Discover Reliable Hubs Supplier: Your Ultimate Sourcing Guide (2025)
Introduction: Navigating the Global Market for hubs supplier
In today’s rapidly evolving global marketplace, sourcing reliable hubs suppliers can be a significant challenge for international B2B buyers, particularly those in Africa, South America, the Middle East, and Europe. The complexities of diverse supplier landscapes, varying quality standards, and fluctuating costs make it imperative for businesses to navigate these waters carefully. This guide serves as a comprehensive resource, covering essential aspects such as different types of hubs, their applications across various industries, effective supplier vetting processes, and cost considerations.
By providing in-depth insights into the hubs supplier market, this guide empowers buyers to make informed purchasing decisions. Whether you are looking to source hubs for manufacturing, automotive, or technology applications, understanding the nuances of supplier capabilities and market dynamics is crucial. We delve into strategies for evaluating suppliers, including quality certifications and production capabilities, ensuring that you select partners who align with your business objectives.
Moreover, this guide addresses unique challenges faced by buyers in specific regions, such as navigating import regulations in Egypt or understanding local market demands in Indonesia. Ultimately, our goal is to equip you with the knowledge and tools needed to confidently engage with hubs suppliers, fostering successful and sustainable business relationships across borders.
Understanding hubs supplier Types and Variations
Type Name | Key Distinguishing Features | Primary B2B Applications | Brief Pros & Cons for Buyers |
---|---|---|---|
Local Service Hubs | Focus on community-based services, often flexible and varied | Home services, maintenance, and repairs | Pros: Personalized service, local knowledge. Cons: Limited scalability, variable quality. |
Manufacturing Hubs | Centralized production facilities with diverse capabilities | Prototyping, mass production, and custom orders | Pros: High efficiency, large output. Cons: Long lead times, potential for quality control issues. |
Logistics Hubs | Specialize in warehousing and distribution | Supply chain management, inventory storage | Pros: Streamlined operations, cost-effective shipping. Cons: Dependency on transportation networks, potential delays. |
Digital Hubs | Platforms connecting buyers with service providers online | Freelance services, tech support, consulting | Pros: Access to diverse talent, flexible engagement. Cons: Quality assurance challenges, potential communication barriers. |
Innovation Hubs | Focus on research and development, often collaborative | Product development, R&D partnerships | Pros: Access to cutting-edge technology, collaborative opportunities. Cons: Higher costs, longer timelines. |
What Are the Characteristics of Local Service Hubs?
Local service hubs are characterized by their focus on community-based offerings, providing tailored services such as home maintenance, cleaning, and repairs. These hubs often emphasize flexibility and responsiveness to local needs, making them suitable for businesses looking for personalized service. When purchasing from local service hubs, buyers should consider the provider’s reputation, service offerings, and responsiveness to inquiries.
How Do Manufacturing Hubs Operate?
Manufacturing hubs serve as centralized production facilities that offer a range of manufacturing capabilities from prototyping to mass production. They are particularly beneficial for businesses requiring custom parts or high-volume output. Key purchasing considerations include understanding lead times, production capacity, and quality assurance processes. Buyers should assess whether the hub can meet their specific production needs efficiently.
What Role Do Logistics Hubs Play in Supply Chains?
Logistics hubs are essential for warehousing and distribution, providing businesses with storage solutions and streamlined shipping processes. These hubs enable efficient supply chain management, allowing companies to optimize inventory levels and reduce shipping costs. When engaging with logistics hubs, buyers should evaluate their shipping capabilities, reliability, and how well they integrate with existing supply chain operations.
What Are Digital Hubs and Their Advantages?
Digital hubs are online platforms that connect businesses with a wide range of service providers, including freelancers and consultants. They offer flexibility in engagement and access to diverse talent pools. However, buyers should be cautious about quality assurance and communication challenges inherent in remote work. Evaluating provider reviews and past work can help mitigate these risks.
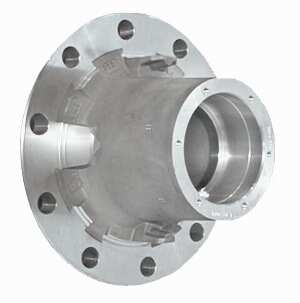
A stock image related to hubs supplier.
Why Are Innovation Hubs Important for B2B Buyers?
Innovation hubs focus on research and development, often fostering collaboration between businesses and academic institutions. They are critical for companies aiming to stay competitive through cutting-edge technology and product development. Buyers should consider the hub’s track record in innovation, funding opportunities, and potential for collaborative projects. However, the costs and timelines associated with R&D can be significant, necessitating careful budgeting and planning.
Related Video: Supplier Type Options in Oracle R12
Key Industrial Applications of hubs supplier
Industry/Sector | Specific Application of hubs supplier | Value/Benefit for the Business | Key Sourcing Considerations for this Application |
---|---|---|---|
Automotive | Supply chain optimization for parts | Streamlined production processes reduce costs and lead times. | Quality assurance, compliance with international standards, and reliability of suppliers. |
Aerospace | Prototyping and custom parts manufacturing | Accelerates design iterations and reduces time-to-market. | Need for precision, adherence to safety regulations, and certification requirements. |
Consumer Electronics | Rapid prototyping for new product launches | Faster innovation cycles and improved competitive advantage. | Material selection, capability for small batch runs, and responsiveness to market changes. |
Medical Devices | Custom components for specialized equipment | Enhanced functionality and compliance with health regulations. | Regulatory compliance, traceability of materials, and supplier reliability. |
Industrial Machinery | Replacement parts and tooling | Minimizes downtime and maintains operational efficiency. | Availability of parts, lead times, and compatibility with existing machinery. |
How Are Hubs Suppliers Used in the Automotive Industry?
In the automotive sector, hubs suppliers play a crucial role in optimizing supply chains for various parts. By providing just-in-time manufacturing and logistics solutions, they help automotive companies reduce inventory costs and minimize lead times. International B2B buyers from regions like Africa and South America should ensure that their suppliers can meet rigorous quality assurance standards and comply with local regulations to avoid costly delays and rework.
What Are the Applications of Hubs Suppliers in Aerospace?
Hubs suppliers are essential for the aerospace industry, particularly in prototyping and manufacturing custom parts. They facilitate rapid design iterations, allowing aerospace companies to test and refine components quickly, which is vital for meeting stringent safety and performance criteria. Buyers must consider the precision of the manufacturing processes and the supplier’s ability to adhere to industry-specific certifications, especially when sourcing from Europe or the Middle East.
How Do Hubs Suppliers Impact Consumer Electronics?
In the consumer electronics sector, hubs suppliers enable rapid prototyping for new product launches. This capability helps companies innovate faster and maintain a competitive edge in a rapidly changing market. For international buyers, particularly in emerging markets, it is crucial to assess suppliers’ material options and their ability to handle small batch production effectively, ensuring they can respond swiftly to market demands.
What Role Do Hubs Suppliers Play in Medical Devices?
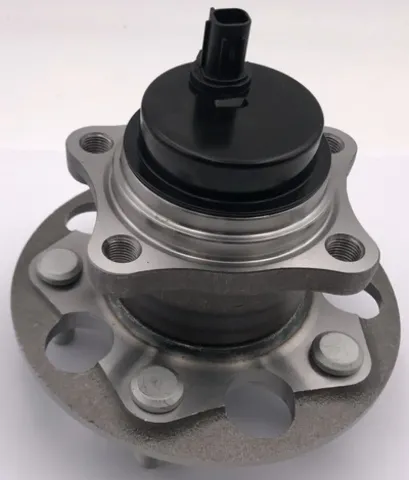
A stock image related to hubs supplier.
Hubs suppliers are vital in the medical device industry, providing custom components that meet specific regulatory and functional requirements. By ensuring that products are compliant with health regulations, these suppliers help medical device manufacturers enhance their offerings. Buyers should prioritize suppliers who can demonstrate traceability of materials and reliability, as these factors are critical in maintaining compliance and ensuring patient safety.
How Are Hubs Suppliers Utilized in Industrial Machinery?
In the industrial machinery sector, hubs suppliers are relied upon for replacement parts and tooling. Their ability to provide high-quality components minimizes downtime and helps maintain operational efficiency in manufacturing processes. International buyers should focus on suppliers’ availability of parts, lead times, and the compatibility of components with existing machinery to ensure seamless integration and continued productivity.
Related Video: Top 5 Industrial Robots you must see
3 Common User Pain Points for ‘hubs supplier’ & Their Solutions
Scenario 1: Navigating Quality Control Challenges in Hubs Supply
The Problem: B2B buyers often face significant challenges related to quality control when sourcing hubs from suppliers. This issue can stem from varying production standards across different regions, leading to inconsistencies in product quality. For example, a manufacturer in South America may have different quality assurance protocols compared to a supplier in Europe. This discrepancy can result in receiving defective products, which can compromise the integrity of the entire project and lead to costly delays.
The Solution: To mitigate quality control issues, B2B buyers should prioritize suppliers who adhere to internationally recognized quality standards, such as ISO certifications. Before committing to a supplier, buyers should request detailed information about their quality assurance processes, including inspection methods and frequency. Establishing clear communication channels with the supplier can also facilitate real-time updates and feedback on production quality. Additionally, conducting periodic audits or site visits to the manufacturing facility can provide firsthand insight into the supplier’s production capabilities and quality control measures. By taking these proactive steps, buyers can ensure they are sourcing high-quality hubs that meet their specifications.
Scenario 2: Overcoming Supply Chain Disruptions for Timely Delivery
The Problem: Supply chain disruptions are a common pain point for B2B buyers, particularly when dealing with international suppliers. Factors such as political instability, transportation delays, or unexpected demand surges can significantly impact delivery schedules. For instance, a company in Africa relying on a European supplier may experience extended lead times due to logistical challenges, resulting in project delays and increased costs.
The Solution: To counteract potential supply chain disruptions, B2B buyers should develop a diversified supplier network. Engaging multiple suppliers across different regions can reduce reliance on a single source and enhance resilience against disruptions. Buyers should also implement a robust inventory management system that allows for real-time tracking of orders and stock levels. Establishing strong relationships with logistics partners can also facilitate smoother transportation processes. Additionally, buyers can negotiate flexible contracts with suppliers that include contingency plans for delays, ensuring that they have alternative solutions in place. By adopting these strategies, buyers can better manage their supply chain risks and maintain timely delivery of hubs.
Scenario 3: Addressing Cost Variability in Hubs Procurement
The Problem: Cost variability is another significant challenge faced by B2B buyers when procuring hubs from suppliers. Fluctuating material prices, currency exchange rates, and varying supplier pricing structures can lead to unexpected costs, complicating budget planning. For example, a buyer in the Middle East may find that the price of hubs has increased unexpectedly due to changes in raw material costs, impacting their overall project budget.
The Solution: To tackle cost variability, buyers should engage in thorough market research to understand pricing trends and factors influencing hub costs. Establishing long-term contracts with suppliers can also help lock in prices and provide budget stability. Buyers should consider implementing a transparent pricing model with suppliers, where all cost components are clearly outlined and understood. Additionally, leveraging technology, such as procurement software, can help buyers track market prices and identify the best purchasing opportunities. By taking these steps, buyers can better anticipate costs and create a more reliable budgeting framework for their projects.
Strategic Material Selection Guide for hubs supplier
What Are the Key Properties of Common Materials Used by Hubs Suppliers?
When selecting materials for hubs, it’s essential to understand their properties and how they align with the intended application. Here are four common materials used in hub manufacturing, analyzed from a B2B perspective.
1. Aluminum: A Lightweight Champion
Aluminum is widely used in hub manufacturing due to its excellent strength-to-weight ratio. It typically exhibits a temperature rating of up to 150°C and is resistant to corrosion, making it suitable for various environments.
Pros:
– Lightweight, which improves efficiency in applications requiring mobility.
– Good corrosion resistance, particularly when anodized.
– Easier to machine compared to other metals, reducing manufacturing complexity.
Cons:
– Lower strength compared to steel, which may limit its use in heavy-duty applications.
– Can be more expensive than other materials like plastic or steel.
Impact on Application:
Aluminum hubs are ideal for applications involving moderate loads and where weight savings are critical, such as in automotive and aerospace industries.
Considerations for International Buyers:
Buyers from regions like Africa and South America should ensure compliance with international standards such as ASTM B221 for aluminum extrusions. Additionally, local sourcing may affect cost and availability.
2. Steel: The Durable Workhorse
Steel is renowned for its durability and strength, with temperature ratings often exceeding 300°C. It offers excellent resistance to wear and tear, making it a preferred choice for heavy-duty applications.
Pros:
– Exceptional strength and durability, suitable for high-load applications.
– Cost-effective compared to other metals, especially in bulk orders.
– Wide availability and variety of grades.
Cons:
– Heavier than aluminum, which may not be suitable for lightweight applications.
– Prone to rusting if not properly treated or coated.
Impact on Application:
Steel hubs are ideal for industrial machinery and automotive applications where strength and durability are paramount.
Considerations for International Buyers:
Compliance with standards such as ASTM A36 for structural steel is crucial. Buyers in Europe should consider EN standards for additional quality assurance.
3. Plastic: The Versatile Alternative
Plastic materials, such as polycarbonate or nylon, are increasingly used in hub applications due to their lightweight and corrosion-resistant properties. They can withstand temperatures up to 100°C.
Pros:
– Lightweight and easy to mold into complex shapes, reducing manufacturing time.
– Corrosion-resistant and suitable for environments with moisture.
– Generally lower cost compared to metals.
Cons:
– Lower strength compared to metals, which may limit their use in high-load applications.
– Susceptible to UV degradation unless treated.
Impact on Application:
Plastic hubs are suitable for applications in consumer products and light machinery where weight and corrosion resistance are prioritized.
Considerations for International Buyers:
Buyers should ensure compliance with standards like ASTM D638 for tensile properties. In regions like the Middle East, UV resistance may be a critical factor due to high sunlight exposure.
4. Composite Materials: The Future of Hubs
Composite materials, such as carbon fiber reinforced polymers, offer high strength-to-weight ratios and excellent corrosion resistance. They can operate effectively in temperatures up to 200°C.
Pros:
– Extremely lightweight and strong, ideal for high-performance applications.
– Excellent resistance to environmental factors, including chemicals and moisture.
– Customizable properties based on specific application needs.
Cons:
– Higher manufacturing costs and complexity, which may deter budget-conscious buyers.
– Limited availability in some regions, affecting lead times.
Impact on Application:
Composite hubs are ideal for aerospace and high-performance automotive applications where weight and strength are critical.
Considerations for International Buyers:
Buyers should verify compliance with industry-specific standards and consider local manufacturing capabilities to ensure timely delivery.
Summary Table of Material Selection for Hubs Suppliers
Material | Typical Use Case for hubs supplier | Key Advantage | Key Disadvantage/Limitation | Relative Cost (Low/Med/High) |
---|---|---|---|---|
Aluminum | Automotive and aerospace hubs | Lightweight and corrosion-resistant | Lower strength than steel | Medium |
Steel | Industrial machinery hubs | Exceptional strength and durability | Heavier and prone to rust | Low |
Plastic | Consumer products and light machinery | Lightweight and cost-effective | Lower strength and UV degradation | Low |
Composite | Aerospace and high-performance automotive | High strength-to-weight ratio | Higher cost and manufacturing complexity | High |
This guide provides a comprehensive overview of materials used in hub manufacturing, enabling international B2B buyers to make informed decisions based on their specific needs and regional considerations.
In-depth Look: Manufacturing Processes and Quality Assurance for hubs supplier
What Are the Main Stages of Manufacturing Processes for Hubs Suppliers?
Understanding the manufacturing processes for hubs is crucial for international B2B buyers, particularly those from diverse markets such as Africa, South America, the Middle East, and Europe. The manufacturing of hubs typically involves several key stages, each integral to ensuring the final product meets quality and performance standards.
1. Material Preparation
The first step in the manufacturing process is material preparation. The selection of appropriate materials, such as aluminum, steel, or composite materials, is critical as it affects the durability and performance of the hubs. Suppliers often source materials from certified vendors to ensure quality. Additionally, materials undergo inspections to confirm they meet specific industry standards before being processed further.
2. Forming Techniques
Forming techniques vary based on the design and intended use of the hubs. Common methods include:
- Casting: This involves pouring molten metal into a mold to create the hub shape. It’s suitable for complex designs and large quantities.
- Machining: Precision machining processes, such as CNC machining, are used to create detailed features and tight tolerances.
- Forging: This method enhances the strength of the material by shaping it under high pressure, making it ideal for high-performance applications.
Each technique has its advantages and is selected based on the specific requirements of the hub design.
3. Assembly
Once the components are formed, the next stage is assembly. This may involve welding, fastening, or bonding different parts together to create the final hub product. Suppliers often utilize automated assembly lines for consistency and efficiency, but skilled labor is also essential for complex assemblies. Proper assembly techniques are vital to ensure that the hubs perform reliably under operational stresses.
4. Finishing Processes
The finishing stage encompasses several processes that enhance the appearance and performance of the hubs. Techniques such as anodizing, plating, and painting not only provide aesthetic appeal but also improve corrosion resistance and wear properties. Quality suppliers typically conduct surface inspections to ensure that finishing meets the required specifications.
How Is Quality Assurance Implemented in Hub Manufacturing?
Quality assurance (QA) is a critical aspect of the manufacturing process for hubs. It ensures that products are consistent and meet the standards expected by international B2B buyers.
Relevant International Standards for Quality Assurance
Suppliers typically adhere to several international quality standards, including:
- ISO 9001: This standard outlines the criteria for a quality management system (QMS) and is applicable to any organization. It ensures consistent quality in manufacturing processes.
- CE Marking: Particularly relevant for products sold within the European Economic Area, CE marking indicates conformity with health, safety, and environmental protection standards.
- API Standards: For hubs used in the oil and gas industry, adherence to American Petroleum Institute (API) standards is crucial for ensuring product reliability and safety.
These standards help B2B buyers assess the credibility and quality commitment of their suppliers.
What Are the Key Quality Control Checkpoints in Hub Manufacturing?
Quality control (QC) involves systematic checks at various stages of the manufacturing process. Here are the main checkpoints:
- Incoming Quality Control (IQC): This involves inspecting raw materials upon arrival at the facility to ensure they meet specified requirements.
- In-Process Quality Control (IPQC): During manufacturing, checks are performed to monitor process parameters and product specifications to catch any deviations early.
- Final Quality Control (FQC): After the hubs are completed, a thorough inspection is conducted to ensure they meet all specifications before shipment.
Each checkpoint is vital for maintaining quality throughout the manufacturing process.
What Testing Methods Are Commonly Used in Hub Manufacturing?
Testing methods vary but generally include:
- Dimensional Inspection: Utilizes tools such as calipers and gauges to measure the physical dimensions of the hubs against specifications.
- Material Testing: Conducted to ensure the material properties meet required standards, including tensile strength and hardness tests.
- Functional Testing: Involves testing the hubs under operational conditions to assess performance and reliability.
These testing methods provide B2B buyers with confidence in the quality and durability of the hubs.
How Can International B2B Buyers Verify Supplier Quality Control?
For international B2B buyers, verifying the quality control processes of suppliers is essential to ensure product reliability. Here are some effective strategies:
Conducting Supplier Audits
Regular audits of suppliers can help buyers assess compliance with quality standards and identify areas for improvement. Audits can be performed by the buyer’s quality team or by third-party inspection agencies, providing an objective evaluation of the supplier’s processes.
Reviewing Quality Control Reports
Requesting detailed quality control reports from suppliers can offer insights into their QC processes. Reports should include data on inspection results, non-conformities, and corrective actions taken, which help in assessing the supplier’s commitment to quality.
Utilizing Third-Party Inspection Services
Engaging third-party inspection services can provide an additional layer of assurance. These services can conduct inspections at various stages of the manufacturing process, ensuring that products meet specified standards before shipment.
What Are the Quality Control Nuances for B2B Buyers in Different Regions?
International B2B buyers, especially from diverse regions such as Africa, South America, the Middle East, and Europe, should be aware of specific nuances in quality control:
- Cultural Differences: Understanding local manufacturing practices and business ethics is essential, as these can affect quality standards and expectations.
- Regulatory Compliance: Different regions may have varying regulatory requirements. Buyers should familiarize themselves with local laws and standards applicable to their products.
- Supply Chain Complexity: Buyers should consider the complexities of global supply chains, including potential delays and quality variations that may arise from sourcing materials from different regions.
By understanding these nuances, B2B buyers can make more informed decisions when selecting hub suppliers and ensure a successful partnership.
Practical Sourcing Guide: A Step-by-Step Checklist for ‘hubs supplier’
Introduction
When sourcing a reliable hubs supplier, international B2B buyers must navigate a complex landscape of options. This practical sourcing guide provides a step-by-step checklist to ensure you make informed decisions that align with your operational needs and strategic goals. By following these steps, you can identify, evaluate, and engage with suppliers who can meet your requirements effectively.
Step 1: Define Your Technical Specifications
Before reaching out to suppliers, clearly outline your technical needs. This includes the types of hubs you require, materials, sizes, and any specific functionalities. A well-defined specification helps suppliers understand your requirements and provides a basis for accurate quotes.
- Consider application: Identify the intended use of the hubs to ensure compatibility with existing systems.
- Detail quality standards: Specify any industry standards or certifications necessary for your projects.
Step 2: Research Potential Suppliers
Conduct thorough research to compile a list of potential suppliers that specialize in hubs manufacturing. Utilize online directories, industry forums, and trade shows to find reputable companies.
- Look for experience: Prioritize suppliers with a proven track record in your industry, especially those familiar with international standards.
- Check reviews and testimonials: Explore feedback from previous clients to gauge reliability and service quality.
Step 3: Evaluate Supplier Certifications
It is crucial to verify the certifications of potential suppliers to ensure they adhere to quality standards. Look for ISO certifications or other relevant industry certifications that indicate a commitment to quality and safety.
- Request documentation: Ask suppliers to provide copies of their certifications and any compliance records.
- Assess quality control processes: Understand their quality assurance measures to ensure consistent product quality.
Step 4: Request and Compare Quotes
Once you have shortlisted suppliers, request detailed quotes that outline pricing, lead times, and terms of service. Comparing these quotes will help you assess the best value for your investment.
- Analyze total cost of ownership: Consider not just the price, but also shipping costs, duties, and potential delays.
- Negotiate terms: Don’t hesitate to negotiate terms, including payment schedules and delivery timelines to find a mutually beneficial agreement.
Step 5: Conduct Site Visits or Virtual Tours
If feasible, visiting the supplier’s facility can provide invaluable insights into their operations. If an in-person visit isn’t possible, request a virtual tour to understand their manufacturing capabilities.
- Observe production processes: This helps you evaluate their technology, workforce, and overall production environment.
- Assess infrastructure: Look for signs of efficient operations, such as inventory management and quality control areas.
Step 6: Finalize Contracts and Agreements
Once you have selected a supplier, ensure all terms are clearly outlined in a formal contract. This should include specifications, pricing, delivery schedules, and liability clauses.
- Consult legal experts: It’s advisable to have a legal professional review the contract to safeguard your interests.
- Establish communication protocols: Define how you will communicate with the supplier throughout the contract duration to ensure smooth collaboration.
Step 7: Establish a Relationship for Future Sourcing
Building a strong relationship with your hubs supplier can lead to better service and pricing in the future. Regular communication and feedback can help both parties understand each other’s needs and expectations.
- Schedule regular check-ins: This fosters a collaborative environment and keeps both parties aligned.
- Encourage feedback: Ask for input on your processes and offer your own to improve efficiency and service quality.
By following this step-by-step checklist, international B2B buyers can confidently source hubs suppliers that meet their specific needs and ensure a successful procurement process.
Comprehensive Cost and Pricing Analysis for hubs supplier Sourcing
What Are the Key Cost Components in Hubs Supplier Sourcing?
When sourcing hubs from suppliers, understanding the cost structure is critical for international B2B buyers. The primary cost components include:
-
Materials: The cost of raw materials varies significantly based on type, quality, and sourcing location. High-quality materials tend to increase costs but can enhance durability and performance.
-
Labor: Labor costs can vary widely depending on the supplier’s location. Countries with lower labor costs might provide cheaper rates, but this can impact the quality of craftsmanship and expertise.
-
Manufacturing Overhead: This includes indirect costs such as utilities, facility maintenance, and administrative expenses. A supplier with efficient overhead management can offer more competitive pricing.
-
Tooling: Specialized tooling for manufacturing hubs can be a significant upfront cost. Buyers should consider whether the supplier’s tooling is state-of-the-art or outdated, as this affects production efficiency.
-
Quality Control (QC): Rigorous QC processes ensure that products meet specifications and standards. Suppliers with robust QC protocols may charge higher prices, but they also reduce the risk of defects.
-
Logistics: Shipping and handling costs vary based on distance, shipping method, and the complexity of customs clearance. Understanding Incoterms is essential to gauge who bears these costs.
-
Margin: Suppliers add a profit margin on top of the costs outlined above. This can vary based on the supplier’s market position and competitive landscape.
How Do Price Influencers Affect Hubs Supplier Costs?
Several factors influence pricing in the hubs supply chain:
-
Volume/MOQ: Higher order volumes can lead to discounts. Buyers should negotiate minimum order quantities (MOQ) that align with their needs while ensuring cost-effectiveness.
-
Specifications/Customization: Custom hubs tailored to specific requirements often incur additional costs. Buyers should assess whether customization is essential for their application or if standard options suffice.
-
Materials: The choice of materials not only affects performance but also pricing. Buyers should weigh the benefits of premium materials against budget constraints.
-
Quality and Certifications: Suppliers with ISO certifications or industry-specific qualifications may charge more due to their adherence to quality standards. This investment can lead to long-term savings by reducing failure rates.
-
Supplier Factors: Supplier reputation, location, and reliability impact pricing. Established suppliers with proven track records may command higher prices but offer better service and reliability.
-
Incoterms: Understanding Incoterms such as FOB (Free On Board) and CIF (Cost, Insurance, and Freight) is crucial. These terms dictate responsibility for shipping costs and risks, affecting the total landed cost.
What Tips Can Buyers Use to Negotiate Better Prices?
International buyers from Africa, South America, the Middle East, and Europe can utilize several strategies to negotiate favorable terms:
-
Conduct a Total Cost of Ownership (TCO) Analysis: Evaluate all costs associated with the product, including maintenance and potential failures. This helps in understanding the long-term value rather than focusing solely on the upfront price.
-
Leverage Volume Discounts: If possible, consolidate orders to meet MOQ requirements. This can reduce per-unit costs significantly.
-
Build Relationships: Establishing a good relationship with suppliers can lead to better pricing and priority service. Regular communication can also yield insights into future cost-saving opportunities.
-
Be Flexible with Specifications: If standard products can fulfill the requirement, consider opting for them instead of customized solutions. This can often lead to significant savings.
-
Understand Regional Market Dynamics: Familiarize yourself with the local market conditions in the supplier’s country. This knowledge can be leveraged during negotiations to ensure fair pricing.
Disclaimer on Indicative Prices
It’s important to note that prices can fluctuate based on market conditions, currency exchange rates, and other external factors. Therefore, always seek updated quotes from multiple suppliers before making purchasing decisions. By understanding the cost structure and price influencers, B2B buyers can make informed decisions that align with their operational budgets and strategic objectives.
Alternatives Analysis: Comparing hubs supplier With Other Solutions
In the competitive landscape of B2B supply solutions, it is essential for international buyers to consider various alternatives to ‘hubs supplier.’ By evaluating different options, businesses can ensure they choose the most effective solution tailored to their specific needs. Below is a comparison of ‘hubs supplier’ against two viable alternatives: traditional distributors and digital marketplace platforms.
Comparison Aspect | Hubs Supplier | Traditional Distributor | Digital Marketplace Platform |
---|---|---|---|
Performance | High flexibility with rapid response | Moderate, often slower due to inventory | Variable, depends on seller reliability |
Cost | Competitive pricing, often lower | Can be higher due to overhead costs | Variable pricing, often includes fees |
Ease of Implementation | User-friendly interface | Established processes, but may require contracts | Easy to set up, but quality varies |
Maintenance | Minimal, mostly software updates | Ongoing relationship management required | Limited, but requires monitoring of sellers |
Best Use Case | Quick access to localized suppliers | Bulk orders and long-term contracts | Small to medium orders with varied suppliers |
What Are the Advantages and Disadvantages of Traditional Distributors?
Traditional distributors serve as intermediaries between manufacturers and end-users, providing a reliable supply chain. They often hold significant inventory, allowing for quicker delivery times for bulk orders. However, the cost structure can be higher due to operational overheads, and their performance may suffer due to slower response times in a fast-moving market. This makes them suitable for businesses requiring consistency and bulk purchasing but may not be ideal for those needing flexibility and speed.
How Do Digital Marketplace Platforms Compare?
Digital marketplace platforms offer a different approach, facilitating direct transactions between buyers and sellers. They provide a wide range of options, allowing buyers to compare prices and services from various suppliers. While this can lead to cost savings and increased choice, the quality of products and reliability of sellers can vary significantly. Buyers need to invest time in vetting suppliers and may face challenges with customer service and support. This method is particularly beneficial for small to medium-sized orders where flexibility and a broad range of options are needed.
How Can International B2B Buyers Choose the Right Solution?
When selecting the appropriate solution, international B2B buyers should assess their specific operational needs, budget constraints, and urgency for supply. If flexibility and rapid sourcing are critical, ‘hubs supplier’ may be the best fit. Conversely, if a company requires bulk purchases with a consistent supply, traditional distributors might be more suitable. For those seeking a diverse range of suppliers and competitive pricing, digital marketplace platforms could be the ideal choice. Ultimately, the decision should align with the company’s strategic goals and supply chain requirements.
Essential Technical Properties and Trade Terminology for hubs supplier
What Are the Key Technical Properties for Hubs Suppliers?
When sourcing hubs from suppliers, understanding the essential technical properties is crucial for ensuring product quality and compatibility with your specific needs. Here are several critical specifications to consider:
1. Material Grade
Material grade refers to the specific classification of materials based on their composition and properties. Common materials for hubs include aluminum, steel, and composite materials. The choice of material affects the hub’s strength, weight, and corrosion resistance. For example, aluminum hubs are lightweight and resistant to corrosion, making them suitable for automotive applications, while steel hubs offer greater strength for heavy-duty use. Buyers should assess the material grade to ensure it meets their operational requirements.
2. Tolerance
Tolerance specifies the permissible limit of variation in a physical dimension of the hub. It is expressed as a range (e.g., ±0.01 mm) and is critical for ensuring the proper fit within mechanical assemblies. Tight tolerances are essential in precision applications, such as aerospace and automotive sectors, where even minor discrepancies can lead to failure or performance issues. Understanding tolerance levels helps buyers select suppliers capable of meeting their precision requirements.
3. Load Capacity
Load capacity defines the maximum load a hub can support during operation. It is vital for applications in various industries, from automotive to industrial machinery. Buyers should consider the expected load during operation and select a hub that can safely accommodate it, thereby preventing premature failure and ensuring safety.
4. Surface Finish
Surface finish refers to the texture and smoothness of the hub’s surface, which can affect both aesthetics and performance. Common finishes include anodizing, plating, and polishing. A well-finished surface can enhance corrosion resistance and reduce friction in mechanical assemblies. Buyers should consider the environmental conditions the hub will face and select an appropriate surface finish that enhances longevity and performance.
5. Dimensional Specifications
Dimensional specifications encompass the overall size and shape of the hub, including diameter, height, and design features like bolt holes or grooves. These dimensions must align with the requirements of the assembly in which the hub will be used. Buyers must ensure compatibility with existing systems to avoid costly modifications or replacements.
6. Weight
Weight is an important consideration, especially in applications where reducing mass is crucial for efficiency, such as in aerospace or automotive industries. Lighter hubs can lead to improved fuel efficiency and performance. When evaluating suppliers, buyers should consider the weight of the hub relative to the required strength and durability.
Which Trade Terms Are Essential for B2B Transactions with Hubs Suppliers?
Familiarizing yourself with common trade terminology can significantly enhance communication and negotiation with suppliers. Here are several key terms to know:
1. OEM (Original Equipment Manufacturer)
OEM refers to a company that produces parts or equipment that may be marketed by another manufacturer. In the context of hubs, an OEM supplier provides components that are integral to a larger product. Understanding OEM relationships can help buyers identify reliable sources for high-quality components.
2. MOQ (Minimum Order Quantity)
MOQ is the minimum quantity of a product that a supplier is willing to sell. This term is crucial for budget-conscious buyers, as it directly impacts inventory management and cash flow. Knowing the MOQ helps buyers plan their purchases and avoid overstocking or stockouts.
3. RFQ (Request for Quotation)
An RFQ is a formal document sent to suppliers requesting a quote for specific products or services. It outlines the buyer’s requirements and allows suppliers to provide pricing and terms. Utilizing RFQs can streamline the sourcing process and ensure competitive pricing.
4. Incoterms (International Commercial Terms)
Incoterms are a set of standardized trade terms that define the responsibilities of buyers and sellers regarding shipping, risk, and insurance. Familiarity with these terms helps buyers understand their obligations and rights in international transactions, facilitating smoother logistics and cost management.
5. Lead Time
Lead time refers to the amount of time it takes from placing an order until the product is delivered. This term is critical for project planning and inventory control. Buyers should discuss lead times with suppliers to ensure that their timelines align with production schedules.
6. Quality Assurance
Quality assurance encompasses the processes and procedures that ensure a product meets specified standards and requirements. For hubs, this may involve inspections, testing, and certifications. Buyers should inquire about the quality assurance measures employed by suppliers to guarantee product reliability and performance.
Understanding these technical properties and trade terms will empower B2B buyers to make informed decisions when sourcing hubs, ultimately leading to better product quality and improved supplier relationships.
Navigating Market Dynamics and Sourcing Trends in the hubs supplier Sector
What Are the Current Market Dynamics and Key Trends in the Hubs Supplier Sector?
The global hubs supplier market is experiencing significant transformation driven by technological advancements, shifting consumer preferences, and the increasing demand for efficient supply chains. Key drivers include the rise of digital platforms that enhance connectivity between suppliers and buyers, enabling more streamlined sourcing processes. For international B2B buyers, particularly those in Africa, South America, the Middle East, and Europe, understanding these dynamics is crucial.
Emerging trends such as the adoption of Industry 4.0 technologies—like IoT, AI, and automation—are reshaping the landscape of hubs supply. These technologies not only improve operational efficiency but also facilitate real-time tracking and transparency in sourcing. Buyers should leverage data analytics to gain insights into supplier performance and market conditions, enabling informed decision-making.
Additionally, globalization continues to play a pivotal role in market dynamics. As companies seek to expand their reach, they are increasingly sourcing from diverse regions. This trend presents opportunities for buyers in emerging markets to access a wider range of suppliers and competitive pricing. However, it also necessitates a robust understanding of local regulations, cultural nuances, and logistical challenges to ensure successful international transactions.
How Does Sustainability and Ethical Sourcing Impact the Hubs Supplier Sector?
In today’s environmentally conscious marketplace, sustainability and ethical sourcing have become paramount for B2B buyers in the hubs supplier sector. The environmental impact of sourcing practices is under scrutiny, with stakeholders demanding greater accountability from suppliers. Buyers should prioritize suppliers that demonstrate a commitment to sustainable practices, such as reducing carbon footprints and minimizing waste.
The importance of ethical supply chains cannot be overstated. Consumers and businesses alike are increasingly favoring suppliers that uphold ethical standards, including fair labor practices and responsible sourcing of materials. Buyers should seek out certifications that indicate compliance with sustainability standards, such as ISO 14001 or Fair Trade certifications. These certifications not only enhance a supplier’s credibility but also align with the corporate social responsibility goals of many organizations.
Moreover, the use of ‘green’ materials is gaining traction. Suppliers offering eco-friendly options—such as biodegradable materials or recycled components—can provide a competitive edge in the marketplace. By sourcing from suppliers that adhere to sustainable practices, international B2B buyers can not only meet regulatory requirements but also improve their brand reputation and appeal to a growing segment of environmentally conscious consumers.
What Is the Brief Evolution of the Hubs Supplier Sector?
The hubs supplier sector has evolved significantly over the past few decades, transitioning from traditional supply chains to more integrated, technology-driven models. Initially, suppliers operated in silos, focusing on localized markets. However, globalization and advancements in technology have prompted a shift towards a more interconnected approach.
The rise of e-commerce and digital platforms has accelerated this evolution, allowing suppliers to reach international buyers more efficiently. Additionally, the increasing emphasis on sustainability and ethical practices has transformed the sector, leading to a demand for transparency and accountability in sourcing.
As the industry continues to adapt, the focus on innovation and sustainability will likely shape its future trajectory. International B2B buyers must stay informed about these changes to navigate the complexities of sourcing effectively and to leverage emerging opportunities in the hubs supplier market.
Frequently Asked Questions (FAQs) for B2B Buyers of hubs supplier
-
How do I choose the right hubs supplier for my business needs?
Choosing the right hubs supplier involves evaluating several key factors. Start by assessing the supplier’s industry experience and reputation, particularly in your region (Africa, South America, the Middle East, or Europe). Check for certifications and quality standards they adhere to, as these can indicate reliability. Additionally, consider their product range and customization options, ensuring they can meet your specific requirements. Engaging in direct communication to discuss your needs and expectations can also help gauge their responsiveness and customer service quality. -
What are the minimum order quantities (MOQ) for hubs from suppliers?
Minimum order quantities (MOQ) can vary widely among hubs suppliers based on their production capabilities and business model. Some suppliers may offer low MOQs for prototypes or small batch orders, while others might require larger quantities for cost efficiency. It’s essential to inquire about MOQs before placing an order, especially if you’re a smaller business or starting a new project. Understanding the MOQ will help you plan your inventory and budget effectively. -
How can I ensure quality assurance when sourcing hubs suppliers?
To ensure quality assurance when sourcing hubs suppliers, start by requesting samples of their products to assess material quality and craftsmanship. Look for suppliers with established quality management systems, such as ISO certifications, which indicate adherence to international quality standards. Additionally, consider conducting factory audits or third-party inspections to verify manufacturing processes. Building a strong relationship with your supplier can also facilitate better communication regarding quality expectations and improvements. -
What customization options are typically available from hubs suppliers?
Most hubs suppliers offer a range of customization options to cater to specific business needs. This may include variations in size, material, color, and design features tailored to your application. When discussing customization, provide detailed specifications and requirements to the supplier. Some may also offer design assistance or prototyping services to help you refine your product before full-scale production. Always confirm the lead times and costs associated with customization to align with your project timeline and budget. -
What payment terms should I expect when dealing with hubs suppliers?
Payment terms can vary significantly between hubs suppliers, depending on their policies and your relationship with them. Common practices include advance payments, net terms (e.g., net 30 or net 60), and payment upon delivery. For international transactions, be aware of currency exchange rates and potential transaction fees. Always negotiate terms that suit your cash flow requirements, and consider using secure payment methods such as letters of credit or escrow services for larger orders to mitigate risk.
-
How do logistics and shipping work for international orders of hubs?
Logistics and shipping for international orders typically involve several key steps. After confirming your order with the supplier, they will prepare the goods for shipment, which may include packaging and labeling according to international standards. You must decide on shipping methods (air, sea, or land) based on cost, speed, and reliability. Ensure that the supplier provides all necessary documentation for customs clearance. It’s advisable to work with a freight forwarder who can assist with logistics management and ensure compliance with import regulations in your country. -
What are the common challenges in sourcing hubs suppliers internationally?
Sourcing hubs suppliers internationally can present various challenges, including language barriers, cultural differences, and varying regulations. Additionally, managing time zone differences can complicate communication and project timelines. Quality control can also be a concern, as it may be harder to oversee production processes from afar. To mitigate these challenges, establish clear communication channels, utilize technology for real-time updates, and consider working with local agents or intermediaries who understand the market dynamics and can facilitate smoother transactions. -
How can I build a long-term relationship with my hubs supplier?
Building a long-term relationship with your hubs supplier is essential for sustained success and collaboration. Start by maintaining open and transparent communication, providing feedback, and discussing future needs and expectations. Regularly review performance metrics and address any concerns promptly to foster trust. Consider involving your supplier in product development processes, as this can enhance their commitment to your business. Additionally, loyalty and timely payments can strengthen your partnership and encourage the supplier to prioritize your needs in the future.
Important Disclaimer & Terms of Use
⚠️ Important Disclaimer
The information provided in this guide, including content regarding manufacturers, technical specifications, and market analysis, is for informational and educational purposes only. It does not constitute professional procurement advice, financial advice, or legal advice.
While we have made every effort to ensure the accuracy and timeliness of the information, we are not responsible for any errors, omissions, or outdated information. Market conditions, company details, and technical standards are subject to change.
B2B buyers must conduct their own independent and thorough due diligence before making any purchasing decisions. This includes contacting suppliers directly, verifying certifications, requesting samples, and seeking professional consultation. The risk of relying on any information in this guide is borne solely by the reader.
Strategic Sourcing Conclusion and Outlook for hubs supplier
What Are the Key Takeaways for International B2B Buyers in Strategic Sourcing?
In today’s global marketplace, strategic sourcing is not just a necessity but a significant competitive advantage for B2B buyers. By leveraging a diverse supplier network, particularly from regions like Africa, South America, the Middle East, and Europe, businesses can ensure they have access to high-quality products and services at competitive prices. This approach not only enhances operational efficiency but also fosters innovation by enabling buyers to tap into unique local insights and capabilities.
How Can Buyers Benefit from a Strategic Sourcing Approach?
Engaging with hubs suppliers provides international buyers with flexibility and scalability, allowing them to adapt quickly to market demands. The ability to source from various geographical regions mitigates risks associated with supply chain disruptions and fluctuating costs. Furthermore, as businesses increasingly prioritize sustainability, working with local suppliers can help reduce carbon footprints and promote ethical sourcing practices.
What’s Next for International B2B Buyers?
Looking ahead, the landscape of strategic sourcing will continue to evolve with advancements in technology and shifting market dynamics. International B2B buyers are encouraged to embrace these changes by investing in robust supplier relationships and exploring innovative sourcing strategies. By doing so, they can position themselves for long-term success and resilience in an ever-changing environment. Seize the opportunity today to transform your sourcing strategy and unlock new growth avenues for your business.