Discover Top Benefits of Choosing a Laser Manufacturer (2025)
Introduction: Navigating the Global Market for laser manufacturer
In today’s competitive landscape, sourcing reliable laser manufacturers can pose significant challenges for B2B buyers, particularly in regions such as Africa, South America, the Middle East, and Europe. The demand for advanced laser technology spans various industries, from medical devices to automotive applications, making it crucial for businesses to navigate this complex market effectively. This guide provides a comprehensive overview of the laser manufacturing sector, covering essential aspects like types of lasers, their applications, and critical factors to consider when vetting suppliers.
Understanding the intricacies of laser technology and its diverse applications is vital for making informed purchasing decisions. This guide empowers international B2B buyers by offering insights into the latest innovations in laser technology, cost considerations, and best practices for supplier evaluation. Buyers will learn how to assess product quality, reliability, and compliance with regional standards, ultimately leading to more successful partnerships.
By delving into the global laser market, this resource aims to equip buyers with the knowledge they need to not only find the right manufacturers but also to ensure that their investments yield maximum returns. Whether you’re in the UK, Saudi Arabia, or beyond, our guide is tailored to support you in navigating the complexities of laser sourcing, ensuring that you make strategic decisions that align with your business goals.
Understanding laser manufacturer Types and Variations
Type Name | Key Distinguishing Features | Primary B2B Applications | Brief Pros & Cons for Buyers |
---|---|---|---|
CO2 Lasers | High power, versatile, suitable for cutting and engraving | Wood, acrylic, textiles, and metal processing | Pros: Excellent for thick materials; Cons: Requires regular maintenance. |
Fiber Lasers | Compact, efficient, high beam quality | Metal cutting, welding, and marking | Pros: Low operational costs; Cons: More expensive upfront. |
Solid-State Lasers | High energy output, longer lifespan | Medical, industrial, and military applications | Pros: Robust and reliable; Cons: Limited to specific materials. |
Diode Lasers | Small size, low cost, easy integration | Printing, barcode scanning, and medical devices | Pros: Cost-effective; Cons: Lower power than other types. |
Nd:YAG Lasers | Versatile, can operate in continuous or pulsed modes | Materials processing, medical applications | Pros: High peak power; Cons: Requires complex cooling systems. |
What Are the Key Characteristics of CO2 Lasers and Their B2B Suitability?
CO2 lasers are renowned for their high power output and versatility, making them ideal for applications such as cutting, engraving, and marking a variety of materials, including wood, acrylic, and certain metals. They are particularly suitable for industries requiring precision in cutting thick materials. Buyers should consider the ongoing maintenance needs, as CO2 lasers may require more frequent upkeep compared to other types, impacting long-term operational costs.
How Do Fiber Lasers Stand Out in B2B Applications?
Fiber lasers are distinguished by their compact design and superior beam quality. They are highly efficient and are primarily used in metal cutting, welding, and marking applications. The low operational costs associated with fiber lasers make them attractive for businesses looking to optimize their production processes. However, the initial investment can be higher, which may be a consideration for budget-conscious buyers.
What Are the Advantages of Solid-State Lasers for B2B Buyers?
Solid-state lasers offer high energy output and longer lifespans, making them suitable for a wide range of applications, including medical, industrial, and military fields. Their robustness and reliability are significant advantages for businesses that require consistent performance. However, they may be limited in terms of the materials they can process effectively, which buyers should evaluate based on their specific needs.
Why Choose Diode Lasers for Cost-Effective Solutions?
Diode lasers are compact, cost-effective, and easy to integrate into existing systems, making them popular in applications like printing, barcode scanning, and medical devices. Their affordability is a major selling point for many businesses, particularly startups or small enterprises. However, their lower power output compared to other laser types may limit their use in more demanding industrial applications.
What Makes Nd:YAG Lasers Versatile in Different Industries?
Nd:YAG lasers are known for their versatility, capable of operating in both continuous and pulsed modes, which makes them suitable for materials processing and medical applications. Their high peak power is beneficial for cutting and welding, providing precision and efficiency. However, the complexity of their cooling systems can lead to higher operational costs, a factor that buyers must consider when evaluating their investment.
Related Video: Laser MicroJet – Most Advanced Technology for High Precision Cutting ( Explained in Details )
Key Industrial Applications of laser manufacturer
Industry/Sector | Specific Application of laser manufacturer | Value/Benefit for the Business | Key Sourcing Considerations for this Application |
---|---|---|---|
Manufacturing | Laser Cutting and Engraving | Enhanced precision and reduced material waste | Look for high-speed, high-accuracy systems; service support is crucial. |
Healthcare | Laser Surgery and Medical Devices | Minimally invasive procedures leading to faster recovery | Ensure compliance with international medical standards and certifications. |
Automotive | Laser Welding and Joining Techniques | Improved structural integrity and reduced production time | Consider the compatibility with existing production lines and training for operators. |
Telecommunications | Fiber Laser Technology for Data Transmission | Increased bandwidth and data transfer efficiency | Assess the scalability and integration with current infrastructure. |
Aerospace | Laser Additive Manufacturing (3D Printing) | Lightweight components and complex geometries | Verify material certifications and ensure adherence to aerospace regulations. |
How is Laser Cutting and Engraving Used in Manufacturing?
In the manufacturing sector, laser cutting and engraving are pivotal for producing intricate designs and components with high precision. Lasers can cut through various materials, including metals, plastics, and wood, allowing for customization and rapid prototyping. This technology reduces material waste and enhances production efficiency, making it a cost-effective solution. International buyers, particularly from Africa and South America, should consider the speed and accuracy of the laser systems, as well as the availability of local support and maintenance services to minimize downtime.
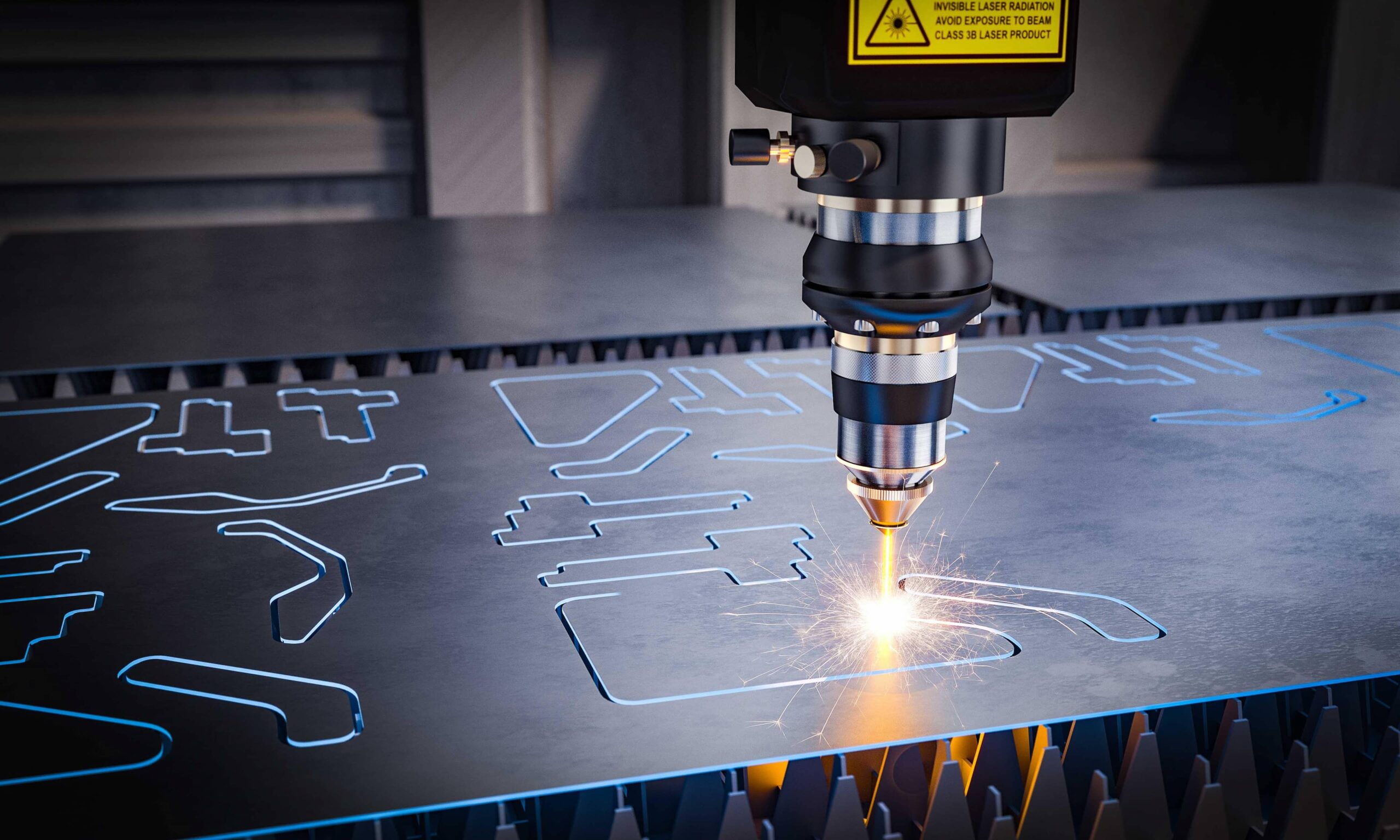
A stock image related to laser manufacturer.
What Role Does Laser Technology Play in Healthcare?
Laser technology in healthcare has revolutionized surgical procedures, allowing for minimally invasive techniques that reduce recovery times and improve patient outcomes. Applications range from laser eye surgery to the use of lasers in cosmetic procedures and diagnostics. For B2B buyers in the healthcare sector, especially in the Middle East and Europe, sourcing lasers requires ensuring compliance with stringent medical standards and certifications. Additionally, understanding the technological advancements and training requirements for medical personnel is crucial for successful implementation.
How is Laser Welding Transforming the Automotive Industry?
In the automotive industry, laser welding is increasingly used for joining metal components due to its ability to produce strong, clean welds with minimal heat distortion. This method enhances the structural integrity of vehicles and reduces production time compared to traditional welding techniques. For international B2B buyers, particularly in Europe and the Middle East, it is essential to evaluate the compatibility of laser welding equipment with existing assembly lines and consider the necessary operator training to maximize efficiency.
What Advantages Does Fiber Laser Technology Offer for Telecommunications?
Fiber laser technology is instrumental in telecommunications, facilitating high-speed data transmission with increased bandwidth capabilities. This technology is vital for supporting the growing demand for internet connectivity and data services worldwide. Buyers from South America and Africa should focus on the scalability of laser systems and their integration with existing networks to ensure long-term viability. Additionally, evaluating the supplier’s reputation for service and support can significantly impact operational success.
How is Laser Additive Manufacturing Benefiting the Aerospace Sector?
Laser additive manufacturing, or 3D printing, is a game-changer in the aerospace industry, enabling the production of lightweight components with complex geometries that traditional methods cannot achieve. This technology significantly reduces material waste and allows for rapid prototyping of parts. International B2B buyers in this sector must verify that the materials used meet aerospace standards and regulations, while also considering the supplier’s experience and capabilities in delivering specialized solutions.
Related Video: New method of manufacturing using powder bed: Additive Manufacturing with Selective Laser Melting
3 Common User Pain Points for ‘laser manufacturer’ & Their Solutions
Scenario 1: High Initial Investment Costs for Laser Equipment
The Problem: One of the most significant challenges faced by B2B buyers in Africa, South America, the Middle East, and Europe when purchasing laser equipment is the high initial investment cost. Many businesses, particularly small to medium enterprises (SMEs), struggle to justify the expense of advanced laser systems, especially when budgets are tight and operational costs are high. This can lead to hesitation in upgrading or acquiring necessary technology, ultimately affecting productivity and competitiveness.
The Solution: To navigate this challenge, buyers should consider financing options or leasing agreements offered by laser manufacturers. Many companies provide flexible payment plans that allow businesses to spread the cost over time, making it easier to manage cash flow. Additionally, conducting thorough market research to compare prices and features across various suppliers can uncover more affordable solutions. Buyers should also evaluate the long-term ROI of investing in laser technology, as improved efficiency and precision can lead to significant cost savings and higher output in the long run. Engaging with manufacturers for a demonstration or trial period can help justify the expense by showcasing the tangible benefits of the technology.
Scenario 2: Complexity in Selecting the Right Laser Technology
The Problem: With the myriad of laser technologies available—ranging from fiber lasers to CO2 lasers—B2B buyers often find it overwhelming to select the right type for their specific applications. This complexity can lead to poor purchasing decisions, resulting in wasted resources and inadequate performance for their intended tasks. Buyers from various industries, such as manufacturing or healthcare, may not have the technical expertise required to make an informed choice.
The Solution: To alleviate this pain point, buyers should engage in a consultative approach with laser manufacturers. Requesting a needs assessment can help identify the specific requirements of your operations, such as material types, thicknesses, and desired outcomes. Manufacturers often have technical experts who can provide tailored recommendations based on industry standards and best practices. Additionally, participating in workshops or industry seminars focused on laser applications can enhance understanding and facilitate better decision-making. Buyers should also consider suppliers that offer comprehensive support, including training and after-sales service, to ensure the selected technology integrates seamlessly into their operations.
Scenario 3: Maintenance and Downtime Challenges
The Problem: After investing in laser technology, many businesses face the challenge of ongoing maintenance and potential downtime, which can significantly disrupt operations and lead to lost revenue. In regions with limited access to expert technicians or spare parts, the risk of prolonged equipment failure increases, causing frustration and financial strain for B2B buyers.
The Solution: To combat maintenance issues, buyers should prioritize sourcing laser manufacturers that provide robust after-sales support, including maintenance contracts and remote monitoring services. Establishing a preventive maintenance schedule can help identify potential issues before they escalate into costly repairs. Moreover, investing in training for in-house personnel can empower teams to perform basic maintenance tasks and troubleshoot minor issues, reducing reliance on external technicians. Buyers should also consider forming partnerships with local service providers or technicians who specialize in laser technology to ensure rapid response times when repairs are needed. By taking proactive steps towards maintenance, businesses can minimize downtime and keep their operations running smoothly.
Strategic Material Selection Guide for laser manufacturer
What Are the Key Materials Used in Laser Manufacturing?
In the laser manufacturing industry, the selection of materials is crucial for ensuring optimal performance and durability. Below, we analyze four common materials used in laser manufacturing, focusing on their properties, advantages, limitations, and specific considerations for international B2B buyers.
How Do Metals Contribute to Laser Performance?
Stainless Steel
Key Properties: Stainless steel is known for its excellent corrosion resistance, high tensile strength, and ability to withstand high temperatures. It typically has a temperature rating of up to 800°C and can endure significant pressure.
Pros & Cons: The durability of stainless steel makes it suitable for various applications, including structural components and housings. However, its higher cost compared to other metals can be a drawback for budget-conscious buyers. Manufacturing complexity can also increase due to the need for specialized welding techniques.
Impact on Application: Stainless steel is compatible with a range of media, making it ideal for laser systems used in harsh environments, such as those found in the oil and gas industry.
Considerations for International Buyers: Buyers from regions like Europe and the Middle East should ensure compliance with relevant standards such as ASTM A240 or EN 10088. The availability of stainless steel may vary by region, impacting lead times and costs.
What Role Does Glass Play in Laser Systems?
Optical Glass
Key Properties: Optical glass is characterized by its high transparency to specific wavelengths, low thermal expansion, and excellent optical clarity. It can handle temperature fluctuations and has a low coefficient of thermal expansion.
Pros & Cons: The primary advantage of optical glass is its ability to transmit laser light efficiently, making it essential for laser lenses and mirrors. However, it can be more fragile than metals, leading to concerns about durability and potential breakage during manufacturing and transportation.
Impact on Application: Optical glass is crucial for applications requiring precision, such as medical lasers and high-precision cutting systems. Its compatibility with various laser types enhances performance.
Considerations for International Buyers: Buyers should be aware of optical glass standards such as ISO 10110, which governs optical elements. Shipping and handling practices must also be considered to prevent damage during transport.
How Do Polymers Enhance Laser Applications?
Polycarbonate
Key Properties: Polycarbonate is a lightweight, impact-resistant polymer that can withstand temperatures up to 120°C. It offers good optical clarity and is often used in protective covers and lenses.
Pros & Cons: The flexibility and lower cost of polycarbonate make it an attractive option for many applications. However, it has a lower thermal resistance compared to glass and can be prone to scratching, which may affect long-term performance.
Impact on Application: Polycarbonate is often used in consumer laser products due to its lightweight nature and ease of manufacturing. It is suitable for applications where impact resistance is critical, such as in handheld laser devices.
Considerations for International Buyers: Compliance with standards like ASTM D635 is essential for ensuring quality. Buyers in Africa and South America should consider local availability and potential import tariffs that may affect overall costs.
What Advantages Do Ceramics Offer in Laser Manufacturing?
Ceramic Materials
Key Properties: Ceramics are known for their high-temperature resistance, hardness, and low thermal expansion. They can withstand temperatures exceeding 1,000°C and are often used in high-performance applications.
Pros & Cons: The durability and thermal stability of ceramics make them ideal for laser applications requiring high precision. However, they can be brittle and challenging to machine, leading to higher manufacturing costs.
Impact on Application: Ceramics are commonly used in laser components that need to withstand extreme conditions, such as aerospace and defense applications.
Considerations for International Buyers: Buyers should ensure that ceramic materials meet specific standards such as ISO 13006. Availability can vary significantly by region, and sourcing from local suppliers may mitigate lead time issues.
Summary Table of Material Selection for Laser Manufacturing
Material | Typical Use Case for Laser Manufacturer | Key Advantage | Key Disadvantage/Limitation | Relative Cost (Low/Med/High) |
---|---|---|---|---|
Stainless Steel | Structural components and housings | Excellent corrosion resistance | Higher cost and manufacturing complexity | High |
Optical Glass | Lenses and mirrors for precision lasers | High transparency and optical clarity | Fragility and potential for breakage | Medium |
Polycarbonate | Protective covers and lenses | Lightweight and impact-resistant | Lower thermal resistance and scratch-prone | Low |
Ceramic Materials | High-performance laser components | High-temperature resistance and durability | Brittle and challenging to machine | High |
This strategic material selection guide provides international B2B buyers with insights into the most common materials used in laser manufacturing, helping them make informed decisions based on application requirements and regional considerations.
In-depth Look: Manufacturing Processes and Quality Assurance for laser manufacturer
What Are the Main Stages of the Manufacturing Process for Laser Equipment?
The manufacturing process of laser equipment involves several critical stages, each contributing to the overall quality and performance of the final product. The primary stages include material preparation, forming, assembly, and finishing.
-
Material Preparation: This initial stage involves selecting the appropriate materials, such as optical components, semiconductor materials, and housing materials. Quality assurance begins here, as the integrity of these materials directly affects the performance of the laser. Suppliers should provide certificates of authenticity and material safety data sheets (MSDS) to validate the quality and specifications of the materials used.
-
Forming: This stage encompasses various techniques like cutting, machining, and molding to shape the components. CNC (Computer Numerical Control) machining is widely used for its precision and repeatability, ensuring that all parts meet the required specifications. During this phase, it is essential to monitor the processes closely to avoid defects that could compromise the laser’s functionality.
-
Assembly: In this phase, the formed components are assembled into the final laser product. This may involve aligning optical components, integrating electronic circuits, and ensuring proper thermal management. Assembly quality checks should be performed to guarantee that all parts fit correctly and function as intended.
-
Finishing: The final stage involves surface treatment, coating, and any necessary calibration of the laser system. Finishing processes enhance the laser’s performance and durability. Techniques such as anti-reflective coating or protective surface treatments are common.
How Is Quality Assurance Integrated into the Manufacturing Process?
Quality assurance (QA) is critical throughout the manufacturing process to ensure that the laser products meet international and industry-specific standards. Key components of QA include adherence to standards like ISO 9001 and specific certifications such as CE for the European market and API for the oil and gas sector.
-
International Standards: ISO 9001 is a widely recognized quality management standard that outlines requirements for a quality management system (QMS). Compliance with ISO 9001 demonstrates a commitment to quality and continuous improvement, which is vital for B2B buyers looking for reliable suppliers.
-
Industry-Specific Certifications: For laser manufacturers, certifications like CE mark indicate compliance with European health, safety, and environmental protection standards. In regions like the Middle East, obtaining local certifications may also be necessary to meet regulatory requirements.
-
Quality Control Checkpoints: Implementing checkpoints throughout the manufacturing process is essential for maintaining quality. These checkpoints include:
– Incoming Quality Control (IQC): Assessing materials upon arrival to ensure they meet specified criteria.
– In-Process Quality Control (IPQC): Monitoring the production process to catch defects early.
– Final Quality Control (FQC): Conducting thorough inspections and testing of the finished product before it is shipped.
What Testing Methods Are Commonly Used for Laser Products?
Testing methods are crucial in verifying the performance and safety of laser products. Common testing methods include:
-
Optical Testing: This involves measuring beam quality, power output, and wavelength stability. These parameters are critical for ensuring that the laser performs as expected in its intended application.
-
Electrical Testing: Electrical components must be tested for functionality and safety. This includes checking circuit integrity, power consumption, and thermal performance.
-
Durability Testing: Manufacturers often subject laser systems to stress tests to evaluate their performance under extreme conditions, such as temperature fluctuations and humidity variations.
-
Compliance Testing: For lasers intended for specific industries, compliance testing ensures adherence to safety and operational standards set by regulatory bodies.
How Can B2B Buyers Verify Supplier Quality Control?
B2B buyers must take proactive steps to verify the quality control measures of their suppliers. Here are some actionable strategies:
-
Supplier Audits: Conducting on-site audits of potential suppliers can provide insights into their manufacturing processes and quality control systems. During the audit, check for compliance with international standards and industry-specific certifications.
-
Quality Control Reports: Requesting access to quality control reports, including inspection and testing results, can help buyers understand the reliability of the manufacturing processes.
-
Third-Party Inspections: Engaging third-party inspection services can offer an unbiased evaluation of the supplier’s quality control practices. This can be particularly beneficial when dealing with suppliers in different regions, as local inspectors may have a better understanding of regional compliance requirements.
What Are the QC and Certification Nuances for International B2B Buyers?
For international B2B buyers, particularly those from Africa, South America, the Middle East, and Europe, understanding the nuances of quality control and certification is essential for making informed purchasing decisions.
-
Regional Compliance Differences: Different regions may have varying compliance requirements. For example, while the CE marking is crucial for European markets, buyers in the Middle East might prioritize local certifications. Understanding these differences can prevent compliance issues during importation.
-
Documentation and Traceability: Ensure that suppliers maintain thorough documentation of their quality control processes and certification statuses. This traceability is vital for buyers who may need to present compliance documentation during regulatory audits.
-
Cultural Considerations: Be aware of cultural differences that may influence business practices and expectations regarding quality assurance. Building strong relationships with suppliers can facilitate better communication and understanding of quality expectations.
Conclusion
In summary, the manufacturing processes and quality assurance protocols for laser manufacturers are complex yet essential for delivering high-quality products. By understanding the stages of manufacturing, the integration of quality assurance, testing methods, and the nuances of international standards, B2B buyers can make informed decisions and establish reliable partnerships with laser manufacturers. This knowledge will not only enhance operational efficiency but also contribute to long-term success in the competitive global market.
Practical Sourcing Guide: A Step-by-Step Checklist for ‘laser manufacturer’
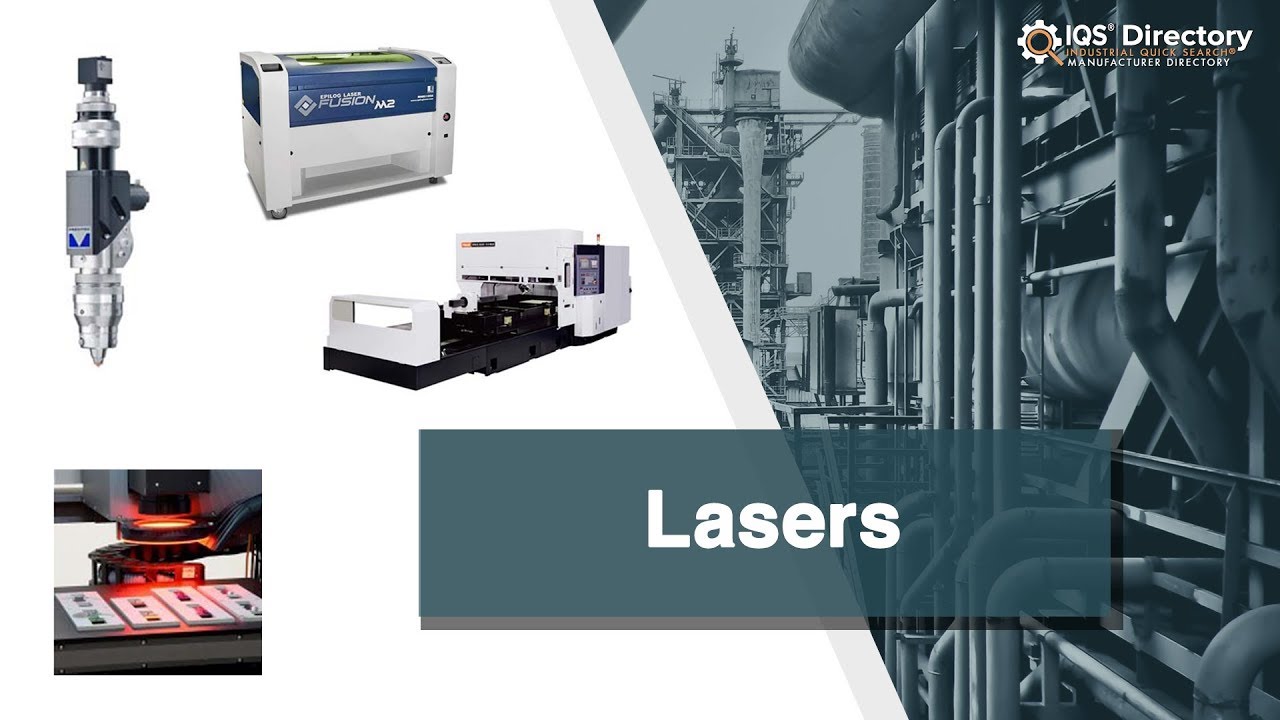
A stock image related to laser manufacturer.
In the competitive landscape of laser manufacturing, selecting the right supplier is crucial for ensuring product quality and operational efficiency. This step-by-step checklist aims to guide international B2B buyers, especially those from Africa, South America, the Middle East, and Europe, in making informed sourcing decisions.
Step 1: Define Your Technical Specifications
Understanding your specific needs is the foundation of a successful procurement process. Clearly outline the type of laser technology required (e.g., fiber lasers, CO2 lasers) and the intended application (cutting, engraving, medical use). This clarity will help you communicate effectively with potential suppliers and ensure they can meet your requirements.
- Consider power output: Specify the wattage needed for your applications.
- Identify material compatibility: Make sure the laser can work with the materials you intend to process.
Step 2: Conduct Market Research
Before engaging suppliers, it’s essential to familiarize yourself with the market landscape. Research various manufacturers, their product offerings, and their reputation within the industry. This knowledge will empower you to make comparisons and identify potential suppliers who align with your needs.
- Utilize online resources: Explore industry reports and reviews to gauge market trends.
- Network within industry circles: Engage with peers or attend trade shows to gather insights.
Step 3: Evaluate Potential Suppliers
Vetting suppliers thoroughly is vital to avoid costly mistakes. Request company profiles, case studies, and references from clients in similar industries or regions. A reputable supplier will have a proven track record and the capacity to deliver on their promises.
- Check for certifications: Ensure suppliers comply with international standards like ISO 9001.
- Assess customer support: Evaluate the responsiveness and expertise of their customer service.
Step 4: Request Samples or Prototypes
Before finalizing any orders, request samples or prototypes of the laser systems. This step allows you to assess the quality, performance, and suitability of the products for your specific applications.
- Evaluate precision and speed: Test the laser’s ability to meet your production requirements.
- Inspect build quality: Look for durability and the quality of components used.
Step 5: Discuss Pricing and Terms
Once you have shortlisted potential suppliers, initiate discussions on pricing, payment terms, and delivery schedules. Understanding the total cost of ownership, including maintenance and operational costs, is essential to avoid unexpected expenses.
- Negotiate bulk discounts: If you anticipate high-volume purchases, inquire about pricing adjustments.
- Clarify warranty and service agreements: Ensure you understand what support is available post-purchase.
Step 6: Verify Logistics and Delivery Capabilities
Assess the supplier’s logistics capabilities, particularly if you are sourcing from international manufacturers. Timely delivery is critical to maintaining your production schedules.
- Check shipping options: Understand the costs and timelines for delivery to your location.
- Evaluate customs and import regulations: Be aware of any potential delays or additional costs involved in importing equipment.
Step 7: Finalize Your Decision
After completing your evaluations and discussions, make a well-informed decision based on all gathered information. Ensure that your chosen supplier aligns with your technical requirements, budget, and overall business strategy.
- Document agreements: Keep clear records of all discussions and agreements to avoid misunderstandings.
- Prepare for onboarding: Plan how you will integrate the new equipment into your operations.
By following this checklist, B2B buyers can streamline the sourcing process for laser manufacturing, ensuring they select suppliers that meet their technical and operational needs effectively.
Comprehensive Cost and Pricing Analysis for laser manufacturer Sourcing
What Are the Key Cost Components in Laser Manufacturing?
When sourcing lasers for industrial applications, understanding the cost structure is crucial for making informed purchasing decisions. The primary cost components in laser manufacturing include:
-
Materials: The quality and type of materials used significantly influence costs. High-performance lasers often require specialized materials that can withstand high temperatures or provide better efficiency.
-
Labor: Skilled labor is essential in laser manufacturing, particularly for assembly, calibration, and quality control processes. Labor costs can vary significantly based on geographic location and local wage standards.
-
Manufacturing Overhead: This includes costs related to utilities, facility maintenance, and equipment depreciation. Efficient manufacturing processes can help minimize overhead costs.
-
Tooling: The initial investment in tooling can be substantial, particularly for custom laser designs. This upfront cost should be factored into the overall pricing.
-
Quality Control (QC): Stringent QC measures are essential to ensure that lasers meet performance specifications. These costs can include testing equipment, personnel, and processes that ensure compliance with international standards.
-
Logistics: Shipping costs, including customs duties and tariffs, can add to the final price. The logistics of transporting delicate laser equipment require specialized handling to prevent damage.
-
Margin: Manufacturers typically apply a margin that reflects their business model and market positioning. This margin can vary based on competition and demand.
How Do Price Influencers Impact Laser Sourcing?
Several factors influence the pricing of lasers, which B2B buyers must consider when negotiating:
-
Volume and Minimum Order Quantity (MOQ): Larger orders often lead to discounted pricing. Understanding the manufacturer’s MOQ can help buyers negotiate better deals.
-
Specifications and Customization: Customized lasers tailored to specific applications can incur additional costs. Buyers should clearly define their specifications to avoid unexpected charges.
-
Materials Quality and Certifications: Lasers that meet specific industry certifications (e.g., ISO, CE) may come at a premium. Buyers should assess whether the certifications align with their operational needs.
-
Supplier Factors: Supplier reputation and reliability can influence pricing. Established suppliers with a track record of quality may charge more but can provide better assurance of performance.
-
Incoterms: The terms of delivery (e.g., FOB, CIF) can significantly affect the total cost. Buyers should clarify these terms to understand who bears the risk and costs at various stages of shipping.
What Are Essential Buyer Tips for Cost-Efficient Laser Sourcing?
For international B2B buyers, particularly from regions like Africa, South America, the Middle East, and Europe, the following strategies can enhance cost efficiency:
-
Negotiate Wisely: Always negotiate terms and pricing. Understanding the cost structure can provide leverage during discussions.
-
Consider Total Cost of Ownership (TCO): Evaluate the TCO, which includes not only the purchase price but also operating costs, maintenance, and potential downtime. This holistic view can lead to better long-term decisions.
-
Understand Pricing Nuances: Different regions have varied pricing strategies influenced by local market conditions, currency fluctuations, and economic factors. Buyers should be aware of these nuances to avoid overpaying.
-
Build Relationships with Suppliers: Establishing strong relationships with suppliers can lead to better pricing, access to exclusive products, and improved service levels.
-
Stay Informed: Regularly review market trends and technological advancements in laser manufacturing. This knowledge can empower buyers to make timely and informed purchasing decisions.
Disclaimer on Indicative Prices
Prices for laser manufacturing can vary widely based on the factors discussed above. It is essential for buyers to obtain tailored quotes from manufacturers to understand the specific costs related to their requirements.
Alternatives Analysis: Comparing laser manufacturer With Other Solutions
When considering the procurement of laser manufacturing technology, it is essential to explore various alternative solutions that could meet similar operational needs. By comparing these options, international B2B buyers can make informed decisions that align with their business objectives, budget constraints, and specific application requirements.
Comparison Aspect | Laser Manufacturer | Waterjet Cutting System | CNC Plasma Cutter |
---|---|---|---|
Performance | High precision and speed | Excellent for thick materials | Good for various thicknesses |
Cost | High initial investment | Moderate to high | Lower initial cost |
Ease of Implementation | Requires specialized training | Moderate, but needs skilled operators | Easier setup and operation |
Maintenance | Regular maintenance required | Lower maintenance needs | Moderate maintenance needs |
Best Use Case | Detailed cuts in metals and plastics | Cutting hard materials like stone and metal | General metal fabrication |
What are the Advantages and Disadvantages of Waterjet Cutting Systems?
Waterjet cutting systems utilize high-pressure water streams mixed with abrasives to cut through materials. One of the primary advantages of this technology is its ability to cut a wide variety of materials, including metals, glass, and stone, without thermal distortion. This makes it an excellent choice for intricate designs and sensitive materials. However, the initial investment can be significant, and the operational costs can be higher due to the need for abrasives and water filtration systems. Additionally, the speed of cutting is generally slower than lasers, which may impact productivity for certain applications.
How Does CNC Plasma Cutting Compare to Laser Manufacturing?
CNC plasma cutters use high-velocity ionized gas to cut through conductive materials. They are particularly effective for cutting sheet metal and are known for their speed and lower initial costs compared to laser systems. This technology is ideal for larger, less detailed cuts, making it suitable for industries like automotive and construction. However, plasma cutting produces a rougher edge finish and may not be suitable for applications requiring high precision. Maintenance and operational training are also necessary, but they tend to be less complex than laser systems.
How Can Buyers Choose the Right Solution for Their Needs?
When selecting the right cutting technology, B2B buyers should consider several factors, including the type of materials they work with, the precision required for their applications, and their budget constraints. For organizations that prioritize high precision and detailed cutting in materials like metals and plastics, laser manufacturers may be the best fit despite the higher costs. Conversely, if the focus is on cutting thick materials or if budget constraints are significant, alternatives like waterjet or plasma cutting may provide a more cost-effective solution while still meeting operational requirements.
In conclusion, understanding the unique characteristics of laser manufacturing in relation to alternative solutions such as waterjet cutting systems and CNC plasma cutters is vital for international B2B buyers. By evaluating performance, costs, ease of implementation, and maintenance requirements, businesses can select the most appropriate technology that aligns with their specific operational needs and long-term goals.
Essential Technical Properties and Trade Terminology for laser manufacturer
What Are the Essential Technical Properties for Laser Manufacturers?
When sourcing lasers for industrial applications, understanding the key technical properties is crucial. Here are several important specifications that B2B buyers should consider:
1. Wavelength
The wavelength of a laser determines its color and the type of materials it can effectively cut or engrave. Common wavelengths include 1064 nm for Nd:YAG lasers and 532 nm for frequency-doubled lasers. For buyers, selecting the appropriate wavelength is essential for matching the laser to specific applications, such as materials processing or medical uses.
2. Power Output
Power output, measured in watts, indicates the laser’s capability to perform tasks such as cutting, engraving, or welding. Higher power outputs allow for faster processing speeds and the ability to work with thicker materials. Buyers should assess their operational requirements to choose lasers that deliver sufficient power without compromising efficiency.
3. Pulse Duration
Pulse duration affects the precision and heat impact of the laser on the material being processed. Short pulse durations (in the picosecond or femtosecond range) are ideal for delicate applications, while longer pulses are suitable for bulk material removal. Buyers should consider the nature of their applications to select lasers that minimize thermal damage and maximize precision.
4. Beam Quality
Beam quality is a measure of how well the laser beam can focus. It is quantified using the M² factor, with lower values indicating a higher quality beam. High beam quality translates to better cutting edges and finer engraving details. Buyers should prioritize beam quality to ensure optimal performance in their manufacturing processes.
5. Cooling System
The cooling system is vital for maintaining laser performance and longevity. Options include air-cooled and water-cooled systems. The choice of cooling system can affect operational costs, maintenance requirements, and the laser’s ability to operate continuously. Buyers should evaluate their facility’s capabilities and operational needs when selecting a laser cooling system.
What Are Common Trade Terms Used in the Laser Manufacturing Industry?
Understanding industry jargon can significantly enhance communication and negotiations with suppliers. Here are some common terms B2B buyers should be familiar with:
1. OEM (Original Equipment Manufacturer)
An OEM is a company that produces parts or equipment that may be marketed by another manufacturer. In the laser industry, buyers often work directly with OEMs to procure lasers tailored to their specifications. Understanding the OEM relationship can help buyers ensure they receive high-quality products that meet their exact needs.
2. MOQ (Minimum Order Quantity)
MOQ refers to the smallest quantity of a product that a supplier is willing to sell. This is crucial for buyers to know, as it can impact budgeting and inventory management. Understanding MOQs allows buyers to negotiate better terms, particularly when sourcing lasers for large-scale production.
3. RFQ (Request for Quotation)
An RFQ is a document sent to suppliers requesting pricing and specifications for specific products. In laser procurement, issuing an RFQ can streamline the purchasing process and ensure competitive pricing. Buyers should provide detailed specifications in their RFQ to receive accurate quotes.
4. Incoterms (International Commercial Terms)
Incoterms are standardized international trade terms that define the responsibilities of buyers and sellers in shipping goods. Familiarity with Incoterms helps buyers understand shipping costs, risk management, and delivery timelines when sourcing lasers from international suppliers.
5. Lead Time
Lead time is the amount of time it takes from placing an order to receiving the product. In the laser manufacturing sector, understanding lead times is critical for project planning and inventory management. Buyers should communicate with suppliers to set realistic expectations regarding delivery schedules.
By grasping these essential technical properties and trade terms, B2B buyers can make informed decisions that align with their operational requirements and strategic goals.
Navigating Market Dynamics and Sourcing Trends in the laser manufacturer Sector
What Are the Current Market Dynamics and Key Trends in the Laser Manufacturing Sector?
The laser manufacturing sector is experiencing significant growth driven by advancements in technology and increasing applications across various industries. Key drivers include the rising demand for precision manufacturing, automation in production lines, and the proliferation of laser-based technologies in healthcare, telecommunications, and automotive sectors. For international B2B buyers, particularly in Africa, South America, the Middle East, and Europe, understanding these dynamics is crucial for making informed sourcing decisions.
Emerging technologies such as fiber lasers and solid-state lasers are reshaping the landscape by offering enhanced efficiency and versatility. These innovations not only improve the quality of laser applications but also reduce operational costs, making them appealing to manufacturers. Additionally, the trend towards Industry 4.0 is prompting companies to integrate laser systems with IoT devices, enabling real-time monitoring and predictive maintenance. B2B buyers should prioritize suppliers who offer technologically advanced solutions that align with these trends.
Another notable trend is the globalization of the laser market. As companies expand their operations internationally, sourcing strategies are evolving. B2B buyers should be mindful of regional differences in technology adoption and regulatory environments. For instance, while European markets may prioritize stringent quality standards, buyers in emerging markets may seek cost-effective solutions. Collaborating with suppliers who understand these regional nuances can enhance sourcing efficiency and product quality.
How Is Sustainability and Ethical Sourcing Impacting the Laser Manufacturing Sector?
Sustainability has become a cornerstone of modern manufacturing practices, and the laser sector is no exception. Environmental impact considerations are increasingly influencing sourcing decisions for B2B buyers. Laser manufacturers are adopting eco-friendly practices, such as using energy-efficient lasers and minimizing waste through precision cutting techniques. These measures not only reduce the carbon footprint but also appeal to environmentally conscious clients.
Ethical sourcing is also gaining traction within the industry. Buyers are increasingly scrutinizing supply chains to ensure compliance with environmental and social standards. This shift is driving manufacturers to obtain certifications such as ISO 14001 for environmental management and ISO 26000 for social responsibility. B2B buyers should seek suppliers who demonstrate a commitment to ethical sourcing, as this not only enhances brand reputation but also mitigates risks associated with supply chain disruptions.
Moreover, the use of ‘green’ materials in manufacturing processes is on the rise. Buyers are encouraged to explore options for biodegradable or recyclable materials in laser systems. Suppliers offering such sustainable materials can help B2B buyers meet their own sustainability goals while fostering a competitive edge in the market.
What Is the Brief Evolution and History of Laser Technology in the B2B Context?
The evolution of laser technology dates back to the early 1960s, when the first operational laser was developed. Initially, lasers were primarily used in research and military applications. However, the 1970s marked a significant turning point as industries began to recognize the potential of lasers for precision cutting, welding, and engraving.
In the 1980s and 1990s, advancements in laser technology led to the development of more compact and efficient laser systems, making them accessible to a wider range of industries, including manufacturing and healthcare. Today, lasers are integral to numerous applications, from high-speed manufacturing processes to advanced medical treatments.
As the laser manufacturing sector continues to evolve, understanding its historical context can provide B2B buyers with insights into current trends and future developments. By leveraging this knowledge, buyers can make more strategic sourcing decisions that align with their operational needs and industry standards.
Frequently Asked Questions (FAQs) for B2B Buyers of laser manufacturer
-
How do I choose the right laser manufacturer for my business needs?
Choosing the right laser manufacturer involves evaluating several key factors. Start by defining your specific requirements, such as the type of laser technology (CO2, fiber, etc.), application (cutting, engraving, marking), and production capacity. Research potential manufacturers by reviewing their certifications, client testimonials, and case studies. Engage in direct communication to assess their technical expertise and customer support. Additionally, consider their ability to provide customization options and after-sales service, which can significantly impact your operational efficiency. -
What are the most important features to look for in a laser cutting machine?
When sourcing a laser cutting machine, prioritize features that align with your production goals. Look for power output (measured in watts) that matches the material thickness you intend to cut. Consider the machine’s speed and precision, as well as its compatibility with various materials such as metals, plastics, or wood. Advanced features like automated loading systems, user-friendly software, and maintenance requirements are also crucial for maximizing productivity and minimizing downtime. -
What is the typical lead time for laser equipment manufacturing and delivery?
Lead times for laser equipment can vary significantly based on the manufacturer, complexity of the machine, and customization level required. Generally, standard models may have a lead time of 4 to 12 weeks, while customized solutions could take longer, ranging from 12 to 24 weeks. It’s essential to discuss timelines upfront during negotiations and factor in potential delays due to logistics, especially when importing equipment from overseas. Planning ahead can help mitigate disruptions in your production schedule. -
What are the minimum order quantities (MOQ) for laser machines or parts?
Minimum order quantities (MOQ) can differ based on the manufacturer and the type of equipment or components being ordered. Some manufacturers may allow single-unit purchases for standard machines, while custom configurations may require higher MOQs to justify production costs. Always clarify the MOQ during initial discussions to ensure it aligns with your budget and needs. If your order volume is low, consider forming partnerships with other businesses to meet MOQ requirements collectively. -
What payment terms should I expect when purchasing laser equipment internationally?
Payment terms for international laser equipment purchases often vary between manufacturers. Common arrangements include a deposit (usually 30-50%) upon order confirmation, with the balance due before shipping or upon delivery. Some suppliers may offer financing options or payment through letters of credit, especially for larger orders. Always ensure that payment terms are clearly defined in the contract to avoid misunderstandings and protect your investment. -
How can I ensure quality assurance when sourcing laser equipment?
To ensure quality assurance when sourcing laser equipment, start by choosing manufacturers with ISO certifications and a proven track record in the industry. Request detailed product specifications, performance data, and certification documents. Consider visiting the manufacturer’s facility or requesting a factory audit, if feasible. Additionally, inquire about their quality control processes, including testing and warranty policies, to ensure that the equipment meets your operational standards. -
What are the logistics considerations for importing laser machines to my country?
When importing laser machines, logistics considerations include shipping methods, customs regulations, and potential tariffs. Choose a reliable freight forwarder familiar with the specific regulations of your country to ensure compliance and minimize delays. Consider the total landed cost, which encompasses shipping, taxes, and insurance. It’s also advisable to prepare all necessary documentation, such as import permits and certificates of origin, to facilitate smooth customs clearance. -
How can I customize laser solutions to fit my specific manufacturing processes?
Customizing laser solutions to fit your manufacturing processes begins with a thorough analysis of your operational needs. Engage with manufacturers early in the design phase to discuss specific requirements, such as size, power, and software compatibility. Many manufacturers offer tailored solutions, including specialized optics, automation features, and unique software interfaces. Providing detailed information about your application will help manufacturers propose the most effective customization options to enhance productivity and efficiency.
Important Disclaimer & Terms of Use
⚠️ Important Disclaimer
The information provided in this guide, including content regarding manufacturers, technical specifications, and market analysis, is for informational and educational purposes only. It does not constitute professional procurement advice, financial advice, or legal advice.
While we have made every effort to ensure the accuracy and timeliness of the information, we are not responsible for any errors, omissions, or outdated information. Market conditions, company details, and technical standards are subject to change.
B2B buyers must conduct their own independent and thorough due diligence before making any purchasing decisions. This includes contacting suppliers directly, verifying certifications, requesting samples, and seeking professional consultation. The risk of relying on any information in this guide is borne solely by the reader.
Strategic Sourcing Conclusion and Outlook for laser manufacturer
As international B2B buyers navigate the complex landscape of laser manufacturing, strategic sourcing emerges as a pivotal component for maximizing value and ensuring competitive advantage. Understanding the specific needs of industries in Africa, South America, the Middle East, and Europe allows buyers to effectively align with manufacturers that not only meet quality standards but also offer innovative solutions tailored to regional demands.
Investing time in evaluating suppliers based on their technological capabilities, production efficiencies, and commitment to sustainability will yield significant long-term benefits. Engaging in strategic partnerships can foster collaboration, leading to improved product offerings and enhanced service delivery. Buyers should prioritize manufacturers that demonstrate a clear understanding of market trends and customer requirements.
Looking ahead, the demand for advanced laser technologies is expected to rise, driven by their diverse applications across multiple sectors. This presents an opportune moment for international buyers to reassess their sourcing strategies, ensuring they partner with forward-thinking manufacturers poised to lead in innovation. Embrace the future of laser technology—initiate strategic discussions with potential suppliers today to harness the full potential of this dynamic industry.