Discover Top Benefits from a Corner Sofa Manufacturer (2025)
Introduction: Navigating the Global Market for corner sofa manufacturer
In the competitive landscape of furniture manufacturing, sourcing the right corner sofa manufacturer can present a myriad of challenges for B2B buyers, particularly when aiming to meet diverse consumer demands across continents. Buyers from Africa, South America, the Middle East, and Europe face unique obstacles, such as fluctuating import regulations, varying quality standards, and cultural preferences that influence design choices. This guide is designed to demystify the process of finding and partnering with reliable corner sofa manufacturers, offering insights that cater specifically to your regional market needs.
Throughout this comprehensive guide, we will explore various types of corner sofas, their applications in both residential and commercial settings, and the critical factors to consider when vetting potential suppliers. From understanding the cost implications of different manufacturing processes to evaluating the sustainability practices of manufacturers, this resource aims to empower international buyers to make informed purchasing decisions.
By delving into the intricacies of the global corner sofa market, you will gain actionable insights that enhance your sourcing strategy, improve supplier relationships, and ultimately elevate your business offerings. Whether you are based in the bustling markets of Istanbul, the vibrant cities of South America, or the rapidly developing regions of Africa and the Middle East, this guide will equip you with the knowledge necessary to navigate the complexities of sourcing corner sofas effectively.
Understanding corner sofa manufacturer Types and Variations
Type Name | Key Distinguishing Features | Primary B2B Applications | Brief Pros & Cons for Buyers |
---|---|---|---|
Modular Corner Sofas | Customizable sections, versatile configurations | Office spaces, hospitality | Pros: Flexible design; Cons: May require more space. |
Reclining Corner Sofas | Built-in reclining features for comfort | Residential, lounges | Pros: Enhanced comfort; Cons: Higher maintenance. |
Sectional Sofas | Multi-piece units that offer extensive seating | Large family spaces, commercial | Pros: Maximizes seating; Cons: Can be bulky. |
L-shaped Sofas | Traditional design with a right-angle configuration | Small apartments, waiting areas | Pros: Space-efficient; Cons: Limited customization. |
U-shaped Sofas | Extensive seating with a U formation | Event spaces, large gatherings | Pros: Ideal for social settings; Cons: Requires ample space. |
What are the Characteristics of Modular Corner Sofas?
Modular corner sofas are designed with interlocking sections that can be rearranged to fit various spaces. This flexibility allows businesses to customize their seating arrangements based on specific needs, making them ideal for office environments or hospitality sectors where adaptability is crucial. When purchasing, consider the fabric options, ease of assembly, and warranty terms, as these factors can impact long-term satisfaction and usability.
How do Reclining Corner Sofas Enhance Comfort?
Reclining corner sofas come equipped with mechanisms that allow users to lean back and elevate their legs, providing a luxurious seating experience. These sofas are particularly suitable for residential settings and lounges where comfort is paramount. Buyers should evaluate the quality of the reclining mechanism and the durability of the upholstery to ensure they are making a sound investment for high-traffic areas.
Why Choose Sectional Sofas for Large Spaces?
Sectional sofas consist of multiple pieces that can be arranged in various configurations, maximizing seating capacity in large areas. They are especially useful in family rooms or commercial spaces where accommodating large groups is necessary. When considering sectional sofas, buyers should assess the overall size, modularity, and assembly requirements to ensure they fit seamlessly into their designated areas.
What are the Benefits of L-shaped Sofas for Space Efficiency?
L-shaped sofas are characterized by their right-angle design, making them an excellent choice for smaller living spaces or waiting areas. Their ability to fit snugly into corners allows for efficient use of space without sacrificing comfort. B2B buyers should focus on the dimensions and available fabric choices, as these will determine how well the sofa integrates into existing decor.
How Do U-shaped Sofas Facilitate Social Interaction?
U-shaped sofas are designed to promote conversation and social interaction, making them ideal for event spaces and large gatherings. Their expansive seating capacity allows multiple people to sit comfortably together. Buyers should consider the sofa’s dimensions and the required floor space, as these factors will influence the overall layout and functionality of the area where the sofa will be placed.
Key Industrial Applications of corner sofa manufacturer
Industry/Sector | Specific Application of corner sofa manufacturer | Value/Benefit for the Business | Key Sourcing Considerations for this Application |
---|---|---|---|
Hospitality | Hotel lobbies and lounges | Enhances guest experience and aesthetic appeal | Durability, style, and compliance with local regulations |
Corporate Offices | Breakout areas and meeting rooms | Promotes collaboration and comfort for employees | Ergonomics, modularity, and customization options |
Residential Development | Multi-family housing and apartment complexes | Adds value to properties and attracts tenants | Cost-effectiveness, design versatility, and delivery timelines |
Retail | Showrooms and display areas | Improves customer engagement and product visibility | Quality materials, branding alignment, and scalability |
Event Management | Temporary setups for exhibitions and trade shows | Provides functional seating solutions in limited space | Lightweight materials, ease of assembly, and transportability |
How Are Corner Sofas Used in the Hospitality Industry?
In the hospitality sector, corner sofas are essential for hotel lobbies and lounges. They create inviting spaces that enhance guest experiences and contribute to the overall aesthetic appeal of the establishment. International buyers in this sector should prioritize durability and style to withstand heavy usage while ensuring compliance with local regulations regarding fire safety and material standards. Selecting a corner sofa manufacturer that offers customizable options can further align the furniture with the hotel’s branding and design ethos.
What Role Do Corner Sofas Play in Corporate Offices?
Corner sofas are increasingly used in corporate offices, particularly in breakout areas and meeting rooms. They foster a collaborative environment, allowing employees to engage comfortably during discussions. B2B buyers in this sector must consider ergonomics and modularity, ensuring that the sofas can be reconfigured as needed. Customization options are also crucial to align the furniture with the company’s culture and branding, making it a strategic investment for enhancing workplace dynamics.
How Are Corner Sofas Beneficial for Residential Development Projects?
For residential development projects, corner sofas are a key feature in multi-family housing and apartment complexes. They not only provide functional seating but also add value to properties, making them more attractive to potential tenants. Buyers in this sector should focus on cost-effectiveness and design versatility, ensuring that the sofas can fit various layouts and styles. Timely delivery is also critical, as it impacts project timelines and overall tenant satisfaction.
How Do Retail Environments Utilize Corner Sofas?
In the retail industry, corner sofas are utilized in showrooms and display areas to improve customer engagement. They create comfortable spaces for customers to relax while exploring products, ultimately enhancing the shopping experience. B2B buyers should prioritize quality materials that align with their brand image and consider scalability to accommodate future growth. Additionally, ensuring that the sofas are visually appealing can significantly boost product visibility and customer interaction.
Why Are Corner Sofas Important in Event Management?
In event management, corner sofas are frequently employed in temporary setups for exhibitions and trade shows. They provide functional seating solutions in limited spaces, making them ideal for networking and informal meetings. Buyers should look for lightweight materials that are easy to transport and assemble, ensuring efficiency during setup and breakdown. The versatility of these sofas can also allow for various configurations, catering to different event needs.
Related Video: Manufacturing a Larsen Sofa
3 Common User Pain Points for ‘corner sofa manufacturer’ & Their Solutions
Scenario 1: Understanding Quality and Durability Concerns
The Problem:
B2B buyers, especially those operating in markets like Africa and South America, often face significant challenges when it comes to assessing the quality and durability of corner sofas. Many manufacturers may provide attractive designs at competitive prices, but without a clear understanding of the materials and construction methods used, buyers risk investing in products that may not withstand the rigors of commercial use. This is particularly critical in environments where furniture is subject to heavy usage, such as hotels, lounges, and public spaces.
The Solution:
To mitigate these concerns, it’s essential for buyers to conduct thorough due diligence before finalizing any purchases. Start by requesting detailed product specifications and certifications from manufacturers that outline the materials used and the testing methods employed to ensure durability. For instance, inquire about the type of foam, fabric, and frame materials, and seek information about their resistance to wear and tear. Additionally, consider visiting manufacturing facilities when possible or leveraging third-party audits to gain insights into their production processes. Building strong relationships with manufacturers who can provide samples or prototypes can also help in evaluating the quality before making bulk orders.
Scenario 2: Navigating Shipping and Import Challenges
The Problem:
B2B buyers from regions like the Middle East and Europe frequently encounter logistical hurdles when importing corner sofas. These challenges can include high shipping costs, customs delays, and complications in adhering to local regulations regarding furniture imports. Such issues can lead to increased lead times and potential disruption in business operations, especially when timely delivery is critical for projects or retail launches.
The Solution:
To effectively navigate these shipping and import challenges, it is vital to work with manufacturers who have experience in international logistics. Buyers should seek manufacturers that can provide comprehensive support throughout the shipping process, including documentation assistance and guidance on local customs requirements. Establishing a clear timeline for production and shipping is crucial; ensure that manufacturers can meet your deadlines. Additionally, consider partnering with a logistics provider that specializes in furniture transport to manage the complexities of shipping and minimize the risk of delays. Regular communication with both the manufacturer and the logistics partner can help preempt potential issues and keep all parties aligned.
Scenario 3: Customization and Flexibility Limitations
The Problem:
In markets where consumer preferences are highly diverse, such as Turkey and Italy, B2B buyers often face the challenge of limited customization options when sourcing corner sofas. Many manufacturers offer standard designs that may not meet the specific aesthetic or functional requirements of buyers, which can lead to dissatisfaction and lost sales opportunities. This is particularly true for businesses looking to create unique environments that reflect their brand identity.
The Solution:
To address the limitations of customization, buyers should prioritize manufacturers that offer flexible design options and are willing to collaborate on tailored solutions. Engage in discussions about the possibility of modifying existing designs or creating entirely new concepts that align with your brand vision. It’s also beneficial to outline your specific needs regarding dimensions, materials, and colors from the outset. Consider leveraging technology like 3D modeling or virtual design tools that some manufacturers may provide to visualize custom options before production. Finally, establishing long-term partnerships with manufacturers who are responsive to customization requests can foster innovation and ensure that your specific requirements are consistently met.
Strategic Material Selection Guide for corner sofa manufacturer
When selecting materials for corner sofas, manufacturers must consider various factors that influence product performance, durability, and market acceptance. This guide analyzes four common materials used in corner sofa manufacturing: wood, metal, fabric, and leather. Each material has distinct properties, advantages, and limitations that can significantly impact the final product and its reception in diverse international markets.
What Are the Key Properties of Wood in Corner Sofa Manufacturing?
Wood is a traditional choice for corner sofa frames due to its strength and aesthetic appeal. Key properties include high compressive strength, which allows it to support significant weight without deformation. Additionally, wood can be treated for moisture resistance, making it suitable for various climates. However, it may be vulnerable to pests and requires careful selection of types, such as hardwoods like oak or walnut, which offer better durability.
Pros and Cons of Wood:
The primary advantage of wood is its durability and natural beauty, which can enhance the overall design of the sofa. However, it can be more expensive than alternative materials and may require more complex manufacturing processes, including joinery and finishing.
Impact on Application:
Wood frames are compatible with various upholstery options and can be designed to accommodate different styles, from modern to traditional.
Considerations for International Buyers:
Buyers from regions like Europe may prioritize sustainable sourcing and compliance with standards such as FSC certification. In contrast, buyers in Africa and South America may focus on cost-effectiveness and local wood availability.
How Does Metal Influence the Durability of Corner Sofas?
Metal, often used in the structural components of corner sofas, offers excellent strength and stability. Key properties include high tensile strength and corrosion resistance, particularly with materials like stainless steel or aluminum. These metals can withstand heavy loads and are less susceptible to environmental factors compared to wood.
Pros and Cons of Metal:
Metal frames provide a modern aesthetic and can be manufactured with precision, allowing for sleek designs. However, the manufacturing process can be complex and costly, which may increase the final product price.
Impact on Application:
Metal components are ideal for modular designs and can support various upholstery materials, enhancing flexibility in design.
Considerations for International Buyers:
Compliance with international standards such as ASTM for metal strength and durability is essential. Buyers in the Middle East may prefer designs that incorporate metal for their modern appeal, while European buyers may focus on sustainability in sourcing metals.
What Are the Advantages of Fabric in Corner Sofa Upholstery?
Fabric is a popular choice for upholstery in corner sofas due to its versatility and comfort. Key properties include breathability and a wide range of textures and colors. Some fabrics, like polyester blends, offer excellent stain resistance and durability, making them suitable for high-traffic areas.
Pros and Cons of Fabric:
The primary advantage of fabric is its affordability and variety, allowing for customization in design. However, some fabrics may not be as durable as leather or may require more frequent cleaning.
Impact on Application:
Fabric can be used in various climates, but care must be taken to select materials that resist fading and wear in regions with high sun exposure.
Considerations for International Buyers:
Buyers from South America may prioritize cost-effective fabric options, while European buyers may look for eco-friendly materials that comply with standards like Oeko-Tex.
Why Choose Leather for Corner Sofas?
Leather is synonymous with luxury and durability, making it a favored choice in high-end corner sofas. Key properties include excellent tensile strength and resistance to wear and tear, which ensures longevity. Leather also has a unique aesthetic that can elevate the overall design.
Pros and Cons of Leather:
The main advantage of leather is its durability and ease of maintenance; it can be wiped clean and ages beautifully. However, it is typically more expensive than fabric and may not be suitable for all market segments.
Impact on Application:
Leather is compatible with various frame materials and can be used in both modern and traditional designs.
Considerations for International Buyers:
Buyers in Turkey and Italy may have a strong preference for high-quality leather, while those in Africa may seek more affordable options. Compliance with animal welfare standards and sourcing transparency is increasingly important.
Summary Table of Material Selection for Corner Sofa Manufacturers
Material | Typical Use Case for corner sofa manufacturer | Key Advantage | Key Disadvantage/Limitation | Relative Cost (Low/Med/High) |
---|---|---|---|---|
Wood | Frame construction, traditional designs | Durable and aesthetically pleasing | Expensive and complex manufacturing | High |
Metal | Structural components, modern designs | High strength and corrosion resistance | Complex and costly manufacturing | Medium |
Fabric | Upholstery for comfort and variety | Affordable with many design options | May require frequent cleaning | Low |
Leather | High-end upholstery for luxury appeal | Durable and easy to maintain | Generally more expensive | High |
This guide provides a comprehensive overview of the materials used in corner sofa manufacturing, enabling international B2B buyers to make informed decisions based on their specific market needs and compliance requirements.
In-depth Look: Manufacturing Processes and Quality Assurance for corner sofa manufacturer
What Are the Main Stages of the Manufacturing Process for Corner Sofas?
The manufacturing process of corner sofas involves several critical stages, each designed to ensure the final product meets quality standards and customer expectations. Understanding these stages is vital for international B2B buyers looking to establish reliable partnerships with manufacturers.
1. Material Preparation
The first step in the manufacturing process is material preparation. Manufacturers typically source high-quality raw materials such as wood, foam, fabric, and hardware. For B2B buyers, it’s essential to inquire about the sourcing practices, as sustainable and responsibly sourced materials can significantly impact the quality and durability of the corner sofa.
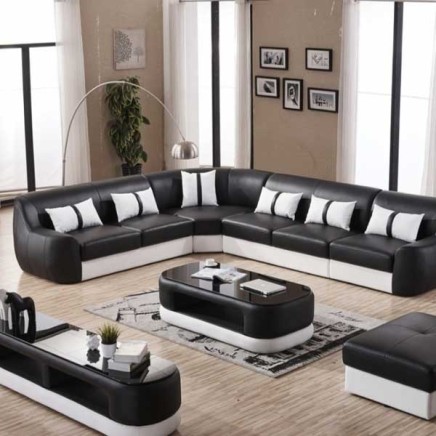
A stock image related to corner sofa manufacturer.
Key Techniques:
– Wood Treatment: Wood components may undergo treatments to prevent pests and enhance durability.
– Foam Selection: Different densities of foam are chosen based on comfort requirements and intended use.
2. Forming
Once the materials are prepared, the next stage is forming. This involves cutting and shaping the materials to create the individual components of the corner sofa.
Key Techniques:
– CNC Machining: This computer-controlled process allows for precision cutting of wood and other materials, ensuring consistency across production runs.
– Sewing and Upholstery: Fabrics are cut and sewn to fit the sofa’s design, often using specialized sewing machines for durability.
How Is Assembly Conducted in Corner Sofa Manufacturing?
The assembly process is where all the individual components come together to form the final product.
3. Assembly
During assembly, manufacturers focus on the structural integrity and aesthetics of the corner sofa. This stage typically includes:
- Frame Assembly: The wooden frame is assembled, ensuring all joints are secure.
- Cushion Attachment: Foam cushions are attached to the frame, often secured with zippers or Velcro for easy removal.
- Upholstery Application: The final fabric is stretched and attached, ensuring a smooth finish.
What Finishing Techniques Are Used for Corner Sofas?
Finishing touches are crucial in the manufacturing process, as they enhance both the appearance and durability of the sofa.
4. Finishing
Finishing techniques can vary widely, but they often include:
- Staining and Sealing: Wooden surfaces may be stained and sealed to enhance appearance and protect against wear and tear.
- Quality Control Checks: Before the sofas are packaged and shipped, a thorough quality check is performed to ensure each unit meets the required specifications.
What Quality Assurance Standards Should B2B Buyers Be Aware Of?
Quality assurance (QA) is a critical aspect of the corner sofa manufacturing process. B2B buyers should be familiar with both international and industry-specific standards that manufacturers adhere to.
Relevant International Standards
- ISO 9001: This standard sets the criteria for a quality management system and is applicable to any organization, regardless of size or industry. Manufacturers certified with ISO 9001 demonstrate a commitment to quality and continuous improvement.
- CE Marking: For products sold in Europe, the CE marking indicates compliance with health, safety, and environmental protection standards.
How Are Quality Control Checkpoints Integrated into the Manufacturing Process?
Quality control checkpoints are essential throughout the manufacturing process to ensure that products meet established standards.
Key Quality Control Checkpoints
-
Incoming Quality Control (IQC): This initial checkpoint involves inspecting raw materials upon arrival. Manufacturers should have protocols to reject substandard materials.
-
In-Process Quality Control (IPQC): During assembly, ongoing inspections are performed to ensure that each stage of the manufacturing process adheres to quality standards. This may include checking the alignment of frames and the quality of stitching.
-
Final Quality Control (FQC): Before shipping, the completed sofas undergo final inspection to verify that they meet the specified design and quality standards.
What Common Testing Methods Are Used in Quality Control?
Manufacturers utilize various testing methods to ensure the durability and safety of corner sofas.
- Durability Testing: Sofas may be subjected to weight tests and repeated use simulations to assess their longevity.
- Material Testing: Fabrics are tested for color fastness, tear strength, and flammability to ensure they meet industry standards.
How Can B2B Buyers Verify a Manufacturer’s Quality Control Practices?
For international B2B buyers, verifying a manufacturer’s quality control practices is crucial to establishing a trustworthy partnership.
Strategies for Verification
- Supplier Audits: Conducting regular audits of potential suppliers can provide insights into their manufacturing processes and quality assurance measures.
- Quality Reports: Requesting detailed quality assurance reports can help buyers understand the manufacturer’s compliance with industry standards.
- Third-Party Inspections: Engaging third-party inspection services can offer an unbiased assessment of the manufacturer’s quality control practices.
What Nuances Should B2B Buyers from Different Regions Consider?
B2B buyers from Africa, South America, the Middle East, and Europe should be aware of specific nuances that can affect their purchasing decisions.
- Regional Standards: Different regions may have varying standards and regulations that manufacturers must comply with. Buyers should familiarize themselves with local requirements to ensure compliance.
- Cultural Preferences: Design preferences can vary significantly across regions. Understanding local tastes can help buyers choose the right products for their markets.
Conclusion: The Importance of Understanding Manufacturing Processes and Quality Assurance
In conclusion, a comprehensive understanding of the manufacturing processes and quality assurance practices is essential for B2B buyers in the corner sofa market. By focusing on material preparation, forming, assembly, and finishing, as well as the various quality control measures in place, buyers can make informed decisions when selecting manufacturers. Engaging in supplier audits and understanding regional nuances will further enhance the buyer’s ability to secure high-quality products that meet their specific needs.
Practical Sourcing Guide: A Step-by-Step Checklist for ‘corner sofa manufacturer’
In the competitive landscape of sourcing corner sofas, it is essential for international B2B buyers to have a structured approach. This checklist serves as a practical guide to streamline your sourcing process, ensuring you find the right manufacturer that meets your specific needs. Follow these steps to make informed decisions and establish successful partnerships.
Step 1: Define Your Technical Specifications
Before initiating the sourcing process, clearly outline your technical specifications. Determine the dimensions, materials, styles, and features you desire in a corner sofa. This clarity will help you communicate effectively with potential suppliers and ensure they can meet your requirements.
- Considerations: Think about the target market’s preferences and any regional standards that may apply, especially in diverse markets like Africa and Europe.
Step 2: Research Potential Suppliers
Conduct thorough research to identify potential corner sofa manufacturers. Utilize online platforms, trade directories, and industry forums to compile a list of candidates.
- Actionable Tips: Look for suppliers with a strong online presence and positive customer reviews. Pay attention to their experience in exporting to your target regions, such as South America or the Middle East.
Step 3: Evaluate Supplier Capabilities
Assess the capabilities of each supplier to ensure they can deliver on your specifications. This includes evaluating their production capacity, technology, and workforce skills.
- Key Questions: Ask about their manufacturing processes, quality control measures, and lead times. A supplier that invests in modern technology is more likely to produce high-quality products consistently.
Step 4: ✅ Verify Supplier Certifications
It’s crucial to verify that potential suppliers hold relevant certifications and comply with international standards. Certifications such as ISO, CE, or local equivalents indicate that the manufacturer meets industry benchmarks.
- Why It Matters: Compliance with standards ensures that the products you receive are safe, durable, and meet quality expectations, which is particularly important in regulated markets.
Step 5: Request Samples and Product Catalogs
Before making a bulk order, request samples and product catalogs from shortlisted suppliers. This step allows you to evaluate the quality, design, and craftsmanship of their offerings firsthand.
- Consideration: Pay attention to the details in the samples, including stitching, material quality, and overall finish. This assessment can help avoid costly mistakes down the line.
Step 6: Negotiate Terms and Conditions
Once you have narrowed down your options, engage in negotiations regarding pricing, payment terms, delivery schedules, and return policies. Establishing clear terms upfront can prevent misunderstandings later.
- Tips for Success: Be transparent about your budget and seek mutually beneficial arrangements. Consider discussing volume discounts if you plan to order in large quantities.
Step 7: Establish Communication Channels
Effective communication is critical for successful sourcing. Ensure that you establish clear communication channels with your chosen supplier, including preferred languages, time zones, and methods of contact.
- Best Practices: Regular updates and open lines of communication can help address any issues promptly and foster a strong working relationship with your supplier.
By following this step-by-step checklist, B2B buyers can streamline their sourcing process for corner sofas, ensuring they select a manufacturer that aligns with their business needs and market demands.
Comprehensive Cost and Pricing Analysis for corner sofa manufacturer Sourcing
When sourcing corner sofas from manufacturers, understanding the comprehensive cost structure is critical for international B2B buyers. The cost components and pricing influencers will provide insights into how to approach negotiations and ensure cost-efficiency.
What Are the Key Cost Components in Corner Sofa Manufacturing?
-
Materials: The choice of materials significantly affects the overall cost. High-quality fabrics, hardwood frames, and premium cushioning materials can increase prices. Additionally, sourcing local versus imported materials can impact costs, particularly for buyers in Africa and South America, where logistics may add to the final price.
-
Labor: Labor costs vary by region. Countries like Turkey and Italy may have higher labor costs due to skilled craftsmanship, while some African nations might offer lower labor costs, albeit potentially at the expense of quality. Understanding labor market dynamics in the manufacturing country can help buyers anticipate labor-related expenses.
-
Manufacturing Overhead: This includes the indirect costs associated with production, such as utilities, rent, and administrative expenses. Buyers should inquire about the manufacturer’s overhead costs, as they can significantly influence pricing.
-
Tooling: For custom designs, tooling costs can add a considerable amount to the initial investment. It’s essential to evaluate whether the manufacturer has the necessary tooling capabilities and what the associated costs will be.
-
Quality Control (QC): Ensuring product quality is paramount. Manufacturers who implement rigorous QC processes may charge higher prices but can provide assurance of product consistency and durability. Buyers should consider the implications of QC on long-term satisfaction and potential returns.
-
Logistics: Shipping costs can vary widely based on distance, shipping methods, and Incoterms. For international buyers, understanding how logistics will impact total costs is crucial. This includes the costs of transportation, customs duties, and warehousing.
-
Margin: Manufacturers typically add a profit margin to cover costs and ensure profitability. The margin can vary based on competition, demand, and the uniqueness of the product.
How Do Price Influencers Affect Corner Sofa Sourcing?
-
Volume/MOQ: Minimum Order Quantities (MOQs) often lead to better pricing per unit. Buyers should assess their purchasing power and consider consolidating orders to meet MOQs, thereby reducing per-unit costs.
-
Specifications and Customization: Custom designs or specific features can increase costs. Buyers should weigh the benefits of customization against the additional expenses, particularly in competitive markets.
-
Materials: The choice of materials can influence not only the cost but also the perceived value of the product. Understanding market trends regarding sustainable or luxury materials can help buyers make informed decisions.
-
Quality and Certifications: Products that meet certain quality certifications may command higher prices but offer better assurance of durability and compliance with international standards. Buyers should evaluate the importance of these certifications in their markets.
-
Supplier Factors: The reputation and reliability of the supplier can affect pricing. Established manufacturers may charge more due to their track record, while newer entrants might offer lower prices to gain market share.
-
Incoterms: The terms of shipping can significantly influence costs. Incoterms define the responsibilities of buyers and sellers in shipping and insurance, impacting final pricing. Buyers should be clear on these terms to avoid unexpected costs.
What Are the Best Practices for International Buyers in Corner Sofa Sourcing?
-
Negotiate Wisely: Understanding the cost structure allows for informed negotiations. Be prepared to discuss each cost component to achieve favorable terms.
-
Focus on Cost-Efficiency: Evaluate total cost of ownership (TCO) rather than just the purchase price. Consider long-term costs like maintenance, shipping, and potential tariffs.
-
Be Aware of Pricing Nuances: Different regions may have unique pricing strategies influenced by local market conditions. Buyers from Europe may expect different pricing models compared to those from Africa or South America.
-
Seek Transparency: Request detailed breakdowns of costs from manufacturers. Transparency can help identify areas for negotiation and ensure fair pricing.
-
Stay Informed: Keep abreast of market trends and economic factors that may influence pricing. Currency fluctuations, material shortages, and changing labor costs can all impact final prices.
Disclaimer
Prices discussed in this section are indicative and may vary based on specific circumstances, supplier negotiations, and market conditions. Always conduct thorough market research and supplier evaluations to obtain the most accurate pricing.
Alternatives Analysis: Comparing corner sofa manufacturer With Other Solutions
When considering the procurement of corner sofas, international B2B buyers must evaluate various manufacturing solutions. Understanding alternatives can lead to more informed purchasing decisions, potentially optimizing costs and enhancing product offerings. Below, we will compare the traditional corner sofa manufacturer with two alternative solutions: modular sofa systems and custom upholstery services.
Comparison Aspect | Corner Sofa Manufacturer | Modular Sofa Systems | Custom Upholstery Services |
---|---|---|---|
Performance | High durability and style; tailored to specific needs | Versatile configurations; adaptable to different spaces | Unique designs; high-quality craftsmanship |
Cost | Higher initial investment, but long-term value | Moderate pricing; flexibility in spending | Variable costs based on design complexity |
Ease of Implementation | Requires lead time for production and delivery | Quick setup; often available off-the-shelf | Longer lead times for design and production |
Maintenance | Low maintenance; built for durability | Moderate maintenance; depends on materials used | Maintenance varies; high-quality materials may require more care |
Best Use Case | Ideal for permanent installations in upscale settings | Suitable for dynamic environments, such as co-working spaces | Best for bespoke projects requiring unique designs |
What Are the Advantages and Disadvantages of Modular Sofa Systems?
Modular sofa systems are an attractive alternative to traditional corner sofa manufacturing. They offer flexibility in design, allowing buyers to customize the arrangement based on the specific layout of a space. This adaptability makes them ideal for environments that may change frequently, such as offices or communal areas. However, while modular systems can be less expensive upfront, they may not provide the same level of durability or aesthetic appeal as a traditional corner sofa. Buyers should consider the long-term implications of investing in modular options, especially if durability is a primary concern.
How Do Custom Upholstery Services Compare?
Custom upholstery services provide a highly personalized approach to seating solutions. They allow businesses to select unique fabrics, colors, and designs that align with their branding or specific aesthetic preferences. The craftsmanship involved often results in high-quality products that can stand out in competitive markets. However, this bespoke service comes at a variable cost, which can be significantly higher than standard manufacturing options. Additionally, the lead times for custom upholstery can be longer, which may not suit businesses needing immediate solutions. Buyers should weigh the benefits of customization against their budget and timeline constraints.
How Can B2B Buyers Choose the Right Solution for Their Needs?
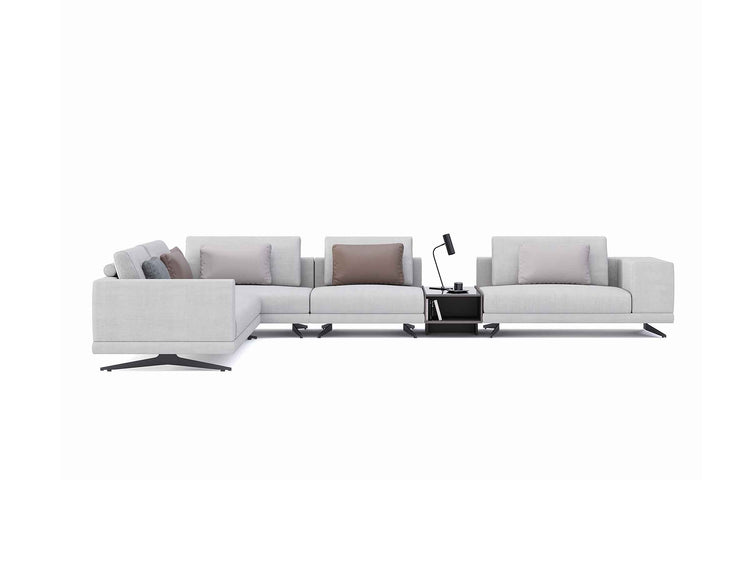
A stock image related to corner sofa manufacturer.
Choosing the right solution for corner sofas involves careful consideration of various factors, including budget, intended use, and design requirements. B2B buyers from Africa, South America, the Middle East, and Europe should assess their specific needs against the alternatives presented. For instance, if flexibility and quick turnaround are priorities, modular sofa systems may be ideal. Conversely, if a unique and high-quality aesthetic is paramount, custom upholstery could be the best route. Ultimately, aligning the choice with the company’s vision, operational demands, and target market will lead to a more satisfactory investment.
Essential Technical Properties and Trade Terminology for corner sofa manufacturer
What Are the Key Technical Properties for Corner Sofas?
When sourcing corner sofas for international markets, understanding the essential technical properties is crucial. Here are several critical specifications that B2B buyers should consider:
1. Material Grade
The material grade of a corner sofa encompasses the quality of the fabrics and frame used. Common materials include hardwood, plywood, and various upholstery fabrics such as leather, polyester, or cotton. Higher material grades often correlate with increased durability and longevity, which is essential for commercial settings such as hotels or offices. Buyers should prioritize sourcing from manufacturers that provide detailed material specifications to ensure they meet local regulations and standards.
2. Load Tolerance
Load tolerance refers to the maximum weight a sofa can support without compromising its structural integrity. This property is particularly important for commercial environments where heavier usage is expected. Understanding the load tolerance can help buyers select the right product for their needs, ensuring safety and longevity. Manufacturers typically provide load tolerance ratings, which should be clearly communicated in product specifications.
3. Dimensions and Configurations
Corner sofas come in various sizes and configurations, impacting their suitability for different spaces. Buyers need to consider the available area in their intended setting and ensure that the sofa dimensions fit accordingly. Additionally, modular options that allow for reconfiguration can be advantageous for adaptability in changing environments. Clear dimensions and configuration options should be a part of the product listing to facilitate informed purchasing decisions.
4. Fire Resistance Rating
In many markets, especially in Europe and North America, fire safety regulations require furniture to meet specific fire resistance standards. Buyers should look for corner sofas that comply with these regulations, as it not only ensures safety but also affects insurance costs. Manufacturers should provide certificates or documentation verifying compliance with fire safety standards.
5. Warranty and After-Sales Support
A comprehensive warranty and robust after-sales support are essential for B2B buyers. This property reflects the manufacturer’s confidence in their product and provides reassurance to buyers regarding potential defects or issues. Warranties typically cover structural integrity and material defects for a specified period, which is crucial for managing long-term investments.
What Are the Common Trade Terms in the Corner Sofa Manufacturing Industry?
Understanding industry jargon is vital for effective communication and negotiation. Here are some common trade terms that B2B buyers should be familiar with:
1. OEM (Original Equipment Manufacturer)
OEM refers to a company that produces parts or equipment that may be marketed by another manufacturer. In the context of corner sofas, buyers may engage with OEMs to customize designs or materials for specific markets. Understanding OEM relationships can enhance product offerings and cater to regional preferences.
2. MOQ (Minimum Order Quantity)
MOQ indicates the smallest number of units that a manufacturer is willing to produce or sell. This term is crucial for B2B buyers as it directly impacts inventory management and cost-efficiency. Buyers should negotiate MOQs that align with their purchasing capabilities and market demand to avoid excess stock.
3. RFQ (Request for Quotation)
An RFQ is a formal process where buyers request pricing and terms from manufacturers for a specific quantity of goods. This process helps buyers compare offers from multiple suppliers, ensuring competitive pricing and favorable terms. Crafting a clear RFQ with detailed specifications can lead to more accurate quotes and better negotiations.
4. Incoterms
Incoterms (International Commercial Terms) define the responsibilities of buyers and sellers in international shipping transactions. Familiarity with these terms helps B2B buyers understand shipping costs, risks, and logistics. Common Incoterms include FOB (Free on Board) and CIF (Cost, Insurance, and Freight), which clarify who is responsible for shipping and insurance during transit.
5. Lead Time
Lead time refers to the period between placing an order and receiving the goods. Understanding lead times is critical for inventory planning and ensuring timely deliveries to customers. Buyers should inquire about lead times during negotiations to align their supply chain needs with production schedules.
By comprehensively understanding these technical properties and trade terms, international B2B buyers can make informed decisions, ensuring they select corner sofas that meet their quality, safety, and operational needs.
Navigating Market Dynamics and Sourcing Trends in the corner sofa manufacturer Sector
What Are the Key Market Dynamics Affecting Corner Sofa Manufacturers?
The corner sofa manufacturing sector is experiencing significant shifts driven by global trends such as urbanization, changing consumer preferences, and technological advancements. As urban populations grow, there is an increasing demand for multifunctional furniture that maximizes limited living spaces. This trend is particularly relevant for international B2B buyers in regions like Africa and South America, where urban housing is often compact.
Emerging technologies are also reshaping the sourcing landscape. Automation in manufacturing processes and the integration of AI for inventory management streamline operations, reduce costs, and enhance product quality. B2B buyers should prioritize partnerships with manufacturers that leverage these technologies to ensure competitive pricing and timely delivery. Additionally, the rise of e-commerce platforms is making it easier for international buyers to source products directly from manufacturers, thereby reducing reliance on intermediaries.
Another crucial dynamic is the increasing importance of customization. Buyers now seek tailored solutions that reflect their brand identity and meet specific market needs. Manufacturers that offer flexible design options and quick turnaround times will gain a competitive edge in attracting B2B clients from diverse regions, including the Middle East and Europe.
How Important is Sustainability and Ethical Sourcing in the Corner Sofa Manufacturing Sector?
Sustainability has become a cornerstone of the corner sofa manufacturing industry, significantly influencing purchasing decisions among B2B buyers. The environmental impact of furniture production is under scrutiny, leading to a demand for sustainable practices. Manufacturers are now expected to use eco-friendly materials and processes, which can reduce waste and energy consumption.
Ethical sourcing is equally critical. Buyers are increasingly concerned about the conditions under which their products are made, leading to a preference for manufacturers with transparent supply chains. Certifications such as FSC (Forest Stewardship Council) and Greenguard can enhance a manufacturer’s credibility and appeal to environmentally conscious buyers.
Investing in sustainable and ethical sourcing not only aligns with global trends but also opens up new market opportunities. Buyers from Europe and the Middle East, in particular, are actively seeking suppliers that prioritize sustainability, making it essential for manufacturers to adopt green practices to stay competitive in the international market.
How Has the Corner Sofa Manufacturing Sector Evolved Over Time?
The corner sofa manufacturing sector has evolved significantly from its early days of traditional craftsmanship to a modern industry characterized by mass production and innovation. Initially, corner sofas were primarily handcrafted, limiting their availability and accessibility. As consumer demand grew, particularly in Europe and North America, manufacturers began to adopt industrial processes to increase output and reduce costs.
In recent years, the focus has shifted towards customization and sustainability, reflecting changing consumer preferences. The introduction of advanced materials and technologies, such as 3D printing and smart fabrics, has further transformed the sector. Today, corner sofas are not only functional but also serve as statement pieces in modern interiors, catering to diverse aesthetic preferences and practical needs. This evolution offers B2B buyers a wide range of options, making it essential to stay informed about the latest trends and innovations in the market.
Frequently Asked Questions (FAQs) for B2B Buyers of corner sofa manufacturer
-
How do I choose the right corner sofa manufacturer for my business needs?
Selecting the right corner sofa manufacturer involves assessing various factors such as production capacity, design capabilities, and material sourcing. Start by evaluating their portfolio to ensure they align with your aesthetic and functional requirements. Additionally, consider their experience in international trade, especially in your target markets like Africa or Europe. Request references from previous clients to gauge reliability and quality. Finally, visiting the factory, if possible, can provide insight into their production processes and quality control measures. -
What customization options are typically available from corner sofa manufacturers?
Most corner sofa manufacturers offer a range of customization options, including fabric choices, colors, dimensions, and configurations. Some may also provide bespoke design services to create unique pieces that fit specific spaces or styles. When discussing customization, ensure to inquire about the lead times and any additional costs associated with tailored designs. This flexibility can significantly enhance your product offering and appeal to diverse customer preferences in various markets. -
What is the minimum order quantity (MOQ) for corner sofas from manufacturers?
Minimum order quantities can vary widely among corner sofa manufacturers, often ranging from 10 to 100 units depending on the manufacturer’s scale and production capabilities. For B2B buyers, understanding the MOQ is crucial for budgeting and inventory management. Some manufacturers may offer lower MOQs for trial orders, while others may require higher quantities for customized pieces. Always clarify the MOQ upfront to avoid misunderstandings later in the procurement process. -
What payment terms should I expect when sourcing corner sofas internationally?
Payment terms can vary by manufacturer and region but typically include options like 30% upfront and 70% upon delivery or net 30/60 days after invoice. It’s essential to negotiate terms that suit your cash flow while ensuring the supplier feels secure in the transaction. Be aware of additional costs such as shipping and customs duties that may arise. Using secure payment methods and considering escrow services can also help mitigate risks in international transactions. -
How can I ensure quality assurance when sourcing corner sofas?
To ensure quality assurance, request detailed product specifications and samples before placing a bulk order. Establish clear quality control standards and communicate them to the manufacturer. Many reputable suppliers will have in-house QA teams or third-party inspection services to verify compliance. Consider conducting regular audits or requiring pre-shipment inspections to guarantee that the products meet your expectations in terms of durability and design. -
What logistics considerations should I keep in mind when importing corner sofas?
Logistics is a critical aspect of importing corner sofas, particularly regarding shipping methods, transit times, and customs clearance. Work closely with your supplier to understand the best shipping options based on your location. Air freight is faster but more expensive, while sea freight is cost-effective for larger orders. Also, ensure that your supplier provides the necessary documentation for customs to avoid delays. Partnering with a reliable freight forwarder can help streamline the process. -
What are the key certifications to look for in a corner sofa manufacturer?
When sourcing corner sofas, look for manufacturers that hold industry certifications such as ISO 9001 for quality management and certifications related to environmental standards like FSC or GREENGUARD. These certifications indicate that the manufacturer adheres to best practices in production and sustainability. Additionally, inquire about compliance with safety standards relevant to your market, such as fire resistance and material safety, especially if you are targeting regions with strict regulations. -
How do I build a long-term relationship with my corner sofa supplier?
Building a long-term relationship with your corner sofa supplier involves consistent communication, mutual respect, and transparent dealings. Regularly provide feedback on product quality and delivery times to foster a collaborative atmosphere. Establishing a partnership mindset, rather than a transactional one, can lead to better pricing, priority service, and more flexibility in future orders. Consider visiting their facility or inviting them to trade shows to strengthen your professional relationship.
Important Disclaimer & Terms of Use
⚠️ Important Disclaimer
The information provided in this guide, including content regarding manufacturers, technical specifications, and market analysis, is for informational and educational purposes only. It does not constitute professional procurement advice, financial advice, or legal advice.
While we have made every effort to ensure the accuracy and timeliness of the information, we are not responsible for any errors, omissions, or outdated information. Market conditions, company details, and technical standards are subject to change.
B2B buyers must conduct their own independent and thorough due diligence before making any purchasing decisions. This includes contacting suppliers directly, verifying certifications, requesting samples, and seeking professional consultation. The risk of relying on any information in this guide is borne solely by the reader.
Strategic Sourcing Conclusion and Outlook for corner sofa manufacturer
As the global market for corner sofas continues to evolve, the importance of strategic sourcing cannot be overstated. For B2B buyers in regions such as Africa, South America, the Middle East, and Europe, understanding the nuances of sourcing high-quality corner sofas can lead to significant cost savings and enhanced customer satisfaction. Key takeaways include the need to evaluate suppliers based on their production capabilities, material quality, and adherence to sustainability practices.
Building strong relationships with manufacturers can also facilitate better negotiation terms and more favorable pricing structures. Additionally, being aware of regional trends and consumer preferences is crucial for making informed purchasing decisions that align with market demands.
Looking ahead, international B2B buyers should leverage technological advancements to streamline sourcing processes and enhance supply chain visibility. Engaging in thorough market research and actively seeking partnerships with reputable manufacturers will position buyers to capitalize on emerging opportunities.
In conclusion, prioritize strategic sourcing as a cornerstone of your procurement strategy, and take proactive steps to explore new avenues for growth. The future of the corner sofa market is bright, and those who adapt and innovate will lead the way.