Discover Top Benefits of Choosing a Relay Manufacturer (2025)
Introduction: Navigating the Global Market for relay manufacturer
In the fast-evolving global market, sourcing the right relay manufacturer can be a daunting task for international B2B buyers, especially those hailing from diverse regions such as Africa, South America, the Middle East, and Europe. With the increasing demand for reliable electromagnetic switches in various applications, understanding the nuances of relay technology is crucial. This guide aims to demystify the complexities surrounding relay manufacturing by providing a comprehensive overview of different types of relays, their applications, and the critical factors to consider when selecting a supplier.
Buyers will gain insights into the various relay types, including electromechanical, solid-state, and hybrid relays, alongside their specific use cases ranging from industrial automation to automotive systems. We will delve into essential topics such as supplier vetting processes, cost considerations, and best practices for ensuring product quality and compliance with international standards. By arming yourself with this knowledge, you can make informed purchasing decisions that align with your operational needs and budget constraints.
Whether you are a purchasing manager in Mexico seeking cost-effective solutions or a project engineer in Egypt looking for high-performance relays, this guide will serve as your roadmap to successfully navigate the global market for relay manufacturers. Empower yourself with the tools to enhance your sourcing strategy and build lasting partnerships that drive your business forward.
Understanding relay manufacturer Types and Variations
Type Name | Key Distinguishing Features | Primary B2B Applications | Brief Pros & Cons for Buyers |
---|---|---|---|
Electromechanical Relays | Operate via electromagnetic coils; suitable for high power | Industrial machinery, automotive systems | Pros: Reliable, versatile. Cons: Slower switching speed, larger size. |
Solid State Relays | Utilize semiconductor technology; no moving parts | HVAC systems, lighting controls | Pros: Fast switching, longer lifespan. Cons: Higher initial cost, sensitive to overloading. |
Reed Relays | Use magnetic fields to operate; compact and lightweight | Telecommunications, sensors | Pros: Small size, low power consumption. Cons: Limited current capacity, sensitive to vibrations. |
Time Delay Relays | Incorporate timing functions; delay circuit activation | Automation systems, safety circuits | Pros: Flexible timing options. Cons: More complex, potential for failure if not calibrated correctly. |
Latching Relays | Maintain their position after being energized; energy efficient | Energy management, remote controls | Pros: Low power consumption, reliable in power outages. Cons: More expensive, complex circuitry. |
What Are the Key Characteristics of Electromechanical Relays for B2B Buyers?
Electromechanical relays (EMRs) are widely utilized in various industries due to their ability to handle high power loads. They operate through electromagnetic coils that physically move contacts to open or close circuits. Buyers should consider EMRs for applications requiring robust switching, such as industrial machinery or automotive systems. However, their size and slower switching speeds compared to solid-state alternatives may be limiting factors in compact or high-frequency applications.
Why Choose Solid State Relays for Modern Applications?
Solid state relays (SSRs) leverage semiconductor technology, which eliminates the need for mechanical parts. This feature allows them to achieve rapid switching speeds and a longer operational lifespan. B2B buyers in industries like HVAC and lighting controls will find SSRs advantageous due to their reliability and minimal maintenance needs. However, the initial costs can be higher, and they may require careful management to avoid overloading.
How Do Reed Relays Fit into Telecommunications and Sensor Applications?
Reed relays are compact and lightweight, making them ideal for applications in telecommunications and various sensor systems. They operate using magnetic fields to switch contacts, which allows for low power consumption. Buyers should consider reed relays for projects where space is limited. However, their limited current capacity and sensitivity to vibrations may pose challenges in more demanding environments.
What Advantages Do Time Delay Relays Offer in Automation?
Time delay relays are designed to activate circuits after a predetermined delay, making them essential in automation systems and safety circuits. They provide flexibility in timing options, which can enhance operational efficiency. B2B buyers should account for the complexity and calibration requirements of these relays, as improper settings can lead to failures or safety risks.
In What Scenarios Are Latching Relays Most Beneficial?
Latching relays maintain their state even after power is removed, making them energy efficient and reliable during power outages. These relays are particularly useful in energy management and remote control applications. However, their complexity and higher costs may deter buyers who are seeking simpler solutions. Understanding the specific needs of the application will help buyers determine if latching relays are the right choice.
Related Video: How Relay Works Types of Relay SPST SPDT DPDT in English
Key Industrial Applications of relay manufacturer
Industry/Sector | Specific Application of relay manufacturer | Value/Benefit for the Business | Key Sourcing Considerations for this Application |
---|---|---|---|
Industrial Automation | Control systems for machinery and production lines | Enhances efficiency by automating processes and reducing downtime | Reliability, response time, and compatibility with existing systems |
Telecommunications | Signal routing and switching in telecommunication networks | Ensures uninterrupted service and improves signal integrity | Compliance with international standards and environmental ratings |
Energy Management | Protective relaying in electrical grids | Minimizes risk of outages and equipment damage | Voltage ratings, load capacity, and safety certifications |
Transportation | Control systems in railway and traffic management | Increases safety and operational efficiency | Durability under varying environmental conditions and regulatory compliance |
Home Appliances | Remote control systems in smart home devices | Provides convenience and energy savings for consumers | Energy efficiency ratings and integration with IoT platforms |
How Is Relay Manufacturer Used in Industrial Automation?
In industrial automation, relay manufacturers provide essential components that control machinery and production lines. Relays are used to automate processes, enabling machines to operate without human intervention. This not only enhances efficiency but also significantly reduces downtime. For international buyers, especially from Africa and South America, sourcing reliable relays that can withstand harsh industrial environments is crucial. Factors such as response time and compatibility with existing systems should be prioritized to ensure seamless integration.
What Are the Applications of Relay Manufacturers in Telecommunications?
In the telecommunications sector, relays play a critical role in signal routing and switching. They ensure that data transmission remains uninterrupted and that signals maintain their integrity over long distances. This is particularly important for businesses in the Middle East and Europe where high standards of communication are expected. Buyers should consider sourcing relays that comply with international standards and have robust environmental ratings to ensure reliability in diverse conditions.
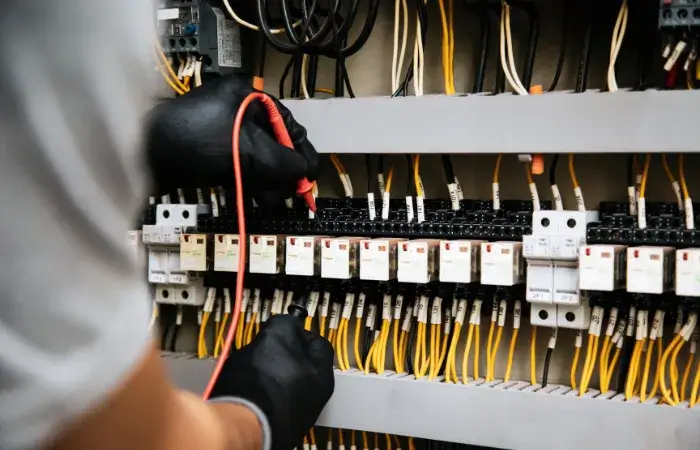
A stock image related to relay manufacturer.
How Do Relay Manufacturers Contribute to Energy Management?
Relay manufacturers supply protective relays that are vital for electrical grid management. These relays help minimize the risk of outages and potential equipment damage by automatically disconnecting faulty circuits. For international B2B buyers, particularly in regions like Africa and Europe, sourcing relays with appropriate voltage ratings and load capacity is imperative. Additionally, safety certifications are critical to ensure compliance with local regulations and standards.
What Role Do Relays Play in Transportation Systems?
In transportation, relays are integral to control systems used in railways and traffic management. They enhance safety and operational efficiency by enabling automated responses to changing conditions. B2B buyers in this sector, particularly from regions like South America and the Middle East, should prioritize sourcing relays that can withstand extreme environmental conditions and meet regulatory compliance. This ensures that the systems remain operational and safe under various circumstances.
How Are Relay Manufacturers Used in Home Appliances?
Relay manufacturers are key suppliers for remote control systems in smart home devices. These relays allow users to control appliances remotely, leading to increased convenience and energy savings. For buyers from Europe and Africa, it is essential to consider energy efficiency ratings and the ability of relays to integrate with IoT platforms. This ensures that the devices not only function effectively but also align with modern energy management practices.
Related Video: Why we use Relay in PLC Applications | Relay Wiring Diagram | Types of Relay-SPST, SPDT, DPST, DPDT
3 Common User Pain Points for ‘relay manufacturer’ & Their Solutions
Scenario 1: Understanding Relay Specifications for Different Applications
The Problem: Many B2B buyers, especially those from regions like Africa and South America, face challenges when it comes to understanding the specific relay types that suit their applications. They may struggle with technical jargon, differing standards, and the need for specific functionalities like voltage ratings, switching capacity, and operational life. This confusion can lead to incorrect purchases, resulting in costly project delays and operational inefficiencies.
The Solution: To overcome this issue, buyers should engage in detailed discussions with relay manufacturers about their specific application needs. It’s crucial to provide comprehensive information about the electrical loads, environmental conditions, and intended use cases. Buyers can also request detailed specifications and datasheets from manufacturers that outline the operational parameters of various relay types. Furthermore, leveraging online resources such as comparison charts and technical documentation can aid in making informed decisions. Establishing a partnership with manufacturers who provide technical support and consultancy can also ensure that the right relay is sourced for the intended application.
Scenario 2: Managing Supply Chain Disruptions for Relay Procurement
The Problem: International B2B buyers often face supply chain disruptions, particularly in regions like the Middle East and Europe, where geopolitical factors and transportation issues can lead to delays in obtaining necessary relay components. This unpredictability in lead times can stall production schedules and impact project timelines, causing frustration and potential financial losses.
The Solution: To mitigate supply chain risks, buyers should diversify their sourcing strategies. Instead of relying on a single manufacturer, it’s beneficial to establish relationships with multiple suppliers in different geographical locations. This approach not only provides alternatives in case of disruptions but also fosters competitive pricing. Additionally, implementing a just-in-time (JIT) inventory system can help manage stock levels efficiently, reducing the need for large inventories that can become obsolete. Buyers should also consider collaborating with local distributors who have a better understanding of regional logistics and can expedite the procurement process.
Scenario 3: Ensuring Quality and Compliance in Relay Manufacturing
The Problem: Quality assurance is a significant concern for B2B buyers, particularly in industries like automotive and industrial automation, where relay failures can lead to severe safety hazards and regulatory non-compliance. Buyers from Europe and Africa, in particular, may encounter challenges in verifying the quality standards of relays, especially when sourcing from international manufacturers with varying compliance levels.
The Solution: To ensure quality and compliance, buyers should prioritize sourcing from manufacturers who hold recognized certifications (such as ISO 9001 or UL certification) that demonstrate adherence to international quality standards. Requesting samples for testing can provide firsthand insight into the product’s reliability and performance. Additionally, implementing a robust quality control process that includes regular audits of suppliers can help maintain high standards. It’s also beneficial to stay informed about regional compliance regulations and standards, as this knowledge can guide sourcing decisions and help avoid legal pitfalls associated with non-compliant products. Building long-term relationships with trusted manufacturers can further enhance the assurance of consistent quality.
Strategic Material Selection Guide for relay manufacturer
What Are the Key Materials for Relay Manufacturing?
When selecting materials for relay manufacturing, it is crucial to consider their properties, advantages, limitations, and compliance with international standards. Here, we analyze four common materials used in relay construction: copper, plastic, steel, and silicone rubber.
How Does Copper Influence Relay Performance?
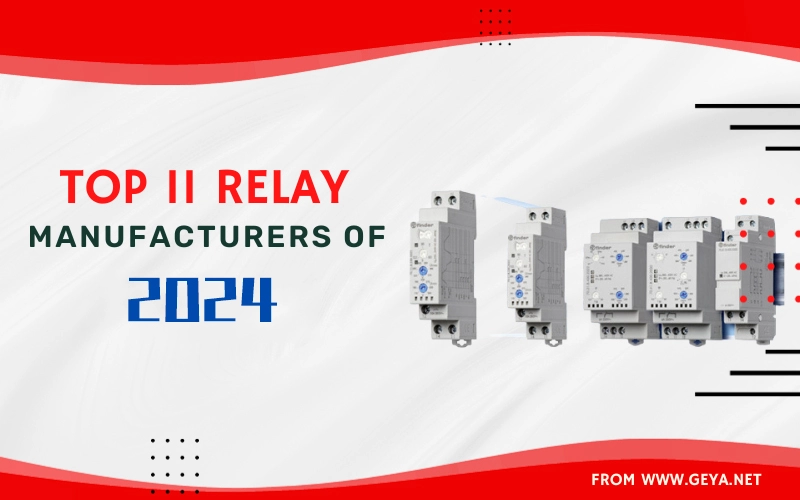
A stock image related to relay manufacturer.
Copper is widely used in relay contacts due to its excellent electrical conductivity and thermal properties. It typically has a high melting point (around 1,984°F or 1,085°C), making it suitable for high-temperature applications. Copper also exhibits good corrosion resistance, especially when alloyed with other metals.
Pros:
– Exceptional conductivity leads to lower energy loss.
– High durability and resistance to thermal fatigue.
Cons:
– Higher cost compared to other conductive materials like aluminum.
– Prone to oxidation, which can affect performance over time.
Impact on Application:
Copper is ideal for applications requiring high reliability in electrical connections, such as automotive and industrial relays. However, it may not be suitable for environments with high humidity without proper coating.
Considerations for International Buyers:
Buyers from regions like Africa and the Middle East should ensure compliance with standards such as ASTM B187 for copper alloys. In Europe, DIN standards may apply, particularly for electrical applications.
What Role Does Plastic Play in Relay Manufacturing?
Plastics, particularly thermoplastics like polycarbonate and nylon, are commonly used for relay housings and insulation. They offer excellent dielectric properties and can withstand moderate temperatures (up to around 300°F or 150°C).
Pros:
– Lightweight and cost-effective.
– Good chemical resistance and insulating properties.
Cons:
– Limited thermal resistance compared to metals.
– May degrade under UV exposure unless treated.
Impact on Application:
Plastic is suitable for low to medium voltage applications where insulation is critical. It is often used in consumer electronics and automotive relays.
Considerations for International Buyers:
Buyers should check for compliance with UL 94 for flammability ratings and ISO standards for quality assurance. In regions like South America, ensure that local regulations regarding plastic materials are met.
How Does Steel Contribute to Relay Durability?
Steel is often used for the structural components of relays, such as the frame and armature. It provides strength and stability, with a temperature rating that can exceed 1,500°F (815°C) depending on the alloy.
Pros:
– High strength and durability, making it suitable for heavy-duty applications.
– Good resistance to mechanical wear.
Cons:
– Heavier than alternatives like aluminum or plastic.
– Susceptible to corrosion unless treated or coated.
Impact on Application:
Steel is ideal for industrial applications where mechanical robustness is essential, such as in heavy machinery and power distribution systems.
Considerations for International Buyers:
Ensure compliance with ASTM A36 for structural steel standards. Buyers in Europe may need to adhere to EN 10025 standards for steel quality.
What Benefits Does Silicone Rubber Offer in Relay Design?
Silicone rubber is often used for gaskets and seals in relays due to its excellent thermal stability and flexibility. It can withstand temperatures ranging from -80°F to 500°F (-62°C to 260°C).
Pros:
– Excellent resistance to extreme temperatures and environmental factors.
– Flexible and durable, providing good sealing properties.
Cons:
– Higher cost compared to traditional rubber materials.
– Limited mechanical strength compared to metals.
Impact on Application:
Silicone rubber is particularly useful in applications exposed to harsh environments, such as automotive relays in extreme climates.
Considerations for International Buyers:
Buyers should ensure compliance with FDA regulations if the relay is used in food-related applications. Additionally, check for compliance with ASTM D412 for rubber properties.
Summary Table of Material Selection for Relay Manufacturing
Material | Typical Use Case for relay manufacturer | Key Advantage | Key Disadvantage/Limitation | Relative Cost (Low/Med/High) |
---|---|---|---|---|
Copper | Electrical contacts in automotive relays | Exceptional conductivity | Prone to oxidation | High |
Plastic | Insulation and housing for consumer electronics | Lightweight and cost-effective | Limited thermal resistance | Medium |
Steel | Structural components in industrial relays | High strength and durability | Heavier and susceptible to corrosion | Medium |
Silicone Rubber | Seals and gaskets in harsh environments | Excellent thermal stability and flexibility | Higher cost and limited mechanical strength | Medium |
This strategic material selection guide provides valuable insights for international B2B buyers looking to optimize their relay manufacturing processes while ensuring compliance with relevant standards and regulations.
In-depth Look: Manufacturing Processes and Quality Assurance for relay manufacturer
What Are the Main Stages of Manufacturing Processes for Relay Manufacturers?
Manufacturing relays involves several critical stages that ensure the final product meets quality and performance standards. Understanding these stages can empower international B2B buyers to make informed decisions when selecting suppliers.
1. Material Preparation: What Materials Are Used in Relay Manufacturing?
The manufacturing process begins with the preparation of raw materials, which typically include:
- Copper Wire: Used for the electromagnetic coil.
- Iron Core: Serves as the core for the electromagnet.
- Plastic or Metal Housing: Provides insulation and protection for internal components.
- Contact Materials: Often made from silver or gold alloys to ensure good conductivity and longevity.
Quality control in this stage involves verifying the purity and conductivity of materials. Suppliers should provide material certification to assure buyers of the material quality.
2. Forming: How Are Relay Components Shaped?
Once materials are prepared, the next step is forming the components, which typically involves:
- Winding the Coil: Copper wire is wound around the iron core to create the electromagnetic coil. Precision in this step is crucial to ensure the relay operates efficiently.
- Stamping Contacts: The contacts are stamped from metal sheets and must be shaped accurately to maintain proper functionality.
- Injection Molding: Plastic components, including the housing, are created using injection molding techniques. This allows for complex shapes and designs while maintaining uniform quality.
Quality checks during this stage may include dimensional inspections and tensile strength tests.
3. Assembly: What Is the Assembly Process for Relays?
The assembly process involves bringing together all the formed components. Key steps include:
- Coil Assembly: The wound coil is fitted onto the iron core.
- Contact Assembly: Contacts are positioned and secured to ensure they can move freely without obstruction.
- Housing Assembly: The assembled coil and contacts are placed inside the housing, which is then sealed to protect against environmental factors.
During assembly, manufacturers should implement automated systems for precision and speed. B2B buyers can inquire about the use of robotics or automation in this process to gauge efficiency.
4. Finishing: What Finishing Processes Are Commonly Used?
Finishing processes enhance the performance and appearance of the relay. Common techniques include:
- Surface Treatment: Processes such as plating or coating are used to prevent corrosion and improve conductivity.
- Testing: Each relay undergoes a series of tests to ensure it meets operational specifications.
Finishing quality control includes visual inspections and functional tests to verify that each relay performs as intended.
How Does Quality Assurance Work in Relay Manufacturing?
Quality assurance (QA) is critical in relay manufacturing, ensuring that each product meets international standards and customer expectations.
What International Standards Are Relevant to Relay Manufacturing?
International standards like ISO 9001 provide a framework for quality management systems. Compliance with these standards ensures that manufacturers maintain consistent quality in their processes. Other relevant certifications include:
- CE Marking: Indicates compliance with EU safety, health, and environmental protection standards.
- API Certification: Important for relays used in oil and gas industries, ensuring adherence to industry-specific standards.
B2B buyers should prioritize suppliers who hold these certifications to mitigate risks associated with product quality.
What Are the Key QC Checkpoints in Relay Manufacturing?
Quality control in relay manufacturing typically involves several checkpoints:
- Incoming Quality Control (IQC): Raw materials are inspected upon arrival to ensure they meet specified requirements.
- In-Process Quality Control (IPQC): Regular inspections during the manufacturing process help identify defects early.
- Final Quality Control (FQC): Finished products undergo comprehensive testing to verify performance and reliability.
These checkpoints are essential for maintaining product integrity throughout the manufacturing process.
What Common Testing Methods Are Used for Relays?
Testing methods vary depending on the relay type and application. Common testing procedures include:
- Functional Testing: Verifying that the relay operates as intended under various conditions.
- Dielectric Strength Testing: Ensuring the relay can withstand high voltage without failure.
- Environmental Testing: Assessing performance under extreme conditions, such as temperature and humidity variations.
B2B buyers should request detailed testing reports from suppliers to ensure that products meet required specifications.
How Can B2B Buyers Verify Supplier Quality Control?
To ensure a supplier’s quality control practices align with their expectations, buyers can take several steps:
- Conduct Audits: Regular audits of suppliers can provide insights into their manufacturing processes and quality control systems.
- Request Quality Reports: Suppliers should provide documentation of quality control measures, including test results and certifications.
- Third-Party Inspections: Engaging third-party inspectors can provide an unbiased assessment of a supplier’s quality control processes.
Particularly for buyers from Africa, South America, the Middle East, and Europe, understanding these verification methods is crucial for establishing reliable supply chains.
What Are the QC and Certification Nuances for International B2B Buyers?
International B2B buyers must navigate various certification and quality control nuances. This includes:
- Understanding Regional Regulations: Each region may have specific regulations governing electrical components, and buyers should be aware of these to ensure compliance.
- Assessing Supplier Capabilities: Evaluating a supplier’s ability to meet international standards is essential, particularly when sourcing from regions with varying quality assurance practices.
By being informed about these nuances, B2B buyers can make better procurement decisions and reduce the risk of quality-related issues in their supply chains.
Practical Sourcing Guide: A Step-by-Step Checklist for ‘relay manufacturer’
Introduction
When sourcing a relay manufacturer, especially for international B2B transactions, it is essential to follow a structured approach. This checklist is designed to guide buyers through the critical steps necessary to identify, evaluate, and engage with reliable relay manufacturers. By adhering to these steps, you can ensure that your procurement process aligns with your technical requirements and business objectives.
1. Define Your Technical Specifications
Clearly outline the technical specifications for the relays you need, including voltage ratings, current ratings, and types (e.g., electromechanical, solid-state). This step is crucial because different applications require different relay characteristics. Providing specific details helps manufacturers understand your needs and offer suitable products.
2. Research Potential Manufacturers
Conduct thorough research to compile a list of potential relay manufacturers. Utilize industry directories, trade shows, and online platforms to identify companies with a strong reputation. Pay attention to their experience in your specific industry and the types of relays they specialize in.
3. ✅ Verify Supplier Certifications
Before proceeding with a supplier, confirm that they possess the necessary certifications such as ISO 9001 or UL certification. These certifications indicate adherence to quality management standards and safety regulations. This step is vital to ensure the reliability of the relays and compliance with international standards.
4. Evaluate Potential Suppliers
Engage with shortlisted suppliers to assess their capabilities. Request company profiles, case studies, and references from clients in similar industries. This evaluation helps you gauge their experience, production capacity, and commitment to quality, which are essential for long-term partnerships.
5. Request Samples for Testing
Before making a bulk purchase, request samples of the relays you intend to procure. Testing samples allows you to assess the quality, performance, and compatibility with your existing systems. This step is important to mitigate risks associated with product failures or incompatibility in real-world applications.
6. Inquire About Lead Times and Pricing
Discuss lead times and pricing structures with potential manufacturers. Understanding their production capabilities and delivery schedules is crucial for planning your inventory and project timelines. Additionally, compare pricing to ensure you are getting competitive rates without compromising quality.
7. Negotiate Terms and Finalize Contracts
Once you have selected a supplier, negotiate the terms of the contract, including payment terms, delivery schedules, and warranty conditions. Clear agreements protect both parties and ensure a smooth procurement process. It’s advisable to include clauses related to quality assurance and penalties for non-compliance to safeguard your interests.
By following this practical sourcing guide, B2B buyers can confidently navigate the complexities of procuring relays from manufacturers, ensuring they select partners that meet their technical and business needs.
Comprehensive Cost and Pricing Analysis for relay manufacturer Sourcing
What Are the Key Cost Components in Relay Manufacturing?
Understanding the cost structure of relay manufacturing is essential for B2B buyers, especially when sourcing internationally. The primary cost components include:
-
Materials: The raw materials used in relay production, such as copper for windings, ferromagnetic materials for cores, and plastics for casings, significantly influence the overall cost. Prices can fluctuate based on global commodity markets, so buyers should stay informed about market trends.
-
Labor: Labor costs vary widely across regions. Countries in Africa and South America may offer lower labor costs compared to Europe and the Middle East. However, skill levels and labor laws can impact productivity and quality, which should be considered when comparing costs.
-
Manufacturing Overhead: This encompasses expenses related to utilities, rent, equipment maintenance, and other indirect costs associated with the manufacturing process. Efficient production processes can help lower these overhead costs, making it vital to evaluate potential suppliers’ operational efficiency.
-
Tooling: The cost of tooling depends on the complexity of the relay design and the volume of production. Custom tooling can be expensive, so buyers should assess whether standard components can meet their needs to reduce initial costs.
-
Quality Control (QC): Implementing stringent QC measures ensures product reliability but can add to the overall cost. Buyers should inquire about the QC processes of potential suppliers, as this can affect both pricing and product quality.
-
Logistics: Shipping costs, including freight and insurance, can vary based on the supplier’s location and the chosen Incoterms. For international buyers, understanding these logistics costs is crucial for accurate budgeting.
-
Margin: Manufacturers typically add a margin to cover their profit and any unexpected costs. This margin can vary depending on the supplier’s market position and the level of competition.
How Do Price Influencers Affect Relay Sourcing?
Several factors can influence pricing when sourcing relays:
-
Volume and Minimum Order Quantity (MOQ): Larger orders often attract discounts, so understanding the MOQ policies of suppliers is essential for cost-effective purchasing.
-
Specifications and Customization: Custom relays tailored to specific applications can significantly increase costs. Buyers should evaluate whether off-the-shelf solutions can meet their requirements to optimize spending.
-
Material Quality and Certifications: Higher quality materials and certifications (like ISO standards) enhance reliability but come at a premium. International buyers should weigh the importance of these factors against their budget.
-
Supplier Factors: Supplier reputation, location, and operational efficiency can all impact pricing. Building relationships with reliable suppliers can lead to better terms and pricing.
-
Incoterms: Understanding the chosen Incoterms can help buyers predict total landed costs, including shipping, duties, and taxes, which are crucial for accurate budgeting.
What Tips Can International B2B Buyers Use for Cost-Efficiency?
To maximize cost-efficiency when sourcing relays, consider the following strategies:
-
Negotiation: Engage in negotiations with suppliers to explore bulk discounts, payment terms, and price flexibility. Building rapport can lead to better deals.
-
Total Cost of Ownership (TCO): Focus on TCO rather than just the initial purchase price. Consider factors like reliability, maintenance, and potential downtime costs associated with inferior products.
-
Pricing Nuances for Different Regions: Be aware of regional pricing differences. For instance, sourcing from manufacturers in Africa or South America might yield lower prices, but consider potential trade-offs in quality or shipping times.
-
Stay Informed: Keep abreast of market trends and global supply chain issues that could affect pricing and availability. This knowledge can empower you to make informed sourcing decisions.
Disclaimer on Indicative Prices
Prices for relays can vary widely based on the aforementioned factors. The information provided serves as a general guide, and buyers should request quotes from multiple suppliers to get an accurate picture of current market rates and conditions.
Alternatives Analysis: Comparing relay manufacturer With Other Solutions
When considering the best solution for controlling electrical circuits, it is essential for international B2B buyers to evaluate alternatives to traditional relay manufacturers. Various technologies can achieve similar objectives, each with distinct advantages and disadvantages depending on specific application requirements. This analysis will compare relay manufacturers with two viable alternatives: Solid State Relays (SSRs) and Programmable Logic Controllers (PLCs).
Comparison Table
Comparison Aspect | Relay Manufacturer | Solid State Relay (SSR) | Programmable Logic Controller (PLC) |
---|---|---|---|
Performance | High current capacity, reliable switching | Faster switching, less noise | Highly versatile, programmable functions |
Cost | Generally low-cost | Moderate cost, higher than electromechanical relays | Higher initial investment, cost-effective for complex tasks |
Ease of Implementation | Simple integration in circuits | Easy to install, minimal setup | Requires programming knowledge, more complex setup |
Maintenance | Requires occasional checks | Low maintenance needs | Regular software updates and checks needed |
Best Use Case | Basic on/off control | High-speed switching applications | Complex automation systems requiring logic control |
What are the advantages and disadvantages of Solid State Relays (SSRs)?
Solid State Relays (SSRs) provide a modern alternative to electromechanical relays, offering faster switching times and enhanced durability. SSRs operate without moving parts, which significantly reduces the risk of mechanical failure and extends their lifespan. Their compact design allows for easier integration into various systems, making them ideal for applications with limited space. However, SSRs can be more expensive than traditional relays and may require heat sinks for proper thermal management, which can complicate installation in some scenarios.
How do Programmable Logic Controllers (PLCs) compare to relay manufacturers?
Programmable Logic Controllers (PLCs) are advanced devices that can perform complex control tasks through programmed logic. They are highly flexible, capable of handling multiple inputs and outputs, and can be programmed to respond to various conditions dynamically. This makes PLCs suitable for large-scale industrial applications where automation and efficiency are critical. However, the initial investment is often higher, and they require specialized knowledge to program and maintain. For businesses with straightforward control needs, a relay might be more cost-effective and easier to implement.
Conclusion: How can international B2B buyers choose the right solution?
Selecting the right solution for circuit control depends on the specific needs of your application. For straightforward on/off control tasks, traditional relay manufacturers may provide the most cost-effective solution. If your application demands faster switching and higher reliability, Solid State Relays could be the better choice. For complex systems requiring automation and programmable logic, investing in a PLC may yield the best long-term benefits despite the higher upfront costs. Ultimately, understanding your operational requirements and budget constraints will guide your decision toward the most suitable technology.
Essential Technical Properties and Trade Terminology for relay manufacturer
What Are the Key Technical Properties of Relays That B2B Buyers Should Consider?
Understanding the essential technical properties of relays is crucial for international B2B buyers, especially when sourcing from diverse regions such as Africa, South America, the Middle East, and Europe. Here are some critical specifications that should be considered:
1. Contact Rating
Contact rating refers to the maximum voltage and current that a relay can handle safely. It is typically expressed in amperes (A) and volts (V). For B2B buyers, selecting a relay with an appropriate contact rating is vital to ensure that the relay can operate effectively within the intended application, whether for low-voltage electronics or high-power industrial equipment.
2. Coil Voltage
Coil voltage is the electrical voltage required to energize the relay’s coil and activate its switching mechanism. Common values include 5V, 12V, and 24V. B2B buyers should ensure that the coil voltage matches their system specifications to avoid malfunction or damage to the relay.
3. Operating Temperature Range
The operating temperature range defines the environmental conditions in which a relay can function optimally. Typically expressed in degrees Celsius, it is crucial for applications in harsh climates or industrial settings. Buyers need to verify that the relay can withstand the temperature extremes of their operational environment to maintain reliability and longevity.
4. Insulation Resistance
Insulation resistance measures the relay’s ability to resist electrical leakage between its contacts and coil. High insulation resistance values are essential for preventing short circuits and ensuring safety. For B2B buyers, understanding this property helps in selecting relays that meet safety standards and regulatory requirements.
5. Mechanical Life
Mechanical life refers to the number of operations a relay can perform before mechanical failure occurs, typically expressed in millions of operations. This specification is critical for applications requiring high reliability. Buyers should consider mechanical life in relation to their expected usage to minimize the need for frequent replacements.
6. Material Grade
Material grade refers to the quality of materials used in the relay’s construction, including contact materials and housing. Higher-grade materials often lead to better performance and durability. B2B buyers should inquire about material specifications to ensure that the relay will perform well in their specific applications.
What Are Common Trade Terminology and Jargon in the Relay Manufacturing Industry?
Familiarity with industry-specific terminology can significantly streamline the procurement process for B2B buyers. Here are some essential terms to know:
1. OEM (Original Equipment Manufacturer)
OEM refers to companies that produce parts or equipment that may be marketed by another manufacturer. In the relay industry, understanding OEM relationships can help buyers identify reputable suppliers who ensure quality and compatibility with existing systems.
2. MOQ (Minimum Order Quantity)
MOQ denotes the smallest quantity of a product that a supplier is willing to sell. This term is important for B2B buyers as it affects inventory management and cost efficiency. Understanding MOQ can help buyers negotiate better terms and avoid excess stock.
3. RFQ (Request for Quotation)
An RFQ is a formal document sent to suppliers requesting pricing and terms for specific products or services. For international buyers, sending an RFQ can facilitate transparent communication and help obtain competitive pricing for relays.
4. Incoterms (International Commercial Terms)
Incoterms are standardized trade terms that define the responsibilities of buyers and sellers in international transactions. Familiarity with these terms is essential for B2B buyers to understand shipping costs, insurance, and risk responsibilities, thereby simplifying logistics management.
5. Lead Time
Lead time refers to the amount of time it takes from placing an order until the product is delivered. Understanding lead times is crucial for buyers to manage project timelines and inventory levels effectively.
6. Technical Data Sheet (TDS)
A TDS is a document that provides detailed specifications and performance characteristics of a product. B2B buyers should request TDS from suppliers to ensure that the relays meet their technical requirements and application needs.
By grasping these essential properties and terminology, international B2B buyers can make informed decisions when sourcing relays, ultimately enhancing operational efficiency and product reliability.
Navigating Market Dynamics and Sourcing Trends in the relay manufacturer Sector
What Are the Key Trends Shaping the Relay Manufacturing Market?
The global relay manufacturing market is undergoing significant transformation, driven by technological advancements and changing consumer demands. One of the primary drivers is the increasing automation across various industries, including automotive, telecommunications, and renewable energy sectors. As businesses seek to enhance efficiency and reduce operational costs, the demand for reliable and efficient relay systems is surging. Furthermore, the integration of Internet of Things (IoT) technologies is opening new avenues for smart relay applications, enabling remote control and monitoring capabilities.
International B2B buyers, particularly from Africa, South America, the Middle East, and Europe, are also witnessing shifts in sourcing strategies. The focus is increasingly on local sourcing to mitigate supply chain disruptions experienced during global crises. Buyers are looking for manufacturers that can provide rapid delivery times and customized solutions tailored to specific regional needs. Moreover, the emphasis on energy-efficient products is pushing manufacturers to innovate and produce relays that consume less power while maintaining high performance.
Emerging trends such as the adoption of Industry 4.0 practices are also influencing the relay sector. This includes the use of advanced manufacturing techniques such as 3D printing and automation in production processes, which can lead to reduced lead times and lower costs. As a result, international buyers should prioritize suppliers that embrace these technologies to ensure they remain competitive in a rapidly evolving market landscape.
How Can Sustainability and Ethical Sourcing Impact B2B Relay Manufacturers?
Sustainability has become a pivotal concern for B2B buyers, particularly in the relay manufacturing sector. The environmental impact of production processes and the sourcing of raw materials are under scrutiny as companies strive to align with global sustainability goals. B2B buyers are increasingly favoring manufacturers that implement sustainable practices, such as reducing carbon emissions, minimizing waste, and conserving energy throughout their operations.
Ethical sourcing is also gaining importance, as buyers demand transparency regarding the origin of materials used in relay production. Manufacturers that can demonstrate compliance with ethical sourcing standards and certifications are more likely to gain trust and loyalty from international buyers. For instance, obtaining certifications such as ISO 14001 (Environmental Management) or certifications for conflict-free materials can significantly enhance a manufacturer’s reputation and marketability.
Additionally, there is a growing trend towards using ‘green’ materials in relay manufacturing. Buyers should look for suppliers that utilize recyclable or biodegradable materials, as well as those that adhere to stringent environmental regulations. By prioritizing sustainable and ethical sourcing, B2B buyers not only contribute to environmental conservation but also position themselves as responsible partners in the global supply chain.
What Is the Historical Context of Relay Manufacturing Relevant to B2B Buyers?
The relay manufacturing sector has evolved significantly since its inception in the late 19th century. Originally developed for telecommunication applications, relays have transformed into essential components across various industries, including automotive, industrial automation, and energy management. The early designs focused on mechanical switches, but advancements in materials and technology have led to the development of more sophisticated electromechanical and solid-state relays.
In the 20th century, the advent of electronic control systems significantly impacted relay design, enabling the production of smaller, more efficient devices capable of handling higher currents and voltages. This evolution is particularly relevant for international B2B buyers, as understanding the historical context allows them to appreciate the technological advancements that have shaped current relay offerings. As the industry continues to innovate, buyers are encouraged to stay informed about emerging technologies and trends that may influence their sourcing decisions in the future.
Frequently Asked Questions (FAQs) for B2B Buyers of relay manufacturer
-
How do I choose the right relay for my application?
Selecting the appropriate relay involves understanding your specific application needs. Consider the voltage and current ratings, the type of load (AC or DC), and whether you need normally open (NO) or normally closed (NC) contacts. Additionally, assess the relay’s switching speed and life expectancy, especially for high-frequency applications. Consult with manufacturers to explore customization options that suit your unique requirements. -
What are the key specifications to look for in a relay?
Key specifications include the voltage rating, current rating, coil resistance, switching capacity, and contact configuration. Ensure that the relay can handle the load it will control, and check for compatibility with your circuit’s specifications. Other important factors are the relay’s mechanical and electrical life ratings, as well as environmental ratings such as temperature range and humidity resistance, particularly for diverse climates in Africa, South America, the Middle East, and Europe.
-
What is the minimum order quantity (MOQ) for relays from manufacturers?
Minimum order quantities can vary significantly between manufacturers. Some may have an MOQ of just a few units, while others might require larger orders to justify production costs. It’s crucial to discuss your needs with potential suppliers to understand their MOQ policies and negotiate terms that align with your business requirements, especially if you are sourcing in smaller quantities for initial testing or specific projects. -
How can I ensure the quality of relays from manufacturers?
To ensure quality, request certifications such as ISO 9001 and industry-specific standards like UL or CE. Conduct audits or request samples before placing large orders. Additionally, review the manufacturer’s quality assurance processes, including testing protocols for each relay type. Feedback from previous customers can also provide insights into the manufacturer’s reliability and product performance. -
What payment terms should I expect when sourcing relays internationally?
Payment terms can vary widely based on the manufacturer and the region. Common terms include payment in advance, 30% deposit with the balance before shipping, or net 30/60 days after delivery. It’s important to clarify these terms upfront to avoid any misunderstandings. Additionally, consider using secure payment methods that offer buyer protection, particularly for international transactions. -
What logistics considerations should I keep in mind when importing relays?
When importing relays, consider shipping methods, customs regulations, and potential tariffs. Choose a reliable logistics provider familiar with international shipping to ensure timely delivery. Additionally, be aware of lead times for manufacturing and shipping, especially when sourcing from different continents like Africa or South America. Proper documentation and compliance with local regulations will facilitate smoother customs clearance. -
Can I customize relays to meet specific operational requirements?
Yes, many manufacturers offer customization options for relays. You can request specific coil voltages, terminal types, or contact configurations tailored to your application. Discuss your requirements early in the procurement process to ensure that the manufacturer can accommodate your needs. Custom solutions may involve additional lead times and costs, so factor these into your planning. -
What are the common applications for relays in various industries?
Relays find applications across multiple industries, including automotive, telecommunications, industrial automation, and home appliances. They are used for circuit protection, load switching, and automation tasks. For buyers in Africa, South America, the Middle East, and Europe, understanding industry-specific applications can help in selecting the right relay type that meets operational needs, from simple on/off control to complex automation systems.
Important Disclaimer & Terms of Use
⚠️ Important Disclaimer
The information provided in this guide, including content regarding manufacturers, technical specifications, and market analysis, is for informational and educational purposes only. It does not constitute professional procurement advice, financial advice, or legal advice.
While we have made every effort to ensure the accuracy and timeliness of the information, we are not responsible for any errors, omissions, or outdated information. Market conditions, company details, and technical standards are subject to change.
B2B buyers must conduct their own independent and thorough due diligence before making any purchasing decisions. This includes contacting suppliers directly, verifying certifications, requesting samples, and seeking professional consultation. The risk of relying on any information in this guide is borne solely by the reader.
Strategic Sourcing Conclusion and Outlook for relay manufacturer
Why is Strategic Sourcing Essential for B2B Buyers of Relays?
In the competitive landscape of relay manufacturing, strategic sourcing emerges as a vital approach for B2B buyers seeking to optimize their procurement processes. By focusing on building long-term relationships with reliable manufacturers, international buyers can ensure consistent quality and supply of relays that meet their specific operational needs. This not only mitigates risks associated with supply chain disruptions but also enhances product innovation through collaborative development.
How Can B2B Buyers from Africa, South America, the Middle East, and Europe Leverage Market Trends?
As buyers from regions such as Africa, South America, the Middle East, and Europe increasingly embrace digital transformation, understanding market trends becomes crucial. The demand for energy-efficient and smart relays is on the rise, driven by the global shift towards automation and sustainability. By staying informed about these trends, buyers can make more strategic decisions that align with their organizational goals and environmental commitments.
What Should International B2B Buyers Do Next?
In conclusion, the future of relay manufacturing is bright, characterized by technological advancements and evolving market demands. International B2B buyers are encouraged to engage proactively with manufacturers, evaluate their sourcing strategies, and explore innovative solutions that drive operational efficiency. Embrace the power of strategic sourcing today to secure a competitive edge in your industry.