Discover Top Benefits of Choosing a Flexible PCB Supplier (2025)
Introduction: Navigating the Global Market for flexible pcb supplier
In an increasingly interconnected world, sourcing a reliable flexible PCB supplier can present a unique set of challenges for international B2B buyers. Companies in regions such as Africa, South America, the Middle East, and Europe often struggle with identifying suppliers that not only meet their technical specifications but also adhere to quality standards and competitive pricing. This guide aims to equip decision-makers with the knowledge needed to navigate the complexities of the flexible PCB market, ultimately empowering them to make informed purchasing decisions.
The comprehensive scope of this guide covers various essential aspects of flexible PCB sourcing, including types of flexible PCBs, their diverse applications across industries, and critical supplier vetting processes. Additionally, we delve into cost considerations, enabling buyers to evaluate pricing structures and budget implications effectively. By understanding these key elements, businesses can mitigate risks associated with supplier selection and ensure they partner with manufacturers that align with their operational needs.
For international buyers, particularly from emerging markets like Kenya and Turkey, this guide provides actionable insights that enhance the procurement process. By leveraging this information, companies can streamline their sourcing strategies, reduce lead times, and ultimately drive innovation in their product offerings. Prepare to embark on a journey that transforms the way you approach flexible PCB procurement, ensuring you remain competitive in the global marketplace.
Understanding flexible pcb supplier Types and Variations
Type Name | Key Distinguishing Features | Primary B2B Applications | Brief Pros & Cons for Buyers |
---|---|---|---|
Single-Sided Flexible PCB | One conductive layer, cost-effective, simpler design | Consumer electronics, medical devices | Pros: Lower cost, easier to manufacture. Cons: Limited functionality, less complex designs. |
Double-Sided Flexible PCB | Two conductive layers, more complex designs | Automotive, telecommunications | Pros: Higher density of components, better performance. Cons: More expensive, complex manufacturing. |
Multilayer Flexible PCB | Multiple conductive layers, highly complex designs | Aerospace, industrial equipment | Pros: Compact design, high reliability. Cons: Higher cost, longer lead times. |
Rigid-Flex PCB | Combination of rigid and flexible substrates | Medical devices, military applications | Pros: Enhanced durability, space-saving. Cons: Complex assembly, higher initial costs. |
High-Frequency Flexible PCB | Specialized for high-frequency applications | RF devices, satellite technology | Pros: Excellent signal integrity, tailored for specific applications. Cons: Requires specialized knowledge for design and manufacturing. |
What are the Characteristics of Single-Sided Flexible PCBs?
Single-sided flexible PCBs are characterized by having only one conductive layer, making them a cost-effective choice for many applications. They are ideal for simpler electronic designs where space is limited, such as in consumer electronics and medical devices. When considering procurement, buyers should focus on the supplier’s manufacturing capabilities and material quality, as these factors significantly impact the performance and reliability of the final product.
How Do Double-Sided Flexible PCBs Stand Out?
Double-sided flexible PCBs feature two conductive layers, allowing for more complex circuit designs and increased component density. They are commonly used in automotive and telecommunications applications where performance is critical. Buyers should evaluate the supplier’s experience with double-sided designs, as the manufacturing process can be more intricate, potentially leading to longer lead times and higher costs.
What Makes Multilayer Flexible PCBs Unique?
Multilayer flexible PCBs consist of multiple conductive layers, which enable highly complex and compact designs. They are particularly suited for industries like aerospace and industrial equipment, where reliability and performance are paramount. When purchasing multilayer PCBs, B2B buyers should consider the supplier’s expertise in multilayer technology, as well as their ability to meet stringent quality standards and certifications.
Why Choose Rigid-Flex PCBs for Your Projects?
Rigid-flex PCBs combine the benefits of both rigid and flexible substrates, offering enhanced durability and flexibility in design. They are commonly used in medical devices and military applications where space-saving and resilience are essential. Buyers should assess the supplier’s capabilities in producing rigid-flex designs, as the assembly process can be complex, requiring specialized equipment and knowledge.
What are the Benefits of High-Frequency Flexible PCBs?
High-frequency flexible PCBs are designed specifically for applications that require excellent signal integrity, such as RF devices and satellite technology. These PCBs are built with materials that can handle high-frequency signals without significant loss. When sourcing high-frequency flexible PCBs, buyers should prioritize suppliers with specialized expertise and experience in this niche, ensuring that they can meet the specific design and performance requirements of their projects.
Related Video: DIY Flexible Arduino | Flexible PCB Tutorial | JLCPCB
Key Industrial Applications of flexible pcb supplier
Industry/Sector | Specific Application of flexible pcb supplier | Value/Benefit for the Business | Key Sourcing Considerations for this Application |
---|---|---|---|
Consumer Electronics | Wearable Technology | Enhanced comfort and functionality for users | Supplier’s ability to produce high-density interconnections |
Automotive | Advanced Driver-Assistance Systems (ADAS) | Improved safety and vehicle performance | Compliance with automotive industry standards and certifications |
Medical Devices | Portable Diagnostic Equipment | Increased portability and user-friendliness | Quality assurance and biocompatibility certifications |
Telecommunications | Smartphones and Tablets | Slimmer designs with advanced capabilities | Supplier’s experience with high-frequency applications |
Industrial Automation | Robotics and Automation Systems | Increased efficiency and reduced operational costs | Supplier’s capacity for customization and rapid prototyping |
How Are Flexible PCBs Used in Consumer Electronics?
In the consumer electronics sector, flexible PCBs are vital for the development of wearable technology, such as smartwatches and fitness trackers. These devices require lightweight and compact designs without compromising on functionality. Flexible PCBs facilitate intricate circuit layouts that conform to the device’s shape, enhancing user comfort and usability. International buyers, particularly from regions like Africa and South America, should prioritize suppliers who can deliver high-density interconnections and reliable performance in variable environmental conditions.
What Role Do Flexible PCBs Play in Automotive Applications?
Flexible PCBs are increasingly used in Advanced Driver-Assistance Systems (ADAS) within the automotive industry. They enable the integration of multiple sensors and cameras into a compact form factor, improving vehicle safety and performance. As global automotive standards evolve, buyers from the Middle East and Europe must ensure their suppliers comply with rigorous automotive industry certifications. This guarantees that the flexible PCBs can withstand harsh conditions while delivering consistent performance.
How Are Flexible PCBs Beneficial for Medical Devices?
In the medical field, flexible PCBs are essential for portable diagnostic equipment, such as blood glucose monitors and ECG devices. Their lightweight and compact nature allows for easy integration into handheld devices, enhancing portability and user-friendliness. For international B2B buyers, especially those in Turkey and surrounding regions, sourcing from suppliers that offer quality assurance and biocompatibility certifications is crucial to ensure compliance with health regulations and maintain patient safety.
Why Are Flexible PCBs Important in Telecommunications?
Flexible PCBs play a significant role in the telecommunications industry, particularly in smartphones and tablets. They allow for thinner designs while accommodating advanced features such as high-speed data transmission. As demand for slimmer devices grows, buyers from Europe and Africa should focus on suppliers with proven experience in high-frequency applications. This ensures that the flexible PCBs can handle the rigorous demands of modern telecommunications technology.
How Do Flexible PCBs Enhance Industrial Automation?
In industrial automation, flexible PCBs are integral to the functionality of robotics and automation systems. They facilitate complex circuitry in compact spaces, leading to increased efficiency and reduced operational costs. International buyers, especially from South America and the Middle East, should consider suppliers that offer customization options and rapid prototyping capabilities. This flexibility allows businesses to adapt to changing technological needs while ensuring high-quality production standards.
3 Common User Pain Points for ‘flexible pcb supplier’ & Their Solutions
Scenario 1: Inconsistent Quality Standards Across Suppliers
The Problem: International B2B buyers often face significant challenges with inconsistent quality when sourcing flexible PCBs from various suppliers. For companies in regions like Africa and South America, where local suppliers may not adhere to global standards, this inconsistency can lead to product failures, increased costs, and reputational damage. Buyers may find themselves receiving batches of PCBs that vary in flexibility, thermal stability, or electrical performance, complicating their production processes and delaying time-to-market.
The Solution: To mitigate this issue, B2B buyers should prioritize sourcing from suppliers who can demonstrate adherence to international quality standards, such as ISO 9001 or IPC-6013. When evaluating potential suppliers, request detailed documentation of their quality assurance processes, including certifications and third-party audits. Establish clear specifications for the flexible PCBs you require, and consider incorporating a trial period with the supplier to assess product consistency before placing larger orders. Furthermore, maintaining open lines of communication with suppliers can facilitate rapid feedback and adjustments, ensuring that quality remains a top priority.
Scenario 2: High Costs and Long Lead Times for Flexible PCBs
The Problem: A common pain point for buyers is facing exorbitant costs and prolonged lead times when ordering flexible PCBs, especially when working with suppliers in regions with high tariffs or shipping costs. This can be particularly detrimental for companies in the Middle East and Europe that require rapid prototyping and production cycles to stay competitive. The pressure to reduce costs while not sacrificing quality can lead to a frustrating balancing act.
The Solution: To overcome high costs and long lead times, buyers should consider developing long-term partnerships with suppliers who offer competitive pricing structures and reliable delivery schedules. Engaging in strategic discussions regarding bulk purchasing or establishing a dedicated inventory can help mitigate costs. Additionally, utilizing suppliers that have local manufacturing capabilities can significantly reduce shipping times and costs. Leveraging technology for better demand forecasting can also allow buyers to place orders more effectively, thus optimizing inventory levels and reducing the risk of stockouts.
Scenario 3: Difficulty in Understanding Technical Specifications
The Problem: Many B2B buyers find themselves struggling to comprehend the technical specifications of flexible PCBs, leading to miscommunications and inappropriate product selections. This challenge can be exacerbated for companies in Africa and South America, where access to technical resources may be limited. Buyers may inadvertently order PCBs that do not meet their electrical or mechanical requirements, resulting in costly redesigns and delays.
The Solution: To address this knowledge gap, buyers should invest in training and resources that enhance their understanding of flexible PCB specifications. Collaborating closely with suppliers who provide comprehensive technical support can also bridge this gap. When engaging with a supplier, request detailed explanations of the specifications, including materials, thickness, and performance characteristics. Establishing a collaborative relationship where suppliers offer design assistance or prototyping services can empower buyers to make informed decisions. Additionally, attending industry trade shows or webinars can provide valuable insights into the latest innovations and technical developments in flexible PCBs, further enhancing buyer competence and confidence.
Strategic Material Selection Guide for flexible pcb supplier
When selecting materials for flexible printed circuit boards (PCBs), international B2B buyers must consider various factors that impact product performance, manufacturing processes, and end-user applications. Below is an analysis of four common materials used in flexible PCBs, focusing on their properties, advantages, disadvantages, and specific considerations for buyers from Africa, South America, the Middle East, and Europe.
What Are the Key Properties of Polyimide in Flexible PCBs?
Polyimide is one of the most widely used materials for flexible PCBs due to its excellent thermal stability and mechanical properties. It can withstand temperatures ranging from -269°C to 400°C, making it suitable for high-performance applications. Additionally, polyimide exhibits good chemical resistance, which is vital for environments where exposure to solvents and corrosive substances is common.
Pros & Cons: The durability of polyimide is a significant advantage, allowing it to maintain performance under extreme conditions. However, it tends to be more expensive than other materials, which can affect overall project budgets. The manufacturing complexity is moderate, requiring specialized processes that may not be available in all regions.
Impact on Application: Polyimide’s compatibility with various media makes it ideal for aerospace, automotive, and medical applications. Buyers should ensure that their suppliers can meet specific industry standards, such as ASTM or DIN, particularly in regions like Europe.
How Does PET Compare as a Material for Flexible PCBs?
Polyethylene Terephthalate (PET) is another popular choice for flexible PCBs, especially in consumer electronics. It offers a good balance of flexibility, strength, and cost-effectiveness. PET can operate effectively at temperatures up to 150°C, making it suitable for applications that do not require extreme thermal performance.
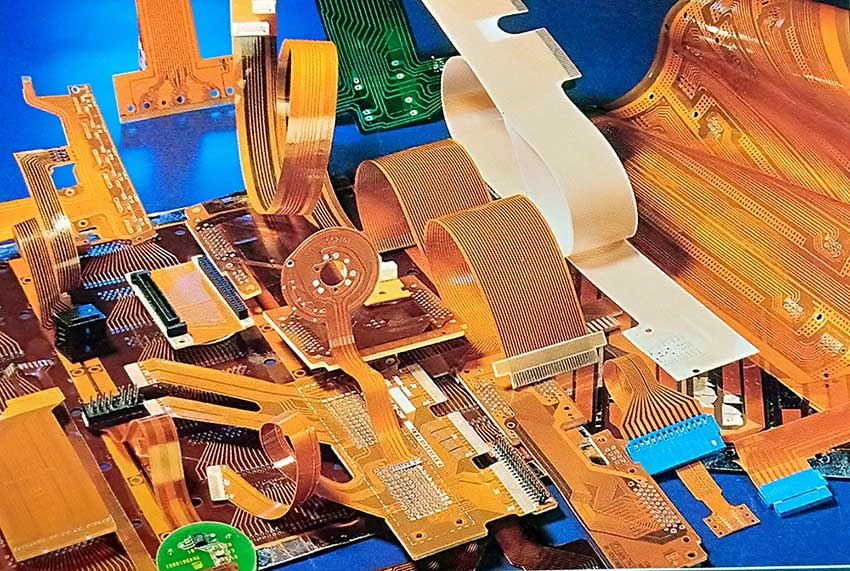
A stock image related to flexible pcb supplier.
Pros & Cons: The primary advantage of PET is its lower cost compared to polyimide, making it an attractive option for high-volume production. However, its thermal and chemical resistance is not as robust, limiting its use in more demanding applications. The manufacturing process is relatively straightforward, which can be beneficial for suppliers in emerging markets.
Impact on Application: PET is commonly used in devices like smartphones and wearable technology. Buyers should consider local regulations regarding material safety and recycling, particularly in regions with stringent environmental standards.
What Are the Benefits of Using FR-4 in Flexible PCB Manufacturing?
FR-4, a composite material made from woven fiberglass and epoxy resin, is primarily known for its use in rigid PCBs but can also be adapted for flexible applications. It offers good mechanical strength and electrical insulation properties, with a temperature rating of up to 130°C.
Pros & Cons: The durability of FR-4 is a major advantage, especially in applications requiring structural integrity. However, its flexibility is limited compared to other materials, which can restrict its use in highly flexible designs. The cost is generally moderate, making it a viable option for various projects.
Impact on Application: FR-4 is suitable for consumer electronics, industrial equipment, and automotive applications. Buyers should be aware of the need for compliance with international standards, especially when exporting products to regions with specific regulations.
What Is the Role of LCP in Advanced Flexible PCB Applications?
Liquid Crystal Polymer (LCP) is a high-performance material that provides excellent thermal stability and low moisture absorption. It can operate effectively at temperatures above 200°C, making it suitable for high-frequency applications.
Pros & Cons: LCP offers superior electrical performance and is highly resistant to chemicals and moisture. However, it is one of the more expensive materials, and its manufacturing process can be complex, requiring specialized equipment.
Impact on Application: LCP is ideal for applications in telecommunications, medical devices, and aerospace. Buyers should ensure that their suppliers can meet the necessary compliance requirements and certifications, particularly in regions like Europe and the Middle East, where standards are stringent.
Summary Table of Material Selection for Flexible PCBs
Material | Typical Use Case for flexible pcb supplier | Key Advantage | Key Disadvantage/Limitation | Relative Cost (Low/Med/High) |
---|---|---|---|---|
Polyimide | Aerospace, automotive, medical devices | Excellent thermal stability | Higher cost and manufacturing complexity | High |
PET | Consumer electronics, wearables | Cost-effective and good flexibility | Limited thermal and chemical resistance | Low |
FR-4 | Consumer electronics, industrial equipment | Good mechanical strength | Limited flexibility | Medium |
LCP | Telecommunications, aerospace | Superior electrical performance | High cost and complex manufacturing | High |
This material selection guide provides international B2B buyers with the insights needed to make informed decisions when sourcing flexible PCBs, taking into account specific regional considerations and compliance requirements.
In-depth Look: Manufacturing Processes and Quality Assurance for flexible pcb supplier
What Are the Key Stages in the Manufacturing Process of Flexible PCBs?
Flexible printed circuit boards (PCBs) are essential components in various electronic devices due to their lightweight and adaptable nature. Understanding the manufacturing processes is crucial for international B2B buyers looking to source flexible PCBs efficiently.
1. Material Preparation
The first stage involves selecting and preparing the materials, which typically include flexible substrates such as polyimide or polyester. These materials are chosen based on their electrical, thermal, and mechanical properties. Buyers should inquire about the supplier’s sourcing practices for these materials to ensure they meet international quality standards.
Key techniques in this phase include:
- Material Testing: Conducting initial tests to verify the properties of the substrates, ensuring they conform to specifications.
- Surface Treatment: Applying treatments to enhance adhesion for subsequent layers, which can significantly affect performance.
2. Forming the Flexible PCB
Once materials are prepared, the next step is the formation of the PCB. This includes several key techniques:
- Printing Circuit Patterns: This is commonly done through photolithography, where a light-sensitive photoresist is applied, exposing it to UV light to create intricate circuit patterns.
- Etching: The exposed areas are chemically etched away to create conductive traces. Buyers should understand the etching methods used, as they can impact the precision and quality of the final product.
3. Assembly of Components
After forming the PCB, the assembly process begins, which involves integrating various electronic components onto the flexible substrate.
Key techniques include:
- Soldering: Both surface-mount technology (SMT) and through-hole soldering methods are employed. Understanding the soldering techniques is critical, as improper soldering can lead to circuit failure.
- Testing During Assembly: Implementing in-process testing to catch defects early, which enhances overall quality.
4. Finishing Touches
The final stage involves applying protective coatings, laminations, and cutting the PCBs into the desired shapes.
Important aspects include:
- Surface Finishing: Techniques such as ENIG (Electroless Nickel Immersion Gold) are often used to enhance solderability and prevent oxidation.
- Quality Control Checkpoints: Before shipping, final inspections ensure that all specifications are met.
How Is Quality Assurance Ensured in Flexible PCB Manufacturing?
Quality assurance is a critical aspect of flexible PCB production, ensuring that the final product meets both industry standards and client specifications. International buyers should be particularly vigilant about the quality assurance processes employed by their suppliers.
What International Standards Should B2B Buyers Be Aware Of?
Several international standards govern the quality assurance of PCBs, which include:
- ISO 9001: This standard focuses on quality management systems, ensuring that suppliers have processes in place for continuous improvement.
- IPC Standards: These standards, such as IPC-A-600 for acceptability of printed boards, provide guidelines specific to PCB manufacturing.
Additionally, industry-specific certifications like CE (Conformité Européenne) for products sold in Europe and API (American Petroleum Institute) for specific applications in oil and gas sectors are crucial for compliance and market access.
What Are the Common Quality Control Checkpoints?
Quality control (QC) should be integrated at various stages of the manufacturing process. Key QC checkpoints include:
- Incoming Quality Control (IQC): This involves inspecting raw materials before they enter the production line.
- In-Process Quality Control (IPQC): Conducting inspections and tests at various points during the manufacturing process to catch defects early.
- Final Quality Control (FQC): Comprehensive testing and inspection of the finished product before shipping.
What Testing Methods Are Commonly Used for Flexible PCBs?
Testing is vital to ensure the reliability and performance of flexible PCBs. Common testing methods include:
- Electrical Testing: Verifying the electrical integrity of the circuits through techniques like continuity and isolation testing.
- Mechanical Testing: Assessing the flexibility and durability of the PCB under various conditions, including bending and thermal cycling.
- Environmental Testing: Evaluating the performance of PCBs in different environmental conditions, such as humidity and temperature extremes.
How Can B2B Buyers Verify Supplier Quality Control Practices?
International B2B buyers must take proactive steps to verify the quality control practices of potential suppliers:
- Conduct Audits: Regular supplier audits can help assess compliance with international standards and internal quality processes.
- Request Quality Reports: Suppliers should provide documentation of their quality control processes, including test results and compliance certifications.
- Engage Third-party Inspectors: Utilizing third-party inspection services can provide an unbiased evaluation of the supplier’s quality practices.
What Are the Quality Control Nuances for International Buyers?
When sourcing flexible PCBs from suppliers in regions such as Africa, South America, the Middle East, and Europe, buyers should consider several nuances:
- Cultural Differences: Understanding cultural attitudes towards quality and compliance can influence supplier relationships.
- Regulatory Compliance: Different regions may have varying regulations regarding electronic products, necessitating thorough understanding and compliance.
- Logistics and Supply Chain Considerations: International shipping can introduce risks that affect quality. Ensuring proper packaging and handling during transit is essential.
By comprehensively understanding the manufacturing processes and quality assurance mechanisms, B2B buyers can make informed decisions when sourcing flexible PCBs, ensuring they receive high-quality products that meet their specific needs.
Practical Sourcing Guide: A Step-by-Step Checklist for ‘flexible pcb supplier’
Introduction
Sourcing a flexible PCB supplier is a critical step for businesses looking to innovate and enhance their electronic products. This guide provides a structured checklist to help international B2B buyers from Africa, South America, the Middle East, and Europe navigate the complexities of selecting the right supplier. By following these steps, you can ensure that your procurement process is efficient, effective, and aligned with your technical and business needs.
Step 1: Define Your Technical Specifications
Clearly outlining your technical specifications is essential for finding a supplier that meets your needs. Determine the dimensions, layer count, and material requirements for your flexible PCB. This will not only streamline communication with suppliers but also help you evaluate their capabilities effectively.
- Considerations:
- What specific applications will the flexible PCB be used for?
- Are there industry standards or certifications that the product must meet?
Step 2: Research Potential Suppliers
Conduct thorough research to identify potential flexible PCB suppliers. Utilize online platforms, industry forums, and trade associations to compile a list of candidates. Pay attention to suppliers that specialize in your required specifications and have a strong reputation in the market.
- Where to Look:
- Industry directories and trade shows
- Online marketplaces and supplier databases
Step 3: Evaluate Supplier Experience and Expertise
Assess the experience and expertise of potential suppliers in the flexible PCB sector. Look for companies that have a proven track record with similar projects and industries. This ensures that they are familiar with the challenges and requirements specific to your needs.
- What to Check:
- Years in business and customer testimonials
- Case studies showcasing previous work
Step 4: Verify Supplier Certifications
Ensure that your potential suppliers hold relevant industry certifications. Certifications such as ISO 9001 for quality management systems or IPC standards for PCB manufacturing can indicate a commitment to quality and reliability.
- Importance of Certifications:
- They serve as a benchmark for quality assurance.
- They can mitigate risks associated with compliance and product failures.
Step 5: Request Samples and Prototypes
Before making a large purchase, request samples or prototypes of the flexible PCBs. This hands-on approach allows you to assess the quality, functionality, and suitability of the products for your specific application.
- What to Evaluate:
- Overall build quality and craftsmanship
- Compatibility with your existing systems
Step 6: Assess Production Capabilities and Lead Times
Investigate the production capabilities of your shortlisted suppliers, including their capacity to handle your order size and their typical lead times. Understanding their manufacturing processes can help you gauge their ability to meet deadlines and scalability.
- Key Questions:
- What is their minimum order quantity (MOQ)?
- How do they manage production delays or quality control issues?
Step 7: Establish Clear Communication Channels
Effective communication is vital for a successful partnership. Ensure that the supplier has a dedicated point of contact who can provide timely updates and address any concerns throughout the procurement process.
- What to Look For:
- Responsiveness to inquiries
- Availability of support in your preferred language
By following this comprehensive checklist, B2B buyers can confidently navigate the sourcing process for flexible PCB suppliers, ensuring they select a partner that aligns with their technical requirements and business objectives.
Comprehensive Cost and Pricing Analysis for flexible pcb supplier Sourcing
What Are the Key Cost Components in Sourcing Flexible PCBs?
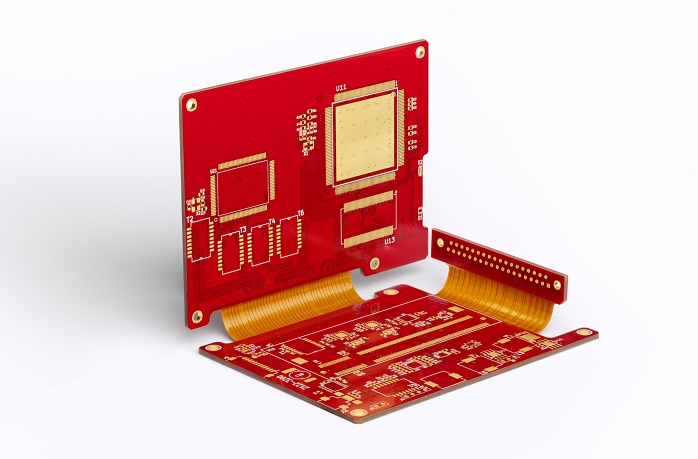
A stock image related to flexible pcb supplier.
Understanding the cost structure associated with flexible PCB suppliers is crucial for international B2B buyers aiming to optimize their sourcing strategies. The main cost components include:
-
Materials: The type of substrate and conductive materials significantly impact the overall cost. High-quality materials like polyimide and copper will be more expensive but can enhance performance and durability.
-
Labor: Labor costs vary based on geographic location and the level of expertise required. Countries with lower labor costs may offer competitive pricing, but this can also lead to variations in quality and production speed.
-
Manufacturing Overhead: This includes costs related to facility operations, utilities, and administrative expenses. Efficient manufacturing processes can reduce overhead, allowing suppliers to offer more competitive pricing.
-
Tooling: Custom tooling can be a significant upfront cost, particularly for unique designs. Buyers should inquire about tooling costs and whether these can be amortized over larger orders.
-
Quality Control (QC): Ensuring that products meet specific standards incurs additional costs. However, investing in robust QC processes can prevent costly defects and delays later in the supply chain.
-
Logistics: Shipping costs can vary greatly depending on the destination and method of transportation. Buyers should consider the total logistics cost, including tariffs and taxes, especially when sourcing from overseas suppliers.
-
Margin: Suppliers typically include a profit margin that reflects their operational costs and market positioning. Understanding the margin can help buyers negotiate better terms.
How Do Price Influencers Impact Flexible PCB Sourcing?
Several factors can influence the pricing of flexible PCBs, which are essential for buyers to consider:
-
Volume and Minimum Order Quantity (MOQ): Larger orders often result in lower per-unit costs due to economies of scale. Buyers should assess their demand and negotiate MOQs that align with their production needs.
-
Specifications and Customization: Customized designs and specifications can lead to higher costs. Buyers should clearly define their requirements to avoid unexpected price increases.
-
Materials and Quality Certifications: Higher quality materials and certifications (e.g., ISO, RoHS) can raise costs but may be necessary for specific applications. Understanding the value of these certifications can justify the investment.
-
Supplier Factors: The supplier’s experience, reputation, and location can affect pricing. Established suppliers may charge more due to their reliability and track record, while newer suppliers might offer lower prices to gain market share.
-
Incoterms: The chosen Incoterms (e.g., FOB, CIF) can significantly affect the final cost. Buyers should be clear about their responsibilities and the costs associated with shipping and delivery.
What Tips Can Help Buyers Negotiate Better Prices for Flexible PCBs?
For international B2B buyers, particularly from Africa, South America, the Middle East, and Europe, effective negotiation strategies can lead to better pricing and terms:
-
Conduct Thorough Research: Understand the market rates and the cost structure of flexible PCBs. This knowledge will empower buyers to negotiate from a position of strength.
-
Leverage Total Cost of Ownership (TCO): Consider not just the purchase price but all associated costs, including logistics, quality control, and potential downtime due to defects. Highlighting TCO in negotiations can justify higher upfront costs for suppliers that offer better long-term value.
-
Build Strong Relationships: Establishing a good relationship with suppliers can lead to more favorable terms and pricing. Long-term partnerships often result in trust, better communication, and potential discounts.
-
Be Open to Multiple Suppliers: Diversifying suppliers can foster competition, which may lead to lower prices. However, ensure that quality standards are maintained across all suppliers.
-
Understand Local and International Market Trends: Stay informed about economic conditions, supply chain disruptions, and technological advancements that may impact prices. This awareness can provide leverage during negotiations.
Disclaimer on Indicative Prices
Prices for flexible PCBs can vary widely based on multiple factors, including market conditions and supplier capabilities. Therefore, it is essential for buyers to obtain detailed quotes tailored to their specific requirements and to conduct due diligence when evaluating suppliers.
Alternatives Analysis: Comparing flexible pcb supplier With Other Solutions
When evaluating the best solutions for your electronic assembly needs, it’s essential to consider various alternatives to flexible PCB suppliers. Flexible PCBs offer unique advantages, but they may not always be the most suitable option depending on your specific requirements. This analysis will compare flexible PCBs against two alternative solutions: rigid PCBs and printed circuit board (PCB) assemblies that utilize traditional materials.
Comparison Table: Flexible PCB Supplier vs. Alternatives
Comparison Aspect | Flexible PCB Supplier | Rigid PCB Supplier | PCB Assembly with Traditional Materials |
---|---|---|---|
Performance | High flexibility and lightweight, ideal for compact spaces | High durability, suited for stable environments | Variable performance based on materials used |
Cost | Generally higher due to specialized manufacturing | Lower cost, widely available | Cost-effective, especially for large volumes |
Ease of Implementation | Requires specialized skills for design and assembly | Easier implementation with standard tools | Moderate complexity depending on the design |
Maintenance | More prone to damage in harsh environments | Easier to repair and maintain | Maintenance varies; traditional materials may be more robust |
Best Use Case | Wearable technology, medical devices | Consumer electronics, industrial applications | High-volume production, cost-sensitive projects |
What Are the Pros and Cons of Rigid PCB Suppliers?
Rigid PCBs are a popular alternative to flexible PCBs, particularly for applications where durability and stability are paramount. The primary advantage of rigid PCBs is their lower cost and ease of manufacturing, making them ideal for high-volume production runs. They are well-suited for consumer electronics and industrial applications where the components will not experience significant movement. However, rigid PCBs lack the flexibility that can be critical in compact and dynamic environments, limiting their use in wearable technology or applications that require bending.
How Do PCB Assemblies with Traditional Materials Compare?
PCB assemblies utilizing traditional materials, such as FR-4, provide a cost-effective solution for many applications. They can be manufactured at scale and are generally easier to implement with existing tools and processes. The best use case for these assemblies is in high-volume production where cost sensitivity is a major consideration. However, the performance can vary based on the materials used, and they may not offer the same design flexibility as flexible PCBs. Additionally, traditional materials can be heavier and bulkier, which might be a drawback for applications requiring lightweight solutions.
Conclusion: How to Choose the Right Solution for Your Needs?
When deciding between a flexible PCB supplier and alternative solutions, B2B buyers should assess their specific application requirements, including performance needs, budget constraints, and implementation capabilities. Flexible PCBs are ideal for innovative designs requiring compactness and adaptability, while rigid PCBs and traditional PCB assemblies may be more suitable for cost-sensitive projects or environments where durability is essential. By carefully considering these factors, international buyers can make informed decisions that align with their product development goals.
Essential Technical Properties and Trade Terminology for flexible pcb supplier
What Are the Key Technical Properties of Flexible PCBs for B2B Buyers?
When sourcing flexible printed circuit boards (PCBs), understanding the essential technical properties is crucial for making informed purchasing decisions. Here are several critical specifications to consider:
-
Material Grade
The material grade of flexible PCBs usually refers to the type of substrate used, such as polyimide (PI) or polyester (PET). Polyimide is preferred for high-temperature applications due to its excellent thermal stability and dielectric properties. For B2B buyers, selecting the right material grade ensures compatibility with the intended application, reduces failure rates, and enhances overall product reliability. -
Tolerance
Tolerance in flexible PCBs indicates the allowable deviation in dimensions, such as the thickness of the substrate or the width of traces. Typically expressed in millimeters or micrometers, tighter tolerances are essential for high-density applications where space is limited. For businesses, understanding tolerance requirements helps in assessing manufacturing capabilities and ensuring that the final product meets specific design criteria. -
Copper Weight
This specification refers to the thickness of copper used in the PCB, typically measured in ounces per square foot. Higher copper weights allow for better current-carrying capacity and heat dissipation, which is particularly important in power applications. Buyers should evaluate copper weight in relation to the operational demands of their products to avoid overheating and ensure longevity. -
Impedance Control
Impedance control is vital for applications involving high-frequency signals. It ensures that the signal integrity remains intact over the PCB’s length, preventing reflections and losses. B2B buyers should discuss impedance requirements with suppliers to ensure that the design aligns with the performance expectations of their electronic devices. -
Bend Radius
The bend radius specifies the minimum radius at which a flexible PCB can be bent without incurring damage. This property is critical for applications requiring frequent movement or tight spaces. Understanding the bend radius helps buyers select PCBs that can withstand the physical demands of their applications, thus reducing the risk of mechanical failure.
What Trade Terminology Should B2B Buyers Know When Sourcing Flexible PCBs?
Familiarity with industry jargon can significantly improve communication and negotiation with flexible PCB suppliers. Here are some common terms:
-
OEM (Original Equipment Manufacturer)
OEMs are companies that produce components or products that are used in another company’s end product. For B2B buyers, partnering with an OEM can provide access to specialized PCB designs tailored to specific applications, ensuring compatibility and performance. -
MOQ (Minimum Order Quantity)
MOQ refers to the minimum number of units a supplier requires for an order. Understanding the MOQ is essential for buyers, particularly those operating on tight budgets or with limited production runs. It allows for better inventory management and cost control. -
RFQ (Request for Quotation)
An RFQ is a formal document requesting suppliers to provide price quotes for specific quantities of flexible PCBs. It is a critical step in the procurement process, enabling buyers to compare prices and terms effectively, ensuring they receive competitive offers. -
Incoterms (International Commercial Terms)
Incoterms define the responsibilities of buyers and sellers in international transactions, including shipping, insurance, and tariffs. Familiarity with Incoterms helps B2B buyers understand their obligations and manage risks associated with international shipping, especially when sourcing from regions like Africa or South America. -
Lead Time
Lead time is the period from placing an order to receiving the finished product. Understanding lead times is vital for B2B buyers to plan their production schedules and inventory needs effectively. This is particularly important for industries with tight timelines or those reliant on just-in-time manufacturing.
By grasping these technical properties and trade terms, international B2B buyers can enhance their sourcing strategies for flexible PCBs, ensuring they select the right components for their unique applications while fostering effective supplier relationships.
Navigating Market Dynamics and Sourcing Trends in the flexible pcb supplier Sector
What Are the Key Trends Shaping the Flexible PCB Supplier Market?
The flexible printed circuit board (FPCB) market is experiencing significant growth driven by advancements in technology and increasing demand across various sectors, including consumer electronics, automotive, and healthcare. As international B2B buyers, particularly from Africa, South America, the Middle East, and Europe, look to source flexible PCBs, understanding the market dynamics is crucial. One of the key trends is the rising demand for miniaturization in electronic devices. This trend pushes manufacturers to adopt flexible PCBs, which allow for compact designs without compromising functionality.
Another critical factor influencing the market is the shift towards automation and the Internet of Things (IoT). The integration of smart technologies in everyday devices is increasing the complexity of PCB designs, prompting suppliers to innovate continuously. Moreover, suppliers are increasingly focusing on advanced materials that offer better performance and reliability, such as polyimide and liquid crystal polymer (LCP).
Pricing strategies are also evolving, as global supply chains face disruptions and fluctuations in raw material costs. Buyers must consider regional sourcing options to mitigate risks associated with long lead times and geopolitical issues. For instance, suppliers in Turkey and Kenya are emerging as competitive alternatives, providing quality products at attractive price points.
How Important Is Sustainability and Ethical Sourcing for B2B Buyers in the Flexible PCB Sector?
Sustainability and ethical sourcing are becoming paramount in the flexible PCB supplier sector. Environmental concerns are driving companies to prioritize sustainable practices, particularly as consumers demand more transparency regarding product origins and manufacturing processes. For B2B buyers, aligning with suppliers that emphasize eco-friendly materials and processes can enhance brand reputation and customer loyalty.
One significant aspect is the use of ‘green’ certifications and materials. Buyers should seek suppliers that adhere to standards such as RoHS (Restriction of Hazardous Substances) and ISO 14001, which demonstrate commitment to reducing environmental impact. Additionally, the incorporation of recyclable materials in PCB manufacturing not only minimizes waste but can also lead to cost savings in the long run.
Furthermore, ethical supply chains are crucial for mitigating risks associated with labor practices and sourcing conflicts. Buyers should assess suppliers based on their adherence to ethical labor standards and their impact on local communities. By prioritizing ethical sourcing, companies can contribute to sustainable development while ensuring compliance with international regulations.
What Is the Historical Context of Flexible PCB Development for B2B Buyers?
The evolution of flexible printed circuit boards dates back to the 1960s when they were primarily used in military applications due to their lightweight and adaptable nature. Over the decades, technological advancements and the growing need for compact electronic devices led to broader adoption across various industries. By the 1990s, flexible PCBs began making their way into consumer electronics, paving the way for innovations in smartphones, wearables, and automotive systems.
Today, as the global demand for electronic devices continues to soar, flexible PCBs have become essential components in modern electronics. This historical context is vital for B2B buyers as it highlights the adaptability and versatility of flexible PCBs, underscoring their importance in future technological advancements. Understanding this evolution allows buyers to make informed decisions when selecting suppliers who are not only innovative but also have a proven track record in the industry.
Frequently Asked Questions (FAQs) for B2B Buyers of flexible pcb supplier
-
How do I choose the right flexible PCB supplier for my business needs?
Selecting the right flexible PCB supplier involves evaluating several key factors: quality standards, production capabilities, and customer reviews. Look for suppliers with ISO certifications and a proven track record in delivering high-quality products. Additionally, consider their experience in your specific industry, as this can impact their understanding of your unique requirements. Request samples and conduct site visits if possible to gauge their operational efficiency and quality control processes. -
What are the typical minimum order quantities (MOQs) for flexible PCBs?
Minimum order quantities for flexible PCBs can vary widely based on the supplier and the complexity of the design. Some suppliers may have MOQs as low as 50 units for simpler designs, while others might require 500 or more for intricate configurations. It’s essential to discuss your specific needs with potential suppliers and negotiate MOQs that align with your production goals. Be mindful that lower MOQs may come with higher per-unit costs. -
What customization options are available when sourcing flexible PCBs?
Most flexible PCB suppliers offer a range of customization options, including size, layer count, and material types. You can also customize features like circuit design, surface finish, and solder mask colors. When discussing your project, provide detailed specifications and, if possible, design files. This clarity helps suppliers understand your requirements and deliver a product that meets your expectations. -
What payment terms should I expect when working with international suppliers?
Payment terms can vary significantly among international suppliers, but common practices include advance payments, net 30, or net 60 terms. For first-time orders, suppliers may request a partial upfront payment (30-50%) with the balance due upon delivery. Always clarify payment methods (e.g., wire transfer, credit card) and any additional fees that may apply. It’s advisable to establish a clear payment agreement in your contract to avoid misunderstandings. -
How can I ensure quality assurance when sourcing flexible PCBs?
To ensure quality assurance, work with suppliers who have robust quality control processes in place. Request information about their inspection methods, testing protocols, and certifications (e.g., IPC standards). Additionally, consider implementing a third-party inspection service to verify product quality before shipment. Regular communication with your supplier throughout the production process also helps address potential issues early. -
What logistics considerations should I keep in mind when importing flexible PCBs?
When importing flexible PCBs, consider shipping methods, lead times, and customs regulations. Air freight is faster but more expensive, while sea freight is cost-effective for larger shipments. Ensure your supplier provides proper documentation for customs clearance. Familiarize yourself with import duties and taxes in your country to avoid unexpected costs. Collaborating with a reliable logistics partner can streamline the shipping process and mitigate delays. -
How do I handle communication with suppliers across different time zones?
Effective communication with suppliers in different time zones can be achieved through a combination of scheduled meetings and asynchronous communication. Use project management tools or platforms that allow for shared updates. Establish a clear communication schedule that accommodates both parties, and utilize email for detailed discussions. Setting expectations around response times can also help maintain a smooth workflow. -
What are the common challenges faced when sourcing flexible PCBs internationally?
International sourcing of flexible PCBs can present challenges such as language barriers, varying quality standards, and cultural differences in business practices. To mitigate these risks, conduct thorough research on potential suppliers and establish clear expectations upfront. Building strong relationships with suppliers through regular communication can foster trust and help navigate any potential misunderstandings. Additionally, consider working with local intermediaries who understand both your market and the supplier’s operations.
Important Disclaimer & Terms of Use
⚠️ Important Disclaimer
The information provided in this guide, including content regarding manufacturers, technical specifications, and market analysis, is for informational and educational purposes only. It does not constitute professional procurement advice, financial advice, or legal advice.
While we have made every effort to ensure the accuracy and timeliness of the information, we are not responsible for any errors, omissions, or outdated information. Market conditions, company details, and technical standards are subject to change.
B2B buyers must conduct their own independent and thorough due diligence before making any purchasing decisions. This includes contacting suppliers directly, verifying certifications, requesting samples, and seeking professional consultation. The risk of relying on any information in this guide is borne solely by the reader.
Strategic Sourcing Conclusion and Outlook for flexible pcb supplier
In the evolving landscape of flexible printed circuit boards (PCBs), strategic sourcing emerges as a critical component for international B2B buyers, particularly in regions like Africa, South America, the Middle East, and Europe. By prioritizing suppliers who offer not only quality but also innovation and reliability, businesses can enhance their competitive edge. Key takeaways include the importance of establishing strong partnerships with manufacturers that align with your operational needs and values, as well as the necessity of understanding regional market dynamics that influence sourcing strategies.
How can international buyers leverage strategic sourcing for flexible PCBs? By conducting thorough market research and fostering relationships with diverse suppliers, companies can mitigate risks associated with supply chain disruptions. Additionally, investing in local suppliers can yield benefits such as reduced lead times and lower transportation costs, which are particularly advantageous for businesses operating in emerging markets.
Looking ahead, the demand for flexible PCBs is set to grow, driven by advancements in technology and an increasing reliance on electronic devices. International B2B buyers are encouraged to actively engage with suppliers who are committed to sustainable practices and innovation. By doing so, you position your business not only for immediate success but also for long-term growth in a competitive marketplace. Take the next step in your sourcing strategy today and explore the potential of flexible PCB suppliers to meet your future needs.