Discover Top Benefits of a Farm Equipment Manufacturer (2025)
Introduction: Navigating the Global Market for farm equipment manufacturer
In today’s rapidly evolving agricultural landscape, sourcing reliable farm equipment manufacturers is a critical challenge for international B2B buyers. As global demand for food production increases, selecting the right equipment not only enhances efficiency but also ensures sustainability in operations. This guide provides a comprehensive exploration of the farm equipment manufacturing sector, delving into various types of machinery, their specific applications, and the nuances of supplier vetting.
Whether you’re based in Africa, South America, the Middle East, or Europe, the insights presented here are tailored to empower your purchasing decisions. We will address key considerations such as cost analysis, technological advancements, and regulatory compliance, all of which are essential for navigating the complexities of international procurement.
Moreover, understanding the unique challenges faced by agricultural sectors in regions like Egypt or Kenya can help you identify manufacturers that align with your operational needs and budget constraints. By leveraging the information in this guide, you will be better equipped to make informed choices, establish strong supplier relationships, and ultimately enhance your agricultural productivity. Join us on this journey as we break down the essential elements of sourcing quality farm equipment manufacturers in a competitive global market.
Understanding farm equipment manufacturer Types and Variations
Type Name | Key Distinguishing Features | Primary B2B Applications | Brief Pros & Cons for Buyers |
---|---|---|---|
Tractor Manufacturers | Focus on horsepower, versatility, and attachments | Crop farming, livestock management | Pros: High efficiency, multi-purpose. Cons: Initial cost can be high. |
Implement Manufacturers | Specialized tools for specific tasks | Tillage, planting, harvesting | Pros: Tailored solutions, improved productivity. Cons: May require additional training. |
Irrigation Equipment Manufacturers | Advanced systems for water management | Crop irrigation, water conservation | Pros: Enhanced yield, resource efficiency. Cons: Maintenance can be complex. |
Precision Agriculture Technology Providers | Data-driven tools for farming optimization | Crop monitoring, yield analysis | Pros: Increased profitability, data insights. Cons: Technology adoption can be challenging. |
Livestock Equipment Manufacturers | Equipment for animal care and management | Feeding, milking, housing | Pros: Improved animal health, labor savings. Cons: Regulatory compliance may be needed. |
What are the Key Characteristics of Tractor Manufacturers?
Tractor manufacturers are pivotal in the agricultural sector, focusing on delivering high horsepower and versatility. These manufacturers produce tractors that can be equipped with various attachments, making them suitable for diverse farming operations, from tilling to transporting goods. For B2B buyers, the primary consideration is the tractor’s ability to meet specific operational needs while balancing cost and efficiency. Buyers should evaluate the long-term return on investment, considering both the initial purchase price and potential operational savings.
How Do Implement Manufacturers Differ in Their Offerings?
Implement manufacturers specialize in creating tools designed for specific agricultural tasks, such as plowing, planting, and harvesting. These implements are often used in conjunction with tractors, enhancing their capabilities. For international B2B buyers, understanding the specific applications of each implement is crucial. Buyers should assess compatibility with existing equipment and consider the potential for increased productivity. While these specialized tools can significantly improve efficiency, they may require additional training for operators.
What Role Do Irrigation Equipment Manufacturers Play in Agriculture?
Irrigation equipment manufacturers provide advanced systems designed to optimize water usage in farming. Their products range from drip irrigation systems to large-scale sprinkler setups, tailored to various crop needs. For B2B buyers, particularly in regions facing water scarcity, investing in efficient irrigation solutions is essential for maximizing yield and sustainability. However, potential buyers should be aware that while these systems can enhance productivity, they often come with complex maintenance requirements that necessitate skilled personnel.
How Can Precision Agriculture Technology Providers Benefit Farmers?
Precision agriculture technology providers offer data-driven solutions aimed at optimizing farming practices. This includes tools for crop monitoring, soil analysis, and yield forecasting, which can lead to increased profitability for farmers. For B2B buyers, the key consideration is the integration of these technologies into existing farming operations. While the insights gained from precision agriculture can significantly enhance decision-making, the adoption of such technologies may present challenges, including the need for training and adaptation to new processes.
What Equipment Do Livestock Equipment Manufacturers Provide?
Livestock equipment manufacturers focus on producing tools and systems designed for the care and management of animals. This includes feeding systems, milking machines, and housing solutions. For B2B buyers in the livestock sector, investing in high-quality equipment is crucial for ensuring animal health and operational efficiency. Buyers should consider factors such as compliance with local regulations, durability of equipment, and the potential for labor savings. While the initial investment may be significant, the long-term benefits often justify the costs.
Related Video: Grade 7/8 TLE : (Agriculture) Lesson 1: Use Farm Tools and Equipment
Key Industrial Applications of farm equipment manufacturer
Industry/Sector | Specific Application of farm equipment manufacturer | Value/Benefit for the Business | Key Sourcing Considerations for this Application |
---|---|---|---|
Agriculture | Tractors and Harvesters | Increased efficiency in planting and harvesting cycles | Local support and service availability, fuel efficiency |
Horticulture | Specialized Sprayers and Irrigation Systems | Enhanced crop yield through targeted application | Compatibility with existing equipment, maintenance plans |
Livestock Farming | Feed Mixers and Manure Spreaders | Improved feed management and waste handling | Durability under local conditions, ease of operation |
Agro-processing | Grain Handling and Storage Solutions | Reduced post-harvest losses and better quality control | Scalability of equipment, integration with processing lines |
Forestry and Land Management | Mulchers and Tree Harvesters | Efficient land clearing and maintenance | Terrain adaptability, service and parts availability |
How are Tractors and Harvesters Beneficial for B2B Buyers in Agriculture?
Tractors and harvesters are fundamental for agricultural operations, enabling B2B buyers to enhance productivity and reduce labor costs. In regions like Africa and South America, where labor shortages can hinder farming, these machines automate critical tasks such as plowing, planting, and harvesting. Buyers should prioritize machines that offer local service support and are fuel-efficient to ensure sustainability and minimize operational costs.
What Role Do Specialized Sprayers and Irrigation Systems Play in Horticulture?
In horticulture, specialized sprayers and irrigation systems are vital for maximizing crop yield and quality. These systems allow for precise application of fertilizers and pesticides, which is crucial in regions with varying climates, such as the Middle East and Europe. Buyers should consider equipment compatibility with existing systems and look for reliable maintenance plans to ensure consistent operation throughout the growing season.
How Do Feed Mixers and Manure Spreaders Improve Livestock Farming Operations?
Feed mixers and manure spreaders are essential for efficient livestock management. These machines help optimize feed distribution and waste management, which directly impacts animal health and farm profitability. International buyers, particularly in developing regions, should assess the durability of equipment to withstand local conditions and ensure ease of operation for farm workers with varying skill levels.
Why Are Grain Handling and Storage Solutions Critical for Agro-processing?
Grain handling and storage solutions are crucial in agro-processing, particularly in minimizing post-harvest losses. Effective storage systems maintain grain quality and reduce spoilage, which is especially important for B2B buyers in Africa and South America, where market access can be limited. Buyers should evaluate the scalability of these solutions to meet future production demands and ensure seamless integration with existing processing lines.
What Advantages Do Mulchers and Tree Harvesters Offer in Forestry and Land Management?
Mulchers and tree harvesters provide efficient land clearing and maintenance, enabling sustainable forestry practices. For international buyers in regions like Europe, where environmental regulations are stringent, these machines help maintain compliance while enhancing operational efficiency. Key considerations for sourcing include the adaptability of equipment to various terrains and the availability of service and parts to minimize downtime.
Related Video: Farm tools and their uses
3 Common User Pain Points for ‘farm equipment manufacturer’ & Their Solutions
Scenario 1: Navigating High Import Costs for Farm Equipment
The Problem:
B2B buyers from regions such as Africa and South America often face exorbitant import costs when sourcing farm equipment from manufacturers in Europe or North America. These costs can be exacerbated by fluctuating exchange rates, high tariffs, and additional logistics fees, making it difficult for businesses to maintain competitive pricing in local markets. This situation not only strains budgets but can also limit the ability to invest in necessary equipment upgrades or expansions.
The Solution:
To mitigate high import costs, buyers should consider sourcing from local or regional manufacturers who offer similar quality equipment. Engage in thorough market research to identify reputable local manufacturers or suppliers that can provide competitive pricing without the hefty import fees. Additionally, forming partnerships with these manufacturers may lead to better financing options or discounts for bulk orders. Buyers can also explore government programs or trade agreements that encourage local production, which could further reduce costs. Utilizing platforms that aggregate suppliers and manufacturers in your region can help streamline this process and uncover cost-effective solutions.
Scenario 2: Ensuring Equipment Reliability and Performance
The Problem:
Another common challenge faced by B2B buyers is the reliability and performance of farm equipment. In regions with diverse agricultural conditions, such as the Middle East and Africa, equipment that performs well in one environment may falter in another. This inconsistency can lead to unexpected downtime, reduced productivity, and increased maintenance costs, ultimately affecting the bottom line.
The Solution:
To ensure equipment reliability, buyers should prioritize manufacturers that offer equipment specifically designed for their local conditions. Conducting field tests or pilot programs before making large purchases can provide insights into how well the equipment performs in specific climates and terrains. Additionally, establishing clear communication with manufacturers about local challenges can lead to customized solutions. Buyers should also seek out manufacturers that provide robust warranties and after-sales support, ensuring that any performance issues can be addressed promptly. Investing in training for operators on the specific equipment can further enhance reliability and performance, reducing the likelihood of operational disruptions.
Scenario 3: Difficulty in Accessing Spare Parts and Support
The Problem:
A significant pain point for B2B buyers is the difficulty in accessing spare parts and technical support for farm equipment, particularly in remote areas. This challenge can lead to prolonged equipment downtime, which directly impacts productivity and profitability. In regions such as South America and the Middle East, where logistics may be less developed, the unavailability of spare parts can create significant operational risks.
The Solution:
To address this issue, buyers should choose manufacturers that offer comprehensive support and a solid supply chain for spare parts. Before finalizing a purchase, inquire about the availability of parts and the manufacturer’s supply chain capabilities. Establishing a relationship with manufacturers that have local distributors can facilitate quicker access to necessary components. Additionally, buyers should consider investing in equipment from manufacturers known for their modular design, which allows for easier upgrades and part replacements. Joining industry networks or forums can also provide insights into best practices for maintenance and support, creating a community that shares solutions for spare part accessibility. Implementing a preventative maintenance schedule can further reduce reliance on spare parts by addressing potential issues before they lead to equipment failure.
Strategic Material Selection Guide for farm equipment manufacturer
When selecting materials for farm equipment manufacturing, it is essential to consider the unique requirements and challenges of the agricultural sector. The choice of material directly influences the performance, durability, and cost-effectiveness of the equipment. Here, we analyze four common materials used in farm equipment manufacturing: steel, aluminum, plastic, and composite materials. Each material has distinct properties, advantages, disadvantages, and implications for international buyers, particularly in regions like Africa, South America, the Middle East, and Europe.
What Are the Key Properties of Steel for Farm Equipment Manufacturing?
Steel is one of the most widely used materials in farm equipment due to its strength and versatility. It offers high tensile strength, excellent wear resistance, and can withstand high temperatures and pressures. Additionally, steel can be treated for corrosion resistance, making it suitable for outdoor applications.
Pros and Cons of Using Steel:
– Pros: Steel is highly durable, cost-effective, and readily available. It can be easily fabricated into various shapes and sizes, allowing for complex designs.
– Cons: Steel is heavy, which can increase transportation costs and reduce fuel efficiency when used in mobile equipment. It is also susceptible to rust if not properly treated.
Impact on Application:
Steel is ideal for heavy-duty applications, such as plows and tractors, where strength and durability are paramount. However, buyers must ensure that the steel used meets local standards, such as ASTM or DIN, particularly in regions with stringent compliance requirements.
How Does Aluminum Compare as a Material for Farm Equipment?
Aluminum is increasingly popular in farm equipment manufacturing due to its lightweight nature and resistance to corrosion. It has a lower density than steel, making it easier to handle and transport.
Pros and Cons of Using Aluminum:
– Pros: Aluminum is resistant to rust and corrosion, making it suitable for humid or wet environments. Its lightweight property can enhance fuel efficiency in mobile equipment.
– Cons: Aluminum is generally more expensive than steel and may not offer the same level of strength for heavy-duty applications.
Impact on Application:
Aluminum is often used in components that require a balance between weight and strength, such as frames and panels. International buyers should consider the cost implications and ensure compliance with relevant standards, particularly in regions with high aluminum usage.
What Are the Benefits of Using Plastic in Farm Equipment?
Plastic materials, such as polyethylene and polypropylene, are commonly used in farm equipment for components like tanks, covers, and fittings. They offer excellent chemical resistance and can be molded into complex shapes.
Pros and Cons of Using Plastic:
– Pros: Plastics are lightweight, resistant to corrosion, and cost-effective for mass production. They can also be designed for specific media compatibility, such as fertilizers and pesticides.
– Cons: Plastics may not withstand high temperatures or mechanical stress as effectively as metals, limiting their use in heavy-duty applications.
Impact on Application:
Plastic is ideal for non-structural components where weight savings are crucial. Buyers should evaluate the specific chemical compatibility of the plastic with the media it will come into contact with, particularly in agricultural settings.
Why Are Composite Materials Gaining Popularity in Farm Equipment?
Composite materials, which combine two or more constituent materials, are gaining traction in farm equipment manufacturing due to their high strength-to-weight ratio and resistance to environmental degradation.
Pros and Cons of Using Composite Materials:
– Pros: Composites can be engineered for specific applications, offering tailored performance characteristics. They are lightweight and resistant to corrosion and UV damage.
– Cons: The manufacturing process for composites can be complex and costly, which may not be suitable for all applications.
Impact on Application:
Composites are used in specialized applications, such as high-performance agricultural machinery and equipment exposed to harsh conditions. International buyers should be aware of the certification requirements for composite materials in their respective regions.
Summary Table of Material Selection for Farm Equipment Manufacturing
Material | Typical Use Case for farm equipment manufacturer | Key Advantage | Key Disadvantage/Limitation | Relative Cost (Low/Med/High) |
---|---|---|---|---|
Steel | Tractors, plows, heavy-duty machinery | High durability and strength | Heavy and prone to rust | Medium |
Aluminum | Frames, panels, lightweight components | Lightweight and corrosion-resistant | Higher cost, lower strength | High |
Plastic | Tanks, covers, fittings | Lightweight and cost-effective | Limited mechanical strength | Low |
Composite | High-performance machinery, specialized equipment | Tailored performance characteristics | Complex and costly manufacturing | High |
This guide provides a strategic overview for international B2B buyers to make informed decisions regarding material selection in farm equipment manufacturing. Understanding the properties, advantages, and limitations of each material will enable buyers to select the most suitable options for their specific agricultural needs.
In-depth Look: Manufacturing Processes and Quality Assurance for farm equipment manufacturer
What Are the Main Stages of Manufacturing Farm Equipment?
The manufacturing process for farm equipment involves several critical stages, each of which plays a vital role in ensuring the final product meets both functional and quality standards. Understanding these stages can help international B2B buyers evaluate suppliers effectively.
Material Preparation: How Is It Done?
The first stage in manufacturing farm equipment is material preparation. This involves selecting high-quality raw materials such as steel, aluminum, and polymers. Suppliers often use advanced techniques like laser cutting and plasma cutting to achieve precise dimensions and shapes.
For buyers, it’s essential to inquire about the types of materials used and their sourcing. Sustainable practices and local sourcing can provide additional benefits, such as reduced lead times and lower costs.
What Techniques Are Used in the Forming Stage?
Following material preparation, the forming stage involves shaping the raw materials into the desired forms. This can include processes such as forging, stamping, and bending. Each technique has its advantages; for instance, forging enhances the strength of components, while stamping allows for mass production of complex shapes.
Buyers should look for manufacturers that utilize modern forming technologies like CNC (Computer Numerical Control) machines. These machines provide higher precision and consistency, which are crucial for the performance of farm equipment.
How Is Assembly Conducted in Farm Equipment Manufacturing?
The assembly stage combines all the manufactured components into a cohesive unit. This may involve welding, riveting, or using fasteners. Effective assembly requires skilled labor and often involves the use of jigs and fixtures to ensure accuracy.
When evaluating potential suppliers, B2B buyers should ask about their assembly processes and workforce training programs. A skilled workforce is essential for maintaining quality and minimizing defects.
What Finishing Techniques Are Common in Farm Equipment Production?
Finishing processes such as painting, powder coating, and galvanizing are essential for protecting farm equipment from corrosion and wear. These techniques not only enhance the aesthetic appeal of the equipment but also extend its lifespan.
Buyers should consider suppliers that employ environmentally friendly finishing techniques, as these can improve sustainability and comply with international regulations.
What Are the Key Quality Assurance Standards for Farm Equipment?
Quality assurance is critical in the manufacturing of farm equipment, as it directly impacts performance and safety. Several international and industry-specific standards guide this process.
How Does ISO 9001 Influence Quality Control?
ISO 9001 is a widely recognized international standard that outlines criteria for a quality management system (QMS). Manufacturers certified under ISO 9001 demonstrate a commitment to quality and customer satisfaction.
B2B buyers should prioritize suppliers with ISO 9001 certification, as this indicates adherence to established quality processes and continuous improvement practices.
What Are Other Relevant Quality Standards for the Farm Equipment Industry?
In addition to ISO 9001, farm equipment manufacturers may also need to comply with industry-specific standards such as CE (Conformité Européenne) marking in Europe or API (American Petroleum Institute) standards for equipment used in oil and gas agriculture. These certifications ensure that products meet safety and performance regulations specific to their market.
Understanding these standards can help buyers gauge the credibility of a supplier and the quality of their products.
How Do Quality Control Checkpoints Work in Manufacturing?
Effective quality control (QC) involves multiple checkpoints throughout the manufacturing process. These checkpoints include:
- Incoming Quality Control (IQC): This stage inspects raw materials upon arrival to ensure they meet specified standards.
- In-Process Quality Control (IPQC): Conducted during the manufacturing process, this involves regular inspections to catch defects early.
- Final Quality Control (FQC): This final inspection occurs before products are shipped, ensuring they meet all quality criteria.
B2B buyers should inquire about the QC processes of potential suppliers. A comprehensive QC system indicates a manufacturer’s commitment to delivering high-quality products.
What Common Testing Methods Are Used in Farm Equipment Quality Assurance?
Various testing methods are employed to verify the quality and performance of farm equipment. These may include:
- Mechanical Testing: Assessing the strength and durability of materials.
- Functional Testing: Ensuring that equipment operates as intended under different conditions.
- Environmental Testing: Simulating conditions such as humidity and temperature to assess equipment durability.
Buyers can request test reports and certifications from suppliers to validate the quality of their products.
How Can B2B Buyers Verify Supplier Quality Control?
To ensure that a supplier adheres to quality standards, B2B buyers should conduct thorough due diligence. This can include:
- Audits: Regular audits help assess compliance with quality management systems and standards.
- Quality Reports: Requesting detailed quality reports provides insights into a supplier’s QC processes and performance history.
- Third-Party Inspections: Engaging independent inspectors can offer an unbiased assessment of a supplier’s quality practices.
In regions like Africa, South America, the Middle East, and Europe, establishing strong relationships with suppliers can also facilitate better communication about quality expectations and practices.
What Are the Quality Control Nuances for International B2B Buyers?
International B2B buyers must navigate various quality control nuances, especially when sourcing from different regions. Understanding local regulations, cultural differences in manufacturing practices, and logistical challenges can significantly impact quality assurance.
For buyers in Africa, South America, the Middle East, and Europe, it is advisable to:
- Research Local Standards: Familiarize yourself with local regulations and certifications that may affect product quality.
- Engage Local Experts: Collaborating with local consultants can provide insights into the manufacturing landscape and help navigate quality assurance challenges.
- Build Relationships: Developing strong relationships with suppliers can lead to better transparency and collaboration on quality issues.
By focusing on these aspects, international B2B buyers can enhance their procurement processes and ensure they receive high-quality farm equipment that meets their needs.
Practical Sourcing Guide: A Step-by-Step Checklist for ‘farm equipment manufacturer’
In the competitive landscape of agricultural procurement, sourcing farm equipment requires a strategic approach to ensure that investments yield optimal returns. This guide provides a practical checklist for international B2B buyers, particularly those from Africa, South America, the Middle East, and Europe, to navigate the complex process of selecting a reliable farm equipment manufacturer.
Step 1: Define Your Technical Specifications
Before engaging with suppliers, it is essential to outline your specific technical requirements. This includes the type of equipment needed, capacity, technology, and any special features that align with your operational needs. A well-defined specification helps in accurately assessing supplier capabilities and ensures that you procure equipment that meets your farming objectives.
Step 2: Research Potential Suppliers
Conduct thorough research to identify potential suppliers who specialize in farm equipment relevant to your needs. Utilize industry directories, trade shows, and online platforms to compile a list of manufacturers. Pay attention to their market reputation, product range, and regional presence, particularly focusing on suppliers with experience in your geographical area.
Step 3: Evaluate Supplier Credentials
Once you have shortlisted suppliers, it’s vital to verify their credentials. Look for certifications that demonstrate compliance with international quality standards, such as ISO certifications or local agricultural standards. Additionally, check for industry affiliations and awards that reflect their commitment to excellence and innovation in farm equipment manufacturing.
Step 4: Request Product Samples and Demonstrations
To ensure the quality of the equipment, request samples or demonstrations. This allows you to assess the performance and durability of the products in real-world conditions. Take note of the equipment’s ease of use, maintenance requirements, and adaptability to your farming practices, as these factors can significantly impact your operational efficiency.
Step 5: Assess After-Sales Support and Warranty
Evaluate the after-sales support offered by the supplier, which is crucial for long-term satisfaction. Inquire about warranty terms, maintenance services, and availability of spare parts. A manufacturer that provides comprehensive support can enhance your operational uptime and reduce the risk of costly breakdowns.
Step 6: Negotiate Pricing and Terms
Engage in negotiations to secure favorable pricing and payment terms. Consider factors such as bulk purchasing discounts, financing options, and delivery timelines. Transparent negotiations help establish a trustworthy relationship with suppliers and ensure that you get the best value for your investment.
Step 7: Finalize the Contract and Monitor Delivery
Once terms are agreed upon, ensure all details are captured in a formal contract. This should include specifications, pricing, delivery schedules, and penalties for non-compliance. After placing the order, closely monitor the delivery process to ensure that the equipment arrives as agreed, and conduct a thorough inspection upon arrival to confirm adherence to specifications.
By following this step-by-step checklist, B2B buyers can make informed decisions when sourcing farm equipment, ultimately enhancing their agricultural operations and contributing to sustainable growth.
Comprehensive Cost and Pricing Analysis for farm equipment manufacturer Sourcing
Understanding the comprehensive cost structure and pricing dynamics for sourcing farm equipment is crucial for international B2B buyers. This analysis will delve into the various cost components, price influencers, and practical tips to optimize purchasing decisions, particularly for buyers from Africa, South America, the Middle East, and Europe.
What Are the Key Cost Components in Farm Equipment Manufacturing?
The cost structure of farm equipment manufacturing encompasses several critical components:
-
Materials: Raw materials constitute a significant portion of production costs. High-quality steel, rubber, and electronic components are essential for durability and performance. Buyers should assess the material specifications to ensure they meet operational needs without incurring excessive costs.
-
Labor: Labor costs vary by region and skill level. Manufacturers in regions with lower labor costs may offer competitive pricing, but it’s essential to evaluate the quality of workmanship. Skilled labor often results in better product reliability.
-
Manufacturing Overhead: This includes costs related to utilities, factory maintenance, and administrative expenses. Efficient overhead management can lead to lower pricing for buyers.
-
Tooling: Specialized tools and machinery for production can be costly. Understanding these costs can provide insight into the pricing of custom or specialized equipment.
-
Quality Control (QC): Implementing rigorous QC processes ensures that the equipment meets industry standards. While this may increase initial costs, it can save buyers from future issues related to equipment failure.
-
Logistics: Shipping and handling costs play a vital role, especially for international buyers. Factors such as distance, shipping mode, and customs duties must be considered to avoid unexpected expenses.
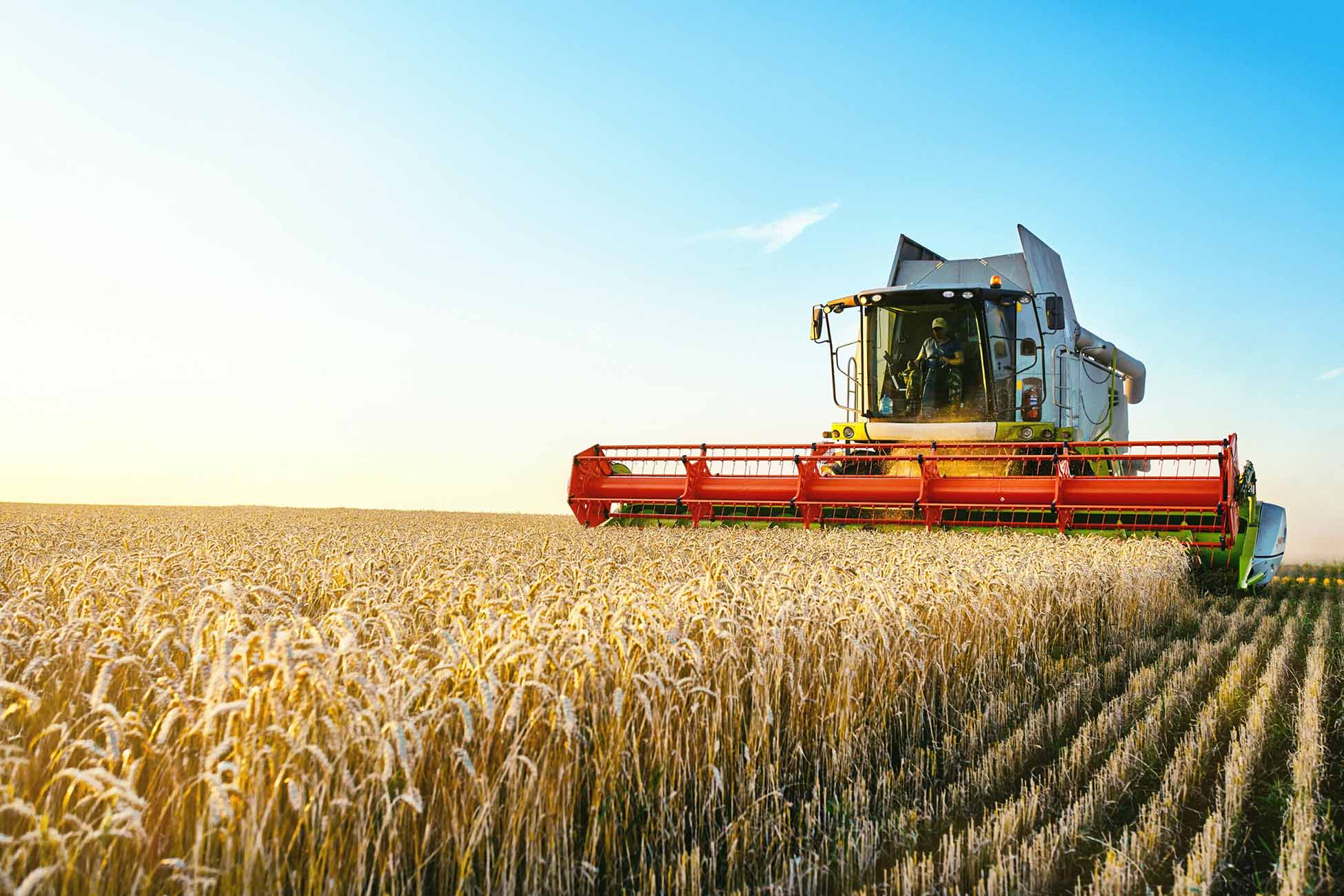
A stock image related to farm equipment manufacturer.
- Margin: Manufacturers typically include a profit margin in their pricing. Understanding industry standards for margins can help buyers identify reasonable pricing.
How Do Price Influencers Affect Farm Equipment Pricing?
Several factors influence the pricing of farm equipment, which buyers should consider:
-
Volume/MOQ (Minimum Order Quantity): Purchasing in bulk often leads to lower per-unit costs. Buyers should negotiate MOQs to maximize savings.
-
Specifications and Customization: Custom features can significantly alter pricing. Buyers need to balance their specific requirements with budget constraints.
-
Materials: The choice of materials affects both cost and quality. Buyers should inquire about alternatives that offer a balance between affordability and performance.
-
Quality Certifications: Certifications can indicate a higher quality product, but they may also increase costs. Buyers should weigh the benefits of certified equipment against their budget.
-
Supplier Factors: The reputation and reliability of suppliers can influence pricing. Established suppliers may charge a premium but often provide better support and warranty options.
-
Incoterms: Understanding Incoterms is crucial for international transactions. Terms like FOB (Free On Board) or CIF (Cost, Insurance, and Freight) can impact overall costs and responsibilities in shipping.
What Are Essential Tips for International B2B Buyers in Farm Equipment Sourcing?
To ensure cost-efficiency and value in farm equipment sourcing, consider the following tips:
-
Negotiation Strategies: Engage in open discussions with suppliers about pricing, especially regarding bulk orders or long-term partnerships. Building relationships can lead to better terms.
-
Total Cost of Ownership (TCO): Look beyond the initial purchase price. Consider maintenance, operational efficiency, and potential resale value to understand the TCO.
-
Pricing Nuances for Different Regions: Buyers from Africa, South America, the Middle East, and Europe should be aware of regional pricing differences influenced by local demand, regulations, and market conditions.
-
Conduct Market Research: Stay informed about market trends and competitor pricing. This knowledge can empower buyers during negotiations and help them identify fair pricing.
-
Seek Local Expertise: For buyers in regions like Egypt or Kenya, leveraging local consultants or agents can provide insights into reputable suppliers and effective negotiation tactics.
Disclaimer on Indicative Prices
Prices for farm equipment can vary significantly based on multiple factors, including market demand, economic conditions, and supplier pricing strategies. It is advisable for buyers to conduct thorough research and obtain multiple quotes to ensure competitive pricing.
Alternatives Analysis: Comparing farm equipment manufacturer With Other Solutions
Understanding Alternatives in Farm Equipment Solutions
In the evolving agricultural landscape, B2B buyers are increasingly seeking alternatives to traditional farm equipment manufacturers. These alternatives can range from innovative technologies to alternative farming methods that can enhance productivity and reduce costs. This analysis aims to provide insights into how farm equipment manufacturers compare against other viable solutions, enabling buyers to make informed decisions tailored to their specific needs.
Comparison Table of Farm Equipment Manufacturer and Alternatives
Comparison Aspect | Farm Equipment Manufacturer | Precision Agriculture Technology | Rental Equipment Services |
---|---|---|---|
Performance | High durability and reliability for heavy-duty tasks | Enhanced productivity through data-driven insights | Access to a variety of equipment without long-term commitment |
Cost | High initial investment, but longevity reduces long-term costs | Moderate investment with potential for high ROI | Lower upfront costs; ongoing rental fees can accumulate |
Ease of Implementation | Requires training and adaptation period | Requires integration with existing systems; training needed | Quick access to equipment with minimal setup time |
Maintenance | Regular maintenance needed; availability of support services | Minimal maintenance; software updates required | Maintenance handled by rental company, but equipment may vary |
Best Use Case | Large-scale farming operations needing robust solutions | Precision farming for data-driven decision-making | Short-term projects or seasonal use of equipment |
What are the Benefits and Drawbacks of Precision Agriculture Technology?
Precision agriculture technology employs data analytics, GPS, and IoT devices to optimize farming practices. Its primary advantage lies in its ability to enhance productivity through informed decision-making based on real-time data. This technology allows farmers to apply resources more efficiently, reducing waste and increasing crop yields.
However, the initial setup costs can be significant, and the technology requires a certain level of expertise to implement effectively. Farmers may need to invest time in training and integrating these systems with their existing workflows. For regions in Africa or South America, where technological infrastructure may be limited, the adoption of precision agriculture might pose additional challenges.
How Do Rental Equipment Services Compare to Traditional Farm Equipment Manufacturers?
Rental equipment services offer a flexible alternative for farmers who may not need to own equipment outright. This solution provides access to a wide range of machinery, allowing farmers to select the right tools for specific tasks or projects without the burden of ownership costs. For seasonal operations, renting can be a financially savvy choice.
On the downside, relying on rental services can lead to inconsistent equipment quality and availability. Farmers might face challenges if the specific machinery they need is not in stock, leading to potential delays in operations. Additionally, while rental costs are lower initially, they can accumulate over time, potentially surpassing the cost of ownership in the long run.
How Can B2B Buyers Choose the Right Solution for Their Needs?
Selecting the right farm equipment solution hinges on understanding your specific operational needs and financial constraints. Buyers should consider factors such as the scale of their operations, the frequency of equipment use, and their capacity for maintenance. For large-scale operations with a consistent need for reliable equipment, investing in a farm equipment manufacturer may be the best choice. Conversely, if flexibility and lower upfront costs are priorities, precision agriculture technology or rental services might be more suitable.
Ultimately, the decision should align with your business goals, financial strategy, and the unique challenges of your operating environment. By carefully weighing these alternatives, B2B buyers can make informed choices that drive efficiency and productivity in their agricultural ventures.
Essential Technical Properties and Trade Terminology for farm equipment manufacturer
What Are the Key Technical Properties of Farm Equipment?
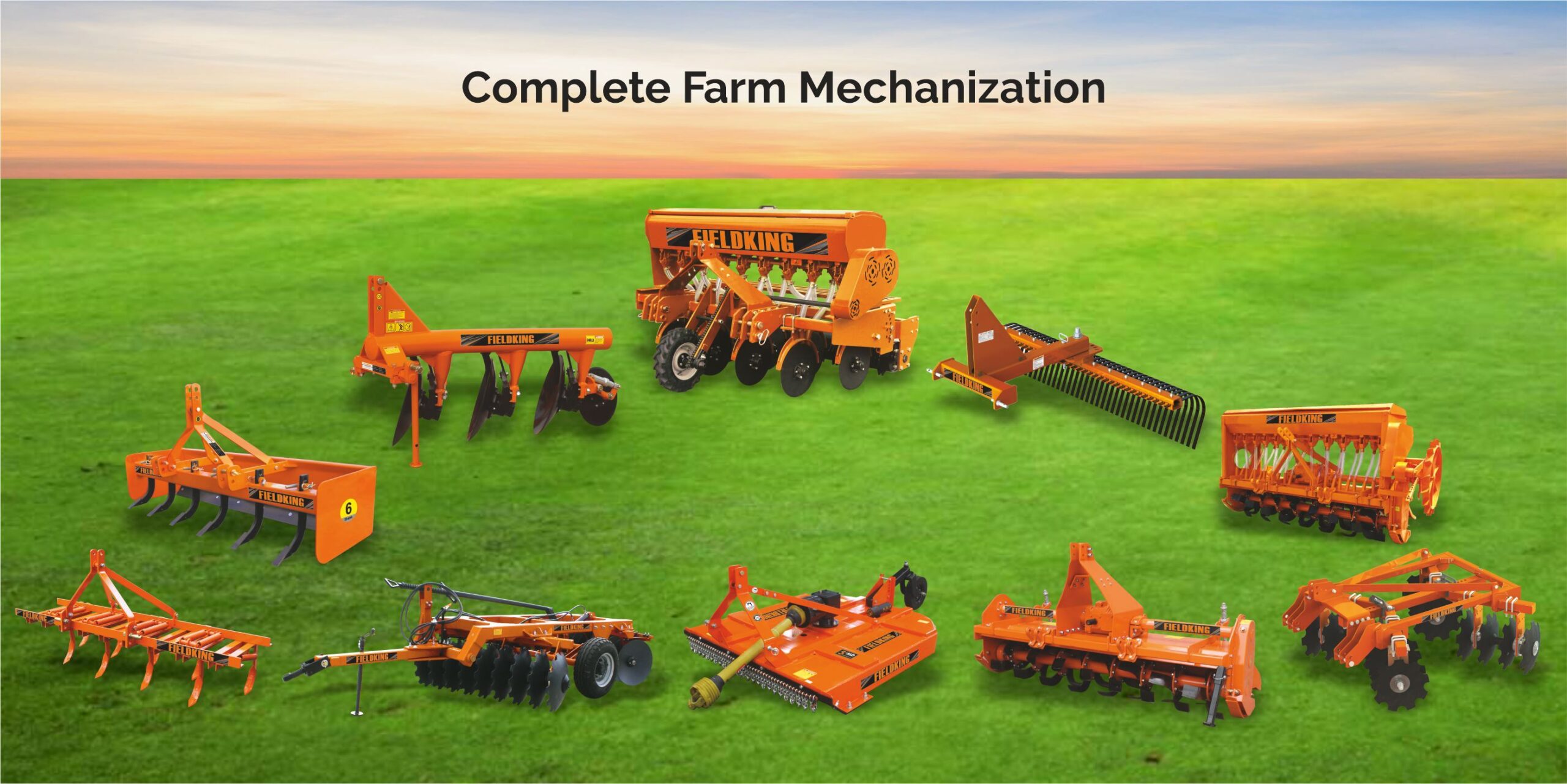
A stock image related to farm equipment manufacturer.
Understanding the technical specifications of farm equipment is crucial for international B2B buyers to ensure optimal performance and longevity. Here are some essential properties to consider:
1. Material Grade
Material grade refers to the quality and type of materials used in manufacturing farm equipment, such as steel or aluminum alloys. High-grade materials are vital for durability, corrosion resistance, and the ability to withstand harsh agricultural environments. For buyers in regions like Africa and South America, where equipment may face extreme conditions, selecting products made from superior material grades can significantly reduce maintenance costs and downtime.
2. Tolerance
Tolerance indicates the permissible limit of variation in a physical dimension or property of the equipment. In manufacturing, tight tolerances ensure that parts fit together correctly, which is essential for the efficient operation of machinery. B2B buyers should prioritize equipment with precise tolerances to minimize wear and tear, especially in high-performance applications like plowing or harvesting.
3. Power Rating
Power rating reflects the engine or motor’s output capacity, usually measured in horsepower (HP) or kilowatts (kW). This specification is critical for buyers to match equipment with their specific operational needs. For instance, a higher power rating may be necessary for large-scale farming operations in the Middle East, where heavy-duty equipment is essential for efficiency.
4. Weight Capacity
Weight capacity denotes the maximum load that equipment can safely handle. It is particularly important for machinery like tractors, trailers, and loaders. Buyers must evaluate weight capacity based on their operational requirements, as inadequate capacity can lead to equipment failure and safety hazards, especially in diverse agricultural practices across Europe and Africa.
5. Fuel Efficiency
Fuel efficiency measures how effectively equipment uses fuel, typically represented in liters per hour or gallons per hour. High fuel efficiency translates to lower operational costs, which is crucial for buyers managing tight budgets, particularly in developing regions. Understanding this property can help buyers make informed decisions that enhance their overall productivity.
What Are Common Trade Terms in the Farm Equipment Industry?
Navigating the terminology used in the farm equipment industry can be challenging. Here are some essential trade terms that every B2B buyer should know:
1. OEM (Original Equipment Manufacturer)
An OEM is a company that produces parts and equipment that may be marketed by another manufacturer. For buyers, understanding OEM relationships can ensure they are sourcing high-quality components that meet industry standards, thereby enhancing the reliability of their equipment.
2. MOQ (Minimum Order Quantity)
MOQ refers to the minimum number of units a supplier is willing to sell. For international buyers, particularly those in emerging markets, knowing the MOQ can aid in planning purchases and managing inventory effectively. It’s important to negotiate MOQ terms to align with production needs without incurring excess costs.
3. RFQ (Request for Quotation)
An RFQ is a document issued by a buyer to solicit price quotes from suppliers. This process is vital for B2B buyers to compare pricing, delivery timelines, and terms of service. Crafting a clear RFQ can lead to better negotiations and pricing advantages.
4. Incoterms (International Commercial Terms)
Incoterms are a series of pre-defined international trade terms published by the International Chamber of Commerce. They clarify the responsibilities of buyers and sellers in international transactions, including shipping, insurance, and tariffs. Familiarity with Incoterms is essential for B2B buyers to avoid misunderstandings and ensure smooth logistics operations.
5. Lead Time
Lead time refers to the amount of time it takes from placing an order to receiving the product. For international buyers, understanding lead times is crucial for planning and inventory management. Shorter lead times can significantly enhance operational efficiency, especially during peak agricultural seasons.
By grasping these technical properties and trade terms, international B2B buyers can make more informed decisions, ultimately leading to improved operational efficiencies and cost savings in their agricultural endeavors.
Navigating Market Dynamics and Sourcing Trends in the farm equipment manufacturer Sector
What Are the Key Drivers Shaping the Farm Equipment Manufacturer Sector?
The farm equipment manufacturing sector is experiencing significant transformation driven by several global factors. Increased demand for food security, climate change, and technological advancements are at the forefront. As populations grow, particularly in regions like Africa and South America, there is an urgent need for efficient agricultural practices. This has led to a surge in demand for modern farming equipment that enhances productivity and sustainability.
Emerging B2B tech trends such as precision agriculture, IoT integration, and automation are reshaping sourcing strategies. For international buyers, particularly in the Middle East and Europe, understanding these trends is essential. The adoption of precision farming techniques allows for more efficient resource use, reducing waste and increasing crop yields. Additionally, manufacturers are increasingly leveraging digital platforms to streamline procurement processes, making it easier for buyers to access a wider range of products and services.
Market dynamics are also influenced by regional economic conditions and trade policies. Buyers from Africa, for instance, should be aware of local regulations that may affect the import of farm equipment. Understanding these dynamics not only aids in effective sourcing but also in building long-term relationships with manufacturers who are attuned to local market needs.
How Is Sustainability Influencing Sourcing Decisions in the Farm Equipment Sector?
Sustainability is becoming a cornerstone of sourcing strategies in the farm equipment manufacturing sector. With increasing awareness of environmental issues, buyers are prioritizing suppliers that demonstrate a commitment to sustainable practices. This includes the use of eco-friendly materials, energy-efficient manufacturing processes, and adherence to environmental regulations.
Ethical supply chains are crucial for building brand reputation and customer loyalty. International buyers, particularly from Europe, are increasingly scrutinizing the sustainability credentials of their suppliers. Certifications such as ISO 14001 (Environmental Management) and adherence to global standards like the Global Reporting Initiative (GRI) can serve as indicators of a manufacturer’s commitment to sustainability.
Moreover, the demand for ‘green’ certifications is on the rise. Buyers should actively seek suppliers who offer products made from recycled materials or those that have received sustainability certifications. By prioritizing sustainable sourcing, buyers can contribute to reducing the overall environmental impact of agriculture while also meeting consumer demand for responsibly sourced products.
What Is the Historical Context of the Farm Equipment Manufacturing Sector?
The farm equipment manufacturing sector has evolved significantly over the past century. Initially dominated by manual tools and animal-drawn implements, the industry began to transform in the early 20th century with the advent of mechanization. Tractors, harvesters, and other machinery revolutionized farming, enabling higher efficiency and productivity.
By the late 20th century, technological advancements such as computer-aided design (CAD) and automation further changed the landscape. Today, the sector is witnessing a new wave of innovation with the integration of smart technologies, including drones and robotics. For B2B buyers, understanding this historical context is vital, as it highlights the trajectory of innovation and the importance of keeping pace with new developments to remain competitive in a rapidly evolving market.
Frequently Asked Questions (FAQs) for B2B Buyers of farm equipment manufacturer
-
How do I solve supply chain challenges when sourcing farm equipment internationally?
To address supply chain challenges, start by conducting thorough market research to identify reliable manufacturers in your target regions. Establish clear communication channels with suppliers to understand their production capabilities and lead times. Additionally, consider diversifying your supplier base to mitigate risks associated with disruptions. Utilizing logistics partners who specialize in international shipping can also streamline the process. Finally, ensure that you have contingency plans in place, such as alternative suppliers or stockpiling essential parts, to maintain operations. -
What is the best way to vet a farm equipment manufacturer before making a purchase?
Vetting a farm equipment manufacturer involves several steps. First, verify their business credentials and industry certifications to ensure compliance with international standards. Seek references from other B2B buyers in your region, especially those with similar needs. Conduct site visits if possible, or utilize video conferencing to inspect facilities. Review product quality through samples or third-party testing. Lastly, assess their financial stability to ensure they can fulfill your orders consistently, which is crucial for long-term partnerships. -
What customization options are typically available when sourcing farm equipment?
Customization options for farm equipment can vary significantly by manufacturer. Many suppliers offer tailored solutions based on your specific agricultural needs, such as modifications to size, capacity, or features. It’s essential to communicate your requirements clearly during the initial discussions. Be prepared to discuss potential costs and lead times for custom orders, as these can affect your overall budget and project timelines. Additionally, inquire about after-sales support and warranty terms related to customized equipment. -
What are the minimum order quantities (MOQ) I should expect from farm equipment manufacturers?
Minimum order quantities (MOQ) can differ widely among farm equipment manufacturers based on their production capabilities and the type of equipment. Generally, established manufacturers may have higher MOQs due to economies of scale, while smaller or specialized producers might offer more flexible options. When negotiating, express your needs and explore whether they can accommodate smaller orders, especially if you’re entering a new market. Always clarify the pricing implications of lower MOQs to ensure they fit within your budget. -
What payment terms are common when dealing with international farm equipment suppliers?
Payment terms can vary, but common practices include upfront deposits, progress payments, and final payments upon delivery. Many suppliers request a deposit of 30-50% to initiate production, with the balance due before shipment or upon receipt. It’s advisable to use secure payment methods, such as letters of credit or escrow services, to protect your investment. Ensure that you discuss and agree on payment terms upfront to avoid misunderstandings and establish a solid foundation for your business relationship. -
How can I ensure quality assurance (QA) for farm equipment sourced internationally?
To ensure quality assurance when sourcing farm equipment, implement a multi-step QA process. Start with comprehensive product specifications and standards that the manufacturer must meet. Conduct regular inspections during production and prior to shipment, utilizing third-party inspection services if necessary. Request quality certifications and test reports for the equipment. Establish a return policy that addresses quality issues, and maintain open communication with the manufacturer for ongoing support and resolution of any concerns. -
What logistics considerations should I keep in mind when importing farm equipment?
When importing farm equipment, logistics considerations are crucial for timely delivery. Begin by researching shipping methods suitable for your equipment type, such as container shipping or air freight. Understand the customs regulations in your destination country, including duties and taxes that may apply. Work with logistics partners who have experience in agricultural equipment to navigate potential challenges. Additionally, plan for storage solutions upon arrival to handle equipment efficiently until it’s ready for use. -
How do I find reliable suppliers of farm equipment in Africa, South America, the Middle East, and Europe?
Finding reliable suppliers in these regions can be achieved through several strategies. Start by attending industry trade shows and exhibitions to meet manufacturers and see their products firsthand. Utilize online B2B marketplaces and directories that list verified suppliers. Networking within industry associations and forums can also provide recommendations from peers. Additionally, consider conducting online research to read reviews and case studies about potential suppliers, ensuring they have a strong reputation for quality and service in your target market.
Important Disclaimer & Terms of Use
⚠️ Important Disclaimer
The information provided in this guide, including content regarding manufacturers, technical specifications, and market analysis, is for informational and educational purposes only. It does not constitute professional procurement advice, financial advice, or legal advice.
While we have made every effort to ensure the accuracy and timeliness of the information, we are not responsible for any errors, omissions, or outdated information. Market conditions, company details, and technical standards are subject to change.
B2B buyers must conduct their own independent and thorough due diligence before making any purchasing decisions. This includes contacting suppliers directly, verifying certifications, requesting samples, and seeking professional consultation. The risk of relying on any information in this guide is borne solely by the reader.
Strategic Sourcing Conclusion and Outlook for farm equipment manufacturer
In the competitive landscape of farm equipment manufacturing, strategic sourcing emerges as a pivotal element for international B2B buyers. By leveraging local and global supply chains, businesses can optimize costs while ensuring quality and sustainability. Key takeaways include the importance of establishing strong relationships with suppliers, understanding regional market dynamics, and embracing technology for better inventory management.
How can strategic sourcing enhance your procurement process? By focusing on these aspects, buyers from Africa, South America, the Middle East, and Europe can improve their operational efficiency and drive profitability. Additionally, the integration of sustainable practices in sourcing not only meets regulatory requirements but also aligns with the growing demand for environmentally friendly farming solutions.
Looking ahead, the farm equipment industry is poised for transformation driven by innovation and digitalization. International B2B buyers are encouraged to stay informed about emerging trends and technologies that can enhance their sourcing strategies. Engage with suppliers who prioritize agility and responsiveness, as this will be crucial in navigating the complexities of global markets. Now is the time to reassess your sourcing strategies and position your business for future success in the evolving agricultural landscape.