Discover Top Benefits from a Sealing Machine Manufacturer (2025)
Introduction: Navigating the Global Market for sealing machine manufacturer
In today’s rapidly evolving global market, sourcing the right sealing machine manufacturer can be a daunting task for international B2B buyers. The complexity of various sealing technologies, coupled with the need for compliance with regional standards, creates significant challenges, especially for businesses in Africa, South America, the Middle East, and Europe. This guide is designed to demystify the process of selecting a sealing machine manufacturer by providing a comprehensive overview of the types of machines available, their applications across different industries, and essential criteria for supplier vetting.
Navigating the intricate landscape of sealing machine options—ranging from vacuum sealers to heat sealers—requires an understanding of not only the machinery but also the specific needs of your business. This guide will empower B2B buyers with actionable insights into cost considerations, sourcing strategies, and supplier assessment methods. By focusing on these critical areas, we aim to equip you with the knowledge necessary to make informed purchasing decisions, ensuring that you choose a sealing machine manufacturer that aligns with your operational requirements and quality standards.
With tailored information for diverse markets, including key insights for buyers in Kenya, the UAE, and beyond, this resource serves as a valuable tool to enhance your procurement strategy in the global sealing machinery landscape.
Understanding sealing machine manufacturer Types and Variations
Type Name | Key Distinguishing Features | Primary B2B Applications | Brief Pros & Cons for Buyers |
---|---|---|---|
Continuous Sealing Machines | Operate in a continuous flow; high-speed sealing | Food packaging, pharmaceuticals | Pros: High efficiency, suitable for bulk. Cons: Higher initial investment. |
Vacuum Sealing Machines | Removes air to extend shelf life; often chamber-based | Meat processing, electronics packaging | Pros: Excellent preservation, reduces spoilage. Cons: Slower cycle time. |
Induction Sealing Machines | Uses electromagnetic induction for sealing | Beverage, cosmetic, and pharmaceutical | Pros: Tamper-evident seals, versatile. Cons: Requires specific container types. |
Manual Sealing Machines | Operated by hand; suitable for low volume | Small-scale producers, artisanal products | Pros: Cost-effective, easy to use. Cons: Labor-intensive, less consistent. |
Semi-Automatic Sealing Machines | Combination of manual and automatic features | Medium-scale operations, flexible packaging | Pros: Balances efficiency and cost. Cons: Requires operator training. |
What Are the Characteristics of Continuous Sealing Machines?
Continuous sealing machines are designed for high-volume production, allowing for the sealing of bags and pouches in a continuous flow. They are particularly suitable for industries such as food packaging and pharmaceuticals, where speed and efficiency are critical. When purchasing, buyers should consider the machine’s sealing speed, temperature control capabilities, and compatibility with various materials. The initial investment may be higher, but the return on investment can be significant for businesses with large production runs.
How Do Vacuum Sealing Machines Work and What Are Their Advantages?
Vacuum sealing machines are ideal for applications that require extended shelf life, such as meat processing and electronics packaging. These machines remove air from the packaging, thereby reducing oxidation and spoilage. Buyers should assess the machine’s capacity, sealing speed, and maintenance requirements. While vacuum sealers offer excellent preservation, they typically operate at a slower cycle time compared to continuous machines, which may impact production rates.
What Makes Induction Sealing Machines Unique?
Induction sealing machines utilize electromagnetic induction to create hermetic seals, making them suitable for a variety of industries, including beverages, cosmetics, and pharmaceuticals. The key advantage is the ability to produce tamper-evident seals, enhancing product security. Buyers should consider the compatibility of the sealing technology with their container types and the potential need for specialized training. Though versatile, these machines can be more complex to integrate into existing production lines.
Who Should Consider Manual Sealing Machines?
Manual sealing machines are primarily designed for low-volume production and are often used by small-scale producers and artisans. They are easy to operate and cost-effective, making them an attractive option for startups or niche markets. However, buyers should be aware that these machines require more labor and may not provide the consistent quality of automated options. Consideration of production volume and labor costs is crucial when evaluating this type of machine.
What Are the Benefits of Semi-Automatic Sealing Machines?
Semi-automatic sealing machines offer a balance between efficiency and cost, making them suitable for medium-scale operations. They combine manual input with automated features, allowing for flexibility in packaging processes. When evaluating these machines, buyers should focus on operator training requirements, machine reliability, and the ability to accommodate various package sizes. While they can enhance productivity, a proper assessment of workflow integration is essential for optimal performance.
Related Video: Sealing Machine Band Sealer
Key Industrial Applications of sealing machine manufacturer
Industry/Sector | Specific Application of Sealing Machine Manufacturer | Value/Benefit for the Business | Key Sourcing Considerations for this Application |
---|---|---|---|
Food and Beverage | Packaging of perishable goods | Extends shelf life and reduces waste | Compliance with food safety regulations, durability, and ease of cleaning |
Pharmaceuticals | Sealing vials and syringes | Ensures product integrity and safety | Sterility requirements, precision, and compatibility with various materials |
Cosmetics and Personal Care | Sealing cosmetic containers | Enhances product appeal and prevents leakage | Customization options, aesthetic design, and material compatibility |
Electronics | Sealing electronic components | Protects against moisture and dust | Material specifications, heat resistance, and compliance with industry standards |
Chemical Industry | Sealing chemical drums and containers | Prevents spills and ensures safety | Chemical compatibility, robustness, and regulatory compliance |
How Are Sealing Machines Used in the Food and Beverage Industry?
In the food and beverage sector, sealing machines are crucial for packaging perishable goods such as meats, dairy, and baked products. These machines create airtight seals that extend the shelf life of products, thereby reducing waste and ensuring food safety. International buyers, particularly from regions like Africa and South America, must consider compliance with local food safety regulations, the durability of the sealing materials, and the ease of cleaning to meet hygiene standards.
What Role Do Sealing Machines Play in Pharmaceuticals?
Sealing machines are indispensable in the pharmaceutical industry for sealing vials, syringes, and other containers that hold sensitive medications. These machines ensure product integrity and safety by providing airtight seals that prevent contamination. Buyers from the Middle East and Europe need to focus on sterility requirements, precision sealing capabilities, and the compatibility of sealing materials with various drug formulations to ensure compliance with stringent regulations.
How Are Sealing Machines Utilized in the Cosmetics and Personal Care Sector?
In the cosmetics and personal care industry, sealing machines are used to package products such as creams, lotions, and serums. They not only enhance product appeal with visually appealing seals but also prevent leakage, which is crucial for maintaining product integrity. For B2B buyers in Africa and Europe, sourcing considerations should include customization options for branding, aesthetic design, and the compatibility of sealing materials with various cosmetic formulations.
What Are the Applications of Sealing Machines in Electronics?
Sealing machines in the electronics sector are employed to seal components and assemblies, providing protection against moisture and dust. This is vital for ensuring the longevity and reliability of electronic devices. Buyers, especially from the Middle East and South America, should prioritize material specifications that meet environmental conditions, heat resistance to prevent damage during operation, and compliance with industry standards to ensure product safety.
How Do Sealing Machines Benefit the Chemical Industry?
In the chemical industry, sealing machines are critical for sealing drums and containers that hold hazardous materials. These machines prevent spills and ensure safety during storage and transportation. International B2B buyers, particularly from regions like Africa and South America, must consider chemical compatibility of sealing materials, robustness to withstand harsh conditions, and compliance with safety regulations to mitigate risks associated with handling chemicals.
Related Video: How to use FR-900 Continuous Sealing Machine
3 Common User Pain Points for ‘sealing machine manufacturer’ & Their Solutions
Scenario 1: Inconsistent Sealing Quality Leads to Product Losses
The Problem: One of the most pressing challenges faced by B2B buyers is the inconsistency in sealing quality, which can lead to product spoilage or contamination. For manufacturers in sectors like food and beverage or pharmaceuticals, this inconsistency can result in significant financial losses, customer dissatisfaction, and potential regulatory issues. For instance, a company in Kenya may find that their sealing machines are unable to maintain uniform pressure, leading to leaks in packaged goods. This not only compromises the product but also damages the brand’s reputation in a competitive market.
The Solution: To address this pain point, B2B buyers should prioritize sourcing sealing machines with advanced monitoring and control systems. When evaluating potential manufacturers, inquire about features such as real-time feedback mechanisms and automated adjustments based on environmental conditions. Additionally, investing in training for staff on proper machine operation can significantly reduce errors. Collaborating with manufacturers that offer ongoing support and maintenance services can also ensure that the machines operate at optimal levels. Regular calibration and quality checks can further enhance sealing consistency, thereby minimizing waste and maximizing product integrity.
Scenario 2: High Operational Costs Due to Inefficient Equipment
The Problem: Many businesses struggle with high operational costs associated with outdated or inefficient sealing machines. This is particularly relevant for companies in South America, where economic pressures necessitate tighter budget controls. A manufacturer may find that their older machines consume excessive energy or require frequent repairs, leading to increased downtime and operational inefficiencies. This scenario not only affects profitability but also hampers the ability to scale production.
The Solution: To combat high operational costs, buyers should consider investing in energy-efficient sealing machines that utilize the latest technology. When negotiating with manufacturers, request detailed specifications on energy consumption and maintenance requirements. Additionally, consider purchasing machines that come with warranties and service packages to mitigate unexpected repair costs. Conducting a cost-benefit analysis can help identify the long-term savings associated with upgraded equipment. Furthermore, exploring leasing options may provide a more flexible financial solution, allowing companies to access cutting-edge technology without the burden of upfront capital expenditure.
Scenario 3: Difficulty in Sourcing Spare Parts and Support
The Problem: A common pain point for B2B buyers is the challenge of obtaining spare parts and technical support for sealing machines, especially in regions like the Middle East where supply chains can be disrupted. If a sealing machine breaks down and parts are not readily available, it can lead to significant production delays. This is particularly concerning for businesses that operate on tight delivery schedules, as any downtime can result in contractual penalties and loss of customer trust.
The Solution: To alleviate this issue, buyers should partner with sealing machine manufacturers that have a robust supply chain and local service networks. Before finalizing a purchase, inquire about the availability of spare parts and the manufacturer’s commitment to after-sales support. Establishing a relationship with manufacturers who have local representatives can also facilitate quicker response times for maintenance and repairs. Additionally, consider keeping a small inventory of critical spare parts on-site, especially for high-wear components. This proactive approach can minimize downtime and ensure smoother operations, ultimately leading to better service delivery and client satisfaction.
Strategic Material Selection Guide for sealing machine manufacturer
What Are the Key Materials Used in Sealing Machines?
When selecting materials for sealing machines, manufacturers often consider several factors, including performance characteristics, cost, and application compatibility. Below is an analysis of four common materials used in sealing machine manufacturing, focusing on their properties, advantages, disadvantages, and implications for international B2B buyers.
How Does Rubber Perform as a Material for Sealing Machines?
Rubber is a widely used material in sealing applications due to its excellent flexibility and resilience. It can withstand a range of temperatures, typically from -40°C to 120°C, depending on the specific type of rubber. Additionally, rubber exhibits good resistance to water and various chemicals, making it suitable for many sealing environments.
Pros & Cons:
Rubber’s durability and low cost make it a popular choice. However, its susceptibility to degradation from UV light and ozone can limit its lifespan in outdoor applications. Furthermore, manufacturing complexity can vary based on the type of rubber used, which may affect production timelines.
Impact on Application:
Rubber seals are particularly effective in applications involving water and light oils. However, they may not be suitable for high-temperature or aggressive chemical environments, which could lead to premature failure.
Considerations for International Buyers:
For buyers in regions like Africa and the Middle East, it is crucial to ensure that the rubber used complies with local standards (e.g., ASTM or DIN). Additionally, sourcing rubber from suppliers with certifications can help mitigate risks associated with material quality.
What Role Does PTFE Play in Sealing Machine Applications?
Polytetrafluoroethylene (PTFE) is renowned for its exceptional chemical resistance and thermal stability, withstanding temperatures up to 260°C. Its low friction properties make it ideal for dynamic sealing applications, reducing wear and tear on components.
Pros & Cons:
The key advantage of PTFE is its compatibility with a wide range of chemicals, making it suitable for harsh environments. However, PTFE can be more expensive than other materials, and its manufacturing process is more complex, which may lead to longer lead times.
Impact on Application:
PTFE is particularly effective in applications involving aggressive chemicals, such as acids and solvents. Its non-stick properties also make it suitable for food processing and pharmaceutical applications.
Considerations for International Buyers:
Buyers from Europe and South America should be aware of the specific grades of PTFE that meet industry standards. Compliance with regulations, such as those set by the European Union, is essential for ensuring product safety and market access.
Why Is Stainless Steel a Preferred Choice for Sealing Machines?
Stainless steel is favored for its strength, durability, and corrosion resistance. It can withstand high pressures and temperatures, making it suitable for demanding sealing applications. Common grades, such as 304 and 316, offer varying levels of corrosion resistance, with 316 being more suitable for marine or chemical environments.
Pros & Cons:
The primary advantage of stainless steel is its longevity and ability to maintain structural integrity under extreme conditions. However, it is generally more expensive than other materials, and its manufacturing can be complex, requiring specialized equipment.
Impact on Application:
Stainless steel seals are ideal for applications in the food and beverage industry, pharmaceuticals, and oil and gas sectors, where hygiene and durability are critical.
Considerations for International Buyers:
For buyers in regions like the UAE and Kenya, understanding the specific standards for stainless steel (e.g., ASTM A240) is crucial. Sourcing from suppliers who adhere to international quality standards can enhance reliability.
How Does Nylon Compare as a Material for Sealing Machines?
Nylon is a versatile engineering plastic known for its strength and abrasion resistance. It can operate effectively at temperatures up to 120°C and offers good chemical resistance, though it is not suitable for strong acids or bases.
Pros & Cons:
Nylon is lightweight and cost-effective, making it an attractive option for many applications. However, its moisture absorption can lead to dimensional changes, which may affect sealing performance over time.
Impact on Application:
Nylon seals are commonly used in applications involving oils and greases, but they may not perform well in high-humidity environments.
Considerations for International Buyers:
International buyers should ensure that the nylon used meets local standards and is sourced from reputable manufacturers to avoid quality issues.
Summary Table of Material Selection for Sealing Machines
Material | Typical Use Case for sealing machine manufacturer | Key Advantage | Key Disadvantage/Limitation | Relative Cost (Low/Med/High) |
---|---|---|---|---|
Rubber | General sealing for water and light oils | Cost-effective and durable | Degrades under UV light | Low |
PTFE | Chemical processing and food applications | Excellent chemical resistance | Higher cost and complex mfg | High |
Stainless Steel | Food, beverage, and oil & gas industries | Strong and corrosion-resistant | Expensive and complex to manufacture | High |
Nylon | Sealing in oil and grease applications | Lightweight and cost-effective | Moisture absorption affects performance | Medium |
This strategic material selection guide provides international B2B buyers with valuable insights into the materials used in sealing machines, helping them make informed decisions based on their specific application needs and regional standards.
In-depth Look: Manufacturing Processes and Quality Assurance for sealing machine manufacturer
What Are the Key Stages in the Manufacturing Process of Sealing Machines?
The manufacturing process of sealing machines involves several crucial stages that ensure the final product meets both functional and quality standards. Understanding these stages is essential for international B2B buyers, especially those from Africa, South America, the Middle East, and Europe.
1. Material Preparation
The first stage in manufacturing sealing machines is material preparation. High-quality materials such as stainless steel, aluminum, and specialized plastics are commonly used. Buyers should look for suppliers who source materials from reputable vendors and can provide certificates of authenticity and compliance. This guarantees that the raw materials meet industry standards, which is particularly important for buyers in regions with stringent regulations.
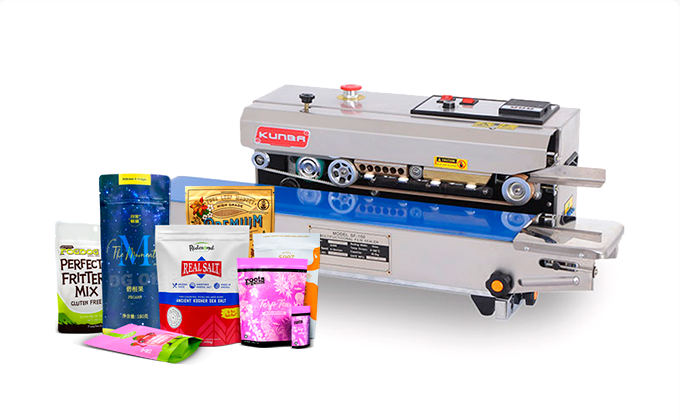
A stock image related to sealing machine manufacturer.
2. Forming Techniques
Forming is the next critical step where materials are shaped into specific components of the sealing machine. Common techniques include stamping, bending, and welding. Advanced manufacturers may also use Computer Numerical Control (CNC) machines for precision forming. International buyers should inquire about the forming techniques used, as this can impact the machine’s durability and performance.
3. Assembly Process
The assembly process involves bringing together all the components manufactured in the previous stages. This is typically done using automated assembly lines that enhance efficiency and reduce human error. For B2B buyers, it’s vital to understand the assembly techniques employed, such as the use of robotics or manual labor, as this can influence lead times and cost.
4. Finishing Techniques
Finishing includes processes such as surface treatment, coating, and painting, which not only enhance the aesthetic appeal of sealing machines but also protect them from environmental factors. Buyers should ask suppliers about the finishing techniques used, as these can significantly affect the longevity and performance of the machines in diverse climates, particularly in regions like Africa and the Middle East.
How Is Quality Assurance Implemented in Sealing Machine Manufacturing?
Quality assurance (QA) is a critical component that ensures the reliability and efficiency of sealing machines. Understanding the quality assurance measures in place can help B2B buyers make informed decisions.
Relevant International Standards for Quality Assurance
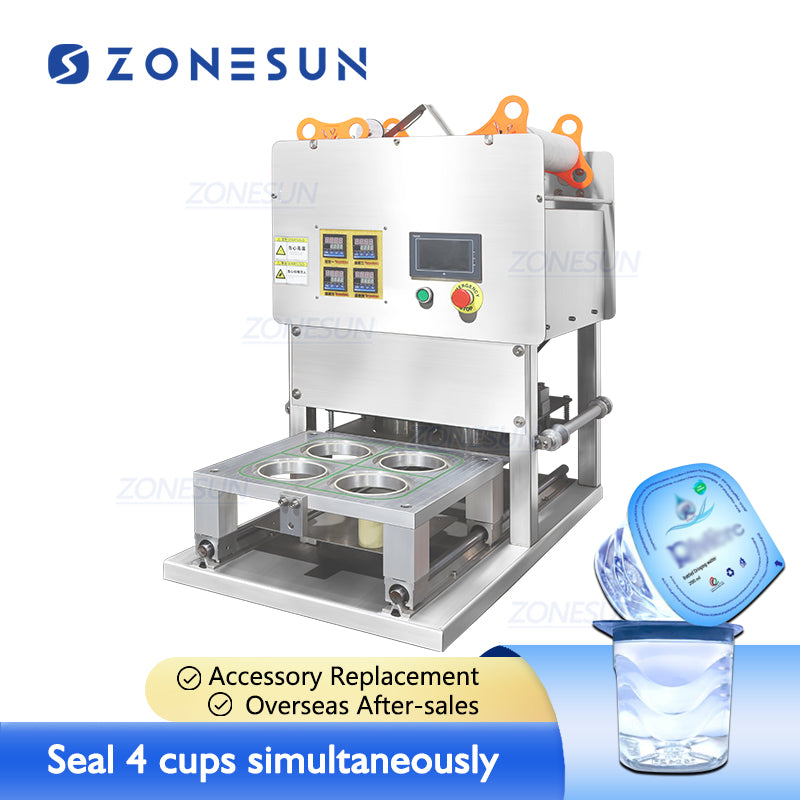
A stock image related to sealing machine manufacturer.
International standards such as ISO 9001 are essential in the manufacturing of sealing machines. ISO 9001 sets forth criteria for a quality management system (QMS) that can enhance customer satisfaction and operational efficiency. In addition, industry-specific certifications like CE marking (for compliance with EU safety standards) and API certification (for equipment used in the petroleum and natural gas industry) are important indicators of quality. Buyers should verify that their suppliers possess these certifications to ensure compliance with international regulations.
What Are the Key Quality Control Checkpoints?
Quality control (QC) consists of several checkpoints throughout the manufacturing process:
-
Incoming Quality Control (IQC): This involves the inspection of raw materials and components before production begins. Buyers should request IQC reports to ensure that only high-quality materials are used.
-
In-Process Quality Control (IPQC): This step monitors the production process itself, ensuring that any defects are caught early. Buyers can ask for detailed reports on IPQC measures implemented by suppliers.
-
Final Quality Control (FQC): Before shipping, the finished sealing machines undergo FQC. This includes functional tests and performance evaluations to ensure they meet specifications. B2B buyers should request FQC documentation as part of their due diligence.
What Common Testing Methods Are Used for Sealing Machines?
Several testing methods are employed to ensure the quality and reliability of sealing machines:
-
Functional Testing: This assesses whether the machine performs its intended tasks under various conditions. Buyers should inquire about the testing protocols used.
-
Durability Testing: This simulates long-term use to evaluate the machine’s lifespan and resilience. Understanding the durability testing methods can help buyers gauge how well the machine will perform in their specific operational environments.
-
Safety Testing: Compliance with safety standards is paramount. Buyers should ensure that suppliers conduct rigorous safety tests and can provide documentation to that effect.
How Can B2B Buyers Verify Supplier Quality Control Measures?
Verification of a supplier’s quality control measures is crucial for B2B buyers to ensure they are investing in reliable products. Here are some actionable steps:
Conducting Supplier Audits
Performing supplier audits is one of the most effective ways to verify quality control practices. This involves on-site inspections of the manufacturing facility, where buyers can assess the production process, quality management systems, and compliance with international standards.
Requesting Quality Reports
Buyers should request comprehensive quality reports that detail the results of IQC, IPQC, and FQC checks. These reports can provide insights into the consistency of the manufacturing process and the reliability of the sealing machines.
Engaging Third-Party Inspection Services
Using third-party inspection services can provide an unbiased evaluation of the supplier’s quality control practices. These services can conduct inspections at various stages of production and provide detailed reports, which can be particularly beneficial for buyers in regions with less access to reliable information about suppliers.
What Are the Quality Control and Certification Nuances for International Buyers?
International B2B buyers should be aware of specific nuances regarding quality control and certifications:
-
Regional Regulations: Different regions may have varying regulatory requirements. For instance, sealing machines sold in the European market must comply with CE standards, while those destined for the Middle East might need to meet specific local certifications. Buyers should familiarize themselves with these requirements to avoid compliance issues.
-
Cultural Differences in Quality Standards: Quality perceptions can differ across cultures. Buyers from Africa, South America, the Middle East, and Europe should ensure that their expectations align with the supplier’s quality standards to avoid misunderstandings.
-
Language Barriers: Documentation and communication can sometimes be hampered by language differences. Buyers should ensure that they can obtain quality reports and certification documents in a language they understand.
In conclusion, a comprehensive understanding of the manufacturing processes and quality assurance measures is vital for international B2B buyers in the sealing machine market. By focusing on the key stages of production, understanding quality control measures, and verifying supplier practices, buyers can make informed purchasing decisions that align with their operational needs and regulatory requirements.
Practical Sourcing Guide: A Step-by-Step Checklist for ‘sealing machine manufacturer’
In the competitive landscape of manufacturing, sourcing a reliable sealing machine manufacturer is crucial for ensuring efficiency and product quality. This practical checklist is designed to guide international B2B buyers—especially those from Africa, South America, the Middle East, and Europe—through the critical steps in the procurement process.
Step 1: Define Your Technical Specifications
Establishing clear technical specifications is the foundation of your sourcing process. Determine the type of sealing machine you need, including parameters like speed, sealing method (heat seal, vacuum seal), and compatibility with your production line. This clarity helps streamline your search and ensures that potential suppliers can meet your specific requirements.
Step 2: Conduct Market Research
Understanding the market landscape is vital for making informed decisions. Research the leading sealing machine manufacturers, comparing their offerings, market reputation, and customer reviews. Focus on suppliers that have experience in your industry and those who have successfully served clients in your region, as this can indicate reliability and support.
Step 3: Evaluate Potential Suppliers
Before making a commitment, vet potential suppliers thoroughly. Request company profiles, detailed product catalogs, and case studies that demonstrate their expertise. Look for references from buyers in similar industries or regions to gauge supplier performance and reliability. This step minimizes risks associated with poor-quality machinery and service.
Step 4: Verify Supplier Certifications
Certifications are a key indicator of a manufacturer’s credibility and compliance with industry standards. Ensure that your shortlisted suppliers possess relevant certifications such as ISO 9001 for quality management systems and CE marking for compliance with European safety standards. This verification not only assures product quality but also enhances your supply chain’s integrity.
Step 5: Request Samples or Prototypes
Once you have narrowed down your choices, request samples or prototypes of the sealing machines. This hands-on evaluation allows you to assess the machine’s functionality, ease of use, and compatibility with your existing processes. Pay attention to the design and materials used, as these factors significantly influence durability and performance.
Step 6: Negotiate Terms and Conditions
Engage in negotiations to establish favorable terms and conditions. Discuss pricing, payment methods, warranty, and after-sales support. A clear understanding of these elements helps prevent misunderstandings and ensures that both parties are aligned on expectations.
Step 7: Plan for Logistics and Delivery
Finally, consider the logistics involved in importing the sealing machines. Factor in shipping times, customs regulations, and potential tariffs that may apply. Collaborate with your supplier to develop a timeline for delivery and ensure that you are prepared for any logistical challenges that may arise.
By following this checklist, B2B buyers can confidently navigate the sourcing process for sealing machines, ensuring they partner with manufacturers that meet their technical needs and support their operational goals.
Comprehensive Cost and Pricing Analysis for sealing machine manufacturer Sourcing
What Are the Key Cost Components in Sealing Machine Manufacturing?
When sourcing sealing machines, understanding the cost structure is crucial for making informed purchasing decisions. The primary cost components include:
-
Materials: The choice of materials significantly impacts the overall cost. Common materials such as stainless steel, plastics, and electronic components can vary in price based on quality and supplier availability. Opting for high-grade materials may increase initial costs but can enhance durability and reduce long-term maintenance expenses.
-
Labor: Labor costs can differ widely based on geographic location. Regions with lower labor costs, such as parts of South America and Africa, might present attractive pricing, but potential trade-offs in quality and expertise should be considered.
-
Manufacturing Overhead: This encompasses costs related to utilities, factory space, and equipment depreciation. Manufacturers in regions with higher energy costs or stringent regulations might reflect these expenses in their pricing.
-
Tooling: Custom tooling for specialized sealing machines can be a significant upfront cost. Understanding the tooling requirements early in the sourcing process can prevent unexpected budget overruns.
-
Quality Control (QC): Ensuring product quality through rigorous QC processes may add to the overall cost. However, investing in quality assurance can mitigate risks associated with machine failure and warranty claims.
-
Logistics: Transportation costs can fluctuate based on distance, shipping methods, and trade tariffs. Buyers must account for these variables when estimating total costs.
-
Margin: Manufacturers typically include a profit margin that reflects their business strategy and market position. Understanding the typical margins in your target market can help in assessing whether pricing is competitive.
How Do Price Influencers Affect Sealing Machine Costs?
Several factors can influence the pricing of sealing machines, which can vary based on buyer requirements and market conditions:
-
Volume/MOQ: Manufacturers often provide discounts for bulk orders. Understanding the minimum order quantity (MOQ) can help buyers negotiate better prices, especially if they can commit to larger volumes.
-
Specifications and Customization: Customized machines tailored to specific industry needs may incur additional costs. Buyers should clearly define their specifications to receive accurate quotes and avoid costly changes later.
-
Materials and Quality Certifications: Premium materials and certifications (such as ISO standards) can raise costs but often lead to better performance and reliability. Buyers should weigh the benefits of higher upfront costs against potential long-term savings.
-
Supplier Factors: The reputation and reliability of the supplier can influence pricing. Established manufacturers may charge more due to perceived quality and service, whereas newer suppliers might offer lower prices to build their customer base.
-
Incoterms: The choice of Incoterms can significantly affect the overall cost. For instance, choosing EXW (Ex Works) might seem cheaper, but it places the burden of logistics on the buyer, potentially increasing the total cost.
What Are the Best Buyer Tips for Negotiating Sealing Machine Prices?
International B2B buyers should consider the following strategies to optimize their sourcing efforts:
-
Negotiate Effectively: Building strong relationships with suppliers can lead to better pricing. Engage in open discussions about pricing structures and express your willingness to place larger orders in exchange for discounts.
-
Focus on Cost-Efficiency: Evaluate the Total Cost of Ownership (TCO) rather than just the purchase price. This includes maintenance, operational costs, and potential downtime, which can significantly impact long-term profitability.
-
Understand Pricing Nuances: Familiarize yourself with regional pricing trends and economic factors that could affect costs. For example, currency fluctuations between Europe and Africa may impact the final price.
-
Evaluate Multiple Suppliers: Obtain quotes from several manufacturers to compare costs and service levels. This can provide leverage during negotiations and ensure you receive a competitive price.
-
Be Aware of Indicative Prices: Always treat quoted prices as indicative. Market conditions, material costs, and other factors can change, so maintain flexibility in your budget and sourcing strategies.
By understanding these cost components, price influencers, and negotiation strategies, international B2B buyers from regions like Africa, South America, the Middle East, and Europe can make more informed sourcing decisions in the sealing machine market.
Alternatives Analysis: Comparing sealing machine manufacturer With Other Solutions
In the quest for efficient packaging solutions, B2B buyers must evaluate various alternatives to sealing machine manufacturers. Understanding the strengths and weaknesses of each option can lead to informed purchasing decisions that align with specific business needs, particularly in dynamic markets across Africa, South America, the Middle East, and Europe. Below, we analyze the sealing machine against two viable alternatives: manual sealing methods and vacuum sealing technologies.
Comparison Table
Comparison Aspect | Sealing Machine Manufacturer | Manual Sealing Method | Vacuum Sealing Technology |
---|---|---|---|
Performance | High throughput and consistency | Variable; depends on operator skill | High, especially for extending shelf life |
Cost | Moderate to high initial investment | Low initial cost | Moderate initial investment; potential savings on spoilage |
Ease of Implementation | Requires training and setup | Very easy; minimal training needed | Requires training and proper setup |
Maintenance | Regular maintenance needed | Minimal maintenance | Regular maintenance needed |
Best Use Case | Large-scale production environments | Small-scale or artisanal production | Food preservation and storage |
What are the Pros and Cons of Manual Sealing Methods?
Manual sealing methods offer low initial costs and ease of implementation, making them attractive for small businesses or startups. Operators can quickly learn to perform manual sealing, which is ideal for low-volume production runs. However, the performance can be inconsistent, heavily reliant on the skill of the operator. This inconsistency can lead to product spoilage and reduced packaging integrity, particularly in environments requiring stringent quality controls. Additionally, while the maintenance is minimal, the potential for human error can lead to higher long-term costs.
How Does Vacuum Sealing Technology Compare?
Vacuum sealing technology is particularly effective for preserving food and extending shelf life, making it a popular choice in the food industry. It offers high performance, especially in reducing air exposure, which can prevent spoilage. However, the initial investment can be moderate, and it often requires training for effective operation. Maintenance is also necessary to ensure that the vacuum systems function optimally. While vacuum sealing is excellent for specific applications, it may not be the best fit for high-volume production where speed and efficiency are paramount.
Conclusion: How to Choose the Right Sealing Solution for Your Business?
Selecting the appropriate sealing solution involves understanding your business’s specific needs, including production volume, budget constraints, and product requirements. For large-scale operations, a sealing machine manufacturer is often the best choice due to its high performance and consistency. Alternatively, businesses focused on artisanal products may find manual sealing methods more suitable due to their low cost and ease of use. For food preservation, vacuum sealing technology provides excellent shelf life benefits but may require additional training and maintenance. Ultimately, evaluating these factors in the context of your operational goals will lead to a more strategic investment in sealing solutions.
Essential Technical Properties and Trade Terminology for sealing machine manufacturer
When engaging with sealing machine manufacturers, international B2B buyers must understand key technical properties and trade terminology that can significantly impact their procurement processes. This understanding not only streamlines communication but also enhances decision-making, especially for buyers from diverse regions such as Africa, South America, the Middle East, and Europe.
What Are the Essential Technical Properties of Sealing Machines?
1. Material Grade: Why Is It Important for Sealing Machines?
The material grade of sealing machines, which often includes stainless steel, aluminum, or specialized plastics, directly influences durability, resistance to corrosion, and suitability for specific applications. For buyers, selecting the appropriate material grade ensures that the sealing machines can withstand the environmental conditions and operational demands of their respective industries.
2. Tolerance: How Does It Affect Sealing Machine Performance?
Tolerance refers to the permissible limit of variation in a physical dimension, such as the size of seals or the alignment of sealing components. High precision in tolerance is crucial for ensuring optimal performance and preventing leakage. B2B buyers should prioritize manufacturers that provide detailed tolerance specifications to ensure that the machines meet their operational standards and reduce downtime.
3. Sealing Speed: What Is Its Role in Production Efficiency?
Sealing speed is a measure of how quickly a machine can seal products. This specification is vital for businesses looking to optimize production lines. A higher sealing speed can lead to increased throughput, making it essential for buyers to assess their production needs against the capabilities of potential sealing machines.
4. Power Consumption: Why Is It Critical for Cost Management?
Power consumption indicates how much energy a sealing machine uses during operation. For B2B buyers, understanding power consumption helps in calculating operational costs over time, which is particularly important for manufacturers aiming for sustainability or those operating in regions where energy costs are high.
5. Automation Level: How Does It Impact Labor Costs?
The level of automation in sealing machines affects both efficiency and labor costs. Fully automated machines can significantly reduce the need for manual labor, thus lowering operational expenses. Buyers should evaluate the automation features of sealing machines to align with their workforce capabilities and budget constraints.
What Are Common Trade Terms in the Sealing Machine Industry?
1. What Does OEM Mean in the Context of Sealing Machines?
OEM stands for Original Equipment Manufacturer. This term refers to companies that produce parts and equipment that may be marketed by another manufacturer. Understanding OEM relationships can help buyers identify reliable suppliers and establish partnerships that enhance their product offerings.
2. Why Is MOQ Critical for B2B Buyers?
MOQ, or Minimum Order Quantity, is the smallest number of units a supplier is willing to sell. This term is crucial for B2B buyers as it impacts inventory management and capital investment. Knowing the MOQ helps buyers plan their purchases to avoid excess inventory or stockouts.
3. What Is an RFQ and How Does It Facilitate Procurement?
RFQ stands for Request for Quotation. It is a document sent to suppliers to invite them to bid on specific products or services. B2B buyers can use RFQs to obtain competitive pricing and terms, making it a vital tool in the procurement process for sealing machines.
4. How Do Incoterms Influence International Trade?
Incoterms, short for International Commercial Terms, define the responsibilities of buyers and sellers in international shipping. Understanding these terms helps B2B buyers in negotiating shipping costs, delivery times, and liability during transportation, ensuring smoother transactions across borders.
5. What Is the Role of Lead Time in Sealing Machine Procurement?
Lead time refers to the time it takes from placing an order until the product is delivered. It is a critical factor for B2B buyers, as longer lead times can disrupt production schedules. Buyers should clarify lead times with manufacturers to ensure timely delivery that aligns with their operational needs.
By grasping these technical properties and trade terms, international B2B buyers can make informed decisions when engaging with sealing machine manufacturers, ultimately enhancing their procurement strategies and operational efficiency.
Navigating Market Dynamics and Sourcing Trends in the sealing machine manufacturer Sector
What Are the Current Market Dynamics and Key Trends in the Sealing Machine Manufacturing Sector?
The sealing machine manufacturing sector is experiencing significant growth, driven by the increasing demand for efficient packaging solutions across various industries, including food and beverage, pharmaceuticals, and consumer goods. Emerging markets in Africa, South America, the Middle East, and Europe are particularly influential, with a surge in local manufacturing and export activities. This trend is fueled by globalization and the need for businesses to streamline their supply chains and enhance operational efficiency.
One of the current B2B tech trends is the integration of automation and smart technology in sealing machines. Manufacturers are increasingly adopting Industry 4.0 principles, which include IoT-enabled devices that facilitate real-time monitoring and predictive maintenance. This shift not only reduces downtime but also improves production quality, making it crucial for international buyers to consider suppliers who can offer these advanced technologies.
Moreover, sustainability is becoming a pivotal factor in sourcing decisions. B2B buyers are now prioritizing suppliers that demonstrate environmental responsibility and offer eco-friendly sealing solutions. This includes machines designed to work with biodegradable or recyclable packaging materials, which are gaining traction in the market. As international buyers from regions like Kenya and the UAE seek competitive advantages, understanding these dynamics will be essential for making informed sourcing decisions.
How Is Sustainability and Ethical Sourcing Shaping the Sealing Machine Industry?
Sustainability is no longer just a trend; it has become a cornerstone of modern manufacturing practices, especially in the sealing machine sector. With growing awareness of environmental issues, international B2B buyers are increasingly focused on the environmental impact of their supply chains. This includes evaluating the energy efficiency of sealing machines, the waste generated during production, and the overall carbon footprint.
Ethical sourcing plays a critical role in this context. Buyers are encouraged to partner with manufacturers that adhere to sustainable practices, which often include fair labor practices and responsible sourcing of materials. Certifications like ISO 14001 for environmental management and compliance with global sustainability standards can help buyers identify manufacturers committed to ethical practices.
Additionally, there is a rising demand for ‘green’ materials in sealing machines, such as biodegradable films and recyclable components. By prioritizing suppliers that offer these options, B2B buyers can enhance their brand reputation and appeal to environmentally conscious consumers. This strategic alignment not only supports sustainability goals but also positions businesses favorably in an increasingly competitive market.
How Has the Sealing Machine Manufacturing Sector Evolved Over Time?
The sealing machine manufacturing sector has undergone remarkable evolution over the past few decades. Initially dominated by mechanical solutions, the industry has shifted towards more sophisticated electronic and automated systems. This evolution has been driven by technological advancements and the growing need for precision and efficiency in packaging processes.
In the early stages, sealing machines primarily focused on basic functionalities. However, with the advent of digital technologies, manufacturers began to incorporate features such as programmable logic controllers (PLCs) and touch-screen interfaces, significantly enhancing user experience and operational flexibility. The rise of e-commerce and global trade has further accelerated this trend, compelling manufacturers to innovate continuously to meet diverse market demands.
This historical context is essential for B2B buyers as it underscores the importance of selecting suppliers who are not only technologically advanced but also capable of adapting to the fast-changing landscape of the sealing machine sector. Understanding the trajectory of this industry can help buyers make informed decisions that align with their long-term strategic goals.
Frequently Asked Questions (FAQs) for B2B Buyers of sealing machine manufacturer
-
How do I select the right sealing machine manufacturer for my business needs?
Choosing the right sealing machine manufacturer requires a thorough evaluation of their experience, product range, and customer reviews. Look for manufacturers with a proven track record in your industry and those who offer machines tailored to your specific requirements, such as size, speed, and sealing technology. Engage in discussions about your needs and request product demonstrations or samples. Additionally, consider their after-sales support and warranty terms, as reliable customer service can significantly impact your operational efficiency. -
What are the key features to look for in a sealing machine?
When sourcing a sealing machine, focus on features that enhance functionality and efficiency. Important aspects include sealing speed, versatility for different packaging types, energy consumption, and ease of operation. Additionally, check for safety features, maintenance accessibility, and compatibility with existing production lines. For international buyers, ensure that the machine complies with local regulations and standards to avoid costly delays in customs clearance. -
What is the typical minimum order quantity (MOQ) for sealing machines?
The minimum order quantity (MOQ) for sealing machines can vary significantly among manufacturers, often depending on the machine type and customization level. Generally, MOQs can range from a single unit for standard machines to several units for custom models. It’s advisable to discuss your specific needs with the manufacturer to negotiate favorable terms, especially if you are a smaller business or entering a new market. Consider consolidating orders with other buyers to meet MOQ requirements. -
What payment terms should I expect when purchasing sealing machines internationally?
Payment terms can vary widely based on the manufacturer and the buyer’s relationship. Common options include partial upfront payment with the balance due upon delivery or a letter of credit, which provides security for both parties. For international transactions, consider the impact of currency fluctuations and transaction fees. Always clarify payment methods and terms in the contract to prevent misunderstandings and ensure smooth transactions. -
How can I ensure quality assurance when sourcing sealing machines?
To ensure quality assurance, request certifications and quality control processes from the manufacturer. Look for ISO certifications or industry-specific standards that demonstrate their commitment to quality. You can also ask for samples or visit the manufacturing facility to observe production practices firsthand. Establishing a clear communication channel for quality feedback during production can help mitigate issues before the machines are shipped. -
What logistics considerations should I keep in mind when importing sealing machines?
When importing sealing machines, consider shipping methods, transit times, and customs regulations in your country. It’s essential to work with a logistics provider experienced in handling machinery imports to navigate these complexities. Factor in duties, taxes, and additional fees that may apply. Preparing all necessary documentation in advance, such as commercial invoices and packing lists, can facilitate smoother customs clearance and minimize delays. -
How do I vet a sealing machine manufacturer for reliability?
Vetting a sealing machine manufacturer involves researching their reputation, examining customer reviews, and checking their history in the industry. Request references from previous clients and assess their responsiveness to inquiries. Attend trade shows or industry events where the manufacturer showcases their products to gain firsthand experience. It’s also beneficial to evaluate their financial stability and production capabilities to ensure they can meet your demands consistently. -
What are the common challenges when sourcing sealing machines internationally, and how can I overcome them?
Common challenges in international sourcing include language barriers, cultural differences, and varying quality standards. To overcome these, establish clear communication channels and consider hiring local representatives who understand the market dynamics. Conduct thorough due diligence on potential suppliers and engage in regular updates throughout the procurement process. Building a strong relationship with the manufacturer can also facilitate smoother transactions and resolve issues promptly.
Important Disclaimer & Terms of Use
⚠️ Important Disclaimer
The information provided in this guide, including content regarding manufacturers, technical specifications, and market analysis, is for informational and educational purposes only. It does not constitute professional procurement advice, financial advice, or legal advice.
While we have made every effort to ensure the accuracy and timeliness of the information, we are not responsible for any errors, omissions, or outdated information. Market conditions, company details, and technical standards are subject to change.
B2B buyers must conduct their own independent and thorough due diligence before making any purchasing decisions. This includes contacting suppliers directly, verifying certifications, requesting samples, and seeking professional consultation. The risk of relying on any information in this guide is borne solely by the reader.
Strategic Sourcing Conclusion and Outlook for sealing machine manufacturer
In today’s competitive landscape, strategic sourcing for sealing machines is not merely a procurement function but a vital component of operational excellence. B2B buyers from regions such as Africa, South America, the Middle East, and Europe should prioritize supplier partnerships that offer innovation, reliability, and sustainability. Engaging with manufacturers who demonstrate a commitment to quality and can adapt to regional market demands will enhance supply chain resilience and reduce costs.
What are the key benefits of strategic sourcing for sealing machines? By leveraging data analytics and market intelligence, companies can identify the best suppliers and negotiate favorable terms that align with their long-term business goals. This proactive approach not only streamlines procurement processes but also fosters collaboration and innovation within the supply chain.
Looking ahead, the sealing machine market is poised for growth, driven by advancements in technology and increasing demand for efficient packaging solutions. International B2B buyers are encouraged to stay informed about emerging trends and invest in partnerships that promote sustainability and technological advancements. By doing so, they can ensure their operations remain competitive and responsive to ever-changing market dynamics. Engage with trusted manufacturers today to secure your position in this evolving landscape.