Discover Top Benefits from an Auto Accessories Supplier (2025)
Introduction: Navigating the Global Market for auto accessories supplier
Navigating the global market for auto accessories suppliers presents a unique set of challenges for international B2B buyers, especially when it comes to sourcing high-quality products that meet specific regional demands. Whether you’re in Kenya seeking durable off-road vehicle accessories or in Turkey looking for innovative car technology enhancements, understanding the nuances of the auto accessories market is crucial. This guide offers a comprehensive overview that covers various types of auto accessories, their applications, and the critical factors to consider when vetting suppliers.
As a B2B buyer, you’ll find actionable insights on cost considerations, quality assurance processes, and the latest trends shaping the industry. Our aim is to empower you to make informed purchasing decisions that align with your business needs and market expectations. By focusing on key aspects such as supplier reliability and product compliance with regional standards, this guide equips you with the knowledge to navigate the complexities of international sourcing effectively.
With the auto accessories market continually evolving, staying ahead of the curve is essential. This guide is designed to be your go-to resource, providing the tools and insights necessary to thrive in the competitive landscape of auto accessories procurement. Whether you’re a seasoned buyer or new to the market, understanding these dynamics will enhance your strategic sourcing efforts across Africa, South America, the Middle East, and Europe.
Understanding auto accessories supplier Types and Variations
Type Name | Key Distinguishing Features | Primary B2B Applications | Brief Pros & Cons for Buyers |
---|---|---|---|
OEM Auto Accessories | Manufactured by original equipment manufacturers (OEMs), ensuring compatibility and quality. | Vehicle manufacturers, fleet operators, and dealerships. | Pros: High quality, guaranteed fit. Cons: Higher cost, limited variety. |
Aftermarket Auto Accessories | Produced by third-party manufacturers, offering a wide range of options and styles. | Retailers, automotive repair shops, and individual consumers. | Pros: Cost-effective, diverse selection. Cons: Variable quality, potential fit issues. |
Specialty Auto Accessories | Focused on niche markets, such as off-road or performance parts. | Racing teams, specialty shops, and enthusiasts. | Pros: Tailored solutions, unique products. Cons: Often expensive, limited availability. |
Custom Auto Accessories | Tailored products based on specific buyer needs and vehicle specifications. | Custom shops, auto body shops, and individual clients. | Pros: Personalized fit, unique designs. Cons: Longer lead times, potentially high costs. |
E-commerce Auto Accessories | Online platforms providing a wide range of products, often at competitive prices. | Online retailers, drop shippers, and wholesalers. | Pros: Convenience, price comparison. Cons: Risk of misrepresentation, shipping delays. |
What Are OEM Auto Accessories and Their B2B Relevance?
OEM auto accessories are produced by the same manufacturers that create the original vehicle parts. This type of supplier is essential for businesses that prioritize quality and compatibility, such as vehicle manufacturers and fleet operators. When purchasing OEM accessories, B2B buyers can expect a guaranteed fit and adherence to stringent quality standards. However, the trade-off includes higher costs and a more limited selection compared to aftermarket options, which can be a crucial consideration for budget-conscious buyers.
How Do Aftermarket Auto Accessories Benefit B2B Buyers?
Aftermarket auto accessories are created by independent manufacturers and are known for their extensive variety and affordability. These suppliers cater to a broad market, including retailers and automotive repair shops, allowing them to meet diverse consumer needs. The key advantage of aftermarket products is their cost-effectiveness, making them attractive for businesses looking to maximize profit margins. However, buyers should be cautious of variable quality and potential fit issues, which can lead to customer dissatisfaction if not adequately vetted.
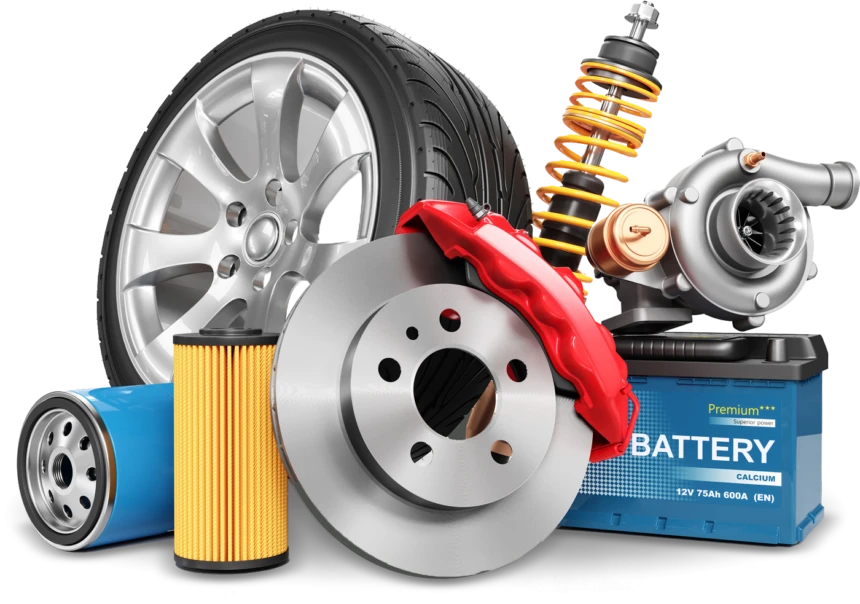
A stock image related to auto accessories supplier.
What Are Specialty Auto Accessories and Who Should Consider Them?
Specialty auto accessories focus on specific vehicle types or applications, such as off-road vehicles or racing components. These suppliers serve niche markets, making them ideal for businesses that cater to enthusiasts or specialized automotive needs. While they offer tailored solutions and unique products, the costs can be significantly higher, and availability may be limited. B2B buyers in racing or off-road markets should consider these suppliers for their specialized offerings, keeping in mind the potential for higher investment.
Why Choose Custom Auto Accessories for Your Business?
Custom auto accessories are designed to meet specific buyer requirements, making them highly suitable for businesses that require unique solutions. Suppliers in this category cater to custom shops and auto body shops, offering products that fit particular vehicles or customer specifications. The primary benefit is a personalized fit and unique designs that can enhance customer satisfaction. However, buyers should be aware of longer lead times and potentially elevated costs, which can impact inventory management and pricing strategies.
How Do E-commerce Auto Accessories Suppliers Operate in the B2B Space?
E-commerce auto accessories suppliers provide a convenient online platform for purchasing a wide range of products. This model is increasingly popular among retailers, drop shippers, and wholesalers due to its ease of access and competitive pricing. B2B buyers benefit from the ability to compare prices and find deals quickly. However, the risks include potential misrepresentation of products and shipping delays, which can affect operational timelines. Buyers should ensure they work with reputable e-commerce platforms to mitigate these risks.
Related Video: 14 COOLEST CAR ACCESSORIES That Are Worth Buying From Amazon (Best Automobile Car Gadgets 2021)
Key Industrial Applications of auto accessories supplier
Industry/Sector | Specific Application of auto accessories supplier | Value/Benefit for the Business | Key Sourcing Considerations for this Application |
---|---|---|---|
Automotive Manufacturing | Custom vehicle interiors | Enhances vehicle aesthetics and comfort, leading to higher customer satisfaction. | Quality of materials, compliance with safety standards, customization options. |
Fleet Management | GPS tracking and fleet monitoring systems | Improves operational efficiency and reduces costs through better route management. | Integration capabilities, reliability, and warranty terms. |
Retail Automotive Accessories | E-commerce platforms for auto parts | Expands market reach and increases sales through online presence. | User-friendly interface, secure payment options, and customer support. |
Logistics and Transportation | Cargo securing accessories | Ensures safe transport of goods, minimizing damage and loss. | Durability, weight capacity, and compliance with transport regulations. |
Car Rental Services | Vehicle customization options | Attracts diverse customer demographics, enhancing rental appeal. | Cost-effectiveness, variety of options, and ease of installation. |
How Are Auto Accessories Used in Automotive Manufacturing?
In the automotive manufacturing sector, auto accessories suppliers provide custom vehicle interiors that significantly enhance the aesthetics and comfort of vehicles. This application solves the problem of standardization in vehicle design, allowing manufacturers to differentiate their products in a competitive market. International buyers, particularly from regions like Africa and South America, should consider the quality of materials and compliance with safety standards when sourcing these accessories. Customization options are also crucial, as they allow for unique branding opportunities.
What Role Do Auto Accessories Play in Fleet Management?
Fleet management companies utilize GPS tracking and fleet monitoring systems from auto accessories suppliers to improve operational efficiency. This technology addresses challenges such as route optimization and vehicle maintenance, ultimately leading to reduced operational costs. For international B2B buyers, especially in the Middle East and Europe, key considerations include the integration capabilities of these systems with existing software and the reliability of the technology, as well as warranty terms that safeguard their investment.
How Do Retail Automotive Accessories Benefit E-commerce Platforms?
Retailers of automotive accessories leverage e-commerce platforms to expand their market reach. By sourcing from auto accessories suppliers, they can offer a wide range of products online, thus increasing sales potential. This application is particularly beneficial for businesses in Europe and Africa, where online shopping trends are rising. Buyers should focus on user-friendly interfaces, secure payment options, and robust customer support when selecting an e-commerce solution to ensure a seamless shopping experience.
Why Are Cargo Securing Accessories Important in Logistics?
In logistics and transportation, cargo securing accessories from auto accessories suppliers are vital for ensuring the safe transport of goods. These accessories help minimize damage and loss during transit, addressing a significant pain point in the industry. International buyers, particularly in South America and Africa, should prioritize durability and weight capacity when sourcing these products, along with compliance with local transport regulations to avoid legal issues.
How Do Customization Options Affect Car Rental Services?
Car rental services benefit from vehicle customization options provided by auto accessories suppliers, which help attract a diverse customer base. This application addresses the need for differentiation in a crowded market, enhancing the appeal of rental offerings. Buyers in Europe and the Middle East should consider the cost-effectiveness of these accessories, the variety of options available, and the ease of installation when making sourcing decisions to ensure a competitive advantage.
Related Video: How a Industrial Pneumatic Systems Works And The Five Most Common Elements Used
3 Common User Pain Points for ‘auto accessories supplier’ & Their Solutions
Scenario 1: Navigating Quality Assurance Challenges in Auto Accessories
The Problem:
B2B buyers often face significant challenges when it comes to ensuring the quality of auto accessories sourced from suppliers. This is particularly true for international buyers from regions such as Africa and South America, where quality control standards may vary widely. The fear of receiving subpar products can lead to costly returns, lost time, and damage to the buyer’s reputation. Additionally, suppliers might not provide adequate documentation or certifications, making it difficult for buyers to validate the quality of the products.
The Solution:
To mitigate quality assurance issues, international buyers should prioritize working with reputable auto accessories suppliers who have a proven track record of delivering high-quality products. Conducting thorough research before entering into any agreements is essential. Buyers should request samples before placing bulk orders, allowing them to assess the quality firsthand. Establishing clear quality standards and expectations in the contract can also protect the buyer’s interests. Utilizing third-party quality inspection services can provide an additional layer of assurance, especially for bulk shipments. Finally, maintaining open lines of communication with suppliers throughout the manufacturing process can help address any potential quality concerns before the products are shipped.
Scenario 2: Overcoming Communication Barriers with Suppliers
The Problem:
Communication barriers can present a significant hurdle for B2B buyers, particularly when dealing with suppliers from different countries. Language differences and varying business practices may lead to misunderstandings regarding product specifications, pricing, and delivery timelines. For buyers from the Middle East or Europe engaging with suppliers in Africa or South America, these barriers can complicate negotiations and affect the overall purchasing experience.
The Solution:
To overcome communication challenges, buyers should consider employing multi-lingual staff or hiring local representatives who understand the cultural nuances and languages of the suppliers. Utilizing technology such as translation tools and communication platforms can facilitate clearer dialogue. It’s also beneficial to establish a standardized communication protocol that outlines how updates and changes will be communicated. Regular check-ins via video calls can foster a stronger relationship and ensure that both parties are aligned on expectations. Additionally, providing suppliers with detailed product specifications and using visual aids can help clarify any ambiguities.
Scenario 3: Managing Supply Chain Delays in Auto Accessories Procurement
The Problem:
Supply chain disruptions are an increasingly common issue for B2B buyers of auto accessories, especially in a global market that is sensitive to geopolitical tensions and economic shifts. Buyers from regions like Africa and South America often experience delays due to logistic constraints, customs issues, or unforeseen circumstances such as pandemics. These delays can lead to inventory shortages, impacting business operations and customer satisfaction.
The Solution:
To effectively manage supply chain delays, buyers should adopt a proactive approach by diversifying their supplier base. Engaging multiple suppliers across different regions can help mitigate the risk of disruptions from a single source. Implementing robust inventory management practices, such as just-in-time inventory or safety stock strategies, can also buffer against delays. It’s crucial to maintain transparent communication with suppliers regarding lead times and to build contingency plans for potential disruptions. Additionally, leveraging supply chain management software can provide real-time insights into the status of orders and shipments, enabling buyers to make informed decisions and adjust their strategies accordingly.
Strategic Material Selection Guide for auto accessories supplier
When selecting materials for auto accessories, international B2B buyers must consider various factors that influence product performance, cost, and compliance with regional standards. Here, we analyze four common materials used in the production of auto accessories, highlighting their properties, advantages, disadvantages, and specific considerations for buyers from Africa, South America, the Middle East, and Europe.
What Are the Key Properties of Plastic in Auto Accessories?
Plastic is widely used in the auto accessories industry due to its versatility and lightweight nature. Key properties include excellent corrosion resistance, a wide range of temperature ratings, and the ability to be molded into complex shapes. Plastics can withstand temperatures ranging from -40°C to 100°C, depending on the type used.
Pros & Cons: Plastics are generally durable, lightweight, and cost-effective, making them suitable for various applications. However, they can be less resistant to high temperatures and UV exposure, leading to potential degradation over time. Manufacturing complexity can vary based on the type of plastic and the required shapes.
Impact on Application: Plastics are compatible with a variety of media, including water and oils, but may not perform well in high-heat environments or with certain chemicals.
Considerations for International Buyers: Buyers should be aware of compliance with standards such as ASTM D638 for tensile properties and ISO 527 for plastics. Regional preferences may dictate the use of specific types of plastics, such as polypropylene or polycarbonate, depending on the application.
How Does Metal Compare as a Material for Auto Accessories?
Metal, particularly aluminum and steel, is another prevalent material in the auto accessories sector. Metals offer high strength, excellent temperature resistance, and good durability, withstanding extreme conditions and pressures.
Pros & Cons: Metals are highly durable and can be recycled, making them an environmentally friendly choice. However, they are heavier than plastics and can be more expensive, especially stainless steel. The manufacturing process for metal components can also be more complex and require specialized equipment.
Impact on Application: Metals are particularly suitable for high-stress applications, such as structural components or fastening systems. Their compatibility with various media is generally high, but corrosion resistance varies significantly between different types of metals.
Considerations for International Buyers: Compliance with standards like ASTM A36 for structural steel and EN 10025 for European applications is crucial. Buyers should also consider the local availability of materials and any import tariffs that may affect overall costs.
What Are the Advantages of Rubber in Auto Accessories Manufacturing?
Rubber is commonly used in seals, gaskets, and vibration dampening components. Its key properties include excellent elasticity, temperature resistance, and the ability to absorb shocks.
Pros & Cons: Rubber is highly effective in preventing leaks and reducing noise, making it ideal for automotive applications. However, it can degrade over time when exposed to UV light and certain chemicals, which limits its lifespan. The manufacturing process can also be more complex due to the need for specific curing processes.
Impact on Application: Rubber is compatible with a variety of automotive fluids, including oils and coolants, making it suitable for seals and gaskets. However, its performance can be compromised in extreme temperatures.
Considerations for International Buyers: Buyers should ensure compliance with ASTM D2000 standards for rubber materials. Additionally, local preferences may lean towards specific rubber compounds that offer better performance in regional climates.
How Does Composite Material Function in Auto Accessories?
Composite materials, often a combination of plastics and fibers, are increasingly used in the auto accessories sector due to their lightweight and high-strength properties. They can be engineered to provide specific performance characteristics.
Pros & Cons: Composites offer excellent strength-to-weight ratios and are resistant to corrosion, making them suitable for a variety of applications. However, they can be more expensive to manufacture and may require specialized processing techniques.
Impact on Application: Composites are particularly effective in applications where weight reduction is critical, such as in performance vehicles. They are generally compatible with automotive fluids but may have limitations in high-temperature environments.
Considerations for International Buyers: Buyers should be aware of standards such as ASTM D3039 for tensile properties of composites. Additionally, the availability of composite materials may vary by region, impacting sourcing decisions.
Summary Table of Material Selection for Auto Accessories
Material | Typical Use Case for auto accessories supplier | Key Advantage | Key Disadvantage/Limitation | Relative Cost (Low/Med/High) |
---|---|---|---|---|
Plastic | Interior trim, dashboards, and lightweight components | Lightweight and cost-effective | Less heat and UV resistance | Low |
Metal | Structural components, brackets, and fasteners | High strength and durability | Heavier and potentially more costly | Medium |
Rubber | Seals, gaskets, and vibration dampeners | Excellent elasticity and shock absorption | Degrades under UV exposure | Medium |
Composite | Performance parts, body panels, and lightweight structures | High strength-to-weight ratio | Expensive and complex to manufacture | High |
This guide provides essential insights into material selection for auto accessories, helping international B2B buyers make informed decisions that align with their operational needs and regional standards.
In-depth Look: Manufacturing Processes and Quality Assurance for auto accessories supplier
What Are the Main Stages of Manufacturing Auto Accessories?
Understanding the manufacturing process of auto accessories is crucial for international B2B buyers, especially when evaluating potential suppliers. The production typically involves several key stages:
-
Material Preparation: This initial stage involves selecting high-quality raw materials such as plastics, metals, and textiles. Suppliers often use advanced technologies like Computer-Aided Design (CAD) to ensure precision in material selection based on durability and compatibility with automotive standards.
-
Forming: After preparation, materials undergo forming processes, which can include injection molding for plastics, stamping for metals, or weaving for textiles. Each technique is chosen based on the specific accessory being produced. For instance, injection molding is prevalent for creating complex shapes in dashboard components or custom fittings.
-
Assembly: Once formed, components are assembled into the final product. This may involve manual labor or automated assembly lines, depending on the scale of production. Robotic assembly can enhance precision and speed, particularly for high-volume orders.
-
Finishing: The final stage includes surface treatments such as painting, coating, or polishing to enhance aesthetics and durability. This step is essential for products like chrome-plated accessories or custom color finishes, which are often requested by clients in various markets.
What Quality Assurance Standards Should B2B Buyers Consider?
For B2B buyers, especially those from regions like Africa, South America, the Middle East, and Europe, understanding quality assurance is vital. Here are the relevant international and industry-specific standards:
-
ISO 9001: This is a globally recognized standard for quality management systems. Suppliers certified under ISO 9001 demonstrate a commitment to consistent quality and customer satisfaction, making it a valuable benchmark for buyers.
-
CE Marking: Particularly important for products sold in the European market, CE marking indicates compliance with EU safety, health, and environmental protection standards. Buyers in Europe should ensure their suppliers have this certification to avoid legal complications.
-
API Standards: For accessories related to automotive engines, suppliers may adhere to American Petroleum Institute (API) standards. This is particularly relevant for lubricants and filters, which must meet specific performance criteria.
How Is Quality Controlled During the Manufacturing Process?
Quality control (QC) is integrated at various stages of the manufacturing process to ensure product integrity. Here are key QC checkpoints:
-
Incoming Quality Control (IQC): This initial checkpoint involves inspecting raw materials upon arrival. Suppliers should have protocols to verify material specifications against purchase orders to prevent defects in the final product.
-
In-Process Quality Control (IPQC): During manufacturing, ongoing inspections are conducted to monitor production processes. This includes checks for dimensional accuracy, assembly quality, and adherence to specifications. Automated systems can provide real-time data, enhancing responsiveness to potential issues.
-
Final Quality Control (FQC): Once production is complete, a thorough inspection is performed on the finished products. This may include functional testing, visual inspections, and performance evaluations to ensure compliance with both international standards and customer requirements.
What Common Testing Methods Are Used in Auto Accessories Manufacturing?
Testing is a critical component of quality assurance in auto accessories manufacturing. Some common methods include:
-
Mechanical Testing: This involves assessing the strength, durability, and flexibility of materials. Tensile tests, impact tests, and fatigue tests are often used to simulate real-world conditions.
-
Environmental Testing: Accessories must withstand various environmental factors, such as temperature fluctuations, humidity, and exposure to chemicals. Tests may include salt spray tests for corrosion resistance and thermal cycling tests.
-
Functional Testing: This ensures that products operate as intended. For example, electronic accessories may undergo electrical testing to verify performance under different conditions.
How Can B2B Buyers Verify Supplier Quality Control?
Verifying a supplier’s quality control processes is essential for mitigating risks in international trade. Here are actionable steps buyers can take:
-
Conduct Audits: Regular audits of potential suppliers can provide insights into their manufacturing processes and quality management systems. Buyers should request access to audit reports and certifications.
-
Review Quality Control Reports: Suppliers should provide comprehensive QC reports that detail inspections and testing results. This transparency is crucial in establishing trust.
-
Engage Third-Party Inspection Services: Utilizing third-party inspection services can add an additional layer of assurance. These organizations can perform independent evaluations of manufacturing processes and product quality before shipment.
What Are the Quality Control Nuances for International B2B Buyers?
International B2B buyers must be aware of specific nuances in quality control, particularly when sourcing from diverse regions:
-
Cultural Differences: Understanding local manufacturing practices and cultural attitudes towards quality can influence supplier relationships. For instance, buyers from Europe might have stricter compliance expectations compared to those in Africa or South America.
-
Regulatory Compliance: Buyers must ensure that suppliers comply with both local and international regulations. This includes understanding the necessary certifications for specific markets, such as the EU’s REACH regulation for chemical safety.
-
Language Barriers: Effective communication is crucial for successful collaboration. Buyers should ensure that suppliers can provide documentation and support in a language that is understandable to them, particularly when dealing with complex specifications.
By focusing on these aspects of manufacturing processes and quality assurance, B2B buyers can make informed decisions when selecting auto accessories suppliers, ensuring they receive high-quality products that meet their specific needs and regulatory requirements.
Practical Sourcing Guide: A Step-by-Step Checklist for ‘auto accessories supplier’
To successfully procure auto accessories from suppliers, it’s essential to follow a structured approach that ensures you partner with reliable vendors who meet your specific needs. This checklist will guide you through the critical steps in the sourcing process, enabling you to make informed decisions and establish fruitful business relationships.
Step 1: Define Your Technical Specifications
Before reaching out to suppliers, clearly outline the technical specifications of the auto accessories you require. This could include dimensions, materials, compatibility with vehicle models, and any regulatory standards that must be met. Having a well-defined set of specifications helps streamline communication with suppliers and ensures that the products you receive meet your expectations.
Step 2: Conduct Market Research
Understanding the market landscape is crucial. Investigate current trends, pricing models, and the types of auto accessories that are in demand within your target region (e.g., Africa, South America, the Middle East, Europe). Utilize online resources, industry reports, and trade publications to gather insights. This knowledge will help you identify potential suppliers who can deliver the products that align with market needs.
Step 3: Evaluate Potential Suppliers
Thoroughly vet potential suppliers before making any commitments. Request detailed company profiles, product catalogs, and case studies that showcase their experience in the auto accessories sector. Look for reviews and testimonials from other buyers in similar regions to gauge their reliability and quality of service. This due diligence minimizes the risk of partnering with unqualified suppliers.
Step 4: Verify Supplier Certifications
Ensure that the suppliers you are considering hold the necessary certifications and licenses to operate in your industry. This includes ISO certifications, safety standards, and compliance with international trade regulations. Validating these certifications not only assures product quality but also protects your business from legal liabilities.
Step 5: Request Samples for Quality Assessment
Before placing a large order, request samples of the auto accessories you intend to purchase. Testing these samples allows you to evaluate the quality, functionality, and durability of the products firsthand. Additionally, this step offers an opportunity to assess the supplier’s responsiveness and willingness to accommodate your needs.
Step 6: Negotiate Terms and Conditions
Once you have selected a supplier, engage in negotiations to establish favorable terms and conditions. Discuss pricing, payment methods, delivery timelines, and return policies. Ensure that all agreements are documented in a formal contract to prevent misunderstandings in the future. Clear terms protect both parties and facilitate a smoother procurement process.
Step 7: Establish a Communication Plan
Effective communication is vital for maintaining a successful partnership. Create a communication plan that outlines how often you will check in with the supplier, preferred communication channels, and points of contact on both sides. This proactive approach fosters transparency and helps address any potential issues before they escalate.
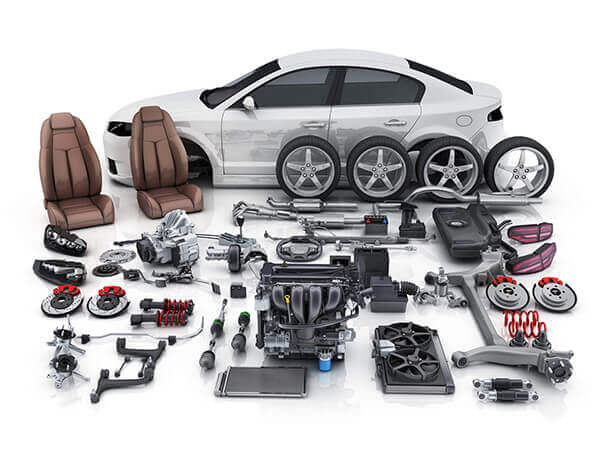
A stock image related to auto accessories supplier.
By following this checklist, international B2B buyers can navigate the complexities of sourcing auto accessories effectively, ensuring that they find the right suppliers to meet their business needs.
Comprehensive Cost and Pricing Analysis for auto accessories supplier Sourcing
What Are the Key Cost Components in Sourcing Auto Accessories?
When sourcing auto accessories, understanding the cost structure is crucial for international B2B buyers. The primary cost components include:
-
Materials: The type of materials used significantly impacts pricing. High-quality materials often result in higher costs but can lead to enhanced durability and customer satisfaction.
-
Labor: Labor costs vary by region and can be influenced by local wage standards. For example, sourcing from regions with lower labor costs, such as parts of Africa or South America, may reduce overall expenses.
-
Manufacturing Overhead: This includes utilities, rent, and administrative expenses associated with production. Efficient factories may offer lower overhead costs, which can translate into better pricing for buyers.
-
Tooling: Initial tooling costs for custom designs can be substantial. Buyers should consider these costs when evaluating price quotes, especially if they require unique specifications.
-
Quality Control (QC): Rigorous QC processes ensure that products meet required standards but can add to overall costs. Investing in suppliers with robust QC can reduce long-term costs related to returns and warranties.
-
Logistics: Shipping and handling costs can vary widely based on distance, shipping method, and the chosen Incoterms. Buyers should factor in logistics when calculating total expenses.
-
Margin: Supplier profit margins can affect pricing. Understanding the typical margins in the industry can help buyers negotiate better terms.
How Do Price Influencers Affect Auto Accessories Pricing?
Several factors can influence the pricing of auto accessories:
-
Volume/MOQ (Minimum Order Quantity): Larger orders typically reduce the per-unit cost. Buyers should assess their capacity to purchase in bulk to take advantage of volume discounts.
-
Specifications and Customization: Custom designs or specific features can increase costs. Buyers should clearly communicate their needs to avoid unexpected charges.
-
Materials: The choice of materials not only affects cost but also impacts the perceived value of the product. Opting for eco-friendly materials can appeal to certain markets but may come with a higher price tag.
-
Quality and Certifications: Products with certifications (like ISO or safety standards) may cost more upfront but can lead to savings in the long run by enhancing brand reputation and reducing liability.
-
Supplier Factors: The reputation and reliability of a supplier can influence pricing. Established suppliers may charge more due to their proven track record, but this can lead to better service and quality assurance.
-
Incoterms: The agreed Incoterms can significantly affect costs. Terms like FOB (Free on Board) may shift transportation costs to the buyer, impacting the total cost of ownership.
What Negotiation Strategies Can Help B2B Buyers Optimize Costs?
For international B2B buyers, particularly from Africa, South America, the Middle East, and Europe, effective negotiation strategies can yield significant cost savings:
-
Understand Total Cost of Ownership (TCO): Evaluate not just the purchase price but the total cost, including shipping, tariffs, and potential repair costs. This comprehensive view helps in making informed decisions.
-
Build Relationships with Suppliers: Establishing strong relationships can lead to better pricing and terms. Suppliers may be more willing to negotiate with trusted partners.
-
Leverage Market Insights: Knowledge of market trends and competitor pricing can provide leverage in negotiations. Being aware of industry standards can help buyers advocate for fair prices.
-
Be Clear About Requirements: Providing detailed specifications and quality expectations can prevent misunderstandings that lead to additional costs. Clear communication can streamline the sourcing process.
-
Negotiate Payment Terms: Favorable payment terms can enhance cash flow. Consider negotiating for extended payment periods or discounts for upfront payments.
Conclusion and Disclaimer
While the insights provided here offer a general overview of costs and pricing for auto accessories sourcing, prices can vary based on specific circumstances and market conditions. Buyers should conduct thorough research and engage in discussions with multiple suppliers to obtain the most accurate pricing information tailored to their needs.
Alternatives Analysis: Comparing auto accessories supplier With Other Solutions
Understanding Alternatives to Auto Accessories Suppliers
In the competitive landscape of auto accessories, B2B buyers often seek various solutions to meet their specific needs. While traditional auto accessories suppliers offer a range of products, there are alternative solutions that can also fulfill similar requirements. These alternatives may vary in terms of performance, cost, ease of implementation, maintenance, and best use cases. Understanding these differences can help buyers make informed decisions that align with their business goals.
Comparison Table of Auto Accessories Supplier and Alternatives
Comparison Aspect | Auto Accessories Supplier | Alternative 1: OEM Partnerships | Alternative 2: Aftermarket Products |
---|---|---|---|
Performance | High quality, standardized | Customized to manufacturer specs | Variable quality, depends on brand |
Cost | Moderate to high | Potentially high, depending on scale | Generally lower than OEM |
Ease of Implementation | Straightforward | Complex, requires agreements | Easy, available through multiple vendors |
Maintenance | Requires regular updates | Manufacturer support available | Varies by product; may require additional support |
Best Use Case | Businesses needing reliability and warranty | Manufacturers wanting brand alignment | Cost-conscious buyers seeking variety |
What Are the Benefits and Drawbacks of OEM Partnerships?
OEM Partnerships involve collaborating with original equipment manufacturers to source auto accessories that meet specific quality and performance standards.
Pros:
– Customization to fit specific vehicle models or business needs.
– High reliability and warranty support from manufacturers.
– Access to cutting-edge technology and innovations.
Cons:
– Higher costs associated with custom manufacturing.
– Lengthy implementation processes due to contractual agreements.
– Limited flexibility in terms of product variation.
This option is ideal for businesses that prioritize quality and have the budget to invest in tailored solutions.
How Do Aftermarket Products Compare to Traditional Suppliers?
Aftermarket Products are those made by companies other than the original manufacturers, often providing a wide range of options.
Pros:
– Generally lower prices, making them attractive for budget-conscious buyers.
– A diverse selection of products, allowing for greater customization.
– Easier availability through numerous retailers and online platforms.
Cons:
– Variable quality; not all aftermarket products meet industry standards.
– Limited or no warranty support, which can lead to higher long-term costs.
– Potential compatibility issues with specific vehicles.
Aftermarket products are suitable for businesses looking for cost-effective solutions without the need for extensive warranties or manufacturer ties.
Conclusion: Choosing the Right Solution for Your B2B Needs
In selecting the right solution for auto accessories, B2B buyers must evaluate their specific requirements, including budget, quality, and implementation capacity. Traditional auto accessories suppliers offer reliability and support, while OEM partnerships provide customization at a premium. On the other hand, aftermarket products present a cost-effective alternative with diverse options but come with varying quality risks. By carefully considering these factors, businesses from regions like Africa, South America, the Middle East, and Europe can make informed choices that align with their operational needs and strategic objectives.
Essential Technical Properties and Trade Terminology for auto accessories supplier
What Are the Key Technical Properties for Auto Accessories?
Understanding the critical specifications of auto accessories is essential for international B2B buyers. Here are some key technical properties you should consider:
-
Material Grade
Material grade refers to the quality and type of materials used in manufacturing auto accessories. Common materials include plastics, metals, and composites. Selecting the right material is crucial as it affects the product’s durability, weight, and resistance to environmental factors. For instance, high-grade aluminum is often preferred for its strength-to-weight ratio in automotive parts. -
Tolerance
Tolerance defines the allowable deviation from a specified dimension in manufacturing. It is vital in ensuring that components fit together properly and function as intended. Tight tolerances are essential for precision parts, while looser tolerances may be acceptable for less critical components. Understanding tolerance levels helps buyers assess the quality and compatibility of parts. -
Surface Finish
The surface finish of auto accessories impacts aesthetics, performance, and durability. Finishes such as anodizing, powder coating, or chrome plating can enhance resistance to corrosion and wear. Buyers should specify surface finish requirements to ensure the product meets both visual and functional criteria. -
Load Capacity
Load capacity indicates the maximum weight or stress an accessory can withstand without failure. This specification is crucial for components like roof racks or towing equipment, where safety is paramount. Buyers must ensure that the load capacity meets their intended use to avoid potential accidents or equipment failure. -
Compatibility
Compatibility refers to how well an accessory integrates with specific vehicle models or systems. It is essential for ensuring that the parts perform as intended. Buyers should always verify compatibility with their vehicles to avoid costly returns or modifications. -
Certifications and Standards
Various certifications (e.g., ISO, SAE) indicate that products meet specific industry standards for quality and safety. Understanding these certifications helps buyers ensure that the products they procure will comply with local regulations and industry best practices.
What Are Common Trade Terms in the Auto Accessories Industry?
Familiarity with trade terminology is equally important for international B2B buyers. Here are some common terms you should know:
-
OEM (Original Equipment Manufacturer)
OEM refers to companies that produce parts or accessories that are used in the original manufacturing of vehicles. Buying OEM parts often guarantees compatibility and quality, as they are designed to meet the vehicle manufacturer’s specifications. -
MOQ (Minimum Order Quantity)
MOQ is the smallest quantity of a product that a supplier is willing to sell. Understanding MOQ is crucial for budgeting and inventory management. Buyers should assess whether they can meet the MOQ without overstocking or incurring additional costs. -
RFQ (Request for Quotation)
An RFQ is a document that buyers send to suppliers to request pricing and terms for specific products. It is a critical step in the procurement process, helping buyers compare offers and make informed purchasing decisions. -
Incoterms (International Commercial Terms)
Incoterms are a set of predefined commercial terms published by the International Chamber of Commerce (ICC). They clarify the responsibilities of buyers and sellers regarding shipping, insurance, and tariffs. Familiarity with Incoterms helps buyers understand their obligations and minimize risks during international trade. -
Lead Time
Lead time refers to the amount of time it takes from placing an order to receiving the goods. Understanding lead time is crucial for inventory management and project planning. Buyers should factor in lead times when scheduling projects or anticipating demand. -
Warranty
A warranty is a guarantee provided by the supplier regarding the quality and performance of the product. It outlines the terms of service and replacement in case of defects. Buyers should review warranty conditions to ensure they are adequately covered for potential issues.
By understanding these technical properties and trade terms, international B2B buyers can make informed decisions when sourcing auto accessories, ultimately leading to more successful transactions and partnerships.
Navigating Market Dynamics and Sourcing Trends in the auto accessories supplier Sector
What Are the Key Trends Influencing the Auto Accessories Supplier Market?
The global auto accessories supplier market is witnessing significant transformation driven by various factors. One of the primary drivers is the growing demand for vehicle customization, which has surged alongside the rise in disposable income and a shift towards personal expression through vehicle modifications. Emerging markets in Africa and South America are particularly ripe for this trend, as consumers increasingly seek unique automotive solutions that reflect their lifestyles.
Technological advancements are reshaping sourcing trends as well. The integration of e-commerce platforms has facilitated easier access to a broader range of products, allowing buyers to compare options quickly and make informed decisions. Digital tools like AI-driven analytics are also enhancing supply chain efficiency, enabling suppliers to predict demand more accurately and manage inventory effectively. Furthermore, the rise of smart automotive accessories—such as GPS devices, dash cameras, and advanced sound systems—reflects a growing consumer preference for connectivity and enhanced driving experiences.
International B2B buyers must also consider regional market dynamics. For instance, in Europe, stringent regulations regarding vehicle emissions and safety standards are pushing suppliers to innovate and offer compliant products. In contrast, markets in the Middle East and Africa may present opportunities in rugged and off-road accessories due to the diverse terrains and driving conditions. Understanding these regional differences can help buyers identify the most suitable suppliers and products for their needs.
How Is Sustainability Impacting B2B Sourcing in the Auto Accessories Sector?
Sustainability is becoming a focal point in the auto accessories supplier sector, driven by increasing consumer awareness and regulatory pressures. The environmental impact of automotive manufacturing and accessory production is significant, prompting buyers to prioritize suppliers that adopt eco-friendly practices. This includes using sustainable materials, reducing waste, and optimizing production processes to minimize carbon footprints.
Ethical sourcing is equally important, as B2B buyers are increasingly scrutinizing their supply chains for transparency and social responsibility. Suppliers that can demonstrate adherence to ethical labor practices and fair trade principles often gain a competitive edge in the market. Certifications such as ISO 14001 for environmental management and Fair Trade certification are becoming crucial for suppliers seeking to appeal to conscientious buyers.
Moreover, the shift towards ‘green’ materials—such as recycled plastics, biodegradable components, and sustainably sourced textiles—can significantly influence purchasing decisions. Buyers from Africa, South America, and the Middle East should look for suppliers who offer these materials to align with global sustainability goals and cater to environmentally conscious consumers in their regions.
What Is the Historical Context of the Auto Accessories Supplier Market?
The auto accessories supplier market has evolved significantly over the decades. Initially, the market was dominated by a few manufacturers offering basic products such as seat covers and floor mats. However, with the advent of globalization in the late 20th century, a surge of new players entered the market, leading to increased competition and innovation.
The early 2000s marked a pivotal shift as the rise of e-commerce transformed how buyers sourced auto accessories. Suppliers began to leverage online platforms to reach international markets, making it easier for B2B buyers from diverse regions, including Europe and Africa, to access a wide range of products. Today, the focus has shifted towards personalization, advanced technology, and sustainability, reflecting broader consumer trends and expectations in the automotive industry.
In summary, understanding the historical context alongside current market dynamics and trends is essential for international B2B buyers looking to navigate the complexities of the auto accessories supplier sector effectively.
Frequently Asked Questions (FAQs) for B2B Buyers of auto accessories supplier
-
How do I evaluate the reliability of an auto accessories supplier?
To assess the reliability of an auto accessories supplier, start by researching their reputation in the industry. Look for customer reviews, testimonials, and case studies. Verify their business credentials, such as certifications and memberships in trade associations. Additionally, consider visiting their manufacturing facility if possible, or request product samples to evaluate quality firsthand. Engaging in direct communication can also provide insight into their customer service and responsiveness, which are crucial for long-term partnerships. -
What is the best way to negotiate payment terms with an auto accessories supplier?
Negotiating favorable payment terms involves clear communication and an understanding of both parties’ needs. Start by discussing your purchasing volume and frequency, as larger orders may warrant better terms. Consider proposing staggered payments or a letter of credit to mitigate risk. Be transparent about your cash flow situation while remaining open to compromise. Document all agreements in the contract to avoid misunderstandings later, and ensure both sides are comfortable with the terms before finalizing the deal. -
How can I ensure quality assurance when sourcing auto accessories?
Quality assurance can be achieved by implementing a multi-step evaluation process. Request samples before placing large orders to assess product quality. Establish clear specifications and standards that the supplier must meet. Consider integrating third-party quality control checks during the manufacturing process. Regular audits and inspections, along with clear communication about quality expectations, will help ensure that the products meet your standards consistently. -
What is the minimum order quantity (MOQ) for auto accessories, and how does it affect my business?
The minimum order quantity (MOQ) varies by supplier and product type. Understanding the MOQ is crucial as it impacts your inventory management and cash flow. Suppliers often set MOQs based on production costs and logistics efficiency. If the MOQ is too high for your needs, consider negotiating for a lower quantity or exploring suppliers who specialize in smaller orders. This flexibility can help you manage risks, especially when entering new markets. -
What are the key considerations for logistics when importing auto accessories?
Logistics is a critical component of sourcing auto accessories. Key considerations include shipping methods, customs regulations, and delivery timelines. Evaluate the supplier’s shipping capabilities and their experience with international logistics. It’s essential to understand the import duties and taxes applicable in your country. Partnering with a reliable freight forwarder can streamline the shipping process and ensure compliance with all legal requirements, ultimately leading to timely deliveries. -
How do I handle disputes with my auto accessories supplier?
Handling disputes effectively requires a proactive approach. Begin by documenting all communications and agreements to provide a clear reference point. Open a dialogue with the supplier to address the issue directly and seek a resolution. If discussions fail, refer to the terms outlined in your contract regarding dispute resolution. Consider mediation or arbitration as alternative methods to resolve conflicts without resorting to litigation, which can be costly and time-consuming. -
What customization options should I discuss with my auto accessories supplier?
Discussing customization options with your supplier can enhance product appeal and meet specific market needs. Inquire about available materials, colors, and design features. Understand the supplier’s capabilities in terms of production flexibility and technology. Also, ask about the lead time for customized orders, as this can affect your inventory planning. A collaborative approach in customization can lead to innovative solutions that differentiate your offerings in competitive markets. -
How can I build a long-term relationship with my auto accessories supplier?
Building a long-term relationship with your supplier involves consistent communication and collaboration. Regularly share your business goals and provide feedback on product performance. Consider visiting the supplier’s facility to strengthen ties and gain insights into their operations. Establishing trust through transparent dealings and timely payments will foster loyalty. Additionally, explore opportunities for joint ventures or co-development projects that can benefit both parties in the long run.
Important Disclaimer & Terms of Use
⚠️ Important Disclaimer
The information provided in this guide, including content regarding manufacturers, technical specifications, and market analysis, is for informational and educational purposes only. It does not constitute professional procurement advice, financial advice, or legal advice.
While we have made every effort to ensure the accuracy and timeliness of the information, we are not responsible for any errors, omissions, or outdated information. Market conditions, company details, and technical standards are subject to change.
B2B buyers must conduct their own independent and thorough due diligence before making any purchasing decisions. This includes contacting suppliers directly, verifying certifications, requesting samples, and seeking professional consultation. The risk of relying on any information in this guide is borne solely by the reader.
Strategic Sourcing Conclusion and Outlook for auto accessories supplier
What Are the Key Takeaways for International B2B Buyers in the Auto Accessories Market?
In the evolving landscape of the auto accessories market, strategic sourcing emerges as a crucial component for international B2B buyers. By prioritizing supplier relationships, understanding regional market dynamics, and leveraging technology for procurement processes, businesses can unlock significant value. Engaging with reliable suppliers not only ensures quality but also enhances supply chain resilience, particularly vital in regions like Africa, South America, the Middle East, and Europe.
How Can Strategic Sourcing Drive Competitive Advantage?
The value of strategic sourcing lies in its ability to foster innovation and cost efficiency. As buyers collaborate closely with suppliers, they can access tailored solutions that meet specific market demands. This collaboration is particularly beneficial for emerging markets, where local insights can drive product relevance and customer satisfaction.
What Does the Future Hold for Auto Accessories Suppliers?
Looking ahead, the auto accessories sector is poised for growth, driven by trends such as sustainability and technological advancements. Buyers are encouraged to adopt a proactive approach to sourcing, integrating sustainability into their procurement strategies. By doing so, they not only enhance their brand reputation but also meet the increasing consumer demand for eco-friendly products.
In conclusion, as international B2B buyers navigate this dynamic market, embracing strategic sourcing will be key to capitalizing on opportunities and ensuring long-term success. Engage with suppliers today to build a robust, future-ready supply chain that can adapt to changing market conditions.