Discover Cost-Saving Tips from Top Spring Manufacturers (2025)
Introduction: Navigating the Global Market for spring manufacturer
In an increasingly competitive global market, sourcing high-quality springs that meet specific industrial requirements can pose a significant challenge for international B2B buyers. Understanding the complexities of spring manufacturing—ranging from material selection to production techniques—becomes crucial for companies aiming to enhance their product offerings. This comprehensive guide delves into various types of springs, their applications across diverse industries, and the critical factors for vetting suppliers effectively.
Whether you are operating in Africa, South America, the Middle East, or Europe, the insights provided here will empower you to make informed purchasing decisions. We will explore cost considerations, quality assurance practices, and logistical aspects of sourcing springs, ensuring that you are well-equipped to navigate this niche market. The goal is to demystify the procurement process, offering actionable strategies that cater to your specific business needs—be it in Argentina or the UK.
By the end of this guide, you will not only have a clearer understanding of the spring manufacturing landscape but also practical tools to enhance your sourcing strategy, ultimately driving efficiency and innovation in your operations.
Understanding spring manufacturer Types and Variations
Type Name | Key Distinguishing Features | Primary B2B Applications | Brief Pros & Cons for Buyers |
---|---|---|---|
Compression Springs | Coiled design, designed to compress under load | Automotive, aerospace, machinery | Pros: High load capacity; versatile. Cons: Limited to compression applications. |
Tension Springs | Designed to stretch and absorb tension | Fitness equipment, industrial machinery | Pros: Excellent elasticity; suitable for dynamic loads. Cons: Can fatigue over time. |
Torsion Springs | Twisted design, stores energy when twisted | Garage doors, automotive components | Pros: Efficient energy storage; compact design. Cons: Requires precise installation. |
Leaf Springs | Flat, elongated design, often made of layered steel | Automotive suspension, trailers | Pros: Simple design; high durability. Cons: Heavy; limited flexibility. |
Constant Force Springs | Provides a constant force over a range of motion | Automotive seatbelts, medical devices | Pros: Reliable performance; consistent force delivery. Cons: Can be more expensive. |
What Are Compression Springs and Their B2B Relevance?
Compression springs are characterized by their coiled structure, which compresses when a load is applied. They are commonly used in automotive, aerospace, and machinery applications where high load capacity and durability are essential. When purchasing compression springs, B2B buyers should consider factors such as material specifications, load requirements, and environmental conditions to ensure optimal performance.
How Do Tension Springs Function in Various Industries?
Tension springs are designed to absorb and store energy when stretched. They find applications in fitness equipment and industrial machinery, where they play a crucial role in providing resistance. B2B buyers need to evaluate the spring’s elasticity, load capacity, and potential fatigue over time, ensuring they select the right tension spring for their specific application.
What Are the Key Features of Torsion Springs?
Torsion springs are unique due to their twisted design, which allows them to store energy when twisted. They are widely used in garage doors and automotive components, where efficient energy storage is vital. Buyers should consider the installation requirements and the precision needed for torsion springs, as improper installation can lead to performance issues.
Why Choose Leaf Springs for Heavy-Duty Applications?
Leaf springs are flat and elongated, typically made from layered steel, making them ideal for automotive suspension systems and trailers. Their simple design and high durability make them a popular choice for heavy-duty applications. However, B2B buyers should be aware of their weight and limited flexibility, which may impact vehicle performance.
What Are the Benefits of Constant Force Springs?
Constant force springs deliver a consistent force over a range of motion, making them suitable for applications like automotive seatbelts and medical devices. They are known for their reliable performance and consistent force delivery. However, B2B buyers should consider the higher cost and specific application requirements when selecting constant force springs for their projects.
Related Video: The Life of a Spring – Spring Manufacturing
Key Industrial Applications of spring manufacturer
Industry/Sector | Specific Application of spring manufacturer | Value/Benefit for the Business | Key Sourcing Considerations for this Application |
---|---|---|---|
Automotive | Suspension Springs | Enhanced vehicle stability and comfort | Quality standards, material specifications, and delivery timelines |
Electronics | Compression Springs | Reliable performance in electronic devices | Precision engineering, compatibility with existing designs |
Aerospace | Retaining Springs | Ensured safety and reliability in flight components | Certification compliance, weight considerations, and durability |
Industrial Machinery | Tension Springs | Improved machinery efficiency and performance | Load specifications, custom designs, and long-term supplier relationships |
Medical Devices | Medical Springs | Enhanced functionality in medical equipment | Biocompatibility, regulatory compliance, and customization options |
How are Springs Used in the Automotive Industry?
In the automotive sector, suspension springs are critical components that provide enhanced vehicle stability and comfort. They absorb shocks from the road, ensuring a smoother ride for passengers. International B2B buyers must focus on quality standards and material specifications, as these factors directly impact the performance and safety of vehicles. Suppliers should also offer reliable delivery timelines to meet production schedules.
What Role Do Springs Play in Electronics Manufacturing?
Compression springs are widely used in electronics, serving as essential components that provide reliable performance in devices such as keyboards and remote controls. These springs help maintain the necessary force for buttons and switches, ensuring a seamless user experience. Buyers in this sector should prioritize precision engineering and ensure compatibility with existing designs, as any discrepancies can lead to product failures.
Why are Springs Important in Aerospace Applications?
In aerospace, retaining springs are crucial for ensuring safety and reliability in flight components. They secure various parts in place, preventing them from dislodging during operation. Buyers from this sector must consider certification compliance and weight considerations, as the aerospace industry has stringent regulations regarding materials and components. Durability is also a key factor, given the extreme conditions faced in flight.
How Do Tension Springs Enhance Industrial Machinery?
Tension springs are integral to the efficiency and performance of industrial machinery. They provide the necessary force to keep components in position, thereby improving machinery operation. For international buyers, understanding load specifications is vital, as custom designs may be required to meet specific machinery needs. Establishing long-term supplier relationships can also ensure consistent quality and supply.
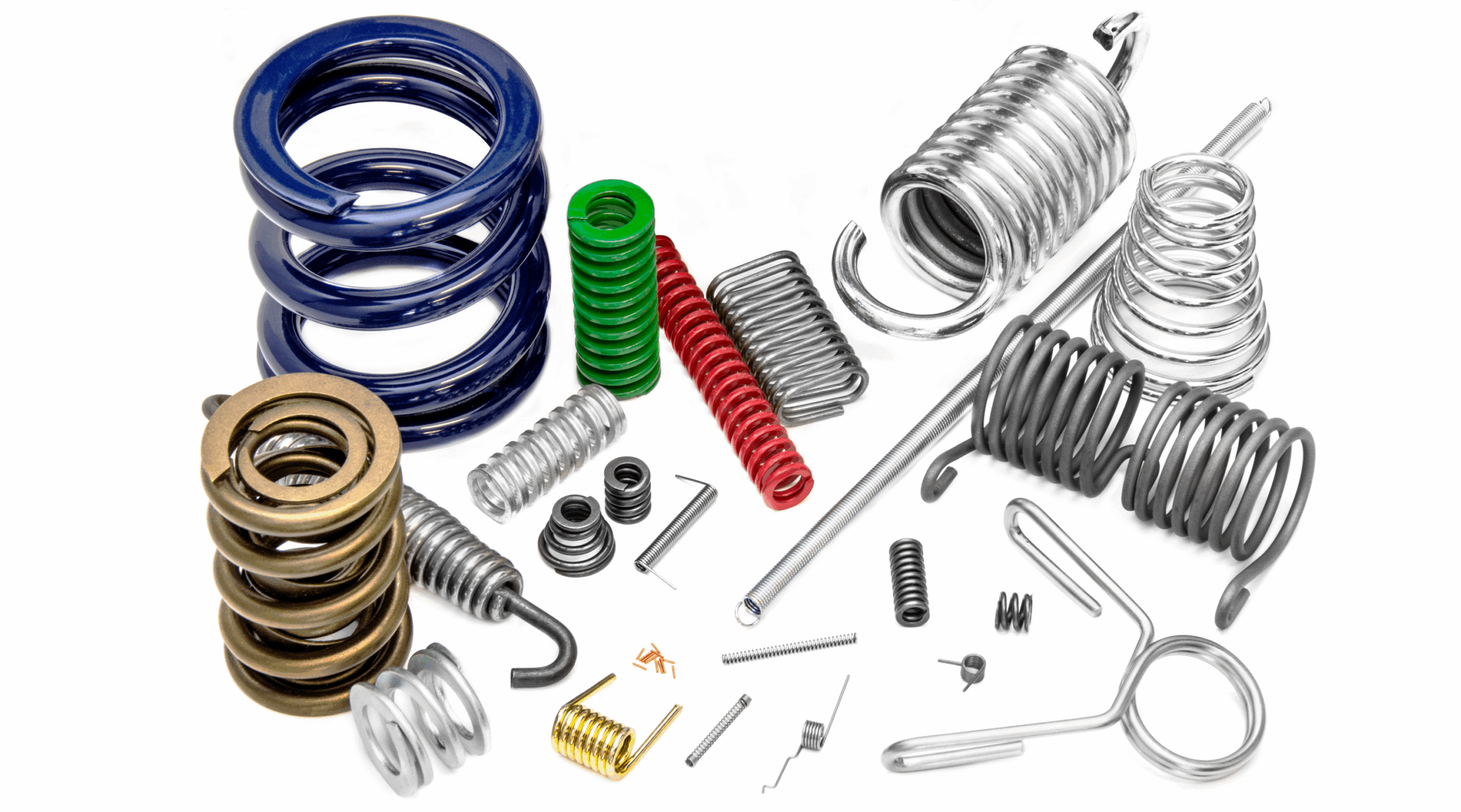
A stock image related to spring manufacturer.
What Are the Applications of Springs in Medical Devices?
In the medical field, springs play a vital role in enhancing the functionality of various medical devices, such as surgical instruments and diagnostic tools. These springs must meet strict biocompatibility and regulatory compliance standards to ensure patient safety. International B2B buyers should seek suppliers who can provide customization options to meet the unique requirements of their medical devices, ensuring both efficacy and safety in application.
Related Video: Types Of Flowmeters And Their Industrial Applications.
3 Common User Pain Points for ‘spring manufacturer’ & Their Solutions
Scenario 1: Navigating Quality Assurance Challenges in Spring Manufacturing
The Problem: For B2B buyers in regions like Africa and South America, sourcing high-quality springs can be daunting. Many manufacturers may provide inconsistent quality, leading to production delays and increased costs. This situation is especially critical for sectors such as automotive and aerospace, where the reliability of components directly impacts safety and performance. Buyers often face challenges verifying the quality standards of suppliers, which can result in the procurement of subpar springs that fail to meet specifications.
The Solution: To mitigate quality assurance challenges, buyers should prioritize sourcing from manufacturers with established quality control processes and certifications, such as ISO 9001. Engaging in due diligence, including site visits and requesting product samples, can provide insights into a manufacturer’s operational capabilities. Additionally, forming partnerships with local representatives or third-party quality inspection services can enhance oversight. Implementing a robust supplier evaluation process that includes criteria for quality assurance and past performance will ensure that only reliable manufacturers are selected.
Scenario 2: Dealing with Long Lead Times and Delivery Issues
The Problem: In the fast-paced B2B environment, long lead times can severely disrupt supply chains. Buyers from Europe and the Middle East often encounter delays when sourcing springs due to manufacturers’ backlogs or inefficient logistics. Such delays can lead to halted production lines and lost revenue, making timely delivery a crucial factor in supplier selection.
The Solution: Buyers should establish clear communication with spring manufacturers regarding lead times and delivery schedules. It’s advisable to implement a just-in-time (JIT) inventory system to minimize excess stock while ensuring that components are available when needed. Additionally, buyers can negotiate for shorter lead times in their contracts and consider multi-sourcing strategies to diversify their supplier base. Engaging manufacturers that offer real-time tracking and updates on order status can also enhance transparency and help in planning production schedules effectively.
Scenario 3: Customization and Technical Specification Challenges
The Problem: Many B2B buyers require customized springs tailored to specific applications, which can be a complex process. In industries such as medical devices or renewable energy, the technical specifications of springs can vary greatly. Buyers often struggle to communicate their needs effectively to manufacturers, leading to misunderstandings and products that do not meet precise requirements.
The Solution: To address customization challenges, buyers should invest time in developing detailed specifications and requirements before engaging with spring manufacturers. Creating comprehensive technical drawings and providing samples of existing components can help clarify needs. Additionally, engaging in collaborative design sessions with manufacturers can foster better communication and ensure that both parties are aligned on expectations. Utilizing manufacturers that have a proven track record in custom solutions and offering prototyping services can significantly streamline the development process, ultimately leading to a more satisfactory product outcome.
Strategic Material Selection Guide for spring manufacturer
When selecting materials for spring manufacturing, it is crucial to consider the specific properties and performance characteristics of each material. The choice of material can significantly impact the durability, functionality, and overall cost-effectiveness of the springs produced. Here, we analyze four common materials used in spring manufacturing, focusing on their properties, advantages, disadvantages, and implications for international B2B buyers.
What are the Key Properties of Music Wire for Spring Manufacturing?
Music Wire is a high-carbon steel known for its excellent tensile strength and fatigue resistance. It typically has a temperature rating of up to 250°F (121°C) and is suitable for applications involving moderate to high loads.
Pros: Music wire springs are highly durable, cost-effective, and can be easily manufactured into various shapes and sizes. They also exhibit good corrosion resistance when properly coated.
Cons: The primary limitation of music wire is its susceptibility to corrosion if not treated, which can be a concern in humid or corrosive environments.
Impact on Application: Music wire is commonly used in automotive and industrial applications where high strength and reliability are required.
Considerations for International Buyers: Buyers in regions like Europe and the Middle East should ensure compliance with standards such as ASTM A228 and DIN 17223. Proper coatings may be necessary for humid climates, particularly in Africa and South America.
How Does Stainless Steel Compare in Spring Manufacturing?
Stainless Steel, particularly grades like 302 and 316, offers excellent corrosion resistance and can withstand higher temperatures (up to 1000°F or 537°C).
Pros: The corrosion resistance of stainless steel makes it ideal for applications in harsh environments, such as marine or chemical industries. It also maintains strength at elevated temperatures.
Cons: The cost of stainless steel is generally higher than that of music wire, and its manufacturing can be more complex due to its hardness.
Impact on Application: Stainless steel springs are often used in medical devices, food processing, and outdoor applications where exposure to moisture is prevalent.
Considerations for International Buyers: Compliance with international standards like ASTM A313 and JIS G4313 is essential. Buyers should also consider the specific grade of stainless steel based on their environmental conditions.
What Are the Advantages of Oil-Tempered Steel in Spring Manufacturing?
Oil-Tempered Steel is another popular choice, known for its enhanced fatigue resistance and ability to withstand high stress. It is typically rated for temperatures up to 400°F (204°C).
Pros: This material exhibits high durability and is less prone to deformation under load. It is often used where springs are subjected to repeated cycles.
Cons: Oil-tempered steel can be more expensive than music wire and may require more complex manufacturing processes.
Impact on Application: Commonly used in automotive and aerospace applications, oil-tempered springs are ideal for high-stress environments.
Considerations for International Buyers: Buyers should be aware of the specific standards such as ASTM A313 and the need for proper heat treatment processes to ensure performance.
Why Choose Inconel for High-Performance Spring Applications?
Inconel is a nickel-chromium alloy known for its exceptional heat and corrosion resistance, making it suitable for extreme environments, with temperature ratings exceeding 2000°F (1093°C).
Pros: Inconel springs maintain their strength and flexibility even at high temperatures, making them ideal for aerospace and chemical processing applications.
Cons: The primary drawback is the high cost and complexity of manufacturing, which can limit its use to specialized applications.
Impact on Application: Inconel is often used in high-stress applications where both heat and corrosion resistance are critical.
Considerations for International Buyers: Compliance with standards like ASTM B168 and the availability of specialized suppliers are important factors for buyers in Europe and the Middle East.
Summary Table of Material Selection for Spring Manufacturing
Material | Typical Use Case for spring manufacturer | Key Advantage | Key Disadvantage/Limitation | Relative Cost (Low/Med/High) |
---|---|---|---|---|
Music Wire | Automotive, industrial applications | High durability and cost-effectiveness | Susceptible to corrosion | Low |
Stainless Steel | Medical devices, food processing | Excellent corrosion resistance | Higher cost and complex manufacturing | High |
Oil-Tempered Steel | Automotive, aerospace applications | High fatigue resistance | More expensive and complex to manufacture | Medium |
Inconel | Aerospace, chemical processing | Exceptional heat/corrosion resistance | High cost and manufacturing complexity | High |
This strategic material selection guide provides international B2B buyers with essential insights into material properties, applications, and considerations, enabling informed purchasing decisions tailored to specific operational needs and regional compliance requirements.
In-depth Look: Manufacturing Processes and Quality Assurance for spring manufacturer
What Are the Main Stages in the Manufacturing Process of Springs?
The manufacturing of springs involves several critical stages, each essential to ensuring the final product meets the necessary specifications and quality standards. Here’s a breakdown of the main processes involved:
Material Preparation: What Types of Materials Are Used?
The first step in spring manufacturing is material preparation. Springs are typically made from high-carbon steel, stainless steel, or specialized alloys, depending on the application. Material selection is crucial as it affects the spring’s performance, durability, and resistance to environmental factors.
- Material Sourcing: B2B buyers should ensure that suppliers source materials from reputable manufacturers. Traceability of the material is vital for quality assurance.
- Testing Materials: Before the manufacturing process begins, suppliers often conduct tensile tests and hardness tests to ensure the material meets industry standards.
How Are Springs Formed?
Once the materials are prepared, the next step is forming. This process involves bending or coiling the material into the desired shape.
- Coiling: For helical springs, coiling machines are used to create the spring shape. This can be done in various configurations, including compression, extension, and torsion springs.
- Cold vs. Hot Forming: Depending on the type of spring and material used, the forming process can be done cold (at room temperature) or hot (at elevated temperatures). Cold forming typically yields better precision and surface finish.
What Techniques Are Used in Spring Assembly?
After forming, the springs may undergo assembly if they are part of a larger component. This stage involves integrating the spring into its intended application or sub-assembly.
- Welding and Joining: Techniques such as welding or adhesive bonding might be used to attach springs to other components. B2B buyers should inquire about the methods used to ensure compatibility with their specific applications.
- Pre-Assembly Inspection: Before assembly, components are often inspected for defects to prevent issues in the final product.
What Finishing Processes Are Involved in Spring Manufacturing?
The finishing process enhances the spring’s performance and longevity. Common finishing techniques include:
- Surface Treatment: Processes like shot peening, coating, or plating are applied to enhance fatigue resistance and corrosion protection. Buyers should ask suppliers about the specific treatments used and their implications for performance.
- Heat Treatment: Springs often undergo heat treatment to improve their mechanical properties. This process can include hardening and tempering, which alters the spring’s hardness and elasticity.
What Quality Assurance Standards Should B2B Buyers Look For?
Quality assurance is a critical component of the manufacturing process for springs. It ensures that products meet international standards and customer specifications.
Which International Standards Are Relevant for Spring Manufacturers?
For B2B buyers, understanding the relevant quality standards is essential. Some of the most recognized include:
- ISO 9001: This standard outlines the criteria for a quality management system and is widely adopted in manufacturing. Suppliers should be able to provide proof of certification.
- CE Marking: For products sold in Europe, CE marking indicates conformity with health, safety, and environmental protection standards.
- API Standards: In the oil and gas sector, API (American Petroleum Institute) standards are critical for springs used in demanding environments.
What Are the Key Quality Control Checkpoints?
Quality control (QC) checkpoints are integral to ensuring product integrity. These typically include:
- Incoming Quality Control (IQC): This involves inspecting raw materials and components upon arrival to ensure they meet specified requirements.
- In-Process Quality Control (IPQC): During manufacturing, various checkpoints are established to monitor processes and detect any deviations from standards.
- Final Quality Control (FQC): After production, the final inspection ensures that the springs meet all specifications before shipment.
How Can B2B Buyers Verify Supplier Quality Control Processes?
For international buyers, particularly from regions like Africa, South America, the Middle East, and Europe, verifying a supplier’s quality control practices is crucial.
What Are Effective Methods for Supplier Audits?
-
Supplier Audits: Conducting regular audits is a practical way to assess a supplier’s manufacturing processes and quality assurance measures. This includes reviewing documentation, visiting manufacturing sites, and observing practices firsthand.
-
Quality Reports: Request detailed quality reports that outline testing results, non-conformities, and corrective actions taken. This transparency can provide insights into the supplier’s commitment to quality.
-
Third-Party Inspections: Engaging third-party inspection services can provide an unbiased assessment of a supplier’s operations and quality management systems. This is particularly beneficial for B2B buyers who may not have the resources to conduct thorough internal audits.
What Are Common Testing Methods Used in Spring Quality Assurance?
Testing methods are fundamental in verifying the performance and reliability of springs. Some common testing methods include:
- Tensile Testing: Measures the strength and ductility of the spring material.
- Fatigue Testing: Assesses the spring’s performance under repeated loading, which is crucial for applications where springs will undergo cyclical stresses.
- Dimensional Inspection: Ensures that springs meet specified tolerances for diameter, length, and wire size.
What Nuances Should International B2B Buyers Consider Regarding Quality Control?
International buyers should be aware of specific nuances that may affect quality control when sourcing springs globally:
- Cultural Differences: Variations in manufacturing practices and quality standards can exist across countries. Buyers should familiarize themselves with local regulations and standards.
- Logistics and Supply Chain: Understand how international shipping and logistics can impact the quality of products. Ensure that suppliers have robust systems in place to handle products during transit.
- Communication Barriers: Clear communication regarding quality expectations and specifications is essential, especially when dealing with suppliers in different regions.
By understanding these manufacturing processes and quality assurance measures, international B2B buyers can make informed decisions when selecting spring manufacturers, ensuring that they source reliable and high-quality products tailored to their specific needs.
Practical Sourcing Guide: A Step-by-Step Checklist for ‘spring manufacturer’
The following checklist serves as a practical guide for international B2B buyers looking to source spring manufacturers effectively. This structured approach ensures that you cover all critical aspects of the procurement process, enhancing your chances of finding the right supplier for your needs.
Step 1: Define Your Technical Specifications
Clearly outlining your technical requirements is the first step in sourcing springs. This includes dimensions, material types, load capacity, and specific tolerances. Having a detailed specification helps suppliers understand your needs, reducing the risk of receiving unsuitable products.
- Material Considerations: Specify if you require stainless steel, carbon steel, or specialized materials based on your application.
- Application Context: Indicate the environment (e.g., automotive, industrial machinery) in which the springs will be used.
Step 2: Research Potential Suppliers
Conduct thorough research to identify potential spring manufacturers. Utilize online platforms, industry directories, and trade shows to compile a list of candidates.
- Supplier Background: Look for manufacturers with a proven track record in your industry.
- Geographical Considerations: Consider suppliers from regions known for spring manufacturing, such as Europe or Asia, which may offer competitive pricing and quality.
Step 3: Evaluate Supplier Certifications
It’s essential to verify that potential suppliers hold relevant certifications. ISO certifications, for example, indicate adherence to international quality standards.
- Quality Assurance: Ensure that the suppliers have quality management systems in place, which is crucial for maintaining product consistency.
- Compliance: Confirm that the suppliers comply with industry regulations pertinent to your sector.
Step 4: Request Samples for Testing
Before making a large order, request samples from shortlisted suppliers. Testing these samples is crucial to verify that they meet your specifications and quality standards.
- Performance Testing: Evaluate the samples under actual working conditions to assess durability and performance.
- Feedback Loop: Use the results to engage suppliers in discussions about any necessary modifications.
Step 5: Assess Production Capabilities
Understanding a supplier’s production capabilities is vital for ensuring they can meet your volume and delivery requirements.
- Capacity Analysis: Inquire about their production capacity and lead times for large orders.
- Flexibility: Check if they can accommodate changes in order size or specifications.
Step 6: Review Pricing and Payment Terms
Pricing is a critical factor in sourcing decisions. Request detailed quotations from multiple suppliers to compare.
- Cost Breakdown: Ask for itemized pricing to understand the cost structure, including materials, labor, and shipping.
- Payment Flexibility: Discuss payment terms and conditions to find options that suit your cash flow and financial strategies.
Step 7: Establish Clear Communication Channels
Effective communication is key to a successful supplier relationship. Ensure you have established channels for ongoing discussions and updates.
- Point of Contact: Designate a specific representative from both your team and the supplier’s for streamlined communication.
- Feedback Mechanisms: Implement regular check-ins to address any issues that arise during production or delivery.
By following this checklist, B2B buyers can systematically approach the sourcing of spring manufacturers, ensuring they secure a reliable partner that meets their specific needs.
Comprehensive Cost and Pricing Analysis for spring manufacturer Sourcing
What Are the Key Cost Components in Sourcing Springs from Manufacturers?
When considering sourcing from spring manufacturers, understanding the cost structure is crucial for effective budgeting and financial planning. The primary components that contribute to the overall cost include:
-
Materials: The choice of raw materials significantly impacts pricing. Common materials for springs, such as stainless steel, carbon steel, or alloys, vary in cost. The market price of these materials can fluctuate, influenced by global supply and demand dynamics.
-
Labor: Labor costs can vary based on the region of the manufacturer. In countries with higher labor costs, such as those in Europe, the expense associated with skilled labor can affect the final price of the springs. Conversely, manufacturers in regions like South America or Africa may offer lower labor costs.
-
Manufacturing Overhead: This includes the costs associated with running the manufacturing facility, such as utilities, maintenance, and administrative expenses. Overhead can vary widely depending on the efficiency of the production process and the technology used.
-
Tooling: Custom springs often require specialized tooling, which can add to the initial costs. Tooling expenses are typically amortized over the production run, making it essential to consider the volume of springs you plan to order.
-
Quality Control (QC): Ensuring that springs meet specific industry standards involves investment in quality control processes. The costs associated with testing and inspection should be factored into the pricing.
-
Logistics: Shipping and handling costs can vary significantly based on the distance from the manufacturer to the buyer, as well as the chosen shipping method. International buyers should also consider customs duties and import taxes, which can substantially increase costs.
-
Margin: Manufacturers will typically include a profit margin in their pricing. Understanding the expected margins in the industry can help buyers gauge whether the prices offered are competitive.
How Do Price Influencers Affect Spring Manufacturing Costs?
Various factors can influence the pricing structure when sourcing springs from manufacturers. These include:
-
Volume and Minimum Order Quantity (MOQ): Higher order volumes often lead to lower unit prices due to economies of scale. Buyers should negotiate for favorable MOQs to optimize costs.
-
Specifications and Customization: Custom specifications or unique designs can lead to increased costs. Buyers should clearly communicate their requirements to avoid unexpected price hikes.
-
Material Quality and Certifications: Springs that require specific certifications (e.g., ISO, ASTM) may have higher costs due to additional testing and compliance measures. Ensure that the materials meet the necessary industry standards.
-
Supplier Factors: The reputation and reliability of the supplier can impact pricing. Established suppliers may charge more due to their track record of quality and service.
-
Incoterms: Understanding international shipping terms (Incoterms) is vital for cost management. Different terms can affect who bears the responsibility for shipping costs, insurance, and customs duties.
What Are the Best Buyer Tips for Negotiating Spring Prices?
For international B2B buyers, particularly from regions like Africa, South America, the Middle East, and Europe, effective negotiation and strategic sourcing can lead to significant savings. Here are some actionable tips:
-
Negotiate Terms: Always discuss payment terms, delivery schedules, and pricing upfront. Flexibility in payment can sometimes lead to better pricing.
-
Consider Total Cost of Ownership (TCO): Evaluate not only the initial price but also the long-term costs associated with the springs, such as maintenance and replacement. A higher-quality spring may have a lower TCO.
-
Leverage Relationships: Building a strong relationship with suppliers can lead to better pricing and terms over time. Consider long-term partnerships rather than one-off transactions.
-
Request Quotes from Multiple Suppliers: Gathering multiple quotes allows for better comparison and can provide leverage in negotiations.
-
Stay Informed on Market Trends: Keeping abreast of material costs and industry trends can help buyers time their purchases effectively and negotiate better deals.
Disclaimer for Indicative Prices
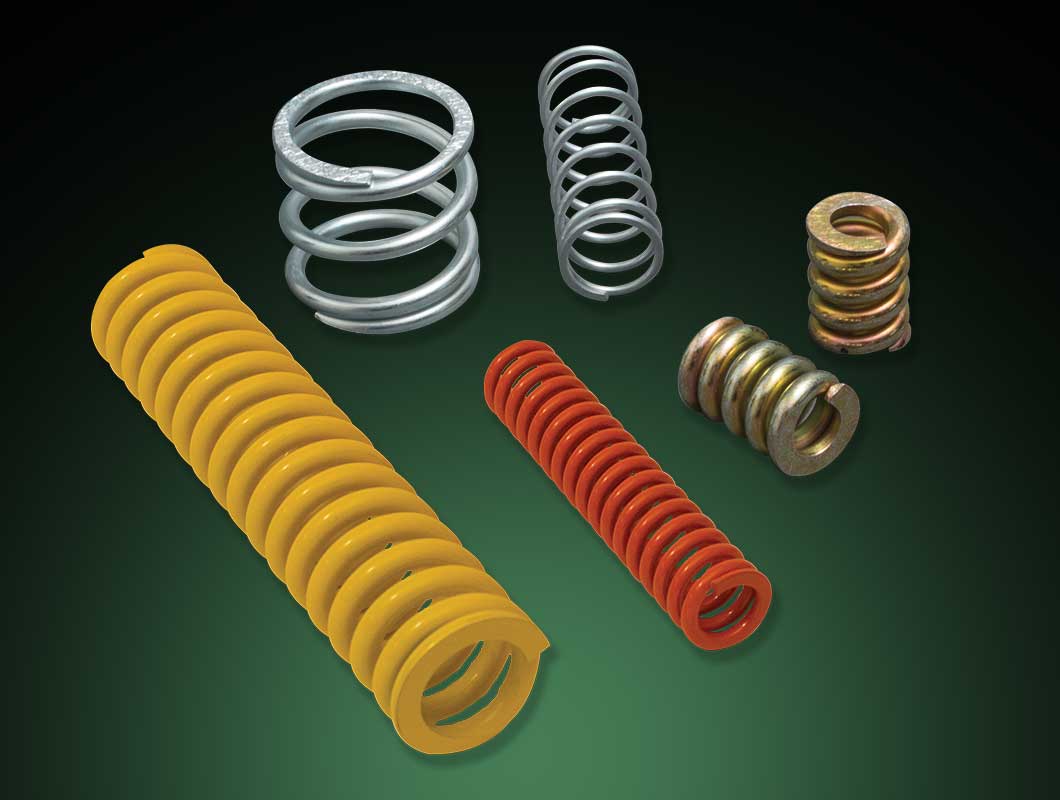
A stock image related to spring manufacturer.
Prices for spring manufacturing can vary widely based on the factors outlined above. Buyers should conduct thorough research and obtain multiple quotes to ensure they are receiving competitive pricing tailored to their specific needs.
Alternatives Analysis: Comparing spring manufacturer With Other Solutions
When evaluating spring manufacturing solutions, it’s essential to consider various alternatives that may offer similar functionalities. Understanding these alternatives can help international B2B buyers make informed decisions based on their specific requirements, such as performance, cost, and ease of implementation. Below, we compare traditional spring manufacturing with two viable alternatives: Composite Springs and Hydraulic Actuators.
Comparison Aspect | Spring Manufacturer | Composite Springs | Hydraulic Actuators |
---|---|---|---|
Performance | High resilience and fatigue strength | Lightweight and corrosion-resistant | High force output and precise control |
Cost | Medium to high depending on material | Generally lower due to material savings | Higher initial investment but can lower lifecycle costs |
Ease of Implementation | Established manufacturing processes, may require tooling | Requires specialized design knowledge | Requires hydraulic system setup and maintenance |
Maintenance | Regular inspection for wear | Minimal, but check for delamination | Requires fluid maintenance and leak checks |
Best Use Case | Heavy machinery, automotive, aerospace | Lightweight applications, automotive, sports equipment | Robotics, heavy machinery, and applications requiring precise movement |
What Are Composite Springs and Their Benefits?
Composite springs, made from advanced materials such as fiberglass or carbon fiber, provide a lightweight and corrosion-resistant alternative to traditional metal springs. Their unique composition allows them to withstand high loads while significantly reducing weight.
Pros:
– Weight Reduction: Ideal for applications where weight is a critical factor, such as in automotive and aerospace industries.
– Corrosion Resistance: Suitable for environments prone to moisture or chemicals.
Cons:
– Higher Design Complexity: Requires specialized knowledge for design and production.
– Limited Load Capacity: While effective for lightweight applications, they may not perform well under extremely high loads compared to metal springs.
How Do Hydraulic Actuators Compare?
Hydraulic actuators utilize pressurized fluid to produce motion, offering a different approach to achieving spring-like functionality. They are known for their ability to generate high force output and precise control over movement.
Pros:
– High Force Output: Capable of lifting and moving heavy loads with ease.
– Precision Control: Ideal for applications requiring accurate positioning and movement.
Cons:
– Higher Initial Costs: The setup and hydraulic system can be expensive.
– Maintenance Needs: Requires regular checks for fluid levels and potential leaks, which can increase operational costs.
Conclusion: How to Choose the Right Solution for Your Needs?
Selecting the right solution between traditional spring manufacturing, composite springs, and hydraulic actuators ultimately depends on your specific application requirements. Consider factors such as load capacity, environmental conditions, and budget constraints. For instance, if weight reduction is paramount, composite springs may be the best choice. Conversely, for applications needing high force and precise control, hydraulic actuators may be more suitable. By understanding the pros and cons of each alternative, B2B buyers can align their needs with the most appropriate technology to enhance their operational efficiency and product performance.
Essential Technical Properties and Trade Terminology for spring manufacturer
What Are the Essential Technical Properties of Springs?
Understanding the technical properties of springs is crucial for international B2B buyers, particularly when sourcing components that meet specific performance standards. Here are some critical specifications to consider:
1. Material Grade
The material used in spring manufacturing significantly influences its performance and durability. Common materials include stainless steel, carbon steel, and alloy steel. Each material has unique properties such as corrosion resistance, tensile strength, and fatigue life. For instance, stainless steel springs are ideal for applications exposed to moisture or corrosive environments, making them suitable for industries like automotive and aerospace.
2. Tolerance
Tolerance refers to the allowable deviation from specified dimensions. This property is vital because even minor discrepancies can impact the spring’s functionality and fit within an assembly. In B2B transactions, understanding tolerance levels is essential for ensuring compatibility with other components, thus reducing the risk of costly production delays.
3. Load Capacity
Load capacity indicates the maximum load a spring can handle without failing. It is essential for applications that require precise force management, such as in automotive suspensions or industrial machinery. Buyers should always specify the load capacity required for their application to ensure safety and performance.
4. Spring Rate
The spring rate measures the stiffness of a spring, indicating how much it will compress under a given load. This property is crucial for applications requiring specific force characteristics. A higher spring rate indicates a stiffer spring, which is necessary for load-bearing applications, while a lower rate allows for more flexibility, which may be desired in consumer products.
5. Finish and Coating
The finish and coating applied to springs can enhance their performance and lifespan. Common treatments include galvanization, powder coating, and oiling. These finishes can provide additional protection against environmental factors, such as rust or wear, and are particularly important for springs used in outdoor or harsh environments.
What Are Common Trade Terms Used in Spring Manufacturing?
Familiarity with industry jargon is vital for effective communication and negotiation in the spring manufacturing sector. Here are some common terms to know:
1. OEM (Original Equipment Manufacturer)
OEM refers to a company that produces parts or equipment that may be marketed by another manufacturer. Understanding OEM relationships is crucial for B2B buyers, as it can affect quality assurance and warranty considerations.
2. MOQ (Minimum Order Quantity)
MOQ is the smallest quantity of a product that a supplier is willing to sell. This term is significant for B2B buyers because it impacts inventory costs and the feasibility of purchasing smaller quantities for testing or prototyping.
3. RFQ (Request for Quotation)
An RFQ is a standard business process to invite suppliers to bid on specific products or services. For international buyers, issuing an RFQ can ensure competitive pricing and allow for better budget management.
4. Incoterms (International Commercial Terms)
Incoterms define the responsibilities of buyers and sellers in international transactions, specifying who pays for shipping, insurance, and tariffs. Familiarity with these terms helps buyers avoid misunderstandings regarding shipping costs and delivery responsibilities.
5. Lead Time
Lead time is the amount of time from when an order is placed until it is received. Understanding lead times is critical for international buyers to ensure timely project completion and inventory management.
By familiarizing themselves with these essential properties and terms, B2B buyers from regions like Africa, South America, the Middle East, and Europe can make informed decisions and negotiate effectively with spring manufacturers.
Navigating Market Dynamics and Sourcing Trends in the spring manufacturer Sector
What Are the Key Trends Shaping the Global Spring Manufacturing Market?
The global spring manufacturing sector is currently undergoing significant transformations driven by various factors, including technological advancements and shifting consumer demands. One of the prominent trends is the increasing adoption of automation and Industry 4.0 technologies, which enhance production efficiency and reduce lead times. For international B2B buyers from regions such as Africa, South America, the Middle East, and Europe, these technologies not only promise cost savings but also improve product quality and customization capabilities.
Moreover, there’s a growing emphasis on data analytics and predictive maintenance, allowing manufacturers to anticipate equipment failures and optimize supply chains. This trend is particularly beneficial for buyers looking to ensure uninterrupted production cycles and reliable sourcing. Additionally, the demand for specialized springs—such as those used in automotive and aerospace applications—is on the rise, driven by advancements in these industries. B2B buyers should therefore keep an eye on suppliers who can provide innovative solutions tailored to these specific needs.
How Is Sustainability Influencing Sourcing Decisions in the Spring Manufacturing Sector?
Sustainability has become a crucial factor in sourcing decisions for international B2B buyers, reflecting a broader shift towards environmentally responsible practices. The spring manufacturing industry, known for its significant energy consumption and material usage, is now focusing on reducing its environmental footprint. This includes optimizing production processes to minimize waste and adopting eco-friendly materials such as recycled metals and biodegradable coatings.
Ethical sourcing is also gaining traction, with buyers increasingly demanding transparency in supply chains. Certifications such as ISO 14001 (Environmental Management) and other ‘green’ labels are becoming essential for suppliers aiming to attract conscientious buyers. By choosing manufacturers that prioritize sustainability, B2B buyers can not only comply with evolving regulatory standards but also enhance their brand reputation among environmentally conscious consumers.
What Is the Historical Context of the Spring Manufacturing Industry?
The spring manufacturing industry has a rich history dating back to the early industrial revolution when mechanical innovations required reliable spring components. Initially, springs were handmade, but the advent of machinery in the late 19th century revolutionized the production process, allowing for mass production and greater precision. Over the decades, the industry has evolved significantly, with advancements in materials science leading to the development of high-performance alloys and specialized coatings.
In recent years, the focus has shifted towards customization and rapid prototyping, enabling manufacturers to cater to niche markets effectively. Understanding this historical context helps B2B buyers appreciate the evolution of spring manufacturing and the importance of partnering with suppliers who are at the forefront of technological advancements and market trends.
Frequently Asked Questions (FAQs) for B2B Buyers of spring manufacturer
-
How do I choose the right spring manufacturer for my business needs?
Selecting the right spring manufacturer involves several key considerations. Start by identifying your specific requirements, such as the type of springs needed (compression, extension, torsion), materials, and quantities. Research potential suppliers by reviewing their industry experience, certifications (like ISO 9001), and customer testimonials. It’s also essential to assess their production capabilities and technology. Engage in direct communication to discuss your project, timelines, and any customization options. This thorough vetting process ensures that you partner with a manufacturer that meets your quality and service expectations. -
What are the typical minimum order quantities (MOQs) for spring manufacturing?
Minimum order quantities for spring manufacturing can vary significantly based on the manufacturer and the type of spring. Generally, MOQs range from a few hundred to several thousand units. For custom springs, manufacturers may require higher MOQs due to setup costs. It’s advisable to discuss your specific needs with potential suppliers to negotiate the best terms. Some manufacturers may offer flexibility for trial orders, especially if you’re a new client or testing a new product line, so always inquire about these options. -
What customization options are available for springs?
Spring manufacturers often provide a variety of customization options to meet specific client needs. These options can include variations in wire diameter, coil dimensions, material selection (e.g., stainless steel, music wire), and surface treatments (like coating or plating). Additionally, manufacturers may offer engineering support to design springs tailored to your application. When discussing your project, be clear about your requirements and ask for samples or prototypes to ensure the product meets your expectations before committing to a larger order. -
What payment terms should I expect when sourcing springs internationally?
Payment terms for international spring purchases typically vary by manufacturer and are influenced by your relationship with them. Common options include advance payment, letters of credit, or payment upon delivery. It’s crucial to negotiate terms that provide you with sufficient security while also accommodating the supplier’s needs. Be aware of potential additional costs such as import duties, taxes, and shipping fees, which can affect your overall budget. Always clarify these terms in your contract to avoid misunderstandings later. -
How can I ensure quality assurance in spring manufacturing?
To ensure quality assurance in spring manufacturing, it’s vital to partner with a manufacturer that implements rigorous QA processes. Look for suppliers that are ISO certified, as this indicates adherence to international quality standards. Request information about their testing procedures, including material inspections, dimensional checks, and performance testing. Additionally, consider arranging for third-party inspections or audits to verify quality before shipment. Establishing clear communication about your quality expectations from the outset can also help maintain standards throughout the manufacturing process. -
What logistics considerations should I keep in mind when importing springs?
When importing springs, logistics play a critical role in the success of your supply chain. Consider the shipping methods available (air freight vs. sea freight), as they can impact delivery times and costs. It’s essential to work closely with your supplier to understand packaging requirements that prevent damage during transit. Additionally, familiarize yourself with import regulations in your country to ensure compliance and avoid delays. Partnering with a reliable logistics provider can streamline the process and provide you with tracking capabilities for better visibility. -
How can I effectively communicate my spring specifications to a manufacturer?
Effectively communicating your spring specifications involves providing clear and detailed documentation. Create a comprehensive technical drawing that includes dimensions, tolerances, material specifications, and any special requirements. Supplement this with a written description outlining your application and performance expectations. If possible, include samples or prototypes of existing springs to illustrate your requirements. Regular communication with the manufacturer during the design phase can help clarify any ambiguities and ensure that the final product meets your needs. -
What are the common challenges faced when sourcing springs internationally?
Sourcing springs internationally can present several challenges, including language barriers, cultural differences, and varying regulations. Additionally, differences in time zones can complicate communication and delay responses. Quality control can also be more challenging, as you may not have direct oversight of the manufacturing process. To mitigate these risks, establish strong relationships with your suppliers, utilize technology for clear communication, and consider hiring local agents who understand the market and can facilitate smoother transactions.
Important Disclaimer & Terms of Use
⚠️ Important Disclaimer
The information provided in this guide, including content regarding manufacturers, technical specifications, and market analysis, is for informational and educational purposes only. It does not constitute professional procurement advice, financial advice, or legal advice.
While we have made every effort to ensure the accuracy and timeliness of the information, we are not responsible for any errors, omissions, or outdated information. Market conditions, company details, and technical standards are subject to change.
B2B buyers must conduct their own independent and thorough due diligence before making any purchasing decisions. This includes contacting suppliers directly, verifying certifications, requesting samples, and seeking professional consultation. The risk of relying on any information in this guide is borne solely by the reader.
Strategic Sourcing Conclusion and Outlook for spring manufacturer
In the evolving landscape of global manufacturing, strategic sourcing remains a critical element for B2B buyers, especially in the spring manufacturing sector. By focusing on establishing robust partnerships with reliable suppliers, companies can not only enhance product quality but also optimize costs. For buyers in regions such as Africa, South America, the Middle East, and Europe, the importance of understanding local market dynamics and supplier capabilities cannot be overstated.
How can international buyers leverage strategic sourcing for competitive advantage? Prioritize suppliers who demonstrate compliance with international quality standards and have a strong track record of innovation. Consider utilizing technology, such as supply chain management software, to streamline procurement processes and facilitate better communication with suppliers.
As the demand for customized spring solutions continues to grow, the outlook for this sector remains promising. International B2B buyers are encouraged to actively engage in strategic sourcing initiatives, ensuring alignment with manufacturers who can adapt to emerging trends and customer needs. Embrace the opportunity to build sustainable partnerships that drive not just profitability but also long-term success in the global marketplace.