Discover Top Benefits of Choosing a Dehumidifier Manufacturer (2025)
Introduction: Navigating the Global Market for dehumidifier manufacturer
The global market for dehumidifier manufacturers presents a myriad of opportunities and challenges for international B2B buyers, particularly in diverse regions such as Africa, South America, the Middle East, and Europe. As businesses strive to create optimal indoor environments—whether in industrial settings, residential spaces, or commercial establishments—the importance of selecting the right dehumidification solutions cannot be overstated. This guide is designed to assist buyers in navigating the complexities of sourcing dehumidifiers, addressing critical aspects such as types, applications, supplier vetting, and cost considerations.
Understanding the specific needs of your environment is crucial when choosing a dehumidifier. Factors like humidity levels, size requirements, and energy efficiency ratings play significant roles in making informed purchasing decisions. This comprehensive guide empowers B2B buyers by providing actionable insights and practical advice, enabling them to evaluate potential suppliers effectively and select the most suitable products for their unique contexts.
Furthermore, the guide highlights key considerations for different geographical markets. For instance, businesses in Brazil might face distinct challenges related to high humidity, while those in the UAE may prioritize energy-efficient solutions due to soaring temperatures. By catering to the specific needs of diverse markets, this resource ensures that international buyers can make strategic decisions that enhance operational efficiency and improve indoor air quality.
Understanding dehumidifier manufacturer Types and Variations
Type Name | Key Distinguishing Features | Primary B2B Applications | Brief Pros & Cons for Buyers |
---|---|---|---|
Refrigerant Dehumidifiers | Use refrigeration coils to condense moisture. | Warehouses, manufacturing facilities | Pros: Effective in humid environments; Cons: Higher energy consumption. |
Desiccant Dehumidifiers | Utilize hygroscopic materials to absorb moisture. | Food processing, pharmaceuticals | Pros: Low-temperature operation; Cons: Limited moisture removal capacity. |
Heat Pump Dehumidifiers | Combine heating and cooling for moisture removal. | Residential, commercial buildings | Pros: Energy efficient; Cons: Higher initial cost. |
Industrial Dehumidifiers | Designed for heavy-duty moisture control. | Construction sites, large-scale manufacturing | Pros: High capacity; Cons: Requires significant space. |
Portable Dehumidifiers | Compact units for localized moisture control. | Small businesses, temporary setups | Pros: Easy to move; Cons: Limited capacity and efficiency. |
What Are Refrigerant Dehumidifiers and Their Applications?
Refrigerant dehumidifiers are among the most common types used in commercial settings. They operate by cooling air to condense moisture, making them particularly effective in environments with high humidity levels, such as warehouses and manufacturing facilities. When purchasing, buyers should consider energy efficiency ratings, as these units can consume significant power, impacting operational costs over time.
How Do Desiccant Dehumidifiers Work for Specific Industries?
Desiccant dehumidifiers use materials that absorb moisture from the air, making them ideal for industries like food processing and pharmaceuticals where humidity control is critical. These units can operate effectively at lower temperatures, which is advantageous for sensitive products. Buyers should evaluate the moisture removal capacity and the type of desiccant material used, as these factors influence operational efficiency and longevity.
What Makes Heat Pump Dehumidifiers a Smart Choice?
Heat pump dehumidifiers are versatile units that can both heat and cool air, making them suitable for residential and commercial buildings. They are known for their energy efficiency, which can lead to lower utility bills. However, buyers should be aware of the higher initial investment required and assess whether the long-term savings on energy costs justify this upfront expenditure.
Why Choose Industrial Dehumidifiers for Large Operations?
Industrial dehumidifiers are built for high-capacity moisture control, essential for environments like construction sites and large-scale manufacturing. These units can handle significant moisture loads, ensuring optimal conditions for processes and materials. When considering these units, buyers need to factor in the space requirements and maintenance needs, as well as the potential ROI in terms of product quality and process efficiency.
What Are the Benefits and Limitations of Portable Dehumidifiers?
Portable dehumidifiers offer flexibility and ease of use, making them suitable for small businesses or temporary setups. They can be easily moved to different locations as needed. However, their limited capacity and efficiency mean they are not ideal for larger spaces or prolonged use. Buyers should assess the specific humidity control needs and consider whether a more permanent solution might be more effective in the long run.
Related Video: Ultimate 340 Dehumidifier – Jon-Don Video
Key Industrial Applications of dehumidifier manufacturer
Industry/Sector | Specific Application of Dehumidifier Manufacturer | Value/Benefit for the Business | Key Sourcing Considerations for this Application |
---|---|---|---|
Food Processing | Controlling humidity in storage and processing areas | Extends shelf life of products, enhances quality | Energy efficiency, capacity, and compliance with health standards |
Pharmaceuticals | Maintaining controlled environments in production facilities | Ensures product integrity and compliance with regulations | Precision control, reliability, and certifications required |
Textile Manufacturing | Reducing moisture during fabric processing and storage | Prevents mold growth, improves product quality | Robustness, moisture removal capacity, and maintenance support |
Electronics | Protecting sensitive components during manufacturing | Reduces risk of corrosion and product failure | Size, energy consumption, and adaptability to different environments |
Construction | Managing moisture levels during building projects | Prevents structural damage and improves air quality | Portability, capacity, and integration with other systems |
How Are Dehumidifiers Used in Food Processing and What Problems Do They Solve?
In the food processing industry, dehumidifiers are crucial for controlling humidity in both storage and processing areas. High humidity can lead to spoilage, mold growth, and reduced shelf life of perishable goods. By maintaining optimal humidity levels, businesses can significantly extend the shelf life of products and enhance their overall quality. International buyers from regions like Africa and South America must consider energy-efficient models that comply with local health and safety regulations, ensuring that their operations meet international standards.
What Role Do Dehumidifiers Play in Pharmaceuticals?
In pharmaceutical manufacturing, maintaining a controlled environment is vital for product integrity and regulatory compliance. Dehumidifiers help manage humidity levels, preventing moisture-related degradation of sensitive compounds and ensuring that products meet stringent quality standards. Buyers in the Middle East and Europe should prioritize dehumidifiers with precise control features and reliability, as well as those that come with necessary certifications to adhere to industry regulations.
How Do Dehumidifiers Benefit Textile Manufacturing?
Textile manufacturers use dehumidifiers to reduce moisture during fabric processing and storage. Excess moisture can lead to mold growth and deterioration of fabric quality, directly impacting production efficiency and product integrity. For B2B buyers in Europe and South America, sourcing robust dehumidifiers with high moisture removal capacities and reliable maintenance support is essential to ensure consistent quality in textile production.
Why Are Dehumidifiers Essential in Electronics Manufacturing?
In electronics manufacturing, dehumidifiers play a vital role in protecting sensitive components from moisture. High humidity can lead to corrosion and product failure, which can be costly for manufacturers. International buyers, especially from regions like the UAE, should focus on compact dehumidifiers that consume less energy and can adapt to various manufacturing environments, ensuring the longevity and reliability of electronic products.
How Do Dehumidifiers Help in Construction Projects?
During construction projects, managing moisture levels is critical to prevent structural damage and improve indoor air quality. Dehumidifiers assist in drying out materials and controlling humidity in newly built structures, which is essential for ensuring the integrity of construction. Buyers from Africa and South America should look for portable dehumidifiers with sufficient capacity to handle large spaces and that can integrate seamlessly with other construction equipment to optimize project timelines.
Related Video: What Does A Dehumidifier Do? | Sylvane
3 Common User Pain Points for ‘dehumidifier manufacturer’ & Their Solutions
Scenario 1: Inconsistent Humidity Control in Commercial Spaces
The Problem: B2B buyers, particularly in sectors such as food storage or pharmaceuticals, often face challenges with maintaining consistent humidity levels. In regions with high ambient humidity, such as parts of Africa and South America, inadequate dehumidification can lead to product spoilage, compromised integrity of sensitive materials, or even health hazards. This inconsistency can also result in increased operational costs due to energy inefficiency and product loss.
The Solution: To address this issue, buyers should prioritize sourcing dehumidifiers equipped with advanced humidity control technologies. Look for manufacturers that offer smart dehumidifiers featuring real-time monitoring and automatic adjustments based on environmental changes. Additionally, establishing a routine maintenance schedule with your supplier can ensure optimal performance and longevity of the units. Implementing data logging tools can also help track performance over time, allowing for better decision-making regarding equipment upgrades or replacements.
Scenario 2: High Energy Costs Associated with Dehumidifiers
The Problem: For many businesses, particularly in the Middle East and Europe, the energy costs associated with running dehumidifiers can be a significant financial burden. Buyers often find that traditional models consume excessive electricity, leading to inflated utility bills that can erode profit margins. This is especially concerning for companies operating in energy-sensitive sectors or those aiming for sustainability.
The Solution: Buyers should explore energy-efficient dehumidifier options, specifically those rated with high Energy Efficiency Ratio (EER) or Energy Star certification. These models are designed to deliver superior moisture removal with lower energy consumption. Additionally, collaborating with manufacturers who provide tailored solutions based on specific facility needs can yield further energy savings. It’s also advisable to conduct an energy audit of the facility to determine the optimal placement and operation of dehumidifiers, which can significantly enhance their efficiency and reduce costs.
Scenario 3: Limited Knowledge on Dehumidifier Specifications and Applications
The Problem: Many B2B buyers lack the necessary expertise to understand the specific requirements and applications of dehumidifiers. This can lead to purchasing decisions that do not align with their operational needs, resulting in underperformance or equipment failure. For instance, a buyer in Brazil may mistakenly purchase a unit designed for residential use instead of a robust commercial model suitable for large warehouses.
The Solution: To mitigate this issue, buyers should engage in thorough research and consult with industry experts or the manufacturers themselves before making a purchase. It is essential to evaluate the specific humidity levels, room sizes, and intended applications of the dehumidifiers. Manufacturers often provide detailed product specifications and use-case scenarios that can guide buyers in selecting the right equipment. Additionally, attending trade shows or industry conferences can provide valuable insights and allow buyers to interact directly with manufacturers, fostering a better understanding of product capabilities and innovations.
Strategic Material Selection Guide for dehumidifier manufacturer
When selecting materials for dehumidifiers, it is essential to consider their properties, advantages, disadvantages, and how they align with the specific needs of international B2B buyers. Below are analyses of four common materials used in the manufacturing of dehumidifiers.
What Are the Key Properties of Aluminum in Dehumidifiers?
Aluminum is a lightweight metal known for its excellent corrosion resistance and thermal conductivity. It typically has a temperature rating of up to 150°C and can handle moderate pressure levels. This makes aluminum an ideal choice for components that require efficient heat exchange and durability in humid environments.
Pros and Cons:
– Advantages: Aluminum is lightweight, which reduces shipping costs and makes installation easier. It is also resistant to corrosion, ensuring longevity even in high-humidity conditions.
– Disadvantages: While aluminum is durable, it can be more expensive than other metals like steel. Additionally, it may not withstand extreme pressure as well as some other materials.
Impact on Application: Aluminum is particularly suitable for heat exchangers and housing components in dehumidifiers, where thermal efficiency is critical.
Considerations for International Buyers: Buyers from regions such as Africa and the Middle East should ensure that aluminum components meet local corrosion standards, particularly in coastal areas where salt exposure is a concern.
How Does Stainless Steel Compare for Dehumidifier Components?
Stainless steel is renowned for its strength and resistance to corrosion, making it suitable for various applications in dehumidifiers. It can handle high temperatures (up to 300°C) and pressures, which is beneficial for industrial-grade dehumidifiers.
Pros and Cons:
– Advantages: Its strength and corrosion resistance make stainless steel ideal for long-lasting components. It also has a polished finish that can enhance the aesthetic appeal of the product.
– Disadvantages: Stainless steel is generally heavier and more expensive than aluminum, which can affect shipping costs and overall pricing.
Impact on Application: Stainless steel is often used in the construction of water tanks and structural components where durability is paramount.
Considerations for International Buyers: Compliance with international standards such as ASTM and DIN is crucial for stainless steel components, especially in Europe, where stringent regulations on material quality are enforced.
What Role Does Plastic Play in Dehumidifier Manufacturing?
Plastics, particularly high-density polyethylene (HDPE) and polycarbonate, are frequently used in dehumidifiers for their lightweight and cost-effective properties. They can typically withstand temperatures up to 100°C and are resistant to many chemicals.
Pros and Cons:
– Advantages: Plastics are lightweight and can be molded into complex shapes, allowing for design flexibility. They are also generally less expensive than metals.
– Disadvantages: Plastics may not have the same level of durability as metals and can degrade over time when exposed to UV light or extreme temperatures.
Impact on Application: Plastic components are often used in the casing and internal parts of dehumidifiers, where weight savings and design flexibility are essential.
Considerations for International Buyers: Buyers should verify that plastics comply with local environmental regulations, especially in Europe, where there are strict guidelines regarding the use of certain materials.
Why Is Copper a Preferred Material for Heat Exchangers?
Copper is widely used in dehumidifiers, particularly in heat exchangers, due to its superior thermal conductivity and resistance to corrosion. It can handle high temperatures (up to 200°C) and has excellent pressure ratings.
Pros and Cons:
– Advantages: Copper’s thermal efficiency leads to lower energy costs and improved performance. Its antimicrobial properties also help in preventing mold growth.
– Disadvantages: Copper is more expensive than aluminum and can be prone to corrosion if not properly treated.
Impact on Application: Copper is essential for heat exchangers, where efficient heat transfer is critical for the dehumidification process.
Considerations for International Buyers: Buyers should consider the local availability of copper and the potential for price fluctuations, as well as compliance with relevant standards.
Summary Table of Material Selection for Dehumidifiers
Material | Typical Use Case for Dehumidifier Manufacturer | Key Advantage | Key Disadvantage/Limitation | Relative Cost (Low/Med/High) |
---|---|---|---|---|
Aluminum | Heat exchangers and housing components | Lightweight and corrosion-resistant | More expensive than some alternatives | Medium |
Stainless Steel | Structural components and water tanks | Strong and durable | Heavier and costlier | High |
Plastic | Casings and internal parts | Lightweight and cost-effective | Less durable than metals | Low |
Copper | Heat exchangers | Excellent thermal conductivity | Prone to corrosion if untreated | High |
This material selection guide provides international B2B buyers with critical insights into the properties, advantages, and limitations of various materials used in dehumidifier manufacturing. Understanding these factors can aid in making informed purchasing decisions that align with regional compliance and performance standards.
In-depth Look: Manufacturing Processes and Quality Assurance for dehumidifier manufacturer
What Are the Key Stages in the Manufacturing Process of Dehumidifiers?
The manufacturing of dehumidifiers involves several critical stages, each designed to ensure efficiency and quality in the final product. For B2B buyers, understanding these stages can help in evaluating potential suppliers.
1. Material Preparation
The first step in dehumidifier manufacturing is material preparation. High-quality materials are essential for durability and performance. Common materials used include:
- Metals: Aluminum and steel for frames and casings, chosen for their strength and resistance to corrosion.
- Plastics: Polypropylene and ABS for internal components, which are lightweight and have good thermal properties.
- Compressors: Selected based on energy efficiency and reliability, often from renowned manufacturers.
Before production begins, materials undergo rigorous inspection to ensure compliance with international standards. This step is crucial for B2B buyers from regions with varying material quality, such as Africa and South America, where sourcing can be inconsistent.
2. Forming Techniques
After materials are prepared, the next stage involves forming techniques, which can include:
- Stamping: Used for creating metal parts such as casings and brackets.
- Injection Molding: Common for producing plastic components, ensuring precise shapes and sizes.
- Welding: Employed to assemble metal parts securely, providing structural integrity.
Each technique has its advantages and should align with the specifications outlined by the buyer. Understanding the forming techniques can aid buyers in selecting manufacturers that meet their specific requirements.
3. Assembly Process
The assembly process is where various components come together to form a complete dehumidifier. This stage typically includes:
- Component Integration: Combining electrical components, compressors, and water collection tanks.
- Testing Fixtures: Setting up initial tests to ensure that parts fit correctly and function as intended.
B2B buyers should inquire about the assembly line’s efficiency and the experience of the workforce, as these factors can significantly impact the final product’s quality.
4. Finishing Touches
Finishing touches are crucial for both aesthetics and functionality. This stage may involve:
- Painting and Coating: Protective coatings are applied to prevent rust and improve the product’s lifespan.
- Final Assembly: All components are put together, and the unit is prepared for testing.
Buyers should pay attention to the finishing techniques used, as these can influence the durability and appearance of the dehumidifiers.
How Is Quality Assurance Implemented in Dehumidifier Manufacturing?
Quality assurance (QA) is an integral part of the manufacturing process for dehumidifiers, ensuring that every unit meets the required standards. For international B2B buyers, understanding QA protocols can be vital in selecting reliable suppliers.
Relevant International Standards for Quality Assurance
Manufacturers must comply with various international standards to ensure product quality and safety. Key standards include:
- ISO 9001: This standard focuses on quality management systems, ensuring consistent quality in products and services.
- CE Marking: Required for products sold in the European Economic Area, indicating compliance with health, safety, and environmental protection standards.
- API Standards: Relevant for manufacturers that produce dehumidifiers used in industrial applications, ensuring they meet specific performance and safety criteria.
Buyers from regions like Europe and the UAE should prioritize suppliers with these certifications, as they indicate a commitment to quality.
What Are the Key QC Checkpoints in the Manufacturing Process?
Quality control (QC) checkpoints are established throughout the manufacturing process to identify and rectify issues early. Common QC checkpoints include:
- Incoming Quality Control (IQC): Inspecting raw materials and components upon arrival to ensure they meet specifications.
- In-Process Quality Control (IPQC): Monitoring the production process at various stages to catch defects before final assembly.
- Final Quality Control (FQC): Conducting thorough testing of finished products to ensure they operate correctly and meet all safety standards.
B2B buyers should ask potential suppliers about their QC procedures and how they handle defective products.
Common Testing Methods for Dehumidifiers
To ensure functionality and reliability, various testing methods are employed, including:
- Performance Testing: Measuring the dehumidifier’s efficiency in moisture removal under controlled conditions.
- Safety Testing: Ensuring compliance with electrical safety standards to prevent hazards during operation.
- Durability Testing: Subjecting units to extreme conditions to evaluate their longevity and performance over time.
Understanding these testing methods can help buyers assess the reliability of the products they purchase.
How Can B2B Buyers Verify Supplier Quality Control?
Verifying a supplier’s quality control processes is crucial for B2B buyers, particularly in regions with diverse manufacturing standards. Here are some actionable steps:
1. Conduct Supplier Audits
Regular audits of potential suppliers can provide insight into their manufacturing processes and QC practices. Buyers should look for:
- Documented Procedures: Ensuring suppliers have standard operating procedures for quality control.
- Training Programs: Evaluating whether staff are trained in quality assurance practices.
2. Request Quality Reports
Buyers should ask suppliers for quality reports that detail testing results and any corrective actions taken for defects. This transparency can help build trust and ensure quality standards are met.
3. Engage Third-Party Inspectors
Utilizing third-party inspection services can provide an unbiased assessment of a supplier’s quality control processes. These inspectors can conduct audits and testing, ensuring compliance with international standards.
What Are the Quality Control Nuances for International B2B Buyers?
B2B buyers, especially from Africa, South America, the Middle East, and Europe, should be aware of specific quality control nuances:
- Cultural Differences: Understanding local manufacturing practices and standards can help buyers set realistic expectations.
- Regulatory Compliance: Different regions have varying regulations regarding product safety and quality. Buyers should familiarize themselves with these to ensure compliance.
- Logistics and Supply Chain: Assessing how a supplier manages logistics can impact product quality. Delays or mishandling can affect the integrity of the dehumidifiers.
By understanding these nuances, international B2B buyers can make informed decisions and choose suppliers that align with their quality expectations.
Practical Sourcing Guide: A Step-by-Step Checklist for ‘dehumidifier manufacturer’
The following guide serves as a practical checklist for B2B buyers aiming to source dehumidifiers from manufacturers. The process involves several crucial steps, ensuring that buyers make informed decisions and select the right partners for their needs.
Step 1: Define Your Technical Specifications
Before initiating the sourcing process, it’s essential to establish your technical requirements for dehumidifiers. This includes the desired capacity, energy efficiency ratings, noise levels, and specific features such as humidity control or smart technology integration.
– Why It Matters: Clearly defined specifications help in filtering potential suppliers and ensure that the products meet your operational needs.
– What to Look For: Compare technical specifications against industry standards and regulations relevant to your region, especially if you are sourcing from diverse markets like Africa or Europe.
Step 2: Conduct Market Research
Researching the market landscape is vital in identifying potential manufacturers. Utilize industry reports, trade shows, and online directories to gather information on various suppliers.
– Why It Matters: Understanding the market helps in identifying leading manufacturers, emerging players, and potential pricing trends.
– What to Look For: Focus on manufacturers with a strong reputation, positive reviews, and a track record of serving clients in your industry.
Step 3: Evaluate Potential Suppliers
Before committing, it’s crucial to vet suppliers thoroughly. Request company profiles, case studies, and references from buyers in a similar industry or region.
– Why It Matters: A thorough evaluation minimizes risks and helps in choosing reliable partners.
– What to Look For: Check for customer testimonials, case studies, and the supplier’s experience with companies in your geographic area, such as Brazil or the UAE.
Step 4: Verify Supplier Certifications
Ensure that your potential suppliers hold relevant certifications, such as ISO 9001 for quality management or energy efficiency certifications that comply with international standards.
– Why It Matters: Certifications indicate that a manufacturer adheres to industry standards and regulations, ensuring product quality and reliability.
– What to Look For: Request copies of certifications and verify their authenticity through the issuing bodies.
Step 5: Request Samples for Evaluation
Before making a bulk purchase, request samples of the dehumidifiers you are considering. This allows you to assess product quality firsthand.
– Why It Matters: Evaluating samples helps you confirm that the products meet your specifications and quality expectations.
– What to Look For: Check the build quality, functionality, and performance of the samples under real-world conditions.
Step 6: Discuss Pricing and Payment Terms
Engage in discussions with your shortlisted suppliers regarding pricing structures, payment terms, and potential discounts for bulk orders.
– Why It Matters: Understanding the financial aspects upfront prevents unexpected costs and aligns your budget with supplier expectations.
– What to Look For: Look for transparency in pricing and negotiate terms that accommodate your financial capabilities, especially if sourcing from regions with varying economic conditions.
Step 7: Establish Clear Communication Channels
Once you choose a supplier, establish clear communication lines to facilitate effective collaboration and quick resolution of issues.
– Why It Matters: Strong communication ensures that both parties are aligned throughout the sourcing process and can address any challenges promptly.
– What to Look For: Utilize multiple communication platforms and ensure that there is a designated point of contact for ongoing support.
By following this checklist, international B2B buyers can navigate the sourcing process for dehumidifiers more effectively, ensuring that they find the right manufacturers who meet their specific needs.
Comprehensive Cost and Pricing Analysis for dehumidifier manufacturer Sourcing
What Are the Key Cost Components in Dehumidifier Manufacturing?
When sourcing dehumidifiers, understanding the cost structure is crucial for international B2B buyers. The primary cost components include:
-
Materials: The quality and type of materials significantly influence the price. Common materials include plastic, metal casings, and electronic components. Sourcing high-quality materials may incur higher initial costs but can lead to better performance and longevity.
-
Labor: Labor costs vary by region. Countries with lower labor costs may offer competitive pricing; however, this can impact product quality. It’s essential to assess the skill level of the workforce involved in manufacturing.
-
Manufacturing Overhead: This encompasses indirect costs such as utilities, rent, and administrative expenses. Efficient overhead management can result in lower overall production costs.
-
Tooling: Initial tooling costs for specialized designs can be substantial. Buyers should inquire about tooling costs if they require custom designs or specifications.
-
Quality Control (QC): Implementing robust QC measures ensures product reliability and compliance with international standards. While this adds to costs, it can prevent costly recalls and enhance customer satisfaction.
-
Logistics: Shipping and handling costs depend on the distance from the supplier to the buyer, shipping methods, and any tariffs or import duties. Understanding Incoterms is vital in negotiating logistics costs effectively.
-
Margin: Manufacturers typically include a profit margin that reflects their operational risks. This margin can vary widely based on market demand and competition.
How Do Price Influencers Affect Dehumidifier Sourcing?
Several factors influence the pricing of dehumidifiers, including:
-
Volume/MOQ (Minimum Order Quantity): Larger orders often lead to discounted pricing due to economies of scale. Buyers should assess their needs and negotiate MOQs that align with their inventory strategies.
-
Specifications and Customization: Customized products that meet specific requirements can incur higher costs due to additional design and manufacturing processes. Buyers should weigh the benefits of customization against potential price increases.
-
Materials and Quality Certifications: Dehumidifiers that meet higher quality standards (e.g., energy efficiency certifications) may command a premium price. Buyers should consider the long-term savings from energy-efficient units versus upfront costs.
-
Supplier Factors: The reputation and reliability of the supplier can affect pricing. Established manufacturers may charge more due to their proven track record, while emerging suppliers might offer lower prices to gain market share.
-
Incoterms: Understanding Incoterms can help buyers manage shipping costs and responsibilities. Different terms can significantly impact the total landed cost of the products.
What Buyer Tips Can Enhance Cost-Efficiency in Dehumidifier Sourcing?
-
Negotiation Strategies: Effective negotiation can lead to better pricing and terms. Buyers should prepare by researching market prices and being clear about their needs and expectations.
-
Focus on Total Cost of Ownership (TCO): When evaluating suppliers, consider the TCO rather than just the purchase price. This includes maintenance, energy consumption, and potential warranty costs over the product’s lifespan.
-
Leverage Regional Knowledge: Buyers from Africa, South America, the Middle East, and Europe should leverage regional market insights. Understanding local market dynamics can enhance negotiation power and lead to better sourcing decisions.
-
Explore Multiple Suppliers: Obtaining quotes from several suppliers can provide insights into market pricing and help identify the best value options. Be cautious of prices that seem too low, as they may indicate compromised quality.
-
Stay Informed About Pricing Trends: Keeping abreast of market trends and material costs can help buyers anticipate price changes and make informed purchasing decisions.
Disclaimer on Indicative Prices
Prices for dehumidifiers can vary significantly based on the factors outlined above. The costs discussed are indicative and should be confirmed with specific suppliers, taking into account current market conditions and individual buyer requirements.
Alternatives Analysis: Comparing dehumidifier manufacturer With Other Solutions
In the quest for effective humidity control, businesses often find themselves weighing the benefits of traditional dehumidifiers against various alternative solutions. Understanding the nuances of these alternatives can significantly influence purchasing decisions, particularly for international B2B buyers from regions such as Africa, South America, the Middle East, and Europe. This analysis will focus on comparing dehumidifier manufacturers with other viable humidity control methods, helping buyers make informed choices.
Comparison Table of Humidity Control Solutions
Comparison Aspect | Dehumidifier Manufacturer | Alternative 1: Air Conditioning Systems | Alternative 2: Desiccant Systems |
---|---|---|---|
Performance | High moisture removal rate; suitable for large areas | Moderate moisture control; primarily cooling | Effective in low-humidity environments; continuous moisture absorption |
Cost | Varies widely; initial investment can be significant | Higher initial cost; ongoing energy costs | Moderate initial cost; low operational costs |
Ease of Implementation | Typically easy to install; requires electricity | Requires professional installation; complex | Generally easy to set up; no electricity needed |
Maintenance | Regular filter changes; occasional servicing | Regular maintenance required; filter changes | Minimal maintenance; replace desiccant periodically |
Best Use Case | Warehouses, manufacturing, and storage facilities | Climate control in residential and commercial buildings | Sensitive materials storage, low-humidity environments |
What Are the Pros and Cons of Air Conditioning Systems as Alternatives?
Air conditioning systems serve dual purposes: they cool the air while also reducing humidity levels. This makes them a popular choice for businesses looking to maintain a comfortable environment. However, they are often more expensive to install and operate than standalone dehumidifiers. While they can effectively manage humidity levels, they may not be as efficient in spaces where only humidity control is needed, as their primary function is cooling.
How Do Desiccant Systems Compare to Dehumidifiers?
Desiccant systems utilize materials that absorb moisture from the air, making them particularly effective in environments where low humidity is critical, such as in the preservation of sensitive products. They are advantageous due to their low operational costs and energy efficiency, as they do not require electricity. However, their performance can be limited in extremely humid conditions, and they may require periodic replacement of desiccant materials, which can lead to additional costs over time.
Conclusion: Which Humidity Control Solution is Right for Your Business?
Choosing the right humidity control solution hinges on understanding your specific operational needs. If your primary concern is moisture control in a large area, investing in a dehumidifier may yield the best results. Conversely, if your operations also require cooling, an air conditioning system might be more appropriate despite its higher cost. For businesses needing low humidity environments for sensitive materials, desiccant systems offer a viable alternative with lower operational costs. By evaluating the performance, costs, and specific use cases of each option, B2B buyers can make informed decisions that align with their business objectives and environmental conditions.
Essential Technical Properties and Trade Terminology for dehumidifier manufacturer
What Are the Key Technical Properties of Dehumidifiers for B2B Buyers?
Understanding the essential technical properties of dehumidifiers is crucial for B2B buyers in industries such as construction, hospitality, and manufacturing. These properties not only influence performance but also affect the total cost of ownership and long-term operational efficiency.
1. Capacity (Pint Removal Rate)
The capacity of a dehumidifier is often measured in pints per day (PPD). This specification indicates how much moisture the unit can extract from the air in a 24-hour period. For B2B buyers, selecting the right capacity is essential based on the size of the space and the humidity levels. Overestimating capacity can lead to increased energy costs, while underestimating can result in ineffective moisture control.
2. Energy Efficiency Ratio (EER)
The Energy Efficiency Ratio is a critical metric that indicates the energy consumption of the dehumidifier relative to its moisture removal capability. A higher EER signifies better efficiency, which translates to lower electricity costs. For international buyers, especially in regions with fluctuating energy prices, prioritizing EER can yield significant savings over time.
3. Material Grade and Build Quality
The materials used in the construction of dehumidifiers can significantly impact durability and performance. Stainless steel and high-grade plastics are common choices that resist corrosion and wear. Buyers should consider material grades when assessing the longevity and reliability of the equipment, especially in harsh environments.
4. Humidity Control Range
This specification indicates the range of humidity levels the dehumidifier can effectively manage. A wider control range allows for greater flexibility in various climates and applications. Understanding the humidity control capabilities is essential for buyers to ensure that the dehumidifier meets specific operational requirements.
5. Noise Level (dB)
For many applications, especially in hospitality and residential settings, the noise level of a dehumidifier is a crucial factor. Buyers should look for units with lower decibel ratings to ensure a comfortable environment. Noise levels can also affect employee productivity in commercial settings.
What Are Common Trade Terms in the Dehumidifier Manufacturing Industry?
Navigating the terminology in the dehumidifier manufacturing industry is key for B2B buyers to ensure smooth transactions and clear communication with suppliers.
1. OEM (Original Equipment Manufacturer)
An OEM refers to a company that produces parts or equipment that may be marketed by another manufacturer. In the context of dehumidifiers, understanding OEM relationships can help buyers identify quality standards and potential customization options for their needs.
2. MOQ (Minimum Order Quantity)
MOQ is the minimum number of units a supplier is willing to sell in a single order. This term is crucial for buyers who need to manage inventory costs and avoid excess stock. Knowing the MOQ helps in budgeting and planning for future purchases.
3. RFQ (Request for Quotation)
An RFQ is a document sent to suppliers to solicit pricing and terms for a specific quantity of products. For B2B buyers, submitting an RFQ can streamline the purchasing process by ensuring they receive competitive quotes from multiple suppliers.
4. Incoterms (International Commercial Terms)
Incoterms are standardized trade terms that define the responsibilities of buyers and sellers in international transactions. Understanding these terms is vital for buyers to clarify shipping responsibilities, risk management, and cost allocation. Key terms include FOB (Free on Board) and CIF (Cost, Insurance, and Freight).
5. Lead Time
Lead time refers to the amount of time it takes for a supplier to fulfill an order after it has been placed. For B2B buyers, understanding lead times is essential for planning projects, especially in industries where timing is critical.
By familiarizing themselves with these technical properties and trade terms, B2B buyers can make informed decisions that align with their operational needs and budget constraints.
Navigating Market Dynamics and Sourcing Trends in the dehumidifier manufacturer Sector
What Are the Current Market Trends in the Dehumidifier Manufacturing Sector?
The global dehumidifier market is witnessing substantial growth, driven by increasing awareness of indoor air quality and rising humidity levels in various regions. This trend is particularly pronounced in Africa, South America, the Middle East, and Europe, where climate variability is prompting both residential and commercial investments in dehumidification solutions. Key drivers include the rise in construction activities, the growth of the hospitality sector, and the need for moisture control in sensitive environments like healthcare and food storage.
Emerging technologies are also shaping the market, with smart dehumidifiers equipped with IoT capabilities becoming increasingly popular. These devices allow users to monitor and control humidity levels remotely, enhancing convenience and energy efficiency. Additionally, energy-efficient models are gaining traction as consumers become more environmentally conscious, seeking products that reduce electricity consumption while maintaining performance.
B2B buyers must stay informed about these trends to align their purchasing strategies with market dynamics. Understanding regional variations in demand and the importance of energy efficiency can help international buyers, especially from regions like Brazil and the UAE, make informed sourcing decisions that enhance their competitive edge.
How Is Sustainability Influencing the Dehumidifier Manufacturing Industry?
Sustainability has become a paramount concern for businesses globally, including the dehumidifier manufacturing sector. The environmental impact of manufacturing processes and product lifecycle management is under scrutiny, pushing manufacturers to adopt more sustainable practices. Ethical sourcing of materials is increasingly important, as B2B buyers prioritize suppliers who demonstrate commitment to reducing their carbon footprint.
In this context, ‘green’ certifications such as Energy Star and eco-labels are critical for buyers looking to validate the sustainability of their purchases. These certifications not only indicate energy efficiency but also signal adherence to environmentally friendly manufacturing processes. Furthermore, the use of recyclable materials and components is becoming standard practice, with manufacturers exploring eco-friendly refrigerants that minimize ozone depletion.
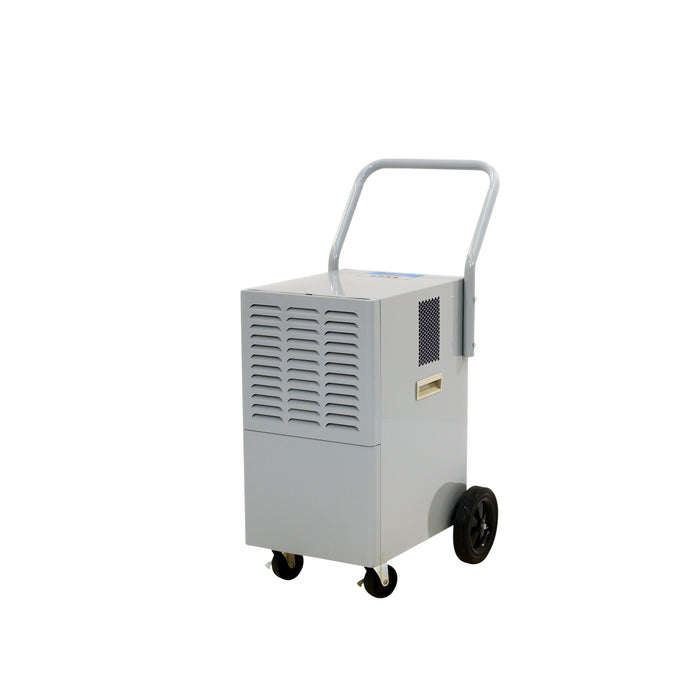
A stock image related to dehumidifier manufacturer.
By prioritizing sustainability, B2B buyers can enhance their corporate social responsibility (CSR) profiles while meeting the growing consumer demand for environmentally friendly products. Engaging with suppliers who share these values can lead to stronger partnerships and improved brand loyalty.
What Is the Historical Context of the Dehumidifier Manufacturing Sector?
The dehumidifier industry has evolved significantly since its inception in the mid-20th century. Initially developed for industrial applications, dehumidifiers have gradually found their place in residential markets, driven by the need for moisture control in homes and commercial spaces. The introduction of refrigerant-based systems in the 1960s marked a turning point, enabling more efficient moisture removal and setting the stage for modern designs.
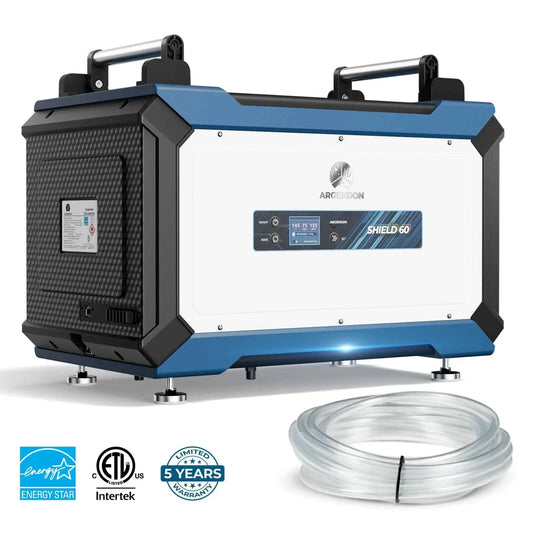
A stock image related to dehumidifier manufacturer.
In recent decades, technological advancements have further transformed the sector, leading to the development of compact, portable models that cater to diverse consumer needs. The integration of smart technology and energy-efficient features reflects the industry’s response to changing consumer preferences and regulatory pressures for sustainability. This historical perspective underscores the importance of innovation and adaptability for manufacturers aiming to thrive in today’s competitive market landscape.
Frequently Asked Questions (FAQs) for B2B Buyers of dehumidifier manufacturer
-
How do I choose the right dehumidifier for my business needs?
Selecting the right dehumidifier involves assessing the specific humidity levels and the size of the area to be dehumidified. Consider factors such as the type of environment (industrial, commercial, or residential), the volume of air to be processed, and the desired humidity levels. Additionally, evaluate energy efficiency ratings and maintenance requirements. Consulting with manufacturers for technical specifications and potential applications can also provide valuable insights tailored to your business needs. -
What are the key features to look for in a dehumidifier?
When sourcing a dehumidifier, key features to consider include capacity (measured in pints per day), energy efficiency (EER ratings), portability, and noise levels. Advanced features like built-in humidistats, automatic shut-off, continuous drainage options, and user-friendly controls can enhance usability. Additionally, check for warranties and customer support services, as these can indicate the manufacturer’s commitment to quality and after-sales service. -
What is the minimum order quantity (MOQ) for dehumidifiers?
The MOQ for dehumidifiers varies by manufacturer and can be influenced by factors such as production capacity and customization options. Typically, MOQs range from 10 to 100 units. It is advisable to communicate directly with potential suppliers to negotiate terms that suit your business needs, especially if you are exploring bulk purchasing or custom designs. -
What payment terms should I expect when dealing with dehumidifier manufacturers?
Payment terms can differ significantly among manufacturers. Common practices include partial payments upfront (often 30-50%) with the balance due upon delivery or after inspection. Some manufacturers may offer credit terms for established businesses. Always clarify payment methods, currency preferences, and any applicable fees to avoid misunderstandings and ensure a smooth transaction. -
How can I verify the credibility of a dehumidifier manufacturer?
To verify a manufacturer’s credibility, conduct thorough research including checking their business registration, certifications (like ISO), and industry reputation. Request references or case studies from previous clients, and review online testimonials. Participating in trade shows or industry forums can also provide insights into the manufacturer’s standing in the market. -
What customization options are available for commercial dehumidifiers?
Many manufacturers offer customization options to meet specific business needs, including size, capacity, and additional features such as integrated air filters or remote monitoring systems. Discuss your requirements directly with the manufacturer to explore available configurations. Customized solutions can enhance operational efficiency and ensure the dehumidifiers fit seamlessly into your existing systems. -
What logistics considerations should I keep in mind when importing dehumidifiers?
When importing dehumidifiers, consider shipping costs, delivery timelines, and customs regulations in your country. Collaborate with logistics providers who have experience in handling similar products to ensure compliance with import duties and taxes. Additionally, confirm that the manufacturer can provide necessary documentation, such as certificates of origin and compliance, to facilitate smooth customs clearance. -
What quality assurance measures should I expect from a dehumidifier manufacturer?
Quality assurance measures vary, but reputable manufacturers will typically conduct rigorous testing on their products before shipment. Look for manufacturers that provide detailed quality control processes, including performance testing and compliance with international standards. Request documentation regarding warranties, return policies, and post-sale support to ensure you are covered in case of defects or performance issues.
Important Disclaimer & Terms of Use
⚠️ Important Disclaimer
The information provided in this guide, including content regarding manufacturers, technical specifications, and market analysis, is for informational and educational purposes only. It does not constitute professional procurement advice, financial advice, or legal advice.
While we have made every effort to ensure the accuracy and timeliness of the information, we are not responsible for any errors, omissions, or outdated information. Market conditions, company details, and technical standards are subject to change.
B2B buyers must conduct their own independent and thorough due diligence before making any purchasing decisions. This includes contacting suppliers directly, verifying certifications, requesting samples, and seeking professional consultation. The risk of relying on any information in this guide is borne solely by the reader.
Strategic Sourcing Conclusion and Outlook for dehumidifier manufacturer
Why is Strategic Sourcing Essential for Dehumidifier Manufacturers?
In today’s competitive landscape, strategic sourcing is crucial for dehumidifier manufacturers looking to thrive in diverse international markets, including Africa, South America, the Middle East, and Europe. By leveraging a well-defined sourcing strategy, businesses can optimize costs, enhance product quality, and ensure timely deliveries. Understanding local regulations, market demands, and logistical challenges enables manufacturers to make informed decisions that align with their operational goals.
What Key Takeaways Should B2B Buyers Consider?
B2B buyers should prioritize suppliers who demonstrate a strong commitment to sustainability and innovation. Evaluate potential partners based on their technological capabilities, responsiveness to market changes, and ability to provide customized solutions. Engaging in partnerships with manufacturers that have a proven track record can lead to improved supply chain resilience and operational efficiency.
How Can International Buyers Prepare for Future Opportunities?
Looking ahead, the demand for dehumidifiers is expected to grow, driven by increasing awareness of indoor air quality and humidity control. Buyers should actively seek out manufacturers that not only meet current needs but are also poised to adapt to future trends. By fostering collaborative relationships with suppliers, buyers can gain insights into emerging technologies and market shifts.
In conclusion, embracing strategic sourcing in your procurement process will not only enhance your competitive edge but also empower your business to seize new opportunities in the global market. Take the next step—evaluate your sourcing strategy today and position your company for long-term success in the dehumidifier sector.