Discover Top Benefits: Choosing the Right Air Cleaner Supplier (2025)
Introduction: Navigating the Global Market for air cleaner supplier
In an increasingly polluted world, sourcing reliable air cleaner suppliers has become a crucial challenge for international B2B buyers. Whether you operate in the bustling urban landscapes of Africa, South America, the Middle East, or Europe, ensuring the health and safety of your workforce through clean air solutions is non-negotiable. This comprehensive guide is designed to equip you with the knowledge needed to navigate the global market for air cleaners effectively.
Within this guide, you will find detailed insights into various types of air cleaning technologies, their applications across different industries, and key considerations for supplier vetting. Additionally, we will explore cost factors and the latest industry trends that can impact your purchasing decisions. By delving into these topics, this guide empowers you to make informed choices that align with your operational needs and sustainability goals.
Understanding the nuances of sourcing air cleaning solutions is essential for maintaining a competitive edge in today’s market. Whether you are looking to enhance indoor air quality in office spaces, industrial facilities, or healthcare environments, our guide will provide actionable insights tailored to your specific context. Get ready to transform your air quality management strategy with reliable suppliers that meet international standards and regional requirements.
Understanding air cleaner supplier Types and Variations
Type Name | Key Distinguishing Features | Primary B2B Applications | Brief Pros & Cons for Buyers |
---|---|---|---|
HEPA Air Cleaners | High-efficiency particulate air filters | Hospitals, laboratories, offices | Pros: Excellent for allergens; Cons: Higher initial cost. |
Activated Carbon Air Cleaners | Utilizes activated carbon to adsorb odors and gases | Restaurants, hotels, industrial sites | Pros: Effective for VOCs; Cons: Requires regular replacement. |
UV-C Air Purifiers | Incorporates UV light to kill bacteria and viruses | Healthcare facilities, schools | Pros: Disinfects air; Cons: Limited to surface pathogens only. |
Ionizers | Uses charged ions to attract and neutralize particles | Manufacturing, warehouses | Pros: Reduces particulate matter; Cons: Ozone production can be a concern. |
Portable Air Cleaners | Compact and mobile units for localized air purification | Small offices, home offices | Pros: Easy to move; Cons: Limited coverage area. |
What are HEPA Air Cleaners and Their B2B Benefits?
HEPA air cleaners are renowned for their ability to filter out at least 99.97% of airborne particles, including dust, pollen, and pet dander. They are particularly suitable for environments requiring stringent air quality, such as hospitals and laboratories. When purchasing, B2B buyers should consider the unit’s airflow rate and filter replacement costs, as these factors directly affect operational efficiency and long-term expenses.
How Do Activated Carbon Air Cleaners Work for Odor Control?
Activated carbon air cleaners leverage the adsorptive properties of activated carbon to capture odors, volatile organic compounds (VOCs), and other gaseous pollutants. They are ideal for restaurants and hotels where odor control is paramount. Buyers should assess the size of the carbon filter and the frequency of replacement to ensure optimal performance and cost management.
Why Choose UV-C Air Purifiers for Disinfection?
UV-C air purifiers utilize ultraviolet light to eliminate bacteria and viruses, making them suitable for healthcare facilities and educational institutions. These units are particularly effective in environments where hygiene is critical. B2B buyers should evaluate the UV intensity and exposure time to ensure that the device meets necessary disinfection standards, alongside considering maintenance requirements.
What are the Advantages of Ionizers in Industrial Settings?
Ionizers work by emitting charged ions that attach to airborne particles, causing them to clump together and fall to the ground or be captured by filters. They are commonly used in manufacturing and warehouse settings where airborne dust can affect product quality. When purchasing, buyers must consider the potential for ozone production, which can be a health concern, and ensure compliance with local regulations.
How Do Portable Air Cleaners Fit into Smaller B2B Environments?
Portable air cleaners offer flexibility and ease of use, making them perfect for small offices and home workspaces. They provide localized air purification without the need for extensive installation. Buyers should evaluate the Clean Air Delivery Rate (CADR) and noise levels, as these factors will influence user satisfaction and overall effectiveness in smaller spaces.
Related Video: Variable Air Volume – VAV system HVAC
Key Industrial Applications of air cleaner supplier
Industry/Sector | Specific Application of air cleaner supplier | Value/Benefit for the Business | Key Sourcing Considerations for this Application |
---|---|---|---|
Manufacturing | Industrial air filtration systems for factories | Reduces airborne contaminants, enhancing worker safety | Compliance with local regulations; energy efficiency; maintenance support |
Healthcare | Air purifiers for hospitals and clinics | Improves air quality, reducing infection rates | HEPA filter certification; low noise operation; reliability in critical environments |
Food Processing | Cleanroom air filtration for food production | Ensures product safety and compliance with health standards | Certifications for food safety; adaptability to various production scales; energy efficiency |
Education | Air filtration systems in schools and universities | Enhances learning environments by improving air quality | Cost-effectiveness; ease of installation; long-term service agreements |
Hospitality | Air purification in hotels and restaurants | Elevates guest experience and satisfaction | Aesthetic design; low maintenance; integration with existing HVAC systems |
How is Air Cleaner Supplier Used in Manufacturing?
In the manufacturing sector, air cleaner suppliers provide industrial air filtration systems designed to reduce airborne contaminants such as dust, smoke, and chemical vapors. These systems not only improve air quality but also enhance worker safety and productivity. International B2B buyers must consider compliance with local regulations, energy efficiency, and the availability of maintenance support when sourcing these systems. For manufacturers in regions like Africa and South America, understanding local industrial standards is crucial to ensure operational continuity.
What Role Do Air Cleaners Play in Healthcare Settings?
Air purifiers are critical in hospitals and clinics to maintain a sterile environment. By filtering out harmful pathogens and particulate matter, these systems significantly reduce infection rates and improve overall patient outcomes. Healthcare buyers should prioritize HEPA filter certification, low noise operation, and the reliability of the equipment in critical environments. Additionally, international buyers from the Middle East and Europe must be aware of specific health regulations governing air quality in healthcare facilities to ensure compliance.
How Do Air Cleaners Benefit Food Processing Facilities?
In the food processing industry, cleanroom air filtration systems are essential for maintaining product safety and adhering to health standards. These systems prevent contamination during production, ensuring that food products meet regulatory requirements. Buyers in this sector should seek suppliers with certifications for food safety, adaptability to various production scales, and energy-efficient solutions. For businesses in Europe and South America, understanding local health regulations related to food production is vital for successful procurement.
Why Are Air Filtration Systems Important in Educational Institutions?
Schools and universities benefit from air filtration systems that enhance learning environments by improving air quality. Clean air contributes to better concentration and reduces absenteeism due to respiratory issues. B2B buyers in the education sector should focus on cost-effectiveness, ease of installation, and long-term service agreements when selecting air cleaning solutions. In regions like Africa, where educational infrastructure may vary, the ability to adapt systems to different environments is particularly important.
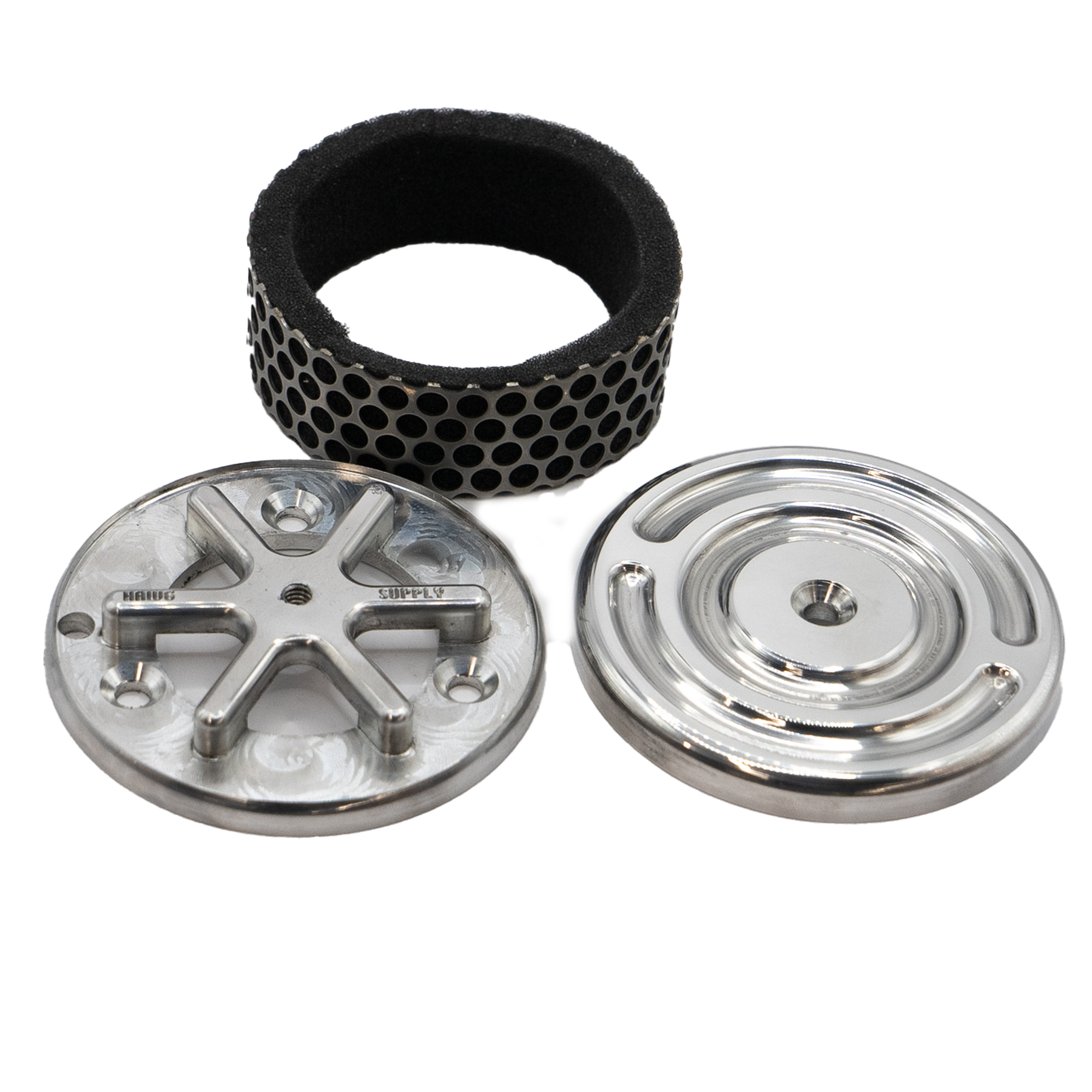
A stock image related to air cleaner supplier.
How Do Air Purifiers Enhance the Hospitality Industry?
In the hospitality sector, air purification systems in hotels and restaurants significantly elevate the guest experience by ensuring clean and pleasant indoor air quality. This not only enhances guest satisfaction but also promotes repeat business. Buyers in this industry should consider the aesthetic design of air cleaners, low maintenance requirements, and compatibility with existing HVAC systems. International buyers, especially from Europe and the Middle East, should also evaluate the latest trends in air purification technology to meet evolving consumer expectations.
Related Video: How to build a Shop Air Cleaner and Paint Booth Ventilation System
3 Common User Pain Points for ‘air cleaner supplier’ & Their Solutions
Scenario 1: Navigating Compliance with Air Quality Standards
The Problem: International B2B buyers, particularly those operating in sectors such as manufacturing or healthcare, often face challenges in adhering to varying air quality regulations across different regions. For instance, a company in South America may struggle to meet stricter European Union air quality standards when sourcing air cleaning solutions. This can lead to costly delays, potential fines, and jeopardized partnerships with local authorities or clients who demand compliance.
The Solution: To effectively navigate these complexities, B2B buyers should prioritize sourcing air cleaners that are certified to meet both local and international standards. Start by researching suppliers who have a proven track record of compliance with relevant regulations in your target market. Engage in discussions with suppliers about their certifications, product specifications, and any third-party testing that validates their claims. Buyers can also request detailed documentation that outlines compliance with specific air quality standards, ensuring that products can be easily integrated into their operations without regulatory risks. Additionally, maintaining a close relationship with suppliers can facilitate timely updates on any changes in regulations, helping buyers stay ahead of compliance challenges.
Scenario 2: Addressing Concerns Over Product Efficacy
The Problem: Many B2B buyers are skeptical about the efficacy of air cleaning products, particularly with the proliferation of various technologies and marketing claims in the market. For example, a buyer in Africa might be uncertain whether a supplier’s HEPA air purifier genuinely removes harmful particulates or if its performance claims are exaggerated. This skepticism can lead to hesitation in making purchasing decisions, resulting in lost opportunities for both the buyer and the supplier.
The Solution: To combat this skepticism, B2B buyers should seek suppliers that provide transparent and verifiable performance data. Request independent lab test results that demonstrate the air cleaner’s effectiveness in removing specific contaminants, including particulate matter and volatile organic compounds (VOCs). Furthermore, consider suppliers that offer trial periods or satisfaction guarantees, allowing businesses to test the product in their own environment before making a full commitment. Engaging in direct conversations with supplier representatives can also provide clarity on product features and real-world performance, helping buyers make informed decisions based on solid evidence rather than marketing hype.
Scenario 3: Overcoming Maintenance and Operational Challenges
The Problem: After purchasing air cleaning solutions, B2B buyers frequently encounter operational challenges related to maintenance and servicing. A buyer in the Middle East, for instance, might find that the air cleaners require frequent filter replacements, leading to increased downtime and operational disruptions. This not only affects the overall air quality but also strains the company’s budget and resources.
The Solution: To mitigate these operational challenges, it is essential for buyers to conduct thorough research on the maintenance requirements of the air cleaning systems before purchase. Engage with suppliers to understand the total cost of ownership, including filter replacement frequency, maintenance schedules, and any additional servicing costs. Opt for suppliers that provide comprehensive support, such as easy access to replacement parts, user-friendly maintenance guides, and even training for in-house staff. Additionally, consider investing in air cleaning systems equipped with smart technology that alerts users when maintenance is due, helping to streamline operations and minimize downtime. By prioritizing maintenance-friendly solutions, buyers can enhance the longevity and effectiveness of their air cleaning systems while managing costs effectively.
Strategic Material Selection Guide for air cleaner supplier
What Are the Common Materials Used in Air Cleaners?
When selecting materials for air cleaners, it’s essential to consider properties that affect performance, durability, and cost. Below are analyses of four common materials used in air cleaner manufacturing, focusing on their key properties, advantages, disadvantages, and specific considerations for international B2B buyers.
How Does Polypropylene Perform in Air Cleaner Applications?
Key Properties:
Polypropylene (PP) is a thermoplastic polymer known for its excellent chemical resistance, lightweight nature, and good temperature stability (up to 100°C). It is non-toxic and can be easily molded into various shapes, making it suitable for diverse applications.
Pros & Cons:
The durability of polypropylene is notable, as it resists fatigue and stress cracking. However, its lower heat resistance compared to other materials can limit its use in high-temperature environments. Manufacturing complexity is relatively low, allowing for cost-effective production.
Impact on Application:
Polypropylene is compatible with various filtration media, including HEPA filters, which are essential for high-efficiency air cleaning. Its lightweight nature also makes it easier to handle and install.
Considerations for International Buyers:
Buyers from regions like Africa and South America should ensure that the polypropylene used meets local compliance standards, such as ASTM or DIN. Additionally, understanding the environmental impact of polypropylene disposal is crucial in regions with strict waste management regulations.
What Are the Benefits of Using Aluminum in Air Cleaners?
Key Properties:
Aluminum is a lightweight metal with excellent corrosion resistance and thermal conductivity. It can withstand high temperatures (up to 600°C) and provides a robust structure for air cleaner frames.
Pros & Cons:
The primary advantage of aluminum is its durability and resistance to corrosion, which extends the lifespan of air cleaners. However, it can be more expensive than plastics, and the manufacturing process can be complex, requiring specialized techniques.
Impact on Application:
Aluminum is particularly suitable for high-performance air cleaners that require structural integrity and heat resistance. Its compatibility with various filter types enhances overall performance.
Considerations for International Buyers:
B2B buyers in Europe should be aware of the EU regulations regarding aluminum sourcing and recycling. Understanding the local market’s preferences for sustainable materials can also influence purchasing decisions.
Why Choose Stainless Steel for Air Cleaners?
Key Properties:
Stainless steel is known for its exceptional strength, corrosion resistance, and temperature tolerance (up to 800°C). It is non-reactive, making it suitable for various environments.
Pros & Cons:
While stainless steel is highly durable and offers a long service life, it is also one of the more expensive materials. The manufacturing process can be complex and energy-intensive, which can increase costs.
Impact on Application:
Stainless steel is ideal for industrial air cleaners that operate in harsh environments, such as chemical plants or food processing facilities. Its robustness ensures reliability and longevity.
Considerations for International Buyers:
Buyers from the Middle East should consider the high humidity and temperature variations when selecting stainless steel grades. Compliance with international standards for food safety may also be necessary.
What Role Does Activated Carbon Play in Air Cleaners?
Key Properties:
Activated carbon is a highly porous material known for its adsorption properties, effectively trapping pollutants and odors. It can operate effectively at ambient temperatures and is often used in combination with other materials.
Pros & Cons:
The main advantage of activated carbon is its ability to improve air quality significantly. However, it has a limited lifespan and may require frequent replacement, adding to maintenance costs.
Impact on Application:
Activated carbon is particularly effective in applications requiring the removal of volatile organic compounds (VOCs) and odors, making it suitable for residential and commercial air cleaners.
Considerations for International Buyers:
Buyers in regions like South America should be aware of the sourcing and sustainability of activated carbon. Compliance with local environmental regulations regarding the disposal of spent carbon is also crucial.
Summary Table of Material Selection for Air Cleaners
Material | Typical Use Case for Air Cleaner Supplier | Key Advantage | Key Disadvantage/Limitation | Relative Cost (Low/Med/High) |
---|---|---|---|---|
Polypropylene | HEPA filters and lightweight frames | Excellent chemical resistance | Lower heat resistance | Medium |
Aluminum | High-performance air cleaner frames | Durable and corrosion-resistant | Higher cost and complex manufacturing | High |
Stainless Steel | Industrial air cleaners in harsh environments | Exceptional strength and longevity | Expensive and complex processing | High |
Activated Carbon | Residential and commercial air cleaners | Effective in odor and VOC removal | Limited lifespan requiring replacement | Medium |
This comprehensive analysis of materials provides B2B buyers with actionable insights to make informed decisions when selecting components for air cleaners, ensuring compliance and suitability for their specific markets.
In-depth Look: Manufacturing Processes and Quality Assurance for air cleaner supplier
What Are the Key Stages in the Manufacturing Process of Air Cleaners?
The manufacturing process for air cleaners involves several critical stages that ensure the final product meets quality and performance standards. Understanding these stages is essential for international B2B buyers, particularly those from Africa, South America, the Middle East, and Europe.
1. Material Preparation: What Materials Are Used in Air Cleaner Manufacturing?
The first stage involves sourcing and preparing materials. Common materials used include:
- Filters: HEPA filters, activated carbon, and pre-filters are typical components.
- Housing: Plastics, metal, and composites are used for the outer shell.
- Electronics: Components like fans and sensors require careful selection.
Suppliers should demonstrate traceability of materials, ensuring compliance with international standards and regulations.
2. Forming: How Are Components Shaped for Air Cleaners?
The forming stage involves shaping the materials into usable components. Techniques include:
- Injection Molding: Widely used for creating plastic parts like housing.
- Die-Cutting: Essential for producing filter shapes and sizes.
- Metal Stamping: Used for metallic parts, ensuring durability.
B2B buyers should inquire about the machinery and technology used, as advanced methods often lead to better precision and efficiency.
3. Assembly: What Assembly Techniques Are Commonly Used?
Once components are formed, they undergo assembly. This stage can include:
- Manual Assembly: Skilled workers assemble parts, especially for complex units.
- Automated Assembly: Robotics and conveyors can enhance speed and reduce labor costs.
Buyers should assess the assembly process for efficiency and consistency, as this directly impacts product reliability.
4. Finishing: What Does the Finishing Process Entail?
The finishing stage is crucial for aesthetics and functionality. Common practices include:
- Surface Treatment: Painting, coating, or polishing to enhance appearance and protect against corrosion.
- Quality Inspection: Ensuring that the assembly meets design specifications.
Understanding the finishing techniques can help buyers gauge the product’s longevity and market readiness.
How Is Quality Assurance Implemented in Air Cleaner Manufacturing?
Quality assurance (QA) is vital in maintaining product integrity throughout the manufacturing process. International B2B buyers should be familiar with the QA practices that air cleaner suppliers employ.
1. What Are the International Standards for Quality Assurance?
Compliance with recognized international standards is essential for suppliers. Key certifications include:
- ISO 9001: A globally recognized standard for quality management systems (QMS) that helps ensure consistent quality in manufacturing.
- CE Marking: Indicates compliance with EU safety, health, and environmental requirements, vital for European buyers.
- API Standards: Relevant for suppliers involved in industrial applications, ensuring reliability in performance.
Buyers should request documentation of these certifications to verify supplier compliance.
2. What Are the Key Quality Control Checkpoints in Manufacturing?
Quality control (QC) involves multiple checkpoints throughout the manufacturing process, including:
- Incoming Quality Control (IQC): Inspection of raw materials upon arrival to ensure they meet specifications.
- In-Process Quality Control (IPQC): Continuous monitoring during manufacturing to catch defects early.
- Final Quality Control (FQC): Comprehensive testing of the finished product before shipment.
These checkpoints help mitigate risks and ensure that only high-quality products reach the market.
Which Testing Methods Are Commonly Used for Air Cleaners?
Air cleaner manufacturers employ various testing methods to validate product performance and safety. Common methods include:
- Performance Testing: Evaluating airflow, filter efficiency, and noise levels under controlled conditions.
- Durability Testing: Assessing the product’s ability to withstand operational stresses over time.
- Safety Testing: Ensuring compliance with electrical safety standards, particularly for models with integrated electronics.
B2B buyers should ask for detailed testing reports to understand the reliability of the products they are considering.
How Can B2B Buyers Verify Supplier Quality Assurance Practices?
Verifying a supplier’s quality assurance practices is critical for international B2B buyers. Here are actionable steps:
1. Conduct Supplier Audits: What Should Buyers Look For?
Performing supplier audits helps assess manufacturing capabilities and QA processes. Key focus areas include:
- Facility Conditions: Cleanliness, organization, and maintenance of equipment.
- Documentation: Availability of quality manuals, process flow charts, and training records for employees.
- Compliance Records: Evidence of adherence to ISO standards and other relevant certifications.
2. Request Quality Assurance Reports: What Information Should Be Included?
Buyers should request comprehensive quality assurance reports from suppliers. Essential elements to include are:
- Inspection Records: Details of inspections conducted at various stages.
- Testing Results: Data from performance, durability, and safety tests.
- Non-Conformance Reports: Instances of defects and the corrective actions taken.
These documents provide insight into the supplier’s commitment to quality.
3. Engage Third-Party Inspection Services: How Can This Benefit Buyers?
Utilizing third-party inspection services can enhance trust and transparency. These independent firms can:
- Verify Compliance: Ensure that the supplier meets international standards.
- Conduct Random Inspections: Evaluate the manufacturing process and finished goods without bias.
This step is particularly valuable for buyers in regions with less stringent local regulations.
What Are the Quality Control Nuances for International B2B Buyers?
Understanding regional nuances can significantly affect the purchasing decision for international B2B buyers. Consider the following:
- Regional Certifications: Different regions may have varying certification requirements. For instance, buyers in Europe may prioritize CE marking, while those in South America might focus on local compliance.
- Cultural Expectations: The definition of quality may vary by region, impacting how products are perceived. Engaging with local experts can provide valuable insights.
In summary, a thorough understanding of manufacturing processes and quality assurance practices is essential for international B2B buyers of air cleaners. By focusing on key stages, quality checkpoints, and verification methods, buyers can make informed decisions that align with their operational needs and market standards.
Practical Sourcing Guide: A Step-by-Step Checklist for ‘air cleaner supplier’
The process of sourcing air cleaner suppliers requires careful consideration and strategic planning. This guide provides a step-by-step checklist to help B2B buyers, especially those from Africa, South America, the Middle East, and Europe, navigate the procurement process effectively.
Step 1: Define Your Technical Specifications
Establishing clear technical specifications is vital for ensuring that the air cleaners meet your operational needs. Consider factors such as airflow rate, filtration efficiency, noise levels, and energy consumption. This step helps prevent miscommunication with suppliers and ensures that the products you receive are fit for purpose.
Step 2: Research Market Trends and Regulations
Understanding current market trends and relevant regulations in your region is crucial. Different countries may have specific standards regarding air quality and product certifications. Familiarize yourself with these regulations to ensure that the products you intend to procure comply with local laws, thereby avoiding potential fines or product recalls.
Step 3: Identify Potential Suppliers
Compile a list of potential suppliers that specialize in air cleaning technologies. Utilize online platforms, trade shows, and industry publications to gather information. Look for suppliers with a solid reputation and a proven track record in delivering quality products to similar markets.
Step 4: Evaluate Supplier Certifications and Compliance
Before proceeding, verify that potential suppliers possess the necessary certifications, such as ISO 9001 for quality management and ISO 14001 for environmental management. Additionally, check for compliance with industry-specific standards relevant to your region. This step is essential for ensuring product reliability and adherence to safety regulations.
Step 5: Request Proposals and Compare Offers
Reach out to shortlisted suppliers to request detailed proposals, including pricing, lead times, and warranty terms. Comparing these offers allows you to assess not only the cost but also the value each supplier provides. Pay attention to factors such as after-sales support and the availability of spare parts.
Step 6: Conduct Site Visits and Product Testing
If possible, arrange site visits to the suppliers’ facilities or request samples for testing. Observing the production process and testing the air cleaners firsthand can provide valuable insights into the supplier’s capabilities and product performance. This step is particularly important for high-value contracts where reliability is crucial.
Step 7: Negotiate Terms and Finalize Contracts
Once you have selected a preferred supplier, begin negotiations to finalize terms. Discuss payment conditions, delivery schedules, and service agreements. Ensure that all terms are clearly documented in a contract to protect both parties and to provide a clear framework for the transaction.
By following this checklist, B2B buyers can make informed decisions when sourcing air cleaner suppliers, ensuring that they select reliable partners who can meet their needs while adhering to local regulations and industry standards.
Comprehensive Cost and Pricing Analysis for air cleaner supplier Sourcing
What Are the Key Cost Components for Air Cleaner Supplier Sourcing?
When sourcing air cleaners, understanding the cost structure is vital for international B2B buyers. The primary cost components typically include:
-
Materials: The choice of materials significantly impacts the pricing. High-quality filters and durable housing materials often lead to higher costs but enhance product longevity and performance.
-
Labor: Labor costs vary depending on the region of manufacturing. Countries with higher labor costs may offer better-skilled workers, which can affect the quality of the final product.
-
Manufacturing Overhead: This includes utilities, facility maintenance, and administrative expenses. Suppliers in different regions may have varying overhead costs that influence their pricing.
-
Tooling: Initial tooling costs can be substantial, especially for custom designs. Buyers should be aware that these costs may be amortized over larger production runs.
-
Quality Control (QC): Implementing stringent QC measures ensures that products meet specified standards. However, this also adds to the cost structure, particularly if certifications are required.
-
Logistics: Shipping costs can vary significantly based on the distance, shipping method, and Incoterms. Buyers should consider these costs as part of the total pricing analysis.
-
Margin: Suppliers typically add a margin on top of their costs. Understanding the expected profit margins in different regions can help buyers gauge pricing fairness.
How Do Price Influencers Impact Air Cleaner Sourcing?
Several factors can influence the final price of air cleaners:
-
Volume and Minimum Order Quantity (MOQ): Ordering larger quantities often leads to bulk discounts. Buyers should negotiate MOQs to optimize their costs.
-
Specifications and Customization: Customized air cleaners may incur additional costs. Buyers need to balance their specific requirements with their budget constraints.
-
Material Quality and Certifications: Higher quality materials and specific certifications (e.g., HEPA filters) can increase costs but are often necessary for regulatory compliance and product efficacy.
-
Supplier Factors: The reputation and reliability of the supplier can influence pricing. Established suppliers with a track record of quality may charge more.
-
Incoterms: The chosen Incoterm can significantly affect the total cost. For instance, “CIF” (Cost, Insurance, and Freight) might include additional costs not covered in the initial quote.
What Tips Can B2B Buyers Use for Effective Negotiation and Cost-Efficiency?
-
Negotiate Pricing and Terms: Leverage your position as a buyer to negotiate better pricing, especially if you are placing large orders or establishing a long-term relationship.
-
Consider Total Cost of Ownership (TCO): Assess not just the upfront costs but also the long-term operational costs associated with the air cleaners, including energy efficiency and maintenance.
-
Research Pricing Nuances for Different Regions: Understand the market dynamics in Africa, South America, the Middle East, and Europe. Prices can vary significantly based on local supply and demand, economic conditions, and currency fluctuations.
-
Evaluate Supplier Proposals Thoroughly: Ensure that all cost components are clearly outlined in supplier quotes. Look for hidden costs that may arise later in the procurement process.
-
Stay Informed About Market Trends: Regularly monitor industry trends and pricing benchmarks to ensure you are making competitive purchases. This knowledge can bolster your negotiation strategy.
Disclaimer for Indicative Prices
Please note that the prices mentioned in supplier quotations can fluctuate based on market conditions, material availability, and other factors. It is essential for buyers to obtain multiple quotes and conduct a comprehensive analysis to ensure competitive pricing.
Alternatives Analysis: Comparing air cleaner supplier With Other Solutions
When considering air quality management solutions, it’s essential for international B2B buyers to evaluate various options available in the market. While air cleaner suppliers offer specialized products, alternative technologies may provide comparable or even superior benefits depending on the specific requirements of a business. This analysis will help buyers make informed decisions tailored to their operational needs.
Comparison Aspect | Air Cleaner Supplier | Alternative 1: Ventilation Systems | Alternative 2: Air Purification Technology |
---|---|---|---|
Performance | High efficiency in removing particulate matter and pollutants. | Effective in circulating fresh air, reducing indoor pollutants. | Can target specific contaminants and allergens effectively. |
Cost | Moderate to high initial investment; long-term savings on health costs. | Lower initial costs but may require ongoing energy costs. | Varies widely; high-end models can be costly. |
Ease of Implementation | Requires specific installation; may need professional services. | Generally straightforward; can often be integrated into existing systems. | Installation can be complex depending on the technology used. |
Maintenance | Regular filter replacement; easy maintenance schedule. | Low maintenance; periodic checks needed. | Varies by technology; some require frequent servicing. |
Best Use Case | Ideal for spaces with high pollutant levels (e.g., factories, hospitals). | Suitable for general use in offices and homes to maintain air quality. | Best for specialized environments needing targeted air quality control (e.g., labs, medical facilities). |
What Are the Benefits and Drawbacks of Ventilation Systems as an Alternative?
Ventilation systems are a popular choice for maintaining indoor air quality by ensuring a constant flow of fresh air. The primary advantage is their cost-effectiveness in terms of initial setup. They can be integrated into existing HVAC systems, making them easier to implement. However, they may not effectively filter out specific pollutants, such as volatile organic compounds (VOCs) or allergens, which could be a significant drawback for environments requiring stringent air quality control.
How Does Air Purification Technology Compare?
Air purification technology encompasses a wide range of systems, including HEPA filters, UV light purifiers, and ionizers. These systems excel at targeting specific contaminants, making them highly effective in environments where air quality is critical, such as healthcare facilities. However, the cost can be a significant factor, particularly for high-end models. Additionally, some air purifiers require more frequent maintenance and servicing, which can lead to increased operational costs over time.
Conclusion: How Can B2B Buyers Choose the Right Solution for Their Needs?
When selecting an air quality solution, B2B buyers should first assess their specific needs, including the types of pollutants present, the size of the space, and budget constraints. While air cleaner suppliers offer robust solutions for high-pollution environments, alternatives like ventilation systems and advanced air purification technologies may be more suitable for general use or specialized applications. By understanding the strengths and weaknesses of each option, buyers can make informed decisions that align with their operational requirements and budgetary considerations, ultimately ensuring a healthier indoor environment for employees and customers alike.
Essential Technical Properties and Trade Terminology for air cleaner supplier
What Are the Key Technical Properties of Air Cleaners for B2B Buyers?
When sourcing air cleaners, understanding specific technical properties is crucial for ensuring product quality and performance. Here are several key specifications to consider:
-
Filtration Efficiency
This property refers to the air cleaner’s ability to remove particles from the air, typically measured in terms of Minimum Efficiency Reporting Value (MERV) or High-Efficiency Particulate Air (HEPA) ratings. A higher rating indicates better performance in trapping airborne contaminants, which is essential for industries where air quality is critical, such as healthcare and manufacturing. -
Material Composition
The materials used in the construction of air cleaners, such as plastic, metal, or composite materials, can significantly affect durability and performance. For example, metal housings are often more durable than plastic ones, making them suitable for industrial applications. Buyers must consider the environment in which the air cleaner will operate to select the appropriate material. -
Airflow Rate
This specification indicates the volume of air the cleaner can process, typically measured in cubic feet per minute (CFM). Understanding the required airflow rate is vital for ensuring that the air cleaner can effectively service the intended space, making it a critical factor for B2B buyers managing large facilities. -
Power Consumption
The energy efficiency of an air cleaner is measured in watts. A lower power consumption rating can lead to reduced operational costs, which is particularly important for businesses aiming to minimize expenses. Buyers should evaluate energy usage against performance to find a balance that meets their operational needs. -
Noise Level
The decibel (dB) level produced by an air cleaner is a key consideration, especially for environments requiring low noise levels, such as offices and hospitals. Selecting a quieter model can enhance the comfort of employees and clients, making it a significant factor in the purchasing decision.
Which Trade Terms Should B2B Buyers Understand When Sourcing Air Cleaners?
Understanding common trade terminology is essential for effective communication with suppliers and ensuring smooth transactions. Here are several key terms to familiarize yourself with:
-
OEM (Original Equipment Manufacturer)
This term refers to companies that produce parts or equipment that may be marketed by another manufacturer. In the context of air cleaners, knowing if a supplier is an OEM can help buyers assess the quality and reliability of the products. -
MOQ (Minimum Order Quantity)
MOQ specifies the smallest quantity of a product that a supplier is willing to sell. Understanding MOQ is vital for budgeting and inventory management, as it can impact overall costs and supply chain efficiency. -
RFQ (Request for Quotation)
An RFQ is a document sent to suppliers asking for pricing and terms for specific products. B2B buyers should use RFQs to solicit detailed proposals from multiple suppliers, helping them compare options and negotiate better deals. -
Incoterms (International Commercial Terms)
These are predefined commercial terms published by the International Chamber of Commerce (ICC) that clarify the responsibilities of buyers and sellers in international transactions. Familiarity with Incoterms is essential for understanding shipping responsibilities, costs, and risks associated with importing air cleaners. -
Lead Time
This term refers to the time it takes from placing an order to receiving the product. Knowing the lead time helps buyers plan their inventory and operations effectively, reducing the risk of stockouts.
By being informed about these technical properties and trade terms, international B2B buyers can make better purchasing decisions, ensuring they select the right air cleaning solutions for their specific needs.
Navigating Market Dynamics and Sourcing Trends in the air cleaner supplier Sector
What Are the Key Market Dynamics and Trends Affecting Air Cleaner Suppliers?
The air cleaner supplier sector is experiencing significant growth driven by global health concerns and increasing regulatory pressures regarding air quality. Key markets in Africa, South America, the Middle East, and Europe are witnessing a surge in demand for air purification technologies, particularly in urban areas where air pollution is a pressing issue. Recent trends show that businesses are increasingly adopting smart technologies in air cleaning solutions, integrating Internet of Things (IoT) capabilities for real-time monitoring and maintenance. This trend allows B2B buyers to not only enhance their environmental compliance but also improve operational efficiencies.
Additionally, the COVID-19 pandemic has heightened awareness about airborne contaminants, leading to a greater emphasis on indoor air quality. Companies are investing in advanced filtration systems, including HEPA filters and UV light technologies, to mitigate health risks. As international B2B buyers, particularly from emerging markets, evaluate suppliers, they should consider those offering innovative, tech-driven solutions that align with their specific regulatory environments and sustainability goals.
How Is Sustainability Shaping the Sourcing Strategies for Air Cleaner Suppliers?
Sustainability is now a cornerstone of sourcing strategies in the air cleaner supplier sector. International buyers are increasingly focused on the environmental impact of their supply chains, prioritizing suppliers who demonstrate a commitment to eco-friendly practices. This includes the use of sustainable materials in product manufacturing, energy-efficient production processes, and ethical labor practices.
Moreover, the importance of certifications such as ENERGY STAR, LEED, and other ‘green’ labels cannot be understated. These certifications not only enhance the credibility of suppliers but also align with the sustainability goals of B2B buyers. For instance, selecting suppliers that utilize recyclable or biodegradable materials in their products can significantly reduce a company’s carbon footprint. Additionally, buyers should seek out suppliers that engage in ethical sourcing practices, ensuring that their products are manufactured in a socially responsible manner. This holistic approach to procurement not only benefits the environment but also enhances brand reputation and market competitiveness.
How Has the Air Cleaner Supplier Market Evolved Over Time?
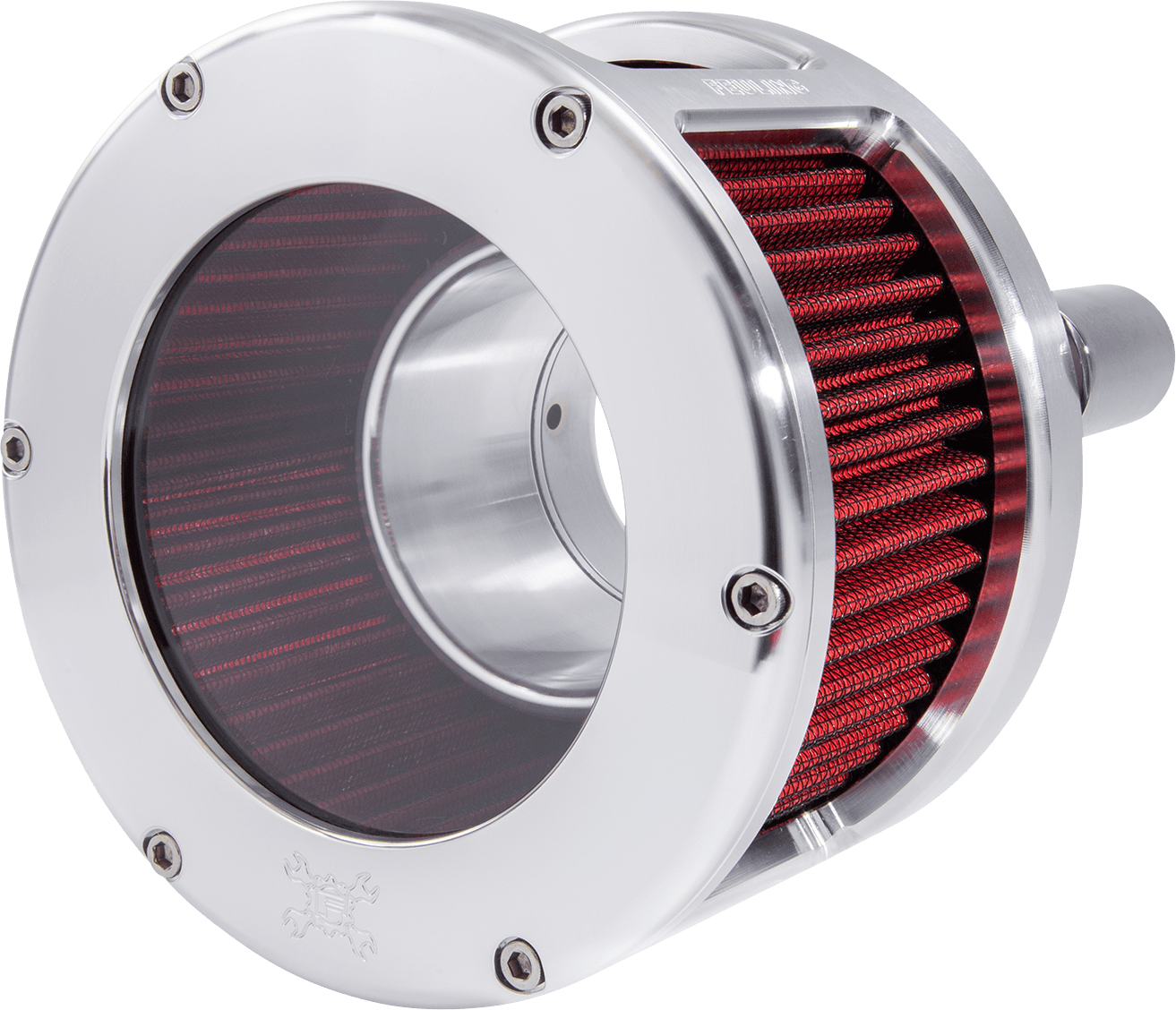
A stock image related to air cleaner supplier.
The air cleaner supplier market has evolved dramatically over the past few decades, transitioning from basic filtration technologies to sophisticated, multi-functional systems. Initially, air purifiers were primarily used in residential settings, but the growing awareness of air quality issues has expanded their application into commercial and industrial sectors.
Technological advancements have led to the introduction of smart air cleaners that utilize real-time data analytics and remote monitoring capabilities. This evolution has paved the way for enhanced efficiency, allowing businesses to maintain compliance with stringent air quality regulations while also addressing health concerns. As air quality continues to be a global priority, the air cleaner supplier market is poised for further innovation and growth, making it essential for B2B buyers to stay informed and adapt their sourcing strategies accordingly.
Frequently Asked Questions (FAQs) for B2B Buyers of air cleaner supplier
-
How do I choose the right air cleaner supplier for my business needs?
Choosing the right air cleaner supplier involves evaluating several critical factors. Start by assessing the supplier’s experience and expertise in the industry, as well as their product range to ensure they offer solutions that meet your specific air quality needs. Consider checking their certifications and compliance with international standards, which can indicate reliability and quality. Additionally, request samples and reviews from other clients, and inquire about their customer service and support capabilities. A thorough vetting process will help you secure a trustworthy supplier that aligns with your business objectives. -
What types of air cleaners are best suited for industrial environments?
For industrial environments, look for air cleaners equipped with HEPA filters, activated carbon, and electrostatic precipitators. HEPA filters can capture 99.97% of particles, making them ideal for environments with dust, smoke, and allergens. Activated carbon filters are effective at removing volatile organic compounds (VOCs) and odors, while electrostatic precipitators help eliminate fine particles. It’s also essential to consider the size and airflow capacity of the air cleaner to ensure it meets the specific air volume requirements of your facility. -
What are the minimum order quantities (MOQ) for air cleaners from suppliers?
Minimum order quantities (MOQ) can vary significantly among air cleaner suppliers, often depending on the type of product and the supplier’s production capabilities. Typically, MOQs can range from 50 to several hundred units for standard models. When negotiating, clarify the MOQ upfront, as this can impact your procurement strategy and inventory management. If you require a smaller quantity, some suppliers may offer flexibility or alternative options, such as ordering through a distributor. -
What payment terms should I expect when sourcing air cleaners internationally?
Payment terms for international transactions can differ based on the supplier’s policies and your negotiation. Common terms include payment in full upfront, a deposit with the balance due upon shipment, or payment via letter of credit. It’s essential to discuss and agree on these terms before finalizing any order. Additionally, be aware of currency exchange rates and potential transaction fees, which can affect the overall cost of procurement. Establishing clear terms will help prevent misunderstandings and ensure a smooth transaction. -
How can I ensure quality assurance (QA) when sourcing air cleaners?
To ensure quality assurance (QA) when sourcing air cleaners, request detailed product specifications and certifications from your supplier. Conduct factory audits or third-party inspections to verify the manufacturing processes and quality control measures in place. Additionally, consider establishing a clear QA protocol that includes testing samples upon arrival and setting performance benchmarks. Regular communication with the supplier about any concerns can also help maintain quality standards throughout the procurement process. -
What logistics considerations should I keep in mind when importing air cleaners?
When importing air cleaners, consider factors such as shipping methods, lead times, and customs regulations. Evaluate whether air freight or sea freight is more suitable based on your budget and urgency. Additionally, research the import duties and taxes applicable in your country, as these can significantly affect total costs. Partnering with a reliable freight forwarder can streamline the logistics process and help you navigate complex customs requirements, ensuring timely delivery of your products.
-
How do I handle warranty and after-sales support for air cleaners?
Handling warranty and after-sales support begins with understanding the warranty terms provided by the supplier. Ensure that you receive documentation outlining the warranty period and coverage details. Establish a communication channel with the supplier for any after-sales inquiries or issues. It’s advisable to discuss potential repair or replacement processes in advance, including how claims are handled and any associated costs. Having a clear understanding of these aspects will help you manage expectations and maintain operational efficiency. -
What factors influence the cost of air cleaners from suppliers?
The cost of air cleaners is influenced by several factors, including the technology used, the materials involved, and the supplier’s production capabilities. Advanced features such as smart technology or enhanced filtration systems can increase the price. Additionally, economies of scale play a role; larger orders may result in lower per-unit costs. Shipping expenses, customs duties, and regional market dynamics can also affect pricing. Understanding these factors will enable you to make informed purchasing decisions and budget accordingly.
Important Disclaimer & Terms of Use
⚠️ Important Disclaimer
The information provided in this guide, including content regarding manufacturers, technical specifications, and market analysis, is for informational and educational purposes only. It does not constitute professional procurement advice, financial advice, or legal advice.
While we have made every effort to ensure the accuracy and timeliness of the information, we are not responsible for any errors, omissions, or outdated information. Market conditions, company details, and technical standards are subject to change.
B2B buyers must conduct their own independent and thorough due diligence before making any purchasing decisions. This includes contacting suppliers directly, verifying certifications, requesting samples, and seeking professional consultation. The risk of relying on any information in this guide is borne solely by the reader.
Strategic Sourcing Conclusion and Outlook for air cleaner supplier
In the evolving landscape of air cleaner suppliers, strategic sourcing emerges as a critical element for international B2B buyers. By prioritizing quality, compliance, and sustainability in their procurement processes, businesses in Africa, South America, the Middle East, and Europe can secure reliable partnerships that enhance their operational efficiency and product offerings. The importance of aligning sourcing strategies with regional regulations and market demands cannot be overstated; this alignment not only mitigates risks but also fosters innovation and responsiveness to customer needs.
As companies increasingly recognize the value of air quality, the demand for effective air cleaning solutions is set to rise. Buyers should leverage data-driven insights and market intelligence to identify suppliers that offer advanced technologies and cost-effective solutions. Engaging in long-term partnerships with reputable manufacturers can lead to shared knowledge and enhanced capabilities.
Looking ahead, international B2B buyers are encouraged to adopt a proactive approach to sourcing air cleaning products. By embracing digital tools and collaborative frameworks, businesses can navigate the complexities of global supply chains and position themselves as leaders in promoting healthier environments. Take the next step in your strategic sourcing journey—evaluate your current suppliers and explore new opportunities that align with your organizational goals.