Discover Top Benefits of a Prototyping Manufacturer (2025)
Introduction: Navigating the Global Market for prototyping manufacturer
In today’s competitive landscape, sourcing a reliable prototyping manufacturer can be a daunting challenge for international B2B buyers, particularly those operating in diverse markets such as Africa, South America, the Middle East, and Europe. The need for quick, efficient, and cost-effective prototypes is paramount to drive innovation and reduce time-to-market for new products. This guide is designed to empower decision-makers by offering a comprehensive overview of the prototyping manufacturing sector, including various types of prototypes, their applications across industries, and key considerations for supplier vetting.
Understanding the nuances of prototyping—from low-fidelity paper models to high-fidelity 3D prints—allows buyers to align their specific needs with the right manufacturing capabilities. Additionally, we delve into critical factors such as cost implications, lead times, and the importance of clear communication in the prototyping process. By equipping international buyers with actionable insights and practical strategies, this guide aims to facilitate informed purchasing decisions, ultimately enhancing product development outcomes.
Whether you’re a startup in Turkey looking to validate your product concept or a seasoned manufacturer in France seeking to refine your existing offerings, navigating the global market for prototyping manufacturers has never been more crucial. This guide will help you make strategic choices that lead to successful collaborations and innovative product launches.
Understanding prototyping manufacturer Types and Variations
Type Name | Key Distinguishing Features | Primary B2B Applications | Brief Pros & Cons for Buyers |
---|---|---|---|
Low-Fidelity Prototyping | Simple, often paper-based models; quick to create | Initial concept testing, UX research | Pros: Cost-effective, rapid iteration. Cons: Limited realism, may not convey complex interactions. |
High-Fidelity Prototyping | Detailed, functional models; closer to final product | Product validation, user testing | Pros: Accurate representation, useful for stakeholder feedback. Cons: Higher cost, longer production time. |
3D Printing Prototyping | Utilizes additive manufacturing; allows complex designs | Product development, engineering | Pros: Fast production, complex geometries possible. Cons: Material limitations, potential for high costs. |
CNC Machining Prototyping | Uses computer-controlled cutting tools; precise | Mechanical parts, industrial design | Pros: High precision, suitable for functional testing. Cons: Setup costs, longer lead times for small batches. |
Injection Molding Prototyping | Creates parts using molds; ideal for mass production | Consumer products, automotive parts | Pros: Cost-effective for large volumes, high durability. Cons: High initial investment, longer lead times. |
What Are the Key Characteristics of Low-Fidelity Prototyping?
Low-fidelity prototyping involves creating simple, often paper-based models that allow for rapid iteration and concept testing. These prototypes are typically inexpensive and quick to produce, making them ideal for early-stage development and initial user feedback. For B2B buyers, this type is suitable when exploring ideas or validating concepts without significant investment. However, it may not accurately represent complex interactions or functionalities, which can be a drawback when presenting to stakeholders.
How Does High-Fidelity Prototyping Differ from Low-Fidelity?
High-fidelity prototyping provides a more detailed and functional representation of the final product. This type often incorporates advanced materials and technology to simulate the user experience more accurately, making it suitable for product validation and user testing. B2B buyers should consider high-fidelity prototypes when they need precise feedback from stakeholders or potential users. While they offer a realistic view of the product, they come with higher costs and longer production times compared to low-fidelity options.
Why Choose 3D Printing Prototyping for Your Projects?
3D printing prototyping leverages additive manufacturing techniques to create complex designs that may be challenging with traditional methods. This approach is particularly beneficial for industries like product development and engineering, where rapid prototyping is essential. Buyers should consider 3D printing for its speed and ability to produce intricate geometries. However, potential limitations in material choices and costs can impact the overall feasibility for large-scale production.
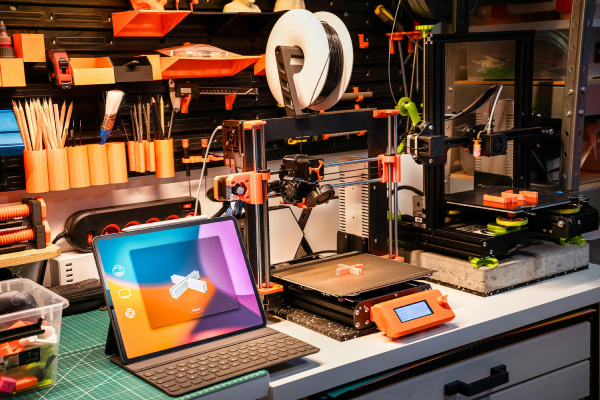
A stock image related to prototyping manufacturer.
What Are the Advantages of CNC Machining Prototyping?
CNC machining prototyping employs computer-controlled cutting tools to produce precise components. This method is highly suitable for mechanical parts and industrial design, offering B2B buyers high accuracy and the ability to test functional prototypes. While CNC machining can provide exceptional precision, buyers should be aware of the setup costs and longer lead times, particularly for small production runs, which may affect project timelines.
When Is Injection Molding Prototyping the Right Choice?
Injection molding prototyping is particularly advantageous for creating parts intended for mass production. This method allows for the rapid production of durable components, making it an excellent choice for consumer products and automotive parts. B2B buyers should consider injection molding when they anticipate high-volume production, as it can be cost-effective in the long run. However, the initial investment in molds can be significant, and the lead times for production can be longer, which may not suit every project timeline.
Related Video: Rapid Prototyping Services at PCBWay | PCB fabrication & Assembly | 3D printing and CNC machining
Key Industrial Applications of prototyping manufacturer
Industry/Sector | Specific Application of Prototyping Manufacturer | Value/Benefit for the Business | Key Sourcing Considerations for this Application |
---|---|---|---|
Automotive | Development of vehicle components and systems | Reduces time-to-market and minimizes costly design errors | Supplier reliability, material quality, and compliance with safety standards |
Consumer Electronics | Creation of product mock-ups for user testing | Enhances user experience and allows for iterative feedback | Prototyping speed, technology compatibility, and design flexibility |
Medical Devices | Prototyping for surgical instruments and implants | Ensures functionality and patient safety before mass production | Regulatory compliance, precision manufacturing, and material biocompatibility |
Aerospace | Testing of aircraft components and systems | Improves safety and performance through early detection of design flaws | Material strength, weight considerations, and adherence to aviation standards |
Industrial Equipment | Prototyping for machinery and tools | Increases efficiency and reduces operational downtime | Production scalability, customization options, and support for maintenance and repairs |
How is Prototyping Manufacturer Used in the Automotive Sector?
In the automotive industry, prototyping manufacturers play a crucial role in developing vehicle components and systems. By creating prototypes, automotive companies can identify design flaws early in the process, significantly reducing time-to-market and minimizing costly design errors. International buyers must consider supplier reliability, material quality, and compliance with safety standards to ensure that their prototypes meet both regulatory requirements and performance expectations.
What are the Applications in Consumer Electronics?
Prototyping manufacturers are essential in the consumer electronics sector for creating product mock-ups that facilitate user testing. This iterative process allows companies to enhance user experience by gathering feedback on functionality and design before mass production. Buyers from regions like Africa and South America should prioritize prototyping speed, technology compatibility, and design flexibility to adapt to rapidly changing market demands.
How is Prototyping Beneficial for Medical Devices?
In the medical device industry, prototyping is vital for the development of surgical instruments and implants. This approach ensures that products are functional and safe for patient use before they enter mass production. International B2B buyers must focus on regulatory compliance, precision manufacturing, and material biocompatibility to meet stringent healthcare standards and patient safety requirements.
What Role Does Prototyping Play in Aerospace?
The aerospace sector relies heavily on prototyping manufacturers for testing aircraft components and systems. Prototyping allows engineers to improve safety and performance by detecting design flaws early in the development cycle. Buyers in this industry should consider material strength, weight considerations, and adherence to aviation standards when sourcing prototypes to ensure that they meet the rigorous demands of aerospace engineering.
How is Prototyping Used in Industrial Equipment?
In the industrial equipment sector, prototyping is used to develop machinery and tools that enhance operational efficiency. By testing prototypes, companies can identify potential issues and optimize designs, ultimately reducing operational downtime. Buyers should look for manufacturers that offer production scalability, customization options, and robust support for maintenance and repairs to ensure that their equipment meets specific operational needs.
3 Common User Pain Points for ‘prototyping manufacturer’ & Their Solutions
Scenario 1: Difficulty in Communicating Design Intentions
The Problem:
B2B buyers often struggle to convey their design intentions clearly to prototyping manufacturers, leading to misunderstandings and misaligned expectations. For instance, a company in South America may have a complex product design idea but lacks the technical vocabulary or visual aids to express their vision effectively. As a result, the prototypes produced may not reflect the buyer’s needs, causing frustration, wasted resources, and extended timelines.
The Solution:
To overcome this communication barrier, buyers should invest time in creating detailed design specifications and visual mock-ups before engaging with a prototyping manufacturer. Utilizing tools like CAD software can help create precise 3D models, which serve as a common reference point for both parties. Additionally, organizing a preliminary meeting to discuss the project in-depth can help clarify expectations. Prototyping manufacturers that offer collaborative platforms for real-time feedback and iterations can significantly enhance communication. This proactive approach ensures that the prototypes align closely with the buyer’s vision, reducing the likelihood of costly revisions.
Scenario 2: Prototyping Costs Escalating Rapidly
The Problem:
Many businesses, particularly in Europe, face the challenge of rapidly escalating costs associated with prototyping. As they iterate on designs, the expenses for materials and labor can quickly add up, straining budgets and timelines. For instance, a tech startup in France may find that after several rounds of revisions, their initial budget for prototyping has tripled due to unforeseen complexities and changes in the design.
The Solution:
To mitigate cost overruns, buyers should adopt a structured prototyping approach that emphasizes low-fidelity prototypes in the early stages. Utilizing inexpensive materials like foam or 3D-printed elements can allow for quick iterations without significant financial risk. Moreover, engaging with a prototyping manufacturer that offers flexible pricing models or bulk discounts can provide financial relief. Setting clear milestones and budget caps within the prototyping agreement can also help monitor expenses closely, ensuring that the project remains on track financially.
Scenario 3: Insufficient Feedback Loops During Prototyping
The Problem:
Another common pain point for B2B buyers is the lack of sufficient feedback loops during the prototyping phase. For example, a manufacturing firm in Africa may develop a prototype without adequate testing or user feedback, leading to a final product that does not meet market needs or user expectations. This oversight often results in additional rounds of prototyping, which can delay product launches and increase costs.
The Solution:
To establish effective feedback loops, it is essential for buyers to incorporate user testing at various stages of the prototyping process. Engaging potential users early on to gather insights can provide valuable information that informs design adjustments. Utilizing methods such as A/B testing with different prototype variations can help identify which features resonate most with users. Additionally, partnering with a prototyping manufacturer that has experience in user-centered design methodologies can enhance the feedback process. They can facilitate user testing sessions and gather data that can be used to refine the prototypes efficiently, ensuring that the final product is well-aligned with market demands.
Strategic Material Selection Guide for prototyping manufacturer
When selecting materials for prototyping, it is crucial for international B2B buyers to consider various factors that can impact the performance, cost, and suitability of the prototypes for their specific applications. Below, we analyze four common materials used in prototyping, focusing on their properties, advantages, disadvantages, and considerations for buyers from diverse regions, including Africa, South America, the Middle East, and Europe.
What Are the Key Properties of PLA (Polylactic Acid) in Prototyping?
PLA is a biodegradable thermoplastic derived from renewable resources like corn starch or sugarcane. It is known for its ease of use and excellent print quality.
- Key Properties: PLA has a low melting point (around 180-220°C) and is not suitable for high-temperature applications. It has good rigidity and is resistant to UV light.
- Pros & Cons: PLA is relatively inexpensive and easy to print, making it ideal for rapid prototyping. However, it is less durable than other materials and can warp under high heat or moisture.
- Impact on Application: PLA is compatible with various media but is not suitable for applications requiring high strength or heat resistance.
- Considerations for International Buyers: Buyers should ensure compliance with local environmental regulations, as PLA is biodegradable. Standards such as ASTM D6400 for compostability may also be relevant.
How Does ABS (Acrylonitrile Butadiene Styrene) Perform in Prototyping?
ABS is a widely used thermoplastic known for its toughness and impact resistance, making it a popular choice for functional prototypes.
- Key Properties: ABS has a higher melting point (around 210-250°C) and excellent durability, with good resistance to chemicals and impact.
- Pros & Cons: The material is strong and suitable for functional testing. However, it can be more challenging to print due to warping and requires a heated bed.
- Impact on Application: ABS is ideal for applications requiring strength and durability, such as automotive parts or consumer products.
- Considerations for International Buyers: Compliance with safety standards like ASTM D256 for impact resistance is essential. Buyers should also consider local regulations regarding emissions during the printing process.
What Are the Benefits of Using Nylon in Prototyping?
Nylon is a versatile material known for its flexibility and strength, making it suitable for a range of applications.
- Key Properties: Nylon has a high melting point (around 220-260°C) and exhibits excellent abrasion resistance and chemical stability.
- Pros & Cons: It is highly durable and suitable for functional prototypes. However, nylon can absorb moisture, which may affect its mechanical properties and printing quality.
- Impact on Application: Nylon is often used in applications requiring wear resistance, such as gears and moving parts.
- Considerations for International Buyers: Buyers should be aware of the need for moisture control in storage and handling. Compliance with standards like ASTM D638 for tensile properties is also important.
Why Is TPU (Thermoplastic Polyurethane) a Good Choice for Prototyping?
TPU is a flexible material known for its elasticity and resilience, making it ideal for prototypes that require flexibility.
- Key Properties: TPU has a moderate melting point (around 200-230°C) and excellent resistance to abrasion, oils, and greases.
- Pros & Cons: Its flexibility allows for the creation of soft prototypes. However, it can be more expensive than other materials and may require specific printing settings.
- Impact on Application: TPU is suitable for applications like phone cases, seals, and other products requiring flexibility.
- Considerations for International Buyers: Buyers should ensure compliance with relevant safety standards and consider the specific printing technology required for TPU.
Summary Table of Material Selection for Prototyping
Material | Typical Use Case for prototyping manufacturer | Key Advantage | Key Disadvantage/Limitation | Relative Cost (Low/Med/High) |
---|---|---|---|---|
PLA | Rapid prototyping, decorative items | Biodegradable and easy to print | Low durability and heat resistance | Low |
ABS | Functional prototypes, automotive parts | Strong and impact-resistant | Warping issues and requires heated bed | Medium |
Nylon | Gears, moving parts | High durability and wear resistance | Moisture absorption affects properties | Medium |
TPU | Flexible products, phone cases | Excellent elasticity and abrasion resistance | Higher cost and specific printing requirements | High |
This strategic material selection guide provides B2B buyers with essential insights into the properties, advantages, and limitations of various prototyping materials. Understanding these factors can help buyers make informed decisions that align with their specific needs and compliance requirements in their respective regions.
In-depth Look: Manufacturing Processes and Quality Assurance for prototyping manufacturer
What Are the Main Stages of Manufacturing Processes for Prototyping?
When engaging with a prototyping manufacturer, understanding the manufacturing processes is crucial for B2B buyers. The typical stages involved include material preparation, forming, assembly, and finishing. Each of these stages plays a pivotal role in ensuring that the final prototype meets the desired specifications and quality standards.
How Is Material Prepared in Prototyping Manufacturing?
Material preparation is the first step, where raw materials are selected based on the specifications of the prototype. This may involve sourcing metals, plastics, or composites that align with the intended use of the product. The preparation process can include cutting, machining, or even 3D printing depending on the complexity and requirements of the prototype.
B2B buyers should ensure that their suppliers adhere to strict material standards, as the quality of materials significantly impacts the prototype’s performance. It’s advisable to request material certifications that comply with international standards, such as ASTM or ISO.
What Techniques Are Used in the Forming Stage?
In the forming stage, various techniques are employed to shape the prepared materials into the desired prototype form. Common techniques include:
- CNC Machining: This precision technique allows for the accurate shaping of materials using computer-controlled tools, making it ideal for complex designs.
- 3D Printing: Increasingly popular due to its rapid prototyping capabilities, 3D printing enables manufacturers to create intricate designs quickly and cost-effectively.
- Injection Molding: This is used for producing high volumes of plastic prototypes, where molten plastic is injected into a mold.
Understanding these techniques can help buyers choose the right manufacturing process for their specific needs.
How Are Prototypes Assembled and Finished?
The assembly stage involves piecing together the various components of the prototype. This can include integrating electronic parts, fastening components, or applying adhesives. Quality during assembly is crucial, as this stage often dictates the prototype’s functionality and aesthetics.
Finishing is the final stage, which may involve surface treatments, painting, or coating to enhance durability and visual appeal. B2B buyers should inquire about the finishing options available and the associated costs, as these can vary significantly among manufacturers.
What Are the Quality Assurance Measures in Prototyping Manufacturing?
Quality assurance (QA) is paramount in prototyping to ensure that the end product meets the specified requirements. Key international standards, such as ISO 9001, are often implemented by manufacturers to maintain quality throughout the production process.
Which International Standards Should B2B Buyers Look For?
B2B buyers should be aware of several relevant international standards, including:
- ISO 9001: A standard that specifies requirements for a quality management system (QMS) to enhance customer satisfaction.
- CE Marking: Particularly important for products sold in the European Economic Area, indicating compliance with safety and environmental standards.
- API Standards: Relevant for manufacturers in the oil and gas sector, ensuring quality and reliability in products.
Understanding these standards helps buyers assess the credibility and reliability of a prototyping manufacturer.
What Are the Key Quality Control Checkpoints?
Quality control (QC) involves several checkpoints throughout the manufacturing process to ensure that every prototype meets quality standards. Key checkpoints include:
- Incoming Quality Control (IQC): This initial checkpoint ensures that the materials received meet specified standards before they enter the production process.
- In-Process Quality Control (IPQC): During manufacturing, ongoing checks are performed to monitor and maintain quality throughout the production stages.
- Final Quality Control (FQC): This final checkpoint involves comprehensive testing and inspection of the completed prototype before it is delivered to the client.
B2B buyers should ask manufacturers about their QC processes and how they handle non-conformities.
How Can B2B Buyers Verify Supplier Quality Control?
Verifying the quality control measures of a prototyping manufacturer is essential for ensuring that you receive a product that meets your specifications. Here are some actionable steps buyers can take:
What Should Buyers Request During Supplier Audits?
-
Supplier Audits: Conducting audits allows buyers to assess the manufacturer’s facilities, processes, and compliance with quality standards firsthand. It’s advisable to create a checklist that includes key areas of focus, such as equipment maintenance, employee training, and adherence to QC protocols.
-
Quality Reports: Requesting regular quality reports can provide insights into the manufacturer’s performance over time. These reports should include metrics on defect rates, corrective actions taken, and overall compliance with quality standards.
How Do Third-Party Inspections Work?
Engaging third-party inspection services can further enhance the verification process. These independent entities can provide unbiased evaluations of the manufacturing process, ensuring that it adheres to specified standards and practices. B2B buyers should inquire if their suppliers allow third-party inspections and under what conditions.
What Are the Quality Control Nuances for International B2B Buyers?
International B2B buyers, particularly from regions like Africa, South America, the Middle East, and Europe, should be aware of certain nuances in quality control:
-
Cultural Differences: Understanding cultural attitudes towards quality can affect communication and expectations. Buyers should foster open communication with suppliers to clarify quality expectations.
-
Regulatory Compliance: Different regions have varying regulations regarding product safety and quality. Buyers should ensure that their manufacturers are compliant with both local and international regulations relevant to their industry.
-
Logistics and Supply Chain Considerations: The distance between buyer and manufacturer can impact delivery times and product quality. Buyers should consider logistics in their quality assurance processes and factor in potential delays or disruptions.
By understanding the manufacturing processes and quality assurance measures in prototyping, B2B buyers can make informed decisions, ensuring that they partner with manufacturers that meet their quality standards and project requirements.
Practical Sourcing Guide: A Step-by-Step Checklist for ‘prototyping manufacturer’
The following checklist is designed to assist international B2B buyers, particularly from Africa, South America, the Middle East, and Europe, in sourcing a reliable prototyping manufacturer. Each step is critical in ensuring that the selected manufacturer aligns with your project requirements and business goals.
Step 1: Define Your Technical Specifications
Before reaching out to potential manufacturers, it’s essential to clearly outline your project requirements. This includes the materials, dimensions, functionality, and any specific technologies you wish to incorporate. A well-defined specification will help you communicate your needs effectively and ensure that the manufacturer understands the scope of your project.
- Consider product complexity: Determine if your prototype requires intricate design features or is relatively straightforward.
- Identify industry standards: Familiarize yourself with applicable regulations or standards in your region to ensure compliance.
Step 2: Conduct Market Research for Potential Suppliers
Invest time in researching potential prototyping manufacturers. Look for companies that specialize in your industry and have a proven track record. Utilize online platforms, industry directories, and networking events to gather a list of potential candidates.
- Leverage local resources: Explore manufacturers within your region to reduce shipping costs and time.
- Seek referrals: Engage with industry peers or forums to get recommendations based on firsthand experiences.
Step 3: Evaluate Potential Suppliers
Before committing, it’s crucial to vet suppliers thoroughly. Request company profiles, case studies, and references from buyers in a similar industry or region. Don’t just rely on their website; a comprehensive evaluation will help you gauge their capabilities and reliability.
- Assess past projects: Look for examples of prototypes they have previously developed that align with your specifications.
- Check for relevant experience: Ensure they have experience in your specific market or industry to mitigate risks.
Step 4: Verify Supplier Certifications and Quality Standards
Quality assurance is paramount in prototyping. Ensure that the manufacturer holds relevant certifications, such as ISO 9001, which demonstrates their commitment to quality management systems. This step is crucial for maintaining the integrity of your prototypes.
- Inquire about quality control processes: Understand their testing protocols and how they handle defects or revisions.
- Confirm material sourcing: Ensure that they source materials that meet your quality expectations and compliance requirements.
Step 5: Request Prototypes and Samples
Once you have shortlisted potential suppliers, ask for prototypes or samples of their previous work. This will allow you to assess the quality of their output and determine if it meets your standards before making a larger commitment.
- Evaluate craftsmanship: Pay attention to details such as finish, fit, and functionality.
- Test for performance: If applicable, conduct tests to ensure the prototype meets your intended use.
Step 6: Discuss Pricing and Payment Terms
Before finalizing your choice, clearly discuss pricing structures and payment terms. Understanding the cost implications upfront will help you budget effectively and avoid unexpected expenses later on.
- Inquire about additional costs: Be aware of potential hidden fees for shipping, materials, or revisions.
- Negotiate terms: Discuss payment schedules that align with your financial capabilities and project timeline.
Step 7: Establish Clear Communication Channels
Good communication is vital for a successful partnership. Ensure that the manufacturer is responsive and open to ongoing dialogue throughout the prototyping process. Establishing clear communication channels will help prevent misunderstandings and keep the project on track.
- Set regular check-ins: Schedule updates to discuss progress, challenges, and any necessary adjustments.
- Utilize project management tools: Consider using collaborative platforms to streamline communication and document project details.
Following this checklist will help you make informed decisions when sourcing a prototyping manufacturer, ultimately leading to successful project outcomes.
Comprehensive Cost and Pricing Analysis for prototyping manufacturer Sourcing
What Are the Key Cost Components in Prototyping Manufacturing?
When sourcing a prototyping manufacturer, understanding the cost structure is essential for international B2B buyers. The primary cost components include:
-
Materials: The choice of materials significantly impacts the overall cost. For example, high-quality plastics or metals will increase costs, while standard materials may reduce them.
-
Labor: Labor costs can vary widely depending on the region and skill level required. Countries with lower labor costs may offer more competitive pricing, but this could affect quality.
-
Manufacturing Overhead: This includes costs related to utilities, facility maintenance, and administrative expenses. Efficient manufacturers tend to have lower overhead, which can translate to better pricing for buyers.
-
Tooling: Initial setup costs for tooling can be substantial, especially for complex designs. Understanding these costs upfront is crucial for budgeting.
-
Quality Control (QC): Implementing strict quality control measures adds to costs but is necessary for ensuring product reliability. Buyers should weigh the cost of QC against potential risks of defects.
-
Logistics: Shipping costs can be a significant part of the total cost, especially for international transactions. Factors such as distance, mode of transport, and shipping terms (Incoterms) play a vital role here.
-
Margin: Manufacturers will apply a margin over their costs. Understanding typical margins in the industry can help buyers negotiate better.
How Do Pricing Influencers Affect Prototyping Costs?
Several factors influence the pricing of prototypes, which international buyers should consider:
-
Volume/MOQ (Minimum Order Quantity): Larger orders often result in lower per-unit costs due to economies of scale. Buyers should assess their needs and negotiate terms that align with their volume requirements.
-
Specifications and Customization: Custom designs or specific requirements can increase costs significantly. Buyers should be clear about their specifications and seek quotes from multiple manufacturers.
-
Material Quality and Certifications: Higher quality materials and compliance with industry certifications can increase costs. Buyers must decide on the necessary quality level based on their end-use.
-
Supplier Factors: The reputation and experience of the supplier can affect pricing. Established manufacturers may charge more but often offer better quality and reliability.
-
Incoterms: The chosen Incoterms can impact pricing and logistics costs. Buyers should understand terms like FOB (Free on Board) or CIF (Cost, Insurance, and Freight) to make informed decisions.
What Are the Best Practices for Negotiating Prototyping Costs?
International B2B buyers can employ several strategies to optimize costs when sourcing prototypes:
-
Conduct Thorough Research: Understand the typical pricing structures and market rates for prototyping services in your target region.
-
Negotiate Terms: Engage in discussions about volume discounts, payment terms, and delivery timelines. Be prepared to walk away if the terms are not favorable.
-
Evaluate Total Cost of Ownership (TCO): Consider not just the initial price but the long-term implications, including quality, durability, and potential defects that could lead to higher costs.
-
Leverage Relationships: Building strong relationships with manufacturers can lead to better pricing and priority service.
-
Explore Multiple Suppliers: Don’t settle for the first quote. Comparing multiple manufacturers can provide insights into fair pricing and quality expectations.
What Should International Buyers Keep in Mind Regarding Pricing Nuances?
For buyers from Africa, South America, the Middle East, and Europe, specific nuances can influence prototyping costs:
-
Currency Fluctuations: Be aware of how currency exchange rates may affect pricing, particularly for international transactions.
-
Regulatory Compliance: Ensure that the manufacturer complies with local regulations and standards, as this may impact costs.
-
Cultural Differences: Understanding cultural business practices can facilitate smoother negotiations and foster better relationships.
Disclaimer on Indicative Prices
Pricing in prototyping manufacturing can vary widely based on the above factors. Therefore, the prices mentioned here are indicative and may not reflect actual costs. Buyers should obtain tailored quotes based on their specific project requirements and negotiate terms that align with their budget and quality expectations.
Alternatives Analysis: Comparing prototyping manufacturer With Other Solutions
When evaluating the various options available for product development and design, it’s crucial for international B2B buyers, especially from regions such as Africa, South America, the Middle East, and Europe, to understand the alternatives to traditional prototyping manufacturers. These alternatives can offer different benefits and may be more suitable depending on specific project requirements, budget constraints, and resource availability.
Comparison Aspect | Prototyping Manufacturer | Rapid Prototyping Technologies | DIY Prototyping Methods |
---|---|---|---|
Performance | High-quality, detailed prototypes | Fast turnaround, decent quality | Variable quality, depends on skills |
Cost | Moderate to high | Moderate, depending on materials | Low, primarily materials and tools |
Ease of Implementation | Requires vendor selection and setup | Requires knowledge of technology | High, tools are often accessible |
Maintenance | Limited maintenance; mainly supplier-managed | Some maintenance needed for equipment | Self-maintained; dependent on user |
Best Use Case | Complex products needing precision | Quick iterations for concepts | Simple products or concepts needing validation |
What Are the Benefits of Rapid Prototyping Technologies?
Rapid prototyping technologies, such as 3D printing and CNC machining, are designed to produce prototypes quickly and efficiently. These methods can handle both low-fidelity and high-fidelity prototypes, allowing for rapid iterations based on user feedback. The main advantage is speed; designs can be produced in days rather than weeks, facilitating faster time-to-market. However, the quality can sometimes lag behind that of a professional prototyping manufacturer, especially for complex designs that require intricate details. The initial investment in technology and training can also be a barrier for some businesses.
How Do DIY Prototyping Methods Compare?
DIY prototyping methods involve using readily available materials and tools to create prototypes. This approach is particularly useful for startups or small businesses that may have limited budgets. The main advantage of DIY methods is the cost-effectiveness, as they often require minimal investment in tools and materials. However, the quality of the prototypes can vary significantly based on the skills of the individual creating them. This method is best for simple concepts where the goal is to validate an idea rather than produce a market-ready prototype.
Conclusion: How Can B2B Buyers Choose the Right Prototyping Solution?
Selecting the right prototyping solution depends on various factors, including the complexity of the product, budget constraints, and the timeline for development. For high-quality, complex products, a prototyping manufacturer may be the best option despite the higher costs and longer timelines. Conversely, if speed is crucial and the product is less complex, rapid prototyping technologies can offer a compelling alternative. For startups and smaller businesses looking to validate ideas with minimal investment, DIY methods may provide an effective way to test concepts. Ultimately, buyers should carefully assess their specific needs and resources to make an informed decision that aligns with their business objectives.
Essential Technical Properties and Trade Terminology for prototyping manufacturer
What Are the Key Technical Properties of Prototyping Materials?
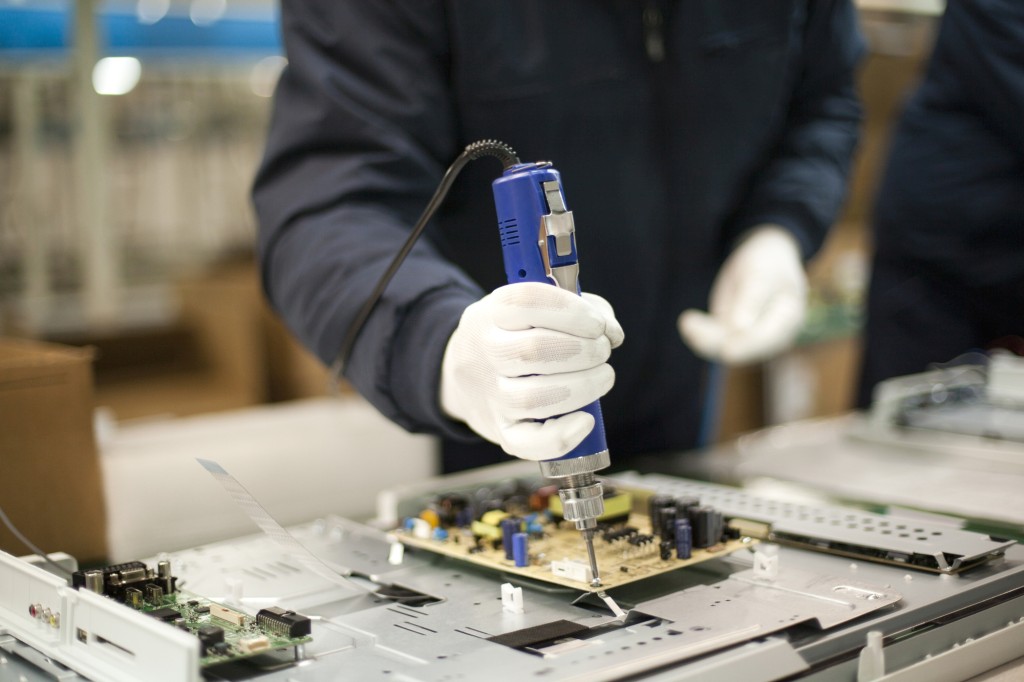
A stock image related to prototyping manufacturer.
In the realm of prototyping manufacturing, understanding critical technical properties is essential for making informed purchasing decisions. Below are some of the most significant specifications that international B2B buyers should consider:
1. Material Grade
Material grade refers to the quality and composition of the materials used in the prototype. Different grades offer varying levels of strength, flexibility, and durability. For instance, when prototyping metal components, buyers should consider aluminum versus steel, as each has distinct properties suitable for different applications. Selecting the right material grade ensures that the prototype can withstand testing and real-world conditions.
2. Tolerance
Tolerance indicates the allowable deviation from a specified dimension. It is crucial in ensuring that the prototype fits accurately with other components or assemblies. Tight tolerances are often necessary for high-precision applications, such as in the aerospace or medical industries. Buyers should communicate their tolerance requirements clearly to manufacturers to avoid costly errors in the production process.
3. Surface Finish
The surface finish of a prototype affects its aesthetic appeal and functionality. Common finishes include polished, matte, or textured surfaces. Depending on the intended use—whether for visual prototypes or functional testing—the chosen surface finish can impact product performance and user experience. Understanding surface finish options helps buyers align prototypes with their project requirements.
4. Dimensional Stability
Dimensional stability refers to a material’s ability to maintain its shape and size under varying environmental conditions, such as temperature and humidity. Materials with high dimensional stability are particularly important in industries where precision is vital. This property ensures that prototypes perform reliably over time, making it a key consideration for B2B buyers.
5. Mechanical Properties
Mechanical properties, including tensile strength, elongation, and hardness, define how a material behaves under various loads and stresses. These properties are critical when assessing whether a prototype can perform its intended function without failure. Buyers should request detailed mechanical property data from manufacturers to ensure their prototypes meet functional requirements.
What Are Common Trade Terms Used in Prototyping Manufacturing?
Navigating the prototyping manufacturing landscape involves familiarizing oneself with specific trade terminology. Here are some essential terms that B2B buyers should understand:
1. OEM (Original Equipment Manufacturer)
An OEM is a company that produces parts or equipment that may be marketed by another manufacturer. In prototyping, buyers often work with OEMs to create custom prototypes based on their designs. Understanding OEM relationships can facilitate smoother collaboration and production processes.
2. MOQ (Minimum Order Quantity)
MOQ refers to the smallest quantity of a product that a supplier is willing to sell. In prototyping, this term is vital as it directly impacts the cost and feasibility of producing a prototype. Buyers should inquire about MOQs to determine if they can meet the manufacturer’s requirements without incurring excess costs.
3. RFQ (Request for Quotation)
An RFQ is a document sent to suppliers to solicit price quotes for specific products or services. For prototyping, submitting an RFQ allows buyers to compare costs and services among different manufacturers. Clear and detailed RFQs can lead to more accurate quotes and better decision-making.
4. Incoterms (International Commercial Terms)
Incoterms are a set of international rules that define the responsibilities of buyers and sellers in a transaction. They clarify who is responsible for shipping, insurance, and tariffs. For international B2B buyers, understanding Incoterms is crucial to avoid misunderstandings and ensure smooth logistics during the prototyping process.
5. Lead Time
Lead time is the amount of time it takes from placing an order until the product is delivered. In prototyping, shorter lead times can be critical for meeting project deadlines. Buyers should discuss lead times with manufacturers to align production schedules and avoid delays in product development.
By grasping these technical properties and trade terms, B2B buyers can make more informed decisions, fostering successful partnerships in the prototyping manufacturing sector.
Navigating Market Dynamics and Sourcing Trends in the prototyping manufacturer Sector
What Are the Current Market Dynamics and Key Trends for Prototyping Manufacturers?
The prototyping manufacturing sector is experiencing significant shifts driven by technological advancements and changing buyer expectations. One of the most notable trends is the rise of digital prototyping technologies, such as 3D printing and computer-aided design (CAD). These innovations allow manufacturers to produce prototypes faster and at a lower cost, making it easier for businesses in regions like Africa and South America to enter the market with minimal capital investment. Furthermore, the increasing demand for customized solutions is prompting prototyping manufacturers to offer more flexible and scalable options, catering to diverse industries ranging from automotive to consumer electronics.
International B2B buyers are also gravitating towards collaborative platforms that enable real-time communication and feedback during the prototyping process. This trend is particularly relevant in the Middle East and Europe, where partnerships across borders are becoming commonplace. Buyers should consider manufacturers that leverage these platforms to enhance transparency and responsiveness, ultimately leading to better product outcomes.
Another key driver is the emphasis on sustainability, as companies seek to minimize waste and utilize eco-friendly materials in their prototypes. This shift not only aligns with global environmental goals but also appeals to increasingly conscious consumers. As a result, suppliers that prioritize sustainable practices are likely to gain a competitive edge in the marketplace.
How Important Is Sustainability and Ethical Sourcing in Prototyping Manufacturing?
Sustainability and ethical sourcing are becoming paramount in the prototyping manufacturing sector. The environmental impact of manufacturing processes, particularly in terms of waste generation and resource consumption, has led to a growing demand for sustainable practices. International B2B buyers, especially those in Europe, are increasingly prioritizing suppliers that adhere to green certifications such as ISO 14001, which focuses on effective environmental management systems.
Moreover, the use of recycled materials and biodegradable substances in prototyping not only reduces the ecological footprint but also meets regulatory requirements in various regions. Companies that incorporate these practices into their supply chains demonstrate a commitment to corporate social responsibility, which can enhance brand reputation and customer loyalty.
Ethical sourcing extends beyond environmental considerations; it encompasses fair labor practices and transparent supply chains. B2B buyers should prioritize manufacturers that provide clear documentation of their sourcing strategies and labor practices, ensuring that their operations align with ethical standards. This not only mitigates risks associated with supply chain disruptions but also fosters long-term partnerships based on trust and shared values.
What Is the Brief Evolution of Prototyping Manufacturing?
The prototyping manufacturing sector has evolved significantly over the last few decades. Initially dominated by traditional methods such as handcrafting and manual assembly, the industry witnessed a revolution with the advent of computer-aided design (CAD) in the 1980s, which allowed for more precise and efficient design processes. The introduction of 3D printing technology in the 1990s marked another pivotal moment, enabling rapid prototyping that drastically reduced lead times and costs.
Today, the industry is characterized by a focus on iterative design processes and user-centered approaches, influenced by methodologies like Design Thinking. This evolution reflects a broader trend towards agility and responsiveness in product development, allowing businesses to adapt quickly to market demands. As the prototyping sector continues to innovate, international B2B buyers are encouraged to stay informed about these trends to capitalize on emerging opportunities and secure a competitive advantage.
Frequently Asked Questions (FAQs) for B2B Buyers of prototyping manufacturer
-
How do I choose the right prototyping manufacturer for my project?
Choosing the right prototyping manufacturer involves evaluating their expertise, technology, and past projects. Look for manufacturers that specialize in your industry and have a portfolio showcasing relevant work. Request samples and assess their quality, as well as their ability to adhere to timelines. Additionally, consider their communication style and responsiveness, as these factors will significantly affect your collaboration. Engaging in initial discussions about your project requirements can provide insight into their understanding and capability to meet your needs. -
What are the key factors to consider when vetting a prototyping supplier?
When vetting a prototyping supplier, prioritize their experience, reputation, and certifications. Investigate their production capabilities, including machinery, materials, and technology used. Client testimonials and case studies can reveal their strengths and weaknesses. Additionally, assess their compliance with international standards, especially if you are importing prototypes. Establishing clear communication and understanding their processes will help ensure alignment and mitigate potential issues during production. -
What is the minimum order quantity (MOQ) for prototyping services?
Minimum order quantities (MOQs) for prototyping services can vary significantly between manufacturers. While some may offer low MOQs for initial samples, others might require larger quantities for cost efficiency. It’s essential to discuss your specific needs with potential suppliers and inquire about their flexibility regarding MOQs. In many cases, manufacturers are willing to accommodate smaller orders, especially for new clients or unique projects. -
How can I ensure quality assurance (QA) in the prototyping process?
To ensure quality assurance in the prototyping process, request detailed documentation of the manufacturer’s QA protocols. This should include inspection processes, testing methods, and compliance with industry standards. Regular updates and checkpoints during the production phase can help you monitor quality. Establishing a robust communication channel will allow you to address any concerns promptly and ensure that the final product meets your specifications. -
What customization options should I expect from a prototyping manufacturer?
Prototyping manufacturers often offer a range of customization options, including materials, dimensions, and finishes. Discuss your specific requirements during initial consultations to understand the extent of their customization capabilities. Some manufacturers may also provide design support, helping you refine your ideas before production. Be clear about your expectations, as this will ensure that the final prototype aligns with your vision. -
What payment terms are typically offered by prototyping manufacturers?
Payment terms can vary widely among prototyping manufacturers. Common arrangements include upfront payments, milestone payments during production, or full payment upon delivery. It’s advisable to negotiate terms that suit both parties, considering factors such as project size and risk. Ensure that the payment terms are clearly outlined in the contract to avoid misunderstandings and facilitate a smoother transaction process. -
How do logistics impact the prototyping process for international buyers?
Logistics play a crucial role in the prototyping process, especially for international buyers. Consider shipping methods, customs regulations, and potential delays that can affect delivery timelines. Collaborating with manufacturers who have experience in international shipping can streamline the process. Discuss logistics upfront to establish clear expectations regarding delivery times and costs, as well as any potential risks associated with cross-border transactions. -
What should I look for in the prototyping contract?
When reviewing a prototyping contract, ensure it includes detailed specifications of the project, timelines, payment terms, and quality assurance measures. Pay attention to clauses regarding intellectual property rights, confidentiality, and dispute resolution. Clear communication about each party’s responsibilities will help prevent misunderstandings. It’s wise to consult with legal professionals familiar with international trade agreements to ensure that your interests are protected.
Important Disclaimer & Terms of Use
⚠️ Important Disclaimer
The information provided in this guide, including content regarding manufacturers, technical specifications, and market analysis, is for informational and educational purposes only. It does not constitute professional procurement advice, financial advice, or legal advice.
While we have made every effort to ensure the accuracy and timeliness of the information, we are not responsible for any errors, omissions, or outdated information. Market conditions, company details, and technical standards are subject to change.
B2B buyers must conduct their own independent and thorough due diligence before making any purchasing decisions. This includes contacting suppliers directly, verifying certifications, requesting samples, and seeking professional consultation. The risk of relying on any information in this guide is borne solely by the reader.
Strategic Sourcing Conclusion and Outlook for prototyping manufacturer
What Are the Key Takeaways for B2B Buyers in Prototyping?
In the realm of prototyping manufacturing, strategic sourcing is paramount. By leveraging the insights gained through prototyping, businesses can significantly reduce time-to-market and mitigate risks associated with product development. This process allows companies to test concepts before committing extensive resources, ensuring that the final product aligns with market needs and user preferences. For international B2B buyers, particularly those in Africa, South America, the Middle East, and Europe, understanding the nuances of prototyping can lead to more informed purchasing decisions and stronger partnerships with manufacturers.
How Can Strategic Sourcing Enhance Your Prototyping Experience?
Adopting a strategic sourcing approach not only streamlines the procurement process but also facilitates collaboration with manufacturers who prioritize innovation and quality. By focusing on suppliers that embrace advanced prototyping techniques—such as 3D printing and iterative testing—buyers can enhance product accuracy and reduce development costs. This proactive engagement enables buyers to stay ahead of market trends and customer expectations.
What’s Next for International B2B Buyers in Prototyping?
As you explore opportunities in the prototyping sector, consider the potential of forming long-term partnerships with manufacturers that align with your vision and values. Embrace the power of prototyping to refine your ideas and accelerate your product development journey. The future of prototyping is bright, with evolving technologies and methodologies set to redefine the landscape. Take action now to position your business for success by engaging with innovative prototyping manufacturers today.