Discover Top Benefits of Sourcing a Tissue Paper Manufacturer (2025)
Introduction: Navigating the Global Market for tissue paper manufacturer
In the ever-evolving landscape of global trade, sourcing high-quality tissue paper manufacturers presents a unique set of challenges for international B2B buyers. Companies from regions such as Africa, South America, the Middle East, and Europe face pressure to balance cost-efficiency with quality, all while navigating a diverse array of suppliers. This guide aims to demystify the complexities of the tissue paper market, offering insights into various types of tissue products, their applications, and strategies for effective supplier vetting.
With a focus on actionable information, this comprehensive resource equips buyers with the necessary tools to make informed purchasing decisions. From understanding production processes to evaluating supplier reliability, the guide covers critical aspects such as pricing strategies, shipping logistics, and compliance with international standards. By addressing common pain points and offering expert advice, we empower B2B buyers to streamline their sourcing processes and establish robust supply chains.
As you delve into this guide, expect to uncover practical tips and best practices tailored specifically for your region. Whether you are in Thailand, Nigeria, or anywhere in between, the insights provided will help you navigate the global market for tissue paper manufacturing effectively. Your informed choices today can lead to sustainable partnerships and successful business outcomes in the future.
Understanding tissue paper manufacturer Types and Variations
Type Name | Key Distinguishing Features | Primary B2B Applications | Brief Pros & Cons for Buyers |
---|---|---|---|
Conventional Tissue | Made from recycled paper, typically single-ply | Retail, hospitality, healthcare | Pros: Cost-effective; Cons: Lower absorbency |
Premium Tissue | Higher fiber quality, often multi-ply, softer texture | Luxury hotels, fine dining | Pros: Superior softness; Cons: Higher price point |
Industrial Tissue | Bulk production, thicker, more durable | Manufacturing, janitorial services | Pros: High durability; Cons: May be too rough for some uses |
Eco-Friendly Tissue | Made from sustainable sources, biodegradable | Green businesses, eco-conscious consumers | Pros: Environmentally friendly; Cons: Limited availability |
Specialty Tissue | Custom sizes, colors, or patterns | Events, marketing materials | Pros: Customization options; Cons: Longer lead times |
What are the Characteristics of Conventional Tissue Paper Manufacturers?
Conventional tissue paper manufacturers focus on producing cost-effective products primarily made from recycled paper. These tissues are typically single-ply and are widely used in retail settings, healthcare facilities, and hospitality industries. When purchasing, B2B buyers should consider the balance between cost and quality, as conventional tissues often lack the absorbency of higher-end products. However, they offer significant savings for high-volume usage.
How Do Premium Tissue Paper Manufacturers Stand Out?
Premium tissue paper manufacturers distinguish themselves by using higher-quality fibers and multi-ply construction, resulting in a noticeably softer and more absorbent product. These tissues are ideal for luxury hotels and fine dining establishments where customer experience is paramount. Buyers should weigh the benefits of enhanced softness and absorbency against the higher price point, making this a suitable choice for businesses prioritizing quality.
What are the Key Features of Industrial Tissue Paper Manufacturers?
Industrial tissue paper manufacturers focus on producing thicker, more durable products designed for heavy-duty applications. These tissues are commonly used in manufacturing settings and janitorial services, where strength and absorbency are crucial. When considering industrial tissue, buyers should evaluate the specific requirements of their applications, as these tissues may be too rough for consumer-facing settings but excel in high-demand environments.
What Makes Eco-Friendly Tissue Paper Manufacturers Unique?
Eco-friendly tissue paper manufacturers create products from sustainable sources, often emphasizing biodegradable materials. These tissues cater to businesses that prioritize environmental responsibility, such as green businesses and eco-conscious consumers. While buyers benefit from aligning with sustainability goals, they may encounter limited availability and higher prices, necessitating careful supplier selection.
How Do Specialty Tissue Paper Manufacturers Cater to Unique Needs?
Specialty tissue paper manufacturers offer customized solutions, including unique sizes, colors, or patterns tailored to specific applications, such as events or marketing materials. These manufacturers allow businesses to differentiate their brand and enhance customer engagement. Buyers should consider the lead times associated with custom orders, as these can extend the purchasing process but ultimately provide valuable branding opportunities.
Related Video: Tissue Paper production / manufacturing process
Key Industrial Applications of tissue paper manufacturer
Industry/Sector | Specific Application of Tissue Paper Manufacturer | Value/Benefit for the Business | Key Sourcing Considerations for this Application |
---|---|---|---|
Healthcare | Disposable medical products (e.g., wipes, gowns) | Ensures hygiene and compliance with health regulations. | Quality certifications, compliance with medical standards, supply chain reliability. |
Food and Beverage | Food packaging and napkins | Enhances customer experience and maintains food safety. | Food-grade materials, sustainability certifications, and local regulations. |
Hospitality | Guest amenities (e.g., tissues, towels) | Improves guest satisfaction and brand perception. | Customization options, bulk purchasing agreements, and delivery timelines. |
Retail | Point-of-sale materials (e.g., bags, wraps) | Enhances branding and customer engagement at checkout. | Design flexibility, eco-friendly options, and cost-effectiveness. |
Industrial | Absorbent materials for spills | Minimizes workplace hazards and maintains cleanliness. | Durability, absorbency levels, and compliance with safety standards. |
How is Tissue Paper Used in the Healthcare Sector?
In the healthcare industry, tissue paper manufacturers supply products such as disposable wipes, surgical gowns, and patient drapes. These items are crucial for maintaining hygiene standards and preventing cross-contamination in medical settings. International buyers must ensure that the manufacturers comply with relevant health regulations and possess necessary certifications to guarantee product safety and quality. Additionally, reliable supply chains are essential to avoid interruptions in critical healthcare services.
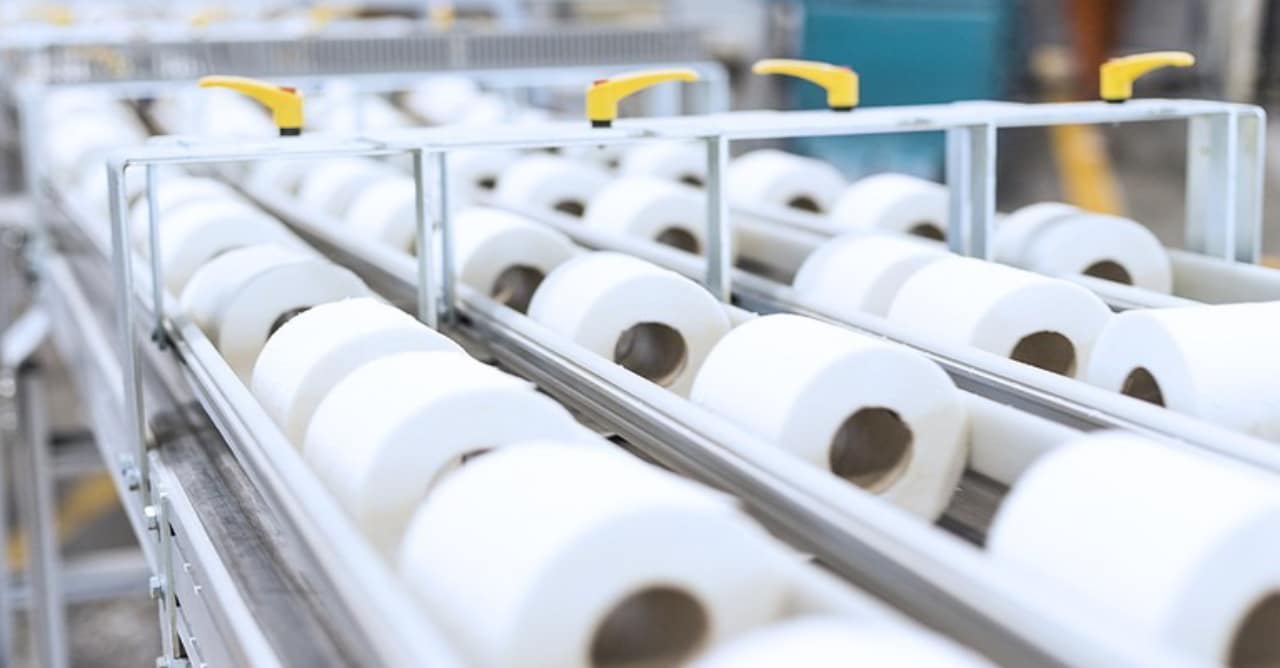
A stock image related to tissue paper manufacturer.
What Role Does Tissue Paper Play in Food and Beverage Applications?
The food and beverage industry utilizes tissue paper for packaging, napkins, and food wraps, which are vital for enhancing customer experience while ensuring food safety. Tissue paper products must be made from food-grade materials and meet local health regulations to prevent contamination. Buyers from international markets need to consider sustainability certifications, as eco-friendly packaging is increasingly becoming a consumer preference. This focus on sustainability can also enhance a brand’s reputation in the competitive food sector.
How is Tissue Paper Beneficial in the Hospitality Industry?
In the hospitality sector, tissue paper is commonly used for guest amenities such as facial tissues, towels, and toilet paper. These products significantly contribute to guest satisfaction and can enhance the overall brand perception of hotels and restaurants. When sourcing, international buyers should look for customization options that align with their brand identity, as well as bulk purchasing agreements to optimize costs. Timely delivery is also a key consideration to ensure that amenities are always available for guests.
What is the Impact of Tissue Paper in Retail Environments?
Retail businesses leverage tissue paper for point-of-sale materials, including bags and wraps, which not only serve functional purposes but also enhance branding efforts. High-quality tissue paper can create a positive impression during the checkout process, encouraging repeat business. Buyers need to evaluate design flexibility, eco-friendly options, and cost-effectiveness when sourcing tissue paper products. The ability to customize these materials can also play a critical role in differentiating a retail brand in a crowded market.
How is Tissue Paper Used in Industrial Applications?
In industrial settings, tissue paper is often used as absorbent materials for spills and cleanup tasks. These products help minimize workplace hazards and maintain cleanliness, which is vital for compliance with safety standards. When purchasing, international buyers should consider the durability and absorbency levels of the tissue paper, as well as its compliance with industry safety regulations. Ensuring that suppliers can deliver consistent quality and meet demand is essential for maintaining operational efficiency.
Related Video: How Toilet Paper Is Made in Factory – Toilet Tissue Paper Making Machine
3 Common User Pain Points for ’tissue paper manufacturer’ & Their Solutions
Scenario 1: Navigating Quality Variability in Tissue Paper Products
The Problem: B2B buyers often face significant challenges regarding the quality and consistency of tissue paper products. A common scenario involves sourcing tissue paper for a large-scale operation, such as a hotel chain or restaurant group. Buyers may encounter discrepancies in the quality of tissue paper, leading to issues like poor absorption, excessive lint, or even customer complaints about product performance. This inconsistency not only affects the end-user experience but can also damage the reputation of the business relying on these products.
The Solution: To mitigate quality variability, buyers should establish robust supplier evaluation criteria. Begin by conducting thorough research on potential manufacturers, focusing on their production processes, certifications, and customer reviews. Request samples to assess quality firsthand before making bulk orders. Additionally, engage in direct communication with manufacturers to clarify specifications and quality standards. Implementing a quality assurance program that includes regular audits and feedback loops can help maintain consistency over time. Consider forming long-term partnerships with a few reliable suppliers rather than frequently switching manufacturers, as this can lead to more stable quality control and better pricing agreements.
Scenario 2: Managing Cost Fluctuations in Tissue Paper Procurement
The Problem: International buyers often grapple with unpredictable cost fluctuations in raw materials, which can severely impact the pricing of tissue paper products. For instance, a buyer in Africa sourcing tissue paper may find that sudden increases in pulp prices or shipping costs lead to unanticipated budget overruns. These fluctuations can complicate financial planning and potentially disrupt inventory management, leading to stock shortages or overstock situations.
The Solution: To effectively manage cost fluctuations, buyers should adopt a strategic sourcing approach. This involves negotiating long-term contracts with manufacturers that include fixed pricing or price caps, which can shield against sudden market changes. Additionally, consider diversifying suppliers and sourcing from different regions to mitigate risks associated with single-source dependency. Implementing a just-in-time inventory system can also help minimize holding costs and reduce the impact of price volatility on overall procurement budgets. Regularly monitor market trends and engage with industry associations to stay informed about potential shifts in raw material costs.
Scenario 3: Ensuring Compliance with Environmental Standards
The Problem: With increasing global focus on sustainability, B2B buyers are often challenged to ensure that their tissue paper suppliers comply with environmental regulations and sustainability practices. A buyer in South America, for example, may struggle to verify whether their tissue paper products are sourced from responsibly managed forests or if the manufacturing processes adhere to eco-friendly standards. Failure to comply with these standards can lead to reputational damage and legal repercussions.
The Solution: To ensure compliance with environmental standards, buyers should prioritize sourcing from manufacturers who provide transparent supply chain information and certifications, such as FSC (Forest Stewardship Council) or SFI (Sustainable Forestry Initiative). Request detailed documentation of the sourcing and production processes, and consider conducting site visits to observe practices firsthand. Establish clear expectations regarding sustainability in your procurement contracts, including penalties for non-compliance. Collaborating with organizations that specialize in environmental compliance can also provide buyers with additional resources and support in evaluating supplier practices.
Strategic Material Selection Guide for tissue paper manufacturer
What Are the Common Materials Used in Tissue Paper Manufacturing?
When selecting materials for tissue paper manufacturing, it is crucial to consider the properties, advantages, and limitations of each option. Below, we analyze four common materials used in the industry, providing insights tailored for international B2B buyers, particularly from Africa, South America, the Middle East, and Europe.
What Are the Key Properties of Virgin Pulp in Tissue Paper Manufacturing?
Key Properties: Virgin pulp is derived from fresh wood fibers, offering excellent absorbency and softness. It typically withstands high temperatures and pressures during the manufacturing process, making it suitable for various tissue applications.
Pros & Cons: The primary advantage of virgin pulp is its superior quality, resulting in a soft, strong, and highly absorbent end product. However, it is more expensive than recycled alternatives and may raise concerns regarding sustainability and deforestation.
Impact on Application: Virgin pulp is ideal for high-end consumer products such as premium toilet paper and facial tissues, where softness and absorbency are paramount. However, buyers should consider the environmental impact and potential compliance with sustainability standards.
Considerations for International Buyers: Buyers in regions like Europe may prefer suppliers that adhere to strict sustainability certifications, such as FSC or PEFC. Compliance with local regulations regarding sourcing and sustainability is also essential.
How Does Recycled Pulp Compare in Tissue Paper Production?
Key Properties: Recycled pulp is made from post-consumer waste, offering a lower environmental impact. It generally has a lower absorbency compared to virgin pulp but can still produce quality tissue products.
Pros & Cons: The main advantage of recycled pulp is its cost-effectiveness and reduced environmental footprint. However, it may not achieve the same softness and absorbency levels as virgin pulp, which can limit its use in premium applications.
Impact on Application: Recycled pulp is suitable for standard tissue products like napkins and paper towels, where cost and environmental impact are significant factors.
Considerations for International Buyers: Buyers from Africa and South America may find recycled pulp more accessible and aligned with local sustainability efforts. Compliance with recycling standards and certifications can enhance marketability.
What Role Does Bamboo Fiber Play in Tissue Paper Manufacturing?
Key Properties: Bamboo fiber is a sustainable alternative that boasts natural antibacterial properties and high absorbency. It can withstand various manufacturing processes, making it versatile for different tissue products.
Pros & Cons: The key advantage of bamboo fiber is its rapid growth and renewability, making it an eco-friendly choice. However, it can be more expensive than traditional materials and may require specialized processing techniques.
Impact on Application: Bamboo fiber is ideal for eco-conscious brands targeting consumers who prioritize sustainability. It is suitable for premium tissue products but may not be widely available in all markets.
Considerations for International Buyers: Buyers in Europe and the Middle East may be particularly interested in bamboo products due to growing consumer demand for sustainable options. Ensuring compliance with international standards for bamboo sourcing is vital.
How Do Synthetic Fibers Fit into Tissue Paper Manufacturing?
Key Properties: Synthetic fibers, such as polyester, can enhance strength and durability in tissue products. They can withstand higher temperatures and pressures during manufacturing.
Pros & Cons: The main advantage of synthetic fibers is their durability and cost-effectiveness. However, they may lack the softness and absorbency that consumers expect from traditional tissue products.
Impact on Application: Synthetic fibers are often used in industrial applications or products requiring additional strength, such as heavy-duty paper towels.
Considerations for International Buyers: Buyers should assess the market demand for synthetic versus natural fibers in their region. Compliance with industry standards regarding synthetic materials is also essential.
Summary of Material Selection for Tissue Paper Manufacturing
Material | Typical Use Case for tissue paper manufacturer | Key Advantage | Key Disadvantage/Limitation | Relative Cost (Low/Med/High) |
---|---|---|---|---|
Virgin Pulp | Premium toilet paper, facial tissues | Superior softness and absorbency | Higher cost, sustainability concerns | High |
Recycled Pulp | Napkins, paper towels | Cost-effective, eco-friendly | Lower absorbency, less softness | Medium |
Bamboo Fiber | Eco-friendly premium tissues | Sustainable, antibacterial | Higher cost, specialized processing | High |
Synthetic Fibers | Heavy-duty paper towels | Durable, cost-effective | Lacks softness, absorbency | Medium |
This comprehensive analysis of materials used in tissue paper manufacturing provides international B2B buyers with the insights necessary to make informed purchasing decisions. Understanding the properties, advantages, and limitations of each material is essential for aligning product offerings with market demands and regulatory standards.
In-depth Look: Manufacturing Processes and Quality Assurance for tissue paper manufacturer
The manufacturing of tissue paper is a complex process that requires careful attention to detail and adherence to quality standards. For international B2B buyers, particularly those from Africa, South America, the Middle East, and Europe, understanding the manufacturing processes and quality assurance (QA) measures is crucial for making informed purchasing decisions. Below is a comprehensive overview of the typical manufacturing stages, key techniques, relevant international standards, and quality control checkpoints.
What Are the Main Stages of Tissue Paper Manufacturing?
Material Preparation: What Raw Materials Are Used?
The primary raw materials for tissue paper production include virgin pulp, recycled paper, and additives for softness and strength. The selection of high-quality raw materials is essential to ensure the final product meets customer expectations. In many cases, manufacturers opt for sustainable sourcing practices, which can appeal to environmentally conscious buyers.
- Pulping: This involves breaking down the raw materials into pulp, either through mechanical or chemical methods. Mechanical pulping retains more fiber but results in lower quality, while chemical pulping produces higher quality pulp suitable for tissue products.
- Bleaching: For white tissue products, the pulp is bleached using eco-friendly chemicals to remove color without harming the fibers. Buyers should inquire about the bleaching process to ensure it meets environmental standards.
Forming: How Is Tissue Paper Shaped?
The forming stage involves transforming the pulp into sheets of tissue paper.
- Sheet Formation: The pulp slurry is spread onto a moving screen, allowing water to drain and forming a wet sheet. Advanced technologies, such as twin-wire forming, can enhance sheet quality by optimizing drainage and fiber orientation.
- Pressing: The wet sheets are pressed to remove excess water, enhancing the density and strength of the tissue paper.
What Finishing Techniques Are Common in Tissue Paper Production?
Finishing techniques contribute to the final texture, softness, and appearance of the tissue paper.
- Drying: The pressed sheets are dried using heated rollers or air dryers. This step is crucial in achieving the desired moisture content.
- Reeling: Dried sheets are wound into large rolls. Manufacturers may use automated systems to ensure consistent tension and avoid defects.
- Slitting and Packaging: The rolls are slit into smaller sizes based on customer specifications and packaged for shipment. Considerations for packaging include moisture protection and branding.
How Is Quality Assurance Implemented in Tissue Paper Manufacturing?
What International Standards Should B2B Buyers Be Aware Of?
Quality assurance in tissue paper manufacturing is governed by various international standards, which help ensure product safety and quality.
- ISO 9001: This standard focuses on quality management systems and is applicable to all organizations. Manufacturers certified under ISO 9001 demonstrate their commitment to quality and continuous improvement.
- CE Marking: Required for products sold in the European Economic Area, CE marking indicates compliance with health, safety, and environmental protection standards.
What Are the Key Quality Control Checkpoints?
Quality control (QC) checkpoints throughout the manufacturing process are critical for maintaining product quality.
- Incoming Quality Control (IQC): Raw materials are inspected upon arrival to ensure they meet specified quality standards. This includes checking for contaminants and verifying material specifications.
- In-Process Quality Control (IPQC): During the manufacturing stages, periodic checks are performed to monitor critical parameters such as weight, moisture content, and sheet thickness.
- Final Quality Control (FQC): Before packaging, the finished products undergo rigorous testing for strength, softness, and other specifications. This may involve tactile assessments and laboratory tests.
What Common Testing Methods Are Used in Quality Assurance?
Several testing methods are commonly employed to assess tissue paper quality:
- Tensile Strength Testing: Measures how much force the paper can withstand before breaking, which is crucial for durability.
- Absorbency Testing: Evaluates how quickly and effectively the tissue can absorb liquids, an important characteristic for many tissue products.
- Softness Testing: Often performed using specialized equipment to ensure that the final product meets consumer expectations for comfort.
How Can B2B Buyers Verify Supplier Quality Control?
For international buyers, verifying the quality control processes of suppliers is essential to ensure compliance with standards and specifications.
- Supplier Audits: Conducting audits of potential suppliers can provide insights into their manufacturing processes, quality control measures, and adherence to international standards.
- Quality Reports: Requesting detailed quality reports from suppliers can help buyers understand the QC measures in place and the outcomes of various tests conducted.
- Third-Party Inspections: Engaging independent third-party inspection agencies to assess the manufacturing facility and processes can provide an unbiased evaluation of the supplier’s quality assurance practices.
What Nuances Should International B2B Buyers Consider?
When sourcing tissue paper from manufacturers in different regions, it is important to consider local regulations, certifications, and cultural expectations. For example, buyers from Africa and South America may need to account for different environmental regulations compared to their European counterparts. Additionally, understanding local market preferences can help buyers choose the right products that align with consumer demands.
In conclusion, the manufacturing processes and quality assurance measures in the tissue paper industry are multifaceted and crucial for ensuring product quality and compliance. By understanding these elements, B2B buyers can make informed decisions when selecting suppliers, ultimately leading to successful partnerships and satisfied customers.
Practical Sourcing Guide: A Step-by-Step Checklist for ’tissue paper manufacturer’
In today’s global marketplace, sourcing tissue paper manufacturers requires a structured approach to ensure quality, reliability, and compliance with industry standards. This checklist is designed to guide international B2B buyers, particularly those from Africa, South America, the Middle East, and Europe, through the essential steps needed to procure tissue paper effectively.
Step 1: Define Your Technical Specifications
Understanding your specific requirements is critical. Identify the type of tissue paper you need, such as facial tissue, toilet paper, or industrial wipes. Consider factors like grammage, ply, and any desired certifications (e.g., eco-friendliness, food safety). A clear specification will help you communicate effectively with potential suppliers and avoid misunderstandings.
Step 2: Research Potential Suppliers
Conduct thorough research to identify manufacturers that meet your specifications. Utilize online platforms, industry directories, and trade shows to compile a list of potential suppliers. Pay attention to their reputation, customer reviews, and product range. Focusing on suppliers with a proven track record in your target market can lead to more fruitful partnerships.
Step 3: Evaluate Supplier Certifications and Compliance
Verify that suppliers hold relevant certifications and comply with international standards. Look for certifications such as ISO 9001 for quality management systems or certifications related to environmental management (ISO 14001). This step ensures that you are dealing with reputable manufacturers who adhere to best practices, ultimately reducing risks in your supply chain.
Step 4: Request Product Samples
Before making a bulk purchase, always request samples of the tissue paper products. This allows you to assess quality, texture, and functionality firsthand. Evaluate the samples against your specifications to ensure they meet your standards. Additionally, consider testing the samples in real-world applications to gauge performance.
Step 5: Assess Pricing and Payment Terms
Once you have shortlisted potential suppliers, request detailed quotations that outline pricing, payment terms, and delivery schedules. Compare these quotes while considering not only the price but also the quality and service levels offered. Negotiate terms that are favorable for both parties, ensuring a sustainable relationship.
Step 6: Check References and Reviews
Before finalizing your supplier choice, seek references from other clients who have worked with them. This can provide insights into the supplier’s reliability, customer service, and responsiveness. Online reviews can also offer valuable information about the supplier’s performance and any potential red flags.
Step 7: Finalize Contractual Agreements
Once you have selected a supplier, draft a comprehensive contract that outlines all agreed-upon terms, including pricing, delivery schedules, quality standards, and penalties for non-compliance. Clear contractual agreements protect both parties and ensure accountability throughout the sourcing process.
By following this step-by-step checklist, B2B buyers can navigate the complexities of sourcing tissue paper manufacturers more effectively, leading to successful procurement outcomes and long-term partnerships.
Comprehensive Cost and Pricing Analysis for tissue paper manufacturer Sourcing
What Are the Key Cost Components in Tissue Paper Manufacturing?
Understanding the cost structure of tissue paper manufacturing is essential for international B2B buyers. The primary cost components include:
-
Materials: The choice of raw materials significantly impacts costs. Common materials include virgin pulp, recycled fiber, and additives for texture and strength. Prices can fluctuate based on market conditions, so it’s wise to monitor trends and negotiate bulk purchasing agreements.
-
Labor: Labor costs vary widely depending on the region and the skill level required. In regions like Africa and South America, labor can be more affordable, but this can come with trade-offs in terms of expertise and efficiency.
-
Manufacturing Overhead: This encompasses utilities, maintenance, and factory management. Efficient production processes can help mitigate these costs, so inquire about the manufacturer’s efficiency ratings.
-
Tooling: Initial investment in machinery and equipment is substantial but necessary for quality production. Understanding the lifespan and maintenance costs of tooling is crucial for calculating long-term expenses.
-
Quality Control (QC): Ensuring product quality can incur additional costs, but it is vital to avoid returns and dissatisfied customers. Manufacturers with robust QC processes may charge higher prices, but the investment can yield better quality and fewer defects.
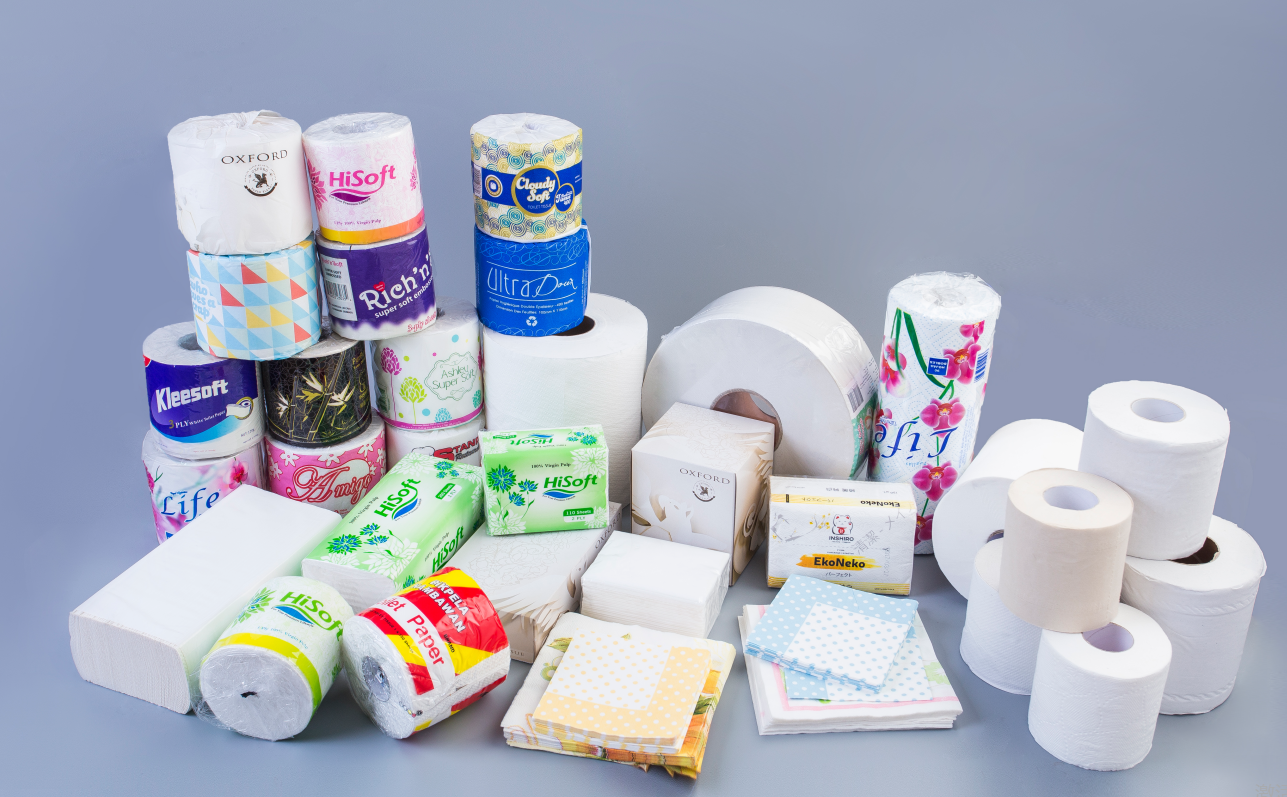
A stock image related to tissue paper manufacturer.
-
Logistics: Transportation costs can vary significantly based on distance, mode of transport, and volume. International buyers should consider the logistics involved in importing tissue products, including shipping, customs duties, and insurance.
-
Margin: Lastly, manufacturers will include a profit margin in their pricing. This margin can be influenced by market demand, competition, and the perceived value of the product.
How Do Price Influencers Affect Tissue Paper Sourcing?
Several factors influence the pricing of tissue paper, impacting your sourcing strategy:
-
Volume and Minimum Order Quantity (MOQ): Larger orders often lead to lower per-unit costs. Buyers should assess their needs carefully and negotiate MOQs that align with their consumption patterns.
-
Specifications and Customization: Custom tissue products, such as specialized sizes or branded designs, can incur higher costs. Clearly define your requirements to avoid unexpected expenses.
-
Materials Quality and Certifications: Higher-quality materials and certifications (e.g., FSC, ISO) can drive up costs. However, investing in certified products may enhance marketability and consumer trust, particularly in Europe.
-
Supplier Factors: The reputation and reliability of the supplier can influence pricing. Established suppliers may charge a premium for their reliability, while newer entrants might offer lower prices to gain market share.
-
Incoterms: Understanding the Incoterms (International Commercial Terms) agreed upon in your contract can significantly affect costs. Terms like CIF (Cost, Insurance, and Freight) or FOB (Free on Board) dictate who bears the costs and responsibilities at various stages of the shipping process.
What Are the Best Negotiation Tips for International B2B Buyers?
When negotiating with tissue paper manufacturers, consider the following tips to enhance cost-efficiency:
-
Focus on Total Cost of Ownership (TCO): Look beyond the initial purchase price. Consider long-term costs associated with quality, durability, and logistics to determine the true value of a supplier.
-
Leverage Relationships: Building strong relationships with suppliers can lead to better pricing and favorable terms. Consistent communication and reliability can foster mutual trust.
-
Explore Regional Suppliers: For buyers in Africa and South America, sourcing locally can reduce shipping costs and lead times. Evaluate regional manufacturers who may offer competitive pricing without compromising quality.
-
Be Transparent About Your Needs: Clearly communicate your volume requirements and customization needs. This transparency can lead to more tailored pricing structures that benefit both parties.
-
Stay Informed About Market Trends: Keeping abreast of global market trends in raw materials and manufacturing can provide leverage during negotiations. Use this knowledge to negotiate better prices based on current market conditions.
Disclaimer on Indicative Prices
It is essential to note that prices can vary significantly based on the factors outlined above. Always request detailed quotes from manufacturers and consider conducting a thorough market comparison to ensure competitive pricing.
Alternatives Analysis: Comparing tissue paper manufacturer With Other Solutions
Understanding Alternatives to Tissue Paper Manufacturers
In the quest for effective solutions for hygiene and cleaning needs, tissue paper manufacturers offer a popular choice. However, international B2B buyers should consider alternative products and methods that might better suit their specific requirements. This analysis will compare tissue paper manufacturers with two viable alternatives: biodegradable wipes and cloth-based cleaning solutions. Understanding these options can help businesses make informed decisions that align with their operational goals and sustainability commitments.
Comparison Table of Tissue Paper Manufacturer and Alternatives
Comparison Aspect | Tissue Paper Manufacturer | Biodegradable Wipes | Cloth-Based Cleaning Solutions |
---|---|---|---|
Performance | High absorbency, single-use | Moderate absorbency, disposable | High absorbency, reusable |
Cost | Moderate cost per unit | Higher cost per unit | Lower long-term cost |
Ease of Implementation | Simple, widely available | Requires storage space | Requires laundering |
Maintenance | Minimal (disposable) | Minimal (disposable) | Moderate (requires washing) |
Best Use Case | Quick clean-ups in various industries | On-the-go cleaning, sensitive surfaces | Deep cleaning, reusable for multiple applications |
What Are the Pros and Cons of Biodegradable Wipes?
Biodegradable wipes provide a convenient and environmentally-friendly alternative to traditional tissue paper. Their moderate absorbency makes them suitable for quick clean-ups, especially in healthcare or food service settings. However, they tend to be more expensive per unit compared to tissue paper, which can add up for businesses requiring large quantities. Additionally, while they are designed to decompose, they still contribute to waste, albeit less than conventional wipes. Businesses should weigh the convenience against the higher cost and the environmental impact.
Why Consider Cloth-Based Cleaning Solutions?
Cloth-based cleaning solutions are an excellent alternative for businesses focused on sustainability and long-term cost savings. These solutions offer high absorbency and can be reused multiple times, which significantly reduces waste. Although the initial investment may be higher due to the need for purchasing and maintaining a stock of cloths, the long-term savings can be substantial. However, cloths require regular laundering, which may necessitate additional resources and time. This option is ideal for organizations that prioritize eco-friendliness and have the capacity to manage washing and storage.
How Should B2B Buyers Choose the Right Solution?
When evaluating the right solution for their needs, B2B buyers should consider factors such as budget, intended use, and environmental impact. Tissue paper manufacturers are a solid choice for quick, one-time uses, while biodegradable wipes offer a balance between convenience and sustainability. Cloth-based solutions are best for those looking to minimize long-term costs and environmental footprints. Ultimately, the decision should align with the company’s operational strategy and values, ensuring that the chosen solution meets both practical and ethical standards.
Essential Technical Properties and Trade Terminology for tissue paper manufacturer
What Are the Essential Technical Properties of Tissue Paper for B2B Buyers?
When sourcing tissue paper, understanding the technical properties is crucial for making informed purchasing decisions. Here are key specifications to consider:
1. Material Grade
Material grade refers to the quality and type of fibers used in the production of tissue paper. Common grades include virgin fiber, recycled fiber, and blended materials. Importance: High-quality virgin fiber offers superior softness and absorbency, making it ideal for premium products, while recycled fibers may be more cost-effective for basic applications.
2. Basis Weight
Basis weight is the weight of a ream (500 sheets) of paper expressed in grams per square meter (gsm). Tissue paper typically ranges from 12 to 30 gsm. Importance: A higher basis weight indicates greater thickness and durability, which is essential for products designed for heavy-duty use, such as industrial wipes or high-end facial tissues.
3. Tolerance
Tolerance refers to the allowable variation in the weight and dimensions of the tissue paper. For example, a tolerance of ±5% means that the actual weight or size can vary by that percentage from the specified value. Importance: Understanding tolerances helps buyers ensure consistency in product quality, which is critical for applications requiring precise specifications.
4. Absorbency
Absorbency measures how much liquid a tissue paper can hold before becoming saturated. This property is often tested using standardized methods. Importance: High absorbency is crucial for products like napkins and towels, where effective liquid management is a priority. Buyers should inquire about absorbency ratings to match their product needs.
5. Softness
Softness is a subjective measure but is crucial for consumer products like facial tissues and toilet paper. It can be assessed through various testing methods, including tactile evaluations. Importance: A softer product enhances user experience, which is vital in consumer markets. Buyers should request softness ratings or samples to evaluate this property.
What Are Common Trade Terms Used in the Tissue Paper Industry?
Familiarity with industry terminology can streamline communication and negotiations with suppliers. Here are essential trade terms for B2B buyers:
1. OEM (Original Equipment Manufacturer)
An OEM refers to a company that produces parts or products that are used in another company’s end products. In the tissue paper industry, this might involve manufacturers who produce tissue paper for brands that sell under their own label. Importance: Understanding OEM relationships can help buyers identify potential partners or negotiate better pricing based on production capabilities.
2. MOQ (Minimum Order Quantity)
MOQ is the smallest quantity of a product that a supplier is willing to sell. This varies widely among manufacturers. Importance: Knowing the MOQ helps buyers assess whether a supplier can meet their needs without overcommitting financially. It’s especially relevant for smaller businesses or those testing new products.
3. RFQ (Request for Quotation)
An RFQ is a formal process where buyers request pricing and terms from suppliers. This document typically includes specifications, quantities, and delivery requirements. Importance: Using an RFQ allows buyers to compare offers from multiple suppliers, ensuring they receive competitive pricing and favorable terms.
4. Incoterms (International Commercial Terms)
Incoterms are a set of international rules that define the responsibilities of buyers and sellers in international transactions. Common terms include FOB (Free on Board) and CIF (Cost, Insurance, and Freight). Importance: Understanding Incoterms helps buyers clarify shipping costs, insurance, and liability, which is essential for budgeting and risk management.
5. Lead Time
Lead time is the time taken from placing an order to receiving the goods. It includes production time and shipping. Importance: Knowing the lead time is critical for inventory management and ensuring that supply meets demand, especially in fast-moving consumer goods markets.
By grasping these technical properties and trade terms, international B2B buyers can enhance their procurement strategies and foster stronger supplier relationships in the tissue paper manufacturing sector.
Navigating Market Dynamics and Sourcing Trends in the tissue paper manufacturer Sector
What Are the Key Trends Driving the Tissue Paper Manufacturing Market?
The global tissue paper manufacturing sector is undergoing significant transformations, influenced by various market dynamics. One of the most notable drivers is the increasing demand for hygiene products, spurred by heightened awareness of health and sanitation, particularly in the wake of global health crises. As B2B buyers from regions like Africa, South America, the Middle East, and Europe navigate these changes, understanding current and emerging sourcing trends becomes crucial.
Digitalization is reshaping the way companies in this sector operate. Advanced technologies like automation and IoT (Internet of Things) are improving production efficiency, reducing operational costs, and enhancing supply chain transparency. B2B buyers should look for manufacturers that leverage these technologies, as they can provide better pricing and reliability.
Moreover, the rise of e-commerce is facilitating direct purchasing channels, allowing buyers to access a wider range of suppliers and products. This trend is particularly pronounced in regions where traditional distribution channels may be less developed. Buyers should consider partnering with suppliers that offer robust online platforms for easier ordering and tracking.
How Is Sustainability Impacting Sourcing Decisions in the Tissue Paper Sector?
Sustainability has emerged as a critical factor in the sourcing strategies of international B2B buyers. The environmental impact of tissue paper production, particularly concerning deforestation and water usage, has led to a growing emphasis on ethical sourcing practices. Manufacturers are increasingly adopting sustainable forestry practices and using recycled materials to reduce their ecological footprint.
Certifications such as FSC (Forest Stewardship Council) and PEFC (Programme for the Endorsement of Forest Certification) have become essential indicators of responsible sourcing. Buyers should prioritize suppliers with these certifications to ensure they are contributing to sustainable practices. Additionally, the use of biodegradable and compostable materials is gaining traction, appealing to environmentally conscious consumers and businesses alike.
By integrating sustainability into their sourcing decisions, B2B buyers can not only meet regulatory requirements but also align with the growing consumer demand for eco-friendly products. This alignment can enhance brand reputation and foster customer loyalty, making it a strategic advantage in today’s competitive market.
What Is the Historical Context of the Tissue Paper Manufacturing Industry?
The tissue paper manufacturing industry has evolved significantly over the decades, from its early days of manual production to the highly automated processes seen today. The advent of mechanization in the late 19th century marked a pivotal moment, allowing for mass production and increased accessibility to tissue products.
In the latter half of the 20th century, innovations in raw materials and manufacturing processes transformed the industry, leading to a broader range of products, including facial tissues, toilet paper, and paper towels. As consumer preferences shifted towards convenience and hygiene, the industry adapted, resulting in the diverse product offerings available today.
For B2B buyers, understanding this evolution is important as it highlights the industry’s responsiveness to market demands, setting the stage for future innovations and trends. Being aware of these historical shifts can inform strategic sourcing decisions, ensuring alignment with market expectations and consumer needs.
Frequently Asked Questions (FAQs) for B2B Buyers of tissue paper manufacturer
-
How do I select a reliable tissue paper manufacturer for my business needs?
Selecting a reliable tissue paper manufacturer involves several critical steps. Begin by conducting thorough research on potential suppliers, examining their reputation, certifications, and customer reviews. Request samples to assess product quality and ensure they meet your specifications. It’s also advisable to inquire about their production capacity, lead times, and adherence to sustainability practices. Establish communication to gauge responsiveness and support, as these factors are essential for long-term partnerships, especially for buyers from diverse regions like Africa, South America, and Europe. -
What are the key factors to consider when negotiating payment terms with tissue paper suppliers?
When negotiating payment terms, consider factors such as your cash flow needs, supplier’s payment preferences, and the overall risk involved in the transaction. Common terms include advance payments, letters of credit, and net payment terms (e.g., net 30, net 60). Always clarify currency exchange rates and potential fees associated with international transactions. Establishing mutually agreeable terms can enhance trust and ensure smoother transactions, especially for international buyers who may face additional complexities in cross-border payments. -
What is the minimum order quantity (MOQ) for tissue paper products?
The MOQ for tissue paper products can vary significantly between manufacturers and is often influenced by production costs and material availability. Generally, MOQs can range from a few hundred to several thousand units. When sourcing, communicate your requirements clearly and explore options for smaller initial orders or trial runs. Some manufacturers may offer flexibility, especially if you establish a long-term partnership, which can be beneficial for B2B buyers in emerging markets looking to minimize initial investment risks. -
How can I ensure the quality of tissue paper products from international suppliers?
Ensuring product quality involves multiple strategies. First, request certifications such as ISO or other relevant quality standards. Implement a quality assurance process that includes pre-shipment inspections and testing samples for durability and absorbency. Establish clear specifications and expectations before production begins. Additionally, consider working with third-party inspection services, particularly if you are importing from regions with varying quality standards, to provide an added layer of assurance. -
What customization options are typically available for tissue paper products?
Many tissue paper manufacturers offer customization options, including size, ply, color, and packaging. Some suppliers may also provide printing services for branding purposes. When discussing customization, be clear about your needs and any specific design elements you wish to incorporate. It’s advisable to verify the manufacturer’s capabilities and minimum requirements for customized orders, as these can impact lead times and costs. -
How do logistics and shipping impact the sourcing of tissue paper products?
Logistics and shipping are crucial in the sourcing process, especially for international transactions. Factors such as shipping methods (air vs. sea), lead times, and customs regulations can significantly affect your delivery schedules and costs. Work closely with your supplier to understand their logistics capabilities and discuss options for efficient shipping. Additionally, consider working with freight forwarders who specialize in international trade to streamline the process and minimize potential delays. -
What are the common challenges faced when sourcing tissue paper from overseas manufacturers?
Common challenges include language barriers, cultural differences, varying quality standards, and potential delays in shipping. Additionally, international buyers may face issues with tariffs, customs, and compliance with local regulations. To mitigate these challenges, establish clear communication channels, conduct thorough due diligence, and consider engaging local agents or partners who understand the regional market dynamics. -
What should I do if I encounter issues with my tissue paper supplier?
If you encounter issues, start by addressing the problem directly with your supplier. Clearly communicate your concerns, whether they relate to product quality, delivery delays, or payment terms. Document all interactions and agreements to maintain a record. If the issue persists, explore alternative dispute resolution methods, such as mediation. In extreme cases, consider legal action, but always weigh the costs versus the potential benefits, especially in international contexts where laws may differ significantly.
Important Disclaimer & Terms of Use
⚠️ Important Disclaimer
The information provided in this guide, including content regarding manufacturers, technical specifications, and market analysis, is for informational and educational purposes only. It does not constitute professional procurement advice, financial advice, or legal advice.
While we have made every effort to ensure the accuracy and timeliness of the information, we are not responsible for any errors, omissions, or outdated information. Market conditions, company details, and technical standards are subject to change.
B2B buyers must conduct their own independent and thorough due diligence before making any purchasing decisions. This includes contacting suppliers directly, verifying certifications, requesting samples, and seeking professional consultation. The risk of relying on any information in this guide is borne solely by the reader.
Strategic Sourcing Conclusion and Outlook for tissue paper manufacturer
How Can Strategic Sourcing Enhance Your Tissue Paper Procurement?
In conclusion, strategic sourcing in the tissue paper manufacturing sector is vital for international B2B buyers aiming to optimize their supply chains. By focusing on quality, sustainability, and cost-effectiveness, companies can secure reliable suppliers that meet their specific needs. Buyers should leverage data analytics to assess supplier performance, enabling informed decisions that drive efficiency and enhance product quality.
Moreover, understanding regional market dynamics is crucial for buyers from Africa, South America, the Middle East, and Europe. Each market presents unique challenges and opportunities, and adapting sourcing strategies to local conditions can lead to better outcomes. For instance, engaging with local suppliers can reduce lead times and enhance community relations, while partnerships with international manufacturers may offer advanced technologies and products.
As the global demand for tissue products continues to rise, now is the time for B2B buyers to refine their sourcing strategies. Embrace innovation, prioritize sustainability, and seek collaborative partnerships to position your business for success in a competitive landscape. Start your journey today by evaluating your current sourcing strategies and exploring new avenues to enhance your supply chain resilience.