Discover Top Benefits of a Lithium Ion Batterie Manufacturer (2025)
Introduction: Navigating the Global Market for lithium ion batterie manufacturer
Navigating the global market for lithium-ion battery manufacturers presents a unique challenge for international B2B buyers, particularly those in regions like Africa, South America, the Middle East, and Europe. With the increasing demand for electric vehicles and renewable energy solutions, sourcing reliable lithium-ion batteries has become crucial. This guide serves as a comprehensive resource, covering various battery types, their applications, effective supplier vetting strategies, and cost considerations.
Understanding the intricacies of lithium-ion battery sourcing is essential for making informed purchasing decisions. Buyers will find valuable insights into the supply chain dynamics, including key production countries and the significance of sustainable sourcing practices. The guide also emphasizes the importance of quality assurance and compliance with international standards, ensuring that businesses can confidently select suppliers that meet their specific needs.
By empowering B2B buyers with actionable information, this guide aims to streamline the purchasing process and foster successful partnerships with manufacturers. Whether you are based in the UAE, the UK, or other regions, the insights provided will enhance your ability to navigate the complexities of the lithium-ion battery market, ultimately contributing to your business’s growth and sustainability in an increasingly electrified world.
Understanding lithium ion batterie manufacturer Types and Variations
Type Name | Key Distinguishing Features | Primary B2B Applications | Brief Pros & Cons for Buyers |
---|---|---|---|
Cylindrical Lithium-ion | Standardized size, high energy density, and good thermal stability | Consumer electronics, power tools | Pros: Widely available, cost-effective; Cons: Limited customization options. |
Prismatic Lithium-ion | Flat, rectangular design, optimized for space efficiency | Electric vehicles, energy storage systems | Pros: Space-efficient, high capacity; Cons: Higher production costs. |
Pouch Lithium-ion | Flexible packaging, lightweight, and high energy density | Wearables, drones, and portable devices | Pros: Lightweight, customizable shapes; Cons: Less robust, sensitive to punctures. |
Lithium Iron Phosphate (LiFePO4) | Enhanced thermal stability and safety, longer cycle life | Electric vehicles, solar energy storage | Pros: Safe, long lifespan; Cons: Lower energy density compared to others. |
Lithium Nickel Manganese Cobalt (NMC) | Balanced performance, high energy density, and good thermal stability | Electric vehicles, medical devices | Pros: Versatile, high performance; Cons: Expensive raw materials. |
What are the Characteristics of Cylindrical Lithium-ion Batteries?
Cylindrical lithium-ion batteries are characterized by their standardized cylindrical shape, which allows for mass production and compatibility across various applications. They typically offer high energy density and good thermal stability, making them suitable for consumer electronics and power tools. When purchasing, businesses should consider the availability and cost-effectiveness of these batteries, but may find limitations in customization.
How Do Prismatic Lithium-ion Batteries Stand Out?
Prismatic lithium-ion batteries feature a flat, rectangular design that optimizes space efficiency. This design is particularly beneficial for applications like electric vehicles and energy storage systems, where maximizing available space is crucial. Buyers should weigh the advantages of higher capacity and space efficiency against the potentially higher production costs associated with prismatic batteries.
What are the Advantages of Pouch Lithium-ion Batteries?
Pouch lithium-ion batteries are known for their flexibility and lightweight nature, allowing for customizable shapes and sizes. They are commonly used in wearables, drones, and portable devices, where weight and form factor are critical. However, buyers must consider the trade-off of less robustness and increased sensitivity to punctures, which can affect long-term durability.
Why Choose Lithium Iron Phosphate (LiFePO4) Batteries?
Lithium Iron Phosphate (LiFePO4) batteries are recognized for their enhanced thermal stability and safety, along with a longer cycle life compared to other lithium-ion types. These features make them ideal for applications in electric vehicles and solar energy storage. While they offer a safe and long-lasting solution, buyers should note that they have a lower energy density, which may limit their use in high-performance applications.
What Makes Lithium Nickel Manganese Cobalt (NMC) Batteries a Versatile Option?
Lithium Nickel Manganese Cobalt (NMC) batteries are designed to deliver a balanced performance, combining high energy density with good thermal stability. This versatility makes them suitable for a range of applications, including electric vehicles and medical devices. However, the higher costs associated with raw materials can be a significant consideration for buyers, particularly in budget-sensitive projects.
Related Video: Types of Lithium ion battery with application | Lithium ion battery types LCO,LMO,LFP, NMC, NCA, LTO
Key Industrial Applications of lithium ion batterie manufacturer
Industry/Sector | Specific Application of lithium ion batterie manufacturer | Value/Benefit for the Business | Key Sourcing Considerations for this Application |
---|---|---|---|
Automotive | Electric Vehicles (EVs) | Enhanced performance, longer range, and sustainability | Battery capacity, thermal management, and charging infrastructure compatibility |
Renewable Energy | Energy Storage Systems | Efficient energy management and grid stability | Scalability, lifecycle performance, and integration with renewable sources |
Consumer Electronics | Portable Electronics | Lightweight and compact design for improved portability | Energy density, safety features, and rapid charging capability |
Telecommunications | Backup Power Solutions | Reliability in critical communication infrastructures | Battery lifespan, environmental resilience, and regulatory compliance |
Industrial Automation | Robotics and Automated Machinery | Increased productivity and operational efficiency | Customization for specific applications and durability under varying conditions |
How Are Lithium Ion Batteries Used in the Automotive Sector?
In the automotive industry, lithium-ion batteries are primarily utilized in electric vehicles (EVs). These batteries provide high energy density, allowing vehicles to achieve longer ranges on a single charge. For international B2B buyers in regions like Africa and Europe, sourcing these batteries involves ensuring compliance with local regulations and standards. Additionally, manufacturers must consider the integration of thermal management systems to optimize battery performance and safety, addressing challenges such as overheating and degradation over time.
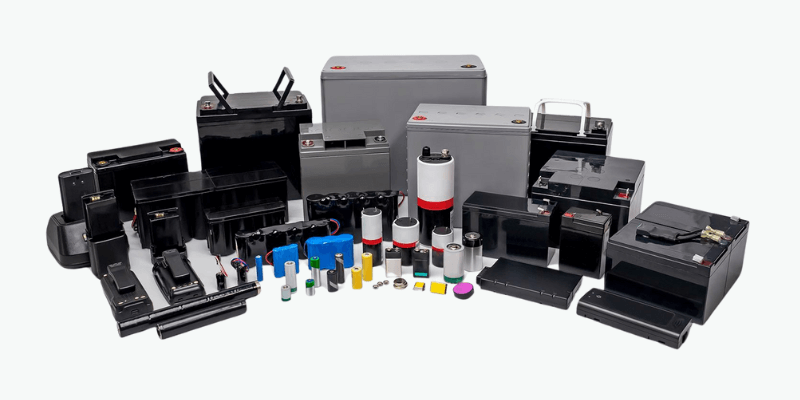
A stock image related to lithium ion batterie manufacturer.
What Role Do Lithium Ion Batteries Play in Renewable Energy Solutions?
In the renewable energy sector, lithium-ion batteries are essential for energy storage systems, enabling the effective management of energy produced from solar and wind sources. These batteries help stabilize the grid by storing excess energy for use during peak demand periods. Buyers from South America and the Middle East should focus on sourcing batteries that offer scalability and long lifecycle performance to ensure a reliable return on investment. The integration of these systems with existing infrastructure is also a critical consideration for maximizing efficiency.
How Are Lithium Ion Batteries Enhancing Consumer Electronics?
Lithium-ion batteries are integral to consumer electronics, powering devices such as smartphones, laptops, and tablets. Their lightweight and compact design allows for improved portability, making them ideal for modern consumer demands. International buyers, particularly in Europe and the UAE, should prioritize sourcing batteries that offer high energy density and rapid charging capabilities. Safety features, such as overcharge protection and thermal stability, are also vital to prevent potential hazards, ensuring consumer trust and satisfaction.
Why Are Lithium Ion Batteries Important for Telecommunications?
In the telecommunications sector, lithium-ion batteries serve as backup power solutions, ensuring uninterrupted service during outages. These batteries provide reliability for critical communication infrastructures, which is crucial in regions with unstable power supplies, such as parts of Africa. When sourcing batteries for this application, businesses should consider lifespan, environmental resilience, and compliance with industry regulations to guarantee operational reliability and safety.
How Do Lithium Ion Batteries Contribute to Industrial Automation?
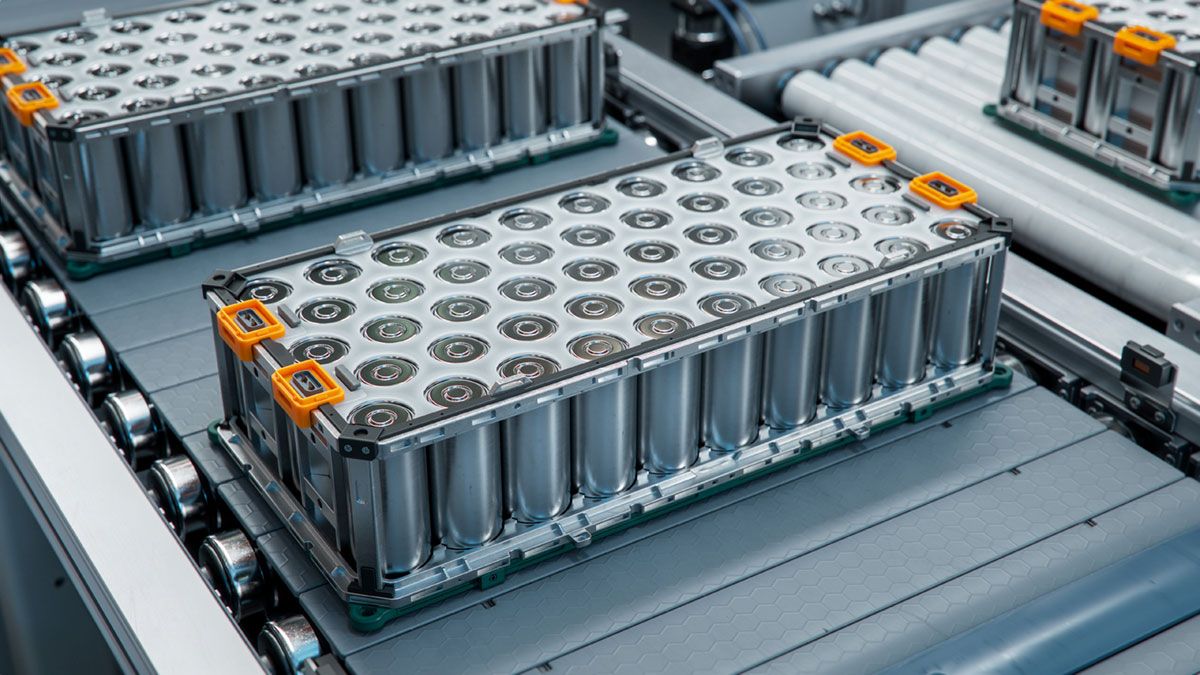
A stock image related to lithium ion batterie manufacturer.
In industrial automation, lithium-ion batteries are used to power robotics and automated machinery, enhancing productivity and operational efficiency. These batteries enable machines to operate autonomously, reducing downtime and labor costs. B2B buyers in sectors like manufacturing and logistics should focus on sourcing batteries that can be customized for specific applications, ensuring they meet the durability and performance requirements of various industrial environments.
Related Video: How It’s Made – Lithium Ion Batteries
3 Common User Pain Points for ‘lithium ion batterie manufacturer’ & Their Solutions
Scenario 1: Sourcing Quality Lithium Ion Batteries Amidst Supply Chain Disruptions
The Problem:
International B2B buyers often face significant challenges in sourcing high-quality lithium ion batteries due to supply chain disruptions. Factors such as geopolitical tensions, trade restrictions, and fluctuating raw material prices can lead to inconsistent supply and quality issues. This unpredictability can result in production delays and increased costs, severely impacting businesses that rely on timely deliveries for their operations.
The Solution:
To navigate these challenges, buyers should develop a multi-supplier strategy. Engaging with multiple lithium ion battery manufacturers across different regions can mitigate risks associated with supply chain disruptions. Additionally, implementing a thorough vetting process is crucial. This involves assessing potential suppliers based on their production capabilities, quality certifications (such as ISO 9001), and financial stability. Establishing long-term partnerships with manufacturers who have a proven track record can also enhance reliability. Finally, leveraging data analytics to monitor market trends and anticipate potential disruptions will allow buyers to make informed decisions and adjust their sourcing strategies accordingly.
Scenario 2: Ensuring Compliance with Regional Regulations for Battery Manufacturing
The Problem:
B2B buyers often grapple with the complexity of compliance when procuring lithium ion batteries. Different regions, particularly in Africa, South America, the Middle East, and Europe, have varying regulations regarding battery safety, recycling, and environmental impact. Navigating these legal frameworks can be daunting, leading to potential fines, product recalls, or damage to brand reputation if compliance is overlooked.
The Solution:
To address compliance challenges, buyers should invest in understanding the regulatory landscape of their target markets. This can be achieved by collaborating with legal experts or compliance consultants who specialize in battery regulations. Furthermore, buyers should prioritize sourcing from manufacturers who are transparent about their compliance processes and have certifications relevant to their region. Establishing a compliance checklist that includes key regulations such as the European Union’s Battery Directive or local environmental laws will help in maintaining adherence. Regular audits of suppliers can also ensure ongoing compliance, reducing the risk of legal issues down the line.
Scenario 3: Managing Performance Expectations and Technical Specifications
The Problem:
A common pain point for B2B buyers is the misalignment of performance expectations with the technical specifications of lithium ion batteries. This can lead to underperformance in applications such as electric vehicles or renewable energy storage systems, resulting in customer dissatisfaction and financial losses. The challenge lies in accurately assessing the specifications needed for specific applications and ensuring manufacturers can meet these requirements consistently.
The Solution:
To effectively manage performance expectations, buyers should engage in detailed discussions with manufacturers about their specific applications and performance criteria. Utilizing simulation software to model battery performance in real-world scenarios can provide valuable insights into how different batteries will perform under varying conditions. Additionally, requesting prototype samples for testing before full-scale orders can help validate performance claims. Establishing clear metrics for battery performance—such as cycle life, energy density, and charge/discharge rates—will enable buyers to make informed decisions and select the most suitable batteries for their needs. Regular communication with manufacturers during the production process can also help address any discrepancies and ensure that the final products meet the expected standards.
Strategic Material Selection Guide for lithium ion batterie manufacturer
What Are the Key Materials Used in Lithium-Ion Battery Manufacturing?
When selecting materials for lithium-ion batteries, manufacturers must consider various factors that affect performance, cost, and compliance with international standards. Below are analyses of four common materials used in lithium-ion battery production, focusing on their properties, advantages, disadvantages, and considerations for international buyers.
What Are the Key Properties of Lithium Cobalt Oxide (LCO)?
Lithium Cobalt Oxide (LCO) is widely used in consumer electronics due to its high energy density. It typically operates effectively at temperatures ranging from -20°C to 60°C and offers excellent thermal stability. However, it is susceptible to corrosion, which may limit its application in harsh environments.
Pros: LCO provides high capacity and energy density, making it suitable for devices requiring long battery life, such as smartphones and laptops.
Cons: The material is relatively expensive and can lead to thermal runaway if not managed properly. Additionally, its manufacturing process is complex, requiring stringent quality control.
Impact on Application: LCO is well-suited for applications where space and weight are critical, but its susceptibility to overheating necessitates careful thermal management.
Considerations for International Buyers: Buyers in Africa, South America, the Middle East, and Europe should ensure compliance with local safety standards and regulations, such as ASTM and IEC standards, particularly regarding thermal stability and safety.
How Does Lithium Iron Phosphate (LFP) Compare?
Lithium Iron Phosphate (LFP) is known for its excellent thermal stability and safety features. It operates efficiently within a temperature range of -20°C to 60°C and exhibits good resistance to corrosion.
Pros: LFP offers a longer cycle life and enhanced safety, making it ideal for electric vehicles and stationary energy storage systems.
Cons: While LFP is more affordable than LCO, it has a lower energy density, which may not be suitable for all applications, especially where space is limited.
Impact on Application: LFP’s stability makes it suitable for applications requiring high safety standards, such as electric buses and energy storage systems.
Considerations for International Buyers: Buyers should be aware of local regulations regarding environmental impact and recycling, as LFP is often preferred in regions with stringent sustainability requirements.
What Are the Advantages of Nickel Manganese Cobalt (NMC)?
Nickel Manganese Cobalt (NMC) combines the benefits of its constituent materials to achieve a balance between energy density, cost, and safety. It operates effectively at temperatures between -20°C and 60°C and has good corrosion resistance.
Pros: NMC batteries offer a higher energy density than LFP, making them suitable for electric vehicles and high-performance applications.
Cons: The complexity of the manufacturing process can drive up costs, and sourcing nickel may present supply chain challenges, particularly for international buyers.
Impact on Application: NMC is particularly effective in applications where a balance of performance and safety is required, such as in electric vehicles and grid storage.
Considerations for International Buyers: Compliance with international standards is crucial, especially regarding the sourcing of materials and sustainability practices. Buyers should also consider geopolitical factors affecting nickel supply.
How Does Graphite Function in Lithium-Ion Batteries?
Graphite is commonly used as an anode material in lithium-ion batteries due to its excellent conductivity and stability. It operates well within a temperature range of -20°C to 60°C and is generally resistant to corrosion.
Pros: Graphite is cost-effective and has a well-established supply chain, making it a reliable choice for manufacturers.
Cons: While graphite has good performance, it has limitations in terms of energy density compared to silicon-based alternatives, which are emerging in the market.
Impact on Application: Graphite is suitable for a wide range of applications, including consumer electronics and electric vehicles, due to its reliability and cost-effectiveness.
Considerations for International Buyers: Buyers should ensure that their graphite sources comply with environmental regulations and standards, particularly in regions with strict sustainability practices.
Summary Table of Material Selection for Lithium-Ion Battery Manufacturing
Material | Typical Use Case for lithium ion batterie manufacturer | Key Advantage | Key Disadvantage/Limitation | Relative Cost (Low/Med/High) |
---|---|---|---|---|
Lithium Cobalt Oxide (LCO) | Consumer electronics (smartphones, laptops) | High energy density | Expensive, risk of thermal runaway | High |
Lithium Iron Phosphate (LFP) | Electric vehicles, stationary storage | Excellent thermal stability, safety | Lower energy density | Medium |
Nickel Manganese Cobalt (NMC) | Electric vehicles, high-performance applications | Balanced performance and safety | Complex manufacturing, supply risks | Medium to High |
Graphite | Wide range of applications (electronics, EVs) | Cost-effective, stable supply | Lower energy density than alternatives | Low |
This guide provides crucial insights for international B2B buyers, helping them make informed decisions regarding material selection in lithium-ion battery manufacturing. Understanding the properties, advantages, and limitations of these materials is essential for optimizing performance while adhering to regional compliance and sustainability standards.
In-depth Look: Manufacturing Processes and Quality Assurance for lithium ion batterie manufacturer
What are the Key Stages in the Manufacturing Process of Lithium-Ion Batteries?
Manufacturing lithium-ion batteries involves a meticulous process that ensures high efficiency and reliability. The main stages include:
-
Material Preparation: This stage involves sourcing and preparing the raw materials, including lithium, cobalt, nickel, and graphite. The purity and quality of these materials are crucial, as impurities can significantly affect battery performance. Suppliers should provide certificates of analysis (CoA) to confirm the material quality.
-
Electrode Formation: In this stage, the active materials are mixed with binders and solvents to form slurries. The slurries are then coated onto metal foils, typically aluminum for the cathode and copper for the anode. The coating thickness and uniformity are critical, as they directly impact battery capacity and efficiency.
-
Cell Assembly: Once the electrodes are prepared, they are assembled into cells. This involves stacking or winding the anode, separator, and cathode together. Proper alignment and cleanroom conditions are essential to prevent contamination during this sensitive process.
-
Electrolyte Filling: After assembly, the cells are filled with electrolyte, which facilitates ion transfer. This step must be performed under controlled conditions to avoid moisture ingress, which can lead to battery failure.
-
Finishing Processes: The final stage includes formation cycling, where the battery is charged and discharged to activate the electrodes. This is followed by aging, testing, and packaging. Each of these steps ensures the battery meets performance specifications.
How is Quality Assurance Integrated into Lithium-Ion Battery Manufacturing?
Quality assurance (QA) is integral to the manufacturing process of lithium-ion batteries. International and industry-specific standards guide the QA protocols, ensuring that products meet stringent quality criteria.
Which International Standards Should B2B Buyers Be Aware Of?
-
ISO 9001: This widely recognized standard outlines the requirements for a quality management system (QMS). Manufacturers adhering to ISO 9001 demonstrate their commitment to quality and continuous improvement.
-
CE Marking: For products sold in Europe, CE marking indicates compliance with health, safety, and environmental protection standards. This is crucial for B2B buyers in Europe looking to ensure regulatory compliance.
-
API Standards: For manufacturers involved in the battery supply chain, compliance with American Petroleum Institute (API) standards can be relevant, particularly in sectors intersecting with energy and oil.
What are the Key Quality Control Checkpoints in Lithium-Ion Battery Production?
Quality control (QC) checkpoints are established at various stages of the manufacturing process to ensure compliance with quality standards:
-
Incoming Quality Control (IQC): This initial checkpoint involves inspecting raw materials upon receipt. Suppliers should provide documentation, including CoAs, to verify material specifications.
-
In-Process Quality Control (IPQC): During the manufacturing process, IPQC monitors critical parameters such as coating thickness, temperature, and humidity. These checks help identify issues before they escalate.
-
Final Quality Control (FQC): At the end of the production line, FQC involves comprehensive testing of the finished products. This includes performance testing, capacity checks, and safety assessments.
What Common Testing Methods are Used in Lithium-Ion Battery Quality Assurance?
Several testing methods are employed to verify the quality and performance of lithium-ion batteries:
-
Cycle Life Testing: This assesses how many charge-discharge cycles a battery can undergo before its capacity degrades significantly. It’s crucial for applications requiring longevity.
-
Safety Testing: This includes thermal runaway tests, short-circuit tests, and puncture tests to ensure that the battery can withstand extreme conditions without failure.
-
Capacity Testing: Determines the actual capacity of the battery against its rated capacity, providing insights into its efficiency and usability.
How Can B2B Buyers Verify Supplier Quality Control Practices?
For international B2B buyers, especially from regions like Africa, South America, the Middle East, and Europe, verifying a supplier’s QC practices is critical. Here are actionable steps:
-
Supplier Audits: Conducting regular audits allows buyers to evaluate the manufacturer’s processes and compliance with quality standards. This can be scheduled or surprise audits, depending on the relationship.
-
Quality Reports: Requesting detailed quality reports and documentation, including test results and compliance certificates, can provide insights into the supplier’s QA practices.
-
Third-Party Inspections: Engaging independent third-party inspection services can add an extra layer of verification. These services can perform on-site inspections and provide unbiased assessments of the manufacturer’s practices.
What Nuances Should International Buyers Consider Regarding Quality Control and Certification?
B2B buyers must navigate various nuances when it comes to quality control and certification, particularly in international trade:
-
Regulatory Compliance: Different regions have unique regulatory requirements. For instance, batteries sold in Europe must comply with RoHS (Restriction of Hazardous Substances) directives, while other regions may have different standards.
-
Certification Recognition: Not all certifications are recognized globally. Buyers should ensure that the certifications held by manufacturers are relevant to their market to avoid compliance issues.
-
Cultural and Communication Barriers: Engaging with suppliers from different regions may involve cultural differences and language barriers. Establishing clear communication channels can help in aligning expectations and understanding QC processes.
Conclusion
Understanding the manufacturing processes and quality assurance measures in lithium-ion battery production is vital for B2B buyers seeking reliable suppliers. By focusing on the key stages of manufacturing, relevant international standards, quality checkpoints, testing methods, and verification practices, buyers can make informed decisions that align with their operational needs and regulatory requirements.
Practical Sourcing Guide: A Step-by-Step Checklist for ‘lithium ion batterie manufacturer’
This practical sourcing guide is designed to assist international B2B buyers in navigating the complexities of procuring lithium-ion battery manufacturers. With the increasing demand for sustainable energy solutions, understanding the sourcing process is crucial for making informed decisions that align with your business needs.
Step 1: Define Your Technical Specifications
Clearly outlining your technical requirements is essential before initiating the sourcing process. This includes determining the battery capacity, voltage, size, weight, and intended application (e.g., electric vehicles, consumer electronics). Having precise specifications will enable you to filter potential suppliers effectively and ensure that the products meet your operational needs.
Step 2: Research Market Trends and Suppliers
Conduct thorough market research to identify leading lithium-ion battery manufacturers. Look for trends affecting supply and demand, particularly in regions like Africa and South America, where lithium resources are abundant. Utilize industry reports, online databases, and trade shows to gather insights about potential suppliers, their capabilities, and market reputation.
Step 3: Evaluate Potential Suppliers
Before committing to any supplier, it’s crucial to conduct a comprehensive evaluation. Request detailed company profiles, case studies, and references from previous clients in similar industries. Pay attention to:
– Quality Assurance: Inquire about their quality control processes and any relevant certifications (e.g., ISO 9001).
– Production Capacity: Ensure they can meet your volume requirements without compromising quality.
Step 4: Verify Supplier Certifications and Compliance
Check that your selected suppliers comply with international safety and environmental standards. This is particularly important in regions with stringent regulations, such as Europe. Look for certifications such as CE, UL, and RoHS, which demonstrate adherence to safety and environmental protocols. Non-compliance can lead to legal issues and damage to your business reputation.
Step 5: Request Samples and Conduct Testing
Before finalizing any contracts, request samples of the batteries you intend to purchase. Conduct thorough testing to verify performance metrics against your specifications. This step is crucial to ensure the reliability and efficiency of the products in real-world applications. Testing can include:
– Cycle Life: Assess how many charge/discharge cycles the battery can endure.
– Temperature Performance: Evaluate performance across various temperatures to ensure reliability.
Step 6: Negotiate Terms and Pricing
Once you’ve identified a suitable supplier, it’s time to negotiate terms. Discuss pricing, payment terms, and delivery schedules. Ensure that the negotiated terms align with your budget and operational timelines. Consider including clauses for quality assurance and penalties for delays or non-compliance to protect your interests.
Step 7: Establish Communication and Follow-Up
Establish clear communication channels with your supplier to facilitate ongoing collaboration. Regular follow-ups can help address any potential issues early and ensure that production timelines are met. Consider setting up regular review meetings to discuss performance, quality, and any changes in market conditions that might affect your supply chain.
By following these steps, B2B buyers can make informed decisions when sourcing lithium-ion battery manufacturers, ensuring they partner with reliable suppliers that meet their specific needs.
Comprehensive Cost and Pricing Analysis for lithium ion batterie manufacturer Sourcing
What Are the Key Cost Components in Lithium-Ion Battery Manufacturing?
When sourcing lithium-ion batteries, understanding the cost structure is critical for international B2B buyers. The primary components include:
-
Materials: The cost of raw materials such as lithium, cobalt, nickel, and graphite significantly impacts overall pricing. Prices for these materials can fluctuate based on global demand and geopolitical factors, particularly in regions like Latin America, which is a key lithium producer.
-
Labor: Labor costs vary by region, impacting manufacturing expenses. In countries with lower labor costs, such as some South American nations, manufacturers might offer more competitive pricing. However, higher labor costs in Europe or the Middle East could translate into higher product prices.
-
Manufacturing Overhead: This encompasses costs related to factory operation, utilities, and maintenance. Efficient manufacturing processes can help mitigate these costs. Buyers should inquire about the production scale, as larger operations often benefit from economies of scale.
-
Tooling: Investments in specialized equipment for battery production can be substantial. The cost of tooling can be amortized over larger production runs, making it essential for buyers to consider minimum order quantities (MOQs) when negotiating.
-
Quality Control (QC): Ensuring that batteries meet industry standards requires robust QC processes. The associated costs can vary depending on the certification requirements and the complexity of the battery specifications.
-
Logistics: Transportation and warehousing costs can significantly influence the final price. For international buyers, understanding Incoterms (International Commercial Terms) is crucial as they define responsibilities for shipping, insurance, and tariffs.
-
Margin: Manufacturers typically apply a margin on top of their costs to ensure profitability. This margin can vary based on market conditions, competition, and the perceived value of the product.
How Do Price Influencers Affect Lithium-Ion Battery Sourcing?
Several factors can influence the pricing of lithium-ion batteries:
-
Volume/MOQ: Larger orders often lead to better pricing. Suppliers may have tiered pricing structures that offer discounts at higher volumes, making it essential for buyers to evaluate their demand forecasts accurately.
-
Specifications and Customization: Custom designs or specific performance characteristics can increase costs. Buyers should clearly define their needs to avoid unexpected charges later in the sourcing process.
-
Material Quality and Certifications: Higher quality materials and certifications (like ISO or CE marking) can drive up prices. Buyers must assess the necessity of these certifications based on their target markets and applications.
-
Supplier Factors: The relationship with suppliers can also affect pricing. Long-term partnerships may yield better rates due to established trust and reliability.
-
Incoterms: Understanding delivery terms can help buyers manage costs effectively. Choosing the right Incoterm can mitigate risks associated with shipping delays or unexpected fees.
What Are the Best Practices for Negotiating Lithium-Ion Battery Prices?
-
Research and Compare: Conduct thorough market research to understand pricing trends and competitors. This knowledge can empower buyers during negotiations.
-
Focus on Total Cost of Ownership (TCO): Consider all costs associated with the battery, including installation, maintenance, and potential downtime. A slightly higher upfront cost might be justified by lower TCO.
-
Negotiate Terms: Engage in discussions about payment terms, delivery schedules, and after-sales support. Flexible terms can lead to better overall pricing.
-
Consider Long-Term Contracts: Committing to long-term agreements can secure better pricing and supply stability, especially in volatile markets.
-
Be Open to Alternative Suppliers: Expanding the search to include suppliers from various regions, such as Africa or South America, can uncover more competitive pricing options.
What Should International Buyers Be Aware Of When Sourcing Lithium-Ion Batteries?
For buyers in regions like Africa, South America, the Middle East, and Europe, it is essential to understand the specific market dynamics and regulatory environments. Local tariffs, import regulations, and environmental standards can affect the overall cost and feasibility of sourcing batteries.
Additionally, it is advisable to work with suppliers who have a proven track record in international trade to mitigate risks associated with cross-border transactions.
Disclaimer on Pricing
Prices for lithium-ion batteries can vary widely based on market conditions, supplier negotiations, and specific project requirements. Buyers are encouraged to request quotes from multiple suppliers and conduct due diligence to ensure they are making informed purchasing decisions.
Alternatives Analysis: Comparing lithium ion batterie manufacturer With Other Solutions
When considering energy storage solutions, it’s essential to evaluate various options available in the market. While lithium-ion batteries have become the industry standard due to their widespread use in electric vehicles and renewable energy systems, other alternatives may offer unique advantages depending on specific applications and requirements. This analysis will compare lithium-ion battery manufacturers with two viable alternatives: solid-state batteries and flow batteries.
Comparison Table of Lithium-Ion Batteries and Alternatives
Comparison Aspect | Lithium-Ion Batterie Manufacturer | Solid-State Batteries | Flow Batteries |
---|---|---|---|
Performance | High energy density, fast charging | Higher energy density, improved safety | Moderate energy density, scalable |
Cost | Moderate to high | High initial costs | Lower initial costs, variable operational costs |
Ease of Implementation | Established technology, easy integration | Complex manufacturing, longer development | Simple design, modular setup |
Maintenance | Requires regular monitoring | Low maintenance | Requires periodic electrolyte replacement |
Best Use Case | Consumer electronics, EVs | Next-gen electronics, high-end EVs | Renewable energy storage, grid applications |
What Are Solid-State Batteries and Their Advantages?
Solid-state batteries use a solid electrolyte instead of a liquid one, which allows for increased energy density and safety. Their performance is typically superior to that of lithium-ion batteries, especially in high-temperature environments. However, the manufacturing process is complex and currently results in higher production costs. As the technology matures, solid-state batteries could become the go-to solution for applications requiring enhanced safety and performance, such as electric vehicles and portable electronics.
Pros:
– Higher energy density, allowing for longer usage times.
– Enhanced safety with reduced risk of fire or leakage.
Cons:
– Higher initial costs may deter early adoption.
– Manufacturing processes are still being optimized, leading to limited availability.
How Do Flow Batteries Compare in Energy Storage Solutions?
Flow batteries represent a different approach to energy storage, utilizing liquid electrolytes stored in external tanks. This design allows for scalability and longer discharge times, making them ideal for large-scale applications, such as grid storage and renewable energy integration. While flow batteries have a lower energy density than lithium-ion batteries, their ability to scale and relatively lower initial investment make them an attractive option for businesses looking to invest in sustainable energy solutions.
Pros:
– Scalable design suitable for large energy storage needs.
– Lower initial investment compared to lithium-ion systems.
Cons:
– Lower energy density results in larger physical footprint.
– Requires periodic maintenance and electrolyte replacement.
How Should B2B Buyers Choose the Right Energy Storage Solution?
When selecting an energy storage solution, B2B buyers should carefully evaluate their specific needs, including budget, application requirements, and scalability. For applications requiring quick charging and high energy density, lithium-ion batteries remain a strong choice. Conversely, if safety and long-term storage are priorities, solid-state batteries may be the future solution worth the investment. For large-scale energy storage, especially in renewable energy systems, flow batteries offer flexibility and lower costs. Ultimately, understanding the unique benefits and limitations of each technology is crucial for making an informed decision that aligns with business objectives.
Essential Technical Properties and Trade Terminology for lithium ion batterie manufacturer
What Are the Essential Technical Properties of Lithium-Ion Batteries?
When sourcing lithium-ion batteries, understanding their technical specifications is crucial for international B2B buyers. Here are some key properties that significantly impact performance, reliability, and overall application.
1. Material Grade
The material grade refers to the quality and composition of the materials used in the battery, such as lithium, cobalt, and nickel. High-grade materials ensure better energy density, longer life cycles, and improved safety. For manufacturers, selecting the right material grade can lead to enhanced battery performance, which is a critical factor for end-users in sectors like electric vehicles (EVs) and renewable energy storage.
2. Energy Density
Energy density indicates the amount of energy a battery can store relative to its weight or volume. Measured in watt-hours per kilogram (Wh/kg), higher energy density translates to longer usage times and reduced weight, making it essential for applications in portable electronics and EVs. B2B buyers should prioritize batteries with higher energy densities to meet market demands for efficiency and performance.
3. Cycle Life
Cycle life refers to the number of complete charge and discharge cycles a battery can undergo before its capacity significantly diminishes. A longer cycle life reduces the frequency of replacements, leading to lower operational costs. This property is particularly important for industries that rely on consistent energy output, such as renewable energy systems and automotive applications.
4. Operating Temperature Range
The operating temperature range defines the environmental conditions under which a battery can function effectively. Lithium-ion batteries typically operate best within a specific range, often between -20°C to 60°C. Understanding this property is vital for B2B buyers, as extreme temperatures can affect performance and safety, particularly in regions with harsh climates.
5. Internal Resistance
Internal resistance affects the efficiency and thermal performance of a battery. Lower internal resistance leads to reduced energy loss during operation, resulting in better performance and longer life. For manufacturers, minimizing internal resistance is crucial for applications requiring rapid charging and high discharge rates, such as in high-performance vehicles.
What Trade Terms Should B2B Buyers Know in the Lithium-Ion Battery Industry?
Navigating the lithium-ion battery market involves familiarizing oneself with specific trade terminology that can influence procurement decisions. Here are some common terms that B2B buyers should understand:
1. OEM (Original Equipment Manufacturer)
An OEM is a company that produces parts or equipment that may be marketed by another manufacturer. In the context of lithium-ion batteries, an OEM may design and manufacture batteries that are used in various applications, such as automotive or consumer electronics. Understanding OEM relationships can help buyers ensure product compatibility and quality.
2. MOQ (Minimum Order Quantity)
MOQ refers to the smallest quantity of a product that a supplier is willing to sell. This term is particularly important for B2B buyers looking to manage inventory costs and production schedules. Knowing the MOQ can aid in negotiating better terms with suppliers and ensuring adequate supply without overcommitting.
3. RFQ (Request for Quotation)
An RFQ is a document that a buyer sends to suppliers to solicit price quotes for specific products. In the lithium-ion battery industry, issuing an RFQ allows buyers to compare pricing, specifications, and delivery timelines from different manufacturers. This process is essential for making informed purchasing decisions.
4. Incoterms (International Commercial Terms)
Incoterms are a set of international rules that define the responsibilities of buyers and sellers in international transactions. They clarify aspects such as delivery points, risk transfer, and costs. Familiarity with Incoterms is crucial for B2B buyers to avoid misunderstandings and ensure smooth logistics in battery procurement.
5. LFP (Lithium Iron Phosphate)
LFP is a type of lithium-ion battery chemistry known for its safety, thermal stability, and long cycle life. Understanding the various battery chemistries, including LFP, can help B2B buyers select the most appropriate battery type for their specific applications, particularly in industries prioritizing safety and longevity.
By grasping these technical properties and trade terms, international B2B buyers can make more informed decisions when sourcing lithium-ion batteries, ensuring they meet their operational needs while optimizing cost-efficiency.
Navigating Market Dynamics and Sourcing Trends in the lithium ion batterie manufacturer Sector
What Are the Key Market Trends Affecting Lithium Ion Battery Manufacturers?
The lithium-ion battery market is experiencing rapid growth, driven primarily by the global transition to renewable energy and electric vehicles (EVs). Regions such as Africa, South America, the Middle East, and Europe are witnessing increased demand for lithium-ion batteries as they adopt more sustainable energy solutions. In particular, countries in South America, notably Chile and Argentina, are pivotal due to their rich lithium reserves, which are essential for battery production.
Emerging B2B technologies, such as advanced manufacturing processes and automation, are reshaping how lithium-ion batteries are produced. Manufacturers are increasingly leveraging data analytics and IoT solutions to optimize supply chains and enhance production efficiency. This shift towards digitalization allows manufacturers to respond rapidly to market demands and mitigate potential disruptions in sourcing materials.
For international buyers, understanding regional market dynamics is crucial. The geopolitical landscape can significantly impact supply chains, making it essential to establish reliable partnerships with manufacturers who prioritize resilience and flexibility. Furthermore, as European regulations tighten around carbon emissions, European buyers are particularly focused on sourcing from manufacturers who can demonstrate compliance with sustainability standards.
How Can B2B Buyers Ensure Sustainability and Ethical Sourcing in Lithium Ion Battery Manufacturing?
Sustainability is a critical consideration for B2B buyers in the lithium-ion battery sector. The environmental impact of lithium extraction and battery production is substantial, prompting a shift towards more responsible sourcing practices. Buyers should prioritize manufacturers who implement sustainable mining practices and utilize recycled materials in their production processes.
Ethical sourcing is paramount, as many lithium mines are located in regions where labor practices can be questionable. Buyers should seek suppliers that are certified by recognized standards, such as the Responsible Minerals Initiative (RMI) or the International Council on Mining and Metals (ICMM), which ensure ethical labor practices and environmental stewardship.
Additionally, buyers should look for manufacturers that provide transparency in their supply chains. Certifications such as ISO 14001 for environmental management can indicate a commitment to minimizing ecological impact. Engaging with suppliers who are proactive about sustainability not only supports ethical practices but also enhances brand reputation and meets the growing consumer demand for environmentally friendly products.
What Is the Evolution of the Lithium-Ion Battery Sector Relevant for B2B Buyers?
The lithium-ion battery sector has evolved significantly since its commercial introduction in the 1990s. Initially limited to consumer electronics, advancements in technology and increasing energy demands have expanded their applications to electric vehicles and renewable energy storage.
The rise of electric vehicles in recent years has been a game-changer, prompting major investments in battery technology and manufacturing capabilities. This evolution has also led to a surge in competition among manufacturers, resulting in innovations that improve battery efficiency, reduce costs, and minimize environmental impact. For B2B buyers, understanding this historical context is crucial, as it highlights the importance of partnering with forward-thinking manufacturers who are equipped to meet future demands and sustainability goals.
In summary, navigating the complexities of the lithium-ion battery market requires a strategic approach that considers market dynamics, sustainability, and the historical evolution of the sector. By aligning with ethical manufacturers and leveraging technological advancements, international B2B buyers can secure a competitive edge in this rapidly changing landscape.
Frequently Asked Questions (FAQs) for B2B Buyers of lithium ion batterie manufacturer
-
How do I ensure quality when sourcing lithium-ion batteries from manufacturers?
To ensure quality, start by verifying the manufacturer’s certifications, such as ISO 9001 for quality management systems. Request samples and conduct thorough testing to assess performance, durability, and safety features. It’s also advisable to visit the manufacturing facility if possible, or use third-party inspection services to evaluate production processes. Establish clear quality assurance protocols in your contracts, including warranties and compliance with international safety standards. -
What are the key factors to consider when choosing a lithium-ion battery manufacturer?
When selecting a manufacturer, consider their production capacity, technological expertise, and track record in the industry. Evaluate their supply chain reliability and the availability of raw materials, particularly lithium, which is critical for battery production. Additionally, assess their ability to offer customization options that meet your specific needs, such as battery size, capacity, and energy density. Finally, review customer testimonials and case studies to gauge their reputation and service quality. -
What are the minimum order quantities (MOQ) for lithium-ion batteries?
Minimum order quantities can vary significantly between manufacturers, typically ranging from a few hundred to several thousand units. Factors influencing MOQ include the complexity of the battery design, production capabilities, and material costs. When negotiating with suppliers, be clear about your volume needs and explore flexibility in order sizes, especially if you are a smaller buyer. Some manufacturers may offer lower MOQs for custom orders as a way to establish a business relationship.
-
What payment terms should I expect when dealing with lithium-ion battery manufacturers?
Payment terms can differ widely among manufacturers. Common practices include a deposit (usually 30-50%) upon order confirmation, with the balance due before shipping or upon delivery. Some manufacturers may offer credit terms depending on your relationship and order history. It’s essential to discuss payment methods that work for both parties, including bank transfers, letters of credit, or escrow services, to mitigate risks associated with international transactions. -
How can I customize lithium-ion batteries to fit my specific needs?
Customization options often include variations in voltage, capacity, size, and form factor. Start by discussing your requirements with potential manufacturers, focusing on the application of the batteries and performance criteria. Many manufacturers have engineering teams that can assist in designing solutions tailored to your specifications. Be prepared to share detailed information about your intended use, including environmental conditions and energy demands, to facilitate effective customization. -
What logistics considerations should I be aware of when importing lithium-ion batteries?
When importing lithium-ion batteries, consider the specific regulations and shipping requirements due to their classification as hazardous materials. Research the transportation regulations in both the exporting and importing countries, including packaging, labeling, and documentation. Work with logistics providers experienced in handling such products to ensure compliance with safety standards. Additionally, factor in lead times, customs clearance processes, and potential tariffs that may affect overall costs. -
What certifications should lithium-ion battery manufacturers have?
Look for manufacturers with certifications that demonstrate compliance with international safety and quality standards. Key certifications include ISO 9001 for quality management, UL 2054 for safety, and UN 38.3 for transportation safety. Depending on your market, additional certifications like CE for Europe or RoHS for environmental compliance may be necessary. These certifications not only indicate the manufacturer’s commitment to quality but also ensure that the batteries meet regulatory requirements in your region. -
How do I effectively vet potential lithium-ion battery suppliers?
To vet suppliers, start with thorough online research to review their company profiles, product offerings, and customer feedback. Request references from other clients and inquire about their experience with the supplier regarding product quality and service. Perform background checks to assess the financial stability and manufacturing capabilities of the supplier. Lastly, consider conducting on-site audits or using third-party verification services to ensure the supplier meets your standards before entering into a contract.
Important Disclaimer & Terms of Use
⚠️ Important Disclaimer
The information provided in this guide, including content regarding manufacturers, technical specifications, and market analysis, is for informational and educational purposes only. It does not constitute professional procurement advice, financial advice, or legal advice.
While we have made every effort to ensure the accuracy and timeliness of the information, we are not responsible for any errors, omissions, or outdated information. Market conditions, company details, and technical standards are subject to change.
B2B buyers must conduct their own independent and thorough due diligence before making any purchasing decisions. This includes contacting suppliers directly, verifying certifications, requesting samples, and seeking professional consultation. The risk of relying on any information in this guide is borne solely by the reader.
Strategic Sourcing Conclusion and Outlook for lithium ion batterie manufacturer
As the demand for lithium-ion batteries continues to surge, strategic sourcing has become essential for international B2B buyers looking to optimize their supply chains. By focusing on regions rich in lithium reserves—such as Latin America, Africa, and parts of Europe—businesses can secure a reliable supply of materials necessary for battery production. Moreover, engaging with manufacturers who prioritize sustainable practices not only enhances brand reputation but also aligns with the global push for greener technologies.
How can international buyers effectively navigate the lithium supply chain? Establishing strong partnerships with local suppliers and manufacturers can facilitate smoother transactions and mitigate risks associated with geopolitical uncertainties. Additionally, leveraging data analytics to assess market trends and pricing fluctuations will empower buyers to make informed decisions.
Looking ahead, the lithium-ion battery market is poised for significant growth, driven by the increasing adoption of electric vehicles and renewable energy solutions. International B2B buyers are encouraged to stay proactive in their sourcing strategies, ensuring they align with the evolving landscape. By investing in strategic sourcing today, businesses can position themselves as leaders in a sustainable energy future.