Discover Top Benefits of Alloy Wheel Manufacturer Sourcing (2025)
Introduction: Navigating the Global Market for alloy wheel manufacturer
In the competitive landscape of automotive components, international B2B buyers face the critical challenge of sourcing high-quality alloy wheels that meet specific performance and aesthetic criteria. Understanding the intricacies of the alloy wheel manufacturing process is essential for buyers, particularly those from diverse markets such as Africa, South America, the Middle East, and Europe. This guide offers a comprehensive overview of the alloy wheel manufacturing industry, detailing various types of wheels, their applications across different vehicle segments, and the importance of material selection.
Buyers will gain insights into the vetting process for suppliers, ensuring that they partner with manufacturers who uphold stringent quality standards and ethical production practices. Additionally, the guide delves into cost considerations, allowing businesses to make informed budgeting decisions without compromising on quality. By equipping B2B buyers with the knowledge necessary to navigate the complexities of sourcing alloy wheels, this resource empowers them to make confident purchasing decisions that align with their operational needs and market demands.
Whether you are a buyer in South Africa looking for durable wheels for off-road vehicles or a distributor in France seeking stylish options for luxury cars, this guide serves as a vital tool in your procurement strategy, ultimately enhancing your competitive edge in the global marketplace.
Understanding alloy wheel manufacturer Types and Variations
Type Name | Key Distinguishing Features | Primary B2B Applications | Brief Pros & Cons for Buyers |
---|---|---|---|
Cast Alloy Wheels | Produced by pouring molten metal into a mold; typically heavier and less expensive. | Standard vehicles, fleet services | Pros: Cost-effective, widely available. Cons: Heavier, less performance-oriented. |
Forged Alloy Wheels | Made from a solid piece of metal, offering superior strength and weight reduction. | High-performance vehicles, motorsports | Pros: Lightweight, enhanced performance. Cons: Higher cost, limited availability. |
Flow-formed Alloy Wheels | Combines features of both cast and forged wheels; offers strength with reduced weight. | Performance upgrades, luxury vehicles | Pros: Good balance of cost and performance. Cons: May not be as durable as forged options. |
Multispoke Alloy Wheels | Characterized by intricate designs with multiple spokes; often aesthetic-focused. | Custom vehicles, aftermarket modifications | Pros: Enhanced aesthetics, unique designs. Cons: May compromise strength, higher maintenance. |
Steel Alloy Wheels | Made from steel alloys, generally heavier but more durable and less expensive. | Heavy-duty vehicles, commercial fleets | Pros: Strong, economical. Cons: Heavier, less stylish than alloy alternatives. |
What Are the Key Characteristics of Cast Alloy Wheels?
Cast alloy wheels are among the most commonly produced types, made by pouring molten aluminum into molds. They are typically heavier and less expensive compared to other types. This makes them suitable for standard vehicles and fleet services, where cost-effectiveness is paramount. B2B buyers should consider the balance between price and performance, as cast wheels may not offer the same benefits in terms of speed and fuel efficiency as lighter options.
How Do Forged Alloy Wheels Stand Out?
Forged alloy wheels are manufactured from a single piece of metal, which provides superior strength and reduces weight. This makes them ideal for high-performance vehicles and motorsports. B2B buyers looking for enhanced performance should consider investing in forged wheels despite their higher cost. The durability and lightweight nature of these wheels can significantly improve vehicle handling and speed, making them a worthwhile investment for performance-focused applications.
What Makes Flow-formed Alloy Wheels a Good Choice?
Flow-formed alloy wheels represent a hybrid approach, combining the benefits of cast and forged wheels. They undergo a unique manufacturing process that enhances strength while minimizing weight. These wheels are suited for performance upgrades and luxury vehicles, providing a good balance of cost and performance. B2B buyers should evaluate their specific needs and consider flow-formed wheels as a versatile option that offers both aesthetics and functionality.
Why Consider Multispoke Alloy Wheels?
Multispoke alloy wheels are designed with intricate patterns that enhance the visual appeal of vehicles. These wheels are often used in custom vehicles and aftermarket modifications, appealing to buyers who prioritize aesthetics. However, while they can enhance the look of a vehicle, B2B buyers should be cautious about potential compromises in strength and increased maintenance requirements. It’s essential to align aesthetic choices with practical applications.
What Are the Advantages of Steel Alloy Wheels?
Steel alloy wheels are known for their durability and cost-effectiveness, making them a popular choice for heavy-duty vehicles and commercial fleets. They are generally heavier than alloy options, which can be a disadvantage in terms of performance but offers benefits in terms of strength and resilience. B2B buyers focusing on budget constraints and durability should consider steel wheels as a practical solution, especially in demanding environments where longevity is critical.
Related Video: Amazing Modern Car Wheel Mass Production Factory. Korean Alloy Wheel Manufacturing Process
Key Industrial Applications of alloy wheel manufacturer
Industry/Sector | Specific Application of alloy wheel manufacturer | Value/Benefit for the Business | Key Sourcing Considerations for this Application |
---|---|---|---|
Automotive | Production of lightweight alloy wheels for passenger vehicles | Improved fuel efficiency and performance due to reduced weight | Compliance with international safety standards and certifications |
Aerospace | Manufacturing of alloy wheels for aircraft landing gears | Enhanced durability and weight reduction for better fuel economy | Need for high-quality materials with specific aerospace-grade certifications |
Heavy Machinery | Development of alloy wheels for construction and mining equipment | Increased strength and load-bearing capacity, leading to longer equipment life | Consideration of environmental factors and resistance to harsh conditions |
Sports and Racing | Custom alloy wheels for high-performance vehicles | Enhanced aesthetics and performance, catering to niche markets | Demand for bespoke designs and quick turnaround times |
Rail Transport | Production of alloy wheels for trains and trams | Improved safety and reduced maintenance costs through better material properties | Requirement for compliance with rail industry regulations and standards |
How is Alloy Wheel Manufacturing Applied in the Automotive Industry?
In the automotive sector, alloy wheels are essential for producing lightweight wheels that enhance fuel efficiency and vehicle performance. By reducing the overall weight of the vehicle, manufacturers can significantly lower fuel consumption and improve handling. International buyers, particularly from regions like Africa and South America, should consider sourcing from manufacturers that comply with global safety standards and certifications to ensure product reliability.
What Role Do Alloy Wheels Play in Aerospace Applications?
Alloy wheels are critical in the aerospace industry, specifically for aircraft landing gears. These wheels need to withstand extreme conditions while remaining lightweight to optimize fuel efficiency. Buyers in the aerospace sector must prioritize suppliers who provide aerospace-grade materials and have the necessary certifications to meet stringent safety and performance requirements.
How Are Alloy Wheels Used in Heavy Machinery?
In the heavy machinery industry, alloy wheels are utilized in construction and mining equipment, where strength and load-bearing capacity are paramount. The use of alloy materials increases the durability of wheels, which leads to extended equipment lifespan and reduced downtime for repairs. Buyers should focus on sourcing from manufacturers that understand the environmental challenges faced in these industries and can provide wheels that resist wear and tear.
Why Are Custom Alloy Wheels Important in Sports and Racing?
Custom alloy wheels are a significant aspect of high-performance vehicles in the sports and racing sectors. These wheels not only improve the vehicle’s aesthetics but also enhance its performance by reducing weight and improving aerodynamics. International B2B buyers should seek manufacturers that offer bespoke designs and can deliver products within tight timelines, especially for competitive racing applications.
How Do Alloy Wheels Benefit Rail Transport Systems?
In rail transport, alloy wheels are vital for trains and trams, contributing to safety and maintenance efficiency. Their superior material properties help in reducing wear and tear, which translates to lower maintenance costs over time. Buyers in this sector must ensure that their suppliers comply with specific rail industry regulations and standards, which are crucial for operational safety and reliability.
3 Common User Pain Points for ‘alloy wheel manufacturer’ & Their Solutions
Scenario 1: Difficulties in Sourcing Quality Alloy Wheels
The Problem: B2B buyers often face challenges in sourcing high-quality alloy wheels that meet their specific requirements. This issue is particularly pronounced in regions such as Africa and South America, where local suppliers may not have access to advanced manufacturing technologies or stringent quality controls. Buyers may receive subpar products that do not perform as expected, leading to increased costs and dissatisfied end customers.
The Solution: To overcome this challenge, buyers should establish partnerships with reputable alloy wheel manufacturers who adhere to international quality standards, such as ISO certifications. Conducting thorough research and requesting samples before placing bulk orders can help ensure product quality. Buyers can also leverage online platforms and industry trade shows to connect with manufacturers from Europe and the Middle East known for their advanced manufacturing processes. Creating a detailed specification sheet that outlines the required materials, dimensions, and performance standards will further aid manufacturers in delivering products that meet expectations. Additionally, consider implementing a quality assurance process that includes periodic audits of the manufacturing facility to ensure compliance with agreed-upon standards.
Scenario 2: Navigating Import Regulations and Logistics Challenges
The Problem: International B2B buyers often encounter complex import regulations and logistical hurdles when sourcing alloy wheels from overseas manufacturers. These challenges can lead to delays in delivery, unexpected tariffs, and complications with customs clearance, which can impact a buyer’s inventory management and customer satisfaction.
The Solution: To mitigate these issues, buyers should familiarize themselves with the import regulations specific to their country. Consulting with a customs broker can provide insights into tariffs, necessary documentation, and compliance requirements, ensuring smoother transactions. Additionally, working closely with the manufacturer to establish a clear logistics plan can help streamline the shipping process. This may involve selecting reliable freight forwarders who specialize in handling automotive parts, thus minimizing delays and ensuring timely delivery. Establishing a buffer inventory can also help manage potential delays in the supply chain, allowing businesses to maintain operations without interruption.
Scenario 3: Concerns Over Product Customization and Compatibility
The Problem: Many B2B buyers worry about the ability of alloy wheel manufacturers to provide customized products that align with specific vehicle models and performance requirements. Incompatibility issues can arise, leading to additional costs for modifications or, worse, safety concerns for end-users.
The Solution: Buyers should engage in proactive communication with manufacturers about their customization needs early in the sourcing process. Providing detailed specifications, including vehicle make, model, and intended use (such as racing or off-road driving), allows manufacturers to offer tailored solutions. Additionally, it is beneficial to inquire about the manufacturer’s experience with similar projects and their ability to accommodate unique requests. Buyers should also seek manufacturers that offer a range of finishes, sizes, and designs to ensure compatibility with various vehicles. Utilizing technology such as 3D modeling and CAD software during the design phase can help visualize the final product, reducing the likelihood of errors and ensuring that the wheels fit perfectly. By prioritizing manufacturers who demonstrate flexibility and innovation in their product offerings, buyers can achieve the desired balance of style, performance, and safety.
Strategic Material Selection Guide for alloy wheel manufacturer
What Are the Key Materials Used in Alloy Wheel Manufacturing?
When selecting materials for alloy wheels, manufacturers typically consider several key options, each with distinct properties, advantages, and disadvantages. Understanding these materials is crucial for international B2B buyers, especially those in regions like Africa, South America, the Middle East, and Europe, where compliance with specific standards and preferences can significantly affect procurement decisions.
Aluminum Alloys: The Most Common Choice
Aluminum alloys are the most widely used materials in alloy wheel manufacturing due to their favorable properties. They offer excellent strength-to-weight ratios, which enhance vehicle performance by reducing unsprung weight. Aluminum wheels typically have good corrosion resistance, making them suitable for various climates.
Pros:
– Lightweight, which improves fuel efficiency and handling.
– Corrosion-resistant, reducing maintenance costs.
– Easier to manufacture and shape than some other metals.
Cons:
– Can be more expensive than steel alternatives.
– May not withstand extreme impacts as well as some heavier materials.
– Requires protective coatings to enhance durability.
Considerations for Buyers:
International buyers should ensure that aluminum alloys meet regional standards, such as ASTM or DIN, to guarantee quality and performance. In regions with high humidity or saline environments, additional corrosion resistance treatments may be necessary.
Magnesium Alloys: Lightweight and Strong
Magnesium alloys are another option for alloy wheels, known for their lightweight properties and strength. They can provide superior performance in terms of handling and acceleration.
Pros:
– Extremely lightweight, further enhancing vehicle performance.
– High strength-to-weight ratio allows for thinner designs without compromising integrity.
– Excellent thermal conductivity.
Cons:
– Higher manufacturing complexity and costs.
– Susceptible to corrosion, requiring protective coatings.
– Limited availability compared to aluminum.
Considerations for Buyers:
B2B buyers must be aware of the specific corrosion resistance requirements in their region, especially in coastal areas. Compliance with international standards is also crucial, as magnesium alloys may face stricter regulations.
Steel Alloys: Durability and Cost-Effectiveness
Steel alloys, while heavier than aluminum and magnesium, are often favored for their durability and cost-effectiveness. They are particularly popular in regions where road conditions are poor, as they can withstand rough usage better than lighter materials.
Pros:
– Highly durable and resistant to impact.
– Generally lower cost than aluminum or magnesium alloys.
– Easier to repair in case of damage.
Cons:
– Heavier, which can negatively impact fuel efficiency.
– Prone to rust if not properly coated.
– Less aesthetically appealing than aluminum or magnesium.
Considerations for Buyers:
International buyers should evaluate the cost versus performance trade-offs, especially in regions with rough terrain. Compliance with standards related to weight and safety is essential for ensuring the wheels meet local regulations.
Composite Materials: The Future of Alloy Wheels?
Composite materials, including carbon fiber and reinforced plastics, are emerging as alternatives for high-performance applications. They offer excellent strength and weight advantages but come with higher costs and manufacturing complexities.
Pros:
– Exceptional strength-to-weight ratio.
– Can be molded into complex shapes, allowing for innovative designs.
– Resistant to corrosion and environmental factors.
Cons:
– High manufacturing costs and complexity.
– Limited repairability compared to metals.
– May not be suitable for all vehicle types.
Considerations for Buyers:
Buyers should consider the application and vehicle type when looking at composite materials. Compliance with safety standards and performance metrics is critical, especially for high-performance vehicles.
Summary Table of Materials for Alloy Wheel Manufacturing
Material | Typical Use Case for Alloy Wheel Manufacturer | Key Advantage | Key Disadvantage/Limitation | Relative Cost (Low/Med/High) |
---|---|---|---|---|
Aluminum Alloys | Standard passenger vehicles | Lightweight and corrosion-resistant | Higher cost and potential impact damage | Medium |
Magnesium Alloys | High-performance vehicles | Extremely lightweight | Corrosion susceptibility and high cost | High |
Steel Alloys | Heavy-duty vehicles and trucks | Durable and cost-effective | Heavier and prone to rust | Low |
Composite Materials | Luxury and performance vehicles | Exceptional strength-to-weight ratio | High cost and limited repairability | High |
This strategic material selection guide provides valuable insights for international B2B buyers in the alloy wheel manufacturing sector, helping them make informed decisions based on material properties, advantages, and regional considerations.
In-depth Look: Manufacturing Processes and Quality Assurance for alloy wheel manufacturer
What Are the Main Stages of Manufacturing for Alloy Wheels?
Manufacturing alloy wheels involves several critical stages, each designed to ensure that the final product meets both aesthetic and performance standards. The main stages of the manufacturing process include:
-
Material Preparation
The primary materials used in alloy wheel production are aluminum and magnesium alloys. The process begins with sourcing high-quality raw materials that comply with international standards. These materials undergo a thorough inspection to ensure they meet specific criteria for composition and purity. Buyers should inquire about the supplier’s sourcing practices and material certifications to ensure reliability. -
Forming
The forming stage involves shaping the prepared materials into the desired wheel profile. This can be achieved through various methods, including casting, forging, and machining.
– Casting involves pouring molten metal into molds and allowing it to solidify, creating complex shapes with high precision.
– Forging entails applying pressure to pre-heated metal, resulting in a denser structure and improved strength.
– Machining is used to refine the wheel’s dimensions and surface finish, ensuring tight tolerances and high-quality surfaces. -
Assembly
In this phase, the individual components of the wheel, such as the rim and spokes, are joined together. This may involve welding or adhesive bonding, depending on the design and material properties. Buyers should look for manufacturers that utilize automated assembly processes to enhance consistency and reduce human error. -
Finishing
The final stage of manufacturing involves surface treatments such as anodizing, painting, or polishing. These finishing processes not only enhance the wheel’s visual appeal but also provide protection against corrosion and wear. Buyers should consider the types of finishes offered and how they align with their market needs.
How Is Quality Assurance Integrated into Alloy Wheel Manufacturing?
Quality assurance (QA) is crucial for maintaining product integrity and customer satisfaction. The following international and industry-specific standards are often adhered to during the manufacturing process:
-
International Standards
– ISO 9001: This standard outlines the criteria for a quality management system and is essential for ensuring consistent quality across all manufacturing processes. Buyers should confirm that their suppliers are ISO 9001 certified, as this indicates a commitment to continuous improvement and customer satisfaction. -
Industry-Specific Standards
– CE Marking: Required for products sold within the European Economic Area, CE marking indicates compliance with safety, health, and environmental protection standards.
– API Standards: For manufacturers supplying the automotive industry, adherence to American Petroleum Institute standards can be vital, particularly in regions with stringent automotive regulations.
What Are the Key Quality Control Checkpoints in Alloy Wheel Manufacturing?
Quality control (QC) checkpoints are strategically implemented throughout the manufacturing process to identify defects early and ensure compliance with standards. Key checkpoints include:
-
Incoming Quality Control (IQC)
This initial stage involves inspecting raw materials upon receipt. Key aspects include verifying material specifications, conducting chemical composition tests, and assessing physical attributes. Buyers should request IQC reports to confirm that incoming materials meet quality standards. -
In-Process Quality Control (IPQC)
During production, various inspections are conducted to monitor compliance with specifications. This includes checks on dimensional accuracy, surface finish, and mechanical properties. B2B buyers can benefit from understanding the IPQC methods used by their suppliers, such as automated monitoring systems or manual inspections. -
Final Quality Control (FQC)
Before shipment, a comprehensive inspection is conducted on the finished wheels. This includes visual inspections, dimensional checks, and functional tests, such as load testing. Buyers should ensure that FQC results are documented and available for review.
What Testing Methods Are Commonly Used for Alloy Wheels?
To guarantee the performance and safety of alloy wheels, manufacturers employ several testing methods, including:
- Tensile Testing: This determines the strength and ductility of the alloy material.
- Fatigue Testing: Wheels are subjected to repeated stress to evaluate their durability under real-world conditions.
- Impact Testing: This simulates sudden impacts to assess the wheel’s resistance to damage.
- Corrosion Testing: Assessing the wheel’s resistance to environmental factors, particularly important for buyers in humid or coastal regions.
How Can B2B Buyers Verify Supplier Quality Control Practices?
B2B buyers can take several steps to ensure that their suppliers maintain rigorous quality control practices:
-
Supplier Audits
Conducting regular audits of suppliers can help verify compliance with quality standards and practices. These audits can assess the entire manufacturing process, from material sourcing to final inspection. -
Requesting Quality Reports
Buyers should ask for quality assurance reports that detail inspection results, testing outcomes, and compliance with relevant standards. This documentation provides transparency and builds trust. -
Third-Party Inspections
Engaging third-party inspection services can provide an unbiased assessment of the manufacturing process and product quality. This is particularly important for buyers in regions with less stringent local regulations.
What Are the Nuances of Quality Control for International Buyers?
International buyers, particularly from diverse regions like Africa, South America, the Middle East, and Europe, must consider various nuances in quality control:
- Cultural Differences: Understanding the cultural context of suppliers can impact communication and expectations regarding quality standards.
- Regulatory Compliance: Different regions have varying regulatory requirements. Buyers should ensure that suppliers can meet local standards in their markets.
- Logistics and Supply Chain Management: Quality assurance extends beyond manufacturing. Buyers should evaluate how logistics and transportation impact product integrity during shipment.
By focusing on these manufacturing processes and quality assurance measures, international B2B buyers can make informed decisions when sourcing alloy wheels, ensuring they partner with reputable manufacturers committed to quality and reliability.
Practical Sourcing Guide: A Step-by-Step Checklist for ‘alloy wheel manufacturer’
Introduction
Navigating the procurement of alloy wheels for your business can be a complex process, especially for international buyers. This practical sourcing guide serves as a step-by-step checklist to help you identify, evaluate, and select reliable alloy wheel manufacturers. By following these steps, you will ensure that you make informed purchasing decisions that align with your quality, cost, and delivery expectations.
Step 1: Define Your Technical Specifications
Clearly outlining your technical requirements is the first step in sourcing alloy wheels. This includes specifications such as size, weight, material composition, and design features. Having these details defined will not only help you communicate your needs effectively to potential suppliers but will also assist in evaluating their capabilities.
- Key Considerations:
- Understand the specific alloy compositions that meet your performance standards.
- Determine whether you require custom designs or standard products.
Step 2: Conduct Market Research for Suppliers
Engage in thorough market research to identify potential alloy wheel manufacturers. Use online directories, industry trade shows, and business networks to compile a list of suppliers. Research their reputation, product range, and customer reviews to narrow down your options.
- Key Resources:
- B2B marketplaces like Alibaba, ThomasNet, or local industry-specific platforms.
- Trade associations and industry publications that highlight reputable suppliers.
Step 3: Evaluate Potential Suppliers
Before committing, it’s crucial to vet suppliers thoroughly. Request company profiles, case studies, and references from buyers in a similar industry or region. Ensure you do not solely rely on their website for information; look for third-party reviews and testimonials.
- Assessment Criteria:
- Years of experience in the alloy wheel manufacturing sector.
- Proven track record of delivering quality products on time.
Step 4: Verify Supplier Certifications
Ensure that the manufacturers you are considering hold relevant certifications such as ISO 9001 for quality management systems or specific automotive industry standards. Certifications indicate a commitment to quality and reliability, which is essential for maintaining your product standards.
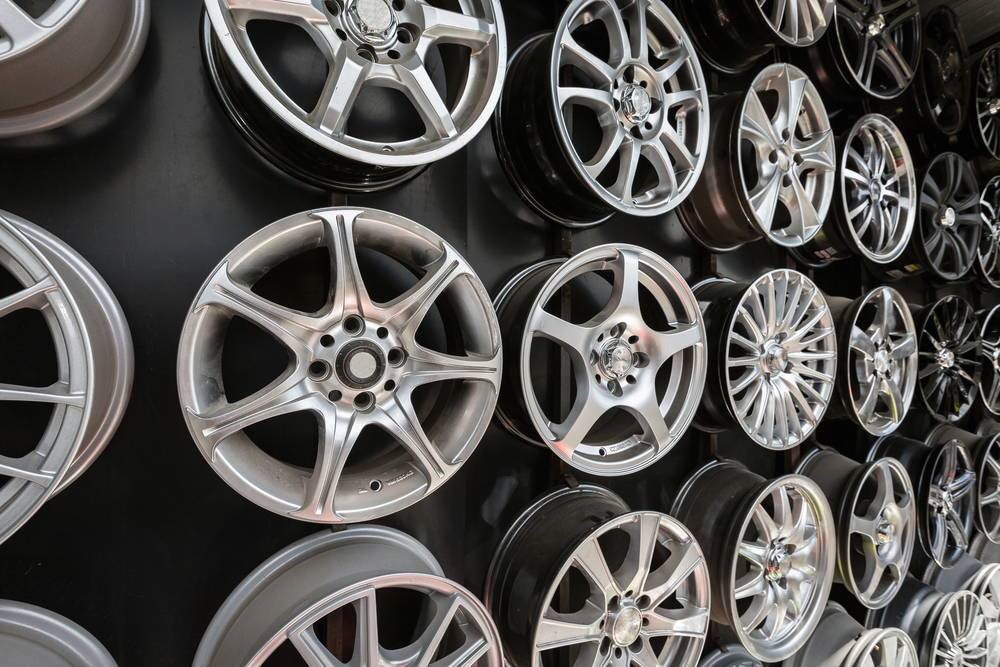
A stock image related to alloy wheel manufacturer.
- What to Look For:
- Check for compliance with international quality standards.
- Request documentation to verify their certifications.
Step 5: Request Samples for Quality Assessment
Before placing a bulk order, request samples of the alloy wheels. This step allows you to assess the quality, finish, and overall workmanship. Testing the samples for durability and performance in real-world conditions can prevent potential issues later.
- Testing Parameters:
- Conduct visual inspections for defects or inconsistencies.
- Perform performance tests if applicable, such as weight tolerance tests.
Step 6: Negotiate Terms and Conditions
Once you have identified a suitable supplier, negotiate the terms of your purchase. This includes pricing, payment terms, lead times, and delivery schedules. Clear agreements will help avoid misunderstandings and ensure that both parties are aligned on expectations.
- Negotiation Tips:
- Discuss volume discounts for larger orders.
- Clarify responsibilities for shipping and handling costs.
Step 7: Establish a Communication Plan
Maintaining effective communication with your supplier is essential throughout the sourcing process. Establish a point of contact and agree on communication channels and frequency. This will facilitate timely updates and address any concerns that may arise.
- Communication Strategies:
- Use project management tools for ongoing updates.
- Schedule regular check-ins to monitor progress and resolve issues promptly.
By following this comprehensive checklist, international B2B buyers can streamline their sourcing process for alloy wheels, ensuring they partner with manufacturers who meet their specific needs and standards.
Comprehensive Cost and Pricing Analysis for alloy wheel manufacturer Sourcing
What Are the Key Cost Components in Alloy Wheel Manufacturing?
When sourcing alloy wheels, understanding the cost structure is critical. The primary cost components include:
-
Materials: The choice of alloys, typically aluminum or magnesium, significantly impacts costs. Prices fluctuate based on global supply and demand, and sourcing from different regions may affect material availability and pricing.
-
Labor: Labor costs vary based on the geographical location of the manufacturer. Regions with lower labor costs may offer more competitive pricing, but this can sometimes come at the expense of quality.
-
Manufacturing Overhead: This includes utilities, facility maintenance, and indirect labor costs. Manufacturers in regions with higher operational costs will reflect this in their pricing.
-
Tooling: Initial tooling costs can be substantial, especially for custom designs. Buyers should consider whether the manufacturer has existing tooling that can reduce costs.
-
Quality Control (QC): Investment in QC processes ensures that the products meet industry standards. This may increase upfront costs but can save money in the long run by reducing defects and returns.
-
Logistics: Shipping costs can be a significant factor, especially for international buyers. Factors such as distance, shipping method, and freight terms (Incoterms) can all influence logistics costs.
-
Margin: Manufacturers typically include a profit margin in their pricing. Understanding the market rates and typical margins can aid in negotiations.
How Do Price Influencers Affect Alloy Wheel Sourcing?
Several factors can influence the pricing of alloy wheels, including:
-
Volume and Minimum Order Quantity (MOQ): Larger orders often result in lower per-unit costs due to economies of scale. Discussing potential volume discounts with manufacturers can lead to significant savings.
-
Specifications and Customization: Custom designs or specifications can increase production complexity, impacting costs. It’s essential to clearly define requirements to avoid unexpected price hikes.
-
Material Quality and Certifications: Higher-quality materials that meet specific certifications may be more expensive. Buyers should assess whether the added cost aligns with their performance requirements.
-
Supplier Factors: The reputation and reliability of the supplier can influence pricing. Established manufacturers may charge more due to their proven track record, while new entrants might offer lower prices to gain market share.
-
Incoterms: Understanding the agreed-upon Incoterms is crucial for calculating total costs. Different terms can shift responsibilities for shipping, insurance, and customs duties, affecting the overall price.
What Are Effective Buyer Tips for Negotiating Alloy Wheel Prices?
International B2B buyers should consider several strategies to enhance cost-efficiency and negotiate better pricing:
-
Negotiate with Transparency: Clearly outline your purchasing intentions, including expected volumes and timelines. This openness can foster a collaborative relationship, leading to better pricing.
-
Evaluate Total Cost of Ownership (TCO): Beyond the initial purchase price, consider long-term costs associated with maintenance, durability, and potential resale value. This holistic view can help justify higher upfront costs for better quality products.
-
Understand Pricing Nuances for International Markets: Buyers from Africa, South America, the Middle East, and Europe should be aware of regional market dynamics. For example, tariffs, taxes, and local regulations can influence pricing and should be factored into cost calculations.
-
Request Quotes from Multiple Suppliers: Obtaining several quotes can provide a clearer picture of the market and help identify the best value. Ensure that all quotes include the same specifications for accurate comparisons.
-
Stay Informed About Market Trends: Keeping abreast of material prices, labor costs, and geopolitical developments can provide leverage during negotiations and help anticipate future pricing changes.
Conclusion
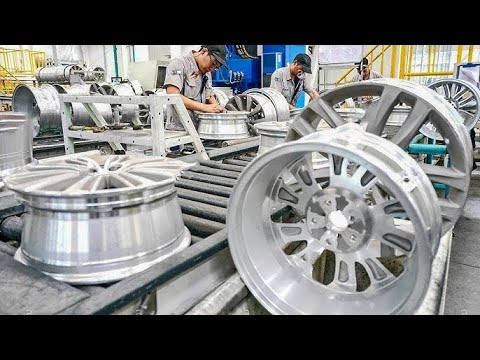
A stock image related to alloy wheel manufacturer.
Understanding the comprehensive cost structure and the various pricing influencers is essential for international B2B buyers of alloy wheels. By applying these insights and negotiating effectively, buyers can secure favorable deals that align with their quality and cost expectations. Remember, while indicative prices can serve as a guideline, actual costs may vary based on the specifics of each deal and market conditions.
Alternatives Analysis: Comparing alloy wheel manufacturer With Other Solutions
When evaluating options for sourcing wheels for vehicles, international B2B buyers often consider a variety of solutions that can meet their operational requirements. While alloy wheels are a popular choice due to their lightweight and aesthetic appeal, several alternative solutions exist that may better suit specific needs, especially when considering factors such as cost, performance, and maintenance.
Comparison Aspect | Alloy Wheel Manufacturer | Steel Wheel Manufacturer | Forged Aluminum Wheel Manufacturer |
---|---|---|---|
Performance | High strength-to-weight ratio; enhances fuel efficiency | Heavier, lower strength; can affect fuel efficiency negatively | Superior strength and lightweight; excellent for performance applications |
Cost | Moderate to high | Low to moderate | High |
Ease of Implementation | Standard manufacturing process; widely available | Simple production process; easier supply chain | Complex manufacturing; may require specialized suppliers |
Maintenance | Generally low; prone to cosmetic damage | Durable; resistant to corrosion | Requires careful handling; can be prone to cracking |
Best Use Case | Everyday vehicles, sports cars | Commercial vehicles, trucks | High-performance racing applications, luxury vehicles |
What are the Benefits and Drawbacks of Steel Wheel Manufacturers?
Steel wheels are a cost-effective alternative for many buyers, particularly in the commercial vehicle sector. They are less expensive to produce and purchase, making them a viable option for companies looking to minimize expenses. However, their heavier weight can negatively impact fuel efficiency and overall vehicle performance. Steel wheels are durable and resistant to damage, which makes them suitable for rugged terrains. Nonetheless, they can suffer from rust and corrosion over time, which may require additional maintenance efforts.
How Do Forged Aluminum Wheel Manufacturers Compare?
Forged aluminum wheels represent a premium alternative that offers a blend of strength and lightweight characteristics. They are often favored in high-performance applications due to their ability to withstand greater stresses without compromising on weight. The manufacturing process for forged wheels is complex and typically results in higher costs, which may deter budget-conscious buyers. However, for those operating luxury or performance vehicles, the investment can yield significant benefits in terms of handling and efficiency. It’s important to note that while they offer superior performance, they can be more susceptible to cracking under extreme conditions.
Conclusion: How Can B2B Buyers Choose the Right Wheel Solution?
When choosing the right wheel solution, B2B buyers must consider their specific operational needs, budget constraints, and the intended application of the wheels. Alloy wheels are an excellent choice for many vehicles due to their balance of performance and aesthetics. However, for businesses focused on cost-efficiency or those requiring wheels for heavy-duty applications, steel wheels may provide a more economical solution. Conversely, for high-performance or luxury applications, investing in forged aluminum wheels could be worthwhile despite the higher price point. Ultimately, assessing the trade-offs between performance, cost, and maintenance will guide buyers to the most suitable option for their fleet or individual vehicles.
Essential Technical Properties and Trade Terminology for alloy wheel manufacturer
What Are the Essential Technical Properties for Alloy Wheel Manufacturing?
Understanding the key technical properties of alloy wheels is crucial for B2B buyers, particularly in regions like Africa, South America, the Middle East, and Europe. Here are some critical specifications that every buyer should consider:
-
Material Grade
– Definition: Alloy wheels are typically made from aluminum alloys, which may include specific grades such as 6061 or 7075.
– Importance: The material grade affects the wheel’s strength, weight, and corrosion resistance. A higher-grade alloy provides better performance and durability, which is essential for safety and longevity. -
Tolerance
– Definition: Tolerance refers to the permissible limit of variation in a wheel’s dimensions.
– Importance: Accurate tolerances ensure that wheels fit properly onto vehicles without issues. Poor tolerances can lead to vibrations, decreased performance, and increased wear on vehicle components. -
Weight
– Definition: The weight of an alloy wheel is a significant factor in vehicle performance.
– Importance: Lighter wheels improve fuel efficiency and handling. Understanding the weight specifications helps buyers choose wheels that meet their performance criteria without compromising structural integrity. -
Finish
– Definition: The surface treatment of alloy wheels, which can include anodizing, powder coating, or polishing.
– Importance: A good finish not only enhances aesthetic appeal but also provides protection against environmental factors like rust and corrosion, which is particularly important in humid or coastal areas. -
Load Rating
– Definition: The maximum weight that a wheel can support safely.
– Importance: Load ratings ensure that wheels can handle the weight of the vehicle and any additional loads. This is crucial for buyers in commercial sectors where vehicles carry heavy loads. -
Offset
– Definition: The distance from the wheel’s hub mounting surface to the centerline of the wheel.
– Importance: Offset affects handling and suspension geometry. Understanding the offset requirements for specific vehicle models can help buyers avoid compatibility issues.
Which Trade Terminology Should International Buyers Know?
Familiarizing yourself with common industry terms can streamline the procurement process for alloy wheels. Here are some essential terms:
-
OEM (Original Equipment Manufacturer)
– Definition: Refers to companies that produce parts that are used in the assembly of a vehicle by the original manufacturer.
– Importance: Buyers often prefer OEM parts for their reliability and compatibility with specific vehicle models. Understanding this term can help in sourcing quality products. -
MOQ (Minimum Order Quantity)
– Definition: The smallest quantity of a product that a supplier is willing to sell.
– Importance: Knowing the MOQ is crucial for budget management and inventory planning. Some suppliers may offer lower MOQs for new customers, which can be advantageous for smaller businesses. -
RFQ (Request for Quotation)
– Definition: A document sent by a buyer to suppliers requesting pricing and terms for a specific product or service.
– Importance: An RFQ is essential for comparing prices and terms among different suppliers, enabling buyers to make informed purchasing decisions. -
Incoterms (International Commercial Terms)
– Definition: A set of international rules that define the responsibilities of buyers and sellers for the delivery of goods under sales contracts.
– Importance: Understanding Incoterms helps buyers manage risks and costs associated with shipping and logistics, which is particularly relevant for international transactions. -
Lead Time
– Definition: The amount of time from when an order is placed until it is fulfilled.
– Importance: Knowledge of lead times is vital for planning and inventory management. Buyers should communicate their timelines to suppliers to ensure timely delivery. -
Certification Standards
– Definition: Standards that indicate a product meets specific quality and safety requirements, such as ISO or TUV certifications.
– Importance: Certifications assure buyers that the alloy wheels comply with industry standards, enhancing trust and reliability in the products purchased.
By understanding these technical properties and industry terms, international B2B buyers can make informed decisions, ensuring they procure the best alloy wheels for their needs.
Navigating Market Dynamics and Sourcing Trends in the alloy wheel manufacturer Sector
What are the Current Market Dynamics and Key Trends in the Alloy Wheel Manufacturing Sector?
The alloy wheel manufacturing sector is witnessing significant growth driven by several global factors. The increasing demand for lightweight and fuel-efficient vehicles is a primary driver, as alloy wheels contribute to reducing overall vehicle weight, enhancing performance, and improving fuel efficiency. Additionally, the rise in automotive production, especially in emerging markets like South Africa and Brazil, is creating new opportunities for B2B buyers seeking reliable suppliers.
Technological advancements are also reshaping the industry, with the adoption of automation and advanced manufacturing techniques such as 3D printing. These innovations not only streamline production processes but also allow for customization, catering to the specific needs of international buyers. Furthermore, the trend toward online sourcing platforms is gaining traction, enabling buyers from regions like the Middle East and Europe to connect with manufacturers globally, compare products, and negotiate better deals.
With the growing emphasis on vehicle aesthetics, the demand for innovative designs and finishes is increasing, compelling manufacturers to invest in R&D. Buyers should keep an eye on these trends as they can influence purchasing decisions and supplier selection.
How is Sustainability and Ethical Sourcing Shaping the Alloy Wheel Manufacturing Sector?
Sustainability is becoming a cornerstone in the alloy wheel manufacturing industry, driven by environmental concerns and consumer preferences. The production of alloy wheels often involves energy-intensive processes, which can lead to significant carbon emissions. Consequently, manufacturers are increasingly adopting eco-friendly practices, such as utilizing recycled materials and investing in energy-efficient technologies.
B2B buyers should prioritize suppliers who demonstrate a commitment to sustainability through certifications like ISO 14001 or adherence to environmental regulations. Ethical sourcing is equally important, as it ensures that the materials used in manufacturing are obtained responsibly and do not contribute to social or environmental harm.
Moreover, the use of ‘green’ materials, such as aluminum alloys with lower environmental footprints, is gaining popularity. Buyers who align their sourcing strategies with sustainable practices not only enhance their brand reputation but also meet the growing demand from consumers for environmentally responsible products.
What is the Historical Context of Alloy Wheel Manufacturing Relevant to B2B Buyers?
The alloy wheel manufacturing sector has evolved significantly since its inception in the mid-20th century. Initially, alloy wheels were primarily used in high-performance and luxury vehicles due to their superior strength and lightweight properties. Over the decades, advancements in metallurgy and manufacturing processes have made alloy wheels more accessible and affordable for mainstream automotive production.
In recent years, the shift towards electric vehicles has further accelerated the demand for alloy wheels, as manufacturers seek to optimize performance and efficiency. Understanding this historical context allows B2B buyers to appreciate the technological advancements and market shifts that influence current sourcing strategies. As the industry continues to evolve, buyers must remain informed about the latest trends and innovations to make strategic purchasing decisions.
Frequently Asked Questions (FAQs) for B2B Buyers of alloy wheel manufacturer
-
How do I choose the right alloy wheel manufacturer for my business?
Selecting an alloy wheel manufacturer requires careful consideration of several factors. Start by assessing their reputation and experience in the industry. Look for manufacturers with a track record of producing high-quality products that meet international standards. Additionally, consider their production capacity, lead times, and ability to customize products according to your specifications. Engage in direct communication to discuss your specific needs, and request samples to evaluate the quality of their wheels before making a decision. -
What are the advantages of sourcing alloy wheels from international manufacturers?
Sourcing alloy wheels internationally can provide several benefits, including access to advanced manufacturing technologies and materials that may not be available locally. International manufacturers often offer competitive pricing due to lower production costs in their regions. Additionally, they may have a wider variety of designs and specifications, enabling you to cater to diverse customer preferences. However, it’s essential to consider logistics and tariffs that may impact overall costs. -
What is the minimum order quantity (MOQ) for alloy wheels?
The MOQ for alloy wheels can vary significantly among manufacturers, typically ranging from a few hundred to several thousand units. It’s crucial to discuss your specific needs with potential suppliers to understand their MOQ requirements. Some manufacturers may offer flexibility for smaller orders, especially for new clients or for specific product lines. Negotiating the MOQ can lead to better terms, especially if you plan to establish a long-term partnership. -
How can I ensure the quality of alloy wheels from a manufacturer?
To ensure the quality of alloy wheels, request documentation of the manufacturer’s quality assurance processes. Look for certifications like ISO 9001, which indicate adherence to international quality management standards. It’s also advisable to request samples for testing and inspection. Consider visiting the manufacturing facility to observe their production processes firsthand. Additionally, establish a clear agreement on quality expectations and potential penalties for non-compliance. -
What payment terms should I negotiate with alloy wheel manufacturers?
Payment terms can vary widely between manufacturers, so it’s essential to negotiate favorable conditions that protect your interests. Common arrangements include a deposit upfront (typically 30-50%) with the balance due upon delivery or after inspection. Consider using secure payment methods such as letters of credit or escrow services to mitigate risks. Be sure to clarify the currency used for transactions and any additional fees that might apply. -
What customization options are available when ordering alloy wheels?
Many alloy wheel manufacturers offer customization options, including varying sizes, finishes, colors, and design patterns. When discussing your requirements, specify any unique features you want, such as weight reductions or enhanced durability. Some manufacturers may also offer design services to help create bespoke products tailored to your brand. It’s advisable to review their portfolio of previous custom projects to gauge their capabilities. -
How do logistics and shipping impact my sourcing of alloy wheels?
Logistics and shipping are critical factors in the sourcing process. Consider the lead times for production and the shipping duration from the manufacturer to your location. Evaluate the shipping options available, including air freight for faster delivery or sea freight for cost-effectiveness. Additionally, factor in customs duties and taxes that may apply when importing alloy wheels. Collaborating with a freight forwarder can streamline the logistics process and ensure compliance with international regulations. -
What are the key factors to consider for after-sales support from alloy wheel manufacturers?
After-sales support is vital for maintaining customer satisfaction and addressing potential issues with the alloy wheels. Inquire about the manufacturer’s warranty policy and the duration of coverage for defects or damages. Ensure they provide accessible channels for customer support and technical assistance. Additionally, consider their responsiveness to inquiries and their ability to supply replacement parts or services in case of defects. Establishing a good after-sales relationship can enhance your business reputation and customer loyalty.
Important Disclaimer & Terms of Use
⚠️ Important Disclaimer
The information provided in this guide, including content regarding manufacturers, technical specifications, and market analysis, is for informational and educational purposes only. It does not constitute professional procurement advice, financial advice, or legal advice.
While we have made every effort to ensure the accuracy and timeliness of the information, we are not responsible for any errors, omissions, or outdated information. Market conditions, company details, and technical standards are subject to change.
B2B buyers must conduct their own independent and thorough due diligence before making any purchasing decisions. This includes contacting suppliers directly, verifying certifications, requesting samples, and seeking professional consultation. The risk of relying on any information in this guide is borne solely by the reader.
Strategic Sourcing Conclusion and Outlook for alloy wheel manufacturer
In today’s competitive landscape, strategic sourcing is vital for B2B buyers seeking to enhance their supply chain efficiency and reduce costs when procuring alloy wheels. By engaging with reputable manufacturers and understanding the nuances of alloy composition, buyers can ensure they select products that not only meet quality standards but also align with their specific market needs.
Buyers from Africa, South America, the Middle East, and Europe must consider factors such as local regulations, import tariffs, and sustainability practices when sourcing. Establishing partnerships with manufacturers who prioritize innovation and quality can lead to long-term benefits, including increased customer satisfaction and brand loyalty.
Looking ahead, the demand for lightweight, durable alloy wheels is poised to grow, driven by advancements in automotive technology and consumer preferences for performance. International B2B buyers should proactively explore partnerships with manufacturers that demonstrate a commitment to quality and sustainability. By doing so, they position themselves to capitalize on emerging trends and maintain a competitive edge in their respective markets.
Take the next step—evaluate your sourcing strategies today and engage with industry leaders to secure the best alloy wheel solutions for your business.