Discover the Best Weight Scale Supplier: A Complete Guide (2025)
Introduction: Navigating the Global Market for weight scale supplier
Navigating the global market for weight scale suppliers can be a daunting task for B2B buyers, particularly when seeking reliable solutions that meet diverse needs across industries. From manufacturing to logistics, the demand for accurate and durable weight scales is pivotal. This guide is designed to assist international buyers, especially those from Africa, South America, the Middle East, and Europe, in overcoming common sourcing challenges while ensuring compliance with local regulations and standards.
In this comprehensive resource, we will delve into various types of weight scales, including industrial, digital, and portable options, as well as their applications in different sectors. We will also discuss essential factors to consider when vetting suppliers, such as certifications, customer reviews, and after-sales support. Additionally, we will explore cost considerations and how to negotiate favorable terms without compromising on quality.
By equipping buyers with the knowledge to make informed decisions, this guide aims to streamline the procurement process and foster successful partnerships with weight scale suppliers. Whether you are based in France, Germany, or any other region, understanding the nuances of the global weight scale market will empower you to secure the best products tailored to your specific requirements.
Understanding weight scale supplier Types and Variations
Type Name | Key Distinguishing Features | Primary B2B Applications | Brief Pros & Cons for Buyers |
---|---|---|---|
Mechanical Scales | Simple, no power required, often portable | Retail, agriculture, shipping | Pros: Low cost, easy to use. Cons: Limited precision, not suitable for heavy-duty use. |
Digital Scales | Electronic, often with advanced features like data storage | Warehousing, logistics, laboratories | Pros: High accuracy, easy to read. Cons: Requires power, potentially higher cost. |
Industrial Scales | Heavy-duty, designed for large weights and rough conditions | Manufacturing, construction, shipping | Pros: Robust, high capacity. Cons: Can be expensive, may require calibration. |
Load Cells | Sensor-based, used in various scales, can be integrated | Automated systems, conveyor belts | Pros: Highly accurate, versatile. Cons: Requires installation, may need specialized knowledge. |
Portable Scales | Lightweight, often battery-operated, designed for mobility | Fieldwork, transport, trade shows | Pros: Convenient, easy to transport. Cons: Limited capacity, may not be as durable. |
What Are Mechanical Scales and Their B2B Use Cases?
Mechanical scales are traditional weighing devices that operate without electricity, relying on springs or levers for measurement. They are commonly used in retail environments, agriculture, and shipping due to their portability and low cost. When purchasing mechanical scales, buyers should consider the scale’s capacity and ease of use, especially in environments where electricity may not be available.
How Do Digital Scales Enhance B2B Operations?
Digital scales employ electronic mechanisms to provide precise measurements and often feature advanced functions such as data storage and connectivity options. They are widely utilized in warehousing, logistics, and laboratories where accuracy is paramount. Buyers should focus on the scale’s resolution and functionality, including whether it meets specific industry standards for weight measurement.
What Are the Benefits of Industrial Scales for Heavy-Duty Applications?
Industrial scales are built to withstand harsh conditions and handle heavy loads, making them ideal for manufacturing, construction, and shipping industries. Their robustness and high weight capacity are significant advantages. Buyers should evaluate the scale’s durability and the cost of maintenance, as these scales may require regular calibration to maintain accuracy.
How Do Load Cells Function in Weighing Systems?
Load cells are sensors that convert force into an electrical signal, which can be used in various weighing systems. They are commonly integrated into automated systems and conveyor belts, offering high accuracy and versatility. When considering load cells, buyers should assess the compatibility with existing systems and the need for specialized installation or calibration expertise.
Why Choose Portable Scales for Field Applications?
Portable scales are designed for mobility, often battery-operated, and are perfect for fieldwork, transport, and trade shows. Their lightweight nature allows for easy transportation, making them ideal for businesses that require flexibility. Buyers should keep in mind the capacity limits and durability of these scales, as they may not withstand the same wear and tear as industrial models.
Related Video: Heavy duty Platform Weighing Scales Supplier For Industries
Key Industrial Applications of weight scale supplier
Industry/Sector | Specific Application of Weight Scale Supplier | Value/Benefit for the Business | Key Sourcing Considerations for this Application |
---|---|---|---|
Agriculture | Livestock Weight Management | Accurate monitoring for optimal feed and health management | Calibration standards, environmental resilience, and portability |
Food and Beverage | Ingredient Weighing for Production | Ensures consistency and quality in food products | Compliance with food safety regulations, hygiene standards, and precision |
Manufacturing | Raw Material Measurement | Facilitates inventory management and cost control | Load capacity, durability, and integration with existing systems |
Logistics and Shipping | Freight and Cargo Weighing | Reduces shipping costs and ensures compliance with regulations | Accuracy under varying conditions and certification for trade compliance |
Pharmaceuticals | Chemical and Drug Formulation | Guarantees precise dosing and formulation accuracy | Certification for pharmaceutical use, reliability, and traceability |
How is Weight Scale Supplier Used in Agriculture for Livestock Management?
In the agricultural sector, weight scale suppliers play a crucial role in livestock weight management. Accurate weight measurements allow farmers to monitor the health and growth of their animals, ensuring they receive the correct amount of feed. This practice not only optimizes feeding strategies but also enhances overall animal welfare. For international buyers, especially from regions like Africa and South America, sourcing scales that are portable and can withstand harsh environments is essential. Additionally, understanding local calibration standards is vital for compliance.
What Role Does Weight Scale Supplier Play in the Food and Beverage Industry?
In the food and beverage industry, weight scale suppliers are essential for ingredient weighing during production. Accurate measurements are critical to maintaining product consistency and adhering to quality standards. This is particularly important for B2B buyers in Europe, where food safety regulations are stringent. Suppliers must ensure that their scales meet hygiene standards and are capable of precise measurements to avoid costly production errors. International buyers should also consider local regulations regarding food safety to ensure compliance.
Why is Weight Measurement Important in Manufacturing?
Manufacturers rely on weight scale suppliers for raw material measurement to facilitate efficient inventory management. By accurately weighing materials, businesses can control costs and reduce waste, ultimately improving profitability. For international buyers, especially in Europe and the Middle East, sourcing scales that can handle high load capacities and are durable enough for industrial environments is crucial. Buyers should also seek suppliers who can provide integration options with their existing inventory management systems.
How Does Weight Scale Supplier Benefit Logistics and Shipping?
In logistics and shipping, weight scale suppliers are vital for freight and cargo weighing. Accurate weight measurements help businesses comply with shipping regulations and optimize costs by preventing overloading. For B2B buyers from Africa and South America, sourcing scales that maintain accuracy under varying conditions, such as humidity and temperature fluctuations, is essential. Additionally, ensuring that the scales are certified for trade compliance can prevent costly fines and delays.
What is the Importance of Weight Scale Supplier in Pharmaceuticals?
In the pharmaceutical industry, weight scale suppliers are critical for chemical and drug formulation. Precise dosing is essential for ensuring the efficacy and safety of medications. International buyers in this sector must prioritize sourcing scales that are certified for pharmaceutical use, ensuring reliability and traceability. Compliance with stringent pharmaceutical regulations in Europe and the Middle East is also a significant consideration, necessitating thorough research into suppliers’ certifications and quality assurance processes.
Related Video: LABORATORY APPARATUS AND THEIR USES
3 Common User Pain Points for ‘weight scale supplier’ & Their Solutions
Scenario 1: Inaccurate Weight Measurements Leading to Financial Losses
The Problem: A B2B buyer from a logistics company frequently encounters discrepancies in weight measurements from their weight scales. This issue arises from using outdated or poorly calibrated scales, resulting in inaccurate readings. Such inaccuracies can lead to overcharging clients or incurring unexpected costs due to weight-related penalties imposed by shipping companies. For companies in Africa and South America, where logistics networks may already face challenges, these financial losses can significantly impact profitability.
The Solution: To mitigate this problem, it’s crucial to invest in high-quality, reliable weight scales from reputable suppliers. When sourcing weight scales, buyers should prioritize suppliers who offer calibration services and demonstrate a commitment to maintaining the accuracy of their products. Regular calibration and maintenance of scales are essential; therefore, establishing a service agreement with the supplier for periodic checks can ensure ongoing accuracy. Additionally, buyers should train their staff on proper usage and calibration techniques to enhance the overall reliability of their measurements. Investing in advanced technology, such as digital scales with automatic calibration features, can also significantly reduce human error.
Scenario 2: Compliance with Regional Weight Regulations
The Problem: International buyers in Europe, particularly in countries like Germany and France, face stringent regulations regarding weight measurement for imported goods. Non-compliance can lead to fines, product returns, and damage to the company’s reputation. Many suppliers may not provide adequate documentation or support to ensure compliance with local laws, making it challenging for buyers to navigate these regulations.
The Solution: To address this challenge, buyers must choose suppliers who are knowledgeable about local regulations and can provide necessary certifications and documentation. Engaging with suppliers that have a proven track record in the specific markets you operate in is essential. Buyers should conduct thorough due diligence on potential suppliers to verify their compliance history and ask for references from other businesses within the same industry. Additionally, staying updated with local regulatory changes and implementing a robust compliance strategy that includes regular training for staff on regulatory requirements will help avoid costly compliance issues.
Scenario 3: Limited After-Sales Support and Training
The Problem: B2B buyers often experience frustration with the lack of after-sales support and training from weight scale suppliers. This is particularly common in the Middle East, where businesses may invest heavily in sophisticated weight scales but find themselves struggling to utilize these tools effectively due to inadequate training and support. As a result, buyers may not fully leverage the capabilities of their scales, leading to inefficient operations and potential downtime.
The Solution: To overcome this pain point, buyers should select suppliers who offer comprehensive after-sales support, including training sessions and technical assistance. Before finalizing a purchase, inquire about the training programs available and how the supplier plans to support your team post-purchase. Buyers should also consider establishing a clear communication channel with their suppliers for ongoing technical support. Furthermore, investing in suppliers that provide resources such as user manuals, online training videos, and customer service hotlines can empower your staff and ensure optimal utilization of the weight scales. Encouraging a culture of continuous learning within the organization will also help staff remain proficient in using the equipment effectively.
Strategic Material Selection Guide for weight scale supplier
When selecting materials for weight scales, international B2B buyers must consider various factors that impact performance, durability, and compliance with regional standards. Here, we analyze four common materials used in weight scales: stainless steel, aluminum, plastic, and cast iron. Each material has unique properties, advantages, and limitations that can significantly affect the end product’s suitability for different applications.
What Are the Key Properties of Stainless Steel for Weight Scales?
Stainless steel is renowned for its excellent corrosion resistance, high strength, and ability to withstand extreme temperatures. It typically has a temperature rating that can exceed 1000°F (537°C) and a pressure rating suitable for various industrial applications. The most common grades used in weight scales are 304 and 316, with 316 offering superior resistance to chlorides and other corrosive environments.
Pros and Cons of Stainless Steel
The primary advantage of stainless steel is its durability and longevity, making it ideal for heavy-duty applications. However, it is more expensive than other materials, which can impact the overall cost of the weight scale. Additionally, the manufacturing process can be complex, requiring specialized equipment and techniques.
Impact on Application
Stainless steel scales are compatible with a wide range of media, including food products, chemicals, and pharmaceuticals. This versatility makes them suitable for various industries, including food processing and pharmaceuticals.
Considerations for International Buyers
Buyers in regions such as Europe and the Middle East should ensure compliance with standards like ASTM and DIN, particularly in food-related applications where hygiene is critical.
How Does Aluminum Perform in Weight Scale Applications?
Aluminum is a lightweight, corrosion-resistant metal that is often used in portable weight scales. It has a lower temperature rating than stainless steel, typically around 600°F (316°C), and is not as strong under high pressure.
Pros and Cons of Aluminum
The key advantage of aluminum is its lightweight nature, which makes it ideal for portable applications. However, it is less durable than stainless steel and can be prone to deformation under heavy loads. The cost of aluminum is generally lower, making it an attractive option for budget-conscious buyers.
Impact on Application
Aluminum scales are suitable for applications where portability is essential, such as in logistics and shipping. However, they may not be suitable for environments with harsh chemicals or extreme temperatures.
Considerations for International Buyers
Buyers should be aware of the specific grades of aluminum used and their compliance with relevant standards, especially in industrial applications.
What Are the Advantages of Using Plastic in Weight Scales?
Plastic materials, particularly high-density polyethylene (HDPE) and polycarbonate, are used in weight scales designed for specific applications, such as laboratory environments or light-duty tasks. These materials offer good chemical resistance and are lightweight.
Pros and Cons of Plastic
The primary advantage of plastic is its cost-effectiveness and ease of manufacturing. However, it lacks the strength and durability of metals, making it unsuitable for heavy-duty applications. Additionally, plastic can be sensitive to temperature extremes, which may limit its use.
Impact on Application
Plastic scales are often used in laboratory settings or for weighing lightweight items. They are not ideal for industrial applications where heavy loads or harsh environments are present.
Considerations for International Buyers
Buyers should ensure that the plastic materials used meet safety and quality standards, particularly in sensitive applications like pharmaceuticals.
Why Choose Cast Iron for Weight Scales?
Cast iron is a traditional material used in weight scales, particularly in industrial applications. It offers excellent stability and is capable of withstanding high loads without deforming.
Pros and Cons of Cast Iron
The main advantage of cast iron is its durability and ability to provide accurate readings under heavy loads. However, it is heavy and can be prone to rust if not properly coated or maintained. The manufacturing process can also be more complex and costly.
Impact on Application
Cast iron scales are commonly used in industrial environments where heavy items need to be weighed. They are less suitable for portable applications due to their weight.
Considerations for International Buyers
Buyers should consider the maintenance requirements and ensure that the cast iron used complies with relevant standards to prevent rust and degradation.
Summary Table of Material Selection for Weight Scales
Material | Typical Use Case for weight scale supplier | Key Advantage | Key Disadvantage/Limitation | Relative Cost (Low/Med/High) |
---|---|---|---|---|
Stainless Steel | Heavy-duty industrial applications | Excellent durability and corrosion resistance | Higher cost and complex manufacturing | High |
Aluminum | Portable weight scales | Lightweight and cost-effective | Less durable under heavy loads | Medium |
Plastic | Laboratory and light-duty applications | Cost-effective and easy to manufacture | Limited strength and temperature resistance | Low |
Cast Iron | Industrial applications | High stability under heavy loads | Heavy and prone to rust | Medium |
This strategic material selection guide provides international B2B buyers with essential insights into the properties, advantages, and limitations of various materials used in weight scales, enabling informed decision-making tailored to specific applications and compliance requirements.
In-depth Look: Manufacturing Processes and Quality Assurance for weight scale supplier
What Are the Key Stages in the Manufacturing Process of Weight Scales?
The manufacturing of weight scales involves several critical stages that ensure precision and reliability. Understanding these stages can help B2B buyers from Africa, South America, the Middle East, and Europe make informed purchasing decisions.
1. Material Preparation
The first step involves selecting and preparing raw materials. Common materials for weight scales include high-grade stainless steel, aluminum, and specialized polymers. These materials are chosen for their durability, resistance to corrosion, and lightweight properties. Before production begins, materials undergo stringent quality checks to ensure they meet the required specifications and standards.
2. Forming Techniques
In the forming stage, manufacturers utilize techniques such as stamping, molding, and machining to shape the components of the weight scale. This process is crucial for creating the scale’s housing and internal mechanisms. Advanced technologies like CNC (Computer Numerical Control) machining are often employed to achieve high precision in component dimensions. For example, CNC technology allows for the creation of intricate parts that fit together seamlessly, which is essential for the accurate functioning of the scale.
3. Assembly Process
The assembly stage involves bringing together all the manufactured components. This step typically includes the installation of load cells, displays, and other electronic parts. Skilled technicians often conduct this process to ensure that each component is properly installed and calibrated. Additionally, manufacturers may use automated assembly lines for efficiency, especially in high-volume production settings.
4. Finishing Touches
Once assembled, the weight scales undergo finishing processes such as painting, coating, or surface treatment. These steps not only enhance the aesthetic appeal of the scales but also provide additional protection against environmental factors. For instance, a powder coating may be applied to improve durability and resistance to scratches and chemicals.
How Is Quality Assurance Implemented in Weight Scale Manufacturing?
Quality assurance (QA) is a critical aspect of the manufacturing process for weight scales. It ensures that the final product meets both customer expectations and regulatory standards.
Relevant International Standards for Quality Assurance
B2B buyers should be familiar with key quality standards that impact weight scale suppliers. ISO 9001 is a widely recognized standard that outlines quality management principles, including customer focus and continuous improvement. Other industry-specific certifications, such as CE marking for compliance with European health, safety, and environmental protection standards, may also be relevant.
What Are the Quality Control Checkpoints?
Quality control (QC) involves several checkpoints throughout the manufacturing process:
- Incoming Quality Control (IQC): This initial checkpoint focuses on raw materials. Suppliers must provide documentation proving that materials meet specified standards.
- In-Process Quality Control (IPQC): This occurs during the manufacturing process. Operators monitor key parameters and perform tests to ensure that production remains within specified tolerances.
- Final Quality Control (FQC): After assembly, weight scales undergo comprehensive testing to verify their accuracy and functionality. This includes load tests, calibration checks, and performance evaluations.
What Testing Methods Are Commonly Used for Weight Scales?
Testing is essential to ensure the accuracy and reliability of weight scales. Common methods include:
- Load Testing: This evaluates the scale’s ability to handle specified weights without failure. It helps in determining the maximum capacity and ensures the scale does not deviate from its specifications under load.
- Calibration Testing: This process ensures that the scale provides accurate readings. Calibration involves comparing the scale’s measurements against a standard reference and making necessary adjustments.
- Environmental Testing: This assesses how well the scales perform under various environmental conditions, such as humidity and temperature fluctuations.
How Can B2B Buyers Verify Supplier Quality Control?
B2B buyers should take proactive steps to verify the quality control practices of potential weight scale suppliers. Here are some recommended approaches:
Conducting Supplier Audits
Buyers can perform on-site audits of suppliers to assess their manufacturing processes, quality control measures, and compliance with international standards. During these audits, buyers should look for documented procedures, quality certifications, and evidence of regular testing.
Reviewing Quality Reports
Requesting quality assurance reports from suppliers is essential. These reports should detail the results of various tests conducted on the weight scales, including IQC, IPQC, and FQC results.
Utilizing Third-Party Inspections
Engaging third-party inspection agencies can provide an unbiased assessment of the supplier’s quality control practices. These agencies can conduct inspections at various stages of the manufacturing process and provide detailed reports on compliance with standards.
What Are the Nuances of Quality Control for International Buyers?
B2B buyers from different regions, particularly Africa, South America, the Middle East, and Europe, should be aware of specific quality control nuances that may affect their purchasing decisions:
- Regional Compliance Standards: Different regions may have unique compliance standards and regulations. For instance, Europe has strict CE marking requirements, while other regions may have their own regulatory frameworks.
- Cultural Considerations: Understanding cultural differences in business practices can help buyers communicate effectively with suppliers and ensure that quality expectations are met.
- Logistical Challenges: When sourcing from international suppliers, buyers should consider the logistics of transporting weight scales, including potential delays and customs regulations that could impact quality assurance.
By paying attention to these manufacturing processes and quality assurance practices, international B2B buyers can make more informed decisions when selecting weight scale suppliers, ensuring they receive high-quality products that meet their operational needs.
Practical Sourcing Guide: A Step-by-Step Checklist for ‘weight scale supplier’
In the global marketplace, sourcing a reliable weight scale supplier is critical for businesses aiming to enhance their operational efficiency and product quality. This checklist serves as a comprehensive guide for international B2B buyers from regions such as Africa, South America, the Middle East, and Europe. Following these steps will help ensure that you select a supplier who meets your specific needs and standards.
Step 1: Define Your Technical Specifications
Establishing clear technical specifications is the foundation of effective procurement. Determine the type of weight scales you need—be it digital, mechanical, or specialized for particular industries (e.g., food, pharmaceuticals). Ensure you consider factors such as load capacity, precision, and compliance with local regulations.
- Load Capacity: Assess the maximum weight the scale must handle.
- Precision Requirements: Identify the level of accuracy required for your operations.
Step 2: Research Potential Suppliers
Conduct thorough research to identify potential weight scale suppliers. Utilize online platforms, trade shows, and industry directories to compile a list of candidates. Look for suppliers that have a proven track record and positive customer reviews.
- Online Reviews: Check platforms like Trustpilot or industry-specific forums.
- Supplier History: Investigate how long they have been in the business and their market reputation.
Step 3: Verify Supplier Certifications
Before engaging with a supplier, verify that they possess necessary certifications and compliance with international standards. Certifications such as ISO 9001 or specific industry-related certifications are indicators of quality management practices.
- ISO Certification: Indicates adherence to quality management systems.
- Local Compliance: Ensure they meet local regulatory requirements relevant to your industry.
Step 4: Request Product Samples
Always request product samples before finalizing your order. This allows you to evaluate the quality, functionality, and suitability of the weight scales for your specific needs.
- Testing: Assess the scale’s performance in real-life conditions relevant to your business.
- Comparative Analysis: If possible, compare samples from multiple suppliers to make an informed decision.
Step 5: Assess After-Sales Support and Warranty
A supplier’s commitment to after-sales support can significantly impact your experience. Confirm the warranty period offered and what it covers, including repairs and maintenance services.
- Response Time: Inquire about their average response time for support requests.
- Service Plans: Look for suppliers that offer extended service plans or maintenance contracts.
Step 6: Negotiate Pricing and Terms
Once you have identified a suitable supplier, enter into negotiations regarding pricing and contract terms. Consider bulk purchasing discounts, payment terms, and delivery timelines.
- Transparent Pricing: Ensure that all costs are clearly outlined, including shipping and handling.
- Flexible Payment Options: Discuss payment terms that suit your financial capacity and cash flow.
Step 7: Establish Clear Communication Channels
Effective communication is essential for a successful supplier relationship. Establish clear channels for ongoing communication to facilitate smooth transactions and address any issues promptly.
- Regular Updates: Set expectations for regular updates on order status and delivery timelines.
- Point of Contact: Designate a primary contact person for both parties to streamline communication.
By following this step-by-step checklist, international B2B buyers can confidently navigate the sourcing process for weight scale suppliers, ensuring that they choose a partner that meets their quality, performance, and service expectations.
Comprehensive Cost and Pricing Analysis for weight scale supplier Sourcing
What Are the Key Cost Components in Sourcing Weight Scales?
When sourcing weight scales, understanding the cost structure is crucial for international B2B buyers. The primary cost components include:
-
Materials: The choice of materials significantly affects the cost. High-quality materials, such as stainless steel or specialized polymers, can increase the upfront price but enhance durability and accuracy.
-
Labor: Labor costs vary by region. Countries in Europe may have higher labor costs compared to manufacturers in Africa or South America, impacting the overall pricing of weight scales.
-
Manufacturing Overhead: This encompasses the indirect costs associated with production, including utilities, rent, and administrative expenses. Efficient manufacturing processes can lower overhead costs, leading to more competitive pricing.
-
Tooling: Investment in tooling for custom designs can be substantial. Buyers should consider whether standard models meet their needs or if custom tooling is necessary, which will increase costs.
-
Quality Control (QC): Implementing rigorous QC processes ensures that the scales meet international standards. This can add to the cost but is vital for maintaining product integrity and trustworthiness.
-
Logistics: Shipping costs can fluctuate based on the Incoterms used, the distance from the supplier, and the shipping method. Understanding these factors can help buyers budget accurately.
-
Margin: Suppliers typically include a profit margin that reflects their operational efficiency and market positioning. It’s essential to evaluate whether the margin is justified based on the quality and service provided.
How Do Price Influencers Affect Weight Scale Sourcing?
Several factors can influence the pricing of weight scales:
-
Volume/MOQ (Minimum Order Quantity): Ordering in bulk often leads to discounts. Buyers should assess their needs to negotiate favorable terms based on expected volume.
-
Specifications and Customization: Customized scales, tailored to specific industry requirements, will generally incur additional costs. Buyers need to balance customization benefits against the potential price increase.
-
Material Quality and Certifications: Scales that meet specific quality standards or certifications (like ISO) may have a higher price tag. However, these certifications can enhance marketability and compliance.
-
Supplier Factors: The reliability and reputation of the supplier can influence pricing. Established suppliers with a track record may charge more, but they often provide better support and warranty options.
-
Incoterms: The chosen Incoterms can significantly impact total costs. For example, choosing Ex Works (EXW) may lower the purchase price but increase logistics costs for the buyer.
What Are the Best Tips for Negotiating Weight Scale Prices?
Negotiating effectively can lead to significant savings:
-
Understand Total Cost of Ownership (TCO): Look beyond the purchase price. Consider maintenance, operational costs, and potential downtimes. A lower initial cost may result in higher long-term expenses.
-
Leverage Supplier Relationships: Building strong relationships with suppliers can lead to better pricing and terms. Regular communication and feedback can enhance partnerships.
-
Benchmark Pricing: Research market prices for similar products to provide leverage during negotiations. This data can help justify your pricing expectations.
-
Be Aware of Cultural Nuances: Different regions have varied negotiation styles. For example, buyers in Europe may expect more formal negotiations than those in Africa or South America. Adapting to these cultural differences can facilitate smoother discussions.
-
Request Samples: Before committing to a large order, request samples to evaluate quality. This can also be a negotiation point if the supplier’s product does not meet expectations.
Conclusion
Understanding the cost structure and pricing influences when sourcing weight scales is essential for international B2B buyers. By being informed about the components involved and leveraging negotiation strategies, buyers can optimize their sourcing decisions, ensuring they achieve the best value for their investments.
- Disclaimer: Prices mentioned in this analysis are indicative and may vary based on specific supplier agreements, market conditions, and regional factors.*
Alternatives Analysis: Comparing weight scale supplier With Other Solutions
Understanding Alternative Solutions to Weight Scale Suppliers
When it comes to selecting a weight measurement solution, B2B buyers often face a multitude of options. While weight scale suppliers offer specialized products tailored for precise weight measurement, there are alternative technologies and methods that can meet similar needs. This section will compare weight scale suppliers with two viable alternatives: load cells and RFID-based weight tracking systems. Each option presents unique advantages and limitations that can significantly influence a buyer’s decision-making process.
Comparison Aspect | Weight Scale Supplier | Load Cells | RFID-Based Weight Tracking Systems |
---|---|---|---|
Performance | High accuracy and reliability for static weights | Excellent for dynamic measurements; can be highly accurate | Good for tracking weight changes; less precise for static weights |
Cost | Moderate to high; varies with features and capacity | Generally lower; cost-effective for large-scale applications | Higher initial investment due to technology costs |
Ease of Implementation | Straightforward installation with minimal training | Requires calibration and integration into existing systems | Complex setup; training needed for effective use |
Maintenance | Low; periodic calibration recommended | Moderate; requires regular checks and recalibration | Low; minimal maintenance post-installation |
Best Use Case | Ideal for retail, shipping, and industrial applications | Best for production lines and dynamic weighing scenarios | Effective for logistics and inventory management in large warehouses |
What Are the Pros and Cons of Load Cells as an Alternative?
Load cells are transducers that convert force or weight into an electrical signal. They are widely used in various industrial applications due to their versatility.
Pros:
– Dynamic Measurement: Load cells excel in situations where weights fluctuate, such as in conveyor systems.
– Cost-Effectiveness: They often have a lower upfront cost compared to traditional weight scales, especially in bulk applications.
Cons:
– Calibration Needs: Load cells require regular calibration to maintain accuracy, which can increase operational downtime.
– Integration Complexity: They may necessitate additional integration work with existing systems, leading to potential complications during implementation.
How Do RFID-Based Weight Tracking Systems Compare?
RFID-based weight tracking systems utilize radio-frequency identification technology to monitor the weight of items in real-time. This method is particularly advantageous for supply chain and inventory management.
Pros:
– Real-Time Data: RFID systems provide continuous weight tracking, which can enhance inventory management and reduce losses.
– Automation Potential: These systems can be integrated into automated environments, streamlining operations.
Cons:
– Higher Initial Costs: The technology involved in RFID systems can lead to a significant initial investment.
– Less Precision for Static Weights: RFID systems may not offer the same level of precision as traditional weight scales for static measurements.
How Can B2B Buyers Choose the Right Solution?
When selecting a weight measurement solution, B2B buyers must assess their specific requirements, including the nature of their operations, budget constraints, and the level of accuracy needed. For businesses focused on precise, static measurements, weight scale suppliers may be the best choice. Conversely, companies needing dynamic measurements or real-time tracking might benefit more from load cells or RFID-based systems. Ultimately, the right choice depends on aligning the selected technology with the operational goals and challenges of the business. By carefully considering these factors, buyers can ensure they invest in a solution that meets their needs effectively.
Essential Technical Properties and Trade Terminology for weight scale supplier
What Are the Essential Technical Properties of Weight Scales?
Understanding the technical properties of weight scales is crucial for international B2B buyers. These specifications not only affect the performance of the scales but also influence purchasing decisions based on operational needs and regulatory compliance.
1. Material Grade: Why Is It Important for Durability?
The material grade of a weight scale often determines its durability and accuracy. Common materials include stainless steel and aluminum, each with unique properties. Stainless steel offers corrosion resistance and strength, making it ideal for industrial environments. Aluminum is lighter but may not provide the same level of durability. Selecting the right material grade is essential for long-term investment and operational efficiency.
2. Capacity: How Does It Affect Your Business Operations?
Capacity refers to the maximum weight that a scale can measure. This specification is crucial for businesses that handle heavy loads. For instance, a scale with a capacity of 500 kg is unsuitable for a company regularly weighing items over this limit. Ensure that the scale’s capacity aligns with your specific operational needs to avoid inaccurate readings and potential damage to the equipment.
3. Tolerance: What Does It Mean for Precision?
Tolerance is the allowable deviation from a specified weight. A scale with a high tolerance (e.g., ±0.01 kg) is critical in industries like pharmaceuticals, where precise measurements are essential for compliance and safety. Understanding tolerance levels helps buyers select scales that meet their accuracy requirements, ensuring quality control throughout the supply chain.
4. Calibration: Why Is Regular Calibration Necessary?
Calibration refers to the process of adjusting the scale to ensure accurate measurements. Regular calibration is necessary to maintain compliance with industry standards and regulations. Buyers should consider whether the supplier offers calibration services and what the recommended calibration frequency is, as this can impact overall operational efficiency and product quality.
5. Display Technology: How Does It Enhance User Experience?
The type of display technology used in weight scales can significantly enhance user experience. Digital displays provide clear readings and may include features like backlighting and connectivity options for data transfer. In contrast, analog displays may be less user-friendly. Choosing a scale with intuitive display technology can improve workflow efficiency and reduce human error.
What Are Common Trade Terms in the Weight Scale Industry?
Familiarizing yourself with industry jargon is essential for effective communication and negotiation with suppliers.
1. OEM: What Does It Mean for Customization?
OEM stands for Original Equipment Manufacturer. This term refers to companies that produce equipment that is sold under another company’s brand. Understanding OEM relationships can help buyers negotiate better terms and ensure they receive quality products tailored to their specifications.
2. MOQ: How Does Minimum Order Quantity Impact Your Purchase?
MOQ, or Minimum Order Quantity, is the smallest quantity of product a supplier is willing to sell. This term is crucial for budgeting and inventory management. Buyers should clarify MOQs with suppliers to ensure that they can meet their purchasing needs without overcommitting resources.
3. RFQ: Why Is a Request for Quotation Important?
An RFQ, or Request for Quotation, is a document sent to suppliers asking for price quotes on specific products or services. This process is essential for cost comparison and helps buyers make informed decisions based on pricing and terms.
4. Incoterms: How Do They Affect Shipping and Delivery?
Incoterms, or International Commercial Terms, are standardized trade terms that define the responsibilities of buyers and sellers in international transactions. Understanding these terms is vital for managing shipping costs, delivery timelines, and liability. Familiarity with Incoterms can help buyers negotiate better shipping agreements.
5. Lead Time: What Should You Expect for Delivery?
Lead time refers to the time taken from placing an order to receiving the goods. This term is crucial for planning and inventory management. Buyers should inquire about lead times when negotiating with suppliers to ensure they align with their operational schedules.
By understanding these technical properties and trade terms, international B2B buyers can make more informed decisions when sourcing weight scales, ultimately improving operational efficiency and compliance.
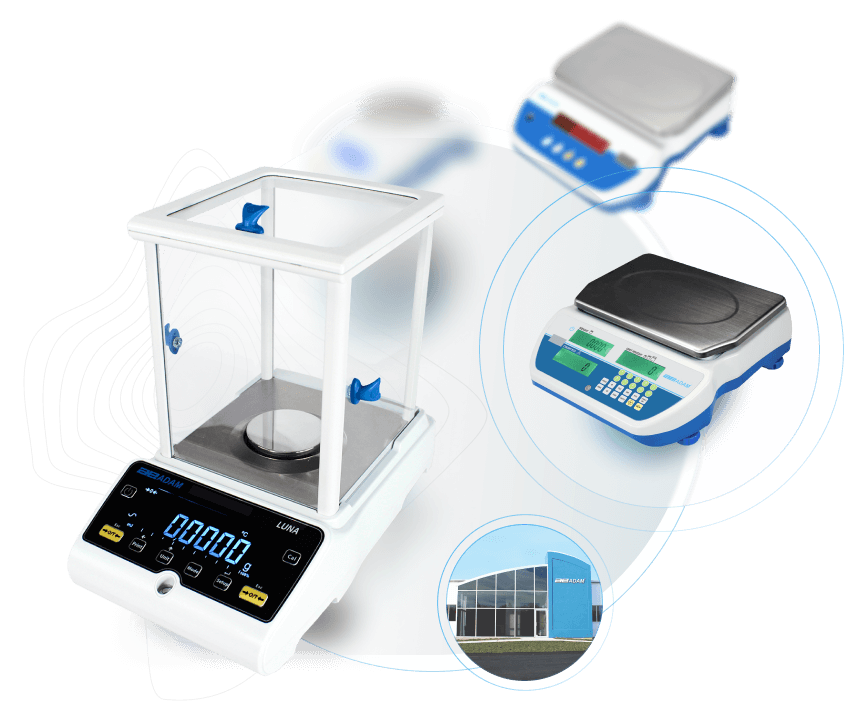
A stock image related to weight scale supplier.
Navigating Market Dynamics and Sourcing Trends in the weight scale supplier Sector
What Are the Current Market Dynamics and Key Trends in the Weight Scale Supplier Sector?
The weight scale supplier sector is experiencing significant shifts driven by technological advancements, increased demand for precision measurement, and evolving regulatory standards. Global drivers such as the rise of e-commerce and the need for accurate weight measurements in logistics are pushing suppliers to innovate. For international B2B buyers, particularly in Africa, South America, the Middle East, and Europe, understanding these dynamics is crucial for making informed sourcing decisions.
Emerging technologies, such as IoT-enabled scales and digital weighing solutions, are becoming increasingly popular. These innovations not only enhance accuracy but also facilitate real-time data collection, which is invaluable for inventory management and operational efficiency. Buyers should pay close attention to suppliers offering integrated solutions that align with Industry 4.0 standards, enabling seamless connectivity with other systems.
Furthermore, market dynamics are influenced by regional regulations, particularly in Europe, where compliance with strict standards is mandatory. Buyers from France and Germany, for example, should ensure that potential suppliers adhere to CE marking requirements, which signify conformity with health, safety, and environmental protection standards. The trend towards automation in manufacturing and warehousing also underscores the importance of selecting suppliers who can provide scalable solutions that meet future demands.
How Is Sustainability Influencing Sourcing Decisions for Weight Scale Suppliers?
Sustainability is becoming a cornerstone of sourcing strategies in the weight scale supplier sector. B2B buyers are increasingly recognizing the environmental impact of their supply chains and are seeking suppliers that prioritize sustainable practices. This shift is not only driven by regulatory pressures but also by consumer demand for ethically sourced products.
Ethical sourcing includes the use of environmentally friendly materials and processes. Buyers should look for suppliers that offer ‘green’ certifications, such as ISO 14001 for environmental management or certifications from recognized organizations that promote sustainable practices. This not only enhances the brand image but can also lead to cost savings in the long run through energy-efficient practices and reduced waste.
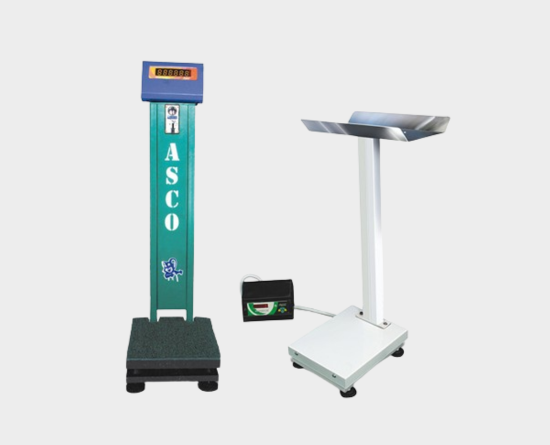
A stock image related to weight scale supplier.
Furthermore, as the global market shifts towards circular economies, suppliers are encouraged to adopt practices that minimize waste and promote recycling. For instance, weight scales made from recyclable materials or those designed for longevity can significantly reduce the environmental footprint. Buyers should engage with suppliers who demonstrate a commitment to sustainability, ensuring that their sourcing decisions align with global environmental goals.
How Has the Weight Scale Supplier Sector Evolved Over Time?
The weight scale supplier sector has evolved considerably over the last few decades, transitioning from basic mechanical scales to sophisticated digital solutions. Historically, weight measurement was often a manual process, reliant on mechanical components that required frequent calibration and maintenance. However, the introduction of electronic weighing systems revolutionized the industry by providing greater accuracy and ease of use.
In recent years, the integration of digital technology has further transformed the sector. The rise of data analytics and IoT has enabled weight scales to become part of larger automated systems, offering real-time insights into inventory levels and operational efficiency. This evolution is crucial for B2B buyers as it opens up new opportunities for improved supply chain management and operational effectiveness.
As the industry continues to advance, international buyers must remain informed about the latest technological developments and market trends to leverage these innovations effectively. Understanding the historical context of the weight scale supplier sector can provide valuable insights into current and future sourcing strategies.
Frequently Asked Questions (FAQs) for B2B Buyers of weight scale supplier
-
How do I determine the right weight scale supplier for my business needs?
To identify the ideal weight scale supplier, first, assess your specific requirements, such as the type of scales (e.g., digital, mechanical, or industrial), capacity, and accuracy needed for your operations. Research potential suppliers by reviewing their product catalogs, certifications, and industry experience. Request samples or demonstrations to evaluate the quality and functionality of their scales. Additionally, consider suppliers with strong customer service and after-sales support, especially for international transactions. -
What factors should I consider when evaluating the quality of weight scales?
Quality evaluation of weight scales should include factors like precision, durability, and compliance with international standards (e.g., ISO, OIML). Look for certifications that ensure product reliability. Testing scales under real operating conditions can also provide insights into their performance. Furthermore, consider the warranty and return policies, as these can indicate the manufacturer’s confidence in their product quality. -
What are common payment terms offered by weight scale suppliers?
Payment terms can vary widely among weight scale suppliers. Common options include upfront payment, a deposit with the balance due upon delivery, or net payment terms (e.g., Net 30, Net 60). For international purchases, it’s crucial to discuss terms that mitigate risks, such as using letters of credit or escrow services. Always clarify any potential additional fees for currency conversion or international transactions to avoid unexpected costs. -
What is the typical minimum order quantity (MOQ) for weight scales?
Minimum order quantities (MOQs) for weight scales can vary based on the supplier and the scale type. Generally, MOQs can range from a single unit for customized scales to several dozen for standard models. When negotiating with suppliers, inquire about flexibility in MOQs, especially if you are a smaller business or testing new products. Some suppliers may offer lower MOQs for trial orders, which can be beneficial for assessing product fit. -
How can I customize weight scales to suit my business requirements?
Many weight scale suppliers offer customization options, allowing you to tailor scales to your specific needs. Customizations may include modifications in size, display features, weighing capacities, and software integrations. When approaching suppliers, clearly communicate your requirements and ask for examples of previous custom work. Ensure that the supplier can meet your deadlines and quality standards during the customization process. -
What logistics considerations should I keep in mind when importing weight scales?
When importing weight scales, consider shipping methods, customs regulations, and import duties that may apply. Work with suppliers who have experience in international shipping to navigate logistics smoothly. Additionally, confirm the delivery timelines and shipping insurance options to protect your investment. Understanding local regulations in your destination country regarding weight scales is also crucial to ensure compliance. -
How do I ensure quality assurance for weight scales purchased internationally?
To ensure quality assurance for internationally purchased weight scales, request detailed product specifications and certifications from the supplier. Conduct factory audits, if possible, to inspect manufacturing processes. Implement a quality control plan that includes pre-shipment inspections and testing upon receipt. Establish clear communication channels with the supplier for addressing any quality concerns post-purchase. -
What are the key features to look for in a weight scale for industrial use?
For industrial applications, focus on features such as high weight capacity, durability under harsh conditions, and advanced functionalities like tare weight, data logging, and connectivity options (e.g., Bluetooth, USB). Ensure the scale has a robust design to handle frequent use and possible environmental challenges. Additionally, consider ease of calibration and maintenance to ensure long-term reliability and accuracy in your operations.
Important Disclaimer & Terms of Use
⚠️ Important Disclaimer
The information provided in this guide, including content regarding manufacturers, technical specifications, and market analysis, is for informational and educational purposes only. It does not constitute professional procurement advice, financial advice, or legal advice.
While we have made every effort to ensure the accuracy and timeliness of the information, we are not responsible for any errors, omissions, or outdated information. Market conditions, company details, and technical standards are subject to change.
B2B buyers must conduct their own independent and thorough due diligence before making any purchasing decisions. This includes contacting suppliers directly, verifying certifications, requesting samples, and seeking professional consultation. The risk of relying on any information in this guide is borne solely by the reader.
Strategic Sourcing Conclusion and Outlook for weight scale supplier
What Are the Key Takeaways for Strategic Sourcing in Weight Scale Procurement?
In the dynamic landscape of weight scale procurement, international B2B buyers must prioritize strategic sourcing to optimize their supply chain efficiency and cost-effectiveness. Understanding the nuances of gross weight versus net weight, along with the implications of quality metrics like w/w (weight by weight), can significantly impact purchasing decisions. Buyers from Africa, South America, the Middle East, and Europe should leverage local and global supplier networks to enhance product quality while ensuring compliance with regional regulations.
How Can Buyers Enhance Their Strategic Sourcing Practices?
By fostering strong relationships with weight scale suppliers, businesses can negotiate better pricing, secure favorable terms, and gain insights into emerging technologies. Establishing a clear communication channel with suppliers allows for timely updates on product innovations and shifts in market demand, which is crucial in maintaining a competitive edge.
What Is the Future Outlook for Weight Scale Suppliers?
Looking ahead, the integration of advanced technologies such as IoT and AI into weight scale systems will redefine operational efficiencies and data accuracy. As sustainability becomes a global priority, suppliers that innovate in eco-friendly practices will be more appealing to buyers. International B2B buyers are encouraged to stay informed about these trends and proactively engage with suppliers to position themselves for future success. Take action today by evaluating your sourcing strategies and exploring new partnerships that align with your business goals.