Discover Top Benefits of Glass Container Manufacturer (2025)
Introduction: Navigating the Global Market for glass container manufacturer
In the competitive landscape of international trade, sourcing high-quality glass containers can present significant challenges for B2B buyers. Whether you are looking to supply products to the burgeoning beverage industry in Brazil or seeking sustainable packaging solutions for cosmetics in Turkey, understanding the intricacies of the global market for glass container manufacturers is essential. This guide provides a comprehensive overview of the types of glass containers available, their applications across various industries, and critical insights into supplier vetting processes.
Navigating through the complexities of sourcing involves evaluating manufacturers based on quality standards, production capabilities, and compliance with international regulations. Buyers from Africa, South America, the Middle East, and Europe will find actionable insights into cost considerations, shipping logistics, and negotiation strategies that can enhance their purchasing decisions. The guide also addresses how to identify reputable suppliers, ensuring that your partnerships are built on transparency and reliability.
By empowering international B2B buyers with in-depth knowledge and practical tools, this guide aims to facilitate informed decision-making in a market characterized by rapid changes and emerging trends. Whether you are an established player or a newcomer in the glass packaging sector, understanding the global landscape of glass container manufacturing will help you navigate your sourcing challenges effectively.
Understanding glass container manufacturer Types and Variations
Type Name | Key Distinguishing Features | Primary B2B Applications | Brief Pros & Cons for Buyers |
---|---|---|---|
Bottled Glass Containers | Available in various shapes, sizes, and closures; often custom-designed. | Beverage industry, cosmetics, pharmaceuticals | Pros: High-quality presentation; customizable. Cons: Heavier than plastic; potential breakage. |
Glass Jars | Typically wide-mouthed; available with metal or plastic lids; often used for food storage. | Food packaging, retail, home goods | Pros: Excellent barrier properties; reusable. Cons: Can be more expensive; requires careful handling. |
Glass Vials | Small, cylindrical containers; often used in laboratory settings; available in various sizes. | Pharmaceuticals, laboratories, cosmetics | Pros: Precise dosage; tamper-proof. Cons: Limited volume; can be fragile. |
Glass Tubes | Long, cylindrical shapes; often used for specialty applications; can be custom-made. | Laboratory use, scientific applications | Pros: Versatile; can be made to specific dimensions. Cons: Not suitable for all products; may require special handling. |
Specialty Glass Containers | Tailored designs for niche markets; may include features like UV protection or custom labeling. | Niche markets, luxury goods, specialty foods | Pros: Unique branding opportunities; tailored to specific needs. Cons: Higher production costs; longer lead times. |
What Are the Key Characteristics of Bottled Glass Containers?
Bottled glass containers are versatile and come in a range of shapes and sizes, making them suitable for various industries, particularly beverages and cosmetics. They are often custom-designed to meet branding requirements. When considering bottled glass containers, B2B buyers should evaluate factors such as weight, design complexity, and potential for breakage. These containers offer an upscale presentation that can enhance brand image but may incur higher shipping costs due to their weight.
How Do Glass Jars Stand Out in the Market?
Glass jars are characterized by their wide mouths and compatibility with various lid types, making them ideal for food packaging and retail. Their excellent barrier properties protect contents from contamination, which is crucial for food safety. Buyers should consider the cost-effectiveness of bulk purchasing versus individual units and the potential for reusability. While glass jars may be more expensive upfront, their durability and recyclability can offer long-term savings and environmental benefits.
What Are the Advantages of Using Glass Vials?
Glass vials are small, cylindrical containers that excel in applications requiring precision, such as pharmaceuticals and laboratory use. They are often designed to be tamper-proof, ensuring the safety and integrity of their contents. B2B buyers should consider the specific size and volume requirements for their products, as well as any special features like airtight seals. While glass vials are ideal for sensitive applications, their fragility and limited volume may pose challenges in certain scenarios.
Why Choose Glass Tubes for Specialty Applications?
Glass tubes are long, cylindrical containers that can be custom-made for various applications, particularly in scientific and laboratory settings. Their versatility allows for tailored dimensions, catering to specific project needs. B2B buyers should assess the intended use and compatibility of glass tubes with their products. While they offer unique advantages, such as customizability, they may not be suitable for all types of products and can require special handling during transport.
What Makes Specialty Glass Containers Unique?
Specialty glass containers are designed for niche markets, offering unique features like UV protection and custom labeling. These containers allow brands to differentiate themselves in competitive markets, particularly in luxury goods and specialty foods. Buyers should evaluate the production costs and lead times associated with these custom designs. While specialty containers can enhance branding and product appeal, they often come with higher production costs, necessitating careful budget considerations.
Related Video: Manufacturing process of a glass bottle || Machines and Industry
Key Industrial Applications of glass container manufacturer
Industry/Sector | Specific Application of Glass Container Manufacturer | Value/Benefit for the Business | Key Sourcing Considerations for this Application |
---|---|---|---|
Food and Beverage | Packaging for Juices and Sauces | Enhances product shelf life and preserves flavor integrity | Ensure compliance with food safety regulations and certifications. |
Pharmaceuticals | Bottles for Medicines and Vaccines | Provides a sterile environment, ensuring product safety | Look for manufacturers with experience in pharmaceutical standards. |
Cosmetics and Personal Care | Containers for Skincare Products | Protects product integrity and enhances brand presentation | Consider customization options and sustainability practices. |
Chemicals | Storage Containers for Industrial Chemicals | Ensures safe transport and storage, minimizing contamination | Verify chemical compatibility and durability of materials. |
Home and Garden | Jars for Preserves and Home Decor Items | Versatile use for both functional and decorative purposes | Assess design and size options suitable for target markets. |
How is Glass Used in Food and Beverage Packaging?
In the food and beverage industry, glass container manufacturers produce packaging solutions for juices, sauces, and other consumables. Glass is favored for its inert properties, which prevent chemical reactions that could alter the taste or safety of food products. International buyers should prioritize sourcing from manufacturers that comply with food safety regulations, ensuring that their products meet both local and international standards. Additionally, the ability to provide custom designs can enhance brand visibility and appeal in competitive markets.
What Role Does Glass Play in Pharmaceuticals?
Glass containers are critical in the pharmaceutical sector, where they are used for packaging medicines and vaccines. The primary advantage of glass is its ability to provide a sterile environment, which is essential for maintaining the efficacy of sensitive products. Buyers in regions like Africa and South America should focus on suppliers that adhere to stringent pharmaceutical guidelines and quality assurance processes. This ensures that the glass containers not only protect the product but also comply with health regulations in their respective markets.
How is Glass Utilized in Cosmetics and Personal Care?
In the cosmetics and personal care industry, glass containers are widely used for skincare products and fragrances. These containers not only enhance the aesthetic appeal of the products but also protect them from environmental factors that could degrade quality. When sourcing glass containers, buyers should consider manufacturers that offer customization options to align with their branding strategies. Sustainability is also a growing concern, so selecting suppliers that prioritize eco-friendly practices can provide a competitive edge in the market.
What Are the Benefits of Glass in Chemical Storage?
Glass containers are essential for the safe storage and transport of industrial chemicals. They are resistant to many chemicals, minimizing the risk of contamination and ensuring safe handling. B2B buyers in sectors dealing with hazardous materials should verify the compatibility of glass with specific chemicals, as well as the durability of the containers under various conditions. Ensuring that suppliers have robust quality control measures in place is crucial for maintaining safety and compliance.
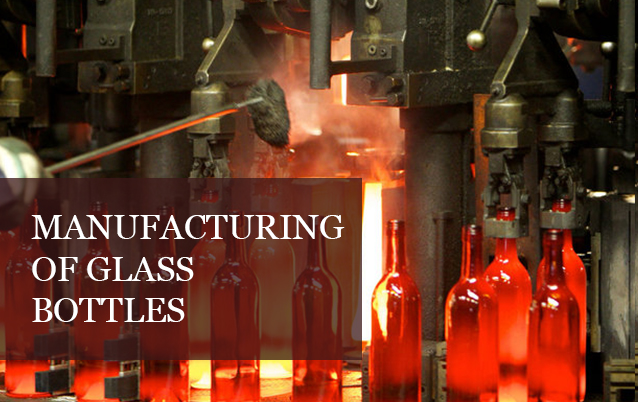
A stock image related to glass container manufacturer.
How is Glass Used in Home and Garden Products?
In the home and garden sector, glass containers are popular for preserves and decorative items. Their versatility allows them to be used for both functional storage and aesthetic purposes. Buyers should assess the variety of designs and sizes available from manufacturers to meet the diverse needs of consumers. Additionally, understanding market trends and consumer preferences in different regions, such as Europe and the Middle East, can inform better sourcing decisions and product selections.
3 Common User Pain Points for ‘glass container manufacturer’ & Their Solutions
Scenario 1: Challenges with Customization and Design
The Problem: One of the most common pain points for B2B buyers in the glass container sector is the need for customization. Many companies require specific sizes, shapes, or branding features that off-the-shelf solutions cannot meet. Buyers often find themselves frustrated when manufacturers are unable to accommodate these requests, leading to delays in product launches and potential loss of market competitiveness. This challenge is especially pronounced for buyers in industries like cosmetics or food and beverage, where packaging design can significantly impact consumer perception.
The Solution: To effectively address the challenge of customization, buyers should first engage in detailed discussions with potential manufacturers regarding their specific needs. This includes providing sketches, specifications, and even prototypes to ensure the manufacturer fully understands the requirements. Additionally, consider partnering with manufacturers that have a robust design team capable of offering insights and suggestions based on current market trends. Establishing clear communication channels and setting up regular checkpoints throughout the design process can help ensure that the final product aligns with expectations. Finally, requesting samples before committing to a larger order can help mitigate risks associated with custom designs.
Scenario 2: Quality Control and Consistency Issues
The Problem: For international B2B buyers, maintaining quality control in glass container production can be a daunting task. Variability in glass quality, thickness, and finish can lead to inconsistent products that do not meet regulatory standards or customer expectations. This inconsistency can be particularly problematic for companies that distribute products across multiple regions, as differing regulations and consumer preferences can amplify the impact of quality issues.
The Solution: To combat quality control challenges, buyers should prioritize working with manufacturers that have established quality assurance protocols. This can include certifications such as ISO 9001 or compliance with local and international standards. Buyers should also consider implementing a quality control checklist specific to their needs, which can include criteria like clarity, weight, and durability. Regular audits of the manufacturing process and the ability to visit production facilities can also help ensure that quality standards are upheld. Additionally, establishing a clear return policy for defective items can protect the buyer’s interests and foster better relationships with manufacturers.
Scenario 3: Supply Chain Disruptions and Lead Time Delays
The Problem: Supply chain disruptions are a significant concern for B2B buyers in the glass container industry, especially in regions like Africa and South America, where logistics can be more complex. Delays in lead times can occur due to factors such as material shortages, transportation issues, or unexpected demand fluctuations. These delays can lead to stockouts, negatively impacting sales and customer satisfaction.
The Solution: To mitigate supply chain risks, buyers should adopt a proactive approach to inventory management. This includes maintaining a buffer stock to cover potential delays and collaborating closely with manufacturers to understand their production capacities and timelines. Buyers should also explore diversifying their supplier base to avoid over-reliance on a single manufacturer, which can provide more flexibility in meeting demand. Additionally, utilizing technology, such as supply chain management software, can help track orders in real time, allowing buyers to respond swiftly to any disruptions. Establishing strong relationships with logistics partners can also facilitate smoother transportation and minimize lead time variability.
Strategic Material Selection Guide for glass container manufacturer
When selecting materials for glass containers, it is essential to consider various factors that influence performance, durability, and compliance with industry standards. Below is a detailed analysis of four common materials used in the manufacturing of glass containers, focusing on their properties, advantages, disadvantages, and specific considerations for international B2B buyers, particularly in Africa, South America, the Middle East, and Europe.
What Are the Key Properties of Soda-Lime Glass for Glass Containers?
Soda-lime glass is the most widely used type of glass in container manufacturing. It typically consists of silica, soda, and lime, which contribute to its favorable properties. This material can withstand moderate temperatures and pressures, making it suitable for a variety of applications. Its corrosion resistance is adequate for many beverages and food products, but it may not be suitable for highly acidic or alkaline substances.
Pros & Cons: Soda-lime glass is durable and cost-effective, making it a popular choice for mass production. However, it has limitations in terms of thermal shock resistance and can break under sudden temperature changes. Additionally, while it is relatively inexpensive to produce, the costs can increase with decorative finishes or custom shapes.
Impact on Application: Soda-lime glass containers are commonly used for beverages, food storage, and pharmaceuticals. However, manufacturers must ensure compatibility with the specific media, especially if the contents are sensitive to glass leachables.
How Does Borosilicate Glass Compare for High-Performance Applications?
Borosilicate glass is known for its exceptional thermal resistance and low thermal expansion coefficient. This makes it ideal for applications that involve high temperatures or rapid temperature changes, such as laboratory glassware and certain food containers. It also exhibits excellent chemical resistance, making it suitable for storing aggressive chemicals.
Pros & Cons: The primary advantage of borosilicate glass is its durability under extreme conditions, which can lead to longer product lifespans. However, it is more expensive to manufacture than soda-lime glass, which can impact overall project budgets. Additionally, the manufacturing process is more complex, potentially leading to longer lead times.
Impact on Application: Borosilicate glass is particularly beneficial for applications requiring high thermal stability, such as in the pharmaceutical and laboratory sectors. Buyers should ensure compliance with relevant standards, especially for laboratory use, where ASTM and ISO standards may apply.
What Are the Benefits of Using Recycled Glass in Container Manufacturing?
Recycled glass, often referred to as cullet, is increasingly being used in glass container manufacturing due to its sustainability benefits. Using recycled materials can significantly reduce energy consumption during production and lower overall manufacturing costs. The properties of recycled glass are similar to those of soda-lime glass, making it a viable option for many applications.
Pros & Cons: The key advantage of using recycled glass is its environmental impact, as it contributes to a circular economy. However, the quality of recycled glass can vary, which may affect the final product’s strength and clarity. Additionally, sourcing high-quality cullet can be challenging in certain regions.
Impact on Application: Recycled glass is suitable for a wide range of applications, including food and beverage containers. International buyers should be aware of local regulations regarding the use of recycled materials, as compliance can vary significantly between regions.
Why Is Specialty Glass Important for Niche Applications?
Specialty glass, which includes materials such as lead glass or aluminosilicate glass, is designed for specific applications requiring unique properties. For example, lead glass is often used in high-end packaging due to its aesthetic qualities and weight, while aluminosilicate glass offers superior strength and thermal resistance.
Pros & Cons: Specialty glass can provide significant advantages in terms of performance and aesthetics, making it suitable for niche markets. However, the manufacturing processes are often more complex and costly, which can limit its use in mass production.
Impact on Application: Specialty glass is often used in luxury packaging, medical applications, and high-performance environments. Buyers should consider the specific requirements of their applications and ensure compliance with relevant industry standards.
Summary Table of Material Selection for Glass Container Manufacturing
Material | Typical Use Case for glass container manufacturer | Key Advantage | Key Disadvantage/Limitation | Relative Cost (Low/Med/High) |
---|---|---|---|---|
Soda-Lime Glass | Beverages, food storage | Cost-effective and durable | Limited thermal shock resistance | Low |
Borosilicate Glass | Laboratory glassware, high-temperature food | Excellent thermal and chemical resistance | Higher manufacturing costs | High |
Recycled Glass | Food and beverage containers | Environmentally friendly | Variable quality of recycled materials | Medium |
Specialty Glass | Luxury packaging, medical applications | Unique properties for niche markets | Complex and costly manufacturing processes | High |
This strategic material selection guide serves as a valuable resource for international B2B buyers, enabling informed decisions that align with performance requirements, budget constraints, and compliance with regional standards.
In-depth Look: Manufacturing Processes and Quality Assurance for glass container manufacturer
What Are the Main Stages in the Manufacturing Process of Glass Containers?
The manufacturing process of glass containers is complex and involves several critical stages. Understanding these can help B2B buyers evaluate potential suppliers more effectively.
1. Material Preparation
The first step in glass container manufacturing is material preparation. The primary raw materials used are silica sand, soda ash, and limestone. These materials must be of high purity to ensure the final product meets quality standards.
For international buyers, it is essential to verify that suppliers source their raw materials responsibly and sustainably. This includes checking for certifications and understanding the supplier’s supply chain practices, especially in regions with varying regulations.
2. Forming
Once the materials are prepared, they are melted in a furnace at temperatures exceeding 1,500°C (2,732°F). The molten glass is then shaped into containers using various techniques, including:
- Blow Molding: Commonly used for producing hollow glass containers, where air is blown into the molten glass to shape it.
- Press Molding: Used for thicker glass items, where a plunger presses molten glass into a mold.
- Forming Machines: These can produce containers at high speed, suitable for mass production.
Buyers should inquire about the forming techniques utilized by their suppliers to ensure they can meet specific product requirements.
3. Annealing
After forming, glass containers undergo annealing, a slow cooling process that relieves internal stresses. This stage is crucial for ensuring the durability and structural integrity of the glass.
B2B buyers should look for suppliers that adhere to strict annealing practices, as improper cooling can lead to defects and breakage during transportation or use.
4. Finishing
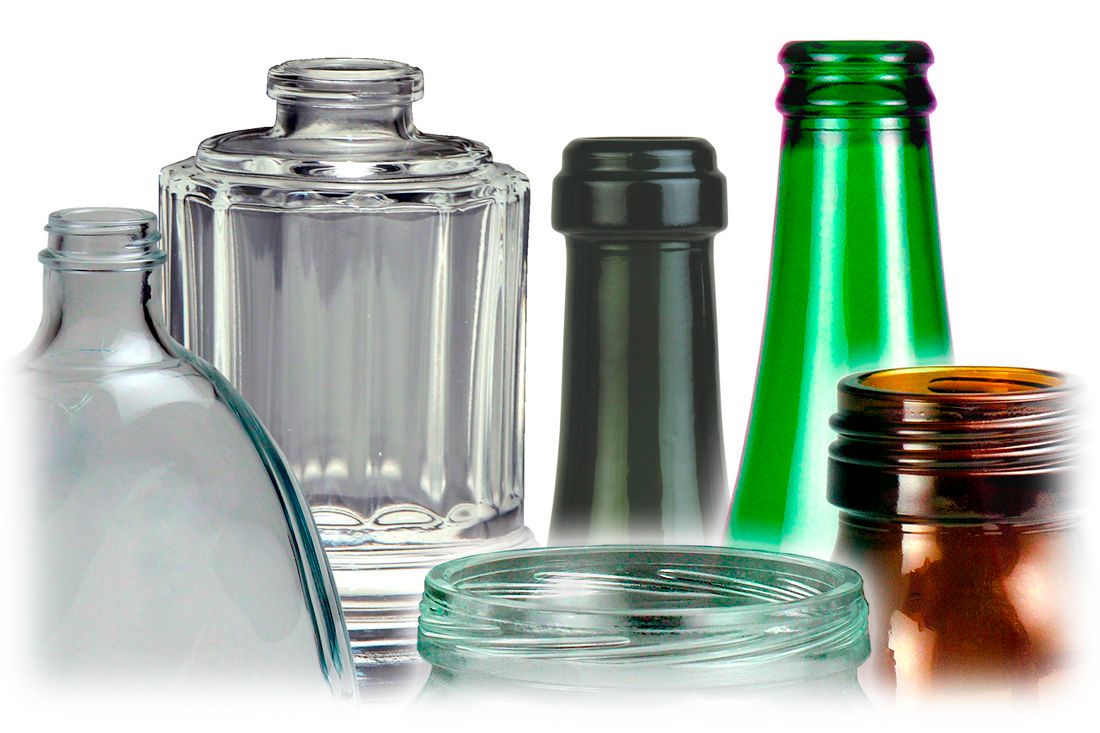
A stock image related to glass container manufacturer.
The finishing stage includes processes such as surface treatment, printing, and coating. This is where branding and labeling occur, making it vital for buyers to communicate their specific requirements.
Additionally, surface treatments may enhance the glass’s resistance to scratches and chemicals, which is particularly important in sectors like food and beverage.
How Is Quality Assurance Implemented in Glass Container Manufacturing?
Quality assurance (QA) is crucial in ensuring that glass containers meet international standards and client specifications. Understanding the QA process can help B2B buyers assess supplier reliability.
International Quality Standards to Consider
For international buyers, familiarizing themselves with relevant quality standards is essential. Key certifications include:
- ISO 9001: This standard focuses on quality management systems and is applicable to any organization seeking to improve quality and customer satisfaction.
- CE Marking: Essential for products sold within the European Economic Area, this marking indicates conformity with health, safety, and environmental protection standards.
- API Standards: Particularly relevant for buyers in the pharmaceutical and food industries, ensuring that containers meet specific safety and quality criteria.
Buyers should request documentation proving compliance with these standards from potential suppliers.
What Are the Key Quality Control Checkpoints?
Quality control (QC) in glass container manufacturing involves several checkpoints throughout the production process:
- Incoming Quality Control (IQC): This checkpoint involves inspecting raw materials upon arrival to ensure they meet specified standards.
- In-Process Quality Control (IPQC): During production, samples are regularly tested to identify defects early. This includes monitoring the forming process and the annealing stage.
- Final Quality Control (FQC): Finished products undergo a thorough inspection before shipment, checking for defects in shape, size, and surface quality.
B2B buyers should inquire about the frequency and rigor of these QC checkpoints to gauge the supplier’s commitment to quality.
Which Testing Methods Are Commonly Used in Quality Assurance?
Several testing methods are employed to ensure the quality of glass containers:
- Visual Inspection: A straightforward method where trained personnel examine containers for surface defects.
- Dimensional Testing: Ensures that the glass containers meet specified dimensions and tolerances.
- Strength Testing: Includes tests like the drop test to evaluate the container’s durability under stress.
- Chemical Resistance Testing: Important for containers used in the food and beverage industry, ensuring they do not leach harmful substances.
B2B buyers should ask suppliers for detailed reports on these tests, as they provide insight into the quality of the products being offered.
How Can B2B Buyers Verify Supplier Quality Control Practices?
Verifying a supplier’s quality control practices is essential for mitigating risks. Here are actionable steps for B2B buyers:
-
Conduct Audits: Regular audits, whether conducted by the buyer or third-party organizations, can provide a comprehensive view of a supplier’s quality control practices.
-
Request Quality Reports: Suppliers should be willing to provide documentation of their QC processes, including results from testing methods and compliance with international standards.
-
Engage Third-Party Inspectors: Employing independent inspectors can offer an unbiased assessment of the supplier’s manufacturing and quality control practices.
-
Check Certifications: Ensure that suppliers possess relevant certifications, and verify their validity through the issuing bodies.
What Are the Quality Control Nuances for International Buyers?
When dealing with suppliers from different regions, particularly in Africa, South America, the Middle East, and Europe, B2B buyers should be aware of the following nuances:
- Regulatory Differences: Different regions may have varying regulations regarding glass manufacturing, which can affect product quality.
- Cultural Practices: Understanding local business practices and expectations can facilitate better communication and cooperation with suppliers.
- Logistical Considerations: Shipping glass containers involves risks of breakage. Buyers should discuss packaging and shipping methods to ensure product integrity upon arrival.
By being proactive and thorough in assessing manufacturing processes and quality assurance practices, international B2B buyers can make informed decisions when selecting glass container manufacturers, ensuring high-quality products that meet their specific needs.
Practical Sourcing Guide: A Step-by-Step Checklist for ‘glass container manufacturer’
Introduction
Navigating the procurement process for glass containers can be complex, especially for international B2B buyers from diverse regions like Africa, South America, the Middle East, and Europe. This checklist serves as a practical guide to streamline your sourcing journey, ensuring that you find a reliable glass container manufacturer that meets your specific needs.
Step 1: Define Your Technical Specifications
Before reaching out to potential suppliers, it’s essential to outline your technical requirements. Consider factors such as container size, shape, weight, and any specific design features. This clarity not only helps in communicating your needs but also aids manufacturers in providing accurate quotations.
- Material Quality: Specify the type of glass (e.g., borosilicate, soda-lime) needed for durability and application.
- Compliance Standards: Ensure your specifications meet industry standards relevant to your region, such as FDA regulations for food-safe containers.
Step 2: Research Potential Suppliers
Conduct thorough research to identify potential glass container manufacturers. Utilize online directories, trade shows, and industry associations to compile a list of candidates.
- Market Presence: Look for manufacturers with a solid market presence and positive reviews from previous clients.
- Regional Considerations: Focus on suppliers within or near your target market to reduce shipping costs and lead times.
Step 3: Evaluate Supplier Capabilities
Assess the capabilities of each manufacturer to ensure they can meet your requirements. This includes evaluating production capacity, technology, and quality control processes.
- Production Techniques: Inquire about the manufacturing processes used, such as automated vs. manual production.
- Quality Assurance: Check for certifications like ISO 9001, which indicate adherence to quality management standards.
Step 4: Verify Supplier Certifications
Before finalizing a supplier, confirm their certifications and compliance with international standards. This step is crucial for ensuring product quality and safety.
- Regulatory Compliance: Verify that the supplier complies with local and international regulations pertinent to your industry.
- Sustainability Practices: Investigate if the manufacturer follows sustainable practices, which can enhance your brand image.
Step 5: Request Samples for Evaluation
Always request product samples before making a bulk purchase. Evaluating samples allows you to assess the quality and suitability of the glass containers for your specific application.
- Design Verification: Ensure the samples match your design specifications and expectations.
- Functionality Testing: Conduct tests to evaluate the durability and performance of the samples under real-world conditions.
Step 6: Negotiate Terms and Pricing
Once you have identified a suitable supplier, engage in negotiations regarding pricing, payment terms, and delivery schedules.
- Volume Discounts: Discuss pricing based on your order volume, as many manufacturers offer discounts for larger orders.
- Payment Security: Ensure that payment terms are secure, favoring both parties, to mitigate risks associated with international transactions.
Step 7: Establish Clear Communication Channels
Effective communication is vital throughout the sourcing process. Establish clear channels of communication with your chosen supplier to facilitate smooth interactions.
- Point of Contact: Designate a specific person from both sides for regular updates and issue resolution.
- Regular Updates: Schedule regular check-ins to monitor progress and address any concerns promptly.
By following this checklist, B2B buyers can confidently navigate the sourcing process for glass containers, ensuring they partner with a reliable manufacturer that meets their unique requirements.
Comprehensive Cost and Pricing Analysis for glass container manufacturer Sourcing
What Are the Key Cost Components in Glass Container Manufacturing?
Understanding the cost structure of glass container manufacturing is crucial for international B2B buyers. The primary components that influence the overall pricing include:
-
Materials: The cost of raw materials, such as silica sand, soda ash, and limestone, significantly impacts pricing. Fluctuations in global commodity prices can lead to variations in costs, so buyers should consider sourcing agreements or long-term contracts to mitigate risks.
-
Labor: Labor costs vary significantly by region. In countries with lower labor costs, like some parts of Africa and South America, you may find more competitive pricing. However, it’s essential to ensure that labor standards and quality are not compromised.
-
Manufacturing Overhead: This includes costs related to utilities, equipment maintenance, and facility operations. Efficient manufacturing processes can help reduce these overheads, which can be beneficial when negotiating prices.
-
Tooling: The initial investment in molds and tooling can be substantial. Custom designs may require additional tooling costs, which should be factored into the total pricing.
-
Quality Control (QC): Ensuring that products meet international quality standards often involves additional costs for QC processes. Certifications such as ISO or specific industry-related standards can also add to the overall price.
-
Logistics: Shipping costs depend on the distance, mode of transport, and volume. For international buyers, understanding Incoterms can help clarify who is responsible for shipping and insurance costs.
-
Margin: Manufacturers typically apply a margin based on their operational costs and market conditions. Understanding the market landscape can provide leverage during negotiations.
How Do Price Influencers Affect Glass Container Sourcing?
Several factors can influence pricing dynamics in glass container sourcing:
-
Volume and Minimum Order Quantity (MOQ): Higher order volumes often result in lower per-unit costs. Buyers should assess their demand forecasts and negotiate MOQs that align with their business needs.
-
Specifications and Customization: Customized products may incur additional costs. Buyers should clarify their specifications upfront to avoid unexpected charges later in the process.
-
Material Quality and Certifications: Higher quality materials and certifications can lead to increased costs. However, investing in quality can reduce waste and improve customer satisfaction in the long run.
-
Supplier Factors: The supplier’s reputation, reliability, and location can all influence pricing. It’s advisable to conduct thorough due diligence to ensure that suppliers can meet both quality and delivery expectations.
-
Incoterms: Understanding the implications of various Incoterms can affect overall costs. Buyers should negotiate terms that minimize risks and clarify responsibilities for shipping, insurance, and tariffs.
What Buyer Tips Can Enhance Cost-Efficiency in Glass Container Sourcing?
For international B2B buyers, particularly from regions like Africa, South America, the Middle East, and Europe, several strategic tips can enhance cost-efficiency:
-
Negotiate Effectively: Don’t hesitate to negotiate pricing, especially when placing large orders. A well-prepared buyer can leverage market knowledge to negotiate better terms.
-
Consider Total Cost of Ownership (TCO): Look beyond the initial purchase price. TCO includes shipping, handling, storage, and potential disposal costs. Assessing TCO can lead to better long-term decisions.
-
Stay Informed About Pricing Nuances: Global market conditions can change rapidly, affecting the cost of raw materials and logistics. Staying updated on these factors can provide a competitive edge in negotiations.
-
Build Long-term Relationships with Suppliers: Establishing strong relationships can lead to better pricing and terms. Suppliers may be more willing to offer discounts or favorable terms to loyal customers.
-
Leverage Technology: Use supply chain management tools and platforms to streamline sourcing processes. These technologies can help track costs, manage inventory, and improve communication with suppliers.
Disclaimer on Pricing
Prices for glass container manufacturing can vary widely based on numerous factors, including geographic location, market conditions, and specific customer requirements. It is advisable for buyers to conduct their own research and obtain multiple quotes to get a clearer picture of current pricing trends and options.
Alternatives Analysis: Comparing glass container manufacturer With Other Solutions
In the competitive landscape of packaging solutions, international B2B buyers must evaluate various alternatives to glass container manufacturers. Each option presents unique advantages and drawbacks that can impact overall business performance. Understanding these alternatives allows buyers to make informed decisions tailored to their specific needs.
Comparison Aspect | Glass Container Manufacturer | Plastic Container Manufacturer | Metal Container Manufacturer |
---|---|---|---|
Performance | High durability, preserves product quality, recyclable | Lightweight, versatile, but less durable | Excellent for high-pressure contents, recyclable but heavier |
Cost | Generally higher initial investment | Lower initial cost, but potential long-term environmental costs | Moderate initial investment, often reusable |
Ease of Implementation | Requires specialized handling and logistics | Easy to produce and distribute | Moderate complexity in manufacturing and handling |
Maintenance | Minimal, but requires careful handling to avoid breakage | Low maintenance, easy to clean and reuse | Moderate; may require coating to prevent corrosion |
Best Use Case | Ideal for beverages, pharmaceuticals, and premium products | Suitable for a wide range of products, especially consumables | Best for food preservation and industrial applications |
What Are the Pros and Cons of Using Plastic Containers?
Plastic container manufacturers offer lightweight and versatile solutions that are often more cost-effective than glass. Their lower initial costs make them an attractive option for companies looking to minimize expenses. However, the environmental implications of plastic waste and potential leaching of chemicals into products can deter some buyers. Additionally, while plastic containers are generally easy to handle and distribute, they do not provide the same level of product protection as glass.
How Do Metal Containers Compare in Terms of Performance?
Metal container manufacturers produce robust options that excel in high-pressure environments, making them suitable for carbonated beverages and certain industrial applications. Their durability is a significant advantage, and they can often be reused, adding to their sustainability credentials. However, they can be heavier and may require additional coatings to prevent corrosion. The initial investment for metal containers is moderate, making them a viable option for specific use cases, though they might not be as cost-effective for all product types.
How Can B2B Buyers Choose the Right Solution for Their Needs?
When selecting the right packaging solution, B2B buyers should consider several factors, including the nature of the product, target market, and long-term sustainability goals. For products requiring preservation and premium branding, glass containers are often the best choice despite their higher costs. Conversely, for products where weight and cost are more critical, plastic containers may provide a better fit. Metal containers serve well in high-pressure scenarios but may not suit all consumer preferences. Ultimately, aligning the packaging choice with the overall business strategy will ensure that buyers make the most suitable decision for their operational needs.
Essential Technical Properties and Trade Terminology for glass container manufacturer
What Are the Key Technical Properties of Glass Containers?
Understanding the essential technical properties of glass containers is crucial for international B2B buyers. These properties can significantly influence product quality, safety, and compliance with regulations. Here are some critical specifications:
1. Material Grade
The material grade of glass containers, often categorized as soda-lime, borosilicate, or lead glass, determines the container’s durability, thermal resistance, and chemical stability. For example, borosilicate glass is favored in laboratories and pharmaceuticals due to its high thermal resistance. Buyers must select the appropriate material grade based on the intended use of the container, ensuring it meets industry standards and regulations.
2. Tolerance
Tolerance refers to the permissible limits of variation in dimensions, such as thickness and diameter. In glass manufacturing, tight tolerances are crucial for ensuring the containers fit machinery or packaging systems precisely. For instance, a tolerance of ±0.5mm may be acceptable for certain applications, while others may require stricter limits. Understanding tolerances helps buyers ensure compatibility with their production processes and reduces the risk of defects.
3. Capacity
Capacity indicates the volume that a glass container can hold, typically measured in milliliters or liters. This property is vital for buyers in sectors such as food and beverage, pharmaceuticals, and cosmetics, where precise volumes are essential for product formulation and packaging. Buyers should evaluate the required capacity based on market demand and regulatory guidelines, ensuring that their supply meets consumer needs.
4. Chemical Resistance
Chemical resistance is the ability of glass to withstand exposure to various substances without degrading. This property is particularly important for containers used in the pharmaceutical and chemical industries. Buyers must verify that the glass type is compatible with the substances they plan to store, as incompatible materials can lead to contamination or product failure.
5. Thermal Shock Resistance
Thermal shock resistance measures a material’s ability to withstand sudden temperature changes without breaking. This property is crucial for glass containers used in applications where rapid temperature fluctuations occur, such as in the food and beverage industry. Buyers should ensure that their chosen glass meets the thermal shock resistance standards necessary for their specific application.
What Are Common Trade Terms in the Glass Container Industry?
Familiarity with industry jargon can help B2B buyers navigate the complexities of sourcing and procurement. Here are some common trade terms:
1. OEM (Original Equipment Manufacturer)
OEM refers to a company that produces parts or equipment that may be marketed by another manufacturer. In the glass container industry, an OEM might produce containers that are then branded and sold by a different company. Understanding OEM relationships can help buyers identify reliable suppliers and negotiate better terms.
2. MOQ (Minimum Order Quantity)
MOQ is the smallest quantity of a product that a supplier is willing to sell. For glass containers, MOQs can vary significantly based on the manufacturer and the complexity of the order. Buyers should be aware of MOQs to manage inventory effectively and ensure that their orders align with production schedules.
3. RFQ (Request for Quotation)
An RFQ is a document used to solicit price quotes from suppliers for specific products or services. In the context of glass containers, submitting an RFQ allows buyers to compare prices, lead times, and terms from multiple manufacturers, enabling informed purchasing decisions.
4. Incoterms (International Commercial Terms)
Incoterms are a set of predefined international trade terms that define the responsibilities of buyers and sellers in the shipping process. Understanding Incoterms, such as FOB (Free on Board) or CIF (Cost, Insurance, and Freight), is essential for B2B buyers to clarify shipping costs, risk transfer, and insurance responsibilities when importing glass containers.
5. Lead Time
Lead time refers to the amount of time it takes for a supplier to fulfill an order after it has been placed. For glass containers, lead times can vary based on manufacturing processes and order complexity. Buyers should factor in lead times when planning their production schedules to avoid delays and ensure timely delivery to customers.
By understanding these technical properties and trade terms, international B2B buyers can make informed decisions, optimize their procurement processes, and establish strong supplier relationships in the glass container industry.
Navigating Market Dynamics and Sourcing Trends in the glass container manufacturer Sector
What Are the Current Market Dynamics and Key Trends in the Glass Container Manufacturing Sector?
The glass container manufacturing sector is experiencing significant growth, driven by increasing consumer demand for sustainable packaging solutions and a shift towards eco-friendly materials across various industries. As international B2B buyers, particularly from Africa, South America, the Middle East, and Europe, evaluate sourcing strategies, understanding these dynamics is crucial.
One of the most prominent trends is the rising emphasis on lightweight glass packaging, which not only reduces shipping costs but also minimizes energy consumption during production. Additionally, advancements in production technologies, such as automated manufacturing processes and smart logistics, are enhancing efficiency and reducing lead times. These innovations are particularly beneficial for buyers in emerging markets like Brazil and Turkey, where operational costs can significantly impact profit margins.
Moreover, the growing popularity of artisanal and premium products is pushing manufacturers to offer customized glass containers. This trend presents an opportunity for B2B buyers to differentiate their offerings in competitive markets. As consumer preferences evolve, buyers must stay informed about the latest design trends and functionalities that appeal to end-users, such as convenience and reusability.
How Can Sustainability and Ethical Sourcing Impact Your B2B Sourcing Strategy?
Sustainability has become a pivotal factor in the glass container manufacturing sector. The environmental impact of glass production, which involves high energy consumption and significant CO2 emissions, has led to an increased demand for sustainable practices. For international B2B buyers, this translates into a need to prioritize suppliers that adhere to ethical sourcing standards and demonstrate a commitment to reducing their environmental footprint.
Buyers should look for manufacturers that utilize recycled materials in their production processes, as this not only lessens the demand for virgin materials but also minimizes waste. Certifications such as ISO 14001 for environmental management and the Forest Stewardship Council (FSC) certification for sustainable sourcing can serve as indicators of a supplier’s commitment to sustainability.
Furthermore, engaging with suppliers who invest in renewable energy and eco-efficient technologies can enhance your supply chain’s sustainability profile. The increasing consumer preference for environmentally friendly products means that aligning your sourcing strategy with these values can also enhance brand reputation and customer loyalty.
How Has the Glass Container Manufacturing Sector Evolved Over Time?
The glass container manufacturing sector has a rich history that dates back thousands of years, evolving significantly with advancements in technology and changes in consumer behavior. Initially, glass containers were handcrafted and limited in production, making them a luxury item. However, the Industrial Revolution brought about mechanization, leading to mass production and wider accessibility.
In the latter half of the 20th century, the focus shifted toward efficiency and cost-effectiveness, with manufacturers adopting innovative techniques and materials. Today, the sector is witnessing a renaissance driven by sustainability and consumer demand for quality packaging. This evolution underscores the importance of staying informed about market trends and technological advancements, enabling B2B buyers to make strategic sourcing decisions that align with current and future market dynamics.
Understanding these historical shifts can provide valuable insights into the current landscape, helping buyers navigate the complexities of sourcing glass containers that meet both quality and sustainability standards.
Frequently Asked Questions (FAQs) for B2B Buyers of glass container manufacturer
-
How do I choose the right glass container manufacturer for my business needs?
Selecting the right glass container manufacturer involves evaluating several factors. First, assess the manufacturer’s experience and expertise in producing the specific type of glass containers you require. Look for certifications that indicate quality assurance, such as ISO standards. Additionally, consider their ability to customize products to meet your specifications. Reviewing customer testimonials and case studies can provide insight into their reliability and service quality. Finally, initiate communication to gauge their responsiveness and willingness to collaborate on your projects. -
What are the minimum order quantities (MOQ) for glass containers from manufacturers?
Minimum order quantities can vary significantly between manufacturers and depend on factors like product type and customization. Typically, MOQs for standard glass containers may range from 1,000 to 10,000 units. For custom designs, manufacturers might require higher MOQs due to the additional costs involved in production setup. It’s essential to discuss your needs upfront with potential suppliers to understand their MOQ policies and negotiate if necessary, especially if you are a smaller business or just starting. -
What payment terms should I expect when sourcing glass containers internationally?
Payment terms for international transactions can differ widely based on the manufacturer and the countries involved. Common practices include upfront deposits (usually 30-50%) with the balance due upon completion or before shipping. Some manufacturers may offer flexible payment options, such as letters of credit or payment through escrow services. Always clarify payment terms and conditions before finalizing your order to avoid misunderstandings and ensure compliance with international trade regulations. -
How can I ensure the quality of glass containers from overseas manufacturers?
To ensure quality, first, confirm that the manufacturer adheres to international quality standards, such as ISO or ASTM certifications. Request samples of the glass containers before placing a bulk order to evaluate their quality and suitability. Additionally, consider conducting third-party inspections during production or before shipment. Regular communication with the manufacturer throughout the production process can also help address any concerns promptly. -
What are the shipping and logistics considerations for importing glass containers?
When importing glass containers, consider factors like shipping methods, costs, and lead times. Glass is fragile, so it’s crucial to choose a manufacturer experienced in packaging and shipping glass products securely. Determine whether you will handle logistics or if the manufacturer offers freight services. Familiarize yourself with import regulations in your country, including tariffs and customs duties. It’s advisable to work with a reliable freight forwarder to navigate these complexities effectively. -
How do I vet a glass container supplier for reliability and trustworthiness?
Vetting a supplier starts with researching their background, including years in business and industry reputation. Look for reviews and feedback from other clients, preferably within your industry. Request references and follow up with them to gain insights into their experiences. Additionally, consider visiting the manufacturing facility if possible, or arrange a virtual tour to assess their operations. Engaging in discussions about their processes and capabilities can also reveal their professionalism and commitment to quality. -
What customization options are available for glass containers?
Many glass container manufacturers offer a range of customization options, including size, shape, color, and printing. You can often choose from existing molds or request a completely custom design. Discuss your branding needs, such as labeling and logo printing, as these can enhance product visibility. Be prepared to provide detailed specifications and possibly collaborate on design prototypes to ensure the final product meets your expectations. -
What are the common uses of glass containers in various industries?
Glass containers are versatile and used across numerous industries, including food and beverage, cosmetics, pharmaceuticals, and chemicals. In the food industry, they are favored for packaging sauces, jams, and beverages due to their non-reactive nature. In cosmetics, glass containers are used for creams and perfumes, providing an upscale appearance. Understanding the specific requirements of your industry can help you choose the right type of glass container that meets regulatory standards and consumer preferences.
Important Disclaimer & Terms of Use
⚠️ Important Disclaimer
The information provided in this guide, including content regarding manufacturers, technical specifications, and market analysis, is for informational and educational purposes only. It does not constitute professional procurement advice, financial advice, or legal advice.
While we have made every effort to ensure the accuracy and timeliness of the information, we are not responsible for any errors, omissions, or outdated information. Market conditions, company details, and technical standards are subject to change.
B2B buyers must conduct their own independent and thorough due diligence before making any purchasing decisions. This includes contacting suppliers directly, verifying certifications, requesting samples, and seeking professional consultation. The risk of relying on any information in this guide is borne solely by the reader.
Strategic Sourcing Conclusion and Outlook for glass container manufacturer
What Are the Key Takeaways for B2B Buyers in the Glass Container Industry?
In the increasingly competitive landscape of glass container manufacturing, strategic sourcing emerges as a vital element for international B2B buyers. By prioritizing supplier relationships, buyers can ensure consistent quality and innovation, which are crucial for maintaining brand reputation and customer satisfaction. Understanding regional dynamics, such as the growing demand in Africa and South America, allows businesses to align their sourcing strategies with market needs, ensuring resilience and adaptability.
How Can Strategic Sourcing Drive Value for International Buyers?
Investing in strategic sourcing not only streamlines procurement processes but also fosters sustainable practices that resonate with environmentally conscious consumers. By leveraging local suppliers in the Middle East and Europe, businesses can reduce transportation costs and carbon footprints, contributing to a more sustainable supply chain. Additionally, this approach opens doors for collaboration on product development, enhancing the competitive edge in various markets.
What is the Future Outlook for Glass Container Manufacturers?
Looking ahead, the glass container industry is poised for growth, driven by increasing consumer preference for sustainable packaging solutions. International B2B buyers should remain proactive, exploring partnerships that align with their strategic goals. As markets evolve, those who embrace innovative sourcing strategies will not only meet current demands but also anticipate future trends. Engage with suppliers who share your vision for sustainability and quality, and together, you can shape the future of the glass container market.