Discover the Best Hand Blender Manufacturer for Your Needs (2025)
Introduction: Navigating the Global Market for hand blender manufacturer
In today’s fast-paced global market, sourcing a reliable hand blender manufacturer can be a daunting task for international B2B buyers, particularly those operating in diverse regions such as Africa, South America, the Middle East, and Europe. Buyers often face challenges related to quality assurance, supplier reliability, and pricing. This guide aims to demystify the complexities of the hand blender manufacturing landscape, providing actionable insights that empower purchasing decisions.
This comprehensive resource will explore various types of hand blenders, their applications in different industries, and the key factors to consider when vetting suppliers. Additionally, we will delve into cost considerations, helping you understand pricing structures and how to negotiate favorable terms with manufacturers. By addressing these critical aspects, this guide equips you with the knowledge to make informed choices that align with your business needs.
Navigating the intricacies of global sourcing can be overwhelming, but with the right information, you can streamline your procurement process. Whether you are a buyer from South Africa looking for innovative designs or a distributor in Spain seeking cost-effective solutions, this guide is tailored to meet your specific needs. By leveraging the insights provided here, you will be better positioned to build strong partnerships with manufacturers, ensuring quality products that enhance your market competitiveness.
Understanding hand blender manufacturer Types and Variations
Type Name | Key Distinguishing Features | Primary B2B Applications | Brief Pros & Cons for Buyers |
---|---|---|---|
Immersion Hand Blenders | Lightweight, portable, and easy to use | Food processing, catering, small kitchens | Pros: Versatile, easy to clean. Cons: Limited power for heavy-duty tasks. |
Commercial Hand Blenders | Heavy-duty, often equipped with multiple speeds | Restaurants, food service operations | Pros: High power, durable. Cons: Higher cost, requires more storage space. |
Multi-Functional Blenders | Versatile with attachments for different tasks | Food production, R&D kitchens | Pros: Multi-use, saves space. Cons: Complexity may require training. |
Cordless Hand Blenders | Battery-operated, offering mobility | Catering, outdoor events | Pros: Convenient, no power outlet needed. Cons: Limited battery life. |
Professional Hand Blenders | Designed for industrial use, robust materials | Large-scale food production | Pros: Long-lasting, efficient. Cons: Higher initial investment. |
What Are the Characteristics of Immersion Hand Blenders?
Immersion hand blenders, also known as stick blenders, are characterized by their lightweight design and ease of use. They are ideal for blending soups, sauces, and smoothies directly in the pot or container. These blenders are particularly suitable for small-scale operations such as cafes and catering services, where quick and efficient blending is essential. When considering a purchase, B2B buyers should evaluate the motor power, ease of cleaning, and the variety of attachments available, as these factors can significantly influence operational efficiency.
How Do Commercial Hand Blenders Stand Out in the Market?
Commercial hand blenders are built for heavy-duty applications, featuring robust construction and multiple speed settings to cater to a variety of food processing needs. These blenders are commonly used in restaurants and food service environments where large batches of food need to be prepared quickly. Buyers should consider the power rating and warranty options when purchasing, as these features can indicate durability and reliability in high-volume settings. While the initial investment may be higher, the long-term value often justifies the cost.
Why Choose Multi-Functional Blenders for B2B Applications?
Multi-functional blenders come equipped with various attachments, enabling them to perform multiple tasks such as chopping, whisking, and blending. This versatility makes them suitable for food production facilities and research and development kitchens that require a range of culinary processes. When purchasing, B2B buyers should assess the quality of the attachments and the ease of switching between functions, as these factors will impact workflow efficiency. Although they can be more complex to operate, their multifunctionality can save space and reduce the need for multiple appliances.
What Are the Advantages of Cordless Hand Blenders?
Cordless hand blenders offer unmatched mobility, making them ideal for catering services and outdoor events where access to power outlets may be limited. These blenders are powered by rechargeable batteries, allowing for easy maneuverability without the constraints of cords. B2B buyers should consider the battery life and charging time, as these elements are crucial for uninterrupted service. While they provide convenience, it is essential to note that their blending power may be less than that of corded models, which could limit their use for certain applications.
When Should You Invest in Professional Hand Blenders?
Professional hand blenders are designed for industrial use, often featuring heavy-duty materials and powerful motors to handle large-scale food processing tasks. These blenders are perfect for food manufacturers and large kitchens where efficiency and durability are paramount. Buyers should consider the capacity, ease of maintenance, and energy consumption when making a purchase. Although they tend to be pricier, their long lifespan and ability to withstand rigorous use make them a worthwhile investment for businesses focused on high productivity.
Related Video: Video of Horizontal Ribbon Mixer/Blender Machine
Key Industrial Applications of hand blender manufacturer
Industry/Sector | Specific Application of Hand Blender Manufacturer | Value/Benefit for the Business | Key Sourcing Considerations for this Application |
---|---|---|---|
Food Processing | Pureeing fruits and vegetables for juice production | Enhances product quality and consistency | Assess blending capacity and durability |
Hospitality | Preparing sauces and soups in bulk | Saves time and labor costs | Look for models with easy cleaning features |
Pharmaceutical | Creating emulsions for topical applications | Ensures product homogeneity and safety | Verify compliance with health and safety standards |
Cosmetics | Mixing ingredients for creams and lotions | Improves product texture and effectiveness | Consider sourcing from manufacturers with R&D capabilities |
Agriculture | Mixing feed and supplements for livestock | Increases nutritional value and palatability | Evaluate the energy efficiency of the unit |
What Are the Key Industrial Applications of Hand Blenders in Food Processing?
In the food processing industry, hand blenders are extensively used for pureeing fruits and vegetables, particularly for juice production. This application is crucial as it enhances product quality and consistency, ensuring that the final product meets customer expectations. International buyers, especially from regions like Africa and South America, should consider the blending capacity and durability of the units to accommodate high-volume production while maintaining operational efficiency.
How Do Hand Blenders Benefit the Hospitality Sector?
In the hospitality sector, hand blenders play a vital role in preparing sauces and soups in bulk, significantly reducing preparation time and labor costs. This efficiency is particularly beneficial for restaurants and catering services looking to streamline their kitchen operations. Buyers from Europe and the Middle East should prioritize models that feature easy cleaning mechanisms to minimize downtime and ensure hygiene compliance.
What Role Do Hand Blenders Play in the Pharmaceutical Industry?
In pharmaceutical manufacturing, hand blenders are used to create emulsions for topical applications, ensuring product homogeneity and safety. This application is critical as it directly impacts the efficacy of medical creams and ointments. B2B buyers must verify that the equipment complies with health and safety standards, particularly those specific to their region, to guarantee the integrity of their products.
Why Are Hand Blenders Important in Cosmetics Manufacturing?
Within the cosmetics industry, hand blenders are essential for mixing ingredients for creams and lotions. This process improves the texture and effectiveness of beauty products, which can significantly influence consumer satisfaction and brand loyalty. Buyers should consider sourcing from manufacturers that have strong research and development capabilities, as innovation in product formulation is key to maintaining competitive advantage.
How Are Hand Blenders Used in Agriculture?
In agriculture, hand blenders are utilized for mixing feed and supplements for livestock, enhancing the nutritional value and palatability of animal feed. This application not only promotes animal health but also optimizes feed efficiency, which is vital for sustainable farming practices. Buyers should evaluate the energy efficiency of the units they intend to source, as this can lead to long-term cost savings and a reduced carbon footprint.
Related Video: Vortex Ribbon Blender Overview
3 Common User Pain Points for ‘hand blender manufacturer’ & Their Solutions
Scenario 1: Difficulty in Sourcing Reliable Hand Blenders for Diverse Markets
The Problem:
B2B buyers from regions like Africa and South America often face significant challenges when sourcing hand blenders that meet the diverse requirements of their local markets. Variations in voltage standards, safety regulations, and consumer preferences can make it difficult to find a manufacturer that offers products suitable for their specific needs. For instance, a buyer in South Africa may struggle to find a hand blender that operates efficiently at 220V while also being compliant with local safety standards. This can lead to dissatisfaction among end-users and result in financial losses for the buyer.
The Solution:
To overcome these sourcing difficulties, buyers should prioritize working with manufacturers that have a proven track record in international markets. Engage with suppliers who can provide comprehensive product specifications, including voltage compatibility and compliance certifications for different regions. Additionally, consider establishing partnerships with manufacturers that offer customization options, allowing you to adapt products to suit local preferences. Conduct thorough market research to identify popular features in specific regions, and communicate these insights to your manufacturer for tailored solutions. Utilizing platforms that specialize in connecting international buyers with manufacturers can also streamline this process and enhance the chances of finding a suitable supplier.
Scenario 2: Ensuring Product Quality and Longevity
The Problem:
One of the most pressing concerns for B2B buyers is the quality and durability of hand blenders, especially in demanding kitchen environments. Buyers from the Middle East, where commercial kitchens often operate under intense conditions, may experience high failure rates with lower-quality products, leading to increased replacement costs and dissatisfied customers. The challenge lies in distinguishing between quality manufacturers and those offering subpar products.
The Solution:
To ensure product quality, buyers should conduct rigorous supplier evaluations before placing bulk orders. Request samples for testing in real-world conditions, and consider using third-party testing services to assess durability and performance. Additionally, look for manufacturers that provide warranties and guarantees, which can indicate a commitment to quality. Establishing clear communication with suppliers regarding quality standards and expectations is crucial. Consider leveraging industry certifications (like ISO or CE markings) as a benchmark for quality assurance. Regularly solicit feedback from end-users to identify any recurring issues and work collaboratively with manufacturers to address them.
Scenario 3: Navigating Supply Chain Disruptions
The Problem:
Supply chain disruptions can pose significant challenges for B2B buyers in Europe and Africa, especially in the wake of global events such as pandemics or geopolitical tensions. A buyer may find themselves facing delays in receiving shipments of hand blenders, which can impact their inventory and lead to lost sales opportunities. This unpredictability can complicate demand forecasting and inventory management.
The Solution:
To mitigate supply chain risks, buyers should diversify their supplier base to include manufacturers from different regions. This strategy can help ensure continuity in supply even if one source is disrupted. Implementing just-in-time inventory practices can also aid in managing stock levels more effectively, allowing for quicker response times to market changes. Additionally, maintaining open lines of communication with suppliers regarding their production schedules and capacity can provide valuable insights into potential delays. Utilizing technology such as supply chain management software can enhance visibility and facilitate better planning and forecasting, enabling buyers to make informed decisions and reduce the impact of disruptions.
Strategic Material Selection Guide for hand blender manufacturer
When selecting materials for hand blenders, manufacturers must consider a variety of factors that influence the performance, durability, and cost-effectiveness of the final product. Below, we analyze four common materials used in hand blender manufacturing, focusing on their properties, advantages, disadvantages, and specific considerations for international B2B buyers.
What are the Key Properties of Plastic in Hand Blenders?
Plastic, particularly high-density polyethylene (HDPE) and polycarbonate, is widely used for the body and components of hand blenders. These materials are lightweight, resistant to impact, and can be molded into complex shapes. They typically have a temperature rating of up to 80°C, making them suitable for blending hot liquids.
Pros: The primary advantages of plastic include its low cost and ease of manufacturing. It is also resistant to corrosion and can be produced in various colors, enhancing the aesthetic appeal of the product.
Cons: However, plastic is less durable than metal and may warp or degrade over time, especially with high-temperature exposure. Additionally, certain plastics may not be suitable for prolonged contact with acidic foods.
Impact on Application: Plastic is generally compatible with most food media, but manufacturers should ensure that the selected plastic complies with food safety standards, especially in regions with strict regulations.
How Does Stainless Steel Enhance the Performance of Hand Blenders?
Stainless steel is another popular choice, particularly for blades and some internal components. Known for its strength and resistance to corrosion, stainless steel can withstand high temperatures and pressures, making it ideal for commercial applications.
Pros: The durability of stainless steel ensures a longer lifespan for the product, and it is easy to clean, which is a significant advantage in food preparation environments. Additionally, it does not absorb odors or flavors.
Cons: The main drawbacks are the higher cost and the complexity of manufacturing stainless steel components compared to plastic. It is also heavier, which may affect the ergonomics of hand blenders.
Impact on Application: Stainless steel is highly compatible with various food types, including acidic and oily substances. Its robustness makes it suitable for both home and commercial use.
What Role Does Silicone Play in Hand Blender Design?
Silicone is increasingly used for seals and grips in hand blenders. This material is known for its flexibility, heat resistance (up to 200°C), and non-stick properties.
Pros: Silicone provides excellent grip, enhancing user comfort and safety. It is also resistant to high temperatures and does not react with food, making it an ideal choice for components that come into contact with hot liquids.
Cons: One limitation is that silicone can be more expensive than traditional plastics. Additionally, it may not be as durable in terms of mechanical stress compared to metals.
Impact on Application: Silicone is compatible with a wide range of food media and is particularly beneficial in ensuring that the blender remains safe and easy to handle during operation.
Why is Glass a Viable Option for Hand Blender Containers?
Glass is often used for blending containers due to its inert properties and ability to withstand high temperatures. It does not react with food, ensuring that flavors remain pure.
Pros: The main advantages of glass include its durability and aesthetic appeal. It is also dishwasher safe, making it easy to clean.
Cons: However, glass is heavier and more prone to breakage than plastic or metal, which can be a significant drawback in a kitchen environment. Additionally, the manufacturing process can be more complex and costly.
Impact on Application: Glass containers are suitable for all types of food media and are particularly favored in markets that prioritize product safety and purity.
Summary Table of Material Selection for Hand Blenders
Material | Typical Use Case for hand blender manufacturer | Key Advantage | Key Disadvantage/Limitation | Relative Cost (Low/Med/High) |
---|---|---|---|---|
Plastic | Body and components | Lightweight and cost-effective | Less durable, may warp over time | Low |
Stainless Steel | Blades and internal components | High durability and corrosion resistance | Higher cost and heavier | High |
Silicone | Seals and grips | Excellent grip and heat resistance | More expensive, less durable under stress | Medium |
Glass | Blending containers | Inert, durable, and aesthetically pleasing | Heavy and prone to breakage | Medium |
This guide provides international B2B buyers with actionable insights into material selection for hand blenders, ensuring compliance with local standards and preferences while optimizing product performance.
In-depth Look: Manufacturing Processes and Quality Assurance for hand blender manufacturer
What Are the Key Stages in the Manufacturing Process of Hand Blenders?
The manufacturing of hand blenders involves several critical stages that ensure the final product meets both performance and aesthetic standards. Understanding these stages can help international B2B buyers evaluate potential suppliers more effectively.
Material Preparation: What Materials Are Used in Hand Blender Manufacturing?
The first stage of manufacturing hand blenders involves selecting the right materials. Common materials include high-grade plastics for the body, stainless steel for blades, and rubber or silicone for grips. This stage is crucial as the quality of materials directly impacts the durability and performance of the product. Suppliers often use advanced materials that are resistant to wear and heat, ensuring the longevity of the hand blenders. Buyers should inquire about the specific grades of materials used and whether they meet international safety standards.
How Are Hand Blenders Formed and Shaped?
Following material preparation, the forming stage comes into play. This typically involves processes like injection molding for plastic components and stamping or die-cutting for metal parts. Precision in these processes is vital, as any deviation can affect the overall quality and functionality of the hand blender. Buyers should look for manufacturers that utilize modern machinery and technology to achieve tight tolerances, which are essential for the assembly of moving parts.
What Does the Assembly Process Entail?
The assembly stage is where various components come together. This process can be manual, automated, or a hybrid of both, depending on the manufacturer’s capabilities. Key components include the motor, blades, and housing. Quality control during assembly is paramount; hence, manufacturers often employ specialized fixtures and jigs to ensure proper alignment and fit. B2B buyers should assess whether the manufacturer has a streamlined assembly process that minimizes the risk of defects.
How Are Hand Blenders Finished for Market Readiness?
Finishing processes can include polishing, painting, or applying coatings to enhance appearance and resistance to stains and scratches. This stage may also involve packaging for shipment. Buyers should consider whether the finishing processes used by the manufacturer comply with international standards, as this can affect both aesthetics and functionality.
What Quality Assurance Protocols Are Essential for Hand Blender Manufacturers?
Quality assurance (QA) is a critical aspect of the manufacturing process for hand blenders. Implementing rigorous QA protocols helps ensure that the final product meets both domestic and international standards.
Which International Standards Should B2B Buyers Be Aware Of?
International standards such as ISO 9001 are fundamental for assessing the quality management systems of manufacturers. ISO 9001 certification indicates that a company adheres to consistent quality standards, thereby reducing risks for B2B buyers. Additionally, compliance with CE (Conformité Européenne) certification is crucial for products sold in Europe, ensuring that they meet safety, health, and environmental protection standards.
What Are the Key Quality Control Checkpoints in Manufacturing?
Quality Control (QC) checkpoints during the manufacturing process are critical to maintaining product integrity. Common checkpoints include:
- Incoming Quality Control (IQC): This involves inspecting raw materials before they enter the production line.
- In-Process Quality Control (IPQC): Inspections during the manufacturing process ensure that any defects are caught early.
- Final Quality Control (FQC): This is the last step before products are packaged and shipped, focusing on the overall functionality and appearance.
B2B buyers should confirm that their suppliers have established rigorous QC checkpoints throughout the manufacturing process.
What Common Testing Methods Are Used in Hand Blender Manufacturing?
Manufacturers typically employ various testing methods, including:
- Performance Testing: Evaluates the blender’s functionality, including motor strength and blade effectiveness.
- Durability Testing: Assesses how well the blender withstands wear and tear over time.
- Safety Testing: Ensures that the product complies with electrical safety standards and does not pose any hazards to users.
Buyers should ask suppliers for detailed testing protocols and results to ensure that products meet their requirements.
How Can B2B Buyers Verify Supplier Quality Control?
Verifying a supplier’s quality control measures is essential for B2B buyers. Here are some actionable steps:
What Audit Processes Should Buyers Implement?
Conducting regular audits of potential suppliers can help assess their manufacturing processes and quality assurance practices. Audits can be either announced or unannounced and should focus on both manufacturing capabilities and adherence to quality standards. Buyers from regions like Africa, South America, the Middle East, and Europe can benefit from third-party auditing services that provide unbiased evaluations of suppliers.
How Can Buyers Review Quality Control Reports?
Requesting access to quality control reports is another effective way to verify a manufacturer’s quality processes. These reports should detail inspection results, testing outcomes, and any corrective actions taken in response to identified issues. Such transparency can significantly enhance trust between buyers and suppliers.
Why Consider Third-Party Inspections for Quality Assurance?
Engaging third-party inspection services can provide an additional layer of assurance. These services offer independent verification of quality standards and can help identify potential risks in the supply chain. B2B buyers should consider incorporating this practice, especially when dealing with suppliers in regions with varying quality assurance practices.
What Are the Nuances of QC and Certification for International B2B Buyers?
Navigating the nuances of quality control and certification can be complex for international buyers, particularly those from Africa, South America, the Middle East, and Europe. Buyers should be aware of the specific certifications that apply to their markets and ensure that their suppliers are compliant. Additionally, understanding regional variations in standards can help buyers make informed decisions when sourcing hand blenders.
By focusing on these manufacturing processes and quality assurance practices, B2B buyers can enhance their sourcing strategies and ensure they partner with reliable suppliers in the hand blender market.
Practical Sourcing Guide: A Step-by-Step Checklist for ‘hand blender manufacturer’
In the competitive landscape of sourcing hand blenders, international B2B buyers must navigate a myriad of options while ensuring quality and compliance with regional standards. This practical sourcing guide provides a step-by-step checklist to facilitate informed decision-making and streamline the procurement process.
Step 1: Define Your Technical Specifications
Before initiating the sourcing process, it is essential to clearly outline your technical requirements. This includes specifications such as power ratings, blade materials, capacity, and design features. A well-defined set of specifications helps in communicating your needs effectively to potential suppliers, ensuring they can meet your expectations.
- Consider Industry Standards: Research any applicable industry standards for hand blenders in your region to ensure compliance.
- Identify Unique Selling Points: Determine what features will differentiate your product in the market, such as energy efficiency or ergonomic design.
Step 2: Conduct Market Research
Gather insights about the hand blender market specific to your target regions, such as Africa or South America. Understanding market trends, consumer preferences, and competitive products will inform your sourcing strategy.
- Utilize Online Resources: Leverage platforms like trade publications, market research reports, and industry forums.
- Network with Industry Peers: Engage with other businesses in your sector to gain firsthand knowledge about supplier performance and market dynamics.
Step 3: Evaluate Potential Suppliers
Thorough evaluation of suppliers is critical to ensure reliability and quality. Request comprehensive company profiles, including their manufacturing capabilities, certifications, and past performance.
- Review Client References: Ask for references from similar businesses to validate the supplier’s credibility.
- Examine Product Samples: Whenever possible, request samples to assess quality firsthand and determine if they meet your standards.
Step 4: Verify Supplier Certifications
Ensure that potential suppliers possess the necessary certifications that validate their compliance with international quality standards. Certifications such as ISO 9001, CE marking, or relevant safety certifications are crucial indicators of quality assurance.
- Ask for Documentation: Request copies of certifications and verify them with the issuing bodies if necessary.
- Understand Compliance Regulations: Familiarize yourself with the compliance requirements specific to your target market to avoid legal issues.
Step 5: Negotiate Terms and Conditions
Once you have shortlisted suppliers, it is time to negotiate pricing, payment terms, delivery schedules, and after-sales support. Clear communication during this phase can prevent misunderstandings later.
- Discuss Minimum Order Quantities (MOQs): Clarify MOQs and how they align with your inventory needs.
- Establish Clear Payment Terms: Agree on payment methods that are secure and convenient for both parties.
Step 6: Plan for Logistics and Supply Chain Management
Consider logistics and supply chain factors that may affect the timely delivery of your hand blenders. Evaluate the supplier’s shipping capabilities and the potential impact of tariffs or import duties.
- Assess Shipping Options: Explore various shipping methods to find the most cost-effective and timely solutions.
- Account for Local Regulations: Be aware of any import regulations or tariffs that may apply in your country to avoid unexpected costs.
Step 7: Monitor Supplier Performance Post-Purchase
After the procurement process, continuously monitor supplier performance to ensure they meet agreed-upon standards. Regular assessments can help maintain quality and foster long-term partnerships.
- Establish Key Performance Indicators (KPIs): Set metrics for evaluating delivery times, product quality, and customer service.
- Provide Feedback: Share your experiences with suppliers to encourage improvement and strengthen your business relationship.
By following this checklist, international B2B buyers can streamline their sourcing of hand blenders, ensuring they choose suppliers that align with their quality standards and market demands.
Comprehensive Cost and Pricing Analysis for hand blender manufacturer Sourcing
What Are the Key Cost Components in Sourcing Hand Blenders?
When sourcing hand blenders from manufacturers, understanding the cost structure is crucial for international B2B buyers. The primary cost components include:
-
Materials: The choice of materials significantly impacts the overall cost. Common materials include plastic, stainless steel, and electronic components. Prices can fluctuate based on global market conditions, so it’s essential to stay informed about trends in raw material pricing.
-
Labor: Labor costs vary by region, influenced by local wage standards and labor laws. For example, sourcing from countries with lower labor costs may initially seem appealing, but consider the potential trade-offs in quality and reliability.
-
Manufacturing Overhead: This includes all indirect costs associated with production, such as utilities, rent, and administrative expenses. Efficient manufacturers often have lower overhead costs, which can translate to better pricing for buyers.
-
Tooling: Initial tooling costs can be significant, especially for custom designs. Understanding the tooling requirements and amortization over production runs is essential for calculating the total cost.
-
Quality Control (QC): Ensuring quality through robust QC processes is non-negotiable. While it may add to costs, effective QC can prevent losses from defective products.
-
Logistics: Shipping and handling costs can vary greatly depending on the origin of the goods and the destination. Consider the implications of freight costs, import duties, and insurance when calculating total costs.
-
Margin: Manufacturers typically build a profit margin into their pricing. This margin can vary depending on market competition and the manufacturer’s brand positioning.
How Do Price Influencers Impact Hand Blender Sourcing Decisions?
Several factors can influence the pricing of hand blenders, and understanding these can help buyers negotiate better deals:
-
Volume and Minimum Order Quantity (MOQ): Larger orders often qualify for bulk pricing discounts. Understanding the MOQ for various suppliers can help buyers strategize their purchasing to maximize cost efficiency.
-
Specifications and Customization: Custom features or specific requirements can significantly affect the price. Buyers should clearly define their needs to avoid unexpected costs later in the process.
-
Materials and Quality Certifications: Higher-quality materials and certifications (like CE, RoHS) often lead to higher costs. Buyers should weigh the benefits of these certifications against their budget and market expectations.
-
Supplier Factors: The reputation and reliability of the supplier can also influence pricing. Established suppliers may charge more due to their proven track record, while newer entrants might offer lower prices to attract business.
-
Incoterms: Understanding Incoterms is crucial for international transactions. Terms like FOB (Free On Board) or CIF (Cost, Insurance, and Freight) can affect the total landed cost of the product.
What Are the Best Practices for Negotiating Prices with Hand Blender Manufacturers?
When negotiating prices with manufacturers, B2B buyers should consider the following tips:
-
Conduct Comprehensive Market Research: Understand the prevailing market rates for hand blenders to establish a baseline for negotiations. This knowledge can empower you to negotiate more effectively.
-
Focus on Total Cost of Ownership (TCO): Beyond the purchase price, consider the long-term costs associated with the product, including maintenance, warranty, and potential replacement costs. A higher initial investment may lead to lower TCO.
-
Leverage Relationships: Building strong relationships with suppliers can facilitate better negotiations. Trust and communication can lead to more favorable terms and pricing.
-
Be Prepared to Walk Away: If negotiations are not progressing favorably, be prepared to explore other suppliers. This attitude can often lead to better offers from your current suppliers.
-
Understand Pricing Nuances: Be aware of seasonal fluctuations and economic factors that could influence pricing. For example, demand spikes during holiday seasons can lead to price increases.
Disclaimer on Indicative Prices
Prices for hand blenders can vary significantly based on the factors discussed above. It is essential for buyers to conduct thorough research and obtain quotes from multiple suppliers to get a realistic view of current market pricing. Always consider local economic conditions and currency fluctuations when making purchasing decisions.
Alternatives Analysis: Comparing hand blender manufacturer With Other Solutions
When considering the best solutions for blending and mixing in various industrial applications, it’s essential to evaluate the potential alternatives to a hand blender manufacturer. These alternatives can provide different functionalities, efficiencies, and costs that may better suit the specific needs of B2B buyers, especially those operating in diverse markets such as Africa, South America, the Middle East, and Europe.
Comparison Table of Hand Blender Manufacturer vs. Alternative Solutions
Comparison Aspect | Hand Blender Manufacturer | Commercial Food Processor | Immersion Blender |
---|---|---|---|
Performance | High blending efficiency | Versatile with multi-functionality | Good for smaller batches |
Cost | Moderate investment | Higher initial cost | Lower cost option |
Ease of Implementation | Simple to use and install | Requires training for optimal use | User-friendly, minimal setup |
Maintenance | Low maintenance | Moderate maintenance needs | Very low maintenance |
Best Use Case | Small to medium batches | Large volume production | Quick blending tasks |
What Are the Pros and Cons of Using a Commercial Food Processor?
A commercial food processor is a powerful alternative to hand blenders, designed for high-capacity blending, chopping, and mixing.
Pros:
– Versatility: Offers multiple functions, including slicing, shredding, and pureeing, making it suitable for various culinary tasks.
– Efficiency: Capable of handling larger volumes of ingredients, which can be beneficial for restaurants and catering services.
Cons:
– Cost: Generally has a higher upfront cost compared to hand blenders, which may be a concern for smaller businesses.
– Complexity: Requires a bit of training to operate effectively, which could lead to longer onboarding for staff.
How Does an Immersion Blender Compare as a Solution?
An immersion blender, also known as a stick blender, is a compact and portable option for blending directly in pots or containers.
Pros:
– Affordability: Typically more budget-friendly, making it an attractive option for small businesses or startups.
– Ease of Use: Simple design allows for quick blending without the need for extensive training or setup.
Cons:
– Limited Capacity: Best suited for small batches, which may not meet the demands of larger operations.
– Performance: While effective, it may not achieve the same level of uniformity and texture as a commercial food processor or hand blender for certain applications.
How Can B2B Buyers Choose the Right Blending Solution?
When selecting the right blending solution, B2B buyers should assess their specific operational needs, including volume, frequency of use, and types of ingredients. Factors such as budget constraints, available space, and required functionality should also play a crucial role in the decision-making process. For businesses focused on small batch production or those with budget limitations, hand blenders or immersion blenders may be the most suitable. Conversely, for high-volume commercial operations, investing in a commercial food processor may yield better long-term benefits despite the higher initial cost. Ultimately, understanding the unique requirements of your operation will guide you in selecting the most effective blending solution for your business.
Essential Technical Properties and Trade Terminology for hand blender manufacturer
What Are the Key Technical Properties of Hand Blenders?
When evaluating hand blenders for manufacturing, understanding the technical properties is crucial for ensuring product quality and performance. Here are some essential specifications that B2B buyers should consider:
1. Material Grade
The material used in the construction of hand blenders significantly affects durability and safety. Common materials include stainless steel for blades (which resist corrosion) and BPA-free plastic for the body. Selecting high-grade materials can enhance product longevity and user satisfaction, making it essential for buyers to assess material specifications before procurement.
2. Motor Power
Motor power is typically measured in watts and directly influences the performance of the hand blender. A higher wattage usually indicates better blending efficiency and the ability to handle tougher ingredients. For instance, a motor with 400 watts or more is generally suitable for commercial applications. Understanding the power requirements helps buyers match the product to their specific usage needs.
3. Speed Settings
The number of speed settings available on a hand blender can significantly impact its versatility. Many models offer multiple speeds, allowing users to blend, chop, or puree at varying intensities. B2B buyers should consider how these settings align with their customers’ preferences and the types of food they intend to prepare.
4. Blade Design and Material
Blade design, including the number of blades and their shape, affects the blending efficiency and texture of the final product. Stainless steel is preferred for its sharpness and longevity. Understanding the blade configuration can help buyers assess whether the hand blender will meet their quality standards and customer expectations.
5. Tolerance and Safety Standards
Tolerance levels refer to the allowable variations in manufacturing that ensure parts fit together correctly. Compliance with safety standards, such as CE or UL certification, is also crucial. Buyers should confirm that the hand blenders meet the necessary regulations to avoid liability issues and ensure consumer safety.
What Are Common Trade Terms Used in the Hand Blender Industry?
Familiarity with industry terminology can streamline the procurement process and facilitate better communication between buyers and manufacturers. Here are some common trade terms that B2B buyers should know:
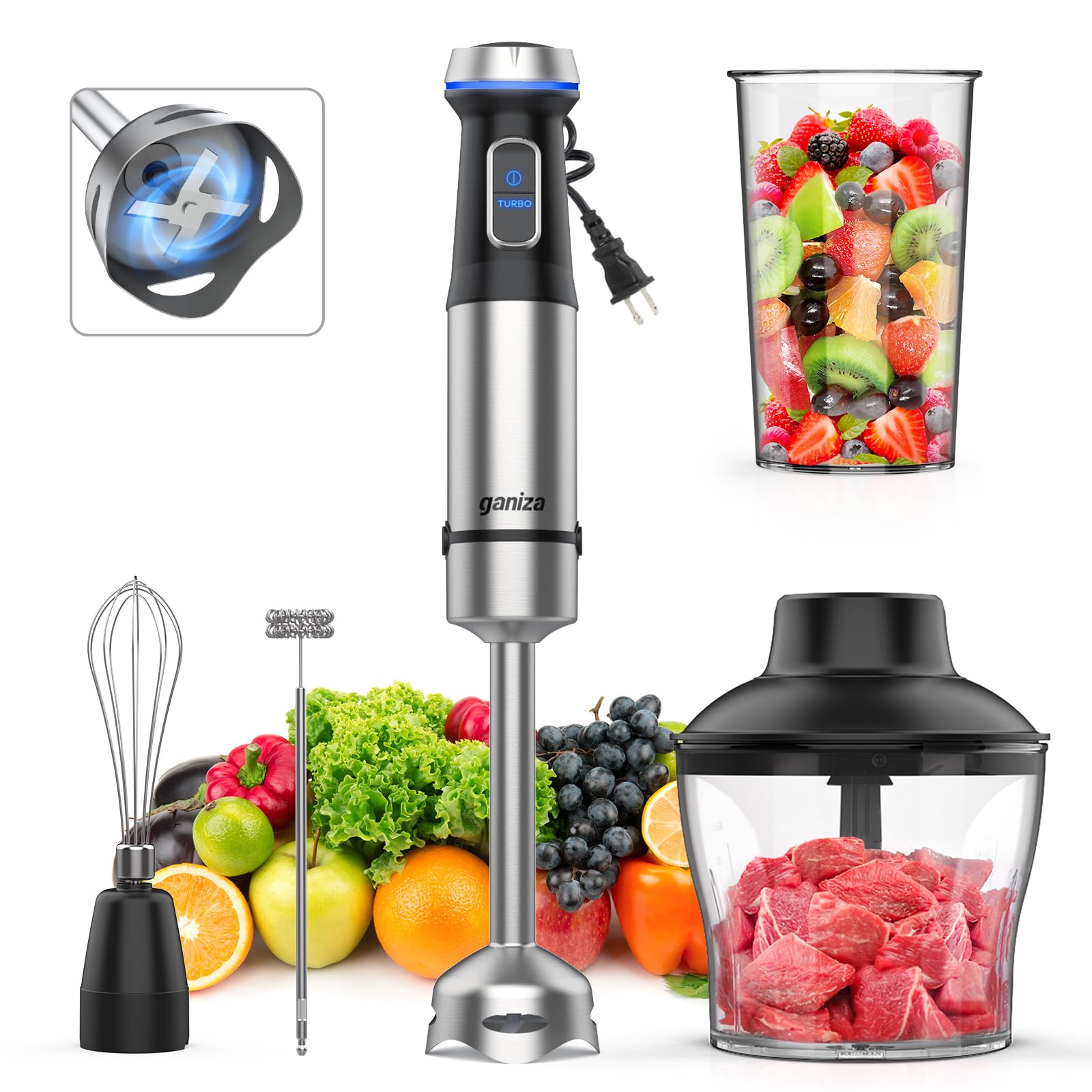
A stock image related to hand blender manufacturer.
1. OEM (Original Equipment Manufacturer)
OEM refers to a company that produces parts or equipment that may be marketed by another manufacturer. For hand blenders, this means that a buyer can source components from an OEM to create a branded product. Understanding OEM relationships can help buyers leverage manufacturing capabilities effectively.
2. MOQ (Minimum Order Quantity)
MOQ is the smallest amount of product a supplier is willing to sell. For hand blender manufacturers, MOQs can vary widely based on production capacity and material costs. Knowing the MOQ is essential for buyers to manage their inventory effectively and avoid overcommitting resources.
3. RFQ (Request for Quotation)
An RFQ is a document that buyers use to solicit price quotes from potential suppliers. This process allows buyers to compare pricing and terms across different manufacturers. For hand blenders, a detailed RFQ can help clarify specifications and ensure that all parties are aligned on expectations.
4. Incoterms (International Commercial Terms)
Incoterms define the responsibilities of buyers and sellers in international trade transactions. They specify who is responsible for shipping, insurance, and tariffs. Understanding these terms is vital for B2B buyers to manage logistics effectively and avoid unexpected costs.
5. Lead Time
Lead time refers to the amount of time it takes from placing an order to receiving the goods. For hand blenders, lead times can vary based on production schedules and shipping methods. Awareness of lead times helps buyers plan their inventory and ensure timely product availability.
By grasping these technical properties and trade terms, international B2B buyers can make informed decisions when sourcing hand blenders, ultimately leading to better product offerings and enhanced customer satisfaction.
Navigating Market Dynamics and Sourcing Trends in the hand blender manufacturer Sector
What Are the Current Market Dynamics and Key Trends in the Hand Blender Manufacturer Sector?
The hand blender manufacturing sector is experiencing significant growth driven by increasing consumer demand for convenient kitchen appliances and the rise of home cooking trends. International B2B buyers, particularly from Africa, South America, the Middle East, and Europe, are witnessing a shift towards multifunctional and compact appliances that cater to diverse culinary needs. Innovations such as cordless models, ergonomic designs, and advanced blending technologies are gaining traction, making them appealing to both retailers and end-users.
Moreover, the integration of smart technology in kitchen appliances is reshaping market dynamics. Features like Bluetooth connectivity, app integration, and programmable settings are becoming essential for modern consumers. For B2B buyers, this presents opportunities to partner with manufacturers who prioritize technological advancements, ensuring their product offerings are competitive and appealing to tech-savvy customers.
Emerging sourcing trends also reflect a growing preference for local suppliers to mitigate risks related to international logistics and tariffs. For buyers in regions such as South Africa and Spain, sourcing from local manufacturers not only reduces lead times but also supports regional economies. Collaborating with suppliers that demonstrate agility in adapting to market demands can lead to enhanced supply chain efficiency and product availability.
How Can Sustainability and Ethical Sourcing Impact B2B Relationships in the Hand Blender Sector?
Sustainability is becoming a crucial factor for B2B buyers in the hand blender manufacturing sector. Environmental concerns regarding plastic waste and energy consumption are prompting manufacturers to seek eco-friendly materials and production methods. Buyers are increasingly prioritizing suppliers who demonstrate a commitment to reducing their environmental impact, which can enhance brand reputation and customer loyalty.
Ethical sourcing is also essential in establishing trust between manufacturers and buyers. Companies that implement transparent supply chains and fair labor practices are more likely to attract international partners. Certifications such as Fair Trade and ISO 14001 not only validate a manufacturer’s commitment to sustainability but can also be a decisive factor for buyers looking to align with socially responsible brands.
Investing in “green” materials, such as biodegradable plastics or recycled components, can differentiate products in a crowded market. Buyers should actively seek partnerships with manufacturers who prioritize sustainability, as this will resonate with environmentally conscious consumers and meet regulatory requirements in various regions.
What Is the Brief Evolution of the Hand Blender Manufacturing Sector?
The hand blender, also known as an immersion blender, has evolved significantly since its inception in the 1950s. Initially designed for commercial kitchens, it gained popularity in domestic settings as home cooking surged in the late 20th century. The introduction of electric models revolutionized the market, offering consumers convenience and efficiency.
Over the decades, advancements in motor technology and ergonomic design have made hand blenders more user-friendly and versatile. Today, they are equipped with various attachments, allowing users to blend, chop, and puree with ease. This evolution reflects broader trends in consumer behavior, emphasizing convenience and multifunctionality, which continue to shape the landscape of the hand blender manufacturing sector. For B2B buyers, understanding this evolution can inform strategic sourcing decisions that align with current market demands.
Frequently Asked Questions (FAQs) for B2B Buyers of hand blender manufacturer
-
How do I evaluate the reliability of a hand blender manufacturer?
To evaluate the reliability of a hand blender manufacturer, start by checking their business credentials, such as ISO certifications and industry affiliations. Look for reviews and testimonials from other B2B buyers, especially those in your region. Conduct a factory audit if possible, and assess their production capabilities, quality control processes, and customer service responsiveness. Additionally, inquire about their experience in international trade, as this can significantly affect logistics and compliance with import regulations. -
What are the key features to consider when sourcing a hand blender?
When sourcing a hand blender, consider features such as motor power, blade quality, speed settings, and ergonomics. Assess whether the product meets safety standards relevant to your market, such as CE marking for Europe or FDA compliance for the U.S. Also, consider the blender’s ease of cleaning and whether it has a warranty or service agreement. Customization options can be a significant factor, so inquire about the ability to adjust designs to suit your brand or specific market needs. -
What is the minimum order quantity (MOQ) for hand blenders?
Minimum order quantities (MOQ) for hand blenders can vary significantly depending on the manufacturer and the specific model. Typically, MOQs range from 100 to 1,000 units. Discuss your requirements with potential suppliers to see if they can accommodate lower quantities, especially if you are a new business or entering a new market. Some manufacturers may offer flexible MOQs for first-time buyers or for bulk orders, so it’s worth negotiating. -
How can I ensure quality assurance when sourcing hand blenders?
To ensure quality assurance, ask potential manufacturers about their quality control processes. Request documentation of their testing methods, including any certifications for their products. It’s beneficial to request samples before placing a large order to evaluate the product firsthand. Additionally, consider implementing third-party inspections during production and before shipment to verify that the products meet your quality standards. -
What payment terms should I expect when purchasing hand blenders internationally?
Payment terms vary by manufacturer but typically include options like Letter of Credit, Advance Payment, or Net 30/60 days. It’s essential to clarify these terms upfront and ensure they align with your cash flow needs. Some suppliers may require a deposit upfront, especially for custom orders, while others might be open to more flexible arrangements for established clients. Always ensure that payment terms are documented in the contract to avoid misunderstandings. -
How do logistics and shipping work for hand blenders sourced from abroad?
Logistics for sourcing hand blenders internationally involve several steps, including selecting a shipping method (air or sea), customs clearance, and delivery to your location. Discuss shipping options with your supplier, as they may offer to handle logistics or recommend freight forwarders. Ensure you understand the Incoterms used in your agreement, as they dictate who is responsible for shipping costs and risks at various stages of the transportation process. -
What should I consider regarding warranty and after-sales support for hand blenders?
When sourcing hand blenders, inquire about the warranty period and what it covers, such as parts and labor. After-sales support is crucial for addressing issues that may arise post-purchase, so ensure the manufacturer has a responsive customer service team. Clarify how warranty claims are processed, the expected turnaround time for repairs, and whether they provide spare parts. Understanding these aspects will help you maintain customer satisfaction and brand reputation. -
How can I customize hand blenders to suit my market needs?
To customize hand blenders, discuss your specific requirements with manufacturers early in the sourcing process. Customization can include altering design, color, branding, and features based on your target market’s preferences. Some manufacturers offer design services to help you create a product that stands out. Be prepared to meet MOQs for customized products, and factor in additional lead times for production. It’s also wise to review market trends in your region to ensure your customizations align with consumer demand.
Important Disclaimer & Terms of Use
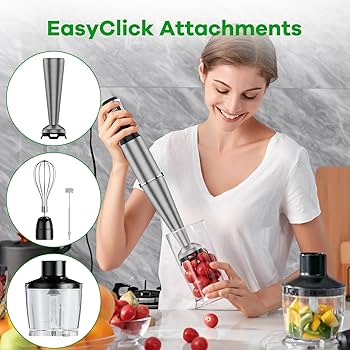
A stock image related to hand blender manufacturer.
⚠️ Important Disclaimer
The information provided in this guide, including content regarding manufacturers, technical specifications, and market analysis, is for informational and educational purposes only. It does not constitute professional procurement advice, financial advice, or legal advice.
While we have made every effort to ensure the accuracy and timeliness of the information, we are not responsible for any errors, omissions, or outdated information. Market conditions, company details, and technical standards are subject to change.
B2B buyers must conduct their own independent and thorough due diligence before making any purchasing decisions. This includes contacting suppliers directly, verifying certifications, requesting samples, and seeking professional consultation. The risk of relying on any information in this guide is borne solely by the reader.
Strategic Sourcing Conclusion and Outlook for hand blender manufacturer
In navigating the competitive landscape of hand blender manufacturing, strategic sourcing emerges as a pivotal factor for success. By focusing on key elements such as supplier reliability, product innovation, and cost-effectiveness, international B2B buyers can significantly enhance their procurement processes. Establishing strong relationships with manufacturers not only ensures consistent product quality but also fosters collaboration for future innovations, catering to the unique needs of diverse markets across Africa, South America, the Middle East, and Europe.
As buyers, understanding regional market dynamics and consumer preferences is essential. For instance, aligning product features with local demands can drive higher sales and customer satisfaction. Additionally, leveraging technology and data analytics during the sourcing process can unveil valuable insights, leading to more informed decision-making.
Looking ahead, the hand blender market is poised for growth, driven by advancements in technology and increasing consumer interest in culinary appliances. By prioritizing strategic sourcing practices, B2B buyers can position themselves to capitalize on emerging trends and maintain a competitive edge. Engage with reliable manufacturers today to explore innovative solutions that meet your business needs and drive sustainable growth in your markets.