Discover Top Benefits of Choosing a Patch Panel Manufacturer (2025)
Introduction: Navigating the Global Market for patch panel manufacturer
In the rapidly evolving landscape of telecommunications and data management, sourcing the right patch panel manufacturer can present a significant challenge for B2B buyers. As organizations worldwide increasingly rely on robust networking infrastructure, the need for high-quality patch panels—integral components that help organize and manage network cables—becomes paramount. This guide is designed to navigate the complexities of the global market, providing a comprehensive overview of various types of patch panels, their applications, and the critical factors to consider when selecting a supplier.
International B2B buyers, particularly those from Africa, South America, the Middle East, and Europe, face unique hurdles, including varying market standards, logistical considerations, and supplier reliability. This guide empowers you with actionable insights on how to effectively vet suppliers, assess costs, and understand the diverse applications of patch panels in different industries. You will learn how to identify reputable manufacturers that align with your specific needs, whether you are looking for fiber optic, Ethernet, or modular patch panels.
By leveraging this resource, you can make informed purchasing decisions that enhance your organization’s network performance and reliability. Equip yourself with the knowledge needed to navigate the global patch panel market confidently and ensure your infrastructure supports your operational goals.
Understanding patch panel manufacturer Types and Variations
Type Name | Key Distinguishing Features | Primary B2B Applications | Brief Pros & Cons for Buyers |
---|---|---|---|
Standard Patch Panels | Fixed ports, typically 24 or 48 ports | Office networks, data centers | Pros: Cost-effective, easy installation. Cons: Limited flexibility for future needs. |
Modular Patch Panels | Interchangeable modules for customization | Large enterprises, telecom industries | Pros: High adaptability, scalable. Cons: Higher initial investment. |
Smart Patch Panels | Integrated monitoring and management features | Data centers, cloud services | Pros: Enhanced control and diagnostics. Cons: More complex setup and higher costs. |
Fiber Optic Patch Panels | Designed specifically for fiber connections | Telecommunications, high-speed networks | Pros: Optimized for speed, minimal signal loss. Cons: More expensive, requires specialized knowledge. |
Industrial Patch Panels | Rugged design for harsh environments | Manufacturing, outdoor installations | Pros: Durability, resistance to environmental factors. Cons: Heavier, less aesthetic. |
What are the Characteristics of Standard Patch Panels?
Standard patch panels are the most common type, featuring a fixed number of ports—typically 24 or 48. They are designed for straightforward installations in office networks and data centers. Their simplicity makes them an attractive option for businesses looking for cost-effective solutions. However, the rigidity of standard patch panels can be a drawback for organizations anticipating future expansion, as they may require additional equipment to accommodate growth.
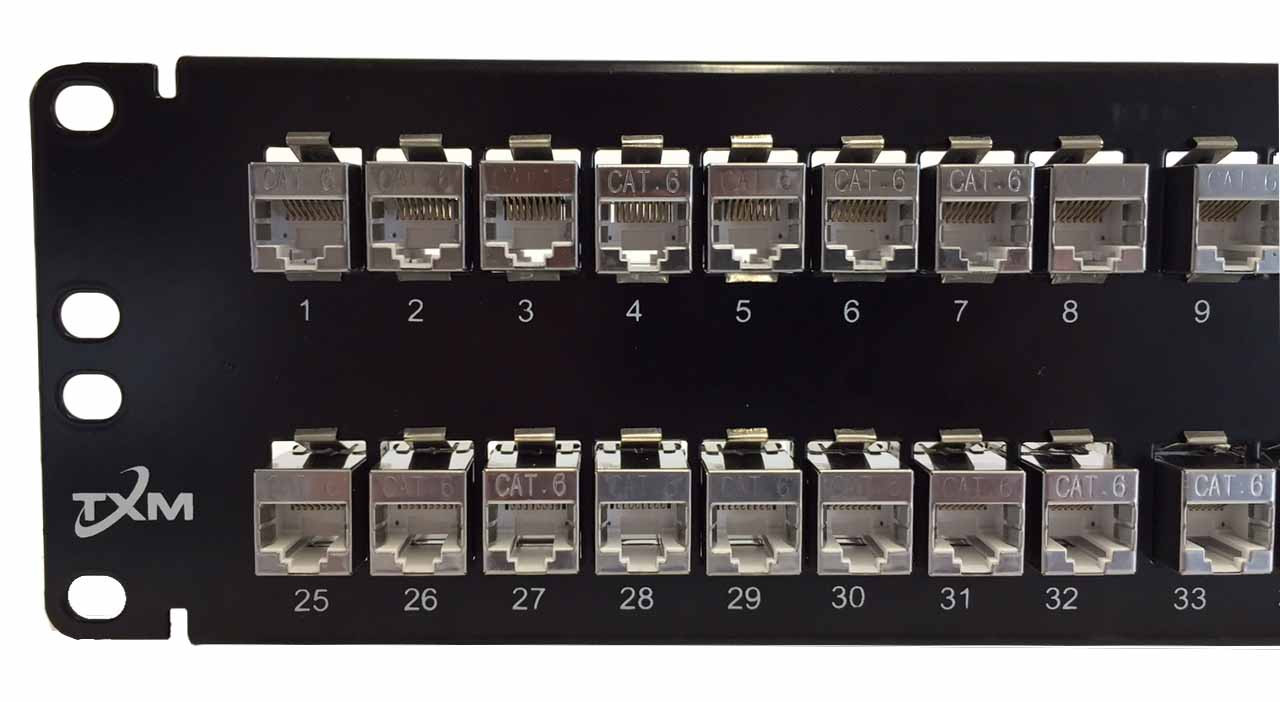
A stock image related to patch panel manufacturer.
How Do Modular Patch Panels Offer Flexibility?
Modular patch panels stand out due to their interchangeable modules, allowing businesses to customize their configurations based on specific needs. This adaptability is particularly beneficial for large enterprises and telecom industries that require scalability. While they may involve a higher initial investment, the long-term flexibility they offer can lead to cost savings as business needs evolve. Buyers should consider their future requirements when evaluating this type.
What Advantages Do Smart Patch Panels Provide?
Smart patch panels come equipped with integrated monitoring and management capabilities, making them ideal for data centers and cloud service providers. These panels allow for real-time diagnostics and control, enhancing network reliability and performance. However, the complexity of setup and higher costs associated with smart patch panels may deter smaller businesses. Organizations should weigh their need for advanced features against their budget and technical expertise.
Why Choose Fiber Optic Patch Panels for High-Speed Networks?
Fiber optic patch panels are specifically designed for fiber connections, making them essential in telecommunications and high-speed network environments. They minimize signal loss and optimize performance, which is crucial for data-intensive applications. While fiber optic panels tend to be more expensive and require specialized knowledge for installation, they are indispensable for businesses that prioritize speed and efficiency in their operations.
What Makes Industrial Patch Panels Suitable for Harsh Environments?
Industrial patch panels are built to withstand harsh conditions, making them ideal for manufacturing and outdoor installations. Their rugged design offers durability and resistance to environmental factors such as dust, moisture, and extreme temperatures. Although they may be heavier and less aesthetically pleasing than other types, their reliability in challenging settings makes them a worthwhile investment for businesses operating in demanding environments.
Related Video: Terminating Patch Panel – How to do it fast and easy
Key Industrial Applications of patch panel manufacturer
Industry/Sector | Specific Application of patch panel manufacturer | Value/Benefit for the Business | Key Sourcing Considerations for this Application |
---|---|---|---|
Telecommunications | Network Infrastructure Management | Enhanced connectivity and reduced downtime | Compatibility with existing systems and scalability |
Data Centers | Data Management and Distribution | Improved data flow and operational efficiency | High-density configurations and cooling solutions |
Industrial Automation | Machine Connectivity and Control | Streamlined operations and reduced maintenance costs | Durability and resistance to environmental factors |
Education | Campus Network Solutions | Reliable internet access for students and faculty | Ease of installation and support for future upgrades |
Healthcare | Medical Device Integration | Improved patient care and operational efficiency | Compliance with safety regulations and reliability |
How Are Patch Panels Used in Telecommunications?
In the telecommunications industry, patch panels are essential for managing network infrastructure. They facilitate the organization and connection of various network cables, ensuring efficient data transmission and reducing the risk of downtime. For international buyers, particularly from regions like Africa and the Middle East, sourcing patch panels that offer compatibility with local network standards is crucial. Additionally, scalability is a key consideration, as businesses may need to expand their networks in the future.
What Role Do Patch Panels Play in Data Centers?
Data centers utilize patch panels for effective data management and distribution. These devices help in organizing large volumes of cables, which is vital for maintaining efficient data flow and operational efficiency. For B2B buyers in Europe and South America, selecting patch panels with high-density configurations can maximize space utilization. Moreover, considering cooling solutions is essential, as overheating can lead to equipment failure and increased operational costs.
How Do Patch Panels Support Industrial Automation?
In industrial automation, patch panels play a critical role in connecting machinery and control systems. They streamline operations by simplifying the wiring process and reducing maintenance costs through organized cable management. Buyers from regions with developing industrial sectors, such as Colombia and Vietnam, should prioritize sourcing durable patch panels that can withstand harsh environments. Understanding the specific connectivity requirements of their machinery will also guide their purchasing decisions.
Why Are Patch Panels Important for Educational Institutions?
Educational institutions leverage patch panels to create robust campus network solutions. By ensuring reliable internet access for students and faculty, these panels enhance the learning experience and operational efficiency. For international buyers in Africa and South America, ease of installation is a vital consideration, as many institutions may lack advanced technical staff. Additionally, the ability to support future upgrades is important, given the rapid pace of technological advancement in education.
How Do Patch Panels Enhance Healthcare Operations?
In the healthcare sector, patch panels are crucial for integrating medical devices and ensuring seamless communication between equipment. This integration leads to improved patient care and operational efficiency. For B2B buyers in the Middle East and Europe, compliance with safety regulations is a top priority when sourcing patch panels. Reliability is also critical, as any downtime can significantly affect patient outcomes and operational costs.
Related Video: 1U Rack Mount Fiber Optic Patch Panel Cabling Solution | FS
3 Common User Pain Points for ‘patch panel manufacturer’ & Their Solutions
Scenario 1: Difficulty in Ensuring Compatibility with Existing Infrastructure
The Problem: Many B2B buyers face the challenge of integrating new patch panels with their existing network infrastructure. This is particularly pertinent for companies in regions such as Africa and South America, where diverse systems and outdated technologies can complicate compatibility. Buyers often struggle with the nuances of different standards (like CAT5e, CAT6, etc.) and the implications these have on performance and scalability. As a result, they risk investing in products that either underperform or require additional upgrades, leading to increased costs and project delays.
The Solution: To overcome compatibility issues, buyers should conduct a thorough audit of their current infrastructure before purchasing. This involves documenting existing cabling types, bandwidth requirements, and future expansion plans. When sourcing patch panels, it is crucial to consult with manufacturers who offer compatibility guarantees or extensive technical support. Look for patch panel manufacturers that provide detailed specifications and installation guides. Furthermore, consider engaging with a local consultant or technician who can provide insight into the specific needs of your network environment, ensuring that any new equipment will mesh seamlessly with your existing setup.
Scenario 2: Limited Support and Technical Assistance Post-Purchase
The Problem: Buyers often report a lack of adequate post-purchase support from patch panel manufacturers. This can be particularly frustrating for businesses in the Middle East and Europe, where timely technical assistance is critical for maintaining operational efficiency. Without proper guidance, users may find themselves struggling with installation, configuration, or troubleshooting, which can lead to extended downtime and lost revenue.
The Solution: To mitigate this risk, buyers should prioritize manufacturers who offer robust customer service and technical support. When evaluating potential suppliers, inquire about their support structure, including availability of installation guides, online tutorials, and direct customer service access. Additionally, consider manufacturers that provide training sessions or workshops, particularly for complex systems. Establishing a relationship with a manufacturer that values ongoing support can be beneficial. Opt for vendors who have a local presence or partnerships within your region, as this can facilitate quicker response times and more personalized service.
Scenario 3: Navigating Regulatory Compliance and Standards
The Problem: International buyers often face regulatory challenges when sourcing patch panels, especially those in Africa and South America, where compliance with local and international standards can vary significantly. This can lead to confusion about which certifications are necessary, risking fines or project delays if the purchased equipment does not meet legal requirements.
The Solution: To effectively navigate compliance issues, B2B buyers should familiarize themselves with the relevant regulations in their respective countries before making a purchase. This may include understanding local telecommunication laws, safety standards, and environmental regulations. Working with a patch panel manufacturer who is knowledgeable about these regulations is crucial. Look for companies that provide documentation and certification for their products, showcasing compliance with both local and international standards. Additionally, consider joining industry associations or forums that focus on telecommunications and networking, as these can provide valuable insights and updates on regulatory changes, helping you stay informed and compliant.
Strategic Material Selection Guide for patch panel manufacturer
When selecting materials for patch panel manufacturing, it is essential to consider various factors that impact performance, durability, and compliance with international standards. Here, we analyze four common materials used in the industry: steel, aluminum, plastic, and fiber-reinforced composites. Each material has distinct properties and implications for international B2B buyers, especially from regions such as Africa, South America, the Middle East, and Europe.
What Are the Key Properties of Steel in Patch Panel Manufacturing?
Steel is renowned for its strength and durability, making it a popular choice for patch panel enclosures. It typically offers excellent temperature and pressure ratings, which are crucial for environments with fluctuating conditions. Steel’s corrosion resistance can be enhanced through galvanization or powder coating, ensuring longevity even in harsh climates.
Pros & Cons:
Steel’s primary advantage is its robustness, which translates to a longer lifespan and better protection for internal components. However, it can be heavier and more expensive to manufacture compared to other materials. Additionally, its susceptibility to rust in humid environments can be a concern, necessitating additional protective measures.
Impact on Application:
Steel patch panels are well-suited for industrial applications where durability is paramount. They can handle a variety of media, including electrical and data cables, making them versatile.
Considerations for International Buyers:
Buyers should ensure compliance with standards such as ASTM A123 for galvanization. In regions with high humidity, like parts of Africa and South America, selecting a coated steel option may be advisable.
How Does Aluminum Compare as a Material for Patch Panels?
Aluminum is another popular choice, known for its lightweight properties and resistance to corrosion. It typically performs well under a range of temperatures and is less prone to rust than steel, making it ideal for outdoor applications.
Pros & Cons:
The key advantage of aluminum is its lightweight nature, which simplifies installation and reduces shipping costs. However, it may not be as strong as steel, leading to potential vulnerabilities in high-impact environments. Additionally, aluminum can be more expensive due to its manufacturing process.
Impact on Application:
Aluminum patch panels are particularly effective in telecommunications and data centers, where weight and thermal management are critical.
Considerations for International Buyers:
Compliance with standards such as ASTM B209 is important. In Europe, buyers may prefer aluminum for its recyclability, aligning with sustainability goals.
What Role Does Plastic Play in Patch Panel Manufacturing?
Plastic materials, particularly high-density polyethylene (HDPE) and polycarbonate, are increasingly used for patch panels due to their lightweight and cost-effective nature. These materials exhibit good resistance to chemicals and moisture, making them suitable for various environments.
Pros & Cons:
The primary advantage of plastic is its low cost and ease of manufacturing, allowing for rapid production. However, plastic may not offer the same level of durability as metals, which can limit its use in high-stress applications.
Impact on Application:
Plastic patch panels are ideal for residential and light commercial applications where weight and cost are primary concerns.
Considerations for International Buyers:
Buyers should look for compliance with ISO 9001 for quality management systems. In regions like the Middle East, where temperatures can soar, ensuring that the selected plastic can withstand heat is crucial.
Why Consider Fiber-Reinforced Composites for Patch Panels?
Fiber-reinforced composites, such as fiberglass, are gaining traction in patch panel manufacturing due to their exceptional strength-to-weight ratio and resistance to environmental factors. These materials can withstand high temperatures and are immune to corrosion, making them suitable for diverse applications.
Pros & Cons:
The key advantage of fiber-reinforced composites is their lightweight nature combined with high strength, making them ideal for demanding environments. However, they can be more expensive to manufacture and may require specialized production techniques.
Impact on Application:
These composites are particularly useful in telecommunications and military applications where performance and reliability are critical.
Considerations for International Buyers:
Buyers should ensure compliance with relevant industry standards, such as ASTM D3039 for tensile properties. In Europe, the use of composites may align with increasing demands for lightweight and durable solutions.
Summary Table of Material Selection for Patch Panel Manufacturing
Material | Typical Use Case for patch panel manufacturer | Key Advantage | Key Disadvantage/Limitation | Relative Cost (Low/Med/High) |
---|---|---|---|---|
Steel | Industrial applications | High durability | Heavier and potential rust issues | Medium |
Aluminum | Telecommunications and data centers | Lightweight and corrosion-resistant | Less strong than steel | High |
Plastic | Residential and light commercial applications | Low cost and easy to manufacture | Lower durability | Low |
Fiber-Reinforced Composites | Telecommunications and military applications | High strength-to-weight ratio | Higher manufacturing costs | High |
This strategic material selection guide provides international B2B buyers with actionable insights into the properties, advantages, and considerations of various materials for patch panel manufacturing. By understanding these factors, buyers can make informed decisions that align with their specific needs and compliance requirements.
In-depth Look: Manufacturing Processes and Quality Assurance for patch panel manufacturer
What Are the Key Manufacturing Processes for Patch Panels?
Manufacturing patch panels involves several critical stages that ensure the final product meets the required specifications for functionality and durability. Understanding these processes is essential for B2B buyers looking to source high-quality patch panels.
Material Preparation: What Materials Are Used in Patch Panel Manufacturing?
The first step in the manufacturing process is material preparation. Patch panels are typically constructed from high-quality metals such as aluminum and steel, alongside plastic components for housing. The choice of material is crucial, as it impacts the panel’s durability and electromagnetic interference (EMI) shielding capabilities.
Suppliers often use pre-formed sheets or rolls of metal, which are cut into specific dimensions. Buyers should inquire about the source of these materials, as well as any certifications that verify material quality. For instance, materials should comply with international standards such as RoHS (Restriction of Hazardous Substances) to ensure safety and sustainability.
Forming: How Are Patch Panels Shaped?
Once materials are prepared, the next stage is forming. This typically involves processes like stamping, bending, and welding. Advanced manufacturers may employ CNC (Computer Numerical Control) machines for precise cutting and shaping, ensuring consistency across batches.
For B2B buyers, understanding the forming techniques used by manufacturers can provide insights into the robustness of the end product. Techniques such as laser cutting offer precision and reduce waste, which can be a significant factor in cost-effectiveness.
Assembly: What Are the Steps Involved in Assembling Patch Panels?
The assembly stage involves bringing together all the components, including connectors, housing, and any additional features like labeling or grounding systems. This process often requires skilled labor and is typically conducted in a clean environment to prevent contamination.
During assembly, it’s vital to ensure that connections are secure and that the overall design adheres to ergonomic and functional standards. Buyers should assess whether the manufacturer utilizes automated assembly lines, as this can enhance precision and speed, ultimately affecting lead times.
Finishing: What Finishing Techniques Are Commonly Used?
Finishing is the final stage of manufacturing patch panels. This can include processes such as painting, coating, and printing labels. The finishing process not only enhances the aesthetic appeal but also contributes to the product’s durability and resistance to environmental factors.
B2B buyers should inquire about the types of coatings used, such as powder coating or anodizing, which can provide additional protection against corrosion and wear. These details can be crucial for applications in harsh environments, particularly for buyers from regions like Africa and the Middle East.
What Quality Assurance Measures Are Essential for Patch Panel Manufacturers?
Quality assurance (QA) is a critical aspect of the manufacturing process, ensuring that the patch panels meet industry standards and customer expectations. Buyers must be aware of the QA protocols employed by manufacturers.
Which International Standards Should Patch Panel Manufacturers Comply With?
International standards such as ISO 9001 play a significant role in quality assurance for patch panel manufacturers. ISO 9001 outlines the criteria for a quality management system, emphasizing the importance of consistent quality and customer satisfaction.
Additionally, industry-specific certifications such as CE marking and API (American Petroleum Institute) standards are relevant, particularly for manufacturers supplying to the telecommunications and oil and gas industries. Buyers should verify that their suppliers hold these certifications, as they reflect a commitment to quality and safety.
What Are the Key Quality Control Checkpoints in Manufacturing?
Quality control (QC) checkpoints are integral to maintaining high standards throughout the manufacturing process. Key checkpoints include:
-
Incoming Quality Control (IQC): This phase involves inspecting raw materials upon delivery to ensure they meet specified standards before production begins.
-
In-Process Quality Control (IPQC): Throughout the manufacturing process, regular inspections are conducted to identify any defects or deviations from quality standards.
-
Final Quality Control (FQC): Once the patch panels are fully assembled, a final inspection is performed to ensure all specifications are met before shipping.
Buyers should inquire about the specific QC protocols and frequency of inspections at each stage, as this can significantly affect product reliability.
How Can B2B Buyers Verify Supplier Quality Control?
Verifying the quality control processes of a patch panel manufacturer is essential for B2B buyers. Here are several methods to ensure that suppliers maintain high standards:
-
Audits: Conducting on-site audits allows buyers to evaluate the manufacturing environment, processes, and adherence to quality standards. This firsthand assessment is invaluable.
-
Quality Reports: Requesting detailed quality reports from suppliers can provide insights into their QC performance, including defect rates and corrective actions taken.
-
Third-Party Inspections: Engaging third-party inspection services can provide an unbiased evaluation of the manufacturer’s quality control processes and product quality.
-
Certifications: Verifying that manufacturers possess relevant certifications not only ensures compliance with international standards but also indicates a commitment to maintaining quality.
What Nuances Should International B2B Buyers Consider in Quality Assurance?
For international buyers, particularly from diverse markets such as Africa, South America, the Middle East, and Europe, understanding the nuances of quality assurance in manufacturing is crucial.
-
Regulatory Compliance: Different regions may have unique regulatory requirements. Buyers should ensure that their suppliers are compliant with local and international regulations relevant to their markets.
-
Cultural Differences: Cultural attitudes toward quality and manufacturing practices can vary significantly. It’s important for buyers to understand these differences and establish clear communication regarding quality expectations.
-
Supply Chain Transparency: Given the complexities of global supply chains, buyers should seek suppliers that provide transparency regarding their sourcing and manufacturing processes. This can enhance trust and facilitate smoother transactions.
By focusing on these aspects of manufacturing processes and quality assurance, B2B buyers can make informed decisions when selecting patch panel manufacturers, ultimately ensuring they receive high-quality products that meet their specific needs.
Practical Sourcing Guide: A Step-by-Step Checklist for ‘patch panel manufacturer’
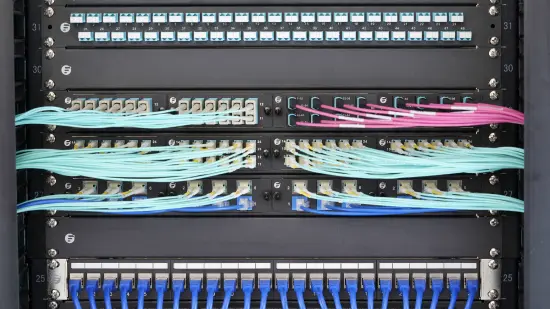
A stock image related to patch panel manufacturer.
This practical sourcing guide aims to provide international B2B buyers with a structured approach to procuring patch panels from manufacturers. By following this checklist, buyers can ensure they select the right suppliers that meet their specific needs, particularly in diverse markets such as Africa, South America, the Middle East, and Europe.
Step 1: Define Your Technical Specifications
Establishing clear technical specifications is the foundation of a successful sourcing process. Determine the type of patch panel you need, considering factors such as capacity, port density, and compatibility with existing equipment. This clarity will guide you in identifying manufacturers that specialize in your required specifications.
- Types of Patch Panels: Identify whether you need a fiber optic, copper, or hybrid patch panel.
- Capacity Requirements: Assess how many ports you will require based on current and future needs.
Step 2: Conduct Market Research
Thorough market research allows you to understand the landscape of patch panel manufacturers. Investigate regional suppliers and their product offerings to gauge which companies align with your needs. This research will also help you identify trends and innovations in the patch panel market.
- Industry Trends: Look for advancements in technology that might affect your purchasing decision.
- Regional Suppliers: Focus on manufacturers that have a strong presence in your specific geographical area.
Step 3: Evaluate Potential Suppliers
Before committing to a supplier, it’s crucial to conduct a thorough evaluation. Request detailed company profiles, product catalogs, and case studies to gauge their expertise and reliability. Additionally, seek references from other clients in similar industries or regions to validate their capabilities.
- Company Reputation: Investigate online reviews and testimonials to assess supplier reliability.
- Client References: Ask for contacts from previous buyers to discuss their experiences.
Step 4: Verify Certifications and Compliance
Ensuring that your chosen manufacturers comply with industry standards and certifications is vital for quality assurance. Check for ISO certifications, CE markings, or any relevant local compliance standards that guarantee product reliability and safety.
- Quality Assurance Standards: Understand the quality control processes they have in place.
- Regulatory Compliance: Make sure they adhere to the regulations specific to your region.
Step 5: Request Samples for Testing
Before making a bulk purchase, requesting samples is essential to evaluate the quality of the patch panels. Testing samples will help you assess performance, durability, and compatibility with your existing systems. This step minimizes the risk of investing in subpar products.
- Testing Parameters: Check for performance metrics such as signal loss and durability under various conditions.
- Compatibility Tests: Ensure the samples work seamlessly with your existing infrastructure.
Step 6: Negotiate Pricing and Terms
Once you’ve selected a supplier, it’s time to discuss pricing and payment terms. Be transparent about your budget and seek to understand their pricing structure. Look for options that provide flexibility, such as volume discounts or favorable payment terms, which can enhance your cash flow management.
- Volume Discounts: Inquire about pricing reductions for larger orders.
- Payment Terms: Negotiate terms that align with your financial capabilities.
Step 7: Establish Clear Communication Channels
Effective communication is crucial throughout the sourcing process. Ensure that you establish clear lines of communication with your supplier for updates, inquiries, and potential issues that may arise. This proactive approach fosters a strong working relationship and helps resolve any concerns quickly.
- Point of Contact: Designate a reliable contact person for both parties.
- Regular Updates: Schedule periodic check-ins to discuss order status and any modifications needed.
By following this comprehensive checklist, international B2B buyers can make informed decisions when sourcing patch panels, ensuring quality, compatibility, and value in their purchases.
Comprehensive Cost and Pricing Analysis for patch panel manufacturer Sourcing
What Are the Key Cost Components in Sourcing Patch Panels?
When sourcing patch panels from manufacturers, understanding the cost structure is essential for making informed purchasing decisions. The main components influencing the overall cost include:
-
Materials: The type of materials used, such as steel or plastic for the housing and copper or fiber for the connections, directly impacts the cost. High-quality materials that meet international standards typically command a higher price.
-
Labor: Labor costs can vary significantly depending on the region of the manufacturer. In countries with lower labor costs, like Vietnam or parts of South America, you might find more competitive pricing. However, ensure that labor quality aligns with your product requirements.
-
Manufacturing Overhead: This includes utilities, equipment maintenance, and facility costs. Efficient manufacturing processes can reduce overhead costs, which can be passed on to buyers.
-
Tooling: Initial setup costs for molds and specialized equipment can be significant, especially for custom patch panels. These costs are typically amortized over production runs, so larger orders can benefit from lower per-unit tooling costs.
-
Quality Control (QC): Investing in rigorous QC processes ensures that the patch panels meet required specifications and certifications. While this can increase upfront costs, it mitigates risks associated with product failures in the field.
-
Logistics: Shipping costs can vary based on distance, weight, and the chosen Incoterms. Understanding the implications of Incoterms such as FOB (Free on Board) or CIF (Cost, Insurance, and Freight) is crucial for accurate cost forecasting.
-
Margin: Manufacturers will also factor in their profit margins, which can vary based on market demand, competition, and perceived value of the product.
How Do Price Influencers Affect Patch Panel Sourcing?
Several factors can influence the pricing of patch panels, and being aware of these can help international buyers negotiate better deals:
-
Volume/MOQ: Manufacturers often have a Minimum Order Quantity (MOQ). Larger orders can lead to price reductions due to economies of scale. Consider consolidating orders across different product lines to meet MOQs.
-
Specifications and Customization: Custom features or specifications can significantly increase costs. Standardized products are generally cheaper, so assess whether customization is necessary for your application.
-
Materials and Quality Certifications: Products that comply with international quality standards (e.g., ISO certifications) may be priced higher but offer long-term reliability. Ensure that the materials used align with your performance expectations.
-
Supplier Factors: Reputation, experience, and reliability of the supplier can impact pricing. Established suppliers may charge more due to their track record, but they often provide better support and quality assurance.
-
Incoterms: The chosen Incoterms can affect the overall cost of ownership. Understanding these terms can help you manage risk and unexpected costs associated with shipping and customs.
What Are the Best Tips for Buyers to Optimize Patch Panel Costs?
-
Negotiate Wisely: Always engage in negotiation to understand the flexibility in pricing. Discuss potential discounts for larger orders or long-term contracts.
-
Focus on Cost-Efficiency: Evaluate the Total Cost of Ownership (TCO) rather than just the initial purchase price. Consider installation costs, maintenance, and potential downtime associated with lower-quality products.
-
Research and Compare Suppliers: Take the time to research multiple suppliers. Request samples to compare quality and service levels, and ensure you are making an informed choice.
-
Understand Pricing Nuances: Be aware that international buyers may face additional costs such as tariffs, taxes, or fluctuations in currency. Budget for these factors when evaluating prices.
-
Utilize Local Networks: Leverage local industry networks or trade organizations that can provide insights into reputable suppliers and prevailing market prices.
Disclaimer on Indicative Prices
The pricing analysis provided here is indicative and can fluctuate based on market dynamics, currency exchange rates, and specific buyer-supplier negotiations. It is advisable for buyers to conduct thorough due diligence and request formal quotes tailored to their specific needs.
Alternatives Analysis: Comparing patch panel manufacturer With Other Solutions
Understanding the Importance of Alternative Solutions in Networking Infrastructure
When considering the infrastructure of networking systems, international B2B buyers must evaluate various solutions to optimize performance and cost-effectiveness. While patch panels are a widely adopted solution for managing and organizing network cables, alternative technologies may offer unique benefits that could better suit specific operational needs. This section explores two viable alternatives: network switches and wireless networking systems.
Comparison Table of Patch Panel Manufacturer and Alternatives
Comparison Aspect | Patch Panel Manufacturer | Network Switch | Wireless Networking System |
---|---|---|---|
Performance | High | Very High | Moderate to High |
Cost | Moderate | Higher | Variable |
Ease of Implementation | Moderate | Moderate to High | Easy |
Maintenance | Low | Moderate | Low |
Best Use Case | Structured cabling | High-density environments | Flexible environments |
What Are the Advantages and Disadvantages of Network Switches?
Network switches are essential components in modern networking, providing high-speed data transfer between devices. Their performance is superior to that of patch panels, especially in environments with high data traffic. However, the initial cost can be higher, and while they require a moderate level of expertise to implement, they also need periodic maintenance to ensure optimal functioning. Network switches are ideal for businesses that require rapid data transfer and have a high density of connected devices, such as data centers or tech companies.
How Do Wireless Networking Systems Compare to Patch Panels?
Wireless networking systems offer the advantage of mobility and flexibility, eliminating the need for extensive cabling. This can greatly reduce installation time and costs, making them appealing for businesses looking for a quick solution. However, wireless systems typically provide moderate to high performance but may be susceptible to interference and signal degradation in densely populated areas. They are best suited for environments where flexibility is paramount, such as offices and retail spaces, allowing for easy movement of devices and personnel without the constraints of wired connections.
How Can B2B Buyers Choose the Right Networking Solution?
In selecting the right solution for their networking needs, B2B buyers should assess their specific operational requirements, including performance expectations, budget constraints, and the physical environment of their operations. For businesses in Africa, South America, the Middle East, and Europe, the choice may hinge on the existing infrastructure and future scalability. Patch panels may be ideal for structured cabling environments, while network switches are better suited for high-density data applications. Conversely, wireless systems provide unparalleled flexibility, making them a strong choice for dynamic workspaces. Ultimately, a thorough understanding of each solution’s strengths and weaknesses will empower buyers to make informed decisions that align with their organizational goals.
Essential Technical Properties and Trade Terminology for patch panel manufacturer
Understanding the technical specifications and trade terminology associated with patch panels is crucial for international B2B buyers. This knowledge not only aids in making informed purchasing decisions but also ensures compliance with industry standards. Below are some essential technical properties and common trade terms that every buyer should be familiar with.
What Are the Key Technical Properties of Patch Panels?
1. Material Grade: Why Does It Matter?
Patch panels are typically constructed from materials like steel, aluminum, or high-grade plastic. The choice of material affects durability, weight, and electromagnetic interference (EMI) shielding. For B2B buyers, selecting a patch panel with the right material grade can significantly impact network reliability and longevity, particularly in environments with high electromagnetic activity.
2. Tolerance Levels: How Do They Affect Performance?
Tolerance refers to the allowable deviation in dimensions and spacing within the patch panel. High tolerance levels are critical for ensuring proper fit and function of connectors and cables. For buyers, understanding tolerance can mean the difference between seamless connectivity and network failures, particularly in high-density environments.
3. Port Density: What Is the Importance of Density?
Port density defines the number of ports available on a patch panel, which can range from a few to several dozen. Higher port density is essential for maximizing space in server racks and data centers. For international buyers, choosing the right port density aligns with future scalability and current network demands.
4. Compatibility Standards: Why Are They Necessary?
Patch panels must meet various compatibility standards, such as TIA/EIA-568 and ISO/IEC 11801. These standards ensure that the patch panel will work effectively with other networking equipment. For B2B buyers, understanding these standards is critical to ensure interoperability and compliance with local regulations.
5. Mounting Style: Which Is Right for Your Needs?
Patch panels come in different mounting styles, including rack-mounted and wall-mounted options. The choice between these depends on space availability and installation preferences. For buyers, understanding the implications of mounting styles can optimize both installation and future maintenance efforts.
What Are the Common Trade Terms Used in the Patch Panel Industry?
1. What Is an OEM and Why Should You Care?
OEM stands for Original Equipment Manufacturer. In the context of patch panels, this term refers to companies that produce components that are then sold under another brand. Understanding OEM relationships can help buyers identify quality assurance and reliability in the products they purchase.
2. What Does MOQ Mean in Patch Panel Orders?
MOQ, or Minimum Order Quantity, is the smallest number of units a supplier is willing to sell. For international buyers, knowing the MOQ is essential for budgeting and inventory management. This term can significantly impact procurement strategies, especially for smaller businesses.
3. How Important Is an RFQ in the Purchasing Process?
RFQ stands for Request for Quotation. It is a formal process where buyers request pricing and terms from suppliers. For B2B buyers, issuing an RFQ can lead to competitive pricing and better negotiation terms, making it a critical step in the purchasing process.
4. What Are Incoterms and How Do They Affect Shipping?
Incoterms, or International Commercial Terms, are standardized rules that define the responsibilities of buyers and sellers regarding shipping, insurance, and tariffs. Understanding these terms is vital for international buyers to avoid unexpected costs and ensure smooth transactions.
5. What Is Lead Time and Why Is It Significant?
Lead time refers to the time taken from placing an order to receiving the product. For buyers, understanding lead time is crucial for project planning and inventory management, especially in industries where downtime can be costly.
By familiarizing themselves with these essential technical properties and trade terms, international B2B buyers can make informed decisions when sourcing patch panels, ultimately leading to more effective network solutions.
Navigating Market Dynamics and Sourcing Trends in the patch panel manufacturer Sector
What Are the Current Market Dynamics and Key Trends in the Patch Panel Manufacturing Sector?
The global patch panel manufacturing sector is experiencing significant transformation, driven by technological advancements and the increasing demand for efficient network infrastructure. Key drivers include the proliferation of data centers, the rise of IoT devices, and the ongoing expansion of 5G networks. These factors have created a surge in demand for high-quality, reliable patch panels that can support complex network setups.
Emerging trends in B2B sourcing are leaning towards integrated solutions that offer scalability and flexibility. International buyers, particularly from Africa, South America, the Middle East, and Europe, should be aware of the shift towards smart patch panels equipped with monitoring capabilities. This innovation allows for real-time diagnostics and management of network traffic, enhancing operational efficiency and reducing downtime.
Moreover, the growing focus on automation in manufacturing processes is impacting sourcing strategies. International B2B buyers should consider manufacturers that utilize advanced robotics and AI in their production lines, as these technologies can lead to improved quality control and faster turnaround times. Understanding these dynamics will enable buyers to make informed decisions and optimize their procurement processes.
How Does Sustainability and Ethical Sourcing Impact the Patch Panel Manufacturing Sector?
In today’s marketplace, sustainability and ethical sourcing are becoming pivotal considerations for B2B buyers. The environmental impact of manufacturing processes is under scrutiny, prompting manufacturers to adopt greener practices. Buyers from regions like Africa and South America are increasingly prioritizing suppliers who demonstrate a commitment to reducing carbon footprints through energy-efficient production and responsible waste management.
The importance of ethical supply chains cannot be overstated. Buyers should look for manufacturers that maintain transparency in their sourcing practices and comply with international labor standards. Certifications such as ISO 14001 for environmental management and Fair Trade for ethical labor practices are critical indicators of a manufacturer’s commitment to sustainability.
Additionally, the use of eco-friendly materials in patch panel production is gaining traction. Buyers should inquire about the availability of products made from recycled or sustainably sourced materials. This not only aligns with global sustainability goals but also resonates with end-users who are increasingly making purchase decisions based on environmental considerations.
What Is the Brief Evolution of the Patch Panel Manufacturing Sector?
The patch panel manufacturing sector has evolved significantly over the past few decades. Initially, patch panels were simple devices used primarily in telecommunications to manage connections. However, the advent of the internet and the explosion of digital communication technologies transformed their functionality.
With the rise of structured cabling systems in the 1990s, patch panels became integral components in modern network infrastructures. This evolution has led to the development of more sophisticated patch panels that incorporate advanced features such as modular designs and integrated network management capabilities. Today, these devices are essential for efficient data management and connectivity in various sectors, including telecommunications, data centers, and enterprise networks.
Understanding this evolution helps B2B buyers appreciate the technological advancements and the importance of selecting suppliers that can provide cutting-edge solutions to meet contemporary networking challenges.
Frequently Asked Questions (FAQs) for B2B Buyers of patch panel manufacturer
-
How do I choose the right patch panel manufacturer for my business needs?
Selecting the right patch panel manufacturer involves assessing several key factors. Look for manufacturers with a proven track record in your industry, as well as positive reviews and testimonials from previous clients. Evaluate their product range to ensure they offer the specific types of patch panels that meet your technical requirements. Additionally, consider their production capabilities and compliance with international quality standards, which are crucial for reliability and performance in diverse environments. -
What customization options should I expect from patch panel manufacturers?
Most reputable patch panel manufacturers offer customization options to cater to specific business needs. This can include variations in port configurations, labeling, and materials. Additionally, inquire about the possibility of bespoke designs that align with your network infrastructure requirements. Customization can also extend to packaging and branding, ensuring that the product fits seamlessly into your operational workflow and enhances your brand image in the market. -
What are the minimum order quantities (MOQ) when sourcing patch panels?
Minimum order quantities (MOQ) can vary significantly among manufacturers. Typically, larger manufacturers may have higher MOQs due to their production processes, while smaller or specialized manufacturers might offer lower MOQs. When negotiating, clarify your expected order volumes and discuss potential flexibility, especially if you are a new buyer. Understanding the MOQ is crucial for budgeting and inventory management, particularly in regions where storage space is limited. -
What payment terms should I negotiate with patch panel suppliers?
When engaging with patch panel suppliers, it is essential to discuss payment terms upfront. Common options include upfront payments, partial payments upon order confirmation, and the balance upon delivery. Consider negotiating favorable terms that align with your cash flow, such as extended payment periods or discounts for early payment. Be sure to discuss the currency of transaction and any potential fees that may arise from international banking. -
How do I ensure quality assurance in my patch panel orders?
To ensure quality assurance, request detailed specifications and certifications from the manufacturer, such as ISO 9001 or relevant industry standards. It’s also beneficial to establish a quality control process that includes pre-shipment inspections and testing of samples before bulk orders. Collaborating with manufacturers that have a transparent quality assurance process will help mitigate risks associated with defective products, ultimately safeguarding your business reputation. -
What logistics considerations should I keep in mind when importing patch panels?
Logistics play a crucial role in international sourcing. Consider factors such as shipping methods, lead times, and customs regulations in your country. Collaborate with logistics providers experienced in handling electronic components to navigate potential challenges. Additionally, factor in costs related to shipping, tariffs, and insurance to ensure that your total landed costs align with your budget. Understanding these logistics elements will help streamline your supply chain and reduce delays. -
How can I vet a patch panel manufacturer before placing an order?
Vetting a patch panel manufacturer involves conducting thorough research. Start by reviewing their website, product catalogs, and customer testimonials. Request references and case studies from similar businesses in your region. It’s advisable to initiate direct communication to assess their responsiveness and willingness to provide additional information. Visiting their facility, if feasible, or engaging with third-party verification services can further enhance your confidence in their capabilities and reliability. -
What are the common challenges faced when sourcing patch panels internationally?
Sourcing patch panels internationally may present challenges such as cultural differences, language barriers, and varying quality standards. Additionally, navigating international shipping logistics and understanding local customs regulations can complicate the process. To mitigate these challenges, establish clear communication with suppliers, utilize professional translation services if necessary, and stay informed about the regulatory landscape in both your country and the manufacturer’s location. Building strong relationships with reliable suppliers will also help in overcoming these hurdles.
Important Disclaimer & Terms of Use
⚠️ Important Disclaimer
The information provided in this guide, including content regarding manufacturers, technical specifications, and market analysis, is for informational and educational purposes only. It does not constitute professional procurement advice, financial advice, or legal advice.
While we have made every effort to ensure the accuracy and timeliness of the information, we are not responsible for any errors, omissions, or outdated information. Market conditions, company details, and technical standards are subject to change.
B2B buyers must conduct their own independent and thorough due diligence before making any purchasing decisions. This includes contacting suppliers directly, verifying certifications, requesting samples, and seeking professional consultation. The risk of relying on any information in this guide is borne solely by the reader.
Strategic Sourcing Conclusion and Outlook for patch panel manufacturer
In today’s rapidly evolving telecommunications landscape, strategic sourcing of patch panels is essential for international B2B buyers. By prioritizing quality, cost-efficiency, and supplier reliability, companies can enhance their network infrastructure while minimizing operational risks. Buyers from regions such as Africa, South America, the Middle East, and Europe must focus on selecting manufacturers that not only meet technical specifications but also understand regional market dynamics and compliance requirements.
What are the key factors influencing your sourcing decisions for patch panels? Evaluate potential suppliers based on their production capabilities, lead times, and after-sales support. Additionally, establishing long-term partnerships with manufacturers can facilitate better pricing agreements and ensure access to the latest technologies.
Looking ahead, as the demand for advanced networking solutions continues to grow, international buyers must remain proactive in their sourcing strategies. Engage with manufacturers who are innovative and adaptable to changing market needs. By doing so, you position your business to leverage emerging opportunities and drive sustainable growth in an increasingly competitive environment. Take the next step today: assess your sourcing strategy and explore partnerships that align with your long-term objectives.