Discover Top ACP Panel Manufacturers: Your Complete Guide (2025)
Introduction: Navigating the Global Market for ACP Panel Manufacturers
Navigating the complex landscape of ACP panel manufacturers can be a daunting task for international B2B buyers. Sourcing high-quality Aluminum Composite Panels (ACP) that meet specific project requirements while ensuring cost-effectiveness is crucial, especially in regions like Africa, South America, the Middle East, and Europe. This guide aims to demystify the ACP manufacturing market, providing insights into various types of panels, their applications, and essential factors to consider when selecting suppliers.
Understanding the nuances of ACP panels—from fire resistance ratings to aesthetic finishes—can significantly impact your project’s success. In this comprehensive resource, we delve into supplier vetting processes, cost considerations, and industry standards that govern ACP manufacturing. By equipping buyers with actionable insights and critical questions to ask potential suppliers, this guide empowers you to make informed purchasing decisions that align with your business objectives.
Whether you’re in Spain exploring sustainable building materials or in South Africa seeking durable solutions for exterior cladding, our guide serves as your roadmap to navigating the global ACP market. We aim to enhance your sourcing strategy, ensuring that you partner with reputable manufacturers who can deliver quality products tailored to your needs. Join us in this exploration to streamline your procurement process and achieve exceptional results in your projects.
Understanding ACP Panel Manufacturers Types and Variations
Type Name | Key Distinguishing Features | Primary B2B Applications | Brief Pros & Cons for Buyers |
---|---|---|---|
Standard ACP Panels | Made from aluminum composite materials, lightweight | Commercial buildings, signage, interior design | Pros: Cost-effective, versatile; Cons: Limited durability compared to other types. |
Fire-Rated ACP Panels | Incorporate fire-resistant materials | High-rise buildings, industrial facilities | Pros: Enhanced safety; Cons: Higher cost, specialized installation required. |
Anti-Graffiti ACP Panels | Special coatings for graffiti resistance | Urban environments, public spaces | Pros: Easy maintenance, aesthetic preservation; Cons: Potentially higher initial investment. |
Eco-Friendly ACP Panels | Made from recycled materials, sustainable options | Green buildings, environmentally-conscious projects | Pros: Low environmental impact; Cons: May be pricier, limited availability. |
Decorative ACP Panels | Custom designs and finishes available | Retail spaces, exhibitions, branding | Pros: Unique aesthetics, branding opportunities; Cons: Higher costs, longer lead times. |
What Are the Key Characteristics of Standard ACP Panels?
Standard ACP panels are primarily composed of two thin layers of aluminum enclosing a non-aluminum core, typically made of polyethylene. They are lightweight yet robust, making them suitable for various applications, such as commercial buildings and signage. When considering B2B purchases, buyers should evaluate the cost-effectiveness and versatility of these panels, as they can be easily cut and shaped to fit specific design requirements. However, their durability may be a concern in high-impact or extreme weather conditions.
How Do Fire-Rated ACP Panels Enhance Safety?
Fire-rated ACP panels are engineered with fire-resistant materials, making them ideal for applications in high-rise buildings and industrial facilities where safety is paramount. These panels undergo rigorous testing to meet fire safety standards, providing peace of mind for buyers concerned with compliance and safety regulations. While they offer enhanced safety features, buyers should be aware of the higher costs and the need for specialized installation, which may affect project timelines.
Why Choose Anti-Graffiti ACP Panels for Urban Spaces?
Anti-graffiti ACP panels are designed with special coatings that resist graffiti and other markings, making them an excellent choice for urban environments and public spaces. These panels not only preserve the aesthetic quality of buildings but also simplify maintenance, as they can be easily cleaned without damaging the surface. However, potential buyers should consider the initial investment, as these panels may come at a premium compared to standard options.
What Makes Eco-Friendly ACP Panels a Sustainable Choice?
Eco-friendly ACP panels are produced using recycled materials and are designed to minimize environmental impact, aligning with the growing demand for sustainable building practices. They are particularly suitable for green buildings and environmentally-conscious projects. While they contribute positively to sustainability goals, buyers should note that these panels may carry a higher price tag and could have limited availability depending on the market.
How Do Decorative ACP Panels Offer Unique Branding Opportunities?
Decorative ACP panels come in a variety of custom designs and finishes, allowing businesses to create unique branding opportunities in retail spaces and exhibitions. They enhance the visual appeal of a space while providing the functionality of standard ACP panels. However, buyers should be prepared for higher costs and potentially longer lead times when sourcing these specialized panels, as customization often requires more extensive manufacturing processes.
Related Video: Aluminium Composite Panel Installation Rout and Return Method
Key Industrial Applications of ACP Panel Manufacturers
Industry/Sector | Specific Application of ACP Panel Manufacturers | Value/Benefit for the Business | Key Sourcing Considerations for this Application |
---|---|---|---|
Construction | Building Facades and Cladding | Enhanced aesthetics, durability, and insulation | Compliance with local building codes and climate needs |
Transportation | Interior Panels for Vehicles | Lightweight, cost-effective, and easy to clean | Material certifications and safety standards |
Retail | Store Fixtures and Displays | Customization options and brand visibility | Design flexibility and lead times for production |
Signage and Advertising | Outdoor Signage Panels | Weather resistance and vibrant color options | UV resistance and longevity in harsh environments |
Industrial Applications | Partitioning and Wall Systems | Space optimization and acoustic insulation | Fire ratings and maintenance requirements |
How Are ACP Panels Used in Construction and What Problems Do They Solve?
ACP panels are extensively used in the construction industry for building facades and cladding. They offer a modern aesthetic while providing excellent insulation and durability against harsh weather conditions. For international B2B buyers, especially in regions like Africa and South America, sourcing ACP panels that comply with local building codes is crucial. Additionally, understanding the specific climate needs—such as UV resistance in sunny regions or thermal insulation in colder climates—can significantly impact the performance and longevity of the building.
What Are the Advantages of ACP Panels in Transportation?
In the transportation sector, ACP panels are utilized for interior applications in vehicles, including buses and trains. Their lightweight nature contributes to fuel efficiency, while their easy-to-clean surfaces enhance hygiene standards. Buyers should prioritize suppliers who provide materials with appropriate certifications and safety standards, especially for public transportation applications in the Middle East and Europe, where regulatory compliance is stringent.
How Do Retail Businesses Benefit from ACP Panels?
Retail businesses leverage ACP panels for store fixtures and displays, allowing for high levels of customization and brand visibility. The versatility of ACP panels enables retailers to create unique shopping experiences, which is essential in competitive markets. For B2B buyers, understanding the lead times for production and the design flexibility offered by manufacturers is key to successful project execution, especially in fast-paced environments like those in South Africa and Spain.
Why Are ACP Panels Ideal for Signage and Advertising?
ACP panels are a popular choice for outdoor signage due to their weather resistance and vibrant color options. They provide a durable solution that can withstand the elements while maintaining aesthetic appeal. Buyers in the advertising sector must consider the longevity of the signage in harsh environments and ensure that the panels possess UV resistance to prevent fading. This is particularly important in regions like Africa, where sun exposure is intense.
How Can ACP Panels Optimize Space in Industrial Applications?
In industrial settings, ACP panels are used for partitioning and wall systems, offering a lightweight yet robust solution for space optimization. They can also provide acoustic insulation, which is beneficial in noisy environments. Buyers should look for panels that meet specific fire ratings and maintenance requirements, ensuring compliance with safety regulations that vary across regions, including Europe and the Middle East. Understanding these factors can help businesses enhance their operational efficiency while maintaining safety standards.
Related Video: What is Aluminium Composite Panel | About ACP in Detail | Price and Other Information by
3 Common User Pain Points for ‘ACP Panel Manufacturers’ & Their Solutions
Scenario 1: Complicated Sourcing Processes for ACP Panels
The Problem: B2B buyers often face significant challenges when sourcing ACP panels due to the complexities involved in identifying reputable manufacturers. This is particularly true for buyers in regions like Africa and South America, where market transparency can be low and access to reliable suppliers is limited. Buyers might struggle with verifying the quality of materials, understanding the certifications necessary for their projects, and navigating the logistics of international shipping. This can lead to delays, increased costs, and a lack of confidence in the final product quality.
The Solution: To address these sourcing challenges, B2B buyers should begin by conducting thorough market research to identify potential ACP panel manufacturers. Utilize platforms such as Alibaba, Global Sources, or local trade shows to gather a list of suppliers. Once you have a list, request samples to assess the quality firsthand. It is crucial to establish clear communication regarding specifications and certifications required for your projects. For instance, inquire about ISO certifications, fire ratings, and compliance with local building codes in your region. Additionally, consider partnering with a local procurement agent who understands the regional market dynamics and can facilitate negotiations, ensuring that you get the best value and quality for your investment.
Scenario 2: Quality Assurance Concerns with ACP Panels
The Problem: Quality assurance is a critical pain point for B2B buyers, especially when it comes to ACP panels. With various manufacturers offering different grades of ACP, buyers can easily fall victim to subpar products that do not meet the necessary performance standards. This issue is particularly prevalent in Europe and the Middle East, where stringent building regulations demand high-quality materials. Buyers may face costly project delays or safety concerns if the panels fail to meet these standards.
The Solution: To mitigate quality assurance concerns, B2B buyers should implement a robust quality control process. Start by creating a detailed specification sheet that outlines the required standards for the ACP panels, including thickness, fire resistance, and surface finish. During the sourcing phase, ask manufacturers for their quality assurance processes and certifications, such as ISO 9001. It’s advisable to conduct factory audits if possible, or hire third-party inspection services to verify that the manufacturing processes align with your quality standards. Additionally, establish a solid return policy with your suppliers, ensuring that you can easily return or exchange panels that do not meet the agreed-upon specifications.
Scenario 3: Navigating Shipping and Logistics Challenges for ACP Panels
The Problem: International shipping and logistics pose significant challenges for B2B buyers of ACP panels, especially when dealing with heavy and bulky materials. Issues such as customs delays, unexpected tariffs, and transportation damages can lead to extended project timelines and increased costs. Buyers from Africa, South America, and even Europe may find it difficult to manage these logistics effectively, resulting in frustration and potential loss of business opportunities.
The Solution: To navigate shipping and logistics challenges effectively, B2B buyers should work closely with logistics experts who specialize in international freight for construction materials. Begin by discussing your shipping needs with the manufacturer to explore their logistics capabilities and preferred shipping partners. This can streamline the process and reduce the likelihood of delays. Additionally, consider using Incoterms (International Commercial Terms) to clearly define the responsibilities of both parties regarding shipping, insurance, and customs clearance. For buyers in regions with frequent customs issues, it may be beneficial to partner with a customs broker who can help facilitate smooth clearance and minimize potential delays. Establishing a clear timeline and maintaining open communication with both the manufacturer and the logistics provider will ensure that you stay informed and can adjust plans as needed to avoid disruptions.
Strategic Material Selection Guide for ACP Panel Manufacturers
When selecting materials for ACP (Aluminum Composite Panel) manufacturing, understanding the properties, advantages, and limitations of each material is crucial for B2B buyers. This section analyzes four common materials used in ACP panels, highlighting their key attributes and considerations for international buyers, particularly from Africa, South America, the Middle East, and Europe.
What are the Key Properties of Aluminum in ACP Panels?
Aluminum is the most widely used material in ACP panels due to its lightweight and corrosion-resistant properties. It typically has a temperature rating of up to 300°C and can withstand moderate pressure, making it ideal for various applications. The key benefits of aluminum include its excellent durability and aesthetic versatility, allowing for a wide range of finishes.
Pros: Aluminum panels are lightweight, making them easy to handle and install. They also offer high durability and resistance to weathering, which is essential for outdoor applications.
Cons: The primary drawback is the cost; while aluminum is generally affordable, high-quality aluminum can be more expensive than other materials. Additionally, the manufacturing process can be complex, requiring specialized equipment.
Impact on Application: Aluminum panels are suitable for a variety of media, including air and water, but may not be ideal for applications involving aggressive chemicals.
How Does Polyethylene Contribute to ACP Panel Performance?
Polyethylene (PE) is often used as the core material in ACP panels. It provides good thermal insulation and is lightweight, contributing to the overall efficiency of the panel. PE typically has a lower temperature resistance compared to aluminum, with a maximum rating of around 80°C.
Pros: Its low cost and ease of manufacturing make polyethylene a popular choice for budget-conscious projects. It also offers good impact resistance.
Cons: The main limitation is its susceptibility to fire; polyethylene is not fire-resistant and can pose safety risks in certain applications.
Impact on Application: PE is suitable for internal applications or areas where fire safety is not a concern. It is compatible with various media but should be avoided in high-temperature environments.
What Role Does Mineral-Filled Composite Material Play in ACP Panels?
Mineral-filled composites, such as those made with magnesium hydroxide, are increasingly used in ACP panels for their fire-resistant properties. These materials can withstand temperatures up to 1200°C, making them suitable for applications requiring enhanced fire safety.
Pros: The primary advantage is their fire resistance, which can be crucial for building codes in many regions. They also provide good mechanical strength and durability.
Cons: Mineral-filled composites tend to be heavier than aluminum and polyethylene, which can complicate installation. They are also generally more expensive due to the complex manufacturing processes involved.
Impact on Application: These materials are ideal for high-rise buildings and other structures where fire safety is paramount. They are compatible with various media but should be assessed for specific chemical interactions.
How Does Steel Compare as a Material for ACP Panels?
Steel is another option for ACP panels, known for its strength and durability. It typically has a higher temperature rating than aluminum, making it suitable for more demanding applications. However, it is also heavier and more prone to corrosion if not properly treated.
Pros: Steel offers exceptional strength and durability, making it suitable for high-load applications. It can also be coated for additional corrosion resistance.
Cons: The main disadvantage is its weight, which can increase transportation and installation costs. Additionally, untreated steel can rust, leading to maintenance issues.
Impact on Application: Steel panels are suitable for industrial applications or environments where strength is critical. They can handle various media but require careful consideration regarding corrosion resistance.
Summary Table of Material Selection for ACP Panel Manufacturers
Material | Typical Use Case for ACP Panel Manufacturers | Key Advantage | Key Disadvantage/Limitation | Relative Cost (Low/Med/High) |
---|---|---|---|---|
Aluminum | General construction, facades | Lightweight and corrosion-resistant | Higher cost for quality aluminum | Medium |
Polyethylene | Internal applications, budget projects | Low cost and easy to manufacture | Not fire-resistant | Low |
Mineral-Filled Composite | High-rise buildings, fire-sensitive areas | Excellent fire resistance | Heavier and more expensive | High |
Steel | Industrial applications, high-load areas | Exceptional strength | Heavier and prone to corrosion | Medium |
This guide provides international B2B buyers with essential insights into material selection for ACP panels, helping them make informed decisions based on performance, application, and regional compliance standards.
In-depth Look: Manufacturing Processes and Quality Assurance for ACP Panel Manufacturers
What Are the Key Stages in the Manufacturing Process of ACP Panels?
The manufacturing process for Aluminum Composite Panels (ACP) typically involves several critical stages, each of which contributes to the final product’s quality and performance. Understanding these stages is essential for B2B buyers looking to source ACP panels for various applications.
1. Material Preparation
The first step in ACP manufacturing is the preparation of raw materials, which primarily includes aluminum sheets and a non-aluminum core material, typically made of polyethylene or mineral-filled materials.
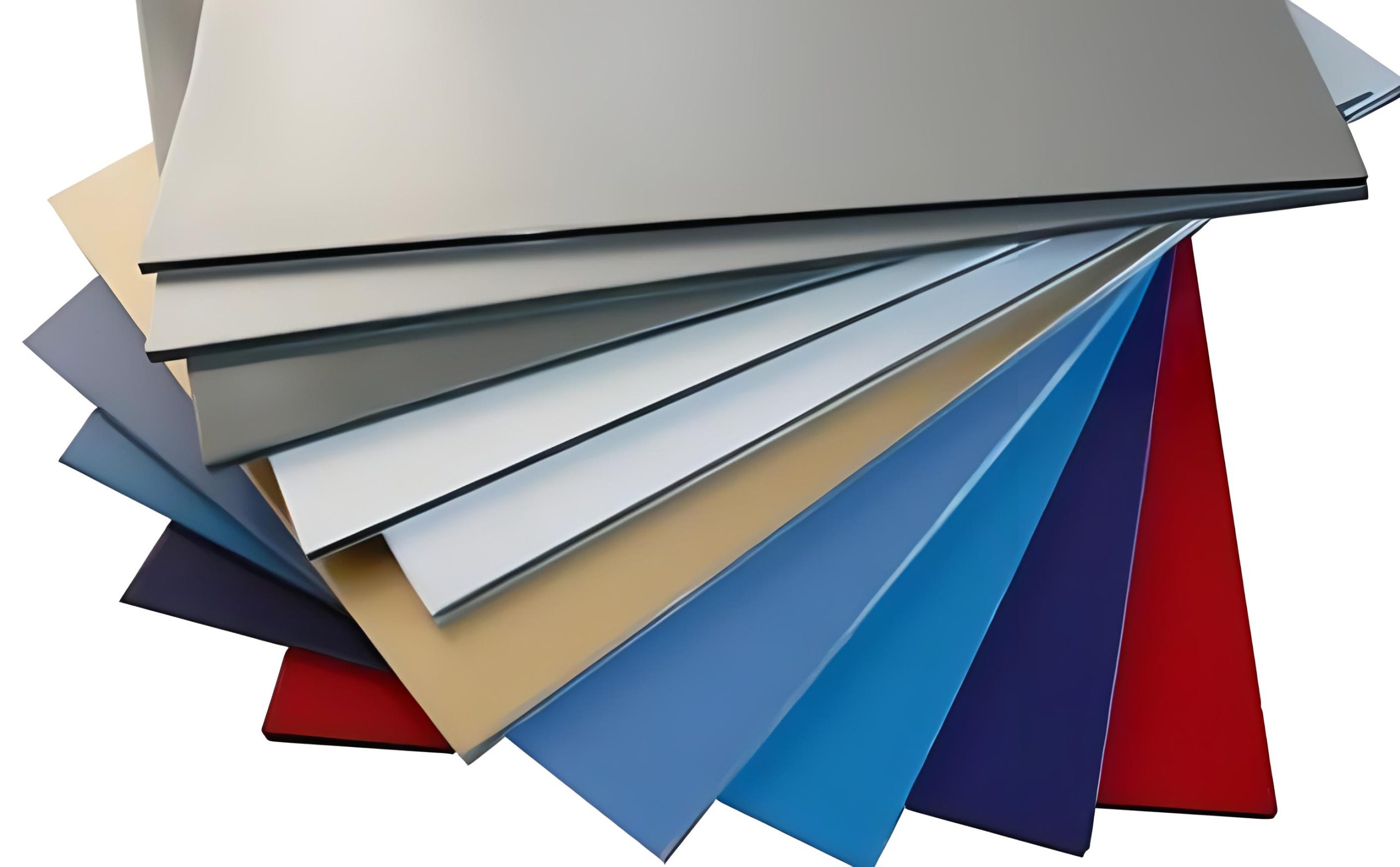
A stock image related to ACP Panel Manufacturers.
- Aluminum Sheets: These are sourced from reputable suppliers and are usually treated for corrosion resistance. The thickness of the aluminum sheets can vary, typically ranging from 0.2 mm to 0.5 mm.
- Core Material: The selection of core material significantly affects the panel’s weight, thermal insulation, and fire resistance properties. Buyers should inquire about the fire rating of the core material as per international standards.
2. Forming
In this stage, the prepared materials are formed into the desired panel shape. This process typically involves:
- Cutting: Aluminum sheets are cut to size using precision cutting tools.
- Coating: A protective coating, often a polyester or PVDF (polyvinylidene fluoride), is applied to the aluminum surface to enhance durability and aesthetics. This coating process should comply with international standards for quality and environmental safety.
- Bonding: The aluminum sheets are then bonded to the core material using high-strength adhesives. This step is crucial for ensuring the panels’ structural integrity.
3. Assembly
The assembly stage involves bringing together the formed components to create the final ACP panels.
- Layering: The coated aluminum sheets are layered with the core material, ensuring proper alignment.
- Pressing: The assembled panels are subjected to heat and pressure to ensure a strong bond and remove any trapped air bubbles. This process can vary based on the equipment used and should meet specific operational parameters to ensure quality.
4. Finishing
Finally, the panels undergo finishing processes to achieve the desired surface quality and performance characteristics.
- Trimming: Edges of the panels are trimmed to ensure uniformity.
- Quality Inspection: Each panel is inspected for defects in coating, bonding, and dimensional accuracy.
- Packaging: Proper packaging is crucial for protecting panels during transportation. Buyers should check if the manufacturer follows best practices in packaging to avoid damage.
How Is Quality Assurance Implemented in ACP Panel Manufacturing?
Quality assurance is a critical aspect of ACP panel manufacturing, ensuring that the final products meet the required standards and specifications. Here’s how it typically works:
1. What International Standards Should B2B Buyers Look For?
ACP panel manufacturers often adhere to various international quality standards, which can be a good indicator of product reliability. Key standards include:
- ISO 9001: This standard ensures that manufacturers have a robust quality management system in place, which is crucial for maintaining consistent product quality.
- CE Marking: This indicates compliance with EU safety, health, and environmental protection standards, particularly relevant for buyers in Europe.
- API Standards: For panels used in industrial applications, adherence to American Petroleum Institute (API) standards can be critical.
2. What Are the Key Quality Control Checkpoints in ACP Manufacturing?
Quality control (QC) checkpoints play a vital role in ensuring that each panel meets the required specifications. The following checkpoints are commonly implemented:
- Incoming Quality Control (IQC): Raw materials are inspected upon arrival to ensure they meet specified standards.
- In-Process Quality Control (IPQC): During manufacturing, regular inspections are performed to identify and rectify any issues early in the process.
- Final Quality Control (FQC): Once the panels are completed, a thorough inspection is conducted to verify that they meet quality and performance standards.
3. What Common Testing Methods Are Used in ACP Quality Assurance?
ACP manufacturers employ various testing methods to ensure product quality. Common tests include:
- Adhesion Tests: To assess the bond strength between the aluminum and core material.
- Weather Resistance Tests: Panels are exposed to simulated weather conditions to evaluate their performance over time.
- Fire Resistance Tests: Conducted to ensure compliance with fire safety regulations, particularly important for construction applications.
How Can B2B Buyers Verify Supplier Quality Control Processes?
For international buyers, particularly from Africa, South America, the Middle East, and Europe, verifying a supplier’s quality control processes is essential to ensure product reliability.
1. Conducting Supplier Audits
One of the most effective ways to assess a manufacturer’s QC processes is through on-site audits. During an audit, buyers can evaluate:
- Manufacturing Practices: Observing the manufacturing environment, equipment used, and adherence to processes.
- Quality Management Systems: Reviewing documentation related to quality control and compliance with international standards.
2. Requesting Quality Reports
Buyers should request regular quality reports from suppliers, which should detail:
- Inspection Results: Data on IQC, IPQC, and FQC outcomes.
- Testing Results: Information on the results of various tests conducted on the panels.
3. Engaging Third-Party Inspection Services
For additional assurance, buyers may consider engaging third-party inspection services to verify the quality of ACP panels before shipment. These services can provide an unbiased assessment of the manufacturing process and final product quality.
What Are the Quality Control and Certification Nuances for International B2B Buyers?
When sourcing ACP panels internationally, buyers should be aware of specific nuances related to quality control and certification:
- Regional Standards Compliance: Ensure that the products comply with local regulations in the buyer’s region, as these can vary significantly.
- Documentation: Buyers should obtain all necessary certification documents, including test reports and compliance certificates, to facilitate customs clearance and local regulations.
- Supplier Reliability: Establishing long-term relationships with reliable suppliers who have a proven track record in quality assurance can mitigate risks associated with sourcing.
By understanding the manufacturing processes and quality assurance protocols of ACP panel manufacturers, international B2B buyers can make informed decisions that align with their project requirements and quality standards.
Practical Sourcing Guide: A Step-by-Step Checklist for ‘ACP Panel Manufacturers’
In the competitive landscape of ACP (Aluminum Composite Panel) manufacturing, sourcing the right supplier is crucial for international B2B buyers. This practical sourcing guide offers a step-by-step checklist designed to facilitate informed procurement decisions, ensuring quality, compliance, and value for businesses in regions such as Africa, South America, the Middle East, and Europe.
Step 1: Define Your Technical Specifications
Establishing precise technical specifications is fundamental for sourcing ACP panels that meet your project’s requirements. Consider factors such as panel size, thickness, fire resistance ratings, and intended application. This clarity not only aids in communicating with potential suppliers but also helps in comparing products effectively.
Step 2: Research Potential Suppliers
Conduct thorough research to identify reputable ACP panel manufacturers. Utilize online directories, trade shows, and industry forums to compile a list of potential suppliers. Pay attention to their production capabilities, experience in the market, and customer reviews. This initial vetting process is essential to ensure you engage with credible manufacturers.
Step 3: ✅ Verify Supplier Certifications
Confirm that the suppliers you are considering possess relevant certifications and compliance with international standards. Look for certifications such as ISO 9001 for quality management and fire safety certifications specific to ACP products. These credentials not only guarantee product quality but also indicate the supplier’s commitment to industry standards.
Step 4: Request Samples for Evaluation
Before making a bulk order, request samples of the ACP panels to evaluate their quality firsthand. Inspect the samples for color consistency, surface finish, and durability. This step is critical in ensuring that the panels meet your aesthetic and functional requirements, thereby reducing the risk of dissatisfaction post-purchase.
Step 5: Evaluate Manufacturing Capabilities and Lead Times
Understanding a supplier’s manufacturing capabilities is vital for ensuring they can meet your order volume and deadlines. Inquire about their production processes, machinery, and workforce expertise. Additionally, clarify lead times for production and delivery, especially if you are working on a tight project schedule.
Step 6: Discuss Pricing and Payment Terms
Engage in discussions about pricing, payment terms, and any potential discounts for bulk orders. Transparency in pricing is crucial to avoid hidden costs later in the transaction. Ensure that payment terms are favorable and consider options like letters of credit or escrow services for larger orders, which can protect your investment.
Step 7: Establish Communication and Support Channels
Finally, ensure that there are clear communication channels with the supplier. Establish points of contact for order inquiries, support, and after-sales service. Effective communication can facilitate smoother transactions and address any issues that may arise during the procurement process.
By following this step-by-step checklist, international B2B buyers can enhance their sourcing strategy for ACP panels, minimizing risks and maximizing the potential for successful partnerships with manufacturers.
Comprehensive Cost and Pricing Analysis for ACP Panel Manufacturers Sourcing
What Are the Key Cost Components for ACP Panel Manufacturers?
Understanding the cost structure of ACP (Aluminum Composite Panel) manufacturers is crucial for international B2B buyers. The primary cost components include:
-
Materials: The price of raw materials, such as aluminum sheets and polyethylene core, significantly impacts overall costs. Fluctuations in the global aluminum market can lead to price variations, so buyers should consider sourcing strategies that accommodate these changes.
-
Labor: Labor costs vary by region and can be influenced by local wage standards and skill levels. For instance, manufacturers in South Africa may have different labor costs compared to those in Spain or Brazil. Understanding the local labor market can help buyers gauge potential cost savings or increases.
-
Manufacturing Overhead: This includes utilities, rent, equipment maintenance, and administrative expenses. Efficient manufacturing processes and technology investments can reduce overhead costs, which can be a point of negotiation for buyers.
-
Tooling: Initial tooling costs for custom designs can be significant. Buyers should inquire about these costs when requesting quotes, especially for unique or large-scale projects.
-
Quality Control (QC): Rigorous QC processes ensure product consistency and compliance with international standards. While these processes add to manufacturing costs, they can save buyers money in the long run by reducing defects and returns.
-
Logistics: Transportation and shipping costs can vary greatly, especially when importing panels across continents. Factors such as shipping distance, transportation mode, and local tariffs can affect the total logistics costs.
-
Margin: Manufacturers typically mark up prices to cover costs and ensure profitability. Understanding the average industry margin can help buyers identify reasonable pricing.
How Do Price Influencers Impact ACP Panel Costs?
Several factors can influence the pricing structure of ACP panels:
-
Volume/MOQ (Minimum Order Quantity): Higher order volumes often lead to lower per-unit costs. Buyers should evaluate their needs against potential savings from bulk purchasing.
-
Specifications and Customization: Customized panels with unique specifications can incur additional costs. Buyers should weigh the benefits of customization against the price increase.
-
Material Quality and Certifications: Higher quality materials and certifications (such as ISO or fire ratings) can elevate costs. Buyers should assess whether the added expense aligns with their project requirements.
-
Supplier Factors: Supplier reliability, reputation, and production capacity can affect pricing. Engaging with well-established suppliers may provide better service and quality assurance, albeit at a potentially higher price.
-
Incoterms: Understanding Incoterms (International Commercial Terms) is vital for budgeting total costs. Terms like FOB (Free on Board) or CIF (Cost, Insurance, and Freight) can significantly impact the final pricing and risk allocation.
What Are the Best Negotiation Tips for International B2B Buyers?
-
Conduct Market Research: Familiarize yourself with the industry pricing standards and regional market conditions. This knowledge can empower you during negotiations.
-
Request Detailed Quotes: Ask for itemized quotes that break down costs. This transparency can reveal areas for negotiation, such as reducing overhead or finding alternative materials.
-
Leverage Volume Discounts: If your organization has a consistent demand for ACP panels, leverage this to negotiate better pricing or terms with suppliers.
-
Consider Total Cost of Ownership (TCO): Evaluate not just the purchase price but also long-term costs, including maintenance, installation, and potential waste. A slightly higher upfront cost may lead to lower TCO.
-
Build Relationships: Establishing long-term relationships with suppliers can lead to better terms, consistent quality, and priority service.
Final Thoughts on Pricing Nuances for International Buyers
International B2B buyers must be aware of the complexities in ACP panel sourcing, especially regarding pricing. Each region, whether Africa, South America, the Middle East, or Europe, presents unique challenges and opportunities. Prices can vary widely based on local economic conditions, material availability, and manufacturing capabilities.
Disclaimer: The prices discussed in this analysis are indicative and can fluctuate based on market conditions and specific project requirements. Always consult directly with suppliers for the most accurate and up-to-date pricing.
Alternatives Analysis: Comparing ACP Panel Manufacturers With Other Solutions
Understanding Alternatives in ACP Panel Solutions
When considering ACP (Aluminum Composite Panel) manufacturers, it’s essential for international B2B buyers to explore alternative solutions that might better suit their specific requirements. This analysis will compare ACP panels against two viable alternatives: Steel Sheets and Glass Panels. Each option has distinct characteristics that can influence performance, cost, and suitability for various applications.
Comparison Table
Comparison Aspect | ACP Panel Manufacturers | Steel Sheets | Glass Panels |
---|---|---|---|
Performance | Lightweight, good thermal insulation, excellent aesthetic appeal | High durability, corrosion resistance, strong structural support | High transparency, excellent aesthetics, fire-resistant options |
Cost | Moderate initial cost, cost-effective over time | Generally lower upfront cost, but higher installation costs | Higher initial cost, expensive to maintain and install |
Ease of Implementation | Easy to install with standard tools | Requires specialized equipment for cutting and installation | Complex installation requiring skilled labor |
Maintenance | Low maintenance, easy to clean | Requires periodic maintenance to prevent rust | High maintenance, prone to scratching and breakage |
Best Use Case | Ideal for modern buildings, signage, and interiors | Suitable for industrial applications, structural components | Best for facades, windows, and high-end architectural designs |
What Are the Pros and Cons of Steel Sheets?
Steel sheets are a popular alternative due to their robust nature and lower initial costs. Pros include excellent durability and the ability to withstand harsh environmental conditions, making them ideal for industrial settings. Additionally, their lower cost can appeal to budget-conscious buyers. However, cons involve higher installation costs and the need for specialized tools, which can offset initial savings. Furthermore, steel requires regular maintenance to prevent corrosion, which can lead to higher long-term costs.
How Do Glass Panels Compare to ACP Panels?
Glass panels offer a unique aesthetic appeal, particularly in modern architecture. Pros of glass include their transparency and design versatility, enabling natural light to enhance interior spaces. They can also provide superior fire resistance compared to ACP panels. However, the cons are significant; glass is generally more expensive to purchase and install, and it requires skilled labor for installation. Moreover, glass panels are susceptible to scratching and breakage, leading to higher maintenance costs, making them less practical for some applications.
Choosing the Right Solution for Your Needs
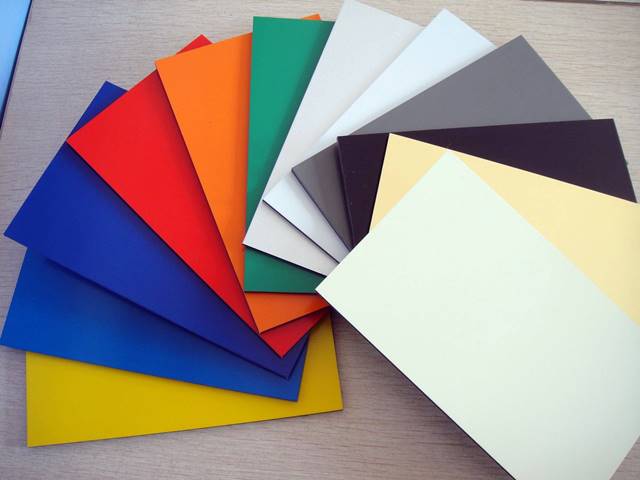
A stock image related to ACP Panel Manufacturers.
When deciding between ACP panels and their alternatives, international B2B buyers should assess their specific project requirements. Factors such as budget constraints, desired aesthetics, and the intended use of the panels will significantly influence the choice. For instance, if aesthetic appeal and natural light are priorities, glass panels may be the best option despite their higher cost. Conversely, for projects requiring durability and cost-effectiveness, ACP panels or steel sheets may be more suitable. Ultimately, thorough research and consideration of these factors will lead to a more informed decision, ensuring the chosen solution aligns with the buyer’s goals and requirements.
Essential Technical Properties and Trade Terminology for ACP Panel Manufacturers
What Are the Key Technical Properties of ACP Panels?
When sourcing ACP (Aluminum Composite Panels), understanding the technical properties is crucial for international B2B buyers. Here are the essential specifications to consider:
1. Material Grade
The material grade of ACP panels typically refers to the type of aluminum alloy used in their construction. Common grades include 3003 and 5005, with 3003 being more ductile and 5005 offering better color retention. The choice of material grade affects durability, weight, and aesthetics, making it vital for buyers to select the right grade based on their specific application needs.
2. Tolerance
Tolerance indicates the permissible variation in dimensions during the manufacturing process. For ACP panels, standard tolerances can range from ±0.5 mm to ±2 mm. Tighter tolerances are essential for applications requiring precision fitting and finishing, such as in architectural facades. Buyers should prioritize suppliers who can consistently meet stringent tolerance requirements to ensure quality installation.
3. Fire Rating
Fire rating is a critical property, especially in regions with strict safety regulations. ACP panels are categorized by their fire performance, often rated as A1, A2, or B. An A1 rating indicates non-combustibility, whereas B-rated panels may have limited combustibility. Understanding these ratings helps buyers comply with local building codes and enhance safety in their projects.
4. Thickness
The thickness of ACP panels typically ranges from 3 mm to 6 mm, influencing both durability and weight. Thicker panels provide greater resistance to impact and bending, making them suitable for high-traffic areas or extreme weather conditions. Buyers should evaluate the intended use of the panels to determine the optimal thickness required for their projects.
5. Surface Finish
The surface finish of ACP panels can vary widely, including options like PVDF (Polyvinylidene fluoride) and polyester coatings. PVDF finishes are renowned for their durability and resistance to UV rays, making them ideal for exterior applications. Choosing the right finish not only impacts aesthetics but also longevity, maintenance, and overall performance.
What Are Common Trade Terms in the ACP Panel Industry?
Familiarity with industry jargon can facilitate smoother transactions and negotiations. Here are key terms that B2B buyers should know:
1. OEM (Original Equipment Manufacturer)
OEM refers to a company that produces parts or equipment that may be marketed by another manufacturer. For ACP panel buyers, working with OEMs allows for custom designs and specifications tailored to their unique project needs, often resulting in cost efficiencies and enhanced product integration.
2. MOQ (Minimum Order Quantity)
MOQ is the smallest number of units that a supplier is willing to sell. Understanding MOQ is crucial for buyers as it impacts inventory management and cost-effectiveness. Suppliers may set MOQs to ensure profitability, so buyers should negotiate to align order quantities with their project requirements.
3. RFQ (Request for Quotation)
An RFQ is a standard business process wherein buyers invite suppliers to submit price quotes for specific products or services. For ACP panel procurement, an RFQ helps in gathering competitive pricing and terms, enabling informed decision-making. Buyers should provide detailed specifications in their RFQs to receive accurate quotes.
4. Incoterms
Incoterms (International Commercial Terms) define the responsibilities of buyers and sellers in international trade. Common terms include FOB (Free On Board) and CIF (Cost Insurance and Freight). Familiarity with these terms helps buyers understand shipping costs, risk transfer, and delivery responsibilities, which are critical for budgeting and logistics planning.
5. Lead Time
Lead time refers to the amount of time from placing an order to receiving the goods. In the ACP industry, lead times can vary based on manufacturing capabilities and shipping logistics. Buyers should factor in lead times when planning projects to avoid delays in construction schedules.
By understanding these technical properties and trade terms, international B2B buyers can make informed decisions when sourcing ACP panels, ensuring quality and efficiency in their procurement processes.
Navigating Market Dynamics and Sourcing Trends in the ACP Panel Manufacturers Sector
What Are the Current Market Dynamics and Key Trends in the ACP Panel Manufacturers Sector?
The ACP (Aluminium Composite Panel) manufacturers sector is experiencing significant growth, driven by the rapid urbanization and infrastructure development across various regions, particularly in Africa, South America, the Middle East, and Europe. Emerging economies are investing heavily in construction and renovation projects, which increases the demand for durable and aesthetically pleasing materials. For international B2B buyers, understanding local regulations, market preferences, and supply chain logistics is crucial for effective sourcing.
Technological advancements are also reshaping the market landscape. The integration of digital tools, such as advanced manufacturing techniques and supply chain management software, is streamlining operations and enhancing product quality. Additionally, the rise of e-commerce platforms is facilitating easier access to suppliers, allowing buyers to compare prices and product specifications more efficiently. As sustainability becomes a focal point in construction, many manufacturers are adopting innovative practices to meet eco-friendly standards.
Furthermore, geopolitical factors, such as trade agreements and tariffs, are influencing sourcing strategies. Buyers must stay informed about changes in international trade policies to mitigate risks and capitalize on opportunities. By leveraging data analytics and market research, B2B buyers can make informed decisions that align with current market dynamics and sourcing trends.
How Can Sustainability and Ethical Sourcing Impact the ACP Panel Manufacturers Sector?
Sustainability is increasingly critical for ACP panel manufacturers, as environmental concerns rise globally. The production process of ACPs can have a significant environmental impact, necessitating the adoption of sustainable practices. B2B buyers are now prioritizing suppliers that demonstrate a commitment to reducing their carbon footprint through energy-efficient production methods and responsible sourcing of raw materials.
Ethical supply chains are equally essential. Manufacturers are under pressure to ensure that their materials are sourced responsibly, minimizing harm to local communities and ecosystems. Certifications such as ISO 14001 (Environmental Management) and LEED (Leadership in Energy and Environmental Design) are becoming important benchmarks for buyers seeking sustainable options. By choosing suppliers with these certifications, B2B buyers can assure their clients of their commitment to environmental stewardship.
In addition, the demand for ‘green’ materials is growing. Buyers are increasingly interested in ACPs made from recycled or sustainably sourced materials, which not only reduce waste but also enhance the marketability of their projects. Emphasizing sustainability and ethical sourcing is not only beneficial for the environment but also enhances brand reputation and consumer trust.
What Is the Brief Evolution of the ACP Panel Manufacturers Sector?
The ACP panel manufacturing sector has evolved significantly over the past few decades. Initially introduced in the 1960s, ACPs were primarily utilized for building facades due to their lightweight and durable nature. Over time, advancements in technology and materials have expanded their applications to include interior design, signage, and more complex architectural projects.
The shift towards sustainability in the 21st century has prompted manufacturers to innovate, focusing on eco-friendly materials and processes. This evolution reflects broader trends in the construction industry, where sustainability and efficiency are increasingly prioritized. As the market continues to grow and diversify, international B2B buyers must remain agile, adapting to changing trends and demands to capitalize on new opportunities in the ACP panel sector.
Frequently Asked Questions (FAQs) for B2B Buyers of ACP Panel Manufacturers
-
How do I evaluate the reliability of ACP panel manufacturers?
To assess the reliability of ACP panel manufacturers, start by researching their industry reputation and customer reviews. Look for certifications like ISO or similar standards that indicate quality assurance. Engage in direct communication with potential suppliers to gauge their responsiveness and willingness to provide detailed product information. Additionally, request references from previous clients to understand their experiences. Attending trade shows or industry events can also provide insights into a manufacturer’s credibility and product quality. -
What is the best way to customize ACP panels for my project needs?
The best approach to customizing ACP panels is to collaborate closely with manufacturers during the design phase. Clearly outline your specifications, including dimensions, colors, finishes, and any specific performance criteria. Many manufacturers offer design consultation services to help align your requirements with their capabilities. Request samples or prototypes to ensure the customization meets your expectations before placing a bulk order. Additionally, inquire about the lead times for custom orders to plan your project timeline effectively. -
What minimum order quantity (MOQ) should I expect from ACP panel manufacturers?
Minimum order quantities (MOQs) for ACP panels can vary significantly among manufacturers, often ranging from 100 to 500 square meters. It’s crucial to discuss MOQs upfront when engaging with suppliers, as smaller manufacturers may be more flexible compared to larger ones. If your project requires a smaller quantity, consider negotiating with the supplier or exploring options for stock panels. Understanding the MOQ will help you manage your budget and ensure that your project remains on schedule. -
What payment terms are typically offered by ACP panel manufacturers?
Payment terms can vary widely, but many ACP panel manufacturers require a deposit of 30-50% upfront, with the balance due upon delivery or prior to shipping. Some may offer more flexible terms, such as letters of credit or installment payments for larger orders. It’s essential to clarify these terms early in negotiations to avoid misunderstandings. Always ensure that payment methods are secure and consider using escrow services for added protection in international transactions. -
How can I ensure the quality of ACP panels I import?
To ensure the quality of imported ACP panels, establish a robust quality assurance process. Request product certifications and test reports from the manufacturer that verify compliance with international standards. Conduct on-site inspections or hire third-party inspection services to assess the panels before shipment. Additionally, consider implementing a sampling strategy where you test a portion of the shipment upon arrival to verify that the panels meet your specifications. -
What logistics considerations should I keep in mind when sourcing ACP panels internationally?
When sourcing ACP panels internationally, consider shipping methods, freight costs, and customs regulations. Choose a reliable freight forwarder experienced in handling construction materials to ensure timely delivery. Be aware of import duties, taxes, and any specific documentation required by your country. Planning for potential delays in customs clearance is also critical. Establish a clear timeline with your supplier to align production schedules with your project needs. -
How do I handle disputes with ACP panel suppliers?
Handling disputes with ACP panel suppliers requires clear communication and documentation. Start by addressing the issue directly with the supplier, providing evidence such as photographs or reports. If resolution is not achieved, refer to the contract terms regarding dispute resolution mechanisms, such as mediation or arbitration. Engaging a legal professional experienced in international trade can also help navigate complex issues. Maintaining a professional demeanor throughout the process will facilitate a more amicable resolution. -
What are the key factors to consider when selecting an ACP panel manufacturer?
When selecting an ACP panel manufacturer, consider factors such as product quality, manufacturing capacity, and technological capabilities. Evaluate their experience in the industry and their ability to meet your specific project requirements. Additionally, assess their customer service responsiveness and willingness to provide support throughout the procurement process. Geographic location can also influence shipping times and costs, so consider manufacturers that are strategically positioned to serve your market effectively.
Important Disclaimer & Terms of Use
⚠️ Important Disclaimer
The information provided in this guide, including content regarding manufacturers, technical specifications, and market analysis, is for informational and educational purposes only. It does not constitute professional procurement advice, financial advice, or legal advice.
While we have made every effort to ensure the accuracy and timeliness of the information, we are not responsible for any errors, omissions, or outdated information. Market conditions, company details, and technical standards are subject to change.
B2B buyers must conduct their own independent and thorough due diligence before making any purchasing decisions. This includes contacting suppliers directly, verifying certifications, requesting samples, and seeking professional consultation. The risk of relying on any information in this guide is borne solely by the reader.
Strategic Sourcing Conclusion and Outlook for ACP Panel Manufacturers
In the dynamic landscape of ACP panel manufacturing, strategic sourcing emerges as a pivotal approach for international B2B buyers. By leveraging a thorough understanding of supplier capabilities, market trends, and technological advancements, companies can optimize their procurement processes to ensure quality, cost-effectiveness, and timely delivery. Buyers from regions such as Africa, South America, the Middle East, and Europe should prioritize establishing strong relationships with manufacturers who demonstrate reliability and innovation.
What are the future trends in ACP panel manufacturing? As sustainability becomes increasingly important, the demand for eco-friendly materials and processes is expected to rise. Furthermore, advancements in manufacturing technology will likely enhance product quality and reduce lead times.
International buyers are encouraged to embrace strategic sourcing as a means to not only secure the best materials but also to foster partnerships that drive mutual growth. By staying informed and adaptable, businesses can position themselves to capitalize on emerging opportunities in the ACP panel market. Take action today—evaluate your sourcing strategies and engage with manufacturers that align with your vision for the future.