Discover Top Benefits from a Magnet Manufacturer (2025)
Introduction: Navigating the Global Market for magnet manufacturer
Navigating the global market for magnet manufacturing presents unique challenges for international B2B buyers, particularly those operating in diverse regions such as Africa, South America, the Middle East, and Europe. With the increasing demand for high-quality magnets across various industries—including automotive, electronics, and renewable energy—sourcing the right magnet manufacturer can be daunting. Buyers often grapple with understanding the myriad types of magnets available, their specific applications, and how to vet suppliers effectively.
This comprehensive guide aims to demystify the magnet manufacturing landscape by providing in-depth insights into different magnet types, their applications, and essential factors to consider when selecting a manufacturer. From evaluating supplier credibility to understanding cost structures, this resource equips B2B buyers with the knowledge necessary to make informed purchasing decisions.
By addressing critical questions such as “What types of magnets are best suited for my needs?” and “How do I evaluate the reliability of a magnet supplier?” this guide not only enhances understanding but also empowers buyers to navigate complexities confidently. Whether you are sourcing magnets for innovative projects in Brazil or Turkey, this guide is tailored to support your strategic procurement efforts, ensuring you find the best fit for your business needs.
Understanding magnet manufacturer Types and Variations
Type Name | Key Distinguishing Features | Primary B2B Applications | Brief Pros & Cons for Buyers |
---|---|---|---|
Ferrite Magnet Manufacturers | Cost-effective, non-metallic, good corrosion resistance | Consumer electronics, automotive, toys | Pros: Low cost, lightweight; Cons: Lower magnetic strength compared to rare earth magnets. |
Neodymium Magnet Manufacturers | High magnetic strength, metallic, susceptible to corrosion | Industrial machinery, medical devices, electronics | Pros: Superior performance, compact size; Cons: Higher cost, requires protective coating. |
Alnico Magnet Manufacturers | High-temperature resistance, made of aluminum, nickel, cobalt | Sensors, microphones, electric motors | Pros: Stable performance at high temperatures; Cons: Generally more expensive, lower magnetic strength than neodymium. |
Samarium-Cobalt Magnet Manufacturers | High magnetic strength, excellent thermal stability | Aerospace, military, high-end audio equipment | Pros: Exceptional performance in extreme conditions; Cons: Very expensive, brittle nature. |
Bonded Magnet Manufacturers | Flexible, can be molded into various shapes, made from bonded materials | Automotive, medical devices, consumer products | Pros: Versatile design options, lightweight; Cons: Lower magnetic strength compared to sintered magnets. |
What Are Ferrite Magnet Manufacturers and Their Suitability for B2B Buyers?
Ferrite magnets, produced by ferrite magnet manufacturers, are composed of iron oxide and are known for their cost-effectiveness. They are ideal for applications requiring lightweight materials, such as consumer electronics and toys. When purchasing, B2B buyers should consider the balance between cost and magnetic strength, as ferrite magnets generally offer lower performance compared to other types.
Why Choose Neodymium Magnet Manufacturers for High-Performance Needs?
Neodymium magnets are among the strongest permanent magnets available, making them suitable for industrial machinery and electronics. B2B buyers should evaluate their specific performance requirements against the higher cost associated with these magnets. Additionally, the susceptibility of neodymium to corrosion necessitates protective coatings, which can influence purchasing decisions.
How Do Alnico Magnet Manufacturers Stand Out in the Market?
Alnico magnets are known for their ability to maintain performance at high temperatures, making them ideal for applications like sensors and electric motors. B2B buyers should weigh the advantages of thermal stability against the typically higher cost and lower magnetic strength when considering alnico magnets for their projects.
What Advantages Do Samarium-Cobalt Magnet Manufacturers Offer?
Samarium-cobalt magnets excel in high-temperature and extreme environmental conditions, making them a popular choice in aerospace and military applications. While their superior performance comes at a high price, B2B buyers must assess whether the investment aligns with their application needs and budget constraints.
Why Consider Bonded Magnet Manufacturers for Versatile Applications?
Bonded magnets offer flexibility in design and can be molded into various shapes, making them suitable for diverse applications, including automotive and medical devices. B2B buyers should consider the versatility and lightweight nature of bonded magnets while being mindful of their generally lower magnetic strength compared to sintered alternatives.
Related Video: Buyer’s Guide: Your first neodymium magnet
Key Industrial Applications of magnet manufacturer
Industry/Sector | Specific Application of magnet manufacturer | Value/Benefit for the Business | Key Sourcing Considerations for this Application |
---|---|---|---|
Automotive | Electric Motors for Vehicles | Enhanced efficiency and reduced energy costs | Quality assurance and compliance with industry standards |
Renewable Energy | Wind Turbine Generators | Increased energy output and reliability | Material durability and environmental resistance |
Electronics | Magnetic Sensors in Consumer Electronics | Improved performance and miniaturization | Precision in specifications and global shipping capabilities |
Healthcare | Magnetic Resonance Imaging (MRI) Machines | Enhanced imaging quality and patient safety | Compliance with medical regulations and timely delivery |
Industrial Manufacturing | Magnetic Separators for Material Handling | Increased productivity and waste reduction | Customization options and after-sales support |
How Are Magnets Used in the Automotive Industry?
In the automotive sector, magnet manufacturers supply electric motors that drive various vehicle functions, from power steering to regenerative braking systems. These motors enhance vehicle efficiency, contributing to lower fuel consumption and reduced emissions. For international buyers, particularly from regions like Africa and South America, understanding the specific quality standards and certifications required for automotive components is crucial. Additionally, buyers should consider the manufacturer’s ability to provide ongoing support and parts availability.
What Role Do Magnets Play in Renewable Energy Applications?
Magnet manufacturers are vital to the renewable energy sector, particularly in wind turbine generators. High-performance magnets are essential for converting mechanical energy into electrical energy efficiently. This application not only boosts energy output but also ensures reliability in energy generation. B2B buyers from the Middle East and Europe should focus on sourcing magnets that meet stringent environmental regulations, as well as those that offer long-term durability in harsh weather conditions.
Why Are Magnets Important in Electronics?
In the electronics industry, magnets are integral to the functionality of magnetic sensors, which are used in devices such as smartphones and wearables. These sensors improve device performance and enable miniaturization, allowing for sleeker designs. Buyers from regions like Turkey and Brazil should prioritize precision in magnet specifications and the ability to meet global shipping requirements to ensure timely production and delivery.
How Are Magnets Utilized in Healthcare Technologies?
Magnet manufacturers provide critical components for medical devices, particularly MRI machines, where high-quality magnets are necessary for producing clear and accurate images. The use of advanced magnet technology enhances imaging quality and improves patient safety. B2B buyers in the healthcare sector must ensure that suppliers comply with medical regulations and can deliver products promptly, as delays can significantly impact patient care.
What Benefits Do Magnets Offer in Industrial Manufacturing?
In industrial manufacturing, magnetic separators are widely used to enhance material handling processes by efficiently separating ferrous materials from non-ferrous ones. This application leads to increased productivity and reduced waste, making operations more cost-effective. Buyers should seek manufacturers that offer customization options tailored to specific operational needs, as well as robust after-sales support to maintain equipment performance.
Related Video: How to Manufacture NdFeB Permanent Magnet?
3 Common User Pain Points for ‘magnet manufacturer’ & Their Solutions
Scenario 1: Sourcing Quality Magnets for Unique Applications
The Problem: B2B buyers often face difficulties in sourcing high-quality magnets that meet specific application requirements. For instance, a manufacturing company in Brazil may require neodymium magnets for a new product line but struggles to find a supplier who can provide the exact specifications, including size, strength, and coating. This can lead to project delays, increased costs, and frustration when suppliers offer generic or incompatible products.
The Solution: To overcome this challenge, B2B buyers should begin by clearly defining their magnet specifications, including dimensions, magnetic strength, and environmental conditions (like temperature and humidity). Once specifications are established, buyers can utilize online platforms and industry directories to find reputable magnet manufacturers. Engaging in direct communication with potential suppliers about their unique needs can help ensure the products meet the required standards. Additionally, requesting samples before committing to a larger order can mitigate risks and foster a better understanding of the manufacturer’s capabilities.
Scenario 2: Managing Supply Chain Disruptions in Magnet Procurement
The Problem: Supply chain disruptions can significantly impact the procurement of magnets, particularly for businesses operating in regions like the Middle East or Africa. Factors such as geopolitical instability, customs delays, or unexpected demand surges can lead to inconsistent delivery schedules, causing production halts and financial losses.
The Solution: To effectively manage these risks, B2B buyers should diversify their supplier base. Instead of relying on a single manufacturer, companies can identify multiple suppliers across different regions. This strategy not only spreads risk but also enhances negotiation power. Implementing inventory management systems that allow for better forecasting and stock levels can also help mitigate the impact of delays. Establishing strong relationships with suppliers through regular communication and collaboration can lead to prioritized service during times of disruption.
Scenario 3: Navigating Compliance and Regulatory Challenges in Magnet Manufacturing
The Problem: International B2B buyers often encounter regulatory hurdles when sourcing magnets, especially when it comes to compliance with safety standards and environmental regulations. For instance, a company in Europe may find that the magnets they wish to import do not meet the stringent EU regulations regarding hazardous materials.
The Solution: To navigate these compliance issues, buyers should familiarize themselves with the regulatory requirements in their target markets. This includes understanding local laws regarding material safety and environmental impacts. When engaging with manufacturers, it’s essential to ask for documentation that proves compliance with these regulations, such as Material Safety Data Sheets (MSDS) and certifications. Additionally, partnering with suppliers who have a proven track record of compliance can simplify the procurement process. Regular training and updates on regulatory changes can also help buyers stay informed and adjust their sourcing strategies accordingly.
Strategic Material Selection Guide for magnet manufacturer
When selecting materials for magnet manufacturing, international B2B buyers must consider various factors that affect performance, durability, and cost. Here, we analyze four common materials used in magnet production: Neodymium Iron Boron (NdFeB), Samarium Cobalt (SmCo), Ferrite, and Alnico. Each material has its unique properties, advantages, and limitations that can significantly influence the end product’s suitability for specific applications.
What are the Key Properties of Neodymium Iron Boron (NdFeB) Magnets?
Neodymium Iron Boron (NdFeB) magnets are known for their exceptional strength and high magnetic performance. They typically have a maximum operating temperature of around 80-230°C, depending on the grade. NdFeB magnets also exhibit good corrosion resistance when coated properly.
Pros and Cons:
– Pros: High magnetic strength, lightweight, and compact size make them suitable for various applications, including motors and sensors.
– Cons: They can be brittle and are sensitive to high temperatures, which may limit their use in certain environments. The cost of raw materials can also be high, impacting overall production expenses.
Impact on Application: NdFeB magnets are ideal for applications requiring strong magnetic fields in compact spaces, such as electric vehicles and consumer electronics.
Considerations for International Buyers: Buyers from Africa, South America, the Middle East, and Europe should ensure compliance with international standards like ASTM and JIS. Additionally, they should consider sourcing from suppliers who can provide reliable coatings to enhance corrosion resistance.
How Does Samarium Cobalt (SmCo) Compare in Terms of Durability?
Samarium Cobalt (SmCo) magnets are known for their excellent temperature stability and corrosion resistance, with a maximum operating temperature of about 300°C. They are also less prone to demagnetization compared to NdFeB.
Pros and Cons:
– Pros: High resistance to demagnetization and corrosion, making them suitable for harsh environments.
– Cons: They are more expensive than NdFeB and can be more challenging to manufacture due to their brittle nature.
Impact on Application: SmCo magnets are commonly used in aerospace and military applications where reliability is critical.
Considerations for International Buyers: Buyers should be aware of the higher costs associated with SmCo and ensure that suppliers can meet the necessary quality certifications for specialized applications.
What are the Advantages of Ferrite Magnets for Cost-Effective Solutions?
Ferrite magnets, made from a combination of iron oxide and barium or strontium carbonate, are known for their low cost and good magnetic properties. They typically operate at temperatures up to 250°C.
Pros and Cons:
– Pros: Cost-effective, resistant to demagnetization, and suitable for a wide range of applications.
– Cons: Lower magnetic strength compared to NdFeB and SmCo, which may limit their use in high-performance applications.
Impact on Application: Ferrite magnets are widely used in household appliances, toys, and loudspeakers due to their affordability.
Considerations for International Buyers: Buyers should consider the balance between cost and performance when selecting ferrite magnets, especially for applications requiring high magnetic strength.
Why Choose Alnico Magnets for High-Temperature Applications?
Alnico magnets, composed primarily of aluminum, nickel, and cobalt, are known for their high-temperature stability, with a maximum operating temperature of around 540°C. They also exhibit good corrosion resistance.
Pros and Cons:
– Pros: Excellent thermal stability and good magnetic properties at high temperatures.
– Cons: They are generally more expensive than ferrite magnets and can be less efficient in terms of size-to-strength ratio.
Impact on Application: Alnico magnets are often used in applications such as electric guitar pickups and industrial sensors where high-temperature performance is essential.
Considerations for International Buyers: Buyers should ensure that they are sourcing Alnico magnets from reputable manufacturers who adhere to international quality standards to guarantee performance in critical applications.
Summary Table of Material Selection for Magnet Manufacturing
Material | Typical Use Case for magnet manufacturer | Key Advantage | Key Disadvantage/Limitation | Relative Cost (Low/Med/High) |
---|---|---|---|---|
Neodymium Iron Boron (NdFeB) | Electric vehicles, consumer electronics | High magnetic strength | Brittle, sensitive to heat | High |
Samarium Cobalt (SmCo) | Aerospace, military applications | Excellent temperature stability | Higher cost, challenging to manufacture | High |
Ferrite | Household appliances, toys | Cost-effective, good demagnetization | Lower magnetic strength | Low |
Alnico | Electric guitar pickups, industrial sensors | High-temperature stability | Less efficient in size-to-strength ratio | Medium |
International B2B buyers must carefully evaluate these materials based on their specific application needs, cost considerations, and compliance with relevant standards to ensure optimal performance and reliability in their magnet products.
In-depth Look: Manufacturing Processes and Quality Assurance for magnet manufacturer
What Are the Key Stages in the Manufacturing Process of Magnets?
The manufacturing process for magnets involves several critical stages, each designed to ensure that the final product meets the specifications required by B2B buyers. Understanding these stages can help international buyers assess potential suppliers effectively.
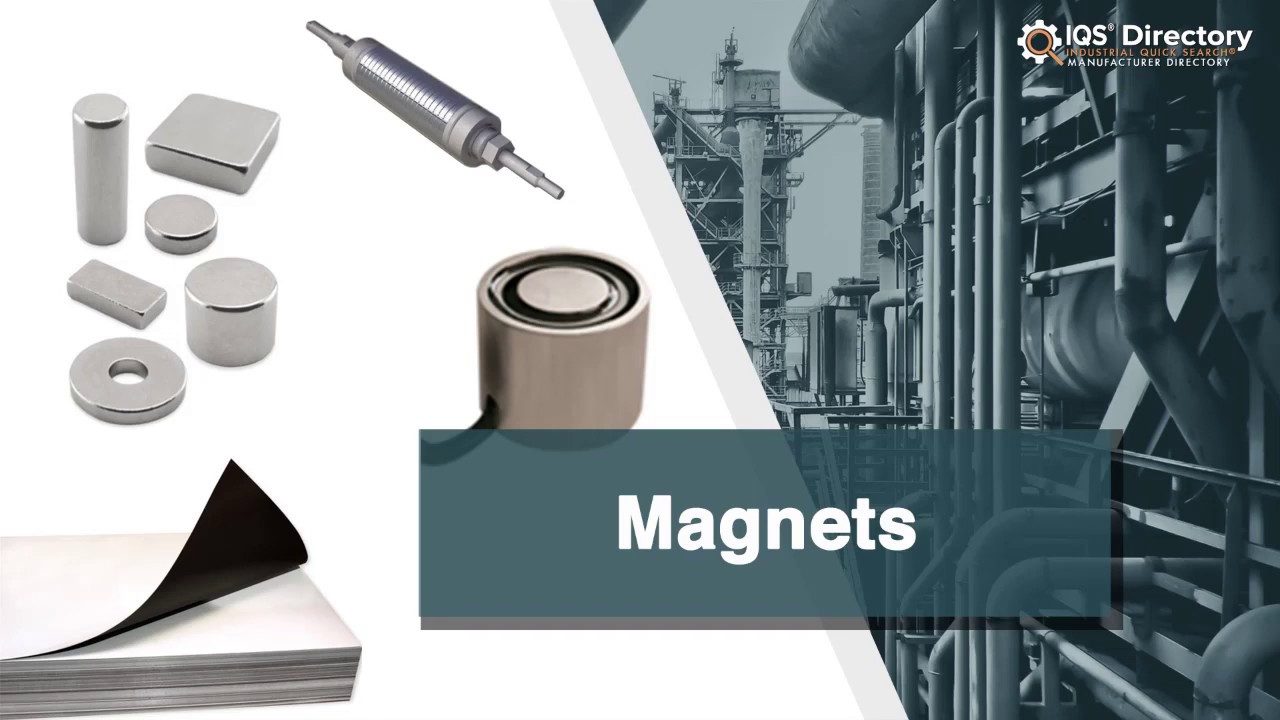
A stock image related to magnet manufacturer.
1. Material Preparation
The first step in magnet manufacturing is material preparation, where raw materials such as iron, cobalt, nickel, and rare earth elements are sourced. The quality of these materials directly affects the performance of the finished magnets. Buyers should inquire about the supplier’s sourcing practices and whether they comply with international standards for material quality.
In this phase, materials undergo purification and alloying processes. For instance, neodymium magnets require high-purity neodymium, iron, and boron. Suppliers often use spectroscopic methods to analyze the composition of the materials, ensuring they meet the required specifications before proceeding to the next stage.
2. Forming Techniques: What Methods Are Used to Shape Magnets?
Forming is the next crucial stage, where the prepared materials are shaped into the desired form. Common techniques include:
- Pressing: Involves compacting the powdered material into a mold under high pressure. This method is widely used for producing sintered magnets, which are known for their high performance.
- Injection Molding: This technique is used for producing bonded magnets, where a magnetic powder is mixed with a polymer and injected into a mold.
- Casting: Less common but used for specific magnet types, such as Alnico magnets. The molten metal is poured into molds and allowed to cool.
During this phase, it’s essential for buyers to understand the types of magnets being produced and the specific techniques employed, as they can significantly influence the final product’s characteristics.
3. Assembly: How Are Magnets Assembled for Specific Applications?
After forming, magnets may require assembly, especially when they are part of a larger system (e.g., motors, sensors). This stage might involve:
- Magnetization: Applying a strong magnetic field to align the magnetic domains within the material, enhancing its magnetic properties.
- Coating: Magnets are often coated to prevent corrosion and improve durability. Common coatings include nickel, zinc, and epoxy.
B2B buyers should verify whether the assembly processes used by suppliers adhere to industry standards, as this impacts the reliability and longevity of the magnets.
4. Finishing: What Processes Ensure Magnets Meet Specifications?
Finishing processes include surface treatments, quality checks, and packaging. These steps ensure that the magnets not only meet physical specifications but are also ready for shipment. Common finishing techniques include:
- Polishing: To achieve a smooth surface finish, which is critical for applications requiring precise tolerances.
- Quality Inspection: Each batch of magnets undergoes rigorous testing to ensure consistency and quality.
Buyers should request details about the finishing processes to ensure they align with their requirements.
How Is Quality Assurance Implemented in Magnet Manufacturing?
Quality assurance (QA) is an integral part of the magnet manufacturing process. Understanding the QA measures taken by suppliers can help B2B buyers mitigate risks associated with product quality.
Relevant International Standards: What Certifications Should Buyers Look For?
Manufacturers often adhere to various international quality standards to demonstrate their commitment to quality. Key standards include:
- ISO 9001: This standard focuses on quality management systems and is applicable to all types of organizations, ensuring consistent quality in products and services.
- CE Marking: Indicates compliance with European health, safety, and environmental protection standards, essential for products sold in Europe.
- API (American Petroleum Institute): Relevant for magnets used in the oil and gas industry, ensuring that products meet industry-specific quality standards.
Buyers should verify that their suppliers possess relevant certifications, as this can serve as a benchmark for quality.
What Are the Key Quality Control Checkpoints?
Quality control (QC) involves several checkpoints throughout the manufacturing process, including:
- Incoming Quality Control (IQC): Materials are inspected upon arrival to ensure they meet specified standards.
- In-Process Quality Control (IPQC): Continuous monitoring during production helps identify and rectify issues in real-time.
- Final Quality Control (FQC): The finished products undergo a comprehensive inspection to verify compliance with specifications.
Each of these checkpoints is critical for maintaining high-quality standards. Buyers should inquire about the QC processes in place at potential suppliers.
What Testing Methods Are Commonly Used for Magnets?
To ensure that magnets meet performance criteria, various testing methods are employed, such as:
- Magnetic Testing: Determines the magnetic strength and direction of the magnets.
- Dimensional Testing: Ensures that magnets conform to specified dimensions and tolerances.
- Environmental Testing: Assesses the magnet’s performance under different environmental conditions (e.g., temperature, humidity).
Buyers should request test reports from suppliers to verify the efficacy of these methods.
How Can B2B Buyers Verify Supplier Quality Control?
For international buyers, particularly from Africa, South America, the Middle East, and Europe, verifying a supplier’s quality control processes is essential. Here are several strategies:
- Supplier Audits: Conduct regular audits of suppliers to assess their manufacturing practices and adherence to quality standards. This can include on-site visits to evaluate processes firsthand.
- Requesting Quality Reports: Suppliers should provide detailed reports on their quality control processes and testing results. This documentation can help buyers understand the reliability of the products.
- Third-Party Inspections: Engaging third-party inspection agencies can provide an unbiased assessment of the supplier’s quality control processes and products.
By employing these strategies, B2B buyers can ensure they partner with reliable magnet manufacturers, minimizing risks associated with poor quality products.
What Are the Quality Control Nuances for International B2B Buyers?
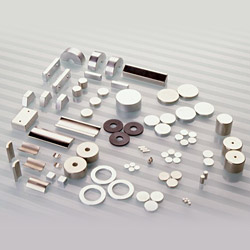
A stock image related to magnet manufacturer.
International buyers need to be aware of specific nuances in quality control that can affect their purchasing decisions. Factors such as local regulations, cultural differences, and logistical challenges can impact quality assurance processes.
- Cultural Understanding: Different regions may have varying standards for quality. Buyers should familiarize themselves with local practices and how they relate to international standards.
- Regulatory Compliance: Understanding local regulations can help buyers ensure that their suppliers meet necessary legal requirements.
- Logistical Considerations: Shipping and handling can affect product quality. Buyers should discuss how suppliers manage logistics to maintain product integrity during transport.
By addressing these nuances, international buyers can make informed decisions when selecting magnet manufacturers.
Practical Sourcing Guide: A Step-by-Step Checklist for ‘magnet manufacturer’
Introduction
Navigating the procurement process for magnet manufacturers can be complex, particularly for international B2B buyers from regions like Africa, South America, the Middle East, and Europe. This practical sourcing guide provides a step-by-step checklist to streamline your decision-making process, ensuring that you identify the right supplier to meet your specific needs.
Step 1: Define Your Technical Specifications
Establishing clear technical specifications is the first critical step in sourcing magnets. This includes determining the type of magnets required—such as neodymium, ferrite, or samarium cobalt—along with their intended applications and performance criteria.
– Considerations: Define dimensions, magnetic strength, temperature resistance, and any specific certifications that may be necessary for your industry.
Step 2: Conduct Market Research
Understanding the market landscape is essential for making informed sourcing decisions. Research potential suppliers to gauge their reputation, product offerings, and market presence.
– Action Items:
– Use platforms like Alibaba or ThomasNet to gather a list of manufacturers.
– Check industry forums and trade publications for insights and reviews.
Step 3: Evaluate Potential Suppliers
Before committing, it’s crucial to vet suppliers thoroughly. Request company profiles, case studies, and references from buyers in a similar industry or region.
– Why It Matters: This step helps mitigate risks associated with quality and reliability.
– What to Look For: Look for suppliers with a proven track record of delivering high-quality products and customer satisfaction.
Step 4: Verify Supplier Certifications
Ensure that the manufacturers you are considering hold the necessary certifications for quality and safety standards. Common certifications include ISO 9001 for quality management and RoHS compliance for environmental safety.
– Importance: Valid certifications indicate adherence to industry standards and can enhance your product’s credibility.
– Checklist: Request copies of their certifications and confirm their validity with the issuing bodies.
Step 5: Request Samples
Before placing a bulk order, request samples of the magnets. This allows you to assess the quality and performance of the products firsthand.
– Testing: Evaluate the samples under actual working conditions to ensure they meet your specifications.
– Feedback Loop: Use this opportunity to communicate any adjustments needed before finalizing your order.
Step 6: Negotiate Terms and Pricing
Once you have identified a suitable supplier, engage in negotiations regarding pricing, payment terms, and delivery schedules.
– Strategies: Be prepared to discuss volume discounts and inquire about shipping costs, especially for international orders.
– Importance of Clarity: Ensure all terms are documented in a formal agreement to avoid misunderstandings later.
Step 7: Establish a Communication Plan
Effective communication is vital throughout the sourcing process. Establish a clear plan for regular updates and feedback between your team and the supplier.
– Best Practices: Use project management tools for tracking progress and maintaining transparency.
– Cultural Sensitivity: Be aware of cultural differences in communication styles, especially when dealing with suppliers from diverse regions.
By following this step-by-step checklist, B2B buyers can enhance their sourcing process for magnet manufacturers, ensuring they find a partner that meets their technical, financial, and operational needs.
Comprehensive Cost and Pricing Analysis for magnet manufacturer Sourcing
What Are the Key Cost Components in Magnet Manufacturing?
When sourcing magnets, understanding the cost structure is crucial for international B2B buyers. The primary cost components include:
-
Materials: The type of magnets (e.g., neodymium, ferrite) significantly impacts the cost. Rare earth materials are typically more expensive due to their scarcity and the complexity of extraction. Buyers should research current market prices for these materials to anticipate costs effectively.
-
Labor: Labor costs vary widely depending on the manufacturing location. Countries with lower labor costs may offer competitive pricing, but it’s essential to assess the skill level and productivity of the workforce.
-
Manufacturing Overhead: This encompasses all indirect costs associated with production, including utilities, rent, and administrative expenses. Understanding the overhead can help buyers gauge the overall pricing strategy of manufacturers.
-
Tooling: Custom tooling for specific magnet shapes or sizes can add significantly to costs. Ensure to factor in these expenses if your requirements include bespoke products.
-
Quality Control (QC): Rigorous QC processes can increase costs but are essential for ensuring product reliability. Certifications such as ISO can also affect pricing, as they require additional investment in quality assurance processes.
-
Logistics: Transportation and shipping costs are critical, especially for international buyers. Factors like distance, shipping method, and local tariffs can influence the final price.
-
Margin: Manufacturer profit margins can vary. Understanding how a supplier calculates their margin can provide insight into their pricing flexibility.
How Do Price Influencers Affect Magnet Sourcing Costs?
Several factors can influence pricing when sourcing magnets:
-
Volume and Minimum Order Quantity (MOQ): Larger orders often lead to reduced per-unit costs. Buyers should negotiate MOQs to align with their purchasing needs while maximizing cost efficiency.
-
Specifications and Customization: Customized magnets with specific dimensions or properties may incur higher costs. Buyers should clearly define their requirements to avoid unexpected charges.
-
Materials and Quality Certifications: The choice of materials directly affects pricing. Additionally, magnets that meet certain quality certifications may be priced higher due to the compliance costs involved.
-
Supplier Factors: The reputation and reliability of suppliers can impact prices. Established suppliers may charge more but offer better quality assurance and service.
-
Incoterms: Understanding Incoterms is crucial for managing logistics costs. Terms like FOB (Free on Board) or CIF (Cost, Insurance, and Freight) determine which party is responsible for shipping and insurance costs, influencing the total price.
What Are the Best Negotiation Tips for B2B Buyers?
To secure the best pricing and terms when sourcing magnets, consider the following tips:
-
Research and Benchmarking: Conduct thorough market research to understand average pricing and identify potential suppliers. Use this information to negotiate favorable terms.
-
Total Cost of Ownership (TCO): Evaluate the TCO, which includes not just the purchase price but also costs related to maintenance, logistics, and disposal. A lower upfront cost may not always be the most economical choice in the long term.
-
Build Relationships: Establishing a good rapport with suppliers can lead to better pricing and terms. Long-term partnerships can yield discounts and priority service.
-
Be Clear on Specifications: Clearly communicate your requirements to avoid misunderstandings that could lead to additional costs. Provide detailed specifications and quality standards upfront.
-
Utilize Volume Discounts: If possible, consolidate orders to leverage volume discounts. Consider joining forces with other businesses to meet higher MOQs and benefit from reduced pricing.
What Are the Pricing Nuances for International Buyers?
International B2B buyers, particularly from regions like Africa, South America, the Middle East, and Europe, should be aware of unique pricing nuances:
-
Currency Fluctuations: Exchange rates can significantly impact costs. Consider negotiating prices in a stable currency to mitigate risks.
-
Import Duties and Taxes: Be aware of any applicable tariffs or taxes that could affect the final price upon importation. Research local regulations to avoid surprises.
-
Cultural Considerations: Different regions may have varying expectations regarding negotiation styles and payment terms. Understanding these cultural nuances can facilitate smoother transactions.
Disclaimer on Indicative Prices
Prices for magnets can fluctuate based on market conditions, material availability, and manufacturing changes. Always consult with multiple suppliers for the most accurate and up-to-date pricing information tailored to your specific requirements.
Alternatives Analysis: Comparing magnet manufacturer With Other Solutions
Understanding Alternatives to Magnet Manufacturing
When considering solutions for magnetic applications, it is essential for international B2B buyers to explore various alternatives to traditional magnet manufacturing. This exploration can lead to more cost-effective, efficient, and innovative solutions tailored to specific industry needs. Below, we compare magnet manufacturers with two viable alternatives: Electromagnets and Permanent Magnet Assemblies.
Comparison Table of Magnet Manufacturing Solutions
Comparison Aspect | Magnet Manufacturer | Electromagnets | Permanent Magnet Assemblies |
---|---|---|---|
Performance | High magnetic strength, stable | Adjustable strength, versatile | High magnetic strength, compact |
Cost | Moderate to high | Generally lower initial cost | Moderate initial cost, less flexible |
Ease of Implementation | Requires specialized setup | Simple installation, plug-and-play | Complex assembly may require expertise |
Maintenance | Low maintenance | Moderate, requires power supply | Minimal, but fragile |
Best Use Case | Precision applications | Industrial lifting, scrap handling | Consumer electronics, motors |
Detailed Breakdown of Alternatives
What Are the Advantages and Disadvantages of Electromagnets?
Electromagnets provide a flexible solution for various applications due to their adjustable magnetic strength. They can be powered on or off, making them ideal for tasks that require temporary magnetic fields, such as lifting heavy metal objects in manufacturing settings. The initial investment is generally lower, and they are easy to install, often requiring only a power source to function. However, they do require ongoing electricity, which can increase operational costs over time. Additionally, their performance can be influenced by the stability of the power supply, making them less reliable in remote locations with inconsistent electricity.
Why Consider Permanent Magnet Assemblies?
Permanent magnet assemblies are another alternative that utilizes permanent magnets arranged in specific configurations to create strong magnetic fields. These assemblies are often used in compact applications, such as in motors or sensors, where space is at a premium. They boast high magnetic strength and low maintenance requirements, making them attractive for long-term applications. However, the complexity of assembly and the need for specialized knowledge can deter some buyers. Furthermore, once installed, their magnetic strength cannot be adjusted, which may limit their versatility in dynamic applications.
How Should B2B Buyers Choose the Right Solution?
When selecting the right magnetic solution, B2B buyers should carefully evaluate their specific needs, including application requirements, budget constraints, and maintenance capabilities. If the application demands a strong, constant magnetic field with low maintenance, traditional magnet manufacturers may be the best choice. On the other hand, if flexibility and cost-effectiveness are priorities, electromagnets may serve better. Permanent magnet assemblies are ideal for compact designs where space is limited but require expertise for assembly and integration.
Ultimately, understanding the strengths and limitations of each alternative will empower buyers to make informed decisions that align with their operational goals and market demands.
Essential Technical Properties and Trade Terminology for magnet manufacturer
What Are the Essential Technical Properties of Magnets for B2B Buyers?
Understanding the critical specifications of magnets is essential for international B2B buyers, especially when sourcing from regions like Africa, South America, the Middle East, and Europe. Here are key properties to consider:
-
Material Grade
Magnets are primarily made from materials like neodymium, samarium-cobalt, ferrite, and alnico. The material grade determines the magnet’s strength, corrosion resistance, and temperature tolerance. For instance, neodymium magnets are known for their high magnetic strength but are prone to corrosion without proper coatings. Buyers should assess their application needs to select the appropriate material grade. -
Magnetic Strength (Gauss/Tesla)
This property indicates the magnet’s ability to attract ferromagnetic materials. It is usually measured in Gauss or Tesla, with higher values signifying stronger magnets. For B2B buyers, understanding the magnetic strength is crucial for applications ranging from industrial machinery to consumer electronics. Ensure to specify the required magnetic strength in your procurement documents to avoid purchasing underperforming magnets. -
Tolerance
Tolerance refers to the allowable deviation in size and shape during the manufacturing process. It is critical for ensuring that magnets fit correctly into assemblies and perform as intended. Tight tolerances can lead to higher manufacturing costs, so buyers should balance the need for precision with budget constraints. Clearly defining tolerance requirements in your specifications can help manufacturers meet your quality expectations. -
Coating and Finish
The coating protects magnets from corrosion and enhances their aesthetic appeal. Common coatings include nickel, zinc, and epoxy. The choice of coating can affect the longevity and performance of the magnet, especially in harsh environments. B2B buyers should evaluate environmental conditions and application requirements when selecting coatings to ensure durability. -
Temperature Resistance
Different magnets have varying temperature tolerances, which can impact their performance in high-heat applications. For example, neodymium magnets typically operate well up to 80°C, while samarium-cobalt can withstand up to 300°C. Buyers must specify temperature resistance in their RFQs to ensure the magnets will function reliably in their intended applications.
What Trade Terminology Should B2B Buyers Know When Sourcing Magnets?
Familiarizing yourself with industry jargon can facilitate smoother negotiations and clearer communications with suppliers. Here are some common terms to understand:
-
OEM (Original Equipment Manufacturer)
This term refers to companies that produce parts or equipment that may be marketed by another manufacturer. When sourcing magnets, knowing if the supplier is an OEM can help buyers assess the quality and compatibility of products with existing systems. -
MOQ (Minimum Order Quantity)
MOQ specifies the smallest quantity of a product that a supplier is willing to sell. Understanding the MOQ is essential for buyers to manage inventory and cash flow effectively. It can vary significantly between manufacturers, so it’s advisable to clarify this in initial discussions. -
RFQ (Request for Quotation)
An RFQ is a document sent to suppliers to request pricing, terms, and conditions for specific products. Including detailed specifications for magnets in your RFQ can yield more accurate quotes and help identify the best supplier based on quality and cost. -
Incoterms (International Commercial Terms)
These are predefined commercial terms published by the International Chamber of Commerce, outlining responsibilities for shipping, insurance, and tariffs between buyers and sellers. Familiarity with Incoterms is vital for international transactions, ensuring both parties understand their obligations. -
Lead Time
This term indicates the time taken from placing an order to delivery. Knowing the lead time is crucial for planning and inventory management, especially in industries with tight production schedules. Communicating your timeframes clearly can help suppliers meet your delivery expectations.
Understanding these technical properties and trade terminologies can empower international B2B buyers to make informed decisions and streamline their sourcing processes, ultimately enhancing their supply chain efficiency.
Navigating Market Dynamics and Sourcing Trends in the magnet manufacturer Sector
What Are the Current Market Dynamics and Key Trends in the Magnet Manufacturing Sector?
The magnet manufacturing sector is experiencing significant transformation driven by technological advancements and global demand shifts. Key trends influencing the market include the rise of electric vehicles (EVs), renewable energy applications, and the miniaturization of electronic devices. As international B2B buyers, particularly from regions like Africa, South America, the Middle East, and Europe, seek to enhance their supply chains, understanding these dynamics is crucial.
The global push for electrification is a primary driver for magnet manufacturers. With the automotive industry transitioning to EVs, demand for high-performance magnets, such as neodymium magnets, is skyrocketing. Furthermore, the growth of wind and solar energy sectors creates a surge in demand for magnets used in generators and other equipment. B2B buyers should align their sourcing strategies with suppliers that innovate in these areas to leverage market opportunities.
Emerging technologies, including automation and smart manufacturing, are also reshaping sourcing strategies. Manufacturers are increasingly adopting Industry 4.0 practices, which optimize production efficiency and reduce costs. For B2B buyers, this means sourcing from suppliers who invest in advanced technologies to ensure competitive pricing and quality assurance. Additionally, the shift towards e-commerce platforms for procurement is changing how businesses interact with suppliers, emphasizing the importance of digital presence and responsiveness.
How Important Is Sustainability and Ethical Sourcing in the Magnet Manufacturing Industry?
Sustainability has become a critical consideration in the magnet manufacturing sector. The environmental impact of magnet production, particularly from rare earth elements, necessitates a focus on ethical sourcing practices. B2B buyers are increasingly scrutinizing their supply chains to ensure compliance with environmental regulations and corporate social responsibility (CSR) standards.
Ethical sourcing involves selecting suppliers who prioritize sustainable practices, such as minimizing waste and reducing carbon footprints. This is particularly pertinent in regions like Europe, where regulatory frameworks are stringent. Buyers from Africa and South America can also benefit from aligning with suppliers who demonstrate a commitment to sustainability, as it can enhance their reputation and marketability.
Moreover, certifications such as ISO 14001 (Environmental Management) and adherence to the Responsible Minerals Initiative (RMI) are becoming essential for suppliers. B2B buyers should seek out manufacturers that hold these certifications, ensuring they source materials responsibly. The use of alternative, environmentally friendly materials in magnet production is also gaining traction, offering an avenue for businesses to differentiate themselves in the marketplace.
What Is the Brief Evolution of the Magnet Manufacturing Sector?
The magnet manufacturing industry has undergone significant evolution since the early 20th century. Initially dominated by traditional ferrite magnets, the sector saw a major shift with the introduction of rare earth magnets in the 1980s, particularly neodymium-iron-boron (NdFeB) magnets. This innovation drastically improved the performance of magnets, leading to their widespread adoption in various applications, from consumer electronics to industrial machinery.
Over the years, the demand for high-performance magnets has surged, driven by advancements in technology and increasing applications in sectors such as renewable energy and automotive. Today, the focus is not only on performance but also on sustainability and ethical sourcing, reflecting changing consumer preferences and regulatory pressures. As the industry continues to evolve, international B2B buyers must stay informed about these trends to effectively navigate the market and make strategic sourcing decisions.
Frequently Asked Questions (FAQs) for B2B Buyers of magnet manufacturer
-
How do I determine the reliability of a magnet manufacturer?
To assess the reliability of a magnet manufacturer, consider their industry certifications, such as ISO 9001 or IATF 16949. Look for customer testimonials and case studies that highlight their track record. Additionally, request samples of their products to evaluate quality firsthand. Engaging in direct communication with their customer service can also provide insights into their responsiveness and willingness to address concerns. Lastly, check their production capabilities and lead times to ensure they can meet your requirements. -
What is the best type of magnet for industrial applications?
The best type of magnet for industrial applications largely depends on the specific use case. Neodymium magnets are ideal for applications requiring strong magnetic force in a compact size, making them suitable for motors and generators. Ferrite magnets are more cost-effective and resistant to corrosion, often used in speaker systems. For high-temperature environments, consider samarium-cobalt magnets, known for their stability. Always evaluate the application needs, such as size, strength, and environmental conditions, to make an informed choice. -
What are the minimum order quantities (MOQ) I should expect from magnet manufacturers?
Minimum order quantities (MOQ) can vary significantly among magnet manufacturers. Typically, MOQs range from 100 to 1,000 pieces for standard products, while custom designs may have higher MOQs due to the additional costs involved in tooling and setup. Before proceeding, clarify with the manufacturer what their specific MOQs are, as well as any potential flexibility based on your order size or future business potential. This can help you manage inventory and cash flow effectively. -
How can I customize magnets to fit my specific needs?
Customizing magnets involves specifying dimensions, shapes, materials, and magnetic strength according to your application requirements. Most manufacturers will work with you to develop prototypes based on your specifications. Provide detailed drawings and any relevant performance criteria to guide the design process. Additionally, inquire about their capabilities for surface treatments or coatings to enhance durability or aesthetic appeal. Be prepared for potential lead times associated with custom orders and ensure clear communication throughout the process. -
What payment terms should I negotiate with a magnet manufacturer?
When negotiating payment terms, consider options such as upfront deposits, net payment terms (e.g., 30, 60, or 90 days), and any discounts for early payments. A standard practice is to pay a percentage upfront, with the balance due upon delivery or acceptance of the goods. Ensure the terms align with your cash flow cycles to avoid disruptions. Additionally, verify the manufacturer’s accepted payment methods, which may include bank transfers, letters of credit, or online payment platforms. -
How do I ensure quality assurance when sourcing magnets internationally?
To ensure quality assurance when sourcing magnets internationally, establish clear specifications and quality standards upfront. Request third-party inspections or certifications to verify product quality before shipment. Many manufacturers offer pre-shipment inspections, which can help identify any issues early. Additionally, consider visiting the manufacturer’s facility if possible, or utilize services from local partners who can perform quality checks on your behalf. Building a strong relationship with the supplier can also facilitate ongoing quality assurance. -
What are the logistics considerations for importing magnets from overseas?
When importing magnets from overseas, consider shipping methods, customs regulations, and lead times. Determine whether air freight or sea freight is more cost-effective based on your urgency and volume. Familiarize yourself with import duties and taxes that may apply, as well as any specific regulations related to magnetic materials. Working with a freight forwarder can simplify the logistics process, ensuring compliance with all shipping and customs requirements. Additionally, keep communication open with your supplier regarding shipment status and tracking. -
How can I effectively communicate my needs to a magnet manufacturer?
Effective communication with a magnet manufacturer begins with providing clear and detailed specifications regarding your requirements. Use technical drawings and examples to illustrate your needs. Be explicit about your intended application, any performance criteria, and timelines for delivery. Establish a point of contact for ongoing discussions and be open to feedback from the manufacturer, as they may offer insights that enhance product performance or reduce costs. Regular updates and check-ins can also help ensure alignment throughout the production process.
Important Disclaimer & Terms of Use
⚠️ Important Disclaimer
The information provided in this guide, including content regarding manufacturers, technical specifications, and market analysis, is for informational and educational purposes only. It does not constitute professional procurement advice, financial advice, or legal advice.
While we have made every effort to ensure the accuracy and timeliness of the information, we are not responsible for any errors, omissions, or outdated information. Market conditions, company details, and technical standards are subject to change.
B2B buyers must conduct their own independent and thorough due diligence before making any purchasing decisions. This includes contacting suppliers directly, verifying certifications, requesting samples, and seeking professional consultation. The risk of relying on any information in this guide is borne solely by the reader.
Strategic Sourcing Conclusion and Outlook for magnet manufacturer
In conclusion, the strategic sourcing of magnets offers substantial opportunities for international B2B buyers, especially those from Africa, South America, the Middle East, and Europe. By prioritizing quality, sustainability, and supplier partnerships, businesses can enhance their operational efficiency and product offerings.
Why is Strategic Sourcing Crucial for Magnet Procurement?
Emphasizing strategic sourcing allows companies to mitigate risks associated with supply chain disruptions while ensuring they remain competitive in a fast-evolving market. Buyers should focus on understanding supplier capabilities, certifications, and innovations that align with their specific industry needs.
What Should International Buyers Consider Moving Forward?
As the demand for high-performance magnets continues to rise, it is essential for buyers to stay informed about technological advancements and emerging market trends. Engaging with reputable magnet manufacturers and participating in industry forums can provide invaluable insights into new applications and materials.
How Can You Take Action Today?
We encourage international B2B buyers to actively seek out partnerships with trusted magnet manufacturers and explore new sourcing strategies that align with their business objectives. By doing so, you will not only enhance your supply chain resilience but also position your company for sustainable growth in the global marketplace.