Discover Top ACP Panel Manufacturers: Your Complete Guide (2025)
Introduction: Navigating the Global Market for acp panel manufacturers,aluminium composite panel
In the rapidly evolving landscape of construction materials, sourcing aluminium composite panels (ACP panels) has become a pivotal challenge for international B2B buyers. These panels, known for their versatility and durability, are essential in various applications, from architectural facades to interior design. However, navigating the myriad of manufacturers and suppliers across global markets can be daunting, particularly for businesses in Africa, South America, the Middle East, and Europe, such as those in Colombia and Vietnam.
This comprehensive guide aims to demystify the process of sourcing ACP panels by covering essential aspects such as different types of panels available, their applications, and how to effectively vet suppliers. Additionally, we will provide insights into cost considerations, ensuring that buyers can make informed decisions that align with their project budgets and quality requirements.
By equipping international B2B buyers with actionable knowledge and strategies, this guide empowers you to navigate the complexities of the ACP panel market confidently. Whether you are looking to enhance your building projects or seeking reliable manufacturers, understanding the nuances of ACP panels will enable you to make sound purchasing decisions that drive success in your ventures.
Understanding acp panel manufacturers,aluminium composite panel Types and Variations
Type Name | Key Distinguishing Features | Primary B2B Applications | Brief Pros & Cons for Buyers |
---|---|---|---|
Standard ACP Panels | Lightweight, durable, and available in various finishes. | Building facades, interior walls. | Pros: Cost-effective, versatile. Cons: Limited insulation. |
Fire-Resistant ACP Panels | Enhanced fire resistance properties, often with a mineral core. | High-rise buildings, public spaces. | Pros: Safety compliance, reduced risk of fire spread. Cons: Higher cost than standard panels. |
Photovoltaic ACP Panels | Integrated solar technology for energy generation. | Eco-friendly buildings, energy facilities. | Pros: Sustainable energy solution, long-term savings. Cons: Higher initial investment. |
Anti-Graffiti ACP Panels | Coated with a protective layer to resist vandalism. | Urban environments, transportation hubs. | Pros: Easy maintenance, preserves aesthetics. Cons: Potentially higher price point. |
Custom ACP Panels | Tailored designs and finishes to meet specific project needs. | Branding, unique architectural designs. | Pros: Unique appearance, brand differentiation. Cons: Longer lead times, potential for increased costs. |
What are the Characteristics and Suitability of Standard ACP Panels?
Standard ACP panels are a popular choice among B2B buyers due to their lightweight and durable nature. They are manufactured using a polyethylene core sandwiched between two aluminum sheets, offering a smooth finish that can be painted or coated in various colors. These panels are suitable for a wide range of applications, including building facades and interior walls, making them a versatile option for construction projects. Buyers should consider the balance between cost and performance, as while they are economical, they may not offer the best insulation properties.
How Do Fire-Resistant ACP Panels Enhance Safety?
Fire-resistant ACP panels are designed with a mineral core that enhances their ability to withstand high temperatures, making them ideal for high-rise buildings and public spaces where fire safety is paramount. These panels comply with strict fire safety regulations, providing peace of mind for B2B buyers in industries such as construction and architecture. While they come with a higher price tag than standard panels, the investment is justified by the added safety benefits and potential insurance savings.
What Advantages Do Photovoltaic ACP Panels Offer?
Photovoltaic ACP panels integrate solar technology, allowing buildings to generate their own energy. This eco-friendly option is becoming increasingly popular among businesses looking to enhance their sustainability credentials. They are particularly suitable for energy facilities and eco-friendly buildings. While the initial investment is higher, the long-term savings on energy costs and potential government incentives make them an attractive option for forward-thinking B2B buyers.
Why Choose Anti-Graffiti ACP Panels for Urban Environments?
Anti-graffiti ACP panels are coated with a protective layer that makes them resistant to vandalism, making them a smart choice for urban environments and transportation hubs. These panels not only help maintain the aesthetic appeal of buildings but also reduce maintenance costs associated with cleaning graffiti. Although they may come at a premium compared to standard panels, the benefits of easy upkeep and long-term durability can outweigh the initial costs for businesses.
What are the Benefits of Custom ACP Panels?
Custom ACP panels are tailored to meet specific project requirements, allowing businesses to create unique branding or architectural features. These panels can be designed with various finishes and colors to enhance visual appeal. While they may involve longer lead times and potentially higher costs, the ability to differentiate one’s brand and meet specific design needs makes them a valuable investment for B2B buyers in sectors like retail and hospitality.
Related Video: aluminium composite panel ACP cladding
Key Industrial Applications of acp panel manufacturers,aluminium composite panel
Industry/Sector | Specific Application of acp panel manufacturers, aluminium composite panel | Value/Benefit for the Business | Key Sourcing Considerations for this Application |
---|---|---|---|
Construction | Exterior wall cladding for commercial buildings | Enhances aesthetic appeal while providing insulation | Durability, fire resistance, and weatherproofing capabilities |
Transportation | Interior and exterior panels for buses and trains | Lightweight and durable, improving fuel efficiency | Compliance with safety standards and weight specifications |
Retail | Storefront facades and signage | Attracts customers with modern design and branding | Customization options and color consistency |
Hospitality | Interior design elements for hotels and restaurants | Creates a luxurious atmosphere with easy maintenance | Availability of various finishes and textures |
Industrial Facilities | Wall partitions and ceilings in manufacturing plants | Provides sound insulation and enhances workplace safety | Resistance to chemicals and ease of installation |
What Are the Key Industrial Applications of Aluminium Composite Panels?
How are ACP panels used in Construction?
Aluminium composite panels (ACP) serve as exterior wall cladding in commercial buildings, providing a modern aesthetic while also enhancing energy efficiency through insulation. They are lightweight yet strong, making them ideal for high-rise structures. For international buyers, especially in regions like Africa and the Middle East, it’s essential to consider local climate conditions, as panels must withstand extreme temperatures and humidity levels. Additionally, compliance with local building codes and fire safety regulations is critical.
In what ways do ACP panels benefit the Transportation sector?
In the transportation industry, ACP panels are used for both interior and exterior applications in buses and trains. Their lightweight nature contributes to improved fuel efficiency, while their durability ensures a long service life. Buyers must prioritize sourcing panels that meet stringent safety standards, particularly regarding flammability and impact resistance. For regions like South America and Europe, where public transport is a major focus, these panels can also be customized to reflect branding and enhance passenger experience.
How do ACP panels enhance Retail environments?
Retailers use ACP panels for storefront facades and signage, which help create an inviting atmosphere that attracts customers. The versatility of ACP allows for a wide range of colors and finishes, enabling retailers to maintain brand identity. For international B2B buyers, sourcing panels that offer UV resistance is vital to prevent fading in sunlight, especially in tropical regions like Colombia. Additionally, ease of installation and maintenance are significant considerations for minimizing operational disruptions.
What role do ACP panels play in Hospitality?
In the hospitality sector, ACP panels are utilized in interior design elements within hotels and restaurants. They contribute to a luxurious ambiance while being easy to clean and maintain. International buyers should focus on sourcing panels with a variety of textures and finishes that meet design preferences. Furthermore, understanding local supply chain dynamics will help ensure timely deliveries, especially in regions with fluctuating demand, such as Europe and the Middle East.
How do ACP panels improve Industrial Facilities?
In industrial settings, ACP panels are commonly used for wall partitions and ceilings, providing sound insulation and enhancing workplace safety. These panels can resist chemicals and are easy to install, making them suitable for manufacturing environments. Buyers should consider the specific chemical exposure levels in their facilities when sourcing ACP panels. Additionally, the ability to customize sizes and configurations to fit unique layouts is crucial for maximizing operational efficiency.
3 Common User Pain Points for ‘acp panel manufacturers,aluminium composite panel’ & Their Solutions
Scenario 1: Difficulty in Finding Reliable Suppliers for ACP Panels
The Problem: International B2B buyers often struggle to identify reliable suppliers of aluminum composite panels (ACP). This issue is particularly pronounced in regions like Africa and South America, where the market may have fewer established manufacturers. Buyers face challenges such as inconsistent product quality, lack of transparency in pricing, and insufficient after-sales support. These uncertainties can lead to delays in project timelines and increased costs, as buyers may have to deal with subpar materials or engage in lengthy negotiations to find trustworthy suppliers.
The Solution: To effectively source reliable ACP panel manufacturers, buyers should leverage online B2B marketplaces that focus on verified suppliers. Platforms like Alibaba or Global Sources provide user reviews, ratings, and product certifications that can help in assessing supplier credibility. It’s advisable to request samples before placing large orders to evaluate the quality firsthand. Additionally, establishing clear communication about specifications, timelines, and after-sales service expectations during the initial discussions can ensure that both parties are aligned. Setting up a supplier evaluation checklist that includes quality certifications, previous client testimonials, and responsiveness can streamline this process and mitigate risks.
Scenario 2: Inconsistent Product Quality Across Suppliers
The Problem: Another significant pain point is the inconsistency in product quality from different ACP panel manufacturers. Buyers may encounter variations in color, thickness, and finish, which can affect the overall aesthetic and structural integrity of their projects. This inconsistency is especially concerning for projects requiring high precision, such as commercial buildings or luxury residential developments, where aesthetic continuity is critical.
The Solution: To combat quality inconsistency, it is crucial for buyers to establish detailed product specifications and quality standards before initiating procurement. Providing manufacturers with comprehensive technical drawings and specifications can help ensure that the final product meets expectations. Conducting factory audits or hiring third-party quality assurance firms to inspect the manufacturing process can further ensure compliance with specified standards. Additionally, establishing a robust quality control process that includes acceptance testing upon delivery can help catch any discrepancies before installation, thereby reducing the risk of costly rework.
Scenario 3: Lack of Technical Knowledge for ACP Applications
The Problem: Many B2B buyers, especially those new to working with ACP panels, often lack the technical knowledge required to select the appropriate materials for their specific applications. This lack of expertise can lead to poor material choices that may not be suitable for the intended use, such as outdoor installations that require weather-resistant properties or fire-rated panels for safety compliance. Such missteps can result in project delays, increased costs, and safety risks.
The Solution: Buyers should invest time in understanding the technical aspects of ACP panels by engaging with manufacturers who offer educational resources and technical support. Seeking out manufacturers that provide comprehensive product documentation, including installation guidelines, material properties, and compliance certifications, can empower buyers to make informed decisions. Additionally, participating in webinars or industry workshops focused on ACP applications can enhance understanding and build confidence. Engaging a project consultant with experience in ACP specifications can also be beneficial, providing tailored advice that aligns with the unique requirements of the project, ensuring optimal material selection and application.
Strategic Material Selection Guide for acp panel manufacturers,aluminium composite panel
What Are the Common Materials Used in Aluminium Composite Panels?
Aluminium Composite Panels (ACP) are widely used in construction and architectural applications due to their versatility and aesthetic appeal. The selection of materials for ACP manufacturing significantly affects the panels’ performance, durability, and suitability for various applications. Below, we analyze four common materials used in ACP manufacturing, providing insights tailored for international B2B buyers, particularly from Africa, South America, the Middle East, and Europe.
Which Core Materials Are Commonly Used in ACP Manufacturing?
1. Polyethylene (PE)
Key Properties:
Polyethylene is lightweight and offers good flexibility, making it a popular choice for ACP cores. It has a moderate temperature resistance (up to 80°C) and is not suitable for high-stress applications.
Pros & Cons:
– Pros: Cost-effective, easy to process, and provides good insulation properties.
– Cons: Limited fire resistance and lower durability compared to other materials.
Impact on Application:
PE cores are suitable for indoor applications and areas with low fire risk, such as commercial interiors. However, they may not be ideal for high-temperature environments.
Considerations for International Buyers:
Compliance with fire safety standards (e.g., ASTM E84) is essential, especially in regions with stringent regulations. Buyers in Europe may prefer materials with higher fire ratings.
2. Fire-Retardant Polyethylene (FR-PE)
Key Properties:
FR-PE is designed to offer improved fire resistance, withstanding temperatures up to 120°C. It incorporates additives that limit flame spread.
Pros & Cons:
– Pros: Enhanced safety features, making it suitable for high-rise buildings and public spaces.
– Cons: Higher manufacturing costs and potential processing complexities.
Impact on Application:
FR-PE is ideal for applications requiring compliance with strict fire safety regulations, such as in urban centers across Europe and the Middle East.
Considerations for International Buyers:
International buyers should ensure that FR-PE complies with local fire safety standards, such as EN 13501 in Europe. Understanding local regulations is crucial for project approvals.
3. Mineral-Filled Core (MFC)
Key Properties:
MFCs are composed of mineral-based materials, providing excellent fire resistance and thermal insulation. They can withstand higher temperatures compared to PE cores.
Pros & Cons:
– Pros: Superior fire resistance and durability, making them suitable for exterior applications.
– Cons: Heavier and more expensive than PE options, which can increase shipping costs.
Impact on Application:
MFCs are ideal for high-performance applications, such as facades in commercial buildings, where aesthetics and safety are paramount.
Considerations for International Buyers:
Buyers should be aware of the increased shipping costs due to weight and ensure compliance with international building codes, especially in regions with seismic activity.
4. Aluminium Honeycomb Core
Key Properties:
Aluminium honeycomb cores are lightweight yet strong, providing excellent structural integrity and thermal insulation. They are resistant to corrosion and can withstand high temperatures.
Pros & Cons:
– Pros: High strength-to-weight ratio and excellent durability, making them suitable for a wide range of applications.
– Cons: Higher manufacturing costs and complexity in production.
Impact on Application:
Aluminium honeycomb cores are perfect for applications requiring high strength and low weight, such as aerospace and high-end architectural projects.
Considerations for International Buyers:
International buyers should consider the manufacturing capabilities of suppliers to ensure quality and compliance with standards like ISO 9001.
Summary Table of Material Properties for ACP Manufacturing
Material | Typical Use Case for acp panel manufacturers,aluminium composite panel | Key Advantage | Key Disadvantage/Limitation | Relative Cost (Low/Med/High) |
---|---|---|---|---|
Polyethylene (PE) | Indoor applications, commercial interiors | Cost-effective, good insulation | Limited fire resistance | Low |
Fire-Retardant Polyethylene (FR-PE) | High-rise buildings, public spaces | Enhanced fire safety | Higher manufacturing costs | Medium |
Mineral-Filled Core (MFC) | Facades in commercial buildings | Superior fire resistance | Heavier, more expensive | High |
Aluminium Honeycomb Core | Aerospace, high-end architectural projects | High strength-to-weight ratio | Higher manufacturing complexity | High |
This guide provides a comprehensive overview of the materials used in ACP manufacturing, ensuring international B2B buyers can make informed decisions based on performance, costs, and compliance with local standards.
In-depth Look: Manufacturing Processes and Quality Assurance for acp panel manufacturers,aluminium composite panel
What Are the Key Stages in the Manufacturing Process of Aluminium Composite Panels?
Aluminium composite panels (ACP) are renowned for their versatility and durability, making them a popular choice in construction and design. Understanding the manufacturing process is crucial for B2B buyers looking to source quality products. The typical manufacturing process involves several key stages:
-
Material Preparation: The first stage includes selecting high-quality raw materials. This typically involves two aluminium sheets and a non-aluminium core, often made from materials like polyethylene or mineral-filled cores for fire resistance. Buyers should ensure that suppliers source materials that meet industry standards.
-
Forming: During this stage, the aluminium sheets are cut and shaped. This can involve processes such as rolling, stamping, or pressing. Advanced techniques like CNC machining may be employed to ensure precision. B2B buyers should inquire about the machinery used and the capabilities of the manufacturer.
-
Assembly: In this phase, the core material is sandwiched between the two aluminium sheets. This assembly can be completed using adhesive bonding or mechanical fastening. The choice of assembly technique can affect the final product’s strength and durability, so it’s essential for buyers to discuss these options with suppliers.
-
Finishing: The final stage includes surface treatment and coating. This often involves applying protective coatings or finishes, such as PVDF (Polyvinylidene Fluoride) or PE (Polyester), to enhance the panel’s resistance to weather and UV rays. Buyers should ask for samples of finishes to assess quality and durability.
How is Quality Assurance Implemented in ACP Manufacturing?
Quality assurance (QA) is critical in ensuring that ACPs meet both international and industry-specific standards. The following outlines the key QA practices:
-
International Standards: Manufacturers should comply with ISO 9001, which focuses on quality management systems. This certification ensures that processes are consistently monitored and improved. Additionally, certifications such as CE mark and API (American Petroleum Institute) can be relevant for specific applications.
-
Quality Control Checkpoints:
– Incoming Quality Control (IQC): This involves inspecting raw materials upon arrival to ensure they meet specified standards. B2B buyers can request IQC reports to verify that materials used in production are of high quality.
– In-Process Quality Control (IPQC): Conducted throughout the manufacturing process, IPQC checks for defects during each stage of production. This step is crucial to minimize waste and ensure product integrity.
– Final Quality Control (FQC): Before shipment, panels undergo thorough inspection and testing. This includes visual inspections and performance tests to ensure compliance with specifications. -
Testing Methods for ACPs: Common testing methods include:
– Bending and tensile strength tests: To evaluate the structural integrity.
– Weather resistance tests: To assess the panel’s durability against environmental factors.
– Fire resistance tests: Particularly important for panels used in high-rise buildings.
How Can B2B Buyers Verify Supplier Quality Control Practices?
For international B2B buyers, particularly those from Africa, South America, the Middle East, and Europe, verifying supplier quality control practices is crucial. Here are some actionable steps:
-
Conduct Audits: Regular audits of potential suppliers can provide insights into their manufacturing processes and quality control measures. Buyers should develop a checklist based on the relevant standards and practices.
-
Request Documentation: Suppliers should provide documentation, including quality assurance plans, certification copies, and test reports. This documentation serves as proof of compliance with industry standards.
-
Third-Party Inspections: Engaging third-party inspection agencies can help verify that the products meet specified requirements. This is particularly valuable for buyers unfamiliar with local manufacturing practices.
-
Sample Testing: Before committing to large orders, B2B buyers should request samples for independent testing. This can help assess the quality and performance of the ACPs.
What Are the Nuances of Quality Control for International B2B Buyers?
Navigating the quality control landscape in international trade can be challenging. Here are some nuances to consider:
-
Cultural Differences: Different regions may have varying expectations regarding quality and standards. Buyers should be aware of these cultural differences and adapt their communication and expectations accordingly.
-
Regulatory Compliance: Different countries have specific regulations regarding building materials. Buyers should ensure that the ACPs sourced comply with local regulations, such as fire safety standards in the Middle East or energy efficiency regulations in Europe.
-
Supplier Relationships: Building strong relationships with suppliers can enhance communication regarding quality expectations. Regular feedback and collaboration can help maintain quality standards over time.
-
Market Variability: The ACP market may vary significantly between regions, affecting pricing, availability, and quality. Buyers should conduct market research to understand these differences and leverage them when negotiating with suppliers.
By understanding the manufacturing processes and quality assurance practices associated with aluminium composite panels, B2B buyers can make informed decisions that align with their quality expectations and business needs.
Practical Sourcing Guide: A Step-by-Step Checklist for ‘acp panel manufacturers,aluminium composite panel’
Introduction
Navigating the procurement of aluminium composite panels (ACP) can be complex, particularly for international B2B buyers in regions like Africa, South America, the Middle East, and Europe. This guide offers a practical checklist to streamline your sourcing process, ensuring that you select the right manufacturers and products to meet your project’s requirements.
Step 1: Define Your Technical Specifications
Establishing clear technical specifications is the foundation of a successful sourcing process. Consider factors such as panel thickness, fire resistance ratings, surface finishes, and color options. Providing detailed specifications helps manufacturers understand your needs, reducing the risk of miscommunication and ensuring that the final product meets your expectations.
Step 2: Conduct Market Research
Before engaging with suppliers, conduct thorough market research to understand the landscape of ACP panel manufacturers. Identify key players in the market and analyze their product offerings, pricing, and service levels. Look for reviews and testimonials from other buyers, particularly from your region, to gauge the reliability and reputation of potential suppliers.
Step 3: Evaluate Potential Suppliers
Before committing, it’s crucial to vet suppliers thoroughly. Request company profiles, case studies, and references from buyers in a similar industry or region. Key aspects to consider include:
– Experience and Expertise: Ensure the supplier has a proven track record in manufacturing ACP panels.
– Production Capacity: Confirm that the supplier can meet your order volume and timeline.
Step 4: Verify Supplier Certifications
Certifications ensure that the manufacturer adheres to industry standards and regulations, which is critical for product quality and safety. Look for certifications such as ISO 9001 for quality management systems and fire safety certifications relevant to your location. Verifying these credentials not only protects your investment but also ensures compliance with local building codes.
Step 5: Request Samples
Once you have narrowed down your options, request samples of the ACP panels. Evaluating samples allows you to assess the product quality, including aesthetics, texture, and durability. It’s an essential step to ensure that the panels meet your design and functional requirements before making a larger investment.
Step 6: Negotiate Terms and Conditions
Engage in discussions to negotiate terms and conditions, including pricing, payment terms, and delivery schedules. Clear agreements on these factors can prevent misunderstandings later. Additionally, consider including clauses regarding warranties and after-sales support to protect your investment.
Step 7: Plan for Logistics and Import Regulations
Understanding the logistics involved in importing ACP panels is crucial, particularly for international buyers. Research shipping options, customs duties, and import regulations specific to your country. Efficient logistics planning will minimize delays and additional costs, ensuring that your panels arrive on time and in good condition.
By following this step-by-step checklist, you can navigate the complexities of sourcing aluminium composite panels effectively, ensuring that you choose the right manufacturer to meet your project needs.
Comprehensive Cost and Pricing Analysis for acp panel manufacturers,aluminium composite panel Sourcing
What Are the Key Cost Components for ACP Panel Manufacturing?
Understanding the cost structure of aluminium composite panels (ACP) is crucial for international B2B buyers. The primary cost components include:
-
Materials: The most significant expense in ACP production. Quality of the aluminium and core material significantly affects price. Buyers should consider sourcing high-quality materials to ensure durability, which can impact the total cost of ownership.
-
Labor: Labor costs vary by region and can significantly influence pricing. Countries with higher labor costs may offer advanced manufacturing technologies that can enhance product quality.
-
Manufacturing Overhead: This includes utility costs, facility maintenance, and equipment depreciation. Efficient manufacturing processes can help reduce overhead, making it essential to evaluate the supplier’s operational efficiency.
-
Tooling: Initial tooling costs can be substantial, especially for custom designs. Understanding the tooling process can provide insight into potential upfront costs and timeframes for production.
-
Quality Control (QC): Implementing rigorous QC processes is vital for ensuring product reliability. While it adds to costs, effective QC can prevent costly returns or reputational damage.
-
Logistics: Transportation and handling can be significant, particularly for international shipments. Costs can vary based on shipping methods, distances, and any applicable tariffs.
-
Margin: This represents the supplier’s profit after covering all costs. Understanding the expected margin can help buyers assess whether the pricing aligns with market standards.
How Do Price Influencers Affect ACP Panel Costs?
Several factors can influence the pricing of ACP panels, which are particularly relevant for international buyers:
-
Volume/MOQ (Minimum Order Quantity): Larger orders often result in lower unit prices due to economies of scale. Buyers should consider their projected needs to negotiate better terms.
-
Specifications and Customization: Custom designs and specific material requirements can increase costs. Buyers should clearly define their specifications to avoid unexpected price hikes.
-
Materials Quality and Certifications: High-quality materials and industry certifications (e.g., fire resistance, environmental certifications) can lead to higher prices. However, they also ensure compliance with international standards, which is crucial for market entry in regions like Europe and the Middle East.
-
Supplier Factors: The supplier’s reputation, production capacity, and geographical location can all impact pricing. Engaging with suppliers who have a proven track record can yield better pricing and reliability.
-
Incoterms: The chosen Incoterms (e.g., FOB, CIF) will affect the overall cost structure. Buyers should understand the implications of these terms on shipping and risk management.
What Negotiation Tips Can Help International B2B Buyers?
For B2B buyers from regions like Africa, South America, the Middle East, and Europe, effective negotiation strategies can significantly impact costs:
-
Research the Market: Understand the typical pricing for ACP panels in your region. This knowledge will empower you to negotiate effectively and avoid overpaying.
-
Establish Relationships: Building a strong relationship with suppliers can lead to better pricing and terms. Regular communication can foster trust and facilitate negotiations.
-
Consider Total Cost of Ownership (TCO): Evaluate the long-term costs associated with the product, including maintenance and potential failures, rather than focusing solely on the initial price.
-
Leverage Multiple Quotes: Obtain quotes from several suppliers to compare pricing and terms. This practice can provide leverage in negotiations.
-
Be Aware of Pricing Nuances: Understand the impact of currency fluctuations, international shipping costs, and tariffs on pricing. These factors can significantly alter the final cost, especially for international transactions.
Disclaimer on Indicative Prices
Prices for aluminium composite panels can vary widely based on the factors discussed. It is essential for buyers to conduct thorough market research and engage directly with suppliers for the most accurate and up-to-date pricing information.
Alternatives Analysis: Comparing acp panel manufacturers,aluminium composite panel With Other Solutions
Understanding Alternatives for ACP Panels: What Are the Options?
When considering alternatives to ACP (Aluminium Composite Panels) for various applications, it’s essential to evaluate different solutions based on performance, cost, ease of implementation, maintenance, and best use cases. This analysis will help international B2B buyers, particularly from Africa, South America, the Middle East, and Europe, make informed decisions tailored to their specific needs.
Comparison Table of ACP Panels with Alternatives
Comparison Aspect | Acp Panel Manufacturers, Aluminium Composite Panel | Alternative 1: Steel Panels | Alternative 2: Glass Panels |
---|---|---|---|
Performance | Excellent durability and weather resistance | High strength, but prone to rust without coating | Superior aesthetics, but can be fragile |
Cost | Moderate initial investment, cost-effective over time | Generally lower upfront cost, higher long-term maintenance | Higher initial cost, limited cost-effectiveness |
Ease of Implementation | Relatively easy to install with proper training | Requires skilled labor for installation | Complex installation requiring specialized skills |
Maintenance | Low maintenance, easy to clean | Moderate, needs regular inspections | High maintenance, requires careful handling |
Best Use Case | Commercial buildings, interior and exterior cladding | Industrial applications, structural components | High-end architectural projects, facades |
Pros and Cons of Each Alternative
Steel Panels: What Are Their Strengths and Weaknesses?
Steel panels are often chosen for their strength and durability. They are suitable for industrial applications where structural integrity is crucial. However, they require protective coatings to prevent rust, which can increase long-term maintenance costs. While the initial investment may be lower compared to ACP panels, the need for regular inspections and upkeep can offset these savings, making them a less cost-effective option over time.
Glass Panels: Are They a Viable Option for Your Project?
Glass panels are celebrated for their aesthetic appeal and ability to create a modern look in architectural designs. They are often used in high-end projects to enhance visual appeal. However, glass panels can be fragile and require careful handling during installation and maintenance. The initial investment is typically higher than ACP panels, and the ongoing maintenance can be cumbersome, especially in environments prone to weathering or impact damage.
Conclusion: How to Choose the Right Solution for Your Needs
Selecting the appropriate solution among ACP panels and their alternatives hinges on your specific project requirements. If durability, low maintenance, and cost-effectiveness are your priorities, ACP panels are likely the best choice. Conversely, if your project demands structural strength or high-end aesthetics, exploring steel or glass panels may be worthwhile. Assessing the unique needs of your application, budget constraints, and long-term maintenance expectations will guide you in making the most suitable decision for your B2B procurement.
Essential Technical Properties and Trade Terminology for acp panel manufacturers,aluminium composite panel
What are the Key Technical Properties of Aluminium Composite Panels (ACP)?
When dealing with ACPs, understanding their technical specifications is crucial for B2B buyers to ensure they meet project requirements and performance standards. Here are the essential properties to consider:
-
Material Grade
– Aluminium composite panels typically consist of two thin layers of aluminium enclosing a non-aluminium core. The material grade of the aluminium (e.g., 3003, 5005) affects the panel’s strength, weight, and corrosion resistance. Choosing the right material grade is vital for applications exposed to harsh environmental conditions. -
Thickness
– The thickness of ACPs generally ranges from 3mm to 6mm. Thicker panels provide enhanced durability and insulation properties, making them suitable for high-traffic areas and extreme weather conditions. Buyers should assess the required thickness based on the intended use and structural demands of their projects. -
Fire Rating
– Fire performance is a critical consideration, particularly in commercial buildings. ACPs are classified according to their fire rating, which can range from non-combustible to combustible. Understanding the fire safety regulations in your region is essential to ensure compliance and safety in building design. -
Surface Finish
– ACPs come with various surface finishes, including PVDF (polyvinylidene fluoride), polyester, and anodized coatings. The choice of finish impacts aesthetics, durability, and resistance to fading and scratching. Buyers should select finishes that align with their design vision and maintenance preferences. -
Tolerance Levels
– Tolerance levels refer to the permissible deviations in dimensions and flatness of the panels. High precision in tolerances is crucial for ensuring proper installation and alignment, which can affect the overall appearance and functionality of the finished project.
What are the Common Trade Terms Used in ACP Manufacturing and Sourcing?
Familiarity with industry jargon can facilitate smoother negotiations and procurement processes. Here are some essential trade terms:
-
OEM (Original Equipment Manufacturer)
– In the context of ACPs, OEM refers to companies that manufacture panels based on specifications provided by another company, often a brand or distributor. Understanding OEM relationships can help buyers leverage quality and pricing advantages. -
MOQ (Minimum Order Quantity)
– MOQ is the smallest quantity of products a supplier is willing to sell. For ACPs, MOQs can significantly impact project budgets and timelines, especially for smaller projects. Buyers should negotiate MOQs to align with their project needs. -
RFQ (Request for Quotation)
– An RFQ is a document issued by buyers to solicit price quotes from suppliers for specific products or services. Crafting a detailed RFQ for ACPs can help ensure that suppliers provide accurate pricing, lead times, and product specifications. -
Incoterms (International Commercial Terms)
– Incoterms define the responsibilities of buyers and sellers in international transactions, particularly regarding shipping and delivery. Understanding these terms (like FOB, CIF) is essential for B2B buyers to manage logistics and costs effectively. -
Lead Time
– Lead time refers to the time taken from placing an order to delivery. In the ACP industry, lead times can vary based on the complexity of the order, stock availability, and production schedules. Buyers should factor in lead times when planning project timelines to avoid delays.
By understanding these technical properties and trade terms, international B2B buyers can make informed decisions when sourcing aluminium composite panels, ensuring that they select the right products for their projects while navigating the complexities of global trade effectively.
Navigating Market Dynamics and Sourcing Trends in the acp panel manufacturers,aluminium composite panel Sector
What Are the Current Market Dynamics and Key Trends in the ACP Panel Manufacturing Sector?
The global aluminium composite panel (ACP) market is experiencing significant growth, driven by increased demand for lightweight and durable building materials across various industries, including construction, automotive, and signage. The expansion of urbanization and infrastructure development in emerging markets, particularly in Africa and South America, has spurred demand for ACPs, as they offer aesthetic appeal, insulation, and weather resistance. Moreover, technological advancements in manufacturing processes, such as automated production lines and innovative coating technologies, are enhancing product quality and reducing costs, making ACPs more accessible for international buyers.
Emerging B2B technology trends, such as online marketplaces and digital procurement solutions, are reshaping sourcing strategies for international buyers. These platforms facilitate direct connections between manufacturers and purchasers, allowing for better price comparisons and streamlined order processes. Additionally, the integration of data analytics in supply chain management is enabling manufacturers to optimize inventory levels and predict market trends more accurately. For buyers from regions like the Middle East and Europe, understanding these dynamics is crucial for making informed purchasing decisions.
How Important Is Sustainability and Ethical Sourcing in the ACP Panel Sector?
Sustainability is becoming a central focus in the aluminium composite panel manufacturing industry. The environmental impact of ACP production, including energy consumption and waste generation, is prompting manufacturers to adopt more sustainable practices. This includes the use of recycled materials and eco-friendly production techniques that minimize carbon footprints. Buyers are increasingly prioritizing suppliers who adhere to sustainable practices, as this not only aligns with corporate social responsibility goals but also meets the growing consumer demand for environmentally friendly products.
Moreover, ethical sourcing has gained traction, with international buyers seeking suppliers who comply with fair labor practices and environmental regulations. Certifications such as ISO 14001 for environmental management and LEED (Leadership in Energy and Environmental Design) for sustainable building materials are becoming essential for manufacturers aiming to appeal to conscientious buyers. By prioritizing suppliers with ‘green’ certifications, international buyers can ensure that their procurement decisions contribute positively to both the environment and society.
What Is the Evolution of the ACP Panel Industry and Its Relevance to B2B Buyers?
The aluminium composite panel industry has evolved significantly since its inception in the late 20th century. Initially developed for architectural applications, ACPs have expanded into a variety of sectors due to their versatility and performance characteristics. The introduction of advanced manufacturing technologies has led to improvements in panel durability, fire resistance, and aesthetic options, making them suitable for high-rise buildings, commercial spaces, and even residential applications.
For B2B buyers, understanding the historical context of ACP development is vital. It highlights the industry’s adaptability and innovation in response to changing market needs and regulatory requirements. As the sector continues to evolve, staying informed about historical trends can help buyers anticipate future developments and make strategic sourcing decisions that align with their business objectives.
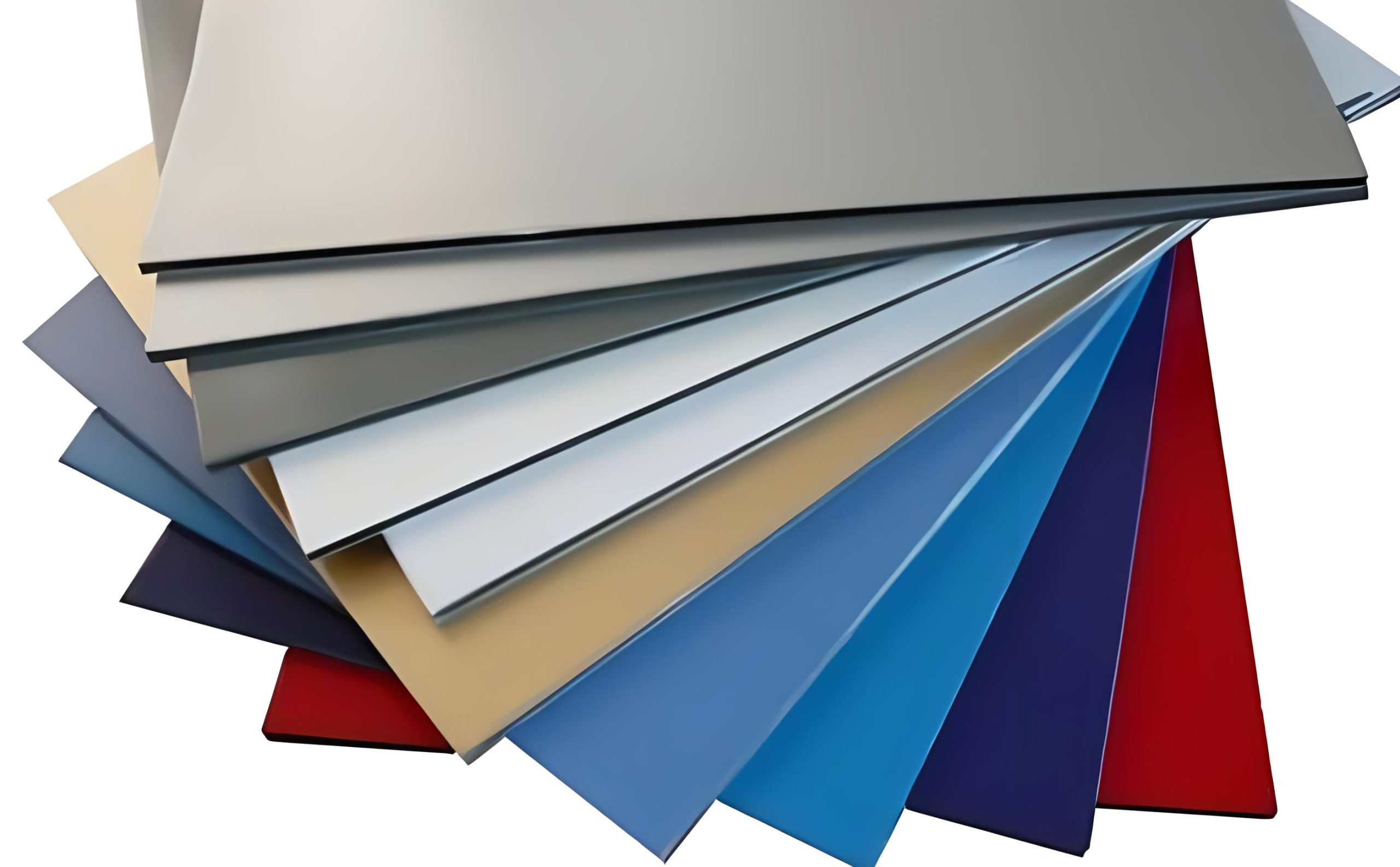
A stock image related to acp panel manufacturers,aluminium composite panel.
Frequently Asked Questions (FAQs) for B2B Buyers of acp panel manufacturers,aluminium composite panel
-
How do I choose the right aluminium composite panel manufacturer for my project?
When selecting an aluminium composite panel manufacturer, consider their industry experience, product quality, and certifications. Look for suppliers with a strong portfolio that showcases past projects similar to yours. It’s also essential to verify their compliance with international standards, such as ISO certifications. Engage in discussions to understand their manufacturing processes and customer service approach. Request samples to assess the quality of the panels before making a commitment. -
What are the typical minimum order quantities (MOQ) for aluminium composite panels?
Minimum order quantities for aluminium composite panels can vary significantly between manufacturers. Typically, MOQs range from 100 to 500 square meters, depending on the supplier and the specific product. If your project requires a smaller quantity, some manufacturers may accommodate you with a premium price or allow consolidation with other orders. Always clarify the MOQ during initial discussions to avoid unexpected costs later on. -
What customization options are available for aluminium composite panels?
Many manufacturers offer a range of customization options for aluminium composite panels, including thickness, color, and surface finishes. Some suppliers may also provide options for custom sizes and shapes to fit specific project needs. Discuss your requirements early in the negotiation process to understand the available choices and any additional costs associated with customization. Be sure to review samples to ensure the customizations meet your expectations. -
What payment terms should I expect when sourcing aluminium composite panels internationally?
Payment terms for international orders can vary widely, but common practices include upfront deposits (typically 30-50%) with the balance due upon delivery or before shipment. Some suppliers may offer more flexible payment options, such as letters of credit or extended payment plans for larger orders. Always confirm payment terms in writing and consider using secure payment methods to mitigate risks associated with international transactions. -
How can I ensure quality assurance when purchasing aluminium composite panels?
To ensure quality assurance, request detailed product specifications and certifications from the manufacturer. Many reputable suppliers will conduct rigorous testing on their panels, including fire resistance and weather durability. Consider arranging third-party inspections or audits if you’re placing a large order. Establish clear quality control standards in your contract and ensure there is a return policy for defective panels. -
What logistics considerations should I be aware of when importing aluminium composite panels?
Importing aluminium composite panels involves several logistics considerations, including shipping methods, customs clearance, and delivery timelines. Choose a reliable freight forwarder experienced in handling construction materials. Understand the shipping costs, which can vary based on weight, volume, and distance. Additionally, ensure that all necessary documentation for customs is prepared in advance to avoid delays.
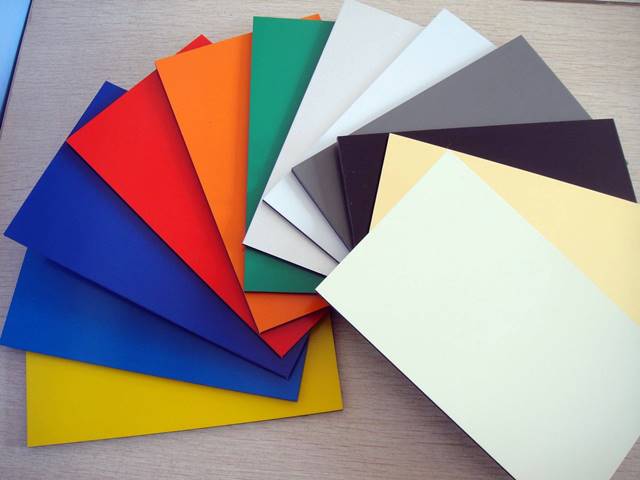
A stock image related to acp panel manufacturers,aluminium composite panel.
-
Are there specific regulations or standards for aluminium composite panels in different regions?
Yes, aluminium composite panels are subject to various regulations and standards that differ by region. For example, in Europe, the EN 13501 standard governs fire performance, while in the US, the ASTM standards apply. It is crucial to familiarize yourself with the local building codes and safety regulations of the destination country to ensure compliance. Manufacturers should provide documentation proving their products meet these standards. -
What should I do if there are issues with my order of aluminium composite panels?
If you encounter issues with your order, such as defective panels or discrepancies in quantity, contact your supplier immediately to discuss the problem. Document the issues with photos and detailed descriptions to support your claim. Most reputable manufacturers will have a customer service protocol in place to address complaints. Review your contract to understand your rights regarding returns, refunds, or replacements.
Important Disclaimer & Terms of Use
⚠️ Important Disclaimer
The information provided in this guide, including content regarding manufacturers, technical specifications, and market analysis, is for informational and educational purposes only. It does not constitute professional procurement advice, financial advice, or legal advice.
While we have made every effort to ensure the accuracy and timeliness of the information, we are not responsible for any errors, omissions, or outdated information. Market conditions, company details, and technical standards are subject to change.
B2B buyers must conduct their own independent and thorough due diligence before making any purchasing decisions. This includes contacting suppliers directly, verifying certifications, requesting samples, and seeking professional consultation. The risk of relying on any information in this guide is borne solely by the reader.
Strategic Sourcing Conclusion and Outlook for acp panel manufacturers,aluminium composite panel
In summary, strategic sourcing remains a pivotal component for international B2B buyers in the aluminium composite panel (ACP) market. By prioritizing supplier relationships and leveraging global networks, businesses can secure high-quality materials while optimizing costs. Buyers from Africa, South America, the Middle East, and Europe must focus on identifying manufacturers that not only meet technical specifications but also align with sustainability goals and compliance standards.
What are the key considerations for successful ACP sourcing? Understanding the local market dynamics, establishing clear communication channels, and evaluating suppliers based on their reliability and innovation capabilities will enhance sourcing effectiveness. As the global demand for ACP panels continues to grow, it is essential for buyers to stay informed about industry trends and technological advancements.
Looking ahead, the ACP market is set to evolve, driven by advancements in manufacturing processes and increasing environmental regulations. International buyers are encouraged to actively engage with suppliers, attend industry events, and explore partnerships that foster innovation. By doing so, they will not only enhance their supply chain resilience but also contribute to the sustainable development of the ACP industry. Embrace the future of sourcing and position your business for success in this dynamic landscape.