Discover Quality & Cost Savings: Your Glass Cup Supplier Guide (2025)
Introduction: Navigating the Global Market for glass cup supplier
In an increasingly competitive global market, sourcing the right glass cup supplier can be a daunting task for B2B buyers, particularly those from regions like Africa, South America, the Middle East, and Europe. The diverse range of available options, coupled with the varying quality standards and production capabilities, often leads to challenges in making informed purchasing decisions. This comprehensive guide aims to demystify the complexities surrounding glass cup procurement, providing valuable insights into the types of glass cups available, their applications across different industries, and essential criteria for vetting suppliers.
From understanding the intricate manufacturing processes to evaluating cost structures and negotiating favorable terms, this guide serves as a roadmap for international buyers seeking reliable partnerships. We delve into the nuances of glass cup types—such as tempered, borosilicate, and decorative options—while exploring their specific applications in hospitality, retail, and consumer goods. Furthermore, we highlight best practices for supplier selection, including assessing production capabilities, certifications, and logistical considerations.
By equipping B2B buyers with this essential knowledge, we empower them to make strategic, informed decisions that align with their business goals. Whether you’re a small business or a large corporation, navigating the global market for glass cup suppliers has never been more straightforward. Let’s explore how to unlock the potential of glass in your product offerings.
Understanding glass cup supplier Types and Variations
Type Name | Key Distinguishing Features | Primary B2B Applications | Brief Pros & Cons for Buyers |
---|---|---|---|
Borosilicate Glass | High thermal resistance, low thermal expansion | Laboratory glassware, kitchenware | Pros: Resistant to thermal shock; Cons: Higher cost compared to soda-lime glass. |
Soda-Lime Glass | Economical, easy to mold, and widely available | Food service, retail displays | Pros: Cost-effective; Cons: Less durable than borosilicate. |
Dichroic Glass | Color-shifting, artistic applications | Art installations, luxury items | Pros: Unique aesthetic appeal; Cons: Higher price point and specialty sourcing. |
Tempered Glass | Strengthened through thermal or chemical processes | Commercial drinkware, safety applications | Pros: Increased durability; Cons: Can be more expensive to replace. |
Crystal Glass | High clarity, lead content for brilliance | High-end dining, giftware | Pros: Luxurious appearance; Cons: Heavy and requires careful handling. |
What are the Characteristics of Borosilicate Glass Cups?
Borosilicate glass is renowned for its high resistance to thermal shock, making it ideal for laboratory glassware and kitchen applications. This type of glass can withstand sudden temperature changes without breaking, which is crucial for buyers in scientific and culinary fields. When considering borosilicate glass cups, B2B buyers should evaluate their suppliers’ certifications, as quality can vary significantly, impacting safety and performance.
Why Choose Soda-Lime Glass Cups for Your Business Needs?
Soda-lime glass is the most common type of glass used for manufacturing cups due to its cost-effectiveness and ease of production. This glass type is widely used in food service and retail displays, making it a practical choice for businesses looking for affordability without sacrificing quality. Buyers should consider the intended use and potential for breakage, as soda-lime glass is less durable than other types, necessitating careful handling and storage.
How Does Dichroic Glass Enhance Product Appeal?
Dichroic glass cups are characterized by their ability to display multiple colors depending on the angle of light, making them popular for artistic and luxury applications. These cups are often used in art installations or as high-end gifts, appealing to niche markets that value uniqueness and aesthetics. Buyers should assess the cost versus perceived value in their target market, as dichroic glass can carry a premium price tag.
What are the Benefits of Using Tempered Glass Cups?
Tempered glass cups are manufactured through a process that increases their strength and resistance to breakage, making them suitable for commercial drinkware and safety applications. B2B buyers should prioritize tempered glass for environments where durability is essential, such as bars and restaurants. While they may have a higher initial cost, the long-term savings from reduced breakage can be significant.
Why Opt for Crystal Glass Cups in High-End Markets?
Crystal glass cups offer exceptional clarity and brilliance due to their lead content, making them highly sought after in high-end dining and giftware markets. The luxurious appearance of crystal glass can enhance brand image and customer experience. However, buyers must consider the weight and fragility of crystal, which may require special handling and storage solutions to prevent damage.
Related Video: The Calculus of Variations and the Euler-Lagrange Equation
Key Industrial Applications of glass cup supplier
Industry/Sector | Specific Application of glass cup supplier | Value/Benefit for the Business | Key Sourcing Considerations for this Application |
---|---|---|---|
Food and Beverage | Custom glass cups for restaurants | Enhances brand image and customer experience | Quality of glass, customization options, lead time |
Hospitality | Glass cups for hotels and resorts | Elevates guest experience and service quality | Durability, design variety, bulk order pricing |
Retail | Glass cups for retail displays | Attracts customers and boosts sales | Aesthetic appeal, packaging, and shipping costs |
Healthcare | Glass cups for medical facilities | Ensures hygiene and safety in patient care | Sterilization standards, material safety, supply chain reliability |
Arts and Crafts | Glass cups for artistic projects | Supports creativity and unique product offerings | Material versatility, availability of sizes, cost-effectiveness |
How Are Glass Cups Used in the Food and Beverage Industry?
In the food and beverage sector, glass cup suppliers provide custom glassware tailored for restaurants and cafes. These glasses not only serve a functional purpose but also enhance the overall dining experience. High-quality, aesthetically pleasing glass cups can elevate a restaurant’s brand image, making it essential for suppliers to offer durable and customizable options. International buyers should consider factors such as glass quality, design flexibility, and delivery timelines to ensure they meet their specific branding needs.
Why Are Glass Cups Important for the Hospitality Sector?
Hotels and resorts utilize glass cups to improve guest experiences, from in-room dining to bar service. The right glassware can significantly impact the perceived quality of service. Suppliers must focus on the durability and design variety of their products, as high turnover rates necessitate robust glassware that can withstand daily use. International buyers in this sector should prioritize suppliers who can offer competitive pricing on bulk orders without compromising on quality.
What Role Do Glass Cups Play in Retail?
In retail, glass cups are often used for product displays, especially in specialty shops and boutiques. The visual appeal of glass can attract customers, making it a valuable tool for increasing sales. Suppliers should provide aesthetically pleasing designs and consider packaging and shipping costs to ensure that their products arrive safely and in good condition. Retailers looking to source glass cups should focus on the supplier’s ability to deliver on time and offer diverse design options.
How Are Glass Cups Utilized in Healthcare Settings?
Glass cups are crucial in healthcare settings, where hygiene and safety are paramount. Medical facilities use glass cups for various purposes, including patient care and laboratory work. Suppliers must comply with strict sterilization standards and ensure that the materials used are safe and non-reactive. International buyers should assess the supplier’s reliability in terms of supply chain logistics and adherence to health regulations, as these factors are critical for maintaining patient safety.
What Are the Applications of Glass Cups in Arts and Crafts?
In the arts and crafts sector, glass cups are utilized for creative projects ranging from decorative art to functional items. Artists and crafters often seek suppliers that offer a variety of sizes and shapes to cater to diverse artistic needs. The versatility of glass as a medium allows for unique creations, making it essential for suppliers to provide high-quality materials at competitive prices. International buyers in this industry should look for suppliers that can accommodate small and large orders while ensuring cost-effectiveness.
Related Video: Manufacturing process of a glass bottle || Machines and Industry
3 Common User Pain Points for ‘glass cup supplier’ & Their Solutions
Scenario 1: Inconsistent Quality Across Suppliers
The Problem:
B2B buyers often face challenges with inconsistent quality when sourcing glass cups from multiple suppliers. This inconsistency can lead to a range of issues, including product returns, customer dissatisfaction, and damage to brand reputation. For instance, a restaurant owner in South Africa might order glass cups for their new café but receives a shipment where some cups are fragile and others are of excellent quality. Such discrepancies not only affect service but also lead to increased costs due to returns and replacements.
The Solution:
To mitigate this issue, B2B buyers should establish strong, long-term relationships with a select few glass cup suppliers rather than spreading orders across many vendors. When evaluating suppliers, focus on those with quality certifications, such as ISO standards, which demonstrate their commitment to consistent product quality. Implement a thorough quality assurance process that includes requesting samples before placing large orders. Additionally, consider conducting factory visits or audits if feasible, especially for suppliers from regions where quality standards may vary. These steps will help ensure that the glass cups received meet the expected quality standards, minimizing risks and enhancing customer satisfaction.
Scenario 2: Complicated Import Regulations and Shipping Delays
The Problem:
International buyers often struggle with complicated import regulations and shipping delays when sourcing glass cups. For example, a buyer in Brazil may find that their shipment is held up in customs due to incomplete paperwork or regulatory compliance issues. This not only delays the availability of products but can also result in additional costs and lost sales opportunities, particularly in competitive markets.
The Solution:
To navigate these challenges, B2B buyers should familiarize themselves with the import regulations specific to their country, including tariffs, taxes, and required documentation for glass products. Collaborating with a freight forwarder who specializes in international shipping can streamline the logistics process. These professionals can provide insights on best practices for compliance and help prepare necessary documents, such as certificates of origin or product safety standards. Additionally, working with suppliers who have experience shipping to the buyer’s country can reduce the likelihood of delays, as they will be more knowledgeable about local regulations and can offer tailored solutions to facilitate smoother transactions.
Scenario 3: Difficulty in Customization and Branding Options
The Problem:
Another common pain point for B2B buyers is the difficulty in obtaining customized glass cups that reflect their brand identity. A company in the Middle East, for example, may want to order branded glass cups for a promotional event but finds that many suppliers offer limited customization options or high minimum order quantities. This can be frustrating, especially for smaller businesses or those looking to create unique, limited-edition products.
The Solution:
B2B buyers should actively seek out suppliers that specialize in custom glassware and have flexible minimum order quantities. When contacting suppliers, clearly outline customization needs such as size, shape, color, and branding elements like logos or slogans. Request digital proofs or prototypes to ensure that the final product aligns with expectations. Additionally, consider utilizing local artisans or manufacturers who may offer more personalized services and flexibility in customization, potentially leading to unique designs that stand out in the market. Building a clear communication channel with suppliers regarding customization can lead to a smoother process and more satisfactory results.
Strategic Material Selection Guide for glass cup supplier
When selecting materials for glass cups, international B2B buyers must consider various factors that influence product performance, durability, and compliance with regional standards. Below, we analyze four common materials used in glass cup manufacturing, focusing on their properties, advantages, disadvantages, and specific considerations for buyers from Africa, South America, the Middle East, and Europe.
What Are the Key Properties of Soda-Lime Glass for Glass Cups?
Soda-lime glass is the most widely used type of glass in the production of glass cups. It typically comprises silica, soda ash, and lime, making it a cost-effective option. Key properties include good thermal resistance, moderate chemical durability, and transparency, which are essential for consumer products.
Pros and Cons: The primary advantage of soda-lime glass is its affordability and ease of manufacturing, making it suitable for high-volume production. However, it has lower thermal and mechanical strength compared to other glass types, which can lead to breakage under extreme conditions.
Impact on Application: Soda-lime glass is compatible with various beverages, including hot and cold liquids, but it may not withstand high-pressure applications.
Considerations for Buyers: Buyers should ensure compliance with international standards such as ASTM C162 and DIN 52322, especially when exporting to regions with stringent regulations.
How Does Borosilicate Glass Enhance Performance in Glass Cups?
Borosilicate glass is known for its superior thermal resistance and chemical durability, making it ideal for glass cups designed for hot beverages. Its composition includes silica and boron trioxide, which provide excellent thermal shock resistance.
Pros and Cons: The key advantage of borosilicate glass is its ability to withstand rapid temperature changes, making it suitable for laboratory and culinary applications. However, it is generally more expensive than soda-lime glass and can be more complex to manufacture.
Impact on Application: This material is particularly beneficial for applications involving boiling liquids or acidic beverages, as it exhibits high resistance to chemical corrosion.
Considerations for Buyers: International buyers should verify compliance with food safety regulations and standards like FDA and JIS, especially in markets that prioritize health and safety.
What Are the Benefits of Using Crystal Glass in Premium Glass Cups?
Crystal glass, often containing lead oxide or other metal oxides, offers a luxurious appearance and enhanced clarity, making it a popular choice for high-end glass cups. Its refractive properties give it a sparkling finish that appeals to consumers.
Pros and Cons: The primary advantage of crystal glass is its aesthetic appeal and weight, which convey a sense of quality. However, it is more fragile and less durable than other types of glass, making it unsuitable for everyday use.
Impact on Application: Crystal glass is ideal for serving premium beverages, such as fine wines and spirits, but it may not be suitable for hot liquids due to its lower thermal resistance.
Considerations for Buyers: Buyers should be aware of regulations regarding lead content in glass products, especially in regions with strict health guidelines, such as the EU.
Why Choose Tempered Glass for Enhanced Safety in Glass Cups?
Tempered glass is produced through a process of extreme heating and rapid cooling, which increases its strength and safety. It is less likely to shatter upon impact, making it a suitable choice for environments where safety is a concern.
Pros and Cons: The main advantage of tempered glass is its enhanced durability and safety features. However, the manufacturing process is more complex, leading to higher costs.
Impact on Application: Tempered glass cups are ideal for both hot and cold beverages, as they can withstand temperature fluctuations without breaking.
Considerations for Buyers: Buyers should ensure that tempered glass products meet safety standards such as ASTM C1048 and EN 12150, particularly in regions where consumer safety is a priority.
Summary Table of Material Selection for Glass Cup Suppliers
Material | Typical Use Case for glass cup supplier | Key Advantage | Key Disadvantage/Limitation | Relative Cost (Low/Med/High) |
---|---|---|---|---|
Soda-Lime Glass | Everyday glass cups | Cost-effective and easy to produce | Lower thermal and mechanical strength | Low |
Borosilicate Glass | Laboratory and culinary glass cups | Excellent thermal shock resistance | Higher cost and manufacturing complexity | Medium |
Crystal Glass | Premium glass cups | Luxurious appearance and clarity | Fragile and less durable | High |
Tempered Glass | Safety-focused glass cups | Enhanced strength and safety | More complex manufacturing process | Medium |
This strategic material selection guide aims to empower international B2B buyers with the insights needed to make informed decisions when sourcing glass cups. Understanding the properties and applications of each material can significantly impact product performance and customer satisfaction.
In-depth Look: Manufacturing Processes and Quality Assurance for glass cup supplier
What Are the Main Stages in the Manufacturing Process of Glass Cups?
The manufacturing of glass cups involves several critical stages that ensure the final product meets the required standards of quality and functionality. Understanding these stages is essential for international B2B buyers, particularly those looking to source glass products from suppliers in Africa, South America, the Middle East, and Europe.
1. Material Preparation: What Are the Key Components of Glass?
The first step in the manufacturing process is the preparation of raw materials. The primary ingredients for glass include silica (sand), soda ash, and limestone. Depending on the desired characteristics of the glass, other materials such as alumina, magnesium oxide, or coloring agents may also be included.
The raw materials are carefully weighed and mixed to create a homogeneous batch. This step is crucial, as the quality of the raw materials directly impacts the final product. A thorough understanding of the composition allows suppliers to tailor the glass to specific applications, such as thermal resistance or clarity.
2. Forming: How Are Glass Cups Shaped?
Once the materials are prepared, the next stage is forming. This can be accomplished through various methods, including:
- Blowing: This technique is often used for creating unique shapes and designs. A molten glass blob is gathered on a blowpipe and inflated to form the cup.
- Pressing: Glass is pressed into molds to create uniform shapes. This method is efficient for mass production.
- Casting: Molten glass is poured into a mold and allowed to cool, which is ideal for intricate designs.
Selecting the appropriate forming technique depends on factors such as the desired volume, design complexity, and production speed.
3. Assembly: How Are Components Joined?
In some cases, glass cups may require additional components, such as handles or decorative elements. The assembly process involves joining these parts securely, often using specialized adhesives or additional melting techniques to fuse components together.
Precision is key during this stage to ensure durability and aesthetic appeal, especially for products targeting high-end markets.
4. Finishing: What Are the Techniques for Surface Treatment?
The finishing stage involves several processes aimed at enhancing the appearance and functionality of glass cups. Common techniques include:
- Polishing: This is done to achieve a smooth, shiny surface. It enhances clarity and visual appeal.
- Coating: Additional layers may be applied for decorative purposes or to improve features such as scratch resistance.
- Printing: Logos or designs can be printed onto the glass using specialized inks designed for durability.
These finishing touches are essential for creating products that meet market expectations and brand requirements.
What Are the Quality Assurance Processes for Glass Cup Manufacturing?
Quality assurance is vital in ensuring that glass cups meet international standards and customer expectations. B2B buyers must be aware of the various quality control (QC) processes involved in glass manufacturing.
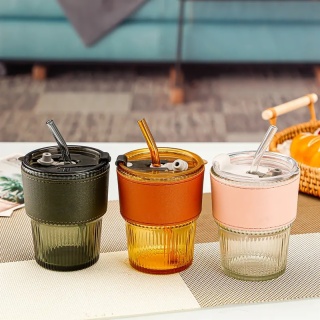
A stock image related to glass cup supplier.
1. What Are the Relevant International and Industry-Specific Standards?
Quality assurance in glass manufacturing often adheres to international standards such as ISO 9001, which focuses on quality management systems. In addition, industry-specific standards like CE marking for products sold in Europe and API standards for certain applications may apply.
Understanding these standards helps buyers assess a supplier’s commitment to quality and regulatory compliance.
2. What Are the Key QC Checkpoints in Glass Manufacturing?
Quality control checkpoints are critical for identifying defects and ensuring product consistency. Key checkpoints include:
- Incoming Quality Control (IQC): This involves inspecting raw materials upon arrival to ensure they meet specified criteria.
- In-Process Quality Control (IPQC): Monitoring during the manufacturing process helps identify issues before they escalate. This includes checking for defects during forming and assembly.
- Final Quality Control (FQC): The final inspection ensures that the finished product meets all quality standards before shipment.
Implementing these checkpoints allows manufacturers to maintain high-quality standards throughout the production process.
3. What Common Testing Methods Are Used in Glass Quality Assurance?
Several testing methods are commonly employed to assess the quality of glass cups:
- Visual Inspection: This method checks for surface defects, clarity, and uniformity.
- Dimensional Testing: Accurate measurements ensure that the cups meet specified dimensions.
- Strength Testing: Glass cups may undergo pressure tests to ensure they can withstand typical usage conditions.
- Thermal Shock Testing: This evaluates how well the glass can handle rapid temperature changes.
These tests provide valuable insights into the durability and performance of the glass cups.
How Can B2B Buyers Verify Supplier Quality Control?
For international B2B buyers, verifying a supplier’s quality control processes is crucial to ensuring product reliability.
1. What Steps Can Buyers Take to Assess Supplier QC?
Buyers should consider the following actions:
- Supplier Audits: Conducting on-site audits of potential suppliers allows buyers to assess their manufacturing processes and quality control measures firsthand.
- Requesting Quality Reports: Suppliers should provide documentation of their quality control processes and test results. This transparency can help build trust.
- Third-Party Inspections: Engaging independent inspection agencies can provide unbiased evaluations of the supplier’s quality assurance practices.
These steps can significantly reduce the risk of quality issues in the final products.
2. What Are the Quality Control Nuances for International Buyers?
International buyers must also consider regional variations in quality standards and regulations. For example, glass products sold in Europe must comply with CE marking requirements, while products intended for markets in Africa or South America may have different regulatory standards.
Understanding these nuances is essential for successful sourcing and compliance with local regulations.
Conclusion: Ensuring Quality in Glass Cup Sourcing
Navigating the complexities of glass cup manufacturing and quality assurance is crucial for international B2B buyers. By understanding the key manufacturing processes, quality assurance standards, and verification methods, buyers can make informed decisions and establish strong relationships with reliable suppliers. This knowledge not only helps in sourcing high-quality glass products but also ensures compliance with relevant international standards, ultimately contributing to successful business outcomes.
Practical Sourcing Guide: A Step-by-Step Checklist for ‘glass cup supplier’
To effectively source glass cups for your business, this practical guide provides a step-by-step checklist to ensure you find the right supplier that meets your needs. Whether you are based in Africa, South America, the Middle East, or Europe, following these steps will help you make informed decisions and establish successful partnerships.
Step 1: Define Your Technical Specifications
Start by detailing the specific requirements for the glass cups you wish to procure. This includes size, design, material quality, and any special features like thermal resistance or decorative elements. Clearly defined specifications help avoid misunderstandings with suppliers and ensure that the final product meets your expectations.
- Consider the market: Research trends in your region to align your product offerings with customer preferences.
- Quality standards: Identify any industry-specific standards or certifications that may apply to your glass products.
Step 2: Research Potential Suppliers
Begin your search by identifying suppliers that specialize in glass cup manufacturing. Utilize online directories, trade shows, and industry forums to gather a list of potential candidates.
- Supplier reputation: Look for reviews and testimonials from previous customers to gauge reliability and product quality.
- Geographical considerations: Assess the advantages of sourcing locally versus internationally, including shipping costs and lead times.
Step 3: Evaluate Supplier Capabilities
Once you have a shortlist of suppliers, evaluate their manufacturing capabilities and production capacity. This step is crucial to ensure they can meet your volume requirements and delivery timelines.
- Visit facilities: If possible, arrange for factory visits or virtual tours to assess their equipment and production processes.
- Ask about customization: Verify whether the supplier can accommodate custom designs or modifications to existing products.
Step 4: Verify Supplier Certifications
Ensure that the suppliers you are considering have the necessary certifications for quality and safety standards relevant to glass production. Certifications may include ISO, ASTM, or any regional-specific quality assurance marks.
- Compliance with regulations: Confirm that the supplier adheres to international safety standards to avoid potential liabilities.
- Sustainability practices: Consider suppliers that follow environmentally friendly practices, as this can enhance your brand’s reputation.
Step 5: Request Samples and Test Quality
Before making a large order, request product samples to assess quality firsthand. This step allows you to evaluate the craftsmanship, finish, and overall aesthetic of the glass cups.
- Conduct quality tests: Perform stress tests or usability trials to ensure the product meets your durability requirements.
- Compare with competitors: Assess how the samples stack up against competitors in terms of design and functionality.
Step 6: Negotiate Terms and Pricing
Once you have selected a supplier, enter negotiations to finalize pricing, payment terms, and delivery schedules. Clear agreements help prevent misunderstandings and ensure a smooth procurement process.
- Bulk discounts: Inquire about potential discounts for larger orders or long-term contracts.
- Payment options: Discuss flexible payment methods that suit your financial strategy.
Step 7: Establish a Communication Plan
Effective communication is vital for a successful partnership. Set up regular check-ins and updates to ensure that both parties are aligned throughout the order process.
- Designate points of contact: Identify key contacts from both your team and the supplier’s side for streamlined communication.
- Feedback loops: Encourage open feedback to address any issues promptly and maintain a positive working relationship.
By following this checklist, you can navigate the complexities of sourcing glass cups and establish a reliable supply chain that meets your business needs.
Comprehensive Cost and Pricing Analysis for glass cup supplier Sourcing
What Are the Key Cost Components for Glass Cup Suppliers?
When sourcing glass cups, international B2B buyers should understand the various cost components that contribute to the overall pricing structure. The primary elements include:
-
Materials: The main ingredients for glass production are silica, soda ash, and limestone. The choice of materials significantly influences the cost, especially if specialized glass types, like tempered or dichroic glass, are required.
-
Labor: Skilled labor is essential in glass manufacturing, particularly for processes requiring precision. Labor costs can vary based on the region of production, with countries in Europe typically having higher labor costs compared to those in Africa or South America.
-
Manufacturing Overhead: This includes expenses related to factory operations, utilities, and equipment maintenance. Efficient production processes can help minimize these costs.
-
Tooling: Custom molds and tooling are necessary for specific designs. The initial investment can be significant but is amortized over larger production runs.
-
Quality Control (QC): Ensuring the glass cups meet quality standards is crucial. QC processes add to the cost but are essential for maintaining product integrity, especially when exporting to markets with stringent regulations.
-
Logistics: Shipping and handling costs can fluctuate based on distance, shipping method, and volume. International logistics can be complex, and understanding Incoterms is vital for determining who bears these costs.
-
Margin: Suppliers typically add a profit margin to cover risks and business expenses. This margin can vary widely based on the supplier’s market position and pricing strategy.
How Do Price Influencers Affect Glass Cup Sourcing?
Several factors influence the pricing of glass cups in the B2B market:
-
Volume and Minimum Order Quantity (MOQ): Larger orders often come with discounts. Understanding the MOQ from suppliers can help buyers negotiate better prices.
-
Specifications and Customization: Custom designs or specifications can increase costs. Buyers should clarify their requirements early to avoid unexpected expenses.
-
Materials and Quality Certifications: The choice of materials and any certifications (e.g., food safety, environmental standards) can significantly affect pricing. High-quality or certified materials generally command a premium.
-
Supplier Factors: Supplier reputation, production capabilities, and location can all impact pricing. Established suppliers may offer higher quality but at a higher price point.
-
Incoterms: The agreed-upon shipping terms can affect overall costs. Understanding Incoterms helps clarify responsibilities and potential additional costs in the supply chain.
What Buyer Tips Can Enhance Cost-Efficiency in Glass Cup Sourcing?
International B2B buyers can employ several strategies to enhance cost-efficiency when sourcing glass cups:
-
Negotiation: Leverage your position as a buyer to negotiate pricing, especially when placing large orders or establishing long-term relationships. Always ask for discounts based on volume or loyalty.
-
Total Cost of Ownership (TCO): Assess the total cost of ownership, which includes initial price, shipping, handling, and potential returns. This holistic approach can reveal better value options.
-
Pricing Nuances for International Markets: Understand that currency fluctuations and trade tariffs can affect costs. Buyers from Africa, South America, the Middle East, and Europe should factor these variables into their budgeting.
-
Research Suppliers: Conduct thorough research on potential suppliers. Check reviews, certifications, and past performance to ensure quality and reliability.
Conclusion
Understanding the cost structure and pricing dynamics of glass cup suppliers is essential for making informed purchasing decisions. By considering the key components of cost, the various price influencers, and strategic negotiation tips, B2B buyers can enhance their sourcing efficiency and achieve better value in their procurement processes. Keep in mind that indicative prices may vary based on market conditions and specific buyer requirements.
Alternatives Analysis: Comparing glass cup supplier With Other Solutions
In today’s competitive market, international B2B buyers have multiple options when sourcing products. When considering a glass cup supplier, it is essential to explore alternative solutions that may meet your needs more effectively or economically. This analysis will compare glass cup suppliers with alternative materials, such as plastic cups and biodegradable cups, to help you make an informed decision.
Comparison Aspect | Glass Cup Supplier | Plastic Cup Alternative | Biodegradable Cup Alternative |
---|---|---|---|
Performance | High durability, aesthetic appeal, reusable | Lightweight, versatile, but less durable | Compostable, often less sturdy than glass |
Cost | Generally higher initial cost, but reusable | Lower initial cost, disposable | Moderate cost, varies by material |
Ease of Implementation | Requires careful handling and storage | Easy to stack and store, no special handling | Requires proper disposal education |
Maintenance | Requires washing and care | Minimal maintenance needed | May require specific disposal methods |
Best Use Case | Fine dining, events, and branding | Casual events, large gatherings | Eco-conscious events, sustainability-focused businesses |
What Are the Pros and Cons of Using Plastic Cups as an Alternative?
Plastic cups are a popular alternative due to their affordability and convenience. They are lightweight, making them easy to transport and stack, which is ideal for large gatherings or casual events. However, while they are disposable and require minimal maintenance, plastic cups lack the durability and aesthetic appeal of glass. Additionally, they contribute to environmental concerns due to their non-biodegradable nature, which may not align with the sustainability goals of many companies.
How Do Biodegradable Cups Compare as an Alternative Solution?
Biodegradable cups have gained traction in the market as an eco-friendly alternative to traditional materials. They are made from materials like corn starch or sugarcane, which break down more easily in the environment. This option is particularly attractive for businesses focused on sustainability. However, biodegradable cups often have a higher cost than plastic and can be less sturdy than glass, making them less suitable for high-end events. Moreover, proper disposal education is necessary to ensure they fulfill their eco-friendly promise.
Conclusion: How Should B2B Buyers Choose the Right Solution for Their Needs?
When selecting the right solution for your business, it is crucial to consider various factors such as performance, cost, and the specific context in which the products will be used. Glass cup suppliers offer durability and a premium feel, making them ideal for upscale events. In contrast, plastic cups provide a cost-effective and convenient solution for casual settings. Biodegradable cups cater to the growing demand for sustainable options, aligning with eco-conscious branding. By assessing your business goals, customer expectations, and environmental impact, you can make an informed choice that best meets your operational needs.
Essential Technical Properties and Trade Terminology for glass cup supplier
What Are the Key Technical Properties of Glass Cups for B2B Buyers?
When sourcing glass cups, understanding the essential technical properties is vital for making informed purchasing decisions. Here are some critical specifications to consider:
1. Material Grade
The material grade of glass cups typically refers to the quality and composition of the glass used. Common types include soda-lime glass, borosilicate glass, and tempered glass. For B2B buyers, selecting the appropriate material grade ensures that the glass cups meet necessary durability and safety standards, especially for food and beverage applications. Higher-grade materials often offer better thermal resistance and impact durability.
2. Tolerance
Tolerance refers to the allowable variation in dimensions and thickness of glass cups. This specification is crucial as it impacts both functionality and aesthetics. For instance, tighter tolerances can enhance the uniformity of products, which is essential for branding and consumer appeal. In sectors like hospitality, where presentation matters, ensuring the right tolerance is key.
3. Thermal Resistance
Thermal resistance indicates how well a glass cup can withstand temperature changes without breaking or deforming. For B2B buyers, especially in the food service industry, thermal resistance is essential for products that may experience extreme heat or cold. Understanding this property helps ensure that the glass cups will maintain their integrity during usage, reducing the risk of breakage and enhancing customer satisfaction.
4. Weight and Size Variations
Weight and size are critical for both shipping logistics and end-use applications. Heavier glass cups may indicate a thicker material, which can be beneficial for durability but may increase shipping costs. B2B buyers should specify these parameters to align with their product offerings and customer preferences, ensuring that the final product meets operational requirements.
5. Surface Finish
The surface finish of glass cups can significantly affect their appearance and usability. Options may include frosted, polished, or etched finishes. For businesses focusing on branding, a specific surface finish can enhance the product’s aesthetic appeal and marketability. Understanding the implications of surface finishes allows buyers to make choices that align with their branding strategies.
What Are Common Trade Terminologies Relevant to Glass Cup Suppliers?
In addition to technical properties, familiarity with industry jargon is crucial for effective communication and negotiation. Here are some common terms:
1. OEM (Original Equipment Manufacturer)
OEM refers to companies that produce parts or products that are marketed by another company under its brand name. In the context of glass cups, an OEM supplier can manufacture custom-designed cups that meet specific branding requirements. This term is essential for buyers looking to establish unique product lines.
2. MOQ (Minimum Order Quantity)
MOQ is the smallest quantity of a product that a supplier is willing to sell. Understanding MOQ helps B2B buyers manage their inventory and budget effectively. For startups or smaller businesses, negotiating lower MOQs can be crucial for maintaining cash flow while testing market demand.
3. RFQ (Request for Quotation)
An RFQ is a document that a buyer sends to suppliers asking for a price quote for specific products or services. This term is vital for initiating the procurement process, allowing buyers to compare costs and terms from various suppliers, ultimately facilitating informed purchasing decisions.
4. Incoterms (International Commercial Terms)
Incoterms are a set of internationally recognized rules that define the responsibilities of buyers and sellers in international transactions. They specify who pays for shipping, insurance, and tariffs. For B2B buyers, understanding these terms is critical for managing logistical costs and responsibilities effectively.
5. Lead Time
Lead time refers to the time it takes from placing an order until the product is delivered. Knowing the lead time helps buyers plan their inventory and manage supply chain risks. For businesses that rely on just-in-time inventory systems, shorter lead times can be a competitive advantage.
By grasping these technical properties and trade terminologies, international B2B buyers can make informed decisions when sourcing glass cups, ensuring they meet both quality standards and operational needs.
Navigating Market Dynamics and Sourcing Trends in the glass cup supplier Sector
What Are the Current Market Dynamics and Key Trends in the Glass Cup Supplier Sector?
The glass cup supplier sector is experiencing a dynamic transformation driven by several global trends. The rising demand for sustainable and environmentally friendly products is reshaping the market landscape. In regions like Africa and South America, increased consumer awareness about sustainability is pushing businesses to seek suppliers who can provide eco-friendly glass products. In Europe and the Middle East, regulatory pressures are also encouraging companies to adopt greener practices, driving innovation in glass recycling and production processes.
Emerging technologies are playing a crucial role in sourcing trends. Digital platforms for supplier discovery and procurement are gaining traction, offering buyers better visibility into supplier capabilities and product offerings. Blockchain technology is also beginning to influence supply chain transparency, enhancing traceability in sourcing and production processes. Additionally, customization is becoming increasingly important, with B2B buyers seeking suppliers that can offer tailored solutions to meet specific branding and functional requirements.
In summary, international B2B buyers should be aware of the shift towards sustainability, the adoption of digital procurement platforms, and the growing demand for customization when navigating the glass cup supplier market.
How Can B2B Buyers Ensure Sustainability and Ethical Sourcing in Glass Cup Procurement?
Sustainability and ethical sourcing are becoming critical considerations for B2B buyers in the glass cup sector. The environmental impact of glass production, primarily due to energy consumption and raw material extraction, necessitates a focus on sourcing from suppliers committed to sustainable practices. Buyers should prioritize suppliers that implement energy-efficient manufacturing processes and utilize recycled materials in their products.
Certifications such as ISO 14001 (Environmental Management Systems) and the Forest Stewardship Council (FSC) certification for packaging materials can serve as indicators of a supplier’s commitment to sustainability. Furthermore, engaging with suppliers who practice ethical labor standards and provide transparent supply chains can help mitigate risks associated with unethical practices.
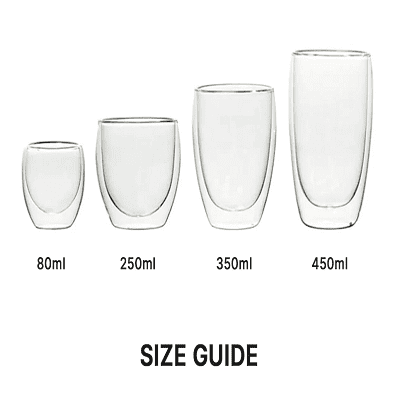
A stock image related to glass cup supplier.
By integrating sustainability into their sourcing strategies, B2B buyers not only enhance their brand reputation but also contribute to a broader global effort toward environmental conservation. This alignment with sustainable practices can lead to increased customer loyalty and market competitiveness.
What Is the Historical Context of the Glass Cup Supplier Sector?
The history of glassmaking dates back thousands of years, with significant advancements shaping the industry into what it is today. The early glass cups were primarily handcrafted, showcasing intricate designs and craftsmanship, particularly in regions like Venice during the Renaissance. As industrialization took hold in the 19th century, mass production techniques revolutionized glass manufacturing, making glass cups more accessible and affordable.
In recent decades, the glass cup supplier sector has seen a shift toward innovative designs and sustainable practices, responding to changing consumer preferences. Modern glass cups not only serve functional purposes but also reflect aesthetic trends and environmental consciousness. Understanding this historical context helps B2B buyers appreciate the evolution of products and the importance of choosing suppliers that align with contemporary values of sustainability and design innovation.
Frequently Asked Questions (FAQs) for B2B Buyers of glass cup supplier
-
How do I evaluate the reliability of a glass cup supplier?
To assess a glass cup supplier’s reliability, start by checking their industry experience and reputation. Look for customer reviews and testimonials, and consider reaching out to previous clients for feedback. Verify their certifications and compliance with international quality standards, such as ISO. Additionally, request samples to evaluate product quality firsthand. Engaging in direct communication and assessing their responsiveness can also provide insights into their reliability and customer service practices. -
What are the essential factors to consider when sourcing glass cups internationally?
When sourcing glass cups internationally, consider factors such as product quality, supplier reliability, and compliance with local regulations. Evaluate the supplier’s manufacturing capabilities, including their production capacity and customization options. Understand the total cost of procurement, including shipping, tariffs, and potential delays. Cultural and language differences can also impact communication, so choose suppliers who can effectively bridge those gaps. Lastly, assess the supplier’s payment terms and risk management strategies to ensure a secure transaction. -
What is the minimum order quantity (MOQ) for glass cups?
The minimum order quantity (MOQ) for glass cups varies by supplier and can range from a few hundred to several thousand units. Factors influencing MOQ include the supplier’s production capabilities, the complexity of the design, and the cost of materials. If you are a smaller buyer, negotiate with suppliers to see if they can accommodate lower MOQs or consider pooling orders with other buyers to meet the MOQ requirements. Always clarify the MOQ upfront to avoid unexpected costs. -
Can I customize glass cup designs with my branding?
Yes, many suppliers offer customization options for glass cups, including printing your logo or specific designs. Customization may involve additional costs and minimum order requirements, so it’s essential to discuss these details early in the negotiation process. Ensure that the supplier has the capabilities to produce the desired design and quality. Request samples of customized products to verify that the final product meets your expectations before placing a larger order. -
What payment terms should I expect from glass cup suppliers?
Payment terms can vary significantly among suppliers, but common practices include a deposit (typically 30-50%) upfront with the balance due before shipment. Some suppliers may offer flexible payment options such as letters of credit or PayPal, especially for established relationships. Always clarify payment terms in writing and ensure they align with your cash flow management strategy. Be cautious of suppliers demanding full payment upfront, as this can increase financial risk. -
How do I ensure quality assurance for glass cups?
To ensure quality assurance, request a detailed quality control plan from your supplier, outlining their inspection processes and standards. It is advisable to conduct pre-shipment inspections, either by hiring third-party quality assurance firms or by visiting the factory yourself. Establish clear specifications regarding materials, dimensions, and finishes before production begins. Documenting all agreements and specifications in contracts can also protect your interests in case of disputes. -
What logistics considerations should I keep in mind when importing glass cups?
Logistics for importing glass cups involves understanding shipping methods, customs regulations, and potential tariffs. Choose a reliable freight forwarder who specializes in handling fragile goods to minimize the risk of damage during transit. Familiarize yourself with import regulations in your country, including any necessary permits or documentation. Consider insurance options to protect your investment during shipping, and calculate lead times to ensure timely delivery for your business needs. -
How can I effectively communicate with international suppliers?
Effective communication with international suppliers requires clarity and professionalism. Use simple language and avoid idioms or slang that may be misunderstood. Establish a clear point of contact and maintain regular updates throughout the procurement process. Utilize communication tools like email, video calls, and instant messaging to facilitate discussions. Be culturally sensitive and aware of time zone differences to ensure timely responses and foster a positive working relationship.
Important Disclaimer & Terms of Use
⚠️ Important Disclaimer
The information provided in this guide, including content regarding manufacturers, technical specifications, and market analysis, is for informational and educational purposes only. It does not constitute professional procurement advice, financial advice, or legal advice.
While we have made every effort to ensure the accuracy and timeliness of the information, we are not responsible for any errors, omissions, or outdated information. Market conditions, company details, and technical standards are subject to change.
B2B buyers must conduct their own independent and thorough due diligence before making any purchasing decisions. This includes contacting suppliers directly, verifying certifications, requesting samples, and seeking professional consultation. The risk of relying on any information in this guide is borne solely by the reader.
Strategic Sourcing Conclusion and Outlook for glass cup supplier
In the competitive landscape of glass cup suppliers, strategic sourcing emerges as a critical factor for international B2B buyers aiming to optimize their procurement processes. By prioritizing suppliers who demonstrate sustainability, innovative production techniques, and quality assurance, businesses can enhance their brand reputation and customer satisfaction. The ability to source high-quality glass cups not only supports operational efficiency but also aligns with consumer trends favoring eco-friendly products.
How Can Strategic Sourcing Enhance Your Business?
Investing time and resources in strategic sourcing allows buyers from Africa, South America, the Middle East, and Europe to build long-term relationships with suppliers that understand their unique market needs. This approach fosters resilience against supply chain disruptions and encourages the adoption of new technologies that can lower costs and improve product offerings.
What Does the Future Hold for Glass Cup Suppliers?
Looking ahead, the demand for innovative and sustainable glass products is expected to rise. B2B buyers should remain proactive in seeking partnerships with suppliers who are committed to environmentally responsible practices. By embracing strategic sourcing now, businesses can position themselves for success in an evolving market landscape. Start your journey toward a sustainable procurement strategy today and unlock the potential of quality glass products for your business growth.