s efficiency and location can influence these costs.
-
Tooling: Initial tooling costs for custom designs or specialized production processes can be significant. These costs are often amortized over large production runs, making them less impactful per unit for larger orders.
-
Quality Control (QC): Implementing robust QC processes ensures product reliability and compliance with international standards, which can add to overall costs but ultimately saves money by reducing returns and defects.
-
Logistics: Shipping and handling costs depend on the shipping method, distance, and volume. For international buyers, understanding Incoterms (International Commercial Terms) is crucial for estimating total shipping costs.
-
Margin: Manufacturers typically include a profit margin in their pricing, which can vary widely depending on the market and competition.
How Do Price Influencers Affect Luggage Sourcing?
Several factors influence pricing in the luggage manufacturing sector:
-
Volume/MOQ (Minimum Order Quantity): Larger orders often yield better pricing per unit. Manufacturers may offer tiered pricing based on the quantity ordered, so negotiating for larger batches can lead to significant savings.
-
Specifications and Customization: Custom designs or unique specifications can increase costs due to additional labor and materials. However, they can also provide a competitive edge in the market.
-
Materials and Quality Certifications: Higher-quality materials and certifications (e.g., ISO, CE) can increase initial costs but may lead to higher customer satisfaction and lower return rates.
-
Supplier Factors: The reputation and reliability of the supplier can influence pricing. Established manufacturers with a strong track record may charge a premium, but they often provide better service and reliability.
-
Incoterms: The choice of Incoterms can significantly impact overall costs. Terms like FOB (Free on Board) or CIF (Cost, Insurance, and Freight) dictate who bears various costs and risks during transportation, affecting the final price.
What Tips Can Help Buyers Negotiate Better Prices?
For international B2B buyers, especially those from Africa, South America, the Middle East, and Europe, navigating the complexities of luggage sourcing requires strategic insights:
-
Negotiation: Always approach negotiations with a clear understanding of your budget and needs. Be prepared to discuss volume commitments or long-term partnerships to secure better pricing.
-
Cost-Efficiency: Evaluate the Total Cost of Ownership (TCO), which includes not only the purchase price but also shipping, handling, and potential returns. Sometimes, a higher upfront cost can lead to lower overall costs due to better quality.
-
Pricing Nuances for International Buyers: Be aware of currency fluctuations and tariffs that may impact the final pricing. Understanding local market conditions in the supplier’s region can also provide leverage during negotiations.
-
Supplier Relationships: Building strong relationships with suppliers can lead to better terms and pricing. Regular communication and trust can often result in better service and potential discounts.
Disclaimer on Indicative Prices
While the above insights provide a foundational understanding of costs and pricing in the luggage manufacturing sector, actual prices can vary widely based on specific circumstances, market conditions, and negotiations. Always request detailed quotes tailored to your specific needs and requirements.
Alternatives Analysis: Comparing luggage manufacturer With Other Solutions
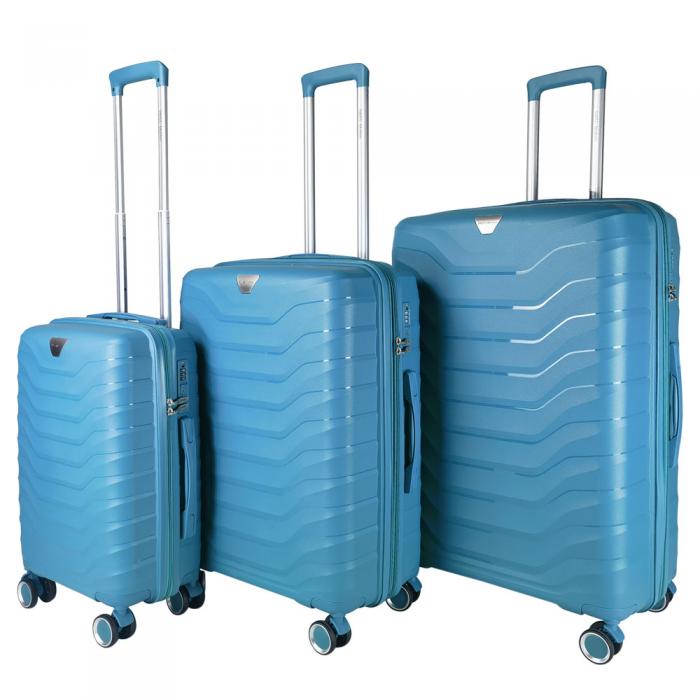
A stock image related to luggage manufacturer.
In the competitive landscape of luggage solutions, international B2B buyers must evaluate not only luggage manufacturers but also alternative approaches that can meet their business needs effectively. This section presents a comparative analysis of traditional luggage manufacturing against two viable alternatives: custom luggage suppliers and rental luggage services. Each option has its unique strengths and weaknesses, making it essential for buyers to understand these differences.
Comparison Table of Luggage Solutions
Comparison Aspect | Luggage Manufacturer | Custom Luggage Suppliers | Rental Luggage Services |
---|---|---|---|
Performance | High durability and variety | Tailored to specific needs | Flexible usage, no purchase required |
Cost | Moderate to high | Variable, based on customization | Typically lower, pay-per-use model |
Ease of Implementation | Straightforward order process | Longer lead times for customization | Quick and easy access, no long-term commitment |
Maintenance | Requires regular upkeep | Minimal, depends on materials used | No maintenance required |
Best Use Case | Bulk orders for resale | Unique branding for companies | Short-term needs, events, or travel |
What Are the Advantages and Disadvantages of Custom Luggage Suppliers?
Custom luggage suppliers offer the flexibility to create products that align with specific branding and functional requirements. This option is particularly advantageous for companies looking to enhance brand visibility through personalized designs. However, the lead time for production can be a drawback, as it may take several weeks to finalize designs and manufacture the luggage. Additionally, costs can vary significantly based on customization levels, making budgeting more challenging for B2B buyers.
How Do Rental Luggage Services Compare to Traditional Manufacturing?
Rental luggage services provide a compelling alternative for businesses that require luggage for short-term use, such as events or temporary projects. These services typically operate on a pay-per-use model, which can result in lower upfront costs compared to purchasing. Furthermore, there is no need for ongoing maintenance or storage, which can be particularly appealing for businesses with limited space. However, the main limitation is the lack of ownership and potential quality variability, as the condition of rented items may vary, impacting the brand image.
Conclusion: How to Choose the Right Luggage Solution for Your Business
When selecting the right luggage solution, B2B buyers should carefully evaluate their specific needs, budget constraints, and operational requirements. If durability and long-term use are priorities, partnering with a reputable luggage manufacturer may be the best option. Conversely, businesses looking for flexibility and cost-effectiveness for short-term needs may find that rental services or custom suppliers better meet their objectives. By weighing the pros and cons of each alternative, buyers can make informed decisions that align with their strategic goals and enhance their operational efficiencies.
Essential Technical Properties and Trade Terminology for luggage manufacturer
What Are the Essential Technical Properties for Luggage Manufacturing?
Understanding the technical properties of luggage is crucial for B2B buyers, as these specifications directly impact product quality, durability, and customer satisfaction. Here are some key properties to consider:
1. Material Grade
The type of material used in luggage production significantly influences durability, weight, and cost. Common materials include polycarbonate, nylon, and leather. For example, polycarbonate is known for its lightweight and high-impact resistance, making it suitable for hard-shell luggage. Selecting the right material grade is vital for meeting specific market needs and customer preferences.
2. Zipper Quality
Zippers are one of the most critical components of luggage. High-quality zippers, such as YKK, provide durability and ease of use. The zipper’s gauge (size) and type (e.g., coil, metal) can affect the overall functionality and aesthetic of the luggage. Ensuring reliable zippers can lead to fewer returns and increased customer satisfaction.
3. Tolerance Levels
Tolerance refers to the allowable variations in dimensions during manufacturing. For instance, tolerances for seams and stitching are crucial to maintain the integrity of the luggage. Consistent tolerances ensure that parts fit together correctly and that the luggage performs as intended, reducing the risk of defects and enhancing product reliability.
4. Weight Specifications
Weight specifications are crucial for compliance with airline regulations and customer preferences. Buyers should consider the weight of the luggage itself, as lighter options can enhance the travel experience. Manufacturers often provide weight specifications to help buyers select products that align with their market segment.
5. Water Resistance
Water resistance is an essential property for luggage, particularly for travelers who may encounter various weather conditions. The level of water resistance can vary based on the materials used and the design features (e.g., waterproof zippers, sealed seams). Buyers should assess water resistance to ensure their products meet consumer expectations for protection against the elements.
What Are Common Trade Terms in the Luggage Manufacturing Industry?
Familiarity with industry jargon is essential for effective communication and negotiation in B2B transactions. Here are some common terms:
1. OEM (Original Equipment Manufacturer)
OEM refers to a company that produces parts and equipment that may be marketed by another manufacturer. In the luggage industry, this means that a manufacturer may produce luggage according to specifications provided by a brand. Understanding OEM relationships can help buyers identify potential suppliers that can deliver products tailored to their specifications.
2. MOQ (Minimum Order Quantity)
MOQ is the smallest number of units a supplier is willing to sell. This term is vital for B2B buyers to understand their purchasing capabilities and budget constraints. Knowing the MOQ helps buyers negotiate better terms and avoid overstocking issues.
3. RFQ (Request for Quotation)
An RFQ is a document that a buyer sends to suppliers to solicit price quotes for specific goods or services. In the luggage industry, issuing an RFQ can help buyers compare prices and terms from multiple manufacturers, ensuring they get the best deal.
4. Incoterms (International Commercial Terms)
Incoterms are a set of predefined commercial terms published by the International Chamber of Commerce (ICC) that define the responsibilities of buyers and sellers in international transactions. Familiarity with these terms helps B2B buyers understand shipping responsibilities, costs, and risk, which is crucial for effective supply chain management.
5. Lead Time
Lead time refers to the time taken from placing an order to receiving the goods. In luggage manufacturing, understanding lead times is critical for inventory planning and meeting market demands. Buyers should negotiate lead times to ensure they can meet their customers’ needs without delays.
By grasping these essential technical properties and industry terminology, international B2B buyers can make informed decisions, negotiate effectively, and select the best luggage products for their markets.
Navigating Market Dynamics and Sourcing Trends in the luggage manufacturer Sector
What Are the Current Market Dynamics and Key Trends in the Luggage Manufacturing Sector?
The luggage manufacturing sector is currently experiencing dynamic shifts influenced by globalization, technological advancements, and changing consumer preferences. International B2B buyers are increasingly drawn to manufacturers who integrate innovative materials and smart technologies into their products. For instance, luggage with built-in GPS tracking and biometric locks is gaining traction, particularly among tech-savvy consumers across Africa, South America, the Middle East, and Europe.
Moreover, the rise of e-commerce has transformed sourcing strategies, allowing B2B buyers to access a broader range of manufacturers, including those in emerging markets like Vietnam and Mexico. Digital platforms facilitate real-time communication and streamline procurement processes, making it easier for buyers to assess product quality and negotiate terms without geographical limitations.
Sustainability is another key driver reshaping the market. As global awareness of environmental issues grows, B2B buyers are increasingly prioritizing eco-friendly materials and ethical production practices. This trend is particularly prominent in Europe, where consumers demand transparency regarding sourcing and manufacturing processes. Consequently, manufacturers who can demonstrate their commitment to sustainability are likely to gain a competitive edge in the international marketplace.
How Important Is Sustainability and Ethical Sourcing for B2B Buyers in the Luggage Sector?
Sustainability and ethical sourcing have become paramount in the luggage manufacturing sector, driven by both consumer demand and regulatory pressures. The environmental impact of traditional manufacturing practices, particularly in terms of plastic waste and carbon emissions, has prompted a shift towards greener alternatives. International B2B buyers are now more discerning, seeking suppliers that utilize recycled materials, biodegradable plastics, and sustainable leather alternatives.
Moreover, certifications such as Global Organic Textile Standard (GOTS) and OEKO-TEX® Standard 100 are gaining importance. These certifications assure buyers that the products meet stringent environmental and safety standards. For instance, luggage manufacturers that source materials from certified suppliers not only enhance their brand reputation but also appeal to a growing segment of eco-conscious consumers.
Ethical supply chains are equally critical. B2B buyers are increasingly concerned about labor practices and the social impact of their sourcing decisions. Manufacturers that prioritize fair labor practices and transparency in their supply chains are more likely to attract business from buyers looking to align with ethical values. This trend is particularly relevant in regions like Africa and South America, where social responsibility can significantly influence purchasing decisions.
What Has Been the Evolution of the Luggage Manufacturing Sector for B2B Buyers?
The luggage manufacturing sector has evolved significantly over the past few decades, transitioning from traditional craftsmanship to a more technology-driven approach. Initially dominated by local artisans, the industry has expanded with globalization, enabling manufacturers to scale operations and tap into international markets. The introduction of advanced manufacturing techniques, such as automation and computer-aided design (CAD), has enhanced production efficiency and product innovation.
In recent years, the focus has shifted towards customization and personalization. B2B buyers are now looking for manufacturers that can offer tailored solutions to meet specific market demands. This evolution reflects a broader trend in the retail sector, where personalized products are increasingly favored by consumers. As the industry continues to adapt to changing market dynamics, international B2B buyers must stay informed about these trends to make strategic sourcing decisions that align with their business objectives.
Frequently Asked Questions (FAQs) for B2B Buyers of luggage manufacturer
-
How do I choose the right luggage manufacturer for my business needs?
Selecting the right luggage manufacturer involves evaluating several factors. Start by assessing their product range and quality standards. Look for manufacturers that specialize in your desired type of luggage, whether it be hard-shell suitcases, soft-sided bags, or travel accessories. Additionally, consider their production capacity, lead times, and customization options to ensure they can meet your demands. Research client testimonials and case studies to gauge reliability and service quality. A personal visit to the manufacturing facility, if feasible, can provide further insights into their operations and capabilities. -
What are the typical minimum order quantities (MOQs) for luggage manufacturers?
Minimum order quantities can vary significantly between manufacturers, typically ranging from 100 to 1,000 units per style. Factors influencing MOQs include the complexity of the product design, materials used, and the manufacturer’s production capacity. For international buyers, it’s crucial to discuss MOQs upfront, as some manufacturers may offer flexibility for first-time orders or bulk purchases. Understanding MOQs can help you better manage your inventory and cash flow, ensuring you meet market demand without overcommitting resources. -
What customization options are available when sourcing luggage?
Most luggage manufacturers offer a range of customization options, including material selection, color choices, logo printing, and design alterations. You can often choose from various fabrics, zippers, and hardware to create a unique product that aligns with your brand identity. Additionally, inquire about custom packaging and labeling options to enhance your product presentation. Be sure to communicate your specific requirements clearly and allow ample time for design iterations to achieve the desired outcome. -
What payment terms should I expect when working with luggage manufacturers?
Payment terms can vary widely among manufacturers, with common practices including a 30% deposit upon order confirmation and the balance due before shipment. Some manufacturers may offer more flexible terms based on your relationship and order size. Ensure you clarify payment methods accepted (e.g., wire transfers, letters of credit) and any potential fees associated with international transactions. It’s advisable to have a written agreement outlining payment terms to avoid misunderstandings later. -
How can I ensure quality assurance when sourcing luggage from manufacturers?
To ensure quality assurance, establish clear quality standards and specifications before production begins. Request samples to evaluate materials, craftsmanship, and durability. Many manufacturers will conduct in-house quality checks, but consider hiring a third-party inspection service, especially for larger orders. Regular communication with the manufacturer during production can help address any issues early. Additionally, familiarize yourself with the manufacturer’s return and warranty policies to protect your investment. -
What logistics considerations should I keep in mind when importing luggage?
Logistics play a critical role in importing luggage. Start by understanding the shipping options available (air vs. sea freight) and associated costs. Ensure you have a reliable freight forwarder who can handle customs clearance and documentation. It’s essential to factor in lead times for production and shipping when planning your inventory. Additionally, be aware of import duties and taxes specific to your country to avoid unexpected expenses. Having a clear logistics strategy will help streamline the import process and maintain your supply chain efficiency. -
What are the best practices for vetting luggage suppliers?
Vetting suppliers is crucial to ensuring a successful partnership. Start by conducting background checks, such as reviewing their business licenses and certifications. Request references from other clients and assess their reputation through online reviews. Evaluate their production capabilities by visiting their facilities or requesting factory audits. It’s also beneficial to initiate a trial order to assess product quality and service reliability before committing to larger orders. Building a strong relationship based on trust and transparency is key to long-term collaboration. -
How can I stay updated on trends in the luggage manufacturing industry?
Staying informed about industry trends is essential for making strategic business decisions. Subscribe to industry publications, attend trade shows, and participate in online forums or webinars focused on luggage and travel accessories. Networking with other B2B buyers and suppliers can provide valuable insights into emerging trends and consumer preferences. Additionally, following key manufacturers and industry leaders on social media platforms can help you stay abreast of innovations and market changes that may impact your sourcing strategy.
Important Disclaimer & Terms of Use
⚠️ Important Disclaimer
The information provided in this guide, including content regarding manufacturers, technical specifications, and market analysis, is for informational and educational purposes only. It does not constitute professional procurement advice, financial advice, or legal advice.
While we have made every effort to ensure the accuracy and timeliness of the information, we are not responsible for any errors, omissions, or outdated information. Market conditions, company details, and technical standards are subject to change.
B2B buyers must conduct their own independent and thorough due diligence before making any purchasing decisions. This includes contacting suppliers directly, verifying certifications, requesting samples, and seeking professional consultation. The risk of relying on any information in this guide is borne solely by the reader.
Strategic Sourcing Conclusion and Outlook for luggage manufacturer
The strategic sourcing of luggage manufacturers is essential for international B2B buyers looking to optimize their supply chains and enhance product offerings. By understanding the diverse landscape of manufacturers across Africa, South America, the Middle East, and Europe, businesses can leverage local expertise and innovative designs that cater to specific market needs. Engaging with reputable manufacturers not only ensures quality and reliability but also fosters sustainable partnerships that can adapt to evolving market demands.
How Can B2B Buyers Navigate the Global Luggage Market?
To effectively navigate the global luggage market, buyers should prioritize research and due diligence. This involves evaluating manufacturers based on their production capabilities, compliance with international standards, and adaptability to custom requirements. Additionally, fostering strong relationships with suppliers can lead to better negotiation terms and improved service levels.
What Is the Future of Strategic Sourcing in the Luggage Industry?
Looking ahead, the luggage manufacturing sector is poised for growth driven by increasing travel demands and a focus on sustainability. Buyers are encouraged to stay informed about industry trends and emerging technologies that can enhance product functionality and eco-friendliness. By embracing strategic sourcing practices, international B2B buyers can position themselves for success, ensuring they remain competitive in a dynamic marketplace.
In conclusion, the path to effective sourcing in the luggage industry is paved with informed decisions, strategic partnerships, and an eye towards innovation. Take the next step in your sourcing journey today—connect with manufacturers who align with your business goals and values.