Discover Top Benefits of Aerial Work Platform Manufacturers (2025)
Introduction: Navigating the Global Market for aerial work platform manufacturer
In an increasingly interconnected world, sourcing aerial work platforms has become a pivotal challenge for international B2B buyers. As industries across Africa, South America, the Middle East, and Europe strive to enhance operational efficiency, the demand for reliable aerial work platforms continues to surge. However, navigating the global market can be daunting due to varying quality standards, supplier credibility, and regional regulations. This guide aims to demystify the complexities of selecting the right aerial work platform manufacturer for your specific needs.
Our comprehensive overview covers a range of essential topics, including the different types of aerial work platforms available, their diverse applications across various sectors, and critical factors to consider when vetting suppliers. We delve into cost considerations, helping you understand not just the initial investment but also the long-term value these platforms can provide. By equipping you with actionable insights and practical tips, this guide empowers B2B buyers from regions like Colombia and Nigeria to make informed purchasing decisions, ensuring that your investment aligns with your operational goals.
Whether you are looking to enhance safety standards in construction, streamline logistics in warehousing, or improve maintenance operations in manufacturing, understanding the aerial work platform market is essential. With this guide, you will gain the knowledge necessary to navigate the complexities of global sourcing effectively, ultimately driving your business success.
Understanding aerial work platform manufacturer Types and Variations
Type Name | Key Distinguishing Features | Primary B2B Applications | Brief Pros & Cons for Buyers |
---|---|---|---|
Scissor Lifts | Vertical lifting mechanism, compact design | Warehousing, maintenance, construction | Pros: Stable, cost-effective. Cons: Limited horizontal reach. |
Boom Lifts | Extendable arm for reaching heights and distances | Construction, film production, maintenance | Pros: Versatile reach, great for uneven terrain. Cons: Higher cost, more complex operation. |
Telescopic Forklifts | Forklift with extendable boom for lifting and moving loads | Construction, agriculture, logistics | Pros: Multi-functional, excellent load capacity. Cons: Limited maneuverability in tight spaces. |
Aerial Work Platforms (AWPs) | General term for platforms with various configurations | Utilities, maintenance, inspection | Pros: Wide range of applications, various designs. Cons: Can be expensive, requires operator training. |
Trailer-Mounted Lifts | Portable lifts mounted on trailers for easy transport | Outdoor events, tree trimming | Pros: Highly portable, quick setup. Cons: Stability can be an issue on uneven ground. |
What Are Scissor Lifts and Their B2B Applications?
Scissor lifts are characterized by their vertical lifting mechanism, which allows for significant height access while maintaining a compact footprint. They are particularly suitable for tasks in warehousing, maintenance, and construction where stability is crucial. When considering a scissor lift, B2B buyers should evaluate the lift’s weight capacity, platform size, and whether it operates on electric or diesel power. Buyers in regions like Nigeria or Colombia may prioritize electric models for indoor use to minimize emissions.
How Do Boom Lifts Differ from Other Aerial Work Platforms?
Boom lifts feature an extendable arm that provides access to hard-to-reach areas, making them ideal for construction, film production, and maintenance tasks. Their versatility in reaching both height and distance is a significant advantage, especially in complex job sites. B2B buyers should consider the lift’s range of motion, weight capacity, and terrain adaptability. In the Middle East, where construction projects are often expansive, boom lifts can significantly enhance efficiency.
What Are the Benefits of Telescopic Forklifts for B2B Buyers?
Telescopic forklifts combine the capabilities of a forklift with an extendable boom, allowing for the lifting and moving of heavy loads across various terrains. Commonly used in construction, agriculture, and logistics, they are favored for their multi-functional capabilities. Buyers should assess the load capacity, boom extension, and overall vehicle dimensions to ensure suitability for their specific operational needs. In South America, where agricultural applications are prevalent, these forklifts can facilitate efficient material handling.
Why Are Aerial Work Platforms Important in Various Industries?
Aerial Work Platforms (AWPs) encompass a broad range of equipment designed for elevated work. They are essential in utilities, maintenance, and inspection tasks. Their versatility allows for various designs and functionalities tailored to specific applications. When purchasing AWPs, B2B buyers should consider factors such as safety features, ease of transport, and operator training requirements. In Europe, where stringent safety regulations are in place, investing in high-quality AWPs can mitigate risks and enhance productivity.
What Makes Trailer-Mounted Lifts a Viable Option for B2B Buyers?
Trailer-mounted lifts are portable solutions that can be easily transported to different job sites, making them ideal for outdoor events and tree trimming. Their quick setup and mobility are significant advantages, but buyers should be cautious about stability on uneven ground. When considering a trailer-mounted lift, it’s crucial to evaluate the lift’s height capacity, weight restrictions, and ease of towing. This type of lift can be particularly beneficial in the diverse landscapes found in regions like Africa, where job sites may vary widely.
Related Video: Aerial Work Platform Safety Training
Key Industrial Applications of aerial work platform manufacturer
Industry/Sector | Specific Application of aerial work platform manufacturer | Value/Benefit for the Business | Key Sourcing Considerations for this Application |
---|---|---|---|
Construction | High-rise building maintenance and construction | Enhances worker safety and productivity on-site | Load capacity, reach height, and terrain adaptability |
Oil & Gas | Equipment maintenance in offshore rigs | Reduces downtime and operational costs | Corrosion resistance, mobility on uneven surfaces |
Telecommunications | Installation and maintenance of cell towers | Improves service reliability and customer satisfaction | Stability, platform size, and weather resistance |
Warehousing and Logistics | Inventory management and stocktaking | Increases efficiency in storage operations | Maneuverability in tight spaces and lift capacity |
Renewable Energy | Installation of wind turbines and solar panels | Supports sustainable energy initiatives and reduces costs | Compatibility with various terrains and equipment |
How Are Aerial Work Platforms Used in Construction?
In the construction industry, aerial work platforms (AWPs) are essential for high-rise building maintenance and construction tasks. They provide safe access to elevated areas, enhancing worker safety and productivity. For international buyers, especially in regions like Africa and South America, sourcing platforms that meet local safety regulations and can withstand diverse weather conditions is crucial. Buyers should also consider the load capacity and reach height to ensure they can handle the specific demands of their projects.
What Role Do Aerial Work Platforms Play in Oil & Gas?
In the oil and gas sector, aerial work platforms are utilized for equipment maintenance on offshore rigs. These platforms allow technicians to access hard-to-reach areas safely, significantly reducing downtime and operational costs. For B2B buyers in the Middle East, where offshore drilling is prevalent, it is vital to source AWPs that are corrosion-resistant and capable of operating on uneven surfaces. Understanding the specific environmental conditions and compliance with industry standards is essential for effective procurement.
How Are Aerial Work Platforms Essential for Telecommunications?
Telecommunications companies depend on aerial work platforms for the installation and maintenance of cell towers. These platforms enable technicians to work at heights safely, which is crucial for improving service reliability and customer satisfaction. Buyers in Europe and Africa should prioritize sourcing AWPs that offer stability and are suited for the specific heights of their tower installations. Weather resistance is another key consideration, as it ensures that equipment remains operational in various conditions.
How Do Aerial Work Platforms Improve Efficiency in Warehousing and Logistics?
In warehousing and logistics, aerial work platforms facilitate inventory management and stocktaking operations. They allow workers to reach high shelves safely and efficiently, significantly increasing productivity in storage operations. For international buyers, particularly in developing markets, maneuverability in tight spaces is a critical factor when sourcing AWPs. Additionally, lift capacity must align with the types of goods being handled to optimize operations and ensure safety.
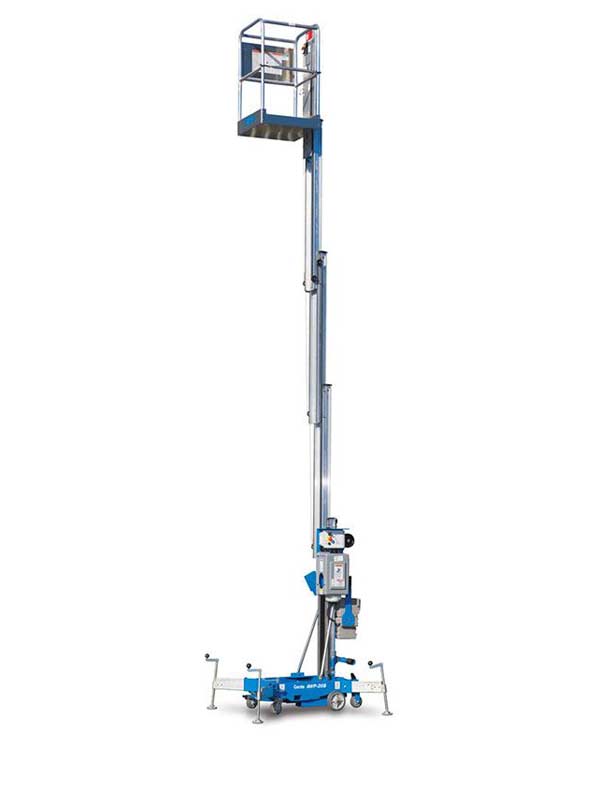
A stock image related to aerial work platform manufacturer.
What Is the Importance of Aerial Work Platforms in Renewable Energy?
Aerial work platforms are critical for the installation of renewable energy solutions, such as wind turbines and solar panels. They support sustainable energy initiatives by allowing for efficient and safe installation processes, which can ultimately reduce costs. Buyers from regions like South America and Africa should focus on sourcing platforms that are compatible with various terrains and can support the specific equipment used in renewable energy installations. Understanding local regulations and environmental conditions is also vital for successful implementation.
Related Video: Scissor Lift Aerial Work Platform SC Series of Noblelift
3 Common User Pain Points for ‘aerial work platform manufacturer’ & Their Solutions
Scenario 1: Navigating Complex Compliance Regulations in Different Regions
The Problem: B2B buyers in regions such as Africa and the Middle East often face challenges related to compliance with local safety and operational regulations when sourcing aerial work platforms (AWPs). The diverse regulatory landscape can lead to confusion about which standards must be met, resulting in delays and potential fines. For instance, a construction company in Nigeria may struggle to ensure that its chosen aerial work platform aligns with the country’s specific safety requirements, while also considering international standards.
The Solution: To navigate these complexities, buyers should conduct thorough research into both local and international regulations governing aerial work platforms. Engaging with a manufacturer that has a proven track record of compliance in multiple regions can provide a competitive advantage. It’s advisable to request detailed documentation of compliance certifications and safety standards from manufacturers. Furthermore, participating in industry forums or workshops can help buyers stay updated on regulatory changes. Lastly, consider partnering with local consultants who specialize in compliance to facilitate a smoother procurement process.
Scenario 2: Managing Equipment Downtime and Maintenance Challenges
The Problem: One of the pressing pain points for B2B buyers is the high cost and frequency of equipment downtime due to maintenance issues. Companies often invest heavily in aerial work platforms but face unexpected breakdowns that halt operations, leading to financial losses. For example, a construction firm in Colombia might find that its AWPs require more frequent repairs than anticipated, affecting project timelines and budget allocations.
The Solution: To mitigate downtime, buyers should prioritize purchasing aerial work platforms with robust warranties and service agreements. Before making a purchase, it’s essential to inquire about the manufacturer’s maintenance protocols and the availability of spare parts. Establishing a preventive maintenance schedule can also help identify potential issues before they escalate. Additionally, consider investing in training programs for staff to ensure that operators are well-versed in proper usage and maintenance practices, which can significantly reduce wear and tear on the equipment.
Scenario 3: Overcoming Limited Access to Specialized Equipment
The Problem: In emerging markets across Africa and South America, B2B buyers often struggle with limited access to specialized aerial work platforms needed for unique projects. This can be particularly challenging for industries such as oil and gas, where specific types of AWPs are essential for operational efficiency. For instance, a company in Angola may find that the required equipment for offshore drilling operations is not readily available, leading to project delays and increased costs.
The Solution: To address this issue, buyers should establish relationships with manufacturers that offer a diverse range of aerial work platforms, including customized options. Engaging in direct discussions with manufacturers about specific project requirements can lead to the development of tailored solutions. Additionally, consider leveraging regional distributors who have a better understanding of local market needs and can facilitate access to specialized equipment. Utilizing technology, such as online platforms, can also help buyers discover available AWPs in the international market, thereby expanding their options and minimizing delays in project execution.
Strategic Material Selection Guide for aerial work platform manufacturer
When selecting materials for aerial work platforms (AWPs), manufacturers must consider various factors that influence performance, durability, and cost-effectiveness. This guide analyzes four common materials used in the construction of AWPs—steel, aluminum, composite materials, and fiberglass—focusing on their properties, advantages, disadvantages, and specific considerations for international B2B buyers, particularly from regions such as Africa, South America, the Middle East, and Europe.
What Are the Key Properties of Steel in Aerial Work Platforms?
Steel is a widely used material in aerial work platforms due to its strength and durability. It typically has a high tensile strength, making it suitable for heavy lifting and supporting significant loads. Steel structures can withstand high temperatures and pressures, which is essential for AWPs operating in demanding environments. Additionally, steel’s corrosion resistance can be enhanced through galvanization or coatings, making it suitable for outdoor applications.
Pros & Cons:
– Pros: High strength-to-weight ratio, excellent durability, and cost-effective for large-scale production.
– Cons: Heavier than alternatives, which can impact mobility and fuel efficiency. Requires protective coatings to prevent corrosion, adding to maintenance costs.
Impact on Application:
Steel AWPs are ideal for heavy-duty tasks in construction and industrial settings. However, they may be less suitable for environments with high humidity or corrosive substances unless adequately treated.
Considerations for International Buyers:
Buyers in regions like Nigeria and Colombia should ensure compliance with local standards such as ASTM or DIN. The availability of high-quality steel may vary, impacting lead times and costs.
How Does Aluminum Compare as a Material for Aerial Work Platforms?
Aluminum is another popular choice for aerial work platforms, known for its lightweight properties and resistance to corrosion. This material is particularly advantageous for applications that require frequent relocation or transport. Aluminum can be extruded into complex shapes, allowing for innovative designs that enhance functionality.
Pros & Cons:
– Pros: Lightweight, which improves fuel efficiency and ease of transport; excellent corrosion resistance; and good strength-to-weight ratio.
– Cons: Generally more expensive than steel; lower tensile strength, which may limit load-bearing capacity.
Impact on Application:
Aluminum AWPs are ideal for indoor applications or environments where weight is a critical factor. They are often used in maintenance and installation tasks in commercial buildings.
Considerations for International Buyers:
In regions like the Middle East, where high temperatures can affect material performance, buyers should verify that the aluminum used meets specific thermal resistance standards.
What Role Do Composite Materials Play in Aerial Work Platforms?
Composite materials, such as fiberglass-reinforced plastics, are increasingly being utilized in aerial work platforms due to their lightweight and high strength. These materials offer excellent resistance to corrosion and can be molded into complex shapes, providing design flexibility.
Pros & Cons:
– Pros: Lightweight, high resistance to chemicals and corrosion, and design versatility.
– Cons: Higher manufacturing complexity and costs; may not be suitable for heavy-duty applications.
Impact on Application:
Composites are particularly effective in environments where chemical exposure is a concern, such as in the oil and gas industry. However, their use may be limited in heavy construction applications due to strength limitations.
Considerations for International Buyers:
Buyers from South America should consider local regulations regarding composite materials, as compliance may differ from traditional materials like steel and aluminum.
Why Choose Fiberglass for Aerial Work Platforms?
Fiberglass is another alternative that offers a unique combination of strength and lightweight characteristics. It is particularly known for its excellent resistance to environmental factors such as UV radiation and moisture.
Pros & Cons:
– Pros: Exceptional corrosion resistance, lightweight, and low maintenance.
– Cons: More expensive than traditional materials; can be brittle under certain conditions.
Impact on Application:
Fiberglass AWPs are suitable for marine or coastal applications where corrosion is a significant concern. However, they may not be ideal for heavy lifting tasks.
Considerations for International Buyers:
European buyers should be aware of the specific manufacturing standards for fiberglass, which may include compliance with EU regulations on safety and material properties.
Summary Table of Material Selection for Aerial Work Platforms
Material | Typical Use Case for aerial work platform manufacturer | Key Advantage | Key Disadvantage/Limitation | Relative Cost (Low/Med/High) |
---|---|---|---|---|
Steel | Heavy-duty construction AWPs | High strength and durability | Heavier, requires protective coatings | Medium |
Aluminum | Indoor maintenance and installation AWPs | Lightweight and corrosion-resistant | More expensive, lower load capacity | High |
Composite | Chemical exposure environments | Excellent corrosion resistance | Higher manufacturing complexity | High |
Fiberglass | Marine applications | Exceptional resistance to UV/moisture | Brittle under certain conditions | Medium |
This guide aims to assist international B2B buyers in making informed decisions regarding material selection for aerial work platforms, considering both performance and regional compliance factors.
In-depth Look: Manufacturing Processes and Quality Assurance for aerial work platform manufacturer
What Are the Key Stages in the Manufacturing Process of Aerial Work Platforms?
Manufacturing aerial work platforms (AWPs) involves a series of well-defined stages, each crucial for ensuring the final product’s safety, reliability, and performance. Understanding these stages helps B2B buyers assess the capabilities of manufacturers and make informed purchasing decisions.
Material Preparation: How Is Raw Material Selected and Processed?
The first stage in manufacturing AWPs is material preparation. Manufacturers typically use high-strength steel and aluminum alloys for their lightweight yet durable properties. The selection process often involves evaluating material specifications against industry standards to ensure they meet performance requirements.
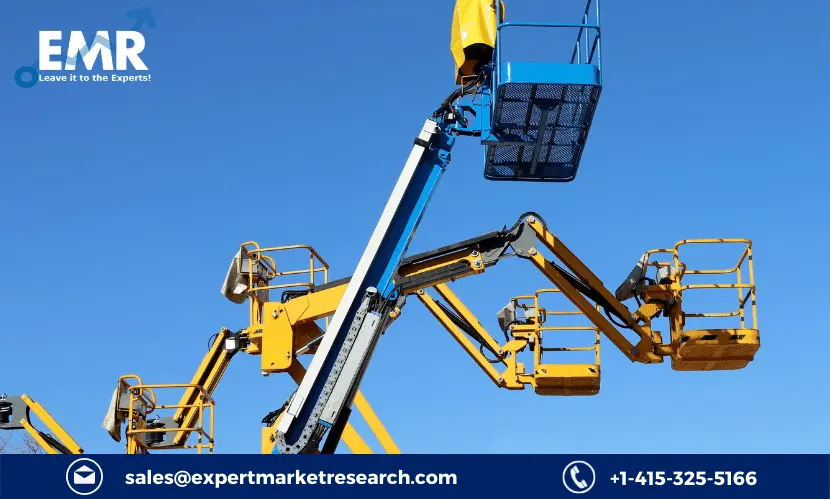
A stock image related to aerial work platform manufacturer.
Once selected, materials undergo cutting and machining processes. Techniques such as laser cutting and CNC machining are common, allowing for precision in shaping components. Buyers should inquire about the source of raw materials and whether they comply with international quality standards, as this significantly impacts the durability of the final product.
What Techniques Are Employed in the Forming Process?
Following material preparation, the forming process shapes the components that will make up the AWP. Techniques such as bending, stamping, and welding are employed to create the frame and other structural elements. Advanced manufacturing technologies, including robotic welding, are increasingly used to enhance precision and consistency.
For B2B buyers, understanding the forming techniques can provide insight into the manufacturer’s capabilities. It’s important to ask for information on the technology used and whether it aligns with best practices in the industry. This can help in evaluating the potential longevity and robustness of the aerial work platforms.
How Does the Assembly Process Ensure Product Integrity?
The assembly phase is critical for integrating various components, including the hydraulic systems, control panels, and safety features. A typical assembly line might utilize modular construction techniques, allowing for flexibility and efficiency in production.
Quality control during assembly is paramount. Manufacturers often implement rigorous checks to ensure that all components fit together correctly and function as intended. B2B buyers should consider asking about the assembly processes and whether there are provisions for customization to meet specific operational needs.
What Finishing Techniques Are Used to Enhance Durability?
Finishing processes, such as painting and coating, are essential for protecting AWPs from environmental factors. Manufacturers typically use powder coating or electrostatic painting techniques, which provide a durable, weather-resistant finish.
Buyers should inquire about the finishing processes and the materials used, as these can significantly affect the equipment’s lifespan and maintenance needs. Additionally, understanding the warranty and service options related to finishing can provide further assurance of quality.
How Is Quality Assurance Implemented in Aerial Work Platform Manufacturing?
Quality assurance (QA) is a critical component of the manufacturing process, ensuring that aerial work platforms meet stringent safety and performance standards. For B2B buyers, understanding the QA measures in place can help in selecting reliable suppliers.
Which International Standards Should Buyers Be Aware Of?
Manufacturers often adhere to international quality standards such as ISO 9001, which emphasizes continuous improvement and customer satisfaction. Additionally, industry-specific certifications like CE (Conformité Européenne) for European markets and API (American Petroleum Institute) standards for certain applications are important.
Buyers should verify that the manufacturer holds relevant certifications and inquire about the processes they follow to maintain compliance. This not only reflects the manufacturer’s commitment to quality but also provides assurance that the products are safe and reliable.
What Are the Key Quality Control Checkpoints in Manufacturing?
Quality control checkpoints are integral to the manufacturing process. Typically, these checkpoints include:
-
Incoming Quality Control (IQC): This stage involves inspecting raw materials before they enter the production process to ensure they meet specified standards.
-
In-Process Quality Control (IPQC): Conducted during manufacturing, IPQC checks ensure that processes are followed correctly and that products are being produced to specification.
-
Final Quality Control (FQC): At this stage, the completed aerial work platforms are thoroughly tested and inspected before shipment. This includes functionality tests and safety checks.
B2B buyers should ask manufacturers about their quality control protocols and the frequency of inspections at each checkpoint to assess the reliability of the production process.
What Testing Methods Are Commonly Used in Quality Assurance?
Common testing methods for aerial work platforms include load testing, stability testing, and functional testing. These tests verify that the equipment can safely support the specified loads and operate correctly under various conditions.
Buyers should request documentation of testing results and certifications to ensure that the products meet industry safety standards. Understanding the testing procedures helps buyers gauge the reliability and safety of the equipment.
How Can B2B Buyers Verify Supplier Quality Control Practices?
Verifying a supplier’s quality control practices is essential for B2B buyers. Here are several methods to ensure that a manufacturer meets required standards:
-
Conduct Audits: Regular audits of the manufacturing facility can help buyers assess compliance with quality standards and manufacturing processes. Buyers should consider third-party audits for an unbiased evaluation.
-
Request Quality Reports: Suppliers should be able to provide quality assurance reports detailing their processes, inspections, and test results. Reviewing these documents can give buyers confidence in the supplier’s commitment to quality.
-
Utilize Third-Party Inspection Services: Engaging third-party inspection services can provide an additional layer of assurance. These services can verify that products meet specified quality standards before shipment.
-
Understand Certification Nuances: For international buyers, it’s crucial to understand the nuances of certifications in different regions. For example, CE certification is mandatory for products sold in Europe, while different standards may apply in Africa or South America.
In conclusion, a thorough understanding of the manufacturing processes and quality assurance practices in aerial work platform production is essential for B2B buyers. By focusing on key stages, quality control measures, and verification methods, buyers can make informed decisions and select manufacturers that meet their operational needs.
Practical Sourcing Guide: A Step-by-Step Checklist for ‘aerial work platform manufacturer’
The purpose of this guide is to provide international B2B buyers with a practical checklist to streamline the sourcing process for aerial work platforms. This equipment is essential for various industries, including construction, maintenance, and logistics, and ensuring you select the right manufacturer can significantly impact operational efficiency and safety.
Step 1: Define Your Technical Specifications
Before initiating the sourcing process, clearly outline your technical requirements for the aerial work platform. Consider factors such as load capacity, height reach, mobility (e.g., wheeled vs. tracked), and safety features. A detailed specification helps in filtering manufacturers who can meet your precise needs and ensures compatibility with your operational environment.
Step 2: Research Market Trends and Innovations
Stay informed about the latest trends and technological advancements in aerial work platforms. Understanding market shifts, such as the rise of electric models or smart technology integration, can influence your purchasing decision. Researching these trends enables you to choose a manufacturer that not only meets current demands but also aligns with future industry developments.
Step 3: Evaluate Potential Suppliers
Thoroughly vet potential suppliers to ensure they can deliver quality products. Request company profiles, case studies, and references from previous clients within your industry. Look for suppliers with a proven track record of reliability and customer satisfaction, particularly in your region, as this can impact service and support.
- Tip: Utilize platforms like LinkedIn or industry-specific forums to gather insights and reviews about suppliers.
Step 4: Verify Supplier Certifications
Ensure that the manufacturers you are considering possess the necessary certifications and comply with international safety standards. Certifications such as ISO 9001 for quality management and CE marking for compliance with EU safety directives are crucial indicators of a reputable manufacturer. This step is vital for mitigating risks associated with product quality and safety.
Step 5: Request Product Samples or Demonstrations
Whenever possible, request samples or arrange for on-site demonstrations of the aerial work platforms. This allows you to assess the equipment’s performance and usability firsthand. Pay attention to ease of operation, safety features, and maintenance requirements, as these factors can significantly impact your long-term satisfaction.
Step 6: Negotiate Pricing and Terms
Once you have narrowed down your options, engage in negotiations with your selected suppliers. Discuss pricing, payment terms, warranty conditions, and after-sales support. Ensure that the terms are transparent and favorable, as this will lay the groundwork for a successful long-term partnership.
- Tip: Consider bulk purchasing agreements or long-term contracts for better pricing advantages.
Step 7: Plan for Logistics and Delivery
Finally, plan the logistics for transporting the aerial work platforms to your location. Discuss shipping options, timelines, and customs requirements with your supplier. A well-defined logistics plan helps avoid delays and unexpected costs, ensuring that your equipment arrives on schedule and in good condition.
By following this checklist, B2B buyers can navigate the complexities of sourcing aerial work platforms effectively, leading to informed decisions that enhance operational capabilities and ensure safety standards.
Comprehensive Cost and Pricing Analysis for aerial work platform manufacturer Sourcing
What Are the Key Cost Components in Aerial Work Platform Manufacturing?
Understanding the cost structure of aerial work platforms (AWPs) is crucial for international B2B buyers aiming to make informed purchasing decisions. The primary cost components include materials, labor, manufacturing overhead, tooling, quality control (QC), logistics, and profit margin.
-
Materials: The choice of materials significantly impacts the overall cost. High-strength steel, aluminum, and composite materials are commonly used, each varying in price. Buyers should consider the trade-off between material quality and cost, as this affects durability and performance.
-
Labor: Labor costs can vary significantly based on geographic location and the complexity of the manufacturing process. Regions with lower labor costs may offer competitive pricing, but it’s essential to assess the skill level and experience of the workforce, as these factors influence product quality.
-
Manufacturing Overhead: This includes all indirect costs related to production, such as utilities, maintenance, and administrative expenses. Understanding these costs helps buyers gauge the manufacturer’s efficiency and pricing strategy.
-
Tooling: Initial tooling costs can be substantial, especially for custom designs. Buyers should inquire about tooling options and their impact on pricing, particularly when considering customizations.
-
Quality Control: Investing in QC processes can raise production costs but ensures product reliability. Certifications such as ISO or CE mark can also add to costs, but they provide assurance of compliance with international standards.
-
Logistics: Shipping costs vary widely depending on distance, mode of transport, and packaging. For international buyers, understanding the logistics involved can help in evaluating total costs.
-
Margin: Manufacturers typically add a profit margin to their costs, which can vary based on market conditions and competition. Knowing the average margins in the industry can assist buyers in negotiating better terms.
How Do Price Influencers Affect Aerial Work Platform Costs?
Several factors influence the pricing of aerial work platforms, and understanding these can help buyers negotiate better deals.
-
Volume and Minimum Order Quantity (MOQ): Purchasing in larger volumes often results in lower per-unit costs. Buyers should negotiate MOQs that align with their operational needs.
-
Specifications and Customization: Custom features or specialized specifications can significantly affect pricing. Buyers should clearly define their requirements to avoid unexpected costs.
-
Materials and Quality Certifications: Higher quality materials and certifications can drive up prices. However, investing in quality can lead to lower maintenance and longer service life, contributing to a favorable Total Cost of Ownership (TCO).
-
Supplier Factors: The reputation and reliability of the supplier can influence pricing. Established manufacturers may charge a premium for their proven track record, while newer companies might offer lower prices to enter the market.
-
Incoterms: Understanding Incoterms is crucial for international transactions, as they determine who bears shipping costs, insurance, and tariffs. Buyers should clarify these terms to avoid unexpected expenses.
What Buyer Tips Can Enhance Cost-Efficiency in Sourcing Aerial Work Platforms?
International B2B buyers should adopt several strategies to optimize their sourcing process for aerial work platforms.
-
Negotiate Effectively: Engage in thorough negotiations with suppliers. Leverage your understanding of cost components and price influencers to secure favorable terms.
-
Evaluate Total Cost of Ownership: Beyond initial purchase price, consider maintenance, operational costs, and potential downtime when evaluating AWPs. A lower upfront cost may lead to higher long-term expenses.
-
Research Market Trends: Stay informed about market trends and price fluctuations in the AWP industry, particularly in your region. This knowledge can empower you during negotiations and sourcing decisions.
-
Leverage Regional Insights: Buyers from Africa, South America, the Middle East, and Europe should understand regional differences in manufacturing capabilities and supply chain dynamics. This awareness can inform sourcing strategies and mitigate risks.
-
Request Detailed Quotations: When seeking quotes, ask suppliers to break down costs transparently. This will help in comparing offers and understanding where savings can be achieved.
Final Thoughts on Aerial Work Platform Sourcing Costs
While this analysis provides a comprehensive overview of the cost structure and pricing dynamics in the aerial work platform manufacturing sector, it is essential to note that prices can vary significantly based on numerous factors. Buyers are encouraged to conduct thorough market research and engage with multiple suppliers to ensure they make informed purchasing decisions tailored to their specific needs.
Alternatives Analysis: Comparing aerial work platform manufacturer With Other Solutions
Understanding Alternative Solutions for Aerial Work Platforms
When considering aerial work platforms (AWPs), international B2B buyers must evaluate various alternatives that can meet their operational needs. Different solutions may offer unique advantages depending on specific industry requirements, budget constraints, and project scopes. This analysis compares aerial work platforms with scaffold systems and telehandlers, providing insights into their respective strengths and weaknesses.
Comparison Table of Aerial Work Platforms and Alternatives
Comparison Aspect | Aerial Work Platform Manufacturer | Scaffold Systems | Telehandlers |
---|---|---|---|
Performance | High reach and mobility | Limited height and mobility | Versatile lifting capabilities |
Cost | Moderate to high | Low to moderate | Moderate to high |
Ease of Implementation | Quick setup and operation | Time-consuming assembly | Requires skilled operators |
Maintenance | Regular checks needed | Minimal maintenance | Regular maintenance required |
Best Use Case | Construction, maintenance, events | Short-term projects, interiors | Heavy lifting, construction sites |
What Are the Pros and Cons of Scaffold Systems?
Scaffold systems provide a cost-effective solution for accessing heights, particularly in construction and maintenance projects. Their primary advantage is affordability; they are typically less expensive than aerial work platforms, making them suitable for short-term projects. However, they require a significant amount of time for assembly and disassembly, which can delay project timelines. Additionally, scaffolding has limitations in height and mobility, which can hinder efficiency in dynamic work environments.
How Do Telehandlers Compare to Aerial Work Platforms?
Telehandlers are versatile machines that combine the functions of a forklift with a boom lift. They excel in lifting heavy loads to considerable heights, making them ideal for construction sites where materials need to be moved and positioned at various elevations. While telehandlers can offer similar reach as aerial work platforms, they often require skilled operators and regular maintenance to ensure safe operation. The initial investment can also be high, similar to aerial work platforms, but they provide greater lifting versatility, which may justify the cost in certain applications.
Conclusion: How to Choose the Right Solution for Your Needs
Choosing the right aerial work platform or alternative solution requires a thorough assessment of your specific operational needs and constraints. Consider factors such as project duration, budget, required lifting height, and the skill level of your workforce. For projects emphasizing cost-effectiveness and shorter durations, scaffold systems may be appropriate. However, for tasks requiring high mobility and efficiency in lifting heavy materials, aerial work platforms or telehandlers could be the better choice. Ultimately, aligning your choice with your project requirements will ensure optimal performance and cost-effectiveness in your operations.
Essential Technical Properties and Trade Terminology for aerial work platform manufacturer
What Are the Key Technical Properties of Aerial Work Platforms?
Understanding the essential technical properties of aerial work platforms is crucial for B2B buyers to ensure they are making informed purchasing decisions. Here are several critical specifications that should be considered:
1. Load Capacity
Load capacity refers to the maximum weight that an aerial work platform can safely lift. This specification is vital as it determines the types of jobs the equipment can handle. For international buyers, particularly in construction-heavy regions like Africa and South America, selecting a platform with an appropriate load capacity ensures compliance with safety regulations and operational efficiency.
2. Working Height
The working height is the maximum vertical reach of the platform, which is essential for tasks that require access to elevated areas. Buyers should assess their project needs and select platforms with sufficient working heights. For instance, European buyers may have specific regulations regarding worksite safety that dictate minimum working heights for various applications.
3. Material Grade
The material grade of an aerial work platform affects its durability, weight, and resistance to environmental factors. Common materials include steel and aluminum, each with distinct benefits. Steel provides strength but is heavier, while aluminum is lightweight and corrosion-resistant. B2B buyers should consider the environmental conditions of their operating regions, such as humidity in the Middle East or rain in South America, to choose the appropriate material.
4. Tolerance Levels
Tolerance levels refer to the allowable variations in dimensions and specifications during manufacturing. High tolerance levels ensure better performance and safety, particularly in critical applications like maintenance or construction work. Buyers should inquire about the manufacturer’s quality control processes to ensure that the equipment meets their operational standards.
5. Drive Type
The drive type indicates how the aerial work platform is powered, which can be electric, diesel, or hybrid. Electric platforms are quieter and environmentally friendly, making them suitable for indoor use. Diesel platforms, on the other hand, provide greater power for outdoor applications. Buyers should evaluate their operational environment and choose a drive type that aligns with their performance needs and regulatory requirements.
What Are Common Trade Terms Used in the Aerial Work Platform Industry?
Familiarity with industry jargon is essential for effective communication and negotiation in the B2B space. Here are several common terms that buyers should understand:
1. OEM (Original Equipment Manufacturer)
OEM refers to the company that manufactures the original product, which is then marketed by another company under its own brand. Understanding OEM relationships is crucial for buyers looking for quality assurance and warranty support.
2. MOQ (Minimum Order Quantity)
MOQ is the minimum number of units a buyer must purchase from a supplier. This term is particularly relevant for buyers from Africa or South America, where bulk purchasing may yield cost advantages, but could also lead to excess inventory if not managed properly.
3. RFQ (Request for Quotation)
An RFQ is a document used to solicit price quotes from suppliers. Buyers should prepare a detailed RFQ, specifying all technical requirements and quantities, to ensure accurate pricing and avoid miscommunication with manufacturers.
4. Incoterms (International Commercial Terms)
Incoterms are a set of international rules that define the responsibilities of buyers and sellers in international transactions. Familiarity with these terms helps buyers understand shipping costs, insurance, and delivery responsibilities, which is especially important for international buyers navigating complex logistics.
5. CE Marking
CE marking indicates that a product meets EU safety, health, and environmental requirements. For European buyers, understanding CE compliance is crucial for ensuring that equipment can be legally sold and used within the EU.
By comprehensively understanding these technical properties and trade terms, B2B buyers can make informed decisions that enhance operational efficiency and compliance in their respective markets.
Navigating Market Dynamics and Sourcing Trends in the aerial work platform manufacturer Sector
What Are the Key Market Drivers for Aerial Work Platforms?
The aerial work platform (AWP) market is witnessing significant growth driven by various global factors. The rise of infrastructure projects across Africa, South America, the Middle East, and Europe is a primary catalyst, as these regions increasingly invest in urban development and construction. The expansion of industries such as logistics, telecommunications, and renewable energy also contributes to the demand for AWPs, as they facilitate safe and efficient access to elevated work sites.
Moreover, technological advancements are reshaping the sourcing landscape for international B2B buyers. The integration of IoT (Internet of Things) in aerial work platforms allows for real-time monitoring and maintenance, enhancing operational efficiency. B2B buyers are increasingly seeking manufacturers that offer smart solutions, including telematics for better fleet management and predictive maintenance capabilities. Additionally, the trend towards rental models rather than outright purchase is gaining traction, particularly in emerging markets, as it allows companies to reduce capital expenditure and adapt to fluctuating demand.
How Are Sustainability and Ethical Sourcing Impacting AWP Manufacturers?
In today’s market, sustainability is not just a trend but a necessity for aerial work platform manufacturers. The environmental impact of production processes and product lifecycle is coming under scrutiny, prompting buyers to prioritize suppliers who adopt eco-friendly practices. Many manufacturers are now focusing on reducing their carbon footprint through energy-efficient production methods and sustainable materials.
Ethical sourcing is also gaining importance. International B2B buyers are increasingly inclined to partner with manufacturers that maintain transparent supply chains and adhere to fair labor practices. Certifications such as ISO 14001 for environmental management and ISO 45001 for occupational health and safety are becoming essential criteria for procurement decisions. By choosing suppliers with these credentials, buyers can ensure that their sourcing aligns with global sustainability goals, thereby enhancing their own corporate responsibility initiatives.
How Has the Aerial Work Platform Market Evolved Over Time?
The aerial work platform industry has evolved significantly over the past few decades. Initially dominated by basic scissor lifts and boom lifts, the market has expanded to include a wide range of products tailored for specific applications, from compact models for urban environments to heavy-duty machines for construction sites. The introduction of electric and hybrid models has revolutionized the sector, catering to the growing demand for sustainable solutions.
This evolution has been influenced by technological advancements and changing regulations, particularly concerning safety standards. Manufacturers are now required to comply with stringent safety and environmental regulations, which has prompted innovation in design and functionality. As a result, today’s aerial work platforms are not only safer but also more efficient, versatile, and user-friendly, providing enhanced value for international B2B buyers seeking reliable equipment for their operations.
Frequently Asked Questions (FAQs) for B2B Buyers of aerial work platform manufacturer
-
How do I choose the right aerial work platform for my project?
Selecting the appropriate aerial work platform (AWP) depends on various factors, including the height required, the weight capacity needed, and the type of terrain where it will be used. Conduct a thorough assessment of your project specifications, including the environment (indoor vs. outdoor), the type of tasks (construction, maintenance, etc.), and any safety regulations in your region. Consult with manufacturers to understand their product range and request demonstrations if possible to ensure the equipment meets your operational needs. -
What are the most important specifications to consider when sourcing aerial work platforms?
Key specifications to evaluate include working height, load capacity, platform size, and mobility features. Additionally, consider the power source (electric vs. diesel), operational controls, and safety features such as guardrails and emergency stop buttons. It’s also important to verify compliance with local safety standards and regulations to avoid potential legal issues and ensure worker safety. -
What customization options are available when purchasing aerial work platforms?
Many manufacturers offer customization options to meet specific operational needs. These may include platform extensions, specialized attachments (e.g., material handling accessories), and bespoke safety features. When discussing customization, ensure that the manufacturer has experience in adapting products for different markets, particularly in regions like Africa and South America, where unique challenges may arise. -
What is the minimum order quantity (MOQ) for aerial work platforms?
The MOQ can vary significantly between manufacturers, with some requiring a single unit while others may set the MOQ at several units. For international buyers, consider negotiating terms based on your project needs and potential future orders. Establishing a good relationship with the manufacturer can often lead to more favorable terms, especially if you demonstrate a commitment to future business. -
What payment terms are typically offered by aerial work platform manufacturers?
Payment terms can range from upfront payments to staggered payments based on delivery milestones. Common arrangements include a deposit upon order confirmation, followed by payment before shipping or upon delivery. When engaging with suppliers, it’s crucial to clarify payment terms early in negotiations to avoid misunderstandings and ensure a smooth transaction process, particularly in cross-border deals. -
How can I ensure quality assurance when sourcing aerial work platforms?
To ensure quality, ask manufacturers about their quality control processes, certifications, and testing procedures. Request documentation that demonstrates compliance with international standards, such as ISO or CE certifications. Additionally, consider conducting site visits or obtaining third-party inspections before finalizing your purchase to validate the manufacturer’s claims about product quality and safety. -
What are the logistics considerations when importing aerial work platforms?
Logistics play a crucial role in the successful importation of AWPs. Consider factors such as shipping methods, customs clearance, and local regulations that may affect delivery timelines and costs. Engage with logistics providers experienced in heavy equipment transport to navigate any challenges related to shipping dimensions, weights, and specialized handling requirements. Additionally, factor in potential tariffs and duties that could impact your overall budget. -
How do I vet potential aerial work platform suppliers effectively?
Vetting suppliers involves thorough research and evaluation of their business practices. Start by checking their reputation through industry reviews, client testimonials, and case studies. Request references from previous customers, particularly those from similar markets or industries. Additionally, assess their financial stability, production capabilities, and after-sales service. A reliable supplier should demonstrate transparency and be willing to share relevant information to build trust in your partnership.
Important Disclaimer & Terms of Use
⚠️ Important Disclaimer
The information provided in this guide, including content regarding manufacturers, technical specifications, and market analysis, is for informational and educational purposes only. It does not constitute professional procurement advice, financial advice, or legal advice.
While we have made every effort to ensure the accuracy and timeliness of the information, we are not responsible for any errors, omissions, or outdated information. Market conditions, company details, and technical standards are subject to change.
B2B buyers must conduct their own independent and thorough due diligence before making any purchasing decisions. This includes contacting suppliers directly, verifying certifications, requesting samples, and seeking professional consultation. The risk of relying on any information in this guide is borne solely by the reader.
Strategic Sourcing Conclusion and Outlook for aerial work platform manufacturer
In the ever-evolving landscape of aerial work platforms, strategic sourcing has emerged as a critical component for B2B buyers seeking competitive advantage. By prioritizing partnerships with manufacturers that emphasize quality, innovation, and sustainability, companies from Africa, South America, the Middle East, and Europe can significantly enhance their operational efficiency and project outcomes.
How Can Strategic Sourcing Drive Value for Your Business?
Investing in strategic sourcing allows businesses to mitigate risks, reduce costs, and improve supply chain resilience. Buyers should focus on suppliers that align with their long-term goals and can adapt to fluctuating market demands. Moreover, engaging with manufacturers that offer customized solutions can lead to better productivity and safety in aerial operations, ensuring compliance with local regulations.
What is the Future of Aerial Work Platform Sourcing?
Looking ahead, the demand for aerial work platforms is set to grow, driven by urbanization and infrastructure development. International buyers are encouraged to explore emerging technologies, such as electric and hybrid models, which not only reduce environmental impact but also lower operational costs.
In conclusion, the path forward for B2B buyers in Colombia, Nigeria, and beyond is clear: leverage strategic sourcing to build robust partnerships and stay ahead of the curve. Embrace innovation and sustainability as core tenets of your sourcing strategy to secure a prosperous future in the aerial work platform market.