Discover Top Benefits of Choosing a Mould Manufacturer (2025)
Introduction: Navigating the Global Market for mould manufacturer
In today’s competitive landscape, sourcing the right mould manufacturer can be a significant challenge for international B2B buyers. With a myriad of options available globally, from the bustling markets of South America to the burgeoning industrial sectors in Africa, it’s essential to navigate this landscape with precision. This guide aims to provide comprehensive insights into the various types of moulds available, their applications across different industries, and effective strategies for supplier vetting.
Understanding the nuances of mould manufacturing is crucial for making informed purchasing decisions that align with your business needs. This includes evaluating cost factors, assessing quality standards, and determining the technological capabilities of potential suppliers. As a buyer from regions like Colombia or South Africa, where local manufacturing might not meet all requirements, knowing how to source moulds that are both cost-effective and high-quality can significantly impact your production processes and overall business success.
This guide is designed to empower you with actionable insights that will streamline your sourcing journey. By leveraging our expertise, you will be equipped to make strategic decisions that enhance your operational efficiency, reduce lead times, and ultimately contribute to your bottom line. Whether you are looking for injection moulds, blow moulds, or custom solutions, our goal is to ensure that you have all the necessary tools to thrive in the global market.
Understanding mould manufacturer Types and Variations
Type Name | Key Distinguishing Features | Primary B2B Applications | Brief Pros & Cons for Buyers |
---|---|---|---|
Injection Moulding | High precision, fast production rates | Automotive, consumer goods, electronics | Pros: High efficiency, excellent surface finish. Cons: Initial tooling costs can be high. |
Blow Moulding | Utilizes air pressure to form hollow parts | Packaging, automotive fuel tanks | Pros: Cost-effective for large volumes. Cons: Limited to hollow shapes. |
Rotational Moulding | Uses a rotating mold for uniform thickness | Toys, large containers, industrial parts | Pros: Ideal for large parts, good material flexibility. Cons: Slower production cycle. |
Compression Moulding | Material is compressed into a heated mold | Automotive parts, rubber products | Pros: Suitable for large parts, lower tooling costs. Cons: Limited to certain materials. |
3D Printing (Additive Moulding) | Layer-by-layer construction for complex shapes | Prototyping, custom parts, small batches | Pros: Flexibility in design, rapid prototyping. Cons: Slower than traditional methods for large volumes. |
What Are the Characteristics and Suitability of Injection Moulding?
Injection moulding is characterized by its ability to produce high-precision parts at rapid speeds. This method is particularly suitable for manufacturing components in industries such as automotive, consumer goods, and electronics, where large quantities of identical parts are required. When purchasing injection moulding services, buyers should consider factors like tooling costs, production rates, and the complexity of the part design. The initial investment in tooling can be significant, but the efficiency and quality of the final product often justify the expense.
How Does Blow Moulding Differ from Other Moulding Types?
Blow moulding is distinct for its use of air pressure to create hollow shapes, making it ideal for products like bottles and automotive fuel tanks. This method is cost-effective for large production runs and is commonly used in packaging applications. When evaluating blow moulding suppliers, buyers should assess the material compatibility and the types of shapes that can be produced. While blow moulding offers economic advantages, it is limited to hollow designs, which may not meet all project requirements.
What Are the Advantages of Rotational Moulding for Large Parts?
Rotational moulding is known for creating parts with uniform thickness and is particularly effective for large items such as toys and industrial containers. The process involves heating a material within a rotating mold, allowing for even distribution. Buyers looking into rotational moulding should consider the material options and the production cycle time, as this method is slower than injection moulding. However, its versatility in producing large, durable parts can be a significant advantage in certain applications.
What Key Considerations Should Buyers Keep in Mind for Compression Moulding?
Compression moulding involves placing material into a heated mold, where it is compressed to form parts. This method is commonly used for automotive components and rubber products. Buyers should weigh the benefits of lower tooling costs and suitability for larger parts against the limitations in material types. Compression moulding can be more economical for lower production volumes but may not be suitable for all material specifications or design complexities.
How Is 3D Printing Revolutionizing Mould Manufacturing?
3D printing, or additive moulding, allows for the creation of complex shapes through layer-by-layer construction. This technology is particularly useful for prototyping and producing custom parts in small batches. Buyers should consider the flexibility in design and the rapid turnaround times offered by 3D printing. However, it is important to note that while this method excels in customization, it may not be as efficient for high-volume production compared to traditional moulding techniques.
Key Industrial Applications of mould manufacturer
Industry/Sector | Specific Application of mould manufacturer | Value/Benefit for the Business | Key Sourcing Considerations for this Application |
---|---|---|---|
Automotive | Production of plastic components for vehicles | Reduces weight, enhances fuel efficiency, and lowers costs | Quality certifications, compatibility with OEM specifications |
Consumer Electronics | Moulding of housings and casings for devices | Improves aesthetics and durability of products | Material selection, precision in design, and lead times |
Medical Devices | Creation of moulds for surgical instruments | Ensures compliance with health regulations and safety | Regulatory compliance, biocompatibility, and production speed |
Packaging | Moulds for creating containers and packaging solutions | Enhances product shelf life and reduces waste | Customization options, sustainability of materials, and cost |
Construction | Moulding of concrete forms and architectural elements | Increases construction efficiency and reduces labor costs | Durability of moulds, precision in design, and material sourcing |
How is Mould Manufacturing Used in the Automotive Sector?
In the automotive industry, mould manufacturers create precise plastic components used in vehicles, such as dashboards, panels, and bumpers. This application not only contributes to the reduction of vehicle weight, enhancing fuel efficiency, but also allows for cost-effective mass production. International buyers, particularly from Africa and South America, must ensure that the moulds meet OEM specifications and quality certifications to maintain safety and performance standards.
What Role Does Mould Manufacturing Play in Consumer Electronics?
Mould manufacturing is pivotal in producing housings and casings for consumer electronics, such as smartphones and laptops. This process enhances product durability and aesthetic appeal, which are critical factors for consumer satisfaction. B2B buyers from Europe and the Middle East should focus on the precision of design and material selection, as these directly impact the product’s longevity and market competitiveness.
Why is Mould Manufacturing Critical for Medical Devices?
In the medical sector, mould manufacturers create highly specialized moulds for surgical instruments and devices. This application is crucial for ensuring compliance with stringent health regulations and safety standards. Buyers in this sector must prioritize regulatory compliance, biocompatibility of materials, and the speed of production to meet urgent healthcare demands, particularly in regions like South Africa and Colombia.
How Does Mould Manufacturing Improve Packaging Solutions?
Mould manufacturers play a vital role in creating containers and packaging solutions that enhance product shelf life and reduce waste. This application is particularly significant in food and beverage sectors, where packaging integrity is paramount. International buyers should consider customization options and the sustainability of materials when sourcing moulds, as these factors are increasingly important in global markets.
In What Ways is Mould Manufacturing Used in Construction?
In construction, mould manufacturers create forms for concrete and architectural elements, significantly improving construction efficiency and reducing labor costs. This application allows for the quick and precise assembly of structures, which is essential in fast-paced construction environments. B2B buyers should assess the durability of moulds and the precision of designs to ensure that they can withstand the rigors of construction while meeting project timelines.
3 Common User Pain Points for ‘mould manufacturer’ & Their Solutions
Scenario 1: Difficulty in Customization of Moulds for Unique Products
The Problem: B2B buyers often face challenges when seeking customized moulds that cater to their specific product requirements. For example, a company in South Africa may need a mould that accommodates a unique component for an industrial application. However, many mould manufacturers offer limited customization options, leading to delays in production and increased costs. This scenario can be frustrating, especially when buyers require quick turnaround times to meet market demands.
The Solution: To effectively address this issue, buyers should prioritize mould manufacturers that specialize in custom solutions and have a proven track record in their industry. When sourcing a supplier, it’s crucial to communicate detailed specifications and provide prototypes or sketches that illustrate the desired mould design. Engaging in collaborative discussions during the design phase can also help refine the mould to meet specific needs. Additionally, consider manufacturers that use advanced technologies, such as CAD (Computer-Aided Design) software, which can streamline the design process and enhance the precision of the final product. By establishing strong partnerships with flexible manufacturers, buyers can ensure that their unique requirements are met efficiently.
Scenario 2: High Costs Associated with Mould Production
The Problem: For international buyers, especially in regions like South America, the costs associated with mould production can be prohibitively high. Factors such as material selection, shipping, and labor costs can significantly inflate the price, making it difficult for companies to maintain competitive pricing in their markets. This situation is particularly challenging for small and medium-sized enterprises (SMEs) that operate on tight budgets.
The Solution: To mitigate high production costs, buyers should explore alternative materials that do not compromise quality but reduce expenses. For instance, opting for lower-cost plastics or composite materials can lead to significant savings. Additionally, consider sourcing moulds from manufacturers located in countries with lower labor costs, while ensuring that they maintain high-quality standards. Establishing long-term relationships with manufacturers can also lead to better pricing structures due to bulk orders or repeat business. Finally, engaging in thorough market research can help identify competitive pricing models and alternative suppliers, allowing buyers to make informed decisions.
Scenario 3: Quality Control Issues with Mould Products
The Problem: Quality control is a persistent concern for B2B buyers when dealing with mould manufacturers. Inconsistent quality can lead to defects in the end products, resulting in costly recalls and damage to brand reputation. For instance, a manufacturer in Europe may receive moulds that do not meet the specified tolerances, leading to production delays and increased waste. This issue often arises from inadequate quality assurance processes or lack of clear communication between buyers and suppliers.
The Solution: To ensure high-quality mould production, buyers should implement a comprehensive supplier evaluation process. This includes reviewing the manufacturer’s quality assurance protocols, certifications, and past performance records. It is also beneficial to request samples or prototypes before placing large orders to assess the quality firsthand. Establishing clear quality metrics and expectations in the initial contract can help set the standard for the manufacturing process. Regular communication throughout the production phase, including progress updates and inspections, can further enhance quality assurance. By taking these proactive steps, buyers can significantly reduce the risk of quality-related issues and ensure that their moulds meet the required standards.
Strategic Material Selection Guide for mould manufacturer
What are the Key Properties of Common Materials Used in Mould Manufacturing?
When selecting materials for mould manufacturing, it is essential to consider their properties that directly affect product performance. The most commonly used materials include steel, aluminum, and thermoplastics, each with distinct characteristics that cater to various applications.
How Does Steel Perform as a Material for Moulds?
Steel is a prevalent choice in mould manufacturing due to its excellent strength and durability. It typically offers high-temperature resistance and can withstand significant pressure, making it suitable for high-volume production runs. The corrosion resistance of steel can vary, but alloying with other metals can enhance this property.
Pros: Steel moulds are highly durable and can produce high-quality parts with precise dimensions. They are ideal for long-term use in production settings.
Cons: The main drawbacks include higher manufacturing complexity and costs. Steel moulds also require more extensive maintenance and can be heavier, which may affect handling.
Impact on Application: Steel is compatible with a wide range of media, including various plastics and metals, making it versatile for different industries.
Considerations for International Buyers: Buyers from regions like Africa and South America should ensure compliance with local standards such as ASTM or DIN. The cost of steel may vary significantly based on local availability and market conditions.
What are the Advantages of Using Aluminum in Mould Manufacturing?
Aluminum is favored for its lightweight nature and excellent thermal conductivity, which allows for faster cooling cycles during production. This can lead to increased efficiency in manufacturing processes.
Pros: Aluminum moulds are easier to machine and can be produced more quickly than steel moulds. They are also less expensive, making them a cost-effective option for smaller production runs.
Cons: However, aluminum is less durable than steel and may not withstand the same levels of heat and pressure. It can also be prone to wear and deformation over time.
Impact on Application: Aluminum is particularly suitable for lower-temperature applications and is often used in the automotive and consumer goods sectors.
Considerations for International Buyers: Buyers should be aware of the specific grades of aluminum that meet industry standards and ensure that they comply with local regulations in their respective regions.
How Do Thermoplastics Compare in Mould Manufacturing?
Thermoplastics, such as polycarbonate and nylon, are increasingly being used in mould manufacturing due to their flexibility and ease of use. They can be molded into complex shapes and are often used for prototype development.
Pros: Thermoplastics are lightweight, resistant to corrosion, and can be produced with lower energy consumption compared to metals. They also allow for rapid prototyping.
Cons: The primary limitation is their lower heat resistance and mechanical strength compared to metals, which may restrict their use in high-performance applications.
Impact on Application: Thermoplastics are ideal for applications requiring intricate designs and lower production volumes, such as in the electronics and medical device industries.
Considerations for International Buyers: It is crucial for buyers to verify that the thermoplastics used comply with relevant safety and environmental standards, especially in Europe and the Middle East, where regulations can be stringent.
Summary Table of Material Selection for Mould Manufacturing
Material | Typical Use Case for mould manufacturer | Key Advantage | Key Disadvantage/Limitation | Relative Cost (Low/Med/High) |
---|---|---|---|---|
Steel | High-volume production runs | High durability and strength | Higher manufacturing complexity | High |
Aluminum | Low to medium production volumes | Lightweight and cost-effective | Less durable than steel | Medium |
Thermoplastics | Prototyping and low-volume applications | Flexibility and rapid prototyping | Lower heat resistance | Low |
This guide provides a foundational understanding of the strategic material selection process for mould manufacturers. By considering the properties, advantages, and limitations of each material, international B2B buyers can make informed decisions tailored to their specific production needs and regional compliance requirements.
In-depth Look: Manufacturing Processes and Quality Assurance for mould manufacturer
What Are the Main Stages of the Manufacturing Process for Moulds?
The manufacturing process for moulds involves several critical stages, each essential to ensuring the final product meets the required specifications and quality standards. Here’s a detailed breakdown of these stages:
Material Preparation: How Is the Right Material Chosen?
Material selection is foundational in mould manufacturing. Common materials include steel, aluminum, and various thermoplastics. The choice depends on factors like production volume, part complexity, and required durability. For instance, steel is preferred for high-volume production due to its longevity, while aluminum is chosen for its lightweight properties and ease of machining.
Once the material is selected, it undergoes preparation, which may include cutting, milling, and heat treatment processes to enhance its properties. This stage is crucial as it directly influences the mould’s performance and lifespan.
How Is the Forming Process Executed?
The forming stage involves shaping the prepared material into the desired mould configuration. Techniques such as injection moulding, blow moulding, and compression moulding are commonly employed.
-
Injection Moulding: This is the most widely used method, where molten material is injected into a mould cavity. It’s ideal for producing intricate designs and high-volume parts.
-
Blow Moulding: Used primarily for hollow objects, this method involves inflating a heated plastic tube within a mould.
-
Compression Moulding: This technique is often used for thermosetting plastics and involves placing the material in a heated mould, which is then closed to shape the product.
Each of these methods has its advantages and is chosen based on the specific requirements of the mould and the end product.
What Is Involved in the Assembly Stage?
The assembly of mould components, such as cores, cavities, and inserts, is a meticulous process. Precision is key, as any misalignment can lead to defects in the final product. This stage may also involve the integration of cooling channels to facilitate temperature control during the moulding process.
Advanced mould manufacturers often employ CAD (Computer-Aided Design) software to simulate the assembly process, ensuring all components fit correctly before physical assembly. This not only saves time but also reduces the risk of costly errors.
How Is the Finishing Process Conducted?
Finishing processes enhance the mould’s surface quality and functionality. Techniques such as polishing, coating, and etching are used to achieve the desired finish.
-
Polishing: This is crucial for reducing surface roughness, which can affect the quality of the final products.
-
Coating: Applying a protective layer can improve durability and reduce wear during production runs.
-
Etching: This technique is often used for creating detailed textures or patterns on the mould surface, which can impact the aesthetics of the final product.
What Quality Assurance Practices Are Important for Mould Manufacturers?
Quality assurance (QA) is vital in the mould manufacturing process to ensure that the final products meet international standards and customer expectations.
What International Standards Should B2B Buyers Be Aware Of?
International standards, such as ISO 9001, are critical for assessing the quality management systems of mould manufacturers. ISO 9001 outlines requirements for a quality management system that can enhance customer satisfaction through effective system processes.
In addition to ISO standards, industry-specific certifications such as CE marking (for products sold in the European Economic Area) and API (American Petroleum Institute) certifications for certain applications in oil and gas are essential. These certifications indicate compliance with safety and quality standards, reassuring buyers of the moulds’ reliability.
How Are Quality Control Checkpoints Implemented?
Quality control (QC) checkpoints are integrated throughout the manufacturing process to catch defects early. The common QC stages include:
-
Incoming Quality Control (IQC): This involves inspecting raw materials before they enter the production process.
-
In-Process Quality Control (IPQC): Continuous monitoring during the manufacturing process ensures that any deviations from specifications are addressed immediately.
-
Final Quality Control (FQC): This final inspection verifies that the finished moulds meet all quality standards before they are shipped to customers.
These checkpoints are crucial for maintaining product integrity and minimizing waste.
What Testing Methods Are Commonly Used in Mould Manufacturing?
Various testing methods are employed to validate the quality and performance of moulds. Common techniques include:
-
Dimensional Inspection: Using tools like calipers and CMM (Coordinate Measuring Machines) to ensure that the mould dimensions conform to specifications.
-
Functional Testing: This involves running the mould in actual production scenarios to assess performance and identify any potential issues.
-
Material Testing: Conducting tensile strength, hardness, and fatigue tests to ensure the material can withstand operational stresses.
These testing methods help in identifying defects and ensuring that the moulds perform as intended.
How Can B2B Buyers Verify Supplier Quality Control?
For B2B buyers, especially those from regions like Africa, South America, the Middle East, and Europe, verifying the quality control processes of a mould manufacturer is essential. Here are actionable steps buyers can take:
-
Supplier Audits: Conducting on-site audits allows buyers to evaluate the manufacturing processes and QC practices firsthand. This is particularly important for buyers who want to ensure compliance with international standards.
-
Requesting QC Reports: Buyers should ask for detailed QC reports that outline the testing methods used, results obtained, and any corrective actions taken.
-
Third-Party Inspections: Engaging a third-party inspection service can provide an unbiased assessment of the manufacturer’s quality control processes.
-
Certifications Verification: Buyers should verify the authenticity of any claimed certifications, ensuring they are up-to-date and relevant to the specific mould manufacturing processes.
What Are the Nuances of Quality Control for International B2B Buyers?
Understanding the nuances of quality control is particularly important for international B2B buyers. Different regions may have varying standards and expectations regarding quality. For instance:
-
Cultural Differences: Buyers must navigate cultural differences that can impact communication and expectations related to quality.
-
Regulatory Compliance: Buyers should be aware of local regulations that may affect the quality standards for moulds in their respective regions.
-
Logistical Considerations: Shipping moulds internationally can introduce risks, such as damage during transit, which necessitates robust packaging and handling standards.
By understanding these nuances, buyers can better navigate the complexities of sourcing moulds from international manufacturers, ensuring they receive high-quality products that meet their specific needs.
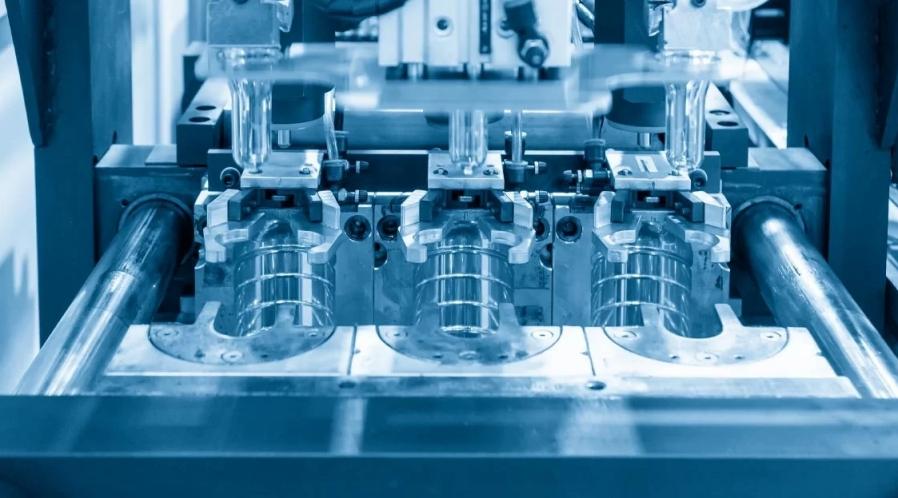
A stock image related to mould manufacturer.
Practical Sourcing Guide: A Step-by-Step Checklist for ‘mould manufacturer’
In the competitive landscape of B2B procurement, sourcing a reliable mould manufacturer is crucial for ensuring product quality and operational efficiency. This checklist aims to guide international buyers from Africa, South America, the Middle East, and Europe through the essential steps for effective sourcing. Following these steps will help you make informed decisions, reduce risks, and build strong supplier relationships.
Step 1: Define Your Technical Specifications
Before engaging with potential suppliers, it’s vital to have a clear understanding of your technical requirements. Define the type of moulds needed, including dimensions, materials, and production processes. This clarity will help you communicate your needs effectively and ensure that suppliers can meet your specifications.
- Consider Industry Standards: Research industry benchmarks for mould quality and performance.
- Document Everything: Create detailed specifications documents to share with suppliers.
Step 2: Conduct Market Research for Suppliers
Identifying potential suppliers is the next critical step. Conduct thorough market research to find mould manufacturers that align with your needs. Look for companies with a proven track record in your industry, particularly those with experience in your geographical region.
- Utilize Online Directories: Platforms like Alibaba or ThomasNet can provide a comprehensive list of manufacturers.
- Industry Associations: Check for membership in industry-specific associations, which can indicate credibility.
Step 3: Evaluate Potential Suppliers
Before committing, it’s crucial to vet suppliers thoroughly. Request company profiles, case studies, and references from buyers in a similar industry or region. Don’t just rely on their website; seek feedback from current or past clients to gauge satisfaction levels and reliability.
- Assess Production Capacity: Ensure the supplier can handle your order volume.
- Quality Assurance Processes: Inquire about their quality control measures and certifications.
Step 4: Verify Supplier Certifications and Compliance
Compliance with international standards is non-negotiable when sourcing moulds. Verify that the supplier holds relevant certifications, such as ISO 9001 or specific industry certifications, which indicate their commitment to quality and safety.
- Request Documentation: Ask for copies of their certifications and quality management processes.
- Check for Regulatory Compliance: Ensure they comply with local and international regulations applicable to your market.
Step 5: Assess Pricing and Payment Terms
Once you have a shortlist of potential suppliers, it’s time to evaluate pricing structures. Request detailed quotes that outline costs for materials, production, and shipping. Additionally, discuss payment terms to find a mutually agreeable arrangement.
- Consider Total Cost of Ownership: Look beyond initial pricing; factor in shipping, duties, and potential tariffs.
- Negotiate Payment Terms: Aim for terms that protect your cash flow while providing the supplier with assurance.
Step 6: Conduct a Factory Visit or Virtual Tour
If possible, visiting the supplier’s facility can provide invaluable insights into their operations. If an in-person visit isn’t feasible, request a virtual tour to assess their manufacturing processes, equipment, and working conditions.
- Evaluate Equipment and Technology: Look for modern equipment and technologies that enhance efficiency and quality.
- Observe Working Conditions: Ensure they adhere to safety and labor standards.
Step 7: Establish Clear Communication Channels
Effective communication is essential for a successful partnership. Establish preferred communication channels and frequency with your chosen supplier to ensure a smooth workflow. Regular check-ins can help address issues promptly and maintain alignment on project goals.
- Use Project Management Tools: Consider tools like Trello or Asana for transparent tracking of progress and tasks.
- Set Up Regular Meetings: Schedule periodic reviews to discuss project developments and any concerns.
Following this checklist will empower you as a B2B buyer to make strategic decisions when sourcing mould manufacturers, ultimately enhancing your supply chain’s reliability and efficiency.
Comprehensive Cost and Pricing Analysis for mould manufacturer Sourcing
What Are the Key Cost Components in Mould Manufacturing?
Understanding the cost structure of mould manufacturing is crucial for international B2B buyers. The primary cost components include:
-
Materials: The type and quality of materials used, such as steel or aluminum, significantly affect costs. High-quality materials may raise initial expenses but can lead to better durability and lower failure rates over time.
-
Labor: Labor costs vary by region. Countries with lower labor costs can offer competitive pricing, but it’s essential to consider the skill level of the workforce, which can impact the quality of the mould.
-
Manufacturing Overhead: This includes costs related to utilities, factory maintenance, and administrative expenses. Understanding these costs helps buyers assess the overall pricing strategy of suppliers.
-
Tooling: Tooling costs can be substantial, especially for custom moulds. This encompasses the equipment and processes required to create the moulds, which can vary greatly depending on the complexity and specifications.
-
Quality Control (QC): Implementing robust QC processes ensures that the moulds meet required standards. This can add to the overall cost but is crucial for reducing defects and ensuring customer satisfaction.
-
Logistics: Shipping costs, including freight and insurance, should be factored into the total price. International buyers need to consider the distance, mode of transport, and associated customs duties.
-
Margin: Suppliers typically include a margin that reflects their profit expectations. Understanding this margin can help in negotiating better prices.
How Do Price Influencers Impact Mould Manufacturing Costs?
Several factors influence pricing in mould manufacturing, particularly for international buyers:
-
Volume and Minimum Order Quantity (MOQ): Bulk purchases can lead to significant discounts. Understanding the MOQ can help buyers negotiate better rates.
-
Specifications and Customization: Custom moulds generally come at a premium. Buyers should assess whether standard moulds can meet their needs to avoid unnecessary costs.
-
Material Choices: The choice of materials directly impacts both quality and price. Buyers should balance cost with performance to find the most cost-effective solution.
-
Quality Certifications: Moulds that meet international quality standards (like ISO certifications) might be priced higher but can save costs related to failures and reworks.
-
Supplier Factors: The reputation and reliability of the supplier can influence pricing. Established suppliers may charge more but often provide better quality assurance.
-
Incoterms: Understanding shipping terms is critical. Different Incoterms (like FOB, CIF) can affect the total landed cost, impacting budgeting and pricing strategies.
What Are the Best Negotiation Tips for International Buyers?
For international B2B buyers, especially from regions like Africa, South America, the Middle East, and Europe, effective negotiation can lead to better pricing:
-
Understand Total Cost of Ownership (TCO): Instead of focusing solely on the initial price, consider the long-term costs associated with quality, maintenance, and potential failures.
-
Leverage Volume Discounts: If planning to make repeated purchases, negotiate for better rates based on anticipated volumes.
-
Be Transparent About Needs: Clearly communicate your specifications and requirements to avoid misunderstandings that could lead to cost overruns.
-
Request Multiple Quotes: Always gather quotes from several suppliers to compare pricing structures and identify the best value.
-
Build Relationships: Establishing a good rapport with suppliers can lead to better pricing and terms over time, as suppliers may be more willing to accommodate loyal customers.
What Pricing Nuances Should International Buyers Consider?
When sourcing moulds internationally, buyers should be aware of several pricing nuances:
-
Currency Fluctuations: Exchange rates can significantly impact costs. Consider locking in prices or using contracts that mitigate currency risk.
-
Import Duties and Taxes: Factor in any applicable import duties and taxes that may apply when bringing moulds into your country.
-
Cultural Considerations: Different regions may have varying expectations around negotiation and pricing. Understanding these cultural nuances can facilitate smoother transactions.
Disclaimer on Indicative Prices
Pricing in mould manufacturing can fluctuate based on various factors, including market conditions, material availability, and supplier pricing strategies. Therefore, the prices discussed should be seen as indicative and subject to change. It is advisable to conduct thorough market research and engage in direct negotiations with suppliers to obtain accurate pricing tailored to specific needs.
Alternatives Analysis: Comparing mould manufacturer With Other Solutions
Understanding the Alternatives to Mould Manufacturing
When considering solutions for mould production, it’s essential to evaluate not only traditional mould manufacturers but also alternative methods that can meet specific business needs. Each alternative presents unique advantages and challenges, which can significantly impact production efficiency, cost, and end-product quality. Below, we explore two viable alternatives to traditional mould manufacturing: additive manufacturing (3D printing) and injection moulding.
Comparison Table of Mould Manufacturing Alternatives
Comparison Aspect | Mould Manufacturer | Additive Manufacturing (3D Printing) | Injection Moulding |
---|---|---|---|
Performance | High precision and durability | Moderate precision; depends on technology used | High precision and scalability |
Cost | Higher initial setup cost | Lower for low-volume production; higher for large-scale | High initial setup cost; lower per unit in mass production |
Ease of Implementation | Requires specialized tooling | Relatively easy; minimal tooling needed | Complex; requires mould design and fabrication |
Maintenance | Moderate; periodic inspections needed | Low; minimal maintenance on printers | High; moulds need regular maintenance |
Best Use Case | Large production runs; complex geometries | Prototyping; low-volume custom parts | High-volume production; standardised parts |
Exploring Additive Manufacturing (3D Printing)
Additive manufacturing, commonly known as 3D printing, offers a flexible approach to producing moulds and components. This method excels in rapid prototyping, allowing businesses to create complex geometries without the need for extensive tooling.
Pros:
– Cost-Effective for Low Volume: 3D printing reduces the initial investment, making it ideal for startups and businesses looking to produce small batches.
– Design Flexibility: It allows for intricate designs that may not be feasible with traditional methods.
Cons:
– Speed Limitations for Large Runs: While fast for prototypes, it may not compete with the speed of mass production methods like injection moulding.
– Material Limitations: The range of materials available for 3D printing is still growing, which can limit application in certain industries.
Evaluating Injection Moulding
Injection moulding is a well-established method for producing high volumes of parts. This process involves injecting molten material into a pre-designed mould, making it a preferred choice for manufacturing standardised components.
Pros:
– High Production Efficiency: Once the mould is created, the cost per unit decreases significantly, making it cost-effective for large quantities.
– Material Versatility: Suitable for a wide range of materials, including plastics and metals.
Cons:
– High Initial Costs: The upfront investment for mould creation can be substantial, making it less attractive for low-volume production.
– Long Lead Times: The design and fabrication of moulds can take time, delaying the production process.
Conclusion: Choosing the Right Solution for Your Needs
Selecting the appropriate mould manufacturing solution depends on specific business requirements, including production volume, budget, and design complexity. For businesses focused on rapid prototyping or low-volume production, additive manufacturing may be the best fit. Conversely, if your goal is to produce large quantities of standardised parts efficiently, injection moulding might be the better choice. B2B buyers should carefully evaluate these alternatives against their unique operational needs to make informed decisions that align with their strategic goals.
Essential Technical Properties and Trade Terminology for mould manufacturer
What Are the Essential Technical Properties for Mould Manufacturing?
In the mould manufacturing industry, understanding the technical properties is crucial for ensuring product quality and performance. Here are some key specifications that international B2B buyers should consider:
1. Material Grade
The grade of material used in mould manufacturing significantly affects durability, thermal resistance, and overall performance. Common materials include steel, aluminum, and various alloys. For example, high-carbon steel is often chosen for its hardness and wear resistance, making it ideal for high-volume production runs. Buyers must ensure that the material grade aligns with their production needs and expected product lifespan.
2. Tolerance Levels
Tolerance refers to the allowable deviation from a specified dimension in a mould. Tight tolerances are essential for precision parts, particularly in industries like automotive or aerospace, where even minor discrepancies can lead to significant failures. Understanding tolerance specifications helps buyers assess whether a manufacturer can meet their quality standards, ensuring that parts fit together correctly during assembly.
3. Surface Finish
Surface finish impacts not only the aesthetic quality of the final product but also its functionality. Different applications may require specific finishes, such as polished surfaces for optical clarity or textured surfaces for better grip. Buyers should specify their surface finish requirements to avoid costly rework and ensure that the end product meets their expectations.
4. Heat Treatment
Heat treatment processes enhance the physical properties of the mould material, improving hardness and resistance to wear and fatigue. Different treatments, such as annealing or quenching, can be applied based on the intended use of the mould. Buyers should inquire about the heat treatment processes used by manufacturers to ensure they are suitable for their production needs.
5. Machining Capabilities
The machining capabilities of a mould manufacturer determine the complexity of designs that can be achieved. Advanced CNC machining allows for intricate designs and high precision, essential for modern manufacturing. Buyers should assess the machining technologies available to ensure they can produce the desired mould designs efficiently.
What Are Common Trade Terms in Mould Manufacturing?
Navigating the mould manufacturing landscape requires familiarity with industry-specific jargon. Here are some essential terms that B2B buyers should understand:
1. OEM (Original Equipment Manufacturer)
OEM refers to a company that produces parts or equipment that may be marketed by another manufacturer. In mould manufacturing, this means that a buyer can source moulds that are specifically designed for their products, ensuring compatibility and quality.
2. MOQ (Minimum Order Quantity)
MOQ is the smallest quantity of a product that a supplier is willing to sell. Understanding MOQ is crucial for budgeting and inventory management, as it can impact the overall cost and feasibility of production runs. Buyers should negotiate MOQs to align with their production schedules and demand.
3. RFQ (Request for Quotation)
An RFQ is a document that buyers send to suppliers requesting pricing and terms for specific mould manufacturing services. Crafting a detailed RFQ helps ensure that suppliers provide accurate quotes, enabling buyers to make informed decisions.
4. Incoterms (International Commercial Terms)
Incoterms define the responsibilities of buyers and sellers in international transactions, including shipping, insurance, and tariffs. Familiarity with these terms helps buyers understand their obligations and manage risks effectively in cross-border transactions.
5. Lead Time
Lead time refers to the time taken from placing an order until the delivery of the mould. Understanding lead times is vital for planning production schedules and managing supply chain expectations. Buyers should communicate their timelines clearly to manufacturers to ensure timely delivery.
By grasping these technical properties and trade terminologies, international B2B buyers can make informed decisions, ensuring that their mould manufacturing needs are met effectively and efficiently.
Navigating Market Dynamics and Sourcing Trends in the mould manufacturer Sector
What Are the Current Market Dynamics and Sourcing Trends in the Mould Manufacturing Sector?
The mould manufacturing sector is experiencing significant transformations driven by globalization, technological advancements, and evolving buyer expectations. Key market drivers include the increasing demand for customized and high-precision moulds across various industries such as automotive, consumer goods, and electronics. The rise of Industry 4.0 has introduced automation and smart manufacturing processes, enabling manufacturers to enhance efficiency and reduce lead times. International B2B buyers from regions like Africa, South America, the Middle East, and Europe should be aware of the trend towards digitalization, which includes the use of advanced software for design and simulation, as well as the integration of IoT devices to monitor production processes in real-time.
Emerging sourcing trends highlight a shift towards just-in-time (JIT) manufacturing, allowing companies to minimize inventory costs and respond swiftly to market demands. Additionally, the adoption of additive manufacturing (3D printing) is becoming prevalent, offering greater design flexibility and reducing material waste. Buyers must also consider regional sourcing strategies, as local suppliers can provide advantages in terms of logistics and reduced tariffs, especially in the context of ongoing trade tensions and supply chain disruptions. Understanding these dynamics is crucial for buyers seeking to optimize their procurement processes and ensure a competitive edge in their respective markets.
How Can Sustainability and Ethical Sourcing Impact the Mould Manufacturing Sector?
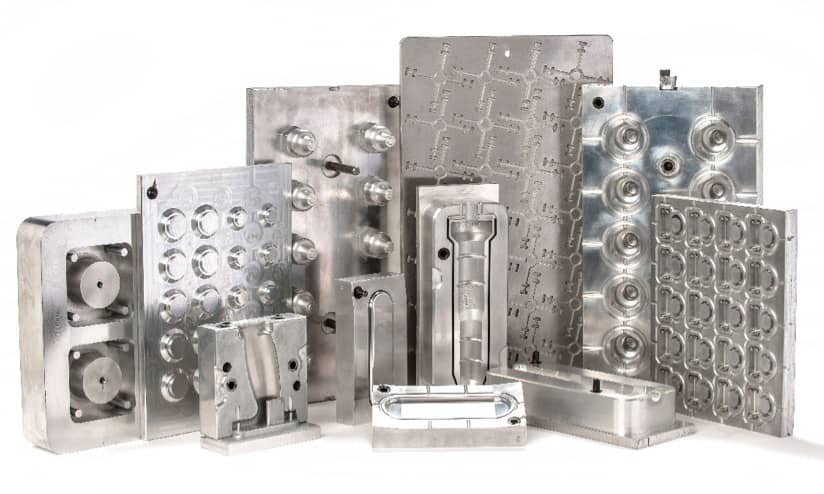
A stock image related to mould manufacturer.
Sustainability has emerged as a central concern for businesses globally, impacting the mould manufacturing sector significantly. The environmental impact of traditional mould production processes, often characterized by high energy consumption and waste generation, is prompting manufacturers to adopt more sustainable practices. For B2B buyers, understanding the sustainability credentials of suppliers is crucial. This includes evaluating suppliers’ commitment to reducing carbon footprints, implementing energy-efficient technologies, and minimizing waste through recycling and reuse.
Ethical sourcing has gained traction as consumers and businesses alike demand transparency in supply chains. Buyers should prioritize suppliers who adhere to ethical practices, such as fair labor conditions and responsible sourcing of raw materials. Certifications such as ISO 14001 (Environmental Management) and ISO 50001 (Energy Management) serve as indicators of a supplier’s commitment to sustainability. Furthermore, the use of eco-friendly materials, such as biodegradable plastics or recycled metals, can enhance product appeal and meet the growing consumer demand for sustainable products. By prioritizing sustainability and ethical sourcing, international buyers can not only mitigate risks but also strengthen their brand reputation and drive long-term business success.
What Is the Historical Context of Mould Manufacturing Relevant to Today’s B2B Buyers?
The mould manufacturing sector has evolved significantly over the past century, transitioning from manual craftsmanship to sophisticated automated production. Initially, moulds were crafted by skilled artisans, which limited production scale and customization options. The introduction of metalworking machines in the early 20th century revolutionized the industry, allowing for greater precision and mass production capabilities.
In recent decades, the advancement of computer-aided design (CAD) and computer-aided manufacturing (CAM) technologies has further transformed the landscape. These innovations not only enhance design accuracy but also facilitate rapid prototyping, enabling manufacturers to respond quickly to market demands. For B2B buyers, understanding this historical context can provide valuable insights into current capabilities and future trends in the mould manufacturing sector, guiding procurement strategies that align with technological advancements and market expectations. As the industry continues to innovate, buyers should remain vigilant in seeking suppliers that are not only technologically adept but also responsive to the evolving landscape of global trade and sustainability.
Frequently Asked Questions (FAQs) for B2B Buyers of mould manufacturer
-
How do I choose the right mould manufacturer for my business needs?
Choosing the right mould manufacturer involves several key factors. First, assess their expertise in your specific industry—whether it’s automotive, consumer goods, or medical devices. Look for manufacturers with proven experience in producing the type of moulds you require. Evaluate their portfolio for quality and innovation. It’s also essential to consider their certifications, such as ISO standards, which indicate quality management practices. Finally, request references from previous clients to gauge their reliability and customer service. -
What are the typical minimum order quantities (MOQs) for mould manufacturing?
Minimum order quantities can vary significantly between manufacturers and depend on factors like complexity and material used. Typically, MOQs can range from 50 to several hundred units. For custom moulds, some manufacturers may require a higher MOQ due to the setup costs involved. It’s important to discuss your specific requirements with potential suppliers to understand their MOQs and explore options for smaller initial orders if necessary. -
What payment terms should I expect when working with international mould manufacturers?
Payment terms can vary widely based on the manufacturer’s policies and your negotiation. Common arrangements include a deposit (usually 30-50%) upfront, with the balance due upon completion or before shipping. Some manufacturers may offer payment through letters of credit or escrow services for added security. Always clarify terms in advance and ensure they are documented in your contract to avoid disputes later. -
How can I ensure quality assurance when sourcing moulds internationally?
To ensure quality assurance, start by verifying the manufacturer’s certifications, such as ISO 9001. Request detailed quality control processes, including inspections at various production stages. Consider establishing a clear quality agreement that outlines standards and acceptance criteria. If feasible, schedule a factory visit or hire a third-party inspection service to assess the production before shipment. This proactive approach can help mitigate risks associated with international sourcing. -
What customization options are available with mould manufacturers?
Most mould manufacturers offer a range of customization options, including material selection, size, shape, and design features. Discuss your specific requirements with the manufacturer to understand what customizations are feasible. Some manufacturers may also provide design assistance or CAD services to help refine your specifications. Ensure you communicate your needs clearly to avoid misunderstandings and ensure the final product meets your expectations. -
How do I vet a mould manufacturer for reliability and quality?
Vetting a mould manufacturer involves thorough research. Start by checking their online presence, including reviews and testimonials from previous clients. Request samples of their work to evaluate quality firsthand. Additionally, inquire about their production capacity, turnaround times, and any warranties they offer. Engaging in discussions about their supply chain and sourcing practices can also provide insights into their reliability and commitment to quality. -
What logistical considerations should I keep in mind when importing moulds?
Logistical considerations include shipping methods, customs regulations, and potential tariffs. Determine the most cost-effective shipping option based on your timeline and budget. Familiarize yourself with the import regulations in your country to avoid delays or additional costs. It may also be beneficial to work with a freight forwarder who can help navigate the complexities of international shipping and ensure compliance with all requirements. -
How can I establish a long-term partnership with a mould manufacturer?
Building a long-term partnership requires clear communication, mutual respect, and a shared vision for quality and innovation. Start by establishing open lines of communication and regularly providing feedback on their products and services. Consider collaborating on new projects or improvements to existing designs. Additionally, honoring payment terms and providing timely orders can help foster trust and reliability, making the partnership beneficial for both parties in the long run.
Important Disclaimer & Terms of Use
⚠️ Important Disclaimer
The information provided in this guide, including content regarding manufacturers, technical specifications, and market analysis, is for informational and educational purposes only. It does not constitute professional procurement advice, financial advice, or legal advice.
While we have made every effort to ensure the accuracy and timeliness of the information, we are not responsible for any errors, omissions, or outdated information. Market conditions, company details, and technical standards are subject to change.
B2B buyers must conduct their own independent and thorough due diligence before making any purchasing decisions. This includes contacting suppliers directly, verifying certifications, requesting samples, and seeking professional consultation. The risk of relying on any information in this guide is borne solely by the reader.
Strategic Sourcing Conclusion and Outlook for mould manufacturer
How Can Strategic Sourcing Enhance Your Mould Manufacturing Process?
In conclusion, strategic sourcing is not just a procurement strategy; it is a vital component for international B2B buyers in the mould manufacturing industry. By leveraging global supplier networks and focusing on quality, sustainability, and innovation, companies from Africa, South America, the Middle East, and Europe can significantly enhance their production capabilities and reduce costs. Key takeaways include the importance of establishing strong supplier relationships, understanding local market dynamics, and utilizing technology for better supply chain management.
What Future Trends Should B2B Buyers Anticipate in Mould Manufacturing?
As we look ahead, the mould manufacturing landscape is poised for transformation driven by advancements in materials science, automation, and eco-friendly practices. B2B buyers should prepare to engage with suppliers who not only meet current demands but also align with future trends such as 3D printing and sustainable production methods.
How Can You Take Action Today for Better Sourcing Outcomes?
For those looking to optimize their sourcing strategy, now is the time to act. Conduct thorough market research, evaluate potential suppliers based on their technological capabilities, and consider forming strategic partnerships that can lead to innovative solutions. By doing so, you will not only secure a competitive advantage but also contribute to a more resilient and sustainable mould manufacturing sector. Engage with suppliers today to explore opportunities that will elevate your business in this evolving market.