Discover Quality: Your Guide to Tape Measure Manufacturers (2025)
Introduction: Navigating the Global Market for tape measure manufacturer
In the dynamic landscape of global trade, sourcing a reliable tape measure manufacturer poses significant challenges for international B2B buyers. The need for precise measurement tools is paramount across various industries, including construction, engineering, and manufacturing. However, navigating the complexities of supplier selection, quality assurance, and cost-effectiveness can be daunting, particularly for businesses operating in diverse markets such as Africa, South America, the Middle East, and Europe. This comprehensive guide aims to demystify the process of sourcing tape measures, providing actionable insights that empower buyers to make informed purchasing decisions.
Throughout this guide, we will explore the various types of tape measures available in the market, their specific applications, and the critical factors to consider when vetting potential suppliers. Understanding the nuances of pricing structures and shipping logistics will also be covered, ensuring that buyers are equipped to negotiate effectively.
By leveraging the knowledge presented here, B2B buyers will be better positioned to identify reputable tape measure manufacturers that meet their unique business needs. Whether you are in Saudi Arabia seeking durable measuring tools for construction projects or in South Africa looking for cost-effective solutions, this guide will serve as your roadmap in the global marketplace for tape measures.
Understanding tape measure manufacturer Types and Variations
Type Name | Key Distinguishing Features | Primary B2B Applications | Brief Pros & Cons for Buyers |
---|---|---|---|
Mechanical Tape Measures | Simple, durable, and often retractable; typically made of metal or fiberglass. | Construction, woodworking, and general measurement tasks. | Pros: Cost-effective, reliable for basic measurements. Cons: Limited features compared to digital options. |
Digital Tape Measures | Incorporate electronic displays and advanced features like Bluetooth connectivity. | Precision measurement in engineering, architecture, and design. | Pros: High accuracy, easy data sharing. Cons: Higher cost and potential battery dependency. |
Laser Distance Measurers | Use laser technology for quick and precise measurements over long distances. | Large-scale construction, real estate, and surveying. | Pros: Extremely accurate, can measure inaccessible areas. Cons: Higher initial investment and requires understanding of technology. |
Custom Tape Measures | Tailored designs or features based on specific industry needs (e.g., branding). | Marketing, branding, and specialized industrial applications. | Pros: Unique branding opportunity, tailored functionality. Cons: Longer lead times and potentially higher costs. |
Specialized Tape Measures | Designed for specific tasks, such as measuring curves or for use in specific industries. | Fashion design, automotive, and specialized engineering. | Pros: Enhanced functionality for specific tasks. Cons: May not be versatile for general use. |
What Are Mechanical Tape Measures and When to Use Them?
Mechanical tape measures are traditional measurement tools known for their durability and simplicity. Typically made from metal or fiberglass, these tools are retractable and easy to use, making them a staple in construction and woodworking industries. When choosing a mechanical tape measure, consider its length, durability, and ease of use, as these factors can significantly impact efficiency on the job site.
How Do Digital Tape Measures Enhance Precision?
Digital tape measures are equipped with electronic displays that provide accurate measurements and often include features such as Bluetooth connectivity for data transfer. These tools are particularly beneficial in fields requiring high precision, such as engineering and architecture. B2B buyers should assess the display clarity, measurement range, and battery life when considering digital options, as these features can affect usability in various environments.
Why Choose Laser Distance Measurers for Large Projects?
Laser distance measurers utilize laser technology to deliver quick and precise measurements over significant distances, making them ideal for large-scale construction, real estate, and surveying applications. Their ability to measure inaccessible areas adds to their appeal. Buyers should consider the range, accuracy, and ease of use when selecting a laser measurer, as these factors are critical for effective project execution.
What Are the Benefits of Custom Tape Measures for Branding?
Custom tape measures can be tailored to meet specific industry needs, such as incorporating unique branding elements. They serve as effective marketing tools in various sectors, providing both functionality and brand visibility. When considering custom options, B2B buyers should evaluate lead times, design capabilities, and cost implications to ensure alignment with their promotional strategies.
How Do Specialized Tape Measures Cater to Unique Needs?
Specialized tape measures are designed for specific tasks, such as measuring curves or serving specialized industries like fashion design or automotive. These tools enhance functionality for niche applications, providing users with the precision required for their specific tasks. Buyers should assess the particular features and adaptability of these tools to ensure they meet their unique measurement requirements.
Related Video: How to read a tape measure : Tips for reading a tape faster
Key Industrial Applications of tape measure manufacturer
Industry/Sector | Specific Application of tape measure manufacturer | Value/Benefit for the Business | Key Sourcing Considerations for this Application |
---|---|---|---|
Construction | Accurate site measurements for building projects | Ensures precision in construction, reducing waste and rework | Quality of materials, measurement range, durability |
Manufacturing | Quality control in product dimensions | Guarantees compliance with specifications, enhancing product quality | Calibration accuracy, ease of use, metric vs imperial units |
Interior Design and Architecture | Space planning and layout design | Optimizes space utilization and enhances design efficiency | Flexibility in measurement units, portability, and storage |
Retail and Merchandising | Inventory management and product display measurements | Improves stock management and maximizes display effectiveness | Length accuracy, material quality, and ease of measurement |
Automotive | Vehicle component measurements during assembly | Increases assembly efficiency and product reliability | Resistance to wear, accurate scaling, and ease of handling |
How is Tape Measure Used in the Construction Industry?
In the construction sector, tape measures are essential tools for obtaining precise site measurements, ensuring that materials are cut and installed accurately. They help avoid costly mistakes that can arise from incorrect measurements, such as misaligned structures or excess waste from over-ordering materials. International buyers from regions like Africa and South America should prioritize sourcing tape measures that offer durability and a good measurement range, as construction sites often face challenging conditions.
What Role Does Tape Measure Play in Manufacturing Quality Control?
Manufacturers utilize tape measures to verify product dimensions during various stages of production. This ensures that products meet quality standards and specifications, which is crucial for maintaining customer satisfaction and compliance with industry regulations. For B2B buyers, especially in Europe and the Middle East, sourcing tape measures with high calibration accuracy and user-friendly features can significantly enhance the quality control process.
How is Tape Measure Beneficial for Interior Design and Architecture?
In interior design and architecture, tape measures are used for space planning and layout design. They assist designers in visualizing and optimizing space utilization, which is vital for creating functional and aesthetically pleasing environments. Buyers in regions like Saudi Arabia and South Africa should consider sourcing flexible tape measures that can easily switch between metric and imperial units, accommodating diverse design preferences.
Why is Tape Measure Important in Retail and Merchandising?
Retailers use tape measures for inventory management and ensuring that product displays are correctly sized. Accurate measurements help improve stock management and enhance the effectiveness of product displays, ultimately driving sales. International buyers should focus on tape measures that are easy to use and transport, ensuring that staff can quickly and efficiently manage inventory across various store layouts.
What is the Application of Tape Measure in the Automotive Industry?
In the automotive sector, tape measures are critical for measuring vehicle components during assembly. They help ensure that parts fit together correctly, which is essential for product reliability and performance. For B2B buyers in regions like Europe, sourcing tape measures that are resistant to wear and easy to handle can streamline the assembly process and improve overall production efficiency.
Related Video: How to Use a Tape Measure
3 Common User Pain Points for ‘tape measure manufacturer’ & Their Solutions
Scenario 1: Inaccurate Measurements Lead to Project Delays
The Problem: One of the most significant challenges faced by B2B buyers in the construction and manufacturing sectors is ensuring the accuracy of measurements. Inaccurate tape measures can lead to costly mistakes, such as cutting materials to the wrong size, which not only delays projects but also increases waste and expenses. For buyers in regions like South Africa or Saudi Arabia, where precise measurements are critical for compliance with local building codes, this issue can severely impact timelines and budgets.
The Solution: To address this challenge, buyers should prioritize sourcing tape measures from manufacturers that provide detailed specifications and quality assurance certifications. Before making a purchase, it’s essential to verify the calibration standards of the tape measures. Buyers can request test reports or certifications that confirm the accuracy of the tools. Furthermore, investing in digital or laser tape measures can enhance precision and reduce human error. Regularly training staff on proper measurement techniques and the importance of double-checking measurements can also mitigate the risk of inaccuracies.
Scenario 2: Limited Product Range Affects Operational Efficiency
The Problem: Many B2B buyers struggle with limited product ranges offered by tape measure manufacturers. This limitation can hinder operational efficiency, particularly when a business requires various types of tape measures for different applications, such as construction, woodworking, or metalworking. Buyers from regions like Europe, where diverse industries coexist, may find it challenging to source all necessary tools from a single supplier, resulting in increased procurement time and costs.
The Solution: To overcome this pain point, buyers should seek manufacturers that provide a comprehensive range of tape measure products, including specialized options like heavy-duty, retractable, and digital tape measures. Creating partnerships with suppliers that can offer customized solutions tailored to specific industry needs can streamline procurement processes. Additionally, buyers should communicate their requirements clearly to manufacturers, enabling them to recommend the most suitable products. Regularly reviewing supplier catalogs and engaging in product training sessions can also help buyers stay updated on new offerings and innovations in tape measure technology.
Scenario 3: Poor Durability and Quality Affect Long-Term Use
The Problem: Another common issue is the durability and quality of tape measures. Buyers often face frustration when tools wear out quickly, especially in demanding environments like construction sites in the Middle East or manufacturing facilities in South America. This not only leads to frequent replacements but also raises concerns about safety and reliability, as a broken tape measure can cause injuries or measurement errors.
The Solution: To ensure long-term satisfaction, buyers should conduct thorough research on the materials and construction of the tape measures they intend to purchase. Opting for tape measures made with high-quality materials such as reinforced nylon or steel can enhance durability. Buyers should also look for manufacturers that offer warranties or guarantees, as these can be indicators of product reliability. Additionally, establishing a maintenance routine, including regular inspections and cleaning, can prolong the life of tape measures. Engaging with manufacturers for feedback on product performance and seeking user reviews can also provide insights into the best options available in the market.
Strategic Material Selection Guide for tape measure manufacturer
What are the Key Properties of Common Materials Used in Tape Measures?
When selecting materials for tape measures, manufacturers often consider several common options, each with distinct properties that affect performance, durability, and cost. The most prevalent materials include steel, fiberglass, plastic, and aluminum. Understanding these materials helps international B2B buyers make informed decisions based on their specific needs and regional standards.
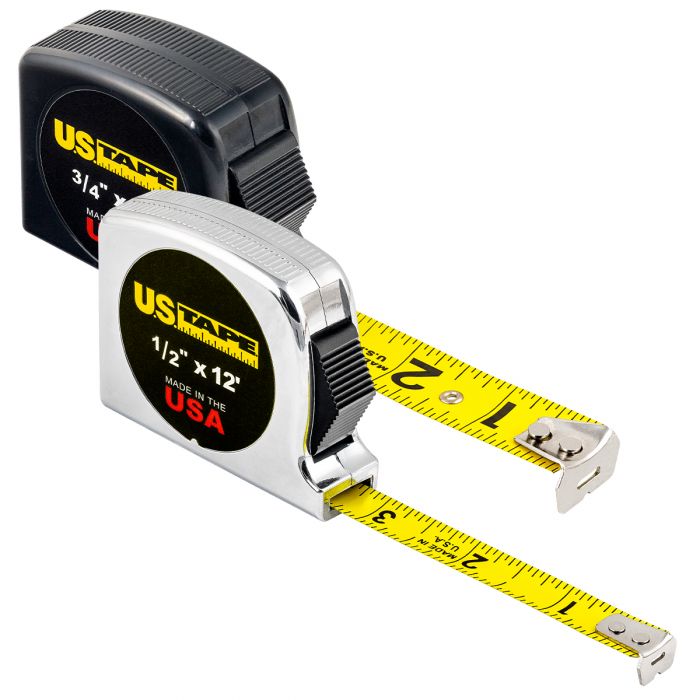
A stock image related to tape measure manufacturer.
How Does Steel Perform as a Material for Tape Measures?
Steel is a traditional choice for tape measures due to its strength and durability. It typically has a high tensile strength, making it resistant to bending and breaking under pressure. Steel tape measures can withstand a wide range of temperatures and are generally resistant to corrosion, especially when coated.
Pros:
– Durability: Steel tape measures are robust and can endure heavy use.
– Accuracy: They provide precise measurements due to their rigidity.
– Cost-Effectiveness: Steel is relatively inexpensive compared to other materials.
Cons:
– Weight: Steel tape measures are heavier, which can be a disadvantage for portability.
– Corrosion: While resistant, they can rust if not properly maintained, particularly in humid environments.
For international buyers, compliance with standards such as ASTM A1008 for steel quality is crucial, especially in regions with specific regulations like the Middle East and Europe.
Why Choose Fiberglass for Tape Measures?
Fiberglass is another popular material, especially for measuring tapes used in construction and landscaping. It is lightweight and flexible, allowing it to be easily coiled and carried.
Pros:
– Flexibility: Fiberglass can bend without breaking, making it ideal for measuring curved surfaces.
– Non-Conductive: It is safe for electrical applications since it does not conduct electricity.
– Weather Resistance: Fiberglass is resistant to moisture and UV light, making it suitable for outdoor use.
Cons:
– Durability: While flexible, fiberglass can be less durable than steel and may wear out faster.
– Cost: Fiberglass tape measures can be more expensive than their steel counterparts.
International buyers should consider compliance with DIN EN 131 standards, particularly in Europe, which ensures that the tape measures meet safety and performance criteria.
What are the Benefits of Using Plastic in Tape Measures?
Plastic is often used in budget-friendly tape measures. It is lightweight and can be molded into various shapes, making it versatile for different designs.
Pros:
– Lightweight: Plastic tape measures are easy to carry and handle.
– Cost-Effective: They are usually cheaper than both steel and fiberglass options.
– Corrosion Resistance: Plastic does not rust or corrode, making it suitable for various environments.
Cons:
– Durability: Plastic is less durable and can break or warp under stress.
– Accuracy: Plastic tape measures may not provide the same level of accuracy as metal options.
For international buyers, ensuring that plastic tape measures comply with relevant safety and material standards is essential, especially in regions like Africa and South America where regulations may vary.
How Does Aluminum Compare as a Material for Tape Measures?
Aluminum is often chosen for its balance between weight and strength. It is lightweight yet offers good durability, making it a suitable alternative to steel.
Pros:
– Lightweight: Aluminum tape measures are easy to handle and transport.
– Corrosion Resistance: They are resistant to rust and corrosion, ideal for various environments.
– Durability: Aluminum can withstand significant wear and tear.
Cons:
– Cost: Aluminum can be more expensive than steel and plastic.
– Flexibility: While more flexible than steel, aluminum may not be as durable under extreme bending.
International buyers should ensure compliance with JIS standards for aluminum products, particularly in regions such as Japan and South Korea, to guarantee quality and safety.
Summary Table of Material Selection for Tape Measures
Material | Typical Use Case for Tape Measure Manufacturer | Key Advantage | Key Disadvantage/Limitation | Relative Cost (Low/Med/High) |
---|---|---|---|---|
Steel | General construction and industrial applications | High durability and accuracy | Heavier and can rust | Medium |
Fiberglass | Landscaping and outdoor measurements | Flexible and weather-resistant | Less durable than steel | High |
Plastic | Budget-friendly consumer tape measures | Lightweight and corrosion-resistant | Less durable and accurate | Low |
Aluminum | Lightweight industrial applications | Good balance of weight and strength | More expensive than steel | Medium |
This guide serves as a strategic resource for international B2B buyers, providing insights into material selection that align with regional standards and application requirements.
In-depth Look: Manufacturing Processes and Quality Assurance for tape measure manufacturer
What are the Main Stages of the Manufacturing Process for Tape Measures?
The manufacturing of tape measures involves a series of precise stages, each critical to ensuring the final product meets the rigorous standards expected in various industries. Below are the primary stages of manufacturing:
-
Material Preparation
The first step involves selecting high-quality materials, typically a blend of steel, fiberglass, or nylon, depending on the intended use of the tape measure. The material is then cut into strips of required widths, which will form the basis of the tape. Proper material preparation ensures durability and accuracy in measurements. -
Forming
In this stage, the prepared material undergoes processes such as stamping or laser cutting to create the tape’s primary structure. For metal tape measures, this often involves rolling the steel into flat strips that can be further shaped. Fiberglass tapes may be molded into specific forms to enhance flexibility and resistance to stretching. -
Assembly
Once the tape is formed, it is assembled with other components such as the casing, locking mechanisms, and hooks. This stage may involve automated machinery for precision or manual labor for more intricate designs. The assembly must ensure that the tape retracts smoothly and that the locking mechanism functions reliably. -
Finishing
The final stage includes polishing, coating, and branding the tape measures. This not only enhances the aesthetic appeal but also adds protective layers against corrosion and wear. Quality finishing processes can significantly impact the longevity of the product in the field.
How is Quality Assurance Integrated into the Manufacturing Process of Tape Measures?
Quality assurance (QA) is a fundamental aspect of the manufacturing process, ensuring that each tape measure produced adheres to international and industry-specific standards. Here’s how quality assurance is typically structured:
-
International Standards Compliance
Many tape measure manufacturers adhere to ISO 9001, which outlines the requirements for a quality management system. Compliance with this standard ensures that manufacturers have established effective processes for quality control, documentation, and continuous improvement. Additionally, specific certifications such as CE marking or API certification may be required for certain markets or applications. -
Quality Control Checkpoints
Quality control is integrated into various stages of the manufacturing process through specific checkpoints:
– Incoming Quality Control (IQC): This involves inspecting raw materials upon receipt to ensure they meet predefined quality standards.
– In-Process Quality Control (IPQC): During manufacturing, various checks are conducted to monitor the quality of the product at different stages, ensuring that deviations are corrected in real-time.
– Final Quality Control (FQC): After assembly and finishing, tape measures undergo rigorous testing to verify that they meet all specifications before being packaged and shipped. -
Common Testing Methods
Manufacturers utilize various testing methods to ensure the accuracy and durability of tape measures:
– Calibration Tests: These tests confirm that the tape measures provide accurate measurements over their entire length.
– Durability Tests: Tape measures are subjected to stress tests to evaluate their resistance to wear and tear, including bending, stretching, and exposure to elements like moisture and temperature changes.
How Can B2B Buyers Verify Supplier Quality Control?
For international B2B buyers, particularly those from Africa, South America, the Middle East, and Europe, verifying a supplier’s quality control processes is crucial. Here are actionable strategies:
-
Supplier Audits
Conducting supplier audits provides firsthand insight into the manufacturing processes and quality control measures in place. Buyers should assess the manufacturing facilities, review production lines, and evaluate the implementation of quality management systems. -
Quality Control Reports
Requesting detailed quality control reports from suppliers can shed light on their testing procedures and results. These reports should outline the methods used, frequency of testing, and compliance with relevant standards. -
Third-Party Inspections
Engaging third-party inspection services offers an unbiased assessment of a supplier’s quality control. These agencies can conduct independent inspections and testing, providing buyers with additional confidence in the supplier’s capabilities.
What are the Quality Control and Certification Nuances for International B2B Buyers?
When sourcing tape measures from international suppliers, buyers must navigate various quality control and certification nuances:
-
Understanding Local Regulations
Different regions may have specific regulations regarding product safety and quality. For instance, CE marking is mandatory for products sold within the European Economic Area, ensuring they meet health, safety, and environmental protection standards. -
Cultural Considerations
Cultural differences can impact the manufacturing and quality assurance processes. Buyers should be aware of these nuances and communicate effectively with suppliers to ensure mutual understanding of quality expectations. -
Establishing Long-Term Relationships
Building strong relationships with suppliers can facilitate better communication regarding quality issues. Engaging in regular discussions about quality metrics, improvement initiatives, and feedback mechanisms can enhance product quality over time.
Conclusion
Understanding the manufacturing processes and quality assurance measures in the tape measure industry is essential for international B2B buyers. By focusing on material preparation, forming, assembly, and finishing, along with rigorous quality control practices, buyers can make informed decisions. Verifying supplier quality through audits, reports, and third-party inspections, as well as being aware of international standards and regional regulations, ensures that the tape measures sourced meet the highest quality standards. This comprehensive approach not only safeguards investments but also enhances the overall supply chain efficiency.
Practical Sourcing Guide: A Step-by-Step Checklist for ‘tape measure manufacturer’
To successfully procure tape measures from manufacturers, international B2B buyers must navigate various crucial steps to ensure they select the right supplier. This checklist serves as a practical guide to streamline your sourcing process and mitigate risks.
Step 1: Define Your Technical Specifications
Clearly articulating your technical requirements is vital in the procurement process. This includes dimensions, materials (e.g., fiberglass, steel), measurement units (imperial vs. metric), and any additional features such as locking mechanisms or digital displays. By specifying these details upfront, you can better communicate your needs to potential manufacturers and avoid misunderstandings.
Step 2: Conduct Market Research
Before reaching out to suppliers, conduct thorough market research to understand the landscape of tape measure manufacturers. Look into various regions, such as Europe and the Middle East, to identify leading suppliers and their product offerings. Utilize online databases, industry reports, and trade shows to gather insights on market trends, pricing, and competitor products.
Step 3: Evaluate Potential Suppliers
Vetting suppliers is crucial to ensure reliability and quality. Request company profiles, including their history, production capacity, and case studies relevant to your industry. Additionally, ask for references from other buyers in similar markets to assess their experiences. Be cautious of relying solely on a supplier’s website; a comprehensive evaluation will provide deeper insights into their credibility.
Step 4: Verify Supplier Certifications
Ensuring that your potential suppliers have the necessary certifications can safeguard your procurement process. Look for ISO certifications, quality management standards, and compliance with local and international regulations. Certifications indicate that the manufacturer adheres to industry best practices, which can enhance product quality and reliability.
Step 5: Request Samples and Conduct Quality Testing
Before placing a bulk order, request samples of the tape measures to evaluate their quality firsthand. Conduct practical tests to assess durability, accuracy, and usability. This step is crucial in verifying that the product meets your specifications and performance expectations.
Step 6: Negotiate Terms and Pricing
Once you’ve selected a suitable supplier, engage in discussions regarding pricing, payment terms, and delivery schedules. Consider the total cost of ownership, which includes shipping, tariffs, and potential customs fees, especially when sourcing from international manufacturers. A clear agreement will help avoid disputes later in the process.
Step 7: Establish a Communication Plan
Effective communication is key to a successful partnership. Set up a clear communication plan with your chosen supplier, outlining points of contact, preferred communication channels, and response timelines. Regular updates on production status, shipping, and any potential issues will foster transparency and collaboration.
By following this checklist, international B2B buyers can navigate the sourcing process for tape measures effectively, ensuring they partner with reliable manufacturers that meet their specific needs.
Comprehensive Cost and Pricing Analysis for tape measure manufacturer Sourcing
When sourcing tape measures, understanding the comprehensive cost structure and pricing dynamics is crucial for international B2B buyers. This analysis delves into the various cost components, price influencers, and actionable buyer tips to facilitate informed purchasing decisions.
What are the Key Cost Components in Tape Measure Manufacturing?
-
Materials: The primary cost driver for tape measures is the raw materials used, such as steel, plastic, or fiberglass. The quality and type of materials directly affect durability and performance. For instance, stainless steel may have a higher upfront cost but offers better longevity.
-
Labor: Labor costs vary significantly based on geographic location and the skill level required for production. In regions like Africa and South America, labor might be cheaper, but the trade-off could be in the skill level, impacting quality.
-
Manufacturing Overhead: This includes costs related to factory operations, utilities, maintenance, and administrative expenses. Efficient manufacturing processes can reduce overhead costs, which is beneficial for maintaining competitive pricing.
-
Tooling: Investment in specialized tools and molds is necessary for producing tape measures, especially for custom designs. Tooling costs can be amortized over larger production volumes, making high-volume orders more cost-effective.
-
Quality Control (QC): Ensuring products meet specified standards is essential, especially for international buyers who may require certifications. QC processes add to the cost but are vital for minimizing returns and maintaining brand reputation.
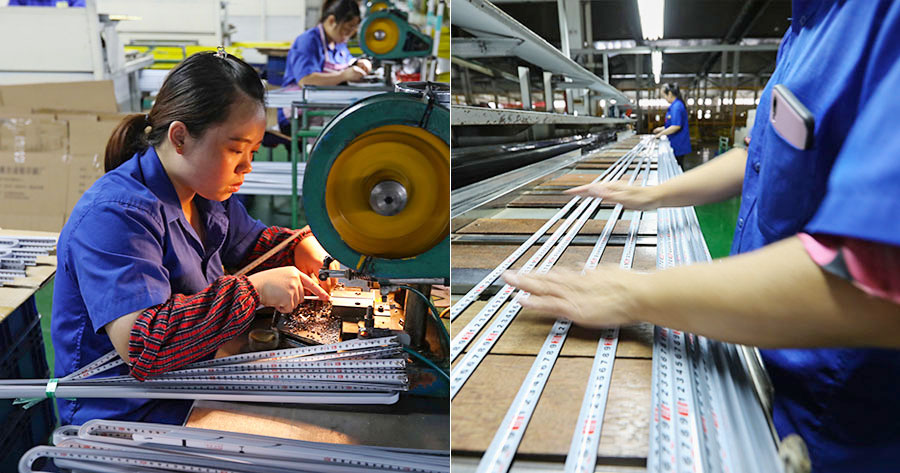
A stock image related to tape measure manufacturer.
-
Logistics: Shipping and handling can significantly impact total costs, particularly for international transactions. Factors such as shipping distance, mode of transportation, and customs duties need to be accounted for.
-
Margin: Manufacturers typically add a profit margin to cover their risks and operational costs. Understanding the average margins in the industry can help buyers gauge price fairness.
How Do Price Influencers Affect Tape Measure Costs?
-
Volume/MOQ (Minimum Order Quantity): Bulk orders often lead to lower per-unit costs. Manufacturers are more likely to offer discounts for larger orders, making it advantageous for buyers to consolidate purchases.
-
Specifications and Customization: Customized tape measures with unique features or branding can incur additional costs. Buyers should clarify their requirements upfront to avoid unexpected pricing changes.
-
Materials and Quality Certifications: Higher quality materials and certifications (like ISO) can raise prices but may be necessary for specific applications or markets. Buyers should weigh the benefits of certification against costs.
-
Supplier Factors: The reliability and reputation of the supplier can influence pricing. Established suppliers may charge more due to their proven track record, while newer entrants might offer lower prices to gain market share.
-
Incoterms: The chosen Incoterms can significantly impact total costs. Understanding terms like FOB (Free on Board) or CIF (Cost, Insurance, and Freight) is essential for calculating the total landed cost.
What Tips Can Help Buyers Negotiate Better Pricing?
-
Conduct Thorough Market Research: Understanding the market landscape and average pricing for tape measures can empower buyers during negotiations. Utilize industry reports and competitor analysis.
-
Evaluate Total Cost of Ownership (TCO): Consider not just the purchase price but the total cost of ownership, including shipping, duties, and potential maintenance. This perspective can help justify higher upfront costs for better-quality products.
-
Leverage Long-Term Relationships: Building strong relationships with suppliers can lead to better pricing and terms over time. Suppliers are often more willing to negotiate with loyal customers.
-
Be Clear About Specifications: Clearly define your needs and specifications to avoid miscommunication that can lead to increased costs. Ensure that all parties are aligned on quality and performance expectations.
-
Explore Alternative Suppliers: Diversifying your supplier base can lead to competitive pricing. Consider sourcing from manufacturers in different regions, like Europe or the Middle East, to compare costs and quality.
Disclaimer on Indicative Prices
It’s important to note that prices can vary widely based on the factors mentioned above, and the figures provided in any pricing discussion should be considered indicative. Always request detailed quotes from multiple suppliers to ensure accurate pricing tailored to your specific needs.
Alternatives Analysis: Comparing tape measure manufacturer With Other Solutions
In the world of measurement tools, tape measures have long been a staple for professionals across various industries. However, as technology evolves, so do the alternatives available to businesses seeking accurate and efficient measurement solutions. This analysis will compare traditional tape measure manufacturers with alternative solutions such as digital measuring devices and laser distance measurers, helping international B2B buyers make informed decisions tailored to their specific needs.
Comparison Table of Measurement Solutions
Comparison Aspect | Tape Measure Manufacturer | Digital Measuring Device | Laser Distance Measurer |
---|---|---|---|
Performance | High accuracy, manual operation | High accuracy, easy-to-read displays | Very high accuracy, quick measurements |
Cost | Low to moderate | Moderate to high | High |
Ease of Implementation | Simple, no training required | Requires basic tech familiarity | Some training needed for optimal use |
Maintenance | Minimal | Moderate, battery changes | Low, occasional calibration |
Best Use Case | General construction, DIY | Interior design, quick measurements | Large spaces, construction, surveying |
What Are the Advantages and Disadvantages of Digital Measuring Devices?
Digital measuring devices offer a modern alternative to traditional tape measures. They typically feature easy-to-read displays and can provide instant measurements with the push of a button. Their accuracy is comparable to that of tape measures, but they come at a moderate to high cost, depending on the model. While these devices are generally user-friendly, they may require users to have some familiarity with technology, which can be a barrier in certain markets, especially in regions where digital literacy varies.
How Do Laser Distance Measurers Compare to Traditional Tape Measures?
Laser distance measurers represent the cutting edge of measurement technology. They provide very high accuracy and can measure distances quickly, making them ideal for large spaces and professional applications such as surveying and construction. However, the cost is significantly higher compared to tape measures, which can deter some buyers. Additionally, while they are relatively easy to use, users may need training to maximize their functionality, especially in terms of understanding features like area and volume calculations.
How Can International B2B Buyers Choose the Right Measurement Solution?
When choosing between a tape measure manufacturer and alternative solutions, B2B buyers should consider several factors. Assess the specific needs of their projects, including the required accuracy, the typical environments in which measurements will be taken, and budget constraints. For example, in regions like South Africa or Saudi Arabia, where construction projects are booming, investing in laser distance measurers may provide a competitive edge despite the higher initial cost. Conversely, for smaller projects or DIY tasks, traditional tape measures may remain the most practical and cost-effective solution.
In conclusion, while tape measures have served as reliable measurement tools for years, alternatives like digital measuring devices and laser distance measurers are worth considering for their advanced features and efficiency. Each solution has its own set of advantages and disadvantages, and the best choice ultimately depends on the specific requirements and context of the buyer’s operations.
Essential Technical Properties and Trade Terminology for tape measure manufacturer
What Are the Essential Technical Properties of Tape Measures?
Understanding the technical properties of tape measures is crucial for B2B buyers, particularly when sourcing from manufacturers. Here are several key specifications to consider:
-
Material Grade
Tape measures are typically made from materials like fiberglass, steel, or nylon. Fiberglass is lightweight and flexible, ideal for measuring curved surfaces, while steel is durable and suited for heavy-duty applications. The choice of material affects durability and accuracy, making it essential for buyers to align material selection with their specific needs. -
Measurement Accuracy
Accuracy is a fundamental property, typically defined by the tolerance level, which indicates how much the actual measurement can deviate from the stated measurement. A common tolerance for tape measures is ±1mm for lengths up to 5 meters. For buyers in precision-dependent industries, understanding this specification ensures that the tape measure meets their quality standards. -
Length and Width
Tape measures come in various lengths, commonly ranging from 3 to 30 meters. The width of the tape can also vary, impacting both the visibility of the markings and the ease of use. Buyers should choose a length that accommodates their typical measuring requirements, ensuring they have the right tool for the job. -
Graduation Marks
Graduation refers to the markings on the tape that indicate measurements. Commonly, these are in metric (millimeters and centimeters) or imperial (inches and feet). The clarity and size of these markings are crucial for usability, especially for industries requiring quick and accurate readings. -
Case Material and Design
The housing of the tape measure can be made from plastic, metal, or rubberized materials. A robust casing protects the tape from damage and wear. Buyers should consider the environment in which the tape measure will be used—construction sites may require more rugged designs than those needed in an office setting. -
Blade Lock Mechanism
A reliable blade lock mechanism ensures that the tape stays extended while measuring. This feature is particularly important in construction and manufacturing, where accurate measurements are critical. Buyers should evaluate different locking mechanisms for ease of use and reliability.
What Trade Terminology Should B2B Buyers Know When Sourcing Tape Measures?
Familiarizing oneself with industry terminology is essential for effective communication with manufacturers and suppliers. Here are several key terms:
-
OEM (Original Equipment Manufacturer)
OEM refers to a company that produces parts or equipment that may be marketed by another manufacturer. In the context of tape measures, buyers may source products from OEMs who specialize in tape measure production, ensuring they receive high-quality products tailored to their specifications. -
MOQ (Minimum Order Quantity)
MOQ is the smallest quantity of a product that a supplier is willing to sell. Understanding MOQ is vital for buyers to manage inventory costs effectively. For tape measures, MOQs can vary significantly based on the manufacturer and the product specifications. -
RFQ (Request for Quotation)
An RFQ is a document sent to suppliers to request pricing and other relevant information for a specific quantity of goods. For tape measure buyers, issuing an RFQ can help compare prices, delivery times, and terms, enabling informed purchasing decisions. -
Incoterms (International Commercial Terms)
Incoterms define the responsibilities of buyers and sellers in international trade, including shipping, insurance, and tariffs. Familiarity with terms like CIF (Cost, Insurance, and Freight) or FOB (Free on Board) can help buyers negotiate better shipping conditions for their tape measures. -
Lead Time
Lead time refers to the time taken from placing an order to receiving the goods. Understanding lead times is crucial for planning and managing projects effectively, especially in industries where timing is critical. -
Certification Standards
Many regions have specific certification requirements for measuring tools, such as ISO standards. Buyers should ensure that the tape measures they source comply with relevant certifications, which can be a mark of quality and reliability in the industry.
By grasping these technical properties and trade terminologies, international B2B buyers can make more informed decisions when sourcing tape measures, ultimately leading to better procurement outcomes.
Navigating Market Dynamics and Sourcing Trends in the tape measure manufacturer Sector
What Are the Current Market Dynamics and Key Trends in the Tape Measure Manufacturing Sector?
The global tape measure manufacturing sector is influenced by various drivers that shape its market dynamics. As construction and DIY projects continue to proliferate, especially in emerging markets in Africa and South America, the demand for reliable and durable measuring tools has surged. In regions like the Middle East, infrastructure development projects are pushing the need for precise measuring instruments. Additionally, advancements in technology are facilitating the integration of digital measuring solutions, which are becoming increasingly popular among B2B buyers seeking enhanced accuracy and efficiency.
Emerging B2B sourcing trends reflect a shift towards digitalization and e-commerce platforms. Buyers are increasingly leveraging online marketplaces to source tape measures, allowing for greater access to international suppliers and competitive pricing. Moreover, the demand for customization is on the rise, as companies look for tape measures tailored to specific applications or industries. This trend is particularly relevant in Europe, where regulations and standards can vary significantly across countries.
Furthermore, sustainability is becoming a critical consideration for B2B buyers. Manufacturers are being urged to adopt eco-friendly practices, such as using recycled materials and reducing waste in production processes. This shift not only aligns with consumer preferences but also helps companies comply with increasingly stringent environmental regulations.
How Is Sustainability and Ethical Sourcing Transforming the Tape Measure Manufacturing Sector?
Sustainability and ethical sourcing are paramount in today’s B2B landscape, particularly in the tape measure manufacturing sector. The environmental impact of production processes is under scrutiny, with buyers increasingly prioritizing suppliers that demonstrate a commitment to reducing their carbon footprint. This includes the use of sustainable materials, such as bioplastics or recycled metals, which not only help in minimizing waste but also appeal to eco-conscious consumers.
Ethical supply chains are equally vital, as buyers seek transparency in sourcing practices. Companies that can provide certifications—such as ISO 14001 for environmental management or Forest Stewardship Council (FSC) certification—are more likely to gain the trust of international buyers. This is particularly important in regions like Africa and South America, where ethical sourcing can significantly influence purchasing decisions.
Moreover, the integration of ‘green’ materials in tape measure manufacturing is becoming a competitive advantage. Suppliers that invest in sustainable technologies and practices are not only contributing to environmental conservation but are also positioning themselves favorably in a market that increasingly values corporate social responsibility.
How Has the Tape Measure Manufacturing Sector Evolved Over Time?
The evolution of the tape measure manufacturing sector reflects broader technological advancements and changes in consumer needs. Initially, tape measures were simple, mechanical devices made of cloth or metal, primarily used by carpenters and builders. The introduction of fiberglass tape measures in the mid-20th century revolutionized the industry, offering flexibility and durability.
In recent years, the rise of digital technology has led to the development of electronic tape measures, which provide digital readouts and memory functions for storing measurements. This evolution has made tape measures not only more user-friendly but also more accurate, catering to the needs of professional users in construction, engineering, and design sectors.
As the industry continues to adapt, international B2B buyers must stay informed about these trends to make educated sourcing decisions that align with their operational needs and sustainability goals.
Frequently Asked Questions (FAQs) for B2B Buyers of tape measure manufacturer
-
How do I choose the right tape measure manufacturer for my business needs?
Choosing the right tape measure manufacturer involves several key factors. Start by identifying your specific requirements, such as the type of tape measure (e.g., steel, fiberglass, or retractable) and any custom features you may need. Research potential manufacturers by checking their certifications, production capabilities, and client testimonials. Additionally, consider their geographic location, as this can affect shipping costs and lead times, especially for international transactions. Finally, request samples to assess the quality of their products before making a commitment. -
What is the best way to verify the reliability of a tape measure manufacturer?
To verify the reliability of a tape measure manufacturer, conduct thorough due diligence. This includes checking their business licenses, ISO certifications, and compliance with international quality standards. Reach out to current and past clients to gather feedback on their experiences. Utilize platforms like LinkedIn or industry forums to gauge the manufacturer’s reputation in the market. If possible, arrange a factory visit or request a third-party audit to ensure their production processes meet your quality expectations.
-
What customization options are typically available when sourcing tape measures?
Most tape measure manufacturers offer a variety of customization options to cater to specific business needs. These may include custom lengths, branding with your logo, special markings or scales (like metric or imperial), and unique casing designs. Some manufacturers can even provide tailored packaging solutions. When discussing customization, clearly outline your requirements and ask for a prototype to ensure the final product meets your expectations. -
What are the typical minimum order quantities (MOQs) for tape measures?
Minimum order quantities (MOQs) for tape measures can vary significantly between manufacturers and depend on factors like customization and production capabilities. Generally, MOQs can range from 500 to 5,000 units. It’s essential to communicate your needs with potential suppliers, as some may offer flexible MOQs for new clients or bulk orders. Be aware that lower MOQs may lead to higher per-unit costs, so evaluate the trade-offs based on your budget and inventory strategy. -
What payment terms should I expect when working with international tape measure suppliers?
Payment terms when sourcing from international tape measure suppliers typically include options like upfront deposits, letters of credit, or payment on delivery. It’s common to pay a 30% deposit upfront, with the remaining balance due upon shipment. Always clarify payment terms before finalizing agreements to avoid misunderstandings. Be cautious of suppliers who demand full payment upfront, as this could indicate a lack of confidence in their product or service delivery.
-
How can I ensure quality assurance when sourcing tape measures internationally?
To ensure quality assurance when sourcing tape measures, implement a robust quality control process. Establish clear specifications and quality standards in your purchase agreement. Request that manufacturers provide samples for testing before bulk production. Consider employing third-party inspection services to conduct quality checks at various stages of production. Additionally, maintain open communication with the supplier throughout the manufacturing process to address any issues promptly. -
What logistics considerations should I keep in mind when importing tape measures?
When importing tape measures, logistics considerations are crucial for timely delivery and cost management. Evaluate shipping options, including air freight for faster delivery or sea freight for cost-effectiveness. Understand the customs regulations and import duties applicable in your country to avoid unexpected fees. Work closely with your supplier to coordinate shipping schedules and ensure proper documentation, such as invoices and packing lists, to facilitate smooth customs clearance. -
What are the common challenges faced by B2B buyers in sourcing tape measures?
B2B buyers often face challenges such as varying quality standards, communication barriers, and the risk of supply chain disruptions when sourcing tape measures. Establishing clear communication channels with suppliers can mitigate misunderstandings. Additionally, varying regulations across countries may impact compliance. To address these challenges, conduct thorough research on potential manufacturers and consider diversifying your supplier base to ensure reliability and quality in your sourcing strategy.
Important Disclaimer & Terms of Use
⚠️ Important Disclaimer
The information provided in this guide, including content regarding manufacturers, technical specifications, and market analysis, is for informational and educational purposes only. It does not constitute professional procurement advice, financial advice, or legal advice.
While we have made every effort to ensure the accuracy and timeliness of the information, we are not responsible for any errors, omissions, or outdated information. Market conditions, company details, and technical standards are subject to change.
B2B buyers must conduct their own independent and thorough due diligence before making any purchasing decisions. This includes contacting suppliers directly, verifying certifications, requesting samples, and seeking professional consultation. The risk of relying on any information in this guide is borne solely by the reader.
Strategic Sourcing Conclusion and Outlook for tape measure manufacturer
As the global demand for high-quality tape measures continues to rise, strategic sourcing emerges as a pivotal component for B2B buyers looking to secure reliable partnerships. Understanding the nuances of supply chain dynamics, particularly in regions like Africa, South America, the Middle East, and Europe, enables buyers to make informed decisions that align with their operational needs.
What Are the Key B2B Takeaways for Sourcing Tape Measures?
-
Prioritize Supplier Reliability: Establish relationships with manufacturers known for their quality assurance and timely delivery. This not only minimizes disruptions but also enhances brand credibility.
-
Leverage Technology in Procurement: Utilize digital tools to streamline sourcing processes, enabling better tracking of orders and inventory management, crucial for maintaining competitiveness in the market.
-
Evaluate Cost vs. Quality: While cost is a significant factor, prioritize quality to ensure product longevity and customer satisfaction, which ultimately leads to repeat business.
How Can International Buyers Benefit from Strategic Sourcing?
Strategic sourcing not only optimizes procurement costs but also strengthens supplier relationships, fostering innovation and adaptability in product offerings. As we look to the future, B2B buyers are encouraged to actively engage in market research and build networks that can support their sourcing strategies. By embracing these practices, companies can navigate challenges and seize opportunities in the evolving global marketplace.
In conclusion, the path forward is clear: invest in strategic sourcing to enhance your supply chain resilience, and position your business for sustainable growth in an increasingly interconnected world.