Discover Top Benefits of Sourcing a Bus Bar Manufacturer (2025)
Introduction: Navigating the Global Market for bus bar manufacturer
In today’s interconnected world, sourcing reliable bus bar manufacturers is a critical challenge for international B2B buyers, especially those in regions like Africa, South America, the Middle East, and Europe. With the increasing demand for efficient power distribution solutions, understanding the nuances of bus bar applications and specifications becomes essential. This guide aims to equip you with the necessary insights to navigate the global market effectively, covering diverse types of bus bars, their applications across various industries, and strategies for vetting potential suppliers.
As an international buyer, you may face hurdles in identifying reputable manufacturers that meet your specific requirements. This guide will provide you with a comprehensive overview of the factors to consider when selecting bus bar suppliers, including quality standards, certification processes, and pricing structures. We will also delve into the logistical aspects of sourcing, such as shipping considerations and import regulations that may impact your purchasing decisions.
By empowering you with this knowledge, we aim to facilitate informed purchasing decisions that enhance your operational efficiency and project success. Whether you are in South Africa looking for robust solutions or in Italy seeking innovative designs, this guide will serve as a valuable resource to help you confidently navigate the complexities of the global bus bar market.
Understanding bus bar manufacturer Types and Variations
Type Name | Key Distinguishing Features | Primary B2B Applications | Brief Pros & Cons for Buyers |
---|---|---|---|
Copper Bus Bars | High conductivity, corrosion resistance, and durability | Power distribution, industrial plants | Pros: Excellent conductivity; Cons: Higher cost than aluminum. |
Aluminum Bus Bars | Lightweight, cost-effective, and good conductivity | Renewable energy systems, commercial buildings | Pros: Lower weight and cost; Cons: Less conductive than copper. |
Insulated Bus Bars | Coated with insulation for safety and reduced short-circuit risk | Data centers, commercial buildings | Pros: Enhanced safety; Cons: May require higher initial investment. |
Flexible Bus Bars | Adaptable design for complex layouts and installations | Mobile applications, temporary setups | Pros: Easy installation; Cons: May have lower current capacity. |
Bus Bar Assemblies | Pre-assembled units for ease of installation and maintenance | Electrical panels, switchgear | Pros: Reduced installation time; Cons: Less customization available. |
What are the Characteristics of Copper Bus Bars for B2B Buyers?
Copper bus bars are renowned for their exceptional electrical conductivity and resistance to corrosion, making them ideal for high-load applications. Typically used in power distribution systems and industrial plants, these bus bars provide reliable performance in demanding environments. When considering copper bus bars, buyers should weigh their higher cost against long-term durability and efficiency, especially in critical applications where performance is paramount.
How Do Aluminum Bus Bars Compare for International B2B Buyers?
Aluminum bus bars are a popular choice due to their lightweight nature and cost-effectiveness. They are commonly found in renewable energy systems and commercial buildings, where reduced weight can lead to easier handling and installation. While they offer good conductivity, it is essential for buyers to consider that aluminum has lower conductivity compared to copper. This means that for high-current applications, larger cross-sections may be necessary, which can offset some cost advantages.
Why Choose Insulated Bus Bars for Safety in B2B Applications?
Insulated bus bars are designed with a protective coating that enhances safety and minimizes the risk of short circuits. These features make them particularly suitable for data centers and commercial buildings where operational safety is critical. While they may require a higher initial investment, the long-term benefits in terms of safety and reduced maintenance costs can be significant, making them a wise choice for B2B buyers concerned about operational risks.
What Advantages Do Flexible Bus Bars Offer for Complex Installations?
Flexible bus bars provide an adaptable solution for complex electrical layouts, making them ideal for mobile applications and temporary setups. Their design allows for easy installation and reconfiguration, which is beneficial in dynamic environments. However, buyers should note that flexible bus bars may have a lower current capacity compared to rigid alternatives, which could limit their use in high-power applications.
How Do Bus Bar Assemblies Simplify Installation for B2B Buyers?
Bus bar assemblies are pre-assembled units that facilitate quicker installation and maintenance, making them a practical choice for electrical panels and switchgear. These assemblies help reduce labor costs and installation time, which is critical for large projects. However, buyers should consider that the standardization of these assemblies may limit customization options, potentially impacting specific project requirements.
Related Video: What is a Bus Coupler? What are the Steps to Operate | Explained | TheElectricalGuy
Key Industrial Applications of bus bar manufacturer
Industry/Sector | Specific Application of bus bar manufacturer | Value/Benefit for the Business | Key Sourcing Considerations for this Application |
---|---|---|---|
Power Generation | Electrical distribution in substations | Enhanced reliability and efficiency in energy distribution | Compliance with regional standards and certifications |
Renewable Energy | Solar power systems | Improved energy transfer efficiency and reduced losses | Material quality for durability in harsh environments |
Transportation & Infrastructure | Rail and metro systems | Increased safety and reduced maintenance costs | Customization for specific voltage and current ratings |
Manufacturing | Automation systems | Streamlined operations and reduced downtime | Compatibility with existing systems and equipment |
Data Centers | Power management in data centers | Optimized power usage and enhanced cooling efficiency | Scalability and modular design for future expansion |
How are Bus Bars Used in Power Generation and What Benefits Do They Provide?
In the power generation sector, bus bars are essential for electrical distribution within substations. They facilitate the transfer of electricity from generators to transformers and distribution lines, ensuring a reliable power supply. For international B2B buyers, especially in regions like Africa and South America where infrastructure may be developing, sourcing high-quality bus bars that comply with local regulations is critical. This ensures safety and reliability, ultimately benefiting businesses through reduced downtime and maintenance costs.
What Role Do Bus Bars Play in Renewable Energy Systems?
Bus bars are integral to solar power systems, connecting solar panels to inverters and ensuring efficient energy transfer. They minimize energy losses, which is crucial for maximizing the return on investment in renewable energy projects. Buyers from the Middle East, where solar energy is rapidly expanding, need to prioritize sourcing bus bars that can withstand extreme weather conditions. This durability translates into long-term savings and enhanced system performance.
How Are Bus Bars Utilized in Transportation and Infrastructure Projects?
In transportation, particularly in rail and metro systems, bus bars are used for power distribution to trains and signaling systems. They ensure a consistent power supply, which is vital for safety and operational efficiency. For European buyers, understanding the specific voltage and current requirements of their systems is essential when sourcing bus bars. Customization options can lead to significant reductions in maintenance costs and improved safety standards.
What Benefits Do Bus Bars Offer in Manufacturing Automation?
Manufacturing industries rely on bus bars for their automation systems to facilitate efficient power distribution to machinery and equipment. By optimizing power delivery, bus bars help streamline operations and reduce downtime, which is crucial for maintaining productivity. Buyers should consider compatibility with existing systems when sourcing bus bars, ensuring that they can seamlessly integrate into their operations without requiring extensive modifications.
Why Are Bus Bars Important for Data Centers?
In data centers, bus bars manage power distribution, ensuring that servers receive a stable and efficient power supply. This is vital for reducing energy consumption and enhancing cooling efficiency, which can significantly lower operational costs. International B2B buyers must focus on sourcing scalable bus bar solutions that can adapt to future expansion needs, ensuring that their data centers remain competitive and efficient in a rapidly evolving technological landscape.
Related Video: Uses and Gratifications Theory – UGT
3 Common User Pain Points for ‘bus bar manufacturer’ & Their Solutions
Scenario 1: Ensuring Quality and Compliance in Bus Bar Manufacturing
The Problem:
B2B buyers often face significant challenges in ensuring that bus bars meet stringent quality and compliance standards. For companies operating in regions like Africa and the Middle East, where regulatory frameworks can vary dramatically, the risk of sourcing substandard products increases. This can lead to costly project delays, safety hazards, and potential legal repercussions if the bus bars do not comply with local and international standards.
The Solution:
To mitigate these risks, buyers should conduct thorough due diligence when selecting a bus bar manufacturer. Start by verifying the manufacturer’s certifications and compliance with relevant industry standards such as IEC, UL, and ISO. It’s beneficial to request documentation that proves their adherence to quality control processes. Additionally, establishing a direct line of communication with the manufacturer can facilitate transparency regarding production practices and materials used. Consider conducting site visits if feasible, or request third-party audits to gain further assurance of product quality. Engaging with suppliers who have a proven track record in your specific region can also help navigate local compliance issues effectively.
Scenario 2: Navigating Supply Chain Disruptions in Bus Bar Procurement
The Problem:
Supply chain disruptions can severely impact the availability of bus bars, particularly for international buyers in regions like South America and Europe. Factors such as geopolitical tensions, natural disasters, or logistics failures can delay shipments, leading to project stagnation and increased costs. This unpredictability in lead times can frustrate project timelines and affect overall operational efficiency.
The Solution:
To combat supply chain challenges, buyers should implement a multi-sourcing strategy. This involves identifying several qualified manufacturers across different geographic locations to diversify supply risk. When negotiating contracts, consider including clauses that address supply chain disruptions, such as penalties for delays or guarantees of expedited shipping in case of unforeseen circumstances. Additionally, leveraging technology such as supply chain management software can help track orders in real-time and provide alerts on potential delays. Building strong relationships with logistics providers can also enhance your ability to adapt to changes and find alternative shipping methods when necessary.
Scenario 3: Customization Challenges in Bus Bar Specifications
The Problem:
Many B2B buyers encounter difficulties when seeking custom bus bar solutions tailored to specific project requirements. This is particularly true in industries like renewable energy and heavy manufacturing, where unique specifications are often essential. The challenge lies in effectively communicating these requirements to the manufacturer and ensuring they can deliver the desired product without compromising quality or performance.
The Solution:
To address customization challenges, it is crucial to engage in collaborative design discussions with potential bus bar manufacturers early in the procurement process. Provide detailed specifications, including dimensions, materials, and performance criteria, while being open to suggestions based on the manufacturer’s expertise. Utilizing 3D modeling or simulation tools can help visualize the final product and allow for adjustments before production begins. Additionally, consider manufacturers who offer prototyping services, enabling you to test and validate the design before committing to large-scale production. Establishing a clear feedback loop during the manufacturing process can also ensure that any issues are identified and resolved promptly, leading to a successful outcome.
Strategic Material Selection Guide for bus bar manufacturer
When selecting materials for bus bars, manufacturers must consider various factors that affect performance, cost, and compliance with international standards. Below, we analyze four common materials used in bus bar manufacturing, highlighting their properties, advantages, disadvantages, and specific considerations for international B2B buyers, particularly from regions such as Africa, South America, the Middle East, and Europe.
What are the Key Properties of Copper for Bus Bars?
Copper is the most widely used material for bus bars due to its excellent electrical conductivity, thermal conductivity, and ductility. It typically has a temperature rating of up to 200°C and exhibits good corrosion resistance in most environments. The high conductivity of copper allows for efficient energy transmission, making it ideal for high-load applications.
Pros and Cons of Using Copper
The primary advantage of copper bus bars is their superior performance in electrical applications, which translates to lower energy losses. However, copper is relatively expensive compared to other materials, which can impact overall project costs. Additionally, its weight can be a concern in applications where weight reduction is critical.
Impact on Application
Copper bus bars are compatible with various media, including air and oil, and are often used in power distribution systems, transformers, and switchgear.
Considerations for International Buyers
Buyers should ensure compliance with international standards such as ASTM B187 for copper bus bars. In regions like South Africa and Italy, local regulations may also dictate specific material grades and testing requirements.
How Does Aluminum Compare as a Bus Bar Material?
Aluminum is another popular choice for bus bars, particularly in applications where weight is a critical factor. It has a lower density than copper and is typically rated for temperatures up to 150°C. Aluminum also offers decent electrical conductivity, approximately 60% that of copper.
Pros and Cons of Using Aluminum
The key advantage of aluminum is its cost-effectiveness and lightweight nature, which makes it easier to handle and install. However, aluminum’s lower conductivity means that larger cross-sectional areas are required to achieve the same performance as copper, potentially increasing material costs. Additionally, aluminum is more prone to corrosion, requiring protective coatings in certain environments.
Impact on Application
Aluminum bus bars are suitable for indoor applications and environments with low humidity. They are commonly used in residential and commercial electrical systems.
Considerations for International Buyers
International buyers should verify compliance with standards such as ASTM B221. In regions like South America, where humidity can be high, additional corrosion resistance measures may be necessary.
What are the Advantages of Using Stainless Steel for Bus Bars?
Stainless steel is known for its excellent corrosion resistance and mechanical strength, making it suitable for harsh environments. It typically has a temperature rating of up to 300°C, which allows for use in high-temperature applications.
Pros and Cons of Using Stainless Steel
The primary advantage of stainless steel is its durability and resistance to oxidation, making it ideal for outdoor or corrosive environments. However, stainless steel has lower electrical conductivity compared to copper and aluminum, which can lead to higher energy losses. It is also more expensive and complex to manufacture.
Impact on Application
Stainless steel bus bars are often used in industrial applications, including chemical processing and marine environments, where corrosion resistance is crucial.
Considerations for International Buyers
Buyers should ensure that the stainless steel used complies with standards such as ASTM A276. In Europe, EN standards may also apply, and buyers should be aware of local sourcing options to minimize costs.
When Should You Consider Using Brass for Bus Bars?
Brass, an alloy of copper and zinc, is sometimes used for bus bars due to its good electrical conductivity and corrosion resistance. It typically has a temperature rating of up to 200°C.
Pros and Cons of Using Brass
Brass offers a balance between cost and performance, making it a viable option for applications where copper is too expensive. However, brass is less conductive than pure copper, which can impact efficiency. Additionally, its mechanical properties may not be as robust as those of stainless steel.
Impact on Application
Brass bus bars are suitable for low to medium voltage applications and are often used in electronic devices and connectors.
Considerations for International Buyers
International buyers should check compliance with ASTM B16 for brass materials. In regions like the Middle East, where environmental conditions can be harsh, additional protective measures may be necessary.
Summary Table of Material Selection for Bus Bars
Material | Typical Use Case for Bus Bar Manufacturer | Key Advantage | Key Disadvantage/Limitation | Relative Cost (Low/Med/High) |
---|---|---|---|---|
Copper | Power distribution systems | Superior electrical conductivity | High cost and weight | High |
Aluminum | Residential/commercial electrical systems | Lightweight and cost-effective | Lower conductivity and corrosion-prone | Medium |
Stainless Steel | Industrial applications | Excellent corrosion resistance | Lower conductivity and higher cost | High |
Brass | Electronic devices | Good balance of cost and performance | Less conductive than copper | Medium |
This analysis provides a comprehensive overview of the materials commonly used in bus bar manufacturing, equipping international B2B buyers with the insights needed to make informed decisions based on their specific application requirements and regional considerations.
In-depth Look: Manufacturing Processes and Quality Assurance for bus bar manufacturer
What Are the Main Stages in the Manufacturing Process of Bus Bars?
Manufacturing bus bars involves several critical stages that ensure the final product meets both performance and quality standards. Understanding these stages can help B2B buyers make informed decisions when selecting suppliers.
Material Preparation: What Materials Are Used in Bus Bar Manufacturing?
The first step in the manufacturing process is material preparation. Bus bars are typically made from high-conductivity materials such as copper or aluminum. The choice of material affects the bus bar’s electrical performance and physical properties.
-
Selection of Materials: Suppliers should provide detailed specifications of the materials used, including conductivity levels and alloy compositions. Buyers should prioritize manufacturers who source materials from reputable suppliers to ensure quality.
-
Cutting and Shaping: Once the materials are selected, they are cut to size using precision tools. This step often involves the use of laser cutting or CNC (Computer Numerical Control) machines to ensure accuracy.
How Are Bus Bars Formed and Assembled?
The forming and assembly stages are crucial for ensuring that bus bars meet design specifications and functional requirements.
Forming Techniques: What Methods Are Used to Shape Bus Bars?
Bus bars are typically formed using several techniques, including:
- Bending: This process shapes the bus bars to fit specific installation requirements. Automated bending machines are commonly used for high-volume production.
- Stamping: This technique is used for creating complex shapes and features in the bus bars, enhancing their functionality and fit.
- Extrusion: For aluminum bus bars, extrusion is a common method where material is forced through a die to create a specific cross-sectional shape.
Each of these methods should be performed with precision to maintain the integrity of the material and ensure optimal electrical performance.
Assembly: How Are Bus Bars Assembled with Other Components?
After forming, bus bars are assembled, which may involve:
- Welding: This technique is often used to join bus bars to other electrical components, ensuring a robust connection.
- Screwing and Bolting: Mechanical fasteners may also be used, especially in modular systems where components can be easily replaced or adjusted.
Quality control during assembly is vital. Each connection should be tested for electrical continuity and mechanical strength.
What Finishing Processes Are Essential for Bus Bars?
Finishing processes enhance the durability and performance of bus bars.
Surface Treatment: What Are Common Surface Treatments for Bus Bars?
Surface treatments are critical for preventing corrosion and enhancing conductivity. Common methods include:
- Electroplating: Applying a thin layer of metal (e.g., tin) to improve corrosion resistance.
- Anodizing: Particularly for aluminum bus bars, anodizing increases surface hardness and corrosion resistance.
These treatments should be performed according to industry standards to ensure long-lasting performance.
How Is Quality Assurance Implemented in Bus Bar Manufacturing?
Quality assurance (QA) is a cornerstone of bus bar manufacturing, ensuring that the final products meet international standards and customer expectations.
What International Standards Should B2B Buyers Be Aware Of?
International quality standards such as ISO 9001 play a significant role in the manufacturing process. This standard outlines requirements for a quality management system, helping manufacturers consistently provide products that meet customer and regulatory requirements.
Additionally, industry-specific standards such as CE marking for European markets and API standards for oil and gas applications may apply, depending on the intended use of the bus bars.
What Are the Key Quality Control Checkpoints in Bus Bar Manufacturing?
Quality control involves several checkpoints throughout the manufacturing process:
-
Incoming Quality Control (IQC): This initial stage assesses the quality of raw materials upon delivery. Manufacturers should conduct tests to verify material specifications.
-
In-Process Quality Control (IPQC): During production, IPQC ensures that processes are followed correctly and that products meet specified standards. This can include monitoring equipment calibration and production methods.
-
Final Quality Control (FQC): Once the bus bars are completed, FQC checks the finished product against specifications. This may involve electrical testing, dimensional checks, and visual inspections.
How Can B2B Buyers Verify Supplier Quality Control Processes?
B2B buyers from regions such as Africa, South America, the Middle East, and Europe should take proactive steps to verify the quality control processes of potential suppliers.
What Audit Practices Should Buyers Consider?
-
Supplier Audits: Conducting on-site audits allows buyers to assess the supplier’s manufacturing processes and quality control measures firsthand. Key areas to evaluate include equipment maintenance, staff training, and compliance with quality standards.
-
Requesting Quality Reports: Buyers should request detailed quality reports, including testing results and certifications. These documents provide insights into the supplier’s QA practices.
-
Third-Party Inspections: Engaging independent third-party inspection services can provide an objective assessment of the supplier’s quality control processes and product quality.
What QC and Certification Nuances Should International Buyers Be Aware Of?
B2B buyers must understand that QC and certification requirements can vary significantly between regions. For instance, European buyers may prioritize CE certification, while buyers in the Middle East may focus on local standards.
How Do Regional Standards Affect Supplier Selection?
Buyers should familiarize themselves with the local regulations and standards in their respective markets. Understanding these nuances can help buyers select suppliers who are compliant and capable of delivering products that meet local requirements.
Conclusion
By understanding the intricacies of the manufacturing processes and quality assurance practices in bus bar production, B2B buyers can make informed decisions when selecting suppliers. Thorough evaluations of manufacturing capabilities, adherence to international standards, and robust quality control measures are essential to ensure the reliability and performance of bus bars in diverse applications.
Practical Sourcing Guide: A Step-by-Step Checklist for ‘bus bar manufacturer’
This guide serves as a comprehensive checklist for international B2B buyers looking to source bus bars effectively. By following these steps, you can ensure that you choose the right manufacturer that meets your technical requirements and business needs.
Step 1: Define Your Technical Specifications
Before initiating the sourcing process, clearly outline your technical requirements for bus bars. Consider factors such as dimensions, materials (e.g., copper, aluminum), and electrical specifications (current rating, voltage rating).
– Why it matters: Having precise specifications helps you communicate effectively with potential suppliers and ensures that the products meet your operational needs.
Step 2: Research the Market Landscape
Conduct thorough market research to identify leading bus bar manufacturers. Utilize industry reports, trade shows, and online platforms to gather insights on various suppliers’ reputations and capabilities.
– What to look for: Focus on manufacturers that specialize in your required specifications and have a proven track record in your region, especially from Africa, South America, the Middle East, and Europe.
Step 3: Evaluate Potential Suppliers
Before committing, it’s crucial to vet suppliers thoroughly. Request company profiles, case studies, and references from buyers in a similar industry or region.
– What to check: Look for customer testimonials and case studies that demonstrate the supplier’s experience and reliability. Ensure they have experience working with businesses similar to yours.
Step 4: Verify Supplier Certifications
Confirm that potential suppliers hold relevant industry certifications, such as ISO 9001 or IEC standards, which indicate adherence to quality management systems and safety standards.
– Importance: Certifications not only reflect the quality of the manufacturing process but also ensure compliance with international standards, which is essential for global transactions.
Step 5: Request Samples and Prototypes
Ask for product samples or prototypes to assess the quality and performance of the bus bars. This step allows you to conduct hands-on evaluations and tests under your specific operational conditions.
– What to evaluate: Check for physical quality, finish, and compatibility with your existing systems. Performing electrical tests can also verify the manufacturer’s claims regarding performance.
Step 6: Discuss Pricing and Payment Terms
Engage in discussions about pricing structures, payment terms, and shipping costs. Make sure to understand the total cost of ownership, including potential tariffs or duties if importing.
– Tips: Consider negotiating bulk pricing or long-term contracts, which can lead to cost savings. Additionally, clarify the payment options available to ensure they align with your financial processes.
Step 7: Establish Communication and Support Channels
Ensure that the supplier offers robust communication and after-sales support. This includes clarity on how to reach them for inquiries, technical assistance, or issues that may arise post-purchase.
– Why it’s essential: Reliable support can significantly reduce downtime and facilitate smoother operations, especially in complex projects where timely assistance is critical.
By following this structured checklist, international B2B buyers can make informed decisions when sourcing bus bar manufacturers, ultimately leading to successful partnerships and enhanced operational efficiency.
Comprehensive Cost and Pricing Analysis for bus bar manufacturer Sourcing
What Are the Key Cost Components in Bus Bar Manufacturing?
When sourcing bus bars, understanding the cost structure is vital for international B2B buyers. The primary cost components include:
-
Materials: The type and quality of materials used in bus bar production significantly impact costs. Copper and aluminum are the most common materials; however, variations in purity and sourcing can lead to price fluctuations. Buyers should consider long-term supplier relationships to secure better rates.
-
Labor: Labor costs vary by region and are influenced by local wage standards and workforce availability. In countries with lower labor costs, such as some regions in Africa and South America, manufacturers may offer competitive pricing. However, ensure that labor quality meets international standards.
-
Manufacturing Overhead: This includes expenses related to factory operations, utilities, and maintenance. Efficient manufacturing processes can reduce overhead, making it essential for buyers to inquire about a manufacturer’s operational efficiencies.
-
Tooling: The initial investment in tooling for custom bus bars can be substantial. Tooling costs should be factored into the total cost, especially for custom designs. Buyers may negotiate shared tooling costs for larger orders.
-
Quality Control (QC): Robust QC processes ensure that products meet industry standards and specifications. Investing in quality control can mitigate risks of defects, which may incur additional costs in the long run.
-
Logistics: Shipping costs depend on the distance from the manufacturer to the buyer and the chosen Incoterms. Buyers should evaluate logistics options to find a balance between cost and delivery speed.
-
Margin: Manufacturers typically mark up their prices to cover costs and achieve profit. Understanding the average margin in your target market can help in negotiations.
How Do Price Influencers Affect Bus Bar Costs?
Several factors can influence the pricing of bus bars, making it essential for buyers to be informed:
-
Volume/MOQ (Minimum Order Quantity): Larger orders often qualify for lower unit prices. Buyers should assess their needs and negotiate bulk purchasing to achieve cost savings.
-
Specifications and Customization: Custom designs or specific technical requirements can increase costs. Buyers should clearly communicate their needs to obtain accurate quotes and avoid unexpected expenses.
-
Material Quality and Certifications: Higher quality materials or those that meet specific certifications (e.g., ISO, UL) can command higher prices. Buyers must evaluate whether the additional costs align with their application requirements.
-
Supplier Factors: Reputation, reliability, and service levels of suppliers can influence pricing. Established suppliers may charge a premium due to their track record, but they often provide better support and quality assurance.
-
Incoterms: The choice of Incoterms (e.g., FOB, CIF) affects shipping costs and responsibilities. Buyers should understand the implications of their selected terms on the overall cost structure.
What Tips Can Help Buyers Optimize Costs?
International B2B buyers can implement several strategies to enhance cost-efficiency:
-
Negotiation Strategies: Prepare to negotiate prices by understanding market rates and being clear about your requirements. Building rapport with suppliers can also lead to better deals.
-
Evaluate Total Cost of Ownership (TCO): Consider not just the purchase price but also long-term costs such as maintenance, energy consumption, and potential downtime. This holistic view can uncover cost-saving opportunities.
-
Understand Pricing Nuances in Different Markets: Prices can vary significantly between regions like Africa, South America, the Middle East, and Europe. Familiarize yourself with regional market dynamics to make informed purchasing decisions.
-
Request Detailed Quotes: Ensure quotes include a breakdown of all cost components. This transparency helps in understanding pricing structures and identifying areas for negotiation.
-
Monitor Currency Fluctuations: Exchange rates can impact costs, especially for international purchases. Keeping an eye on currency trends can aid in timing purchases for optimal pricing.
Disclaimer on Indicative Prices
Prices for bus bars can fluctuate based on market conditions, material costs, and supplier pricing strategies. Buyers should seek current quotes and conduct thorough market research to validate costs before making purchasing decisions.
Alternatives Analysis: Comparing bus bar manufacturer With Other Solutions
When considering electrical distribution solutions in industrial applications, it’s crucial for B2B buyers to evaluate not only bus bars but also viable alternatives that can meet their operational needs. Understanding the comparative advantages and disadvantages of each option can significantly impact efficiency, cost management, and overall project success.
Comparison Aspect | Bus Bar Manufacturer | Alternative 1: Insulated Bus Ducts | Alternative 2: Cable Trays |
---|---|---|---|
Performance | High efficiency, low impedance; ideal for heavy loads | Moderate efficiency; suitable for medium loads | Variable efficiency; depends on cable type |
Cost | Higher initial investment but lower long-term costs | Moderate cost; additional installation complexity | Lower upfront cost; ongoing maintenance costs can accumulate |
Ease of Implementation | Requires skilled labor for installation | More complex installation; may require specialized training | Easier to install, especially for existing structures |
Maintenance | Low maintenance needs; durable | Moderate maintenance; inspections needed | High maintenance; cables may require frequent checks |
Best Use Case | High-load applications in industrial settings | Environments with space constraints and high electrical demands | General-purpose applications with standard power needs |
What Are Insulated Bus Ducts and Their Pros and Cons?
Insulated bus ducts are an alternative to traditional bus bars, designed to carry electrical power while minimizing space usage. These systems encapsulate bus bars in insulation, providing enhanced safety and flexibility in routing.
Pros:
– They can handle high electrical loads effectively while occupying less space.
– Insulation reduces the risk of electrical hazards, making them safer in crowded environments.
Cons:
– The installation process is more complex, requiring specialized knowledge and potentially longer installation times.
– While the initial costs are moderate, the need for regular inspections can lead to increased operational costs over time.
How Do Cable Trays Compare to Bus Bars?
Cable trays serve as a support structure for electrical cables, offering a more flexible and accessible solution. They are widely used in various industries for routing and organizing power and data cables.
Pros:
– The installation of cable trays is generally simpler and can be accomplished with less specialized labor.
– They provide easy access for maintenance and upgrades, making them suitable for dynamic environments where changes are frequent.
Cons:
– While initial costs are lower, the long-term maintenance associated with cable management can be higher.
– Cable trays can become cluttered, leading to potential inefficiencies in power distribution if not managed properly.
How Can B2B Buyers Choose the Right Solution for Their Needs?
In deciding between bus bars, insulated bus ducts, and cable trays, B2B buyers must first assess their specific operational requirements. For high-load industrial applications, bus bars typically offer the best efficiency and durability. However, if space is a constraint, insulated bus ducts might be the ideal choice, provided that the organization is prepared for the associated installation complexities. For more general applications or environments where flexibility and ease of access are paramount, cable trays could serve as a cost-effective solution.
Ultimately, thorough analysis of performance metrics, cost implications, and maintenance requirements will guide buyers in selecting the most appropriate electrical distribution method that aligns with their operational goals and budget constraints.
Essential Technical Properties and Trade Terminology for bus bar manufacturer
What Are the Essential Technical Properties for Bus Bar Manufacturing?
When considering bus bar manufacturing, understanding the essential technical properties is crucial for B2B buyers. These specifications ensure the product meets operational requirements and industry standards, ultimately impacting performance and reliability.
1. Material Grade: Why Is It Critical for Bus Bars?
The choice of material directly influences the electrical conductivity, thermal conductivity, and mechanical strength of bus bars. Common materials include copper and aluminum, with copper offering superior conductivity. For buyers, selecting the right material grade is vital for optimizing efficiency and minimizing energy loss in electrical systems.
2. Tolerance: How Does It Affect Fit and Function?
Tolerance refers to the allowable deviation from specified dimensions during the manufacturing process. In bus bar applications, maintaining tight tolerances ensures proper fit and function within electrical systems. Poor tolerances can lead to increased resistance, heat generation, and potential failures, making it essential for buyers to prioritize manufacturers that adhere to stringent tolerance standards.
3. Cross-Sectional Area: What Should Buyers Consider?
The cross-sectional area of a bus bar determines its current-carrying capacity. A larger cross-section allows for higher currents without overheating, which is crucial for applications in industrial and commercial settings. Buyers should evaluate the specific current requirements of their applications to select appropriately sized bus bars that ensure safety and efficiency.
4. Surface Finish: Why Is It Important?
The surface finish of a bus bar can impact its resistance to corrosion and overall longevity. A smooth finish reduces the likelihood of surface imperfections that can attract dirt and moisture, leading to corrosion over time. For B2B buyers, understanding the implications of surface treatment options—such as plating or anodizing—can aid in making informed purchasing decisions that enhance the lifespan of their electrical systems.
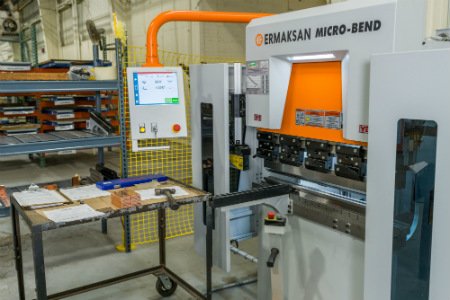
A stock image related to bus bar manufacturer.
5. Thermal Conductivity: How Does It Impact Performance?
Thermal conductivity is a measure of a material’s ability to conduct heat. In bus bars, effective thermal management is critical to prevent overheating, which can result in equipment failure. Buyers should consider the thermal properties of the materials used in bus bar manufacturing to ensure they can withstand operational temperatures without compromising performance.
What Are Common Trade Terms in Bus Bar Manufacturing?
Familiarity with industry jargon is essential for smooth negotiations and effective communication in the B2B environment. Here are some commonly used terms that buyers should understand:
1. OEM (Original Equipment Manufacturer): What Does It Mean?
OEM refers to companies that produce parts or equipment that may be marketed by another manufacturer. In the bus bar industry, understanding whether a supplier is an OEM can help buyers assess the quality and reliability of the products being sourced.
2. MOQ (Minimum Order Quantity): How Does It Affect Purchasing?
MOQ is the smallest quantity of a product that a supplier is willing to sell. Knowing the MOQ helps buyers plan their procurement strategies effectively and ensures they meet the supplier’s requirements for cost-effective purchasing.
3. RFQ (Request for Quotation): Why Is It Important?
An RFQ is a document sent to suppliers requesting pricing for specific products or services. Buyers use RFQs to compare quotes from multiple suppliers, enabling them to make informed decisions based on price and quality.
4. Incoterms: What Are They and Why Do They Matter?
Incoterms (International Commercial Terms) define the responsibilities of buyers and sellers in international trade, including who is responsible for shipping, insurance, and tariffs. Understanding these terms helps buyers navigate logistics and avoid unexpected costs during the procurement process.
5. Lead Time: How Does It Impact Project Planning?
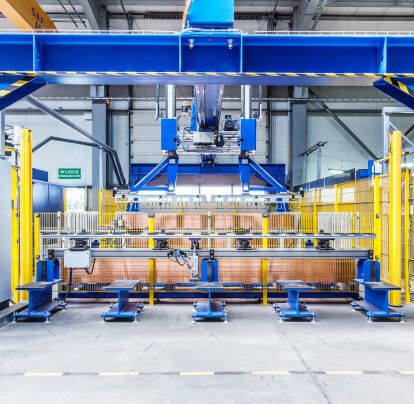
A stock image related to bus bar manufacturer.
Lead time refers to the time taken from placing an order to receiving the product. Knowing the lead time is essential for buyers to align their project schedules and ensure timely delivery of bus bars for their applications.
By understanding these technical properties and trade terms, international B2B buyers can make more informed decisions when sourcing bus bars, ensuring they select high-quality products that meet their operational needs.
Navigating Market Dynamics and Sourcing Trends in the bus bar manufacturer Sector
What Are the Current Market Dynamics and Key Trends in the Bus Bar Manufacturing Sector?
The global bus bar manufacturing market is experiencing significant growth driven by various factors such as increased demand for efficient energy distribution, advancements in electrical infrastructure, and the shift toward renewable energy sources. In regions like Africa and South America, rapid urbanization and industrialization are fueling investments in electrical grids, making sourcing bus bars a priority for international buyers. In the Middle East, government initiatives aimed at enhancing smart city projects further increase the demand for high-performance bus bars.
Emerging technologies such as IoT (Internet of Things) and smart grid systems are reshaping the bus bar landscape. The integration of these technologies allows for real-time monitoring and management of electrical systems, providing buyers with enhanced operational efficiency and safety. Additionally, the trend towards modular and customizable bus bar solutions is gaining traction, enabling businesses to tailor products to specific application needs, from data centers to renewable energy installations.
For international B2B buyers, understanding regional differences in electrical standards and regulations is crucial. In Europe, for instance, compliance with stringent EU directives on energy efficiency and safety is mandatory, while in Africa, local sourcing and partnerships can significantly reduce costs and lead times. Consequently, buyers must stay informed about these dynamics to make informed sourcing decisions.
How Does Sustainability and Ethical Sourcing Impact the Bus Bar Manufacturing Sector?
Sustainability is becoming a non-negotiable aspect of the bus bar manufacturing sector. With increasing awareness of environmental impacts, buyers are increasingly prioritizing suppliers that demonstrate commitment to sustainable practices. This includes sourcing materials with low environmental footprints and minimizing waste throughout the production process. Bus bar manufacturers are now more frequently adopting eco-friendly materials such as aluminum and copper that can be recycled, further enhancing their sustainability credentials.
Ethical sourcing is equally important, as B2B buyers are now scrutinizing supply chains for fair labor practices and transparency. In regions such as Africa and South America, where resource extraction can lead to social and environmental challenges, ensuring ethical supply chains is critical for maintaining a positive brand image and customer loyalty. Certifications such as ISO 14001 for environmental management and Fair Trade can serve as indicators of a manufacturer’s commitment to ethical sourcing.
Moreover, the demand for ‘green’ certifications is on the rise, with buyers increasingly looking for manufacturers who comply with global standards such as LEED (Leadership in Energy and Environmental Design) and the Green Building Council. By prioritizing sustainability and ethical practices, international B2B buyers can not only meet regulatory requirements but also contribute positively to their corporate social responsibility objectives.
How Has the Bus Bar Manufacturing Sector Evolved Over Time?
The evolution of the bus bar manufacturing sector can be traced back to the early 20th century when electrical distribution systems were in their infancy. Initially, bus bars were primarily made from copper due to its excellent conductivity, but over time, the industry has seen the introduction of aluminum as a cost-effective alternative. With the rise of renewable energy technologies and the increasing complexity of electrical systems, the focus has shifted toward innovation in design and materials, allowing for lighter, more efficient, and more adaptable bus bar solutions.
In recent decades, the advent of digital technology and automation has transformed manufacturing processes, resulting in improved precision and reduced lead times. Today, the industry is poised to embrace further advancements, particularly in smart technologies that enhance energy efficiency and operational reliability. This historical context is essential for international B2B buyers to understand the competitive landscape and the technological advancements that are shaping the future of bus bar manufacturing.
Frequently Asked Questions (FAQs) for B2B Buyers of bus bar manufacturer
-
How do I choose the right bus bar manufacturer for my business needs?
When selecting a bus bar manufacturer, evaluate their industry experience, product range, and customization capabilities. Look for manufacturers that offer a variety of materials and specifications to meet your unique requirements. Additionally, consider their reputation for quality and reliability by reviewing client testimonials and case studies. Request samples to assess the product quality firsthand. Finally, ensure that they comply with international standards, which is crucial for maintaining safety and performance in your applications. -
What are the common materials used in bus bar manufacturing?
Bus bars are typically made from copper or aluminum, each with distinct advantages. Copper offers superior conductivity and durability, making it ideal for high-performance applications. Aluminum, while slightly less conductive, is lighter and more cost-effective, suitable for applications where weight and budget are critical factors. Some manufacturers may also provide bus bars with protective coatings or treatments to enhance corrosion resistance and longevity, depending on your environmental requirements. -
What customization options should I look for in bus bar products?
Customization is vital to ensuring that bus bars fit your specific application requirements. Look for manufacturers that offer options for size, shape, and thickness. You may also want to inquire about different finishes, such as tin or silver plating, which can enhance conductivity and prevent oxidation. Additional features like pre-drilled holes or integrated insulation can further tailor the bus bars to your needs, improving installation efficiency and overall performance. -
What is the minimum order quantity (MOQ) for bus bars from manufacturers?
Minimum order quantities can vary significantly between manufacturers, often depending on the complexity of the bus bar design and the material used. For standard bus bars, MOQs might range from 50 to 500 units, while custom designs could require larger orders. It’s essential to discuss your specific needs with the manufacturer to determine their MOQ and whether they offer flexibility for smaller orders, especially for startups or pilot projects. -
What payment terms are typically offered by bus bar manufacturers?
Payment terms can vary widely among bus bar manufacturers. Many offer options such as a 30% deposit upon order confirmation with the remaining balance due before shipping. Some manufacturers may also accept letters of credit or offer extended payment terms for larger orders. It’s crucial to discuss these terms upfront to avoid any misunderstandings and ensure that the payment process aligns with your cash flow requirements. -
How can I ensure quality assurance in bus bar manufacturing?
To ensure quality assurance, choose manufacturers that adhere to international standards like ISO 9001 for quality management. Request documentation of their quality control processes, including material testing, dimensional checks, and performance evaluations. Additionally, consider asking for third-party certifications or audits that validate their manufacturing practices. Regular communication with the manufacturer during production can also help address any quality concerns early in the process. -
What logistics considerations should I be aware of when sourcing bus bars internationally?
When sourcing bus bars from international manufacturers, consider shipping costs, lead times, and customs regulations. Understand the logistics involved in transporting heavy materials like bus bars, as this can impact delivery schedules and overall costs. Work with manufacturers who have experience in exporting to your region and can provide clarity on the shipping process, including any tariffs or duties that may apply. Additionally, establish a clear communication plan for tracking shipments. -
How do I handle disputes with a bus bar supplier?
In the event of a dispute with a bus bar supplier, start by reviewing your contract to understand the terms and conditions related to quality, delivery, and payment. Open a line of communication with the supplier to discuss the issue directly and seek an amicable resolution. If the dispute cannot be resolved through direct communication, consider mediation or arbitration, which can provide a neutral platform for addressing the issue. Always document all communications and agreements to protect your interests.
Important Disclaimer & Terms of Use
⚠️ Important Disclaimer
The information provided in this guide, including content regarding manufacturers, technical specifications, and market analysis, is for informational and educational purposes only. It does not constitute professional procurement advice, financial advice, or legal advice.
While we have made every effort to ensure the accuracy and timeliness of the information, we are not responsible for any errors, omissions, or outdated information. Market conditions, company details, and technical standards are subject to change.
B2B buyers must conduct their own independent and thorough due diligence before making any purchasing decisions. This includes contacting suppliers directly, verifying certifications, requesting samples, and seeking professional consultation. The risk of relying on any information in this guide is borne solely by the reader.
Strategic Sourcing Conclusion and Outlook for bus bar manufacturer
As global markets evolve, the importance of strategic sourcing for bus bar manufacturers cannot be overstated. By leveraging strategic partnerships and supply chain efficiencies, B2B buyers can secure high-quality bus bars that meet their specific needs while optimizing costs. It is essential for buyers in regions such as Africa, South America, the Middle East, and Europe to engage with manufacturers who understand local market dynamics and regulatory requirements.
How Can B2B Buyers Enhance Their Sourcing Strategies?
Investing in long-term relationships with reliable suppliers can lead to improved product quality and innovation. International buyers should prioritize manufacturers that offer flexibility in production capabilities and customization options, ensuring that their unique specifications are met. Additionally, buyers should remain vigilant about market trends and technological advancements, as these factors can significantly influence pricing and availability.
What is the Future Outlook for Bus Bar Manufacturing?
Looking ahead, the demand for efficient and sustainable electrical solutions will continue to drive the bus bar market. B2B buyers are encouraged to proactively seek out manufacturers who are committed to sustainability and innovation. By doing so, they not only enhance their operational efficiency but also contribute to a greener future.
In conclusion, as you navigate the complexities of sourcing bus bars, prioritize strategic partnerships and stay informed about industry trends. Take action now to secure a competitive advantage in your market.