Discover Top Benefits of a Toilet Paper Holder Manufacturer (2025)
Introduction: Navigating the Global Market for toilet paper holder manufacturer
In the ever-evolving global marketplace, sourcing reliable toilet paper holder manufacturers can present significant challenges for international B2B buyers. Whether you’re in Nigeria, Indonesia, or any other region, understanding the complexities of supplier capabilities, product types, and pricing structures is crucial. This comprehensive guide aims to illuminate the various dimensions of sourcing toilet paper holders, addressing everything from material specifications to compliance with international quality standards.
As you navigate this landscape, you will encounter a diverse range of products designed for different applications—from residential use to commercial facilities. We will delve into the intricacies of supplier vetting, ensuring that you can identify trustworthy partners who meet your specific needs. Additionally, we will provide insights into cost considerations, helping you strike the right balance between quality and affordability.
By the end of this guide, you will be equipped with the knowledge necessary to make informed purchasing decisions. Whether you are looking to enhance your product offerings or ensure customer satisfaction, our actionable insights will empower you to forge strong relationships with manufacturers in Europe, Africa, South America, and the Middle East. Understanding these dynamics will not only streamline your procurement process but also position your business for success in a competitive market.
Understanding toilet paper holder manufacturer Types and Variations
Type Name | Key Distinguishing Features | Primary B2B Applications | Brief Pros & Cons for Buyers |
---|---|---|---|
Wall-Mounted Holders | Fixed installation, space-saving designs | Hotels, offices, public restrooms | Pros: Saves space, durable; Cons: Installation required, less flexible for layout changes. |
Freestanding Holders | Portable, no wall installation needed | Homes, small businesses | Pros: Easy to move, no installation; Cons: Requires floor space, can be less stable. |
Dual Roll Holders | Accommodates two rolls, often with a cover | High-traffic venues, large facilities | Pros: Reduces maintenance, convenient; Cons: Bulkier design, may not fit all spaces. |
Decorative Holders | Stylish designs, often made from premium materials | Upscale hotels, restaurants | Pros: Enhances decor, adds value; Cons: Higher cost, potential for wear. |
Automatic Holders | Touchless operation, often with sensors | Healthcare facilities, airports | Pros: Hygiene-focused, reduces waste; Cons: Higher initial investment, requires power source. |
What are the Characteristics of Wall-Mounted Toilet Paper Holders?
Wall-mounted toilet paper holders are designed for fixed installation, making them an ideal choice for environments where space is at a premium. Commonly used in hotels, offices, and public restrooms, these holders are typically made from durable materials such as stainless steel or plastic. When considering a wall-mounted option, B2B buyers should evaluate the installation requirements and the specific layout of their facilities, as these holders can limit flexibility in restroom design.
Why Choose Freestanding Toilet Paper Holders?
Freestanding toilet paper holders are a versatile choice for various settings, particularly homes and small businesses. Their portability allows for easy relocation without the need for installation. These holders can be made from materials like metal or wood, appealing to different aesthetic preferences. Buyers should consider the space available and the desired stability, as freestanding options may require more floor space and can be prone to tipping if not designed with a solid base.
What Benefits Do Dual Roll Holders Offer for High-Traffic Areas?
Dual roll holders are particularly advantageous in high-traffic venues such as large facilities and restrooms. By accommodating two rolls, these holders minimize the need for frequent maintenance and ensure that users always have access to toilet paper. While they provide convenience, B2B buyers should assess the size and compatibility of these holders with existing restroom layouts, as their bulkier design may not suit all spaces.
How Do Decorative Toilet Paper Holders Enhance B2B Environments?
Decorative toilet paper holders are designed with aesthetics in mind, often crafted from premium materials to complement upscale environments like hotels and restaurants. These holders can enhance the overall decor, adding a touch of luxury and value to the restroom experience. However, buyers should weigh the higher costs associated with decorative options against their budget, as well as consider potential wear and tear in high-use areas.
What Are the Advantages of Automatic Toilet Paper Holders?
Automatic toilet paper holders offer a modern solution focused on hygiene, making them suitable for healthcare facilities and airports. With touchless operation, these holders reduce the risk of cross-contamination and can help minimize waste. B2B buyers should consider the initial investment required for automatic systems, as well as the need for a power source, which may limit placement options in certain facilities.
Related Video: HOW TO INSTALL TOILET PAPER HOLDER ( Vanity )
Key Industrial Applications of toilet paper holder manufacturer
Industry/Sector | Specific Application of Toilet Paper Holder Manufacturer | Value/Benefit for the Business | Key Sourcing Considerations for this Application |
---|---|---|---|
Hospitality | Installation in hotels and restaurants | Enhances guest experience and cleanliness | Durability, design aesthetics, and compatibility with existing fixtures |
Healthcare | Usage in hospitals and clinics | Supports hygiene standards and patient comfort | Compliance with health regulations, easy maintenance, and durability |
Commercial Office Spaces | Equipping offices and coworking spaces | Promotes workplace hygiene and employee satisfaction | Bulk purchasing options, modern design, and easy installation |
Retail | Implementation in shopping malls and retail stores | Improves customer experience and store image | Versatility in design, cost-effectiveness, and supplier reliability |
Educational Institutions | Deployment in schools and universities | Ensures student hygiene and promotes a clean environment | Safety standards, ease of use, and maintenance requirements |
How is Toilet Paper Holder Manufacturer Used in the Hospitality Sector?
In the hospitality industry, toilet paper holders are essential for enhancing the overall guest experience in hotels and restaurants. These fixtures not only provide convenience but also contribute to a clean and organized restroom environment. International B2B buyers in this sector should prioritize durability and design aesthetics, ensuring that the holders match the venue’s style while withstanding frequent use. Suppliers that offer customizable options can provide added value, allowing businesses to maintain a consistent brand image.
What Role Does Toilet Paper Holder Manufacturer Play in Healthcare Facilities?
Toilet paper holders in healthcare facilities, such as hospitals and clinics, are critical for maintaining hygiene standards. These holders must be designed for easy access and frequent use, ensuring that patients and staff can maintain cleanliness. Buyers in this sector must consider compliance with health regulations and the ease of maintenance, as these factors directly impact operational efficiency. Durable materials that resist wear and tear are also essential to meet the rigorous demands of healthcare environments.
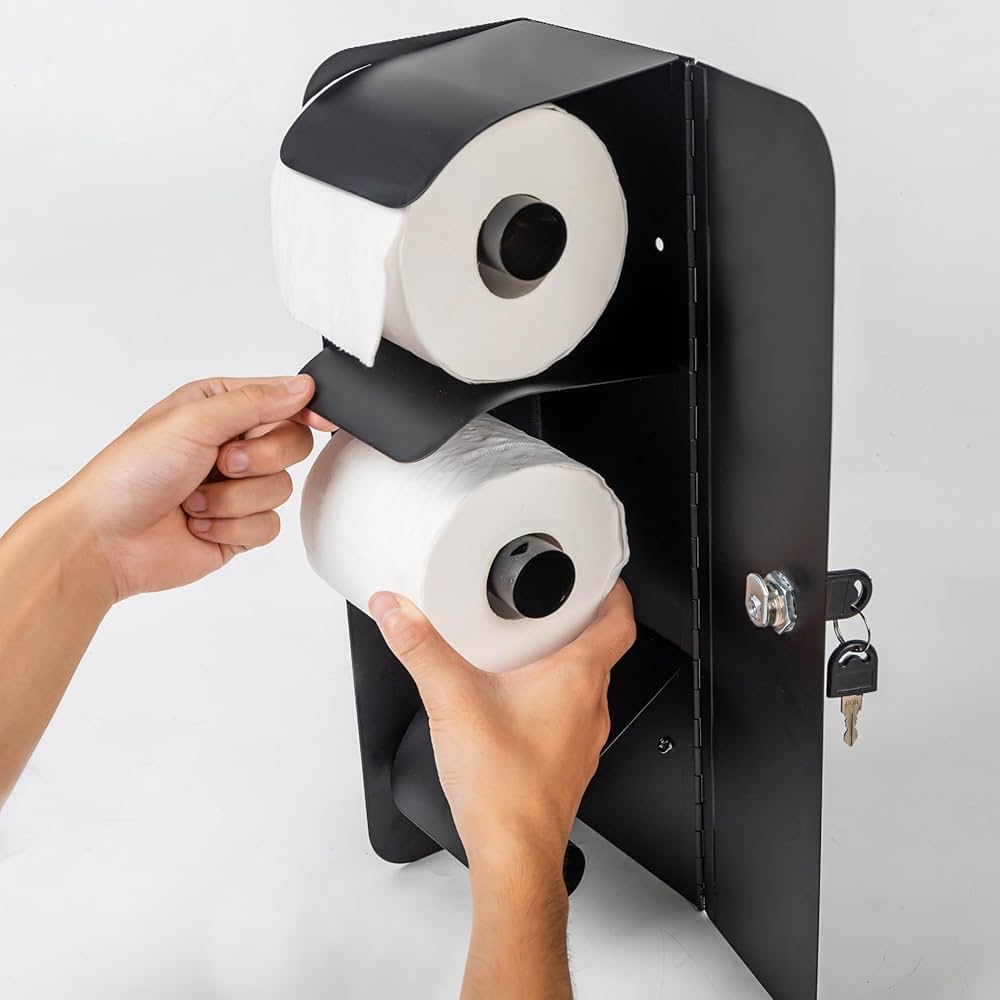
A stock image related to toilet paper holder manufacturer.
How are Toilet Paper Holders Beneficial in Commercial Office Spaces?
In commercial office spaces, toilet paper holders contribute significantly to workplace hygiene and employee satisfaction. They are often installed in restrooms to promote cleanliness, which is essential for employee morale and health. When sourcing these fixtures, B2B buyers should look for bulk purchasing options to accommodate large office environments, as well as modern designs that complement contemporary office aesthetics. Easy installation and maintenance are also key considerations to minimize disruption during setup.
What is the Importance of Toilet Paper Holders in Retail Environments?
In retail settings, such as shopping malls and stores, toilet paper holders enhance the customer experience by ensuring cleanliness in restrooms. A well-maintained restroom can significantly influence a customer’s perception of the store’s overall hygiene standards. For international B2B buyers in this sector, versatility in design and cost-effectiveness are crucial for selecting the right products. Reliable suppliers who can deliver on time and ensure quality are also vital for maintaining a positive customer experience.
How Do Educational Institutions Utilize Toilet Paper Holders?
Toilet paper holders are essential in educational institutions, including schools and universities, to promote hygiene among students. These fixtures ensure that restrooms are equipped to handle the needs of a large number of users while maintaining cleanliness. Buyers from this sector should focus on safety standards, ease of use, and maintenance requirements when sourcing products. Durable and user-friendly designs are particularly important to withstand the wear and tear associated with high-traffic environments like schools.
Related Video: How Toilet Paper Gets Made and Packaged
3 Common User Pain Points for ‘toilet paper holder manufacturer’ & Their Solutions
Scenario 1: Sourcing High-Quality Materials for Durability
The Problem:
B2B buyers often struggle with the inconsistency in quality when sourcing toilet paper holders, particularly when purchasing from manufacturers in different regions. For example, a buyer in Nigeria might find that local manufacturers use subpar materials that do not withstand high usage in commercial settings. This leads to frequent replacements and increased operational costs, ultimately affecting the bottom line and customer satisfaction.
The Solution:
To mitigate this issue, buyers should prioritize manufacturers that provide transparency regarding their material sourcing and production processes. When evaluating potential partners, request detailed information about the materials used in their toilet paper holders, including certifications that verify durability and quality standards. Additionally, consider establishing a long-term relationship with a manufacturer that offers samples or prototypes, allowing for real-world testing before making bulk purchases. This proactive approach not only ensures the durability of the products but also fosters trust and reliability in the supplier relationship.
Scenario 2: Navigating Cultural Preferences in Design
The Problem:
International buyers often encounter challenges related to cultural preferences and design expectations when sourcing toilet paper holders. For instance, a buyer from Europe may prefer sleek, modern designs, while a buyer from the Middle East might lean towards more traditional, ornate styles. Misalignment in design can lead to poor sales performance and customer dissatisfaction, making it crucial for manufacturers to understand these cultural nuances.
The Solution:
To address this challenge, B2B buyers should conduct thorough market research to identify regional design preferences and trends. Collaborating with local design consultants can also provide valuable insights into what styles resonate with the target audience. When engaging with manufacturers, clearly communicate these design requirements and request customization options. Additionally, leveraging digital design tools can facilitate the visualization of tailored designs before production, ensuring the final product aligns with cultural expectations and enhances market appeal.
Scenario 3: Ensuring Compliance with International Standards
The Problem:
Compliance with international safety and quality standards can be a significant pain point for buyers looking to source toilet paper holders. Buyers from Africa or South America may find that manufacturers do not meet necessary regulations, leading to potential legal issues and reputational damage. The complexity of navigating these standards can be overwhelming, especially for businesses new to international procurement.
The Solution:
B2B buyers should familiarize themselves with the specific regulations applicable to toilet paper holders in their target markets. This includes understanding certifications such as ISO standards and local compliance requirements. When selecting a manufacturer, prioritize those who are already compliant with these standards and can provide documentation to verify it. Engaging a third-party inspection service can also add an extra layer of assurance. By doing due diligence in verifying compliance, buyers can mitigate risks and ensure that their products meet the highest safety and quality benchmarks, ultimately protecting their brand and customer trust.
Strategic Material Selection Guide for toilet paper holder manufacturer
When selecting materials for toilet paper holders, manufacturers must consider various factors that influence performance, durability, and compliance with international standards. Here, we analyze four common materials: stainless steel, plastic, brass, and aluminum, focusing on their properties, advantages, disadvantages, and specific considerations for international B2B buyers.
What are the Key Properties of Stainless Steel for Toilet Paper Holders?
Stainless steel is a popular choice for toilet paper holders due to its high corrosion resistance and durability. It can withstand high temperatures and pressures, making it suitable for various environments. The typical grades used, such as 304 and 316, provide excellent resistance to rust and tarnishing, which is crucial in humid bathroom settings.
Pros & Cons: The primary advantage of stainless steel is its longevity and aesthetic appeal, often associated with a modern look. However, it comes at a higher cost compared to other materials, and manufacturing can be complex due to the need for specialized tools and techniques.
Impact on Application: Stainless steel is compatible with most cleaning agents, ensuring that the product maintains its appearance over time.
Considerations for International Buyers: Buyers from regions like Europe and the Middle East should ensure compliance with standards such as ASTM A240 for stainless steel, while also considering local preferences for finishes and styles.
How Does Plastic Compare as a Material for Toilet Paper Holders?
Plastic is another common material used in toilet paper holders, often made from high-density polyethylene (HDPE) or polyvinyl chloride (PVC). These plastics are lightweight and resistant to moisture, making them ideal for bathroom applications.
Pros & Cons: The key advantage of plastic is its low cost and ease of manufacturing, allowing for mass production. However, plastic may not be as durable as metal options, and it can be susceptible to fading or cracking over time, especially in high UV exposure areas.
Impact on Application: Plastic holders are generally suitable for residential use but may not withstand heavy-duty commercial applications.
Considerations for International Buyers: Buyers in Africa and South America should consider local regulations regarding plastic use, especially concerning recyclability and environmental impact.
What Advantages Does Brass Offer for Toilet Paper Holders?
Brass is a traditional material known for its aesthetic appeal and durability. It has excellent corrosion resistance, especially in humid environments, and can be easily shaped into intricate designs.
Pros & Cons: The main advantage of brass is its classic look, which can add a touch of elegance to any bathroom. However, it is more expensive than both plastic and stainless steel, and it may require regular polishing to maintain its appearance.
Impact on Application: Brass is compatible with various cleaning agents, but harsh chemicals can lead to tarnishing.
Considerations for International Buyers: Buyers should be aware of the standards for brass products in their regions, such as compliance with the European Union’s REACH regulations regarding hazardous substances.
Why Choose Aluminum for Toilet Paper Holders?
Aluminum is a lightweight and corrosion-resistant material that is increasingly being used in toilet paper holders. It can be anodized to enhance its durability and aesthetic appeal.
Pros & Cons: The key advantage of aluminum is its lightweight nature, making installation easier. However, it is less durable than stainless steel and can be prone to scratching.
Impact on Application: Aluminum holders are suitable for residential and light commercial use, but they may not hold up in high-traffic areas.
Considerations for International Buyers: Buyers in regions like the Middle East should be aware of local climatic conditions that may affect aluminum’s performance, such as high temperatures and humidity.
Summary Table of Material Selection for Toilet Paper Holders
Material | Typical Use Case for toilet paper holder manufacturer | Key Advantage | Key Disadvantage/Limitation | Relative Cost (Low/Med/High) |
---|---|---|---|---|
Stainless Steel | Commercial and high-end residential applications | High durability and corrosion resistance | Higher cost and complex manufacturing | High |
Plastic | Residential and low-cost commercial applications | Low cost and easy to manufacture | Less durable, susceptible to fading | Low |
Brass | High-end residential and luxury applications | Aesthetic appeal and durability | Expensive and requires maintenance | High |
Aluminum | Residential and light commercial applications | Lightweight and corrosion-resistant | Less durable than stainless steel | Medium |
This strategic material selection guide provides B2B buyers with essential insights to make informed decisions that align with their operational needs and regional compliance requirements.
In-depth Look: Manufacturing Processes and Quality Assurance for toilet paper holder manufacturer
What Are the Key Stages in the Manufacturing Process of Toilet Paper Holders?
Toilet paper holders are essential components in both residential and commercial settings, and understanding their manufacturing process can help B2B buyers make informed decisions. The typical manufacturing process can be broken down into several main stages: material preparation, forming, assembly, and finishing.
Material Preparation: What Materials Are Commonly Used?
The choice of materials is critical in the production of toilet paper holders. Common materials include stainless steel, plastic, and aluminum. Each material has its advantages and drawbacks regarding cost, durability, and aesthetic appeal. For instance, stainless steel is highly durable and resistant to corrosion, making it ideal for high-traffic areas, while plastic may be more cost-effective for less demanding environments.
In this stage, raw materials are sourced from reputable suppliers. B2B buyers should ensure that these suppliers adhere to international standards to guarantee the quality of the materials used.
How Are Toilet Paper Holders Formed?
The forming stage involves converting raw materials into the desired shapes and sizes. Key techniques include:
- Stamping: Used for metal components, where sheets of metal are cut and shaped using dies.
- Injection Molding: Common for plastic holders, where molten plastic is injected into molds.
- Extrusion: Suitable for continuous shapes, particularly in aluminum production.
B2B buyers should inquire about the specific forming techniques used by manufacturers, as this can influence both the quality and price of the final product.
What Does the Assembly Process Look Like for Toilet Paper Holders?
After individual components are formed, the next step is assembly. This process typically involves:
- Joining Components: Methods such as welding for metal parts, or adhesive application for plastic components.
- Quality Checks: At this stage, manufacturers often conduct preliminary inspections to catch defects early.
B2B buyers should consider manufacturers who have established a streamlined assembly process, as this can lead to faster turnaround times and reduced costs.
How Are Toilet Paper Holders Finished for Market Readiness?
Finishing is the final stage before products are packaged and shipped. This includes:
- Surface Treatment: Processes such as polishing, painting, or applying a powder coat to enhance durability and aesthetics.
- Final Inspection: A thorough check to ensure that the product meets design specifications and quality standards.
Buyers should ensure that manufacturers implement effective finishing techniques, as this impacts the product’s longevity and appearance.
What Are the International Quality Standards Relevant to Toilet Paper Holders?
Quality assurance is paramount in manufacturing, and adhering to international standards is essential for maintaining product integrity. Key standards include:
- ISO 9001: This standard outlines criteria for a quality management system, ensuring consistent product quality and customer satisfaction.
- CE Marking: Required for products sold within the European Economic Area, demonstrating compliance with safety and environmental requirements.
- API Standards: Applicable in specific markets, particularly for manufacturers producing holders for commercial or industrial use.
B2B buyers should verify that their suppliers are compliant with these standards to ensure the products meet international safety and quality benchmarks.
What Are the Key Quality Control Checkpoints in Manufacturing?
Quality control (QC) is a systematic process that ensures products meet specified requirements. Key QC checkpoints include:
- Incoming Quality Control (IQC): Assessing raw materials upon arrival.
- In-Process Quality Control (IPQC): Continuous monitoring during production to catch defects early.
- Final Quality Control (FQC): Comprehensive inspection before products are shipped.
Understanding these checkpoints helps buyers gauge the reliability of their suppliers. Manufacturers who implement rigorous QC processes are more likely to deliver high-quality products.
What Testing Methods Are Commonly Used for Quality Assurance?
Various testing methods are employed to ensure that toilet paper holders meet quality standards:
- Dimensional Testing: Ensuring that products are manufactured to the correct specifications.
- Durability Testing: Assessing the strength and lifespan of the product under simulated conditions.
- Corrosion Resistance Testing: Particularly important for metal holders, ensuring they can withstand various environmental conditions.
B2B buyers should ask manufacturers for detailed reports on their testing methods and results to confirm the quality of their products.
How Can B2B Buyers Verify Supplier Quality Control?
B2B buyers can take several steps to verify the quality control practices of suppliers:
- Audits: Conducting regular audits of suppliers can help assess their compliance with quality standards.
- Quality Reports: Requesting detailed QC reports can provide insights into the manufacturer’s processes and outcomes.
- Third-Party Inspections: Engaging independent agencies to inspect the manufacturing facility and products can offer an unbiased evaluation of quality.
In regions like Africa, South America, the Middle East, and Europe, where standards may vary, these verification methods are crucial for mitigating risks associated with supplier reliability.
What Are the Quality Control Nuances for International B2B Buyers?
Navigating the complexities of quality control in international trade can be challenging. B2B buyers should be aware of the following nuances:
- Regulatory Variations: Different countries may have varying regulations regarding product safety and quality. Understanding these can prevent compliance issues.
- Cultural Differences: Approaches to quality assurance may differ based on cultural practices. Open communication with suppliers can help bridge these gaps.
- Logistics and Supply Chain Challenges: International shipping can affect product quality. Buyers should inquire about how suppliers manage logistics to maintain quality during transit.
By being informed about these nuances, international B2B buyers can make better decisions and foster successful partnerships with toilet paper holder manufacturers.
Practical Sourcing Guide: A Step-by-Step Checklist for ‘toilet paper holder manufacturer’
This practical sourcing guide is designed to assist international B2B buyers in efficiently procuring toilet paper holders from manufacturers. It outlines essential steps to ensure a successful sourcing process, helping you identify reliable suppliers while addressing quality, compliance, and logistical considerations.
Step 1: Define Your Technical Specifications
Before reaching out to manufacturers, clearly outline your technical requirements for toilet paper holders. This includes dimensions, materials, weight capacity, and design features. Having precise specifications helps suppliers understand your needs and reduces the chances of miscommunication.
- Material Requirements: Specify if you require stainless steel, plastic, or eco-friendly materials.
- Design Preferences: Consider whether you need wall-mounted, free-standing, or decorative holders.
Step 2: Conduct Market Research
Investigate the current market landscape for toilet paper holders, focusing on suppliers in Africa, South America, the Middle East, and Europe. Understanding market trends, pricing structures, and competitive offerings can provide leverage in negotiations.
- Identify Key Players: Make a list of manufacturers known for quality and reliability.
- Analyze Pricing Trends: Research average prices to ensure you’re getting competitive quotes.
Step 3: Evaluate Potential Suppliers
Before making a commitment, thoroughly vet potential suppliers. Request detailed company profiles, case studies, and references from buyers within your industry or region to gauge their reliability and performance.
- Check Reviews and Ratings: Look for testimonials or feedback from previous customers.
- Visit Trade Shows or Exhibitions: If possible, attend events to meet suppliers in person and view their products.
Step 4: Verify Supplier Certifications
Ensure that your chosen suppliers hold the necessary certifications and comply with industry standards. Certifications such as ISO, CE, or specific environmental certifications can indicate a commitment to quality and safety.
- Request Documentation: Ask for copies of relevant certifications.
- Assess Compliance: Verify that the certifications align with your market’s regulatory requirements.
Step 5: Negotiate Terms and Conditions
Once you have identified potential suppliers, enter into negotiations to discuss pricing, payment terms, delivery schedules, and warranties. Clear communication at this stage helps establish a solid foundation for your business relationship.
- Discuss Minimum Order Quantities (MOQs): Ensure MOQs are manageable for your operations.
- Clarify Shipping Terms: Confirm responsibilities for shipping costs and logistics.
Step 6: Request Samples for Quality Assurance
Before placing a large order, request samples to evaluate the quality of the toilet paper holders. This allows you to assess the product firsthand and ensure it meets your specifications.
- Test Durability and Functionality: Check how the holder performs under real-world conditions.
- Evaluate Aesthetic Appeal: Ensure the design aligns with your brand’s image.
Step 7: Establish a Communication Plan
Finally, set up a clear communication plan with your chosen supplier. Regular updates and feedback loops can help address any issues promptly and maintain a smooth supply chain.
- Define Points of Contact: Establish who will handle communications on both sides.
- Schedule Regular Check-ins: Plan for periodic reviews to discuss performance and address any concerns.
By following these steps, you can effectively navigate the sourcing process for toilet paper holders, ensuring that you partner with a manufacturer that meets your business needs and quality standards.
Comprehensive Cost and Pricing Analysis for toilet paper holder manufacturer Sourcing
What Are the Key Cost Components in Sourcing Toilet Paper Holders?
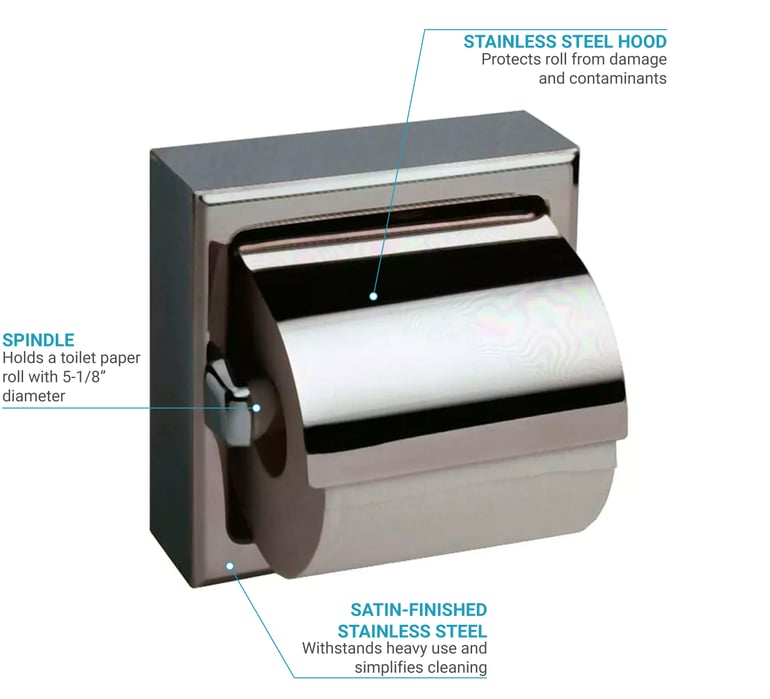
A stock image related to toilet paper holder manufacturer.
When evaluating the total cost of sourcing toilet paper holders from manufacturers, several key components come into play. Understanding these elements can significantly enhance your negotiation strategy and overall purchasing decisions.
-
Materials: The choice of materials directly influences the cost. Common materials include plastic, stainless steel, and brass. Each comes with varying price points and durability. For example, stainless steel may be more expensive but offers superior longevity and resistance to corrosion, which can be a selling point in regions with high humidity.
-
Labor: Labor costs can differ widely depending on the manufacturing location. For instance, manufacturers in countries with lower wage standards may offer more competitive pricing. However, it’s essential to consider the skill level of the workforce, as it impacts the quality of the finished product.
-
Manufacturing Overhead: This includes indirect costs such as utilities, rent, and administrative expenses. These costs can vary based on the manufacturer’s operational efficiency and location, affecting the overall pricing structure.
-
Tooling: Initial tooling costs for custom designs can be significant. If you require specialized designs, ensure to factor in these costs, as they can be amortized over larger order volumes.
-
Quality Control (QC): Effective QC processes ensure product reliability and compliance with international standards. Investing in stringent QC can increase upfront costs but may save money in the long run by reducing returns and enhancing customer satisfaction.
-
Logistics: Shipping costs, tariffs, and handling fees can greatly affect the final price. Understanding the Incoterms agreed upon in your contracts is crucial for budgeting these expenses accurately.
-
Margin: Finally, the manufacturer’s profit margin will also be a component of the final price. This margin can vary significantly based on the manufacturer’s reputation, market demand, and competition.
How Do Price Influencers Affect Your Sourcing Strategy?
Several factors can influence the pricing of toilet paper holders. Recognizing these will help you tailor your sourcing strategy effectively.
-
Volume/MOQ (Minimum Order Quantity): Larger orders often lead to better pricing due to economies of scale. Negotiating for a lower MOQ can be beneficial if you’re testing a new product line but be prepared for higher per-unit costs.
-
Specifications and Customization: Custom designs or specific material requirements can lead to increased costs. It’s advisable to clearly outline specifications to avoid unexpected charges during production.
-
Materials and Quality Certifications: Products made from high-quality materials or those that meet specific industry standards (such as ISO certification) may command a premium price. However, they often provide a better return on investment through durability and customer satisfaction.
-
Supplier Factors: The reputation and reliability of the supplier can influence pricing. Established manufacturers may charge more due to their proven track record, while emerging companies might offer lower prices to gain market share.
-
Incoterms: Understanding the agreed-upon Incoterms is essential for accurately calculating total costs. Terms like FOB (Free on Board) and CIF (Cost, Insurance, and Freight) dictate who is responsible for shipping costs and risks, impacting your overall expenditure.
What Buyer Tips Can Enhance Cost-Efficiency in Sourcing?
B2B buyers can adopt several strategies to ensure cost-effectiveness when sourcing toilet paper holders.
-
Effective Negotiation: Leverage your knowledge of cost components and price influencers during negotiations. Be prepared to discuss volume discounts, payment terms, and delivery schedules to optimize your procurement costs.
-
Total Cost of Ownership (TCO): Look beyond the initial purchase price. Consider factors like maintenance, potential returns, and the lifespan of the product. A higher upfront cost may be justified if the product lasts longer or requires less maintenance.
-
Understanding Pricing Nuances: Be aware of regional differences in pricing. For example, manufacturers in Europe may have higher labor costs compared to those in Africa or South America. This understanding can help in benchmarking prices and making informed sourcing decisions.
-
Continuous Supplier Assessment: Regularly review supplier performance and pricing structures. This ensures you remain competitive and can switch suppliers if necessary, based on changing market conditions.
Disclaimer
Prices for toilet paper holders can vary widely based on the factors outlined above. This analysis serves as a guideline and should be supplemented with current market research and supplier quotes to ensure accuracy in budgeting and procurement strategies.
Alternatives Analysis: Comparing toilet paper holder manufacturer With Other Solutions
In the quest for effective restroom solutions, international B2B buyers often encounter a variety of options beyond traditional toilet paper holders. Exploring alternative solutions can lead to innovative choices that align with specific operational needs and budget constraints. This analysis will compare the conventional toilet paper holder manufacturer with two viable alternatives: automatic toilet paper dispensers and bidet systems.
Comparison Table of Toilet Paper Holder Manufacturer and Alternatives
Comparison Aspect | Toilet Paper Holder Manufacturer | Automatic Toilet Paper Dispenser | Bidet System |
---|---|---|---|
Performance | Reliable and consistent access to toilet paper | Automated dispensing reduces waste | Provides a thorough clean, reduces paper use |
Cost | Low to moderate initial investment; ongoing paper costs | Higher initial investment; minimal ongoing costs | Moderate to high initial investment; low ongoing costs |
Ease of Implementation | Simple installation; minimal training required | Requires electrical setup; some training may be needed | Installation may require plumbing adjustments; user education necessary |
Maintenance | Low maintenance; occasional replacement of holders | Regular refills needed; occasional mechanical maintenance | Requires cleaning; occasional part replacement |
Best Use Case | High-traffic restrooms; budget-conscious settings | Modern facilities aiming for hygiene and efficiency | Eco-conscious establishments; upscale venues |
What Are the Pros and Cons of Automatic Toilet Paper Dispensers?
Automatic toilet paper dispensers offer a modern alternative to traditional holders. The primary advantage is their ability to reduce waste through controlled dispensing, which is especially beneficial in high-traffic areas. Additionally, they enhance hygiene by minimizing contact with surfaces. However, the initial setup cost can be significantly higher than that of conventional holders, and they require a power source, which may not be available in all locations. Regular maintenance is also essential to ensure proper functioning.
How Do Bidet Systems Compare in Terms of Efficiency?
Bidet systems present an eco-friendly solution that minimizes the reliance on toilet paper altogether. They provide a thorough cleansing experience, which can enhance personal hygiene and comfort. The long-term cost savings from reduced paper use can offset the initial investment over time. However, installation may require plumbing modifications, and educating users on proper bidet use is necessary. This option may not be suitable for all markets, particularly where cultural preferences lean towards traditional toilet paper use.
Conclusion: How Should B2B Buyers Choose the Right Restroom Solution?
Choosing the right restroom solution depends on various factors, including budget, space, and user preferences. B2B buyers should evaluate the specific needs of their facilities and consider the long-term operational costs of each option. For establishments focused on cost-effectiveness and ease of use, traditional toilet paper holders may suffice. Conversely, those aiming for sustainability and modern hygiene standards might find that automatic dispensers or bidet systems align better with their goals. Assessing the unique context of their operations will enable buyers to make informed decisions that enhance user experience while optimizing resource use.
Essential Technical Properties and Trade Terminology for toilet paper holder manufacturer
What Are the Key Technical Properties of Toilet Paper Holders?
Understanding the technical properties of toilet paper holders is vital for B2B buyers. These specifications directly affect product quality, durability, and compatibility with various environments. Here are some essential properties to consider:
1. Material Grade
The material used in toilet paper holders significantly impacts their performance and longevity. Common materials include stainless steel, plastic, and brass. Stainless steel, for instance, is favored for its corrosion resistance, making it ideal for high-humidity environments like bathrooms. Buyers should inquire about the material grade, as higher grades offer better durability and aesthetic appeal, which is crucial for both residential and commercial applications.
2. Load Capacity
Load capacity refers to the maximum weight a toilet paper holder can safely support. This property is particularly important for commercial settings where heavy-duty usage is common. Manufacturers often provide load capacity specifications, which can guide buyers in selecting products that meet the demands of their specific applications, ensuring safety and preventing product failure.
3. Finish and Coating
The finish of a toilet paper holder affects both its appearance and resistance to wear. Options include brushed, polished, or matte finishes, often treated with coatings to enhance durability and prevent tarnishing. Buyers should consider how the finish aligns with their design preferences and maintenance capabilities, as well as its performance in different environmental conditions.
4. Tolerance Levels
Tolerance levels define the permissible variation in dimensions during manufacturing. High tolerance levels indicate a more precise manufacturing process, which is essential for ensuring that components fit together correctly. For B2B buyers, understanding tolerance levels is important when sourcing components that need to be integrated with other bathroom fixtures or installations.
5. Installation Type
Different toilet paper holders come with various installation types, such as wall-mounted or free-standing. Each type has implications for space utilization and ease of installation. Buyers must assess the installation type to ensure it fits their specific project requirements, especially in spaces where layout and accessibility are critical.
What Common Trade Terms Should B2B Buyers Know?
Familiarizing yourself with industry terminology can streamline communication with manufacturers and suppliers. Here are some common terms that are essential for B2B transactions in the toilet paper holder sector:
1. OEM (Original Equipment Manufacturer)
OEM refers to companies that produce parts or equipment that may be marketed by another manufacturer. Understanding OEM relationships can help buyers identify reliable sources for customized toilet paper holders that meet specific design and functionality requirements.
2. MOQ (Minimum Order Quantity)
MOQ is the smallest quantity of a product that a supplier is willing to sell. Knowing the MOQ is crucial for buyers to manage inventory costs and ensure they can meet their project demands without over-committing resources. This term often varies between manufacturers, making it essential to confirm before placing orders.
3. RFQ (Request for Quotation)
An RFQ is a document that solicits price quotes from suppliers for specific products or services. B2B buyers should prepare detailed RFQs to ensure they receive accurate and competitive pricing. Including technical specifications, quantities, and delivery timelines can improve the effectiveness of the RFQ process.
4. Incoterms (International Commercial Terms)
Incoterms are a set of international rules that define the responsibilities of buyers and sellers in international transactions. Understanding these terms is essential for buyers to clarify shipping costs, risk management, and delivery responsibilities. Common Incoterms include FOB (Free on Board) and CIF (Cost, Insurance, and Freight), which dictate when the ownership and risk transfer from seller to buyer.
5. Lead Time
Lead time is the period between placing an order and receiving the goods. For B2B buyers, understanding lead times is essential for project planning and inventory management. It can vary based on factors such as manufacturing capacity, material availability, and shipping conditions, so it’s vital to discuss this with suppliers upfront.
By grasping these technical properties and trade terms, international B2B buyers can make more informed purchasing decisions, ensuring they select the right toilet paper holders for their specific needs.
Navigating Market Dynamics and Sourcing Trends in the toilet paper holder manufacturer Sector
What Are the Key Market Dynamics Affecting Toilet Paper Holder Manufacturers?
The toilet paper holder manufacturing sector is witnessing significant transformations driven by global market trends. Key factors include increased demand for hygiene products, a shift towards e-commerce platforms, and innovations in product design and materials. In regions like Africa and South America, urbanization and rising disposable incomes are leading to heightened consumption of household and commercial bathroom accessories. Meanwhile, in Europe and the Middle East, the emphasis on aesthetics and functionality is influencing purchasing decisions.
Emerging technologies such as smart manufacturing and automation are redefining sourcing strategies. B2B buyers are increasingly leveraging digital platforms for procurement, allowing for a wider selection of suppliers and competitive pricing. Additionally, data analytics is being used to forecast demand trends, helping manufacturers adjust production accordingly. International buyers should stay alert to these tech-driven shifts, as they can lead to cost efficiencies and improved supply chain management.
How Is Sustainability Shaping the Sourcing of Toilet Paper Holders?
Sustainability has become a cornerstone of modern business practices, and the toilet paper holder sector is no exception. The environmental impact of manufacturing processes and materials is under scrutiny, prompting many manufacturers to adopt eco-friendly practices. This includes the use of recycled materials and sustainable sourcing of raw materials, which are increasingly demanded by consumers and businesses alike.
Ethical supply chains are also gaining importance, especially among international B2B buyers who prioritize corporate social responsibility (CSR) in their sourcing decisions. Certifications such as Forest Stewardship Council (FSC) and Global Recycled Standard (GRS) can serve as indicators of a manufacturer’s commitment to sustainability. Buyers should seek out suppliers who can provide evidence of these certifications to ensure they are partnering with responsible manufacturers. This not only enhances brand reputation but can also lead to loyalty among environmentally-conscious consumers.
What Is the Historical Context of the Toilet Paper Holder Manufacturing Sector?
The toilet paper holder manufacturing sector has evolved significantly over the decades, transitioning from simple, utilitarian designs to a diverse array of styles and materials. Initially dominated by basic metal and plastic options, the market has expanded to include high-end finishes, eco-friendly materials, and innovative designs tailored to various consumer preferences.
The rise of the wellness movement and heightened awareness of hygiene has further accelerated demand for quality bathroom accessories. As international trade barriers have lowered, manufacturers from different regions have gained access to global markets, allowing for a richer variety of products. This evolution reflects broader societal changes and highlights the importance of adaptability in the sector, which is vital for B2B buyers aiming to keep pace with consumer trends and preferences.
In conclusion, understanding the market dynamics, sustainability practices, and historical context of the toilet paper holder manufacturing sector is essential for international B2B buyers looking to make informed purchasing decisions. By focusing on innovative sourcing strategies and ethical partnerships, buyers can enhance their product offerings and align with contemporary consumer expectations.
Frequently Asked Questions (FAQs) for B2B Buyers of toilet paper holder manufacturer
-
How can I ensure the quality of toilet paper holders from manufacturers?
To ensure quality when sourcing toilet paper holders, start by requesting samples from potential manufacturers. Evaluate the materials, design, and durability of the samples. Additionally, verify their quality assurance processes, such as ISO certification or compliance with international standards. Establishing clear communication about your expectations and conducting factory visits, if feasible, can further mitigate quality risks. Utilize third-party inspection services to conduct quality checks before shipment, particularly when dealing with suppliers from regions with varying manufacturing standards. -
What are the typical minimum order quantities (MOQs) for toilet paper holders?
Minimum order quantities for toilet paper holders can vary significantly among manufacturers. Generally, MOQs range from 100 to 1,000 units, depending on the type of holder and materials used. When negotiating, consider your budget and storage capabilities. Some manufacturers may offer flexibility on MOQs for first-time buyers or bulk orders, so it’s essential to communicate your needs upfront. Engaging with manufacturers who cater specifically to your target market can also provide better options regarding MOQs. -
What payment terms should I expect when dealing with toilet paper holder manufacturers?
Payment terms vary by manufacturer and often depend on the order size and buyer’s creditworthiness. Common arrangements include a 30% deposit upfront with the remaining 70% due before shipment. Some manufacturers may offer letter of credit options for larger transactions, which can provide additional security. Ensure you clarify payment terms in the contract, including any penalties for late payments and conditions for refunds or disputes. It’s advisable to establish a payment method that minimizes risk, such as using escrow services for larger orders. -
How can I customize toilet paper holders to meet my specific needs?
Most manufacturers offer customization options for toilet paper holders, including size, material, finish, and branding. To initiate customization, provide detailed specifications and design requirements to the manufacturer. Discuss potential costs and lead times associated with custom orders, as these can differ significantly from standard products. It’s beneficial to collaborate closely with the manufacturer’s design team to ensure your vision is accurately translated into the final product. Additionally, requesting prototypes can help refine your requirements before mass production. -
What logistics considerations should I keep in mind when importing toilet paper holders?
When importing toilet paper holders, logistics considerations include shipping methods, costs, and import regulations. Evaluate options such as sea freight for cost-effectiveness versus air freight for speed. Familiarize yourself with the import duties and taxes applicable in your country, as these can impact overall costs. Partnering with a reliable freight forwarder can streamline the shipping process, helping you navigate customs clearance and ensuring timely delivery. Always factor in lead times for production and shipping when planning your supply chain. -
How do I vet potential suppliers for toilet paper holders?
To vet potential suppliers, start by researching their business history and reputation in the industry. Request references from previous clients and check online reviews or forums for feedback. Conduct a site visit if possible, or utilize third-party audit services to assess their manufacturing capabilities. Verify their certifications and compliance with relevant standards. Establish clear communication to gauge their responsiveness and willingness to collaborate. A thorough vetting process can significantly reduce risks associated with quality and delivery. -
What are the common materials used in manufacturing toilet paper holders?
Toilet paper holders are typically made from a variety of materials, including stainless steel, plastic, brass, and aluminum. Stainless steel is favored for its durability and resistance to corrosion, making it ideal for high-moisture environments. Plastic holders are lightweight and cost-effective, while brass offers a classic aesthetic and sturdiness. Understanding the material properties and their suitability for your target market can influence your purchasing decisions. Consider the balance between cost, aesthetics, and functionality when selecting materials. -
What certifications should I look for when sourcing toilet paper holders?
When sourcing toilet paper holders, look for certifications that ensure quality and safety. ISO 9001 certification indicates a manufacturer’s commitment to quality management systems. Additionally, certifications such as CE marking or ASTM compliance can assure that products meet specific safety and performance standards. For eco-conscious buyers, certifications like FSC (Forest Stewardship Council) or recycled material certifications can highlight sustainable practices. Ensuring your suppliers have relevant certifications can enhance your brand’s credibility and meet regulatory requirements in your target markets.
Important Disclaimer & Terms of Use
⚠️ Important Disclaimer
The information provided in this guide, including content regarding manufacturers, technical specifications, and market analysis, is for informational and educational purposes only. It does not constitute professional procurement advice, financial advice, or legal advice.
While we have made every effort to ensure the accuracy and timeliness of the information, we are not responsible for any errors, omissions, or outdated information. Market conditions, company details, and technical standards are subject to change.
B2B buyers must conduct their own independent and thorough due diligence before making any purchasing decisions. This includes contacting suppliers directly, verifying certifications, requesting samples, and seeking professional consultation. The risk of relying on any information in this guide is borne solely by the reader.
Strategic Sourcing Conclusion and Outlook for toilet paper holder manufacturer
In the evolving landscape of toilet paper holder manufacturing, strategic sourcing emerges as a critical component for international B2B buyers looking to optimize their supply chains. By leveraging insights from various markets, particularly in Africa, South America, the Middle East, and Europe, businesses can identify reliable manufacturers who not only meet quality standards but also align with ethical sourcing practices.
How Can Strategic Sourcing Enhance Your Procurement Process?
Implementing a robust strategic sourcing framework enables buyers to negotiate better pricing, improve supplier relationships, and ensure a consistent supply of innovative products. This is especially vital in regions where market dynamics can fluctuate rapidly. It is advisable to conduct thorough market research and supplier evaluations to mitigate risks and enhance procurement efficiency.
What Should B2B Buyers Focus on for Future Sourcing Success?
As the demand for sustainable and eco-friendly products continues to rise, international buyers should prioritize manufacturers who demonstrate a commitment to environmental responsibility. Engaging with suppliers that invest in sustainable practices not only enhances brand reputation but also meets the growing consumer demand for green products.
In conclusion, the future of toilet paper holder manufacturing holds significant opportunities for strategic sourcing. By taking proactive steps today, B2B buyers can position themselves for success in a competitive marketplace. Start exploring your sourcing options now to build a resilient supply chain that can adapt to changing consumer preferences and market conditions.