Discover Top Benefits of Choosing a Tungsten Carbide Supplier (2025)
Introduction: Navigating the Global Market for tungsten carbide supplier
In the competitive landscape of industrial materials, sourcing high-quality tungsten carbide suppliers can present a significant challenge for international B2B buyers. This durable compound, known for its exceptional hardness and resistance to wear, is crucial for various applications ranging from cutting tools to mining equipment. As buyers navigate the global market, understanding the nuances of tungsten carbide sourcing becomes vital to ensure operational efficiency and cost-effectiveness.
This comprehensive guide delves into the multifaceted world of tungsten carbide suppliers, covering essential aspects such as types of tungsten carbide products, their diverse applications across industries, and critical supplier vetting processes. Additionally, we will explore cost factors influencing purchasing decisions, ensuring that buyers from Africa, South America, the Middle East, and Europe—particularly countries like Mexico and the UAE—are well-equipped to make informed choices.
By providing actionable insights and a structured approach to evaluating suppliers, this guide empowers B2B buyers to not only identify reliable sources but also to optimize their procurement strategies. With a clear focus on maximizing value and minimizing risks, our aim is to facilitate smarter purchasing decisions in a complex global market. Whether you are seeking to enhance your production capabilities or streamline your supply chain, this guide is your go-to resource for navigating the intricacies of tungsten carbide sourcing.
Understanding tungsten carbide supplier Types and Variations
Type Name | Key Distinguishing Features | Primary B2B Applications | Brief Pros & Cons for Buyers |
---|---|---|---|
High-Grade Tungsten Carbide Suppliers | Offer premium quality tungsten carbide with high purity levels and superior hardness. | Aerospace, mining, and oil drilling tools. | Pros: Enhanced durability and performance. Cons: Higher cost may limit budget flexibility. |
Custom Tungsten Carbide Manufacturers | Provide tailored solutions based on specific client requirements, including size and composition. | Specialized industrial tools and components. | Pros: Meets unique specifications. Cons: Longer lead times for production. |
Bulk Tungsten Carbide Suppliers | Focus on high-volume sales, often at reduced rates per unit. | Construction and heavy machinery industries. | Pros: Cost-effective for large orders. Cons: Limited customization options. |
Tungsten Carbide Recycling Companies | Specialize in reclaiming and recycling tungsten carbide materials to reduce waste. | Sustainable manufacturing processes. | Pros: Eco-friendly and cost-saving. Cons: May have variability in material quality. |
Integrated Tungsten Carbide Suppliers | Offer a full range of services from raw material supply to finished products. | Manufacturing and tooling sectors. | Pros: Streamlined procurement and logistics. Cons: May lack specialization in niche applications. |
What Are the Characteristics of High-Grade Tungsten Carbide Suppliers?
High-grade tungsten carbide suppliers focus on providing products with superior quality and purity. These suppliers often cater to industries that require exceptional hardness and durability, such as aerospace and mining. When purchasing, B2B buyers should consider the supplier’s certifications and quality assurance processes, as these factors significantly influence product reliability and performance. While the upfront costs may be higher, the long-term benefits of reduced wear and tear can justify the investment.
How Do Custom Tungsten Carbide Manufacturers Meet Unique Needs?
Custom tungsten carbide manufacturers specialize in creating tailored solutions to meet specific client requirements, including unique dimensions and compositions. This type of supplier is ideal for businesses needing specialized tools or components that standard products cannot fulfill. Buyers should assess the manufacturer’s capabilities in terms of design flexibility and turnaround times. Although custom solutions may come with longer lead times, they ensure that the products align perfectly with operational needs.
What Are the Benefits of Bulk Tungsten Carbide Suppliers?
Bulk tungsten carbide suppliers focus on high-volume sales, making them a cost-effective option for industries like construction and heavy machinery. These suppliers typically offer lower rates per unit, appealing to businesses with large-scale procurement needs. However, buyers should be aware that bulk suppliers may not provide the same level of customization as smaller manufacturers. It is essential to evaluate whether the standard offerings meet the specific requirements of your projects.
Why Choose Tungsten Carbide Recycling Companies?
Tungsten carbide recycling companies are becoming increasingly relevant in today’s eco-conscious market. These suppliers specialize in reclaiming and recycling tungsten carbide materials, providing a sustainable option for manufacturers looking to minimize waste. When considering these suppliers, buyers should evaluate the quality of the recycled materials and the processes used for reclamation. While cost savings and environmental benefits are significant advantages, variability in material quality may pose challenges.
What Advantages Do Integrated Tungsten Carbide Suppliers Offer?
Integrated tungsten carbide suppliers provide a comprehensive range of services, from raw material supply to finished product manufacturing. This approach streamlines the procurement process for B2B buyers, allowing them to manage logistics and quality assurance more effectively. However, buyers should consider whether the supplier has the necessary expertise in niche applications, as a one-size-fits-all approach may not be suitable for specialized needs.
Related Video: Understanding Carbide Cutters
Key Industrial Applications of tungsten carbide supplier
Industry/Sector | Specific Application of tungsten carbide supplier | Value/Benefit for the Business | Key Sourcing Considerations for this Application |
---|---|---|---|
Mining and Drilling | Manufacturing drill bits and cutting tools | Enhanced durability and efficiency in mineral extraction | Quality certifications, wear resistance, and global delivery options |
Construction | Production of concrete and asphalt cutting tools | Increased productivity and reduced downtime during projects | Customization options and compliance with local regulations |
Aerospace and Defense | Components for jet engines and military equipment | High-performance under extreme conditions | Supplier reliability, material specifications, and testing standards |
Manufacturing | Creation of wear-resistant parts for machinery | Lower maintenance costs and extended machinery lifespan | Availability of technical support and quick turnaround times |
Oil and Gas | Production of valves and pumps | Improved safety and efficiency in fluid transport | Understanding of industry-specific standards and certifications |
How is Tungsten Carbide Used in Mining and Drilling Applications?
Tungsten carbide suppliers play a crucial role in the mining and drilling sector by providing durable drill bits and cutting tools. These tools are essential for penetrating hard rock formations, significantly improving extraction efficiency. The primary problem addressed is wear and tear on drilling equipment, which can lead to costly downtimes. Buyers in this sector must ensure that suppliers meet strict quality certifications and offer products with high wear resistance, as well as reliable global delivery options to mitigate supply chain disruptions.

A stock image related to tungsten carbide supplier.
What Role Does Tungsten Carbide Play in Construction?
In the construction industry, tungsten carbide is utilized in the production of cutting tools for concrete and asphalt. These tools benefit from tungsten carbide’s exceptional hardness, which allows for faster cutting speeds and less frequent tool replacement, thereby increasing overall productivity. For international buyers, particularly from regions with stringent building regulations, sourcing options must include customization to meet specific project requirements and compliance with local standards to ensure safety and quality.
How is Tungsten Carbide Applied in Aerospace and Defense?
Tungsten carbide is integral in manufacturing components for jet engines and military equipment due to its ability to withstand extreme temperatures and pressures. This application enhances performance and reliability in critical aerospace operations. Buyers in this sector need to consider the supplier’s reliability and adherence to material specifications, as well as rigorous testing standards that ensure product safety and performance in high-stakes environments.
What Benefits Does Tungsten Carbide Provide in Manufacturing?
In manufacturing, tungsten carbide is used to create wear-resistant parts for various machinery, including cutting tools and dies. The key advantage is the significant reduction in maintenance costs and an extended lifespan of machinery, which translates into higher operational efficiency. International buyers should prioritize suppliers that offer robust technical support and can deliver products with quick turnaround times, especially in regions where manufacturing demands are high.
How Does Tungsten Carbide Enhance Oil and Gas Operations?
In the oil and gas industry, tungsten carbide is crucial for producing valves and pumps used in fluid transport systems. The material’s durability ensures improved safety and efficiency, reducing the risk of leaks and failures. Buyers in this sector must have a clear understanding of industry-specific standards and certifications when sourcing tungsten carbide components, as compliance is critical for operational integrity and safety in hazardous environments.
Related Video: TUNGSTEN CARBIDE COATING (HVOF)
3 Common User Pain Points for ‘tungsten carbide supplier’ & Their Solutions
Scenario 1: Inconsistent Quality of Tungsten Carbide Products
The Problem:
International B2B buyers often encounter significant challenges when sourcing tungsten carbide from suppliers, particularly regarding product quality. Discrepancies in material composition and manufacturing processes can lead to variations in hardness, durability, and overall performance. For instance, a buyer in South America may receive a batch of tungsten carbide that fails to meet the required specifications for a specific application, resulting in increased operational costs and delays in production.
The Solution:
To ensure consistent quality from tungsten carbide suppliers, buyers should implement a rigorous supplier evaluation process. This includes requesting detailed material certifications and performance data, such as hardness tests and wear resistance metrics. Establishing long-term partnerships with reputable suppliers who adhere to international standards (like ISO certifications) can also mitigate quality issues. Additionally, conducting regular audits and quality checks on shipments can help ensure that the products meet your specifications before they are put into use. Engaging in open communication about quality expectations and feedback can foster a more transparent relationship, ultimately leading to improved product consistency.
Scenario 2: Difficulty in Finding Reliable Suppliers for Tungsten Carbide
The Problem:
Buyers often struggle to find reliable tungsten carbide suppliers, especially when sourcing from regions like Africa or the Middle East. The lack of transparency in the supply chain, coupled with language barriers and differing business practices, can create confusion and mistrust. This situation is further complicated when trying to verify the legitimacy and credibility of new suppliers, leading to potential financial losses and delays in project timelines.
The Solution:
To navigate the complexities of supplier selection, buyers should leverage industry-specific networks and platforms that facilitate introductions to verified tungsten carbide suppliers. Utilizing resources such as trade shows, industry associations, and B2B marketplaces can help establish connections with reputable suppliers. Additionally, conducting thorough due diligence, including checking references and customer reviews, can provide insights into a supplier’s reliability. Buyers should also consider implementing a trial order to assess the supplier’s capabilities and product quality before committing to larger contracts. By prioritizing suppliers with established track records and positive feedback, buyers can reduce the risks associated with sourcing.
Scenario 3: Understanding the Technical Specifications of Tungsten Carbide
The Problem:
Many international B2B buyers face challenges in understanding the technical specifications of tungsten carbide products, which can vary significantly depending on the application. This knowledge gap can lead to the procurement of inappropriate grades or forms of tungsten carbide, resulting in suboptimal performance or premature failure in applications like cutting tools or industrial machinery.
The Solution:
To bridge the knowledge gap, buyers should invest time in understanding the various grades and specifications of tungsten carbide, including their mechanical properties and applications. Engaging with suppliers who offer technical support and guidance can also be beneficial. Buyers should request detailed product data sheets and consult with supplier engineers to clarify any uncertainties regarding product specifications. Furthermore, participating in workshops or training sessions on tungsten carbide applications can enhance a buyer’s understanding and decision-making capabilities. By equipping themselves with this knowledge, buyers can make informed procurement choices that align with their operational needs, ultimately enhancing productivity and reducing costs.
Strategic Material Selection Guide for tungsten carbide supplier
When selecting materials for tungsten carbide applications, international B2B buyers must consider various factors that influence performance, cost, and suitability for specific applications. Below, we analyze several common materials that are integral to tungsten carbide production, providing actionable insights for buyers from Africa, South America, the Middle East, and Europe.
What are the Key Properties of Tungsten Carbide?
Tungsten carbide (WC) is a composite material made from tungsten and carbon, known for its exceptional hardness and durability. Key properties include:
- Hardness: Comparable to diamond, making it ideal for cutting and drilling tools.
- Temperature Resistance: Maintains structural integrity at high temperatures, up to 2870°C.
- Corrosion Resistance: Generally resistant to acids and bases, although it can be affected by strong acids like nitric and hydrofluoric acid.
These properties make tungsten carbide suitable for various industrial applications, including mining, metalworking, and manufacturing.
What are the Pros and Cons of Tungsten Carbide?
Pros:
- Durability: Tungsten carbide tools have a long lifespan, reducing the need for frequent replacements.
- Versatility: Can be used in a variety of applications, from cutting tools to wear-resistant surfaces.
- Cost-Effectiveness: Although initial costs may be high, the longevity of tungsten carbide products often leads to lower overall costs.
Cons:
- Brittleness: Pure tungsten carbide can be brittle, necessitating the addition of other metals (like cobalt) to enhance toughness.
- Manufacturing Complexity: The production process can be intricate and requires specialized equipment, which may increase costs.
How Does Material Selection Impact Application?
The choice of materials in tungsten carbide applications significantly affects performance. For example, the addition of titanium carbide (TiC) can enhance hardness and wear resistance, making it suitable for high-impact applications. Conversely, using cobalt as a binder can improve toughness but may reduce hardness.
What Should International B2B Buyers Consider?
International buyers need to be aware of compliance with regional standards such as ASTM (American Society for Testing and Materials), DIN (Deutsches Institut für Normung), and JIS (Japanese Industrial Standards). Additionally, local preferences regarding material properties and performance should guide material selection. For instance, buyers from the UAE may prioritize corrosion resistance due to the region’s climate, while those in South America might focus on cost-effectiveness and durability.
Summary Table of Material Selection for Tungsten Carbide
Material | Typical Use Case for tungsten carbide supplier | Key Advantage | Key Disadvantage/Limitation | Relative Cost (Low/Med/High) |
---|---|---|---|---|
Tungsten Carbide (WC) | Cutting tools, wear-resistant surfaces | Exceptional hardness and durability | Brittle without additives | High |
Cobalt-Bonded Tungsten Carbide | Mining tools, industrial machinery | Enhanced toughness | Lower hardness compared to pure WC | Medium |
Titanium Carbide (TiC) | High-performance cutting tools | Improved hardness and wear resistance | Higher production costs | High |
Tungsten Carbide with Nickel | Oil and gas drilling components | Excellent corrosion resistance | Costly compared to other binders | High |
This guide provides a strategic overview of material selection for tungsten carbide suppliers, helping international B2B buyers make informed decisions that align with their operational needs and regional standards.
In-depth Look: Manufacturing Processes and Quality Assurance for tungsten carbide supplier
What Are the Main Stages of Tungsten Carbide Manufacturing Processes?
Tungsten carbide (WC) is an essential material for various industrial applications, particularly in cutting tools and wear-resistant components. Understanding the manufacturing processes involved in producing tungsten carbide can help B2B buyers assess potential suppliers effectively. The manufacturing process typically includes four main stages: material preparation, forming, assembly, and finishing.
How Is Material Prepared in Tungsten Carbide Production?
The initial stage involves the selection and preparation of raw materials, primarily tungsten powder and carbon. The tungsten powder is usually produced through a reduction process where tungsten oxide is reduced with hydrogen. The purity and particle size of these powders are critical, as they directly influence the final product’s properties.
Once the raw materials are ready, they are mixed in specific ratios, often with the addition of binder materials such as cobalt or nickel. This mixture is then subjected to a milling process to achieve a uniform particle size, which is essential for consistent properties in the final product.
What Techniques Are Used in the Forming Stage?
The forming stage employs various techniques to shape the tungsten carbide powder into the desired form. The most common methods include:
- Cold Isostatic Pressing (CIP): This technique uses high pressure to compact the powder uniformly in a mold, creating a green part that retains its shape during subsequent processing.
- Hot Pressing (HP): In this method, heat and pressure are applied simultaneously, which facilitates the sintering process and enhances the density of the final product.
These techniques ensure that the tungsten carbide components achieve the required density and structural integrity before moving on to assembly.
What Happens During the Assembly and Finishing Processes?
After forming, the green parts undergo sintering, where they are heated to a temperature below their melting point in a controlled atmosphere. This process allows the tungsten carbide particles to bond together, creating a hard, durable material.
Once sintering is complete, finishing processes such as grinding, polishing, and coating are performed to achieve precise dimensions and surface finishes. These finishing techniques are critical for applications requiring high precision and surface quality, such as in cutting tools.
How Is Quality Assurance Implemented in Tungsten Carbide Manufacturing?
Quality assurance (QA) is a vital aspect of tungsten carbide manufacturing, ensuring that products meet international standards and customer expectations. B2B buyers should be aware of the quality control measures employed by suppliers to verify the reliability of their products.
Which International Standards Are Relevant for Tungsten Carbide Suppliers?
Many tungsten carbide suppliers adhere to international quality standards, with ISO 9001 being the most recognized. This standard focuses on establishing a quality management system (QMS) that enhances customer satisfaction through effective processes. Additionally, suppliers may comply with industry-specific standards such as CE marking for products sold in Europe and API standards for oil and gas applications.
What Are the Key Quality Control Checkpoints in the Manufacturing Process?
Quality control in tungsten carbide manufacturing involves several checkpoints throughout the production process:
- Incoming Quality Control (IQC): This involves inspecting raw materials and components before they enter the manufacturing process. Suppliers should have stringent criteria to ensure that only high-quality materials are used.
- In-Process Quality Control (IPQC): During manufacturing, regular checks are conducted to monitor process parameters and product characteristics, ensuring that any deviations are promptly addressed.
- Final Quality Control (FQC): After the product is finished, a comprehensive inspection is performed to verify that it meets the specified requirements before shipment.
What Common Testing Methods Are Used to Ensure Quality?
To ensure quality, suppliers typically employ several testing methods, including:
- Microstructure Analysis: This involves examining the material’s microstructure to assess grain size, phase distribution, and other characteristics that influence performance.
- Hardness Testing: Hardness is a crucial property for tungsten carbide applications. Common methods include Rockwell and Vickers hardness tests.
- Dimensional Checks: Precision measurement tools are used to verify that the final product meets specified dimensions.
How Can B2B Buyers Verify Supplier Quality Control?
For international B2B buyers, particularly those from Africa, South America, the Middle East, and Europe, verifying a supplier’s quality control processes is essential to mitigate risks associated with product quality.
What Steps Can Buyers Take to Conduct Supplier Audits?
Conducting supplier audits is one of the most effective ways to assess a supplier’s quality control practices. Buyers should consider the following steps:
- Request Documentation: Ask for quality management system documentation, including certifications, quality manuals, and audit reports.
- On-Site Visits: If possible, conduct on-site visits to observe the manufacturing processes and quality control measures in action.
- Third-Party Inspections: Engage third-party inspection agencies to conduct independent assessments of the supplier’s quality control systems and product quality.
What Are the Quality Control Nuances for International Buyers?
International buyers should be aware of specific nuances that may affect quality control, such as:
- Regulatory Compliance: Different regions may have varying regulatory requirements that suppliers must meet. Understanding these can help buyers ensure compliance and avoid potential issues.
- Cultural Differences: Quality standards and expectations may vary across cultures. Buyers should communicate their quality requirements clearly to ensure alignment with suppliers.
Conclusion
Understanding the manufacturing processes and quality assurance measures in tungsten carbide production is crucial for B2B buyers. By focusing on the stages of manufacturing, the implementation of quality control, and the verification of supplier practices, international buyers can make informed decisions when selecting tungsten carbide suppliers, ensuring that they receive high-quality products that meet their specific needs.
Practical Sourcing Guide: A Step-by-Step Checklist for ‘tungsten carbide supplier’
When sourcing tungsten carbide suppliers, it’s essential to follow a structured approach to ensure you select a reliable partner who meets your specific needs. This guide provides a practical checklist that international B2B buyers, particularly from Africa, South America, the Middle East, and Europe, can use to streamline their procurement process.
Step 1: Define Your Technical Specifications
Before reaching out to potential suppliers, it’s crucial to have a clear understanding of your technical requirements. This includes specifying the grade of tungsten carbide needed, dimensions, and any particular properties like hardness or thermal resistance.
– Considerations:
– Are you looking for tungsten carbide for cutting tools, industrial machinery, or wear-resistant parts?
– Ensure that your specifications align with industry standards to facilitate smoother discussions with suppliers.
Step 2: Conduct Market Research on Suppliers
Research potential suppliers to understand their reputation and track record in the industry. Look for reviews, ratings, and testimonials from other buyers, especially those in your region.
– Key actions:
– Utilize platforms like Alibaba, ThomasNet, or industry-specific directories to gather supplier options.
– Pay attention to suppliers who specialize in your required applications, as they will likely have more relevant experience.
Step 3: Evaluate Supplier Certifications
It’s vital to verify the certifications and compliance of your shortlisted suppliers. Quality certifications such as ISO 9001 or industry-specific standards indicate that the supplier adheres to international quality management practices.
– What to check:
– Request copies of certifications and ask about their quality control processes.
– Ensure they comply with any local regulations relevant to your industry, particularly if you are importing products.
Step 4: Request Samples for Testing
Once you have narrowed down your options, request samples of the tungsten carbide products you intend to purchase. This allows you to evaluate the quality and performance before making a larger commitment.
– Why it matters:
– Testing samples helps ensure that the products meet your specifications and perform as required.
– Consider using the samples in your actual applications to assess durability and suitability.
Step 5: Inquire About Pricing and Payment Terms
Discuss pricing structures with potential suppliers to understand their cost models. Be clear about your budget and negotiate payment terms that are favorable to your business.
– Important factors:
– Ask about volume discounts, payment options, and shipping costs.
– Ensure that the pricing reflects the quality of the materials and that there are no hidden fees.
Step 6: Assess Communication and Support Services
Effective communication is crucial for a successful supplier relationship. Assess how responsive and helpful suppliers are during your initial interactions.
– Considerations:
– Evaluate their customer service capabilities and whether they offer support in your preferred language.
– Strong communication can prevent misunderstandings and facilitate smoother transactions.
Step 7: Check References and Case Studies
Before finalizing your choice, ask suppliers for references or case studies from previous clients. This step can provide insight into their reliability and customer satisfaction levels.
– What to look for:
– Contact references to inquire about their experiences and any challenges they faced.
– Review case studies to see how the supplier has handled similar projects or industries.
By following this step-by-step checklist, B2B buyers can effectively navigate the complexities of sourcing tungsten carbide suppliers, ensuring that they make informed decisions that align with their business objectives.
Comprehensive Cost and Pricing Analysis for tungsten carbide supplier Sourcing
What Are the Key Cost Components in Tungsten Carbide Supplier Pricing?
When evaluating the costs associated with sourcing tungsten carbide, several key components must be considered. These include:
-
Materials: The primary raw materials for tungsten carbide are tungsten and carbon. Fluctuations in the prices of these metals can significantly impact overall costs. Buyers should monitor market trends for tungsten and carbon to better anticipate price changes.
-
Labor: Labor costs can vary widely based on the supplier’s location. Regions with higher labor costs, such as Western Europe, may result in higher prices for tungsten carbide products compared to suppliers in countries with lower labor costs.
-
Manufacturing Overhead: This includes expenses related to facilities, equipment, and utilities. Efficient manufacturing processes can lead to lower overhead costs, which can be passed on to buyers.
-
Tooling: The creation of specialized tooling for tungsten carbide products can add to the initial costs. However, investing in high-quality tooling can improve production efficiency and product quality over time.
-
Quality Control (QC): Ensuring that products meet industry standards incurs additional costs. Suppliers that implement rigorous QC processes may charge higher prices, but this investment can result in superior product performance and reliability.
-
Logistics: Transportation and shipping costs are crucial, especially for international buyers. Factors such as distance, shipping method, and customs duties can all influence the total logistics cost.
-
Margin: Suppliers typically include a profit margin in their pricing. Understanding the average industry margin can help buyers gauge whether the offered price is competitive.
How Do Price Influencers Affect Tungsten Carbide Supplier Pricing?
Several factors can influence the pricing of tungsten carbide products:
-
Volume and Minimum Order Quantity (MOQ): Larger orders often qualify for discounts. Buyers should negotiate MOQs that align with their needs to optimize costs.
-
Specifications and Customization: Custom specifications, such as unique sizes or material blends, can significantly increase costs. Buyers should clearly communicate their requirements to avoid unnecessary customization charges.
-
Material Quality and Certifications: Higher quality materials or specific certifications (e.g., ISO) can lead to increased prices. However, investing in certified products can enhance performance and compliance with industry standards.
-
Supplier Factors: The reputation and reliability of the supplier play a crucial role in pricing. Established suppliers may charge a premium for their experience and service quality.
-
Incoterms: Understanding Incoterms is essential for international transactions. Different terms can affect the final price by determining who is responsible for shipping costs, insurance, and customs duties.
What Are the Best Buyer Tips for Cost-Efficiency in Tungsten Carbide Sourcing?
To achieve cost-efficiency when sourcing tungsten carbide, international buyers should consider the following strategies:
-
Negotiate Effectively: Always enter negotiations with a clear understanding of the market price and the supplier’s cost structure. Building a strong relationship with suppliers can lead to better pricing and terms over time.
-
Evaluate Total Cost of Ownership (TCO): Rather than focusing solely on the upfront price, consider the TCO, which includes maintenance, durability, and potential downtime costs. A higher initial investment may yield long-term savings.
-
Research Pricing Nuances for Your Region: Different regions may have varying price structures due to local market conditions and regulations. Buyers in Africa, South America, the Middle East, and Europe should conduct thorough market research to understand regional pricing dynamics.
-
Seek Multiple Quotes: Obtaining quotes from various suppliers allows for better comparison and negotiation leverage. It’s essential to evaluate not just the price but also the quality and reliability of the suppliers.
-
Stay Informed on Market Trends: Keeping abreast of global commodity prices, especially for tungsten and carbon, can help buyers anticipate price changes and make informed purchasing decisions.
Disclaimer on Indicative Prices
It is important to note that the prices for tungsten carbide products can vary widely based on the factors discussed above. Buyers should consult with suppliers for the most accurate and up-to-date pricing information tailored to their specific needs.
Alternatives Analysis: Comparing tungsten carbide supplier With Other Solutions
Understanding Alternatives to Tungsten Carbide Suppliers
In the competitive landscape of industrial materials, B2B buyers must consider various options that can meet their specific needs. Tungsten carbide is renowned for its hardness and durability, making it a preferred choice for numerous applications. However, alternative solutions exist that may offer unique advantages depending on the context of use. This section delves into these alternatives, providing a comprehensive comparison to help buyers make informed decisions.
Comparison Table of Tungsten Carbide and Alternatives
Comparison Aspect | Tungsten Carbide Supplier | Alternative 1: Ceramic Tools | Alternative 2: High-Speed Steel (HSS) |
---|---|---|---|
Performance | High hardness, excellent wear resistance | Good hardness, less durable than tungsten carbide | Moderate hardness, good for various cutting tasks |
Cost | Higher initial investment | Generally lower cost | Moderate cost, but varies with grade |
Ease of Implementation | Requires specialized handling | Easier to handle and operate | Standard tools, widely available |
Maintenance | Minimal maintenance needed | Requires regular checks for wear | Regular sharpening needed |
Best Use Case | Heavy-duty machining, mining tools | Light to medium-duty applications | General machining, tool bits |
Detailed Breakdown of Alternative Solutions
What are the Benefits and Drawbacks of Ceramic Tools?
Ceramic tools are an increasingly popular alternative to tungsten carbide, particularly in applications that do not require extreme durability. Their primary advantage lies in their lower cost and sufficient performance for light to medium-duty tasks. They exhibit good hardness and can maintain a sharp edge longer than some metals. However, ceramics are more brittle than tungsten carbide, making them susceptible to chipping and breaking under high-stress conditions. Consequently, they are best suited for non-impact applications like fine machining of softer materials.
How Does High-Speed Steel (HSS) Compare to Tungsten Carbide?
High-speed steel (HSS) is another viable alternative that offers a balance between performance and cost. HSS tools are versatile and can be used in a wide range of machining processes, making them ideal for general applications. They are easier to sharpen and repair, which can be a significant advantage in environments where downtime needs to be minimized. However, HSS lacks the extreme hardness and wear resistance of tungsten carbide, meaning it may wear out faster under rigorous conditions. As such, HSS is best employed in environments where the workload is moderate, and tool replacement can be managed efficiently.
Conclusion: How Should B2B Buyers Select the Right Material?
Choosing the right material or supplier for industrial applications requires a careful assessment of specific operational needs and constraints. For buyers from Africa, South America, the Middle East, and Europe, understanding the performance characteristics, cost implications, and maintenance requirements of each alternative is crucial. While tungsten carbide excels in durability and performance, alternatives like ceramic tools and high-speed steel may provide cost-effective solutions for less demanding applications. Ultimately, the decision should align with the intended use case, budget constraints, and the operational environment to ensure optimal performance and return on investment.
Essential Technical Properties and Trade Terminology for tungsten carbide supplier
What Are the Key Technical Properties of Tungsten Carbide for B2B Buyers?
Understanding the essential technical properties of tungsten carbide is crucial for international B2B buyers, especially when sourcing high-performance materials for manufacturing and industrial applications. Here are some of the critical specifications to consider:
-
Material Grade: Tungsten carbide is available in various grades that determine its hardness, toughness, and wear resistance. Common grades include WC-Co (tungsten carbide-cobalt) and WC-Ni (tungsten carbide-nickel). Selecting the appropriate grade is vital for applications ranging from cutting tools to mining equipment, as it directly impacts performance and durability.
-
Density: The density of tungsten carbide typically ranges from 14.5 to 15.9 g/cm³. This property is significant because higher density often correlates with greater hardness and strength, making it suitable for heavy-duty applications. Buyers should evaluate density specifications to ensure the material meets their application requirements.
-
Hardness: Tungsten carbide exhibits a hardness rating of about 1500-2000 HV (Vickers hardness). This exceptional hardness makes it ideal for cutting tools and industrial machinery, where wear resistance is critical. Understanding the hardness levels can help buyers assess the longevity of their tools and components.
-
Tolerance: Tolerance refers to the allowable deviation from a specified dimension. For tungsten carbide components, maintaining tight tolerances (often ±0.01 mm) is crucial for ensuring proper fit and function in precision applications. Buyers should verify the manufacturer’s ability to meet specified tolerances to avoid costly rework or failures.
-
Thermal Conductivity: Tungsten carbide is known for its excellent thermal conductivity, which allows it to dissipate heat effectively during high-speed machining processes. This property is particularly important in applications where heat build-up can lead to tool failure or decreased performance.
-
Chemical Resistance: Tungsten carbide is resistant to various chemicals, including acids and alkalis, making it suitable for harsh environments. This property is essential for buyers in industries like oil and gas, where equipment may encounter corrosive substances.
What Are the Common Trade Terms Used in Tungsten Carbide Procurement?
Familiarizing oneself with industry jargon is vital for effective communication and negotiation in the B2B sector. Here are some common terms relevant to tungsten carbide suppliers:
-
OEM (Original Equipment Manufacturer): This term refers to companies that produce parts or equipment that may be marketed by another manufacturer. For tungsten carbide, OEMs often require specific grades and tolerances tailored to their equipment, making it essential for suppliers to understand their unique needs.
-
MOQ (Minimum Order Quantity): MOQ is the smallest quantity of a product that a supplier is willing to sell. Understanding MOQ is crucial for B2B buyers as it can affect inventory management and cash flow. Buyers should negotiate MOQs to ensure they align with their production schedules.
-
RFQ (Request for Quotation): An RFQ is a document sent to suppliers requesting pricing for specific quantities of materials. Including detailed specifications in the RFQ helps suppliers provide accurate quotes, facilitating smoother procurement processes.
-
Incoterms (International Commercial Terms): These are internationally recognized rules that define the responsibilities of buyers and sellers in shipping and delivery. Familiarity with Incoterms like FOB (Free on Board) or CIF (Cost, Insurance, and Freight) can help B2B buyers negotiate better shipping terms and avoid misunderstandings.
-
Lead Time: This term refers to the time taken from placing an order to receiving the product. Understanding lead times is essential for production planning, as delays can impact project timelines and costs.
-
Certification: Many tungsten carbide products require certifications to meet industry standards (e.g., ISO, ASTM). Buyers should ensure that their suppliers provide the necessary certifications to guarantee product quality and compliance with regulations.
By grasping these technical properties and trade terms, international B2B buyers from regions like Africa, South America, the Middle East, and Europe can make informed decisions when sourcing tungsten carbide products, ensuring they meet their operational needs effectively.
Navigating Market Dynamics and Sourcing Trends in the tungsten carbide supplier Sector
What Are the Current Market Dynamics and Key Trends in the Tungsten Carbide Supplier Sector?
The tungsten carbide supplier sector is witnessing significant growth driven by a variety of global factors. Key markets in Africa, South America, the Middle East, and Europe are increasingly demanding high-performance materials for industries such as manufacturing, mining, and construction. The growing need for precision engineering tools, such as cutting and drilling equipment, is pushing suppliers to innovate and improve product quality. Furthermore, technological advancements in manufacturing processes, including additive manufacturing and enhanced sintering techniques, are enabling suppliers to offer tailored solutions to meet specific customer needs.
B2B buyers are increasingly leveraging digital platforms to source tungsten carbide products, with e-commerce and online marketplaces becoming essential tools for procurement. This trend is particularly pronounced in regions like the UAE and Mexico, where businesses are seeking to streamline their supply chains and reduce lead times. Additionally, the rise of Industry 4.0 is fostering a shift towards smarter supply chain management, allowing companies to better predict demand and optimize inventory levels. As a result, buyers must stay informed about these trends to remain competitive in a rapidly evolving marketplace.
How Does Sustainability and Ethical Sourcing Impact the Tungsten Carbide Supply Chain?
Sustainability is becoming a critical consideration for international B2B buyers in the tungsten carbide sector. The environmental impact of tungsten carbide production, particularly regarding mining practices and waste management, cannot be overlooked. Ethical sourcing is increasingly important, as companies face pressure from consumers and regulatory bodies to ensure that their materials are sourced responsibly. Buyers should prioritize suppliers who adhere to sustainable practices and who can demonstrate transparency in their supply chains.
Green certifications and eco-friendly materials are gaining traction in the tungsten carbide market. Certifications such as ISO 14001 (Environmental Management) and adherence to the OECD Due Diligence Guidance for Responsible Supply Chains can help buyers identify suppliers committed to sustainability. Moreover, the development of recycled tungsten carbide products offers a viable alternative for companies looking to minimize their environmental footprint. By choosing suppliers who prioritize sustainability, buyers not only comply with regulatory demands but also enhance their brand reputation in a market that increasingly values corporate social responsibility.
What Is the Historical Context of Tungsten Carbide Supply and Its Relevance Today?
The history of tungsten carbide dates back to the early 20th century when it was first synthesized for use in cutting tools due to its exceptional hardness and durability. Over the decades, the material has evolved significantly, expanding its applications beyond traditional manufacturing into sectors such as aerospace and oil and gas. The introduction of advanced materials and composites has further enhanced the performance of tungsten carbide, making it indispensable in high-stress environments.
Understanding the historical context of tungsten carbide can help B2B buyers appreciate the material’s unique properties and its evolution in manufacturing technologies. This knowledge not only informs purchasing decisions but also fosters strategic partnerships with suppliers who can provide innovative solutions that meet the demands of modern industry. As the market continues to grow and diversify, buyers equipped with this historical insight will be better positioned to navigate the complexities of sourcing tungsten carbide effectively.
Frequently Asked Questions (FAQs) for B2B Buyers of tungsten carbide supplier
-
How do I evaluate the quality of tungsten carbide suppliers?
To evaluate the quality of tungsten carbide suppliers, start by reviewing their certifications and industry standards, such as ISO 9001. Look for suppliers with a proven track record of quality control and customer satisfaction. Request samples to assess the material’s hardness, durability, and resistance to wear. Additionally, consider customer reviews and case studies that demonstrate their ability to meet specific needs, especially in your region, whether it be Africa, South America, the Middle East, or Europe. -
What are the key factors to consider when choosing a tungsten carbide supplier?
When choosing a tungsten carbide supplier, consider factors such as product range, customization capabilities, minimum order quantities (MOQs), and lead times. Assess their manufacturing processes and technology to ensure they can meet your quality standards. Evaluate their logistics and shipping capabilities, especially for international transactions, to avoid delays. Finally, examine their customer support and after-sales service to ensure a smooth purchasing experience. -
What is the typical lead time for tungsten carbide orders?
The typical lead time for tungsten carbide orders can vary significantly based on the supplier and the complexity of the order. Generally, standard products may have a lead time of 2-4 weeks, while custom orders can take 6-12 weeks or more. It’s crucial to communicate your timeline requirements upfront and confirm the supplier’s ability to meet these deadlines, especially if you are operating within tight project schedules. -
What payment terms should I expect when sourcing tungsten carbide?
Payment terms for tungsten carbide suppliers can vary widely. Many suppliers require a deposit upfront, typically 30-50%, with the balance due before shipment. Some may offer credit terms for established businesses, such as net 30 or net 60 days. Always clarify payment methods accepted, such as wire transfer, credit card, or letters of credit, especially for international transactions, to ensure a secure payment process. -
Can tungsten carbide products be customized for specific applications?
Yes, many tungsten carbide suppliers offer customization options tailored to specific applications. Customizations can include variations in size, shape, and composition, which can enhance performance for particular industries such as mining, drilling, or manufacturing. When discussing customization, provide detailed specifications to the supplier to ensure that the final product meets your operational needs. -
What are the common quality assurance practices used by tungsten carbide suppliers?
Common quality assurance practices among tungsten carbide suppliers include rigorous testing and inspection of raw materials, in-process checks during manufacturing, and final product evaluations. Suppliers often employ techniques such as hardness testing, microstructural analysis, and dimensional inspections to ensure compliance with quality standards. Inquire about their QA processes and certifications to ensure they align with your quality requirements. -
How do international shipping and logistics work for tungsten carbide products?
International shipping and logistics for tungsten carbide products typically involve multiple steps, including customs clearance and freight forwarding. Suppliers should provide details about shipping options, estimated transit times, and any potential tariffs or duties applicable to your country. Ensure that the supplier can handle all logistics aspects, including packaging, documentation, and delivery to your specified location, to streamline the process. -
What should I do if I encounter issues with my tungsten carbide order?
If you encounter issues with your tungsten carbide order, promptly communicate with the supplier to discuss the problem. Document all relevant details, including order numbers, product specifications, and photos of the issues. Most reputable suppliers will have a return or resolution policy in place. Work collaboratively with them to resolve the issue, whether it involves replacements, refunds, or adjustments to future orders.
Important Disclaimer & Terms of Use
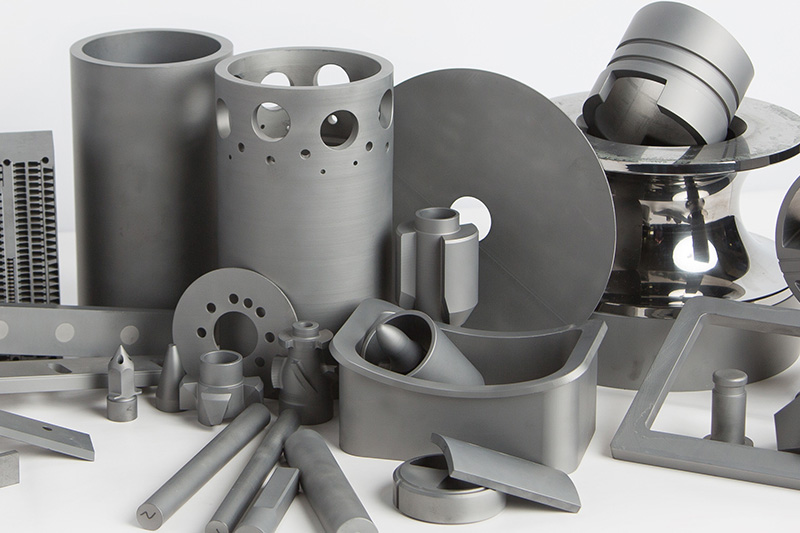
A stock image related to tungsten carbide supplier.
⚠️ Important Disclaimer
The information provided in this guide, including content regarding manufacturers, technical specifications, and market analysis, is for informational and educational purposes only. It does not constitute professional procurement advice, financial advice, or legal advice.
While we have made every effort to ensure the accuracy and timeliness of the information, we are not responsible for any errors, omissions, or outdated information. Market conditions, company details, and technical standards are subject to change.
B2B buyers must conduct their own independent and thorough due diligence before making any purchasing decisions. This includes contacting suppliers directly, verifying certifications, requesting samples, and seeking professional consultation. The risk of relying on any information in this guide is borne solely by the reader.
Strategic Sourcing Conclusion and Outlook for tungsten carbide supplier
In the dynamic landscape of tungsten carbide sourcing, the importance of strategic sourcing cannot be overstated. By understanding the unique properties and applications of tungsten carbide, international B2B buyers from regions such as Africa, South America, the Middle East, and Europe can make informed decisions that enhance their operational efficiencies. Key takeaways include the significance of supplier reliability, the necessity of quality assurance, and the advantages of establishing long-term partnerships with manufacturers who can provide consistent product quality and competitive pricing.
Moreover, leveraging regional suppliers can mitigate risks associated with supply chain disruptions, particularly in volatile markets. Buyers are encouraged to conduct thorough market research and engage with multiple suppliers to compare capabilities and offerings. This proactive approach not only secures better pricing but also fosters innovation through collaborative development.
Looking ahead, the tungsten carbide market is poised for growth, driven by advancements in technology and increasing demand across various sectors. International B2B buyers should capitalize on these trends by forging strategic alliances with reputable suppliers. By doing so, they will position themselves favorably in a competitive global market, ensuring sustainability and profitability in their operations.