Discover Top Air Filter Manufacturers: A Complete Guide (2025)
Introduction: Navigating the Global Market for air filter manufacturer
In today’s rapidly evolving global market, sourcing high-quality air filters presents a significant challenge for international B2B buyers, especially those from regions like Africa, South America, the Middle East, and Europe. The demand for efficient air filtration systems is rising, driven by increasing industrialization, stringent environmental regulations, and a growing focus on workplace health. This guide aims to simplify the complex landscape of air filter manufacturers, providing a comprehensive overview of types, applications, supplier vetting processes, and cost considerations.
As you navigate the myriad options available, understanding the various categories of air filters—such as HEPA, activated carbon, and electrostatic filters—will empower you to make informed purchasing decisions. This guide will delve into the essential criteria for evaluating suppliers, including certifications, product quality, and customer service. Furthermore, it will address the cost factors associated with sourcing air filters, helping you identify budget-friendly solutions without compromising on quality.
By equipping B2B buyers with actionable insights and strategies tailored to their specific needs, this guide serves as a vital resource for companies seeking reliable air filter manufacturers. Whether you’re in Mexico, Indonesia, or elsewhere, understanding the global market landscape will enhance your procurement processes, ensuring you secure the best possible products for your operational requirements.
Understanding air filter manufacturer Types and Variations
Type Name | Key Distinguishing Features | Primary B2B Applications | Brief Pros & Cons for Buyers |
---|---|---|---|
HEPA Filter Manufacturers | High efficiency particulate air (HEPA) filters | Hospitals, cleanrooms, laboratories | Pros: Excellent air quality; high filtration efficiency. Cons: Higher initial cost; requires regular maintenance. |
Activated Carbon Filter Manufacturers | Use of activated carbon for odor and gas removal | Food processing, chemical industries | Pros: Effective in removing odors and VOCs; improves air quality. Cons: Limited particulate filtration; needs replacement after saturation. |
Electrostatic Filter Manufacturers | Utilizes electrostatic charge for particle capture | HVAC systems, industrial applications | Pros: Low energy consumption; reusable and washable. Cons: Initial setup cost; may require specialized maintenance. |
Disposable Filter Manufacturers | Single-use filters made from various materials | Residential, commercial HVAC systems | Pros: Cost-effective; easy to replace. Cons: Higher long-term costs; more waste generated. |
Custom Air Filter Manufacturers | Tailored filters designed for specific applications | Aerospace, automotive, manufacturing | Pros: Optimized performance for unique needs; enhances operational efficiency. Cons: Longer lead times; potentially higher costs. |
What Are HEPA Filter Manufacturers and Their B2B Relevance?
HEPA filter manufacturers produce filters that meet stringent efficiency standards, capturing at least 99.97% of particles 0.3 microns in size. These filters are crucial in environments where air quality is paramount, such as hospitals and laboratories. B2B buyers should consider the initial investment and ongoing maintenance costs, as HEPA filters require regular replacement to maintain their efficacy. However, the benefits of enhanced air quality and compliance with health regulations often justify the expense.
How Do Activated Carbon Filter Manufacturers Enhance Air Quality?
Activated carbon filter manufacturers focus on producing filters that excel at removing odors, volatile organic compounds (VOCs), and other gaseous pollutants. These filters are widely used in food processing and chemical industries where air quality is vital. When purchasing, B2B buyers should evaluate the filter’s saturation point and replacement frequency, as these factors can impact long-term operational costs. While effective for gas removal, these filters may not be suitable for particulate filtration, necessitating a dual-filter system in some applications.
What Are the Benefits of Electrostatic Filter Manufacturers?
Electrostatic filter manufacturers create filters that utilize an electrostatic charge to attract and capture airborne particles. Commonly used in HVAC systems and various industrial applications, these filters are known for their low energy consumption and ability to be washed and reused. B2B buyers should weigh the initial setup costs against the long-term savings from reduced waste and lower energy bills. However, specialized maintenance may be required, which could complicate operations for some businesses.
Why Choose Disposable Filter Manufacturers for Your B2B Needs?
Disposable filter manufacturers provide single-use filters that are cost-effective and easy to replace, making them ideal for residential and commercial HVAC systems. These filters are typically made from various materials designed for quick installation and disposal. B2B buyers must consider the cumulative costs of frequent replacements and the environmental impact of increased waste. While they offer convenience, the long-term financial implications may lead companies to explore more sustainable options.
How Can Custom Air Filter Manufacturers Meet Specific Requirements?
Custom air filter manufacturers specialize in creating tailored solutions for unique applications, such as aerospace, automotive, and manufacturing sectors. These filters are designed to optimize performance and enhance operational efficiency based on specific requirements. B2B buyers should be prepared for longer lead times and potentially higher costs, but the benefits of customized solutions can lead to significant operational improvements. Collaborating closely with manufacturers during the design phase is crucial to ensure that the final product meets all necessary specifications.
Related Video: Air Filter Making Machine Manufacturing Process Producers Production Machinery Line For HEPA HVAC
Key Industrial Applications of air filter manufacturer
Industry/Sector | Specific Application of Air Filter Manufacturer | Value/Benefit for the Business | Key Sourcing Considerations for this Application |
---|---|---|---|
Manufacturing | Dust Collection Systems | Improved air quality leading to better employee health and productivity. | Filter efficiency ratings, maintenance requirements, and compatibility with existing systems. |
Food and Beverage | Air Filtration in Processing Plants | Enhanced product quality by preventing contamination. | Compliance with food safety standards and certifications, as well as filter material suitability. |
Pharmaceuticals | Cleanroom Air Filtration | Ensures a sterile environment critical for drug production. | Regulatory compliance, filter lifespan, and performance under varying humidity and temperature. |
Automotive | Cabin Air Filters in Vehicle Manufacturing | Increased customer satisfaction through improved air quality in vehicles. | Durability, fitment specifications, and performance in diverse climatic conditions. |
HVAC Systems | Air Filters for Heating, Ventilation, and Air Conditioning | Energy efficiency and cost savings by reducing system strain. | Filter type (HEPA, carbon, etc.), compatibility with HVAC systems, and local availability. |
How Are Air Filters Used in the Manufacturing Sector?
In the manufacturing sector, air filters are primarily utilized in dust collection systems. These filters capture harmful particulate matter, ensuring a cleaner working environment. By improving air quality, companies can enhance employee health and productivity, thereby reducing absenteeism and increasing overall efficiency. International buyers should consider filter efficiency ratings and maintenance requirements to ensure compatibility with existing systems while also factoring in local regulations regarding workplace air quality.
What Role Do Air Filters Play in Food and Beverage Processing?
Air filtration is crucial in food and beverage processing plants to prevent contamination of products. Filters are used to maintain a clean atmosphere, which is essential for preserving food quality and ensuring compliance with safety regulations. For businesses in regions like Africa and South America, sourcing filters that meet local food safety standards and are made from suitable materials is paramount. This not only protects consumer health but also enhances the brand reputation of the manufacturer.
Why Are Air Filters Critical in Pharmaceutical Manufacturing?
In the pharmaceutical industry, cleanroom air filtration is essential for maintaining sterile environments necessary for drug production. Air filters help in removing airborne contaminants, thus ensuring product integrity and compliance with stringent regulatory standards. International B2B buyers must prioritize suppliers that can provide filters with proven performance under varying humidity and temperature conditions, as well as those that meet regulatory compliance for pharmaceutical applications.
How Do Air Filters Enhance Automotive Manufacturing?
In the automotive sector, air filters are integral to the manufacturing of cabin air filters, which significantly enhance air quality within vehicles. By filtering out pollutants, allergens, and other particulates, these filters contribute to increased customer satisfaction and can improve vehicle resale value. Buyers should consider durability and fitment specifications to ensure that the filters perform effectively in diverse climatic conditions, particularly in regions with varying air quality standards.
What Are the Benefits of Air Filters in HVAC Systems?
Air filters in HVAC systems play a vital role in ensuring energy efficiency and cost savings. By reducing the strain on heating and cooling systems, high-quality filters can lower operational costs and extend equipment lifespan. For international buyers, understanding the different types of filters available (such as HEPA or carbon filters) and their compatibility with existing HVAC systems is crucial. Additionally, local availability and maintenance support should be key considerations when sourcing these essential components.
Related Video: How to Install Industrial Filter Bags | Dust Collector Bag Installation Guide
3 Common User Pain Points for ‘air filter manufacturer’ & Their Solutions
Scenario 1: Inefficient Filtration Leading to Equipment Damage
The Problem: Many B2B buyers, particularly in industries such as manufacturing and energy, face the challenge of using air filters that do not adequately filter out contaminants. This inefficiency can lead to significant equipment damage, increased maintenance costs, and unplanned downtime. For instance, a factory in South America may rely on subpar filters that allow dust and particulate matter to enter machinery, ultimately resulting in costly repairs and lost productivity.
The Solution: To address this issue, buyers should prioritize sourcing high-quality air filters that are specifically designed for their operational environment. When evaluating suppliers, consider their certifications and the performance data of their filters. Request samples and conduct side-by-side tests in your operational setting to compare their efficiency against competitors. Additionally, establish a regular maintenance schedule to replace filters before they reach saturation, ensuring optimal performance and longevity. By investing in superior filters and maintenance practices, businesses can prevent equipment damage and enhance overall operational efficiency.
Scenario 2: Difficulty in Sizing and Specification of Air Filters
The Problem: Another common pain point is the challenge of correctly sizing and specifying air filters for various applications. B2B buyers in Europe often struggle with selecting the right filters due to a lack of clear specifications from manufacturers, leading to improper fit and functionality. For example, a facility might install filters that are too small, which can compromise air quality and system performance.
The Solution: To mitigate this problem, buyers should engage in thorough consultations with manufacturers or suppliers who offer expert guidance on sizing and specifications. It is crucial to understand the specific requirements of your air handling systems, including airflow rates and filter dimensions. Utilize tools such as filter selection software provided by manufacturers, which can simplify the selection process based on your unique specifications. Additionally, consider forming long-term partnerships with manufacturers who can provide ongoing support and advice, ensuring that your filtration needs evolve alongside your business.
Scenario 3: Limited Awareness of Environmental and Regulatory Compliance
The Problem: B2B buyers, especially in regions like Africa and the Middle East, often face the challenge of navigating environmental regulations and compliance standards related to air filtration. Many buyers may not be fully aware of the standards that their operations need to meet, leading to potential fines and reputational damage. For example, a company might inadvertently use filters that do not comply with local regulations, resulting in operational shutdowns or legal issues.
The Solution: To avoid compliance pitfalls, it is essential for buyers to stay informed about the latest environmental regulations and standards in their industry. Establishing a relationship with an air filter manufacturer that provides compliance documentation and guidance can be invaluable. Regularly attend industry seminars and workshops focused on environmental standards to enhance your knowledge. Additionally, integrating compliance checks into your procurement process can help ensure that all air filters meet the necessary requirements. By being proactive about compliance, businesses can avoid costly mistakes and maintain their operational integrity.
Strategic Material Selection Guide for air filter manufacturer
When selecting materials for air filter manufacturing, several factors come into play, including performance characteristics, cost, and regional compliance standards. This guide analyzes four common materials used in air filters, providing insights into their properties, advantages, disadvantages, and considerations for international B2B buyers, particularly from Africa, South America, the Middle East, and Europe.
What Are the Key Properties of Synthetic Fibers in Air Filters?
Synthetic fibers, such as polyester and polypropylene, are widely used in air filter manufacturing due to their excellent filtration efficiency and durability. These materials typically have high-temperature resistance and can withstand varying pressure levels, making them suitable for both residential and industrial applications. Their corrosion resistance is a significant advantage, especially in humid or chemically aggressive environments.
Pros & Cons: Synthetic fibers are known for their long lifespan and low maintenance requirements. However, they can be more expensive than natural fibers, and their manufacturing process can be complex, requiring specialized equipment. In terms of application, synthetic filters are highly effective in capturing fine particulate matter, making them ideal for environments with stringent air quality standards.
Considerations for International Buyers: Buyers should be aware of compliance with local standards such as ASTM or ISO. In regions like Africa and South America, where air quality regulations are evolving, selecting synthetic fibers that meet these standards can enhance marketability.
How Do Natural Fibers Compare in Air Filter Manufacturing?
Natural fibers, including cotton and cellulose, offer a sustainable alternative to synthetic materials. They are biodegradable and provide good filtration capabilities, particularly for larger particles. Natural fibers can also be treated to enhance their moisture resistance and durability.
Pros & Cons: While natural fibers are generally less expensive, they may not perform as well under extreme temperatures or humidity compared to synthetic options. Their susceptibility to mold and degradation can limit their application in certain environments, particularly in tropical regions.
Considerations for International Buyers: Buyers in Europe, where sustainability is increasingly prioritized, may prefer natural fibers for their eco-friendly attributes. However, they must ensure that these materials comply with local regulations regarding biodegradability and emissions.
What Are the Advantages of Metal Mesh in Air Filter Design?
Metal mesh filters, often made from stainless steel or aluminum, are known for their robustness and longevity. They can withstand high temperatures and pressures, making them suitable for industrial applications where durability is paramount.
Pros & Cons: The key advantage of metal mesh is its reusability; these filters can be cleaned and reused multiple times, reducing long-term costs. However, they tend to be heavier and more expensive upfront than other materials, which may deter some buyers.
Considerations for International Buyers: In regions like the Middle East, where dust and particulate matter are prevalent, metal mesh filters can be particularly effective. Buyers should consider local standards for metal materials and ensure compliance with relevant certifications.
Why Are Activated Carbon Filters Important for Air Quality?
Activated carbon filters are essential for removing odors and volatile organic compounds (VOCs) from the air. They are often used in conjunction with other filter types to enhance overall air quality.
Pros & Cons: The primary advantage of activated carbon is its ability to adsorb harmful gases, making it invaluable in both residential and commercial settings. However, these filters have a limited lifespan and require regular replacement, which can increase operational costs.
Considerations for International Buyers: Buyers from regions with strict air quality regulations, such as Europe, should prioritize activated carbon filters that meet specific compliance standards. Understanding the local demand for air purification solutions can also guide material selection.
Material | Typical Use Case for air filter manufacturer | Key Advantage | Key Disadvantage/Limitation | Relative Cost (Low/Med/High) |
---|---|---|---|---|
Synthetic Fibers | Industrial and residential air filters | High durability and filtration efficiency | Higher manufacturing complexity | High |
Natural Fibers | Eco-friendly air filters | Biodegradable and sustainable | Limited performance in extreme conditions | Medium |
Metal Mesh | Heavy-duty industrial applications | Reusable and long-lasting | Heavier and more expensive upfront | High |
Activated Carbon | Odor and VOC removal filters | Excellent for air quality improvement | Limited lifespan and higher replacement costs | Medium |
This strategic material selection guide provides B2B buyers with a comprehensive overview of the materials used in air filter manufacturing. Understanding the properties, advantages, and regional considerations will aid in making informed purchasing decisions that align with both performance requirements and local regulations.
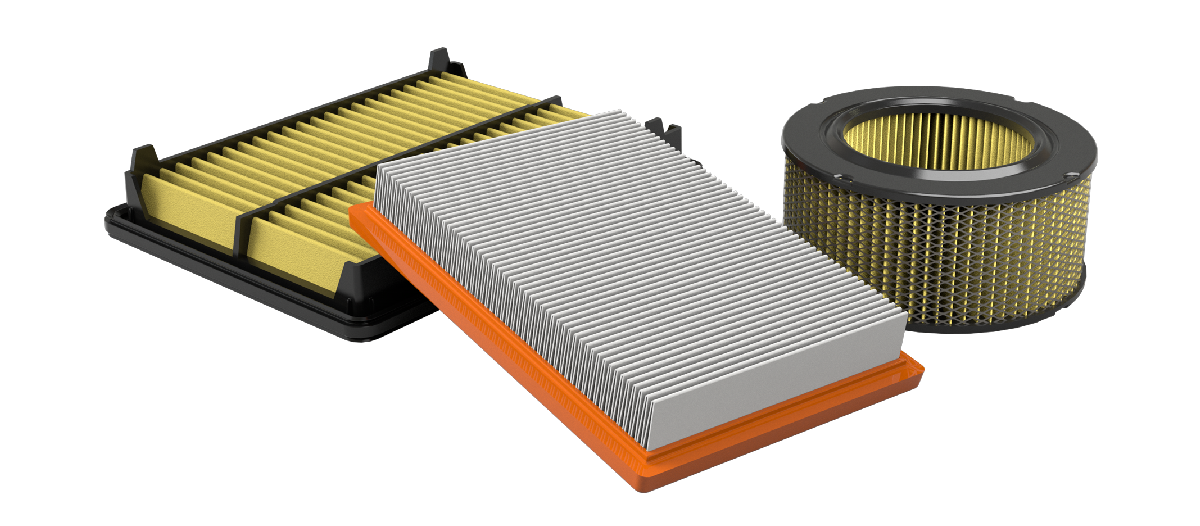
A stock image related to air filter manufacturer.
In-depth Look: Manufacturing Processes and Quality Assurance for air filter manufacturer
What Are the Key Stages in the Manufacturing Process of Air Filters?
The manufacturing process of air filters involves several critical stages that ensure the final product meets the required standards for efficiency and durability. Understanding these stages is essential for B2B buyers, as it helps in evaluating potential suppliers.
-
Material Preparation
– The first step involves sourcing high-quality raw materials such as synthetic fibers, activated carbon, and HEPA media. Suppliers often conduct rigorous assessments of material quality to ensure compliance with international standards.
– For international buyers, especially those from Africa, South America, and the Middle East, it is crucial to inquire about the sourcing practices of manufacturers. Sustainable and ethically sourced materials can enhance your brand’s reputation. -
Forming
– During the forming stage, the raw materials are shaped into the desired filter dimensions. This may involve processes such as pleating, layering, or granulating depending on the filter type.
– Advanced techniques such as thermal bonding or ultrasonic welding may be employed to enhance structural integrity. Buyers should look for manufacturers that utilize state-of-the-art technology to ensure consistent quality. -
Assembly
– The assembly phase involves bringing together different components of the filter, such as frames, sealing materials, and media. Automated assembly lines are common, but some manufacturers may also employ skilled labor for precision tasks.
– For B2B buyers, it’s beneficial to ask about the assembly processes used. Manual assembly can allow for more quality control, while automation can lead to higher throughput. -
Finishing
– In the finishing stage, filters are inspected for defects, cleaned, and packaged. This step is vital to ensure that the filters are free of contaminants before they reach the end-user.
– Buyers should consider the packaging methods used by suppliers, as this can affect product integrity during transportation.
How Is Quality Assurance Implemented in Air Filter Manufacturing?
Quality assurance (QA) is a vital component of the air filter manufacturing process, ensuring that products meet both safety and performance standards.
-
What International Standards Should Buyers Look For?
– International standards such as ISO 9001 are essential for ensuring that manufacturers maintain a quality management system. Compliance with this standard indicates a commitment to continuous improvement and customer satisfaction.
– Additionally, industry-specific certifications such as CE marking for European markets or API standards for certain applications can significantly enhance a manufacturer’s credibility. B2B buyers should verify these certifications during supplier evaluations. -
What Are the Key Quality Control Checkpoints?
– Quality control (QC) is typically divided into several checkpoints: Incoming Quality Control (IQC), In-Process Quality Control (IPQC), and Final Quality Control (FQC).- IQC involves inspecting raw materials upon arrival to ensure they meet specifications.
- IPQC monitors the manufacturing process at various stages to catch defects early.
- FQC ensures that the final product meets all quality standards before shipment.
- Buyers should inquire about the frequency and methods of these inspections, as they play a crucial role in the overall quality of the product.
-
What Common Testing Methods Are Used?
– Common testing methods include airflow tests, pressure drop tests, and efficiency tests to determine the filter’s ability to capture particulates.
– Additionally, manufacturers may conduct durability tests to simulate the filter’s lifespan under various conditions. B2B buyers should request detailed testing reports to understand how the filters perform in real-world conditions.
How Can B2B Buyers Verify Supplier Quality Control?
Verifying a supplier’s quality control processes is essential for ensuring that the products you receive meet your expectations. Here are some actionable steps for international buyers:
-
Conduct Supplier Audits
– Regular audits allow buyers to assess a supplier’s manufacturing processes and quality assurance measures firsthand. Consider hiring third-party auditors who specialize in the air filter industry to gain an unbiased perspective. -
Request Detailed Quality Reports
– Suppliers should provide comprehensive quality reports that outline their QC processes, including inspection results and testing methodologies. This transparency is critical for building trust and ensuring product reliability. -
Engage Third-Party Inspection Services
– Utilizing third-party inspection services can provide an additional layer of assurance. These services can conduct inspections at various stages of the manufacturing process, ensuring compliance with your quality standards. -
Understand Quality Control Nuances for International Trade
– International buyers must be aware of different quality standards and regulations that may apply in their region. For instance, filters sold in Europe must comply with specific EU regulations, while those in South America may have different requirements. Understanding these nuances can help mitigate risks associated with non-compliance.
What Are the Benefits of Partnering with a Manufacturer with Robust QC Processes?
Partnering with an air filter manufacturer that emphasizes quality control can yield significant benefits for B2B buyers:
- Increased Reliability: High-quality filters reduce the risk of premature failure, ensuring consistent performance and customer satisfaction.
- Cost Savings: By investing in quality, businesses can minimize the costs associated with returns, replacements, and warranty claims.
- Enhanced Reputation: Offering reliable products strengthens your brand’s reputation in the market, leading to increased customer loyalty and potential new business opportunities.
In conclusion, understanding the manufacturing processes and quality assurance measures in air filter production is crucial for international B2B buyers. By evaluating suppliers based on their processes, certifications, and commitment to quality, businesses can make informed decisions that lead to long-term success.
Practical Sourcing Guide: A Step-by-Step Checklist for ‘air filter manufacturer’
In today’s global marketplace, sourcing air filters requires a strategic approach to ensure quality, compliance, and value. This guide offers a step-by-step checklist designed to help international B2B buyers from regions such as Africa, South America, the Middle East, and Europe effectively navigate the procurement process for air filter manufacturers.
Step 1: Define Your Technical Specifications
Clearly outlining your technical requirements is essential before initiating the sourcing process. Specify the type of air filters you need, including dimensions, filtration efficiency (e.g., HEPA, MERV ratings), and materials. This clarity helps in identifying suppliers that can meet your exact needs and ensures that you receive quotes that are relevant and comparable.
Step 2: Research Potential Suppliers
Conduct thorough research to create a shortlist of potential manufacturers. Utilize online directories, trade fairs, and industry networks to find suppliers with a solid reputation in the air filter market. Pay special attention to their experience, product range, and geographical reach, as these factors can influence their ability to meet your needs effectively.
Step 3: Evaluate Supplier Certifications and Compliance
Before proceeding with any supplier, verify their certifications and compliance with international standards. Look for ISO certifications, environmental compliance (such as RoHS or REACH), and any industry-specific certifications relevant to air filters. This step not only ensures product quality but also mitigates risks associated with regulatory non-compliance.
Step 4: Request Samples and Test Quality
Once you have narrowed down your list, request product samples to assess their quality firsthand. Testing the samples in your operational environment can provide valuable insights into their performance and durability. Pay attention to the filters’ efficiency, ease of installation, and any relevant technical documentation.
Step 5: Analyze Pricing and Payment Terms
After evaluating the quality of the products, compare pricing across your shortlisted suppliers. Be mindful of the total cost of ownership, which includes shipping, duties, and potential after-sales support. Additionally, clarify payment terms to ensure they align with your financial processes and cash flow management.
Step 6: Check References and Past Performance
Request references from other customers who have procured similar products. This can provide insights into the supplier’s reliability, customer service, and after-sales support. Look for reviews or case studies that highlight their ability to meet deadlines and handle issues effectively.
Step 7: Negotiate Terms and Finalize Contracts
Once you are satisfied with your supplier choice, engage in negotiations to finalize terms. Discuss lead times, warranty provisions, and any service agreements. Ensure that all terms are documented in a contract to protect both parties and establish clear expectations moving forward.
By following this structured checklist, B2B buyers can confidently navigate the sourcing process for air filter manufacturers, ensuring they select the right partner to meet their operational needs while adhering to quality and compliance standards.
Comprehensive Cost and Pricing Analysis for air filter manufacturer Sourcing
What Are the Key Cost Components in Air Filter Manufacturing?
When sourcing from air filter manufacturers, understanding the cost structure is crucial for making informed purchasing decisions. The primary components that contribute to the overall cost include:
-
Materials: The choice of raw materials significantly impacts pricing. Common materials include synthetic fibers, activated carbon, and metal frames. Specialty materials for high-efficiency filters can drive up costs.
-
Labor: Labor costs vary by region, influenced by wage levels and workforce skillsets. Countries with lower labor costs may provide a competitive advantage, but this could affect quality.
-
Manufacturing Overhead: This includes costs related to utilities, equipment maintenance, and facility management. Efficient manufacturing processes can help reduce overhead, which is essential for competitive pricing.
-
Tooling: Initial tooling costs for custom molds and machinery can be substantial. Buyers should consider these costs when ordering customized filters, as they affect the unit price.
-
Quality Control (QC): Robust QC processes ensure product reliability and compliance with international standards, which can add to the overall cost but is essential for quality assurance.
-
Logistics: Shipping costs, tariffs, and insurance can significantly influence the final price, especially for international transactions. Understanding the logistics landscape is vital for cost-effective sourcing.
-
Margin: Manufacturers typically add a profit margin that varies based on competition, market demand, and product uniqueness. Buyers should be aware of this when assessing total costs.
How Do Price Influencers Affect Air Filter Sourcing Decisions?
Several factors can influence the pricing of air filters, making it essential for buyers to analyze these elements to optimize their sourcing strategy:
-
Volume and Minimum Order Quantity (MOQ): Larger orders often lead to lower per-unit costs. Buyers should negotiate MOQs that align with their needs to benefit from volume discounts.
-
Specifications and Customization: Custom filters tailored to specific applications can incur additional costs. Buyers need to clearly define their requirements to avoid unexpected expenses.
-
Materials Quality and Certifications: High-quality materials and certifications (such as ISO or HEPA) can increase the price but may be necessary for compliance with regulatory standards in certain markets.
-
Supplier Factors: The reliability and reputation of the supplier play a role in pricing. Established suppliers may charge a premium for their proven track record, while new entrants might offer lower prices to gain market share.
-
Incoterms: Understanding Incoterms (International Commercial Terms) is essential as they define the responsibilities of buyers and sellers in shipping and logistics, affecting overall cost.
What Tips Can Help International B2B Buyers Optimize Costs?
For international buyers, particularly from regions such as Africa, South America, the Middle East, and Europe, optimizing sourcing costs requires strategic approaches:
-
Negotiate Effectively: Always negotiate terms with suppliers. Presenting data on market prices and competitor offerings can strengthen your position.
-
Focus on Cost-Efficiency: Assess the Total Cost of Ownership (TCO), which includes not just the purchase price but also shipping, maintenance, and disposal costs. This holistic view can reveal cheaper long-term options.
-
Understand Pricing Nuances: Be aware that prices can fluctuate based on geopolitical factors, currency exchange rates, and economic conditions in both the supplier and buyer’s countries. Regularly review market trends to anticipate changes.
-
Build Relationships with Suppliers: Establishing long-term partnerships can lead to better pricing, more favorable payment terms, and priority treatment during high-demand periods.
Conclusion: Why is a Comprehensive Cost Analysis Essential?
Conducting a thorough cost and pricing analysis is indispensable for B2B buyers in the air filter industry. It not only aids in understanding the components that influence pricing but also equips buyers with the knowledge to negotiate better deals, ensuring cost-effective sourcing strategies that align with their operational needs. Keep in mind that the prices discussed are indicative and can vary based on specific circumstances and market dynamics.
Alternatives Analysis: Comparing air filter manufacturer With Other Solutions
Introduction: Why Consider Alternatives to Air Filters?
When evaluating air quality management solutions, it is essential for B2B buyers to consider alternatives to traditional air filter manufacturers. Different technologies and methods can achieve similar outcomes, providing various benefits and challenges. Understanding these alternatives allows buyers from regions such as Africa, South America, the Middle East, and Europe to make informed decisions that align with their unique operational needs and budget constraints.
Comparison Table of Air Filter Solutions
Comparison Aspect | Air Filter Manufacturer | Electrostatic Precipitators | UV-C Air Purification Systems |
---|---|---|---|
Performance | High efficiency in particulate removal. | Excellent for smoke and particulate, but less effective against gases. | Effective at eliminating airborne pathogens and odors. |
Cost | Moderate initial investment with recurring filter costs. | Higher initial investment with low ongoing costs. | Moderate initial investment with low maintenance costs. |
Ease of Implementation | Relatively easy to install; requires regular filter changes. | More complex installation; requires professional setup. | Generally easy installation; minimal setup required. |
Maintenance | Regular filter replacements needed; moderate upkeep. | Low maintenance; requires periodic cleaning. | Low maintenance; lamp replacement every 12-24 months. |
Best Use Case | General air quality improvement in commercial spaces. | Industrial settings with high particulate matter. | Healthcare facilities and spaces requiring high pathogen control. |
Detailed Breakdown of Alternatives
What Are the Benefits and Drawbacks of Electrostatic Precipitators?
Electrostatic precipitators (ESPs) are a viable alternative for businesses dealing with high levels of smoke or particulate matter. They operate by charging particles in the air, causing them to be attracted to collector plates. The primary advantage of ESPs is their ability to handle large volumes of air and remove fine particles effectively. However, the initial investment can be significant, and the installation often requires specialized expertise. For industries like manufacturing or power generation, where particulate control is crucial, ESPs can provide a long-term solution with low operational costs.
How Do UV-C Air Purification Systems Compare?
UV-C air purification systems utilize ultraviolet light to kill or deactivate airborne pathogens, making them an excellent choice for environments such as hospitals and laboratories. These systems are effective in reducing viruses, bacteria, and mold spores, contributing to a healthier indoor environment. The installation is generally straightforward, and maintenance is minimal, primarily involving lamp replacement. However, they may not be as effective in removing particulate matter or gases compared to traditional air filters. Therefore, for buyers focused on pathogen control rather than general air quality, UV-C systems can be a superior option.
Conclusion: How to Choose the Right Air Quality Solution for Your Needs
Selecting the right air quality solution depends on various factors including the specific environment, performance needs, and budget constraints. B2B buyers should assess their primary air quality challenges—whether it’s particulate matter, pathogens, or a combination of both. While traditional air filters offer reliable performance for general air quality improvement, alternatives like electrostatic precipitators and UV-C systems may provide enhanced capabilities for specific industrial or healthcare applications. By carefully evaluating the pros and cons of each option, buyers can make informed decisions that best suit their operational requirements and ensure a healthier indoor environment.
Essential Technical Properties and Trade Terminology for air filter manufacturer
What Are the Essential Technical Properties of Air Filters?
When sourcing air filters, understanding the technical properties is crucial for making informed purchasing decisions. Here are several key specifications that B2B buyers should consider:
1. Material Grade: What Types of Materials Are Used in Air Filters?
Air filters are primarily made from materials such as fiberglass, polyester, and pleated paper. Each material has its own filtration efficiency and durability characteristics. For instance, fiberglass filters are often used in industrial applications due to their high dust-holding capacity, while polyester filters offer a balance between cost and performance. Choosing the right material grade can significantly impact filter performance and longevity.
2. Filtration Efficiency: How Is It Measured and Why Does It Matter?
Filtration efficiency is typically measured using MERV (Minimum Efficiency Reporting Value) ratings. These ratings range from 1 to 20, indicating how well a filter captures particles of various sizes. For B2B buyers, selecting the appropriate MERV rating is essential to ensure that the air quality meets regulatory standards and operational needs. Higher MERV ratings generally correlate with better filtration but may also require more frequent replacements.
3. Airflow Resistance: What Is It and How Does It Affect Performance?
Airflow resistance, often referred to as pressure drop, indicates how easily air can pass through the filter. High resistance can lead to increased energy costs and reduced efficiency in HVAC systems. Understanding the airflow resistance of a filter helps buyers assess compatibility with existing systems and anticipate maintenance needs, ultimately contributing to cost savings in energy consumption.
4. Dimensions and Tolerances: Why Are They Important in Sourcing?
Filters come in various sizes and shapes, and precise dimensions are critical for ensuring a proper fit in HVAC systems. Tolerances, which refer to the allowable variations in size, play a significant role in maintaining system integrity. B2B buyers should ensure that the filters meet specified tolerances to prevent air leaks and maintain optimal performance.
5. Lifespan and Replacement Cycle: How Do They Impact Overall Costs?
The lifespan of an air filter can vary widely based on its type and usage conditions. Understanding the expected lifespan helps buyers plan their procurement cycles and budget for replacements. Filters with longer lifespans may have higher upfront costs but can lead to lower total ownership costs over time.
What Are Common Trade Terms in the Air Filter Manufacturing Industry?
Navigating the air filter manufacturing landscape involves familiarizing oneself with specific trade terms. Here are several common terms that B2B buyers should understand:
1. OEM (Original Equipment Manufacturer): What Does It Signify?
An OEM refers to a company that produces components that are used in another company’s end products. In the air filter industry, OEMs may manufacture filters for HVAC systems or automotive applications. Understanding the role of OEMs can help buyers identify reliable suppliers who adhere to quality standards.
2. MOQ (Minimum Order Quantity): Why Is It Critical for Bulk Purchases?
MOQ is the smallest quantity of a product that a supplier is willing to sell. For B2B buyers, knowing the MOQ is essential for budgeting and inventory management. Suppliers often set MOQs based on production costs and economies of scale, making it important to negotiate terms that suit your purchasing needs.
3. RFQ (Request for Quotation): How Can It Streamline Procurement?
An RFQ is a formal process where buyers request pricing and terms from suppliers. Utilizing RFQs can help buyers compare options and negotiate better terms, ensuring they secure the best deal for their air filter needs. This process is especially beneficial for large-scale purchases.
4. Incoterms: What Are They and How Do They Affect Shipping?
Incoterms are international trade terms that define the responsibilities of buyers and sellers in shipping goods. Understanding these terms is crucial for B2B buyers to clarify who bears the risk and cost during transportation. Familiarity with Incoterms can prevent misunderstandings and streamline logistics in international transactions.
By grasping these essential technical properties and trade terminologies, international B2B buyers can make more informed decisions when sourcing air filters, ultimately enhancing their operational efficiency and cost-effectiveness.
Navigating Market Dynamics and Sourcing Trends in the air filter manufacturer Sector
What Are the Current Market Dynamics in the Air Filter Manufacturing Sector?
The air filter manufacturing sector is witnessing a surge in demand driven by global health concerns, industrial regulations, and environmental sustainability efforts. Key markets in Africa, South America, the Middle East, and Europe are responding to heightened awareness of air quality, particularly in urban areas where pollution levels are critical. Emerging technologies such as IoT and AI are reshaping sourcing trends, enabling manufacturers to optimize production processes and improve product quality. Buyers should pay attention to the integration of smart filtration systems, which provide real-time data and enhance operational efficiency.
Moreover, as countries implement stricter environmental regulations, businesses are compelled to source filters that meet specific air quality standards. This creates opportunities for international B2B buyers to engage with suppliers who are compliant with these regulations, ensuring that their products align with local and international quality benchmarks. The shift towards e-commerce and digital procurement platforms is also notable, offering buyers greater access to a diverse range of suppliers and facilitating transparent pricing models.
How Can Sustainability and Ethical Sourcing Impact B2B Relationships?
The growing emphasis on sustainability is reshaping the way businesses approach sourcing in the air filter manufacturing sector. International B2B buyers are increasingly prioritizing suppliers who demonstrate a commitment to environmental stewardship and ethical practices. The environmental impact of manufacturing processes is significant, and buyers must consider how their sourcing decisions affect the overall carbon footprint.
Ethical supply chains are not just about compliance; they are also about building trust and reputation. Suppliers that obtain ‘green’ certifications, such as ISO 14001 for environmental management, or those using recycled and eco-friendly materials in their products, can provide a competitive edge. Buyers should seek partnerships with manufacturers who prioritize sustainability, as this can lead to enhanced brand loyalty and customer satisfaction. Additionally, integrating sustainability into procurement strategies can help mitigate risks associated with regulatory changes and supply chain disruptions.
What Is the Historical Context of Air Filter Manufacturing for B2B Buyers?
The evolution of the air filter manufacturing sector has been significantly influenced by technological advancements and growing environmental awareness. Initially focused on basic filtration needs, the industry has transformed over the decades, with the introduction of advanced materials and innovative designs that enhance air quality. The 1970s marked a turning point when regulatory frameworks began to emerge, prompting manufacturers to improve their products to comply with health and safety standards.
In recent years, the focus has shifted towards developing filters that not only capture particulate matter but also address volatile organic compounds (VOCs) and other harmful pollutants. This historical context is essential for international B2B buyers, as understanding past trends can provide insights into current market dynamics and future developments. Engaging with suppliers who have a proven track record in innovation and compliance can offer significant advantages in today’s competitive landscape.
Frequently Asked Questions (FAQs) for B2B Buyers of air filter manufacturer
-
How do I choose the right air filter manufacturer for my business needs?
Selecting the right air filter manufacturer involves assessing several factors. Start by defining your specific requirements, such as filter type, application, and performance standards. Research manufacturers with a proven track record in your industry and check for certifications like ISO 9001. Request samples to evaluate quality and performance, and consider suppliers who offer customization to meet your unique needs. Engaging in discussions about their production processes and lead times can also provide insight into their capabilities. -
What are the key quality assurance practices to look for in an air filter manufacturer?
Quality assurance is critical when sourcing air filters. Look for manufacturers who implement strict QA protocols, including testing for efficiency, durability, and compliance with international standards. Inquire about their quality control certifications and whether they conduct regular audits of their production facilities. Additionally, assess their response to quality issues and their willingness to provide product guarantees or warranties. A transparent QA process is a good indicator of a reliable partner. -
What is the minimum order quantity (MOQ) when sourcing air filters from manufacturers?
Minimum order quantities can vary significantly among air filter manufacturers, often influenced by the type of filter and customization requirements. Typically, MOQs can range from a few hundred to several thousand units. When negotiating with potential suppliers, discuss your needs and see if they offer flexibility in MOQs, especially for first-time orders or trial runs. This can help reduce upfront costs and assess the product’s fit for your business. -
How can I ensure timely logistics and delivery when sourcing air filters internationally?
To ensure timely logistics and delivery, begin by discussing shipping options with your chosen manufacturer. Opt for suppliers who have established logistics partnerships and a clear understanding of international shipping regulations. Consider using freight forwarders who specialize in your region to navigate customs and import requirements effectively. Establish clear timelines for production and delivery, and maintain open communication throughout the process to address any potential delays proactively. -
What payment terms should I expect when working with air filter manufacturers?
Payment terms can vary widely, but common practices include upfront deposits followed by balance payments upon delivery or after a specified period. International buyers should negotiate terms that align with their cash flow and risk tolerance. Look for manufacturers who offer secure payment methods, such as letters of credit or escrow services, to protect both parties. Understanding the currency and potential exchange rate fluctuations is also essential when finalizing payment terms. -
How can I assess the reliability of an air filter manufacturer?
To assess a manufacturer’s reliability, conduct thorough research by checking their reputation in the industry. Look for customer reviews, testimonials, and case studies that highlight their experience with similar projects. Ask for references from other businesses in your region and consider visiting their facilities if possible. Engaging in direct communication about their production capabilities and responsiveness can also provide valuable insights into their reliability as a partner. -
What customization options are available when sourcing air filters?
Many air filter manufacturers offer customization options to meet specific operational needs. This can include variations in size, material, filtration efficiency, and additional features such as activated carbon or HEPA filters. When discussing your requirements, provide detailed specifications to ensure the manufacturer understands your needs. Some manufacturers may also offer design support, helping to optimize the filter for your particular application, which can enhance performance and efficiency. -
What are the common challenges faced by international buyers of air filters?
International buyers often face challenges such as language barriers, differing regulations, and logistics complexities. Understanding local market conditions and compliance requirements is crucial. Additionally, currency fluctuations can impact costs, so consider securing fixed pricing where possible. Establishing a strong communication channel with your manufacturer can mitigate misunderstandings and ensure smoother transactions. Building a relationship over time can also help navigate these challenges more effectively.
Important Disclaimer & Terms of Use
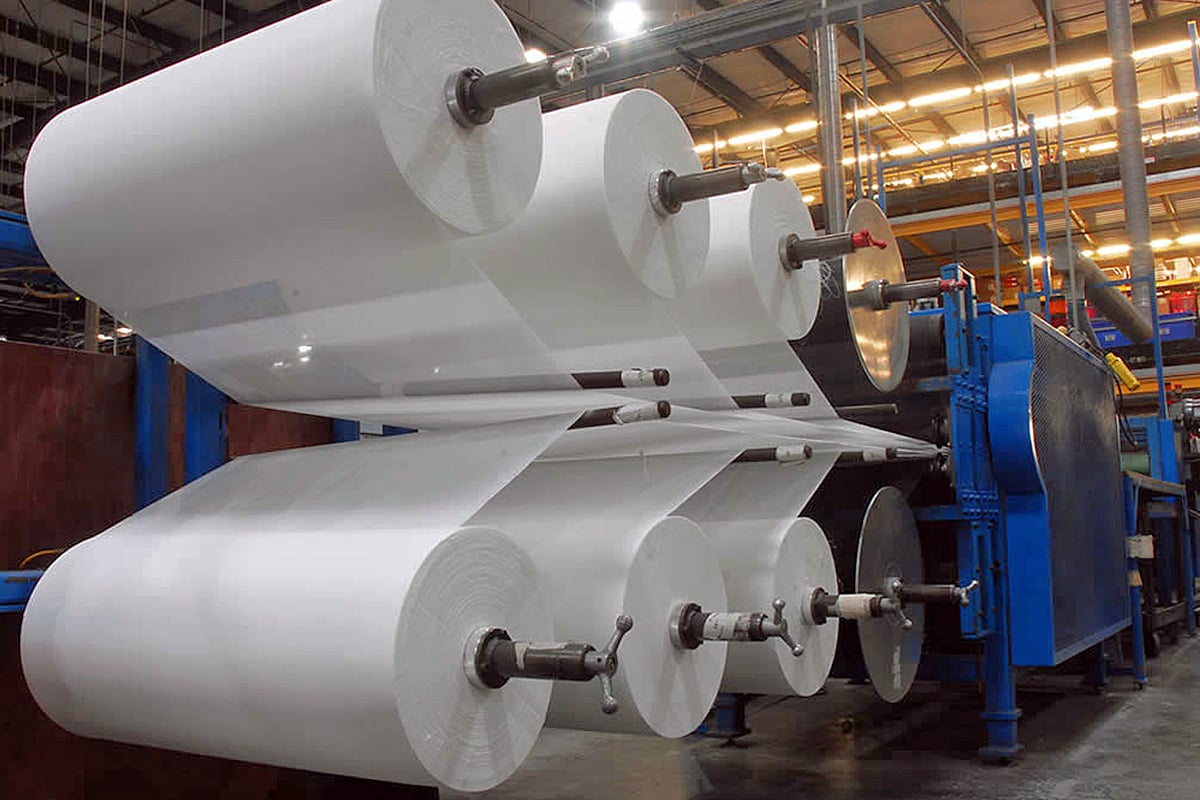
A stock image related to air filter manufacturer.
⚠️ Important Disclaimer
The information provided in this guide, including content regarding manufacturers, technical specifications, and market analysis, is for informational and educational purposes only. It does not constitute professional procurement advice, financial advice, or legal advice.
While we have made every effort to ensure the accuracy and timeliness of the information, we are not responsible for any errors, omissions, or outdated information. Market conditions, company details, and technical standards are subject to change.
B2B buyers must conduct their own independent and thorough due diligence before making any purchasing decisions. This includes contacting suppliers directly, verifying certifications, requesting samples, and seeking professional consultation. The risk of relying on any information in this guide is borne solely by the reader.
Strategic Sourcing Conclusion and Outlook for air filter manufacturer
Why is Strategic Sourcing Crucial for Air Filter Manufacturers?
In the dynamic landscape of air filter manufacturing, strategic sourcing emerges as a vital component for international B2B buyers. By leveraging a comprehensive understanding of supplier capabilities, quality standards, and regional compliance requirements, businesses can significantly enhance their supply chain resilience. This is particularly important for buyers from Africa, South America, the Middle East, and Europe, where local regulations and market needs vary widely.
How Can B2B Buyers Optimize Their Sourcing Strategy?
Buyers should focus on building strong relationships with suppliers who demonstrate reliability and innovation. Evaluating suppliers based on their sustainability practices and technological advancements can lead to better product quality and lower long-term costs. Engaging in collaborative partnerships not only fosters mutual growth but also aligns with the increasing demand for environmentally friendly products.
What Does the Future Hold for Air Filter Sourcing?
As global air quality concerns rise, the air filter market is poised for significant growth. B2B buyers must stay ahead of emerging trends such as smart filtration technologies and regulatory changes that affect product standards. By adopting a proactive approach to sourcing, businesses can position themselves competitively in this evolving market.
In conclusion, international B2B buyers are encouraged to prioritize strategic sourcing as a cornerstone of their procurement strategy. The benefits of informed decision-making, supplier collaboration, and market awareness will be crucial in navigating the complexities of the air filter manufacturing sector. Embrace the opportunity to enhance your sourcing practices today for a more sustainable and efficient tomorrow.