Discover Top Benefits of Choosing a Wood Chipper Manufacturer (2025)
Introduction: Navigating the Global Market for wood chipper manufacturer
The global market for wood chipper manufacturers presents a unique set of challenges for international B2B buyers, particularly those operating in regions like Africa, South America, the Middle East, and Europe. Sourcing high-quality wood chippers that meet specific operational needs can be daunting, especially when navigating diverse supplier landscapes and varying local regulations. This guide aims to equip buyers with essential insights into the types of wood chippers available, their applications across different industries, and the critical factors to consider when vetting suppliers.
In this comprehensive resource, we will explore various wood chipper models, from portable machines suitable for small-scale operations to industrial-grade equipment designed for extensive forestry projects. Additionally, we will cover vital aspects such as understanding the cost structures associated with procurement, maintenance considerations, and the importance of after-sales support.
By providing actionable insights and detailed information, this guide empowers international B2B buyers to make informed purchasing decisions. Whether you are based in the bustling markets of Colombia or the established industries of France, our aim is to enhance your sourcing strategy and ensure that your investment in wood chipper machinery yields optimal results for your operations.
Understanding wood chipper manufacturer Types and Variations
Type Name | Key Distinguishing Features | Primary B2B Applications | Brief Pros & Cons for Buyers |
---|---|---|---|
Commercial Wood Chippers | High-capacity, robust design for heavy-duty use | Landscaping, forestry, waste management | Pros: Efficient for large operations; durable. Cons: Higher upfront costs; requires skilled operation. |
Portable Wood Chippers | Compact, lightweight, and easy to transport | Small-scale landscaping, residential use | Pros: Versatile and easy to use; lower cost. Cons: Limited capacity; may struggle with larger branches. |
Electric Wood Chippers | Environmentally friendly, quieter operation | Urban landscaping, residential gardens | Pros: Low emissions; quieter than gas models. Cons: Limited power; may not handle tough materials. |
Towable Wood Chippers | Designed for towing behind vehicles, high mobility | Large landscaping projects, tree services | Pros: High capacity; easy to transport. Cons: May require a vehicle; higher maintenance needs. |
Industrial Wood Chippers | Extremely powerful, designed for continuous operation | Biomass production, large-scale forestry | Pros: High throughput; suitable for tough materials. Cons: Significant investment; requires specialized training. |
What Are the Key Characteristics of Commercial Wood Chippers?
Commercial wood chippers are designed for high-capacity tasks, making them ideal for landscaping companies, forestry operations, and waste management services. These machines can process large volumes of wood quickly, which is crucial for businesses that need to maintain efficiency. When considering a commercial wood chipper, buyers should evaluate the machine’s power, durability, and ease of maintenance to ensure it meets their operational needs.
How Do Portable Wood Chippers Benefit Small Businesses?
Portable wood chippers are compact and lightweight, making them perfect for small-scale landscaping jobs or residential use. These machines can handle smaller branches and brush effectively, allowing businesses to manage yard waste efficiently. Buyers should consider the machine’s capacity, ease of transport, and user-friendliness, especially if they require a machine for varied job sites.
Why Choose Electric Wood Chippers for Urban Landscaping?
Electric wood chippers are becoming increasingly popular due to their eco-friendly operation and quieter performance. They are particularly suitable for urban landscaping and residential gardens, where noise and emissions are a concern. While they are generally less powerful than gas-powered models, buyers should assess the specific requirements of their projects to determine if an electric chipper will suffice.
What Are the Advantages of Towable Wood Chippers?
Towable wood chippers offer high mobility and capacity, making them suitable for larger landscaping projects and tree services. They can be towed behind vehicles, allowing for easy transport to job sites. However, businesses should consider the towing requirements and the associated costs of maintaining such equipment, as well as the need for a compatible vehicle.
How Do Industrial Wood Chippers Support Large-Scale Operations?
Industrial wood chippers are designed for continuous operation and are capable of processing large volumes of wood and tough materials, making them essential for biomass production and large-scale forestry operations. While they represent a significant investment, the high throughput and efficiency can lead to long-term cost savings. Buyers must also consider the training requirements for operating such powerful machinery effectively.
Related Video: SHD Biomass machine manufacturer,wood chipper,crusher,horizontal grinder,wood chip machine
Key Industrial Applications of wood chipper manufacturer
Industry/Sector | Specific Application of wood chipper manufacturer | Value/Benefit for the Business | Key Sourcing Considerations for this Application |
---|---|---|---|
Forestry | Processing timber waste into mulch | Reduces waste disposal costs and creates valuable mulch | Durability, capacity, and energy efficiency of the machine |
Landscaping and Gardening | Preparing organic material for landscaping | Enhances soil health and reduces costs for raw materials | Size, mobility, and ease of operation |
Bioenergy Production | Converting wood waste into biomass fuel | Supports renewable energy initiatives and reduces landfill waste | Compliance with environmental standards and processing efficiency |
Waste Management | Shredding yard waste for recycling | Improves recycling rates and reduces landfill dependency | Versatility, maintenance requirements, and cost-effectiveness |
Agriculture | Producing feedstock from agricultural residues | Enhances soil quality and reduces the need for chemical fertilizers | Adaptability to different materials and operational support |
How is Wood Chipper Manufacturing Applied in the Forestry Industry?
In the forestry sector, wood chipper manufacturers provide essential equipment for processing timber waste into mulch. This application significantly reduces waste disposal costs, turning what would otherwise be a financial burden into a valuable resource. Buyers in this industry should consider the durability and capacity of the chipper, as high-performance machines can handle various wood types and sizes, ensuring efficient processing.
What Role Does Wood Chipper Manufacturing Play in Landscaping and Gardening?
Wood chipper manufacturers cater to landscaping and gardening businesses by offering machines that prepare organic material for landscaping projects. This process enhances soil health by adding organic matter and reduces costs associated with purchasing raw materials. International buyers should focus on the size and mobility of the chipper, ensuring it meets the specific needs of their projects while being easy to operate in diverse environments.
How Can Wood Chippers Support Bioenergy Production?
In the bioenergy sector, wood chipper manufacturers play a crucial role by converting wood waste into biomass fuel. This application supports renewable energy initiatives and minimizes landfill waste, contributing to sustainability goals. Buyers, especially in regions like Africa and South America, should prioritize sourcing chippers that comply with environmental standards and demonstrate high processing efficiency to maximize their investment.
What Benefits Do Wood Chippers Offer in Waste Management?
In waste management, wood chipper manufacturers provide solutions for shredding yard waste, facilitating recycling efforts. This application improves recycling rates and lessens reliance on landfills, making it a vital tool for waste management companies. When sourcing wood chippers, businesses should consider the versatility of the machine, as well as maintenance requirements to ensure long-term reliability.
How Do Wood Chippers Enhance Agricultural Practices?
In agriculture, wood chipper manufacturers supply equipment that produces feedstock from agricultural residues, enhancing soil quality and reducing the need for chemical fertilizers. This application is particularly beneficial for farmers aiming for sustainable practices. Buyers should look for chippers that are adaptable to different materials and come with operational support, ensuring they can efficiently integrate the equipment into their farming operations.
Related Video: Woodland Mills WC46 Wood Chipper Full Length Demo (2018)
3 Common User Pain Points for ‘wood chipper manufacturer’ & Their Solutions
Scenario 1: Difficulty Sourcing Quality Wood Chippers
The Problem:
Many international B2B buyers, particularly those in Africa and South America, face significant challenges in sourcing high-quality wood chippers. This can stem from a lack of established suppliers in their regions, leading to reliance on distant manufacturers with uncertain quality assurance. Buyers often report receiving equipment that does not meet specified standards or fails to perform under local conditions, resulting in wasted resources and operational downtime.
The Solution:
To overcome sourcing challenges, buyers should conduct thorough market research to identify reputable manufacturers known for quality. Utilize platforms like Alibaba, or specialized industrial equipment directories, to compare manufacturers and read reviews. When narrowing down options, request samples or visit manufacturing facilities if possible. It is also wise to engage with local distributors who can provide insights into the best models suited for specific regional needs. Establishing a direct line of communication with manufacturers can help clarify specifications and ensure that the equipment meets local operational conditions.
Scenario 2: Navigating Technical Specifications and Compatibility
The Problem:
B2B buyers often struggle with understanding the technical specifications of wood chippers, particularly in ensuring compatibility with existing equipment or local power sources. This issue is prevalent in the Middle East and Europe, where varying voltage standards and equipment requirements can complicate purchases. The risk of acquiring equipment that cannot be integrated into their operations leads to frustration and additional costs.
The Solution:
To mitigate compatibility concerns, buyers should develop a detailed understanding of their operational requirements before engaging with manufacturers. Create a checklist of essential specifications, including power requirements, feed capacity, and output size. When discussing options with manufacturers, leverage this checklist to ensure that all specifications align with existing systems. Additionally, consider consulting with an industry expert or a local technician who can provide insights on compatibility and recommend suitable models. This proactive approach will help prevent costly mistakes and ensure a seamless integration of the new equipment.
Scenario 3: Insufficient After-Sales Support and Maintenance
The Problem:
Another common pain point for B2B buyers is the lack of adequate after-sales support and maintenance services. This is especially concerning for buyers in Europe and the Middle East, where operational efficiency is crucial. Many manufacturers fail to provide the necessary training, spare parts, or service contracts that ensure the longevity and effective operation of wood chippers, leading to increased downtime and repair costs.
The Solution:
Buyers should prioritize manufacturers that offer comprehensive after-sales support and maintenance packages. When evaluating potential suppliers, inquire about their warranty policies, availability of spare parts, and the extent of their service offerings. It is beneficial to select manufacturers that have local representatives or partnerships with local service providers who can offer timely support. Additionally, consider negotiating service agreements that include regular maintenance checks and training for staff on proper operation and troubleshooting techniques. This not only extends the lifespan of the equipment but also enhances overall productivity and reduces long-term operational costs.
Strategic Material Selection Guide for wood chipper manufacturer
What Are the Key Materials for Wood Chipper Manufacturing?
When selecting materials for wood chipper manufacturing, it is essential to consider their properties, advantages, disadvantages, and their impact on performance. Below are analyses of four common materials used in the production of wood chippers: steel, aluminum, composite materials, and high-density polyethylene (HDPE).
How Does Steel Perform in Wood Chipper Manufacturing?
Key Properties: Steel is known for its high tensile strength and durability, making it suitable for heavy-duty applications. It can withstand high temperatures and pressures, which is crucial for the mechanical components of wood chippers.
Pros & Cons: The primary advantage of steel is its durability and resistance to wear and tear, which extends the lifespan of the equipment. However, steel is relatively heavy and can be prone to corrosion if not properly treated. The manufacturing complexity is moderate, requiring skilled labor for machining and welding.
Impact on Application: Steel components are compatible with various media, including wood and other organic materials. However, if exposed to moisture without protective coatings, they may rust, impacting performance.
Considerations for International Buyers: Buyers from regions like Africa and South America should ensure that the steel meets local standards (e.g., ASTM, ISO) for quality and corrosion resistance. In Europe, compliance with environmental regulations regarding material sourcing is also critical.
What Are the Benefits of Aluminum in Wood Chipper Design?
Key Properties: Aluminum is lightweight, corrosion-resistant, and has good thermal conductivity. It is also relatively easy to machine, which can speed up production.
Pros & Cons: The primary advantage of aluminum is its lightweight nature, which enhances the mobility of wood chippers. However, it is less durable than steel and may not withstand high-impact operations as effectively. The cost of aluminum can be higher than steel, depending on market conditions.
Impact on Application: Aluminum is suitable for applications where weight is a concern, such as portable wood chippers. Its corrosion resistance makes it ideal for humid environments.
Considerations for International Buyers: Buyers in the Middle East and Europe should verify that the aluminum used complies with local standards for durability and environmental impact. Additionally, they should consider the cost implications of sourcing aluminum from different regions.
Why Use Composite Materials in Wood Chipper Manufacturing?
Key Properties: Composite materials, such as fiberglass or carbon fiber, are known for their high strength-to-weight ratio and resistance to corrosion and environmental degradation.
Pros & Cons: The main advantage of composites is their lightweight nature and resistance to corrosion, which can significantly reduce maintenance costs. However, they can be more expensive to manufacture and may require specialized skills for repairs.
Impact on Application: Composites are particularly beneficial in applications where weight savings are crucial, such as in mobile or portable wood chippers. They also offer excellent performance in harsh environments.
Considerations for International Buyers: Buyers should ensure that composite materials meet international standards for safety and performance. In regions like Europe, compliance with environmental regulations regarding the use of composites is essential.
How Does High-Density Polyethylene (HDPE) Fit into Wood Chipper Manufacturing?
Key Properties: HDPE is a lightweight, flexible material known for its excellent chemical resistance and durability. It can withstand a wide range of temperatures and is resistant to impact.
Pros & Cons: The key advantage of HDPE is its resistance to chemicals and moisture, making it ideal for outdoor applications. However, it may not have the same strength as metals, limiting its use in high-stress components.
Impact on Application: HDPE is often used for non-structural components, such as hoppers and covers, where flexibility and resistance to the elements are more critical than structural integrity.
Considerations for International Buyers: Buyers should confirm that HDPE materials comply with local environmental regulations and standards. In regions like Africa and South America, sourcing from local suppliers may reduce costs and improve supply chain reliability.
Summary Table of Material Selection for Wood Chipper Manufacturing
Material | Typical Use Case for Wood Chipper Manufacturer | Key Advantage | Key Disadvantage/Limitation | Relative Cost (Low/Med/High) |
---|---|---|---|---|
Steel | Structural components | High durability and strength | Heavy and prone to corrosion | Medium |
Aluminum | Portable wood chippers | Lightweight and corrosion-resistant | Less durable under high impact | High |
Composite | High-performance, lightweight applications | Excellent strength-to-weight ratio | Higher manufacturing costs | High |
High-Density Polyethylene (HDPE) | Non-structural components | Chemical resistance and flexibility | Lower strength compared to metals | Low |
By understanding the properties and implications of each material, international B2B buyers can make informed decisions that align with their operational needs and compliance requirements.
In-depth Look: Manufacturing Processes and Quality Assurance for wood chipper manufacturer
What Are the Key Stages in the Manufacturing Process of Wood Chippers?
The manufacturing process of wood chippers involves several critical stages, each designed to ensure the final product meets the required specifications and quality standards. Understanding these stages helps international B2B buyers, especially from regions like Africa, South America, the Middle East, and Europe, make informed purchasing decisions.
1. Material Preparation: How Is Raw Material Selected and Processed?
The first step in manufacturing wood chippers is selecting the appropriate raw materials. High-quality steel and durable components are essential for ensuring longevity and performance. Suppliers often source materials from reputable vendors who can provide certifications of material quality.
Once the materials are sourced, they undergo preparation, which includes cutting, bending, and treating to enhance durability. Techniques such as laser cutting and CNC machining are commonly employed to achieve precise dimensions. Buyers should inquire about the suppliers’ material sourcing strategies and whether they conduct material inspections to verify quality.
2. Forming: What Techniques Are Used to Shape Wood Chipper Components?
Forming is the next stage, where the prepared materials are shaped into various components of the wood chipper. This process may involve several techniques:
-
Stamping and Pressing: These methods are used to create metal parts with high precision. They are particularly effective for producing large quantities of identical parts, reducing production costs.
-
Welding: This technique is critical for assembling components. The welding process must be carefully controlled to maintain structural integrity.
-
Casting: Some manufacturers use casting for complex shapes that are difficult to achieve through machining. This is often used for the chipper’s housing and blade assemblies.
B2B buyers should consider asking suppliers about their forming techniques and the technology they employ, as advanced methods can significantly impact product quality and reliability.
3. Assembly: How Are Wood Chippers Assembled for Optimal Performance?
The assembly stage is where all the individual components come together to form the complete wood chipper. This process requires skilled labor and precise assembly techniques to ensure that each part functions correctly. Key aspects include:
-
Assembly Line Techniques: Many manufacturers utilize assembly lines to streamline production, allowing for efficient workflows and minimizing errors.
-
Quality Control Checkpoints: Throughout the assembly process, quality checks are implemented to catch defects early. These checkpoints ensure that components fit together perfectly and function as intended.
International buyers should verify how a supplier organizes their assembly process and the quality checks they perform during this stage. This can help mitigate risks associated with product failures.
4. Finishing: What Are the Final Touches Applied to Wood Chippers?
Finishing processes enhance the aesthetic appeal and functional performance of wood chippers. This stage includes:
-
Painting and Coating: Protective coatings are applied to prevent rust and wear. Manufacturers may use powder coating or liquid paint, each offering different benefits in terms of durability and finish.
-
Final Inspection: After finishing, a thorough inspection is conducted to ensure that the product meets all specifications. This includes checking for surface defects, ensuring proper assembly, and testing functionality.
Buyers should inquire about the finishing processes used by suppliers, as these can significantly affect the longevity and maintenance of the equipment.
How Is Quality Assurance Implemented in Wood Chipper Manufacturing?
Quality assurance (QA) is a critical aspect of wood chipper manufacturing, ensuring that products meet international standards and customer expectations. B2B buyers should familiarize themselves with the various QA processes and certifications that reputable manufacturers adhere to.
What International Standards Are Relevant for Wood Chipper Manufacturers?
Manufacturers often comply with various international quality standards to ensure their products are reliable and safe. Key standards include:
-
ISO 9001: This standard focuses on quality management systems and is crucial for manufacturers aiming to improve their operational processes and customer satisfaction.
-
CE Marking: Required for products sold in the European Economic Area, CE marking indicates compliance with health, safety, and environmental protection standards.
-
API Certification: For manufacturers producing equipment that may be used in oil and gas applications, API standards ensure that products meet stringent safety and quality requirements.
B2B buyers should ask potential suppliers for their certifications and how they maintain compliance with these standards.
What Are the Key Quality Control Checkpoints in the Manufacturing Process?
Quality control (QC) is integrated throughout the manufacturing process with specific checkpoints:
-
Incoming Quality Control (IQC): This initial stage involves inspecting raw materials upon arrival to ensure they meet specified standards.
-
In-Process Quality Control (IPQC): During the manufacturing process, ongoing inspections are conducted to identify any deviations from quality standards.
-
Final Quality Control (FQC): Once the product is fully assembled, a final inspection is performed to ensure everything functions correctly and meets all specifications.
Buyers can assess a supplier’s commitment to quality by inquiring about their QC processes and the frequency of inspections.
How Can B2B Buyers Verify Supplier Quality Assurance Practices?
For international B2B buyers, especially those from diverse markets, verifying a supplier’s quality assurance practices is crucial. Here are some effective strategies:
-
Conduct Audits: Regular audits of suppliers can provide insights into their manufacturing processes and quality control measures.
-
Request Quality Reports: Suppliers should be able to provide detailed reports on their QC processes, including data from inspections and testing.
-
Engage Third-Party Inspectors: Utilizing independent third-party inspectors can help verify that suppliers adhere to quality standards and practices.
By employing these strategies, buyers can mitigate risks and ensure they partner with reliable manufacturers.
What Are the Unique Quality Control Considerations for International Buyers?
When sourcing wood chippers from manufacturers in different regions, there are several quality control nuances to consider:
-
Cultural Differences: Different regions may have varying standards for quality and business practices. Understanding these differences can help buyers navigate negotiations and expectations.
-
Regulatory Compliance: Buyers should be aware of local regulations in their home countries regarding machinery imports, as compliance can affect the ability to use or sell the product.
-
Shipping and Handling: The logistics of transporting machinery across borders can impact quality. Buyers should confirm that suppliers have protocols in place to protect products during transit.
By understanding these factors, B2B buyers can make more informed decisions and ensure they select manufacturers that prioritize quality and reliability in their wood chipper products.
Practical Sourcing Guide: A Step-by-Step Checklist for ‘wood chipper manufacturer’
In the competitive landscape of sourcing wood chipper manufacturers, having a structured approach is essential for B2B buyers, especially those operating in diverse regions such as Africa, South America, the Middle East, and Europe. This checklist will guide you through the crucial steps in the procurement process, ensuring you make informed decisions.
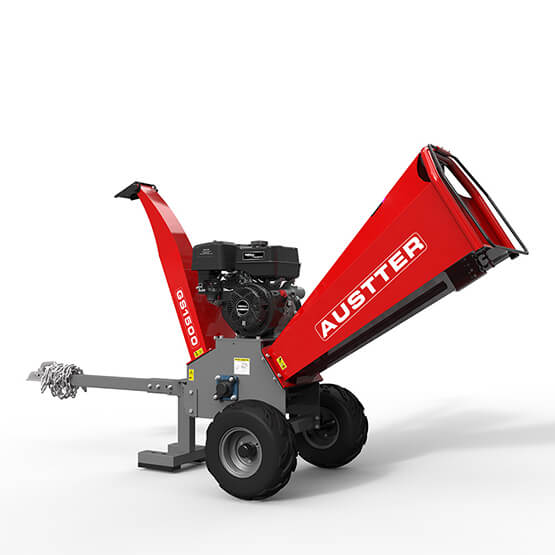
A stock image related to wood chipper manufacturer.
Step 1: Define Your Technical Specifications
Before initiating the sourcing process, clearly outline your technical requirements. Consider factors such as the type of wood you will be processing, the volume of material, and desired output size. This clarity will help you communicate effectively with potential manufacturers and ensure that the machines meet your operational needs.
- Key Considerations:
- What is the maximum diameter of wood the chipper must handle?
- Are you looking for a portable model or a stationary unit?
Step 2: Research Potential Manufacturers
Conduct thorough research to identify manufacturers with a solid reputation in the industry. Look for companies that specialize in wood chippers and have experience in exporting to your region. Utilize online platforms, industry directories, and trade shows to gather information.
- Where to Look:
- Industry trade shows (e.g., LIGNA for Europe)
- Online marketplaces (e.g., Alibaba, Made-in-China)
Step 3: Evaluate Supplier Certifications
Verify that potential suppliers hold relevant certifications and compliance with international standards. Certifications such as ISO 9001 for quality management systems or CE marking for safety can indicate a manufacturer’s commitment to quality and reliability.
- Why It Matters:
- Certifications ensure that the equipment meets safety and performance standards, reducing the risk of operational failures.
Step 4: Request and Compare Quotes
After narrowing down your list of potential suppliers, request detailed quotes. Ensure that these include all costs associated with the purchase, such as shipping, taxes, and installation fees. Comparing multiple quotes will help you identify competitive pricing and value-added services.
- What to Include in Your Request:
- Specifications for the wood chipper
- Delivery timelines and payment terms
Step 5: Assess After-Sales Support and Warranty
Evaluate the after-sales support offered by manufacturers, including warranty terms and availability of spare parts. A solid warranty can provide peace of mind and protect your investment, while responsive customer service can be invaluable if issues arise.
- Key Questions to Ask:
- What is covered under the warranty?
- How quickly can they provide spare parts?
Step 6: Check References and Reviews
Before finalizing your decision, check references and read reviews from other buyers. Insights from previous clients can reveal the reliability and performance of the wood chipper, as well as the manufacturer’s customer service track record.
- Sources for Feedback:
- Online forums and industry-specific groups
- Directly contacting past clients if possible
Step 7: Finalize the Purchase Agreement
Once you have selected a manufacturer, ensure that all terms are clearly defined in a purchase agreement. This should include delivery timelines, payment schedules, and responsibilities for both parties. Having a formal contract can protect you in case of disputes.
- Important Elements to Include:
- Payment terms and conditions
- Delivery and installation responsibilities
By following this step-by-step checklist, B2B buyers can navigate the complexities of sourcing wood chipper manufacturers more effectively, ensuring they select a supplier that aligns with their operational needs and business goals.
Comprehensive Cost and Pricing Analysis for wood chipper manufacturer Sourcing
What Are the Key Cost Components in Wood Chipper Manufacturing?
When sourcing wood chippers, understanding the cost structure is essential for making informed purchasing decisions. The primary cost components include:
-
Materials: The choice of materials significantly impacts the overall cost. High-quality steel, for example, increases durability but also raises the price. For international buyers, sourcing local materials can mitigate costs but may affect quality.
-
Labor: Labor costs vary widely by region. In countries with a lower cost of living, labor may be cheaper, which can reduce the overall production cost. However, be mindful of the skill level and training required for quality production.
-
Manufacturing Overhead: This includes indirect costs such as utilities, rent, and equipment maintenance. Understanding these costs can help buyers assess whether a manufacturer is operating efficiently.
-
Tooling: Investment in specialized tools for production can lead to higher upfront costs. However, efficient tooling can enhance production speed and quality, which may justify the initial expense.
-
Quality Control (QC): Effective QC processes are crucial in ensuring product reliability. While they add to the cost, they can prevent costly returns and reputational damage.
-
Logistics: Transportation costs, including shipping and handling, can be substantial, particularly for international shipments. Understanding the logistics involved can help buyers budget appropriately.

A stock image related to wood chipper manufacturer.
- Margin: Manufacturers typically include a profit margin in their pricing, which can vary based on market conditions and competition. International buyers should be aware of how these margins fluctuate in their specific regions.
How Do Price Influencers Affect Wood Chipper Costs?
Several factors can influence the pricing of wood chippers:
-
Volume/MOQ (Minimum Order Quantity): Ordering in bulk often results in discounts. International buyers should negotiate to achieve better pricing based on their expected order volume.
-
Specifications and Customization: Customized features can increase costs. Buyers should clearly define their requirements to avoid unexpected charges.
-
Materials and Quality Certifications: Higher quality materials and certifications (like ISO or CE) can justify a higher price but also ensure better performance and safety.
-
Supplier Factors: The reputation and reliability of the supplier can influence costs. Established suppliers may charge more but offer better service and warranty options.
-
Incoterms: Understanding the shipping terms can affect the total cost. Buyers should clarify who bears the risk and costs during transportation to avoid hidden fees.
What Are the Best Buyer Tips for Cost-Efficiency in Sourcing Wood Chippers?
-
Negotiate Wisely: Leverage your purchasing power by negotiating terms and pricing. Establishing a long-term relationship with suppliers can lead to better deals over time.
-
Evaluate Total Cost of Ownership (TCO): Consider not just the purchase price but also maintenance, operation, and disposal costs. A cheaper machine may lead to higher operational costs in the long run.
-
Understand Pricing Nuances for International Transactions: Currency fluctuations, tariffs, and import duties can all impact the final price. It’s advisable to work with suppliers who have experience in international trade.
-
Conduct Market Research: Stay informed about market trends and competitor pricing. This knowledge can empower you to negotiate better terms and identify opportunities for cost savings.
-
Consider Local Suppliers: Sourcing from local manufacturers in regions like Africa or South America can reduce shipping costs and lead times, enhancing overall value.
Disclaimer for Indicative Prices
Prices for wood chippers can vary significantly based on the factors mentioned above. The figures provided should be considered indicative and subject to change based on market conditions and specific supplier negotiations. Always request detailed quotes and breakdowns from manufacturers to ensure clarity and transparency in pricing.
Alternatives Analysis: Comparing wood chipper manufacturer With Other Solutions
Understanding Alternatives for Wood Chipper Solutions
When evaluating equipment for wood processing, particularly for international B2B buyers, it’s essential to consider alternatives to wood chippers. While wood chipper manufacturers offer robust solutions, other technologies and methods can also achieve similar outcomes. This analysis will compare wood chippers with two viable alternatives: biomass shredders and mulchers. Each option has its unique advantages and considerations, making it critical for buyers to assess their specific needs.
Comparison Table
Comparison Aspect | Wood Chipper Manufacturer | Biomass Shredder | Mulcher |
---|---|---|---|
Performance | High throughput for branches and wood logs | Versatile; handles various biomass materials | Excellent for grass and soft plant materials |
Cost | Moderate to high initial investment | Generally lower than wood chippers | Lower initial costs, but may require frequent replacements |
Ease of Implementation | Requires skilled operation | Typically user-friendly, fewer training needs | Easy to use, minimal training required |
Maintenance | Moderate; blades need regular sharpening | Low; fewer moving parts | Moderate; blades need periodic maintenance |
Best Use Case | Ideal for landscaping and forestry applications | Suitable for recycling organic waste and biomass | Best for garden maintenance and landscaping |
Detailed Breakdown of Alternatives
What Are Biomass Shredders and Their Advantages?
Biomass shredders are designed to process a wide range of organic materials, including branches, leaves, and other plant debris. They provide a versatile solution for businesses focused on recycling waste.
Pros:
– Versatility in handling various materials, from wood to softer plant matter.
– Generally lower initial costs compared to wood chippers, making them accessible for smaller operations.
Cons:
– Performance may be less efficient for larger wood logs, which could slow down operations.
– May require more frequent maintenance on parts that are exposed to harsher conditions.
How Do Mulchers Compare in Performance and Cost?
Mulchers are particularly effective for landscaping and garden maintenance. They excel in processing softer materials like grass and small branches, making them ideal for maintaining parks and gardens.
Pros:
– Lower initial investment and operational costs, making them attractive for small businesses.
– Easy to operate with minimal training, reducing overhead costs related to employee training.
Cons:
– Limited effectiveness with larger, harder materials, which can lead to operational inefficiencies if not properly matched to tasks.
– Regular maintenance of blades is necessary, which can add to long-term costs if not managed properly.
Conclusion: Choosing the Right Solution for Your Needs
Selecting the right equipment for wood processing requires a thorough understanding of your operational needs and material types. For B2B buyers, the choice between a wood chipper manufacturer, a biomass shredder, and a mulcher will depend on factors such as the types of materials processed, budget constraints, and the desired efficiency of operations. Conducting a detailed needs assessment will ensure that you invest in the most suitable solution for your business, ultimately leading to improved productivity and cost-efficiency.
Essential Technical Properties and Trade Terminology for wood chipper manufacturer
What Are the Essential Technical Properties of Wood Chippers?
When evaluating wood chippers, international B2B buyers should consider several critical technical specifications. These specifications not only impact performance but also play a significant role in operational efficiency and cost-effectiveness.
1. Material Grade
The material grade of a wood chipper, often categorized by its steel composition, determines its durability and resistance to wear and tear. High-grade steel is essential for components like the blades and chassis, ensuring longevity and reduced maintenance costs. For buyers in regions like Africa and South America, where operational conditions may be harsh, investing in high-quality materials can lead to significant long-term savings.
2. Cutting Capacity
Cutting capacity refers to the maximum diameter of wood the chipper can handle. This specification is crucial for businesses that deal with varying sizes of wood debris. A wood chipper with a higher cutting capacity can increase productivity and reduce the need for multiple machines. For example, buyers from the Middle East may prioritize machines that can handle larger branches due to the types of vegetation common in the region.
3. Power Rating
The power rating, usually measured in horsepower (HP) or kilowatts (kW), indicates the engine’s capability to process wood efficiently. A higher power rating can lead to faster processing times and the ability to handle denser materials. For European buyers, understanding power requirements can also be tied to local energy regulations and availability.
4. Weight and Portability
The weight of the wood chipper affects its portability and ease of transport. Lighter models may be more suitable for small-scale operations or for companies that need to move their equipment frequently. Conversely, heavier models may offer more stability and durability for larger operations. Buyers should assess their specific operational needs to determine the best option.
5. Noise Level
Noise level is an important specification, particularly in urban or residential areas. Manufacturers often provide decibel ratings for their machines. Understanding the noise output can help buyers comply with local regulations and minimize disturbances, especially in regions like Europe where noise restrictions are more stringent.
What Are Common Trade Terms Relevant to Wood Chipper Manufacturers?
Familiarity with industry terminology is essential for effective communication and negotiation in the B2B marketplace. Here are several key terms that buyers should know:
1. OEM (Original Equipment Manufacturer)
OEM refers to companies that produce parts and equipment that may be marketed by another manufacturer. In the context of wood chippers, buyers may seek OEM parts for maintenance and repairs, ensuring compatibility and quality.
2. MOQ (Minimum Order Quantity)
MOQ is the smallest quantity of a product that a supplier is willing to sell. This term is crucial for B2B buyers who need to understand the minimum investment required for purchasing wood chippers or replacement parts, especially when sourcing from manufacturers in different regions.
3. RFQ (Request for Quotation)
An RFQ is a document that buyers submit to suppliers to request pricing information for specific products or services. This process is vital for comparing offers from multiple manufacturers and ensuring competitive pricing for wood chippers.
4. Incoterms
Incoterms (International Commercial Terms) are standardized terms used in international trade to define the responsibilities of buyers and sellers. Understanding these terms is essential for B2B buyers when negotiating shipping and delivery conditions, particularly when importing wood chippers from manufacturers in Europe or the Middle East.
5. Lead Time
Lead time refers to the amount of time it takes from placing an order to receiving the goods. For B2B buyers, knowing the lead time can help in planning operations and inventory management, especially in regions with fluctuating demand.
By grasping these technical properties and trade terms, international B2B buyers can make informed decisions, ensuring they select the right wood chipper for their operational needs while navigating the complexities of the global supply chain.
Navigating Market Dynamics and Sourcing Trends in the wood chipper manufacturer Sector
What are the Key Market Dynamics and Trends in the Wood Chipper Manufacturer Sector?
The global wood chipper manufacturer market is influenced by several key drivers, including the increasing demand for sustainable forestry practices and the rising need for efficient waste management solutions. As industries in Africa, South America, the Middle East, and Europe ramp up their environmental initiatives, the demand for high-performance wood chippers that can efficiently process wood waste into usable materials is on the rise. This trend is particularly prominent in sectors such as landscaping, agriculture, and construction, where wood waste management is critical.
Emerging B2B technology trends, such as automation and IoT (Internet of Things) integration, are reshaping the wood chipper landscape. Manufacturers are investing in smart chippers that offer real-time monitoring, predictive maintenance, and enhanced operational efficiency. This technology not only reduces downtime but also optimizes resource utilization, making it appealing to international buyers looking for cost-effective solutions. Additionally, the shift towards electric and hybrid models is gaining traction, especially in regions where emissions regulations are stringent.
Market dynamics are also shifting due to increased competition and a growing focus on customization. Buyers are increasingly seeking machines tailored to their specific operational needs, prompting manufacturers to diversify their product offerings. This trend is particularly evident in regions like Europe, where buyers prioritize features like portability, ease of use, and energy efficiency.
How Can Sustainability and Ethical Sourcing Impact Your B2B Relationships?
Sustainability has become a cornerstone of the wood chipper manufacturing sector, driven by both regulatory requirements and consumer preferences. International buyers are now more focused on the environmental impact of their purchases, making it essential for manufacturers to adopt sustainable practices throughout their supply chains. Ethical sourcing of materials—ensuring they come from responsibly managed forests—is increasingly vital. This not only helps in reducing deforestation but also supports local economies and biodiversity.
Certifications such as FSC (Forest Stewardship Council) and PEFC (Programme for the Endorsement of Forest Certification) are becoming crucial for B2B buyers. These certifications provide assurance that the wood and components used in manufacturing wood chippers meet high environmental and social standards. By opting for manufacturers that hold these certifications, buyers can enhance their own brand reputation and align with global sustainability goals.
Moreover, the adoption of ‘green’ technologies—such as energy-efficient designs and recyclable materials—adds another layer of value. Buyers in regions like Africa and South America, where environmental considerations are becoming increasingly important, stand to gain a competitive edge by partnering with manufacturers committed to sustainability.
What is the Historical Context of the Wood Chipper Manufacturing Sector?
The wood chipper manufacturing sector has evolved significantly over the past few decades. Initially, wood chippers were simple machines designed for basic wood processing tasks. However, advancements in technology have transformed these machines into sophisticated, multifunctional tools capable of handling a variety of materials and applications.
The shift towards more efficient and environmentally friendly practices began in the late 20th century, driven by rising environmental awareness and regulatory changes. Today, manufacturers are not only focused on performance but also on sustainability and ethical sourcing, reflecting the changing priorities of international B2B buyers. As the market continues to evolve, manufacturers that embrace innovation and sustainability will be better positioned to meet the diverse needs of their global clientele.
Frequently Asked Questions (FAQs) for B2B Buyers of wood chipper manufacturer
-
How do I choose the right wood chipper for my business needs?
Choosing the right wood chipper involves assessing your specific requirements, such as the type and volume of material you need to process. Consider the chipper’s capacity, power source (gas or electric), and the size of the branches it can handle. Additionally, evaluate features like portability, ease of maintenance, and safety mechanisms. For international buyers, it’s crucial to ensure that the specifications align with local regulations and operational conditions in your region, whether in Africa, South America, the Middle East, or Europe. -
What is the best wood chipper for commercial use?
The best wood chipper for commercial use typically has a high feed rate and robust power, enabling it to handle larger volumes of wood efficiently. Look for models with features like dual feed rollers and heavy-duty engines. Brands that are well-regarded in the industry include Vermeer, Bandit, and Timberwolf. When selecting a chipper, consider your specific business needs, such as the type of wood you will process and the frequency of use, to ensure optimal performance. -
What should I know about international sourcing of wood chippers?
When sourcing wood chippers internationally, it’s essential to understand the import regulations and standards in your country. Research potential manufacturers thoroughly, checking for certifications, warranty policies, and after-sales support. Building relationships with suppliers can also facilitate smoother transactions. Moreover, consider language barriers and time zone differences that may impact communication. Engaging a local representative can help navigate these challenges effectively. -
How can I vet wood chipper manufacturers before making a purchase?
Vetting wood chipper manufacturers requires due diligence. Start by reviewing their online presence, including customer testimonials and industry certifications. Request references from previous clients and inquire about their production capabilities and quality control processes. Visiting the manufacturing facility, if feasible, can provide valuable insights into their operations. Additionally, check for compliance with international standards to ensure reliability and safety in your purchase. -
What are typical minimum order quantities (MOQ) for wood chippers?
Minimum order quantities (MOQ) for wood chippers can vary significantly depending on the manufacturer and the model. Generally, MOQs can range from a single unit for smaller manufacturers to several units for larger manufacturers focusing on bulk sales. It’s advisable to negotiate these terms directly with suppliers, especially if you are a new buyer or exploring options for trial orders. Understand that some suppliers may offer flexible MOQ terms to establish long-term relationships. -
What payment terms should I expect when purchasing from a wood chipper manufacturer?
Payment terms when purchasing wood chippers can vary widely. Common terms include a deposit upfront (often 30-50%) with the balance due prior to shipping or upon delivery. Some manufacturers may offer financing options or extended payment plans for larger orders. Always ensure that the payment method is secure, and consider using letters of credit for international transactions to protect against risks. Clarifying payment terms upfront can help prevent misunderstandings later in the purchasing process. -
What quality assurance measures should I look for in wood chippers?
Quality assurance measures in wood chippers include certifications such as ISO 9001, which indicates adherence to quality management systems. Inquire about the manufacturer’s testing protocols, including performance tests and safety checks before shipment. Request documentation of warranty coverage and post-purchase support, as reliable manufacturers often provide comprehensive service agreements. Understanding these measures will help ensure that you receive a durable and efficient product that meets your operational needs. -
How can I manage logistics and shipping for imported wood chippers?
Managing logistics for imported wood chippers involves coordinating with freight forwarders who specialize in heavy machinery. Ensure that you understand the shipping terms (FOB, CIF, etc.) and have a clear timeline for delivery. Consider the costs associated with customs clearance and duties, which can vary by region. It’s also essential to verify that the chipper is adequately packaged to prevent damage during transit. Establishing a reliable logistics partner can simplify the shipping process and ensure timely delivery to your location.
Important Disclaimer & Terms of Use
⚠️ Important Disclaimer
The information provided in this guide, including content regarding manufacturers, technical specifications, and market analysis, is for informational and educational purposes only. It does not constitute professional procurement advice, financial advice, or legal advice.
While we have made every effort to ensure the accuracy and timeliness of the information, we are not responsible for any errors, omissions, or outdated information. Market conditions, company details, and technical standards are subject to change.
B2B buyers must conduct their own independent and thorough due diligence before making any purchasing decisions. This includes contacting suppliers directly, verifying certifications, requesting samples, and seeking professional consultation. The risk of relying on any information in this guide is borne solely by the reader.
Strategic Sourcing Conclusion and Outlook for wood chipper manufacturer
In the evolving landscape of wood chipper manufacturing, strategic sourcing has emerged as a critical component for international B2B buyers. By prioritizing supplier relationships and leveraging global sourcing strategies, businesses can secure not only competitive pricing but also enhanced product quality and innovation. Buyers from regions such as Africa, South America, the Middle East, and Europe should consider local market dynamics, regulatory frameworks, and sustainability practices when selecting suppliers.
How Can Strategic Sourcing Drive Value for B2B Buyers?
Investing in strategic sourcing allows companies to mitigate risks associated with supply chain disruptions and fluctuating market conditions. It also facilitates access to cutting-edge technologies and sustainable materials, which are increasingly important to consumers and regulatory bodies alike. By aligning procurement strategies with long-term business goals, buyers can enhance operational efficiency and drive profitability.
What is the Future Outlook for Wood Chipper Manufacturers?
As the demand for eco-friendly and efficient wood processing solutions continues to grow, international buyers are encouraged to engage with manufacturers that prioritize innovation and sustainability. The future holds significant opportunities for those willing to adapt and evolve with market trends. By fostering strong partnerships and embracing strategic sourcing practices, businesses can position themselves at the forefront of the wood chipper industry.