Discover Top Benefits: Choosing a Limit Switch Manufacturer (2025)
Introduction: Navigating the Global Market for limit switch manufacturer
Navigating the global market for limit switch manufacturers can be daunting, especially for B2B buyers in regions like Africa, South America, the Middle East, and Europe. With a plethora of options available, sourcing high-quality limit switches that meet specific operational needs requires careful consideration and strategic planning. This comprehensive guide aims to demystify the complexities associated with purchasing limit switches by exploring various types, applications, and essential factors to consider when vetting suppliers.
From understanding the different kinds of limit switches—such as electromechanical, magnetic, and electronic—to evaluating their applications across industries like manufacturing, automation, and safety, this guide provides actionable insights tailored for international buyers. Additionally, it addresses critical aspects such as supplier reliability, quality certifications, pricing structures, and negotiation strategies.
By equipping B2B buyers with the knowledge needed to make informed purchasing decisions, this guide empowers you to navigate the intricate landscape of limit switch manufacturers confidently. Whether you’re in Turkey seeking advanced automation solutions or in Germany looking for reliable safety devices, our insights will help you streamline your sourcing process and enhance operational efficiency. Embrace the opportunity to optimize your supply chain and ensure that your business remains competitive in the global marketplace.
Understanding limit switch manufacturer Types and Variations
Type Name | Key Distinguishing Features | Primary B2B Applications | Brief Pros & Cons for Buyers |
---|---|---|---|
Mechanical Limit Switch | Uses physical movement to activate; robust design | Manufacturing, automotive, packaging | Pros: Durable, cost-effective. Cons: Limited precision. |
Electronic Limit Switch | Utilizes sensors for activation; offers high accuracy | Robotics, automation, CNC machines | Pros: High precision, adjustable settings. Cons: Higher cost, requires power supply. |
Proximity Limit Switch | Senses object proximity without contact; versatile | Material handling, conveyors, elevators | Pros: No wear and tear, compact design. Cons: Limited range, potential interference from nearby objects. |
Adjustable Limit Switch | Allows for setting custom activation points | Custom machinery, production lines | Pros: Flexibility, tailored solutions. Cons: May require technical expertise to adjust. |
Safety Limit Switch | Designed to prevent accidents; often features redundancy | Heavy machinery, construction, energy | Pros: Enhanced safety, compliance with regulations. Cons: More complex installation and maintenance. |
What Are the Characteristics of Mechanical Limit Switches?
Mechanical limit switches are characterized by their reliance on physical movement to activate. Typically featuring a simple actuator, they are known for their robust design, making them suitable for harsh industrial environments. These switches are widely used in manufacturing, automotive, and packaging applications where durability is essential. When purchasing, buyers should consider their operational environment, as mechanical switches might be less precise compared to electronic options, but they often come at a lower cost.
How Do Electronic Limit Switches Compare to Other Types?
Electronic limit switches utilize advanced sensor technology, providing high accuracy and the ability to adjust settings as needed. These switches are ideal for applications in robotics, automation, and CNC machines where precision is critical. B2B buyers should evaluate their need for accuracy against the higher cost and requirement for a power supply. While they deliver superior performance, the complexity of installation and potential for electronic interference are important considerations.
What Are the Benefits of Proximity Limit Switches?
Proximity limit switches operate without physical contact, sensing the presence of an object through magnetic or capacitive fields. This feature makes them highly versatile, suitable for material handling, conveyors, and elevator systems. Their design minimizes wear and tear, which can lead to longer operational life. However, buyers should be mindful of their limited sensing range and the potential for interference from nearby objects, which can affect performance.
Why Choose Adjustable Limit Switches?
Adjustable limit switches allow users to set custom activation points, making them particularly useful in custom machinery and production lines. Their flexibility can lead to tailored solutions that meet specific operational needs. However, buyers should be prepared for the technical expertise required for adjustments, which can complicate installation and maintenance. Evaluating the balance between flexibility and ease of use is crucial for B2B buyers.
What Makes Safety Limit Switches Essential in B2B Operations?
Safety limit switches are designed to prevent accidents and often incorporate redundancy features to enhance operational safety. They are commonly used in heavy machinery, construction, and energy sectors where compliance with safety regulations is paramount. While these switches provide significant safety benefits, buyers must consider the complexities involved in installation and ongoing maintenance. Investing in safety limit switches can ultimately protect employees and minimize liability, making them a worthwhile consideration for B2B buyers.
Related Video: A2B Switch | Limit Switch | Over-hoist Switch | For All Cranes | Klug Avalon
Key Industrial Applications of limit switch manufacturer
Industry/Sector | Specific Application of Limit Switch Manufacturer | Value/Benefit for the Business | Key Sourcing Considerations for this Application |
---|---|---|---|
Manufacturing | Automated machinery control | Enhances operational efficiency and safety | Ensure compatibility with existing systems and durability |
Oil & Gas | Safety interlocks for equipment | Mitigates risk of accidents and equipment damage | Look for high-temperature and pressure ratings |
Automotive | Position sensing in assembly lines | Improves accuracy in manufacturing processes | Require fast response times and robust construction |
Food & Beverage | Product flow control | Ensures compliance with safety standards | Need for materials that meet hygiene regulations |
Construction | Crane and hoist operations | Increases safety in heavy lifting operations | Consider environmental resilience and ease of installation |
How are Limit Switches Used in Manufacturing Automation?
In the manufacturing sector, limit switches play a pivotal role in automating machinery control. They act as sensors that detect the position of moving parts, ensuring that machines operate within safe parameters. By implementing limit switches, manufacturers can significantly enhance operational efficiency and safety, reducing the likelihood of equipment malfunctions. International buyers should focus on sourcing limit switches that are compatible with their existing systems and are durable enough to withstand harsh industrial environments.
What Role do Limit Switches Play in Oil & Gas Safety?
In the oil and gas industry, limit switches are crucial for implementing safety interlocks on various equipment. These devices help prevent accidents by ensuring that machinery does not operate outside of designated safe zones. By incorporating limit switches, companies can mitigate risks associated with equipment failure, thereby protecting both personnel and assets. Buyers in this sector should prioritize sourcing limit switches that can withstand extreme temperatures and pressures, as these conditions are common in oil and gas applications.
How are Limit Switches Essential in Automotive Manufacturing?
Limit switches are extensively used in the automotive industry for position sensing along assembly lines. They provide precise feedback on the location of components, which is essential for maintaining accuracy throughout the manufacturing process. This technology not only improves production efficiency but also reduces waste and errors. Buyers should look for limit switches that offer fast response times and robust construction to ensure reliability in high-paced automotive environments.
What Benefits do Limit Switches Offer in Food & Beverage Processing?
In the food and beverage sector, limit switches are vital for controlling product flow and ensuring that processes comply with safety standards. These switches help manage the movement of ingredients and finished products, thereby maintaining quality and efficiency. When sourcing limit switches, buyers must ensure that the materials used meet hygiene regulations, as cleanliness is paramount in food processing environments.
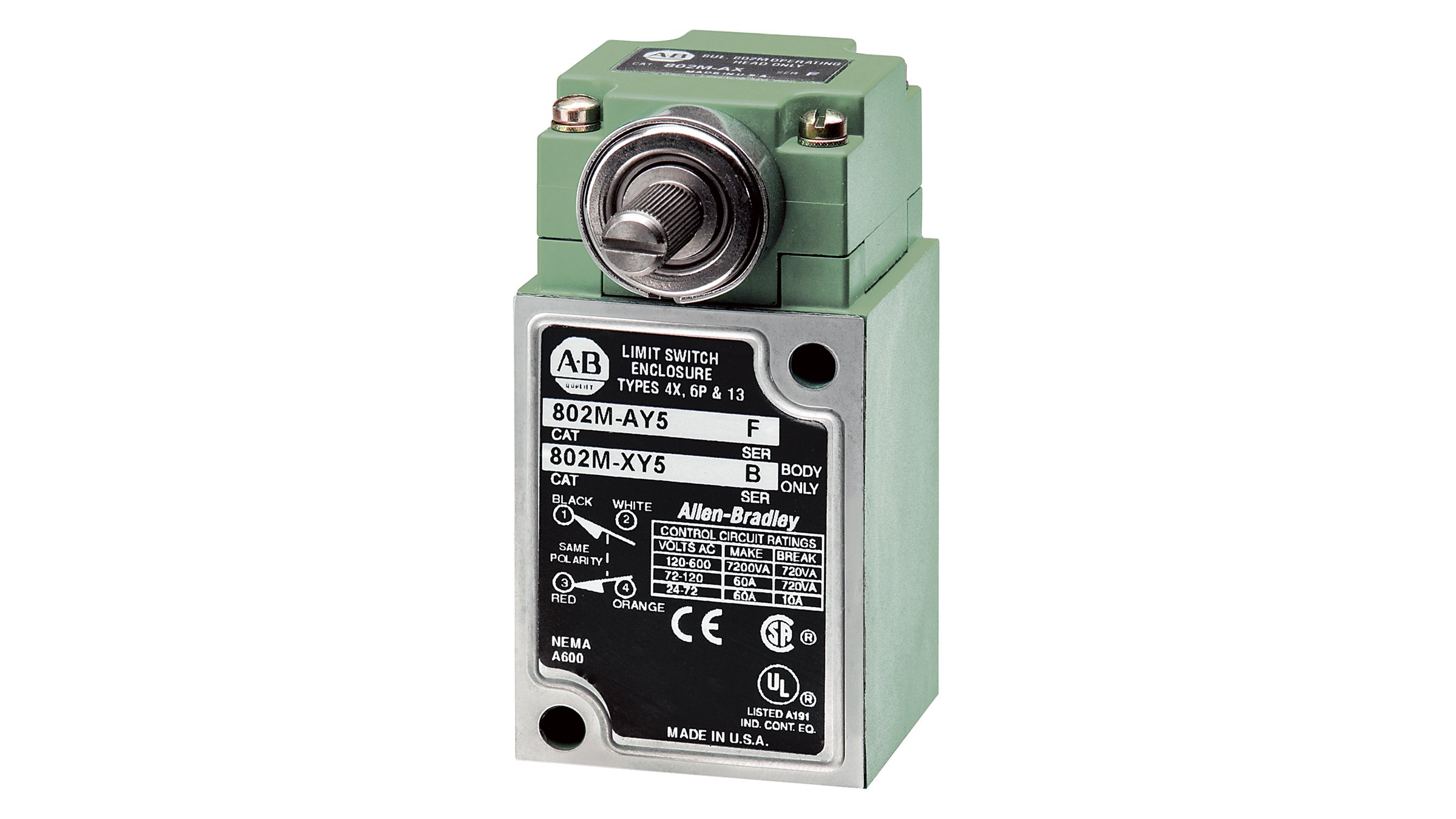
A stock image related to limit switch manufacturer.
Why are Limit Switches Important in Construction Equipment?
In construction, limit switches are extensively utilized in crane and hoist operations to enhance safety during heavy lifting tasks. They provide critical feedback on the position and movement of loads, preventing accidents that could result from overloading or improper positioning. International buyers should consider sourcing limit switches that are resilient to environmental factors and easy to install, as construction sites often present challenging conditions.
Related Video: Limit Switch || Working and Connection of Limit Switch
3 Common User Pain Points for ‘limit switch manufacturer’ & Their Solutions
Scenario 1: Navigating Compatibility Issues with Limit Switches
The Problem:
B2B buyers often face significant challenges when integrating limit switches into existing machinery or systems. For instance, a manufacturing plant in South America may find that the limit switches they ordered from a European supplier are not compatible with their existing equipment. This can lead to delays in production, increased costs due to returns or modifications, and frustration among engineers who are tasked with troubleshooting the issues. Buyers may also struggle with understanding the specifications required for their specific applications, leading to miscommunication with suppliers.
The Solution:
To mitigate compatibility issues, it is crucial for buyers to engage in thorough pre-purchase research and specification validation. First, create a detailed list of requirements that includes voltage ratings, physical dimensions, environmental conditions (like humidity and temperature), and connection types. Engaging with the manufacturer early in the process allows for discussions about compatibility with existing systems.
Consider utilizing sample units or prototypes to conduct tests before making a large order. This approach provides a practical understanding of how the switches perform in real-world applications. Additionally, ensuring that suppliers provide clear documentation regarding technical specifications and compatibility can prevent future issues. Establishing a good relationship with the manufacturer can also lead to better support and customization options tailored to your needs.
Scenario 2: Dealing with Quality Assurance and Reliability Concerns
The Problem:
Quality assurance is a critical concern for B2B buyers in industries like automotive or industrial automation. For example, a limit switch that fails unexpectedly can cause costly downtime, safety hazards, and damage to machinery. Buyers may find that certain manufacturers do not adhere to stringent quality control measures, resulting in inconsistencies in product reliability. This can be especially problematic for companies in Africa or the Middle East, where sourcing high-quality components can be a challenge.
The Solution:
To address quality assurance concerns, buyers should prioritize sourcing from manufacturers with a proven track record of reliability and quality control. Look for certifications such as ISO 9001 or industry-specific standards that demonstrate a commitment to quality. Conducting audits or site visits to the manufacturing facility can also provide insights into their production processes.
Furthermore, consider requesting a comprehensive warranty and after-sales support, as this can indicate the manufacturer’s confidence in their product quality. Setting up a robust testing protocol upon receipt of the limit switches can help identify any potential issues early on. This proactive approach will not only ensure that the products meet your quality standards but also foster a long-term relationship with reliable suppliers.
Scenario 3: Understanding Technical Support and After-Sales Service
The Problem:
B2B buyers often encounter difficulties when it comes to technical support and after-sales service for limit switches. For instance, a company in Turkey might require immediate assistance with installation or troubleshooting but finds that their supplier does not provide adequate support. This can lead to significant delays in project timelines and increased frustration among staff who are not able to resolve issues independently.
The Solution:
To ensure robust technical support, buyers should prioritize manufacturers that offer comprehensive after-sales service, including installation guidance, troubleshooting assistance, and accessible customer service. Before finalizing a purchase, inquire about the availability of technical resources, such as manuals, installation videos, and live support options.
Additionally, consider suppliers that provide training sessions for your staff, either in-person or through webinars. This investment in education can empower your team to handle basic issues independently, reducing reliance on external support. Establishing a clear line of communication with your supplier will enable quick resolutions to any problems that arise, ensuring that your operations remain efficient and uninterrupted. By selecting manufacturers committed to excellent customer service, buyers can significantly improve their overall experience and operational performance.
Strategic Material Selection Guide for limit switch manufacturer
When selecting materials for limit switches, international B2B buyers must consider various factors that affect performance, durability, and cost. This section analyzes four common materials used in limit switch manufacturing: plastic, stainless steel, aluminum, and brass. Each material has distinct properties, advantages, disadvantages, and implications for specific applications, particularly relevant for buyers from Africa, South America, the Middle East, and Europe.
What Are the Key Properties of Plastic in Limit Switch Manufacturing?
Plastic is often used in limit switches due to its lightweight and versatile nature. Key properties include good electrical insulation, resistance to corrosion, and a temperature rating typically between -40°C to 85°C. However, its mechanical strength can be lower than metals, making it less suitable for high-stress applications.
Pros and Cons:
– Pros: Lightweight, cost-effective, good insulation properties.
– Cons: Lower durability compared to metals, limited temperature range, and potential for wear over time.
Impact on Application:
Plastic limit switches are ideal for environments where moisture and corrosion are concerns but may not withstand high mechanical stress or extreme temperatures.
Considerations for International Buyers:
Buyers should ensure compliance with local regulations regarding plastic materials, particularly in regions with stringent environmental laws. Standards such as ASTM or DIN may apply.
How Does Stainless Steel Enhance Limit Switch Performance?
Stainless steel is renowned for its excellent corrosion resistance and durability, making it suitable for harsh environments. It typically offers a temperature rating of up to 300°C and can withstand high-pressure applications.
Pros and Cons:
– Pros: High durability, excellent corrosion resistance, and suitable for high-temperature applications.
– Cons: Higher cost compared to plastic and aluminum, heavier, and may require specialized machining processes.
Impact on Application:
Stainless steel limit switches are ideal for industrial applications, especially in food processing or chemical industries where hygiene and corrosion resistance are critical.
Considerations for International Buyers:
Buyers should verify that the stainless steel used meets international standards such as JIS or ASTM for quality assurance. Buyers in regions like Germany may also look for certifications related to food safety.
What Advantages Does Aluminum Offer in Limit Switches?
Aluminum is a popular choice for limit switches due to its lightweight nature and good strength-to-weight ratio. It typically withstands temperatures up to 150°C and offers decent corrosion resistance, especially when anodized.
Pros and Cons:
– Pros: Lightweight, good thermal conductivity, and relatively low cost.
– Cons: Less corrosion-resistant than stainless steel, may not be suitable for extreme environments, and can be prone to scratching.
Impact on Application:
Aluminum limit switches are suitable for applications requiring lightweight components, such as in automation systems or portable machinery.
Considerations for International Buyers:
Buyers should ensure that aluminum components comply with local manufacturing standards and consider the anodizing process for enhanced corrosion resistance, especially in humid climates.
Why Choose Brass for Limit Switch Manufacturing?
Brass is often used in limit switches for its excellent electrical conductivity and resistance to corrosion. It typically has a temperature rating of around 120°C and is commonly used in low-pressure applications.
Pros and Cons:
– Pros: Good electrical conductivity, corrosion-resistant, and aesthetically pleasing.
– Cons: Higher cost than aluminum and plastic, lower strength compared to stainless steel, and not suitable for high-temperature applications.
Impact on Application:
Brass limit switches are ideal for electrical applications where conductivity is essential, such as in control systems for machinery.
Considerations for International Buyers:
Buyers should check for compliance with electrical standards and ensure that brass components meet local regulations regarding metal usage, especially in Europe where compliance with REACH and RoHS directives may be necessary.
Summary Table of Material Selection for Limit Switch Manufacturers
Material | Typical Use Case for Limit Switch Manufacturer | Key Advantage | Key Disadvantage/Limitation | Relative Cost (Low/Med/High) |
---|---|---|---|---|
Plastic | Moisture-sensitive environments | Lightweight and cost-effective | Lower durability and temperature range | Low |
Stainless Steel | Industrial applications, food processing | High durability and corrosion resistance | Higher cost and heavier | High |
Aluminum | Automation systems, portable machinery | Lightweight and good thermal conductivity | Less corrosion-resistant | Medium |
Brass | Electrical applications | Excellent conductivity and corrosion resistance | Higher cost and lower strength | Medium |
This guide provides a comprehensive overview of material selection for limit switch manufacturers, enabling international B2B buyers to make informed decisions based on their specific needs and regional standards.
In-depth Look: Manufacturing Processes and Quality Assurance for limit switch manufacturer
What Are the Key Manufacturing Processes for Limit Switches?
Manufacturing limit switches involves several critical stages that ensure the final product meets specific operational requirements and quality standards. Understanding these processes can help international B2B buyers make informed decisions when selecting a supplier.
Material Preparation: What Materials Are Used in Limit Switch Manufacturing?
The manufacturing process begins with material preparation, which typically involves selecting high-quality components such as metals (like stainless steel or brass) and plastics. The choice of materials is crucial, as they directly affect the durability and performance of the limit switches.
Suppliers often employ advanced techniques such as laser cutting and CNC machining to ensure precision in shaping the materials. Ensuring that suppliers use materials compliant with international standards (like RoHS) can also enhance the reliability of the limit switches.
How Are Limit Switches Formed During Manufacturing?
After the materials are prepared, the next stage is forming. This includes processes such as stamping, molding, and extrusion. Stamping is commonly used to create metal parts, while injection molding is employed for plastic components. These techniques allow for high-volume production with consistent quality.
In this phase, specialized machinery is utilized to achieve precise dimensions, which is essential for the functionality of limit switches. B2B buyers should inquire about the machinery used and its maintenance history to understand the potential variability in product quality.
What Is the Assembly Process for Limit Switches?
Once individual components are formed, the assembly process begins. This involves integrating various parts, including the actuator, housing, and electrical contacts. Automated assembly lines are often used to enhance efficiency and reduce human error.
Quality control during assembly is paramount. B2B buyers should look for suppliers that implement standardized assembly procedures and documentation to ensure traceability. This can include using assembly jigs and fixtures to maintain consistency across production runs.
How Do Finishing Techniques Enhance Limit Switch Quality?
The finishing stage includes processes such as coating, painting, and surface treatment. These techniques not only improve the aesthetic appeal of the limit switches but also enhance their resistance to environmental factors such as moisture, dust, and corrosion.
For instance, applying a powder coating can provide a durable finish that extends the product’s lifespan. Buyers should confirm that suppliers adhere to finishing standards relevant to their industry, ensuring that the limit switches can withstand specific operational conditions.
What Quality Assurance Practices Are Essential for Limit Switch Manufacturers?
Quality assurance is a critical aspect of the manufacturing process for limit switches. It ensures that products meet specific international and industry standards, which is particularly important for B2B buyers in diverse markets.
Which International Standards Should Limit Switch Manufacturers Comply With?
International standards such as ISO 9001 play a significant role in quality management systems. ISO 9001 certification indicates that a manufacturer has established a quality management system that consistently meets customer and regulatory requirements.
Additionally, industry-specific certifications like CE marking in Europe or API standards for certain applications are essential. Buyers should verify that their suppliers hold these certifications, as they often reflect the manufacturer’s commitment to quality and safety.
What Are the Key Quality Control Checkpoints in Limit Switch Manufacturing?
Quality control (QC) should be integrated at various checkpoints throughout the manufacturing process:
- Incoming Quality Control (IQC): This involves inspecting raw materials upon arrival to ensure they meet specified standards.
- In-Process Quality Control (IPQC): During the manufacturing process, periodic checks are conducted to identify any deviations from quality standards.
- Final Quality Control (FQC): Before shipping, the finished products undergo rigorous testing to ensure they function correctly and meet all specifications.
B2B buyers should request detailed QC reports and procedures from suppliers to gain insight into their quality management practices.
What Common Testing Methods Are Used for Limit Switches?
Testing methods for limit switches can vary based on their intended application but generally include:
- Functional Testing: Verifying that the switch operates correctly under various conditions.
- Environmental Testing: Assessing performance under extreme temperatures, humidity, and vibration.
- Electrical Testing: Ensuring that electrical components meet safety and operational standards.
Understanding these testing methods helps B2B buyers evaluate the reliability of the products they are purchasing.
How Can International Buyers Verify Supplier Quality Control?
For B2B buyers, especially those from Africa, South America, the Middle East, and Europe, verifying a supplier’s quality control is crucial. Here are several ways to do this effectively:
What Are the Best Practices for Conducting Supplier Audits?
Conducting supplier audits is one of the most effective ways to assess quality control processes. Buyers should establish criteria for audits, focusing on production capabilities, compliance with standards, and overall operational efficiency.
Regular audits can uncover potential risks and allow buyers to ensure that suppliers adhere to their quality commitments. It’s advisable to schedule audits periodically or before significant contracts to mitigate risks.
How Can Buyers Utilize Third-Party Inspections?
Engaging third-party inspection services can provide an unbiased assessment of a supplier’s quality control processes. These services can conduct pre-shipment inspections, ensuring that products meet specified requirements before they are dispatched.
Buyers should consider incorporating third-party inspections as part of their procurement process, especially when dealing with new suppliers or entering new markets.
What Documentation Should Buyers Request from Suppliers?
Buyers should request comprehensive documentation from suppliers, including:
- Certificates of Compliance: To verify adherence to international standards.
- Quality Control Reports: Detailing inspections and testing results.
- Production Process Documentation: Outlining the steps taken to ensure quality during manufacturing.
Having access to these documents can significantly enhance a buyer’s confidence in the supplier’s capabilities.
Conclusion: How Can B2B Buyers Ensure Quality in Limit Switch Manufacturing?
Understanding the manufacturing processes and quality assurance practices of limit switch manufacturers is essential for international B2B buyers. By focusing on material preparation, assembly, and finishing techniques, alongside stringent quality control measures, buyers can make informed decisions.
Verifying supplier certifications, conducting audits, and requesting comprehensive documentation will further ensure that the limit switches meet both operational and regulatory standards, fostering successful business relationships across diverse markets.
Practical Sourcing Guide: A Step-by-Step Checklist for ‘limit switch manufacturer’
The purpose of this guide is to provide international B2B buyers, particularly from Africa, South America, the Middle East, and Europe, with a practical checklist for sourcing limit switch manufacturers. By following these steps, buyers can ensure they select a reliable supplier that meets their technical requirements and business needs.
Step 1: Define Your Technical Specifications
Before starting your search for a limit switch manufacturer, clearly outline your technical specifications. This includes the type of limit switches required (mechanical, magnetic, etc.), operational voltage, environmental conditions (temperature, humidity), and installation requirements. Knowing these details will help you communicate effectively with potential suppliers and narrow down your options.
Step 2: Research Potential Suppliers
Conduct thorough research to identify potential limit switch manufacturers. Utilize online directories, industry forums, and trade shows to compile a list of candidates. Pay attention to suppliers that have experience in your specific industry, as they will be more familiar with your unique requirements.
Step 3: Evaluate Supplier Certifications
✅ Verify Supplier Certifications
It’s crucial to ensure that the manufacturers you consider have relevant certifications, such as ISO 9001 for quality management systems or UL certification for safety standards. These certifications demonstrate a commitment to quality and compliance with international standards, which is vital for ensuring the reliability of your limit switches.
Step 4: Request Samples and Technical Data
Once you have shortlisted potential suppliers, request samples of their limit switches along with technical data sheets. This will allow you to assess the quality and performance of their products firsthand. Evaluate the materials used, the robustness of the switches, and any additional features that may enhance functionality.
Step 5: Assess Customer Support and Service Levels
📞 Check Customer Support Availability
Evaluate the level of customer support offered by each supplier. This includes response times for inquiries, the availability of technical support, and the ease of communication. A supplier that offers strong support can be invaluable, especially if you encounter issues post-purchase.
Step 6: Review Pricing and Payment Terms
Analyze the pricing structures of the shortlisted manufacturers. While cost is a significant factor, it’s essential to consider the total cost of ownership, which includes shipping, tariffs, and potential maintenance costs. Additionally, clarify payment terms to ensure they align with your cash flow requirements.
Step 7: Check References and Reviews
Finally, reach out to other companies that have sourced limit switches from your potential suppliers. Request references and look for online reviews to gauge customer satisfaction. Understanding the experiences of other businesses can provide insights into the reliability and reputation of the manufacturer.
By following this step-by-step checklist, B2B buyers can effectively navigate the sourcing process for limit switch manufacturers, ensuring they select a supplier that meets their technical requirements and business expectations.
Comprehensive Cost and Pricing Analysis for limit switch manufacturer Sourcing
What Are the Key Cost Components in Limit Switch Manufacturing?
Understanding the cost structure of limit switch manufacturing is essential for international B2B buyers. The primary cost components include:
-
Materials: The choice of materials significantly impacts pricing. Common materials for limit switches include metals like stainless steel, plastics, and electronic components. Buyers should consider not only the base material cost but also the availability and sourcing conditions in different regions.
-
Labor: Labor costs vary by region and are influenced by local wage standards and skill availability. In countries with higher labor costs, such as Germany, the overall price may be higher compared to regions in Africa or South America.
-
Manufacturing Overhead: This includes costs associated with factory operations, utilities, and equipment maintenance. Efficient manufacturing processes can help mitigate these costs, making it essential for buyers to assess the production capabilities of their suppliers.
-
Tooling: Tooling costs are incurred during the setup of production equipment and molds necessary for manufacturing. Custom designs typically require higher tooling costs, impacting the overall pricing.
-
Quality Control (QC): Implementing a robust QC process ensures product reliability but can add to manufacturing costs. Buyers should inquire about the QC measures taken by suppliers and how these impact pricing.
-
Logistics: Shipping and handling costs vary based on the distance from the manufacturer to the buyer. Incoterms can significantly influence these costs, as they define the responsibilities for transportation, insurance, and duties.
-
Margin: The supplier’s profit margin is also a critical factor. Margins can vary based on market demand, competition, and the supplier’s operational efficiency.
How Do Price Influencers Affect Limit Switch Costs?
Several factors can influence the pricing of limit switches:
-
Volume/MOQ: The minimum order quantity (MOQ) often determines the price per unit. Larger orders typically result in lower costs due to economies of scale, making it advantageous for buyers to consolidate purchases.
-
Specifications and Customization: Custom specifications can lead to higher costs due to the additional resources required for design and production. Buyers should clearly define their requirements to avoid unexpected charges.
-
Material Quality and Certifications: Higher quality materials or specific certifications (e.g., ISO, CE) can increase costs. Buyers should balance the need for quality with budget constraints.
-
Supplier Factors: Supplier reputation, experience, and geographic location can impact pricing. Established suppliers may charge more due to their reliability and service quality.
-
Incoterms: The choice of Incoterms affects shipping costs and responsibilities. Understanding the implications of terms like FOB (Free on Board) or CIF (Cost, Insurance, and Freight) is crucial for accurate budgeting.
What Are the Best Practices for Negotiating Limit Switch Prices?
-
Conduct Thorough Research: Understand market rates and competitor pricing to strengthen your negotiation position. Being informed can help you identify fair pricing and avoid overpaying.
-
Emphasize Long-Term Relationships: Building long-term partnerships with suppliers can lead to better pricing and terms. Suppliers may be more willing to negotiate if they foresee ongoing business.
-
Leverage Total Cost of Ownership (TCO): Consider all costs associated with a product, including maintenance, warranty, and potential downtime. This broader perspective can justify higher upfront costs if they lead to lower overall expenses.
-
Be Transparent About Your Needs: Clearly communicate your volume requirements and any flexibility you have regarding specifications. This transparency can help suppliers offer more competitive pricing.
-
Explore Multiple Suppliers: Don’t rely on a single source. Engaging multiple suppliers can create competition, leading to better pricing and terms.
What Should International Buyers Be Aware of Regarding Pricing Nuances?
For international B2B buyers, particularly from Africa, South America, the Middle East, and Europe, several pricing nuances should be considered:
-
Exchange Rates: Fluctuations in currency can impact costs, particularly when dealing with suppliers in different currencies. Buyers should monitor exchange rates and consider hedging options if dealing in large volumes.
-
Import Duties and Tariffs: Understanding the local regulations regarding imports is crucial. Tariffs can significantly affect the total cost, making it essential to factor these into your pricing calculations.
-
Cultural Differences: Negotiation styles vary by region. Understanding cultural norms can facilitate better communication and successful negotiations.
Disclaimer on Indicative Prices
Prices for limit switches can vary widely based on the factors discussed. It is essential for buyers to request detailed quotes from multiple suppliers to ensure they receive accurate and competitive pricing tailored to their specific needs.
Alternatives Analysis: Comparing limit switch manufacturer With Other Solutions
In the landscape of industrial automation, selecting the right solution for controlling machinery and processes is critical for operational efficiency. Limit switches have long been a staple in various applications, but alternative technologies are emerging that may provide similar or enhanced functionalities. This section explores viable alternatives to limit switches and compares them across several key aspects.
Comparison Table of Limit Switch Manufacturer and Alternatives
Comparison Aspect | Limit Switch Manufacturer | Proximity Sensors | Photoelectric Sensors |
---|---|---|---|
Performance | Reliable for mechanical actuation; limited by physical contact | Non-contact sensing; can detect objects without direct contact | High-speed detection; versatile in various lighting conditions |
Cost | Moderate initial investment; low operational costs | Generally lower cost; installation may vary | Higher upfront cost; potential long-term savings on maintenance |
Ease of Implementation | Straightforward installation; may require mechanical adjustments | Simple installation; often plug-and-play | Requires precise alignment; more complex setup |
Maintenance | Low maintenance; physical wear over time | Minimal maintenance; robust against dirt and dust | Moderate maintenance; may require cleaning of lenses |
Best Use Case | Ideal for heavy machinery and applications requiring precise mechanical feedback | Suitable for detecting the presence of objects in conveyor systems | Excellent for high-speed applications and environments with varying light |
What Are the Advantages and Disadvantages of Proximity Sensors?
Proximity sensors operate without physical contact, making them an attractive alternative to limit switches. They use electromagnetic fields or light to detect nearby objects, which means they can be placed in positions where mechanical switches might be impractical.
Pros:
– Non-contact sensing reduces wear and tear, leading to potentially longer lifespans.
– Quick response times enhance operational efficiency in automation.
Cons:
– They may not work effectively in environments with heavy interference or extreme conditions.
– Limited range compared to some mechanical systems, which might restrict application scope.
How Do Photoelectric Sensors Compare?
Photoelectric sensors are another robust alternative, utilizing light beams to detect objects. They can operate over greater distances and can be highly versatile, adapting to different environments.
Pros:
– Capable of detecting transparent or small objects that may not be easily sensed by limit switches.
– Versatile in applications across different industries, from packaging to automotive.
Cons:
– More complex installation process, requiring careful alignment and calibration.
– Higher initial investment costs can deter some buyers, although they may provide savings through reduced downtime.
How to Choose the Right Solution for Your Needs?
When evaluating alternatives to limit switches, B2B buyers should consider their specific operational requirements, including the environment in which the technology will be used, the types of materials being handled, and the expected lifecycle of the equipment.
Limit switches remain a reliable choice for many applications, especially in heavy machinery scenarios. However, if your operations demand higher speeds or non-contact sensing, exploring proximity or photoelectric sensors may yield better long-term results.
Ultimately, the decision should align with the overall automation strategy of your business, factoring in both short-term costs and long-term operational efficiencies.
Essential Technical Properties and Trade Terminology for limit switch manufacturer
What Are the Key Technical Properties of Limit Switches?
When sourcing limit switches, understanding their technical properties is crucial for ensuring they meet specific operational needs. Here are some essential specifications to consider:
1. Material Grade
The material used in limit switches significantly affects their durability and performance. Common materials include stainless steel, plastic, and brass. Stainless steel offers corrosion resistance, making it ideal for harsh environments, while plastic may be used in less demanding applications due to its lightweight nature. For B2B buyers, selecting the right material can enhance product longevity and reduce maintenance costs.
2. Tolerance
Tolerance refers to the acceptable limits of variation in a manufactured part’s dimensions. For limit switches, tight tolerances ensure accurate triggering and consistent performance. Understanding tolerance levels is critical for applications requiring precision, such as automation in manufacturing processes. Buyers should consult with manufacturers to ensure the specified tolerances align with their operational requirements.
3. Electrical Rating
Limit switches come with various electrical ratings, indicating the maximum voltage and current they can handle. This specification is vital for ensuring compatibility with the intended electrical systems. Buyers must choose switches with electrical ratings that match or exceed their application requirements to avoid failures and potential safety hazards.
4. Actuation Force
The actuation force is the amount of force required to activate the switch. Different applications may require varying actuation forces, and understanding this specification helps ensure that the limit switch will perform effectively under specific conditions. For instance, in heavy machinery, a higher actuation force may be necessary to prevent accidental triggering.
5. IP Rating
The Ingress Protection (IP) rating indicates the degree of protection against dust and water. For applications in challenging environments, a higher IP rating (e.g., IP67) is preferable. This ensures that the limit switch remains functional despite exposure to contaminants or moisture. Buyers should assess their operational environment to determine the necessary IP rating.
What Are the Common Trade Terms Used in the Limit Switch Industry?
Familiarity with industry terminology can enhance communication and streamline transactions. Here are some common terms that B2B buyers should know:
1. OEM (Original Equipment Manufacturer)
An OEM is a company that produces components that are used in another company’s end products. In the limit switch industry, buyers often source from OEMs to ensure compatibility with their systems. Understanding this term is vital for buyers looking to integrate limit switches into larger machinery or systems.
2. MOQ (Minimum Order Quantity)
MOQ refers to the smallest number of units that a supplier is willing to sell. This term is particularly important for international buyers, as MOQs can vary significantly between manufacturers. Knowing the MOQ helps buyers budget and plan their inventory accordingly.
3. RFQ (Request for Quotation)
An RFQ is a document sent to suppliers requesting pricing and terms for specific products. When buying limit switches, issuing an RFQ can lead to competitive pricing and better negotiation outcomes. It is an essential step in the procurement process for B2B buyers.
4. Incoterms (International Commercial Terms)
Incoterms are a set of predefined commercial terms used in international trade. They define the responsibilities of buyers and sellers regarding shipping, insurance, and tariffs. Understanding Incoterms is critical for buyers in Africa, South America, the Middle East, and Europe, as they help clarify who bears the risk and cost of transporting goods.
5. Lead Time
Lead time is the time taken from placing an order to receiving the goods. This term is crucial for supply chain management, especially for international buyers who need to synchronize their operations with product availability. Clear communication about lead times can help avoid disruptions in manufacturing schedules.
By grasping these technical properties and trade terms, international B2B buyers can make informed decisions when selecting limit switches that best suit their operational needs.
Navigating Market Dynamics and Sourcing Trends in the limit switch manufacturer Sector
What Are the Current Market Dynamics and Key Trends in the Limit Switch Manufacturer Sector?
The limit switch manufacturer sector is experiencing significant evolution driven by technological advancements and changing consumer expectations. One of the primary global drivers is the increasing automation across various industries, such as manufacturing, automotive, and energy. This trend is prompting B2B buyers to seek reliable limit switches that enhance operational efficiency and safety. Emerging technologies such as IoT (Internet of Things) and Industry 4.0 are also shaping sourcing trends, as manufacturers integrate smart features into their products. These innovations allow for real-time monitoring and data collection, facilitating predictive maintenance and reducing downtime.
Moreover, international B2B buyers from regions like Africa, South America, the Middle East, and Europe are increasingly focusing on suppliers that offer custom solutions tailored to specific industry needs. For example, buyers from Turkey and Germany are looking for limit switches that comply with stringent European safety standards. This demand for customization is coupled with a growing emphasis on quality assurance and robust supply chain management, as buyers seek to mitigate risks associated with sourcing.
Furthermore, the competitive landscape is evolving, with a rise in local manufacturers offering cost-effective solutions. This trend is particularly visible in emerging markets where buyers are balancing quality with affordability. Understanding these market dynamics is crucial for international B2B buyers to make informed sourcing decisions that align with their operational goals.
How Is Sustainability and Ethical Sourcing Affecting the Limit Switch Manufacturer Sector?
Sustainability and ethical sourcing have become central to the limit switch manufacturer sector, reflecting broader environmental concerns and regulatory pressures. The environmental impact of manufacturing processes, particularly in terms of waste generation and energy consumption, has prompted manufacturers to adopt greener practices. B2B buyers are increasingly prioritizing suppliers who demonstrate a commitment to sustainability through responsible sourcing of materials and energy-efficient production methods.
The importance of ethical supply chains cannot be overstated. Buyers are now scrutinizing the entire lifecycle of limit switches, from raw material extraction to end-of-life disposal. This scrutiny is leading to the demand for ‘green’ certifications and materials, such as RoHS (Restriction of Hazardous Substances) compliance, which ensures that products are free from harmful substances. Additionally, buyers are seeking suppliers who engage in fair labor practices and transparency in their operations, fostering trust and long-term partnerships.
By aligning with suppliers who prioritize sustainability and ethical sourcing, international B2B buyers can not only enhance their corporate social responsibility (CSR) profiles but also meet the increasing regulatory demands in their respective regions. This shift is not just a trend but a necessary adaptation to the evolving market landscape.
What Is the Evolution of the Limit Switch Manufacturer Sector?
The limit switch manufacturer sector has undergone significant transformations since its inception in the early 20th century. Initially, limit switches were mechanical devices used primarily for basic on/off control in industrial applications. Over the decades, advancements in technology have led to the integration of electronic components, enhancing the functionality and reliability of these devices.
The evolution continued with the introduction of smart limit switches that incorporate sensors and connectivity features, enabling real-time data transmission. This shift has been crucial for industries embracing automation and IoT technologies. Today, limit switches are not only essential for operational efficiency but also play a vital role in safety and compliance with global standards.
As the market progresses, international B2B buyers must stay informed about these developments, ensuring they source limit switches that not only meet current operational needs but also anticipate future technological advancements.
Frequently Asked Questions (FAQs) for B2B Buyers of limit switch manufacturer
-
How do I choose the right limit switch manufacturer for my business needs?
Choosing the right limit switch manufacturer involves evaluating several factors. First, consider the manufacturer’s experience in your industry; a specialized manufacturer is likely to understand your unique requirements better. Look for certifications that indicate compliance with international standards, such as ISO 9001. Additionally, request samples to assess product quality and performance. Finally, check customer reviews and case studies to gauge the manufacturer’s reliability and customer service reputation. -
What types of limit switches are available for different applications?
Limit switches come in various types, including mechanical, magnetic, and proximity switches. Mechanical limit switches are ideal for heavy-duty applications due to their durability. Magnetic switches work well in environments with dust or moisture, while proximity switches are suitable for applications requiring non-contact operation. Assess your specific application needs, such as load capacity and environmental conditions, to select the most appropriate type. -
What customization options can I expect from limit switch manufacturers?
Many limit switch manufacturers offer customization options to meet specific requirements. These may include variations in size, shape, material, and electrical specifications. Some manufacturers can also provide tailored mounting solutions and integration with existing systems. When discussing customization, be clear about your specifications and desired performance criteria, as this will help the manufacturer propose the best solutions for your application. -
What is the minimum order quantity (MOQ) for limit switches?
Minimum order quantities (MOQs) for limit switches can vary significantly among manufacturers. Some may have a low MOQ of just a few units, while others may require larger orders, especially for customized products. It’s crucial to discuss MOQs upfront to ensure they align with your purchasing capabilities. If you require a smaller quantity, inquire about the possibility of sample orders or trial purchases to evaluate the product before committing to larger quantities. -
What payment terms should I expect when sourcing limit switches internationally?
Payment terms can differ based on the manufacturer and your negotiation. Common options include advance payment, partial payment upon order confirmation, and balance upon delivery. For international transactions, consider using secure payment methods like letters of credit or escrow services, which can protect both parties. Always clarify payment terms before placing an order to avoid misunderstandings and ensure smooth transactions. -
How do I verify the quality assurance processes of a limit switch manufacturer?
To verify a manufacturer’s quality assurance processes, request documentation that details their quality management system. Look for certifications like ISO 9001, which indicate adherence to international quality standards. Additionally, ask about their testing procedures, including the types of tests conducted on limit switches before shipping. A reputable manufacturer will be transparent about their QA processes and provide evidence of compliance with industry standards. -
What logistics considerations should I keep in mind when importing limit switches?
When importing limit switches, consider shipping methods, delivery times, and customs regulations in your country. Research the most efficient logistics providers that specialize in industrial equipment. Be aware of any import duties or taxes that may apply, and ensure that all documentation, such as bills of lading and customs declarations, is in order. Clear communication with your supplier about logistics will help prevent delays and unexpected costs. -
How can I ensure effective communication with my limit switch supplier?
Effective communication with your limit switch supplier is vital for a successful partnership. Start by establishing clear channels of communication, such as dedicated email addresses and phone lines. Regularly update each other on project status, and do not hesitate to ask questions or request clarifications. Utilizing project management tools can enhance collaboration and track progress. Additionally, consider cultural differences in communication styles, especially when dealing with international suppliers, to foster a more productive relationship.
Important Disclaimer & Terms of Use
⚠️ Important Disclaimer
The information provided in this guide, including content regarding manufacturers, technical specifications, and market analysis, is for informational and educational purposes only. It does not constitute professional procurement advice, financial advice, or legal advice.
While we have made every effort to ensure the accuracy and timeliness of the information, we are not responsible for any errors, omissions, or outdated information. Market conditions, company details, and technical standards are subject to change.
B2B buyers must conduct their own independent and thorough due diligence before making any purchasing decisions. This includes contacting suppliers directly, verifying certifications, requesting samples, and seeking professional consultation. The risk of relying on any information in this guide is borne solely by the reader.
Strategic Sourcing Conclusion and Outlook for limit switch manufacturer
What Are the Key Takeaways for B2B Buyers in Limit Switch Manufacturing?
In conclusion, strategic sourcing in the limit switch manufacturing sector is essential for optimizing supply chains and enhancing operational efficiencies. By focusing on reliable suppliers, particularly those that understand the specific needs of diverse markets across Africa, South America, the Middle East, and Europe, businesses can secure high-quality components that meet stringent safety and performance standards.
International buyers should prioritize partnerships with manufacturers that offer a blend of innovation, customization options, and robust customer support. This approach not only mitigates risks but also fosters sustainable business relationships that can adapt to changing market demands.
How Can Buyers Position Themselves for Future Success?
Looking ahead, it is crucial for B2B buyers to remain agile and informed about market trends and technological advancements in limit switch production. Engaging in industry forums, participating in trade shows, and leveraging digital platforms for supplier discovery can significantly enhance sourcing strategies.
Take proactive steps today to explore potential partnerships with limit switch manufacturers who are committed to quality and innovation. By doing so, you can ensure your business is well-equipped to navigate future challenges and capitalize on emerging opportunities in the global marketplace.