Discover Top Benefits of Choosing a Pulley Manufacturer (2025)
Introduction: Navigating the Global Market for pulley manufacturer
Navigating the global market for pulley manufacturers can be a daunting task for international B2B buyers, especially when sourcing high-quality products that meet specific operational needs. As industries worldwide increasingly rely on efficient machinery and equipment, understanding the nuances of pulley systems becomes crucial. This guide aims to provide comprehensive insights into the types of pulleys available, their various applications across different sectors, and the critical factors to consider when vetting suppliers.
With a focus on empowering B2B buyers from Africa, South America, the Middle East, and Europe—particularly in countries like Poland and Italy—this resource offers actionable strategies to enhance purchasing decisions. From evaluating cost structures to understanding material specifications and compliance standards, our guide equips buyers with the knowledge necessary to navigate supplier landscapes effectively.
Furthermore, we delve into the latest trends in the pulley manufacturing industry, including technological advancements and sustainability practices, ensuring that your procurement strategy aligns with global market expectations. By leveraging the insights provided in this guide, you can make informed choices that optimize performance and drive operational success in your business.
Understanding pulley manufacturer Types and Variations
Type Name | Key Distinguishing Features | Primary B2B Applications | Brief Pros & Cons for Buyers |
---|---|---|---|
Block Pulleys | Composed of two or more pulleys; offers mechanical advantage | Construction, shipping, and rigging | Pros: High load capacity; efficient. Cons: Can be bulky and require more space. |
Sheave Pulleys | Features a grooved wheel; often used in belt systems | Manufacturing, automotive, and conveyor systems | Pros: Reduces wear on belts; versatile. Cons: Requires precise alignment for optimal performance. |
Fixed Pulleys | Mounted in a stationary position; simple design | Elevators, cranes, and hoisting systems | Pros: Easy to install; minimal maintenance. Cons: Limited mechanical advantage. |
Movable Pulleys | Can move with the load; provides a mechanical advantage | Lifting heavy equipment and materials | Pros: Reduces effort needed to lift; enhances efficiency. Cons: More complex setup required. |
Compound Pulleys | Combination of fixed and movable pulleys; maximizes efficiency | Industrial lifting and heavy machinery | Pros: Significant mechanical advantage; effective for heavy loads. Cons: More expensive and complex to install. |
What Are Block Pulleys and Their Applications?
Block pulleys consist of multiple pulleys mounted on a frame, allowing for the lifting of heavy loads with reduced effort. Their design provides a mechanical advantage, making them ideal for construction, shipping, and rigging applications. When purchasing block pulleys, buyers should consider the load capacity, available space for installation, and the specific lifting needs of their operations.
How Do Sheave Pulleys Function in B2B Settings?
Sheave pulleys are designed with a grooved wheel, primarily used in belt systems to redirect motion and reduce wear. They find applications in manufacturing, automotive, and conveyor systems, where efficiency and longevity are crucial. B2B buyers should evaluate the alignment requirements and compatibility with existing systems when considering sheave pulleys for their operations.
What Are the Benefits of Fixed Pulleys?
Fixed pulleys are mounted in a stationary position, providing a straightforward lifting mechanism. They are commonly used in elevators, cranes, and hoisting systems. Their simplicity means they are easy to install and require minimal maintenance. Buyers should assess the specific lifting tasks and whether the limited mechanical advantage suits their needs before opting for fixed pulleys.
Why Choose Movable Pulleys for Heavy Lifting?
Movable pulleys can shift with the load, providing a mechanical advantage that significantly reduces the effort required to lift heavy items. They are particularly effective for lifting equipment and materials in various industrial sectors. When purchasing movable pulleys, buyers should consider the complexity of the setup and ensure they have the necessary space and resources to implement them effectively.
What Makes Compound Pulleys Effective for Industrial Use?
Compound pulleys combine fixed and movable pulleys to maximize lifting efficiency, making them suitable for industrial lifting and heavy machinery applications. They offer a significant mechanical advantage, which is beneficial for handling heavy loads. However, their complexity and higher cost should be weighed against the operational benefits they can provide when evaluating options for purchase.
Related Video: Common 13 Types of Sheet Metal Fabrication Techniques
Key Industrial Applications of pulley manufacturer
Industry/Sector | Specific Application of pulley manufacturer | Value/Benefit for the Business | Key Sourcing Considerations for this Application |
---|---|---|---|
Construction | Hoisting Systems for Heavy Equipment | Increases efficiency in lifting heavy materials | Durability, load capacity, and compliance with safety standards |
Mining | Conveyor Systems for Material Transport | Streamlines material movement, reducing labor costs | Resistance to harsh environments and wear resistance |
Manufacturing | Automated Assembly Lines | Enhances production speed and accuracy | Precision engineering and customization options |
Agriculture | Irrigation Systems and Machinery | Optimizes resource usage and crop yield | Adaptability to various terrains and climates |
Marine and Shipping | Cargo Handling Systems on Ships | Improves loading/unloading efficiency | Corrosion resistance and compliance with maritime regulations |
How is ‘Pulley Manufacturer’ Used in the Construction Industry?
In the construction sector, pulleys are integral to hoisting systems that facilitate the lifting of heavy materials, such as steel beams and concrete blocks. By utilizing robust pulley systems, construction companies can significantly enhance their operational efficiency, ensuring projects are completed on time and within budget. International buyers, particularly from regions like Africa and South America, must prioritize sourcing durable pulleys that comply with local safety regulations and can withstand the rigors of heavy-duty use.
What Role Do Pulleys Play in Mining Operations?
Pulleys are essential in mining for conveyor systems that transport materials from extraction sites to processing facilities. This application minimizes manual handling, thereby reducing labor costs and improving safety. Buyers in the mining sector, especially in the Middle East and Europe, should consider sourcing pulleys that are designed to endure extreme conditions, such as dust and moisture, ensuring long-term reliability and minimal downtime.
How Are Pulleys Utilized in Manufacturing Processes?
In manufacturing, pulleys are critical components of automated assembly lines, where they facilitate the movement of products through various stages of production. This application not only speeds up the manufacturing process but also enhances accuracy and consistency in product quality. B2B buyers in Europe, particularly in Poland and Italy, should seek manufacturers that offer precision-engineered pulleys tailored to specific production requirements, ensuring optimal performance and integration with existing systems.
What is the Importance of Pulleys in Agriculture?
Pulleys are used in agricultural machinery, particularly in irrigation systems, where they help in the efficient distribution of water resources. By optimizing irrigation, farmers can enhance crop yields while conserving water. For buyers in Africa and South America, selecting pulleys that are adaptable to different terrains and climatic conditions is crucial for maximizing agricultural productivity and sustainability.
How Do Pulleys Benefit Marine and Shipping Industries?
In the marine and shipping industries, pulleys are vital for cargo handling systems that streamline the loading and unloading of goods. This application significantly boosts operational efficiency, reducing turnaround times at ports. International buyers need to prioritize sourcing corrosion-resistant pulleys that meet maritime safety regulations, ensuring reliability and longevity in harsh marine environments.
Related Video: What are all the Laboratory Apparatus and their uses?
3 Common User Pain Points for ‘pulley manufacturer’ & Their Solutions
Scenario 1: Inconsistent Quality in Pulley Manufacturing
The Problem: International B2B buyers often face significant challenges regarding the quality consistency of pulleys from manufacturers. This inconsistency can lead to operational inefficiencies, increased maintenance costs, and safety concerns. For instance, a construction company in South Africa might source pulleys from different suppliers, only to find that some products do not meet the required specifications, resulting in delays and potential project failures.
The Solution: To mitigate these quality issues, B2B buyers should implement a robust supplier evaluation process before committing to any manufacturer. Start by requesting detailed product specifications, certifications, and quality assurance processes from potential suppliers. Additionally, consider conducting site visits or audits to assess manufacturing capabilities firsthand. Establish clear quality benchmarks and engage in regular communication with suppliers to ensure alignment. Building long-term relationships with reputable manufacturers who have a proven track record can also enhance product quality and consistency.
Scenario 2: Complex Sourcing Processes for Specialized Pulleys
The Problem: Sourcing specialized pulleys that cater to unique operational requirements can be daunting for B2B buyers. For example, a manufacturing plant in Italy may require custom pulleys for a specific machinery setup, but the complexity of sourcing from overseas can lead to lengthy lead times and increased costs. This challenge is exacerbated when buyers are not familiar with the technical specifications needed for their specific applications.
The Solution: To streamline the sourcing process for specialized pulleys, buyers should begin with a detailed assessment of their operational needs, including load requirements, environmental conditions, and compatibility with existing systems. Engage with manufacturers that offer customization options and are open to collaboration. Utilize platforms that connect buyers with specialized manufacturers, facilitating direct communication regarding technical requirements. Additionally, consider leveraging local distributors who may have established relationships with manufacturers, thus simplifying the logistics and reducing lead times.
Scenario 3: Lack of Technical Support and After-Sales Service
The Problem: After purchasing pulleys, many international buyers face a lack of technical support and after-sales service. This can create challenges when issues arise during installation or operation. For instance, a construction firm in the Middle East might install a new pulley system but encounter unforeseen operational difficulties without access to timely support from the manufacturer, potentially leading to project delays and additional costs.
The Solution: To address this pain point, buyers should prioritize manufacturers that provide comprehensive technical support and after-sales service. When evaluating suppliers, inquire about their customer service policies, including the availability of technical assistance, training resources, and warranty terms. Establish clear channels of communication for troubleshooting and support. It can also be beneficial to request case studies or testimonials from other clients regarding their experiences with the manufacturer’s support services. Engaging in a partnership with a manufacturer who is committed to ongoing support can significantly enhance operational efficiency and reduce downtime.
By recognizing these common pain points and implementing the proposed solutions, international B2B buyers can enhance their purchasing strategies for pulleys, ensuring they secure high-quality products tailored to their specific needs while fostering strong supplier relationships.
Strategic Material Selection Guide for pulley manufacturer
What are the Key Properties of Common Materials Used in Pulley Manufacturing?
When selecting materials for pulleys, it is crucial to consider their mechanical properties, environmental resistance, and suitability for specific applications. Here, we analyze four common materials used in pulley manufacturing: steel, aluminum, plastic, and composite materials. Each has unique characteristics that can significantly impact performance and cost-effectiveness.
How Does Steel Perform as a Material for Pulleys?
Key Properties: Steel is renowned for its high tensile strength and durability, making it ideal for heavy-duty applications. It typically offers excellent temperature and pressure ratings, allowing it to withstand extreme conditions.
Pros & Cons: The primary advantage of steel pulleys is their exceptional strength and longevity. However, they can be susceptible to corrosion if not properly treated, which may necessitate additional coatings or finishes. Steel is generally more expensive than plastic but offers superior performance, particularly in high-load applications.
Impact on Application: Steel is compatible with a wide range of media, including water, oil, and various chemicals, making it versatile for different industries. However, its weight can be a disadvantage in applications where reducing overall weight is critical.
Considerations for International Buyers: B2B buyers in regions like Africa and South America should ensure compliance with local standards, such as ASTM or DIN. In Europe, buyers may prefer steel that meets specific environmental regulations, particularly regarding corrosion resistance.
What Advantages Does Aluminum Offer for Pulley Manufacturing?
Key Properties: Aluminum is lightweight and has good corrosion resistance, which is beneficial in environments where moisture or chemicals are present. It also has a decent strength-to-weight ratio, making it suitable for many applications.
Pros & Cons: The main advantage of aluminum pulleys is their lightweight nature, which can lead to reduced energy consumption in mechanical systems. However, aluminum is generally less durable than steel, especially under heavy loads, and can be more expensive due to the manufacturing processes involved.
Impact on Application: Aluminum is suitable for applications involving corrosive environments, such as marine or chemical industries. Its lower weight can also be advantageous in applications where speed and efficiency are paramount.
Considerations for International Buyers: Buyers in the Middle East and Europe should be aware of the specific grades of aluminum required for their applications, as well as compliance with local manufacturing standards.
Why Choose Plastic for Pulley Applications?
Key Properties: Plastic materials, such as nylon or polypropylene, are lightweight and offer good chemical resistance. They can perform well in moderate temperature and load conditions.
Pros & Cons: Plastic pulleys are cost-effective and can be produced quickly, making them suitable for high-volume applications. However, they generally have lower strength compared to metal options, which can limit their use in high-load scenarios.
Impact on Application: Plastic is ideal for applications where weight savings are essential, such as in the automotive or consumer goods industries. They are also suitable for environments where corrosion is a concern.
Considerations for International Buyers: Buyers in South America should consider the specific types of plastics available locally and their compliance with international standards, particularly in food or medical applications.
What Role Do Composite Materials Play in Pulley Manufacturing?
Key Properties: Composite materials combine the benefits of different materials, offering high strength while remaining lightweight. They often exhibit excellent fatigue resistance and can be tailored to specific performance requirements.
Pros & Cons: The primary advantage of composites is their versatility and high performance in specialized applications. However, they can be more expensive to manufacture and may require specific handling and installation practices.
Impact on Application: Composites are suitable for high-performance applications, such as aerospace or advanced manufacturing, where traditional materials may not suffice.
Considerations for International Buyers: Buyers from Europe, particularly in sectors like aerospace, should ensure that composite materials meet stringent safety and quality standards.
Summary Table of Material Selection for Pulley Manufacturing
Material | Typical Use Case for pulley manufacturer | Key Advantage | Key Disadvantage/Limitation | Relative Cost (Low/Med/High) |
---|---|---|---|---|
Steel | Heavy-duty industrial applications | Exceptional strength and durability | Susceptible to corrosion | High |
Aluminum | Lightweight machinery and automotive | Lightweight, good corrosion resistance | Less durable under heavy loads | Medium |
Plastic | Consumer goods and moderate load systems | Cost-effective, lightweight | Lower strength compared to metals | Low |
Composite | Aerospace and advanced manufacturing | High performance and tailored properties | Higher manufacturing costs | High |
This strategic material selection guide aims to equip international B2B buyers with the necessary insights to make informed decisions regarding pulley manufacturing materials, ensuring compliance with regional standards while optimizing performance and cost.
In-depth Look: Manufacturing Processes and Quality Assurance for pulley manufacturer
What Are the Main Stages in the Manufacturing Process of Pulleys?
When it comes to manufacturing pulleys, understanding the primary stages can help B2B buyers assess potential suppliers more effectively. The manufacturing process generally involves several key stages: material preparation, forming, assembly, and finishing.
-
Material Preparation: This initial stage involves selecting the right materials for the pulley, which typically include metals such as steel, aluminum, or composite materials. Suppliers must ensure that the materials meet specific mechanical properties and corrosion resistance standards. Proper material selection is critical, as it affects the pulley’s strength and longevity.
-
Forming: During this phase, raw materials are shaped into the desired pulley form. Techniques such as machining, casting, or forging are commonly employed. For instance, CNC machining allows for high precision in the creation of complex pulley designs. The choice of forming technique will depend on the pulley size, shape, and intended application.
-
Assembly: In this stage, different components of the pulley are brought together. This may include the integration of bearings, grooves, or other features that enhance functionality. Efficient assembly practices are crucial to ensure that each pulley operates smoothly and meets quality standards.
-
Finishing: The final stage involves surface treatment processes such as anodizing, powder coating, or plating. These treatments not only enhance the aesthetic appeal but also provide additional protection against wear and corrosion. Effective finishing processes are vital for ensuring the durability and performance of the pulley in various environments.
Which Key Techniques Are Used in Pulley Manufacturing?
Understanding the manufacturing techniques used in pulley production can provide valuable insights for international B2B buyers. Here are some of the most critical techniques:
-
CNC Machining: This technique utilizes computer-controlled machines for high precision in cutting and shaping the material. It is particularly beneficial for producing complex designs that require tight tolerances.
-
Casting: Often used for larger pulleys, casting involves pouring molten metal into a mold to create the desired shape. This method is cost-effective for high-volume production.
-
Forging: This process involves shaping metal through compressive forces, resulting in a stronger product due to the grain structure of the metal being aligned. Forged pulleys are typically more durable and better suited for heavy-duty applications.
-
Welding: For pulleys that require multiple parts to be joined together, welding is a common technique. It is essential for ensuring the structural integrity of the assembled pulley.
What Quality Assurance Standards Should B2B Buyers Expect from Pulley Manufacturers?
Quality assurance is paramount in ensuring that pulleys meet safety and performance standards. International standards such as ISO 9001 are essential benchmarks for B2B buyers. This standard focuses on quality management systems and is applicable across industries.
In addition to ISO certifications, buyers should look for industry-specific certifications, such as:
- CE Marking: Ensures that products meet EU safety, health, and environmental protection standards.
- API Certification: Relevant for pulleys used in the oil and gas industry, ensuring compliance with stringent performance standards.
How Are Quality Control Checkpoints Structured in Pulley Manufacturing?
Quality control (QC) is typically structured around several checkpoints during the manufacturing process:
-
Incoming Quality Control (IQC): This initial checkpoint involves inspecting raw materials for compliance with specifications before they enter the manufacturing process. Ensuring high-quality materials is critical for the final product’s performance.
-
In-Process Quality Control (IPQC): During manufacturing, continuous monitoring of processes and materials is conducted. This includes checking dimensions, tolerances, and surface finishes at various stages of production.
-
Final Quality Control (FQC): After assembly and finishing, pulleys undergo final inspections to verify that they meet all design specifications and quality standards. This may involve functional testing and dimensional checks.
What Common Testing Methods Are Used in Pulley Quality Assurance?
To ensure the reliability and performance of pulleys, various testing methods are employed:
-
Load Testing: This method assesses the pulley’s ability to bear loads without failure, crucial for applications in lifting and transportation.
-
Visual Inspection: A thorough visual check for surface defects, alignment issues, and overall craftsmanship is essential for maintaining high-quality standards.
-
Non-Destructive Testing (NDT): Techniques such as ultrasonic testing or magnetic particle inspection can detect internal flaws without damaging the pulley, ensuring structural integrity.
How Can B2B Buyers Verify Supplier Quality Control Processes?
For international B2B buyers, verifying a supplier’s quality control processes is crucial. Here are actionable steps to consider:
-
Supplier Audits: Conducting on-site audits can provide valuable insights into a supplier’s manufacturing practices, quality assurance protocols, and overall operational efficiency.
-
Requesting Quality Reports: Suppliers should be willing to provide documentation of their quality control processes, including testing results, certifications, and compliance with relevant standards.
-
Third-Party Inspections: Engaging independent inspection agencies can offer an unbiased evaluation of the supplier’s quality control measures, ensuring that they meet international standards.
What Are the Quality Control Nuances for International B2B Buyers?
When sourcing pulleys from international suppliers, particularly in regions like Africa, South America, the Middle East, and Europe, buyers should be aware of the following nuances:
-
Cultural Differences: Understanding cultural attitudes towards quality and customer service can affect negotiations and expectations. Building strong relationships with suppliers can facilitate better communication and adherence to quality standards.
-
Regulatory Compliance: Different regions may have varying regulatory requirements. Buyers should ensure that suppliers are compliant with local and international regulations that apply to their products.
-
Logistical Considerations: Quality assurance is not just about manufacturing; it also extends to how products are packaged and shipped. Ensuring that pulleys are adequately protected during transport is vital for maintaining quality upon arrival.
By focusing on these aspects, international B2B buyers can make informed decisions when selecting pulley manufacturers, ensuring that they partner with suppliers who prioritize quality and compliance in their manufacturing processes.
Practical Sourcing Guide: A Step-by-Step Checklist for ‘pulley manufacturer’
In the competitive landscape of manufacturing, sourcing the right pulley manufacturer is crucial for ensuring operational efficiency and product quality. This guide provides a structured checklist for international B2B buyers, particularly those in Africa, South America, the Middle East, and Europe, to follow when procuring pulleys. By adhering to these steps, buyers can mitigate risks and establish fruitful partnerships.
Step 1: Define Your Technical Specifications
Before reaching out to potential suppliers, it’s essential to clearly outline your technical requirements. This includes the type of pulleys you need, materials, dimensions, and load capacities. Having a detailed specification helps suppliers provide accurate quotes and ensures that the products meet your operational needs.
- Consider the application: Are the pulleys for industrial machinery, automotive use, or another application?
- Material requirements: Will you need steel, aluminum, or plastic pulleys? Each material has different properties and costs.
Step 2: Research Potential Suppliers
Conduct thorough research to identify potential manufacturers. Look for companies with a proven track record and positive reviews from previous clients. Online platforms like industry-specific directories and trade associations can be excellent resources for finding reputable suppliers.
- Check their online presence: A well-maintained website with detailed product information often indicates professionalism.
- Look for industry certifications: Certifications can signify adherence to quality standards.
Step 3: Evaluate Supplier Capabilities
Once you have a shortlist of suppliers, assess their manufacturing capabilities. This includes understanding their production processes, technology, and capacity to meet your demands.
- Inquire about production capacity: Can they handle large orders or custom designs?
- Ask about quality control measures: What processes do they have in place to ensure product quality?
Step 4: Verify Supplier Certifications
It’s vital to ensure that your chosen supplier holds relevant certifications that comply with international standards. Certifications like ISO 9001 for quality management systems can indicate a commitment to quality and continuous improvement.
- Request documentation: Don’t hesitate to ask for copies of their certifications.
- Understand regional regulations: Ensure they comply with the regulations pertinent to your country or industry.
Step 5: Request Samples
Before finalizing your order, request samples of the pulleys. This step allows you to evaluate the quality and suitability of the products for your specific applications.
- Assess the sample quality: Look for durability, finish, and design.
- Test the samples: If possible, conduct trials to see how the pulleys perform in your operations.
Step 6: Discuss Pricing and Payment Terms
Once you are satisfied with the samples, it’s time to discuss pricing and payment terms. Ensure that you understand all costs involved, including shipping and duties, to avoid surprises later.
- Negotiate terms: Don’t hesitate to negotiate for better pricing, especially for bulk orders.
- Clarify payment methods: Understand the payment options available and the terms for each.
Step 7: Establish Communication Channels
Effective communication is crucial for a successful partnership. Establish clear lines of communication with your supplier to ensure that both parties are aligned on expectations and timelines.
- Agree on contact points: Identify who will be your primary contact on both sides.
- Set regular check-ins: Schedule updates to discuss progress and address any issues promptly.
By following this checklist, international B2B buyers can enhance their sourcing strategy for pulleys, ensuring they select a manufacturer that aligns with their operational needs and quality expectations.
Comprehensive Cost and Pricing Analysis for pulley manufacturer Sourcing
What Are the Key Cost Components in Pulley Manufacturing?
When sourcing pulleys, understanding the cost structure is essential for international B2B buyers. The primary cost components include:
-
Materials: The choice of materials significantly affects the overall cost. Common materials include steel, aluminum, and plastic. Prices can fluctuate based on global commodity markets, so it’s prudent to lock in prices with suppliers.
-
Labor: Labor costs vary by region and are influenced by local wage standards and skill levels. In countries with higher labor costs, such as those in Western Europe, manufacturers may implement automation to offset expenses.
-
Manufacturing Overhead: This encompasses utilities, maintenance, and indirect labor costs. Efficient production processes can help reduce overhead, but buyers should be aware that lower overhead might indicate less investment in quality control.
-
Tooling: Custom tooling can be a significant upfront cost, especially for specialized pulleys. Buyers should evaluate if the tooling costs are amortized over high production volumes to lower per-unit costs.
-
Quality Control (QC): Ensuring high quality is critical, especially for safety-critical applications. Costs associated with QC processes, certifications, and inspections should be factored into the overall pricing.
-
Logistics: Shipping costs can vary widely based on distance, mode of transport, and tariffs. International buyers need to account for logistics costs in their total cost calculations, especially when sourcing from regions like Asia or North America.
-
Margin: Suppliers will add a profit margin to cover their costs and risks. Understanding typical margins within the industry can help buyers gauge whether a quote is reasonable.
How Do Price Influencers Impact Pulley Manufacturing Costs?
Several factors influence the pricing of pulleys, making it essential for buyers to understand these dynamics:
-
Volume and Minimum Order Quantity (MOQ): Higher order volumes often lead to lower prices per unit due to economies of scale. Negotiating MOQs can also yield better pricing, especially for long-term contracts.
-
Specifications and Customization: Custom designs or specific performance requirements can increase costs. Buyers should clarify their needs upfront to avoid unexpected expenses later in the process.
-
Materials and Quality Certifications: The choice of materials and the presence of quality certifications (e.g., ISO, CE) can affect pricing. Higher quality materials and certifications typically command higher prices but can lead to lower failure rates and longer product lifespans.
-
Supplier Factors: The reliability and reputation of the supplier play a significant role in pricing. Established suppliers with strong track records may charge more but offer better service and reliability.
-
Incoterms: The choice of Incoterms (International Commercial Terms) affects cost allocation between buyers and sellers. Understanding these terms can lead to significant savings in logistics and insurance costs.
What Are the Best Buyer Tips for Cost-Efficient Sourcing of Pulleys?
To optimize sourcing strategies, international buyers should consider the following tips:
-
Negotiate Effectively: Don’t accept the first quote. Engage in discussions to find cost-saving opportunities and explore volume discounts or longer-term contracts for better pricing.
-
Evaluate Total Cost of Ownership (TCO): Beyond initial purchase price, consider maintenance, operational costs, and expected lifespan. A lower-priced pulley may result in higher long-term costs if it requires frequent replacements.
-
Understand Pricing Nuances in Different Regions: Prices can vary based on regional factors, including local economic conditions, labor costs, and material availability. Conduct market research specific to the regions you are sourcing from, such as Africa, South America, the Middle East, and Europe.
-
Stay Informed on Market Trends: Keep an eye on global commodity prices and industry trends. Understanding market conditions can empower buyers to negotiate better terms and timing for orders.
Disclaimer on Indicative Prices
All prices mentioned are indicative and may vary based on supplier, material specifications, and market conditions. It is advisable for buyers to obtain detailed quotes tailored to their specific requirements for accurate cost assessments.
Alternatives Analysis: Comparing pulley manufacturer With Other Solutions
When evaluating solutions for material handling and mechanical applications, it’s crucial for B2B buyers to consider various alternatives to pulley manufacturers. This section explores how pulleys stack up against other methods, such as conveyor systems and hoisting mechanisms, providing actionable insights for international buyers from regions like Africa, South America, the Middle East, and Europe.
Comparison Table of Pulley Manufacturers and Alternative Solutions
Comparison Aspect | Pulley Manufacturer | Conveyor System | Hoisting Mechanism |
---|---|---|---|
Performance | High load capacity | Continuous operation | Excellent for vertical lifts |
Cost | Moderate initial cost | Higher installation cost | Varies based on system type |
Ease of Implementation | Simple installation | Requires infrastructure | Moderate complexity |
Maintenance | Low maintenance | Moderate upkeep | High maintenance |
Best Use Case | General mechanical tasks | Bulk material transport | Lifting heavy loads |
How Do Conveyor Systems Compare to Pulley Manufacturers?
Conveyor systems provide a continuous method for moving materials, making them ideal for high-volume applications. One of the significant advantages is their ability to transport goods over long distances without manual effort. However, the initial installation cost can be substantial, and the required infrastructure may not be feasible for all businesses, especially smaller operations in developing regions. Additionally, maintenance can be moderate, requiring regular checks to ensure smooth operation.
What Advantages Do Hoisting Mechanisms Offer Over Pulleys?
Hoisting mechanisms excel in scenarios where heavy lifting is required, particularly in construction and industrial settings. They can handle significant weight and are designed for vertical movement, which makes them suitable for transporting materials to elevated areas. However, they often come with a higher maintenance burden and complexity in installation compared to pulleys. The cost can vary widely based on the type of hoist and its capacity, which may not always align with budget constraints for smaller enterprises.
Conclusion: How Should B2B Buyers Choose the Right Solution?
Selecting the right material handling solution requires a clear understanding of specific operational needs and constraints. Buyers should assess their load requirements, the complexity of installation, and ongoing maintenance capabilities. For general mechanical tasks, pulley systems may be the most cost-effective and low-maintenance choice. However, for high-volume transport, conveyor systems might be more efficient. In cases where heavy lifting is paramount, hoisting mechanisms could be the best fit despite their higher costs and maintenance needs. By weighing these factors, B2B buyers can make informed decisions that align with their operational objectives and budget constraints.
Essential Technical Properties and Trade Terminology for pulley manufacturer
What Are the Essential Technical Properties for Pulley Manufacturers?
Understanding the technical properties of pulleys is crucial for B2B buyers as these specifications directly influence performance, durability, and suitability for specific applications. Here are some of the key properties to consider:
1. Material Grade
Pulleys are commonly made from materials such as steel, aluminum, and plastic. The material grade determines the strength, weight, and resistance to corrosion or wear. For example, a higher-grade steel pulley is typically used in heavy-duty applications where high tensile strength is required. Buyers should assess the material properties based on the operational environment—marine, industrial, or agricultural—to ensure longevity and effectiveness.
2. Tolerance Levels
Tolerance refers to the permissible limit of variation in the dimensions of a pulley. It is vital in ensuring that pulleys fit correctly with other components in a system. For precision applications, tighter tolerances are necessary to avoid mechanical failures. Buyers should communicate their tolerance requirements clearly to manufacturers to ensure product compatibility and reliability.
3. Load Capacity
The load capacity indicates the maximum weight that a pulley can safely handle. This specification is critical for applications in construction, manufacturing, and transportation. Buyers must evaluate the expected loads in their operational scenarios to select pulleys that can sustain these demands without failure.
4. Surface Finish
The surface finish affects the pulley’s friction properties, corrosion resistance, and overall aesthetic. A smooth finish can reduce friction and improve efficiency, whereas a rough finish may enhance grip in certain applications. Buyers should consider the environmental conditions and operational requirements when specifying surface finishes.
5. Diameter and Groove Design
The diameter of the pulley and the design of its grooves play a significant role in its performance. A larger diameter typically allows for smoother operation and reduced wear on associated belts or ropes. The groove design affects the grip and alignment of the belt. Buyers should ensure that the pulley dimensions align with their systems to optimize performance.
What Are Common Trade Terminology and Jargon in the Pulley Manufacturing Industry?
Familiarity with industry terminology is essential for effective communication and negotiation with suppliers. Here are some commonly used terms:
1. OEM (Original Equipment Manufacturer)
OEM refers to companies that produce parts or equipment that may be marketed by another manufacturer. In the context of pulleys, understanding if a product is OEM can assure buyers of quality and compatibility with existing systems.
2. MOQ (Minimum Order Quantity)
MOQ is the smallest amount of a product that a supplier is willing to sell. This term is crucial for buyers as it impacts inventory management and overall costs. Understanding the MOQ helps in budgeting and planning for stock levels.
3. RFQ (Request for Quotation)
An RFQ is a document sent to suppliers requesting pricing and terms for specific products. For B2B buyers, crafting a clear RFQ is vital to ensure accurate and competitive quotes, facilitating better decision-making.
4. Incoterms
Incoterms are international commercial terms that define the responsibilities of buyers and sellers in shipping agreements. Familiarity with terms like FOB (Free on Board) or CIF (Cost, Insurance, and Freight) is essential for understanding shipping costs and responsibilities, which can significantly affect the total landed cost of products.
5. Lead Time
Lead time refers to the time taken from placing an order to receiving the goods. For B2B buyers, understanding lead times is crucial for planning and inventory management, especially when dealing with large-scale projects or just-in-time manufacturing.
By grasping these technical properties and trade terms, international B2B buyers can make informed decisions that align with their operational needs and strategic goals.
Navigating Market Dynamics and Sourcing Trends in the pulley manufacturer Sector
What Are the Current Market Dynamics and Key Trends in the Pulley Manufacturer Sector?
The global pulley manufacturing sector is witnessing a transformative phase driven by several key factors. One of the most significant drivers is the increasing demand for automation and mechanization across various industries, including manufacturing, construction, and logistics. As businesses strive for efficiency, the need for high-quality pulleys, which are essential components in various machinery, is on the rise. Additionally, the global push towards Industry 4.0 is prompting manufacturers to incorporate advanced technologies such as IoT and AI into their production processes, enhancing product quality and operational efficiency.
Emerging B2B technology trends are also shaping sourcing dynamics. The adoption of digital procurement platforms is gaining traction, allowing international buyers to streamline sourcing processes, compare suppliers more effectively, and make data-driven decisions. E-commerce platforms specifically designed for B2B transactions are becoming increasingly popular, particularly in regions like Africa and South America, where traditional supply chains may be less established. This shift towards digital solutions not only provides access to a broader range of suppliers but also facilitates better communication and collaboration.
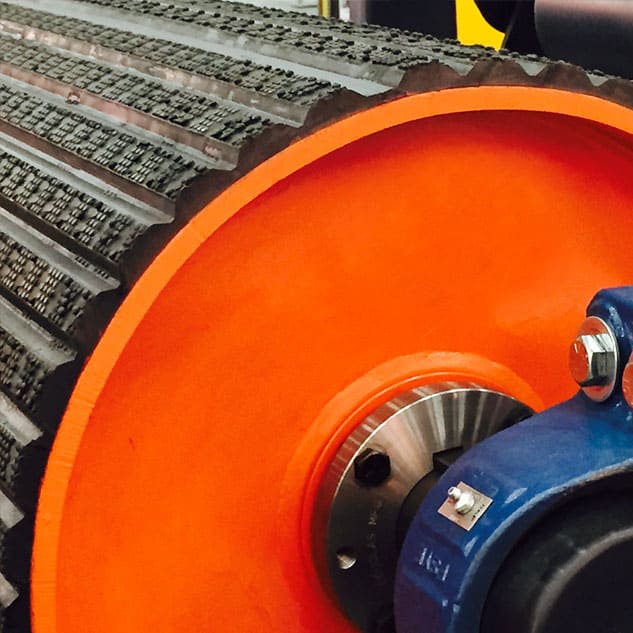
A stock image related to pulley manufacturer.
For international buyers, understanding regional market dynamics is crucial. In Europe, particularly in countries like Poland and Italy, there is a growing emphasis on innovation and quality standards. Conversely, in regions like Africa and the Middle East, buyers may face challenges related to infrastructure and regulatory environments, which necessitate careful supplier evaluation and risk management strategies.
How Can Sustainability and Ethical Sourcing Impact the Pulley Manufacturer Sector?
Sustainability has emerged as a vital consideration for international B2B buyers in the pulley manufacturing sector. The environmental impact of manufacturing processes, including energy consumption and waste generation, is under increasing scrutiny. Buyers are seeking manufacturers that implement sustainable practices, such as using recycled materials and optimizing production processes to minimize waste. This shift not only addresses environmental concerns but also aligns with the growing consumer demand for sustainable products.
Ethical sourcing is another critical aspect influencing procurement decisions. Buyers are increasingly prioritizing suppliers who demonstrate a commitment to fair labor practices and transparency in their supply chains. Certifications such as ISO 14001 (Environmental Management) and ISO 45001 (Occupational Health and Safety) are becoming standard requirements. Additionally, ‘green’ certifications for materials, such as those compliant with the Global Recycled Standard (GRS), are gaining importance as buyers look to enhance the sustainability of their operations.
Incorporating sustainability and ethical sourcing into procurement strategies not only helps mitigate risks associated with regulatory compliance but also strengthens brand reputation and customer loyalty. B2B buyers who prioritize these factors are better positioned to meet the evolving demands of their stakeholders and contribute positively to the global sustainability agenda.
What Is the Brief Evolution of the Pulley Manufacturing Sector?
The pulley manufacturing sector has evolved significantly over the decades, transitioning from rudimentary designs used in ancient machinery to sophisticated, high-performance products integral to modern industrial applications. Early pulleys were simple wooden or metal wheels used in manual labor, primarily for lifting heavy loads. With the advent of the Industrial Revolution, the demand for more durable and efficient pulleys surged, leading to advancements in materials and manufacturing techniques.
The late 20th century saw the introduction of advanced materials such as composites and high-strength alloys, which improved the performance and longevity of pulleys. The rise of automation and robotics in the 21st century further accelerated innovation within the sector, prompting manufacturers to develop smart pulleys equipped with sensors and IoT capabilities. This evolution reflects the broader trends in industrial manufacturing, where the focus has shifted towards efficiency, sustainability, and technological integration, providing a robust foundation for future growth in the pulley manufacturing sector.
Frequently Asked Questions (FAQs) for B2B Buyers of pulley manufacturer
-
How do I choose the right pulley manufacturer for my business needs?
Selecting the right pulley manufacturer involves assessing their experience, production capacity, and the types of materials they use. Look for manufacturers with a strong reputation in your industry, particularly those that have experience with similar applications to yours. Request samples or prototypes to evaluate quality. Additionally, consider their customer service responsiveness and ability to customize products to fit your specific requirements. -
What are the key factors to consider when sourcing pulleys internationally?
When sourcing pulleys internationally, focus on the manufacturer’s compliance with international quality standards, such as ISO certification. Evaluate logistics, including shipping costs and delivery times, as these can significantly impact your operations. Also, consider the manufacturer’s ability to provide after-sales support and warranty terms, ensuring you have recourse in case of defects or issues. -
What customization options are available for pulleys from manufacturers?
Many pulley manufacturers offer a range of customization options, including size, material, and design. You can specify dimensions, load capacities, and even coatings to enhance durability. It’s essential to communicate your specific requirements clearly and inquire about any additional costs associated with customization. Manufacturers may also provide engineering support to help design pulleys that meet your operational needs. -
What is the minimum order quantity (MOQ) when ordering pulleys?
Minimum order quantities (MOQ) can vary significantly among manufacturers. Some may have a low MOQ, suitable for small businesses or trial orders, while others may require larger quantities to ensure cost-effectiveness. Always clarify the MOQ upfront and discuss potential flexibility if your needs do not meet their standard order sizes. This will help you manage inventory and cash flow effectively. -
What payment terms should I negotiate with a pulley supplier?
Negotiating payment terms is crucial for maintaining cash flow. Common practices include partial upfront payments, with the balance due upon delivery or after a specified period. Consider using secure payment methods such as letters of credit, especially for international transactions, to protect your interests. Additionally, discuss any bulk order discounts or incentives for early payment to optimize your procurement costs. -
How can I ensure quality assurance when sourcing pulleys?
To ensure quality assurance, request detailed product specifications and certifications from the manufacturer. Conduct pre-production inspections and request samples for testing before full-scale production. It’s advisable to establish clear quality standards and conduct regular audits of the manufacturing process. Consider hiring third-party inspection services for additional assurance, especially for high-volume orders.
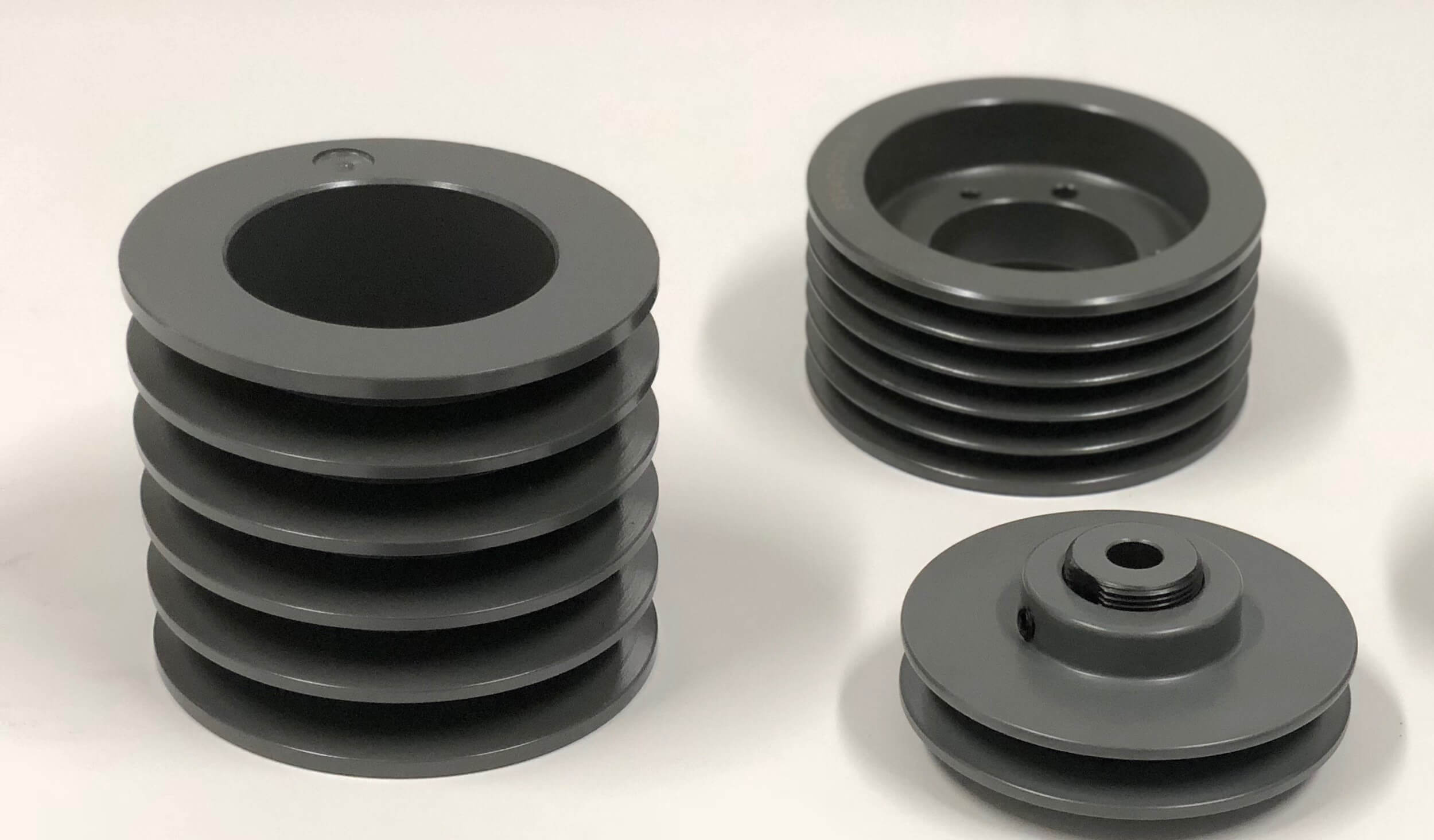
A stock image related to pulley manufacturer.
-
What logistics considerations should I keep in mind when sourcing pulleys from abroad?
Logistics play a critical role in international sourcing. Evaluate the manufacturer’s shipping options, delivery times, and associated costs, including customs duties and taxes. It’s important to choose a reliable freight forwarder who can navigate the complexities of international shipping. Additionally, factor in the potential for delays and plan your inventory management accordingly to prevent disruptions in your supply chain. -
How do I vet a pulley manufacturer to ensure reliability?
Vetting a pulley manufacturer involves researching their business history, client testimonials, and industry reputation. Request references from previous clients, particularly those in your industry. Conduct site visits if possible to assess their production capabilities and quality control measures. Additionally, verify their financial stability and compliance with local and international regulations to ensure they can meet your long-term supply needs.
Important Disclaimer & Terms of Use
⚠️ Important Disclaimer
The information provided in this guide, including content regarding manufacturers, technical specifications, and market analysis, is for informational and educational purposes only. It does not constitute professional procurement advice, financial advice, or legal advice.
While we have made every effort to ensure the accuracy and timeliness of the information, we are not responsible for any errors, omissions, or outdated information. Market conditions, company details, and technical standards are subject to change.
B2B buyers must conduct their own independent and thorough due diligence before making any purchasing decisions. This includes contacting suppliers directly, verifying certifications, requesting samples, and seeking professional consultation. The risk of relying on any information in this guide is borne solely by the reader.
Strategic Sourcing Conclusion and Outlook for pulley manufacturer
In the competitive landscape of pulley manufacturing, strategic sourcing emerges as a crucial element for international B2B buyers. By focusing on quality, supplier reliability, and cost-effectiveness, businesses can ensure they are making informed decisions that bolster their operational efficiency. Engaging with manufacturers who prioritize innovation and sustainability not only enhances product offerings but also aligns with global trends favoring environmentally responsible practices.
How Can Strategic Sourcing Benefit Your Business?
Investing in strategic sourcing allows companies to tap into the expertise of established pulley manufacturers, particularly those located in emerging markets across Africa, South America, the Middle East, and Europe. This approach not only fosters long-term partnerships but also opens avenues for customized solutions that meet specific industry needs.
What Does the Future Hold for International B2B Buyers?
Looking ahead, the demand for high-quality, durable pulleys will only continue to rise, driven by advancements in technology and industrial automation. Buyers are encouraged to stay proactive by exploring new supplier relationships, leveraging digital platforms for sourcing, and adopting data-driven decision-making processes. By prioritizing strategic sourcing now, companies can position themselves for growth and resilience in an ever-evolving marketplace.