Discover Top Angle Grinder Manufacturers: The Ultimate Guide (2025)
Introduction: Navigating the Global Market for angle grinder manufacturer
Navigating the global market for angle grinder manufacturers presents significant challenges for international B2B buyers, particularly those based in Africa, South America, the Middle East, and Europe. Sourcing high-quality angle grinders that meet specific operational requirements while balancing cost-effectiveness can be daunting. With an array of manufacturers offering varying specifications, it becomes essential to understand the nuances of the market, including product types, applications, supplier vetting processes, and pricing strategies.
This comprehensive guide serves as an essential resource for B2B buyers aiming to make informed purchasing decisions. We delve into the different types of angle grinders available, exploring their diverse applications across industries such as construction, metalworking, and automotive repair. Furthermore, we provide insights into evaluating suppliers based on quality, reliability, and compliance with international standards, ensuring that buyers can confidently select partners that align with their business goals.
By addressing critical questions and challenges, this guide empowers buyers to navigate the complexities of sourcing angle grinders effectively. Whether you are looking for specialized tools to enhance productivity or seeking competitive pricing without compromising quality, our insights will equip you with the knowledge necessary to thrive in the global marketplace. Understanding these dynamics is crucial for making strategic purchasing decisions that can lead to successful business outcomes.
Understanding angle grinder manufacturer Types and Variations
Type Name | Key Distinguishing Features | Primary B2B Applications | Brief Pros & Cons for Buyers |
---|---|---|---|
Corded Angle Grinders | Continuous power supply, typically higher RPMs | Heavy-duty construction, metalworking | Pros: High power, no battery limitations. Cons: Limited mobility, requires power source. |
Cordless Angle Grinders | Battery-operated, portable, versatile | Construction sites, maintenance tasks | Pros: Greater mobility, no cords to manage. Cons: Limited run time, may require multiple batteries. |
Pneumatic Angle Grinders | Air-powered, lightweight, and often high RPM | Automotive repair, fabrication shops | Pros: Lightweight, consistent power. Cons: Requires air compressor, can be noisy. |
Variable Speed Angle Grinders | Adjustable speed settings for different materials | Precision work, metal fabrication | Pros: Versatile for various tasks, reduces risk of damage. Cons: More complex, potentially higher cost. |
Die Grinders | Smaller size, designed for detailed work | Precision grinding, engraving, polishing | Pros: Excellent for tight spaces, highly versatile. Cons: Less power compared to larger models. |
What Are Corded Angle Grinders and Their Key Characteristics?
Corded angle grinders are known for their consistent power output, making them ideal for heavy-duty applications in construction and metalworking. They typically operate at higher RPMs, allowing for efficient grinding and cutting. B2B buyers should consider the availability of power sources at job sites and the need for mobility when choosing corded models. While they provide uninterrupted operation, the lack of portability can be a drawback for some applications.
How Do Cordless Angle Grinders Enhance Operational Flexibility?
Cordless angle grinders offer unmatched mobility, allowing users to operate in areas without immediate access to power outlets. They are perfect for construction sites and maintenance tasks where flexibility is essential. Buyers should evaluate battery life and charging times, as these factors can impact productivity. While they may not match the power of corded models, advancements in battery technology have significantly improved their performance.
What Are the Benefits of Pneumatic Angle Grinders in Industrial Settings?
Pneumatic angle grinders are air-powered tools that are favored for their lightweight design and high RPM capabilities. They are commonly used in automotive repair and fabrication shops. B2B buyers need to consider the requirement for an air compressor and the potential noise levels when selecting these tools. While they deliver consistent power and are easy to handle, the dependency on an air source can limit their use in some environments.
Why Choose Variable Speed Angle Grinders for Precision Work?
Variable speed angle grinders allow users to adjust the speed settings according to the material being worked on, making them suitable for precision tasks in metal fabrication and other detailed applications. This versatility helps reduce the risk of damaging the workpiece. Buyers should be aware of the added complexity and potential cost associated with these models, but the ability to tailor performance can justify the investment.
What Makes Die Grinders Ideal for Detailed Applications?
Die grinders are compact tools designed for precision grinding, engraving, and polishing. Their smaller size allows for work in tight spaces, making them highly versatile for various applications. B2B buyers should consider the specific tasks they need to accomplish, as die grinders may not provide the same power as larger angle grinders. However, their adaptability for detailed work often outweighs this limitation in suitable contexts.
Related Video: Learn how to Properly install cutting and Grinding discs | Angle grinder tutorial
Key Industrial Applications of angle grinder manufacturer
Industry/Sector | Specific Application of angle grinder manufacturer | Value/Benefit for the Business | Key Sourcing Considerations for this Application |
---|---|---|---|
Metal Fabrication | Cutting and shaping metal sheets and rods | Enhances precision in metalworking and reduces waste | Quality of grinding discs, power specifications, durability |
Construction | Surface preparation for concrete and masonry | Improves adhesion of coatings and finishes | Compatibility with various materials, ease of use, safety features |
Automotive Repair | Rust removal and bodywork repairs | Increases efficiency in repair processes | Availability of replacement parts, customer support, warranty |
Shipbuilding | Grinding welds and finishing metal surfaces | Ensures structural integrity and aesthetic quality | Portability, power source options, ergonomic design |
Electrical Installation | Deburring and cutting electrical conduits | Facilitates safer and cleaner installations | Versatility in attachments, compliance with safety standards, ease of handling |
How is Angle Grinder Manufacturer Used in Metal Fabrication?
In the metal fabrication industry, angle grinders are essential for cutting, shaping, and finishing metal sheets and rods. They solve common problems like inefficient cuts and uneven surfaces, which can lead to material wastage. Buyers in this sector, particularly from Africa and South America, should consider the quality of grinding discs and power specifications to ensure optimal performance and durability, especially in harsh working environments.
What Role Does Angle Grinder Manufacturer Play in Construction?
Angle grinders are widely used in construction for surface preparation of concrete and masonry. By providing a smooth surface, they enhance the adhesion of coatings and finishes, thus extending the longevity of structures. International buyers, especially from the Middle East and Europe, should focus on the compatibility of grinders with various materials and prioritize safety features, as construction sites often pose unique hazards.
Why is Angle Grinder Manufacturer Important in Automotive Repair?
In automotive repair, angle grinders are invaluable for rust removal and bodywork repairs. They significantly enhance efficiency in repair processes by allowing quick and effective removal of imperfections. Buyers in this sector, particularly in Europe and South America, should look for manufacturers that offer a wide range of replacement parts and robust customer support, as ongoing maintenance is crucial for prolonged equipment life.
How Does Angle Grinder Manufacturer Contribute to Shipbuilding?
In shipbuilding, angle grinders are used for grinding welds and finishing metal surfaces to ensure both structural integrity and aesthetic quality. Their use helps in meeting stringent safety and quality standards in the maritime industry. Buyers should consider the portability and power source options of grinders, as shipbuilding environments can vary greatly in terms of space and accessibility.
What is the Application of Angle Grinder Manufacturer in Electrical Installation?
Angle grinders are utilized in electrical installation for deburring and cutting electrical conduits. This application is vital for ensuring safe and clean installations, which is essential for compliance with safety regulations. International buyers, particularly from Africa and the Middle East, should prioritize versatility in attachments and compliance with safety standards when sourcing angle grinders, ensuring they meet the specific needs of electrical work.
Related Video: Angle Grinders 101 | How to Use an Angle Grinder
3 Common User Pain Points for ‘angle grinder manufacturer’ & Their Solutions
Scenario 1: Ensuring Quality and Performance Consistency in Angle Grinders
The Problem: One of the primary challenges faced by B2B buyers when sourcing angle grinders is the inconsistency in quality and performance across different manufacturers. Businesses require tools that can withstand rigorous use while maintaining high safety standards. For instance, a construction company in Africa may find that the angle grinders they receive from a supplier do not perform uniformly, leading to downtime and safety risks. This inconsistency can also complicate inventory management and increase costs due to frequent replacements or repairs.
The Solution: To mitigate this issue, B2B buyers should establish a robust supplier evaluation process. This includes asking for product certifications (e.g., ISO standards), performance data, and detailed specifications from manufacturers. Buyers can also request samples for trial before committing to larger orders, allowing them to assess quality firsthand. Engaging in direct communication with manufacturers regarding their production processes and quality control measures can provide further assurance. Additionally, consider forming partnerships with reputable manufacturers known for their reliability and consistency in product quality. Leveraging reviews and testimonials from other businesses in similar industries can also guide decision-making.
Scenario 2: Navigating Compliance and Regulatory Challenges with Angle Grinders
The Problem: Compliance with local regulations and safety standards is a significant concern for international B2B buyers, particularly in regions with stringent laws, such as Europe. Angle grinders must meet specific safety and performance criteria, and failure to comply can lead to legal issues and financial penalties. For example, a metal fabrication company in South America may struggle to ensure that the angle grinders they import adhere to both local and international safety standards, impacting their operational legality and market reputation.
The Solution: To address compliance issues, B2B buyers should conduct thorough research into the regulatory landscape of their target market. This involves understanding the specific standards applicable to angle grinders in their region and ensuring that the manufacturers they choose can provide the necessary certifications. Buyers can also work closely with legal experts or compliance consultants to navigate these regulations effectively. When selecting an angle grinder manufacturer, inquire about their compliance history and ask for documentation that proves adherence to relevant standards. Establishing a transparent relationship with suppliers can also facilitate easier communication regarding any changes in regulations, ensuring ongoing compliance.
Scenario 3: Managing Cost and Supply Chain Efficiency for Angle Grinders
The Problem: Cost management is a critical concern for B2B buyers, especially in emerging markets like Africa and South America. Fluctuating prices for raw materials and transportation can significantly impact the overall cost of angle grinders. Additionally, delays in supply chains can lead to project interruptions, causing financial losses and damaging relationships with clients. A contractor in the Middle East may experience delays due to unforeseen logistics issues, which can jeopardize project deadlines.
The Solution: To enhance supply chain efficiency and manage costs effectively, B2B buyers should explore multiple sourcing options and maintain relationships with various manufacturers. This diversification can help mitigate risks associated with price fluctuations and supply chain disruptions. Buyers should also consider negotiating long-term contracts with manufacturers to lock in prices and ensure a steady supply. Implementing technology solutions, such as supply chain management software, can help track orders and inventory levels in real-time, allowing for proactive decision-making. Additionally, establishing strong communication channels with suppliers can facilitate faster responses to potential delays, enabling buyers to adjust their project timelines accordingly.
Strategic Material Selection Guide for angle grinder manufacturer
When selecting materials for angle grinders, manufacturers must consider various factors that impact performance, cost, and compliance with international standards. Below are analyses of four common materials used in angle grinder manufacturing, focusing on their properties, advantages, disadvantages, and specific considerations for international B2B buyers.
What Are the Key Properties of Steel for Angle Grinder Manufacturing?
Steel is the most commonly used material for angle grinder components, particularly for the housing and internal gears.
- Key Properties: Steel offers high tensile strength, good ductility, and excellent wear resistance. It typically has a temperature rating up to 500°C and can withstand significant pressure, making it ideal for heavy-duty applications.
- Pros & Cons: The durability of steel ensures a long product lifespan, but it can be susceptible to corrosion if not properly treated. While steel is generally cost-effective, high-grade steel variants can be expensive and require complex manufacturing processes.
- Impact on Application: Steel is compatible with most grinding media, including metal and masonry. However, it may not perform as well in environments with high humidity unless coated or treated.
- Considerations for International Buyers: Compliance with standards like ASTM A36 or DIN EN 10025 is crucial. Buyers from regions like Africa or South America should ensure that suppliers meet these standards to avoid quality issues.
How Does Aluminum Benefit Angle Grinder Components?
Aluminum is often used in angle grinder manufacturing, particularly for housings and non-load-bearing components.
- Key Properties: Aluminum is lightweight, resistant to corrosion, and has a good thermal conductivity rating. It can handle temperatures up to 250°C, making it suitable for lower-intensity applications.
- Pros & Cons: The lightweight nature of aluminum enhances user comfort and reduces fatigue during prolonged use. However, its lower strength compared to steel may limit its use in high-stress applications. Additionally, aluminum can be more expensive than steel.
- Impact on Application: Aluminum is particularly effective for applications requiring portability and ease of handling. However, it may not be suitable for heavy-duty grinding tasks.
- Considerations for International Buyers: Buyers should check for compliance with standards like ASTM B221. In regions like Europe, where lightweight tools are preferred, aluminum components are increasingly popular.
What Role Does Plastic Play in Angle Grinder Manufacturing?
Plastic is utilized in non-structural components of angle grinders, such as handles and covers.
- Key Properties: Plastics are lightweight, provide good insulation, and are resistant to corrosion. They can withstand temperatures up to 100°C, which may limit their use in high-heat applications.
- Pros & Cons: The main advantage of plastic is its low cost and ease of manufacturing. However, it may lack the durability and strength required for heavy-duty applications, making it less suitable for professional-grade tools.
- Impact on Application: Plastic components are ideal for consumer-grade tools where weight reduction is essential. However, they may not perform well in industrial settings.
- Considerations for International Buyers: Buyers should ensure that plastic components meet safety standards, such as those outlined by ASTM D638. In regions like the Middle East, where high temperatures are common, the thermal resistance of plastics must be evaluated.
Why Is Composite Material Gaining Popularity in Angle Grinder Manufacturing?
Composite materials are increasingly being used in angle grinder manufacturing, particularly for housings and protective covers.
- Key Properties: Composites offer high strength-to-weight ratios and excellent resistance to corrosion and temperature fluctuations. They can handle temperatures up to 200°C.
- Pros & Cons: The lightweight nature of composites enhances user comfort, while their durability makes them suitable for various applications. However, composites can be more expensive to produce and may require specialized manufacturing processes.
- Impact on Application: Composites are particularly effective in applications where weight and durability are critical. They can be used in both consumer and professional-grade tools.
- Considerations for International Buyers: Compliance with standards like ASTM D790 is essential. Buyers in Europe may find composites increasingly appealing due to their performance characteristics.
Summary Table of Material Selection for Angle Grinder Manufacturing
Material | Typical Use Case for Angle Grinder Manufacturer | Key Advantage | Key Disadvantage/Limitation | Relative Cost (Low/Med/High) |
---|---|---|---|---|
Steel | Housing and internal gears | High durability and strength | Susceptible to corrosion | Medium |
Aluminum | Housings and non-load-bearing components | Lightweight and corrosion-resistant | Lower strength compared to steel | Medium |
Plastic | Handles and covers | Low cost and ease of manufacturing | Lacks durability for heavy-duty use | Low |
Composite | Housings and protective covers | High strength-to-weight ratio | Higher production costs | High |
This strategic material selection guide provides international B2B buyers with insights into the properties and considerations of various materials used in angle grinder manufacturing, aiding in informed purchasing decisions.
In-depth Look: Manufacturing Processes and Quality Assurance for angle grinder manufacturer
What Are the Main Stages in the Manufacturing Process of Angle Grinders?
The manufacturing process for angle grinders involves several critical stages that ensure the final product meets quality and performance standards. Understanding these stages can help international B2B buyers assess potential suppliers effectively.
-
Material Preparation: The initial stage involves sourcing high-quality raw materials, such as high-carbon steel for the housing and aluminum or plastic for the handles. Suppliers often conduct material testing to ensure compliance with specific standards, such as ASTM or ISO certifications, which guarantee the integrity and durability of the materials.
-
Forming: This stage includes processes like stamping, forging, and machining. Stamping is used to create metal parts, while forging shapes components under high pressure to enhance strength. Machining, including CNC (Computer Numerical Control) processes, is crucial for precision parts, ensuring that components fit together seamlessly.
-
Assembly: During assembly, various components such as the motor, gears, and safety features are integrated. This stage is critical, as it dictates the overall performance and safety of the angle grinder. Automated assembly lines are often utilized to enhance efficiency and maintain consistency.
-
Finishing: The finishing stage involves surface treatments like painting or powder coating to enhance aesthetics and corrosion resistance. Additionally, quality checks occur throughout this stage to confirm that the finishing meets international standards.
How Is Quality Assurance Ensured in Angle Grinder Manufacturing?
Quality assurance (QA) is vital for angle grinder manufacturers to ensure reliability and safety. B2B buyers should be familiar with the key quality control measures and international standards that reputable suppliers adhere to.
-
International Standards: Many manufacturers comply with ISO 9001, a widely recognized quality management standard that outlines requirements for a quality management system. Compliance with CE marking standards ensures that the products meet European safety and environmental requirements, which is crucial for buyers in Europe.
-
Industry-Specific Standards: Depending on the application, angle grinders may need to comply with specific standards such as API (American Petroleum Institute) for industrial applications. Understanding these standards helps buyers verify that products are suitable for their intended use.
-
Quality Control Checkpoints:
– Incoming Quality Control (IQC): This initial checkpoint involves inspecting raw materials for defects before they enter the production process.
– In-Process Quality Control (IPQC): Throughout the manufacturing process, regular inspections ensure that each stage meets predefined specifications. This might include dimensional checks and functional tests of key components.
– Final Quality Control (FQC): Once the angle grinders are assembled, FQC is conducted to ensure that the finished products meet all performance and safety criteria before packaging.
What Common Testing Methods Are Used to Ensure Quality?
Testing methods are critical in the quality assurance process for angle grinders. These methods help verify that the products meet safety and performance standards.
-
Electrical Testing: This includes testing the motor for electrical safety, ensuring that it operates within specified voltage and current limits. Insulation resistance tests are also performed to prevent electrical hazards.
-
Performance Testing: Angle grinders undergo various performance tests, such as measuring power output, speed, and vibration levels. This ensures that the tools can perform their intended functions effectively.
-
Durability Testing: Products are subjected to stress tests to evaluate their durability under extreme conditions, simulating long-term use. This may include drop tests and load tests to assess structural integrity.
-
Safety Testing: Compliance with safety standards is verified through tests that check features like guards, switches, and emergency shut-off mechanisms. This is particularly important for B2B buyers in regions with stringent safety regulations.
How Can B2B Buyers Verify Supplier Quality Control Measures?
For international B2B buyers, verifying the quality control measures of suppliers is essential to ensure product reliability and safety. Here are some actionable steps:
-
Conduct Audits: Regular audits of the manufacturing facilities can provide insights into the supplier’s quality control processes. Audits should assess compliance with both international standards and internal QA protocols.
-
Request Quality Reports: Suppliers should provide comprehensive quality reports, including results from IQC, IPQC, and FQC. These reports help buyers understand the quality levels maintained throughout the manufacturing process.
-
Third-Party Inspections: Engaging third-party inspection agencies can offer an unbiased assessment of the supplier’s quality control measures. This is particularly useful for buyers in regions like Africa and South America, where local suppliers may not always have a proven track record.
What Are the QC and Certification Nuances for International B2B Buyers?
Navigating the quality assurance landscape can be complex for international B2B buyers. Understanding the nuances of certifications and quality control can help mitigate risks.
-
Cultural and Regulatory Differences: Different regions have varying regulatory requirements. For example, European buyers may prioritize CE certifications, while buyers in the Middle East may focus on local safety standards. It’s essential for buyers to be aware of these differences to ensure compliance.
-
Supplier Reputation and Reviews: Researching supplier reputation through reviews and testimonials can provide valuable insights. Buyers should consider feedback from other B2B partners regarding the reliability and quality of products.
-
Long-Term Partnerships: Establishing long-term relationships with suppliers can lead to better quality assurance practices. Suppliers who value their reputation are more likely to invest in quality control measures that align with the needs of their partners.
By understanding these manufacturing processes and quality assurance measures, B2B buyers can make informed decisions when sourcing angle grinders from manufacturers across different regions. This knowledge not only enhances procurement strategies but also ensures that the tools acquired meet the highest standards of safety and performance.
Practical Sourcing Guide: A Step-by-Step Checklist for ‘angle grinder manufacturer’
To effectively source an angle grinder manufacturer, especially for international B2B buyers from regions such as Africa, South America, the Middle East, and Europe, it is essential to follow a structured approach. This checklist provides actionable steps to ensure that you find a reliable supplier who meets your technical and business requirements.
Step 1: Define Your Technical Specifications
Before initiating the sourcing process, clarify the specifications of the angle grinders you need. This includes aspects like power ratings, size, weight, and intended applications.
– Consider the market requirements: Different regions may have specific standards or preferences. For instance, heavy-duty grinders may be favored in construction sectors in Africa, while compact models might be preferred in Europe for precision work.
Step 2: Conduct Market Research
Explore the landscape of angle grinder manufacturers globally. Utilize online platforms and trade databases to identify potential suppliers.
– Focus on supplier ratings: Look for manufacturers with strong reputations and reviews, especially from buyers in similar regions or industries. This will help ensure you are considering reliable options.
Step 3: Evaluate Potential Suppliers
Once you have a shortlist, evaluate each supplier thoroughly. Request detailed company profiles, certifications, and customer references.
– Check for industry experience: Suppliers with a proven track record in your industry will likely understand your specific needs better and provide tailored solutions.
Step 4: Verify Supplier Certifications
Confirm that potential suppliers hold relevant certifications and adhere to international standards, such as ISO 9001 for quality management systems.
– Importance of compliance: Compliance with safety and quality standards is critical, especially when sourcing for markets with stringent regulations.
Step 5: Request Samples for Testing
Before making a bulk purchase, request samples of the angle grinders you are considering. Testing these samples can reveal their performance and quality.
– Assess usability and durability: Ensure that the grinders meet your expectations in terms of efficiency and longevity, which are crucial for operational effectiveness.
Step 6: Negotiate Terms and Conditions
Discuss pricing, payment terms, delivery schedules, and warranty conditions with your chosen supplier.
– Aim for clarity: Clear agreements can prevent misunderstandings and ensure that both parties are aligned on expectations, especially regarding after-sales support.
Step 7: Establish a Communication Protocol
Set up a reliable communication channel with your supplier to facilitate ongoing discussions regarding orders, updates, and feedback.
– Importance of transparency: A strong communication framework can help in resolving issues quickly and maintaining a positive relationship, which is vital for long-term partnerships.
By following these steps, international B2B buyers can effectively navigate the sourcing process for angle grinders, ensuring they partner with manufacturers that meet their technical and operational needs. This strategic approach not only enhances procurement efficiency but also contributes to building solid business relationships.
Comprehensive Cost and Pricing Analysis for angle grinder manufacturer Sourcing
What Are the Key Cost Components for Sourcing Angle Grinders?
When sourcing angle grinders, understanding the cost structure is crucial for international B2B buyers. The primary components include:
-
Materials: The choice of materials significantly affects the overall cost. High-quality steel for the housing and premium motor components will lead to higher production costs but can enhance durability and performance, which is essential for long-term use.
-
Labor: Labor costs vary widely by region. In countries with lower labor costs, such as some in Africa and South America, manufacturers may offer competitive pricing. However, this can sometimes come at the expense of quality, so buyers must evaluate the trade-off.
-
Manufacturing Overhead: This includes indirect costs associated with production, such as utilities, factory rent, and equipment maintenance. Manufacturers with advanced technology and efficient processes may have lower overhead costs, allowing them to pass savings onto buyers.
-
Tooling: Initial setup costs for molds and machinery can be significant, especially for customized products. Buyers should inquire about these costs, particularly when considering unique specifications or designs.
-
Quality Control (QC): Effective QC processes ensure product reliability and compliance with international standards. While this adds to the cost, it is an investment in quality that can prevent costly returns and warranty claims.
-
Logistics: Shipping and handling costs can vary based on the Incoterms agreed upon. Buyers should understand the implications of terms like FOB (Free On Board) or CIF (Cost, Insurance, and Freight) on total expenses.
-
Margin: Manufacturers will typically include a profit margin in their pricing. This margin can vary based on competition, brand reputation, and market demand.
What Influences the Pricing of Angle Grinders?
Several factors can influence the pricing of angle grinders, and understanding these can empower buyers to negotiate better deals:
-
Volume and Minimum Order Quantity (MOQ): Larger orders often attract discounts. Buyers should assess their needs carefully and consider bulk purchasing to leverage better pricing.
-
Specifications and Customization: Custom features or specifications may increase costs. Buyers should clearly define their requirements to avoid unexpected charges.
-
Material Quality and Certifications: Products that meet international quality standards (e.g., ISO certifications) might be priced higher but offer better reliability and performance. Buyers should weigh the cost against the potential benefits of higher-quality products.
-
Supplier Factors: The reliability and reputation of the supplier can affect pricing. Established suppliers may charge more but often provide better service and quality assurance.
-
Incoterms: The agreed-upon Incoterms can significantly influence the total cost. Buyers must understand these terms to avoid hidden costs related to transportation and insurance.
What Tips Can Help Buyers Negotiate Better Prices for Angle Grinders?
To maximize cost-efficiency, international B2B buyers should consider the following strategies:
-
Leverage Total Cost of Ownership (TCO): Evaluate not just the purchase price but the long-term costs associated with maintenance, operation, and potential downtime. A higher initial cost can sometimes result in lower TCO if the product is more durable and efficient.
-
Conduct Market Research: Understanding market rates and competitor pricing can provide leverage during negotiations. Buyers should gather quotes from multiple suppliers to identify reasonable price ranges.
-
Build Relationships with Suppliers: Establishing a rapport with manufacturers can lead to better terms, including discounts and priority service. Long-term partnerships often yield significant benefits.
-
Be Aware of Pricing Nuances for Different Regions: Buyers from Africa, South America, the Middle East, and Europe should recognize that pricing can vary significantly based on local market conditions, tariffs, and trade agreements.
Disclaimer on Indicative Prices
Prices for angle grinders can fluctuate based on numerous factors, including market demand, material costs, and geopolitical influences. Buyers should use indicative prices as a starting point for negotiations and conduct thorough due diligence before making purchasing decisions.
Alternatives Analysis: Comparing angle grinder manufacturer With Other Solutions
Understanding Alternatives in the Angle Grinder Market
When evaluating the best tools for cutting, grinding, and polishing, international B2B buyers must consider various options beyond traditional angle grinders. This section explores viable alternatives to angle grinder manufacturers, focusing on performance, cost, ease of implementation, maintenance, and best use cases. By understanding these alternatives, businesses can make informed decisions that align with their operational needs and budget constraints.
Comparison Table of Angle Grinder Manufacturer and Alternatives
Comparison Aspect | Angle Grinder Manufacturer | Alternative 1: Bench Grinder | Alternative 2: Die Grinder |
---|---|---|---|
Performance | High versatility and power for various materials | Effective for large, flat surfaces | Excellent for precision work in tight spaces |
Cost | Moderate to high, depending on brand and features | Generally lower cost than angle grinders | Typically low to moderate cost |
Ease of Implementation | Requires operator skill and safety precautions | Easier to set up and use for beginners | Requires training for optimal use |
Maintenance | Regular maintenance needed for optimal performance | Low maintenance; infrequent checks | Moderate; depends on usage frequency |
Best Use Case | Ideal for construction and heavy-duty tasks | Best for smoothing and shaping metal | Perfect for intricate detailing and fine work |
What Are the Benefits and Drawbacks of Using a Bench Grinder?
A bench grinder is a stationary tool that utilizes two grinding wheels to perform tasks such as sharpening tools and shaping metal. Its primary advantage lies in its stability and ease of use, making it suitable for beginners or those who require consistent results on larger, flat surfaces. However, it lacks the versatility of angle grinders and is limited in handling complex tasks or tight spaces. This makes it a better choice for workshops focusing on tool maintenance rather than extensive fabrication work.
How Does a Die Grinder Compare as an Alternative?
The die grinder is a handheld tool designed for precision work, often used in automotive and metalworking applications. It excels at reaching confined areas and performing intricate tasks such as engraving or polishing. The major benefit of die grinders is their ability to achieve detailed finishes in tight spots, which angle grinders may struggle with. However, die grinders typically have lower power and may require more time for larger jobs, making them less suitable for heavy-duty applications.
Conclusion: How to Choose the Right Grinding Solution for Your Business Needs
Selecting the right grinding tool depends on the specific requirements of your projects. If your operations demand versatility and the capability to handle various materials, an angle grinder manufacturer might be your best bet. However, for tasks focused on precision and detail, consider investing in die grinders or bench grinders. Assessing factors like performance, cost, and maintenance will guide B2B buyers in making decisions that not only fit their budget but also enhance productivity and efficiency in their operations.
Essential Technical Properties and Trade Terminology for angle grinder manufacturer
What Are the Essential Technical Properties of Angle Grinders?
When evaluating angle grinders for purchase, international B2B buyers should focus on several critical technical properties. These specifications not only determine the performance and durability of the tool but also influence the overall cost and suitability for various applications.
1. What Material Grade is Ideal for Angle Grinders?
The material grade of the angle grinder is crucial as it affects durability and performance. Typically, high-quality angle grinders are made from high-grade steel or aluminum alloys. High-grade materials ensure resistance to wear and tear, which is particularly important in heavy-duty applications. For buyers in regions like Africa and South America, where environmental conditions can vary, selecting grinders with corrosion-resistant coatings is advisable.
2. Why is Motor Power Rating Important?
Motor power, usually measured in watts, directly correlates with the grinder’s cutting and grinding capability. A higher wattage means more power and efficiency, allowing the tool to handle tougher materials. For instance, a power rating of 750-1500 watts is common for professional-grade grinders. Buyers should consider their specific needs; for heavy industrial use, investing in grinders with higher wattage will yield better results.
3. How Do RPM and Speed Settings Affect Performance?
Revolutions per minute (RPM) indicate the speed at which the grinding wheel rotates. Standard angle grinders typically range from 5,000 to 12,000 RPM. Adjustable speed settings are advantageous as they allow operators to match the tool’s speed to the material being worked on, enhancing precision and reducing the risk of damage. This feature is particularly beneficial for buyers looking to use grinders across various applications, from metalworking to masonry.
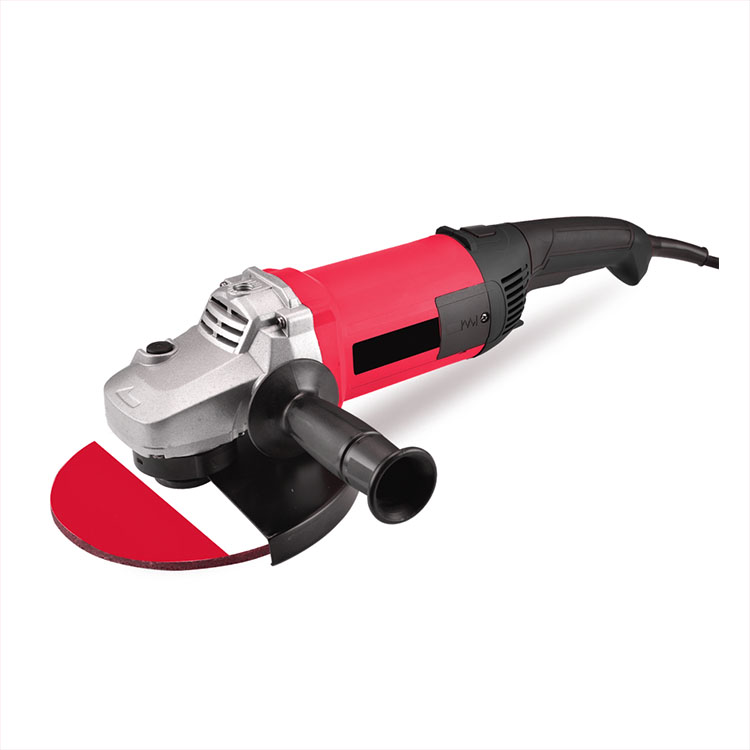
A stock image related to angle grinder manufacturer.
4. What is the Significance of Tolerance Levels?
Tolerance levels refer to the permissible limits of variation in the dimensions of the grinder components. Tight tolerances ensure that the grinder operates smoothly and effectively, reducing vibrations and increasing user safety. In industries where precision is paramount, such as aerospace or automotive, opting for grinders with precise manufacturing tolerances is essential.
5. How Does Weight Influence Usability?
The weight of the angle grinder affects its usability and maneuverability. Lightweight models (around 2-3 kg) are easier to handle for prolonged periods, reducing operator fatigue. However, heavier models may offer better stability during operation. Buyers should consider the intended use and frequency of operation when selecting the appropriate weight for their needs.
What Are Common Trade Terms Used in the Angle Grinder Industry?
Understanding industry-specific terminology is vital for effective communication and negotiation in B2B transactions. Here are several key terms frequently encountered in the angle grinder market:
1. What Does OEM Mean in Angle Grinder Manufacturing?
OEM stands for Original Equipment Manufacturer. It refers to companies that produce parts or equipment that may be marketed by another manufacturer. For B2B buyers, working with OEMs can provide assurance of quality and compatibility with existing systems or tools.
2. How Does MOQ Affect Purchasing Decisions?
MOQ, or Minimum Order Quantity, is the smallest number of units that a supplier is willing to sell. Understanding MOQ is crucial for buyers, especially those in smaller markets or startups. Negotiating lower MOQs can lead to significant cost savings and better inventory management.
3. What is an RFQ and Why is it Important?
An RFQ, or Request for Quotation, is a document that a buyer sends to suppliers to obtain price quotes for specific products. For B2B buyers, issuing an RFQ is an essential step in sourcing angle grinders as it allows for comparison of prices, specifications, and terms across different manufacturers.
4. How Do Incoterms Influence Shipping and Costs?
Incoterms, or International Commercial Terms, define the responsibilities of buyers and sellers in international transactions. Understanding these terms helps buyers clarify shipping costs, risks, and responsibilities, ensuring smoother transactions and reducing potential disputes.
5. What is the Role of Certification Standards?
Certification standards indicate that a product meets specific safety and quality benchmarks. For angle grinders, compliance with international standards (such as ISO or CE) can be a deciding factor for B2B buyers, as it assures product reliability and safety in use.
By familiarizing themselves with these essential technical properties and industry terminology, B2B buyers can make informed purchasing decisions that align with their operational needs and standards.
Navigating Market Dynamics and Sourcing Trends in the angle grinder manufacturer Sector
What Are the Current Market Dynamics and Key Trends in the Angle Grinder Manufacturing Sector?
The global angle grinder market is experiencing significant growth driven by various factors, including increasing demand from construction and metalworking industries. In Africa and South America, the construction boom has been a key driver, with rising investments in infrastructure projects. In the Middle East, the focus on urban development and energy sectors has further propelled demand for angle grinders. Meanwhile, European markets are witnessing a shift towards high-performance, energy-efficient tools, reflecting a growing preference for advanced technology.
Emerging B2B technologies, such as the integration of IoT in power tools, are revolutionizing the angle grinder sector. Smart angle grinders equipped with sensors allow for real-time monitoring of usage and performance, enhancing operational efficiency. This trend is particularly appealing to international buyers seeking to optimize productivity and reduce downtime in their operations.
Moreover, the sourcing landscape is evolving, with manufacturers increasingly adopting direct-to-consumer models and leveraging e-commerce platforms for wider distribution. This shift enables buyers from diverse regions, including Indonesia and Argentina, to access a broader range of products and competitive pricing. Understanding these dynamics is crucial for B2B buyers to align their procurement strategies with market trends.
How Does Sustainability Influence Sourcing in the Angle Grinder Manufacturing Sector?
The angle grinder manufacturing sector is increasingly acknowledging the importance of sustainability and ethical sourcing. Environmental concerns regarding the production processes and product lifecycle are driving manufacturers to adopt greener practices. This includes reducing waste, utilizing eco-friendly materials, and implementing energy-efficient manufacturing processes.
For B2B buyers, sourcing products from manufacturers with established sustainability practices is not just about compliance; it also reflects a commitment to corporate social responsibility. Certifications such as ISO 14001 for environmental management systems and the EU Ecolabel for environmentally friendly products are becoming essential criteria in the procurement process.
Additionally, the use of recycled materials in manufacturing angle grinders is gaining traction. Buyers are encouraged to seek suppliers that prioritize the use of sustainable materials, which not only reduces environmental impact but can also enhance brand reputation. Emphasizing sustainability in sourcing decisions can lead to long-term benefits, including cost savings and improved relationships with environmentally conscious consumers.
How Has the Angle Grinder Manufacturing Sector Evolved Over Time?
The angle grinder manufacturing sector has undergone significant transformations since its inception in the early 20th century. Initially designed for metalworking, angle grinders have evolved to serve a multitude of applications across various industries, including construction, automotive, and woodworking. Advances in technology have led to the development of lighter, more powerful, and versatile tools that cater to the diverse needs of professional users.
In recent decades, the integration of electronic controls and battery technology has revolutionized the sector, enabling cordless models that enhance mobility and ease of use. As a result, B2B buyers now have access to a wide range of products tailored to specific applications, making it essential to stay informed about technological advancements and market shifts to make informed purchasing decisions.
In conclusion, navigating the angle grinder market requires an understanding of the current dynamics, a commitment to sustainability, and a recognition of the historical evolution of the sector. By aligning sourcing strategies with these insights, international B2B buyers can enhance their competitiveness in a rapidly changing landscape.
Frequently Asked Questions (FAQs) for B2B Buyers of angle grinder manufacturer
-
How can I ensure the quality of angle grinders from a manufacturer?
To ensure the quality of angle grinders, start by requesting product samples and conducting a thorough inspection. Look for certifications such as ISO 9001, which indicates adherence to quality management standards. Additionally, ask for details about the manufacturer’s quality assurance processes, including material sourcing, production methods, and testing procedures. Engaging in a third-party quality inspection service can also provide an unbiased evaluation before placing a large order. -
What are the typical payment terms when sourcing angle grinders internationally?
Payment terms can vary by manufacturer but typically include options such as advance payment, letter of credit, or payment upon delivery. It’s common for manufacturers to require a deposit (e.g., 30% upfront) with the balance due before shipment. Ensure to negotiate terms that protect your investment while being reasonable for the manufacturer. Familiarize yourself with international payment methods like PayPal, wire transfers, or escrow services to mitigate risks. -
What is the minimum order quantity (MOQ) for angle grinders from manufacturers?
Minimum order quantities (MOQs) for angle grinders can vary significantly depending on the manufacturer and the type of grinder. Generally, MOQs range from 100 to 1,000 units. Discuss your specific needs with potential suppliers, as some may offer flexibility in MOQs for new customers or bulk orders. Consider the implications of MOQ on your inventory management and cash flow when deciding on a supplier. -
How can I vet potential angle grinder manufacturers for reliability?
To vet potential manufacturers, conduct background checks by reviewing their business licenses, certifications, and industry reputation. Request references from previous clients and look for reviews or testimonials online. Visiting the factory, if possible, allows for firsthand assessment of their operations. Additionally, consider using platforms like Alibaba or Global Sources, which often provide verification services for suppliers. -
What customization options are available when sourcing angle grinders?
Many angle grinder manufacturers offer customization options, including modifications to size, power output, and additional features such as variable speed settings or safety guards. Discuss your specific requirements with potential suppliers to understand the extent of customization they can provide. Be prepared to provide detailed specifications and possibly pay additional costs for custom tooling or design changes. -
How do I handle logistics and shipping for international orders of angle grinders?
Handling logistics involves coordinating with freight forwarders to determine the most efficient shipping method, whether by sea, air, or land. Discuss shipping options with your supplier to understand lead times and costs. Ensure that you account for customs duties, taxes, and potential delays in your logistics planning. Using a reliable logistics partner can help streamline the process and minimize shipping-related issues. -
What are the common certifications for angle grinders, and why are they important?
Common certifications for angle grinders include CE, UL, and CSA, which indicate compliance with safety and performance standards. These certifications are crucial as they ensure that the products meet international safety regulations, reducing the risk of accidents or product failures. When sourcing, always verify that the manufacturer can provide the necessary certifications for the specific markets where you intend to sell. -
What after-sales support should I expect from angle grinder manufacturers?
After-sales support can vary significantly between manufacturers. Look for suppliers that offer warranties on their products, typically ranging from one to three years. Additionally, inquire about technical support, spare parts availability, and return policies for defective units. A manufacturer with strong after-sales support can enhance your business’s reputation by ensuring that your customers receive assistance when needed.
Important Disclaimer & Terms of Use
⚠️ Important Disclaimer
The information provided in this guide, including content regarding manufacturers, technical specifications, and market analysis, is for informational and educational purposes only. It does not constitute professional procurement advice, financial advice, or legal advice.
While we have made every effort to ensure the accuracy and timeliness of the information, we are not responsible for any errors, omissions, or outdated information. Market conditions, company details, and technical standards are subject to change.
B2B buyers must conduct their own independent and thorough due diligence before making any purchasing decisions. This includes contacting suppliers directly, verifying certifications, requesting samples, and seeking professional consultation. The risk of relying on any information in this guide is borne solely by the reader.
Strategic Sourcing Conclusion and Outlook for angle grinder manufacturer
What Are the Key Takeaways for B2B Buyers in Strategic Sourcing of Angle Grinders?
In the ever-evolving landscape of industrial manufacturing, strategic sourcing stands as a cornerstone for B2B buyers, especially in diverse markets such as Africa, South America, the Middle East, and Europe. Understanding supplier capabilities, quality control processes, and logistics can significantly enhance procurement efficiency. Leveraging local partnerships can not only reduce costs but also improve supply chain resilience, ensuring timely delivery of high-quality angle grinders tailored to specific regional needs.
How Can International Buyers Benefit from Strategic Sourcing?
Investing time in building relationships with reputable angle grinder manufacturers can lead to enhanced product innovation and customization, aligning with the unique demands of each market. Furthermore, buyers should prioritize manufacturers with sustainable practices, as global trends increasingly favor eco-friendly solutions. This not only fulfills corporate social responsibility goals but can also lead to long-term cost savings and brand loyalty.
What’s Next for B2B Buyers in the Angle Grinder Market?
As you navigate the complexities of sourcing angle grinders, remember that the future lies in strategic partnerships and adaptability. Embrace the opportunities that arise from collaborating with manufacturers who understand your market. Take the proactive step today to assess your sourcing strategies, ensuring they align with global best practices and market trends. By doing so, you position your business for sustained growth and competitive advantage in the global marketplace.