Discover Top Benefits of Choosing a Bike Frame Supplier (2025)
Introduction: Navigating the Global Market for bike frame supplier
Navigating the global market for bike frame suppliers presents a unique set of challenges for international B2B buyers, especially those from regions such as Africa, South America, the Middle East, and Europe, including key markets like Poland and Egypt. The primary concern often revolves around sourcing high-quality bike frames that meet specific requirements while ensuring cost-effectiveness and timely delivery. This comprehensive guide aims to address these challenges by offering valuable insights into various types of bike frames, their applications, and the nuances of supplier vetting.
Throughout this guide, buyers will discover essential factors to consider when selecting a bike frame supplier, including material specifications, design options, and manufacturing capabilities. We will also delve into the financial aspects, helping you understand pricing structures and potential cost-saving strategies. Additionally, we will highlight best practices for evaluating suppliers, ensuring you make informed decisions that align with your business goals.
By the end of this guide, B2B buyers will be equipped with the knowledge and tools necessary to navigate the complexities of the bike frame supply market confidently. With a focus on empowering buyers from diverse regions, we aim to facilitate successful partnerships that enhance product offerings and drive business growth. Whether you are a startup or an established player in the cycling industry, understanding the global landscape of bike frame suppliers is crucial for staying competitive and meeting customer demands.
Understanding bike frame supplier Types and Variations
Type Name | Key Distinguishing Features | Primary B2B Applications | Brief Pros & Cons for Buyers |
---|---|---|---|
OEM Frame Suppliers | Custom designs, high-quality materials, often proprietary specs | Bicycle manufacturers, custom bike builders | Pros: Tailored solutions, high quality; Cons: Higher costs, longer lead times. |
Mass Production Suppliers | Standardized designs, economies of scale, quick turnaround | Retailers, large-scale distributors | Pros: Lower costs, high availability; Cons: Limited customization, potential quality variance. |
Specialty Frame Suppliers | Focus on niche markets (e.g., racing, mountain biking) | Specialty bike shops, performance-oriented brands | Pros: Unique designs, expert knowledge; Cons: Higher prices, limited production capacity. |
Local Frame Builders | Custom craftsmanship, local materials, often handmade | Boutique shops, local markets | Pros: Unique artistry, community support; Cons: Higher costs, longer production times. |
Importers/Distributors | Wide range of brands, import logistics, competitive pricing | Retailers, online marketplaces | Pros: Diverse product offerings, competitive pricing; Cons: Less direct control over quality. |
What are OEM Frame Suppliers and Their Key Characteristics?
OEM (Original Equipment Manufacturer) frame suppliers are known for their ability to provide custom designs tailored to specific manufacturer needs. These suppliers often utilize high-quality materials and proprietary specifications, making them ideal for bicycle manufacturers and custom bike builders looking for unique solutions. When considering an OEM supplier, B2B buyers should evaluate the supplier’s design capabilities, material sourcing, and lead times, as these factors significantly influence the overall project timeline and budget.
How Do Mass Production Suppliers Operate in the Market?
Mass production suppliers focus on standardized bike frame designs and benefit from economies of scale, allowing them to offer competitive pricing and quick turnaround times. They primarily serve retailers and large-scale distributors who require high volumes of products. For B2B buyers, the key considerations include the supplier’s production capacity, quality control measures, and the potential for variations in product quality. While mass production can lower costs, buyers must be aware of the trade-off regarding customization and quality assurance.
What Makes Specialty Frame Suppliers Unique?
Specialty frame suppliers cater to niche markets, such as racing or mountain biking, providing unique designs and expert knowledge in specific areas. These suppliers are often sought after by specialty bike shops and performance-oriented brands that prioritize quality and innovation. B2B buyers should assess the supplier’s expertise in their specific niche, the uniqueness of the designs offered, and the potential for collaboration on custom projects. While these frames may come at a higher price point, the investment often translates into superior performance and customer satisfaction.
Why Choose Local Frame Builders for Custom Projects?
Local frame builders are known for their craftsmanship and the use of local materials, often producing handmade frames that emphasize unique artistry. They are favored by boutique shops and local markets that want to support community businesses while offering distinctive products. B2B buyers should consider the builder’s reputation, the quality of materials used, and the time required for production. Although local frames can be more expensive and take longer to produce, they provide a unique selling proposition that can attract discerning customers.
What Role Do Importers and Distributors Play in the Bike Frame Market?
Importers and distributors offer a wide range of bike frame brands and styles, leveraging their logistics capabilities to provide competitive pricing. They primarily serve retailers and online marketplaces looking for diverse product offerings. B2B buyers should focus on the distributor’s reputation, the range of brands available, and their ability to manage import logistics effectively. While working with importers can provide cost advantages and variety, buyers must remain vigilant regarding quality control and the consistency of the products they receive.
Related Video: Carbon Vs Aluminium Vs Titanium Vs Steel: Which Bike Frame Material Is Best?
Key Industrial Applications of bike frame supplier
Industry/Sector | Specific Application of bike frame supplier | Value/Benefit for the Business | Key Sourcing Considerations for this Application |
---|---|---|---|
Bicycle Manufacturing | Supply of high-quality, lightweight frames | Enhanced product performance, leading to higher sales and customer satisfaction | Material quality, supplier certifications, lead time, and cost |
E-commerce & Retail | Custom bike frames for online sales | Unique product offerings that attract niche markets | Design capabilities, minimum order quantities, and shipping options |
Sports & Recreation Equipment | Frames for specialized sports bikes | Increased market appeal and brand differentiation | Technical specifications, compliance with safety standards |
Urban Mobility Solutions | Frames for electric bikes (e-bikes) | Support for sustainable transportation initiatives | Battery integration, weight considerations, and regulatory compliance |
Custom Fabrication Services | Bespoke frames for individual client specifications | Tailored solutions that meet specific customer needs | Flexibility in design, production capacity, and turnaround times |
How Are Bike Frame Suppliers Utilized in Bicycle Manufacturing?
In the bicycle manufacturing industry, bike frame suppliers provide essential components that determine the overall performance and durability of the bicycles. High-quality, lightweight frames enhance the riding experience, making them a critical factor for manufacturers looking to produce competitive models. International buyers must consider material quality, supplier certifications, and lead times to ensure they are sourcing frames that meet their performance standards while remaining cost-effective.
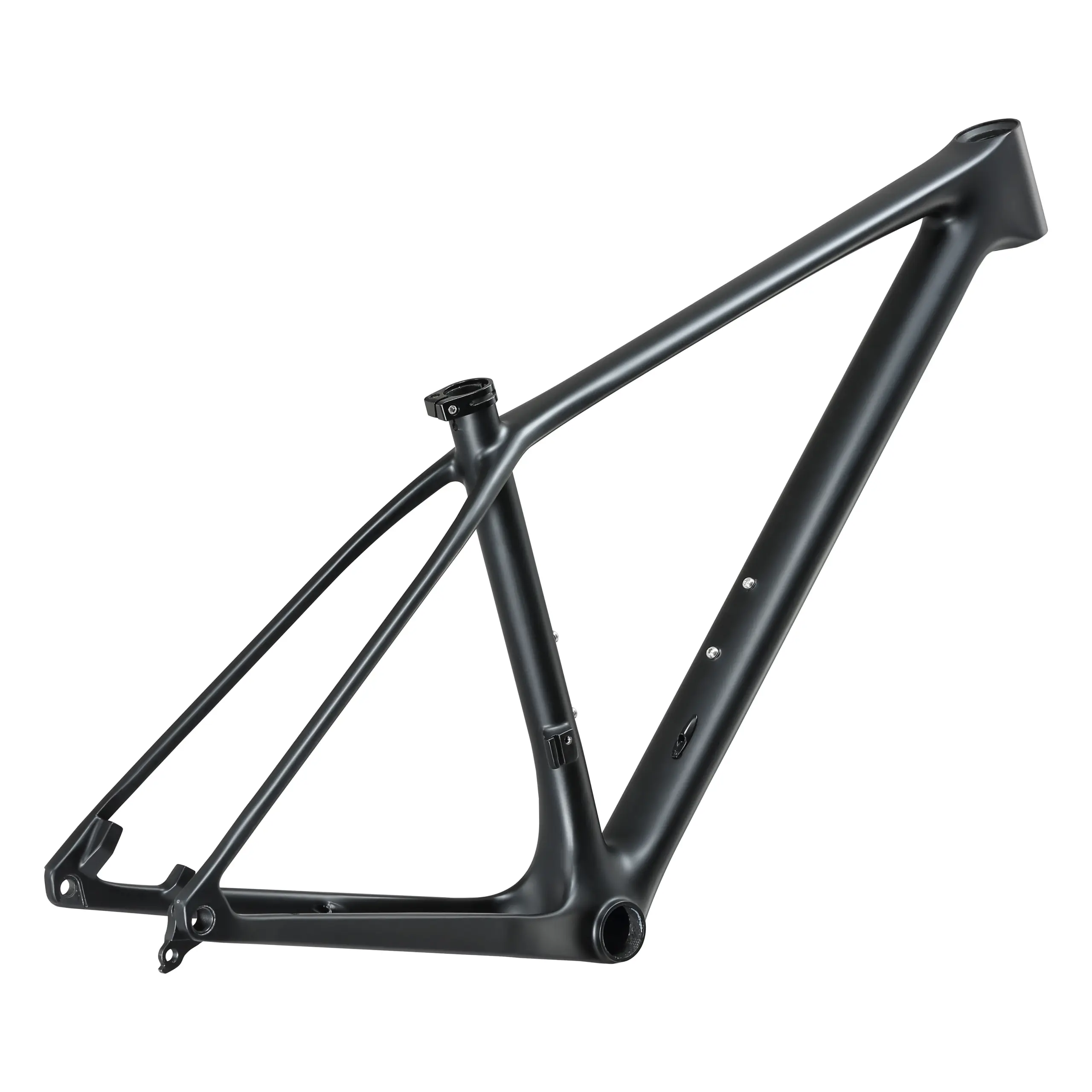
A stock image related to bike frame supplier.
What Role Do Bike Frame Suppliers Play in E-commerce & Retail?
E-commerce platforms and retail businesses often rely on bike frame suppliers to offer custom frames that cater to the unique preferences of customers. By providing a variety of designs and materials, suppliers enable retailers to differentiate their product offerings in a crowded market. Buyers should focus on a supplier’s design capabilities, minimum order quantities, and shipping options to ensure they can meet customer demands efficiently.
Why Are Specialized Frames Important in Sports & Recreation Equipment?
In the sports and recreation sector, bike frame suppliers create frames for specialized bikes, such as mountain or racing bikes. These frames are engineered for specific activities, enhancing performance and safety. Buyers in this industry should prioritize technical specifications and compliance with safety standards to ensure that the frames will perform well under rigorous conditions, which is crucial for maintaining brand reputation.
How Do Bike Frame Suppliers Support Urban Mobility Solutions?
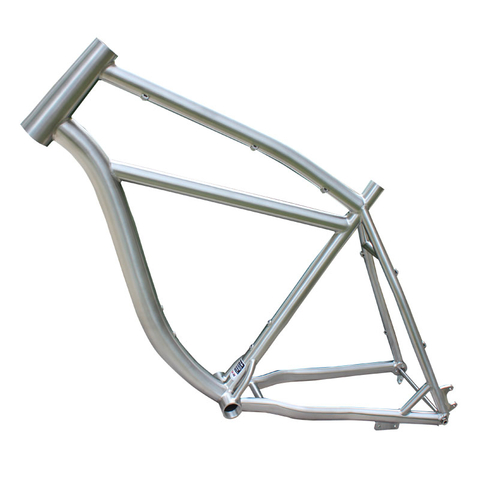
A stock image related to bike frame supplier.
Bike frame suppliers play a vital role in urban mobility solutions by supplying frames for electric bikes (e-bikes). As cities become more congested and environmentally conscious, e-bikes offer a sustainable transportation alternative. Buyers should consider factors such as battery integration, weight, and regulatory compliance when sourcing e-bike frames to ensure they meet local regulations and consumer preferences.
What Advantages Do Custom Fabrication Services Offer with Bike Frame Suppliers?
Custom fabrication services benefit from bike frame suppliers by creating bespoke frames tailored to individual client specifications. This flexibility allows businesses to cater to niche markets or specific customer demands effectively. Buyers should evaluate a supplier’s flexibility in design, production capacity, and turnaround times to ensure they can deliver tailored solutions promptly, enhancing customer satisfaction and loyalty.
Related Video: Sci6 Q3 – Characteristics and Uses of Simple Machines
3 Common User Pain Points for ‘bike frame supplier’ & Their Solutions
Scenario 1: Inconsistent Quality Across Suppliers
The Problem: International B2B buyers often face the challenge of inconsistent quality when sourcing bike frames from different suppliers. This issue is particularly pronounced for businesses in Africa and South America, where local manufacturing standards may not always align with global expectations. A buyer may receive a batch of bike frames that look visually appealing but fail to meet structural integrity or durability requirements. Such discrepancies can lead to increased returns, damaged reputations, and financial losses.
The Solution: To mitigate the risk of inconsistent quality, buyers should establish a clear set of quality standards and specifications before engaging with suppliers. This can include detailed material specifications, testing protocols, and compliance with international standards such as ISO 4210 for safety. Additionally, conducting factory audits and requesting samples for testing before bulk orders can significantly reduce the risk of quality issues. Partnering with suppliers who have a proven track record and positive reviews from other international buyers can further enhance reliability. Utilizing third-party quality assurance services can also provide an additional layer of oversight, ensuring that the frames meet the required standards before they reach the market.
Scenario 2: Complex Customs and Import Regulations
The Problem: Navigating the complexities of customs and import regulations can be a daunting task for B2B buyers, especially those operating across regions like the Middle East and Europe. Delays in customs clearance or unexpected tariffs can disrupt supply chains and lead to missed market opportunities. Buyers may find themselves in a situation where they have ordered a large shipment of bike frames, only to face unforeseen barriers upon arrival, resulting in costly delays and potential storage fees.
The Solution: To tackle these challenges, buyers should invest time in understanding the specific customs regulations of their target market. This includes researching import tariffs, required documentation, and any trade agreements that may be in place. Engaging a local customs broker or logistics provider who specializes in the bicycle industry can streamline the process significantly. They can assist in preparing the necessary paperwork and ensure compliance with local laws, reducing the risk of delays. Additionally, maintaining open communication with suppliers about shipping timelines and potential customs issues can help in planning for contingencies, ensuring that the supply chain remains robust and efficient.
Scenario 3: Limited Customization Options
The Problem: Many B2B buyers encounter limitations when it comes to customizing bike frames to suit their specific branding or performance needs. This challenge is especially relevant for companies looking to differentiate themselves in competitive markets across Europe and Africa. Buyers may find that suppliers offer only standard designs or colors, which does not allow for the unique branding that can attract customers and enhance market presence.
The Solution: To overcome this limitation, buyers should prioritize suppliers who offer flexible customization options. When initiating discussions with potential suppliers, it is essential to inquire about their capacity for custom designs, including frame geometry, colors, and branding elements. Developing a strong relationship with suppliers can lead to collaborative opportunities, where buyers can co-create designs that meet their specific needs. Additionally, leveraging advanced manufacturing technologies, such as 3D printing and CNC machining, can enable suppliers to offer greater customization without significantly increasing costs. By clearly communicating their vision and requirements, buyers can work with suppliers to create unique products that resonate with their target audience and strengthen their market position.
Strategic Material Selection Guide for bike frame supplier
What Are the Key Properties of Common Materials for Bike Frames?
When selecting materials for bike frames, international B2B buyers must consider various factors, including performance properties, manufacturing complexity, and cost-effectiveness. Here are four common materials used in bike frame manufacturing, along with their key properties, advantages, disadvantages, and considerations for international markets.
Aluminum: A Lightweight and Cost-Effective Option
Key Properties: Aluminum is known for its lightweight nature, good corrosion resistance, and decent strength-to-weight ratio. It typically performs well under a variety of temperatures, making it suitable for different climates.
Pros & Cons: The primary advantage of aluminum is its affordability and ease of manufacturing. However, it can be less durable than other materials, especially under extreme stress, leading to potential fatigue over time. Additionally, aluminum frames may require specific welding techniques, which can complicate manufacturing processes.
Impact on Application: Aluminum frames are highly compatible with various bike types, including mountain and road bikes. However, they may not perform as well in high-stress situations compared to stronger materials.
Considerations for International Buyers: Buyers from regions like Africa and South America should ensure compliance with local standards, such as ASTM for material quality. Aluminum’s cost-effectiveness makes it a popular choice in emerging markets, but understanding local manufacturing capabilities is crucial.
Steel: The Classic Choice for Durability
Key Properties: Steel is renowned for its high tensile strength and durability. It can withstand significant stress and is less likely to fail under pressure compared to aluminum.
Pros & Cons: The major advantage of steel is its durability and ability to absorb shocks, making it ideal for rugged terrains. However, it is heavier than aluminum and can be prone to rust if not properly treated, which may increase maintenance costs.
Impact on Application: Steel frames are particularly suitable for touring and commuter bikes, where durability is paramount. They offer a smooth ride due to their shock-absorbing properties.
Considerations for International Buyers: Buyers in Europe, particularly in Poland, may prefer steel due to its historical significance in bike manufacturing. Compliance with European standards (EN) is essential, and buyers should consider local suppliers who can provide high-quality steel that meets these regulations.
Carbon Fiber: The Premium Lightweight Alternative
Key Properties: Carbon fiber is exceptionally lightweight and offers a high strength-to-weight ratio. It is also resistant to corrosion and can be molded into complex shapes, allowing for innovative designs.
Pros & Cons: The key advantage of carbon fiber is its performance, making it ideal for high-end racing bikes. However, it is significantly more expensive than aluminum and steel, and its manufacturing process is complex, requiring specialized equipment.
Impact on Application: Carbon fiber frames excel in competitive environments, providing superior performance and responsiveness. However, they may not be suitable for all types of biking, particularly in rugged conditions where impacts could lead to damage.
Considerations for International Buyers: Buyers from the Middle East and Europe should be aware of the high costs associated with carbon fiber. Compliance with international standards for safety and performance is crucial, especially for high-end markets.
Titanium: The Luxury Material for High-End Bikes
Key Properties: Titanium is known for its exceptional strength, light weight, and resistance to corrosion. It performs well in a variety of temperatures and conditions.
Pros & Cons: The main advantage of titanium is its durability and comfort, as it can absorb vibrations effectively. However, it is one of the most expensive materials, and its manufacturing process is complex, requiring specialized skills.
Impact on Application: Titanium frames are ideal for high-end touring and performance bikes, offering a unique combination of weight, strength, and ride comfort.
Considerations for International Buyers: Buyers from regions like Europe may find titanium appealing due to its prestige and performance benefits. However, they should consider the availability of skilled manufacturers who can work with titanium and ensure compliance with local standards.
Summary Table of Material Selection for Bike Frames
Material | Typical Use Case for bike frame supplier | Key Advantage | Key Disadvantage/Limitation | Relative Cost (Low/Med/High) |
---|---|---|---|---|
Aluminum | Mountain and road bikes | Lightweight and cost-effective | Less durable under extreme stress | Low |
Steel | Touring and commuter bikes | High durability and shock absorption | Heavier and prone to rust | Medium |
Carbon Fiber | High-end racing bikes | Superior performance and lightweight | High cost and complex manufacturing | High |
Titanium | High-end touring and performance bikes | Exceptional strength and comfort | Very high cost and manufacturing complexity | High |
This strategic material selection guide provides a comprehensive overview for international B2B buyers, enabling informed decisions based on material properties, application suitability, and regional considerations.
In-depth Look: Manufacturing Processes and Quality Assurance for bike frame supplier
What Are the Key Stages in the Manufacturing Process of Bike Frames?
The manufacturing process for bike frames involves several critical stages that ensure the final product is both durable and lightweight. Understanding these stages is essential for B2B buyers looking for reliable suppliers.
1. Material Preparation
The first step in bike frame manufacturing is material preparation. Common materials include aluminum, carbon fiber, and steel, each chosen for its specific properties.
- Material Selection: Aluminum is lightweight and resistant to corrosion, making it a popular choice for many bike frames. Carbon fiber offers superior strength-to-weight ratios, ideal for high-performance bikes. Steel, while heavier, is valued for its durability and ease of repair.
- Cutting and Shaping: Once selected, materials are cut into specific shapes using precision tools. This stage often employs CNC (Computer Numerical Control) machines for accuracy, ensuring that each component meets design specifications.
2. Forming
After preparation, the next phase is forming, where the raw materials are shaped into the desired frame components.
- Welding and Joining Techniques: Common methods include TIG (Tungsten Inert Gas) welding for aluminum and steel frames, while carbon frames are typically bonded using specialized adhesives. Each method has its advantages in terms of strength and weight.
- Molding for Carbon Frames: For carbon fiber frames, molding processes such as layup or infusion are used, where layers of carbon fabric are placed in a mold and cured under heat and pressure.
3. Assembly
The assembly stage involves bringing together all individual components into a complete bike frame.
- Jigging: Frames are assembled using jigs that hold the components in place during welding or bonding, ensuring precision alignment.
- Quality Checks: During assembly, manufacturers conduct preliminary quality checks to identify any defects or misalignments before the frame undergoes finishing.
4. Finishing
Finishing processes enhance the bike frame’s appearance and protect it from environmental factors.
- Surface Treatments: Treatments such as anodizing for aluminum or powder coating for steel provide a protective layer while improving aesthetics.
- Final Inspection: A thorough inspection is conducted to ensure that the frame meets all specifications, followed by the application of branding and other cosmetic elements.
How Is Quality Assurance Implemented in Bike Frame Manufacturing?
Quality assurance (QA) in bike frame manufacturing is critical for ensuring product reliability and compliance with international standards. B2B buyers must understand the QA measures that suppliers implement.
Relevant International Standards for Bike Frames
- ISO 9001: This standard focuses on quality management systems and is essential for ensuring consistent quality in manufacturing processes. Suppliers certified to ISO 9001 demonstrate a commitment to continuous improvement and customer satisfaction.
- CE Marking: In Europe, bike frames must meet certain safety and health standards to bear the CE mark, indicating compliance with EU regulations.
What Are the Key Quality Control Checkpoints?
Quality control (QC) is conducted at various checkpoints throughout the manufacturing process to ensure the highest standards are maintained.
- Incoming Quality Control (IQC): At this stage, raw materials are inspected for defects before they enter the manufacturing process. This includes checking material specifications and certifications.
- In-Process Quality Control (IPQC): During manufacturing, ongoing inspections are conducted to monitor critical parameters such as weld integrity and material thickness. This helps catch issues before they escalate.
- Final Quality Control (FQC): After finishing, the final product undergoes extensive testing to ensure it meets all specifications. This includes visual inspections, dimensional checks, and functional tests.
Common Testing Methods for Bike Frames
B2B buyers should be aware of the various testing methods used to verify the quality of bike frames:
- Fatigue Testing: This assesses how well a frame can withstand repeated stress over time, simulating real-world usage.
- Impact Testing: Evaluates the frame’s ability to withstand sudden shocks or impacts, ensuring safety and durability.
- Corrosion Testing: For frames exposed to harsh environments, tests are conducted to determine the material’s resistance to corrosion.
How Can B2B Buyers Verify Supplier Quality Control?
For international B2B buyers, particularly from regions like Africa, South America, the Middle East, and Europe, verifying a supplier’s quality control measures is crucial.
Conducting Supplier Audits
- On-Site Audits: Visiting the supplier’s manufacturing facility allows buyers to observe the production process firsthand, assess equipment, and review quality control documentation.
- Documentation Review: Buyers should request and review the supplier’s quality management documentation, including certifications, inspection reports, and testing results.
Utilizing Third-Party Inspections
Engaging third-party inspection services can provide an unbiased assessment of the supplier’s quality practices. These services can conduct:
- Pre-Shipment Inspections: Assess the quality and quantity of products before shipment, ensuring they meet agreed specifications.
- Random Sampling: Conduct random checks on a selection of frames to validate overall quality against industry standards.
What Nuances Should International Buyers Consider Regarding QC and Certification?
When engaging with suppliers from diverse regions, B2B buyers must navigate various nuances in quality control and certification.
- Regional Certifications: Different regions may have specific standards or certifications that are more relevant. For instance, the API (American Petroleum Institute) certification may not be applicable for bike frames but is crucial in other industries.
- Cultural Differences in Quality Standards: Buyers should be aware that cultural perceptions of quality can vary. What is considered acceptable in one region may not meet the expectations in another. Thus, open communication regarding quality standards is essential.
Conclusion
Understanding the manufacturing processes and quality assurance measures is vital for B2B buyers in the bike frame industry. By focusing on material preparation, forming, assembly, and finishing stages, along with robust quality control practices, buyers can make informed decisions when selecting suppliers. Emphasizing international standards and verification methods will further enhance their procurement strategies, ensuring they partner with reliable manufacturers who meet their quality expectations.
Practical Sourcing Guide: A Step-by-Step Checklist for ‘bike frame supplier’
In the competitive landscape of international B2B procurement, selecting the right bike frame supplier is critical for ensuring product quality, reliability, and cost-effectiveness. This practical sourcing guide will provide you with a step-by-step checklist to streamline your procurement process and help you make informed decisions.
Step 1: Define Your Technical Specifications
Before engaging with suppliers, clearly outline your technical requirements for bike frames. This includes material types (aluminum, carbon fiber, steel), weight limits, design specifications, and intended use (e.g., racing, mountain biking, or commuting). Defining these specifications upfront will guide your discussions with suppliers and ensure they can meet your needs.
- Consider regional preferences: Different markets may have specific preferences for bike frame types based on local terrain and cycling culture.
- Assess future scalability: Think about how your specifications might evolve as your business grows.
Step 2: Research Potential Suppliers
Conduct thorough research to identify potential bike frame suppliers. Utilize online platforms, industry trade shows, and referrals from trusted contacts to compile a list of candidates.
- Look for industry experience: Suppliers with a proven track record in the bike frame market are more likely to understand your needs.
- Investigate their client base: Suppliers serving similar markets or products can indicate their reliability and capability.
Step 3: Evaluate Supplier Certifications
Certifications can provide assurance of quality and compliance with industry standards. Check if the suppliers hold relevant certifications such as ISO 9001 for quality management systems or specific safety certifications pertinent to your market.
- Request documentation: Ask for copies of certifications to verify their validity.
- Understand regional compliance: Different regions may have unique regulations that suppliers must adhere to.
Step 4: Request Samples and Prototypes
Before making a large order, request samples or prototypes of the bike frames. This allows you to assess the quality, weight, and overall craftsmanship.
- Conduct physical tests: Ensure the samples meet your specifications and can withstand the expected use conditions.
- Involve your team: Get feedback from your design or engineering team to ensure the frames align with your product vision.
Step 5: Negotiate Pricing and Terms
Once you have identified a potential supplier, enter negotiations. Discuss pricing, payment terms, minimum order quantities, and delivery timelines.
- Consider total cost of ownership: Factor in shipping, import duties, and potential tariffs when evaluating costs.
- Explore long-term partnerships: Building a relationship with a supplier can lead to better pricing and more favorable terms in the future.
Step 6: Check References and Reviews
Before finalizing a supplier, check their references and read reviews from other clients. This step helps you gauge the supplier’s reliability and service quality.
- Ask for case studies: Suppliers should be able to provide examples of their previous work, especially in your industry.
- Network within your region: Reach out to other businesses in your area that have worked with the supplier for firsthand insights.
Step 7: Establish a Communication Plan
Effective communication is vital for a successful partnership. Establish a clear communication plan that defines points of contact, preferred communication methods, and response times.
- Set expectations: Clearly outline what you expect in terms of updates and responsiveness.
- Utilize technology: Consider using collaborative tools to facilitate ongoing communication and project management.
By following this checklist, international B2B buyers can streamline their sourcing process for bike frame suppliers, ensuring they choose partners who align with their business goals and quality standards.
Comprehensive Cost and Pricing Analysis for bike frame supplier Sourcing
What Are the Key Cost Components in Sourcing Bike Frames?
When sourcing bike frames, understanding the cost structure is essential for B2B buyers. The primary cost components include:
-
Materials: The type of materials used significantly impacts the price. Common materials include aluminum, steel, carbon fiber, and titanium, each with varying costs. For example, carbon fiber frames are lightweight and strong but tend to be the most expensive.
-
Labor: Labor costs vary by region and the complexity of the manufacturing process. Regions with higher labor costs, such as parts of Europe, may yield higher prices compared to countries in Africa or South America where labor is generally less expensive.
-
Manufacturing Overhead: This includes costs related to factory operations, such as utilities, equipment maintenance, and salaries of non-production staff. Efficient manufacturing processes can reduce overhead costs, making it crucial to evaluate the supplier’s operational efficiency.
-
Tooling: The initial setup costs for manufacturing tools and molds can be significant. If a supplier has already invested in tooling for specific designs, they may offer better pricing.
-
Quality Control (QC): Ensuring that frames meet specific standards incurs costs, particularly for certifications and testing. For international buyers, checking the supplier’s QC processes is vital to ensure compliance with local standards.
-
Logistics: Shipping costs vary based on the distance, weight, and shipping methods chosen. Understanding Incoterms can help clarify who bears these costs and responsibilities.
-
Margin: The supplier’s profit margin will also influence the final price. Suppliers in competitive markets may offer lower margins to attract buyers, while those with unique offerings may price higher.
How Do Pricing Influencers Affect Bike Frame Costs?
Several factors can influence the pricing of bike frames, including:
-
Volume and Minimum Order Quantities (MOQ): Suppliers often offer discounts for bulk orders. Understanding the MOQ can help buyers negotiate better pricing, especially when considering long-term partnerships.
-
Specifications and Customization: Customized frames tailored to specific needs can increase costs. Buyers should assess whether the benefits of customization outweigh the added expenses.
-
Material Quality and Certifications: Higher quality materials or those with specific certifications (e.g., ISO standards) can increase costs. Buyers should evaluate whether these certifications are necessary for their target markets.
-
Supplier Factors: The supplier’s reputation, experience, and reliability can impact pricing. Established suppliers may charge a premium for their proven track record.
-
Incoterms: Understanding the terms of shipment is crucial for cost estimation. Different Incoterms can shift responsibilities and costs between the buyer and seller, affecting the total expenditure.
What Negotiation Tips Can Help Achieve Cost Efficiency in Bike Frame Sourcing?
For international B2B buyers, particularly from Africa, South America, the Middle East, and Europe, effective negotiation can lead to substantial savings. Here are some actionable tips:
-
Build Relationships: Establishing a rapport with suppliers can lead to better terms. Suppliers are more likely to offer discounts or favorable terms to long-term partners.
-
Leverage Volume: If possible, consolidate orders to reach MOQ thresholds, which can reduce unit costs significantly.
-
Analyze Total Cost of Ownership (TCO): Beyond the purchase price, consider shipping, duties, and potential warranty costs. A lower initial price may result in higher long-term costs.
-
Request Price Breakdowns: Ask suppliers for detailed cost breakdowns to identify areas where you can negotiate. Understanding the cost structure allows for more informed discussions.
-
Stay Informed on Market Trends: Awareness of material costs and global supply chain dynamics can provide leverage during negotiations.
Why Is It Important to Understand Pricing Nuances for International B2B Buyers?
Understanding the pricing nuances in sourcing bike frames is crucial for effective budgeting and procurement strategies. International buyers face unique challenges, such as fluctuating exchange rates, varying import duties, and shipping complexities. Additionally, cultural differences in negotiation styles and business practices can impact pricing discussions.
Always remember that prices may vary significantly based on location, supplier capabilities, and market conditions. It’s advisable to gather multiple quotes and conduct thorough due diligence before finalizing a supplier.
Disclaimer on Indicative Prices
Prices for bike frames can fluctuate based on numerous factors, including market demand, raw material costs, and geopolitical influences. Therefore, the figures provided in any sourcing discussions should be considered indicative and subject to change. Always confirm current pricing directly with suppliers.
Alternatives Analysis: Comparing bike frame supplier With Other Solutions
In the evolving landscape of the bicycle manufacturing industry, B2B buyers must consider various solutions when sourcing bike frames. While traditional bike frame suppliers offer specific advantages, alternative methods can provide distinct benefits that may align better with certain business needs. Below, we compare the conventional bike frame supplier with two viable alternatives: custom frame manufacturing and sourcing from international suppliers.
Comparison Aspect | Bike Frame Supplier | Custom Frame Manufacturing | International Sourcing |
---|---|---|---|
Performance | High quality, consistent | Tailored to specifications | Variable quality |
Cost | Moderate to high | Higher due to labor and materials | Lower due to global pricing |
Ease of Implementation | Streamlined procurement | More complex, requires design input | Varies by supplier |
Maintenance | Established support | Dependent on manufacturer | Support can be inconsistent |
Best Use Case | Large-scale production | Niche markets, specialized needs | Cost-sensitive markets |
What Are the Advantages and Disadvantages of Custom Frame Manufacturing?
Custom frame manufacturing allows for complete personalization of bike frames, which can be crucial for niche markets or specialized needs. This approach ensures that the frames meet specific performance criteria and fit unique design requirements. However, the cons include higher costs associated with labor and materials, along with a more complex implementation process that requires design input from the buyer. Buyers must weigh the benefits of customization against the increased costs and logistical considerations.
How Does International Sourcing Compare to Local Suppliers?
International sourcing involves purchasing bike frames from overseas suppliers, often at a lower cost due to favorable economic conditions in other countries. This method can provide significant savings for businesses looking to minimize expenses. However, the trade-off can be variable quality and potential difficulties in communication and support. Buyers must consider the reliability of the international suppliers and the implications of longer shipping times and customs regulations.
Conclusion: How to Choose the Right Solution for Your Needs?
Choosing the right solution for sourcing bike frames depends on the specific requirements of your business. If you are aiming for high-quality, consistent products for large-scale production, a traditional bike frame supplier may be the best fit. However, if you are targeting a niche market with specialized needs, custom frame manufacturing could be more advantageous despite the higher costs. Alternatively, for businesses focused on minimizing expenses, international sourcing presents a viable option but requires careful consideration of quality and supplier reliability. Ultimately, a thorough analysis of your operational goals, budget constraints, and market demands will guide you to the most suitable option.
Essential Technical Properties and Trade Terminology for bike frame supplier
What Are the Essential Technical Properties of Bike Frames?
Understanding the technical specifications of bike frames is crucial for international B2B buyers, especially when sourcing from diverse markets like Africa, South America, the Middle East, and Europe. Below are some of the key properties that should be considered:
1. Material Grade
Definition: The material grade refers to the quality and type of material used in the construction of bike frames, such as aluminum, carbon fiber, or steel.
B2B Importance: Different material grades impact the frame’s weight, strength, and durability. For instance, carbon fiber is lighter and offers better vibration dampening, while aluminum is more cost-effective and resistant to corrosion. Buyers should assess material grades based on their target market’s needs and preferences, ensuring they meet local regulations and customer expectations.
2. Frame Geometry
Definition: Frame geometry encompasses the dimensions and angles of the bike frame, which influence the bike’s handling and rider comfort.
B2B Importance: Understanding geometry is essential for ensuring that the bike fits the target demographic. For example, a bike intended for city commuting may have a more upright geometry for comfort, while a racing bike will have a more aggressive geometry for performance. Buyers should communicate these requirements clearly to suppliers to avoid mismatches.
3. Tolerance Levels
Definition: Tolerance levels indicate the allowable deviation in dimensions during manufacturing, such as the thickness of the tubing or the alignment of frame components.
B2B Importance: Tight tolerances are critical for ensuring that parts fit together correctly and perform well. Inconsistent tolerances can lead to structural weaknesses or performance issues. Buyers must inquire about the supplier’s manufacturing processes to ensure they can meet the required tolerances.
4. Weight Capacity
Definition: The weight capacity specifies the maximum load the bike frame can safely support, including the rider and any additional cargo.
B2B Importance: Different markets have varying expectations for weight capacity, especially in regions where cargo bikes or delivery bikes are prevalent. Buyers should ensure that the frames can accommodate typical loads encountered in their target markets.
5. Finish and Coating
Definition: The finish and coating refer to the surface treatment applied to the bike frame, such as anodizing or powder coating.
B2B Importance: The right finish not only enhances aesthetics but also improves durability and corrosion resistance. Buyers should consider environmental factors in their regions, as a frame’s finish can significantly affect its lifespan.
Which Trade Terms Are Commonly Used in the Bike Frame Industry?
Familiarity with industry terminology is essential for effective communication and negotiation in B2B transactions. Here are some commonly used terms:
1. OEM (Original Equipment Manufacturer)
Definition: An OEM is a company that manufactures products that are sold under another company’s brand.
Importance: Understanding OEM relationships can help buyers identify potential suppliers who can produce custom frames or components tailored to their specifications.
2. MOQ (Minimum Order Quantity)
Definition: MOQ is the smallest quantity of a product that a supplier is willing to sell.
Importance: Knowing the MOQ is critical for budget planning and inventory management. Buyers from different regions may face varying MOQs based on local market conditions.
3. RFQ (Request for Quotation)
Definition: An RFQ is a document sent to suppliers to request pricing and terms for specific products.
Importance: Issuing an RFQ allows buyers to compare offers from multiple suppliers, ensuring they receive competitive pricing and favorable terms.
4. Incoterms (International Commercial Terms)
Definition: Incoterms are a series of pre-defined commercial terms published by the International Chamber of Commerce, which clarify the responsibilities of buyers and sellers regarding shipping and delivery.
Importance: Understanding Incoterms helps buyers manage shipping risks and costs effectively, ensuring that both parties are clear on who bears responsibility during transport.
5. Lead Time
Definition: Lead time refers to the amount of time it takes from placing an order to receiving the goods.
Importance: Knowing the lead time is essential for inventory management and planning. Buyers should factor this into their supply chain strategy to avoid stockouts or production delays.
By grasping these technical properties and trade terminologies, B2B buyers can make informed decisions when sourcing bike frames, leading to successful partnerships and satisfied customers.
Navigating Market Dynamics and Sourcing Trends in the bike frame supplier Sector
What Are the Key Market Dynamics Influencing B2B Buyers in the Bike Frame Supplier Sector?
The bike frame supplier sector is experiencing significant transformation driven by global trends, technological advancements, and shifting consumer preferences. A major driver is the increasing demand for sustainable transportation solutions, particularly in urban areas across Africa, South America, the Middle East, and Europe. Governments are promoting cycling as a viable alternative to reduce traffic congestion and lower carbon emissions. This trend is coupled with a rise in e-commerce, allowing B2B buyers to source bike frames directly from manufacturers worldwide, thereby streamlining their supply chains.
Emerging technologies such as 3D printing and advanced materials are revolutionizing the production of bike frames. These technologies enable suppliers to offer customizable solutions, reduce lead times, and lower production costs. Moreover, the integration of IoT (Internet of Things) in bike manufacturing is enhancing product tracking and quality control, which is a critical consideration for international buyers looking for reliable suppliers.
Buyers from diverse regions, including Europe and the Middle East, are increasingly looking for suppliers who can offer competitive pricing without compromising on quality. This shift is leading to a more dynamic market where international partnerships are crucial. B2B buyers should focus on suppliers who demonstrate flexibility and responsiveness to market demands, ensuring they can adapt to changing consumer preferences.
How Important Is Sustainability and Ethical Sourcing for Bike Frame Suppliers?
Sustainability is no longer just a buzzword; it has become a core component of the supply chain in the bike frame industry. The environmental impact of manufacturing processes is under scrutiny, and international buyers are seeking suppliers who prioritize eco-friendly practices. This includes the use of recycled materials, energy-efficient production methods, and waste reduction strategies.
Ethical sourcing is equally important, as consumers are increasingly aware of the social implications of their purchases. Buyers should look for suppliers who are transparent about their sourcing practices and can demonstrate compliance with international labor standards. Certifications such as ISO 14001 for environmental management and Fair Trade practices can serve as indicators of a supplier’s commitment to sustainability and ethical practices.
Incorporating ‘green’ certifications and materials into the procurement process not only enhances brand reputation but also aligns with the values of environmentally conscious consumers. Buyers should evaluate potential suppliers based on their sustainability practices and the certifications they hold, ensuring they partner with companies that contribute positively to the environment and society.
What Is the Historical Context of the Bike Frame Supplier Sector?
The bike frame supplier sector has evolved significantly over the decades, transitioning from basic steel frames to advanced materials such as aluminum, carbon fiber, and titanium. Initially, the industry was dominated by local manufacturers who served regional markets. However, globalization has opened the doors for international suppliers, enabling cross-border trade and collaboration.
In recent years, the rise of the cycling culture and the push for sustainable transport solutions have further accelerated growth in this sector. The emergence of e-bikes has also transformed the landscape, creating new opportunities for suppliers who can innovate and adapt to changing consumer demands. As a result, the bike frame supplier industry is now characterized by a diverse range of products and a global supply chain, making it crucial for B2B buyers to stay informed about market trends and supplier capabilities.
By understanding these dynamics, international buyers can make informed decisions that align with their business goals and sustainability commitments.
Frequently Asked Questions (FAQs) for B2B Buyers of bike frame supplier
-
How do I evaluate a bike frame supplier for quality assurance?
When assessing a bike frame supplier, start by reviewing their certifications and compliance with international quality standards, such as ISO 9001. Request samples of their products to evaluate material quality and craftsmanship. Additionally, seek references from other clients to understand their experience with the supplier’s reliability and after-sales support. Regular audits and visits to the supplier’s manufacturing facility can further ensure that their quality assurance processes meet your expectations. -
What factors should I consider when negotiating payment terms with a bike frame supplier?
Negotiating payment terms is critical in establishing a mutually beneficial relationship. Consider factors such as order size, supplier trustworthiness, and your cash flow requirements. Common terms include a deposit upfront (typically 30-50%), with the balance due upon delivery or after inspection. Always clarify the implications of late payments and explore options for letters of credit or escrow services to protect both parties during the transaction. -
What are the minimum order quantities (MOQ) I should expect from bike frame suppliers?
Minimum order quantities (MOQ) can vary significantly based on the supplier and the complexity of the bike frame design. Typically, MOQs range from 100 to 500 units. When negotiating, consider discussing the possibility of lower MOQs for initial orders, especially if you plan to establish a long-term partnership. This flexibility can be advantageous for new businesses looking to test market demand without significant upfront investment. -
How can I customize bike frames to meet my brand’s specifications?
Most bike frame suppliers offer customization options, including frame geometry, materials, colors, and branding elements. To ensure your specifications are met, provide detailed drawings and specifications, and engage in direct communication with the supplier. Some suppliers may also offer prototyping services, allowing you to test and refine your design before full-scale production. Be sure to discuss lead times and costs associated with customization during negotiations. -
What logistics considerations should I keep in mind when sourcing bike frames internationally?
When sourcing bike frames internationally, consider shipping methods, costs, and timelines. Air freight is faster but more expensive than sea freight, which is more economical for larger shipments. Additionally, understand the customs regulations in your country and any potential tariffs that may apply. Work with a reliable freight forwarder who can assist with documentation and ensure compliance with international trade laws. -
How do I ensure compliance with international trade regulations when sourcing bike frames?
To ensure compliance, familiarize yourself with the import/export regulations of both your country and the supplier’s country. This includes understanding tariffs, quotas, and necessary documentation such as certificates of origin and safety standards. It’s advisable to consult with a trade compliance expert or legal advisor to avoid potential penalties and ensure that all products meet the necessary safety and quality standards. -
What are the common quality control measures for bike frame suppliers?
Quality control measures vary by supplier but generally include inspections at multiple stages of production, such as raw material sourcing, in-process checks, and final product evaluations. Suppliers may use non-destructive testing methods to ensure structural integrity and perform cycle testing to assess performance under real-world conditions. Request detailed quality assurance reports and consider third-party inspections to verify compliance with your standards. -
How can I build a long-term relationship with a bike frame supplier?
Building a long-term relationship with a bike frame supplier requires clear communication, mutual respect, and regular engagement. Establish open lines of communication to address any issues promptly and provide feedback on product performance. Regularly evaluate the partnership’s benefits, and consider collaborative projects or joint marketing initiatives to strengthen ties. Being transparent about your business goals can also help align both parties’ interests for future growth.
Important Disclaimer & Terms of Use
⚠️ Important Disclaimer
The information provided in this guide, including content regarding manufacturers, technical specifications, and market analysis, is for informational and educational purposes only. It does not constitute professional procurement advice, financial advice, or legal advice.
While we have made every effort to ensure the accuracy and timeliness of the information, we are not responsible for any errors, omissions, or outdated information. Market conditions, company details, and technical standards are subject to change.
B2B buyers must conduct their own independent and thorough due diligence before making any purchasing decisions. This includes contacting suppliers directly, verifying certifications, requesting samples, and seeking professional consultation. The risk of relying on any information in this guide is borne solely by the reader.
Strategic Sourcing Conclusion and Outlook for bike frame supplier
In navigating the competitive landscape of bike frame suppliers, international B2B buyers, particularly from regions such as Africa, South America, the Middle East, and Europe, must embrace strategic sourcing as a core component of their procurement strategy. Strategic sourcing not only enhances cost-effectiveness but also fosters long-term partnerships with suppliers who align with your business goals and values. By prioritizing quality, sustainability, and innovation in supplier selection, businesses can secure a competitive edge in the rapidly evolving bicycle market.
What are the key considerations for B2B buyers in selecting a bike frame supplier? It is essential to assess supplier capabilities, production quality, and responsiveness to market trends. Engaging in thorough supplier evaluations and leveraging data analytics will enable buyers to make informed decisions that drive operational efficiency and product excellence.
Looking ahead, the demand for high-quality and environmentally sustainable bike frames will only increase. Buyers are encouraged to adopt a proactive approach, continuously seeking out innovative suppliers and exploring emerging markets. By doing so, you can position your business at the forefront of the cycling industry’s growth, ensuring you meet the evolving needs of your customers while contributing to a sustainable future.