Discover Top Benefits of Choosing a Cabinets Supplier (2025)
Introduction: Navigating the Global Market for cabinets supplier
In the dynamic landscape of international trade, sourcing high-quality cabinets from reliable suppliers can pose significant challenges for B2B buyers. Whether you are looking for kitchen cabinets, office storage solutions, or custom cabinetry, navigating the global market requires a strategic approach. This guide delves into the complexities of finding the right cabinets supplier, addressing critical factors such as product types, applications across various industries, supplier vetting processes, and cost considerations.
For international buyers from regions like Africa, South America, the Middle East, and Europe—including high-demand markets such as the UAE and Vietnam—making informed purchasing decisions is essential. This comprehensive resource aims to empower you with actionable insights, helping you evaluate potential suppliers based on quality, reliability, and compliance with international standards.
Moreover, it highlights practical strategies to assess supplier capabilities, manage risks, and negotiate favorable terms. By leveraging the information presented, you will enhance your procurement strategies, ensuring that your organization not only meets but exceeds its cabinetry needs in a competitive global marketplace.
Understanding cabinets supplier Types and Variations
Type Name | Key Distinguishing Features | Primary B2B Applications | Brief Pros & Cons for Buyers |
---|---|---|---|
Custom Cabinet Suppliers | Tailored designs, materials, and finishes | High-end retail, luxury homes, commercial spaces | Pros: Unique solutions, high-quality craftsmanship. Cons: Longer lead times, higher costs. |
Modular Cabinet Suppliers | Pre-fabricated units, easy assembly | Offices, schools, healthcare facilities | Pros: Cost-effective, quicker installation. Cons: Limited customization, may not fit all spaces. |
Specialty Cabinet Suppliers | Focus on specific industries (e.g., kitchens, bathrooms) | Residential renovations, specialized commercial projects | Pros: Expertise in niche markets, tailored functionality. Cons: May have higher prices, less flexibility in design. |
Eco-Friendly Cabinet Suppliers | Sustainable materials, environmentally friendly processes | Green building projects, eco-conscious businesses | Pros: Supports sustainability goals, unique materials. Cons: Potentially higher costs, availability may vary. |
Wholesale Cabinet Suppliers | Bulk purchasing options, standard designs | Large-scale projects, renovations, new constructions | Pros: Lower prices, large inventory. Cons: Limited design options, may require additional customization. |
What Are the Key Characteristics of Custom Cabinet Suppliers?
Custom cabinet suppliers specialize in creating bespoke solutions tailored to the specific needs of their clients. These suppliers offer a wide range of materials, finishes, and designs, allowing businesses to achieve a unique aesthetic that aligns with their brand identity. They are particularly suitable for high-end retail environments, luxury residential projects, and commercial spaces where personalization is paramount. When purchasing from custom suppliers, buyers should consider lead times, as bespoke orders typically take longer to fulfill, and costs, which can be significantly higher than standard options.
How Do Modular Cabinet Suppliers Differ from Others?
Modular cabinet suppliers provide pre-fabricated units that can be easily assembled on-site. This type of cabinet is ideal for businesses looking for cost-effective solutions that do not compromise on quality. Common applications include office spaces, schools, and healthcare facilities, where quick installation is often necessary. Buyers should weigh the benefits of reduced installation time and lower costs against the limitations of customization, as modular options may not fit every specific design requirement.
What Makes Specialty Cabinet Suppliers Unique?
Specialty cabinet suppliers focus on specific industries, such as kitchens, bathrooms, or commercial applications. Their expertise allows them to deliver products that meet the unique demands of their target markets, making them an excellent choice for residential renovations or specialized commercial projects. When purchasing from specialty suppliers, buyers should evaluate the supplier’s experience and track record in their particular industry, as this can significantly affect the quality and functionality of the cabinets.
Why Should Buyers Consider Eco-Friendly Cabinet Suppliers?
Eco-friendly cabinet suppliers emphasize sustainable materials and environmentally responsible manufacturing processes. This type of supplier is increasingly relevant in green building projects and for businesses committed to sustainability. While eco-friendly cabinets can offer unique materials and align with corporate social responsibility goals, buyers must be prepared for potentially higher costs and variable availability, which can influence project timelines.
What Are the Advantages of Working with Wholesale Cabinet Suppliers?
Wholesale cabinet suppliers provide bulk purchasing options, making them an attractive choice for large-scale projects such as renovations or new constructions. They typically offer standard designs at lower prices, allowing businesses to save on costs while maintaining quality. However, buyers should be aware that wholesale options may come with limited customization and design flexibility, which can affect how well the cabinets fit into specific spaces or branding requirements.
Related Video: Economy Cabinet Making with Melamine: How to Build Cabinets
Key Industrial Applications of cabinets supplier
Industry/Sector | Specific Application of Cabinets Supplier | Value/Benefit for the Business | Key Sourcing Considerations for this Application |
---|---|---|---|
Manufacturing | Tool and Equipment Storage Cabinets | Improved organization and efficiency in operations | Durability, size specifications, and security features |
Healthcare | Medical Supply Cabinets | Enhanced patient care through organized supplies | Compliance with health regulations, material safety |
Retail | Display and Storage Cabinets | Increased product visibility and customer engagement | Customization options, aesthetics, and accessibility |
Education | Classroom and Laboratory Cabinets | Optimized learning environments with organized materials | Space utilization, safety standards, and mobility |
Hospitality | Guest Room and Service Area Cabinets | Enhanced guest experience through efficient storage | Design, functionality, and durability under high use |
How Are Cabinets Used in Manufacturing Settings?
In the manufacturing sector, cabinets serve as essential storage solutions for tools and equipment. By utilizing tool and equipment storage cabinets, businesses can streamline their operations, reducing time spent searching for tools and minimizing workplace accidents. For international buyers, especially from regions like Africa and South America, the focus should be on sourcing cabinets that are durable and can withstand the rigors of manufacturing environments. Key considerations include the cabinet’s material, size specifications, and security features to protect valuable equipment.
What Role Do Cabinets Play in Healthcare Facilities?
In healthcare settings, medical supply cabinets are crucial for organizing and storing supplies efficiently. These cabinets help healthcare providers maintain quick access to essential items, ultimately enhancing patient care. International B2B buyers from the Middle East and Europe should prioritize suppliers that comply with health regulations, ensuring the materials used are safe and suitable for medical environments. Additionally, features such as locking mechanisms and modular designs can provide added functionality and security.
How Do Retail Cabinets Enhance Customer Engagement?
In the retail industry, cabinets are utilized for both display and storage purposes. Display cabinets not only showcase products effectively but also enhance customer engagement by making items easily accessible. For businesses in South America and Africa, sourcing cabinets that offer customization options and aesthetic appeal can significantly impact sales. Buyers should also consider the accessibility of these cabinets to ensure they meet the needs of diverse customer demographics.
Why Are Cabinets Important in Educational Institutions?
Educational institutions rely on classroom and laboratory cabinets to create organized learning environments. These cabinets facilitate better space utilization and ensure that materials are readily available for both teachers and students. For international buyers, particularly in Europe, it is essential to focus on safety standards and mobility features, ensuring that cabinets can accommodate various classroom layouts and needs. Additionally, durability is crucial, given the high usage in educational settings.
How Do Cabinets Improve Hospitality Operations?
In the hospitality sector, cabinets are used in guest rooms and service areas to enhance the guest experience. Efficient storage solutions allow for a tidy environment, which is essential for guest satisfaction. Buyers from the UAE and other regions should look for cabinets that combine design with functionality, ensuring they can withstand high use while maintaining aesthetic appeal. Durability and ease of maintenance are also vital considerations for long-term investment.
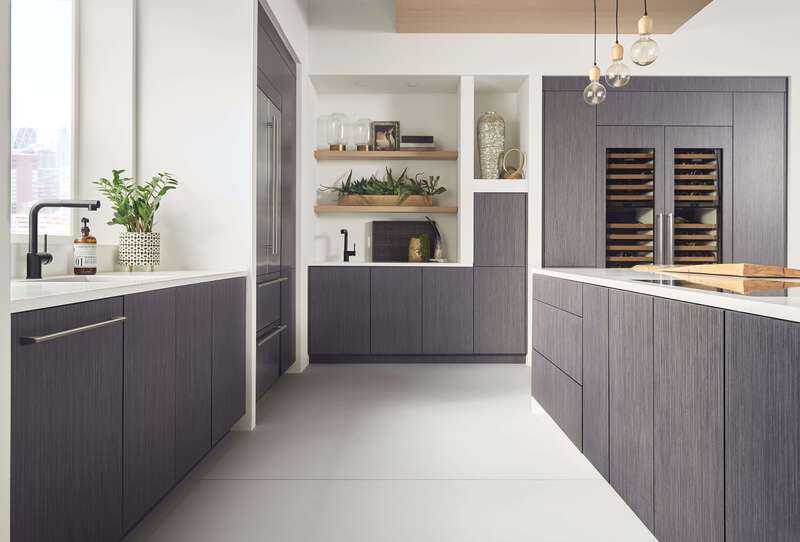
A stock image related to cabinets supplier.
Related Video: Amazing Techniques Build And Assemble A Cabinets Kitchen Using Aluminum
3 Common User Pain Points for ‘cabinets supplier’ & Their Solutions
Scenario 1: Navigating Quality Assurance Challenges in Cabinet Sourcing
The Problem: One of the most pressing challenges faced by B2B buyers in the cabinets sector is ensuring product quality and consistency. Buyers often experience discrepancies between what is promised by suppliers and what is delivered. This can result in subpar products that do not meet industry standards, leading to delays in project timelines, increased costs due to reordering, and potential damage to the buyer’s reputation. Particularly in regions like Africa and South America, where supply chain issues can exacerbate these problems, ensuring quality is paramount.
The Solution: To overcome this challenge, B2B buyers should implement a rigorous quality assurance process when sourcing cabinets. Start by developing a comprehensive checklist that includes material specifications, finish quality, and compliance with relevant local and international standards. Conduct factory audits or request third-party inspections before finalizing orders. Additionally, establish a clear communication channel with suppliers that includes regular updates and quality feedback during production. This proactive approach can significantly mitigate quality issues, ensuring that the cabinets received are up to standard and ready for use.
Scenario 2: Dealing with Delays in Cabinet Delivery
The Problem: Timely delivery of cabinets is critical for project success. However, many international B2B buyers face significant delays due to logistical challenges, customs issues, or supplier mismanagement. For instance, a buyer in the UAE might place an order for custom cabinets only to find that shipping delays have pushed back their project schedule, resulting in financial losses and strained relationships with clients.
The Solution: To tackle delivery delays, B2B buyers should engage in strategic planning and establish clear timelines with suppliers. This involves setting realistic lead times that account for potential shipping and customs delays. Buyers should also consider using suppliers who have a proven track record of timely delivery and robust logistics networks. Utilizing technology, such as project management software that integrates shipment tracking, can provide real-time updates on delivery status. Establishing contingency plans, such as alternative suppliers or expedited shipping options, can further protect against unforeseen delays.
Scenario 3: Understanding Customization Options for Cabinets
The Problem: Many B2B buyers encounter difficulty in understanding the customization options available from cabinet suppliers. This lack of clarity can lead to dissatisfaction with the final product, as buyers may not receive cabinets that align with their specific design requirements or functional needs. This issue is especially prevalent in competitive markets in Europe, where aesthetic appeal and functionality are critical.
The Solution: To effectively navigate customization challenges, buyers should engage in detailed consultations with suppliers early in the procurement process. Clearly articulate specific needs regarding design, materials, dimensions, and functionality. Request detailed samples or prototypes whenever possible to evaluate customization options firsthand. Additionally, consider partnering with suppliers who offer design support or have a robust online platform showcasing various customization possibilities. This collaborative approach not only helps in making informed decisions but also ensures that the final product meets the buyer’s expectations and enhances project outcomes.
Strategic Material Selection Guide for cabinets supplier
What Are the Key Properties of Common Cabinet Materials?
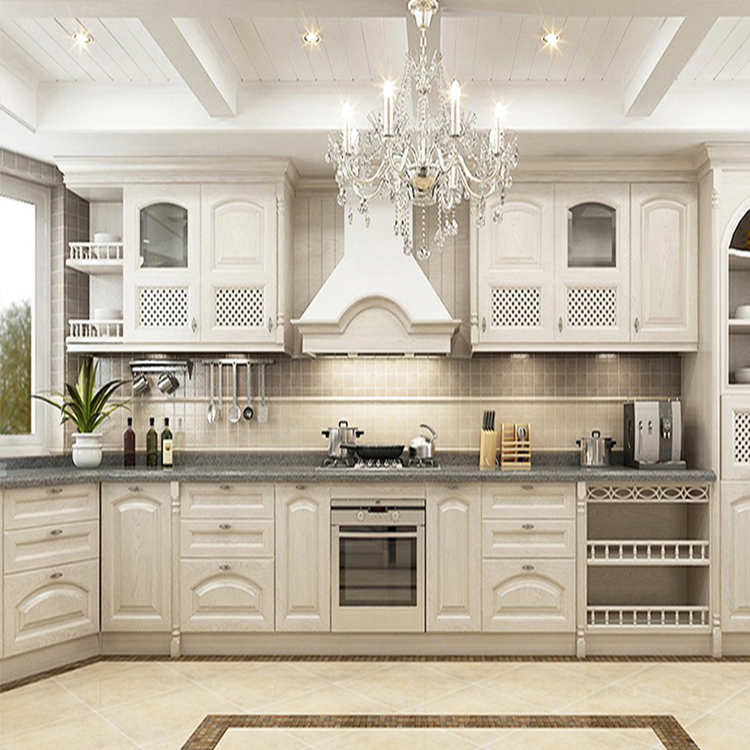
A stock image related to cabinets supplier.
When selecting materials for cabinets, understanding their properties is crucial for ensuring optimal performance in various applications. Here, we analyze four common materials used in cabinet manufacturing: wood, metal, laminate, and MDF (Medium Density Fiberboard).
How Does Wood Perform as a Cabinet Material?
Wood is a traditional choice for cabinets, prized for its aesthetic appeal and strength. It has excellent temperature resistance and can withstand moderate pressure. However, its susceptibility to moisture can lead to warping or swelling, especially in humid climates.
Pros: Wood is durable and offers a timeless look that enhances the value of any space. It can be easily customized and repaired, making it suitable for high-end applications.
Cons: The cost of quality wood can be high, and it requires regular maintenance to prevent damage from moisture and pests. Additionally, the manufacturing process can be complex, requiring skilled labor.
Impact on Application: Wood is compatible with a variety of finishes and can be used in both residential and commercial settings. However, international buyers should consider local climate conditions that may affect wood performance.
What Advantages Does Metal Offer for Cabinets?
Metal, particularly stainless steel and aluminum, is increasingly popular for cabinets due to its strength and durability. It exhibits excellent corrosion resistance and can withstand high temperatures and pressures.
Pros: Metal cabinets are easy to clean, resistant to pests, and offer a modern aesthetic. They are ideal for industrial environments where hygiene is a priority.
Cons: The initial cost of metal cabinets can be higher than wood or laminate. Additionally, they may require specialized manufacturing techniques, which can complicate production.
Impact on Application: Metal cabinets are suitable for environments that demand high durability, such as laboratories or kitchens. International buyers should ensure compliance with relevant standards, such as ASTM for material quality.
How Do Laminates Enhance Cabinet Design?
Laminates are synthetic materials that are applied to surfaces for aesthetic and protective purposes. They are available in a wide range of colors and patterns, making them versatile for design.
Pros: Laminates are cost-effective and offer a durable surface that is resistant to scratches and stains. They are also easy to clean and maintain.
Cons: While laminates can mimic the look of wood or metal, they may not provide the same level of durability. They can be prone to chipping if not handled carefully.
Impact on Application: Laminates are commonly used in residential and commercial cabinetry. For international buyers, it’s essential to check for compliance with local safety standards.
What Makes MDF a Popular Choice for Cabinets?
MDF is engineered from wood fibers, making it a popular choice for cabinetry. It has a smooth surface that is ideal for painting and veneering, and it offers good temperature resistance.
Pros: MDF is generally less expensive than solid wood and provides a uniform surface that can be easily shaped. It is also resistant to warping, making it suitable for various climates.
Cons: MDF is not as strong as solid wood or metal and can be susceptible to moisture damage if not properly sealed. Its manufacturing process can also involve chemicals that may raise environmental concerns.
Impact on Application: MDF is widely used in residential cabinetry and is suitable for painted finishes. International buyers should consider the environmental regulations related to MDF production in their regions.
Summary Table of Cabinet Materials
Material | Typical Use Case for cabinets supplier | Key Advantage | Key Disadvantage/Limitation | Relative Cost (Low/Med/High) |
---|---|---|---|---|
Wood | High-end residential and commercial cabinetry | Aesthetic appeal and durability | Susceptible to moisture and pests | High |
Metal | Industrial and laboratory environments | Corrosion resistance and modern look | Higher initial cost and complex manufacturing | High |
Laminate | Residential and commercial cabinetry | Cost-effective and easy to maintain | Prone to chipping and less durable | Medium |
MDF | Painted cabinetry in residential settings | Smooth surface and cost-effective | Susceptible to moisture damage | Low |
This guide provides international B2B buyers with essential insights into material selection for cabinets, ensuring they make informed choices based on performance, cost, and application suitability.
In-depth Look: Manufacturing Processes and Quality Assurance for cabinets supplier
What Are the Main Stages of Cabinet Manufacturing?
Understanding the manufacturing process of cabinets is crucial for international B2B buyers, especially those from diverse markets like Africa, South America, the Middle East, and Europe. The typical stages involved in cabinet manufacturing include material preparation, forming, assembly, and finishing.
-
Material Preparation: This initial phase involves selecting high-quality materials such as plywood, MDF (medium-density fiberboard), or solid wood. Buyers should ensure that suppliers source materials that meet international standards for sustainability and quality. The preparation also includes cutting the materials to size and ensuring they are free from defects.
-
Forming: During this stage, the prepared materials are shaped into the components of the cabinets. Techniques such as CNC (Computer Numerical Control) machining are commonly employed for precise cutting and shaping. This automation ensures consistency and accuracy, which is crucial for meeting buyer specifications.
-
Assembly: The assembly stage is where individual components are joined together to create the final cabinet structure. Different joining methods, such as dowel joints, pocket screws, or dovetail joints, are used depending on the design and quality requirements. Buyers should inquire about the assembly techniques used by suppliers to ensure durability and strength.
-
Finishing: The final stage involves applying finishes, such as paint, stain, or lacquer, to enhance the aesthetic appeal and protect the surfaces. Quality control during this phase is essential, as improper finishing can lead to issues like peeling or discoloration. Buyers should ask for samples of the finishes used and verify that they meet their expectations.
How Does Quality Assurance Work in Cabinet Manufacturing?
Quality assurance (QA) is a critical aspect of cabinet manufacturing that ensures products meet specified standards and buyer expectations. International B2B buyers should familiarize themselves with relevant quality standards and checkpoints used in the manufacturing process.
-
International Standards: Many cabinet suppliers adhere to international quality standards such as ISO 9001, which outlines criteria for a quality management system. Compliance with ISO standards demonstrates a supplier’s commitment to quality and customer satisfaction. Additionally, buyers should look for certifications like CE marking for products sold in Europe, ensuring they meet EU safety, health, and environmental protection standards.
-
Industry-Specific Standards: Depending on the application of the cabinets (e.g., residential, commercial, or industrial), suppliers may follow industry-specific standards such as the American National Standards Institute (ANSI) or the Architectural Woodwork Standards (AWS). Buyers should verify that the supplier complies with these standards relevant to their market.
-
Quality Control Checkpoints: The manufacturing process typically involves several quality control checkpoints:
– Incoming Quality Control (IQC): This involves inspecting raw materials upon arrival to ensure they meet specified standards before production begins.
– In-Process Quality Control (IPQC): Continuous monitoring during the manufacturing process helps catch defects early. This includes checking dimensions, assembly integrity, and surface finishes.
– Final Quality Control (FQC): Once the cabinets are fully assembled and finished, a final inspection is conducted to ensure the product meets all quality requirements before shipping.
What Testing Methods Are Commonly Used in Cabinet Manufacturing?
Several testing methods are employed to ensure that cabinets meet quality and performance standards. B2B buyers should inquire about these testing procedures when evaluating potential suppliers.
-
Material Testing: This includes assessing the strength, durability, and moisture resistance of the materials used. Common tests include the tensile strength test for wood and formaldehyde emission tests for MDF, ensuring compliance with health standards.
-
Structural Testing: Cabinets are subjected to load tests to determine their ability to hold weight without deforming or failing. This is particularly important for cabinets designed for heavy-duty applications.
-
Finish Testing: Testing the finish for durability, scratch resistance, and colorfastness ensures that the cabinets will maintain their appearance over time. Buyers can request reports on finish testing to gauge long-term performance.
How Can B2B Buyers Verify Supplier Quality Control?
Verifying a supplier’s quality control processes is essential for B2B buyers, particularly in international markets where regulations and standards may vary.
-
Supplier Audits: Conducting on-site audits allows buyers to assess the manufacturing facilities and quality control measures firsthand. An audit can provide insights into the supplier’s adherence to quality standards and their overall production capabilities.
-
Quality Reports: Buyers should request detailed quality reports that document the results of quality control checks and testing procedures. These reports should outline any issues encountered and how they were addressed.
-
Third-Party Inspections: Engaging third-party inspection services can provide an unbiased evaluation of the supplier’s quality control processes. These inspections can be conducted at various stages of production, ensuring compliance with international standards.
What Are the Nuances of Quality Control for International B2B Buyers?
International buyers must navigate various challenges and nuances when it comes to quality control in cabinet manufacturing.
-
Cultural and Regulatory Differences: Different regions may have varying standards for materials and manufacturing processes. Buyers from Africa, South America, the Middle East, and Europe should familiarize themselves with local regulations and ensure suppliers comply with them.
-
Communication Barriers: Clear communication is vital for ensuring that quality expectations are understood. Buyers should establish effective communication channels with suppliers to address any concerns promptly.
-
Logistics and Shipping Considerations: Quality control does not end at the factory. Buyers should consider how cabinets will be handled during shipping to prevent damage. Requesting protective packaging and understanding the logistics involved can mitigate risks.
By thoroughly understanding the manufacturing processes and quality assurance measures, international B2B buyers can make informed decisions when selecting cabinet suppliers. This knowledge not only helps in choosing the right partners but also ensures that the final products meet their quality and performance expectations.
Practical Sourcing Guide: A Step-by-Step Checklist for ‘cabinets supplier’
In this practical sourcing guide, we aim to equip international B2B buyers with a comprehensive checklist for procuring cabinets from suppliers. Whether you are in Africa, South America, the Middle East, or Europe, these actionable steps will help streamline your sourcing process and ensure that you make informed decisions.
Step 1: Define Your Technical Specifications
Establishing clear technical specifications is critical before engaging with suppliers. This includes dimensions, materials, and design features that meet your specific needs. Be precise about your requirements to avoid misunderstandings later in the procurement process.
- Considerations:
- What type of cabinets do you need (e.g., kitchen, office, storage)?
- Are there specific materials that must be used (e.g., wood, metal, laminate)?
Step 2: Conduct Market Research for Suppliers
A thorough market analysis helps identify reputable suppliers in your target regions. Research suppliers through industry directories, trade shows, and online platforms to gather a comprehensive list of potential partners.
- Where to Look:
- Online marketplaces (e.g., Alibaba, Global Sources)
- Local trade associations and business networks
Step 3: Evaluate Potential Suppliers
Before committing, it’s crucial to vet suppliers thoroughly. Request company profiles, case studies, and references from buyers in similar industries or regions. This step ensures you are partnering with a reliable supplier that meets your quality standards.
- What to Check:
- Supplier’s history and experience in the cabinet market
- Feedback from previous clients regarding product quality and service
Step 4: Verify Supplier Certifications
Ensure that the suppliers hold relevant certifications that demonstrate compliance with international standards. This includes quality management systems (e.g., ISO certifications) and adherence to environmental regulations.
- Why It Matters:
- Certifications can signify a commitment to quality and sustainability.
- They help mitigate risks associated with poor-quality products.
Step 5: Request Samples and Prototypes
Before finalizing your order, ask for samples or prototypes of the cabinets. This allows you to assess the craftsmanship, materials, and overall quality before making a large investment.
- Key Points:
- Examine the finish, durability, and design features closely.
- Ensure that the samples align with your initial specifications.
Step 6: Negotiate Terms and Pricing
Effective negotiation can lead to favorable terms and pricing. Discuss payment terms, delivery schedules, and warranties. Be open about your budget constraints while also recognizing the value of quality.
- Negotiation Tips:
- Consider bulk purchasing discounts if you plan to order large quantities.
- Ensure that all agreements are documented to avoid disputes later.
Step 7: Establish a Clear Communication Plan
Establishing a robust communication plan with your supplier is essential for a smooth procurement process. Set expectations regarding updates, timelines, and points of contact to ensure that both parties remain aligned throughout the sourcing journey.
- Communication Essentials:
- Use project management tools for tracking progress.
- Schedule regular check-ins to address any concerns promptly.
By following these steps, B2B buyers can ensure a more streamlined and effective procurement process when sourcing cabinets from suppliers across various regions.
Comprehensive Cost and Pricing Analysis for cabinets supplier Sourcing
What Are the Key Cost Components for Cabinets Suppliers?
When evaluating potential cabinets suppliers, understanding the breakdown of costs is crucial. The primary cost components typically include:
- Materials: The choice of wood, laminates, hardware, and finishes significantly influences the overall price. Premium materials may yield higher durability and aesthetic appeal but will also increase costs.
- Labor: Labor costs vary based on the region, skill level, and wage rates. Countries with lower labor costs may offer competitive pricing, but quality control must be considered.
- Manufacturing Overhead: This encompasses facility costs, utilities, and equipment maintenance. Suppliers with advanced manufacturing technologies may have higher overhead but can offer better efficiency and quality.
- Tooling: Custom tooling for specific designs can be a significant upfront cost. However, these costs may be amortized over larger production runs.
- Quality Control (QC): Robust QC processes ensure product standards but add to the cost. Consider suppliers with certifications like ISO or ANSI for guaranteed quality.
- Logistics: Shipping and handling costs can vary widely based on distance and mode of transport. Import tariffs and local taxes should also be factored into the total cost.
- Margin: Supplier profit margins can vary based on competition and market demand. Understanding the typical margins in your region can help in negotiating better prices.
How Do Price Influencers Affect Cabinets Supplier Costs?
Several factors can influence the pricing structure of cabinets suppliers, including:
- Volume and Minimum Order Quantity (MOQ): Larger orders often lead to lower per-unit costs. Suppliers may offer discounts for bulk purchases, which can significantly reduce your overall expenditure.
- Specifications and Customization: Custom designs or specifications can increase costs. It’s essential to balance the need for customization with budget constraints.
- Materials and Quality Certifications: Higher quality materials and certifications can lead to increased costs but may also result in longer-lasting products. Buyers should evaluate the long-term value versus initial costs.
- Supplier Factors: The reputation and reliability of the supplier can impact pricing. Established suppliers may charge a premium for their experience and customer service.
- Incoterms: The agreed-upon Incoterms can affect overall costs. For instance, FOB (Free on Board) arrangements may result in lower shipping costs, while DDP (Delivered Duty Paid) includes all freight and customs charges.
What Are the Best Negotiation Strategies for International B2B Buyers?
International B2B buyers, especially from regions like Africa, South America, the Middle East, and Europe, should consider the following tips when negotiating with cabinets suppliers:
- Research Market Prices: Understanding the typical price range for cabinets in your target market allows you to negotiate more effectively.
- Discuss Total Cost of Ownership (TCO): Emphasize the importance of TCO, which includes initial costs, maintenance, and potential replacement costs. This perspective can help justify higher initial prices if the quality is superior.
- Leverage Relationships: Building strong relationships with suppliers can lead to better pricing and terms. Suppliers are often more willing to negotiate with established customers.
- Request Detailed Quotations: Ensure that quotes include a detailed breakdown of costs. This transparency helps identify areas for negotiation.
- Be Aware of Pricing Nuances: Different regions may have unique pricing structures based on local economic conditions, currency fluctuations, and demand. Being aware of these factors can enhance negotiation outcomes.
Conclusion: What Should Buyers Keep in Mind About Pricing?
While costs can vary significantly based on the factors discussed, buyers should remain vigilant. It’s essential to recognize that the prices provided by suppliers are often indicative and may change based on market conditions. Conduct thorough due diligence, explore multiple suppliers, and consider the total cost implications to ensure a wise investment in cabinets that meet your operational needs.
Alternatives Analysis: Comparing cabinets supplier With Other Solutions
Exploring Alternatives to Cabinets Suppliers: What Are Your Options?
In the competitive landscape of B2B procurement, especially for international buyers from regions like Africa, South America, the Middle East, and Europe, it is crucial to explore viable alternatives to cabinets suppliers. Understanding the different solutions available can help businesses optimize their operations, reduce costs, and enhance overall efficiency. This section provides a comparative analysis of cabinets suppliers against two alternative solutions: modular storage systems and custom-built cabinetry.
Comparison Aspect | Cabinets Supplier | Modular Storage Systems | Custom-Built Cabinetry |
---|---|---|---|
Performance | High durability, variety of designs | Versatile, scalable, adaptable | Tailored to specific needs, unique designs |
Cost | Moderate to high, depending on materials | Generally lower, especially for bulk orders | High initial investment, but can increase property value |
Ease of Implementation | Straightforward delivery and installation | Quick to set up, especially pre-assembled units | Time-consuming design and construction process |
Maintenance | Low maintenance with proper care | Varies by material; generally low | Requires regular upkeep, depending on materials |
Best Use Case | Commercial settings with specific design requirements | Warehouses and flexible office spaces | High-end residential or bespoke commercial projects |
What Are the Pros and Cons of Modular Storage Systems?
Modular storage systems provide a flexible alternative to traditional cabinets. These systems are designed to be easily assembled and reconfigured to meet changing storage needs. Their adaptability makes them ideal for dynamic environments such as warehouses or offices where space utilization is critical. The major advantages include lower costs, especially when purchasing in bulk, and ease of installation. However, they may lack the aesthetic appeal and durability of custom cabinetry, which can be a drawback for businesses focusing on brand image or customer experience.
How Does Custom-Built Cabinetry Compare?
Custom-built cabinetry offers a highly personalized solution tailored to specific business needs. This alternative allows for unique designs that can enhance the aesthetic and functional aspects of a space. While the initial investment is higher, custom cabinetry can significantly increase the value of a property and provide a unique selling point. However, the design and installation process can be time-consuming, and maintenance may be more involved compared to pre-manufactured cabinets or modular systems. Businesses that prioritize aesthetics and custom solutions often find this option worthwhile.
Conclusion: How Should B2B Buyers Choose the Right Solution?
When selecting the right solution for cabinetry needs, B2B buyers should consider their specific requirements, including budget constraints, space utilization, and desired aesthetics. Cabinets suppliers offer a reliable solution for those seeking established designs and durability. In contrast, modular storage systems present an economical and flexible option for businesses with evolving storage needs. Lastly, custom-built cabinetry serves those looking for uniqueness and premium quality. By evaluating these alternatives against their operational objectives, buyers can make informed decisions that align with their business goals and environments.
Essential Technical Properties and Trade Terminology for cabinets supplier
What Are the Essential Technical Properties for Cabinets Suppliers?
When sourcing cabinets, understanding technical properties is crucial for international B2B buyers. Here are some of the key specifications that should be considered:
1. Material Grade: What Should You Look For?
The material grade determines the quality and durability of the cabinets. Common materials include plywood, MDF (Medium Density Fiberboard), and solid wood. Higher-grade materials tend to offer better resistance to wear and tear, enhancing longevity. For B2B buyers, selecting the right material grade can significantly impact the overall quality of the cabinets, influencing customer satisfaction and return on investment.
2. Tolerance: Why Is It Important?
Tolerance refers to the allowable deviation in dimensions during the manufacturing process. Precise tolerances ensure that components fit together seamlessly, which is crucial for installation and functionality. In a B2B context, understanding tolerance levels can help buyers avoid costly mistakes in assembly and installation, leading to smoother project execution.
3. Finish: How Does It Affect Aesthetics and Maintenance?
The finish applied to cabinets not only affects their appearance but also their maintenance requirements. Common finishes include laminate, paint, and varnish. Each finish offers different benefits regarding durability, resistance to moisture, and ease of cleaning. B2B buyers should assess the finish to ensure it aligns with their client’s needs and preferences, as this can enhance the overall aesthetic appeal of the project.
4. Load-Bearing Capacity: What Should You Know?
Load-bearing capacity indicates how much weight a cabinet can support. This is particularly important for cabinets designed to hold heavy items, such as kitchen appliances or commercial equipment. Understanding the load-bearing capacity ensures that the cabinets will perform as expected in their intended environment, reducing the risk of damage or failure.
5. Sustainability: Why Is It Becoming Essential?
Sustainability is increasingly important in the B2B sector, especially for buyers focused on environmentally friendly practices. Look for cabinets made from sustainable materials or those that comply with eco-certifications. Choosing sustainable options can enhance a company’s reputation and appeal to environmentally-conscious consumers.
What Are the Key Trade Terms You Should Know?
Familiarizing yourself with industry jargon can facilitate smoother transactions and negotiations. Here are some essential terms for B2B buyers in the cabinets industry:
1. OEM (Original Equipment Manufacturer): What Does It Mean?
An OEM refers to a company that produces parts or equipment that may be marketed by another manufacturer. In the cabinets industry, this often means sourcing components from specialized manufacturers to create customized products. B2B buyers should consider OEM relationships to ensure high-quality components and branding flexibility.
2. MOQ (Minimum Order Quantity): How Does It Impact Your Purchase?
MOQ denotes the smallest quantity of a product that a supplier is willing to sell. Understanding MOQ is crucial for inventory management and cash flow. B2B buyers should negotiate MOQs to align with their purchasing capabilities and project requirements, avoiding overstocking or stockouts.
3. RFQ (Request for Quotation): Why Is It Essential?
An RFQ is a document sent to suppliers requesting pricing and details for specific products. It is vital for comparing offers and ensuring transparency in pricing. B2B buyers should utilize RFQs to solicit multiple quotes, enabling informed decision-making based on cost and quality.
4. Incoterms: What Are They and Why Do They Matter?
Incoterms (International Commercial Terms) are a series of pre-defined commercial terms published by the International Chamber of Commerce. They clarify the responsibilities of buyers and sellers in international transactions, including shipping, insurance, and tariffs. Understanding Incoterms helps B2B buyers mitigate risks and manage logistics more effectively.
5. Lead Time: How Does It Affect Your Supply Chain?
Lead time refers to the time taken from placing an order to receiving the product. In the cabinets industry, lead times can vary based on customization and production schedules. B2B buyers should factor lead times into their project timelines to ensure timely delivery and avoid delays in construction or installation.
By understanding these essential technical properties and trade terminology, B2B buyers can make informed decisions that lead to successful cabinet procurement and project execution.
Navigating Market Dynamics and Sourcing Trends in the cabinets supplier Sector
What Are the Current Market Dynamics and Sourcing Trends in the Cabinets Supplier Sector?
The cabinets supplier sector is witnessing transformative changes driven by globalization, technological advancements, and shifting consumer preferences. International B2B buyers, especially from Africa, South America, the Middle East, and Europe, are increasingly influenced by trends such as customization and digital integration in sourcing processes. The rise of e-commerce platforms and digital marketplaces has made it easier for suppliers to reach global buyers, while also allowing buyers to compare prices and quality effortlessly.
Moreover, the increasing adoption of Industry 4.0 technologies—including automation, IoT, and AI—has enhanced supply chain efficiency and transparency. These technologies not only streamline the procurement process but also provide valuable data insights for buyers, enabling better decision-making. In regions like the UAE and Europe, where there is a strong emphasis on quality and design, the demand for innovative and high-quality cabinets is on the rise, pushing suppliers to invest in R&D and sustainable practices.
As international markets continue to evolve, B2B buyers must remain agile and adaptable. Understanding local market dynamics, regulatory frameworks, and cultural preferences is crucial for successful sourcing. For instance, in Africa and South America, local craftsmanship and sustainable materials are increasingly sought after, while European buyers may prioritize design aesthetics and durability.
How Is Sustainability Shaping the Cabinets Supplier Sector?
Sustainability has become a cornerstone of the cabinets supplier sector, as both consumers and businesses are increasingly conscious of their environmental impact. Ethical sourcing and sustainable practices are not just trends but necessities in today’s market. International B2B buyers are often seeking suppliers who demonstrate commitment to sustainable practices, including the use of renewable resources and environmentally friendly manufacturing processes.
The importance of ethical supply chains cannot be overstated. Buyers are encouraged to seek certifications such as FSC (Forest Stewardship Council) and LEED (Leadership in Energy and Environmental Design), which ensure that materials are sourced responsibly and that manufacturing processes adhere to strict environmental standards. The demand for “green” materials, such as reclaimed wood and low-VOC (volatile organic compounds) finishes, is also increasing as buyers aim to reduce their carbon footprint and enhance their brand reputation.
Furthermore, sustainable practices can lead to cost savings in the long run. By investing in energy-efficient production methods and reducing waste, suppliers can lower operational costs, which can be passed on to buyers. As regulatory pressures regarding sustainability grow, understanding these practices is crucial for international B2B buyers looking to maintain compliance and enhance their competitive edge.
How Has the Cabinets Supplier Sector Evolved Over Time?
The cabinets supplier sector has undergone significant evolution over the decades, transitioning from traditional craftsmanship to modern industrial production. Historically, cabinets were primarily custom-made by skilled artisans, but the rise of mass production in the late 20th century allowed suppliers to meet growing consumer demand at scale. This shift not only democratized access to quality cabinets but also enabled suppliers to experiment with new materials and designs.
In recent years, the focus has shifted again towards customization and personalization, spurred by advancements in technology and changing consumer preferences. Today’s buyers are looking for unique, tailored solutions that reflect their individual style and needs. The integration of digital tools in the design and manufacturing process, such as CAD (Computer-Aided Design) software, has made it possible for suppliers to offer more personalized options without sacrificing efficiency.
As the market continues to evolve, B2B buyers must stay informed about these trends and adapt their sourcing strategies accordingly, ensuring they partner with suppliers who are not only innovative but also committed to sustainability and ethical practices.
Frequently Asked Questions (FAQs) for B2B Buyers of cabinets supplier
-
How can I find reliable cabinet suppliers for my business?
To find reliable cabinet suppliers, start by researching online platforms such as Alibaba, ThomasNet, or local trade directories specific to your region. Attend trade shows or industry expos to meet suppliers in person and evaluate their offerings. Additionally, read reviews and testimonials from other buyers to gauge their reputation. Networking with other businesses in your industry can also provide valuable insights and recommendations for trustworthy suppliers. -
What factors should I consider when choosing a cabinet supplier?
When selecting a cabinet supplier, consider their experience and specialization in your required cabinet type. Assess their production capabilities, lead times, and customization options to ensure they can meet your specific needs. Additionally, inquire about quality control processes, certifications, and past client references. Understanding their payment terms and logistics capabilities is crucial to ensure a smooth purchasing process. -
What is the typical minimum order quantity (MOQ) for cabinets?
Minimum order quantities (MOQ) for cabinets can vary significantly based on the supplier and type of cabinets. Generally, MOQs may range from as low as 10 to 100 units. Some suppliers may offer lower MOQs for custom orders, while others may require higher quantities for bulk orders. Always clarify the MOQ with potential suppliers to determine if it aligns with your purchasing capacity. -
How do I ensure the quality of cabinets from international suppliers?
To ensure quality when sourcing cabinets internationally, request samples before placing a bulk order. Establish clear quality standards and specifications in your purchase agreement. Consider hiring third-party inspection services to conduct quality checks before shipment. Additionally, verify the supplier’s certifications and compliance with international quality standards to mitigate risks associated with product quality. -
What payment terms should I negotiate with cabinet suppliers?
When negotiating payment terms with cabinet suppliers, consider options such as a deposit with the balance due upon delivery or a letter of credit for larger orders. Common terms include 30% upfront and 70% upon shipment. Discussing flexible payment terms can help manage cash flow and mitigate risks, especially when working with new suppliers. Always ensure that payment terms are documented in your agreement to avoid misunderstandings. -
What are the shipping and logistics considerations when ordering cabinets?
Shipping and logistics are critical when ordering cabinets internationally. Discuss shipping options with your supplier, including freight forwarding services, and choose between air or sea freight based on your budget and timeline. Understand the customs regulations in your country to avoid delays. Additionally, inquire about packaging methods to ensure your cabinets arrive undamaged. Establish clear timelines for delivery to manage your project effectively. -
Can I customize the cabinets according to my specifications?
Most cabinet suppliers offer customization options, allowing you to tailor designs, materials, finishes, and dimensions to meet your specific needs. When discussing customization, provide detailed specifications and examples of your desired outcome. Ensure that the supplier has the necessary capabilities and experience to fulfill custom orders. It’s also advisable to request prototypes or CAD drawings before finalizing your order to confirm that the design meets your expectations. -
How do I handle disputes with cabinet suppliers?
Handling disputes with cabinet suppliers requires clear communication and documentation. Start by addressing the issue directly with the supplier to seek a resolution. If the matter cannot be resolved amicably, refer to your purchase agreement for any outlined dispute resolution procedures, such as mediation or arbitration. Maintaining a professional demeanor throughout the process can help facilitate a more favorable outcome. Keeping a record of all communications will be beneficial if further action is necessary.
Important Disclaimer & Terms of Use
⚠️ Important Disclaimer
The information provided in this guide, including content regarding manufacturers, technical specifications, and market analysis, is for informational and educational purposes only. It does not constitute professional procurement advice, financial advice, or legal advice.
While we have made every effort to ensure the accuracy and timeliness of the information, we are not responsible for any errors, omissions, or outdated information. Market conditions, company details, and technical standards are subject to change.
B2B buyers must conduct their own independent and thorough due diligence before making any purchasing decisions. This includes contacting suppliers directly, verifying certifications, requesting samples, and seeking professional consultation. The risk of relying on any information in this guide is borne solely by the reader.
Strategic Sourcing Conclusion and Outlook for cabinets supplier
What Are the Key Takeaways for International B2B Buyers in the Cabinet Industry?
In the dynamic landscape of cabinet supply, strategic sourcing emerges as a critical factor for success. For international B2B buyers, particularly those in Africa, South America, the Middle East, and Europe, understanding supplier capabilities, market trends, and logistical challenges can significantly enhance procurement efficiency. Leveraging technology for supplier assessment and adopting a data-driven approach can streamline sourcing processes, ensuring that quality and cost-effectiveness align with business goals.
How Can Strategic Sourcing Benefit Your Business?
Strategic sourcing not only reduces costs but also fosters strong supplier relationships that can lead to better service and innovation. Buyers should prioritize suppliers who demonstrate sustainability practices and compliance with international standards, as these factors increasingly influence market competitiveness. Engaging in long-term partnerships with reliable suppliers can yield significant advantages, including improved negotiation leverage and access to exclusive products.
What Does the Future Hold for Cabinet Suppliers?
Looking ahead, the cabinet supply sector is poised for growth, driven by rising demand in residential and commercial markets. International buyers are encouraged to stay informed about emerging trends and shifts in consumer preferences. By actively engaging with suppliers and participating in industry forums, buyers can position themselves to capitalize on new opportunities.
In conclusion, the strategic sourcing journey is an essential investment for B2B buyers in the cabinet industry. Embrace the future with a proactive sourcing strategy that prioritizes quality, sustainability, and innovation. Take the next step today by evaluating your sourcing strategies and exploring new supplier partnerships to drive your business forward.