Discover Top Acoustic Panel Manufacturers: Your Essential Guide (2025)
Introduction: Navigating the Global Market for acoustic panel manufacturer
In today’s increasingly globalized world, sourcing high-quality acoustic panels can be a significant challenge for B2B buyers, especially in regions like Africa, South America, the Middle East, and Europe. Whether you are looking to reduce noise pollution in urban environments or enhance sound quality in commercial spaces, understanding the nuances of the acoustic panel manufacturing market is essential. This guide aims to illuminate the diverse types of acoustic panels available, their various applications, and the critical factors to consider when selecting a supplier.
Navigating the global market for acoustic panel manufacturers requires a clear strategy. Buyers must evaluate product specifications, assess supplier credentials, and understand cost implications to make informed decisions. This comprehensive guide will provide actionable insights into supplier vetting processes, pricing structures, and emerging trends in acoustic solutions. By addressing these crucial aspects, we empower international B2B buyers to streamline their purchasing processes and ultimately achieve better outcomes for their projects.
From the bustling markets of Nairobi to the innovative hubs of Istanbul, understanding the acoustic panel landscape can greatly influence your project’s success. Whether you are a seasoned procurement professional or a newcomer to the industry, this guide serves as a valuable resource to help you navigate the complexities of sourcing acoustic panels effectively and efficiently.
Understanding acoustic panel manufacturer Types and Variations
Type Name | Key Distinguishing Features | Primary B2B Applications | Brief Pros & Cons for Buyers |
---|---|---|---|
Fabric-Wrapped Panels | Soft fabric surface, customizable colors & patterns | Offices, conference rooms, auditoriums | Pros: Aesthetic appeal, variety; Cons: May require cleaning. |
Foam Acoustic Panels | Lightweight, open-cell structure | Home studios, small meeting rooms | Pros: Cost-effective, easy to install; Cons: Less durable. |
Wood Panel Systems | Natural wood finish, enhanced sound absorption | High-end commercial spaces, restaurants | Pros: Elegant appearance, good acoustics; Cons: Higher cost. |
Metal Acoustic Panels | Durable, sleek design, often perforated | Industrial settings, large venues | Pros: Long-lasting, modern look; Cons: Can be pricier. |
Specialized Acoustic Solutions | Tailored designs for specific sound issues | Theaters, recording studios, schools | Pros: Customized performance; Cons: Longer lead times. |
What are the Characteristics and Suitability of Fabric-Wrapped Panels?
Fabric-wrapped panels are known for their soft fabric surfaces, which can be customized in various colors and patterns to match the interior design of a space. They are particularly suitable for environments like offices and conference rooms where aesthetics are essential alongside sound absorption. Buyers should consider the maintenance needs, as these panels may require periodic cleaning to maintain their appearance.
Why Choose Foam Acoustic Panels for Smaller Spaces?
Foam acoustic panels feature a lightweight, open-cell structure that effectively absorbs sound, making them an excellent choice for home studios and small meeting rooms. Their cost-effectiveness and ease of installation appeal to budget-conscious buyers. However, potential buyers should be aware that foam panels may not offer the same durability as other materials, which could impact long-term use.
What Are the Benefits of Wood Panel Systems?
Wood panel systems combine natural wood finishes with excellent sound absorption qualities, making them a popular choice for high-end commercial spaces and restaurants. These panels not only enhance the acoustic environment but also add a touch of elegance to the decor. However, buyers should be prepared for a higher upfront investment compared to other panel types.
In What Situations Are Metal Acoustic Panels Ideal?
Metal acoustic panels are characterized by their durability and sleek, often perforated designs. They are ideal for industrial settings and large venues where longevity and modern aesthetics are crucial. While they provide a contemporary look and are built to last, buyers need to consider that metal panels can be more expensive than other options, which may affect budgeting.
How Do Specialized Acoustic Solutions Meet Unique Needs?
Specialized acoustic solutions are tailored to address specific sound issues within a space, making them suitable for theaters, recording studios, and educational institutions. These custom-designed solutions can significantly enhance the acoustic performance of challenging environments. However, buyers should factor in longer lead times for production and installation when considering this option, as it may impact project timelines.
Related Video: Acoustic Panels – What & Where
Key Industrial Applications of acoustic panel manufacturer
Industry/Sector | Specific Application of acoustic panel manufacturer | Value/Benefit for the Business | Key Sourcing Considerations for this Application |
---|---|---|---|
Education | Classroom soundproofing | Enhances learning environment, reduces distractions | Material durability, fire resistance standards |
Hospitality | Hotel lobby and conference room acoustics | Improves guest experience, boosts privacy and comfort | Aesthetic appeal, ease of installation |
Healthcare | Hospital waiting areas and patient rooms | Creates a soothing environment, aids patient recovery | Hygiene compliance, sound absorption efficiency |
Commercial Offices | Open-plan workspace acoustics | Increases employee productivity, reduces noise pollution | Customizability, integration with existing design |
Entertainment Venues | Concert halls and theaters acoustics | Enhances sound quality, improves audience experience | Acoustic performance metrics, design flexibility |
How are Acoustic Panels Utilized in Educational Settings?
In educational institutions, acoustic panels are essential for classroom soundproofing. They significantly enhance the learning environment by minimizing distractions caused by excessive noise. This is particularly important in regions like Africa and South America, where classroom sizes can be large, and external noise can be prevalent. Buyers should consider the durability and fire resistance of materials to ensure compliance with safety regulations, especially in densely populated areas.
What Benefits Do Acoustic Panels Bring to the Hospitality Industry?
In the hospitality sector, acoustic panels are widely used in hotel lobbies and conference rooms to improve sound quality. By reducing noise levels, these panels create a more comfortable and inviting atmosphere for guests, ultimately enhancing their experience. For international buyers, especially in the Middle East and Europe, aesthetic appeal and ease of installation are crucial factors. Selecting panels that complement the interior design while providing effective sound absorption is vital for maintaining a high standard of service.
How Do Acoustic Panels Enhance Healthcare Environments?
In healthcare facilities, such as hospitals, acoustic panels play a critical role in patient rooms and waiting areas. They contribute to a soothing environment that aids in patient recovery by minimizing disruptive noise. This is particularly important in regions with high patient turnover, such as Turkey or South Africa. Buyers in the healthcare sector should prioritize hygiene compliance and sound absorption efficiency, ensuring that the materials used are easy to clean and maintain.
Why are Acoustic Panels Important for Commercial Offices?
For commercial offices, acoustic panels are essential in open-plan workspaces to manage sound levels effectively. By reducing noise pollution, these panels help increase employee productivity and create a more conducive working environment. B2B buyers in Europe and the Middle East should consider customizability and the ability to integrate acoustic solutions with existing office designs. This flexibility ensures that the panels meet both functional and aesthetic needs.
How Do Acoustic Panels Improve Entertainment Venues?
In entertainment venues, such as concert halls and theaters, acoustic panels are crucial for enhancing sound quality. They help create an immersive experience for audiences by ensuring that sound is evenly distributed throughout the space. Buyers in this sector should focus on acoustic performance metrics and design flexibility to accommodate various events. This is particularly important for international buyers looking to invest in venues that attract diverse audiences in regions like South America and Africa.
Related Video: Industrial Control Panel Basics
3 Common User Pain Points for ‘acoustic panel manufacturer’ & Their Solutions
Scenario 1: Difficulty in Sourcing High-Quality Acoustic Panels
The Problem:
International B2B buyers often struggle with sourcing high-quality acoustic panels that meet their specific requirements. This challenge is exacerbated by the vast number of manufacturers in the market, leading to confusion over which products offer the best sound absorption and aesthetic appeal. Buyers from diverse regions, such as Africa and South America, may find it difficult to evaluate products that are available locally or through international suppliers. Additionally, language barriers and varying standards across regions can complicate the purchasing process, leaving buyers uncertain about the quality and performance of the panels they select.
The Solution:
To effectively source high-quality acoustic panels, buyers should start by defining their specific requirements, including sound absorption coefficients, material specifications, and design aesthetics. Research manufacturers who are well-reviewed in the industry and have a proven track record of delivering quality products. Utilize online platforms, such as industry forums and B2B marketplaces, to compare product specifications and gather feedback from other buyers. It’s beneficial to request samples before making a bulk purchase to evaluate the quality firsthand. Furthermore, consider manufacturers that offer customization options, allowing you to tailor the panels to your unique environment. Engaging with manufacturers directly can also clarify any regional compliance standards, ensuring that the products meet local regulations.
Scenario 2: Understanding Installation Challenges for Acoustic Panels
The Problem:
Many B2B buyers encounter significant challenges when it comes to the installation of acoustic panels. This issue is particularly common in large commercial spaces like offices, auditoriums, or schools, where improper installation can lead to ineffective sound management. Buyers may not have a clear understanding of the installation process, which can vary significantly between different types of panels and materials. This lack of knowledge can result in increased costs, project delays, and suboptimal performance of the acoustic solutions.
The Solution:
To overcome installation challenges, buyers should seek manufacturers who provide comprehensive installation guides and support. Look for suppliers that offer professional installation services or have partnerships with local contractors who specialize in acoustic panel installation. Before purchasing, inquire about the installation requirements and any necessary tools or materials. Consider engaging a sound engineer or an acoustic consultant during the planning phase to ensure that the panels are installed in optimal locations for maximum sound absorption. Additionally, leveraging video tutorials or training sessions provided by manufacturers can enhance the installation team’s understanding, ensuring the panels are installed correctly and efficiently.
Scenario 3: Navigating Cost Concerns and Budget Constraints
The Problem:
Cost is a primary concern for many B2B buyers, particularly in regions facing economic challenges, such as parts of Africa and South America. Buyers often find themselves balancing quality with budget constraints, leading to difficult decisions about whether to invest in high-quality acoustic solutions or opt for cheaper alternatives that may not perform as well. This dilemma can result in dissatisfaction with the final product and wasted resources if the panels do not effectively meet the acoustic needs of the space.
The Solution:
To navigate cost concerns effectively, buyers should conduct a thorough cost-benefit analysis before making any purchasing decisions. Focus on understanding the long-term value of investing in higher-quality acoustic panels, which may reduce the need for future replacements or additional soundproofing measures. Engage with manufacturers about bulk purchasing options or discounts for large orders, which can significantly lower unit costs. Additionally, consider exploring financing options or payment plans that can make higher-quality products more accessible within budget constraints. Researching and comparing multiple suppliers can also reveal competitive pricing and better value propositions, allowing buyers to make informed decisions without compromising on quality.
Strategic Material Selection Guide for acoustic panel manufacturer
When selecting materials for acoustic panels, manufacturers must consider various factors that influence performance, cost, and suitability for specific applications. Here, we analyze four common materials used in acoustic panels, focusing on their properties, advantages, disadvantages, and implications for international B2B buyers, particularly in Africa, South America, the Middle East, and Europe.
What Are the Key Properties of Fiberglass in Acoustic Panels?
Fiberglass is a popular choice for acoustic panels due to its excellent sound absorption capabilities. It is lightweight, non-combustible, and resistant to moisture, making it suitable for various environments. Fiberglass panels can withstand high temperatures, typically rated up to 500°F (260°C), which is beneficial for applications in industrial settings.
Pros & Cons: The primary advantage of fiberglass is its superior sound absorption, which can significantly improve acoustic performance in spaces like auditoriums and recording studios. However, it can be more expensive than other materials and may require protective coatings to prevent fiber shedding, which could complicate manufacturing.
Impact on Application: Fiberglass panels are compatible with various media, including paints and fabric coverings, allowing for customization in design. International buyers should ensure compliance with local regulations regarding fire safety and indoor air quality.
How Does Mineral Wool Perform as an Acoustic Panel Material?
Mineral wool, made from natural or recycled materials, is another effective sound-absorbing material. It offers excellent thermal insulation properties and is resistant to fire, withstanding temperatures up to 1,200°F (650°C).
Pros & Cons: The key advantage of mineral wool is its dual functionality as both an acoustic and thermal insulator, making it ideal for commercial buildings. However, it can be heavier than fiberglass, which may affect installation and shipping costs.
Impact on Application: Mineral wool panels can absorb sound across a wide frequency range, making them suitable for various applications. Buyers should be aware of local standards, such as ASTM E90 for sound transmission, to ensure compliance.
What Are the Benefits of Polyester Fiber in Acoustic Panels?
Polyester fiber panels are gaining popularity due to their eco-friendly properties, as they are often made from recycled materials. They are lightweight, flexible, and can be produced in various colors and textures.
Pros & Cons: Polyester fiber offers good sound absorption and is resistant to moisture and mold, making it suitable for humid environments. However, their acoustic performance may not match that of fiberglass or mineral wool, and they can be more expensive due to their eco-friendly nature.
Impact on Application: These panels are often used in schools and healthcare facilities where aesthetics and indoor air quality are essential. International buyers should consider compliance with environmental standards and certifications.
Why Choose Wood as a Material for Acoustic Panels?
Wood is a traditional material used in acoustic panels, prized for its aesthetic appeal and natural sound absorption properties. It can be treated to enhance durability and resistance to environmental factors.
Pros & Cons: Wood panels provide a warm, natural look and can be effective in controlling reverberation. However, they are typically more expensive and may require more maintenance than synthetic materials.
Impact on Application: Wood panels are often used in high-end residential and commercial spaces. Buyers should ensure that the wood used complies with local regulations regarding sustainability and sourcing.
Material | Typical Use Case for acoustic panel manufacturer | Key Advantage | Key Disadvantage/Limitation | Relative Cost (Low/Med/High) |
---|---|---|---|---|
Fiberglass | Auditoriums, recording studios | Superior sound absorption | Higher cost, fiber shedding risk | High |
Mineral Wool | Commercial buildings, theaters | Dual acoustic and thermal insulation | Heavier, affects installation costs | Medium |
Polyester Fiber | Schools, healthcare facilities | Eco-friendly, moisture resistant | Lower acoustic performance | Medium |
Wood | High-end residential, commercial spaces | Aesthetic appeal, natural sound absorption | Higher maintenance, cost | High |
This strategic material selection guide provides a comprehensive overview of the materials used in acoustic panels, helping international B2B buyers make informed decisions that align with their specific needs and regional standards.
In-depth Look: Manufacturing Processes and Quality Assurance for acoustic panel manufacturer
What Are the Key Stages in the Manufacturing Process of Acoustic Panels?
The manufacturing of acoustic panels involves several key stages, each critical to producing high-quality products. The main stages include material preparation, forming, assembly, and finishing.
Material Preparation: How Are Raw Materials Processed for Acoustic Panels?
The first stage involves the careful selection and preparation of raw materials. Acoustic panels typically use sound-absorbing materials such as fiberglass, foam, or mineral wool.
- Material Selection: Suppliers must ensure that materials meet specific sound absorption criteria. This is crucial for international buyers who may have different acoustic requirements based on regional standards.
- Cutting and Shaping: Raw materials are cut into desired dimensions. This step often employs CNC machines for precision, ensuring consistency across batches.
Forming: What Techniques Are Used to Shape Acoustic Panels?
After material preparation, the next stage is forming, which involves shaping the materials to create the final panel design.
- Compression Molding: This technique is frequently used for fiberglass panels, where raw materials are placed in a mold and compressed under heat to achieve the desired shape and density.
- Casting: For foam panels, casting techniques can be employed, where liquid foam is poured into molds and allowed to expand and cure. This method allows for intricate designs and shapes.
Assembly: How Are Acoustic Panels Constructed?
The assembly stage involves combining the formed panels with backing materials and additional features.
- Layering: In many cases, acoustic panels are multilayered to enhance sound absorption. Each layer may have different acoustic properties, which must be carefully aligned and bonded.
- Adhesives and Fasteners: The choice of adhesives is critical, especially for international shipments where temperature fluctuations might affect bond integrity. Environmentally-friendly adhesives are increasingly preferred to meet global sustainability standards.
Finishing: What Final Touches Are Applied to Acoustic Panels?
The finishing stage enhances the aesthetics and functionality of the acoustic panels.
- Surface Treatments: This may include painting, fabric wrapping, or applying a veneer. The choice of finish can affect the panel’s acoustic properties and its integration into various environments.
- Quality Control: Each panel undergoes a thorough inspection to ensure it meets the specifications and quality standards. This step is critical for B2B buyers who require consistent quality across all products.
How Is Quality Assurance Implemented in Acoustic Panel Manufacturing?
Quality assurance (QA) is an integral part of the manufacturing process, ensuring that the final products meet both international and industry-specific standards.
What International Standards Should B2B Buyers Look For?
Buyers should be aware of several international standards that may apply to acoustic panels:
- ISO 9001: This standard focuses on quality management systems and is crucial for manufacturers aiming to ensure consistent quality in their processes.
- CE Marking: In Europe, the CE mark indicates compliance with health, safety, and environmental protection standards. It is essential for buyers in Europe to verify that their suppliers meet these requirements.
- Acoustic Performance Standards: Standards such as ASTM E413 in the USA and EN ISO 354 in Europe assess the sound absorption performance of materials.
What Are the Key Quality Control Checkpoints?
Quality control checkpoints are essential for maintaining product integrity throughout the manufacturing process. The main checkpoints include:
- Incoming Quality Control (IQC): This involves inspecting raw materials upon arrival to ensure they meet specified criteria before being used in production.
- In-Process Quality Control (IPQC): During the manufacturing process, periodic checks are performed to monitor production parameters and identify any deviations from standards.
- Final Quality Control (FQC): This final inspection assesses the finished products against quality benchmarks before they are shipped to clients.
What Testing Methods Are Commonly Used for Acoustic Panels?
To validate the acoustic performance and durability of panels, various testing methods are employed:
- Sound Absorption Testing: This typically involves using a reverberation chamber to measure the sound absorption coefficient of panels.
- Durability Testing: Panels are subjected to environmental conditions such as humidity and temperature changes to ensure they maintain performance over time.
- Fire Safety Testing: Compliance with fire safety standards is crucial, especially in commercial applications. Tests like ASTM E84 are commonly used to assess flammability.
How Can B2B Buyers Verify Supplier Quality Control?
Buyers must ensure their suppliers adhere to stringent quality control measures. Here are some actionable steps:
- Conduct Audits: Regular audits of suppliers can reveal their adherence to quality standards and provide insights into their manufacturing processes.
- Request Quality Assurance Reports: Suppliers should be able to provide documentation of their quality control processes and testing results.
- Engage Third-Party Inspectors: For larger orders or higher stakes, hiring third-party inspectors can provide an unbiased assessment of product quality before shipment.
What Are the Quality Control Nuances for International Buyers?
International buyers, particularly from diverse regions like Africa, South America, the Middle East, and Europe, should be aware of specific nuances in quality control:
- Regulatory Compliance: Different regions may have varying regulations. Buyers should familiarize themselves with local requirements for acoustic products.
- Cultural Expectations: Understanding cultural differences in quality expectations can help buyers communicate effectively with suppliers and negotiate terms that meet their needs.
- Logistics and Shipping Considerations: Quality can be affected during transit. Buyers should ensure that suppliers have appropriate packaging and shipping protocols to protect products from damage.
By understanding the manufacturing processes and quality assurance measures in the acoustic panel industry, B2B buyers can make informed decisions that align with their specific needs and standards.
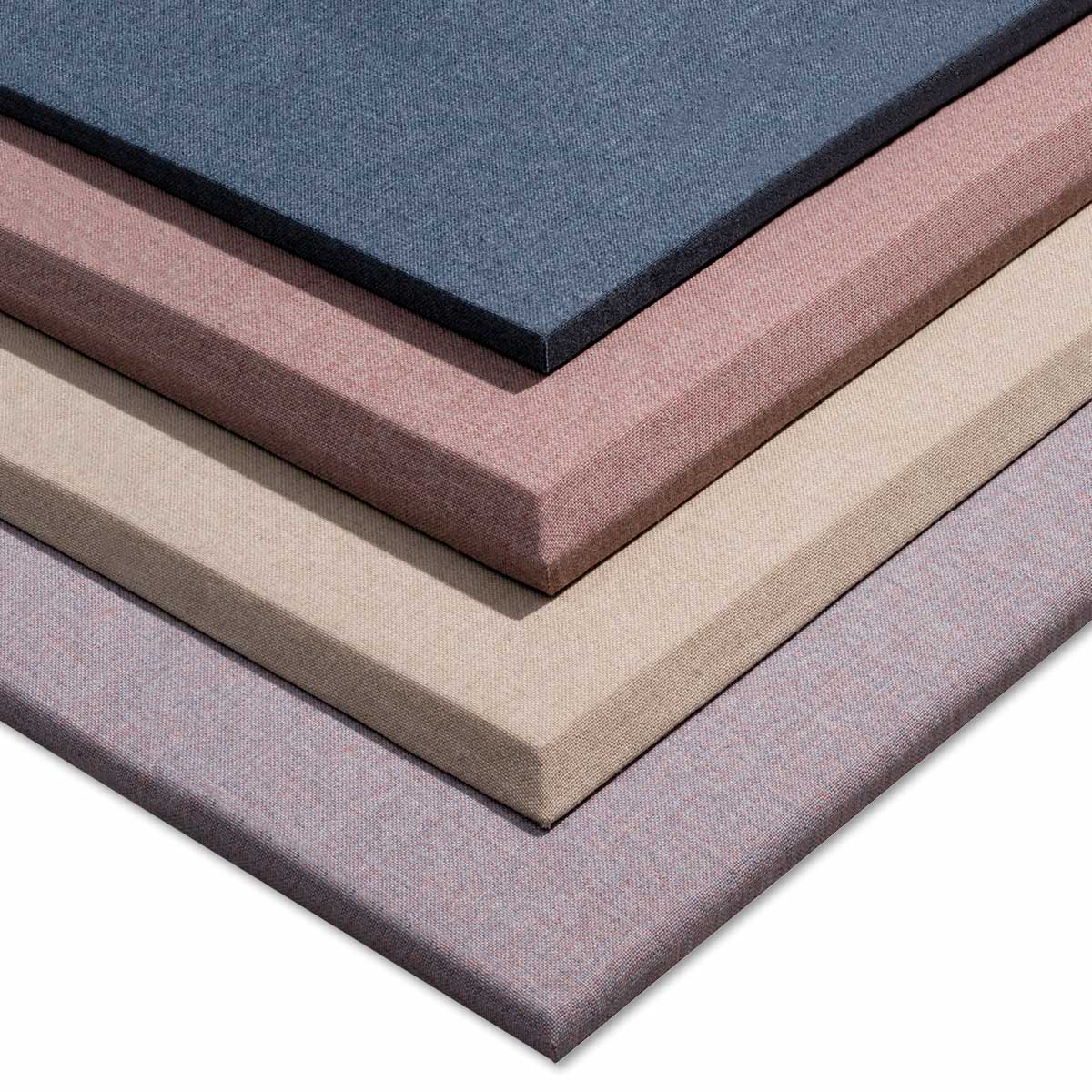
A stock image related to acoustic panel manufacturer.
Practical Sourcing Guide: A Step-by-Step Checklist for ‘acoustic panel manufacturer’
To successfully source an acoustic panel manufacturer, international B2B buyers must follow a structured approach that ensures quality, compliance, and value for money. This guide provides a step-by-step checklist to streamline your sourcing process, helping you make informed decisions.
Step 1: Define Your Technical Specifications
Clearly outline the technical requirements for the acoustic panels you need. Consider factors such as material types, dimensions, sound absorption coefficients, and aesthetic preferences. This step is crucial because having precise specifications will help you communicate effectively with potential suppliers and ensure that the products meet your project’s needs.
Step 2: Research Market Trends and Suppliers
Conduct thorough research on current market trends in acoustic panel manufacturing. Look for suppliers who are recognized for innovation and quality in their offerings. Utilize industry publications, online directories, and trade shows to identify potential manufacturers. Understanding the market landscape will enable you to pinpoint suppliers that align with your business goals.
Step 3: Evaluate Potential Suppliers
Before committing, it’s crucial to vet suppliers thoroughly. Request company profiles, case studies, and references from buyers in a similar industry or region. Consider the following:
– Reputation: Look for reviews and testimonials.
– Experience: Evaluate how long they have been in the industry and their portfolio of projects.
Step 4: Verify Supplier Certifications
Ensure that the manufacturers hold relevant certifications, such as ISO 9001 for quality management systems or specific environmental standards. These certifications indicate a commitment to quality and sustainability. Verify their compliance with local regulations, especially if you are importing products into your region, as this can affect your project’s legality and safety.
Step 5: Request Samples and Conduct Quality Checks
Before finalizing your order, request samples of the acoustic panels. Evaluate the quality of materials, craftsmanship, and performance in sound absorption. Conduct quality checks to ensure that the panels meet your specifications. This step is essential to avoid costly mistakes and ensure that the final products perform as expected in your intended application.
Step 6: Negotiate Terms and Pricing
Engage in discussions regarding pricing, payment terms, and delivery schedules. Be transparent about your budget while being open to negotiation. Consider the total cost of ownership, including shipping, duties, and installation costs, rather than just the upfront price. This holistic approach will help you secure the best overall deal.
Step 7: Establish a Clear Communication Channel
Set up a reliable communication channel with your selected supplier. Establish regular check-ins and updates throughout the manufacturing and delivery process. Clear communication helps mitigate misunderstandings and ensures that any issues are addressed promptly, fostering a strong supplier relationship.
By following this checklist, international B2B buyers can navigate the complexities of sourcing acoustic panels effectively, ensuring that they select a manufacturer that meets their specific needs and contributes to the success of their projects.
Comprehensive Cost and Pricing Analysis for acoustic panel manufacturer Sourcing
What are the Key Cost Components in Acoustic Panel Manufacturing?
When sourcing acoustic panels, international B2B buyers must understand the cost structure involved in manufacturing. The primary components include:
-
Materials: The type of materials used, such as foam, fiberglass, or recycled materials, significantly impacts the overall cost. Higher-quality materials typically lead to better acoustic performance but come at a premium price.
-
Labor: Labor costs vary by region and are influenced by local wage standards and the skill level required for production. Countries in Africa and South America may have lower labor costs compared to Europe or the Middle East, affecting overall pricing.
-
Manufacturing Overhead: This encompasses utilities, facility maintenance, and administrative expenses. Efficient manufacturing processes can help reduce overhead, thus lowering prices.
-
Tooling: Initial costs for molds and machinery are critical, especially for custom designs. Investing in high-quality tooling can enhance production efficiency and quality.
-
Quality Control (QC): Implementing stringent QC measures ensures product reliability but adds to the cost. Suppliers with certifications like ISO may charge more due to their commitment to quality.
-
Logistics: Transportation costs, including shipping and customs duties, can vary widely based on the destination. Buyers must consider the total logistics cost, especially when importing from overseas manufacturers.
-
Margin: Finally, manufacturers will include a profit margin in their pricing. This margin can vary significantly based on the competitive landscape and the manufacturer’s market position.
How Do Price Influencers Impact Acoustic Panel Costs?
Several factors influence pricing, making it essential for buyers to navigate these nuances effectively:
-
Volume/MOQ: Minimum order quantities (MOQ) often dictate pricing tiers. Bulk purchases typically reduce the per-unit cost, making it advantageous for buyers to negotiate larger orders.
-
Specifications and Customization: Customized acoustic panels that require unique designs or features will incur additional costs. Buyers should clearly define their requirements to avoid unexpected expenses.
-
Materials and Quality Certifications: As mentioned, the choice of materials directly affects costs. Panels that meet specific acoustic performance certifications or sustainability standards may be priced higher but offer long-term benefits.
-
Supplier Factors: The supplier’s reputation, reliability, and production capabilities can influence pricing. Established suppliers may charge more but provide assurance of quality and timely delivery.
-
Incoterms: Understanding shipping terms is crucial. Different Incoterms (International Commercial Terms) can affect the overall cost of acquisition, including responsibilities for shipping and insurance.
What are Effective Buyer Tips for Cost-Efficiency?
For B2B buyers, especially those from Africa, South America, the Middle East, and Europe, here are actionable insights to maximize cost-efficiency:
-
Negotiate Terms: Always negotiate pricing and payment terms. Many manufacturers are open to discussions, particularly for larger orders or long-term partnerships.
-
Consider Total Cost of Ownership (TCO): Evaluate the long-term costs associated with the panels, including installation, maintenance, and energy savings from improved acoustics. A higher upfront cost may yield lower overall expenses.
-
Research Market Prices: Conduct market research to understand price ranges for similar products. This knowledge empowers buyers during negotiations and helps identify competitive suppliers.
-
Evaluate the Supply Chain: Assess logistics options, including local suppliers versus international ones. Local sourcing may reduce shipping costs and lead times, enhancing overall efficiency.
-
Stay Informed on Pricing Trends: Keep abreast of market dynamics that may influence prices, such as changes in raw material costs or shifts in demand due to economic factors.
Disclaimer on Pricing
Prices for acoustic panels can vary significantly based on the factors discussed above. It is advisable for buyers to seek multiple quotes and conduct thorough due diligence to ensure they are receiving competitive pricing reflective of their specific needs.
Alternatives Analysis: Comparing acoustic panel manufacturer With Other Solutions
When considering acoustic solutions for improving sound quality in various environments, it’s essential to evaluate not just acoustic panels but also alternative methods. These alternatives may provide different benefits and may be more suitable depending on specific needs and applications. This comparison will help B2B buyers make informed decisions based on their unique requirements.
Comparison Table of Acoustic Solutions
Comparison Aspect | Acoustic Panel Manufacturer | Acoustic Foam Panels | Soundproof Curtains |
---|---|---|---|
Performance | High sound absorption | Moderate absorption | Variable absorption |
Cost | Moderate to high | Low to moderate | Low to moderate |
Ease of Implementation | Moderate | Easy | Very easy |
Maintenance | Low | Low | Low |
Best Use Case | Professional settings | Home studios | Residential spaces |
What Are the Pros and Cons of Acoustic Foam Panels?
Acoustic foam panels are a popular alternative to traditional acoustic panels. They are designed to absorb sound waves, thereby reducing echo and improving sound clarity. The primary advantage of acoustic foam is its cost-effectiveness; they are generally cheaper than manufactured acoustic panels, making them an attractive option for smaller budgets. Additionally, they are lightweight and easy to install, which can significantly reduce labor costs.
However, the performance of acoustic foam can be somewhat limited compared to high-quality acoustic panels. They may not absorb lower frequencies effectively, making them less suitable for environments where bass frequencies are prevalent. Thus, while they are excellent for home studios or small spaces, they may fall short in professional settings where superior sound quality is critical.
How Do Soundproof Curtains Compare to Acoustic Panels?
Soundproof curtains represent another alternative, primarily designed to block external noise rather than absorb it. Their primary benefit lies in their versatility; they can be easily hung in any window or doorway, providing an immediate solution for noise reduction. They are also relatively inexpensive and can enhance the aesthetic of a room.
On the downside, soundproof curtains typically offer variable sound absorption capabilities. While they can reduce noise from outside, they do not provide the same level of sound control as dedicated acoustic panels. Therefore, they might not be ideal for environments that require stringent sound management, such as recording studios or conference rooms.
How Can B2B Buyers Choose the Right Acoustic Solution?
Choosing the right acoustic solution requires careful consideration of several factors, including the specific sound issues being faced, the environment in which the solution will be implemented, and the budget available. For professional settings, investing in high-quality acoustic panels from a reputable manufacturer is often the best choice to ensure optimal sound performance. For smaller projects or more casual environments, acoustic foam panels or soundproof curtains may provide sufficient results without the higher costs associated with traditional acoustic panels.
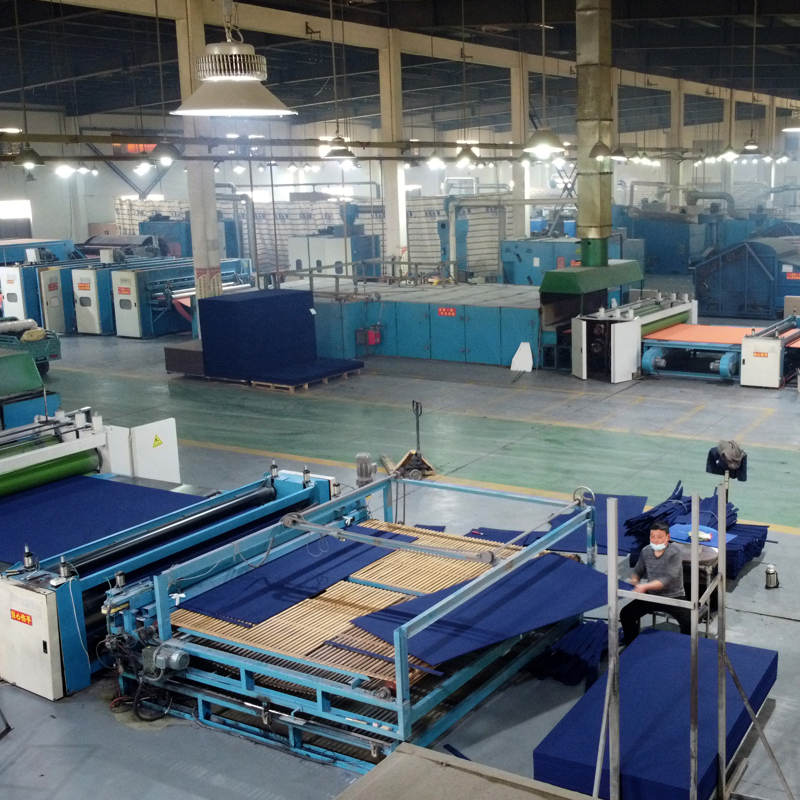
A stock image related to acoustic panel manufacturer.
Ultimately, B2B buyers should assess their unique needs, including performance expectations, installation capabilities, and long-term maintenance considerations, to select the most appropriate acoustic solution for their situation.
Essential Technical Properties and Trade Terminology for acoustic panel manufacturer
What Are the Essential Technical Properties of Acoustic Panels for Manufacturers?
When sourcing acoustic panels, international B2B buyers should pay close attention to specific technical properties that significantly impact performance and suitability for various applications. Here are key specifications to consider:
1. Material Grade and Composition
The material used in acoustic panels, such as fiberglass, foam, or wood, determines their sound absorption capabilities, durability, and aesthetic appeal. Higher-grade materials often provide better acoustic performance and longevity, which is crucial for commercial spaces like offices, schools, and auditoriums. Buyers should inquire about the specific materials and their certifications to ensure compliance with industry standards.
2. Sound Absorption Coefficient (SAC)
The Sound Absorption Coefficient measures how well a material absorbs sound at different frequencies, ranging from 0 (no absorption) to 1 (total absorption). Panels with a higher SAC are more effective at reducing noise, making them vital for spaces requiring sound control. Buyers should request SAC ratings for the specific frequencies relevant to their environments, as different materials perform variably across frequency ranges.
3. Thickness and Density
Thickness and density are critical factors influencing both the acoustic performance and physical characteristics of panels. Thicker and denser panels typically offer better sound attenuation. For example, a 2-inch thick panel will generally absorb more sound than a 1-inch thick panel. Buyers must evaluate the space requirements and sound control needs to select appropriate panel thickness.
4. Fire Rating
Fire safety is paramount in commercial settings, and the fire rating of acoustic panels indicates their resistance to ignition and spread of flames. Buyers should seek panels that comply with local building codes and have certifications like Class A fire ratings. This not only ensures safety but can also influence insurance premiums and compliance with regulations.
5. Tolerance and Finish
Tolerance refers to the allowable variations in dimensions of acoustic panels during manufacturing. Precise tolerances are essential for seamless installation, especially in large projects. Additionally, the finish of the panels—whether fabric, painted, or laminated—affects not only aesthetics but also durability and maintenance. Buyers should specify their requirements clearly to avoid compatibility issues during installation.
What Are Common Trade Terms in the Acoustic Panel Manufacturing Industry?
Understanding industry jargon is crucial for effective communication and negotiation in B2B transactions. Here are some commonly used terms:
1. OEM (Original Equipment Manufacturer)
This term refers to companies that produce parts or equipment that may be marketed by another manufacturer. In the acoustic panel industry, an OEM might create custom panels for a brand that sells them under its own label. Buyers should clarify whether the manufacturer operates as an OEM to ensure that they receive the expected quality and service.
2. MOQ (Minimum Order Quantity)
MOQ is the smallest quantity of a product that a supplier is willing to sell. This is particularly important for acoustic panels, as bulk orders often lead to cost savings. Buyers should negotiate MOQs that suit their project needs while considering inventory management.
3. RFQ (Request for Quotation)
An RFQ is a document sent to suppliers to request pricing and other details for specific products. For acoustic panels, an RFQ should include technical specifications, quantities, and delivery timelines. This helps buyers compare offers effectively and select the best supplier based on price and capability.
4. Incoterms (International Commercial Terms)
Incoterms define the responsibilities of buyers and sellers for shipping and delivery. These terms specify who pays for freight, insurance, and duties, which can significantly impact total costs. Familiarity with Incoterms helps buyers understand their obligations and negotiate better shipping arrangements.
5. Lead Time
Lead time is the amount of time from placing an order to the delivery of the product. In the acoustic panel market, understanding lead times is crucial for project planning and ensuring timely completion. Buyers should always inquire about lead times to avoid delays in their projects.
By being knowledgeable about these essential technical properties and trade terms, international B2B buyers can make informed decisions when sourcing acoustic panels, ensuring they select the right products for their specific needs while navigating the complexities of the global marketplace.
Navigating Market Dynamics and Sourcing Trends in the acoustic panel manufacturer Sector
What Are the Key Trends Shaping the Acoustic Panel Manufacturing Market?
The acoustic panel manufacturing sector is experiencing significant growth, driven by increasing awareness of sound quality in various environments, including commercial, residential, and industrial spaces. Global urbanization and the rise of smart buildings are key factors propelling demand for acoustic solutions. In regions such as Africa and South America, where urban development is accelerating, the necessity for effective sound management in public spaces, offices, and homes is becoming increasingly evident.
Emerging technologies are transforming the sourcing landscape. The integration of digital platforms and e-commerce in the procurement process allows international B2B buyers to access a broader range of manufacturers and suppliers. This trend is particularly beneficial for buyers in the Middle East and Europe, where competitive pricing and quality assurance are paramount. Additionally, advancements in manufacturing techniques, including the use of 3D printing and automated production lines, are enhancing efficiency and reducing lead times.
Moreover, the growing preference for customized acoustic solutions tailored to specific architectural needs is reshaping market dynamics. Buyers are increasingly looking for manufacturers that can provide bespoke designs, which not only meet aesthetic requirements but also optimize acoustic performance. This trend emphasizes the importance of collaboration between architects, designers, and acoustic panel manufacturers.
How Is Sustainability Influencing Sourcing in the Acoustic Panel Sector?
Sustainability is becoming a cornerstone of B2B sourcing strategies in the acoustic panel manufacturing industry. Environmental concerns are prompting buyers to seek suppliers committed to sustainable practices. Acoustic panels, traditionally made from synthetic materials, are now increasingly produced using recycled and eco-friendly materials. This shift not only addresses environmental impact but also resonates with consumers’ growing demand for responsible sourcing.
Ethical supply chains are another critical consideration. B2B buyers are now prioritizing manufacturers who adhere to fair labor practices and transparency throughout their supply chains. Certifications such as Forest Stewardship Council (FSC) and Leadership in Energy and Environmental Design (LEED) are gaining traction, as they provide assurance of a product’s sustainability credentials. Buyers should actively seek manufacturers that hold these certifications, as they reflect a commitment to environmental stewardship and ethical sourcing.
Furthermore, the acoustic panel market is witnessing a rise in the use of biodegradable materials, such as natural fibers and composites. This not only reduces the carbon footprint but also enhances the overall aesthetic appeal of the product. Buyers from regions like Europe, where sustainability standards are stringent, can leverage these developments to meet regulatory requirements while enhancing their brand image.
What Is the Historical Context of the Acoustic Panel Manufacturing Industry?
The acoustic panel manufacturing industry has evolved significantly over the past few decades. Initially, acoustic solutions were limited to basic soundproofing materials, primarily utilized in commercial settings like recording studios and theaters. However, as the understanding of sound dynamics has advanced, so too has the technology behind acoustic panels.
In the late 20th century, the focus shifted towards creating aesthetically pleasing designs that complemented modern architecture. This evolution led to the introduction of various materials, including fabric-wrapped panels and ceiling tiles, which not only enhanced sound quality but also served as decorative elements. Today, the industry is at the forefront of innovation, integrating advanced materials and sustainable practices to meet the diverse needs of international B2B buyers.
As global demand continues to rise, the future of acoustic panel manufacturing looks promising, with an emphasis on technology, sustainability, and customization. This historical context underscores the importance of adaptability for manufacturers aiming to cater to a dynamic market landscape.
Frequently Asked Questions (FAQs) for B2B Buyers of acoustic panel manufacturer
-
How do I choose the right acoustic panel manufacturer for my business needs?
Choosing the right acoustic panel manufacturer involves several key considerations. First, assess their industry experience and expertise, particularly in producing panels suited to your specific applications, such as office spaces, auditoriums, or residential areas. Look for manufacturers that offer customization options to meet your design and acoustic requirements. Additionally, consider their production capacity, lead times, and ability to handle international shipping, especially if you’re located in Africa, South America, the Middle East, or Europe. Finally, check reviews and references to gauge customer satisfaction and reliability. -
What types of acoustic panels are best for soundproofing in commercial spaces?
For commercial spaces, the best acoustic panels for soundproofing typically include fabric-wrapped panels, foam panels, and wall-mounted baffles. Fabric-wrapped panels offer aesthetic versatility and effective sound absorption, making them ideal for offices and conference rooms. Foam panels are lightweight and easy to install, suitable for studios and small offices. Wall-mounted baffles are excellent for large areas, helping to reduce echo and improve sound clarity. Consider the specific acoustics of your space when selecting the right type for optimal performance. -
What is the minimum order quantity (MOQ) for acoustic panels from manufacturers?
Minimum order quantities (MOQs) for acoustic panels can vary significantly between manufacturers. Some may allow orders as low as 50 units, while others might require a minimum of 500 or more, depending on production capabilities and material costs. For international buyers, it’s essential to clarify the MOQ upfront to ensure it aligns with your project needs and budget. Additionally, inquire about any flexibility in MOQs, especially if you’re looking to test a smaller batch before committing to a larger order. -
What customization options should I consider when sourcing acoustic panels?
Customization options for acoustic panels can greatly enhance their functionality and aesthetic appeal. Consider options such as panel size, thickness, and shape to fit your specific space requirements. Additionally, explore fabric choices and colors to match your interior design. Some manufacturers also offer printing services for logos or graphics, which can enhance brand visibility. Ensure the manufacturer can accommodate your customization requests while maintaining quality and performance standards. -
What payment terms are typically offered by acoustic panel manufacturers?
Payment terms can vary among acoustic panel manufacturers but generally include options such as upfront deposits, net 30/60/90 days, or letter of credit for larger orders. For international transactions, it’s crucial to discuss these terms early in the negotiation process. Some manufacturers may offer discounts for early payments or bulk orders. Always ensure that payment terms are clear and documented in your contract to avoid misunderstandings later on. -
How can I ensure quality assurance (QA) when sourcing acoustic panels?
To ensure quality assurance when sourcing acoustic panels, request samples from potential manufacturers before placing a larger order. This allows you to evaluate the materials, craftsmanship, and acoustic performance. Additionally, inquire about the manufacturer’s quality control processes, including testing for sound absorption and durability. Look for certifications such as ISO or specific acoustic performance ratings. Regular communication and follow-ups during production can also help address any concerns promptly. -
What logistics considerations should I keep in mind when importing acoustic panels?
When importing acoustic panels, logistics considerations include shipping methods, customs clearance, and delivery timelines. Choose a reliable freight forwarder familiar with importing goods into your region to navigate customs regulations. Consider the dimensions and weight of the panels, as this will impact shipping costs and methods. Additionally, factor in lead times for production and shipping to ensure timely delivery for your projects. Be prepared for potential delays and have contingency plans in place. -
How do I evaluate the environmental impact of acoustic panels from manufacturers?
To evaluate the environmental impact of acoustic panels, inquire about the materials used in their production. Look for manufacturers that utilize sustainable materials, such as recycled or eco-friendly substances. Certifications like GREENGUARD or LEED can indicate compliance with environmental standards. Additionally, ask about the manufacturer’s commitment to sustainable practices, such as waste reduction and energy-efficient production methods. Understanding the lifecycle impact of the panels will help you make a more environmentally responsible purchasing decision.
Important Disclaimer & Terms of Use
⚠️ Important Disclaimer
The information provided in this guide, including content regarding manufacturers, technical specifications, and market analysis, is for informational and educational purposes only. It does not constitute professional procurement advice, financial advice, or legal advice.
While we have made every effort to ensure the accuracy and timeliness of the information, we are not responsible for any errors, omissions, or outdated information. Market conditions, company details, and technical standards are subject to change.
B2B buyers must conduct their own independent and thorough due diligence before making any purchasing decisions. This includes contacting suppliers directly, verifying certifications, requesting samples, and seeking professional consultation. The risk of relying on any information in this guide is borne solely by the reader.
Strategic Sourcing Conclusion and Outlook for acoustic panel manufacturer
What Are the Key Takeaways for Strategic Sourcing in Acoustic Panels?
Strategic sourcing is vital for international B2B buyers looking to enhance their procurement processes, especially in the acoustic panel market. By focusing on quality, cost efficiency, and supplier relationships, businesses can secure superior products that meet their specific acoustic needs. Collaborating with manufacturers who understand local regulations and market dynamics can lead to more effective sourcing strategies, ensuring compliance and alignment with regional standards.
How Can Buyers Position Themselves for Future Success?
As the demand for acoustic solutions grows, particularly in emerging markets across Africa, South America, the Middle East, and Europe, buyers must remain proactive. Investing in long-term partnerships with acoustic panel manufacturers can provide a competitive edge, enabling access to innovative products and technologies. Additionally, understanding the nuances of each market will facilitate better negotiation terms and reduce lead times.
What Steps Should Buyers Take Moving Forward?
International B2B buyers are encouraged to assess their sourcing strategies critically and seek manufacturers who offer flexibility, customization, and sustainability. As you navigate this evolving landscape, prioritize collaboration and transparency to foster strong supplier relationships. Embrace the future of acoustic solutions and position your organization for growth by engaging with manufacturers that align with your strategic objectives.