Discover Quality: The Ultimate Power Cord Manufacturer Guide (2025)
Introduction: Navigating the Global Market for power cord manufacturer
In the fast-evolving landscape of global commerce, sourcing reliable power cord manufacturers can pose significant challenges for international B2B buyers. With the increasing demand for high-quality electrical components across various industries, understanding the nuances of power cord procurement is crucial. This guide aims to equip buyers from Africa, South America, the Middle East, and Europe—particularly in regions like Italy and Saudi Arabia—with actionable insights on navigating the complexities of the power cord market.
Throughout this comprehensive resource, we will delve into various types of power cords, their applications in different sectors, and the critical factors influencing supplier selection. From assessing manufacturing standards to understanding pricing dynamics, each section is designed to empower decision-makers with the knowledge needed to make informed purchasing choices.
Moreover, this guide emphasizes the importance of vetting potential suppliers, ensuring compliance with international safety standards, and identifying cost-effective solutions without compromising quality. By leveraging the insights provided here, B2B buyers can streamline their procurement processes, mitigate risks, and ultimately enhance their operational efficiency. Join us as we explore the intricate world of power cord manufacturing, unlocking the keys to successful sourcing strategies tailored for your unique business needs.
Understanding power cord manufacturer Types and Variations
Type Name | Key Distinguishing Features | Primary B2B Applications | Brief Pros & Cons for Buyers |
---|---|---|---|
Standard Power Cords | Basic design, various lengths and plug types | Consumer electronics, appliances | Pros: Cost-effective, widely available. Cons: Limited customization options. |
Heavy-Duty Power Cords | Thicker gauge, higher voltage tolerance | Industrial equipment, machinery | Pros: Durable, suitable for high-demand applications. Cons: More expensive, bulkier. |
Custom Power Cords | Tailored specifications, unique connectors | Specialized equipment, custom projects | Pros: Perfect fit for unique needs. Cons: Longer lead times, potentially higher costs. |
Retractable Power Cords | Built-in retraction mechanism, space-saving design | Office environments, trade shows | Pros: Convenient storage, reduces clutter. Cons: May be less durable than traditional cords. |
Smart Power Cords | Integrated technology for energy management | IoT devices, smart homes | Pros: Enhanced functionality, energy efficiency. Cons: Higher initial investment, tech compatibility concerns. |
What are the Characteristics of Standard Power Cords?
Standard power cords are the most common type, designed for general use across various consumer electronics and appliances. They come in a range of lengths and plug types, making them versatile for different applications. When purchasing, B2B buyers should consider compatibility with their devices and the electrical specifications required for safe operation. Their cost-effectiveness and availability make them an attractive choice for businesses with standard power needs.
How Do Heavy-Duty Power Cords Stand Out?
Heavy-duty power cords are characterized by their thicker gauge and higher voltage tolerance, making them ideal for industrial equipment and machinery. These cords are built to withstand harsher conditions and higher demands, ensuring reliability in critical operations. B2B buyers should evaluate the specific voltage and current requirements of their equipment when selecting heavy-duty options. While they come at a premium, their durability and performance justify the investment for many businesses.
Why Choose Custom Power Cords?
Custom power cords are tailored to meet specific requirements, including unique connector types and lengths. They are particularly beneficial for specialized equipment or projects that demand a precise fit. B2B buyers must consider the lead time for manufacturing and the potential for higher costs associated with custom solutions. However, the ability to perfectly match the cord to the application can enhance operational efficiency and safety.
What Benefits Do Retractable Power Cords Provide?
Retractable power cords feature a built-in mechanism that allows for easy storage and organization, making them ideal for office environments and trade shows. Their space-saving design can reduce clutter and improve aesthetics in professional settings. When considering retractable options, B2B buyers should assess the durability and retraction mechanism’s reliability. While they offer convenience, they may not be as robust as traditional cords, so understanding the application is crucial.
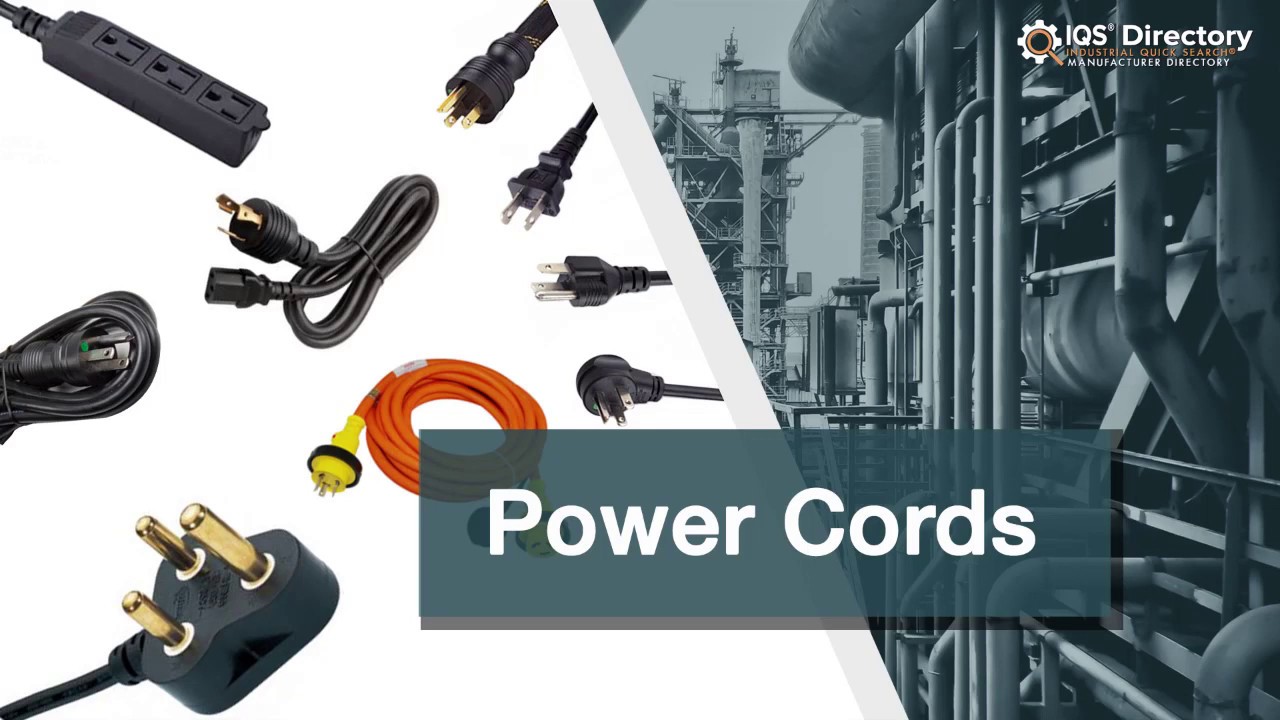
A stock image related to power cord manufacturer.
How Do Smart Power Cords Enhance Functionality?
Smart power cords integrate technology for energy management, often used in IoT devices and smart homes. They offer enhanced functionality, such as remote control and energy monitoring, appealing to businesses looking to improve efficiency. B2B buyers should consider the compatibility of these cords with existing systems and the potential for higher initial costs. However, the long-term energy savings and operational benefits often outweigh the upfront investment, making them a forward-thinking choice.
Related Video: How to Install a 3 Prong Power Cord on an Electric Stove/Range
Key Industrial Applications of power cord manufacturer
Industry/Sector | Specific Application of Power Cord Manufacturer | Value/Benefit for the Business | Key Sourcing Considerations for this Application |
---|---|---|---|
Consumer Electronics | Power cords for home appliances and gadgets | Ensures safety, reliability, and compliance with standards | Certifications, voltage ratings, and compatibility with devices |
Industrial Equipment | Power cords for heavy machinery and equipment | Enhances operational efficiency and reduces downtime | Durability, resistance to environmental factors, and cable length |
Healthcare | Medical-grade power cords for devices like monitors | Critical for patient safety and equipment reliability | Compliance with medical standards, insulation materials, and flexibility |
Renewable Energy | Power cords for solar panels and wind turbines | Supports sustainable energy solutions and reduces costs | Weather resistance, certification for outdoor use, and length options |
Telecommunications | Power cords for networking and communication equipment | Ensures uninterrupted connectivity and data transfer | Shielding requirements, voltage stability, and compatibility with systems |
How Are Power Cords Used in Consumer Electronics?
In the consumer electronics sector, power cords are essential for connecting home appliances and gadgets to electrical outlets. They must adhere to strict safety and quality standards to prevent hazards such as short circuits and electrical fires. For international B2B buyers, especially in regions like Africa and South America, it is crucial to consider certifications that comply with local regulations. Additionally, buyers should ensure that the power cords are compatible with various devices and voltage ratings to avoid operational issues.
What Role Do Power Cords Play in Industrial Equipment?
Power cords are vital components in industrial equipment, facilitating the operation of heavy machinery. These cords must be robust and capable of withstanding harsh working conditions to minimize the risk of failure and downtime. For B2B buyers, particularly in the Middle East and Europe, sourcing durable cables with high resistance to temperature fluctuations, abrasions, and chemicals is essential. Understanding the specific requirements for cable length and connectors is also critical to ensure seamless integration into existing systems.
Why Are Medical-Grade Power Cords Important in Healthcare?
In the healthcare sector, the reliability of medical-grade power cords is paramount, as they are used in critical devices like patient monitors and surgical equipment. These cords must meet stringent medical standards to ensure patient safety and device functionality. For international B2B buyers, particularly in Europe and the Middle East, it is important to verify compliance with regulations such as IEC 60601. Additionally, factors such as insulation materials and flexibility are key to accommodating various medical environments.
How Do Power Cords Contribute to Renewable Energy Solutions?
Power cords play a significant role in renewable energy applications, such as solar panels and wind turbines. They need to be designed to endure outdoor conditions and support efficient energy transfer. B2B buyers from Africa and South America should prioritize sourcing cords that are weather-resistant and certified for outdoor use. This ensures that the energy systems operate efficiently while minimizing maintenance costs and maximizing longevity.
What Are the Sourcing Considerations for Telecommunications Power Cords?
In telecommunications, power cords are critical for maintaining connectivity and ensuring the reliable operation of networking equipment. These cords must be designed to provide stable voltage and include shielding to prevent interference. International B2B buyers, particularly in Europe and the Middle East, should focus on sourcing cords that meet specific voltage stability requirements and are compatible with the technical specifications of their systems. This attention to detail helps maintain uninterrupted service and enhances overall system performance.
Related Video: Power Connectors – Overview
3 Common User Pain Points for ‘power cord manufacturer’ & Their Solutions
Scenario 1: Quality Control Issues in Power Cord Manufacturing
The Problem:
International B2B buyers often encounter significant challenges with product quality when sourcing power cords. This is especially prevalent when dealing with manufacturers from different regions, where varying standards and compliance regulations can lead to discrepancies in product performance. Inconsistent quality can result in increased returns, damaged reputations, and financial losses. For instance, a buyer in Europe may receive power cords that do not meet EU safety standards, which can delay projects and incur penalties.
The Solution:
To mitigate quality control issues, buyers should establish clear quality assurance protocols before finalizing contracts with manufacturers. This includes requesting detailed certifications and compliance documents that outline adherence to international standards, such as IEC or UL certifications. Additionally, it is advisable to conduct pre-shipment inspections through third-party quality control services. Establishing a robust communication channel with the manufacturer can facilitate ongoing quality discussions and improvements. Regular audits of the production process can also help ensure that the manufacturer consistently meets the required quality benchmarks.
Scenario 2: Difficulty in Customization of Power Cords
The Problem:
Many B2B buyers struggle with finding manufacturers that can accommodate specific customization requests for power cords. This is particularly true for businesses in niche markets or those requiring unique specifications, such as length, gauge, or connectors. In South America, for instance, a buyer may need power cords designed to withstand high humidity levels, but many manufacturers offer only standard options, leading to compatibility issues and product failures.
The Solution:
To overcome customization challenges, buyers should clearly articulate their specific needs during the initial discussions with potential manufacturers. Creating a detailed specification document outlining the required features can help manufacturers understand the expectations. Additionally, engaging with manufacturers that have a proven track record in custom solutions is essential. Buyers should seek manufacturers that invest in R&D to innovate their product lines, as they are more likely to accommodate unique requests. Building a partnership approach with the manufacturer can foster flexibility and encourage them to develop bespoke solutions that meet specific regional requirements.
Scenario 3: Supply Chain Delays Impacting Production Timelines
The Problem:
Supply chain disruptions are a common pain point for B2B buyers dealing with power cord manufacturers, particularly in regions like Africa and the Middle East. Delays in shipping, customs clearance, or raw material shortages can significantly impact production timelines and lead to missed deadlines for projects. For example, a construction firm may rely on timely delivery of power cords to complete installations, and any delay can result in financial penalties and loss of client trust.
The Solution:
To address supply chain delays, buyers should consider diversifying their supplier base. Engaging with multiple manufacturers across different regions can reduce reliance on a single source and minimize risk. Implementing a just-in-time inventory system can also help ensure that power cords are available when needed without overstocking. Establishing strong relationships with suppliers can lead to better communication regarding potential delays, allowing buyers to plan accordingly. Additionally, leveraging technology such as supply chain management software can provide real-time visibility into order status, facilitating quicker decision-making and adjustments as needed.
Strategic Material Selection Guide for power cord manufacturer
When selecting materials for power cord manufacturing, it is essential to consider various factors that influence performance, durability, and compliance with international standards. Below, we analyze four common materials used in power cord production, providing insights into their properties, advantages, disadvantages, and specific considerations for international B2B buyers.
What Are the Key Properties of PVC in Power Cord Manufacturing?
Polyvinyl Chloride (PVC) is one of the most widely used materials in power cord manufacturing due to its excellent insulation properties. PVC can withstand temperatures ranging from -10°C to 70°C, making it suitable for various environments. It also offers good resistance to abrasion and chemicals, which is crucial for cords exposed to harsh conditions.
Pros & Cons: PVC is relatively low-cost and easy to manufacture, which makes it an attractive option for mass production. However, it has limitations in high-temperature applications and can become brittle over time, particularly in extreme cold.
Impact on Application: PVC is compatible with a wide range of electrical applications, but its limitations in high-temperature environments may restrict its use in industrial settings.
Considerations for International Buyers: Buyers from regions like Europe and the Middle East should ensure compliance with standards such as IEC 60227 for insulated cables. In Africa and South America, understanding local regulations on PVC use is also critical, given the environmental concerns associated with this material.
How Does Rubber Compare as a Material for Power Cords?
Rubber, particularly thermoplastic elastomers (TPE), is another popular choice for power cords. It offers exceptional flexibility and can operate effectively in temperatures from -40°C to 90°C. Rubber is also resistant to UV light and ozone, making it ideal for outdoor applications.
Pros & Cons: The primary advantage of rubber is its durability and flexibility, which can enhance the lifespan of power cords. However, it tends to be more expensive than PVC and may require more complex manufacturing processes.
Impact on Application: Rubber is particularly suitable for outdoor and industrial applications where flexibility and resilience are paramount. Its superior performance in extreme conditions makes it a preferred choice for high-demand environments.
Considerations for International Buyers: Buyers should be aware of the varying standards across regions. For example, European buyers may need to adhere to EN 50525 standards, while Middle Eastern buyers should consider compliance with local electrical safety regulations.
What Are the Benefits and Limitations of Silicone in Power Cord Manufacturing?
Silicone is increasingly being used in power cord manufacturing due to its high-temperature resistance, withstanding temperatures from -60°C to 200°C. It also offers excellent electrical insulation and is resistant to UV light, ozone, and extreme weather conditions.
Pros & Cons: The key advantage of silicone is its ability to perform in extreme conditions, making it suitable for specialized applications. However, it is one of the more expensive materials and may not be cost-effective for all manufacturers.
Impact on Application: Silicone is ideal for high-performance applications such as medical devices and aerospace, where reliability and safety are critical.
Considerations for International Buyers: Buyers must ensure that silicone products meet stringent international standards, such as FDA regulations for medical applications. Understanding the specific requirements in different regions, such as the Middle East’s focus on durability in extreme conditions, is also essential.
Why Is Polyurethane a Viable Option for Power Cords?
Polyurethane (PU) is known for its excellent abrasion resistance and flexibility, making it a suitable option for power cords that require durability. It can operate within a temperature range of -40°C to 80°C and offers good resistance to oil and chemicals.
Pros & Cons: The main advantage of polyurethane is its robustness and flexibility, which can enhance the longevity of power cords. However, it is generally more expensive than PVC and may require specialized manufacturing techniques.
Impact on Application: PU is particularly effective in applications that involve exposure to oils or chemicals, making it ideal for industrial and automotive uses.
Considerations for International Buyers: Compliance with standards such as ASTM D624 for rubber and elastomer testing is crucial for buyers in North America and Europe. Buyers from Africa and South America should also consider local regulations regarding the use of PU in electrical applications.
Summary Table of Material Selection for Power Cord Manufacturing
Material | Typical Use Case for power cord manufacturer | Key Advantage | Key Disadvantage/Limitation | Relative Cost (Low/Med/High) |
---|---|---|---|---|
PVC | General electrical applications | Low-cost and easy to manufacture | Limited high-temperature performance | Low |
Rubber | Outdoor and industrial applications | Exceptional flexibility and durability | Higher cost and manufacturing complexity | High |
Silicone | High-performance applications | Excellent temperature resistance | Higher cost, not cost-effective for all | High |
Polyurethane | Industrial and automotive applications | Robust and flexible | More expensive and requires special techniques | Medium |
This strategic material selection guide provides international B2B buyers with essential insights to make informed decisions when sourcing power cords, ensuring compliance with regional standards and optimizing product performance.
In-depth Look: Manufacturing Processes and Quality Assurance for power cord manufacturer
What Are the Key Stages in the Manufacturing Process of Power Cords?
The manufacturing of power cords involves several critical stages that ensure the final product meets both functionality and safety standards. Understanding these stages can help B2B buyers assess potential suppliers more effectively.
-
Material Preparation
– Selection of Raw Materials: The process begins with sourcing high-quality raw materials, including copper for conductors, PVC or TPE for insulation, and other components like connectors. Buyers should verify that suppliers use materials that comply with international standards to ensure safety and durability.
– Quality Checks: Before production, materials undergo inspections to confirm they meet specified criteria. This includes assessing electrical conductivity, flexibility, and resistance to environmental factors. -
Forming
– Wire Drawing: In this stage, copper is drawn into thin wires, which are then coated with insulation materials. The diameter of the wire is crucial as it determines the electrical capacity of the power cord.
– Insulation Application: Insulation is applied to the wire using extrusion techniques, ensuring a uniform layer that protects against electrical leakage and environmental damage. -
Assembly
– Connector Attachment: After forming, connectors are attached to the insulated wires. This process requires precision to ensure a secure fit, which is vital for electrical safety and performance.
– Strain Relief Integration: Strain relief mechanisms are integrated to prevent the wire from bending or breaking at the connector point, enhancing the cord’s longevity. -
Finishing
– Sheathing and Final Assembly: The final step involves adding an outer sheath for additional protection. This is often done using a secondary extrusion process, where the entire assembly is encased in a durable outer layer.
– Labeling and Packaging: Finally, cords are labeled with compliance information and packaged for shipment. Proper labeling is essential for regulatory compliance and consumer safety.
How Is Quality Assurance Implemented in Power Cord Manufacturing?
Quality assurance (QA) is integral to the manufacturing process, ensuring that power cords are safe and reliable. B2B buyers should be aware of the various QA methods and international standards that govern production.
-
International Standards and Certifications
– ISO 9001: Many power cord manufacturers adhere to ISO 9001 standards, which focus on quality management systems. This certification indicates that the manufacturer has established a quality management framework that meets customer and regulatory requirements.
– Industry-Specific Certifications: Depending on the market, other certifications like CE (for Europe) and UL (for the USA) may be necessary. These certifications indicate that the product meets specific safety and environmental standards. -
Quality Control Checkpoints
– Incoming Quality Control (IQC): At this stage, raw materials are inspected before entering the production line. IQC ensures that only materials meeting quality standards are used.
– In-Process Quality Control (IPQC): Throughout the manufacturing process, regular checks are conducted to monitor the production quality. This includes measuring insulation thickness and checking for defects in assembly.
– Final Quality Control (FQC): After production, a final inspection is performed to verify that each power cord meets the established specifications. This includes testing electrical conductivity and physical durability. -
Common Testing Methods for Power Cords
– Electrical Testing: This involves checking for short circuits, insulation resistance, and continuity to ensure the cord functions safely under voltage.
– Mechanical Testing: Tests like pull strength and flexing ensure that the connectors and wires can withstand physical stress without failure.
– Environmental Testing: This includes assessing the cord’s performance under various temperature and humidity conditions, ensuring it can operate in diverse environments.
How Can B2B Buyers Verify Supplier Quality Control Processes?
For international B2B buyers, particularly from Africa, South America, the Middle East, and Europe, verifying a supplier’s quality control (QC) measures is crucial. Here are actionable steps to ensure quality compliance.
-
Supplier Audits
– Conducting on-site audits allows buyers to observe the manufacturing processes and quality assurance practices firsthand. During audits, buyers should focus on checking certifications, inspecting production lines, and reviewing QC documentation. -
Requesting Quality Reports
– Buyers should request detailed QC reports from suppliers, including results from IQC, IPQC, and FQC stages. These reports provide insights into the manufacturer’s commitment to quality and compliance with international standards. -
Engaging Third-Party Inspectors
– Utilizing third-party inspection services can provide an unbiased assessment of a supplier’s quality practices. These inspectors can verify that products meet specified standards before shipment, reducing the risk of receiving subpar goods.
What Are the Nuances of QC and Certification for International B2B Buyers?
Understanding the nuances of quality control and certification is essential for B2B buyers operating across different regions. Buyers from Africa, South America, the Middle East, and Europe should consider the following:
- Regional Compliance Requirements: Each region may have specific compliance regulations that manufacturers must follow. For instance, European buyers should ensure that products carry the CE marking, while those in the Middle East may look for G-mark compliance.
- Cultural Differences in Quality Standards: Buyers should be aware that quality expectations may differ between regions. For example, European buyers might prioritize environmental sustainability, while buyers in the Middle East may emphasize durability under harsh conditions.
- Communication and Documentation: Clear communication regarding quality expectations and thorough documentation of certifications can help bridge cultural gaps and enhance trust between buyers and suppliers.
By understanding these manufacturing processes and quality assurance measures, B2B buyers can make informed decisions when selecting power cord manufacturers, ensuring they partner with reliable suppliers who meet international standards.
Practical Sourcing Guide: A Step-by-Step Checklist for ‘power cord manufacturer’
The following practical sourcing guide offers a structured approach for international B2B buyers looking to procure power cords from manufacturers. By following this checklist, you can ensure a thorough evaluation of potential suppliers, leading to successful partnerships.
Step 1: Define Your Technical Specifications
Understanding your technical requirements is crucial before reaching out to manufacturers. Determine the voltage, amperage, and compatibility standards needed for your specific applications. This clarity will help you communicate effectively with suppliers and ensure that the products meet your operational needs.
- Key specifications to consider:
- Plug types and configurations
- Length and gauge of the cord
- Environmental conditions (e.g., indoor, outdoor, temperature resistance)
Step 2: Conduct Market Research for Suppliers
Researching potential suppliers is essential to identify reliable manufacturers. Utilize industry directories, trade shows, and online platforms to compile a list of candidates. Pay particular attention to suppliers with a proven track record in your target regions, such as Africa, South America, and Europe.
- Resources for supplier research:
- B2B marketplaces like Alibaba or Global Sources
- Trade associations related to electrical components
Step 3: Verify Supplier Certifications
Before initiating any discussions, verify that your potential suppliers hold the necessary certifications. Certifications such as ISO 9001 for quality management and UL or CE marks for safety standards are indicators of a reputable manufacturer. This step is vital to ensure compliance with international regulations and reduce risks in your supply chain.
- Important certifications to check:
- ISO certification relevant to manufacturing
- Compliance with local and international safety standards
Step 4: Request Samples for Quality Assessment
Once you have shortlisted potential suppliers, request samples of their power cords. This step allows you to evaluate the quality of materials and craftsmanship firsthand. Assess the samples against your specifications and industry standards to gauge their suitability for your needs.
- What to look for in samples:
- Durability and flexibility of the cords
- Quality of connectors and plugs
Step 5: Evaluate Supplier Capabilities and Capacity
Understanding a supplier’s production capabilities is critical to ensure they can meet your demand. Inquire about their production capacity, lead times, and ability to scale operations if your order volume increases. This assessment helps you avoid potential supply chain disruptions.
- Questions to ask:
- What is the maximum output capacity per month?
- Can they accommodate custom orders or modifications?
Step 6: Negotiate Terms and Pricing
After selecting a suitable supplier, engage in negotiations regarding pricing, payment terms, and delivery schedules. Aim for a mutually beneficial agreement that balances cost and quality. Be clear about your expectations to foster a transparent relationship.
- Key points to negotiate:
- Bulk order discounts
- Payment terms (e.g., upfront, net 30 days)
Step 7: Establish a Clear Communication Channel
Effective communication is essential for a successful partnership. Establish a reliable channel for ongoing dialogue with your supplier to address any issues that may arise during production or delivery. Regular updates and feedback will strengthen the relationship and ensure alignment on project goals.
- Communication tools to consider:
- Email for formal correspondence
- Instant messaging platforms for quick updates
By following this checklist, international B2B buyers can streamline their sourcing process for power cords, ensuring they find a manufacturer that meets their technical, quality, and operational needs.
Comprehensive Cost and Pricing Analysis for power cord manufacturer Sourcing
What Are the Key Cost Components in Power Cord Manufacturing?
When sourcing power cords, understanding the intricate cost structure is vital for B2B buyers. The primary cost components include:
-
Materials: The choice of materials significantly impacts the overall cost. High-quality copper, PVC, and rubber insulation are standard, but opting for eco-friendly or specialized materials can increase expenses.
-
Labor: Labor costs vary by region. In countries with higher wage standards, such as Italy or Germany, labor costs can constitute a larger portion of the total price compared to regions in Africa or South America.
-
Manufacturing Overhead: This includes costs associated with factory operations, such as utilities, rent, and equipment maintenance. Efficient manufacturing processes can help reduce overhead costs.
-
Tooling: Initial tooling costs can be substantial, especially for custom designs. Buyers must consider these costs when evaluating different suppliers, as they can affect the final pricing.
-
Quality Control (QC): Ensuring product quality is essential. Implementing rigorous QC processes can add to costs but ultimately reduces the risk of defects, leading to fewer returns and enhanced customer satisfaction.
-
Logistics: Shipping and handling can significantly affect the final cost. International buyers should factor in freight charges, insurance, and potential tariffs.
-
Margin: Suppliers will add a margin to cover their costs and ensure profitability. Understanding typical margins in the industry can aid in negotiations.
How Do Pricing Influencers Affect Power Cord Sourcing?
Several factors influence pricing in the power cord manufacturing sector:
-
Volume and Minimum Order Quantity (MOQ): Larger orders typically lead to lower per-unit costs. Establishing a long-term relationship with a supplier can allow for favorable pricing structures.
-
Specifications and Customization: Custom specifications, such as unique lengths or specialized connectors, can increase costs. Buyers should assess whether customization is necessary for their needs.
-
Material Quality and Certifications: Higher quality materials and industry certifications (such as UL or CE) may increase costs but are often essential for compliance and safety. Buyers should weigh the benefits against the potential price increase.
-
Supplier Factors: The supplier’s location, reputation, and production capabilities can all affect pricing. Engaging with reputable manufacturers may come at a premium, but it often results in better quality and reliability.
-
Incoterms: Understanding Incoterms (International Commercial Terms) is crucial as they define the responsibilities of buyers and sellers in terms of shipping, insurance, and tariffs. Selecting the right Incoterm can lead to significant cost savings.
What Are Effective Buyer Tips for Negotiating Power Cord Prices?
To navigate the complexities of power cord sourcing, consider the following tips:
-
Leverage Negotiation: Approach negotiations with data on market prices and competitor quotes. Establishing a clear understanding of your budget and requirements can empower your position.
-
Focus on Cost-Efficiency: Evaluate the total cost of ownership (TCO) rather than just the purchase price. Consider factors such as durability, maintenance, and potential energy savings over the product’s lifecycle.
-
Understand Pricing Nuances: International buyers should be aware that pricing can fluctuate based on geopolitical factors, currency exchange rates, and local economic conditions. Keeping abreast of these trends can aid in timing your purchases.
-
Build Relationships with Suppliers: Cultivating strong relationships can lead to better pricing and terms. Suppliers are often more willing to negotiate with buyers who demonstrate loyalty and reliability.
-
Request Samples: Before committing to a large order, request samples to evaluate quality and ensure the product meets your specifications. This step can prevent costly mistakes down the line.
Disclaimer on Indicative Prices
Pricing for power cords can vary widely based on the aforementioned factors. The figures provided here are indicative and should be verified with potential suppliers for accuracy. Always seek multiple quotes to ensure competitive pricing and terms that align with your sourcing strategy.
Alternatives Analysis: Comparing power cord manufacturer With Other Solutions
Understanding Alternatives to Power Cord Manufacturing
In the competitive landscape of electrical components, B2B buyers often encounter various solutions that can fulfill their power connectivity needs. While traditional power cord manufacturers provide reliable options, exploring alternative technologies can lead to enhanced efficiency, cost savings, and tailored solutions for specific applications. This analysis will compare power cord manufacturing with two viable alternatives: wireless power transmission and modular power distribution systems.
Comparison Table
Comparison Aspect | Power Cord Manufacturer | Wireless Power Transmission | Modular Power Distribution Systems |
---|---|---|---|
Performance | High, with consistent current flow | Variable, depends on distance and alignment | High, with customizable load capacities |
Cost | Moderate initial cost, low long-term maintenance | Higher upfront investment, potential for savings over time | Moderate cost, scalable based on needs |
Ease of Implementation | Straightforward, minimal training required | Complex installation, requires specific alignment and technology | Easy to implement with standard components |
Maintenance | Low, durable materials | Moderate, requires regular checks for efficiency | Low, modular parts can be replaced easily |
Best Use Case | General use in homes and industries | Ideal for dynamic environments where mobility is essential | Best for large facilities needing flexibility in power distribution |
Pros and Cons of Wireless Power Transmission
Wireless power transmission offers a unique method of powering devices without physical connections. The key advantage is its ability to provide power to devices in motion, making it ideal for applications like electric vehicles or consumer electronics in dynamic environments. However, the technology is still evolving, and its efficiency can vary based on distance and alignment. Additionally, the initial investment is typically higher than traditional power cords, which may deter some buyers. Overall, this solution is best suited for industries requiring mobility and flexibility.
Analyzing Modular Power Distribution Systems
Modular power distribution systems present an innovative alternative for businesses needing flexible and scalable power solutions. These systems allow for easy customization of power load capacities, which can be particularly advantageous in environments where power demands fluctuate. The ease of implementation is a significant benefit, as they utilize standard components that require minimal training for installation. While the cost is moderate, it can be tailored to fit the specific needs of an organization, making it an appealing choice for large facilities. However, businesses must consider whether they have the infrastructure to support modular systems effectively.
Conclusion: How to Choose the Right Power Solution for Your Business
Selecting the right power solution involves evaluating your specific needs against the strengths and weaknesses of each option. For businesses in Africa, South America, the Middle East, and Europe, understanding the local infrastructure, cost constraints, and intended use cases is crucial. While power cord manufacturers provide reliability and ease of use, alternatives like wireless power transmission and modular systems can offer innovative solutions that may align better with modern operational requirements. Ultimately, the decision should be informed by a comprehensive analysis of performance, cost, and implementation ease, ensuring that the chosen solution supports the long-term goals of the business.
Essential Technical Properties and Trade Terminology for power cord manufacturer
What Are the Critical Technical Properties of Power Cords?
When sourcing power cords, understanding key technical properties is essential for ensuring product performance and compliance with industry standards. Below are several critical specifications that international B2B buyers should consider:
1. Material Grade: Why Is It Important?
The material grade of the conductors and insulation plays a vital role in determining the power cord’s durability and electrical performance. Common materials include copper (for conductors) and PVC or rubber (for insulation). Higher-grade materials typically offer better conductivity, flexibility, and resistance to environmental factors, which can enhance the longevity of the product. For buyers, selecting the right material grade can impact both operational efficiency and safety compliance.
2. Voltage Rating: How Does It Affect Usage?
The voltage rating indicates the maximum voltage a power cord can safely handle. This property is crucial for ensuring that the cord can support the electrical demands of the devices it connects. Buyers should match the voltage rating of the power cord to their specific applications to prevent overheating or electrical failures. This is especially pertinent in regions with varying electrical standards, such as Europe and the Middle East.
3. Current Rating: What Should Buyers Look For?
The current rating specifies the maximum amount of electrical current the power cord can carry without overheating. It is usually measured in amperes (A). Understanding this property is essential for buyers to ensure that the power cord can handle the load of connected devices. Overloading a power cord can lead to serious safety hazards, including fire risks.
4. Tolerance: How Does It Impact Performance?
Tolerance refers to the permissible limit of variation in the cord’s dimensions and electrical properties. For instance, a tight tolerance can lead to improved performance and reliability. Buyers should consider this specification when looking for power cords that must fit specific connectors or applications. A power cord with a loose tolerance may not perform consistently, leading to potential operational issues.
5. Temperature Rating: Why Is It Critical?
The temperature rating indicates the maximum and minimum temperature conditions under which the power cord can safely operate. This property is particularly important in regions with extreme temperatures, such as parts of Africa and the Middle East. Ensuring that the power cord is rated for the appropriate temperature range helps prevent insulation degradation and electrical failures.
What Are Common Trade Terms in the Power Cord Industry?
Navigating the power cord manufacturing industry involves understanding specific jargon that can influence negotiations and purchasing decisions. Here are some common terms that B2B buyers should be familiar with:
1. OEM: What Does It Stand For?
OEM, or Original Equipment Manufacturer, refers to companies that produce parts or equipment that may be marketed by another manufacturer. For buyers, engaging with OEMs can provide access to high-quality components tailored to specific needs, enhancing overall product performance.
2. MOQ: Why Is It Relevant?
MOQ stands for Minimum Order Quantity, which is the smallest number of units a supplier is willing to sell. Understanding MOQ is crucial for buyers, especially those with limited budgets or storage capabilities. It helps in planning inventory and assessing the feasibility of a purchase.
3. RFQ: How Does It Facilitate Procurement?
RFQ, or Request for Quotation, is a document sent to suppliers requesting pricing and terms for a specific quantity of goods. This process allows buyers to compare offers from different manufacturers, ensuring they receive the best possible deal for their power cord needs.
4. Incoterms: How Do They Affect Shipping?
Incoterms, or International Commercial Terms, are a set of predefined rules that clarify the responsibilities of buyers and sellers in international transactions. Understanding these terms helps buyers avoid misunderstandings related to shipping costs, delivery timelines, and risk management.
5. CE Marking: Why Is It Important for European Buyers?
CE marking indicates that a product complies with European safety and environmental standards. For buyers in Europe, ensuring that power cords bear the CE mark is essential for market access and regulatory compliance. It also signifies a commitment to quality and safety.
By grasping these essential technical properties and trade terminology, international B2B buyers can make informed purchasing decisions that align with their operational needs and regulatory requirements.
Navigating Market Dynamics and Sourcing Trends in the power cord manufacturer Sector
What Are the Current Market Dynamics and Key Trends in the Power Cord Manufacturing Sector?
The power cord manufacturing sector is experiencing significant transformations driven by technological advancements, evolving consumer demands, and regulatory changes. One of the primary global drivers is the increasing emphasis on energy efficiency and the adoption of smart technologies. As businesses globally seek to reduce energy consumption, power cords that integrate smart features and energy-efficient designs are gaining traction. Additionally, the rise of e-commerce has reshaped sourcing dynamics, allowing international B2B buyers to access a broader range of suppliers and products, particularly from emerging markets in Africa and South America.
In terms of sourcing trends, buyers are increasingly favoring suppliers who offer customizable solutions that align with specific industry standards and compliance requirements. This trend is particularly relevant for buyers in Europe and the Middle East, where stringent regulations govern product safety and environmental impact. The demand for high-quality, durable materials has also surged, with manufacturers focusing on innovation in materials like PVC, TPE, and recycled components.
Furthermore, collaboration between manufacturers and technology companies is on the rise, leading to the development of advanced power cord solutions that incorporate features such as enhanced durability, flexibility, and compatibility with various devices. International B2B buyers should stay updated on these trends to make informed sourcing decisions that align with their operational needs and market demands.
How Is Sustainability Influencing Sourcing Decisions in the Power Cord Manufacturing Sector?
Sustainability is becoming a crucial factor for B2B buyers in the power cord manufacturing sector. The environmental impact of production processes and materials used in power cords has prompted buyers to prioritize ethical sourcing practices. Companies are increasingly scrutinizing their supply chains to ensure they are not only compliant with local regulations but also contribute positively to global sustainability efforts.
One significant aspect of this trend is the rise in demand for ‘green’ certifications and materials. Certifications such as RoHS (Restriction of Hazardous Substances) and REACH (Registration, Evaluation, Authorisation, and Restriction of Chemicals) are becoming essential for suppliers to demonstrate their commitment to reducing harmful substances in their products. Furthermore, the use of recyclable materials and eco-friendly manufacturing processes is gaining importance among international buyers, particularly in regions like Europe, where environmental regulations are stringent.
For B2B buyers, engaging with suppliers who prioritize sustainability not only enhances their corporate social responsibility (CSR) profile but also mitigates risks associated with environmental compliance. By aligning with manufacturers that adhere to sustainable practices, businesses can ensure a more resilient supply chain and foster long-term partnerships that contribute to both profitability and environmental stewardship.
What Is the Historical Context of Power Cord Manufacturing and Its Relevance Today?
The evolution of power cord manufacturing can be traced back to the early 20th century when electrical appliances began to proliferate in households and industries. Initially, power cords were rudimentary, focusing primarily on functionality without much consideration for safety or design. However, as technology advanced and safety standards became more stringent, manufacturers began to innovate, leading to the development of more durable and flexible materials.
In the late 20th and early 21st centuries, the globalization of supply chains transformed the industry, enabling manufacturers to source raw materials and components from various regions. This shift facilitated competitive pricing and diversified product offerings. Today, the historical context of power cord manufacturing is highly relevant as it informs current practices in quality assurance, safety compliance, and sustainability. Understanding this evolution allows international B2B buyers to appreciate the complexities of the industry and make informed decisions about sourcing strategies and supplier relationships.
Frequently Asked Questions (FAQs) for B2B Buyers of power cord manufacturer
-
How do I choose the right power cord manufacturer for my needs?
Selecting the appropriate power cord manufacturer involves several key factors. First, assess their experience and reputation in the industry, particularly in your target market, whether it’s Africa, South America, the Middle East, or Europe. Investigate their certifications and compliance with international standards, as this ensures product safety and quality. Additionally, consider their capability for customization, minimum order quantities (MOQs), and lead times to meet your specific requirements. Request samples to evaluate the quality before making a commitment. -
What are the key certifications to look for in a power cord manufacturer?
When sourcing power cords, it’s essential to check for certifications such as UL, CE, and RoHS. These certifications indicate compliance with safety standards and regulations in various markets. For example, UL certification is crucial for North American markets, while CE marking is required for products sold in the European Union. Additionally, RoHS compliance ensures that the power cords are free from hazardous substances, which is increasingly important in many regions, including Europe and parts of the Middle East. -
How can I verify the credibility of a power cord supplier?
To verify a supplier’s credibility, conduct thorough research by checking their business licenses, industry certifications, and customer reviews. Utilize platforms like LinkedIn to connect with other businesses that have worked with them. Request references and case studies to understand their operational capabilities and customer service standards. Additionally, consider visiting their manufacturing facility if feasible, as this can provide firsthand insight into their production processes and quality control measures. -
What customization options are typically available for power cords?
Most power cord manufacturers offer a range of customization options, including different lengths, colors, and connector types to suit specific applications. You can also request alterations in wire gauge, insulation materials, and even branding on the cords. Ensure that the manufacturer can accommodate your specific requirements and discuss any additional costs or minimum order quantities associated with custom designs. This is particularly crucial for businesses looking to enhance their branding or meet unique operational needs. -
What are the common minimum order quantities (MOQs) for power cords?
Minimum order quantities can vary significantly depending on the manufacturer and the complexity of the order. Typically, MOQs for power cords may range from 100 to 1,000 units. It’s essential to discuss this upfront with potential suppliers, especially if you are a smaller business or are testing a new product line. Some manufacturers may offer flexible MOQs for established clients or during promotional periods, so it’s worth negotiating based on your specific needs. -
What payment terms should I expect when sourcing power cords internationally?
Payment terms can vary widely among manufacturers and depend on your relationship with the supplier. Common options include advance payments, letters of credit, or payment upon delivery. For first-time purchases, manufacturers may require partial upfront payment, often around 30%, with the remainder due upon shipment. It’s advisable to clarify these terms early in negotiations and ensure they align with your financial processes and cash flow management. -
How do I ensure quality assurance when sourcing power cords?
To ensure quality assurance, request detailed information about the manufacturer’s quality control processes, including testing procedures and inspection protocols. Many reputable manufacturers will have a dedicated QA team and may offer third-party testing services. Consider specifying quality standards in your contract and requesting a pre-shipment inspection before the products are dispatched. This proactive approach helps mitigate risks associated with defective products and ensures compliance with your quality expectations. -
What logistics considerations should I keep in mind when importing power cords?
When importing power cords, consider shipping methods, customs regulations, and potential tariffs that may apply in your country. Understand the lead times for production and shipping, as well as the logistics provider’s reliability. It’s also important to account for potential delays at customs and ensure proper documentation is in place to facilitate smooth clearance. Collaborating with a freight forwarder experienced in your target market can help navigate these logistics challenges efficiently.
Important Disclaimer & Terms of Use
⚠️ Important Disclaimer
The information provided in this guide, including content regarding manufacturers, technical specifications, and market analysis, is for informational and educational purposes only. It does not constitute professional procurement advice, financial advice, or legal advice.
While we have made every effort to ensure the accuracy and timeliness of the information, we are not responsible for any errors, omissions, or outdated information. Market conditions, company details, and technical standards are subject to change.
B2B buyers must conduct their own independent and thorough due diligence before making any purchasing decisions. This includes contacting suppliers directly, verifying certifications, requesting samples, and seeking professional consultation. The risk of relying on any information in this guide is borne solely by the reader.
Strategic Sourcing Conclusion and Outlook for power cord manufacturer
In navigating the complex landscape of power cord manufacturing, strategic sourcing emerges as an essential practice for international B2B buyers. By prioritizing suppliers who demonstrate a commitment to quality, compliance, and innovation, businesses can ensure the reliability of their power cords, which are critical to their operations. Evaluating potential partners based on their manufacturing capabilities, certifications, and past performance can mitigate risks and enhance supply chain resilience.
How Can Strategic Sourcing Enhance Your Competitive Edge?
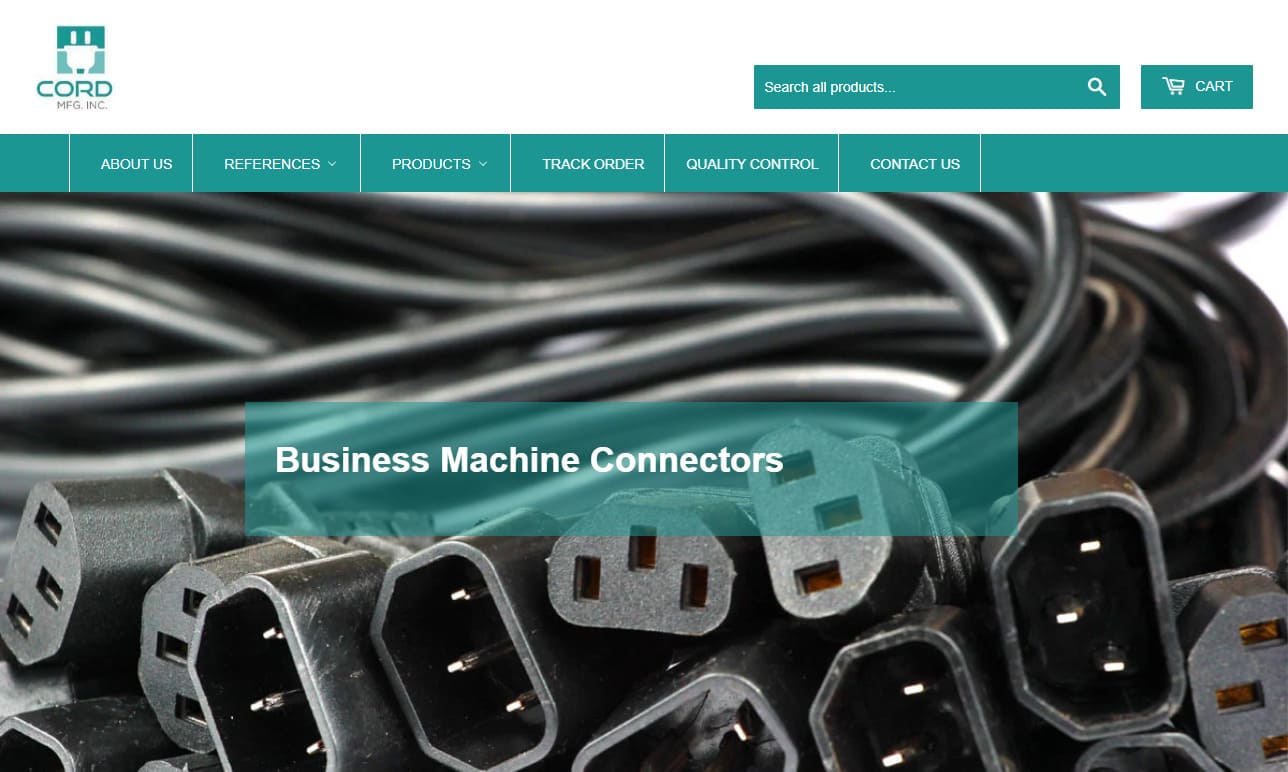
A stock image related to power cord manufacturer.
For buyers in Africa, South America, the Middle East, and Europe, the ability to source power cords strategically not only reduces costs but also improves product availability and fosters long-term partnerships. As global demand for electronic devices continues to rise, so does the need for high-quality power cords that meet diverse regulatory standards.
What Should International Buyers Do Next?
To stay ahead, B2B buyers should actively engage with manufacturers who prioritize sustainability and technological advancements. Investing time in supplier relationship management and conducting regular market assessments will position businesses to adapt to changing market dynamics effectively.
As we look to the future, the call to action is clear: leverage strategic sourcing to unlock new opportunities and drive growth. The power cord manufacturing sector holds significant promise, and by making informed decisions today, you can secure a competitive advantage for tomorrow.