Discover Top Benefits of Choosing a Welded Mesh Supplier (2025)
Introduction: Navigating the Global Market for welded mesh supplier
Navigating the complexities of the global market for welded mesh suppliers can pose significant challenges for international B2B buyers, particularly those operating in Africa, South America, the Middle East, and Europe. The need for reliable sourcing of welded mesh products—critical components in construction, agriculture, and manufacturing—requires a deep understanding of supplier capabilities, quality standards, and pricing structures. This guide aims to equip you with essential insights into the various types of welded mesh, their applications, and the vital considerations for vetting suppliers effectively.
In an increasingly competitive landscape, making informed purchasing decisions is paramount. Buyers must consider factors such as material specifications, compliance with international quality standards, and the supplier’s reputation. This comprehensive resource covers everything from the different varieties of welded mesh available on the market to practical tips for evaluating potential suppliers and understanding cost dynamics. By arming yourself with this knowledge, you can navigate the complexities of sourcing welded mesh with confidence.
Whether you’re looking to enhance project efficiency or ensure the durability of your products, this guide will help you identify the right suppliers that align with your business goals. Join us as we delve into the intricacies of the welded mesh supply chain, empowering you to make strategic decisions that drive success in your procurement processes.
Understanding welded mesh supplier Types and Variations
Type Name | Key Distinguishing Features | Primary B2B Applications | Brief Pros & Cons for Buyers |
---|---|---|---|
Standard Welded Mesh | Made from steel wires welded at intersections; various gauges. | Construction, fencing, and agriculture | Pros: Cost-effective and versatile; Cons: Limited customization. |
Stainless Steel Welded Mesh | Corrosion-resistant, durable, and aesthetically pleasing. | Food processing, pharmaceuticals | Pros: High durability and hygiene; Cons: Higher initial cost. |
Plastic Welded Mesh | Lightweight, non-corrosive, and available in various colors. | Landscaping, DIY projects, and aquaculture | Pros: Flexible and easy to install; Cons: Less strength compared to metal. |
Heavy-Duty Welded Mesh | Thicker wires and closely spaced for enhanced strength. | Industrial applications, security | Pros: Exceptional strength and durability; Cons: Higher weight and cost. |
Custom Welded Mesh | Tailored specifications for unique applications. | Specialized construction, art projects | Pros: Meets specific needs; Cons: Longer lead times and higher prices. |
What Are the Characteristics of Standard Welded Mesh?
Standard welded mesh is characterized by its grid-like structure, formed by steel wires welded at each intersection. This type is typically available in various wire gauges and mesh sizes, making it suitable for a wide range of applications, from construction to agricultural fencing. When considering this option, buyers should evaluate the specific requirements of their project, including load-bearing needs and environmental conditions, as standard welded mesh may not be ideal for highly corrosive environments.
Why Choose Stainless Steel Welded Mesh for B2B Applications?
Stainless steel welded mesh offers exceptional resistance to corrosion and rust, making it a preferred choice in industries such as food processing and pharmaceuticals, where hygiene is paramount. Its aesthetic appeal also makes it suitable for decorative applications. Buyers should consider the higher initial cost of stainless steel mesh against its longevity and reduced maintenance needs, especially in environments where standard mesh may deteriorate quickly.
How Does Plastic Welded Mesh Differ from Metal Options?
Plastic welded mesh is lightweight and non-corrosive, available in various colors and sizes. It is primarily used in landscaping, DIY projects, and aquaculture, where it provides flexibility and ease of installation. While it is a cost-effective option, buyers should be aware that plastic welded mesh lacks the strength and durability of metal alternatives, making it less suitable for high-stress applications.
What Are the Benefits of Heavy-Duty Welded Mesh?
Heavy-duty welded mesh is constructed from thicker wires and features closely spaced intersections, providing superior strength and durability. This type is commonly used in industrial applications and security fencing, where robustness is critical. Buyers should weigh the benefits of enhanced strength against potential higher costs and weight, which may influence transport and installation logistics.
When Should You Consider Custom Welded Mesh Solutions?
Custom welded mesh allows buyers to specify dimensions, wire gauges, and mesh configurations tailored to unique applications. This flexibility is invaluable for specialized construction projects or artistic endeavors. However, buyers should anticipate longer lead times and potentially higher prices, making it essential to assess whether the customization aligns with project timelines and budgets.
Related Video: Welded Wire Mesh Roll Manufacturing And Professional Loading
Key Industrial Applications of welded mesh supplier
Industry/Sector | Specific Application of welded mesh supplier | Value/Benefit for the Business | Key Sourcing Considerations for this Application |
---|---|---|---|
Construction | Reinforcement in concrete structures | Enhances structural integrity and durability | Compliance with local building codes and quality standards |
Agriculture | Fencing and animal enclosures | Protects crops and livestock from predators | Galvanization to prevent rust and corrosion |
Mining | Safety barriers and mesh screens | Ensures worker safety and prevents equipment damage | Material strength and resistance to harsh environments |
Manufacturing | Product shelving and storage solutions | Maximizes storage efficiency and accessibility | Custom sizes and load-bearing capacity |
Transportation | Security fencing for infrastructure | Enhances safety and protects assets | Compliance with safety regulations and local standards |
How is Welded Mesh Used in the Construction Industry?
In the construction sector, welded mesh is primarily utilized as reinforcement in concrete structures. This application is crucial for enhancing the structural integrity and durability of buildings, bridges, and other infrastructures. For international B2B buyers, especially from regions like Africa and South America, understanding local building codes is essential when sourcing welded mesh. Buyers should ensure that the mesh complies with specific quality standards to prevent future structural failures.
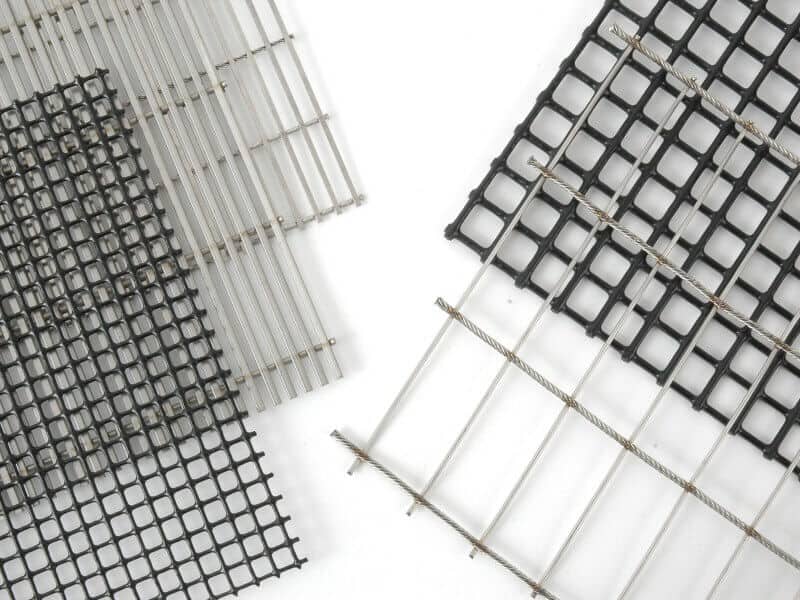
A stock image related to welded mesh supplier.
What Role Does Welded Mesh Play in Agriculture?
Welded mesh serves as fencing and animal enclosures in the agricultural industry, providing essential protection for crops and livestock against predators. This application is particularly relevant in regions with high wildlife activity, such as parts of the Middle East and Africa. Buyers need to consider the galvanization process of the welded mesh to ensure it is resistant to rust and corrosion, thus prolonging its lifespan in outdoor environments.
How is Welded Mesh Beneficial in Mining Operations?
In the mining industry, welded mesh is used for safety barriers and mesh screens to protect workers and equipment. This application is vital in preventing accidents and equipment damage in hazardous environments. Buyers from Europe and South America should focus on sourcing mesh that meets high strength standards and can withstand harsh conditions, ensuring worker safety and compliance with mining regulations.
What Advantages Does Welded Mesh Provide in Manufacturing?
Welded mesh is widely used in manufacturing for product shelving and storage solutions. By maximizing storage efficiency and accessibility, it helps businesses optimize their operations. International buyers should look for custom sizes and load-bearing capacities that fit their specific needs, ensuring that the mesh can support the weight of stored products without compromising safety.
Why is Welded Mesh Important for Transportation Security?
In the transportation sector, welded mesh is employed for security fencing around infrastructure such as airports, train stations, and logistics centers. This application enhances safety and protects valuable assets from unauthorized access. Buyers should ensure that the welded mesh complies with local safety regulations and standards, as this is critical for maintaining operational integrity and security in transportation hubs.
Related Video: This is How Welded Wire Mesh are Manufactured | Wire Mesh Manufacturing Factory
3 Common User Pain Points for ‘welded mesh supplier’ & Their Solutions
Scenario 1: Sourcing High-Quality Welded Mesh for Specific Applications
The Problem:
Many B2B buyers struggle to find welded mesh that meets their specific industry requirements. For instance, construction firms may need welded mesh with precise dimensions and material specifications to ensure structural integrity. Buyers often encounter issues such as inconsistent quality, variations in wire diameter, and inadequate coating that may lead to corrosion over time. This not only compromises the integrity of their projects but also increases costs due to waste and rework.
The Solution:
To effectively source high-quality welded mesh, buyers should start by clearly defining their project specifications, including wire gauge, mesh size, and coating requirements. Engaging with suppliers who provide detailed product descriptions and certifications can help ensure compliance with industry standards. Additionally, requesting samples before placing a bulk order allows buyers to assess the mesh quality firsthand. Establishing a partnership with reputable suppliers who have a proven track record in the industry can also facilitate better communication and understanding of product capabilities, ultimately leading to successful project outcomes.
Scenario 2: Managing Lead Times and Supply Chain Disruptions
The Problem:
B2B buyers often face challenges related to lead times and supply chain disruptions, particularly in regions like Africa and South America where logistics can be complicated. Delays in receiving welded mesh can stall project timelines, leading to financial losses and missed deadlines. Buyers may find themselves in a position where they must either wait for their orders or scramble to find alternative suppliers at the last minute, which can be both time-consuming and costly.
The Solution:
To mitigate lead time issues, buyers should implement proactive supply chain management strategies. This includes maintaining open lines of communication with suppliers regarding production schedules and potential delays. Establishing a buffer inventory for critical materials like welded mesh can also provide a safety net against unexpected disruptions. Furthermore, utilizing local suppliers where possible can significantly reduce transportation times. It is also beneficial to explore advanced planning techniques, such as just-in-time inventory management, to align material availability with project timelines, ensuring a smoother workflow.
Scenario 3: Navigating Compliance and Regulatory Standards
The Problem:
B2B buyers in industries such as construction and manufacturing often encounter complex compliance and regulatory standards related to welded mesh. Different countries have various regulations regarding the materials used, safety standards, and environmental impact. Navigating these regulations can be overwhelming, especially for buyers unfamiliar with local laws or international standards, potentially leading to legal issues and project delays.
The Solution:
To navigate compliance effectively, buyers should invest time in understanding the specific regulations that apply to their projects. This can involve consulting with legal experts or industry associations that specialize in materials compliance. It is also advisable to work with suppliers who are knowledgeable about regulatory requirements and can provide documentation proving compliance with relevant standards. Buyers should request certifications and test results for the welded mesh products to ensure they meet necessary safety and quality benchmarks. Additionally, keeping abreast of changes in regulations can help buyers adapt quickly and maintain compliance without disrupting their operations.
Strategic Material Selection Guide for welded mesh supplier
When selecting materials for welded mesh, international B2B buyers must consider various factors that impact performance, durability, and cost. Below, we analyze four common materials used in welded mesh applications, providing insights tailored for buyers from Africa, South America, the Middle East, and Europe.
What are the Key Properties of Steel Welded Mesh?
Steel is the most common material used for welded mesh due to its strength and versatility. It typically has high tensile strength, making it suitable for heavy-duty applications. Steel welded mesh can withstand high temperatures and pressures, making it ideal for construction and industrial uses. However, it is susceptible to corrosion unless treated with coatings like galvanization.
Pros & Cons: Steel mesh is durable and cost-effective, but its susceptibility to rust can be a significant drawback in humid or corrosive environments. Galvanized options can mitigate this issue but may increase production costs.
Impact on Application: Steel welded mesh is compatible with various media, including concrete and soil, making it ideal for construction projects. Buyers must consider local environmental conditions to determine the best treatment options.
Considerations for International Buyers: Compliance with standards such as ASTM A185 or DIN 488 is crucial. Buyers should also be aware of regional preferences for galvanized versus uncoated steel.
How Does Stainless Steel Compare for Welded Mesh Applications?
Stainless Steel offers superior corrosion resistance compared to regular steel, making it a preferred choice for applications in harsh environments, such as coastal areas or chemical processing plants. It maintains structural integrity at high temperatures and is easy to clean, which is essential in food processing applications.
Pros & Cons: The primary advantage of stainless steel is its longevity and resistance to rust. However, it comes at a higher cost and can be more challenging to manufacture due to its hardness.
Impact on Application: Stainless steel welded mesh is ideal for applications requiring hygiene and corrosion resistance, such as food and pharmaceutical industries.
Considerations for International Buyers: Buyers should ensure compliance with standards like ASTM A240 for stainless steel. The higher initial investment may be justified by lower maintenance costs over time.
What are the Benefits of Using Plastic Welded Mesh?
Plastic Welded Mesh, typically made from materials like PVC or polyethylene, is lightweight and resistant to corrosion and chemicals. It is often used in agricultural applications, such as fencing and plant support structures.
Pros & Cons: The main advantage of plastic mesh is its low weight and resistance to environmental factors. However, it lacks the strength of metal options and may not be suitable for high-load applications.
Impact on Application: Plastic welded mesh is ideal for applications where corrosion resistance and lightweight properties are essential, such as in agriculture or landscaping.
Considerations for International Buyers: Compliance with local standards for agricultural products is necessary. Buyers should also consider the environmental impact of plastic materials and potential recycling options.
Why Choose Galvanized Wire for Welded Mesh?
Galvanized Wire is steel wire that has been coated with zinc to prevent rust. This material combines the strength of steel with enhanced corrosion resistance, making it suitable for outdoor applications.
Pros & Cons: Galvanized welded mesh provides excellent durability and is more cost-effective than stainless steel. However, the zinc coating can wear off over time, especially in abrasive environments.
Impact on Application: This type of mesh is commonly used in construction, fencing, and agricultural applications due to its balance of strength and corrosion resistance.
Considerations for International Buyers: Buyers should ensure that the galvanization process meets standards like ASTM A123. Understanding local climate conditions can help in selecting the appropriate type of galvanized mesh.
Summary Table of Material Selection for Welded Mesh
Material | Typical Use Case for welded mesh supplier | Key Advantage | Key Disadvantage/Limitation | Relative Cost (Low/Med/High) |
---|---|---|---|---|
Steel | Construction, industrial applications | High strength and cost-effective | Susceptible to corrosion | Medium |
Stainless Steel | Food processing, chemical industries | Superior corrosion resistance | Higher cost and manufacturing complexity | High |
Plastic | Agricultural fencing, plant support | Lightweight and corrosion-resistant | Lower strength | Low |
Galvanized Wire | Fencing, outdoor construction | Good balance of strength and cost | Zinc coating can wear off | Medium |
This guide provides actionable insights for international B2B buyers, enabling them to make informed decisions about material selection based on their specific needs and regional considerations.
In-depth Look: Manufacturing Processes and Quality Assurance for welded mesh supplier
What Are the Key Manufacturing Processes for Welded Mesh Production?
The manufacturing of welded mesh involves several critical stages that ensure the final product meets the specific needs of B2B buyers. Understanding these processes can help you assess the capabilities of potential suppliers effectively.
1. Material Preparation: What Materials Are Used and How Are They Processed?
The first step in welded mesh production is the selection of appropriate raw materials. Typically, high-quality steel wire is used, which may be galvanized or coated for enhanced durability. The wire is cut to the required lengths and then straightened to ensure uniformity. This preparation is crucial, as any irregularities can compromise the strength and integrity of the final mesh product.
2. Forming: How Is the Mesh Structure Created?
Once the materials are prepared, the next stage is forming. The straightened wire is fed into a mesh welding machine, which arranges the wires in a grid pattern. This machine utilizes electric resistance welding techniques, where electrodes apply high heat and pressure to fuse the intersecting wires together. This process is efficient and allows for high-speed production while maintaining precise spacing and alignment.
3. Assembly: What Techniques Are Used to Finalize the Product?
After forming, the welded mesh is cut to size based on customer specifications. Additional processes such as bending, shaping, or further reinforcing the edges may be employed, depending on the intended application. For instance, mesh used in construction may require specific dimensions and reinforcement to enhance its load-bearing capacity.
4. Finishing: How Is the Welded Mesh Treated for Durability?
The final stage of manufacturing involves finishing treatments. Common techniques include galvanization, powder coating, or applying protective paints to enhance corrosion resistance and overall durability. The finishing process not only improves the aesthetic appeal of the mesh but also extends its lifespan, making it suitable for diverse applications in various climates.
How Is Quality Assurance Implemented in Welded Mesh Manufacturing?
Quality assurance is integral to the production of welded mesh, ensuring that products meet international standards and customer expectations. Here’s a breakdown of key aspects involved in the quality control process.
Relevant International Standards: What Certifications Should You Look For?
For welded mesh suppliers, adhering to international standards such as ISO 9001 is critical. This standard focuses on quality management systems and ensures that suppliers consistently meet customer and regulatory requirements. Additionally, industry-specific certifications like CE marking in Europe or API standards in the oil and gas sector can also indicate a supplier’s commitment to quality.
What Are the Key Quality Control Checkpoints in the Manufacturing Process?
Quality control (QC) typically involves several checkpoints throughout the manufacturing process:
-
Incoming Quality Control (IQC): This initial inspection ensures that raw materials meet specified standards before production begins. Suppliers should provide certificates of compliance for the materials used.
-
In-Process Quality Control (IPQC): During the manufacturing stages, regular inspections are conducted to monitor the welding process and ensure that all parameters are within acceptable limits. This includes checking weld quality, wire alignment, and dimensional accuracy.
-
Final Quality Control (FQC): After the mesh is fully assembled, a final inspection is performed to verify that the finished product meets all specifications. This can include tensile strength testing and visual inspections for defects.
What Common Testing Methods Are Used for Welded Mesh Quality Assurance?
To ensure the quality of welded mesh, suppliers employ various testing methods:
-
Tensile Testing: This method assesses the strength and ductility of the welded joints, ensuring they can withstand the intended loads.
-
Visual Inspection: A thorough visual inspection can identify surface defects, misalignment, or inadequate welds.
-
Corrosion Resistance Testing: For galvanized or coated products, tests like salt spray testing determine how well the finishing treatments protect the mesh from corrosion.
How Can B2B Buyers Verify Supplier Quality Control?
As an international B2B buyer, verifying the quality control processes of potential suppliers is vital. Here are actionable strategies to ensure compliance and reliability:
Conduct Supplier Audits: What Should You Look For?
Regular audits of suppliers can provide insights into their manufacturing processes and quality assurance practices. During an audit, assess the following:
-
Compliance with Standards: Ensure the supplier adheres to relevant international and industry-specific standards.
-
Quality Control Procedures: Review the supplier’s QC processes, including documentation of inspections and test results.
-
Facility Conditions: Evaluate the manufacturing environment, including cleanliness, organization, and the presence of quality control personnel.
Request Quality Reports: How Can Documentation Help?
Ask suppliers for comprehensive quality reports that detail their QC processes, testing results, and any certifications obtained. These documents can serve as evidence of a supplier’s commitment to quality and can be compared across different suppliers.
Utilize Third-Party Inspections: When Should You Consider This?

A stock image related to welded mesh supplier.
Engaging third-party inspection services can provide an unbiased assessment of a supplier’s quality control practices. These inspections can be particularly beneficial when entering new markets or working with unfamiliar suppliers, offering additional reassurance of product quality.
What Are the Unique Challenges for International Buyers in Quality Assurance?
International B2B buyers, especially those from Africa, South America, the Middle East, and Europe, face unique challenges in ensuring quality assurance. These include:
-
Regulatory Differences: Different regions have varying standards and regulations, making it essential to understand the specific requirements of the target market.
-
Cultural and Communication Barriers: Language differences and varying business practices can complicate negotiations and quality expectations.
-
Logistical Issues: Shipping and handling can affect product integrity, so understanding how suppliers manage their logistics is crucial for maintaining quality.
By addressing these challenges and implementing thorough verification strategies, international buyers can successfully navigate the complexities of sourcing welded mesh products while ensuring high-quality standards.
Practical Sourcing Guide: A Step-by-Step Checklist for ‘welded mesh supplier’
Introduction
Navigating the complexities of sourcing welded mesh can be challenging for international B2B buyers. This practical sourcing guide serves as a checklist to streamline your procurement process, ensuring you find reliable suppliers who meet your specific requirements. By following these steps, you can make informed decisions that enhance your supply chain efficiency.
Step 1: Define Your Technical Specifications
Before you begin contacting suppliers, clearly outline your technical specifications for the welded mesh. This includes details like wire diameter, mesh size, material type (e.g., galvanized, stainless steel), and any specific coatings required. Having precise specifications helps ensure that you receive products that meet your quality standards and performance needs.
Step 2: Research Potential Suppliers
Conduct thorough research to identify potential welded mesh suppliers in your target regions, such as Africa, South America, the Middle East, and Europe. Utilize online platforms, trade shows, and industry directories to compile a list of candidates. Look for suppliers with a strong reputation and positive reviews from previous clients, as this can provide insights into their reliability and product quality.
Step 3: Evaluate Supplier Certifications
Verify that your shortlisted suppliers possess relevant certifications, such as ISO 9001 or other industry-specific standards. Certifications indicate that the supplier adheres to quality management practices, which can significantly reduce the risk of receiving subpar products. Ask for documentation of their certifications and ensure they are up-to-date.
Step 4: Request Samples for Quality Assessment
Before placing a large order, request samples from potential suppliers to assess the quality of their welded mesh. Evaluate the samples for durability, finish, and compliance with your specifications. This step is crucial as it allows you to physically inspect the product and make comparisons between different suppliers.
Step 5: Understand Pricing Structures and Payment Terms
Engage in discussions about pricing structures and payment terms with your shortlisted suppliers. Understanding their pricing model—whether it’s per unit, bulk discounts, or additional charges for shipping—is essential for budgeting purposes. Additionally, clarify payment terms, including deposits, payment schedules, and accepted methods to avoid any misunderstandings later.
Step 6: Assess Production Capacity and Lead Times
Inquire about the production capacity of your potential suppliers and their lead times for fulfilling orders. This is particularly important if you have deadlines for project completion. Ensure that the supplier can meet your demands without compromising quality or timelines, as delays can adversely impact your operations.
Step 7: Establish Communication Channels
Finally, establish clear communication channels with your chosen supplier. Effective communication is vital for addressing any issues that may arise during the procurement process. Ensure you have direct contact with a representative who can assist you promptly, and consider setting up regular check-ins to discuss order progress and any potential changes.
By following this step-by-step checklist, you can confidently navigate the procurement process for welded mesh suppliers, ensuring that you select partners who align with your business objectives and quality standards.
Comprehensive Cost and Pricing Analysis for welded mesh supplier Sourcing
What Are the Key Cost Components in Sourcing Welded Mesh?
When evaluating the cost structure of sourcing welded mesh, several key components must be considered:
-
Materials: The primary material used in welded mesh is typically steel, which can vary in type (e.g., galvanized, stainless) and quality. Prices fluctuate based on market demand, availability, and regional supply chains. Buyers should stay informed about local market trends to anticipate price changes.
-
Labor: Labor costs are influenced by the region of production. In countries with higher labor costs, such as those in Europe, the overall pricing may reflect this. Conversely, sourcing from regions with lower labor costs may yield savings but could impact product quality or lead times.
-
Manufacturing Overhead: This includes costs associated with factory operations, utilities, equipment maintenance, and administrative expenses. Efficient production processes can reduce overhead, but buyers should assess whether suppliers are investing in technology that enhances efficiency.
-
Tooling: Specific tooling costs may arise for customized or specialized welded mesh products. These costs can vary significantly based on the complexity of the design and the material used.
-
Quality Control (QC): Ensuring product quality involves additional costs, especially if certifications or third-party inspections are required. Buyers should inquire about the QC processes of potential suppliers to ensure compliance with international standards.
-
Logistics: Transportation costs can vary widely based on the shipping method (air, sea, or land), distance, and any potential tariffs or customs fees. Understanding the logistics landscape in the supplier’s region can help buyers anticipate these costs.
-
Margin: Supplier margins will vary depending on market competition, product demand, and the supplier’s positioning. Buyers should consider the balance between cost and quality when evaluating supplier margins.
How Do Price Influencers Affect Welded Mesh Sourcing?
Several factors can influence the pricing of welded mesh, particularly for international buyers:
-
Volume and Minimum Order Quantity (MOQ): Larger orders often yield better pricing due to economies of scale. Buyers should negotiate MOQs that align with their needs while ensuring they receive competitive rates.
-
Specifications and Customization: Customized products can lead to increased costs due to additional labor and tooling requirements. Buyers should clearly define specifications to avoid unexpected costs later in the process.
-
Materials Quality and Certifications: High-quality materials or certifications (e.g., ISO, ASTM) can increase costs but may also provide long-term value through enhanced durability and compliance with regulations.
-
Supplier Factors: The reputation and reliability of the supplier can impact pricing. Established suppliers may charge higher prices due to their proven track record, while emerging suppliers might offer lower prices to gain market entry.
-
Incoterms: Understanding Incoterms is crucial for international transactions. These terms dictate the responsibilities of buyers and suppliers regarding shipping, insurance, and tariffs, which can significantly impact the total cost.
What Are the Best Negotiation Tips for International B2B Buyers?
International buyers, particularly from regions like Africa, South America, the Middle East, and Europe, should consider the following negotiation strategies to ensure cost-efficiency:
-
Understand Total Cost of Ownership (TCO): Beyond just the purchase price, assess all costs associated with sourcing, including logistics, customs duties, and potential quality control expenses. This comprehensive view will aid in making informed decisions.
-
Leverage Relationships: Building strong relationships with suppliers can lead to better terms and pricing. Frequent communication and trust can facilitate negotiations and improve the overall partnership.
-
Be Aware of Pricing Nuances: Understand regional pricing dynamics and be prepared to discuss them. Factors such as currency fluctuations, local market conditions, and geopolitical events can all affect pricing.
-
Request Detailed Quotations: Ensure that suppliers provide comprehensive quotations that outline all cost components. This transparency allows for better comparison and negotiation.
-
Explore Multiple Suppliers: Diversifying suppliers can lead to competitive pricing and provide leverage during negotiations. It also mitigates risks associated with reliance on a single source.
Conclusion
Navigating the complexities of sourcing welded mesh requires a thorough understanding of cost structures and pricing influencers. By leveraging actionable insights and negotiation strategies, international B2B buyers can make informed decisions that enhance their sourcing outcomes while managing costs effectively. Always remember that prices are indicative and can fluctuate based on various factors, so continuous market analysis is essential.
Alternatives Analysis: Comparing welded mesh supplier With Other Solutions
When considering a welded mesh supplier, it is essential to evaluate alternative solutions that could serve similar purposes within the B2B landscape. This analysis will help international buyers, particularly from regions like Africa, South America, the Middle East, and Europe, to make informed decisions based on their specific operational needs.
Comparison Table of Welded Mesh Supplier and Alternatives
Comparison Aspect | Welded Mesh Supplier | Alternative 1: Chain Link Fencing | Alternative 2: Expanded Metal Mesh |
---|---|---|---|
Performance | High strength and durability | Moderate strength, less durable | Good strength but less flexible |
Cost | Moderate to high | Generally lower | Higher than chain link but lower than welded mesh |
Ease of Implementation | Requires skilled labor for installation | Easier to install, DIY options available | Moderate, requires specific tools |
Maintenance | Low maintenance, resistant to corrosion | Moderate, can rust over time | Low, but can be prone to bending |
Best Use Case | Industrial applications, security | Residential, commercial properties | Industrial applications, ventilation |
What Are the Pros and Cons of Chain Link Fencing as an Alternative?
Chain link fencing is a popular alternative to welded mesh, particularly for perimeter security. One of its significant advantages is cost-effectiveness, making it suitable for large-scale applications where budget constraints are a consideration. Installation is relatively straightforward, allowing for quicker setups. However, its performance is moderate, as it does not offer the same level of security or durability as welded mesh. Over time, chain link can also rust if not properly coated, which may require additional maintenance.
How Does Expanded Metal Mesh Compare to Welded Mesh?
Expanded metal mesh is another viable alternative that offers unique advantages. It is manufactured by slitting and stretching metal sheets, creating a lightweight yet sturdy product. This option is particularly beneficial for applications requiring ventilation and visibility, such as guardrails or safety barriers. However, while it provides good strength, it lacks the flexibility and ease of installation found in welded mesh or chain link fencing. The cost is often higher than chain link but can be more economical than welded mesh, depending on the material used.
Conclusion: How Can Buyers Choose the Right Solution for Their Needs?
For B2B buyers evaluating alternatives to welded mesh suppliers, the decision should be guided by specific operational requirements, including performance expectations, budget constraints, and installation capabilities. Buyers should consider the long-term implications of maintenance and durability based on the intended use case. By weighing these factors, businesses can select the most appropriate solution that aligns with their strategic goals and operational needs, ensuring both cost-effectiveness and reliability.
Essential Technical Properties and Trade Terminology for welded mesh supplier
What Are the Key Technical Properties of Welded Mesh?
When selecting a welded mesh supplier, understanding the essential technical properties is crucial. Here are some critical specifications that international B2B buyers should consider:
1. Material Grade
Material grade refers to the type of steel used in the welded mesh, which affects its strength, corrosion resistance, and overall durability. Common grades include low carbon steel, stainless steel, and galvanized steel. Choosing the right material grade is vital for applications exposed to harsh environments, ensuring longevity and reducing replacement costs.
2. Wire Diameter
The wire diameter indicates the thickness of the individual wires in the mesh. A thicker wire typically offers greater strength and load-bearing capacity, while a thinner wire may be more cost-effective for lighter applications. Understanding the required wire diameter helps buyers match their project needs with the appropriate product specifications.
3. Mesh Opening Size
This specification defines the space between the wires in the welded mesh. The opening size is critical for determining the mesh’s suitability for specific applications, such as fencing, reinforcement, or filtration. Buyers must consider both the size and the required strength of the welded mesh to ensure it meets their project requirements.
4. Tolerance Levels
Tolerance levels indicate the acceptable variation in dimensions during manufacturing. For welded mesh, this includes the wire diameter and mesh opening size. Tight tolerances are essential for applications requiring precision, such as construction or industrial uses, ensuring compatibility and structural integrity.
5. Coating and Finish
The type of coating or finish applied to the welded mesh, such as galvanization or powder coating, significantly impacts its corrosion resistance and aesthetic appeal. A well-chosen finish can enhance durability, particularly in environments prone to moisture or chemicals. Understanding the options available helps buyers select a product that aligns with their operational environment.
What Are Common Trade Terms in the Welded Mesh Industry?
Familiarity with industry jargon is essential for effective communication with suppliers and understanding contractual obligations. Here are some key terms that buyers should know:
1. OEM (Original Equipment Manufacturer)
OEM refers to companies that produce parts or equipment that may be marketed by another manufacturer. In the context of welded mesh, an OEM might supply mesh products that meet specific requirements for a larger brand or project. Understanding this term helps buyers identify reliable suppliers.
2. MOQ (Minimum Order Quantity)
MOQ is the smallest quantity of a product that a supplier is willing to sell. Knowing the MOQ is crucial for budgeting and inventory management, especially for smaller businesses or projects with limited needs. This term can also indicate the supplier’s production capacity.
3. RFQ (Request for Quotation)
An RFQ is a document sent to suppliers asking for a price quote for specific products. This process helps buyers compare prices and terms across different suppliers, ensuring they get the best deal. A well-structured RFQ can lead to more accurate and competitive quotes.
4. Incoterms (International Commercial Terms)
Incoterms are a series of pre-defined commercial terms published by the International Chamber of Commerce. They clarify the responsibilities of buyers and sellers in international transactions, including shipping, insurance, and tariffs. Understanding Incoterms is essential for international buyers to avoid misunderstandings regarding shipping costs and responsibilities.
5. Lead Time
Lead time refers to the amount of time it takes from placing an order to delivery. This is a critical consideration for project timelines. Buyers should discuss lead times with suppliers to ensure that product availability aligns with their project schedules.
By understanding these technical properties and trade terms, international B2B buyers can make informed decisions when selecting a welded mesh supplier, ultimately enhancing project success and operational efficiency.
Navigating Market Dynamics and Sourcing Trends in the welded mesh supplier Sector
What Are the Key Market Dynamics and Sourcing Trends in the Welded Mesh Supplier Sector?
The welded mesh supply sector is experiencing significant transformation driven by globalization, technological advancements, and shifting consumer preferences. Key global drivers include the increasing demand for construction materials in emerging markets, particularly in Africa and South America, where infrastructure development is a priority. In Europe and the Middle East, stringent regulations regarding safety and quality are also shaping sourcing decisions.
Current B2B tech trends such as automation, IoT, and AI are enhancing supply chain efficiency and transparency. Automated production processes are reducing lead times, while IoT technology allows for real-time tracking of materials and inventory. For international buyers, adopting these technologies can improve operational efficiency and lead to cost savings.
Additionally, buyers are increasingly seeking suppliers who can provide value-added services such as customizations and technical support. The growing trend towards e-commerce in B2B transactions is facilitating easier access to suppliers and competitive pricing. As buyers from regions like Poland and Thailand engage more in global trade, they must be aware of these technological innovations to make informed sourcing decisions.
How Is Sustainability Reshaping Sourcing Practices for Welded Mesh Suppliers?
Sustainability is becoming a crucial factor in the sourcing decisions of international B2B buyers. The environmental impact of production processes, especially in the welded mesh sector, is drawing scrutiny. Suppliers are under pressure to adopt sustainable practices, which include reducing carbon footprints and utilizing recycled materials.
The importance of ethical supply chains cannot be overstated. Buyers are increasingly evaluating suppliers based on their commitment to social responsibility, which includes fair labor practices and community engagement. Certifications such as ISO 14001 for environmental management and LEED for green building practices are becoming essential in supplier evaluations.
For B2B buyers, sourcing from suppliers who prioritize sustainability not only meets regulatory requirements but also enhances brand reputation. As global markets lean towards environmentally responsible practices, aligning with sustainable suppliers will be key to maintaining competitiveness in the welded mesh industry.
What Is the Historical Context of the Welded Mesh Supply Sector?
The welded mesh industry has evolved significantly over the past century. Initially developed for agricultural and construction uses, the technology has advanced to meet the demands of various sectors, including automotive, aerospace, and security. In the early 20th century, welded mesh was primarily produced using manual methods. However, the introduction of mechanized welding processes in the 1950s significantly increased production efficiency and quality.
Today, welded mesh is recognized for its versatility and strength, being utilized in diverse applications from fencing to reinforcement in concrete structures. The evolution of this industry reflects broader trends in manufacturing and technology, making it crucial for international buyers to understand its development to navigate current market dynamics effectively.
By focusing on these insights, B2B buyers can better navigate the complexities of sourcing in the welded mesh sector, ensuring they make informed decisions that align with both their operational goals and ethical standards.
Frequently Asked Questions (FAQs) for B2B Buyers of welded mesh supplier
-
How do I evaluate the quality of welded mesh products from suppliers?
To assess the quality of welded mesh products, request samples to inspect the material, welding technique, and overall durability. Verify compliance with international standards, such as ISO or ASTM certifications. Additionally, inquire about the supplier’s quality assurance processes, including inspections and testing methods. Engaging with previous customers can also provide insights into the reliability and quality of the supplier’s products. -
What are the key factors to consider when selecting a welded mesh supplier?
When selecting a welded mesh supplier, consider factors such as product quality, pricing, delivery timelines, and customer service. Evaluate the supplier’s experience in the industry and their ability to meet specific requirements, such as customization and minimum order quantities (MOQ). It’s also essential to review their logistics capabilities and any trade regulations that might affect shipping to your region. -
What customization options are available for welded mesh products?
Many welded mesh suppliers offer customization options including wire diameter, mesh size, and coating types (e.g., galvanized or PVC). Discuss your specific requirements with potential suppliers to ensure they can accommodate your needs. Customization may also extend to the shape and size of the mesh panels, allowing you to tailor products for particular applications in construction, agriculture, or security. -
What are the typical minimum order quantities (MOQ) for welded mesh?
The minimum order quantity for welded mesh products can vary significantly between suppliers, typically ranging from 500 to 1,000 square meters. Larger orders may result in better pricing per unit, while smaller orders could incur additional fees. Always clarify MOQ during negotiations to avoid surprises and ensure that the supplier can meet your needs without excessive costs. -
What payment terms should I expect when dealing with international welded mesh suppliers?
Payment terms can vary widely, but many suppliers require a deposit (often 30%) upon order confirmation, with the balance due before shipment. Some suppliers may offer letter of credit options for larger transactions to mitigate risk. It’s crucial to negotiate favorable terms that align with your cash flow while ensuring the supplier’s security. Always document these terms in the contract. -
How do I ensure timely delivery of my welded mesh order?
To ensure timely delivery, confirm lead times before placing your order and factor in potential delays due to customs or shipping. Establish clear communication with your supplier regarding production schedules and shipping methods. Consider using a freight forwarder familiar with international shipping regulations to streamline logistics and avoid unexpected delays. -
What should I know about quality assurance (QA) for welded mesh products?
Quality assurance is critical when sourcing welded mesh, as it ensures the products meet industry standards and your specifications. Inquire about the supplier’s QA processes, including inspections, testing for strength and durability, and compliance with relevant standards. Request documentation of QA procedures and certifications to ensure transparency and reliability in the products you receive. -
How can I effectively communicate my needs to a welded mesh supplier?
Effective communication with your supplier involves clearly articulating your specifications, including dimensions, materials, and intended applications. Provide detailed drawings or samples if possible. Establish regular check-ins during production to address any questions or concerns. Building a strong relationship through open dialogue can help ensure that your requirements are met and that any issues are resolved promptly.
Important Disclaimer & Terms of Use
⚠️ Important Disclaimer
The information provided in this guide, including content regarding manufacturers, technical specifications, and market analysis, is for informational and educational purposes only. It does not constitute professional procurement advice, financial advice, or legal advice.
While we have made every effort to ensure the accuracy and timeliness of the information, we are not responsible for any errors, omissions, or outdated information. Market conditions, company details, and technical standards are subject to change.
B2B buyers must conduct their own independent and thorough due diligence before making any purchasing decisions. This includes contacting suppliers directly, verifying certifications, requesting samples, and seeking professional consultation. The risk of relying on any information in this guide is borne solely by the reader.
Strategic Sourcing Conclusion and Outlook for welded mesh supplier
What Are the Key Takeaways for B2B Buyers in the Welded Mesh Market?
In conclusion, strategic sourcing in the welded mesh sector is paramount for international B2B buyers looking to enhance their procurement efficiency and product quality. By understanding the diverse offerings from suppliers across Africa, South America, the Middle East, and Europe, buyers can tailor their sourcing strategies to meet specific project requirements. Key takeaways include the importance of assessing supplier capabilities, ensuring compliance with regional standards, and leveraging competitive pricing to maximize value.
How Can International Buyers Prepare for Future Trends in Welded Mesh Supply?
As the market evolves, staying informed about emerging trends—such as advancements in production technology and shifts in global demand—will be crucial. Buyers should actively seek partnerships with suppliers who demonstrate innovation and adaptability. This proactive approach not only fosters long-term relationships but also positions buyers to capitalize on future opportunities in the welded mesh industry.
What Steps Should B2B Buyers Take Moving Forward?
To navigate the complexities of sourcing welded mesh effectively, international buyers are encouraged to conduct thorough market research, engage in supplier evaluations, and develop a clear sourcing plan. By prioritizing these strategies, businesses can ensure they are well-equipped to make informed decisions that drive success in their projects. Embrace the potential of strategic sourcing today to secure a competitive edge in the welded mesh market.