Discover Top Benefits from Electric Arc Furnace Suppliers (2025)
Introduction: Navigating the Global Market for electric arc furnace supplier
In today’s competitive landscape, sourcing the right electric arc furnace supplier is a critical challenge for international B2B buyers. With the increasing demand for sustainable steel production, companies across Africa, South America, the Middle East, and Europe are seeking reliable partners that can provide high-quality, efficient, and environmentally friendly solutions. However, the global market is saturated with options, making the decision-making process complex and often overwhelming.
This comprehensive guide delves into various aspects of electric arc furnaces, including the types available, their applications in different industries, and essential supplier vetting criteria. Buyers will gain insights into cost considerations, technological advancements, and the importance of after-sales support, enabling them to make informed purchasing decisions.
By understanding the nuances of the electric arc furnace market, B2B buyers from regions such as Colombia and Egypt can strategically align their sourcing efforts with their operational goals. This guide empowers businesses to navigate potential pitfalls and select suppliers that not only meet their immediate needs but also support long-term growth and sustainability. Whether you are a first-time buyer or looking to optimize your existing supplier relationships, this resource is designed to enhance your procurement strategy in the global marketplace.
Understanding electric arc furnace supplier Types and Variations
Type Name | Key Distinguishing Features | Primary B2B Applications | Brief Pros & Cons for Buyers |
---|---|---|---|
Conventional Electric Arc Furnace | Utilizes three-phase AC power; large capacity; high efficiency | Steelmaking, scrap recycling | Pros: High output; versatile; cost-effective for large volumes. Cons: Requires significant space; higher initial investment. |
Mini Electric Arc Furnace | Smaller scale; often uses DC power; suitable for lower production levels | Specialty steel production, foundries | Pros: Lower energy consumption; compact design; flexible operations. Cons: Limited output; may not be suitable for large-scale operations. |
Vacuum Electric Arc Furnace | Operates under vacuum; minimizes contamination; high-quality metal production | Aerospace, automotive, and premium alloys | Pros: Produces high-purity materials; reduces oxidation; ideal for high-value applications. Cons: High operational costs; requires skilled operators. |
Induction Electric Arc Furnace | Combines induction heating with arc technology; energy-efficient | Non-ferrous metal processing, specialty alloys | Pros: Faster heating; lower emissions; better energy efficiency. Cons: More complex technology; potential for higher maintenance costs. |
Hybrid Electric Arc Furnace | Integrates traditional and modern technologies; adaptable to various inputs | Recycling, large-scale steel production | Pros: Flexible input materials; optimized energy use; suitable for varying production demands. Cons: Potentially higher initial setup costs; complexity in operation. |
What Are the Characteristics of a Conventional Electric Arc Furnace?
The Conventional Electric Arc Furnace (EAF) is characterized by its use of three-phase alternating current (AC) power. It is typically large in capacity and designed for high-efficiency operations, making it ideal for steelmaking and scrap recycling. B2B buyers should consider the substantial space requirements and the initial investment needed to set up such a furnace. However, the long-term operational cost savings and versatility in production can offset these challenges, making it a popular choice for large manufacturers.
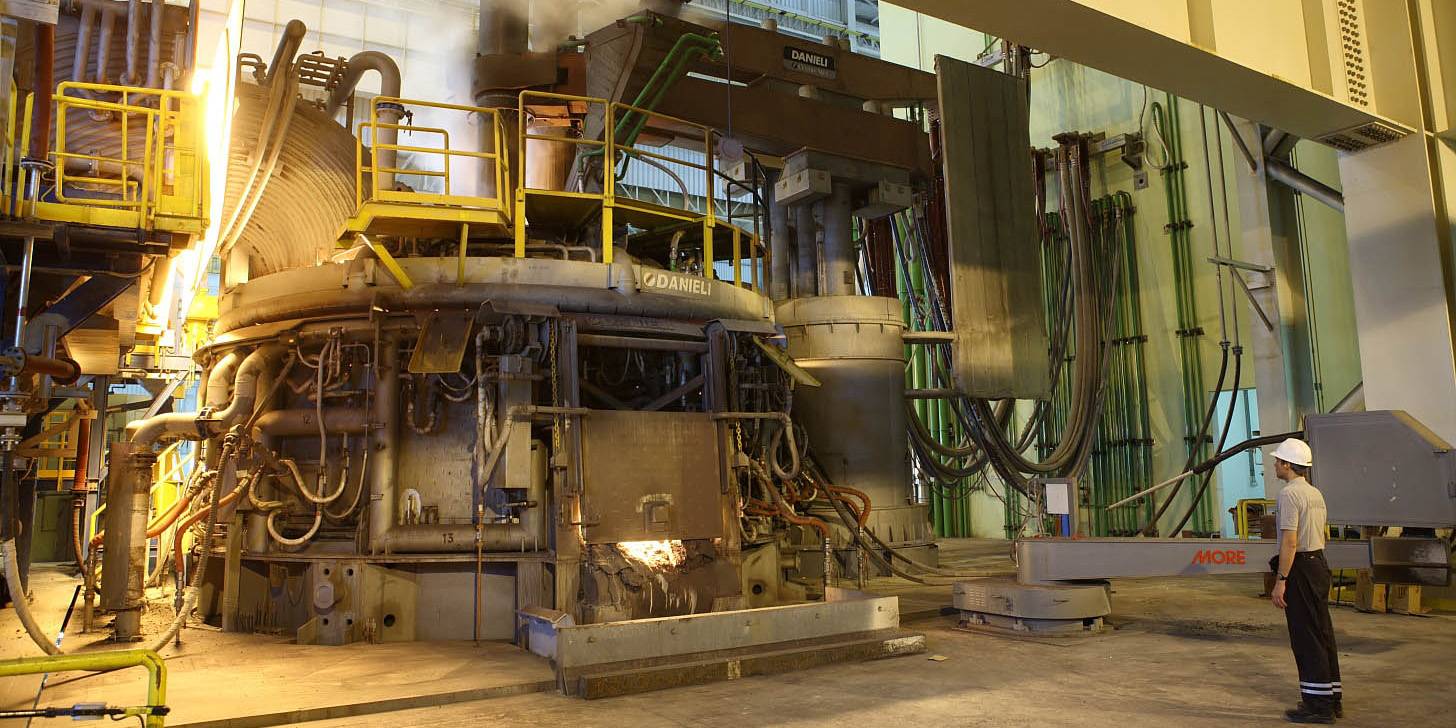
A stock image related to electric arc furnace supplier.
How Does a Mini Electric Arc Furnace Differ from Larger Models?
The Mini Electric Arc Furnace is designed for smaller-scale operations, often utilizing direct current (DC) power. This type of furnace is particularly suitable for specialty steel production and foundries that require lower production levels. Buyers should note its compact design, which allows for easier integration into existing facilities, and its lower energy consumption. However, the output limitations mean it may not be the best choice for large-scale operations, so understanding production needs is crucial before purchasing.
What Are the Benefits of a Vacuum Electric Arc Furnace?
The Vacuum Electric Arc Furnace operates under a vacuum environment, which significantly minimizes contamination during the melting process. This feature makes it particularly valuable in industries requiring high-purity materials, such as aerospace and automotive sectors. While the benefits include producing high-quality alloys, buyers must consider the high operational costs and the necessity for skilled operators to manage this complex technology. Thus, it is most suitable for businesses focusing on premium products.
Why Choose an Induction Electric Arc Furnace?
The Induction Electric Arc Furnace merges induction heating with traditional arc technology, resulting in faster heating and enhanced energy efficiency. This type is particularly advantageous for non-ferrous metal processing and specialty alloys. B2B buyers should weigh the benefits of lower emissions and quicker melting times against the complexity of the technology and potential maintenance costs. It is an excellent option for operations aiming to improve their environmental footprint while maintaining productivity.
What Makes a Hybrid Electric Arc Furnace Unique?
The Hybrid Electric Arc Furnace combines traditional EAF technology with modern innovations, allowing for flexibility in input materials and optimized energy use. This adaptability makes it suitable for recycling and large-scale steel production. Buyers should be aware of the potentially higher initial setup costs and operational complexity. However, the ability to handle varying production demands can lead to significant long-term benefits, particularly for businesses looking to enhance their operational efficiency and sustainability.
Related Video: A Detailed Explanation of the Electric Arc Furnace – What It is and How It Works
Key Industrial Applications of electric arc furnace supplier
Industry/Sector | Specific Application of Electric Arc Furnace Supplier | Value/Benefit for the Business | Key Sourcing Considerations for this Application |
---|---|---|---|
Steel Manufacturing | Scrap Metal Recycling | Cost-effective production of high-quality steel | Supplier reliability, energy efficiency, and capacity |
Foundry and Casting | Production of Cast Iron and Steel Alloys | Enhanced material properties and reduced waste | Material compatibility, precision, and customization |
Non-Ferrous Metal Smelting | Copper and Aluminum Recycling | Sustainable practices and lower raw material costs | Technology level, environmental compliance, and support |
Ferroalloys Production | Production of Ferrochrome and Ferrosilicon | Improved performance in steelmaking | Supplier expertise, quality assurance, and delivery times |
Specialty Alloys | Manufacturing High-Performance Alloys | Tailored solutions for specific applications | Technical support, scalability, and innovation |
How is Electric Arc Furnace Used in Steel Manufacturing?
In the steel manufacturing sector, electric arc furnaces (EAF) are primarily utilized for the recycling of scrap metal. EAF technology allows for the efficient melting of scrap, resulting in high-quality steel production at a lower cost compared to traditional methods. For international B2B buyers, particularly in Africa and South America, sourcing EAF suppliers involves assessing their reliability and energy efficiency, as these factors significantly impact operational costs and sustainability goals.
What is the Role of Electric Arc Furnace in Foundry and Casting?
Electric arc furnaces play a crucial role in the foundry and casting industries, particularly for the production of cast iron and various steel alloys. These furnaces enable the melting of metals with precise temperature control, which is essential for achieving the desired material properties. Buyers in regions like the Middle East and Europe should prioritize suppliers who offer material compatibility and the ability to customize solutions, as this can lead to reduced waste and enhanced product quality.
How Do Electric Arc Furnaces Contribute to Non-Ferrous Metal Smelting?
In the non-ferrous metal smelting industry, electric arc furnaces are increasingly employed for recycling metals such as copper and aluminum. EAF technology supports sustainable practices by reducing the need for virgin raw materials, thus lowering costs and environmental impact. B2B buyers, especially in emerging markets, should consider the technological capabilities of suppliers and their adherence to environmental compliance standards to ensure long-term viability and support for their operations.
What Advantages Does Electric Arc Furnace Offer in Ferroalloys Production?
The ferroalloys production sector benefits significantly from electric arc furnaces, which are used to produce essential ferroalloys like ferrochrome and ferrosilicon. These materials are critical for enhancing the performance of steelmaking processes. When sourcing EAF suppliers, businesses should evaluate the supplier’s expertise in ferroalloy production, quality assurance processes, and delivery timelines to ensure consistent supply and optimal performance in their manufacturing operations.
How are Specialty Alloys Manufactured Using Electric Arc Furnaces?
Electric arc furnaces are essential in the manufacturing of high-performance specialty alloys, which are tailored for specific applications in industries such as aerospace and automotive. The ability of EAFs to provide precise control over the melting and alloying processes allows for the development of innovative materials. For international B2B buyers, particularly those in Europe and South America, it is vital to engage with suppliers who offer strong technical support and scalability, ensuring that the solutions provided meet their unique requirements and future growth plans.
3 Common User Pain Points for ‘electric arc furnace supplier’ & Their Solutions
Scenario 1: Unpredictable Operational Costs in Electric Arc Furnaces
The Problem:
B2B buyers often face the challenge of unpredictable operational costs associated with electric arc furnaces (EAFs). This unpredictability can stem from fluctuating electricity prices, variances in raw material costs, and the need for frequent maintenance. For companies in regions like Africa and South America, where energy costs can be volatile, these financial uncertainties can lead to budget overruns and hinder long-term planning.
The Solution:
To mitigate unpredictable operational costs, buyers should conduct thorough market research on electricity tariffs and raw material pricing trends before procurement. Engaging with multiple suppliers to get a comprehensive view of potential costs will provide leverage in negotiations. Additionally, investing in energy management systems can help monitor and optimize energy consumption. Regular maintenance schedules and predictive maintenance technologies can further reduce unexpected downtimes and repair costs, ensuring that the EAF operates efficiently. It’s also beneficial to consider suppliers that offer comprehensive service agreements to stabilize maintenance costs over time.
Scenario 2: Limited Technical Support and Training for Electric Arc Furnace Operation
The Problem:
Another significant pain point is the lack of adequate technical support and training for staff operating electric arc furnaces. Many suppliers may provide the equipment but fail to offer sufficient training, especially in emerging markets in the Middle East or Africa, where skilled labor may be scarce. This can lead to operational inefficiencies, increased safety risks, and ultimately, higher operational costs.
The Solution:
When selecting an electric arc furnace supplier, buyers should prioritize those who offer extensive training programs and ongoing technical support. This includes on-site training for operators as well as remote assistance options. Buyers should also inquire about the availability of instructional materials, such as manuals and video tutorials, that can be used for continuous learning. Establishing a partnership with suppliers that provide comprehensive after-sales support can enhance the skill level of staff, leading to improved safety and efficiency in operations. Additionally, consider investing in simulation software that allows operators to practice their skills in a risk-free environment before handling real equipment.
Scenario 3: Challenges in Sourcing High-Quality Raw Materials
The Problem:
Sourcing high-quality raw materials for electric arc furnaces is a common challenge that can significantly impact production quality and efficiency. B2B buyers, particularly in regions like Europe and South America, may struggle with inconsistent supply chains and varying quality standards from local suppliers. This inconsistency can lead to issues such as poor melt quality and increased operational disruptions.
The Solution:
To address sourcing challenges, buyers should establish strong relationships with reliable raw material suppliers who can guarantee quality and consistency. Conducting thorough due diligence on suppliers, including site visits and quality audits, can help ensure that they meet required standards. Additionally, consider diversifying the supply chain by identifying multiple suppliers in different regions, reducing dependency on a single source and enhancing resilience against supply chain disruptions. Implementing strict quality control measures, such as regular material testing and certifications, can further ensure that only high-quality materials are used in the electric arc furnace process. Leveraging technology, such as blockchain, can enhance transparency and traceability in the supply chain, ensuring that materials meet the required specifications.
Strategic Material Selection Guide for electric arc furnace supplier
When selecting materials for electric arc furnaces (EAF), international B2B buyers must consider various factors that directly impact performance, durability, and cost-effectiveness. This guide analyzes common materials used in EAF applications, providing actionable insights for buyers from Africa, South America, the Middle East, and Europe.
What Are the Key Properties of Refractory Materials in Electric Arc Furnaces?
Refractory materials are essential for lining electric arc furnaces, as they withstand high temperatures and protect the furnace structure. Common types of refractory materials include alumina, magnesia, and zirconia.
- Alumina: Known for its high melting point (over 2000°C) and excellent thermal stability, alumina is widely used in EAF linings. Its corrosion resistance to basic slags makes it suitable for steel production.
- Magnesia: With a melting point exceeding 2800°C, magnesia offers superior resistance to basic environments. It is often chosen for its durability, especially in high-demand applications.
- Zirconia: Although more expensive, zirconia provides exceptional thermal insulation and resistance to thermal shock, making it ideal for specific high-performance applications.
What Are the Pros and Cons of Using Carbon-Based Materials?
Carbon-based materials, such as graphite and carbon bricks, are integral to the EAF process due to their electrical conductivity and thermal resistance.
- Pros: Carbon materials are highly durable and can withstand extreme temperatures. Their ability to conduct electricity efficiently enhances the melting process.
- Cons: However, carbon materials can be costly and may require complex manufacturing processes. They are also susceptible to oxidation, which could limit their lifespan in certain applications.
How Do Alloying Elements Affect Electric Arc Furnace Performance?
Alloying elements play a crucial role in the final product’s quality and performance. Common alloying elements include manganese, chromium, and nickel.
- Manganese: This element enhances the toughness and wear resistance of steel, making it a popular choice in EAF operations.
- Chromium: Known for its corrosion resistance, chromium improves the hardness and strength of the final product but can increase costs.
- Nickel: While it significantly enhances corrosion resistance and toughness, nickel is one of the more expensive alloying elements, which may impact cost-effectiveness.
What Should International B2B Buyers Consider When Selecting Materials?
International buyers, particularly from regions like Africa, South America, the Middle East, and Europe, must navigate various compliance and standardization issues. Familiarity with common standards such as ASTM, DIN, and JIS is crucial for ensuring material quality and compatibility. Additionally, buyers should consider regional availability and supply chain logistics, which can significantly impact lead times and costs. Understanding local regulations regarding material usage and environmental impact is also essential for compliance and sustainability.
Summary Table of Material Selection for Electric Arc Furnaces
Material | Typical Use Case for electric arc furnace supplier | Key Advantage | Key Disadvantage/Limitation | Relative Cost (Low/Med/High) |
---|---|---|---|---|
Alumina | Lining for EAFs in steel production | High thermal stability and corrosion resistance | Limited performance in acidic environments | Medium |
Magnesia | High-demand applications requiring durability | Superior resistance to basic slags | Higher cost compared to alumina | High |
Zirconia | Specialized high-performance applications | Excellent thermal insulation and shock resistance | Expensive and less commonly available | High |
Carbon-based | Conductive linings and structural components | High durability and electrical conductivity | Susceptible to oxidation and costly | Medium |
This strategic material selection guide equips international B2B buyers with the necessary insights to make informed decisions, ensuring that they choose the right materials for their electric arc furnace applications.
In-depth Look: Manufacturing Processes and Quality Assurance for electric arc furnace supplier
Electric arc furnaces (EAF) have become essential in the steelmaking industry, and understanding the manufacturing processes and quality assurance measures of suppliers is crucial for international B2B buyers. This section explores the typical manufacturing processes involved in producing electric arc furnaces and the quality assurance protocols that ensure compliance with international standards.
What Are the Main Stages of Electric Arc Furnace Manufacturing?
Manufacturing an electric arc furnace involves several key stages, each critical to ensuring the final product meets the required specifications.
1. Material Preparation
The first step in the manufacturing process is material preparation. High-quality raw materials such as scrap steel, direct reduced iron (DRI), and various alloys are sourced based on the specific requirements of the furnace. Suppliers often leverage local sourcing strategies to minimize costs while ensuring material quality. Buyers should inquire about the supplier’s sourcing practices and the quality of the raw materials used, as these factors significantly affect the overall performance of the electric arc furnace.
2. Forming
Once the materials are prepared, they undergo forming, which typically involves processes like casting and machining. The molten steel is poured into molds to create the furnace shell and other components. Advanced techniques such as precision machining are employed to ensure that the parts fit together perfectly, which is essential for the furnace’s efficiency. Buyers should evaluate the supplier’s forming capabilities and technologies to ensure they can produce the specific designs required.
3. Assembly
After forming, the assembly stage begins. This involves fitting together various components, including the furnace shell, electrodes, and cooling systems. Effective assembly techniques, such as robotic welding and automated quality checks, are often employed to enhance precision and reduce human error. B2B buyers should assess whether the supplier utilizes advanced assembly technologies, as this can impact the longevity and performance of the furnace.
4. Finishing
The finishing stage includes surface treatment processes like shot blasting, painting, or coating to protect against corrosion and wear. This stage is crucial for ensuring the furnace’s durability in high-temperature environments. Buyers should verify the types of finishing processes used and their effectiveness in prolonging the life of the electric arc furnace.
How Is Quality Assurance Implemented in Electric Arc Furnace Manufacturing?
Quality assurance (QA) is a vital component in the manufacturing of electric arc furnaces. Suppliers typically adhere to both international and industry-specific standards to ensure their products meet the highest quality benchmarks.
What Are the Relevant International Standards for Electric Arc Furnace Suppliers?
International standards, such as ISO 9001, are critical for suppliers, as they provide a framework for quality management systems (QMS). Compliance with these standards ensures that suppliers have established processes for continuous improvement and customer satisfaction. Additionally, industry-specific certifications like CE marking in Europe or API specifications may be relevant depending on the furnace’s application. Buyers should request documentation proving the supplier’s compliance with these standards to ensure reliability.
What Are the Key Quality Control Checkpoints?
Quality control (QC) involves several checkpoints throughout the manufacturing process. Common checkpoints include:
- Incoming Quality Control (IQC): Verification of raw materials upon receipt to ensure they meet specified quality standards.
- In-Process Quality Control (IPQC): Ongoing inspections during manufacturing to monitor compliance with design specifications and quality standards.
- Final Quality Control (FQC): Comprehensive testing and inspection of the finished product to ensure it meets all performance criteria before shipping.
B2B buyers should inquire about the supplier’s QC processes and the frequency of these inspections, as rigorous QC measures can significantly reduce the risk of defects.
What Testing Methods Are Commonly Used for Electric Arc Furnaces?
Testing methods play a crucial role in quality assurance for electric arc furnaces. Common methods include:
- Non-Destructive Testing (NDT): Techniques like ultrasonic testing or radiography are used to identify internal flaws without damaging the components.
- Mechanical Testing: Evaluating properties such as tensile strength and fatigue resistance to ensure materials can withstand operational stresses.
- Performance Testing: Simulating operational conditions to assess the furnace’s efficiency and effectiveness.
Buyers should ensure that their suppliers conduct thorough testing and can provide detailed reports to verify compliance with required standards.
How Can B2B Buyers Verify Supplier Quality Control?
Verifying a supplier’s quality control measures is essential for international buyers. Here are several strategies to ensure your supplier meets quality expectations:
- Conduct Supplier Audits: Regular audits can help buyers assess the supplier’s manufacturing processes and quality control measures. This can be done through on-site visits or third-party audit services.
- Request Quality Assurance Reports: Buyers should ask for detailed reports outlining the QC processes, including inspection results and compliance with standards.
- Engage Third-Party Inspectors: Utilizing third-party inspection services provides an unbiased evaluation of the supplier’s quality assurance practices. This can be particularly important when sourcing from regions with varying standards.
What Are the Quality Control Nuances for International B2B Buyers?
When sourcing electric arc furnaces from international suppliers, particularly from regions like Africa, South America, the Middle East, and Europe, buyers should be aware of specific nuances:
- Cultural Differences in Quality Standards: Different regions may have varying interpretations of quality assurance standards. It’s crucial to establish clear expectations and understand the local context.
- Logistical Considerations: Ensure that quality control measures are not compromised during shipping. Buyers should discuss logistics and handling processes with suppliers to mitigate risks.
- Regulatory Compliance: Familiarize yourself with the regulatory landscape in both the supplier’s and your own country. This includes import regulations and safety standards that must be adhered to.
By understanding these manufacturing processes and quality assurance protocols, international B2B buyers can make informed decisions when selecting electric arc furnace suppliers, ensuring they meet their operational needs and quality expectations.
Practical Sourcing Guide: A Step-by-Step Checklist for ‘electric arc furnace supplier’
Introduction
Sourcing an electric arc furnace (EAF) supplier is a critical process for businesses involved in steel manufacturing and other metallurgical applications. This guide provides a structured checklist to help international B2B buyers, particularly from Africa, South America, the Middle East, and Europe, navigate the complexities of selecting a reliable EAF supplier. By following these steps, you can ensure that your procurement process is thorough, strategic, and aligned with your operational needs.
Step 1: Define Your Technical Specifications
Before initiating the sourcing process, it’s essential to articulate your technical requirements. This includes understanding the specific capacity, power requirements, and operational features you need in an electric arc furnace.
– Considerations: Assess your production volume, desired output quality, and any unique features necessary for your operations. Document these specifications to facilitate discussions with potential suppliers.
Step 2: Research Potential Suppliers
Conduct thorough research to identify potential EAF suppliers. Utilize industry databases, trade shows, and online platforms to compile a list of candidates.
– Resources: Websites like Alibaba, ThomasNet, and industry-specific directories can be invaluable. Look for suppliers that have a proven track record in your specific region or industry.
Step 3: Evaluate Supplier Credentials
Before committing to any supplier, it’s crucial to vet them thoroughly. Request company profiles, certifications, and evidence of past projects similar to your requirements.
– What to Look For: Check for ISO certifications, industry awards, and compliance with local regulations. This information can help you gauge the supplier’s reliability and quality standards.
Step 4: Request Detailed Proposals
Engage shortlisted suppliers by requesting comprehensive proposals that include technical specifications, pricing, and delivery timelines.
– Important Aspects: Analyze the proposals for clarity and completeness. Ensure that they address your specific needs and include terms regarding warranties, maintenance, and after-sales support.
Step 5: Visit Supplier Facilities
If feasible, plan a visit to the supplier’s manufacturing facility. This step allows you to assess their production capabilities and quality control processes firsthand.
– What to Observe: Look for the technology used, cleanliness of the facility, and the professionalism of the workforce. This insight can help you make an informed decision regarding their operational standards.
Step 6: Conduct Reference Checks
Before finalizing your choice, conduct reference checks with previous clients of the suppliers you are considering.
– Key Questions: Inquire about their experience with delivery timelines, product quality, and customer service. This feedback can provide valuable insights into the supplier’s reliability and performance.
Step 7: Negotiate Terms and Conditions
Once you have selected a supplier, engage in negotiations to finalize terms and conditions. Ensure that both parties have a clear understanding of pricing, delivery schedules, and payment terms.
– Focus Areas: Pay attention to the warranty and support terms offered. Clarify any contingencies for delays or defects to avoid disputes later on.
By following this checklist, B2B buyers can effectively streamline their sourcing process for electric arc furnace suppliers, ensuring that they select a partner who meets their technical needs and aligns with their business goals.
Comprehensive Cost and Pricing Analysis for electric arc furnace supplier Sourcing
When sourcing electric arc furnaces (EAFs), understanding the comprehensive cost structure and pricing dynamics is essential for international B2B buyers. This analysis will delve into the key cost components, price influencers, and actionable tips to optimize procurement strategies, particularly for buyers from Africa, South America, the Middle East, and Europe.
What Are the Key Cost Components in Electric Arc Furnace Sourcing?
-
Materials: The cost of raw materials, such as steel scrap, electrodes, and refractories, forms a significant portion of the total expenditure. Prices can fluctuate based on global market trends and local availability, impacting the overall cost structure.
-
Labor: Skilled labor is essential for the manufacturing and installation of electric arc furnaces. Labor costs can vary widely depending on the region, with countries in Europe often facing higher wages compared to those in Africa or South America.
-
Manufacturing Overhead: This includes costs related to utilities, factory maintenance, and administrative expenses. Efficient manufacturing processes can help reduce these overhead costs, making it vital to assess suppliers’ operational efficiencies.
-
Tooling: The design and production of specialized tools for EAF manufacturing can incur significant upfront costs. Suppliers with advanced tooling capabilities may offer better quality products but at a higher price.
-
Quality Control (QC): Ensuring the EAF meets international quality standards requires investment in QC processes. Suppliers that emphasize stringent quality checks may charge a premium, but this can lead to reduced operational risks and longer equipment lifespans.
-
Logistics: Transportation and shipping costs can vary significantly based on distance, mode of transport, and regional tariffs. Buyers should factor in these costs when evaluating supplier proposals, especially for international shipments.
-
Margin: Suppliers will incorporate a profit margin into their pricing, which can differ based on their market positioning and the perceived value of their products.
How Do Price Influencers Affect Electric Arc Furnace Procurement?
-
Volume and Minimum Order Quantity (MOQ): Purchasing in larger volumes often leads to discounts. Understanding a supplier’s MOQ can help buyers negotiate better pricing.
-
Specifications and Customization: Custom-built EAFs tailored to specific production needs can command higher prices. Buyers should balance the need for customization with budget constraints.
-
Material Quality and Certifications: Suppliers that provide high-quality materials and relevant certifications (e.g., ISO) may charge more. However, investing in quality can lead to lower maintenance costs and improved operational efficiency.
-
Supplier Factors: The reputation and reliability of suppliers can influence pricing. Established suppliers with proven track records may charge a premium, but they often offer better support and warranty services.
-
Incoterms: Understanding the terms of trade can impact the total cost. Buyers should clarify responsibilities regarding shipping, insurance, and customs duties to avoid unexpected expenses.
What Are Some Buyer Tips for Cost-Efficient Electric Arc Furnace Sourcing?
-
Negotiate Effectively: Leverage competitive quotes from multiple suppliers to negotiate better pricing. Establishing long-term relationships can also provide room for more favorable terms.
-
Consider Total Cost of Ownership (TCO): While upfront costs are important, consider the TCO, which includes maintenance, operational efficiency, and potential downtime. A slightly higher initial investment may yield significant savings over time.
-
Understand Pricing Nuances for International Buyers: Currency fluctuations, import duties, and local regulations can affect pricing. Buyers from regions like Africa and South America should be particularly vigilant about these factors, as they can substantially impact the final cost.
-
Stay Informed on Market Trends: Regularly monitor market conditions and commodity prices to make informed purchasing decisions. Being aware of trends can help in timing purchases for optimal pricing.
Conclusion
Navigating the complexities of sourcing electric arc furnaces requires a deep understanding of cost structures and pricing dynamics. By considering the outlined cost components and price influencers, and implementing strategic buyer tips, international B2B buyers can enhance their procurement processes, leading to more efficient and cost-effective operations. Always remember that indicative prices may vary based on specific requirements and market conditions, so thorough due diligence is essential.
Alternatives Analysis: Comparing electric arc furnace supplier With Other Solutions
Understanding the Importance of Alternative Solutions in Electric Arc Furnace Applications
In the rapidly evolving landscape of industrial manufacturing, B2B buyers must consider various options when evaluating electric arc furnace (EAF) suppliers. While EAF technology is widely recognized for its efficiency and flexibility in steel production, it’s essential to explore alternative solutions that may better suit specific operational needs and budget constraints. This analysis compares EAFs with two viable alternatives: induction furnaces and blast furnaces, focusing on key aspects that influence decision-making for international buyers from regions such as Africa, South America, the Middle East, and Europe.
Comparison Aspect | Electric Arc Furnace Supplier | Induction Furnace | Blast Furnace |
---|---|---|---|
Performance | High energy efficiency; flexible operation; ideal for scrap metal recycling | Moderate efficiency; effective for smaller batches | High output; suitable for large-scale production |
Cost | Higher initial capital costs but lower operational costs | Lower initial costs; higher energy costs | High capital and operational costs; requires significant resources |
Ease of Implementation | Complex installation; requires skilled labor for setup | Easier to install and operate; less skilled labor needed | Complex setup; requires extensive infrastructure |
Maintenance | Moderate maintenance; requires skilled technicians | Low maintenance; less technical expertise required | High maintenance; requires specialized knowledge |
Best Use Case | Recycling scrap metal; producing high-quality steel | Smaller operations; specialty metal applications | Large-scale steel production; high-volume output |
What Are the Advantages and Disadvantages of Induction Furnaces?
Induction furnaces utilize electromagnetic induction to heat and melt metal, making them a compelling alternative for certain applications. The primary advantage is their lower initial investment cost and ease of operation, which can be particularly appealing for smaller manufacturers or those new to metal production. However, induction furnaces tend to have higher energy costs and are less efficient for large-scale production, limiting their use in high-volume settings.
How Do Blast Furnaces Compare to Electric Arc Furnaces?
Blast furnaces have long been the backbone of traditional steelmaking, especially for high-volume production needs. They excel in producing large quantities of steel but come with significant capital and operational expenses. The complexity of setup and maintenance, alongside their environmental impact, makes them less favorable for companies looking to adopt more sustainable practices. Nonetheless, for businesses focused on mass production, blast furnaces may still present a viable option.
Conclusion: How Should B2B Buyers Choose the Right Furnace Technology?
When selecting between electric arc furnaces, induction furnaces, and blast furnaces, international B2B buyers must assess their specific operational requirements, budget constraints, and long-term production goals. Factors such as production scale, material types, and environmental considerations should heavily influence the decision-making process. By weighing the pros and cons of each alternative against their unique needs, buyers can make informed choices that align with their strategic objectives, ensuring both economic viability and operational efficiency in their manufacturing processes.
Essential Technical Properties and Trade Terminology for electric arc furnace supplier
What Are the Key Technical Properties of Electric Arc Furnaces?
Understanding the technical specifications of electric arc furnaces (EAF) is crucial for B2B buyers, particularly those in regions like Africa, South America, the Middle East, and Europe. Here are some of the essential properties to consider:
1. Material Grade
The material grade of an electric arc furnace directly affects its performance and lifespan. Common grades include carbon steel and stainless steel. Buyers should evaluate the material based on their production needs, as higher-grade materials often offer better durability and resistance to thermal stress. This is particularly important for industries requiring high-quality steel, such as automotive and construction.
2. Tolerance Levels
Tolerance levels refer to the allowable deviation from specified dimensions and are critical for ensuring the precision of the furnace components. Inaccurate tolerances can lead to operational inefficiencies and increased maintenance costs. Buyers should ensure that suppliers can meet the required tolerances to avoid disruptions in production processes.
3. Power Input Capacity
The power input capacity of an EAF is a vital specification that determines the furnace’s efficiency and output. Typically measured in megawatts (MW), this property dictates how much energy the furnace can consume while melting materials. For buyers, understanding the power requirements is essential for aligning with local energy regulations and costs, which can vary significantly across different regions.
4. Electrode Type and Size
The type and size of electrodes used in the EAF influence its melting efficiency and operational costs. Common electrode materials include graphite and copper. Buyers should consider the electrode specifications, as these can impact the furnace’s performance and the quality of the final steel product. Proper electrode selection can also enhance the energy efficiency of the melting process.
5. Cooling Systems
Effective cooling systems are crucial for maintaining the operational stability of electric arc furnaces. Various cooling methods, such as water-cooled panels and air-cooling systems, can be employed. Buyers should assess the cooling technology used by potential suppliers to ensure it meets the thermal management needs of their operations, particularly in hotter climates.
What Are the Common Trade Terms Used in Electric Arc Furnace Supply?
Familiarizing yourself with industry terminology can streamline the procurement process and enhance communication with suppliers. Here are some essential trade terms to know:
1. OEM (Original Equipment Manufacturer)
An OEM is a company that produces parts or equipment that may be marketed by another manufacturer. In the context of EAFs, knowing whether a supplier is an OEM can assure buyers of the quality and compatibility of the components.
2. MOQ (Minimum Order Quantity)
MOQ refers to the smallest quantity of a product that a supplier is willing to sell. Understanding MOQ is crucial for buyers to manage inventory and budget effectively, especially for companies in regions with fluctuating demand.
3. RFQ (Request for Quotation)
An RFQ is a document issued by buyers to request pricing and terms from suppliers. This process is essential for comparing costs and understanding the full scope of what suppliers offer. Buyers should prepare detailed RFQs to ensure they receive accurate and comprehensive responses.
4. Incoterms (International Commercial Terms)
Incoterms are a series of predefined commercial terms published by the International Chamber of Commerce. They clarify the responsibilities of buyers and sellers in international transactions. Understanding these terms is critical for B2B buyers as they dictate shipping responsibilities, risk, and insurance obligations.
5. Lead Time
Lead time refers to the time between placing an order and receiving it. This term is particularly important for international buyers, as lead times can vary significantly based on geographic location and the supplier’s production capacity. Managing lead times effectively can help mitigate production delays.
By grasping these technical properties and trade terms, international B2B buyers can make informed decisions when sourcing electric arc furnaces, ultimately leading to more successful procurement and production outcomes.
Navigating Market Dynamics and Sourcing Trends in the electric arc furnace supplier Sector
What Are the Current Market Dynamics in the Electric Arc Furnace Supplier Sector?
The electric arc furnace (EAF) sector is witnessing significant transformations driven by technological advancements and shifting market demands. Global initiatives aimed at reducing carbon emissions and promoting sustainability are increasingly influencing the supply chain dynamics. For international B2B buyers, particularly those in Africa, South America, the Middle East, and Europe, understanding these trends is essential for strategic sourcing decisions.
One of the most notable trends is the growing adoption of automation and digitalization within EAF operations. Technologies such as IoT and AI are being integrated to enhance efficiency and productivity, allowing suppliers to offer better insights and data analytics to their clients. This shift not only reduces operational costs but also aids in predictive maintenance, minimizing downtime.
Moreover, the demand for scrap metal as a feedstock for EAFs is rising, particularly in regions like Europe and South America, where recycling initiatives are becoming increasingly robust. Buyers are encouraged to forge relationships with suppliers who can guarantee a consistent and quality supply of scrap materials, as this will impact both production costs and sustainability goals.
Additionally, geopolitical factors, including trade agreements and tariffs, can influence sourcing strategies. Buyers should stay informed about regional trade policies that may affect the availability and pricing of EAF technology and components.
How Does Sustainability Impact Sourcing in the Electric Arc Furnace Sector?
Sustainability has emerged as a critical component in the sourcing strategy for electric arc furnace suppliers. The environmental impact of steel production is substantial, and EAF technology offers a cleaner alternative compared to traditional blast furnaces. This shift is particularly important for international buyers from regions such as Africa and the Middle East, where environmental regulations are tightening.
Ethical sourcing is gaining traction as buyers increasingly prioritize suppliers who adhere to sustainable practices. This includes the use of ‘green’ certifications and materials that reduce carbon footprints. Suppliers that can demonstrate a commitment to sustainability not only enhance their credibility but also attract buyers who are looking to improve their own environmental impact.
Furthermore, establishing ethical supply chains is essential. Buyers should conduct thorough due diligence to ensure that their suppliers are compliant with international environmental standards and labor practices. Engaging with suppliers who prioritize sustainability can also lead to long-term partnerships, as both parties work towards shared goals in reducing environmental impacts.
Incorporating sustainable practices into sourcing strategies not only aligns with global trends but also prepares businesses for future regulatory requirements. Buyers should actively seek out suppliers that provide transparency in their operations, as this can significantly influence their brand reputation and operational success.
What Is the Historical Context of Electric Arc Furnace Technology?
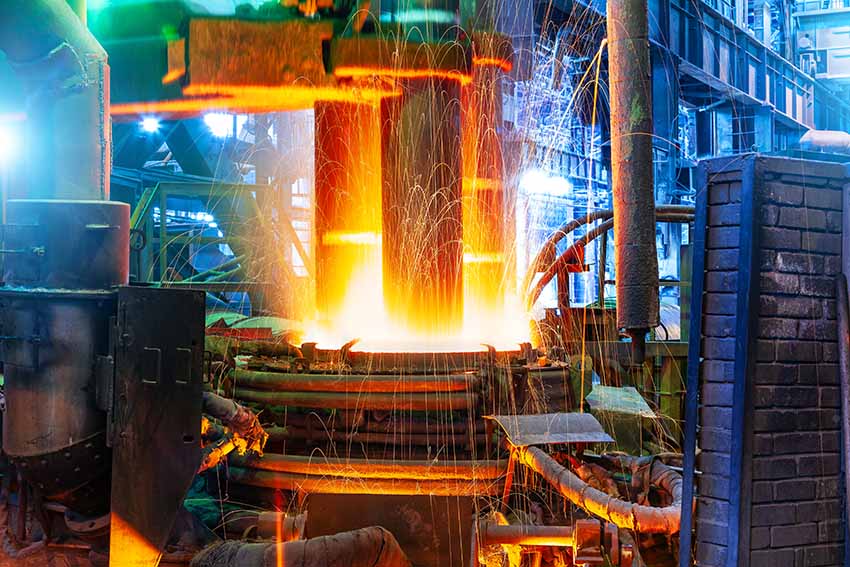
A stock image related to electric arc furnace supplier.
The electric arc furnace technology has evolved significantly since its inception in the late 19th century. Originally developed to produce high-quality steel, EAFs have undergone numerous innovations, particularly in the 20th century with the introduction of improved refractory materials and electrical systems. These advancements have led to increased efficiency, lower energy consumption, and a reduced environmental impact compared to traditional steel-making methods.
As global demand for steel has fluctuated, the EAF sector has adapted to meet changing market conditions. Today, EAFs are recognized for their flexibility and ability to utilize a variety of raw materials, making them a preferred choice for many manufacturers aiming for sustainability. Understanding this historical evolution allows international B2B buyers to appreciate the technological advancements and operational efficiencies that modern EAF suppliers bring to the table.
Frequently Asked Questions (FAQs) for B2B Buyers of electric arc furnace supplier
-
How do I choose the right electric arc furnace supplier for my needs?
Selecting the right electric arc furnace supplier involves evaluating several key factors. Begin by assessing the supplier’s experience in your specific industry and their track record of successful installations. Look for certifications that demonstrate compliance with international standards. Additionally, consider their ability to provide customization options, technical support, and after-sales service. Engaging with previous clients for testimonials can offer insights into their reliability and performance. Finally, ensure the supplier has a robust supply chain that can deliver components and spare parts in a timely manner. -
What are the common specifications I should look for in an electric arc furnace?
When sourcing an electric arc furnace, key specifications to consider include capacity (measured in tons), voltage requirements, and energy efficiency ratings. Additionally, evaluate the furnace’s design features, such as the type of electrodes used and the cooling systems in place. Understanding the operational flexibility—such as the ability to handle different types of scrap metals—can also be vital for optimizing production. Lastly, inquire about the furnace’s environmental compliance, particularly regarding emissions and waste management, to align with regulatory standards in your region. -
What is the minimum order quantity (MOQ) for electric arc furnaces?
The minimum order quantity for electric arc furnaces can vary significantly based on the supplier and the specific model. Many suppliers prefer larger orders due to the high cost of production and shipping. However, some may accommodate smaller orders, particularly for custom or specialized furnaces. It is advisable to discuss your needs directly with potential suppliers to understand their MOQ policies. Additionally, consider negotiating terms that allow for trial orders or phased deliveries, especially if you are entering a new market or testing the equipment’s compatibility with your operations. -
What payment terms should I expect when purchasing an electric arc furnace?
Payment terms for electric arc furnaces typically include a deposit followed by balance payment upon delivery or installation. Common practices involve a 30% to 50% upfront payment, with the remainder due upon shipment or completion of installation. It’s essential to clarify these terms with your supplier and ensure they align with your cash flow management. In some cases, suppliers may offer financing options or payment plans, particularly for large orders. Always verify the supplier’s credibility before making any payments to mitigate risks associated with international transactions. -
How can I ensure quality assurance (QA) when sourcing electric arc furnaces?
To ensure quality assurance when sourcing electric arc furnaces, request detailed documentation of the manufacturing processes, including quality control measures. Many reputable suppliers will provide ISO certifications or other relevant quality standards. Additionally, consider conducting factory visits or audits to assess their production capabilities firsthand. If feasible, ask for samples or trial runs to evaluate the equipment’s performance before full-scale purchase. Finally, establish clear communication channels to discuss any QA concerns that may arise during or after installation. -
What logistics considerations should I keep in mind when importing electric arc furnaces?
When importing electric arc furnaces, logistics considerations include shipping methods, customs clearance, and delivery timelines. Determine whether the supplier can handle logistics or if you will need to engage a freight forwarder. Understanding the shipping terms (FOB, CIF, etc.) is crucial for budgeting and risk management. Additionally, research import regulations specific to your country to avoid delays. It’s also wise to account for potential tariffs and duties, which can significantly impact the overall cost. Ensure that you have a robust plan for receiving and installing the equipment upon arrival. -
How do I evaluate the technical support provided by electric arc furnace suppliers?
Evaluating technical support from electric arc furnace suppliers involves assessing their availability, responsiveness, and expertise. Inquire about their customer service channels, including phone, email, and on-site support. A reliable supplier should provide comprehensive training for your team on operation and maintenance. Additionally, consider whether they offer ongoing support, such as troubleshooting and spare parts availability. Reading reviews from other clients can provide insights into their support quality. Establishing a good relationship with your supplier can also facilitate quicker resolution of any technical issues that may arise. -
What are the key environmental considerations when selecting an electric arc furnace?
When selecting an electric arc furnace, key environmental considerations include energy consumption, emissions, and compliance with local environmental regulations. Look for furnaces designed to minimize energy usage and reduce greenhouse gas emissions. Suppliers should provide data on the furnace’s efficiency and any environmental certifications. Additionally, consider the supplier’s commitment to sustainable practices, such as the use of recyclable materials and waste management strategies. Engaging with suppliers who prioritize environmental responsibility can enhance your company’s sustainability profile and align with global trends in responsible sourcing.
Important Disclaimer & Terms of Use
⚠️ Important Disclaimer
The information provided in this guide, including content regarding manufacturers, technical specifications, and market analysis, is for informational and educational purposes only. It does not constitute professional procurement advice, financial advice, or legal advice.
While we have made every effort to ensure the accuracy and timeliness of the information, we are not responsible for any errors, omissions, or outdated information. Market conditions, company details, and technical standards are subject to change.
B2B buyers must conduct their own independent and thorough due diligence before making any purchasing decisions. This includes contacting suppliers directly, verifying certifications, requesting samples, and seeking professional consultation. The risk of relying on any information in this guide is borne solely by the reader.
Strategic Sourcing Conclusion and Outlook for electric arc furnace supplier
In navigating the complexities of sourcing electric arc furnaces, international B2B buyers must prioritize strategic sourcing to maximize efficiency and minimize costs. Understanding local market conditions, regulatory frameworks, and supplier capabilities is crucial for making informed decisions. Buyers in regions such as Africa, South America, the Middle East, and Europe, including countries like Colombia and Egypt, should leverage local partnerships to enhance supply chain resilience and sustainability.
What are the key benefits of strategic sourcing for electric arc furnace procurement? By establishing long-term relationships with suppliers, companies can negotiate better terms, ensure quality standards, and access innovative technologies that enhance production efficiency. Additionally, fostering collaboration with suppliers can lead to shared insights on market trends and emerging technologies, providing a competitive edge.
Looking ahead, the demand for electric arc furnaces is expected to grow, driven by increasing emphasis on sustainable practices and the shift toward circular economies. Buyers should actively seek out suppliers committed to environmentally friendly practices and technological advancements. Embrace the opportunity to innovate and optimize your sourcing strategies—start building those critical supplier relationships today for a more resilient and efficient future in your operations.