Discover Top Aluminum Composite Panel Manufacturers (2025)
Introduction: Navigating the Global Market for Aluminum Composite Panel Manufacturers
Navigating the global market for aluminum composite panels (ACP) can be daunting for international B2B buyers, particularly those from Africa, South America, the Middle East, and Europe. With varying standards, material specifications, and compliance requirements, sourcing high-quality aluminum composite panels that meet project needs is critical yet complex. This guide serves as a comprehensive resource for understanding the different types of ACP, their applications across various industries, and the nuances of supplier vetting.
From fire-resistant panels for high-rise buildings to aesthetically pleasing finishes for commercial spaces, aluminum composite panels offer versatility that aligns with diverse architectural visions. Buyers will benefit from insights into the manufacturing processes, certifications to look for, and cost considerations, empowering them to make informed purchasing decisions.
Furthermore, this guide addresses key challenges faced by B2B buyers, such as navigating international shipping logistics and understanding local regulations that affect material selection. By equipping buyers with actionable knowledge, this resource aims to streamline the procurement process, ensuring that organizations can confidently source reliable and innovative aluminum composite panels for their projects. Whether you are in Poland, the UAE, or any other market, understanding these elements will enhance your ability to select the right manufacturers and products that meet both budgetary and project-specific requirements.
Understanding Aluminum Composite Panel Manufacturers Types and Variations
Type Name | Key Distinguishing Features | Primary B2B Applications | Brief Pros & Cons for Buyers |
---|---|---|---|
Standard Aluminum Composite Panels | Lightweight, versatile, and typically available in a variety of colors and finishes. | Building facades, interior design, signage. | Pros: Cost-effective, easy to install. Cons: May lack fire resistance. |
Fireproof Aluminum Composite Panels | Enhanced fire-resistant properties, often compliant with stricter building codes. | High-rise buildings, public infrastructure. | Pros: Safety compliance, durable. Cons: Higher initial costs, limited design options. |
High-Gloss Aluminum Composite Panels | Feature a reflective surface, enhancing aesthetics. Available in custom colors. | Retail spaces, luxury interiors. | Pros: Striking appearance, customizable. Cons: Prone to scratches, higher maintenance. |
Wood Finish Aluminum Composite Panels | Mimics the appearance of wood with aluminum durability. | Architectural accents, residential buildings. | Pros: Natural look, resistant to rot. Cons: Higher cost compared to standard panels. |
Custom Aluminum Composite Panels | Tailored specifications, sizes, and finishes according to client needs. | Specialized architectural projects, unique designs. | Pros: Fully customizable, meets specific project requirements. Cons: Longer lead times, potentially higher costs. |
What Are Standard Aluminum Composite Panels and Their Applications?
Standard aluminum composite panels (ACPs) are the most commonly used type in the industry. They are lightweight and versatile, making them suitable for various applications, including building facades, interior design, and signage. When purchasing, buyers should consider factors such as color options, thickness, and ease of installation. While they are cost-effective, it’s essential to verify their fire resistance ratings to ensure compliance with local regulations.
How Do Fireproof Aluminum Composite Panels Differ?
Fireproof aluminum composite panels are specifically designed to meet stringent safety standards, making them ideal for high-rise buildings and public infrastructure projects. These panels boast enhanced fire-resistant properties, ensuring safety in critical applications. When sourcing these products, buyers should look for certifications that validate their fire resistance and compliance with local building codes. Although they come at a higher cost, the investment can be justified by the safety and compliance benefits they provide.
What Are the Benefits of High-Gloss Aluminum Composite Panels?
High-gloss aluminum composite panels are known for their striking reflective surfaces, making them popular in retail spaces and luxury interiors. These panels can be customized to suit specific design needs, offering a modern aesthetic. Buyers should consider the maintenance requirements, as these surfaces can be prone to scratches and may require more frequent cleaning to maintain their appearance. While they may involve a higher initial investment, the visual impact can enhance brand perception significantly.
Why Choose Wood Finish Aluminum Composite Panels?
Wood finish aluminum composite panels provide the aesthetic appeal of natural wood while offering the durability of aluminum. They are commonly used in architectural accents and residential buildings, appealing to buyers looking for a natural look without the downsides of traditional wood, such as rot and insect damage. When purchasing, buyers should evaluate the cost-effectiveness and maintenance requirements compared to standard panels. Although they may be pricier, their longevity and aesthetic benefits can make them a worthwhile investment.
What Are the Advantages of Custom Aluminum Composite Panels?
Custom aluminum composite panels are tailored to meet specific project requirements, offering flexibility in terms of specifications, sizes, and finishes. This type is ideal for specialized architectural projects where unique designs are necessary. Buyers should consider the lead times and potential costs associated with customization, as these factors can affect project timelines and budgets. While custom panels may take longer to produce, they provide an opportunity for innovation and differentiation in design.
Related Video: Aluminum Composite panel fabrication and installation.
Key Industrial Applications of Aluminum Composite Panel Manufacturers
Industry/Sector | Specific Application of Aluminum Composite Panel Manufacturers | Value/Benefit for the Business | Key Sourcing Considerations for this Application |
---|---|---|---|
Construction & Architecture | Exterior cladding for buildings | Enhances aesthetic appeal and energy efficiency | Compliance with local building codes and fire safety standards |
Signage & Advertising | Digital print signage and displays | Lightweight, durable, and customizable for branding | Quick turnaround times and high-quality printing capabilities |
Transportation | Interior and exterior panels for vehicles | Reduces weight, improving fuel efficiency and aesthetics | Durability under varying environmental conditions |
Retail & Hospitality | Interior design elements and fixtures | Creates an inviting atmosphere and enhances brand image | Customization options for colors and finishes |
Industrial Applications | Protective panels in manufacturing facilities | Increases safety and reduces maintenance costs | Availability of fire-resistant and durable materials |
How Are Aluminum Composite Panels Used in Construction & Architecture?
Aluminum composite panels (ACP) serve as a popular choice for exterior cladding in the construction and architecture sectors. They not only enhance the aesthetic appeal of buildings but also contribute to energy efficiency by providing insulation. International buyers, particularly from regions like Africa and the Middle East, must ensure that the ACPs they source comply with local building codes and fire safety standards. This compliance guarantees the longevity and safety of the structures they invest in.
What Role Do Aluminum Composite Panels Play in Signage & Advertising?
In the signage and advertising industry, aluminum composite panels are utilized for creating digital print signage and displays. Their lightweight and durable nature makes them ideal for both indoor and outdoor applications. For B2B buyers in South America and Europe, sourcing ACPs that offer quick turnaround times and high-quality printing capabilities is crucial. This flexibility allows businesses to adapt quickly to market demands and branding changes.
How Do Aluminum Composite Panels Improve Transportation Applications?
In the transportation sector, aluminum composite panels are used for both interior and exterior applications in vehicles, such as buses and trains. Their lightweight properties significantly reduce the overall weight of the vehicle, leading to improved fuel efficiency. Buyers from Europe and the Middle East should prioritize sourcing panels that can withstand varying environmental conditions, as durability is key to maintaining vehicle aesthetics and functionality over time.
What Are the Benefits of Using Aluminum Composite Panels in Retail & Hospitality?
In retail and hospitality, aluminum composite panels are extensively used for interior design elements and fixtures. They help create an inviting atmosphere that enhances the overall customer experience and brand image. For international buyers, especially in Africa and South America, customization options for colors and finishes are essential. This allows businesses to align the design of their spaces with their brand identity effectively.
How Are Aluminum Composite Panels Utilized in Industrial Applications?
Aluminum composite panels also find applications in industrial settings, particularly as protective panels in manufacturing facilities. These panels help increase safety by providing a barrier against hazards while also reducing maintenance costs due to their durability. B2B buyers should consider sourcing fire-resistant and durable materials to ensure compliance with safety regulations and to enhance workplace safety in their operations.
3 Common User Pain Points for ‘Aluminum Composite Panel Manufacturers’ & Their Solutions
Scenario 1: Navigating Quality Assurance Challenges in Aluminum Composite Panels
The Problem:
B2B buyers often face significant challenges in ensuring the quality and durability of aluminum composite panels (ACPs). With varying manufacturing standards across regions, particularly in emerging markets like Africa and South America, buyers may receive products that do not meet their specifications or local building codes. This situation can lead to costly project delays, reputational damage, and financial losses if subpar materials are used in construction projects.
The Solution:
To effectively navigate quality assurance challenges, buyers should implement a rigorous vetting process when selecting aluminum composite panel manufacturers. Start by requesting product samples and certifications that demonstrate compliance with international standards, such as AAMA 2605 for durability and resistance to fading. Establish clear communication with manufacturers regarding their quality control processes and ask for references from previous clients, particularly those within your region or industry.
Additionally, consider engaging third-party inspection services to assess the quality of the panels before shipment. This proactive approach not only protects your investment but also ensures that the materials used in your projects are reliable and compliant with local regulations. Forming long-term partnerships with trusted manufacturers who prioritize quality will also streamline future procurement processes.
Scenario 2: Overcoming Sourcing and Logistics Hurdles for ACPs
The Problem:
Sourcing aluminum composite panels can be fraught with logistical challenges, especially for international buyers. Issues such as shipping delays, customs clearance, and high freight costs can disrupt project timelines and inflate budgets. This problem is particularly pronounced for buyers in regions like the Middle East and Africa, where infrastructure may not support efficient logistics.
The Solution:
To overcome sourcing and logistics hurdles, B2B buyers should develop a strategic procurement plan that includes multiple suppliers to mitigate risks associated with reliance on a single source. Start by identifying manufacturers with robust logistics capabilities and a proven track record of timely deliveries. Inquire about their shipping options, lead times, and how they handle customs documentation to ensure a smooth import process.
Establishing relationships with local distributors can also enhance your supply chain efficiency. These distributors can help manage logistics and provide valuable insights into local market conditions. Furthermore, utilizing technology platforms that track shipments and provide real-time updates can help you stay informed about your order’s status and anticipate any potential delays.
Scenario 3: Addressing Customization Limitations in ACP Designs
The Problem:
As the demand for unique architectural designs increases, many B2B buyers find themselves limited by the standard options available from aluminum composite panel manufacturers. This limitation can hinder creative projects and result in a lack of differentiation in competitive markets, especially in regions like Europe where design innovation is highly valued.
The Solution:
To address customization limitations, buyers should actively seek manufacturers that offer flexible design options and are open to collaborating on bespoke projects. When reaching out to manufacturers, clearly communicate your specific design requirements, including colors, finishes, and panel sizes. This upfront clarity allows manufacturers to assess their capabilities and propose suitable solutions.
Additionally, consider manufacturers that utilize advanced technologies, such as digital printing, which can facilitate greater design flexibility. Engaging in a consultative approach with suppliers can also lead to innovative solutions tailored to your project needs. Lastly, establishing a prototype phase can help validate designs before mass production, ensuring that the final product meets your expectations.
Strategic Material Selection Guide for Aluminum Composite Panel Manufacturers
When selecting materials for aluminum composite panels (ACP), manufacturers must consider various factors that impact performance, durability, and compliance with international standards. Here, we analyze four common materials used in ACP manufacturing, focusing on their properties, advantages, disadvantages, and implications for international B2B buyers, particularly those from Africa, South America, the Middle East, and Europe.
What Are the Key Properties of Polyethylene (PE) Core Aluminum Composite Panels?
Polyethylene (PE) core panels are among the most commonly used in the ACP industry due to their lightweight nature and cost-effectiveness. PE core panels typically exhibit good thermal insulation, making them suitable for a variety of applications, including interior cladding and signage.
Pros:
– Cost-effective and lightweight, which reduces shipping costs.
– Easy to fabricate and install, making them suitable for quick projects.
Cons:
– Limited fire resistance compared to other core materials.
– Lower durability in extreme weather conditions, which can lead to warping or fading.
Impact on Application: PE core panels are ideal for indoor applications but may not be suitable for high-rise buildings or areas with strict fire safety regulations.
Considerations for International Buyers: Buyers should verify compliance with local fire safety standards, such as ASTM E84 in the USA or EN 13501 in Europe, especially in regions with stringent building codes.
How Do Fire-Retardant (FR) Core Aluminum Composite Panels Perform?
Fire-retardant (FR) core panels are engineered to meet higher safety standards, making them essential for applications requiring enhanced fire resistance. These panels typically contain a mineral-filled core that provides better fire performance.
Pros:
– Enhanced fire safety, making them suitable for high-rise buildings and public spaces.
– Good durability and resistance to weathering.
Cons:
– Generally higher cost compared to PE core panels.
– More complex manufacturing processes may lead to longer lead times.
Impact on Application: FR core panels are particularly advantageous in commercial and industrial applications where safety is paramount.
Considerations for International Buyers: Compliance with fire safety standards is critical. Buyers should look for certifications like EN 13501-1 in Europe or NFPA 285 in the USA to ensure compliance.
What Are the Advantages of Aluminum Honeycomb Core Panels?
Aluminum honeycomb core panels are known for their exceptional strength-to-weight ratio and structural integrity. These panels consist of a lightweight honeycomb structure sandwiched between two aluminum sheets, making them ideal for demanding applications.
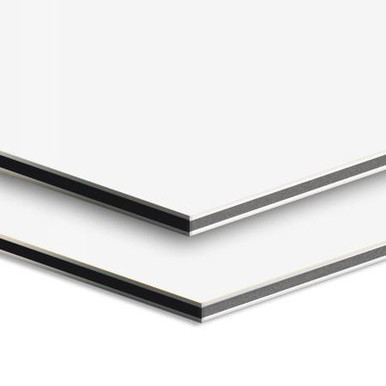
A stock image related to Aluminum Composite Panel Manufacturers.
Pros:
– High strength and rigidity, suitable for large spans and heavy loads.
– Excellent thermal insulation and soundproofing properties.
Cons:
– Higher manufacturing costs due to the complexity of production.
– Limited availability in certain regions may affect supply chains.
Impact on Application: Honeycomb core panels are often used in architectural facades, transportation, and aerospace applications where strength and lightweight characteristics are essential.
Considerations for International Buyers: Buyers should evaluate the supply chain for availability and consider local manufacturing capabilities to avoid delays.
What Are the Benefits of Using Aluminum Composite Panels with a PVDF Coating?
Polyvinylidene fluoride (PVDF) coatings are popular for their durability and resistance to fading, chalking, and corrosion. Panels with PVDF coatings are often used in exterior applications due to their long-lasting performance.
Pros:
– High resistance to UV rays and environmental factors, ensuring longevity.
– Available in a wide range of colors and finishes, enhancing aesthetic appeal.
Cons:
– Higher initial cost compared to standard coatings.
– Requires specialized application techniques, which may increase installation costs.
Impact on Application: PVDF-coated panels are ideal for building facades and other exterior applications where aesthetics and durability are crucial.
Considerations for International Buyers: Ensure that the PVDF coatings meet local environmental regulations and standards, such as VOC emissions, particularly in regions with strict environmental laws.
Summary Table of Material Selection for Aluminum Composite Panels
Material | Typical Use Case for Aluminum Composite Panel Manufacturers | Key Advantage | Key Disadvantage/Limitation | Relative Cost (Low/Med/High) |
---|---|---|---|---|
Polyethylene (PE) Core | Interior cladding, signage | Cost-effective and lightweight | Limited fire resistance | Low |
Fire-Retardant (FR) Core | High-rise buildings, public spaces | Enhanced fire safety | Higher cost and complex manufacturing | Med |
Aluminum Honeycomb Core | Architectural facades, transportation | High strength-to-weight ratio | Higher manufacturing costs | High |
PVDF Coated Panels | Building facades, exterior applications | Excellent durability and aesthetic appeal | Higher initial cost and specialized application | High |
This guide serves as a strategic resource for international B2B buyers, enabling informed decisions when selecting materials for aluminum composite panels, ensuring compliance, and meeting project requirements effectively.
In-depth Look: Manufacturing Processes and Quality Assurance for Aluminum Composite Panel Manufacturers
What Are the Main Stages of Manufacturing Aluminum Composite Panels?
The manufacturing process of aluminum composite panels (ACP) involves several critical stages that ensure the final product meets quality and performance standards. Understanding these stages will help B2B buyers assess potential suppliers effectively.
-
Material Preparation: The first step involves sourcing high-quality raw materials, primarily aluminum sheets and a core material (commonly polyethylene or fire-resistant materials). Manufacturers should ensure that the aluminum is treated for corrosion resistance and that the core material meets fire safety standards.
-
Forming: In this stage, the aluminum sheets are cut and formed into required dimensions. Advanced techniques like CNC machining and laser cutting are often utilized to achieve precise measurements. The forming process may also include bending and shaping the aluminum to meet specific design needs.
-
Assembly: This phase involves bonding the aluminum sheets to the core material. The bonding process is crucial and typically uses either adhesive bonding or extrusion methods. High-quality adhesives ensure durability and longevity, making it vital for buyers to inquire about the types of adhesives used and their compliance with international standards.
-
Finishing: Once assembled, the panels undergo a finishing process that may include painting, coating, or applying protective films. Techniques such as PVDF (polyvinylidene fluoride) coating or powder coating are common to enhance durability and aesthetic appeal. Buyers should look for options that offer UV resistance and color retention.
How Is Quality Assurance Implemented in Aluminum Composite Panel Manufacturing?
Quality assurance (QA) is paramount in ensuring that the aluminum composite panels meet the required standards. Various international and industry-specific standards guide this process.
-
International Standards: Most reputable manufacturers adhere to ISO 9001 standards, which outline the criteria for a quality management system. Compliance ensures that the manufacturer consistently provides products that meet customer and regulatory requirements.
-
Industry-Specific Certifications: In addition to ISO standards, B2B buyers should look for certifications relevant to their markets, such as CE marking in Europe and API standards in the Middle East. These certifications indicate that the products meet specific safety and performance criteria.
-
Quality Control Checkpoints: Effective quality control involves several checkpoints throughout the manufacturing process:
– Incoming Quality Control (IQC): This stage assesses the quality of raw materials before they enter the production line. It ensures that only materials meeting specified criteria are used.
– In-Process Quality Control (IPQC): During the manufacturing stages, IPQC involves regular inspections to monitor adherence to processes and specifications.
– Final Quality Control (FQC): This final checkpoint involves comprehensive testing of finished panels to ensure they meet all standards before shipping.
What Common Testing Methods Are Used for Aluminum Composite Panels?
Testing is integral to the quality assurance process. Here are some common methods used to evaluate the performance of aluminum composite panels:
-
Fire Resistance Testing: Given the importance of safety, panels are subjected to fire resistance tests to comply with local regulations. This includes assessments based on standards like NFPA 285 in North America or S134 in the Middle East.
-
Weathering Tests: Panels are tested for their resistance to UV exposure, humidity, and temperature fluctuations. This ensures that the panels maintain their aesthetic and functional properties over time.
-
Adhesion Testing: This test evaluates the bond strength between the aluminum sheets and the core material. Strong adhesion is crucial for the durability of the panels.
-
Impact Resistance Testing: This assesses how well the panels can withstand physical impacts, which is essential for applications in high-traffic areas.
How Can B2B Buyers Verify Supplier Quality Control Practices?
International B2B buyers need to ensure that their suppliers maintain high standards of quality control. Here are actionable steps for verification:
-
Supplier Audits: Conducting on-site audits can provide insights into the manufacturing processes and quality control measures. Buyers should check for adherence to international standards and certifications.
-
Requesting Quality Reports: Ask suppliers for documentation detailing their quality control processes, including IQC, IPQC, and FQC reports. These documents should outline the testing methods and results.
-
Third-Party Inspections: Engaging independent third-party inspection agencies can provide an unbiased assessment of the supplier’s quality practices. This is especially beneficial for buyers in regions with stringent regulatory requirements.
-
Understanding Certification Nuances: Buyers from Africa, South America, the Middle East, and Europe should be aware of the certification nuances specific to their regions. For instance, European buyers should prioritize CE marking, while Middle Eastern buyers may focus on local fire safety certifications.
What Are the Challenges in Sourcing Quality Aluminum Composite Panels?
Sourcing aluminum composite panels can present challenges, particularly for international buyers. Here are some common issues to consider:
-
Quality Inconsistency: Different manufacturers may have varying quality control practices, leading to inconsistencies in product performance. Conducting thorough due diligence is essential.
-
Regulatory Compliance: Each region may have unique regulations regarding building materials. Buyers must ensure that the panels comply with local standards to avoid legal issues.
-
Supply Chain Reliability: International buyers should assess the supplier’s ability to deliver products on time and in the required quantities. Disruptions in the supply chain can delay projects significantly.
-
Cost Considerations: While high-quality panels may come at a premium, buyers must balance cost with quality to ensure they receive value for their investment. Understanding the total cost of ownership, including maintenance and replacement, can aid in making informed decisions.
By understanding the manufacturing processes, quality assurance practices, and challenges associated with aluminum composite panels, B2B buyers can make informed decisions that enhance their projects’ success.
Practical Sourcing Guide: A Step-by-Step Checklist for ‘Aluminum Composite Panel Manufacturers’
Introduction
Navigating the procurement of aluminum composite panels (ACP) can be a daunting task, especially for international B2B buyers from diverse regions such as Africa, South America, the Middle East, and Europe. This step-by-step checklist aims to streamline your sourcing process by providing actionable insights that help ensure you make informed decisions when selecting manufacturers.
Step 1: Define Your Technical Specifications
Before reaching out to manufacturers, clarify your technical requirements for aluminum composite panels. Consider factors such as thickness, insulation properties, fire resistance ratings, and aesthetic finishes. A well-defined specification not only helps you communicate effectively with suppliers but also ensures that the products meet your project needs and local regulations.
Step 2: Conduct Market Research to Identify Potential Suppliers
Start by researching various aluminum composite panel manufacturers globally. Utilize online platforms, industry publications, and trade shows to compile a list of potential suppliers. Look for manufacturers with a strong reputation, positive customer reviews, and a portfolio that aligns with your project requirements. This groundwork will help you identify reliable sources and gauge the competitive landscape.
Step 3: Evaluate Supplier Certifications and Compliance
Ensure that the manufacturers you consider possess relevant certifications and comply with international standards. Certifications such as ISO 9001 for quality management and AAMA 2605 for durability are essential indicators of a supplier’s commitment to quality. Verify if their products meet local building codes and regulations, as this will save you from potential legal issues down the line.
Step 4: Request Samples for Quality Assessment
Before making a bulk purchase, request samples of the aluminum composite panels. Evaluate the samples for quality, durability, and aesthetic appeal. This step allows you to assess the supplier’s manufacturing capabilities firsthand, ensuring that the products meet your expectations in real-world applications.
Step 5: Review Pricing and Payment Terms
Once you’ve narrowed down your options, compare pricing structures among the shortlisted suppliers. Pay attention to not just the unit price, but also the total cost of ownership, which includes shipping, taxes, and potential duties. Additionally, inquire about payment terms and conditions, as flexible arrangements can benefit your cash flow management.
Step 6: Assess After-Sales Support and Warranty Policies
A reliable supplier should offer robust after-sales support and warranty policies. Inquire about their procedures for handling defects or issues post-purchase. Understanding the warranty terms will give you peace of mind and protect your investment, particularly for large-scale projects where quality is paramount.
Step 7: Finalize the Contract with Clear Terms
Once you select a supplier, draft a detailed contract outlining the terms of the agreement. Include specifications, delivery timelines, payment schedules, and any penalties for non-compliance. A well-structured contract protects both parties and sets clear expectations, reducing the likelihood of disputes.
By following this checklist, you can confidently navigate the procurement process for aluminum composite panels, ensuring that you choose the right manufacturer to meet your project needs effectively.
Comprehensive Cost and Pricing Analysis for Aluminum Composite Panel Manufacturers Sourcing
Understanding the cost structure and pricing of aluminum composite panels (ACPs) is crucial for international B2B buyers, particularly those sourcing from regions like Africa, South America, the Middle East, and Europe. This analysis will break down the key components that influence pricing and offer actionable insights for buyers looking to optimize their purchasing decisions.
What Are the Key Cost Components for Aluminum Composite Panels?
-
Materials
The primary cost driver in ACP manufacturing is the raw materials, which include aluminum sheets and core materials (like polyethylene or mineral-filled). The choice of materials significantly affects the panel’s durability, weight, and thermal insulation properties. High-quality materials may lead to higher upfront costs but can provide better performance and longevity. -
Labor
Labor costs encompass the workforce involved in the production process, which varies by region. Countries with lower labor costs can offer competitive pricing; however, this may sometimes compromise quality. Understanding the labor market in the manufacturing country can provide insights into potential pricing variances. -
Manufacturing Overhead
This includes expenses related to factory operations, such as utilities, maintenance, and equipment depreciation. Efficient production processes can reduce overhead costs, allowing manufacturers to offer more competitive prices. -
Tooling
Tooling costs refer to the investments made in machinery and molds for production. Custom shapes and sizes may require specialized tooling, which can increase initial costs. Buyers should consider how tooling costs are amortized over production runs. -
Quality Control (QC)
Implementing stringent QC measures ensures that products meet industry standards. While this may add to the cost, it is crucial for maintaining quality and compliance, especially for international projects. -
Logistics
Transportation costs can fluctuate based on the distance from the manufacturer to the buyer’s location and the chosen shipping method. Understanding logistics costs is essential for calculating the total cost of ownership. -
Margin
Manufacturers will include a profit margin in their pricing. This margin can vary significantly between suppliers, influenced by their market positioning and operational efficiencies.
What Influences the Pricing of Aluminum Composite Panels?
-
Volume and Minimum Order Quantity (MOQ)
Bulk purchases often lead to lower per-unit costs. Negotiating MOQs can help buyers achieve cost savings, especially for large projects. -
Specifications and Customization
Custom specifications (like unique colors, finishes, or dimensions) can increase costs. Buyers should balance customization needs with budget constraints. -
Quality and Certifications
Panels that meet specific quality standards (e.g., fire resistance, environmental certifications) may command higher prices. Buyers should assess the importance of these certifications in relation to project requirements. -
Supplier Factors
The reputation and reliability of the supplier can affect pricing. Established manufacturers with a track record of quality may charge a premium. -
Incoterms
Understanding shipping terms (like FOB, CIF) is crucial as they dictate who bears the cost and risk at various stages of shipping. This can impact the overall cost significantly.
How Can Buyers Optimize Their Sourcing Strategy?
-
Effective Negotiation
Engage in negotiations with suppliers to secure better pricing, especially for larger orders. Clearly communicate your needs and be open to discussing terms. -
Assess Total Cost of Ownership (TCO)
Consider not just the purchase price but also installation, maintenance, and potential warranty costs. A lower initial price may not always equate to better value. -
Explore Multiple Suppliers
Diversifying your supplier base can provide leverage in negotiations and expose you to various pricing strategies and product offerings. -
Stay Informed on Market Trends
Being aware of fluctuations in raw material prices and global supply chain issues can help buyers anticipate cost changes and adjust their purchasing strategies accordingly.
Disclaimer on Pricing
It is essential to note that pricing for aluminum composite panels can vary widely based on numerous factors, including market conditions, supplier pricing strategies, and specific project requirements. Buyers should request updated quotes directly from manufacturers to obtain accurate pricing for their specific needs.
Alternatives Analysis: Comparing Aluminum Composite Panel Manufacturers With Other Solutions
When selecting materials for construction and design projects, understanding the available alternatives to Aluminum Composite Panels (ACP) is crucial for B2B buyers. While ACPs are renowned for their durability, aesthetic appeal, and versatility, there are several alternative solutions that may better fit specific project requirements. Below, we compare Aluminum Composite Panel Manufacturers with other viable options, providing actionable insights for international buyers.
Comparison Table: Aluminum Composite Panels vs. Alternative Solutions
Comparison Aspect | Aluminum Composite Panel Manufacturers | Fiber Cement Board | High-Pressure Laminate (HPL) |
---|---|---|---|
Performance | Excellent weather resistance, lightweight, and strong. | Highly durable, fire-resistant, and moisture-resistant. | Good impact resistance, extensive design options. |
Cost | Moderate to high initial investment, long-term savings due to durability. | Generally lower initial costs but may require more maintenance. | Higher initial costs but long-lasting and low maintenance. |
Ease of Implementation | Easy to install, lightweight, and customizable. | Requires skilled labor for installation, more complex than ACP. | Straightforward installation, but may need specialized tools. |
Maintenance | Low maintenance, resistant to fading and corrosion. | Moderate maintenance, susceptible to cracking if not properly installed. | Low maintenance, resistant to stains and scratches. |
Best Use Case | Ideal for modern facades, signage, and interior applications. | Best for exterior cladding in harsh environments, commercial buildings. | Suitable for decorative interior surfaces and high-traffic areas. |
What Are the Pros and Cons of Fiber Cement Board?
Fiber Cement Board is a composite material made from cement, sand, and cellulose fibers. It offers exceptional durability and fire resistance, making it a strong contender for exterior applications.
Pros:
– Durability: Extremely resistant to weather, pests, and fire, making it ideal for harsh climates.
– Low Maintenance: Requires minimal upkeep compared to traditional wood siding.
Cons:
– Installation Complexity: Requires skilled labor for proper installation, which may increase labor costs.
– Weight: Heavier than ACP, which may require additional structural support.
How Does High-Pressure Laminate (HPL) Compare?
High-Pressure Laminate is produced by compressing layers of resin-impregnated paper and decorative paper under high pressure. It is often used in interior applications due to its extensive design possibilities.
Pros:
– Design Flexibility: Available in a wide range of colors, patterns, and textures, allowing for unique design solutions.
– Resistance: Good resistance to impact, scratches, and stains.
Cons:
– Cost: Higher initial investment compared to ACP, which may deter budget-sensitive projects.
– Limited Exterior Use: Generally not recommended for exterior applications due to lower weather resistance.
How Can B2B Buyers Choose the Right Solution?
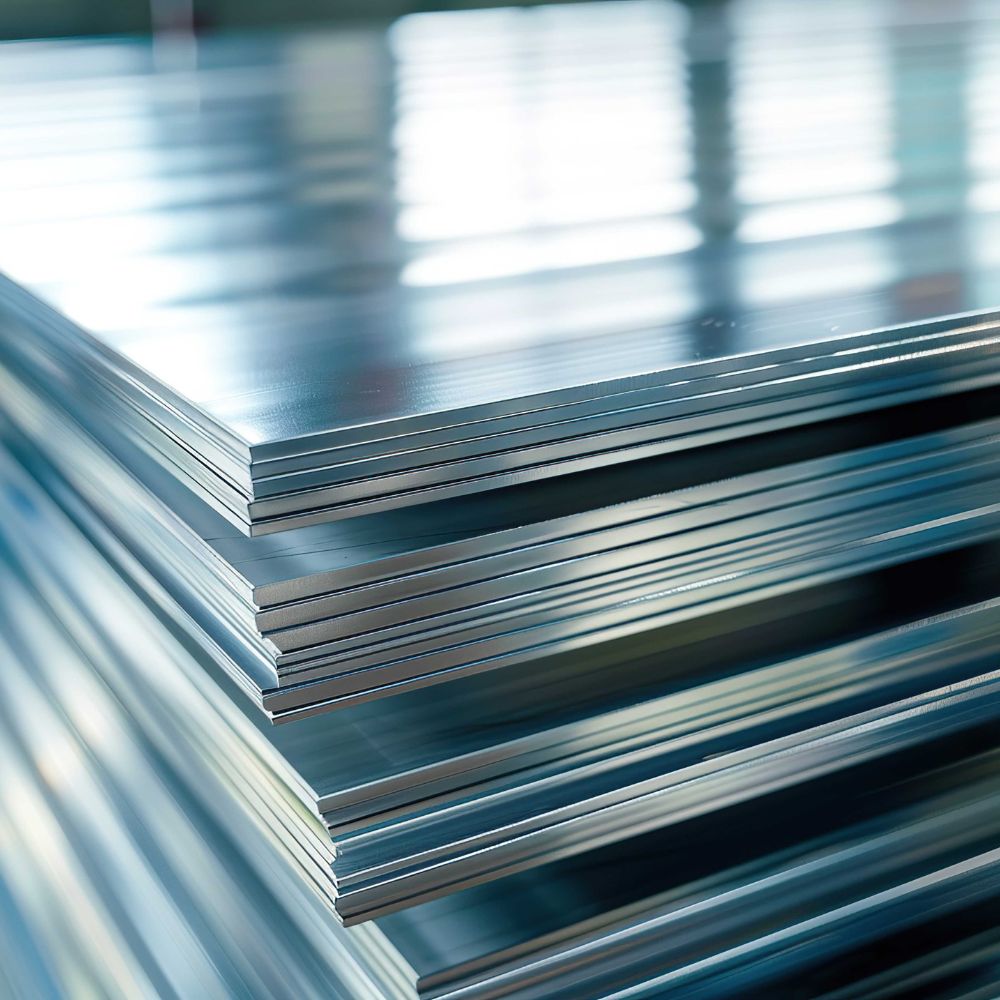
A stock image related to Aluminum Composite Panel Manufacturers.
When selecting between Aluminum Composite Panels and their alternatives, B2B buyers should consider several factors, including the specific application, environmental conditions, budget constraints, and design requirements. For projects requiring lightweight materials that offer aesthetic versatility and low maintenance, ACPs may be the best choice. However, for buyers focused on fire resistance and durability in extreme conditions, Fiber Cement Board could be more appropriate. Conversely, if interior design and unique aesthetics are the priority, High-Pressure Laminate may provide the desired results.
Ultimately, aligning the material choice with project goals and operational needs will help ensure a successful outcome. Buyers should also consider the long-term implications of each material in terms of maintenance, durability, and overall lifecycle costs.
Essential Technical Properties and Trade Terminology for Aluminum Composite Panel Manufacturers
What Are the Key Technical Properties of Aluminum Composite Panels?
When sourcing aluminum composite panels (ACPs), understanding their technical properties is crucial for making informed purchasing decisions. Here are the essential specifications to consider:
1. Material Grade
Material grade refers to the quality of the aluminum used in ACPs. Common grades include 3003 and 5005, with 5005 often providing better corrosion resistance and surface quality. Buyers should prioritize higher-grade materials for durability and longevity, especially in harsh environments typical of regions like the Middle East and South America.
2. Panel Thickness
Panel thickness typically ranges from 3mm to 6mm. Thicker panels offer enhanced durability and resistance to impact, making them suitable for high-traffic areas or extreme weather conditions. Buyers must assess project requirements to choose the appropriate thickness that balances cost and performance.
3. Fire Resistance Rating
Fire resistance is a critical property, especially in commercial applications. ACPs can be classified into different categories based on fire ratings, such as A2 (non-combustible) or B1 (limited combustibility). Understanding local building codes and safety regulations is essential for compliance, particularly in regions with strict fire safety laws.
4. Tolerance
Tolerance refers to the allowable deviation in panel dimensions, typically expressed in millimeters. Tight tolerances are necessary for projects requiring precise installation, such as curtain walls and facades. Buyers should inquire about the manufacturer’s tolerance specifications to ensure compatibility with their design requirements.
5. Coating Types
The surface treatment of ACPs is vital for aesthetic appeal and longevity. Common coatings include Polyvinylidene Fluoride (PVDF) and Polyester (PE). PVDF coatings offer superior UV resistance and color retention, making them ideal for outdoor applications in sunny regions like Africa and the UAE.
6. Weight
The weight of ACPs influences installation methods and structural requirements. Lightweight panels are easier to handle and install, reducing labor costs. However, buyers must ensure that the lightweight option does not compromise the panel’s durability or fire resistance.
What Are Common Trade Terminology and Their Importance in B2B Transactions?
Familiarity with industry terminology can significantly streamline the procurement process. Here are several key terms that every buyer should know:
1. OEM (Original Equipment Manufacturer)
An OEM is a company that produces components that are used in another company’s products. In the ACP industry, many manufacturers operate as OEMs, providing customized panels for specific projects. Understanding OEM relationships can help buyers negotiate better pricing and specifications.
2. MOQ (Minimum Order Quantity)
MOQ refers to the smallest number of units a supplier is willing to sell. This term is crucial for buyers to consider as it affects budget and inventory management. Suppliers often set MOQs to optimize production efficiency, so buyers should negotiate terms that align with their project needs.
3. RFQ (Request for Quotation)
An RFQ is a document sent to suppliers to solicit price quotes for specific products or services. Including detailed specifications in an RFQ helps ensure accurate pricing and reduces misunderstandings. B2B buyers should prepare comprehensive RFQs to facilitate efficient sourcing.
4. Incoterms (International Commercial Terms)
Incoterms are a set of predefined commercial terms published by the International Chamber of Commerce. They define the responsibilities of buyers and sellers regarding shipping, insurance, and tariffs. Familiarity with Incoterms can help buyers avoid unexpected costs and streamline international transactions.
5. Lead Time
Lead time is the period between placing an order and receiving the goods. Understanding lead times is crucial for project planning, especially in industries with tight timelines. Buyers should communicate their project schedules to suppliers to ensure timely delivery.
By grasping these technical specifications and trade terminologies, B2B buyers can make more informed decisions and foster successful partnerships with aluminum composite panel manufacturers.
Navigating Market Dynamics and Sourcing Trends in the Aluminum Composite Panel Manufacturers Sector
What Are the Current Market Dynamics and Sourcing Trends for Aluminum Composite Panels?
The global aluminum composite panel (ACP) market is experiencing significant growth, driven by various factors such as urbanization, infrastructural development, and the rising demand for lightweight yet durable construction materials. According to industry reports, the market is expected to grow at a compound annual growth rate (CAGR) of over 6% from 2023 to 2030. For international B2B buyers, particularly from Africa, South America, the Middle East, and Europe, understanding these dynamics is essential for effective sourcing.
One of the most notable trends is the increasing adoption of advanced manufacturing technologies, such as automation and digital fabrication techniques. These technologies not only enhance production efficiency but also improve product quality and customization options. Buyers should look for manufacturers who leverage these innovations, as they are likely to offer more competitive pricing and superior products.
Additionally, the demand for aesthetic and functional versatility in ACPs is on the rise. Buyers are increasingly seeking panels that offer a variety of finishes, colors, and textures. Manufacturers that can provide customized solutions will have a competitive edge. Regions like Europe and the UAE are particularly focused on high-end finishes that meet strict architectural standards, making it crucial for buyers to partner with manufacturers who understand local regulations and market preferences.
How Is Sustainability Influencing Sourcing Decisions for Aluminum Composite Panels?
Sustainability is becoming a critical factor in the sourcing of aluminum composite panels. The environmental impact of construction materials has gained significant attention, prompting buyers to prioritize ethical sourcing practices. Manufacturers that utilize recycled materials, minimize waste, and adhere to environmentally friendly production processes are increasingly favored.
Moreover, certifications such as LEED (Leadership in Energy and Environmental Design) and BREEAM (Building Research Establishment Environmental Assessment Method) are becoming essential benchmarks for buyers. These certifications not only validate the sustainability of materials but also enhance the marketability of projects, especially in regions like Europe where green building practices are highly emphasized.
B2B buyers should actively seek out suppliers who can demonstrate a commitment to sustainability, offering products made from eco-friendly materials and processes. This focus on sustainability not only aligns with global trends but also meets the growing consumer demand for environmentally responsible products.
How Has the Aluminum Composite Panel Industry Evolved Over Time?
The aluminum composite panel industry has undergone significant evolution since its inception in the 1960s. Initially developed for signage and interior applications, ACPs have expanded into a wide range of applications, including exterior cladding, architectural facades, and interior design. This evolution has been driven by technological advancements and the increasing recognition of ACPs as a viable alternative to traditional materials like wood and brick.
Today, the market is characterized by a diverse range of products that cater to various aesthetic and functional needs. From fire-resistant panels to those with enhanced insulation properties, the evolution of ACPs reflects the industry’s response to changing consumer preferences and regulatory requirements. For B2B buyers, understanding this historical context can provide valuable insights into the capabilities and innovations that different manufacturers bring to the table, enabling informed sourcing decisions.
Conclusion
In summary, the aluminum composite panel market presents numerous opportunities for international B2B buyers. By staying informed about market dynamics, prioritizing sustainability in sourcing, and understanding the historical context of the industry, buyers can make strategic decisions that enhance their projects and align with global trends. As the demand for innovative, sustainable construction materials continues to grow, partnering with forward-thinking manufacturers will be crucial for success.
Frequently Asked Questions (FAQs) for B2B Buyers of Aluminum Composite Panel Manufacturers
-
How do I choose the right aluminum composite panel manufacturer for my project?
To select the ideal aluminum composite panel (ACP) manufacturer, consider factors such as product quality, manufacturing capabilities, and compliance with international standards. Look for manufacturers with certifications like AAMA or NFPA, which indicate adherence to quality and safety regulations. Review their portfolio for a variety of finishes and customization options that align with your project needs. Engage in discussions about their production timelines, minimum order quantities (MOQs), and after-sales support to ensure they can meet your requirements. -
What are the key characteristics of high-quality aluminum composite panels?
High-quality aluminum composite panels should possess durability, lightweight properties, and excellent weather resistance. Look for panels with a robust fire rating and certifications that meet local building codes. The finish should be scratch-resistant and maintain color integrity over time, especially in harsh climates. Additionally, consider panels with a warranty that covers defects and performance, which reflects the manufacturer’s confidence in their product. -
What customization options are available for aluminum composite panels?
Many manufacturers offer extensive customization options, including various colors, textures, and finishes. You can request specific dimensions, thicknesses, and surface treatments to fit your architectural vision. Some companies also provide bespoke designs or printed graphics for branding purposes. It’s advisable to discuss your customization needs early in the procurement process to ensure the manufacturer can meet your specifications effectively. -
What are the typical minimum order quantities (MOQs) for aluminum composite panels?
Minimum order quantities for aluminum composite panels can vary significantly by manufacturer and project type. Generally, MOQs can range from a few hundred to several thousand square meters. Smaller projects may encounter higher costs per unit, while larger orders often benefit from volume discounts. Always clarify MOQs with potential suppliers and assess how they align with your project scale and budget. -
How can I ensure quality assurance when sourcing aluminum composite panels?
To ensure quality assurance, request detailed product specifications and certifications from manufacturers. Ask about their quality control processes, including testing for durability, fire resistance, and color fastness. It is also beneficial to review customer testimonials and case studies that demonstrate the manufacturer’s track record. Consider visiting the manufacturing facility if feasible, or request samples to evaluate the panel quality firsthand before making a significant investment. -
What payment terms should I expect when dealing with aluminum composite panel suppliers?
Payment terms vary by supplier, but common arrangements include a deposit upon order confirmation (typically 30% to 50%) and the balance before shipping or upon delivery. Some manufacturers may offer credit terms for established buyers. Ensure you understand the payment structure, including any additional costs for customization or shipping. It’s wise to negotiate favorable terms that protect your interests, especially if dealing with international suppliers. -
What logistics considerations should I keep in mind when importing aluminum composite panels?
When importing aluminum composite panels, consider the logistics of shipping, including costs, transit times, and customs duties. Verify the supplier’s shipping capabilities and whether they can handle the entire logistics process, including freight forwarding and customs clearance. Understanding the local regulations in your country regarding building materials is crucial to avoid delays or penalties. Collaborate with a reliable logistics partner to streamline the import process. -
How do I assess the reputation of aluminum composite panel manufacturers?
Assessing the reputation of manufacturers involves researching online reviews, industry certifications, and their presence in trade shows or exhibitions. Engage with past clients if possible to gather insights about their experiences. Additionally, review the manufacturer’s history, including years in operation, product range, and market reach. A well-established company with a solid reputation is more likely to provide quality products and reliable service.
Important Disclaimer & Terms of Use
⚠️ Important Disclaimer
The information provided in this guide, including content regarding manufacturers, technical specifications, and market analysis, is for informational and educational purposes only. It does not constitute professional procurement advice, financial advice, or legal advice.
While we have made every effort to ensure the accuracy and timeliness of the information, we are not responsible for any errors, omissions, or outdated information. Market conditions, company details, and technical standards are subject to change.
B2B buyers must conduct their own independent and thorough due diligence before making any purchasing decisions. This includes contacting suppliers directly, verifying certifications, requesting samples, and seeking professional consultation. The risk of relying on any information in this guide is borne solely by the reader.
Strategic Sourcing Conclusion and Outlook for Aluminum Composite Panel Manufacturers
In the rapidly evolving market of aluminum composite panels (ACPs), strategic sourcing remains pivotal for international B2B buyers. By focusing on quality, compliance, and innovative design, companies can differentiate themselves and meet the increasing demands for sustainable and durable construction materials. Buyers from Africa, South America, the Middle East, and Europe should prioritize manufacturers that not only offer advanced technologies but also demonstrate a commitment to customer satisfaction through customizable solutions.
How Can Buyers Leverage Strategic Sourcing in ACP Procurement?
Engaging with leading manufacturers, such as IDEABOND and ALPOLIC, allows businesses to tap into a wealth of expertise and diverse product offerings. By conducting thorough comparisons of suppliers and their capabilities, buyers can ensure they choose partners who align with their project requirements and budget constraints. This approach not only enhances product quality but also streamlines the procurement process, enabling timely project completion.
What Does the Future Hold for the Aluminum Composite Panel Industry?
As the global construction landscape continues to evolve, the demand for innovative ACP solutions will only grow. B2B buyers are encouraged to stay ahead of market trends and technological advancements, ensuring they are well-positioned to capitalize on new opportunities. By fostering strategic partnerships and embracing a proactive sourcing strategy, international buyers can secure their place in this competitive market, paving the way for successful projects in the years to come.