Discover Top Alloy Suppliers: The Ultimate Sourcing Guide (2025)
Introduction: Navigating the Global Market for alloy supplier
In today’s interconnected world, sourcing the right alloy supplier can be a daunting challenge for international B2B buyers, especially those operating in regions such as Africa, South America, the Middle East, and Europe. With a myriad of options available, understanding the nuances of alloy materials, their applications, and the credibility of potential suppliers is crucial. This guide aims to demystify the complexities of the global alloy market, providing actionable insights that empower buyers to make informed purchasing decisions.
Throughout this comprehensive guide, we will explore various types of alloys, their specific applications across industries, and strategies for vetting suppliers effectively. Additionally, we will delve into cost considerations, logistics, and market trends that can influence purchasing decisions. By addressing these key areas, buyers will gain a clearer understanding of what to look for in an alloy supplier, ensuring they choose partners that align with their operational needs and quality standards.
This guide is designed to be a valuable resource for B2B buyers from diverse regions, such as Nigeria’s emerging markets and Spain’s established industrial sectors. It equips you with the knowledge to navigate the complexities of the global alloy supply chain, ultimately enhancing your procurement strategies and fostering successful international partnerships. Whether you are looking to source aluminum, steel, or specialized alloys, this guide will help you connect with reliable suppliers that meet your unique requirements.
Understanding alloy supplier Types and Variations
Type Name | Key Distinguishing Features | Primary B2B Applications | Brief Pros & Cons for Buyers |
---|---|---|---|
Primary Alloy Suppliers | Specialize in producing base alloys; often have large-scale production capabilities. | Automotive, aerospace, construction | Pros: High volume, consistent quality. Cons: Less flexibility in customization. |
Secondary Alloy Suppliers | Focus on recycling and remelting scrap metals to produce alloys; often smaller operations. | Electronics, machinery, consumer goods | Pros: Eco-friendly, cost-effective. Cons: Variable quality depending on source material. |
Specialty Alloy Suppliers | Provide unique or custom alloys tailored to specific applications; often involve R&D. | Aerospace, medical devices, high-performance applications | Pros: Tailored solutions, innovative materials. Cons: Higher costs, longer lead times. |
Global Alloy Distributors | Act as intermediaries between manufacturers and end-users; often stock a variety of alloys. | General manufacturing, construction, automotive | Pros: Wide selection, easier sourcing. Cons: Markup costs, potential delays in supply chain. |
Local Alloy Suppliers | Serve regional markets, often with a focus on specific industry needs; may offer quick turnaround. | Construction, local manufacturing | Pros: Faster delivery, personalized service. Cons: Limited product range, potential quality variability. |
What are Primary Alloy Suppliers and How Do They Operate?
Primary alloy suppliers are typically large-scale manufacturers that produce base alloys in significant quantities. They focus on the mass production of alloys used in industries such as automotive and aerospace. B2B buyers should consider the consistency in quality and reliability of supply, as these suppliers often have stringent quality control processes in place. However, the downside may be less flexibility in terms of customization, which could be a concern for specialized applications.
How Do Secondary Alloy Suppliers Contribute to Sustainable Practices?
Secondary alloy suppliers primarily engage in recycling and remelting scrap metals to create new alloys. This process not only reduces waste but also contributes to sustainability in manufacturing. B2B buyers in sectors like electronics and machinery can benefit from the cost-effectiveness of these suppliers. However, it’s essential to be mindful of the potential variability in quality, which can depend significantly on the source materials used in production.
What Makes Specialty Alloy Suppliers Essential for High-Tech Industries?
Specialty alloy suppliers focus on developing unique or custom alloys that meet specific performance criteria. They often involve research and development to create innovative materials suitable for high-performance applications in sectors like aerospace and medical devices. B2B buyers looking for tailored solutions should weigh the advantages of these specialized materials against the typically higher costs and longer lead times associated with custom orders.
How Do Global Alloy Distributors Facilitate International Sourcing?
Global alloy distributors act as intermediaries, connecting manufacturers with end-users across various regions. They typically stock a wide range of alloys, making them a convenient option for B2B buyers looking to source materials without engaging with multiple suppliers. While they offer the advantage of selection and easier sourcing, buyers should be aware of potential markup costs and delays that can arise in the supply chain.
Why Should B2B Buyers Consider Local Alloy Suppliers?
Local alloy suppliers cater specifically to regional markets and often focus on the unique needs of local industries. They can provide quicker turnaround times and more personalized service, which can be beneficial for construction and local manufacturing projects. However, buyers should consider the limited product range and potential quality variability when choosing to work with local suppliers, ensuring that they meet their specific alloy requirements.
Related Video: Steel & Its Types | Alloy Steel, Carbon Steel, Mild Steel & Stainless Steel
Key Industrial Applications of alloy supplier
Industry/Sector | Specific Application of alloy supplier | Value/Benefit for the Business | Key Sourcing Considerations for this Application |
---|---|---|---|
Aerospace | Aircraft components manufacturing | Enhanced performance and reduced weight | Certification standards, lead times, and alloy specifications |
Automotive | Engine and transmission parts production | Improved durability and fuel efficiency | Material traceability, regulatory compliance, and cost-effectiveness |
Construction | Structural steel and framework systems | Increased strength and corrosion resistance | Local availability, delivery timelines, and customization options |
Electronics | Heat sinks and enclosures | Better thermal management and protection | Precision tolerances, sourcing from reliable suppliers, and pricing |
Oil & Gas | Pipelines and drilling equipment | Resistance to harsh environments and extended lifespan | Compliance with international standards and material certifications |
How is Alloy Supplier Used in Aerospace Applications?
In the aerospace industry, alloy suppliers provide materials for manufacturing aircraft components, such as wings, fuselage, and engine parts. The use of lightweight alloys, like titanium and aluminum, is critical to enhancing performance and reducing fuel consumption. International B2B buyers must consider certification standards, as aerospace materials must meet stringent safety regulations. Additionally, lead times can be a crucial factor, given the industry’s demand for timely delivery to maintain production schedules.
What are the Key Applications of Alloy Suppliers in the Automotive Sector?
Alloy suppliers play a vital role in the automotive sector by providing high-performance materials for engine and transmission components. These alloys are designed to improve durability and fuel efficiency, addressing the industry’s need for lightweight yet strong materials. Buyers from regions like Africa and South America should prioritize material traceability and regulatory compliance to ensure that the products meet local and international standards. Cost-effectiveness is also a significant consideration, especially in competitive markets.
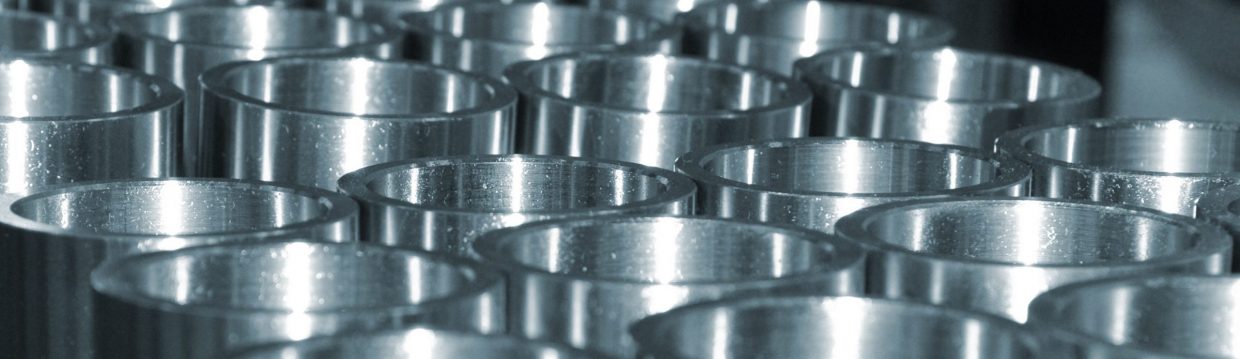
A stock image related to alloy supplier.
How Do Alloy Suppliers Benefit the Construction Industry?
In construction, alloy suppliers deliver materials for structural steel and framework systems that require high strength and corrosion resistance. Alloys like stainless steel are commonly used to enhance the longevity of structures exposed to harsh environmental conditions. Buyers should focus on local availability and delivery timelines, as construction projects often operate under tight schedules. Customization options for specific project requirements can also provide a competitive edge.
In What Ways are Alloys Utilized in Electronics Manufacturing?
Alloy suppliers are essential in the electronics industry, where they provide materials for heat sinks and enclosures that manage thermal performance. The right alloys can significantly improve thermal conductivity, ensuring the longevity and reliability of electronic devices. Precision tolerances are critical in this sector, so buyers must source from reliable suppliers who can deliver consistent quality. Pricing is also a key factor, especially when sourcing materials for large-scale production.
What Role Do Alloy Suppliers Play in Oil & Gas Applications?
In the oil and gas sector, alloy suppliers provide materials for pipelines and drilling equipment designed to withstand extreme conditions. Alloys used in this industry must resist corrosion and wear, extending the lifespan of critical infrastructure. International buyers need to ensure compliance with international standards and material certifications, as these factors can impact operational safety and efficiency. Understanding the specific environmental challenges in different regions, such as the Middle East, is also crucial for selecting the right materials.
Related Video: Uses of Aluminium | Environmental Chemistry | Chemistry | FuseSchool
3 Common User Pain Points for ‘alloy supplier’ & Their Solutions
Scenario 1: Supply Chain Disruptions in Alloy Procurement
The Problem:
International B2B buyers often face significant challenges in securing a reliable supply of alloys due to geopolitical tensions, trade restrictions, or logistical issues. For example, a manufacturing company in Nigeria may struggle to obtain high-quality aluminum alloys for its production line, leading to production delays and increased costs. This unpredictability can severely impact their operational efficiency and profitability, as they rely on timely deliveries to meet customer demands.
The Solution:
To mitigate supply chain disruptions, B2B buyers should establish strong relationships with multiple alloy suppliers across different regions. This diversification can provide a safety net against local disruptions. Additionally, buyers should consider engaging suppliers who offer flexible logistics solutions, such as local warehousing or consignment stock. Leveraging technology like supply chain management software can also provide real-time visibility into inventory levels and shipment statuses, enabling buyers to make informed decisions quickly. Lastly, fostering open communication with suppliers can help anticipate potential issues and devise contingency plans, ensuring that production schedules remain unaffected.
Scenario 2: Difficulty in Sourcing the Right Alloy Grades
The Problem:
Finding the right alloy grade that meets specific application requirements can be a daunting task for B2B buyers. For instance, a European aerospace manufacturer may need a unique titanium alloy that complies with stringent industry standards for safety and performance. Without proper guidance, buyers may end up selecting an unsuitable alloy, leading to product failures, safety risks, and substantial financial losses.
The Solution:
To effectively source the right alloy grades, buyers should conduct thorough research and leverage the expertise of their suppliers. Engaging in pre-purchase consultations with alloy suppliers can provide insights into the best materials for specific applications. It’s also beneficial to request samples and conduct testing to ensure that the alloy meets performance specifications. Additionally, buyers should familiarize themselves with industry standards and certifications related to alloys, as this knowledge can guide their selection process. Joining industry associations or forums can also help buyers stay informed about the latest advancements and trends in alloy materials.
Scenario 3: Understanding Alloy Specifications and Compliance Requirements
The Problem:
Navigating the complex world of alloy specifications and compliance requirements can be overwhelming for B2B buyers, particularly when entering new markets. A South American construction company might face challenges in ensuring that the alloys they procure meet local regulations and international standards. Failure to comply can result in legal issues, project delays, and financial penalties.
The Solution:
To address these challenges, buyers should prioritize education on alloy specifications and compliance standards pertinent to their industry and region. Collaborating closely with suppliers who understand local regulations can provide invaluable insights and ensure that all materials sourced are compliant. Buyers should also consider investing in compliance management tools that can help track and verify the certifications of alloys. Regular training sessions for procurement teams can also enhance their understanding of the specifications needed for various projects. By being proactive and informed, buyers can streamline their procurement processes and reduce the risk of compliance-related issues.
Strategic Material Selection Guide for alloy supplier
When selecting materials for alloys, international B2B buyers must consider various factors that influence performance, cost, and compliance with industry standards. Here, we analyze four common materials used by alloy suppliers, focusing on their properties, advantages, disadvantages, and specific considerations for buyers from Africa, South America, the Middle East, and Europe.
What Are the Key Properties of Aluminum Alloys?
Aluminum alloys are renowned for their lightweight nature and excellent corrosion resistance. They typically exhibit good thermal and electrical conductivity, making them suitable for a range of applications, including automotive and aerospace. Their temperature rating can vary, but many aluminum alloys can withstand temperatures up to 200°C without significant degradation.
Pros & Cons:
Aluminum alloys are durable and easy to fabricate, which reduces manufacturing complexity. However, they can be more expensive than other materials, particularly high-strength options. Their lower strength compared to steel may limit their use in high-load applications.
Impact on Application:
Aluminum is compatible with various media, including water and some chemicals, making it ideal for marine and automotive applications. Buyers should ensure that the specific alloy chosen meets the required standards for their intended use.
Considerations for International Buyers:
Buyers from regions like Nigeria and Spain should be aware of compliance with standards such as ASTM and EN. The availability of specific aluminum alloys may vary by region, impacting sourcing decisions.
How Do Stainless Steel Alloys Perform in Different Environments?
Stainless steel alloys are characterized by their exceptional corrosion resistance and high strength. They can withstand elevated temperatures and pressures, making them suitable for applications in the chemical processing and oil and gas industries. The corrosion resistance of stainless steel is primarily due to the presence of chromium, which forms a passive layer on the surface.
Pros & Cons:
The durability of stainless steel is a significant advantage, especially in harsh environments. However, it can be more challenging to machine and may require specialized tools, increasing manufacturing complexity. Additionally, the cost of stainless steel alloys can be high, particularly for grades with higher nickel content.
Impact on Application:
Stainless steel’s compatibility with various media, including acids and bases, makes it a preferred choice in many industrial applications. Buyers should consider the specific grade of stainless steel to ensure it meets the chemical compatibility requirements of their projects.
Considerations for International Buyers:
Compliance with international standards, such as ASTM A240 for stainless steel sheets, is crucial. Buyers from South America and the Middle East should also consider local regulations regarding material sourcing and environmental impact.
What Are the Benefits and Limitations of Titanium Alloys?
Titanium alloys are known for their high strength-to-weight ratio and excellent corrosion resistance, particularly in extreme environments. They can perform well at temperatures exceeding 600°C, making them suitable for aerospace and high-performance applications.
Pros & Cons:
The main advantage of titanium alloys is their exceptional durability and lightweight properties. However, they are among the most expensive materials, and their machining can be complex, requiring specialized techniques and equipment.
Impact on Application:
Titanium is highly compatible with aggressive media, including seawater and acidic environments, making it ideal for marine and chemical applications. Buyers must ensure that the specific titanium alloy selected aligns with the operational conditions of their application.
Considerations for International Buyers:
International buyers should be aware of the limited availability of certain titanium alloys and the need for compliance with standards such as ASTM B348. Buyers from Europe should also consider the implications of sourcing titanium from regions with stringent environmental regulations.
What Makes Copper Alloys a Viable Option for B2B Buyers?
Copper alloys are widely recognized for their excellent electrical and thermal conductivity, making them suitable for electrical applications. They also exhibit good corrosion resistance, particularly in non-oxidizing environments, with a temperature rating that can exceed 200°C.
Pros & Cons:
The primary advantage of copper alloys is their conductivity, which is unmatched by most other metals. However, they can be prone to corrosion in certain environments, and their cost can be relatively high compared to other materials.
Impact on Application:
Copper alloys are compatible with various media, including water and gases, but buyers should evaluate their specific application requirements to avoid issues related to corrosion.
Considerations for International Buyers:
Compliance with standards such as ASTM B271 is essential for buyers from Africa and South America. Additionally, the fluctuating price of copper due to market demand can impact overall project costs.
Summary Table of Material Selection for Alloy Suppliers
Material | Typical Use Case for alloy supplier | Key Advantage | Key Disadvantage/Limitation | Relative Cost (Low/Med/High) |
---|---|---|---|---|
Aluminum Alloys | Automotive, Aerospace | Lightweight and corrosion-resistant | Lower strength than steel | Medium |
Stainless Steel | Chemical processing, Oil & Gas | Exceptional corrosion resistance | High machining complexity | High |
Titanium Alloys | Aerospace, Marine | High strength-to-weight ratio | Expensive and complex machining | High |
Copper Alloys | Electrical applications | Excellent conductivity | Prone to corrosion in some media | Medium |
This guide aims to equip international B2B buyers with the necessary insights to make informed decisions regarding alloy material selection, ensuring alignment with their specific application requirements and regional compliance standards.
In-depth Look: Manufacturing Processes and Quality Assurance for alloy supplier
What Are the Key Stages in the Manufacturing Process for Alloy Suppliers?
When engaging with alloy suppliers, it is crucial for international B2B buyers to understand the intricacies of the manufacturing process. The production of alloys involves several key stages that ensure the final product meets the required specifications and quality standards.
1. Material Preparation
The manufacturing process begins with material preparation, where raw materials are sourced and inspected. Common raw materials for alloys include metals like aluminum, copper, nickel, and various other elements. Suppliers typically conduct thorough checks on the chemical composition and physical properties of these materials to ensure they align with industry standards. For buyers in Africa and South America, understanding the provenance of these materials is critical, as it can affect both quality and pricing.
2. Forming Techniques
Once the materials are prepared, they undergo various forming techniques, such as casting, forging, or extrusion. Each method has its own advantages:
- Casting: Ideal for complex shapes and high-volume production.
- Forging: Enhances strength and durability through deformation.
- Extrusion: Useful for producing long sections with uniform cross-sections.
Buyers should inquire about the specific forming techniques used by their suppliers, as these can impact the performance and characteristics of the final alloy.
3. Assembly Processes
In some cases, alloys need to be assembled into components or systems. This stage may involve welding, machining, or other joining methods. Understanding the assembly techniques used is crucial for B2B buyers, especially those in sectors like automotive or aerospace, where precision and reliability are paramount.
4. Finishing Touches
The final stage in the manufacturing process is finishing. This may include surface treatments such as anodizing, plating, or polishing. Finishing not only enhances the aesthetic appeal of the alloy but also improves its resistance to corrosion and wear. Buyers from Europe, particularly those in the manufacturing sector, should pay close attention to the finishing processes, as they can significantly affect the longevity and performance of the alloy products.
How Is Quality Assurance Implemented in Alloy Manufacturing?
Quality assurance (QA) is an essential aspect of alloy manufacturing, ensuring that products meet specified standards and customer requirements. Buyers should be familiar with the QA processes used by their suppliers, which often include compliance with international and industry-specific standards.
1. What Are the Relevant International Standards for Alloy Quality Assurance?
One of the most recognized international standards is ISO 9001, which outlines criteria for a quality management system. Compliance with ISO 9001 indicates that a supplier has a systematic approach to managing quality, which is crucial for B2B buyers seeking reliable partnerships.
In addition to ISO standards, buyers should also be aware of industry-specific certifications, such as:
- CE Marking: Indicates conformity with European health, safety, and environmental protection standards.
- API Standards: Relevant for suppliers in the oil and gas sector, ensuring that products meet stringent safety and performance criteria.
2. What Are the Key Quality Control Checkpoints in Alloy Manufacturing?
Quality control (QC) checkpoints are critical in ensuring that each stage of the manufacturing process meets the required standards. Common QC checkpoints include:
- Incoming Quality Control (IQC): Involves inspecting raw materials upon arrival to ensure they meet specifications.
- In-Process Quality Control (IPQC): Monitors production processes to catch defects early and ensure compliance with standards.
- Final Quality Control (FQC): Conducts thorough inspections and testing of the finished product before delivery.
These checkpoints are essential for maintaining quality throughout the manufacturing process.
What Testing Methods Are Commonly Used in Alloy Quality Assurance?
Various testing methods are employed to verify the quality and performance of alloys. Some of the most common methods include:
- Chemical Analysis: Ensures that the alloy’s composition meets specifications.
- Mechanical Testing: Assesses properties such as tensile strength, hardness, and ductility.
- Non-Destructive Testing (NDT): Techniques like ultrasonic testing or radiography are used to detect internal flaws without damaging the product.
B2B buyers should request documentation of these tests to ensure that the supplier adheres to industry standards.
How Can B2B Buyers Verify Supplier Quality Control?
For international buyers, particularly those in Africa and the Middle East, verifying a supplier’s quality control processes is essential for building trust and ensuring product reliability. Here are several ways to conduct due diligence:
1. Conducting Audits
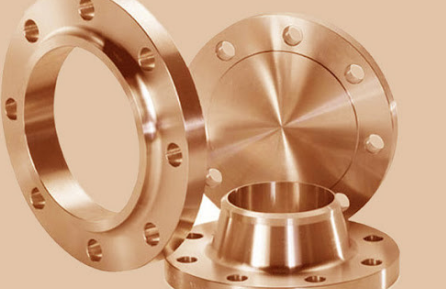
A stock image related to alloy supplier.
Regular audits of suppliers can provide insights into their manufacturing processes and quality assurance practices. Buyers should consider scheduling on-site audits to assess compliance with standards and identify potential areas for improvement.
2. Reviewing Quality Reports
Requesting quality reports from suppliers can help buyers understand the frequency and results of quality inspections. These reports often include data on defect rates, corrective actions taken, and compliance with relevant standards.
3. Engaging Third-Party Inspectors
Using third-party inspection services can provide an unbiased assessment of a supplier’s quality control processes. This is particularly valuable for buyers in regions with less stringent local regulations, as it adds an extra layer of assurance regarding product quality.
What Nuances Should International B2B Buyers Consider in Quality Certification?
When dealing with international suppliers, B2B buyers must navigate various quality certification nuances. For instance, certifications may differ in recognition and acceptance across different regions. Buyers from Europe may find certain certifications more relevant than those in Africa or South America. Therefore, it’s essential to understand which certifications are recognized in the buyer’s specific market.
Moreover, buyers should be aware of the potential for counterfeit certifications. Verifying the authenticity of a supplier’s claims through official channels can help mitigate risks associated with subpar products.
Conclusion
Understanding the manufacturing processes and quality assurance practices of alloy suppliers is vital for international B2B buyers. By focusing on the key stages of production, recognizing international standards, and implementing thorough verification processes, buyers can make informed decisions that ensure product quality and reliability. This knowledge not only enhances procurement strategies but also fosters long-term partnerships with reputable alloy suppliers across Africa, South America, the Middle East, and Europe.
Practical Sourcing Guide: A Step-by-Step Checklist for ‘alloy supplier’
The following guide provides a comprehensive checklist for B2B buyers looking to source alloy suppliers effectively. This practical approach is tailored to international buyers, particularly those operating in Africa, South America, the Middle East, and Europe, ensuring that you can make informed and strategic purchasing decisions.
Step 1: Define Your Technical Specifications
Before initiating your search, clearly outline the technical specifications required for your alloys. This includes understanding the chemical composition, physical properties, and intended application. Having precise specifications helps you communicate your needs effectively to potential suppliers and ensures that you receive products that meet your quality standards.
Step 2: Conduct Market Research
Engage in thorough market research to identify potential alloy suppliers. Utilize online databases, industry reports, and trade associations to compile a list of manufacturers and distributors. Understanding the market landscape allows you to compare offerings and identify suppliers that align with your business needs and geographical considerations.
Step 3: Evaluate Supplier Credentials
Once you have a shortlist of potential suppliers, it’s essential to assess their credentials. Look for certifications such as ISO 9001, which indicates a commitment to quality management systems. Additionally, check for industry-specific certifications relevant to your sector, as these can provide assurance of the supplier’s capability to meet regulatory requirements.
Step 4: Request Samples and Specifications
To ensure the quality and suitability of the alloys, request samples along with detailed specifications. This step allows you to evaluate the physical properties and performance of the materials in your specific applications. Be sure to assess not only the quality but also the consistency of the samples provided.
Step 5: Verify References and Past Performance
Before finalizing your supplier choice, verify references and check their past performance. Reach out to other clients, especially those in similar industries or regions, to gain insights into their experiences. Assessing customer satisfaction and reliability can significantly impact your long-term partnership with the supplier.
Step 6: Negotiate Terms and Conditions
Once you’ve selected a supplier, engage in negotiations regarding pricing, delivery schedules, and payment terms. Clear communication during this phase can help avoid misunderstandings later. Ensure that all agreed-upon terms are documented to protect both parties’ interests.
Step 7: Establish a Communication Plan
Finally, set up a communication plan to facilitate ongoing dialogue with your supplier. Regular check-ins and updates can help address any issues proactively and ensure that your needs are being met. A strong communication strategy fosters a collaborative relationship, enhancing the overall supplier experience.
By following these steps, B2B buyers can confidently navigate the sourcing process for alloy suppliers, ensuring that they choose partners who meet their technical and business requirements effectively.
Comprehensive Cost and Pricing Analysis for alloy supplier Sourcing
What Are the Key Cost Components in Alloy Supplier Pricing?
Understanding the cost structure of alloy suppliers is crucial for international B2B buyers. The primary components influencing pricing include:
-
Materials: The type and quality of raw materials used significantly impact costs. For instance, high-grade alloys may command a premium price due to their enhanced properties and sourcing challenges.
-
Labor: The cost of skilled labor varies by region and can affect production costs. In countries with higher labor costs, such as many European nations, alloy prices may be inflated compared to suppliers in regions with lower labor costs.
-
Manufacturing Overhead: This encompasses indirect costs related to production, such as utilities, facility maintenance, and administrative expenses. Efficient operations can lower these costs, allowing suppliers to offer competitive pricing.
-
Tooling: Custom tooling for specific alloy shapes or specifications can add to upfront costs. However, these costs may be amortized over large production runs, reducing the overall price per unit.
-
Quality Control (QC): Rigorous QC processes ensure product reliability and compliance with international standards. However, they also add to the overall cost structure. Suppliers offering certifications may charge more due to the added assurance of quality.
-
Logistics: Transportation and handling costs can vary widely based on location and shipping terms. These expenses should be factored into the total cost of ownership (TCO).
-
Margin: Suppliers need to maintain a profit margin to stay viable. Understanding the typical margins in the alloy industry can help buyers gauge fair pricing.
How Do Price Influencers Affect Alloy Sourcing Decisions?
Several factors can influence the pricing of alloys, especially for international buyers:
-
Volume and Minimum Order Quantity (MOQ): Larger orders typically result in lower per-unit costs. Buyers should assess their needs to negotiate better terms based on volume.
-
Specifications and Customization: Customized alloys or specific engineering requirements often lead to increased costs. Buyers should clearly define their needs to avoid unexpected pricing escalations.
-
Material Quality and Certifications: Alloys that meet stringent quality certifications, such as ISO standards, may cost more. However, these certifications often justify the expense through enhanced performance and reliability.
-
Supplier Factors: The reputation, reliability, and location of the supplier can affect pricing. Buyers should evaluate potential suppliers based on their track record and customer reviews.
-
Incoterms: Understanding Incoterms is essential for international transactions. They define the responsibilities of buyers and sellers regarding shipping, insurance, and tariffs, impacting the overall cost.
What Are Effective Buyer Tips for Negotiating Alloy Prices?
To effectively navigate the complexities of alloy pricing, buyers from Africa, South America, the Middle East, and Europe should consider the following strategies:
-
Negotiate Based on TCO: Rather than focusing solely on the upfront cost, evaluate the Total Cost of Ownership, which includes logistics, maintenance, and potential downtime. This holistic view can lead to better long-term savings.
-
Build Long-Term Relationships: Establishing a strong relationship with suppliers can yield better pricing and terms. Suppliers are often more willing to negotiate with buyers they trust and who provide consistent orders.
-
Be Aware of Pricing Nuances: Pricing can vary based on economic conditions in the supplier’s region. For instance, currency fluctuations or changes in local demand can impact costs. Staying informed about these trends can enhance negotiation leverage.
-
Request Detailed Quotes: Ask suppliers for itemized quotes that break down each cost component. This transparency can help identify areas for negotiation and ensure there are no hidden fees.
-
Consider Local Regulations: Be aware of import duties, taxes, and compliance requirements in your region. These factors can significantly affect the total cost when sourcing alloys internationally.
Disclaimer on Indicative Prices
Prices for alloys can vary widely based on the factors discussed above. Buyers should seek quotes from multiple suppliers and conduct thorough market research to ensure they are receiving competitive pricing tailored to their specific needs.
Alternatives Analysis: Comparing alloy supplier With Other Solutions
When considering the procurement of alloys, international B2B buyers often seek viable alternatives that can fulfill similar requirements while optimizing cost and efficiency. Understanding the comparative landscape of alloy suppliers and alternative solutions is crucial for making informed decisions that align with business goals. Below, we analyze two notable alternatives to traditional alloy suppliers: Metal 3D Printing and Recycled Metal Sources.
Comparison Aspect | Alloy Supplier | Metal 3D Printing | Recycled Metal Sources |
---|---|---|---|
Performance | High-quality, standardized alloys with consistent properties | Customizable alloys with variable properties depending on the printer and material | May vary in quality but can provide reliable materials for many applications |
Cost | Higher upfront costs, but bulk discounts available | Initial investment in technology can be high; material costs may vary | Generally lower costs due to reduced raw material expenses |
Ease of Implementation | Established supply chains; easy procurement | Requires skilled personnel and training; longer lead times | Established networks exist, but sourcing can be inconsistent |
Maintenance | Minimal maintenance; supplier handles quality control | Requires regular maintenance of printing equipment and software updates | Requires quality checks and sorting of recycled materials |
Best Use Case | Large-scale production with consistent quality | Prototyping and small-batch production of complex geometries | Sustainable projects with cost constraints or eco-friendly initiatives |
What Are the Pros and Cons of Metal 3D Printing?
Metal 3D printing stands out for its ability to produce highly customized parts that are not feasible with traditional alloy manufacturing. This technology allows for rapid prototyping, enabling businesses to test designs quickly and efficiently. However, the initial investment in 3D printing technology and training can be substantial. Additionally, the variability in material properties can pose challenges for applications requiring strict adherence to specifications.
How Do Recycled Metal Sources Compare?
Recycled metal sources present an eco-friendly alternative that can significantly reduce costs associated with raw materials. This method supports sustainable practices, appealing to companies focused on corporate social responsibility. Nevertheless, the quality of recycled materials can be inconsistent, necessitating thorough quality checks before use. Furthermore, the supply of recycled metals can be less predictable, potentially leading to delays in production.
Conclusion: How Can B2B Buyers Choose the Right Solution for Their Needs?
Selecting the right solution for alloy procurement hinges on specific business requirements, including production scale, budget constraints, and sustainability goals. For companies prioritizing high-quality, standardized products with reliable supply chains, traditional alloy suppliers remain a strong choice. Conversely, businesses looking for innovation and customization may benefit from exploring metal 3D printing. Meanwhile, organizations aiming to reduce costs and enhance sustainability should consider recycled metal sources. Ultimately, a thorough assessment of each alternative’s strengths and weaknesses will enable B2B buyers to make strategic decisions that best suit their operational needs.
Essential Technical Properties and Trade Terminology for alloy supplier
What Are the Key Technical Properties of Alloys That B2B Buyers Should Consider?
When sourcing alloys, understanding their technical properties is crucial for ensuring that the materials meet specific application requirements. Here are some essential properties to consider:
1. Material Grade
Material grade refers to the classification of alloys based on their chemical composition and mechanical properties. Different grades offer varying levels of strength, corrosion resistance, and ductility. For B2B buyers, selecting the right grade is vital for ensuring that the alloy can withstand the intended operating conditions, ultimately impacting product performance and longevity.
2. Tolerance
Tolerance indicates the allowable variation in dimensions and physical properties of the alloy. In manufacturing, precise tolerances are crucial for ensuring compatibility with other components, especially in high-stakes industries like aerospace and automotive. B2B buyers should specify tolerances to avoid costly rework or failures in the final product.
3. Yield Strength
Yield strength is the amount of stress that an alloy can withstand without permanently deforming. It is a critical parameter for applications where structural integrity is paramount. Understanding yield strength helps buyers select alloys that can handle expected loads and stresses, ensuring safety and reliability in their applications.
4. Corrosion Resistance
Corrosion resistance refers to the ability of an alloy to resist degradation in hostile environments. This property is particularly significant for industries like oil and gas, marine, and construction. B2B buyers should evaluate the corrosion resistance of alloys to prevent premature failure and reduce maintenance costs.
5. Ductility
Ductility measures how much a material can deform before breaking. Alloys with high ductility can be shaped into complex designs, which is essential for manufacturers needing intricate components. B2B buyers should assess ductility to ensure that the alloy can be easily processed without compromising its integrity.
What Are Common Trade Terms in the Alloy Supply Industry?
Understanding trade terminology is just as important as grasping technical properties when engaging with alloy suppliers. Here are some commonly used terms:
1. OEM (Original Equipment Manufacturer)
An OEM is a company that produces parts or equipment that may be marketed by another manufacturer. For B2B buyers, working with OEMs can provide access to high-quality components that meet specific industry standards. Establishing relationships with reputable OEMs can enhance supply chain efficiency.
2. MOQ (Minimum Order Quantity)
MOQ refers to the smallest quantity of a product that a supplier is willing to sell. This term is critical for B2B buyers as it can affect inventory management and cost efficiency. Understanding the MOQ helps businesses plan their purchases and avoid overstocking or stockouts.
3. RFQ (Request for Quotation)
An RFQ is a document sent to suppliers inviting them to bid on specific products or services. It is an essential tool for B2B buyers to obtain pricing information and compare offers from different suppliers. Crafting a clear RFQ can lead to better pricing and terms.
4. Incoterms (International Commercial Terms)
Incoterms are a series of predefined commercial terms published by the International Chamber of Commerce (ICC) that clarify the responsibilities of buyers and sellers in international transactions. Familiarity with Incoterms is crucial for B2B buyers to understand shipping costs, risk transfer, and delivery obligations, facilitating smoother cross-border transactions.
5. Lead Time
Lead time is the duration between placing an order and receiving the goods. For international B2B buyers, understanding lead times is essential for effective project planning and inventory management. It allows companies to align their production schedules with supply chain timelines.
Conclusion
By grasping essential technical properties and trade terminology, B2B buyers can make informed decisions when sourcing alloys. This knowledge not only aids in selecting the right materials but also enhances communication and negotiation with suppliers, ensuring a more efficient procurement process.
Navigating Market Dynamics and Sourcing Trends in the alloy supplier Sector
What Are the Key Trends Shaping the Alloy Supplier Market?
The alloy supplier sector is currently experiencing significant transformation driven by a combination of global economic factors and technological advancements. International B2B buyers, particularly from Africa, South America, the Middle East, and Europe, must stay informed about these dynamics to make strategic sourcing decisions. One major trend is the increasing demand for high-performance alloys in industries such as aerospace, automotive, and construction. This demand is largely propelled by the growing need for lightweight materials that enhance efficiency and reduce energy consumption.
Additionally, digital transformation is reshaping the way buyers interact with suppliers. The rise of e-procurement platforms and data analytics tools allows for improved visibility into supply chain performance, enabling buyers to make data-driven decisions. Blockchain technology is also gaining traction, enhancing transparency and traceability in the sourcing process, which is particularly important for international transactions.
Moreover, geopolitical factors, such as trade tensions and tariffs, are influencing sourcing strategies. Buyers from regions like Nigeria and Spain must navigate these complexities to mitigate risks associated with supply chain disruptions. As a result, diversifying supplier bases and exploring local sourcing options have become critical strategies for maintaining competitive advantage.
How Is Sustainability Influencing Sourcing Decisions in the Alloy Sector?
Sustainability is no longer just a buzzword; it has become a vital consideration in the alloy supply chain. International B2B buyers are increasingly prioritizing suppliers who adhere to environmentally friendly practices. The environmental impact of alloy production, particularly in terms of carbon emissions and waste generation, necessitates the adoption of sustainable practices.
Ethical sourcing has emerged as a key factor in supplier selection. Buyers are encouraged to evaluate suppliers based on their commitment to responsible sourcing and adherence to industry standards. This includes seeking out ‘green’ certifications such as ISO 14001, which demonstrates a company’s effective environmental management system.
Moreover, the demand for recycled materials is on the rise. By opting for recycled alloys, buyers can reduce their carbon footprint and support the circular economy. Suppliers who can provide verified recycled content not only align with sustainability goals but also appeal to eco-conscious buyers, thereby enhancing their marketability.
What Is the Historical Context of the Alloy Supplier Sector?
The alloy supplier sector has a rich history that has evolved significantly over the decades. Initially, the focus was primarily on the production of basic alloys for industrial applications. However, as technology advanced and industries became more specialized, the demand for high-performance alloys emerged, leading to the development of sophisticated alloys tailored for specific applications.
In the early 2000s, the globalization of supply chains began to reshape the market, allowing buyers to source materials from different regions, thus fostering competition and innovation. This evolution has been further accelerated by the digital revolution, which has transformed how suppliers and buyers interact and transact.
Understanding this historical context is crucial for B2B buyers as it highlights the continuous adaptation of the alloy supplier market to meet changing demands and challenges. Recognizing these trends can help buyers make informed decisions about their sourcing strategies and supplier partnerships.
Frequently Asked Questions (FAQs) for B2B Buyers of alloy supplier
-
How do I choose the right alloy supplier for my business needs?
Selecting the right alloy supplier involves several key considerations. Start by evaluating the supplier’s industry experience and reputation. Look for certifications that ensure quality standards, such as ISO 9001. Additionally, assess their ability to meet your specific alloy requirements, including composition and properties. Engaging in direct communication to understand their customer service and response times can also provide insights into their reliability. Lastly, consider geographical proximity to minimize shipping costs and lead times, especially if you’re sourcing from Africa or South America. -
What are the common payment terms offered by alloy suppliers?
Payment terms can vary widely among alloy suppliers. Common options include upfront payments, net 30 or net 60 terms, and letters of credit. It’s crucial to negotiate terms that align with your cash flow and risk tolerance. For international transactions, consider the currency exchange rates and potential transaction fees. Suppliers may offer discounts for early payments or larger orders, so be sure to discuss these options. Understanding the supplier’s preferred payment methods can also streamline the procurement process. -
What is the minimum order quantity (MOQ) for alloys from suppliers?
The MOQ can significantly differ based on the supplier and the specific alloy being sourced. Some suppliers may have a low MOQ for standard alloys, while others might require larger orders for custom alloys or specialty grades. When negotiating, clarify if the MOQ includes all products or if it can be split across different alloy types. If your project requires smaller quantities, inquire about potential options, such as consolidating orders with other buyers or sourcing from suppliers who specialize in low MOQ offerings. -
How can I ensure quality assurance when sourcing alloys?
Quality assurance is critical when sourcing alloys to ensure they meet your specifications. Request material certification documents that confirm the alloy’s composition and properties. Consider suppliers that conduct third-party testing and provide detailed reports. Establish a clear quality control process, including inspections upon delivery. It’s also beneficial to build a long-term relationship with your supplier, as they will better understand your quality expectations over time. Regular audits and feedback can further enhance the quality assurance process. -
What are the key logistics considerations when importing alloys?
Logistics play a vital role in the successful procurement of alloys. Evaluate shipping options, including air, sea, and land transport, based on cost, urgency, and the nature of the alloy. Consider the supplier’s location and how it impacts lead times and freight charges. Additionally, understand customs regulations and import duties specific to your country, as these can affect overall costs. It’s advisable to work with logistics experts familiar with international trade to navigate potential challenges smoothly. -
How do I vet international alloy suppliers effectively?
Vetting international alloy suppliers requires thorough research and evaluation. Start by reviewing online business directories and industry associations for reputable suppliers. Request references and case studies from previous clients to assess their reliability and service quality. Conduct background checks to verify their business credentials and any certifications. If possible, arrange site visits or virtual tours to get a firsthand look at their operations. Engaging in trial orders can also help gauge their performance before committing to larger contracts. -
What customization options are available when sourcing alloys?
Many alloy suppliers offer customization options to meet specific project requirements. This can include adjustments in chemical composition, mechanical properties, and dimensions. When discussing customization, provide detailed specifications and any relevant standards that must be adhered to. Be aware that custom orders may have longer lead times and higher costs, so plan accordingly. Establishing a clear communication channel with the supplier can facilitate adjustments and ensure that the final product meets your expectations. -
How do trade regulations impact sourcing alloys from different regions?
Trade regulations can significantly affect the sourcing of alloys, especially for international buyers. Import tariffs, quotas, and trade agreements can influence costs and availability. Familiarize yourself with the regulations in your country and the supplier’s country, particularly if you are importing from Africa, South America, or the Middle East. Consider consulting with trade experts or legal advisors to navigate complex regulations. Staying updated on geopolitical developments can also help you anticipate changes that may impact your supply chain.
Important Disclaimer & Terms of Use
⚠️ Important Disclaimer
The information provided in this guide, including content regarding manufacturers, technical specifications, and market analysis, is for informational and educational purposes only. It does not constitute professional procurement advice, financial advice, or legal advice.
While we have made every effort to ensure the accuracy and timeliness of the information, we are not responsible for any errors, omissions, or outdated information. Market conditions, company details, and technical standards are subject to change.
B2B buyers must conduct their own independent and thorough due diligence before making any purchasing decisions. This includes contacting suppliers directly, verifying certifications, requesting samples, and seeking professional consultation. The risk of relying on any information in this guide is borne solely by the reader.
Strategic Sourcing Conclusion and Outlook for alloy supplier
What Are the Key Takeaways for B2B Buyers in Alloy Sourcing?
In the complex landscape of alloy sourcing, strategic sourcing emerges as a pivotal approach for international B2B buyers. By focusing on supplier relationships, quality assurance, and cost-effectiveness, companies can significantly enhance their procurement strategies. Buyers from regions such as Africa, South America, the Middle East, and Europe should prioritize local and regional suppliers to mitigate risks associated with logistics and tariffs, ensuring a more resilient supply chain.
How Can Strategic Sourcing Enhance Competitive Advantage?
Investing time in understanding the nuances of strategic sourcing allows buyers to not only secure better pricing but also access innovative solutions and sustainable practices from suppliers. Leveraging technology to analyze market trends and supplier performance can lead to smarter purchasing decisions. This is particularly important in today’s fast-paced market, where agility and adaptability are crucial.
What Does the Future Hold for Alloy Supply Chains?
Looking ahead, the demand for advanced alloys will continue to rise, driven by technological advancements and changing industry needs. B2B buyers must stay informed about market dynamics and emerging suppliers to capitalize on new opportunities. By embracing a proactive sourcing strategy, international buyers can position themselves for success in an increasingly competitive global marketplace. Engage with your suppliers today to explore tailored solutions that meet your unique requirements and drive your business forward.