Discover Top Benefits of a High Quality Manufacturer (2025)
Introduction: Navigating the Global Market for high quality manufacturer
In today’s competitive landscape, sourcing high-quality manufacturers presents a significant challenge for international B2B buyers. With a plethora of options available, it can be daunting to identify suppliers that not only meet stringent quality standards but also align with regional compliance requirements. This guide serves as an essential roadmap for B2B buyers from Africa, South America, the Middle East, and Europe (including the UK and Poland), aiming to streamline the procurement process for high-quality manufacturing solutions.
This comprehensive resource explores various facets of the manufacturing landscape, including types of manufacturers, their specific applications across different industries, and effective strategies for supplier vetting. It also addresses critical considerations such as cost analysis, quality assurance protocols, and the importance of sustainable practices in manufacturing. By delving into these topics, the guide equips buyers with the knowledge needed to make informed purchasing decisions that cater to their unique operational needs.
Ultimately, this guide empowers B2B buyers by demystifying the complexities of global sourcing. By providing actionable insights and practical strategies, it enables you to navigate the intricate web of international manufacturing with confidence, ensuring that your business can thrive in an increasingly interconnected market. Whether you are looking to enhance product quality, reduce lead times, or forge long-lasting supplier relationships, this guide is your key to success in the realm of high-quality manufacturing.
Understanding high quality manufacturer Types and Variations
Type Name | Key Distinguishing Features | Primary B2B Applications | Brief Pros & Cons for Buyers |
---|---|---|---|
Contract Manufacturers | Specialize in producing goods for other companies under their brand. | Electronics, textiles, pharmaceuticals | Pros: Cost-effective, scalable; Cons: Less control over quality. |
Original Equipment Manufacturers (OEMs) | Design and manufacture products that are sold under another company’s brand. | Automotive, consumer electronics | Pros: High customization, brand recognition; Cons: Potentially higher costs. |
Custom Manufacturers | Create tailored products based on specific client requirements. | Aerospace, medical devices | Pros: Unique solutions, precise specifications; Cons: Longer lead times. |
Bulk Manufacturers | Focus on producing large quantities of standardized products. | Food and beverages, construction | Pros: Economies of scale, lower unit costs; Cons: Limited customization options. |
Artisan Manufacturers | Small-scale producers emphasizing craftsmanship and quality. | Luxury goods, niche markets | Pros: High quality, unique products; Cons: Higher prices, limited production capacity. |
What Are the Characteristics of Contract Manufacturers?
Contract manufacturers play a pivotal role in the global supply chain by producing goods for other businesses under their brand names. They often focus on cost-efficiency and scalability, allowing companies to leverage their manufacturing capabilities without heavy investments in infrastructure. B2B buyers should consider the manufacturer’s reputation, capacity to meet deadlines, and adherence to quality standards. While contract manufacturing can significantly reduce production costs, buyers may face challenges in quality control and brand alignment.
How Do Original Equipment Manufacturers (OEMs) Operate?
Original Equipment Manufacturers (OEMs) are integral to industries such as automotive and consumer electronics. They design and produce products that are marketed under another company’s brand. This type of manufacturer provides high customization options, which can be a significant advantage for businesses looking to differentiate their products in competitive markets. B2B buyers must evaluate the OEM’s design capabilities, manufacturing processes, and ability to maintain quality throughout the production cycle. While OEMs can enhance brand recognition, they often come with higher costs and require careful management of contracts.
What Makes Custom Manufacturers Suitable for Specific Needs?
Custom manufacturers are adept at producing tailored solutions to meet specific client demands, making them ideal for specialized sectors like aerospace and medical devices. These manufacturers work closely with clients to understand their unique requirements, ensuring that the final product meets exact specifications. B2B buyers should assess the manufacturer’s technical expertise, flexibility, and ability to innovate. Although custom manufacturing provides unique solutions, it typically involves longer lead times and higher costs, which buyers must factor into their procurement strategies.
Why Choose Bulk Manufacturers for Standardized Products?
Bulk manufacturers are focused on producing large quantities of standardized products, making them particularly suitable for industries like food and beverages or construction. By leveraging economies of scale, these manufacturers can offer lower unit costs, which is beneficial for businesses looking to maintain competitive pricing. B2B buyers should consider the manufacturer’s production capacity, consistency in quality, and delivery reliability. However, buyers should be aware that bulk manufacturers may offer limited customization options, which could be a drawback for brands seeking to differentiate their products.
What Are the Benefits of Working with Artisan Manufacturers?
Artisan manufacturers prioritize craftsmanship and quality, often producing small batches of goods that cater to luxury markets or niche segments. This focus on quality can result in unique and highly desirable products, appealing to businesses looking to enhance their brand image. B2B buyers should evaluate the artisan manufacturer’s reputation, production methods, and ability to meet demand. While the exceptional quality and uniqueness of artisan products can justify higher prices, buyers must also consider the limited production capacity, which may affect supply consistency.
Related Video: Heat Pump Thermostat O, B, and C Terminal Variations Explained
Key Industrial Applications of high quality manufacturer
Industry/Sector | Specific Application of High Quality Manufacturer | Value/Benefit for the Business | Key Sourcing Considerations for this Application |
---|---|---|---|
Automotive | Precision Engine Components | Enhanced vehicle performance and reliability | Certifications, supply chain stability, and lead times |
Aerospace | Lightweight Structural Components | Improved fuel efficiency and reduced operational costs | Compliance with stringent regulations and quality standards |
Renewable Energy | Wind Turbine Parts | Increased energy output and durability | Material sourcing, sustainability practices, and certifications |
Electronics | Circuit Boards and Components | Higher performance and reliability in devices | Technological compatibility and after-sales support |
Food and Beverage | Processing Equipment | Improved efficiency and product quality | Hygiene standards, local regulations, and customization options |
How is High-Quality Manufacturing Used in the Automotive Sector?
In the automotive industry, high-quality manufacturers produce precision engine components that directly influence vehicle performance and reliability. These components, such as pistons, crankshafts, and fuel injectors, are essential for optimizing engine efficiency and minimizing emissions. For international B2B buyers, particularly from Africa and Europe, sourcing these components requires a focus on certifications and supply chain stability to ensure timely delivery and adherence to local regulations. Establishing relationships with manufacturers who can provide consistent quality and meet lead times is critical for maintaining production schedules.
What Role Does High-Quality Manufacturing Play in Aerospace Applications?
In the aerospace sector, high-quality manufacturers supply lightweight structural components that are crucial for aircraft design and performance. These components must meet rigorous safety and performance standards, contributing to improved fuel efficiency and reduced operational costs. Buyers from regions such as the Middle East and South America should prioritize manufacturers that comply with strict aerospace regulations and quality standards. The ability to demonstrate expertise in advanced materials and manufacturing processes is essential for ensuring the reliability and safety of aerospace products.
How is High-Quality Manufacturing Impacting Renewable Energy?
High-quality manufacturers are vital in the renewable energy sector, particularly in producing wind turbine parts. These components must be durable and capable of withstanding harsh environmental conditions, directly impacting energy output and operational longevity. For international buyers, especially in developing markets in Africa and South America, it is important to consider the manufacturer’s commitment to sustainability practices and the sourcing of materials. Additionally, certifications that verify the quality and environmental impact of the products can enhance buyer confidence.
Why is High-Quality Manufacturing Important in Electronics?
In the electronics industry, high-quality manufacturers produce circuit boards and components that are foundational to the performance of electronic devices. The reliability and efficiency of these components directly affect device functionality and consumer satisfaction. B2B buyers from Europe, particularly in tech hubs like Poland, should assess the technological compatibility of the components with their existing systems. Furthermore, after-sales support and warranty offerings from manufacturers can significantly influence sourcing decisions, ensuring long-term operational success.
How Does High-Quality Manufacturing Benefit the Food and Beverage Sector?
High-quality manufacturing plays a critical role in the food and beverage industry through the production of processing equipment. This equipment must adhere to strict hygiene standards and local regulations to ensure food safety and quality. For international B2B buyers, understanding the customization options available from manufacturers can lead to improved operational efficiency and product quality. Selecting suppliers who prioritize compliance and have a proven track record in the industry can mitigate risks associated with food processing and enhance overall business performance.
Related Video: FANUC Industrial Robots | AUDI Case Study
3 Common User Pain Points for ‘high quality manufacturer’ & Their Solutions
Scenario 1: Quality Assurance in Product Specifications
The Problem:
B2B buyers often face significant challenges when it comes to ensuring that the products manufactured meet the specified quality standards. For instance, a buyer in South America may order a batch of electronic components, only to discover upon delivery that they do not meet the required specifications or industry standards. This not only leads to wasted resources but also impacts production timelines and can damage relationships with end customers. The stakes are particularly high in industries like automotive or healthcare, where subpar quality can result in compliance issues and safety risks.
The Solution:
To mitigate this risk, buyers should implement a rigorous quality assurance process during the sourcing phase. This includes detailed specifications that outline the required quality standards, certifications, and testing protocols. It’s advisable to conduct an initial supplier audit, which can be done remotely, to assess their manufacturing capabilities and quality control systems. Establishing a transparent communication channel with the manufacturer is crucial. Regular updates and check-ins can help ensure that production aligns with the agreed standards. Additionally, consider utilizing third-party inspection services to verify quality before shipment, providing an extra layer of assurance.
Scenario 2: Navigating International Shipping and Logistics
The Problem:
Another common pain point for B2B buyers is the complexity of international shipping logistics. A manufacturer in Europe may promise timely delivery, but unexpected customs delays, documentation issues, or freight mishaps can lead to significant hold-ups. For buyers in Africa or the Middle East, these delays can disrupt their supply chain, leading to lost sales and frustrated customers. The lack of visibility into shipping processes can exacerbate these issues, leaving buyers feeling helpless and uncertain.
The Solution:
To streamline the shipping process, buyers should collaborate closely with manufacturers to establish a clear logistics plan that includes timelines, customs requirements, and potential risks. It is beneficial to work with logistics partners who have experience in international shipping and can navigate the complexities of customs regulations in different regions. Additionally, using technology such as shipment tracking software can provide real-time updates on the status of orders, allowing buyers to manage their inventory more effectively. Setting up contingency plans for potential delays can also help mitigate the impact on operations.
Scenario 3: Cultural and Communication Barriers
The Problem:
Cultural differences and language barriers can lead to misunderstandings between B2B buyers and manufacturers, impacting negotiations and project outcomes. For instance, a buyer from Africa may struggle to articulate their needs to a manufacturer in Europe due to different business etiquette and communication styles. This can result in misaligned expectations, missed deadlines, and ultimately, dissatisfaction with the partnership.
The Solution:
To bridge these cultural gaps, buyers should invest time in understanding the manufacturer’s culture and communication style. This can be facilitated by hiring local representatives or consultants who are familiar with both cultures and can act as intermediaries. Establishing clear and concise communication protocols is essential; this may include written summaries of meetings and agreements to ensure that both parties are on the same page. Leveraging digital communication tools that support multiple languages can also enhance clarity. Furthermore, fostering a relationship built on trust and transparency can help in overcoming these barriers, ensuring a smoother collaboration.
Strategic Material Selection Guide for high quality manufacturer
When selecting materials for high-quality manufacturing, it is essential to consider various factors that influence product performance, durability, and compliance with international standards. Below, we analyze four common materials used in high-quality manufacturing, focusing on their properties, advantages, disadvantages, and specific considerations for international B2B buyers.
What Are the Key Properties of Stainless Steel for High-Quality Manufacturing?
Stainless steel is renowned for its excellent corrosion resistance, high strength-to-weight ratio, and ability to withstand extreme temperatures. It is commonly used in applications requiring durability and hygiene, such as in the food and beverage industry, medical devices, and automotive components. Its temperature rating can reach up to 1,000°F (538°C) depending on the grade, making it suitable for high-temperature applications.
Pros and Cons: The primary advantage of stainless steel is its exceptional durability and resistance to rust and corrosion. However, it can be more expensive than other materials, and its manufacturing complexity may increase costs due to specialized tooling and processes.
Impact on Application: Stainless steel is compatible with a wide range of media, including acidic and alkaline substances, making it ideal for diverse applications.
Considerations for International Buyers: Buyers from regions such as Africa, South America, and Europe should ensure compliance with standards like ASTM, DIN, or JIS, which govern the quality and specifications of stainless steel. Understanding local regulations regarding food safety and medical applications is also crucial.
How Does Aluminum Compare as a Material Choice for High-Quality Manufacturing?
Aluminum is lightweight, corrosion-resistant, and possesses excellent thermal and electrical conductivity. It is often used in aerospace, automotive, and consumer goods manufacturing due to its favorable strength-to-weight ratio and ease of fabrication.
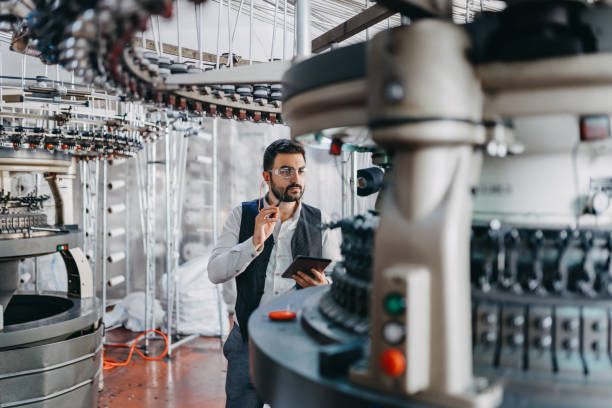
A stock image related to high quality manufacturer.
Pros and Cons: The key advantage of aluminum is its lightweight nature, which contributes to fuel efficiency in transportation applications. However, it has lower strength compared to stainless steel and may not be suitable for high-stress applications. Additionally, while aluminum is generally less expensive, its performance in extreme temperatures can be a limitation.
Impact on Application: Aluminum is compatible with a variety of media but may not perform well in highly corrosive environments unless treated or coated.
Considerations for International Buyers: B2B buyers should be aware of the specific grades of aluminum and their certifications. Compliance with regional standards is essential, particularly in industries like aerospace and automotive, where safety and performance are paramount.
What Are the Benefits and Limitations of Carbon Steel in High-Quality Manufacturing?
Carbon steel is widely used due to its high tensile strength and hardness, making it suitable for structural applications and heavy machinery. It can be heat-treated to enhance its properties, offering versatility in manufacturing.
Pros and Cons: The primary advantage of carbon steel is its cost-effectiveness and strength. However, its susceptibility to rust and corrosion can be a significant drawback, requiring protective coatings or treatments. Additionally, carbon steel may not perform well in high-temperature applications without proper alloying.
Impact on Application: Carbon steel is suitable for applications involving mechanical stress but is not ideal for corrosive environments unless adequately protected.
Considerations for International Buyers: Buyers should ensure that the carbon steel meets local standards and regulations, particularly in construction and heavy machinery. Understanding the environmental conditions in which the product will be used is critical for selecting the right grade.
Why Is Plastic a Viable Material for High-Quality Manufacturing?
Plastics, including high-performance polymers, are increasingly used in high-quality manufacturing due to their lightweight, corrosion resistance, and versatility in design. They can be engineered to meet specific performance criteria, including temperature and chemical resistance.
Pros and Cons: The main advantage of plastics is their adaptability and lower manufacturing costs compared to metals. However, they may not offer the same level of strength and durability, particularly in high-stress applications.
Impact on Application: Plastics can be suitable for a variety of media, but their performance can vary significantly based on the type of polymer used.
Considerations for International Buyers: B2B buyers should pay attention to the specific type of plastic and its compliance with environmental regulations, especially in Europe where standards are stringent. Understanding the end-use application is crucial for selecting the appropriate plastic material.
Summary Table of Material Selection for High-Quality Manufacturing
Material | Typical Use Case for High Quality Manufacturer | Key Advantage | Key Disadvantage/Limitation | Relative Cost (Low/Med/High) |
---|---|---|---|---|
Stainless Steel | Food processing, medical devices, automotive components | Exceptional durability and corrosion resistance | Higher cost and manufacturing complexity | High |
Aluminum | Aerospace, automotive, consumer goods | Lightweight and good thermal conductivity | Lower strength and performance in extreme temperatures | Medium |
Carbon Steel | Structural applications, heavy machinery | Cost-effective and high tensile strength | Susceptible to rust and corrosion | Low |
Plastic | Consumer goods, electrical housings | Lightweight and versatile | Lower strength and durability in high-stress applications | Low |
This strategic guide provides international B2B buyers with actionable insights into material selection, ensuring that they can make informed decisions tailored to their specific industry needs and regional compliance requirements.
In-depth Look: Manufacturing Processes and Quality Assurance for high quality manufacturer
What Are the Main Stages of Manufacturing for High Quality Manufacturers?
The manufacturing process for high quality products typically involves several critical stages: material preparation, forming, assembly, and finishing. Each stage is crucial to ensuring that the final product meets the high standards expected by B2B buyers.
-
Material Preparation: This initial stage involves selecting and preparing raw materials. High quality manufacturers often use advanced materials that offer superior durability and performance. Buyers should inquire about the source and quality of materials, as they directly impact the final product.
-
Forming: This stage includes processes such as machining, molding, and welding. Techniques like precision machining and injection molding are commonly employed to achieve exact specifications. Buyers should ensure that manufacturers utilize modern technology and skilled labor to maintain high precision levels.
-
Assembly: In this phase, individual components are brought together to form the final product. High quality manufacturers often implement automated assembly lines to enhance efficiency and accuracy. Buyers should look for manufacturers that can demonstrate their assembly capabilities through detailed process descriptions and case studies.
-
Finishing: The final stage involves processes such as surface treatment, painting, and packaging. High quality manufacturers pay close attention to finishing details, as they can significantly affect product aesthetics and performance. Buyers should ask about the finishing techniques used and their impact on the product’s longevity and appeal.
How Does Quality Assurance Work in High Quality Manufacturing?
Quality assurance (QA) is a critical aspect of high quality manufacturing. It involves systematic processes that ensure products meet specified standards throughout the manufacturing cycle.
What International Standards Are Relevant for Quality Assurance?
High quality manufacturers often adhere to international quality standards such as ISO 9001, which outlines criteria for a quality management system. Compliance with ISO standards assures buyers that the manufacturer has processes in place to consistently deliver products that meet customer and regulatory requirements.
Additionally, industry-specific certifications such as CE marking (for products sold in the European Economic Area) or API (American Petroleum Institute) certification for oil and gas products can further validate a manufacturer’s quality assurance practices. B2B buyers should ensure that potential suppliers hold relevant certifications applicable to their industry.
What Are the Key Quality Control Checkpoints in Manufacturing?
Quality control (QC) is integrated into various checkpoints throughout the manufacturing process:
-
Incoming Quality Control (IQC): This initial checkpoint involves inspecting raw materials before they enter the production line. Ensuring that materials meet specified standards is vital for maintaining overall product quality.
-
In-Process Quality Control (IPQC): During the manufacturing process, ongoing inspections help identify defects early. High quality manufacturers often implement real-time monitoring systems to catch issues before they escalate.
-
Final Quality Control (FQC): This final checkpoint involves a thorough inspection of the finished product. It typically includes functional testing, visual inspections, and performance assessments to ensure that the product meets all specifications.
What Common Testing Methods Are Used in Quality Assurance?
Manufacturers employ various testing methods to ensure quality, including:
-
Destructive Testing: This method assesses the durability and performance of a product until failure. While it provides valuable insights into material properties, it is not suitable for all products.
-
Non-Destructive Testing (NDT): Techniques such as ultrasonic testing and radiographic inspection allow manufacturers to evaluate a product’s integrity without causing damage. NDT is particularly beneficial for high-stakes industries like aerospace and medical devices.
-
Performance Testing: This involves subjecting products to operational conditions to evaluate their functionality. Buyers should request test reports that detail how products perform under expected usage scenarios.
How Can B2B Buyers Verify Supplier Quality Control?
For B2B buyers, verifying the quality control processes of potential suppliers is essential to mitigate risks. Here are several strategies:
-
Conduct Audits: Organizing on-site audits can provide firsthand insight into a manufacturer’s quality assurance practices. Buyers should prepare a checklist based on industry standards and specific product requirements.
-
Request Quality Reports: Manufacturers should provide detailed quality reports that document their QC processes, results from various checkpoints, and compliance with international standards.
-
Engage Third-Party Inspectors: Utilizing third-party inspection services can offer an unbiased evaluation of a manufacturer’s quality control processes. These inspectors can conduct thorough assessments and provide reports that help buyers make informed decisions.
What Quality Control Nuances Should International Buyers Consider?
International B2B buyers, especially from regions like Africa, South America, the Middle East, and Europe, should be aware of several nuances in quality control:
-
Cultural Differences: Different regions may have varying standards of quality. Understanding local manufacturing practices and expectations can help buyers navigate potential challenges.
-
Regulatory Compliance: Ensure that the manufacturer complies with both local regulations and international standards. This is particularly important for products that will be exported to different markets.
-
Language Barriers: Effective communication is critical in quality assurance. Buyers should ensure that there are clear lines of communication regarding specifications, standards, and expectations to avoid misunderstandings.
By focusing on these aspects of manufacturing processes and quality assurance, international B2B buyers can make more informed decisions, ensuring that they partner with high quality manufacturers capable of delivering products that meet their needs.
Practical Sourcing Guide: A Step-by-Step Checklist for ‘high quality manufacturer’
In the competitive landscape of international B2B sourcing, identifying a high-quality manufacturer is crucial for ensuring product excellence and supply chain reliability. This guide provides a step-by-step checklist to assist buyers, especially from Africa, South America, the Middle East, and Europe, in making informed procurement decisions.
Step 1: Define Your Technical Specifications
Before starting your search, clearly outline your product requirements, including materials, dimensions, tolerances, and any specific industry standards. This clarity helps to communicate effectively with potential suppliers and ensures that the manufacturers you consider can meet your needs. Having precise specifications also aids in evaluating quotes and comparing different manufacturers.
Step 2: Conduct Market Research for Potential Suppliers
Utilize industry-specific directories, trade shows, and online platforms to gather a list of potential manufacturers. Pay attention to their market reputation and experience within your industry sector. Researching suppliers from regions with a strong manufacturing base, such as Asia or Europe, can yield high-quality options.
Step 3: ✅ Verify Supplier Certifications
Check for relevant certifications that demonstrate compliance with international quality standards (e.g., ISO 9001). These certifications indicate that a manufacturer adheres to quality management principles and can consistently produce products that meet customer requirements. Ensure that the certifications are current and issued by recognized bodies.
Step 4: Request Samples and Prototypes
Ask potential suppliers for product samples or prototypes to evaluate their quality firsthand. This step is critical for assessing not only the material quality but also the manufacturer’s attention to detail and ability to meet specifications. Analyze the samples for consistency, durability, and overall craftsmanship.
Step 5: Evaluate Production Capabilities and Capacity
Inquire about the manufacturer’s production capabilities, including their equipment, technology, and workforce expertise. Understanding their capacity to scale production is vital, especially if you anticipate growth or fluctuating order volumes. A manufacturer should have the flexibility to adapt to your demands without compromising quality.
Step 6: Assess Communication and Support
Effective communication is key to a successful partnership. Evaluate how responsive and transparent potential suppliers are during initial interactions. A manufacturer that prioritizes clear communication and provides dedicated support can help mitigate misunderstandings and ensure smoother project management.
Step 7: Request References and Conduct Site Visits
Ask for references from other clients, particularly those in your industry or region. Reach out to these references to gain insights into their experiences with the manufacturer. If feasible, conduct site visits to observe the manufacturing process and working conditions firsthand. This step reinforces your confidence in their capabilities and reliability.
By following this checklist, international B2B buyers can strategically navigate the process of sourcing high-quality manufacturers, ensuring they select partners that align with their business objectives and quality expectations.
Comprehensive Cost and Pricing Analysis for high quality manufacturer Sourcing
What Are the Key Cost Components in High-Quality Manufacturing?
Understanding the cost structure of high-quality manufacturing is essential for international B2B buyers aiming to optimize sourcing strategies. The primary cost components include:
-
Materials: The type and quality of materials significantly impact production costs. Sourcing high-grade raw materials can enhance product quality but may also inflate costs. Buyers should evaluate suppliers’ material specifications to ensure alignment with their quality standards while negotiating favorable prices.
-
Labor: Labor costs vary by region and skill levels. For instance, manufacturers in Africa may offer competitive labor rates, but the availability of skilled labor can affect the overall quality of production. Buyers should consider labor costs alongside the expertise of the workforce.
-
Manufacturing Overhead: This includes utilities, facility costs, and administrative expenses. A manufacturer with higher overhead might pass these costs onto buyers. Understanding the overhead structure can help buyers assess whether a supplier’s pricing is justified.
-
Tooling: Initial tooling costs can be substantial, particularly for custom products. Buyers should inquire about tooling costs upfront, as these can impact the overall pricing structure significantly.
-
Quality Control (QC): Implementing rigorous QC measures ensures product reliability but adds to the cost. Buyers should assess the QC processes in place to balance quality assurance with cost efficiency.
-
Logistics: Transportation and shipping costs can vary greatly depending on the supplier’s location and the chosen Incoterms. Understanding these logistics can lead to more informed decisions on supplier selection.
-
Margin: Manufacturers typically include a profit margin in their pricing. Understanding how a supplier’s margin aligns with industry standards can provide insight into whether a price is competitive.
How Do Price Influencers Affect Sourcing Decisions?
Several factors influence pricing in high-quality manufacturing:
-
Volume/MOQ (Minimum Order Quantity): Ordering in bulk often reduces per-unit costs. Buyers should negotiate MOQs that align with their needs while maximizing cost efficiency.
-
Specifications and Customization: Custom products may incur additional costs. Buyers should clarify specifications early in the negotiation process to avoid unexpected expenses.
-
Materials and Quality Certifications: Higher quality materials and certifications (like ISO) can elevate costs. Buyers should evaluate whether the benefits of certifications justify the price increase.
-
Supplier Factors: The supplier’s reputation, experience, and production capabilities can influence pricing. Conducting due diligence on potential suppliers can lead to better pricing negotiations.
-
Incoterms: Understanding Incoterms is critical for managing logistics costs. Different terms can significantly alter the total landed cost of goods.
What Are Effective Buyer Tips for Cost-Efficiency?
For international B2B buyers, particularly those from Africa, South America, the Middle East, and Europe, here are actionable tips to enhance cost efficiency in sourcing:
-
Negotiate Strategically: Leverage competitive quotes from multiple suppliers to negotiate better terms. Highlighting long-term partnership potential can also encourage suppliers to offer more favorable pricing.
-
Consider Total Cost of Ownership (TCO): Evaluate not just the purchase price but the total cost associated with the product, including shipping, customs duties, and maintenance. This holistic view can lead to more informed sourcing decisions.
-
Understand Pricing Nuances: Pricing structures can vary widely based on regional economic conditions, exchange rates, and local demand. Being aware of these nuances can empower buyers to negotiate more effectively.
-
Leverage Technology: Utilize platforms and tools that provide market insights and cost comparisons. This data can support negotiations and aid in selecting the most cost-effective suppliers.
Disclaimer on Indicative Prices
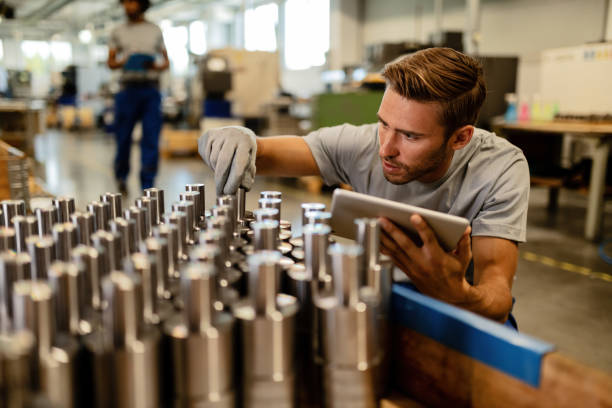
A stock image related to high quality manufacturer.
Prices in high-quality manufacturing can fluctuate based on numerous factors, including market conditions and supplier negotiations. It is advisable for buyers to conduct thorough market research and obtain multiple quotations to ensure they are making informed purchasing decisions.
Alternatives Analysis: Comparing high quality manufacturer With Other Solutions
Understanding the Importance of Alternatives in B2B Manufacturing Solutions
In the competitive landscape of international B2B transactions, particularly for buyers from regions like Africa, South America, the Middle East, and Europe, evaluating alternatives to high-quality manufacturing is crucial. This section explores how high-quality manufacturers stack up against other viable solutions, helping buyers make informed decisions.
Comparison Table of High-Quality Manufacturer vs. Alternatives
Comparison Aspect | High Quality Manufacturer | Alternative 1: Low-Cost Manufacturer | Alternative 2: In-House Production |
---|---|---|---|
Performance | Superior durability and precision | Adequate but inconsistent quality | Highly controlled quality |
Cost | Higher initial investment | Lower initial costs | Variable costs depending on scale |
Ease of Implementation | Requires thorough vetting and setup | Quick onboarding process | Time-consuming setup |
Maintenance | Regular quality checks needed | Minimal maintenance required | Full responsibility on buyer |
Best Use Case | High-stakes projects requiring reliability | Budget-sensitive projects | Long-term projects with consistent demand |
What Are the Pros and Cons of Low-Cost Manufacturers?
Low-cost manufacturers are often appealing due to their reduced pricing structure. They can provide adequate performance for projects where quality is not the primary concern. However, their inconsistent quality can lead to increased rejection rates and potential delays, which can be particularly detrimental in time-sensitive projects. Additionally, while they require less maintenance, the risk of poor quality could lead to higher long-term costs due to rework or product failures.
How Does In-House Production Compare?
In-house production provides buyers with complete control over the manufacturing process, ensuring high quality and customization tailored to specific needs. This solution is particularly beneficial for companies with long-term projects that can justify the investment in facilities and personnel. However, the initial setup is often time-consuming and requires significant capital investment. Furthermore, ongoing operational costs can vary widely, making financial forecasting challenging.
Making the Right Choice: Which Solution Is Best for Your Business?
Choosing the right manufacturing solution depends on various factors, including project scope, budget constraints, and long-term business objectives. For projects demanding high reliability and performance, a high-quality manufacturer is often worth the investment despite the higher costs. Conversely, for budget-sensitive projects or those with less stringent quality requirements, low-cost manufacturers may be more suitable. In-house production is ideal for organizations aiming for full control and customization but requires careful consideration of the associated costs and resource commitments.
Ultimately, buyers should assess their specific needs, evaluate potential risks, and consider the long-term implications of their choice to ensure that they select a solution that aligns with their strategic goals.
Essential Technical Properties and Trade Terminology for high quality manufacturer
What Are the Essential Technical Properties of a High-Quality Manufacturer?
When sourcing products from manufacturers, understanding key technical properties is vital for international B2B buyers. Here are several critical specifications that can influence your purchasing decisions:
1. Material Grade: Why Is It Crucial for Quality?
Material grade refers to the categorization of raw materials based on their mechanical properties and chemical composition. For instance, steel can be classified as mild, medium, or high-grade, affecting its strength, ductility, and corrosion resistance. Selecting the right material grade is essential for ensuring the durability and performance of the final product. Buyers should inquire about the material grades used by manufacturers to ensure they meet industry standards and specific application requirements.
2. Tolerance: What Does It Mean for Product Precision?
Tolerance defines the allowable deviation in dimensions and specifications of a product. It is critical in manufacturing processes where precision is paramount, such as in aerospace or automotive components. A tighter tolerance often indicates higher quality, but it can also lead to increased production costs. Understanding the tolerance levels offered by a manufacturer can help buyers assess whether the products will meet their operational needs and specifications.
3. Surface Finish: How Does It Impact Functionality?
Surface finish refers to the texture and smoothness of a product’s exterior. Different applications may require specific finishes, such as anodizing for aluminum or polishing for stainless steel. The surface finish can affect not only the aesthetic appeal but also the product’s resistance to wear and corrosion. When evaluating manufacturers, inquire about the available surface finishes and their implications for product performance.
4. Mechanical Properties: Why Are They Important for Performance?
Mechanical properties include characteristics such as tensile strength, yield strength, and hardness. These properties are essential for assessing how a material will perform under stress or load. For instance, a high tensile strength indicates that a material can withstand significant force without breaking. Buyers should consider these properties to ensure that the products can handle the demands of their intended applications.
What Are the Common Trade Terminology and Jargon in Manufacturing?
Understanding industry terminology is crucial for effective communication with manufacturers. Here are several common trade terms that international B2B buyers should familiarize themselves with:
1. What Is OEM (Original Equipment Manufacturer)?
OEM refers to a company that produces parts or equipment that may be marketed by another manufacturer. In many cases, OEMs provide customized solutions tailored to the specifications of their clients. For buyers, working with OEMs can ensure that they receive high-quality components designed specifically for their applications.
2. How Does MOQ (Minimum Order Quantity) Affect Purchasing Decisions?
MOQ is the minimum number of units a manufacturer requires a buyer to purchase in a single order. Understanding MOQ is essential for budget planning and inventory management. Buyers should negotiate MOQs that align with their sales forecasts to avoid excess stock or cash flow issues.
3. What Is an RFQ (Request for Quotation)?
An RFQ is a document sent to suppliers requesting pricing and other details for a specific product or service. It is a key tool for buyers to compare offers from different manufacturers. Including detailed specifications in an RFQ can help ensure that you receive accurate quotes that facilitate informed decision-making.
4. How Do Incoterms Influence International Trade?
Incoterms, or International Commercial Terms, are a set of predefined rules that outline the responsibilities of buyers and sellers in international trade. They clarify who is responsible for shipping, insurance, and tariffs. Familiarity with Incoterms can help buyers navigate logistics and avoid unexpected costs during the shipping process.
In summary, understanding these essential technical properties and trade terminologies can significantly enhance the decision-making process for international B2B buyers. By focusing on quality specifications and effective communication, you can ensure a successful partnership with high-quality manufacturers.
Navigating Market Dynamics and Sourcing Trends in the high quality manufacturer Sector
What Are the Key Trends Influencing the High-Quality Manufacturer Sector?
The high-quality manufacturing sector is undergoing significant transformation driven by globalization, technological advancements, and shifting consumer preferences. For international B2B buyers, particularly from Africa, South America, the Middle East, and Europe, understanding these dynamics is crucial for effective sourcing decisions.
One of the most notable trends is the rise of digital transformation within manufacturing. Technologies like IoT, AI, and advanced analytics are being adopted to enhance production efficiency and quality control. This trend allows manufacturers to respond swiftly to market changes and customer demands, making it essential for buyers to seek suppliers who leverage these technologies.
Sourcing trends are also evolving, with an increasing focus on nearshoring and reshoring. Many companies are moving production closer to end markets to reduce lead times and shipping costs. For buyers in Europe, for instance, this can mean sourcing from Eastern European manufacturers who can deliver high-quality products with shorter delivery times. Similarly, buyers in Africa and South America are looking towards local manufacturers to reduce dependency on distant suppliers.
Moreover, sustainability is becoming a driving factor in supplier selection. Buyers are increasingly prioritizing suppliers who demonstrate commitment to sustainable practices, which can enhance brand reputation and compliance with international regulations.
How Is Sustainability Shaping Sourcing Decisions in the High-Quality Manufacturing Sector?
Sustainability and ethical sourcing are no longer optional but essential components of the B2B landscape. The environmental impact of manufacturing processes has come under scrutiny, pushing companies to adopt sustainable practices. For buyers, this means considering not just the quality of the products but also the ecological footprint of their suppliers.
High-quality manufacturers are increasingly obtaining certifications such as ISO 14001 for environmental management and Fair Trade for ethical sourcing. These certifications provide assurance that suppliers adhere to stringent environmental and ethical standards. Buyers should actively seek manufacturers with these credentials to ensure they are aligning with global sustainability goals.
Additionally, the use of ‘green’ materials, such as recycled or biodegradable components, is gaining traction. This trend reflects a broader consumer demand for environmentally friendly products. By sourcing from manufacturers who prioritize sustainability, buyers can enhance their brand image and appeal to eco-conscious consumers.
What Is the Evolution of the High-Quality Manufacturing Sector?
The high-quality manufacturing sector has evolved significantly over the past few decades, transitioning from traditional mass production methods to a more sophisticated, technology-driven approach. Initially, manufacturers focused on cost reduction and efficiency; however, the emergence of globalization and increased competition has shifted the focus toward quality, innovation, and customer-centric solutions.
In the early 2000s, the introduction of lean manufacturing principles revolutionized the industry, emphasizing waste reduction and continuous improvement. This evolution paved the way for the integration of advanced technologies, such as robotics and automation, which further enhanced production capabilities.
Today, the sector is characterized by a blend of traditional craftsmanship and cutting-edge technology. This evolution has empowered B2B buyers to expect not only high-quality products but also flexibility and responsiveness from their suppliers. Understanding this historical context is vital for buyers looking to navigate the complexities of the current manufacturing landscape effectively.
Frequently Asked Questions (FAQs) for B2B Buyers of high quality manufacturer
-
How do I solve quality assurance issues when sourcing from manufacturers?
To address quality assurance concerns, start by establishing clear quality standards and specifications in your contracts. Conduct thorough background checks on potential manufacturers, including their certifications and compliance with international standards. Request samples before placing large orders to evaluate product quality firsthand. Regularly schedule quality audits and inspections, either through third-party services or your own team, to ensure adherence to quality protocols throughout the production process. -
What is the best way to vet high-quality manufacturers for my business needs?
To effectively vet high-quality manufacturers, utilize a multi-step approach. Begin by researching their reputation through industry reviews and feedback from previous clients. Request documentation of certifications, such as ISO or relevant industry standards, to verify their credibility. Conduct factory visits or virtual tours to observe their operations. Additionally, consider engaging local agents or consultants who understand the regional market to provide insights into the manufacturer’s reliability and quality. -
What are the common payment terms to expect when dealing with international manufacturers?
Payment terms can vary significantly by region and manufacturer, but common practices include a 30% upfront deposit with the balance due upon shipment. Letters of credit are also popular for larger transactions, providing security for both parties. It’s crucial to discuss and negotiate terms upfront, considering factors like your cash flow and the manufacturer’s payment history. Ensure all terms are documented in a formal agreement to avoid disputes later. -
What are the implications of Minimum Order Quantities (MOQ) on my purchasing decisions?
Minimum Order Quantities (MOQ) can impact your purchasing strategy, particularly if you’re a small or medium-sized business. Manufacturers set MOQs to cover production costs, which can lead to excess inventory if you overestimate your needs. To manage this, negotiate the MOQ based on your budget and sales forecasts. Alternatively, consider collaborating with other businesses to meet the MOQ collectively or seek manufacturers that offer flexible MOQs. -
How can I ensure my specific requirements are met by manufacturers?
To ensure your specific requirements are met, begin with a detailed request for proposal (RFP) that outlines all your needs, including technical specifications, design elements, and compliance standards. Engage in open communication with potential manufacturers to clarify expectations and capabilities. Consider establishing a prototype phase where adjustments can be made before mass production begins. Building a strong partnership with your manufacturer can also facilitate better customization to meet your needs. -
What logistics considerations should I keep in mind when importing goods?
When importing goods, logistics considerations include shipping methods, customs regulations, and delivery timelines. Choose between air freight for speed or sea freight for cost-effectiveness, depending on your urgency and budget. Familiarize yourself with customs duties and import taxes in your country to avoid unexpected costs. Collaborating with a reliable freight forwarder can streamline the shipping process and ensure compliance with all regulations, minimizing delays. -
How do I handle disputes with international manufacturers effectively?
Handling disputes effectively requires a proactive approach. First, maintain clear and documented communication throughout the business relationship. If a dispute arises, attempt to resolve it amicably through negotiation. If necessary, refer to your contract for dispute resolution clauses, which may include mediation or arbitration. Engaging legal counsel experienced in international trade can provide guidance on navigating complex situations and ensuring your interests are protected. -
What role does cultural understanding play in international B2B relationships?
Cultural understanding is pivotal in fostering strong international B2B relationships. Different cultures have distinct communication styles, negotiation practices, and business etiquettes. Investing time in understanding the cultural nuances of your manufacturing partners can enhance collaboration and reduce misunderstandings. Consider cultural training or working with local intermediaries who can bridge gaps and facilitate smoother interactions, ultimately leading to more successful partnerships.
Important Disclaimer & Terms of Use
⚠️ Important Disclaimer
The information provided in this guide, including content regarding manufacturers, technical specifications, and market analysis, is for informational and educational purposes only. It does not constitute professional procurement advice, financial advice, or legal advice.
While we have made every effort to ensure the accuracy and timeliness of the information, we are not responsible for any errors, omissions, or outdated information. Market conditions, company details, and technical standards are subject to change.
B2B buyers must conduct their own independent and thorough due diligence before making any purchasing decisions. This includes contacting suppliers directly, verifying certifications, requesting samples, and seeking professional consultation. The risk of relying on any information in this guide is borne solely by the reader.
Strategic Sourcing Conclusion and Outlook for high quality manufacturer
Why is Strategic Sourcing Essential for International B2B Buyers?
In today’s competitive landscape, strategic sourcing emerges as a pivotal process for international B2B buyers aiming to collaborate with high-quality manufacturers. By focusing on supplier relationships, thorough market analysis, and aligning procurement strategies with business goals, companies can secure not only cost-effective solutions but also superior quality products. This approach is particularly vital for buyers in Africa, South America, the Middle East, and Europe, where understanding local market dynamics and cultural nuances can significantly influence sourcing success.
What Key Takeaways Should B2B Buyers Consider?
As you embark on your sourcing journey, remember the importance of due diligence. Evaluate potential manufacturers based on their quality certifications, production capabilities, and compliance with international standards. Furthermore, fostering long-term relationships with suppliers can lead to enhanced collaboration, innovation, and responsiveness to market changes. The insights gathered from this guide can help you navigate challenges and leverage opportunities effectively.
How Can B2B Buyers Prepare for the Future?
Looking ahead, the landscape of manufacturing and sourcing will continue to evolve, driven by technological advancements and shifting global trade dynamics. International B2B buyers are encouraged to remain agile, embracing digital tools and platforms that facilitate transparent communication and efficient transactions. By prioritizing strategic sourcing, you position your business to thrive in a rapidly changing environment.
Take action today—assess your current sourcing strategies, identify high-quality manufacturers, and build partnerships that will drive your business forward in the global marketplace.