Discover Top Benefits of a Wooden Boxe Manufacturer (2025)
Introduction: Navigating the Global Market for wooden boxe manufacturer
In today’s competitive landscape, sourcing high-quality wooden boxes can be a daunting task for international B2B buyers. With a myriad of manufacturers to choose from, understanding the nuances of quality, pricing, and supplier reliability is crucial. This guide delves into the global market for wooden box manufacturers, offering insights into various types, applications, and the intricacies of the procurement process. Whether you’re in Africa, South America, the Middle East, or Europe—regions where wooden packaging plays a vital role in logistics and product presentation—this resource is tailored to empower your purchasing decisions.
What Types of Wooden Boxes Are Available for Purchase?
From simple crates to intricately designed gift boxes, wooden boxes come in a variety of forms. Each type serves different purposes, ranging from storage to presentation. Understanding these distinctions will help you select the right product for your business needs.
How Can You Vet Suppliers Effectively?
Supplier vetting is a critical component of the purchasing process. This guide outlines key criteria to consider when evaluating manufacturers, including certifications, production capabilities, and past customer reviews. By following these guidelines, you can mitigate risks and ensure you partner with reputable suppliers.
What Are the Cost Factors Involved in Sourcing Wooden Boxes?
Cost is often a deciding factor in procurement. This guide provides a detailed breakdown of the various elements that influence pricing, including material quality, customization options, and shipping costs. Understanding these factors will enable you to negotiate better deals and make informed decisions that align with your budget.
By leveraging the insights and strategies outlined in this guide, international B2B buyers can navigate the complexities of sourcing wooden boxes, ensuring they make choices that enhance their operational efficiency and product appeal.
Understanding wooden boxe manufacturer Types and Variations
Type Name | Key Distinguishing Features | Primary B2B Applications | Brief Pros & Cons for Buyers |
---|---|---|---|
Custom Wooden Boxes | Tailored designs, specific dimensions, and branding options | Retail, e-commerce packaging, promotional items | Pros: Unique branding, tailored fit. Cons: Higher cost, longer lead time. |
Standard Wooden Boxes | Pre-manufactured sizes and designs, often in bulk | Shipping, storage, general packaging | Pros: Cost-effective, readily available. Cons: Limited customization. |
Decorative Wooden Boxes | Aesthetic designs, often with intricate carvings or finishes | Gift packaging, luxury items, display cases | Pros: High visual appeal, enhances product presentation. Cons: Higher price, may lack durability. |
Pallet Wooden Boxes | Sturdy construction, designed for heavy loads and shipping | Bulk shipping, warehouse storage | Pros: High durability, efficient transport. Cons: Bulky, may require special handling. |
Eco-Friendly Wooden Boxes | Made from sustainable materials, often biodegradable | Green products, eco-conscious brands | Pros: Supports sustainability, appeals to eco-conscious consumers. Cons: Potentially higher cost, availability issues. |
What Are the Key Characteristics of Custom Wooden Boxes?
Custom wooden boxes are designed specifically to meet the unique needs of businesses. They can be tailored in size, shape, and branding to ensure that they align with a company’s image and product requirements. This type of box is particularly suitable for businesses in retail and e-commerce, where packaging plays a critical role in branding. When considering a purchase, buyers should evaluate the potential for increased brand recognition against the higher costs and longer production times associated with custom orders.
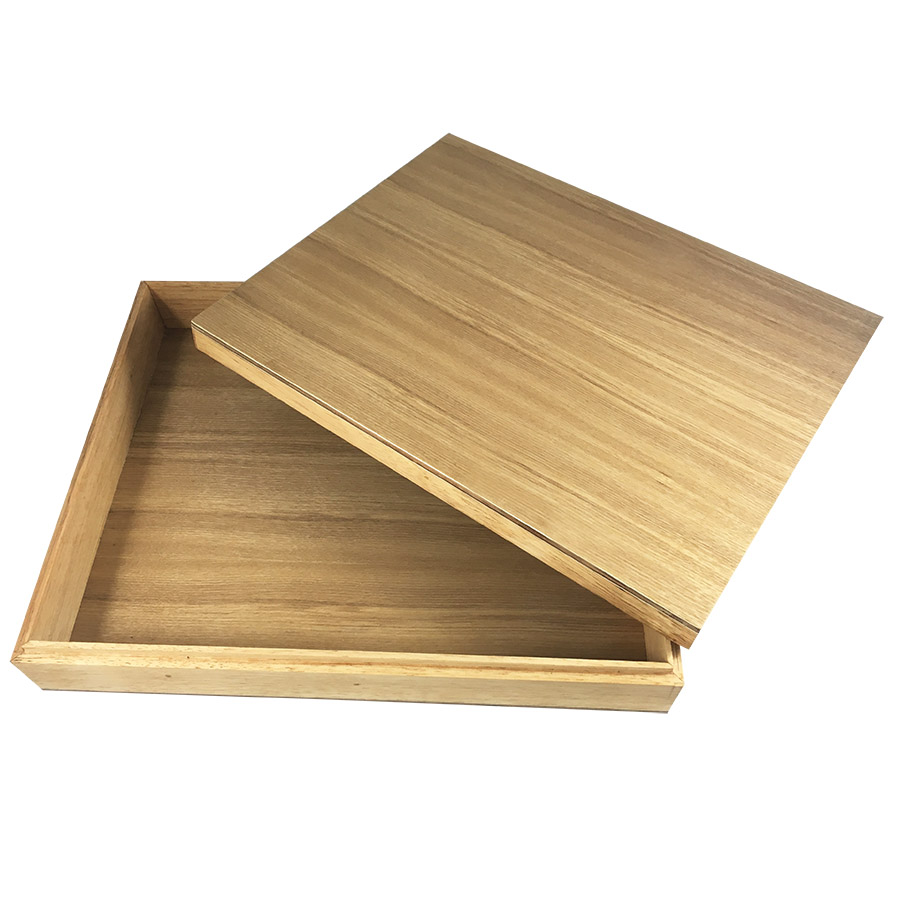
A stock image related to wooden boxe manufacturer.
How Do Standard Wooden Boxes Differ from Other Types?
Standard wooden boxes are mass-produced and come in predetermined sizes and designs. They are ideal for businesses looking for cost-effective packaging solutions for shipping and storage. The primary advantage of standard boxes is their availability in bulk, allowing for quick procurement. However, buyers should weigh the benefits of lower costs against the limitations in customization, which may not meet the specific needs of all products.
What Makes Decorative Wooden Boxes a Good Choice?
Decorative wooden boxes are crafted with a focus on aesthetic appeal, often featuring intricate designs and finishes. These boxes are perfect for high-end gift packaging or luxury items that require an impressive presentation. While they enhance the visual appeal of products, buyers should consider the higher price point and potential durability issues, especially if the boxes are intended for repeated use.
Why Are Pallet Wooden Boxes Essential for Heavy Loads?
Pallet wooden boxes are built to withstand heavy weights, making them ideal for bulk shipping and warehouse storage. Their robust construction ensures that they can handle the rigors of transportation and storage without compromising the integrity of the contents. Buyers should consider the efficiency of shipping and handling that pallet boxes offer, although they may require more space and special handling due to their bulkiness.
How Do Eco-Friendly Wooden Boxes Appeal to Modern Businesses?
Eco-friendly wooden boxes are made from sustainable materials and are often biodegradable, appealing to businesses that prioritize environmental responsibility. These boxes are particularly suitable for brands that market green products or target eco-conscious consumers. While they support sustainability initiatives, buyers should be mindful of the potentially higher costs and availability challenges associated with sourcing these eco-friendly options.
Related Video: Robotic Wooden Pallet Assembly System
Key Industrial Applications of wooden boxe manufacturer
Industry/Sector | Specific Application of Wooden Box Manufacturer | Value/Benefit for the Business | Key Sourcing Considerations for this Application |
---|---|---|---|
Agriculture | Packaging for fruits and vegetables | Protects perishable goods during transport, extends shelf life | Sustainable materials, compliance with food safety regulations |
Pharmaceuticals | Shipping containers for medical supplies | Ensures safe transport of sensitive products, maintains integrity | Temperature control, certifications for medical use |
Furniture & Home Decor | Custom crates for high-value furniture | Prevents damage during shipping, enhances brand image | Custom sizes, durable materials, aesthetic considerations |
Electronics | Protective packaging for electronic components | Reduces risk of damage, minimizes returns and replacements | Anti-static properties, shock absorption, weight limits |
Construction | Storage and transport of tools and materials | Organizes job sites, improves efficiency in material handling | Load capacity, weather resistance, size specifications |
How is Wooden Box Manufacturing Used in Agriculture?
In the agricultural sector, wooden boxes are widely used for packaging fruits and vegetables. These boxes provide essential protection against physical damage during transport, which is crucial for perishable goods. By using wooden boxes, businesses can extend the shelf life of their products, reducing waste and improving profitability. International buyers from regions like Africa and South America should consider sourcing boxes made from sustainable materials that comply with local and international food safety regulations, ensuring that their packaging is both eco-friendly and safe for consumer use.
What Role Does Wooden Box Manufacturing Play in Pharmaceuticals?
The pharmaceutical industry relies heavily on wooden boxes for the safe shipping of medical supplies. These boxes are designed to maintain the integrity of sensitive products, ensuring they arrive at their destination without compromising quality. For international B2B buyers, especially in the Middle East and Europe, sourcing wooden boxes that offer temperature control and adhere to strict medical packaging certifications is vital. This guarantees compliance with health regulations and enhances the reliability of their supply chain.
How Can Furniture and Home Decor Businesses Benefit from Wooden Boxes?
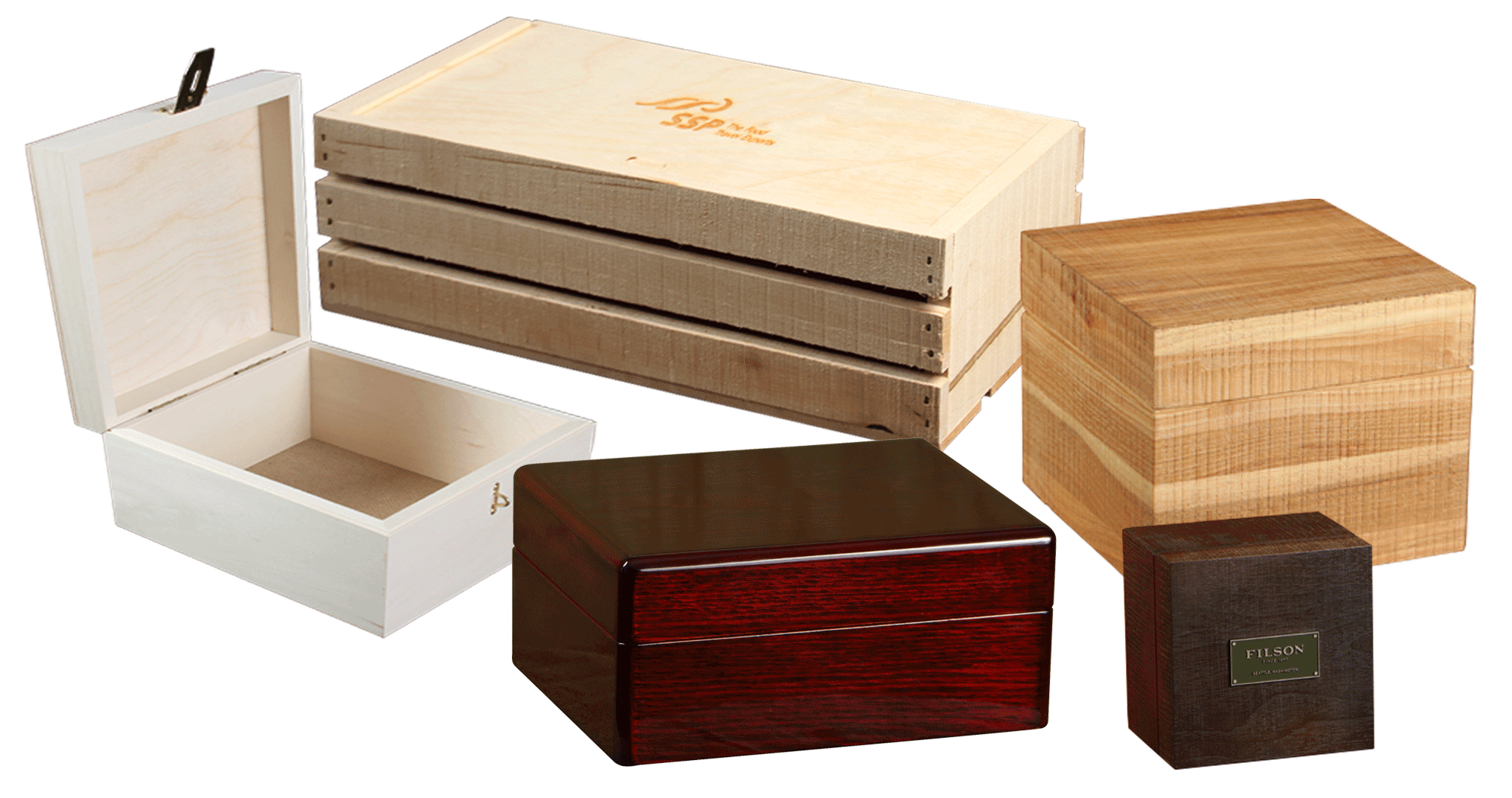
A stock image related to wooden boxe manufacturer.
In the furniture and home decor industry, custom wooden crates are essential for shipping high-value items. These crates not only prevent damage during transport but also enhance the brand image through attractive packaging. Buyers in Europe and other markets should focus on sourcing wooden boxes that meet specific size requirements and are made from durable materials to withstand the rigors of shipping. Customization options can also add significant value, allowing businesses to create a unique unboxing experience for their customers.
Why are Wooden Boxes Important for Electronics Packaging?
Wooden boxes are crucial in the electronics sector for packaging sensitive components. They provide robust protection against physical damage and minimize the risk of returns due to damaged goods. B2B buyers, particularly from Africa and South America, should prioritize sourcing boxes with anti-static properties and shock absorption features. This ensures that electronic products are transported safely, reducing losses and enhancing customer satisfaction.
How Do Wooden Boxes Facilitate Construction Material Handling?
In construction, wooden boxes are used for the storage and transport of tools and materials. They help organize job sites, improving efficiency in material handling. Buyers in this sector should consider the load capacity and weather resistance of wooden boxes when sourcing. Ensuring that these boxes meet specific size specifications is also crucial to maximize space and protect valuable equipment during transit.
Related Video: Sci6 Q3 – Characteristics and Uses of Simple Machines
3 Common User Pain Points for ‘wooden boxe manufacturer’ & Their Solutions
Scenario 1: Difficulty in Meeting Customization Requirements for Packaging
The Problem:
B2B buyers often face challenges when they require customized wooden boxes tailored to specific dimensions, designs, or branding requirements. For instance, a company in Kenya may need unique packaging to reflect local aesthetics while also adhering to international shipping standards. The inability to clearly communicate these specifications can lead to misunderstandings, resulting in boxes that do not meet their needs, causing delays in production and increased costs.
The Solution:
To effectively address this issue, B2B buyers should engage in thorough pre-order consultations with potential wooden box manufacturers. This involves providing detailed specifications, including measurements, design elements, and any necessary branding components. Utilizing CAD (Computer-Aided Design) software to create a visual representation of the desired product can facilitate clearer communication. Additionally, requesting prototypes before full-scale production can help ensure that the final product meets expectations. Establishing a collaborative relationship with the manufacturer can also lead to better customization options and improved turnaround times.
Scenario 2: Concerns About Sustainability and Compliance with Environmental Standards
The Problem:
With increasing global emphasis on sustainability, many B2B buyers, particularly in Europe and South America, are concerned about the environmental impact of their packaging choices. They may struggle to find wooden box manufacturers that use sustainably sourced materials and comply with international environmental regulations. This concern can complicate procurement processes and impact brand reputation if sustainable practices are not verified.
The Solution:
B2B buyers should prioritize manufacturers that hold certifications such as FSC (Forest Stewardship Council) or PEFC (Programme for the Endorsement of Forest Certification). These certifications ensure that the wood used is sourced sustainably. Buyers can also conduct audits or request transparency reports from manufacturers to verify compliance with environmental standards. Engaging in discussions about the manufacturer’s sourcing practices and production processes will provide insights into their commitment to sustainability. Additionally, incorporating eco-friendly designs, such as using minimal packaging or biodegradable materials, can further enhance a company’s commitment to environmental responsibility.
Scenario 3: Managing Logistics and Shipping Challenges with Wooden Boxes
The Problem:
International buyers frequently encounter logistics hurdles when dealing with wooden boxes, particularly concerning shipping costs, delays, and damage during transit. For instance, a company in the Middle East may find that the wooden boxes they ordered arrive damaged due to inadequate packaging or improper handling. This not only leads to financial losses but can also disrupt supply chains and affect customer satisfaction.
The Solution:
To mitigate logistics challenges, B2B buyers should work closely with their chosen wooden box manufacturer to develop a robust shipping strategy. This includes selecting appropriate packaging materials that can withstand the rigors of international transport and ensuring that boxes are reinforced at potential stress points. Buyers should also consider using manufacturers that offer logistics services or have partnerships with reliable shipping companies. Incorporating tracking solutions can provide real-time updates on shipments, allowing for proactive management of potential delays. By implementing these strategies, buyers can enhance the resilience of their supply chains and reduce the likelihood of damage during transit.
Strategic Material Selection Guide for wooden boxe manufacturer
What Are the Key Properties of Common Materials Used in Wooden Box Manufacturing?
When selecting materials for wooden boxes, manufacturers often consider various wood types and composite materials. Each material has distinct properties that affect product performance, durability, and suitability for specific applications.
1. Solid Wood
Key Properties: Solid wood is known for its natural strength and aesthetic appeal. It offers excellent temperature regulation and can withstand moderate pressure. However, its susceptibility to moisture can lead to warping or swelling if not treated properly.
Pros & Cons: Solid wood is highly durable and provides a premium look, making it suitable for high-end applications. However, the cost is relatively high, and manufacturing complexity increases due to the need for precise cuts and finishes.
Impact on Application: Solid wood is ideal for applications requiring a robust structure, such as shipping delicate items. However, its compatibility with certain media (like moisture-sensitive products) must be carefully evaluated.
Considerations for International Buyers: Buyers from regions like Africa and the Middle East should ensure compliance with local regulations regarding wood sourcing and treatment. Standards such as ASTM D198 and JIS Z 2101 may apply.
2. Plywood
Key Properties: Plywood consists of multiple layers of wood veneer glued together, providing excellent strength and stability. It has good resistance to warping and is less susceptible to moisture than solid wood.
Pros & Cons: Plywood is cost-effective and easier to manufacture than solid wood, making it a popular choice for mass production. However, it may not offer the same aesthetic appeal and can be less durable in extreme conditions.
Impact on Application: Plywood is suitable for a variety of applications, including packaging and storage. It can handle moderate loads but may not be ideal for heavy-duty uses.
Considerations for International Buyers: Compliance with international standards like EN 636 for plywood is crucial. Buyers should also consider the origin of the plywood to ensure it meets sustainability criteria.
3. Medium Density Fiberboard (MDF)
Key Properties: MDF is made from wood fibers bonded with resin under heat and pressure. It offers a smooth surface for painting and is less prone to warping than solid wood.
Pros & Cons: MDF is relatively inexpensive and easy to work with, making it suitable for intricate designs. However, it lacks the structural integrity of solid wood and can be sensitive to moisture, leading to swelling.
Impact on Application: MDF is ideal for decorative wooden boxes or items where aesthetics are prioritized over strength. It is not recommended for applications involving heavy loads or exposure to moisture.
Considerations for International Buyers: Buyers should be aware of VOC emissions from MDF, which may be regulated in certain regions. Compliance with standards such as ASTM E1333 is essential for safety.
4. Oriented Strand Board (OSB)
Key Properties: OSB is made from strands of wood arranged in layers and bonded with adhesives. It provides good strength and is more cost-effective than plywood.
Pros & Cons: OSB is durable and suitable for structural applications, but it can be less aesthetically pleasing. Its manufacturing process is simpler, which can reduce costs.
Impact on Application: OSB is commonly used in construction and packaging. It is suitable for applications requiring strength but should be protected from moisture exposure.
Considerations for International Buyers: Buyers should ensure compliance with local building codes and standards like ASTM D7032. Understanding the sourcing of OSB is also important for sustainability considerations.
Summary Table of Material Selection for Wooden Box Manufacturing
Material | Typical Use Case for Wooden Box Manufacturer | Key Advantage | Key Disadvantage/Limitation | Relative Cost (Low/Med/High) |
---|---|---|---|---|
Solid Wood | High-end packaging for delicate items | Premium aesthetic and durability | High cost and manufacturing complexity | High |
Plywood | General packaging and storage solutions | Cost-effective and stable | Less aesthetic appeal | Medium |
Medium Density Fiberboard | Decorative boxes and lightweight applications | Smooth surface for finishes | Sensitive to moisture | Low |
Oriented Strand Board | Structural applications in construction | Good strength and cost-effective | Less aesthetically pleasing | Medium |
This comprehensive analysis of materials provides international B2B buyers with actionable insights, helping them make informed decisions tailored to their specific needs and regional compliance requirements.
In-depth Look: Manufacturing Processes and Quality Assurance for wooden boxe manufacturer
What Are the Main Stages of Manufacturing Wooden Boxes?
The manufacturing of wooden boxes is a multi-step process that emphasizes precision and quality at every stage. Understanding these stages is crucial for B2B buyers, especially when sourcing from international suppliers.
-
Material Preparation: The process begins with selecting high-quality timber, which is often sourced from sustainable forests. The wood is then cut to size, dried, and treated to prevent pests and decay. Buyers should ensure that suppliers follow environmentally responsible practices and can provide documentation of wood sourcing.
-
Forming: This stage involves shaping the wood into the desired box dimensions. Techniques such as sawing, planing, and routing are commonly used. Advanced manufacturers may utilize CNC (Computer Numerical Control) machines to ensure precision. For B2B buyers, inquiring about the equipment and technology used can provide insights into the manufacturer’s capability to produce consistent quality.
-
Assembly: Once the wooden components are formed, they are assembled using various methods, including dovetail joints, screws, or nails. Adhesives may also be used to enhance durability. Understanding the assembly techniques can help buyers assess the strength and longevity of the boxes.
-
Finishing: The final stage includes sanding, staining, and sealing to achieve a polished look. Finishing not only enhances aesthetics but also protects the wood. Buyers should ask about the types of finishes used, as some may be more environmentally friendly or suitable for specific applications.
How Do Quality Assurance Processes Work in Wooden Box Manufacturing?
Quality assurance (QA) is critical in ensuring that the final products meet both international standards and customer expectations. Here’s a breakdown of the QA processes relevant to wooden box manufacturing.
-
Relevant International Standards: Compliance with international standards such as ISO 9001 is essential. This standard ensures that the manufacturer has a quality management system in place, focusing on continuous improvement and customer satisfaction. For specific applications, industry standards like CE marking for safety or API standards for oil and gas applications may also apply.
-
Quality Control Checkpoints:
– Incoming Quality Control (IQC): This step involves inspecting raw materials upon arrival. Buyers should ensure that suppliers have rigorous IQC processes to prevent defects from entering the production line.
– In-Process Quality Control (IPQC): During manufacturing, periodic checks are conducted to ensure adherence to specifications. This can include measuring dimensions and checking assembly integrity.
– Final Quality Control (FQC): Before shipment, finished products undergo a comprehensive inspection to ensure they meet all quality standards. This includes visual inspections, functional tests, and packaging checks. -
Common Testing Methods: Various testing methods are employed to verify the quality of wooden boxes. These may include moisture content tests, strength tests (to assess load-bearing capacity), and durability assessments (such as resistance to environmental factors). Buyers should request reports on these tests to validate product quality.
How Can B2B Buyers Verify Supplier Quality Control?
To ensure that suppliers maintain high standards of quality control, international B2B buyers can adopt several strategies:
-
Conducting Audits: Buyers should consider conducting on-site audits of potential suppliers. This allows for firsthand evaluation of manufacturing processes, quality control systems, and adherence to international standards.
-
Requesting Quality Reports: Suppliers should be able to provide detailed quality reports, including results from IQC, IPQC, and FQC. These documents should be transparent and easily accessible.
-
Engaging Third-Party Inspectors: Utilizing third-party inspection services can provide an unbiased evaluation of the manufacturer’s quality assurance processes. This is particularly useful for buyers in regions with different regulatory standards, such as Africa and South America.
What Are the Quality Control Nuances for International B2B Buyers?
International B2B buyers must navigate various nuances when dealing with suppliers from different regions, including Africa, South America, the Middle East, and Europe. Here are a few considerations:
-
Cultural Differences in Quality Standards: Different regions may have varying perceptions of quality. Understanding local standards and practices is essential for aligning expectations with suppliers.
-
Regulatory Compliance: Buyers should be aware of specific regulatory requirements for importing wooden products into their countries. For instance, the European Union has strict regulations regarding the importation of wood to prevent illegal logging and ensure sustainability.
-
Communication and Transparency: Establishing clear communication channels with suppliers can help mitigate misunderstandings regarding quality expectations. Regular updates and feedback can foster a collaborative relationship focused on quality improvement.
-
Sustainability Considerations: Increasingly, buyers are prioritizing suppliers that adhere to sustainable practices. Ensuring that suppliers comply with certifications such as FSC (Forest Stewardship Council) can enhance the credibility of the products being sourced.
In conclusion, understanding the manufacturing processes and quality assurance measures for wooden boxes is essential for B2B buyers seeking reliable suppliers. By focusing on material preparation, forming, assembly, and finishing, as well as implementing robust quality control practices, buyers can ensure they receive products that meet their needs and comply with international standards.
Practical Sourcing Guide: A Step-by-Step Checklist for ‘wooden boxe manufacturer’
To successfully procure wooden boxes from manufacturers, B2B buyers must navigate a structured sourcing process. This guide offers a step-by-step checklist tailored for international buyers, particularly those from Africa, South America, the Middle East, and Europe. By following these steps, you can ensure a smooth procurement process that meets your quality, cost, and delivery expectations.
Step 1: Define Your Technical Specifications
Clearly outlining your technical specifications is the foundation of the sourcing process. Identify the dimensions, materials, and design features required for the wooden boxes. This clarity not only helps in receiving accurate quotes but also ensures that suppliers understand your exact needs.
- Considerations:
- What type of wood is suitable for your product?
- Are there specific certifications required for the wood (e.g., FSC certification)?
Step 2: Research Potential Suppliers
Conduct thorough research to identify potential wooden box manufacturers. Look for suppliers with a solid reputation and experience in your specific market sector. Utilize online directories, industry trade shows, and trade associations to compile a list of candidates.
- Useful Tools:
- Online platforms like Alibaba, ThomasNet, or local business directories.
- Industry-specific trade shows or exhibitions.
Step 3: Evaluate Supplier Capabilities
Before committing to a supplier, assess their manufacturing capabilities. This includes evaluating production capacity, technology used, and their ability to meet your quality standards. A capable supplier should have the infrastructure to handle your order volume and complexity.
- What to Check:
- Production lead times and scalability.
- Quality control processes in place to ensure consistency.
Step 4: Verify Supplier Certifications
It’s essential to verify that your chosen suppliers possess the necessary certifications and compliance standards relevant to your industry. Certifications can indicate adherence to quality and environmental standards, giving you peace of mind about your procurement.
- Key Certifications:
- ISO 9001 for quality management.
- Environmental certifications like PEFC or FSC.
Step 5: Request Samples and Prototypes
Before finalizing your order, request samples or prototypes of the wooden boxes. This step allows you to assess the quality, craftsmanship, and suitability of the product for your needs.
- Important Aspects:
- Test for durability and finish.
- Evaluate if the samples meet your specifications and expectations.
Step 6: Negotiate Terms and Conditions
Once you’re satisfied with the suppliers and their products, it’s time to negotiate terms and conditions. Focus on pricing, payment terms, delivery timelines, and any potential penalties for delays or quality issues.
- Negotiation Tips:
- Be clear about your expectations.
- Look for long-term partnership opportunities that may yield better pricing.
Step 7: Establish a Communication Plan
Effective communication is vital throughout the sourcing process. Establish a communication plan that includes regular updates and feedback loops with your supplier to address any issues or changes promptly.
- Communication Tools:
- Use project management software or communication platforms like Slack or WhatsApp for real-time updates.
- Schedule regular check-ins to discuss progress and challenges.
By following this comprehensive checklist, B2B buyers can streamline their sourcing process for wooden boxes, ensuring that they partner with reliable manufacturers who can meet their specific needs.
Comprehensive Cost and Pricing Analysis for wooden boxe manufacturer Sourcing
What Are the Key Cost Components in Wooden Box Manufacturing?
When sourcing wooden boxes, understanding the cost structure is essential for international B2B buyers. The primary cost components include:
-
Materials: The choice of wood significantly impacts the cost. High-quality hardwoods such as oak or mahogany are more expensive than softwoods like pine. Additionally, treatments for durability can increase material costs.
-
Labor: Labor costs vary by region and can affect overall pricing. Countries with higher wage standards may have higher labor costs, but they often also provide skilled craftsmanship that can enhance product quality.
-
Manufacturing Overhead: This includes utilities, rent, and equipment depreciation. In regions with high energy costs or rent, these overheads can substantially influence pricing.
-
Tooling: The initial investment in tools and machinery can be significant. Custom tooling for specialized wooden boxes may incur additional costs.
-
Quality Control (QC): Implementing rigorous QC processes ensures that products meet standards, but it can also add to the overall cost. Buyers should consider the implications of QC on pricing, especially if certifications are required.
-
Logistics: Shipping costs can vary widely based on distance, mode of transportation, and the volume of the order. International buyers must factor in customs duties and taxes, which can further inflate costs.
-
Margin: Manufacturers typically include a profit margin in their pricing. Understanding the typical margins in your chosen market can aid in negotiations.
How Do Price Influencers Affect Wooden Box Costs?
Several factors can influence the pricing of wooden boxes:
-
Volume/MOQ (Minimum Order Quantity): Higher order volumes often lead to lower per-unit costs due to economies of scale. Buyers should negotiate MOQs that align with their needs while maximizing cost-efficiency.
-
Specifications and Customization: Custom designs or specific dimensions can increase costs. Clear communication of requirements can help manufacturers provide accurate quotes.
-
Materials and Quality Certifications: Premium materials and certifications (e.g., FSC certification) can elevate costs. Buyers should weigh the benefits of these factors against their budget constraints.
-
Supplier Factors: The reputation and reliability of the supplier can impact pricing. Established suppliers with a track record of quality may charge more but can provide peace of mind.
-
Incoterms: Understanding the terms of trade can affect pricing significantly. FOB (Free on Board) vs. CIF (Cost, Insurance, and Freight) can lead to different cost structures and responsibilities.
What Tips Can Help Buyers Negotiate Better Prices?
To ensure cost-effectiveness in sourcing wooden boxes, buyers should consider the following tips:
-
Engage in Negotiation: Don’t hesitate to negotiate terms and pricing with suppliers. Building a relationship can lead to better deals over time.
-
Focus on Cost-Efficiency: Analyze the Total Cost of Ownership (TCO), which includes purchase price, shipping, handling, and potential waste. This holistic view can uncover hidden costs.
-
Understand Pricing Nuances: International buyers, especially from regions like Africa, South America, the Middle East, and Europe, should be aware of currency fluctuations, trade tariffs, and regional pricing trends.
-
Request Indicative Prices: When starting discussions, ask for indicative prices to gauge the market before committing to larger orders. This can help in budgeting and planning.
Conclusion
Sourcing wooden boxes involves careful consideration of various cost components and price influencers. By understanding these elements and employing strategic negotiation tactics, international B2B buyers can achieve favorable terms and ensure the success of their procurement efforts. Always remember to request indicative prices and consider the Total Cost of Ownership to make informed decisions that align with your business objectives.
Alternatives Analysis: Comparing wooden boxe manufacturer With Other Solutions
When considering packaging solutions for various goods, international B2B buyers often face the decision of choosing between traditional and modern alternatives. The wooden box manufacturing industry has long been a staple due to its sustainability and strength. However, exploring alternatives can reveal additional options that may better suit specific needs.
Comparison Aspect | Wooden Boxe Manufacturer | Alternative 1: Plastic Crates | Alternative 2: Metal Containers |
---|---|---|---|
Performance | High durability and strength; ideal for heavy loads | Good for lightweight items; not as strong | Excellent for heavy and hazardous materials |
Cost | Moderate initial investment; long-term savings due to durability | Lower initial cost; may require more frequent replacement | Higher upfront cost; long lifespan |
Ease of Implementation | Requires skilled labor for custom designs | Lightweight and stackable; easy to transport | Heavy and may require additional equipment for handling |
Maintenance | Low maintenance; can be repaired easily | Susceptible to UV damage; may degrade over time | Requires periodic inspections for rust or corrosion |
Best Use Case | Ideal for artisanal goods, fragile items, or luxury products | Suitable for food and retail; efficient for bulk transport | Best for industrial applications and shipping hazardous materials |
What Are the Advantages and Disadvantages of Using Plastic Crates?
Plastic crates have gained popularity due to their lightweight nature and lower cost. They are stackable, making them easy to transport and store, which can be advantageous for businesses with limited space. However, while they are suitable for lightweight items, they may not provide the same level of durability as wooden boxes. Additionally, they can be affected by UV exposure, leading to degradation over time, which may necessitate more frequent replacements.
How Do Metal Containers Compare to Wooden Boxes?
Metal containers are another alternative that excels in specific scenarios, particularly for shipping hazardous materials or heavy loads. They provide excellent durability and protection against environmental factors. However, the initial investment is generally higher than that of wooden boxes, and they require regular maintenance to prevent rust and corrosion. Furthermore, their weight can make handling more cumbersome compared to lighter alternatives like plastic crates.
Conclusion: How Should B2B Buyers Choose the Right Packaging Solution?
When selecting the right packaging solution, B2B buyers should consider various factors, including the nature of the products, cost implications, and operational efficiency. Wooden boxes are an excellent choice for businesses that prioritize sustainability and need durable packaging for fragile or high-value items. In contrast, plastic crates offer cost-effective solutions for lighter goods, while metal containers are ideal for heavy or hazardous products. By evaluating these alternatives against specific requirements, international buyers can make informed decisions that align with their operational goals and market demands.
Essential Technical Properties and Trade Terminology for wooden boxe manufacturer
What Are the Essential Technical Properties of Wooden Boxes for B2B Buyers?
When sourcing wooden boxes for industrial use, understanding the critical technical properties is essential for ensuring product quality and suitability for your specific applications. Here are some key specifications to consider:
1. Material Grade: Why Is It Important?
The material grade of wood used in manufacturing wooden boxes significantly affects durability and performance. Common grades include select, standard, and industrial. For instance, select grade offers fewer knots and defects, making it ideal for high-end applications, while industrial grade may be suitable for more rugged uses. Buyers should assess the intended use of the boxes to choose the appropriate material grade, as this can impact both longevity and safety during transportation.
2. Dimensional Tolerance: What Should Buyers Know?
Dimensional tolerance refers to the allowable variations in the size of the wooden boxes. It is crucial for ensuring that boxes fit perfectly in storage or shipping containers. Tolerances can vary based on the manufacturing process and wood type. A tighter tolerance might be necessary for precision applications, while broader tolerances may suffice for less critical uses. Understanding these tolerances helps buyers avoid issues related to compatibility and fitting.
3. Load Capacity: How Does It Affect Your Choice?
Load capacity indicates the maximum weight a wooden box can safely carry. This property is vital for businesses that transport heavy goods. Load capacities are often determined by factors such as wood thickness, type, and construction method. B2B buyers should evaluate their product weights and choose boxes that exceed the required load capacity to ensure safety and reliability during transport.
4. Moisture Content: Why Is It Critical for Wooden Boxes?
Moisture content affects the stability and durability of wooden boxes. A high moisture content can lead to warping, cracking, and mold growth. Typically, moisture content is expressed as a percentage, with lower percentages indicating drier wood. B2B buyers should specify acceptable moisture levels to prevent damage during storage and transport, especially in humid climates.
5. Finish Type: What Are the Options Available?
The finish of wooden boxes can include coatings such as varnish, paint, or natural oil. Each finish offers different levels of protection against moisture, chemicals, and physical wear. For example, a waterproof finish is essential for boxes used in shipping perishable goods. Buyers should select finishes based on their specific environmental conditions and product requirements.
What Are Common Trade Terms in the Wooden Box Manufacturing Industry?
Familiarizing yourself with industry jargon can facilitate smoother transactions and negotiations. Here are some essential terms:
1. OEM (Original Equipment Manufacturer): What Does It Mean?
OEM refers to a company that produces parts or equipment that may be marketed by another manufacturer. In the context of wooden boxes, an OEM may supply custom designs or specifications that meet the requirements of a particular buyer. Understanding OEM relationships can help buyers secure tailored solutions for their specific needs.
2. MOQ (Minimum Order Quantity): How Does It Impact Procurement?
MOQ is the smallest number of units a supplier is willing to sell. This term is critical for B2B buyers as it can influence inventory management and cash flow. Understanding MOQs can assist businesses in planning their purchasing strategies and avoiding excess inventory.
3. RFQ (Request for Quotation): What Should Buyers Include?
An RFQ is a document that invites suppliers to submit price proposals for a specific quantity of goods. When creating an RFQ for wooden boxes, buyers should include specifications such as dimensions, material grades, and finish types to ensure accurate quotes. This process helps in comparing different suppliers effectively.
4. Incoterms: Why Are They Important in Shipping?
Incoterms (International Commercial Terms) define the responsibilities of buyers and sellers in international trade. They clarify who is responsible for shipping, insurance, and tariffs. For wooden box procurement, understanding these terms can help buyers manage risks and costs associated with international shipping.
5. FSC Certification: What Is Its Relevance?
FSC (Forest Stewardship Council) certification indicates that the wood used in the products comes from responsibly managed forests. For businesses focused on sustainability, seeking suppliers with FSC certification can enhance brand reputation and meet regulatory requirements.
By understanding these essential technical properties and trade terms, B2B buyers can make informed decisions when procuring wooden boxes, ensuring that their choices align with both their operational needs and sustainability goals.
Navigating Market Dynamics and Sourcing Trends in the wooden boxe manufacturer Sector
What Are the Current Market Dynamics and Key Trends in the Wooden Box Manufacturer Sector?
The wooden box manufacturing sector is experiencing significant growth driven by various global factors. Firstly, the increasing demand for sustainable packaging solutions across industries, particularly in food and beverage, cosmetics, and e-commerce, has been a game changer. International B2B buyers from regions like Africa, South America, the Middle East, and Europe are increasingly seeking suppliers that can provide high-quality wooden boxes that meet their sustainability goals.
Emerging technologies such as automation and digitalization are reshaping sourcing strategies. Manufacturers are adopting advanced machinery that not only enhances production efficiency but also allows for greater customization, catering to specific client needs. Additionally, the integration of e-commerce platforms is facilitating direct sourcing from manufacturers, reducing the reliance on intermediaries. This trend is particularly notable in markets like Kenya and Mexico, where businesses are leveraging online platforms to streamline procurement processes.
Another significant trend is the increased focus on supply chain transparency. Buyers are now more informed and concerned about the origins of their materials, leading to a demand for detailed sourcing information. This shift is prompting manufacturers to adopt more robust tracking systems and certifications to assure buyers of ethical practices.
How Important Is Sustainability and Ethical Sourcing in the Wooden Box Manufacturer Sector?
Sustainability is becoming a cornerstone of business strategies in the wooden box manufacturing sector. The environmental impact of wood sourcing and production processes is under scrutiny, prompting B2B buyers to seek suppliers who prioritize sustainable practices. This includes responsible sourcing of timber, which is increasingly being demanded by clients in Europe and North America.
Ethical supply chains are not just a trend; they are a necessity for long-term viability. Buyers are looking for manufacturers that can provide proof of sustainable practices, such as adherence to Forest Stewardship Council (FSC) certification or similar green certifications. These certifications indicate that the wood used is sourced from responsibly managed forests, ensuring minimal impact on the environment.
Moreover, the use of eco-friendly materials and production methods is gaining traction. Buyers are increasingly interested in wooden boxes that are not only functional but also recyclable or made from reclaimed wood. This shift towards sustainable and ethical sourcing not only meets consumer demands but also positions businesses favorably in a competitive market.
What Is the Historical Context of the Wooden Box Manufacturing Sector?
The wooden box manufacturing sector has a rich history that dates back centuries, originally emerging from the need for durable and reliable packaging solutions. Traditionally, wooden boxes were hand-crafted, with artisans focusing on quality and functionality. Over time, the industrial revolution introduced mechanization, allowing for mass production and standardization of wooden boxes.
In the late 20th century, the focus began to shift towards sustainability, influenced by growing environmental awareness. This evolution is particularly relevant for today’s B2B buyers who prioritize ethical sourcing and sustainability in their procurement decisions. Understanding this historical context helps buyers appreciate the advancements in technology and the ongoing commitment to sustainable practices in the wooden box manufacturing sector, which now caters to a more conscious consumer base.
By leveraging this knowledge, international B2B buyers can make informed decisions that align with their values and business goals.
Frequently Asked Questions (FAQs) for B2B Buyers of wooden boxe manufacturer
-
How can I ensure the quality of wooden boxes from a manufacturer?
To ensure quality, start by vetting potential manufacturers through reviews, certifications, and quality assurance processes. Request samples to assess craftsmanship and material quality. Consider manufacturers who comply with international standards, such as ISO certifications. Establish clear quality control protocols in your contracts, including inspections at various production stages. Finally, maintain open communication to address any quality concerns promptly. -
What are the key factors to consider when selecting a wooden box manufacturer?
Key factors include the manufacturer’s experience, production capacity, and specialization in wooden boxes. Evaluate their ability to meet your specific requirements, such as dimensions, materials, and design features. Additionally, consider their compliance with international shipping standards, lead times, and customer service. Request references from other B2B buyers to gauge reliability and responsiveness. -
What customization options are typically available for wooden boxes?
Most manufacturers offer various customization options, including size, wood type, finishes, and branding elements like logos and colors. Discuss your specific needs with the manufacturer to explore available options and any associated costs. Some manufacturers may also provide design services to help you create a unique product. Ensure that your customization requirements are clearly outlined in your initial discussions to avoid misunderstandings later. -
What is the minimum order quantity (MOQ) for wooden boxes?
MOQs can vary significantly between manufacturers, often ranging from a few dozen to several hundred units. Factors influencing MOQ include the type of wooden box, production processes, and material costs. It’s advisable to communicate your needs upfront to find a manufacturer willing to accommodate smaller orders if necessary. Negotiating MOQs can sometimes yield favorable terms, especially for long-term partnerships. -
What payment terms should I expect when dealing with wooden box manufacturers?
Payment terms can vary, but common arrangements include a deposit (usually 30-50%) before production and the balance upon delivery or before shipping. Some manufacturers may offer credit terms for established relationships. It’s crucial to clarify payment terms upfront and ensure they align with your cash flow needs. Consider using secure payment methods to protect your investment during transactions. -
How do I handle logistics and shipping for my wooden boxes?
When sourcing wooden boxes internationally, coordinate closely with your manufacturer regarding shipping options. Discuss whether they offer shipping services or if you’ll need to arrange logistics through a freight forwarder. Understand the shipping costs, estimated delivery times, and customs requirements specific to your country. Ensure proper packaging to prevent damage during transit and consider insurance for high-value shipments. -
What are the common challenges in international trade for wooden boxes?
Common challenges include navigating customs regulations, tariffs, and potential delays in shipping. Additionally, communication barriers may arise if manufacturers are in different time zones or speak different languages. To mitigate these issues, work with experienced freight forwarders who understand the specifics of international shipping. Establish clear lines of communication with your manufacturer to address any concerns promptly. -
How can I verify the legitimacy of a wooden box manufacturer?
To verify legitimacy, conduct thorough research on the manufacturer’s background, including their business registration and operational history. Look for customer reviews and testimonials, and request references from other clients. Utilize platforms like LinkedIn to view company profiles and employee connections. If possible, arrange a factory visit or request a virtual tour to assess their operations and practices firsthand.
Important Disclaimer & Terms of Use
⚠️ Important Disclaimer
The information provided in this guide, including content regarding manufacturers, technical specifications, and market analysis, is for informational and educational purposes only. It does not constitute professional procurement advice, financial advice, or legal advice.
While we have made every effort to ensure the accuracy and timeliness of the information, we are not responsible for any errors, omissions, or outdated information. Market conditions, company details, and technical standards are subject to change.
B2B buyers must conduct their own independent and thorough due diligence before making any purchasing decisions. This includes contacting suppliers directly, verifying certifications, requesting samples, and seeking professional consultation. The risk of relying on any information in this guide is borne solely by the reader.
Strategic Sourcing Conclusion and Outlook for wooden boxe manufacturer
What Are the Key Takeaways for B2B Buyers in the Wooden Box Manufacturing Sector?
In conclusion, the strategic sourcing of wooden boxes presents a unique opportunity for international B2B buyers, particularly in regions like Africa, South America, the Middle East, and Europe. Prioritizing suppliers who demonstrate sustainable practices and quality craftsmanship is crucial, as these factors significantly impact both product integrity and brand reputation. Additionally, leveraging local suppliers can enhance logistics efficiency and reduce lead times, offering a competitive edge in the marketplace.
How Can Strategic Sourcing Enhance Your Business Operations?
The value of strategic sourcing cannot be overstated. It allows companies to not only reduce costs but also to innovate their supply chains by forming strategic partnerships with manufacturers that align with their values and objectives. As markets become increasingly interconnected, adopting a proactive approach to sourcing will position businesses favorably against competitors.
What Should International Buyers Consider Moving Forward?
Looking ahead, B2B buyers are encouraged to remain vigilant and adaptable to emerging trends in the wooden box manufacturing industry. Engaging in continuous dialogue with suppliers and investing in technology to enhance supply chain visibility will be essential. By doing so, businesses can not only meet the evolving demands of their customers but also contribute positively to sustainable practices in the industry. Now is the time to take actionable steps towards optimizing your sourcing strategy and establishing meaningful partnerships that drive growth and innovation.