Discover the Best ECU Manufacturer: A Complete Guide (2025)
Introduction: Navigating the Global Market for ecu manufacturer
Navigating the global market for ECU manufacturers presents a unique set of challenges for international B2B buyers. As the automotive industry increasingly relies on sophisticated electronic control units (ECUs) to enhance vehicle performance and safety, sourcing these critical components can be daunting. Buyers must not only identify reliable suppliers but also consider factors such as compliance with regional standards, technological advancements, and cost-effectiveness. This comprehensive guide addresses these challenges by providing actionable insights into the different types of ECUs, their applications across various industries, and essential criteria for vetting suppliers.
International B2B buyers from Africa, South America, the Middle East, and Europe, including markets like Germany and Australia, will find this guide particularly beneficial. It covers the entire spectrum of the ECU manufacturing process, from understanding the diverse functionalities of ECUs to evaluating potential suppliers based on quality, certifications, and pricing. Additionally, we delve into the implications of global supply chain dynamics and how they impact procurement strategies.
By leveraging the insights and strategies outlined in this guide, buyers can make informed decisions that not only meet their operational needs but also align with their long-term business goals. This resource is designed to empower you, ensuring that you navigate the complexities of the ECU market with confidence and clarity.
Understanding ecu manufacturer Types and Variations
Type Name | Key Distinguishing Features | Primary B2B Applications | Brief Pros & Cons for Buyers |
---|---|---|---|
OEM ECU Manufacturers | Designed to meet specific vehicle requirements; high reliability | Automotive manufacturers, fleet management | Pros: High quality, tailored specifications. Cons: Higher cost, limited flexibility. |
Aftermarket ECU Suppliers | Offer a variety of customizable solutions; often more affordable | Performance tuning, repair shops | Pros: Cost-effective, wider selection. Cons: Variable quality, potential compatibility issues. |
Specialized ECU Developers | Focus on niche markets; provide bespoke solutions | Racing, specialty vehicles | Pros: Tailored solutions, high performance. Cons: Limited availability, higher prices. |
Remanufactured ECU Providers | Reconditioned units; usually come with warranties | Cost-sensitive buyers, repair shops | Pros: Cost savings, eco-friendly. Cons: Potential reliability issues, limited lifespan. |
Embedded System Manufacturers | Integrate ECUs with advanced technologies; support IoT | Smart vehicles, automation industries | Pros: Advanced features, scalability. Cons: Complexity in integration, higher initial investment. |
What are the Key Characteristics of OEM ECU Manufacturers?
OEM (Original Equipment Manufacturer) ECU manufacturers produce units specifically designed for vehicle manufacturers. These ECUs are built to exact specifications, ensuring compatibility and reliability within the original vehicle systems. B2B buyers, particularly automotive manufacturers and fleet operators, often prefer OEM units for their quality assurance and performance consistency. However, the cost is typically higher, and options for customization may be limited, which can be a drawback for businesses seeking flexibility.
How Do Aftermarket ECU Suppliers Differ from OEM Providers?
Aftermarket ECU suppliers offer a broader range of products, often at lower prices than OEM counterparts. They provide customizable solutions that cater to performance tuning and various repair needs. This type of ECU is popular among automotive repair shops and performance enthusiasts who seek cost-effective alternatives. While these units can offer good value, buyers should be cautious about potential quality variations and compatibility issues that may arise, impacting vehicle performance.
What Makes Specialized ECU Developers Unique?
Specialized ECU developers focus on niche markets such as racing and specialty vehicles. They provide bespoke solutions tailored to specific performance requirements, making them ideal for companies involved in high-performance automotive sectors. These ECUs often come with advanced features that enhance vehicle capabilities. However, buyers must consider the limited availability of these products and the higher costs associated with customized solutions.
Why Consider Remanufactured ECU Providers?
Remanufactured ECU providers offer reconditioned units that can be a cost-effective solution for businesses looking to save on expenses. These units typically come with warranties, providing some assurance of reliability. They are ideal for cost-sensitive buyers, such as repair shops and fleet operators. However, potential buyers should be aware of the possibility of reliability issues and the limited lifespan of remanufactured units compared to new ones.
How Do Embedded System Manufacturers Enhance ECU Functionality?
Embedded system manufacturers integrate ECUs with advanced technologies, often supporting Internet of Things (IoT) applications. This innovation is crucial for smart vehicles and automation industries where enhanced connectivity and functionality are paramount. B2B buyers looking for cutting-edge solutions will find these ECUs beneficial. However, the complexity of integration and higher initial investments may pose challenges for some businesses, requiring careful consideration before purchase.
Related Video: HOW TO REPAIR INTERNAL PARTS OF ECU OR IDENTIFY PARTS, Manufacturerwill never let you know this..
Key Industrial Applications of ecu manufacturer
Industry/Sector | Specific Application of ECU Manufacturer | Value/Benefit for the Business | Key Sourcing Considerations for this Application |
---|---|---|---|
Automotive | Engine Control Units (ECUs) for fuel management | Enhanced fuel efficiency and reduced emissions | Compliance with local regulations and emissions standards |
Agriculture | Precision farming through ECU-based machinery | Increased crop yield and optimized resource usage | Compatibility with existing agricultural equipment |
Industrial Machinery | Automation control in manufacturing processes | Improved productivity and reduced operational costs | Reliability and scalability of ECU solutions |
Marine | Navigation and control systems in vessels | Enhanced safety and operational efficiency | Robustness against harsh marine environments |
Renewable Energy | Control systems for solar panels and wind turbines | Maximized energy output and operational reliability | Adaptability to different energy generation technologies |
How are Engine Control Units (ECUs) Used in the Automotive Sector?
In the automotive industry, Engine Control Units (ECUs) play a critical role in managing engine performance, optimizing fuel consumption, and minimizing emissions. These sophisticated devices monitor various engine parameters and adjust fuel injection, ignition timing, and other functions to ensure optimal performance. For international B2B buyers, particularly those from regions like Africa and South America, understanding local emissions regulations and the need for reliable supply chains is essential when sourcing ECUs. Additionally, buyers should consider the ECU’s compatibility with various engine types and configurations.
What Role do ECUs Play in Precision Agriculture?
In agriculture, ECUs are integral to precision farming technologies, enabling machinery to perform tasks such as planting, fertilizing, and harvesting with high accuracy. By utilizing ECUs, farmers can significantly increase crop yields and optimize resource usage, which is particularly beneficial in regions facing water scarcity or land degradation. B2B buyers in this sector should focus on sourcing ECUs that are compatible with their existing machinery and can withstand the rigors of agricultural environments, including dust and moisture.
How Do ECUs Enhance Productivity in Industrial Machinery?
In the manufacturing sector, ECUs are essential for automating processes and controlling machinery. They help streamline operations, enhance productivity, and reduce operational costs by providing real-time data and analytics. For international buyers, particularly from Europe and the Middle East, it is crucial to evaluate the reliability and scalability of the ECU solutions being sourced, ensuring they can integrate seamlessly into existing manufacturing systems and adapt to future technological advancements.
Why are ECUs Important for Marine Navigation and Control?
Marine vessels rely on ECUs for navigation and control systems, which enhance safety and operational efficiency. These control units manage various aspects of a vessel’s operation, from engine performance to navigation aids, ensuring that vessels can operate reliably under challenging conditions. Buyers in the marine sector should prioritize sourcing ECUs that are robust enough to withstand harsh marine environments, including saltwater exposure and extreme temperatures.
How Do ECUs Optimize Renewable Energy Systems?
In the renewable energy sector, ECUs are vital for managing control systems in solar panels and wind turbines. They optimize energy output by adjusting operational parameters based on environmental conditions. For B2B buyers in this field, particularly in Europe where renewable energy is a priority, it is important to source ECUs that are adaptable to different energy generation technologies and can integrate with existing energy management systems to maximize efficiency.
Related Video: What are all the Laboratory Apparatus and their uses?
3 Common User Pain Points for ‘ecu manufacturer’ & Their Solutions
Scenario 1: Navigating Compatibility Issues with ECU Units
The Problem: International B2B buyers often face compatibility challenges when sourcing Engine Control Units (ECUs) from manufacturers. This is especially true for companies operating in regions with diverse vehicle models and specifications, such as Africa and South America. When a buyer orders an ECU, they may discover that the unit does not integrate seamlessly with their existing systems or the vehicles in their fleet. This can lead to costly delays, wasted resources, and frustration, as the buyer is left scrambling to find a compatible solution.
The Solution: To mitigate compatibility issues, buyers should engage in thorough pre-purchase research. This includes understanding the specific ECU requirements for their vehicle models and systems. Buyers can request detailed specifications and compatibility lists from manufacturers before making a purchase. It’s also beneficial to establish a direct line of communication with the manufacturer’s technical support team. Consider setting up a pilot program where a small batch of ECUs is tested in real-world conditions before committing to larger orders. This proactive approach can save time and resources while ensuring that the chosen ECUs meet operational needs.
Scenario 2: Managing Supply Chain Delays in ECU Manufacturing
The Problem: Supply chain disruptions have become increasingly common in the global marketplace, affecting ECU manufacturers and their clients. B2B buyers often experience delays in receiving their orders due to factors such as raw material shortages or logistical challenges. These delays can halt production lines and impact delivery schedules, leading to dissatisfaction among end customers and potential financial losses.
The Solution: To combat supply chain delays, buyers should adopt a multi-sourcing strategy. By diversifying their supplier base, they can reduce dependency on a single manufacturer. This approach not only provides alternative options in case of delays but also fosters competitive pricing. Buyers should also consider implementing just-in-time inventory practices, allowing them to receive ECUs as needed rather than in bulk. Additionally, establishing a clear communication channel with suppliers to receive timely updates on order status can help in planning and mitigating potential disruptions. Investing in technology that tracks shipments in real time can further enhance supply chain visibility and reliability.
Scenario 3: Ensuring Quality Control in ECU Manufacturing
The Problem: Quality assurance is a significant concern for B2B buyers of ECUs, particularly for those in the automotive and industrial sectors. Poor-quality ECUs can lead to malfunctions, safety issues, and increased warranty claims, all of which can damage a company’s reputation and financial standing. Buyers often find it challenging to ascertain the quality of the ECUs they are purchasing, especially when dealing with overseas manufacturers.
The Solution: To ensure high-quality ECU manufacturing, buyers should implement a rigorous supplier evaluation process. This includes assessing a manufacturer’s certifications, quality control processes, and production capabilities. Buyers should request samples and conduct their own testing to validate the performance and reliability of the ECUs. Additionally, establishing long-term partnerships with manufacturers who prioritize quality can lead to better outcomes. Consider negotiating agreements that include quality guarantees and clear recourse in case of defects. Regular audits and on-site visits can also help maintain quality standards over time. By prioritizing quality control, buyers can protect their investments and ensure operational efficiency.
Strategic Material Selection Guide for ecu manufacturer
When selecting materials for Electronic Control Units (ECUs), manufacturers must consider various factors that impact performance, durability, and compliance with industry standards. Below, we analyze four common materials used in ECU manufacturing, focusing on their properties, advantages, disadvantages, and implications for international B2B buyers.
Which Materials Are Commonly Used in ECU Manufacturing?
1. Aluminum
Aluminum is widely used in ECU housings due to its lightweight nature and excellent thermal conductivity. It typically has a temperature rating of up to 150°C and provides good corrosion resistance when anodized.
Pros & Cons:
The key advantages of aluminum include its low weight, which enhances fuel efficiency in automotive applications, and its ability to dissipate heat effectively. However, it can be more expensive than other metals and may require additional surface treatments to improve corrosion resistance.
Impact on Application:
Aluminum is compatible with various media, including oils and coolants, making it suitable for automotive applications. It is essential to ensure that the selected aluminum alloy meets the specific thermal and mechanical requirements of the ECU.
Considerations for International Buyers:
Buyers from regions like Europe and the Middle East should ensure compliance with standards such as DIN and ASTM for aluminum alloys. Additionally, understanding local regulations regarding aluminum recycling and environmental impact is crucial.
2. Polycarbonate
Polycarbonate is a thermoplastic polymer known for its high impact resistance and transparency. It can withstand temperatures up to 120°C and offers good electrical insulation properties.
Pros & Cons:
The main advantage of polycarbonate is its durability and resistance to breakage, making it ideal for protective casings. However, it can be prone to scratching and may degrade under UV exposure unless treated.
Impact on Application:
Polycarbonate is often used in environments where mechanical protection is essential. Its compatibility with various chemicals makes it suitable for automotive and industrial applications.
Considerations for International Buyers:
International buyers should verify compliance with industry-specific standards, such as ISO and ASTM, regarding the use of polycarbonate. Additionally, understanding the impact of UV exposure in different climates, particularly in regions like Africa and South America, is vital.
3. Stainless Steel
Stainless steel is renowned for its strength and corrosion resistance, making it suitable for harsh environments. It can withstand high temperatures (up to 800°C) and pressures, making it ideal for applications requiring robust materials.
Pros & Cons:
Stainless steel’s primary advantage is its durability and longevity, which reduces the need for frequent replacements. However, it is heavier and more expensive than aluminum and plastic alternatives, which may affect overall vehicle weight and cost.
Impact on Application:
Stainless steel is particularly useful in applications exposed to moisture and corrosive substances, such as marine and industrial environments.
Considerations for International Buyers:
Buyers must ensure that the selected stainless steel grade complies with ASTM and ISO standards. In regions like Europe, adherence to environmental regulations regarding stainless steel production and recycling is also necessary.
4. FR-4 (Fiberglass Reinforced Epoxy)
FR-4 is a composite material made from woven fiberglass cloth and epoxy resin, known for its excellent electrical insulation properties and mechanical strength. It can operate effectively at temperatures up to 130°C.
Pros & Cons:
FR-4’s advantages include its lightweight nature and high dielectric strength, making it ideal for PCB applications within ECUs. However, it can be brittle and may not perform well under extreme mechanical stress.
Impact on Application:
FR-4 is suitable for electronic applications where insulation and heat resistance are critical. It is often used in circuit boards and structural components of ECUs.
Considerations for International Buyers:
International buyers should check for compliance with IPC standards for electronic materials. Additionally, understanding the environmental impact of fiberglass production and disposal is essential, especially in regions with strict regulations.
Summary Table of Material Selection for ECU Manufacturing
Material | Typical Use Case for ECU Manufacturer | Key Advantage | Key Disadvantage/Limitation | Relative Cost (Low/Med/High) |
---|---|---|---|---|
Aluminum | ECU housings and heat sinks | Lightweight and good thermal conductivity | Higher cost and requires surface treatment | Medium |
Polycarbonate | Protective casings | High impact resistance | Prone to scratching and UV degradation | Medium |
Stainless Steel | Components in harsh environments | Excellent durability and corrosion resistance | Heavier and more expensive | High |
FR-4 (Fiberglass Reinforced Epoxy) | Circuit boards and structural components | High electrical insulation | Brittle under extreme stress | Medium |
This strategic material selection guide provides international B2B buyers with essential insights into the materials used in ECU manufacturing, enabling informed decision-making that aligns with performance, cost, and compliance requirements.
In-depth Look: Manufacturing Processes and Quality Assurance for ecu manufacturer
What Are the Main Stages of Manufacturing Processes for ECU Manufacturers?
Manufacturing Electronic Control Units (ECUs) involves a series of structured processes designed to ensure high-quality output. Understanding these stages is crucial for international B2B buyers looking to source reliable ECU components.
Material Preparation: What Is Involved?
The first stage in the manufacturing process is material preparation. This involves selecting high-quality raw materials, such as semiconductors, plastics, and metals, that meet industry specifications. Suppliers often source materials that comply with international standards, such as RoHS (Restriction of Hazardous Substances), to ensure environmental safety. Buyers should inquire about the origin of materials and their compliance with regulations, especially when sourcing from regions with varying quality controls.
Forming: How Are ECUs Shaped and Molded?
Once materials are prepared, the next step is forming, which typically includes processes like injection molding and PCB (Printed Circuit Board) fabrication. Injection molding is used to create the plastic housings of ECUs, while PCB fabrication involves etching and layering materials to create the electronic circuits. Advanced techniques like surface mount technology (SMT) are employed to ensure compact and efficient designs. B2B buyers should ask manufacturers about the technologies used and their capabilities to handle complex designs, as this can directly affect the performance of the ECUs.
Assembly: What Does the Assembly Process Entail?
The assembly stage is critical, involving the integration of various components into a functional unit. This includes soldering components onto the PCB, installing connectors, and encasing the entire assembly. Manufacturers often employ automated assembly lines to enhance precision and efficiency. Buyers should verify if the assembly process includes automated optical inspection (AOI) to detect defects early. Understanding the level of automation can provide insights into the manufacturer’s production capacity and consistency.
Finishing: How Is Quality Enhanced in the Finishing Stage?
The finishing stage includes various processes such as coating, labeling, and testing. Coatings may be applied to protect against environmental factors, while labeling ensures compliance with industry standards. Testing is a crucial part of this stage, where ECUs undergo functional and stress tests to ensure they meet performance specifications. B2B buyers should request detailed information on the testing protocols used, as this can significantly affect the reliability of the ECU in real-world applications.
What Are the Key Quality Assurance Practices for ECU Manufacturers?
Quality assurance (QA) is integral to the manufacturing process, ensuring that the ECUs produced meet both industry standards and client expectations.
What International Standards Should Buyers Be Aware Of?
International standards such as ISO 9001 provide a framework for quality management systems, focusing on continuous improvement and customer satisfaction. Additionally, specific industry standards like CE marking for electronics in Europe and API standards for automotive applications are essential for ensuring compliance with safety and performance regulations. Buyers should ensure that the manufacturers they partner with hold relevant certifications, as this reflects their commitment to quality.
How Are Quality Control Checkpoints Structured?
Quality control (QC) checkpoints are established throughout the manufacturing process to ensure consistent quality. Key checkpoints include:
- Incoming Quality Control (IQC): At this stage, raw materials are inspected for defects before production begins.
- In-Process Quality Control (IPQC): During manufacturing, random samples are tested to monitor compliance with specifications.
- Final Quality Control (FQC): Once production is complete, a thorough inspection is conducted to verify that each ECU meets the required standards.
B2B buyers should inquire about the frequency and methods of these inspections to understand the manufacturer’s QC rigor.
What Common Testing Methods Are Used in ECU Manufacturing?
Testing is a vital aspect of the quality assurance process in ECU manufacturing. Common testing methods include:
- Functional Testing: Verifying that the ECU operates as intended under normal conditions.
- Environmental Testing: Subjecting the ECU to extreme temperatures, humidity, and vibration to ensure durability.
- Electrical Testing: Checking for proper voltage levels and current flow to confirm functionality.
Buyers should seek detailed reports on testing outcomes and methodologies, as this information can help in assessing the reliability of the products.
How Can B2B Buyers Verify Supplier Quality Control?
To ensure that a supplier maintains high-quality standards, B2B buyers can implement several verification strategies:
- Conduct Audits: Regular audits can help assess the supplier’s adherence to quality standards and processes. It’s advisable to schedule these audits periodically or upon major production changes.
- Request Quality Reports: Buyers should ask for detailed QC reports that outline testing methods, results, and any corrective actions taken.
- Utilize Third-Party Inspections: Engaging third-party inspection services can provide an unbiased evaluation of the manufacturing processes and product quality.
What Are the QC and Certification Nuances for International B2B Buyers?
International B2B buyers, particularly from Africa, South America, the Middle East, and Europe, should be aware of specific nuances in quality control and certifications. Different regions may have varying regulatory requirements and standards. For instance, ECUs exported to Europe must comply with CE marking requirements, while those intended for markets in Africa may need to meet local standards, which can differ significantly.
Understanding these regional differences is crucial for avoiding compliance issues and ensuring that products meet the necessary quality standards. Buyers should engage with manufacturers who have a proven track record of navigating these complexities and can provide necessary documentation for all certifications.
In conclusion, a thorough understanding of the manufacturing processes and quality assurance practices is essential for B2B buyers in the ECU market. By focusing on material preparation, forming, assembly, finishing, and rigorous quality control, buyers can make informed decisions and ensure they partner with manufacturers that prioritize quality and compliance.
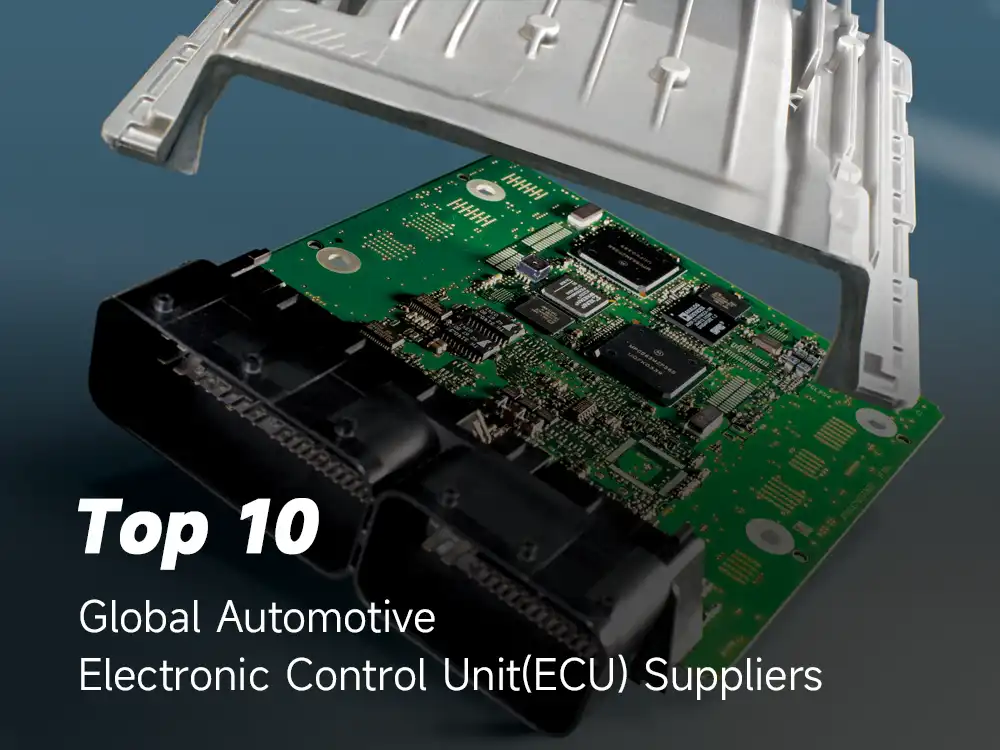
A stock image related to ecu manufacturer.
Practical Sourcing Guide: A Step-by-Step Checklist for ‘ecu manufacturer’
To effectively source from an ECU manufacturer, international B2B buyers must navigate a series of critical steps that ensure they select a reliable supplier capable of meeting their specific needs. This guide outlines a practical checklist to streamline your sourcing process.
Step 1: Define Your Technical Specifications
Before you start searching for suppliers, it’s essential to have a clear understanding of your technical requirements. This includes the type of ECU you need, specifications such as processing power, communication protocols, and compatibility with existing systems.
– Why it Matters: Defining these specifications helps you filter potential manufacturers who can deliver the exact product you require.
– What to Look For: Ensure that your specifications align with industry standards and regulations pertinent to your region, especially if you’re sourcing from different continents.
Step 2: Research Potential Suppliers
Conduct thorough research to identify potential ECU manufacturers. Utilize industry directories, trade shows, and online platforms like Alibaba or ThomasNet to compile a list of candidates.
– Why it Matters: A wide pool of suppliers increases your chances of finding a manufacturer that meets your quality and price requirements.
– What to Look For: Focus on suppliers with a strong reputation, positive reviews, and relevant industry experience.
Step 3: Verify Supplier Certifications
Once you have a shortlist, verify the certifications and compliance of each manufacturer. Check for ISO certifications, industry-specific standards, and any other relevant credentials.
– Why it Matters: Certifications indicate a commitment to quality and adherence to safety standards, which is crucial in the automotive sector.
– What to Look For: Ensure that the certifications are current and applicable to the specific types of ECUs you are sourcing.
Step 4: Request Detailed Proposals
Reach out to selected suppliers and request detailed proposals, including pricing, lead times, and minimum order quantities.
– Why it Matters: Comparing proposals allows you to evaluate the cost-effectiveness and feasibility of each supplier’s offer.
– What to Look For: Pay attention to transparency in pricing and any additional costs that may arise, such as shipping or tariffs.
Step 5: Evaluate Supplier Capabilities
Assess the manufacturing capabilities of each supplier. This includes their production capacity, technology used, and quality control processes.
– Why it Matters: Understanding a supplier’s capabilities helps ensure they can meet your demand and maintain quality standards.
– What to Look For: Request information on their production processes, quality assurance measures, and examples of past projects.
Step 6: Conduct Site Visits or Virtual Tours
If possible, conduct site visits or arrange virtual tours of the manufacturing facilities. This provides insight into their operations and working conditions.
– Why it Matters: A firsthand look can reveal aspects of the supplier’s operations that might not be apparent through documentation alone.
– What to Look For: Observe cleanliness, organization, and the use of modern technology in production.
Step 7: Establish Clear Communication Channels
Finally, ensure that there are clear communication channels established with your chosen supplier. This includes defining points of contact and preferred methods of communication.
– Why it Matters: Effective communication is key to addressing issues quickly and ensuring smooth collaboration throughout the sourcing process.
– What to Look For: Look for suppliers who are responsive and open to regular updates on production status.
By following this structured checklist, international B2B buyers can navigate the complexities of sourcing from ECU manufacturers, ensuring they make informed decisions that align with their business needs.
Comprehensive Cost and Pricing Analysis for ecu manufacturer Sourcing
What are the Key Cost Components in ECU Manufacturing?
When sourcing ECUs (Electronic Control Units), it’s crucial to understand the various cost components involved in the manufacturing process. The primary factors include:
-
Materials: Raw materials, such as semiconductors, circuit boards, and connectors, significantly impact overall costs. Prices can fluctuate based on global supply chain dynamics, so staying informed about market trends is essential.
-
Labor: Labor costs vary widely across regions. Countries with lower wages may provide cost advantages, but it’s important to consider the skill level and expertise required for ECU manufacturing, as higher-skilled labor may be necessary for quality assurance and advanced manufacturing processes.
-
Manufacturing Overhead: This includes indirect costs like utilities, facility maintenance, and administrative expenses. Efficient overhead management can help reduce the overall cost of production.
-
Tooling: The cost of specialized tools and machinery used in the manufacturing process can be substantial, especially for custom or high-volume orders. Investing in versatile tooling can yield long-term savings.
-
Quality Control (QC): Ensuring the reliability and performance of ECUs is paramount. Implementing robust QC processes involves additional costs but is essential for maintaining product integrity and compliance with industry standards.
-
Logistics: Shipping and handling costs can vary significantly based on the distance between the manufacturer and the buyer, shipping methods, and any tariffs that may apply. Understanding the logistics involved can help in accurately calculating total costs.
-
Margin: The profit margin that manufacturers add to their costs will influence the final price. Buyers should seek transparency in pricing to understand how margins are calculated.
How Do Price Influencers Affect ECU Sourcing?
Several factors can influence the pricing of ECUs, including:
-
Volume/MOQ (Minimum Order Quantity): Larger orders often qualify for bulk pricing discounts. Buyers should consider their needs and negotiate for favorable terms based on projected volume.
-
Specifications and Customization: Customized ECUs tailored to specific applications typically incur higher costs due to additional design and engineering efforts. Clear communication of specifications can help mitigate unexpected costs.
-
Materials and Quality Certifications: The choice of materials and adherence to quality certifications (such as ISO/TS 16949 for automotive components) can affect pricing. ECUs that meet stringent quality standards may come at a premium but are essential for reliability.
-
Supplier Factors: The reputation, reliability, and financial stability of suppliers can impact costs. Established suppliers may charge higher prices due to their proven track record, but they can also offer greater assurance of quality and delivery timelines.
-
Incoterms: Understanding the agreed-upon Incoterms (International Commercial Terms) is critical, as they define responsibilities regarding shipping, insurance, and tariffs. This knowledge can significantly affect the total landed cost of the goods.
What Are the Best Practices for Negotiating ECU Prices?
For international B2B buyers, especially those from Africa, South America, the Middle East, and Europe, effective negotiation is key to achieving favorable pricing. Here are some actionable tips:
-
Research and Benchmarking: Gather data on prevailing market prices and benchmark against competitors. This knowledge will empower buyers during negotiations.
-
Focus on Total Cost of Ownership (TCO): Rather than just the purchase price, consider the TCO, which includes costs related to maintenance, warranty, and potential downtime. A slightly higher upfront cost may lead to savings in the long run.
-
Leverage Relationships: Building long-term relationships with suppliers can lead to better pricing, improved service, and priority during high-demand periods.
-
Be Transparent: Clearly communicate your requirements, budget constraints, and timelines. This transparency can foster trust and lead to more favorable terms.
-
Consider Alternative Suppliers: Don’t hesitate to explore multiple suppliers. A competitive environment can lead to better pricing and service options.
Conclusion
Understanding the comprehensive cost structure and pricing dynamics of ECU manufacturing is essential for international B2B buyers. By focusing on cost components, price influencers, and effective negotiation strategies, buyers can optimize their sourcing decisions and achieve significant cost efficiencies. Always remember that indicative prices can vary, and it’s advisable to seek detailed quotes from suppliers to ensure accurate budgeting.
Alternatives Analysis: Comparing ecu manufacturer With Other Solutions
Understanding the Importance of Alternative Solutions in ECU Manufacturing
When considering the procurement of electronic control units (ECUs), it is vital for international B2B buyers to explore various alternatives. The right choice depends on several factors, including performance, cost, ease of implementation, and maintenance. This section delves into a comparative analysis between traditional ECU manufacturers and alternative solutions such as programmable logic controllers (PLCs) and microcontroller-based systems.
Comparison of ECU Manufacturer with Alternative Solutions
Comparison Aspect | ECU Manufacturer | PLC (Programmable Logic Controller) | Microcontroller-Based Systems |
---|---|---|---|
Performance | High reliability and precision | Good for industrial applications, may have limitations in complex tasks | Versatile, suitable for various tasks but may require more development |
Cost | Higher initial investment | Moderate cost, but can escalate with additional features | Generally lower cost, especially for simple applications |
Ease of Implementation | Requires expert knowledge for setup | User-friendly with graphical programming | Moderate, depending on complexity and programming knowledge |
Maintenance | Often requires specialized service | Routine maintenance is manageable | Easy to maintain with proper design |
Best Use Case | Automotive and complex systems | Industrial automation and control | Consumer electronics and simple automation tasks |
Detailed Breakdown of Alternatives
What Are the Advantages and Disadvantages of Using PLCs?
PLCs are widely used in industrial settings for their reliability and ease of programming. They offer a good balance between performance and cost, making them suitable for automation in manufacturing environments. However, PLCs may not be ideal for more complex tasks that require advanced processing capabilities, as they can be limited by their architecture. For B2B buyers in sectors such as manufacturing and logistics, PLCs represent a solid alternative when the requirements align with their operational needs.
How Do Microcontroller-Based Systems Compare?
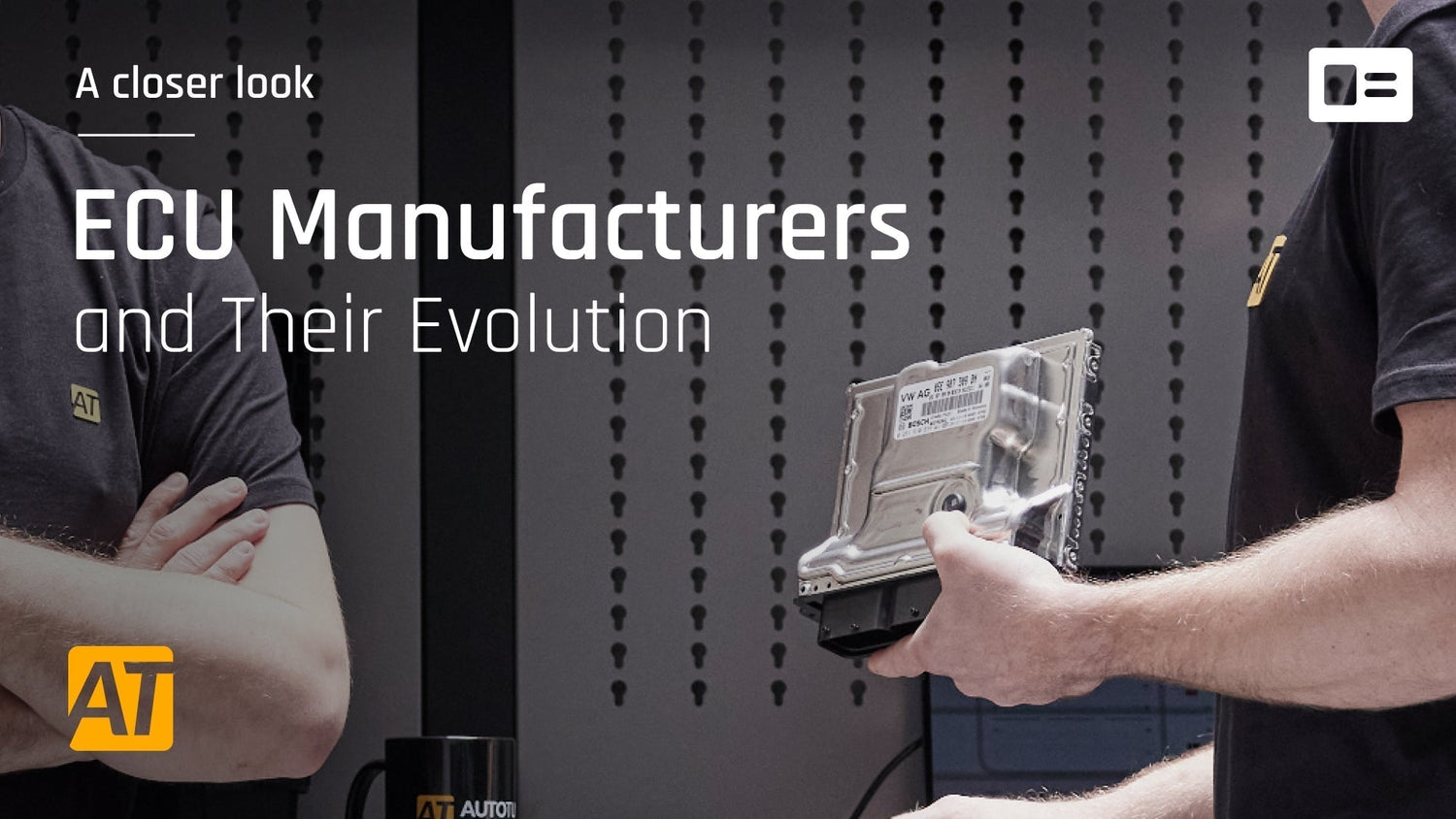
A stock image related to ecu manufacturer.
Microcontroller-based systems provide a versatile solution that can be tailored for various applications, from consumer electronics to industrial automation. Their cost-effectiveness makes them attractive for smaller projects or startups. However, developing a microcontroller-based system may require significant programming expertise and time for development, which can be a barrier for some organizations. Buyers looking for flexibility and lower costs might find microcontroller systems appealing, but they should assess the technical capabilities of their teams before opting for this solution.
Conclusion: How to Choose the Right ECU Solution for Your Business
Selecting the appropriate ECU solution requires careful consideration of your organization’s specific needs and capabilities. International B2B buyers should evaluate not only the cost and performance but also the ease of implementation and maintenance associated with each option. By understanding the strengths and weaknesses of ECU manufacturers compared to alternatives like PLCs and microcontroller-based systems, buyers can make informed decisions that align with their operational goals and budget constraints. This comprehensive approach will ultimately lead to enhanced efficiency and success in their respective industries.
Essential Technical Properties and Trade Terminology for ecu manufacturer
What Are the Key Technical Properties of ECU Manufacturing?
When engaging with ECU (Electronic Control Unit) manufacturers, understanding critical technical properties is essential for making informed purchasing decisions. Here are some of the most important specifications to consider:
-
Material Grade
– The material used in ECU manufacturing, often plastic or metal, affects durability, weight, and heat resistance. High-grade materials ensure longevity and performance, which is crucial for applications in automotive and aerospace sectors. Buyers should inquire about material certifications to ensure compliance with industry standards. -
Tolerance Levels
– Tolerance refers to the allowable deviation from specified dimensions. In ECU manufacturing, tight tolerances (often in the range of micrometers) are vital for ensuring that components fit together correctly and function reliably. This is particularly important for applications where precision is critical, such as in safety systems. -
Temperature Range
– The operational temperature range indicates the conditions under which the ECU can function effectively. An ECU must withstand varying temperatures, especially in automotive applications where engine heat can be extreme. Understanding the temperature range helps buyers select products that will perform reliably in their specific environments. -
Power Consumption
– Power consumption metrics are crucial for determining how efficiently an ECU operates. Low-power ECUs are especially desirable for battery-operated applications, as they extend the operational life of devices. Buyers should look for specifications that detail power requirements during both idle and active states. -
Signal Processing Capability
– This specification indicates how well an ECU can handle data from sensors and other inputs. Higher processing capabilities translate to better performance in real-time applications, such as autonomous driving systems. Buyers should assess the processing power and speed to ensure it meets their application needs. -
Environmental Protection Rating (IP Rating)
– The Ingress Protection (IP) rating defines how well the ECU can resist dust and moisture. For applications in harsh environments, such as off-road vehicles, a higher IP rating (e.g., IP67 or IP68) is critical. Buyers should always check IP ratings to ensure reliability and longevity in challenging conditions.
Which Trade Terminology Should B2B Buyers Understand?
Understanding industry terminology can streamline communication and negotiations with ECU manufacturers. Here are some common terms that every buyer should know:
-
OEM (Original Equipment Manufacturer)
– An OEM is a company that produces parts and equipment that may be marketed by another manufacturer. In the context of ECUs, working with OEMs ensures that parts are designed specifically for compatibility with original systems, which can enhance quality and reliability. -
MOQ (Minimum Order Quantity)
– MOQ refers to the smallest number of units a manufacturer is willing to produce or sell. Understanding MOQ is crucial for budgeting and inventory management. Buyers should negotiate MOQs that align with their demand to avoid excess inventory or stock shortages. -
RFQ (Request for Quotation)
– An RFQ is a formal document that buyers use to request pricing and terms from suppliers. Issuing an RFQ can help buyers compare different manufacturers and select the best option based on price, quality, and delivery times. -
Incoterms (International Commercial Terms)
– Incoterms define the responsibilities of buyers and sellers in international trade. They clarify who is responsible for shipping, insurance, and tariffs. Familiarity with these terms is essential for buyers to understand the total cost of acquisition and the risks involved in the transportation of goods. -
Lead Time
– Lead time is the period between placing an order and receiving it. It includes manufacturing and shipping time. Understanding lead times is vital for project planning and ensuring that components arrive when needed. -
Testing and Validation
– This term refers to the processes used to ensure that ECUs meet specified performance criteria and standards. Buyers should prioritize manufacturers that have robust testing protocols to ensure quality and compliance with industry regulations.
By familiarizing yourself with these technical properties and trade terminologies, you can enhance your procurement strategy and ensure that your business selects the best ECU manufacturers for its needs.
Navigating Market Dynamics and Sourcing Trends in the ecu manufacturer Sector
What Are the Current Market Dynamics and Key Trends in the ECU Manufacturer Sector?
The ECU (Electronic Control Unit) manufacturer sector is experiencing significant growth driven by the rapid advancement of technology and the increasing complexity of automotive systems. Global drivers such as the push for automation, the rise of electric vehicles (EVs), and the integration of advanced driver-assistance systems (ADAS) are reshaping the landscape. International B2B buyers from Africa, South America, the Middle East, and Europe should note that the demand for highly specialized ECUs is on the rise, particularly those that enhance vehicle safety and connectivity.
Emerging trends include the adoption of Industry 4.0 technologies, such as IoT and AI, which are revolutionizing manufacturing processes. This leads to better predictive maintenance and optimized supply chains. Additionally, the trend toward modular ECU designs allows manufacturers to respond quickly to market changes and consumer demands, providing a competitive edge. B2B buyers should consider suppliers that are not only technologically advanced but also adaptable to changing market conditions.
Furthermore, the shift towards localized sourcing is gaining traction, especially in regions with burgeoning automotive markets. Buyers are encouraged to evaluate suppliers based on their ability to deliver just-in-time manufacturing and their proximity to key markets, which can reduce lead times and shipping costs.
How Important Is Sustainability and Ethical Sourcing in the ECU Manufacturing Sector?
Sustainability and ethical sourcing are increasingly critical in the ECU manufacturing sector, particularly as consumers and regulatory bodies demand greater environmental responsibility. The environmental impact of manufacturing processes, including energy consumption and waste generation, is under scrutiny. B2B buyers must prioritize suppliers that demonstrate a commitment to sustainable practices, including the use of renewable energy and efficient resource management.
Moreover, ethical supply chains are becoming a focal point in procurement strategies. The importance of transparency in sourcing materials, particularly for components like semiconductors and metals, cannot be overstated. Buyers should seek manufacturers that hold certifications such as ISO 14001 for environmental management and adhere to strict labor practices, ensuring fair treatment of workers.
The use of ‘green’ materials, such as recyclable plastics and low-impact composites, is also gaining traction in ECU production. Buyers should consider suppliers that are investing in sustainable materials, which not only minimize environmental impact but can also enhance brand reputation and customer loyalty.
What Is the Historical Context of ECU Manufacturing Relevant to B2B Buyers?
The history of ECU manufacturing dates back to the early 1980s when the automotive industry began to incorporate electronic systems for engine management. This marked the transition from purely mechanical systems to more sophisticated electronic solutions, paving the way for enhanced vehicle performance and efficiency. Over the decades, the evolution of ECU technology has paralleled advancements in computing power and software development, leading to the integration of complex functionalities such as infotainment systems and vehicle diagnostics.
For B2B buyers, understanding this evolution is crucial. It highlights the importance of selecting manufacturers with a strong track record of innovation and a commitment to keeping pace with technological advancements. As the sector continues to evolve, suppliers that can adapt and anticipate future trends will be invaluable partners in the journey toward more intelligent and sustainable automotive solutions.
Frequently Asked Questions (FAQs) for B2B Buyers of ecu manufacturer
-
How do I choose the right ECU manufacturer for my business needs?
Selecting the right ECU manufacturer involves assessing their expertise in your specific application, whether it’s automotive, industrial, or marine. Look for manufacturers with a proven track record, certifications like ISO/TS 16949 for automotive, and positive client testimonials. Additionally, consider their ability to customize solutions, responsiveness to inquiries, and support for after-sales services. It’s also beneficial to verify their production capacity to meet your demand and timelines. -
What are the key factors to consider when vetting ECU suppliers?
When vetting ECU suppliers, consider their manufacturing capabilities, quality assurance processes, and compliance with international standards. Assess their experience in your industry, the technology they use, and their ability to offer customization. Request samples and conduct audits to evaluate their production facilities. Furthermore, consider their financial stability, as this can impact their ability to fulfill long-term contracts and provide reliable service. -
What customization options are available when sourcing ECUs?
Many ECU manufacturers offer a range of customization options, including software tuning, hardware modifications, and feature additions tailored to specific applications. Discuss your requirements during initial conversations to ensure they can accommodate your needs. Some manufacturers may also provide design and engineering support to help you optimize the ECU for your particular use case, enhancing performance and efficiency. -
What is the minimum order quantity (MOQ) for ECUs, and how does it vary by manufacturer?
The MOQ for ECUs can vary significantly between manufacturers, typically ranging from 50 to several hundred units depending on the complexity of the product and the manufacturing process. Smaller manufacturers may offer lower MOQs to accommodate startups or smaller businesses, while larger manufacturers may set higher MOQs to ensure cost-effectiveness. Always clarify MOQ during negotiations and consider your demand forecast to avoid excess inventory.
-
What payment terms should I expect when purchasing ECUs internationally?
Payment terms for international ECU purchases can vary widely. Common arrangements include partial upfront payments, Letter of Credit (LC), or payment upon delivery. Larger companies may negotiate better terms based on their purchasing volume and relationship with the supplier. It’s crucial to understand the currency fluctuations and international transaction fees that might apply. Always ensure that payment terms are clearly defined in the contract to avoid disputes. -
How do I ensure quality assurance in the ECUs I purchase?
To ensure quality assurance in your ECU purchases, request documentation for the manufacturer’s quality control processes, including testing procedures and certifications. Consider suppliers that provide detailed reports on their testing results. Establish a quality assurance protocol for incoming products, including inspection and testing of a sample batch. Collaborating closely with the supplier during the production process can also help ensure adherence to quality standards. -
What logistics considerations should I keep in mind when sourcing ECUs internationally?
Logistics is crucial when sourcing ECUs internationally. Consider shipping options, delivery times, and associated costs, including customs duties and taxes. Work with suppliers who have experience in international shipping to ensure compliance with regulations in your country. Establish clear communication regarding tracking shipments and handling any potential delays. Partnering with a reliable freight forwarder can also streamline the logistics process. -
How can I manage communication effectively with ECU manufacturers across different time zones?
Effective communication with ECU manufacturers in different time zones requires establishing a clear communication plan. Utilize digital tools like email, video conferencing, and project management software to facilitate discussions. Set regular meeting times that accommodate both parties, and be mindful of time zone differences when scheduling. It may also be helpful to designate a point of contact on both sides to streamline communication and ensure timely responses.
Important Disclaimer & Terms of Use
⚠️ Important Disclaimer
The information provided in this guide, including content regarding manufacturers, technical specifications, and market analysis, is for informational and educational purposes only. It does not constitute professional procurement advice, financial advice, or legal advice.
While we have made every effort to ensure the accuracy and timeliness of the information, we are not responsible for any errors, omissions, or outdated information. Market conditions, company details, and technical standards are subject to change.
B2B buyers must conduct their own independent and thorough due diligence before making any purchasing decisions. This includes contacting suppliers directly, verifying certifications, requesting samples, and seeking professional consultation. The risk of relying on any information in this guide is borne solely by the reader.
Strategic Sourcing Conclusion and Outlook for ecu manufacturer
What Are the Key Takeaways for International B2B Buyers in ECU Manufacturing?
In navigating the complex landscape of ECU manufacturing, strategic sourcing emerges as a pivotal approach for international B2B buyers. By leveraging a diverse supplier base, companies from Africa, South America, the Middle East, and Europe can enhance their supply chain resilience and reduce risks associated with market fluctuations. Understanding regional suppliers’ capabilities and establishing strong relationships can lead to innovative solutions tailored to specific market demands.
How Can Strategic Sourcing Drive Value in ECU Procurement?
The value of strategic sourcing lies in its ability to optimize costs while ensuring quality and compliance with international standards. Buyers should prioritize suppliers who demonstrate not only competitive pricing but also a commitment to sustainability and technological advancement. This focus will be essential as the ECU market evolves with trends such as electrification and automation.
What Does the Future Hold for ECU Manufacturers and Buyers?
Looking ahead, the ECU manufacturing sector is poised for significant growth driven by technological advancements and increasing global demand for smart automotive solutions. International B2B buyers are encouraged to remain proactive in their sourcing strategies, exploring partnerships that offer innovation and adaptability. By doing so, they can position themselves favorably within this dynamic market landscape and ensure long-term success. Embrace the opportunity to enhance your sourcing strategy today—it’s time to take the next step in your procurement journey.