Discover Top Benefits of Sourcing a Tubing Manufacturer (2025)
Introduction: Navigating the Global Market for tubing manufacturer
In an increasingly competitive global market, sourcing reliable tubing manufacturers can pose significant challenges for B2B buyers, especially in regions like Africa, South America, the Middle East, and Europe. The complexities of international trade, varying quality standards, and the need for compliance with local regulations can make the procurement process daunting. This guide aims to simplify these challenges by providing a comprehensive overview of the tubing manufacturing landscape, covering essential aspects such as types of tubing, applications across diverse industries, supplier vetting techniques, and cost considerations.
International buyers will find valuable insights tailored to their specific needs, empowering them to make informed purchasing decisions. By understanding the nuances of tubing products, from plastic and metal options to specialized applications in sectors like oil and gas, construction, and pharmaceuticals, buyers can better assess their requirements. Moreover, this guide will delve into effective strategies for evaluating suppliers, ensuring quality assurance, and negotiating favorable terms.
As you navigate the complexities of the global tubing market, this resource will serve as your roadmap, equipping you with actionable strategies and critical knowledge. Whether you are a buyer in Germany seeking high-grade materials or a procurement manager in South America looking for cost-effective solutions, this guide is designed to enhance your purchasing power and facilitate successful international transactions.
Understanding tubing manufacturer Types and Variations
Type Name | Key Distinguishing Features | Primary B2B Applications | Brief Pros & Cons for Buyers |
---|---|---|---|
Seamless Tubing | Manufactured without seams, providing uniform strength | Oil & gas, aerospace, automotive | Pros: High pressure tolerance; Cons: Higher cost due to manufacturing process. |
Welded Tubing | Produced by welding flat sheets, allowing for customization | Construction, HVAC, plumbing | Pros: Cost-effective; Cons: Potential weak points at welds. |
Extruded Tubing | Created by forcing material through a die for uniformity | Medical devices, food & beverage, electronics | Pros: Versatile shapes; Cons: Limited size options depending on the die. |
Coiled Tubing | Continuous lengths of tubing wound into coils for easy transport | Oil & gas, geothermal energy | Pros: Space-efficient; Cons: Handling can be challenging. |
Composite Tubing | Made from a combination of materials for enhanced properties | Aerospace, automotive, chemical processing | Pros: Lightweight and corrosion-resistant; Cons: Often more expensive than metal options. |
What Are the Characteristics of Seamless Tubing?
Seamless tubing is known for its robust construction, as it is produced without seams, which can be points of weakness. This type is ideal for applications requiring high pressure and temperature resistance, such as in the oil and gas industry, aerospace, and automotive sectors. When purchasing seamless tubing, consider the specific pressure ratings, material certifications, and the manufacturer‘s ability to meet stringent quality standards. While the initial cost may be higher, the durability often results in long-term savings.
How Does Welded Tubing Differ from Other Types?
Welded tubing is created by welding flat sheets of metal into tubular shapes. This method allows for a higher degree of customization in dimensions and wall thickness, making it a popular choice for construction, HVAC systems, and plumbing. Buyers should evaluate the quality of the welds and the overall integrity of the product, as these can be potential weak points. Although welded tubing is generally more cost-effective than seamless options, it may not perform as well under extreme conditions.
Why Choose Extruded Tubing for Your Applications?
Extruded tubing is formed by pushing material through a die, resulting in uniform shapes. This type is widely used in industries such as medical devices, food and beverage, and electronics due to its versatility. When selecting extruded tubing, consider the specific dimensions and tolerances required for your application, as well as the material properties, such as flexibility and strength. While extruded tubing can offer a variety of shapes, it may have limitations in size based on the die used.
What Are the Advantages of Coiled Tubing?
Coiled tubing is essentially a continuous length of tubing that is wound into coils, making it highly portable and space-efficient. This type is predominantly used in oil and gas applications and geothermal energy projects. When sourcing coiled tubing, it is crucial to assess the coil diameter, length, and material quality, as handling can sometimes pose challenges. Despite its advantages in transport and storage, buyers should be mindful of the potential difficulties in deployment and installation.
How Does Composite Tubing Stand Out in the Market?
Composite tubing combines various materials to enhance performance characteristics such as strength, weight, and corrosion resistance. This type is particularly favored in aerospace, automotive, and chemical processing industries. Buyers should focus on the specific composite materials used, as well as their compatibility with the intended application. While composite tubing often comes at a premium price, the benefits of reduced weight and increased durability can justify the investment in high-performance scenarios.
Related Video: Different types of Pex tubing
Key Industrial Applications of tubing manufacturer
Industry/Sector | Specific Application of tubing manufacturer | Value/Benefit for the Business | Key Sourcing Considerations for this Application |
---|---|---|---|
Oil and Gas | Hydraulic tubing for drilling and extraction | Enhanced efficiency and safety in exploration activities | Material quality, pressure ratings, and compliance with international standards. |
Automotive | Fuel and brake line tubing | Improved vehicle performance and safety | Compatibility with existing systems, corrosion resistance, and regulatory compliance. |
Pharmaceuticals | Sterile tubing for fluid transfer in manufacturing | Ensures product integrity and patient safety | Certifications for biocompatibility, traceability, and cleanroom standards. |
Construction and Infrastructure | Structural tubing for scaffolding and support structures | Increased durability and load-bearing capacity | Structural integrity, local building codes, and environmental resistance. |
Agriculture | Irrigation tubing for efficient water distribution | Maximizes crop yield and resource conservation | UV resistance, flexibility for various terrains, and ease of installation. |
How is Tubing Used in the Oil and Gas Industry?
In the oil and gas sector, hydraulic tubing is critical for drilling and extraction processes. These tubes withstand extreme pressure and corrosive environments, ensuring the safety and efficiency of exploration activities. International B2B buyers must consider material quality, pressure ratings, and compliance with international standards, especially when sourcing from regions with diverse regulatory environments like Africa and the Middle East.
What are the Applications of Tubing in the Automotive Sector?
Automotive manufacturers utilize tubing for fuel and brake lines, which are essential for vehicle performance and safety. The right tubing ensures a reliable flow of fuel and brake fluid, reducing the risk of leaks and failures. Buyers should focus on compatibility with existing systems, corrosion resistance, and adherence to regulatory compliance, particularly in European markets with stringent automotive standards.
Why is Tubing Important in Pharmaceuticals?
In pharmaceutical manufacturing, sterile tubing is used for fluid transfer to maintain product integrity and ensure patient safety. This application is critical in processes that require high levels of cleanliness and compliance with health regulations. Buyers need to prioritize certifications for biocompatibility, traceability, and adherence to cleanroom standards, especially when sourcing materials for sensitive applications in Europe or South America.
How is Tubing Used in Construction and Infrastructure Projects?
Structural tubing is employed in scaffolding and support structures within the construction industry. This tubing provides increased durability and load-bearing capacity, essential for safe construction practices. When sourcing, buyers should consider structural integrity, compliance with local building codes, and environmental resistance, particularly in regions prone to extreme weather conditions, such as parts of Africa and the Middle East.
What Role Does Tubing Play in Agriculture?
In agriculture, irrigation tubing is vital for efficient water distribution, enhancing crop yield while conserving resources. The right tubing can adapt to various terrains and weather conditions, ensuring effective irrigation practices. Buyers should look for UV resistance, flexibility, and ease of installation, particularly in diverse agricultural landscapes found in South America and Africa.
Related Video: Coiled Tubing Equipment
3 Common User Pain Points for ‘tubing manufacturer’ & Their Solutions
Scenario 1: Quality Control Issues in Tubing Manufacturing
The Problem:
International B2B buyers often face the challenge of inconsistent quality in tubing products. This inconsistency can lead to significant operational disruptions, particularly for industries such as oil and gas, construction, and pharmaceuticals where reliability is paramount. For example, a buyer in Africa sourcing tubing for a pipeline project may receive materials that do not meet specified standards, resulting in delays, increased costs, and potential safety hazards. This scenario is further complicated by the logistical challenges of returning defective products across international borders.
The Solution:
To mitigate quality control issues, buyers should conduct thorough due diligence before partnering with a tubing manufacturer. This includes requesting certifications such as ISO 9001, which guarantees adherence to quality management systems. Buyers should also ask for samples and conduct their own testing to ensure the product meets specific project requirements. Establishing clear communication channels with the manufacturer can facilitate ongoing quality assurance. Regular audits and site visits can also be beneficial, particularly for long-term partnerships, to ensure that quality standards are consistently upheld.
Scenario 2: Navigating Complex Compliance Regulations
The Problem:
B2B buyers frequently struggle with navigating the complex compliance regulations that govern tubing materials, especially in industries like healthcare and food processing. For instance, a buyer in South America may find it challenging to ensure that the tubing used in medical devices meets both local and international regulations, such as FDA or CE mark standards. Non-compliance not only risks legal repercussions but can also damage a company’s reputation and lead to costly product recalls.
The Solution:
To effectively navigate compliance regulations, buyers should work closely with manufacturers that have a proven track record in regulatory compliance. It is crucial to engage suppliers who understand the specific legal requirements of the buyer’s target market and can provide necessary documentation, such as Material Safety Data Sheets (MSDS) and compliance certificates. Buyers can also benefit from consulting with legal experts or compliance officers who specialize in the tubing industry. Additionally, leveraging technology, such as compliance management software, can help track and manage regulatory requirements efficiently.
Scenario 3: High Shipping Costs and Delays
The Problem:
High shipping costs and delays are common pain points for international B2B buyers in the tubing sector, particularly when sourcing from manufacturers located in distant regions. For example, a buyer in Europe may encounter exorbitant freight charges and extended lead times when importing tubing from manufacturers in Asia or Africa. These challenges can disrupt supply chains and lead to project delays, ultimately affecting profitability and client satisfaction.
The Solution:
To address shipping-related challenges, buyers should consider a multi-faceted approach to logistics. First, they should explore various shipping options, including freight forwarders and local distributors who can provide more competitive rates and shorter lead times. Building strong relationships with logistics partners can also enhance negotiation power for better shipping terms. Additionally, buyers can evaluate the possibility of sourcing from local or regional manufacturers, which not only reduces shipping costs but also minimizes delivery times. Employing just-in-time inventory strategies can also help manage cash flow while ensuring that materials are available when needed without overcommitting to stock.
Strategic Material Selection Guide for tubing manufacturer
When selecting materials for tubing manufacturing, it’s essential for international B2B buyers to understand the properties, advantages, and limitations of various materials. This knowledge not only ensures the right choice for specific applications but also aligns with regional compliance standards and market preferences. Below, we analyze four common materials used in tubing manufacturing: stainless steel, carbon steel, PVC, and copper.
What Are the Key Properties of Stainless Steel for Tubing Applications?
Stainless steel is renowned for its exceptional corrosion resistance, high strength, and ability to withstand extreme temperatures and pressures. It typically has a temperature rating of up to 1,500°F (815°C) and can handle pressures exceeding 10,000 psi, depending on the specific grade used. This material is particularly suitable for applications involving aggressive media, such as chemicals or high-purity gases.
Pros & Cons: The durability of stainless steel makes it ideal for long-term applications, reducing the need for frequent replacements. However, its higher cost compared to other materials can be a disadvantage for budget-sensitive projects. Additionally, the manufacturing complexity associated with stainless steel can lead to longer lead times.
Impact on Application: Stainless steel tubing is widely used in industries such as pharmaceuticals, food processing, and oil and gas, where cleanliness and corrosion resistance are paramount.
Considerations for International Buyers: Buyers in Europe, particularly in Germany and Spain, must ensure compliance with standards such as DIN and EN. In Africa and South America, awareness of local corrosion factors is crucial, as environmental conditions can vary significantly.
How Does Carbon Steel Compare in Tubing Manufacturing?
Carbon steel is another popular choice for tubing, particularly in applications requiring high strength and durability. It offers good pressure ratings, typically around 2,000 psi, and can endure moderate temperatures. However, its corrosion resistance is significantly lower than that of stainless steel.
Pros & Cons: The primary advantage of carbon steel is its cost-effectiveness, making it suitable for large-scale projects. However, its susceptibility to rust and corrosion can limit its applicability in harsh environments, necessitating protective coatings or treatments.
Impact on Application: Carbon steel is commonly used in construction, automotive, and infrastructure projects, where strength is prioritized over corrosion resistance.
Considerations for International Buyers: Buyers in the Middle East should be aware of the region’s high humidity and saline conditions, which can accelerate corrosion. Compliance with ASTM standards is also important for ensuring quality and safety.
What Are the Benefits of Using PVC in Tubing?
Polyvinyl chloride (PVC) is a versatile plastic material widely used in tubing applications, particularly for water and sewage systems. It offers excellent chemical resistance and is lightweight, making it easy to handle and install. PVC tubing can typically withstand temperatures up to 140°F (60°C) and moderate pressures.
Pros & Cons: The low cost and ease of manufacturing make PVC an attractive option for many applications. However, its limitations in high-temperature and high-pressure scenarios can restrict its use in industrial settings.
Impact on Application: PVC is ideal for plumbing, irrigation, and drainage systems, where chemical resistance and low weight are beneficial.
Considerations for International Buyers: Compliance with local standards, such as ASTM and ISO, is essential, particularly in Europe, where regulatory requirements can be stringent.
Why Is Copper Still Relevant in Tubing Manufacturing?
Copper tubing is prized for its thermal conductivity, corrosion resistance, and antimicrobial properties. It can handle high temperatures (up to 400°F or 204°C) and pressures, making it suitable for various applications, including HVAC systems and refrigeration.
Pros & Cons: The primary advantage of copper is its durability and reliability in thermal applications. However, the rising cost of copper and its susceptibility to corrosion in certain environments can be drawbacks.
Impact on Application: Copper tubing is widely used in plumbing and HVAC applications, where heat transfer efficiency is critical.
Considerations for International Buyers: Buyers in Europe must adhere to stringent regulations regarding copper usage, particularly in plumbing applications. Understanding local market conditions and price fluctuations is vital for effective procurement.
Summary Table of Material Selection for Tubing Manufacturing
Material | Typical Use Case for tubing manufacturer | Key Advantage | Key Disadvantage/Limitation | Relative Cost (Low/Med/High) |
---|---|---|---|---|
Stainless Steel | Pharmaceuticals, food processing | Exceptional corrosion resistance | Higher cost and manufacturing complexity | High |
Carbon Steel | Construction, automotive | Cost-effective for large projects | Susceptible to rust and corrosion | Low |
PVC | Plumbing, irrigation | Lightweight and easy to install | Limited high-temperature applications | Low |
Copper | HVAC systems, refrigeration | Excellent thermal conductivity | Rising costs and corrosion issues | Medium |
This strategic material selection guide serves as a comprehensive resource for B2B buyers, ensuring informed decisions that align with both application requirements and regional standards.
In-depth Look: Manufacturing Processes and Quality Assurance for tubing manufacturer
What Are the Main Stages of Tubing Manufacturing Processes?
Manufacturing tubing involves several critical stages that ensure the final product meets both functional and quality standards. Understanding these stages is essential for international B2B buyers looking to establish reliable supply chains.
Material Preparation: How Is Raw Material Selected and Processed?
The first step in tubing manufacturing is the selection of raw materials, which typically include various metals like stainless steel, aluminum, and carbon steel, as well as plastics like PVC and PTFE. The choice of material directly impacts the tubing’s performance characteristics such as strength, flexibility, and corrosion resistance.
Once the raw materials are selected, they undergo preparation processes, including cutting, heating, and surface treatment. For metals, this may involve processes like annealing to improve ductility, while plastics may require drying to remove moisture. Buyers should ensure that suppliers source high-quality materials that comply with international standards.
Forming: What Techniques Are Used to Shape Tubing?
Forming is the next stage where the prepared materials are shaped into tubes. Common techniques include:
-
Seamless Tubing Production: This method involves heating a solid round billet and piercing it to create a hollow tube, which is then elongated to the desired length. This process minimizes weaknesses and is ideal for high-pressure applications.
-
Welded Tubing Production: In this method, flat metal sheets are formed into a tube and welded along the seam. It is a cost-effective approach for producing large quantities of tubing.
-
Extrusion: For plastic tubing, extrusion is a prevalent technique where raw plastic is melted and forced through a die to create a continuous length of tubing.
For B2B buyers, understanding these techniques is crucial as they affect the tubing’s strength, durability, and suitability for specific applications.
Assembly: What Is Involved in the Tubing Assembly Process?
In the assembly stage, additional components may be integrated into the tubing, such as fittings and connectors. This step is particularly important for tubing used in complex systems, like hydraulic lines or medical devices.
Quality control during assembly is critical to ensure that all components fit correctly and function as intended. Buyers should inquire about the assembly processes and whether suppliers employ automated systems to enhance precision and reduce human error.
Finishing: What Techniques Are Used for Surface Treatment?
Finishing involves various surface treatment techniques that improve the tubing’s aesthetics and performance. Common methods include:
-
Polishing: Enhances surface smoothness, which is particularly important for applications in the food and pharmaceutical industries to prevent contamination.
-
Coating: Tubes may be coated with protective layers to improve corrosion resistance or reduce friction. This is vital for tubing used in harsh environments.
-
Testing and Inspection: Before final packaging, the finished products undergo rigorous testing to ensure they meet specified standards.
How Is Quality Assurance Implemented in Tubing Manufacturing?
Quality assurance (QA) is a fundamental aspect of tubing manufacturing that ensures products meet regulatory and customer requirements.
What International Standards Should B2B Buyers Look For?
For international B2B buyers, it’s essential to ensure that suppliers adhere to recognized quality standards. Key certifications include:
-
ISO 9001: This standard outlines criteria for a quality management system and is applicable to any organization, regardless of its size or industry. It focuses on customer satisfaction and continuous improvement.
-
CE Marking: In Europe, the CE marking indicates that a product meets EU safety, health, and environmental protection requirements. This is crucial for products sold within the European market.
-
API Certification: For tubing used in oil and gas industries, API standards ensure that products are manufactured to specific technical and safety requirements.
Buyers should verify that their suppliers possess these certifications and that they are current.
What Are the Key Quality Control Checkpoints in Tubing Manufacturing?
Quality control (QC) checkpoints are vital throughout the manufacturing process. Common checkpoints include:
-
Incoming Quality Control (IQC): This involves inspecting raw materials upon arrival to ensure they meet specified standards. Buyers can request IQC reports to verify material quality.
-
In-Process Quality Control (IPQC): During manufacturing, periodic inspections are performed to identify and rectify defects early in the process. This minimizes waste and reduces the likelihood of non-conforming products.
-
Final Quality Control (FQC): Before shipment, a final inspection ensures that the products meet all specifications. This may include dimensional checks, visual inspections, and functional testing.
International buyers should inquire about the frequency and methodology of these QC checkpoints to understand the supplier’s commitment to quality.
What Common Testing Methods Are Used for Tubing Quality Assurance?
Various testing methods are utilized to ensure the integrity and quality of tubing products. Key testing methods include:
-
Hydrostatic Testing: This test involves filling the tubing with water and applying pressure to check for leaks. It is essential for ensuring the tubing can withstand operational pressures.
-
Ultrasonic Testing: This non-destructive testing method uses high-frequency sound waves to detect internal flaws in the tubing material.
-
Tensile Testing: This measures the strength and ductility of the material by applying tension until it breaks.
B2B buyers should request testing certifications and reports from suppliers to ensure that products have passed these critical tests.
How Can B2B Buyers Verify Supplier Quality Control?
Verifying a supplier’s quality control processes is crucial for establishing trust and ensuring product reliability. Here are actionable steps B2B buyers can take:
-
Conduct Supplier Audits: Periodic audits allow buyers to assess the supplier’s manufacturing processes, QC systems, and adherence to standards. This can be done either independently or by hiring third-party audit firms.
-
Request Quality Control Reports: Suppliers should be able to provide detailed QC reports that outline testing results, inspection processes, and any corrective actions taken for defects.
-
Engage Third-Party Inspection Services: For international transactions, buyers can hire third-party inspection agencies to conduct pre-shipment inspections, ensuring that products meet all specifications before leaving the supplier’s facility.
What Are the QC and Certification Nuances for International B2B Buyers?
International B2B buyers must navigate various quality assurance nuances specific to their regions. For example:
-
Africa: Buyers should be aware of local standards and certifications that may differ from international norms. Engaging with local experts can provide insights into compliance requirements.
-
South America: Many countries in this region have specific import regulations that may require additional certifications or testing. Understanding these nuances can prevent costly delays.
-
Middle East: The region may have unique quality requirements, especially in industries like construction and oil and gas. Buyers should verify that suppliers meet local standards.
-
Europe (e.g., Germany, Spain): In Europe, strict regulations govern product safety and quality. Buyers should ensure that their suppliers comply with EU directives and have the necessary certifications.
By being proactive in understanding the manufacturing processes and quality assurance measures, international B2B buyers can make informed decisions that lead to successful partnerships with tubing manufacturers.
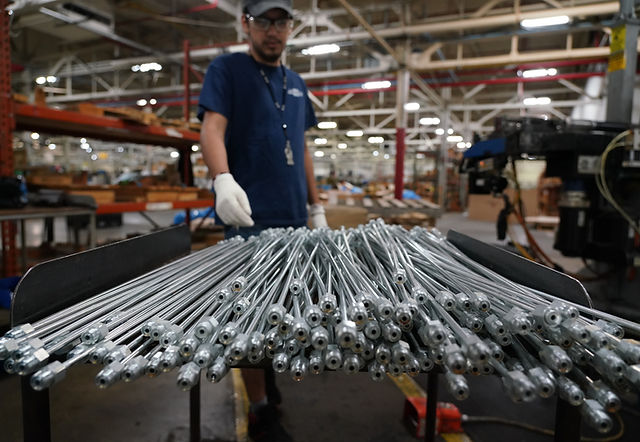
A stock image related to tubing manufacturer.
Practical Sourcing Guide: A Step-by-Step Checklist for ‘tubing manufacturer’
The procurement of tubing manufacturing services can be a complex process, especially for international buyers. This checklist serves as a practical guide to streamline your sourcing efforts, ensuring you find the right manufacturer that meets your technical requirements, budget, and compliance standards. Follow these steps to enhance your sourcing strategy.
Step 1: Define Your Technical Specifications
Before reaching out to manufacturers, clearly outline your technical specifications. This includes details such as material type, dimensions, and tolerance levels. A well-defined specification allows suppliers to provide accurate quotes and ensures that the final product meets your operational needs.
- Material Requirements: Specify whether you need stainless steel, carbon steel, plastic, or other materials.
- Dimension Standards: Include measurements, wall thickness, and any specific industry standards that must be adhered to.
Step 2: Research Potential Suppliers
Conduct thorough research to identify potential tubing manufacturers. Utilize online platforms, industry directories, and trade shows to compile a list of candidates. Focus on suppliers with a strong presence in your target regions, such as Africa, South America, the Middle East, and Europe.
- Online Reviews and Ratings: Check reviews on platforms like Trustpilot or Google to gauge customer satisfaction.
- Industry Reputation: Investigate any industry awards or recognitions that the manufacturers may have received.
Step 3: Evaluate Supplier Certifications
It’s critical to verify that potential suppliers hold the necessary certifications for quality and safety standards. Certifications such as ISO 9001, ISO 13485, or specific industry-related certifications assure you of the manufacturer’s commitment to quality.
- Quality Management Systems: Ensure the supplier has a robust quality management system in place.
- Compliance with Regulations: Check if they meet local and international regulatory standards pertinent to your industry.
Step 4: Request Samples and Prototypes
After narrowing down your options, request samples or prototypes of the tubing. This step allows you to assess the quality, material properties, and precision of the manufacturer’s work before making a bulk order.
- Quality Assessment: Examine the samples for defects, consistency, and adherence to specifications.
- Testing Procedures: Inquire about any testing processes the manufacturer employs to ensure quality.
Step 5: Discuss Pricing and Payment Terms
Engage in discussions about pricing structures and payment terms. Ensure that you understand all costs involved, including shipping, customs duties, and potential taxes. Transparent pricing helps avoid unexpected expenses later in the procurement process.
- Volume Discounts: Ask if they offer discounts for larger orders.
- Payment Flexibility: Determine if they provide flexible payment options, such as net-30 or net-60 terms.
Step 6: Assess Production Capabilities and Lead Times
Understanding a manufacturer’s production capabilities and lead times is essential. Ensure they can handle your volume requirements and deliver within your timeframe.
- Production Capacity: Confirm the manufacturer can scale production to meet your future needs.
- Lead Time Estimates: Request detailed timelines for production and shipping to plan accordingly.
Step 7: Establish Communication Channels
Finally, establish clear communication channels with your chosen supplier. Regular communication helps in resolving issues promptly and ensures alignment throughout the manufacturing process.
- Dedicated Contacts: Identify key contacts within the supplier’s organization for quick resolution of queries.
- Language and Time Zone Considerations: Ensure effective communication by considering language barriers and time zone differences.
By following this step-by-step checklist, you can effectively navigate the sourcing process for tubing manufacturing, ensuring you partner with a reliable supplier that meets your specific needs.
Comprehensive Cost and Pricing Analysis for tubing manufacturer Sourcing
Understanding the cost structure and pricing dynamics of tubing manufacturing is critical for international B2B buyers, especially those from diverse regions like Africa, South America, the Middle East, and Europe. This section delves into the essential components of cost, the factors influencing pricing, and strategic insights to optimize sourcing decisions.
What are the Key Cost Components in Tubing Manufacturing?
-
Materials: The cost of raw materials such as steel, plastic, or other alloys significantly impacts the overall price. The choice of material not only affects durability and performance but also varies in cost depending on market conditions and availability.
-
Labor: Labor costs can differ widely based on the manufacturing location. Countries with higher labor standards may have increased costs, while regions with lower wage expectations can offer more competitive pricing. Understanding local labor regulations and potential labor shortages is crucial.
-
Manufacturing Overhead: This includes fixed costs such as utilities, rent, and equipment maintenance. Efficient production processes can help mitigate these costs, and buyers should consider suppliers that invest in advanced manufacturing technologies.
-
Tooling: The initial investment in tooling is a significant upfront cost for custom tubing. Buyers should inquire about tooling charges, particularly when ordering specialized products, as these can heavily influence the total price.
-
Quality Control (QC): Ensuring product quality through rigorous QC processes can add to costs. However, investing in quality assurance can lead to lower defect rates and long-term savings.
-
Logistics: Shipping, handling, and storage costs are critical, especially for international buyers. The choice of shipping methods and routes can impact delivery times and overall expenses.
-
Margin: Finally, manufacturers will include a profit margin in their pricing. This can vary based on their business strategy and market competition.
How Do Price Influencers Affect Tubing Manufacturing Costs?
-
Volume and Minimum Order Quantity (MOQ): Larger orders typically lead to lower per-unit costs. Buyers should negotiate MOQs to maximize their purchasing power while considering their storage capabilities.
-
Specifications and Customization: Custom specifications often result in higher prices due to the need for specialized tooling and processes. Buyers should assess whether standard products could meet their needs to avoid unnecessary costs.
-
Materials and Quality Certifications: The choice of materials directly correlates with the pricing. Additionally, certifications (such as ISO or ASTM) can add costs but are essential for ensuring compliance and quality, particularly in regulated industries.
-
Supplier Factors: The supplier’s reputation, experience, and location can also influence pricing. Established suppliers may charge a premium for their reliability and quality assurance.
-
Incoterms: Understanding Incoterms is crucial for international transactions. These terms dictate the responsibilities of buyers and sellers in the shipping process and can significantly impact overall costs.
What Are the Best Practices for Negotiating Tubing Manufacturer Prices?
-
Conduct Thorough Market Research: Familiarize yourself with average market prices for the types of tubing you require. This knowledge will empower you during negotiations.
-
Evaluate Total Cost of Ownership (TCO): Look beyond the initial purchase price. Consider logistics, maintenance, and potential downtime costs associated with the products you source.
-
Leverage Relationships: Building long-term relationships with suppliers can lead to better pricing and terms. Regular communication can also facilitate negotiation during future transactions.
-
Explore Regional Variations: When sourcing from different regions, consider local economic conditions. For instance, suppliers in Europe may have different pricing strategies compared to those in Africa or South America due to varying operational costs.
-
Request Samples and Prototypes: Before committing to larger orders, request samples to assess quality and suitability. This step can prevent costly mistakes later on.
Conclusion
For international B2B buyers, particularly in Africa, South America, the Middle East, and Europe, understanding the comprehensive cost and pricing structure of tubing manufacturing is vital. By evaluating the cost components, recognizing the influencers of pricing, and employing strategic negotiation tactics, buyers can make informed decisions that enhance their sourcing effectiveness. Remember that the pricing landscape can fluctuate, and it is essential to stay updated on market trends to secure the best deals.
Alternatives Analysis: Comparing tubing manufacturer With Other Solutions
Understanding Alternatives in Tubing Solutions
When considering tubing solutions, international B2B buyers must evaluate various alternatives that can meet their operational needs. Each option comes with distinct characteristics that can significantly impact performance, cost, and ease of implementation. This analysis will compare traditional tubing manufacturers against two viable alternatives: flexible tubing systems and rigid piping solutions.
Comparison Table of Tubing Solutions
Comparison Aspect | Tubing Manufacturer | Flexible Tubing Systems | Rigid Piping Solutions |
---|---|---|---|
Performance | High durability and strength | Moderate flexibility; good for varied applications | High rigidity; excellent flow rates |
Cost | Generally higher initial cost | Moderate; lower than rigid options | Potentially lower in bulk installations |
Ease of Implementation | Requires skilled labor for installation | Easier to install; often DIY-friendly | Requires skilled labor; can be complex |
Maintenance | Low maintenance; long lifespan | Moderate; susceptible to wear | Low maintenance; long-lasting |
Best Use Case | Industrial applications requiring high strength | Residential and light commercial uses | Heavy industrial and infrastructure applications |
What Are the Benefits and Drawbacks of Flexible Tubing Systems?
Flexible tubing systems offer a versatile solution that is particularly beneficial for applications requiring adaptability. These systems can be easily maneuvered around obstacles and can withstand various environmental conditions. They are generally more cost-effective than traditional tubing, especially in smaller projects. However, their durability may not match that of traditional tubing, leading to more frequent replacements in high-stress environments.
How Do Rigid Piping Solutions Compare?
Rigid piping solutions are ideal for heavy-duty applications where high flow rates and structural integrity are critical. They are often used in industrial settings and can handle extreme temperatures and pressures. The initial installation cost can be lower when considering bulk projects; however, they require significant labor and expertise, making them less appealing for smaller or DIY projects. Additionally, while they are durable, any required repairs can be costly and time-consuming.
Conclusion: How Can B2B Buyers Choose the Right Tubing Solution?
Selecting the appropriate tubing solution depends on several factors, including the specific application, budget constraints, and installation capabilities. For buyers from Africa, South America, the Middle East, and Europe, it is essential to assess not only the upfront costs but also the long-term performance and maintenance requirements of each solution. By understanding the unique advantages and disadvantages of tubing manufacturers, flexible tubing systems, and rigid piping solutions, buyers can make informed decisions that align with their operational goals and budgetary considerations.
Essential Technical Properties and Trade Terminology for tubing manufacturer
What Are the Key Technical Properties of Tubing for Manufacturers?
When sourcing tubing from manufacturers, understanding the essential technical properties is crucial for ensuring product quality and compliance with industry standards. Here are some critical specifications to consider:
1. Material Grade
Material grade refers to the specific type of material used in manufacturing tubing, such as stainless steel, carbon steel, or plastic. Each material grade has distinct properties, such as corrosion resistance, tensile strength, and thermal conductivity. For international buyers, selecting the appropriate material grade is vital for applications in diverse environments, from oil and gas extraction in the Middle East to plumbing systems in Europe.
2. Tolerance
Tolerance defines the permissible limits of variation in dimensions and physical properties of tubing. This specification is critical for ensuring that the tubing fits properly with other components in a system. For example, tight tolerances are essential in high-precision applications, such as aerospace or medical devices. Understanding tolerance requirements helps buyers minimize assembly issues and reduce costs associated with rework.
3. Wall Thickness
Wall thickness is a significant factor influencing the strength and durability of tubing. Thicker walls typically provide greater resistance to internal pressure and external forces. Buyers should assess wall thickness in relation to the intended application and regulatory requirements, especially in high-pressure environments like oil pipelines or hydraulic systems.
4. Yield Strength
Yield strength is the maximum stress that a material can withstand without permanently deforming. It is a crucial property for determining how much load the tubing can bear during operation. For B2B buyers, understanding yield strength helps ensure safety and reliability in applications, particularly in industries such as construction and automotive.
5. Surface Finish
The surface finish of tubing can affect its performance in various applications. A smooth surface finish minimizes friction, reduces wear, and enhances flow characteristics in fluid transport systems. Buyers should consider the required surface finish based on the specific application, such as food-grade tubing requiring stringent sanitary standards.
What Are Common Trade Terms Used in Tubing Manufacturing?
Familiarity with industry terminology can significantly enhance communication between buyers and manufacturers. Here are essential trade terms relevant to tubing procurement:
1. OEM (Original Equipment Manufacturer)
OEM refers to a company that produces parts or equipment that may be marketed by another manufacturer. Understanding OEM relationships is critical for buyers who need specific tubing tailored to fit their unique equipment or applications.
2. MOQ (Minimum Order Quantity)
MOQ is the smallest quantity of tubing that a manufacturer is willing to produce or sell. Knowing the MOQ is essential for buyers to ensure that they can meet their project requirements without overcommitting resources. This is particularly relevant for small to medium-sized enterprises in Africa or South America, where budget constraints may limit large purchases.
3. RFQ (Request for Quotation)
An RFQ is a document sent to suppliers requesting pricing and terms for specific products or services. For B2B buyers, submitting a well-structured RFQ can streamline the procurement process and enhance negotiation outcomes, ensuring competitive pricing for tubing orders.
4. Incoterms (International Commercial Terms)
Incoterms are internationally recognized rules that define the responsibilities of buyers and sellers in international trade. Familiarity with these terms, such as FOB (Free on Board) or CIF (Cost, Insurance, and Freight), is crucial for buyers to understand shipping costs and risk management, especially when sourcing tubing from different continents.
5. Lead Time
Lead time is the time taken from placing an order to its delivery. Understanding lead times helps buyers plan their inventory and production schedules effectively. For international buyers, especially in Europe and the Middle East, knowing lead times can help mitigate supply chain disruptions.
By grasping these essential technical properties and trade terms, international B2B buyers can make informed decisions that align with their operational needs and strategic goals.
Navigating Market Dynamics and Sourcing Trends in the tubing manufacturer Sector
What Are the Current Market Dynamics and Key Trends in the Tubing Manufacturer Sector?
The tubing manufacturing sector is currently experiencing a transformative phase driven by several global factors. The demand for high-quality tubing solutions is escalating across industries such as construction, automotive, oil and gas, and pharmaceuticals. This growth is largely fueled by technological advancements, particularly the adoption of automation and digitalization in manufacturing processes. As international B2B buyers, especially from Africa, South America, the Middle East, and Europe, it is essential to understand these dynamics to make informed sourcing decisions.
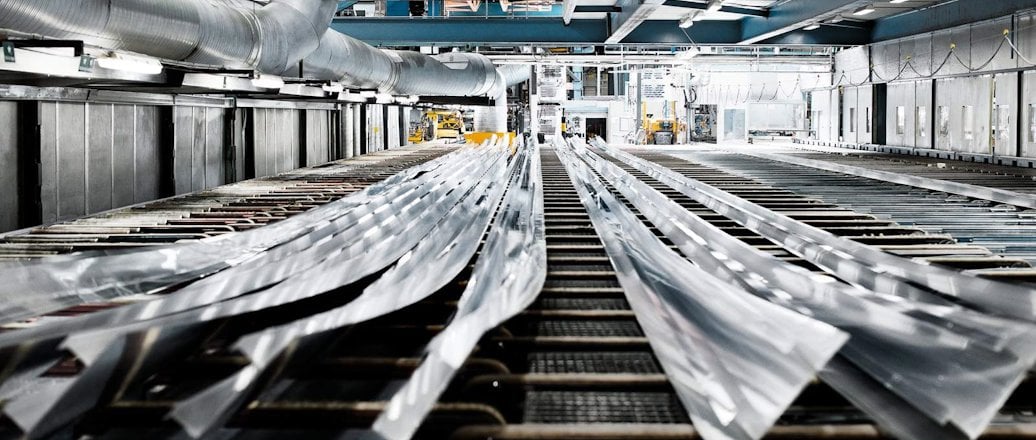
A stock image related to tubing manufacturer.
Emerging B2B technologies, such as Industry 4.0 and the Internet of Things (IoT), are revolutionizing the tubing manufacturing landscape. These innovations enhance efficiency, reduce costs, and improve product quality. Additionally, trends like just-in-time (JIT) manufacturing and agile sourcing are gaining traction. JIT reduces inventory costs, while agile sourcing allows companies to quickly adapt to changing market demands. Buyers should prioritize suppliers who leverage these technologies to ensure competitive pricing and timely delivery.
Moreover, international trade agreements and regional economic policies are influencing sourcing strategies. For instance, trade agreements within the European Union facilitate smoother transactions for European buyers, while African Continental Free Trade Area (AfCFTA) initiatives are opening up new markets for African buyers. Understanding these market dynamics will enable B2B buyers to navigate the complexities of sourcing tubing products effectively.
How Does Sustainability Impact Sourcing in the Tubing Manufacturer Sector?
Sustainability has become a critical factor in the decision-making process for B2B buyers in the tubing manufacturing sector. The environmental impact of manufacturing processes and the materials used is under increasing scrutiny. Buyers are now more aware of the need for ethical sourcing practices that minimize ecological footprints. This shift is not merely a trend but a necessity, as regulations around environmental standards become stricter globally.
Ethical supply chains are paramount for companies aiming to maintain their reputation and customer loyalty. Buyers should seek manufacturers that prioritize sustainable practices, such as using recycled materials and implementing energy-efficient processes. Certifications such as ISO 14001 (Environmental Management) and LEED (Leadership in Energy and Environmental Design) are valuable indicators of a supplier’s commitment to sustainability.
Additionally, there is a growing market for “green” materials in tubing manufacturing. Biodegradable and recyclable options are gaining traction among environmentally-conscious buyers. By choosing suppliers who offer these sustainable alternatives, international B2B buyers can not only meet their own corporate social responsibility goals but also appeal to a broader customer base that prioritizes sustainability.
What Is the Historical Context of the Tubing Manufacturer Sector?
The tubing manufacturing sector has evolved significantly over the last century, adapting to technological advancements and changing market demands. Initially, tubing was primarily produced using traditional methods, which limited production efficiency and material quality. However, the introduction of advanced manufacturing technologies, such as extrusion and welding techniques, revolutionized the industry.
In recent decades, globalization has played a crucial role in shaping the sector. The rise of international trade has enabled manufacturers to source raw materials from various regions, leading to cost reductions and improved product offerings. This evolution has created a highly competitive market where international B2B buyers must be strategic in their sourcing decisions to ensure they partner with the most capable and sustainable suppliers.
As the industry continues to innovate and adapt to modern challenges, understanding its historical context is essential for buyers looking to make informed and strategic sourcing decisions. By recognizing the trajectory of the tubing manufacturing sector, buyers can better anticipate future trends and position themselves advantageously within the market.
Frequently Asked Questions (FAQs) for B2B Buyers of tubing manufacturer
-
How do I solve supply chain disruptions when sourcing tubing from international manufacturers?
Supply chain disruptions can be mitigated by establishing strong relationships with multiple suppliers across different regions. Diversifying your supplier base not only reduces dependency on a single manufacturer but also provides flexibility in case of local disruptions. Additionally, investing in supply chain visibility tools can help you track shipments and anticipate potential delays. Ensuring clear communication with your suppliers regarding lead times, production capacities, and contingency plans is essential for smoother operations. -
What is the best tubing material for high-pressure applications?
For high-pressure applications, materials like stainless steel, titanium, and high-density polyethylene (HDPE) are often recommended. Stainless steel offers excellent strength and corrosion resistance, making it suitable for various industries, including oil and gas. Titanium is lightweight yet strong, ideal for aerospace applications. HDPE is a cost-effective option that provides good chemical resistance. Always consult with your manufacturer to ensure that the tubing meets specific industry standards and performance requirements. -
How can I assess the quality assurance processes of a tubing manufacturer?
To assess a tubing manufacturer’s quality assurance (QA) processes, request documentation of their certifications, such as ISO 9001 or industry-specific certifications. Inquire about their testing protocols, including material inspections, dimensional checks, and pressure testing. A reputable manufacturer should provide transparent information about their QA procedures and be willing to share test results. Additionally, consider visiting their facility or requesting third-party audits to gain further insight into their quality management practices. -
What are the typical minimum order quantities (MOQs) for tubing products?
Minimum order quantities (MOQs) for tubing can vary significantly based on the manufacturer, material, and customization options. Generally, MOQs can range from a few hundred to several thousand units. For specialized or custom tubing, MOQs may be higher due to the need for specific tooling or setup processes. It’s advisable to discuss your needs with potential suppliers and negotiate MOQs that align with your purchasing capacity, especially if you are a smaller business. -
What payment terms should I expect when dealing with international tubing manufacturers?
Payment terms with international tubing manufacturers can vary widely, but common practices include advance payment, letters of credit, or net 30-90 days after delivery. Many suppliers may require a deposit before production begins, especially for custom orders. It’s essential to clarify payment terms upfront to avoid misunderstandings. Understanding the currency exchange rates and potential transaction fees is also crucial when dealing with international payments. -
How can I verify the reliability of a tubing manufacturer before placing an order?
To verify a tubing manufacturer’s reliability, conduct thorough research including checking customer reviews, testimonials, and case studies. Utilize platforms like LinkedIn or industry-specific forums to gauge feedback from other buyers. Request references from the manufacturer and follow up with past clients to understand their experiences. Additionally, consider third-party verification services to assess the manufacturer’s financial stability and production capabilities. -
What logistics considerations should I keep in mind when sourcing tubing internationally?
When sourcing tubing internationally, consider factors such as shipping methods, lead times, and customs regulations. Evaluate the cost-effectiveness of air versus sea freight based on your timeline and budget. Understanding the import/export regulations in both your country and the manufacturer’s country is crucial to avoid delays. Collaborating with a logistics partner experienced in international trade can help navigate these complexities and ensure timely delivery. -
How can I customize tubing products to meet my specific needs?
Customizing tubing products typically involves discussions with the manufacturer regarding your specific requirements, such as dimensions, materials, and finishes. Most manufacturers offer design consultations to help you refine your specifications. Providing detailed drawings or prototypes can facilitate the customization process. Be prepared for potential minimum order requirements for custom products and ensure that you receive samples for testing before full-scale production.
Important Disclaimer & Terms of Use
⚠️ Important Disclaimer
The information provided in this guide, including content regarding manufacturers, technical specifications, and market analysis, is for informational and educational purposes only. It does not constitute professional procurement advice, financial advice, or legal advice.
While we have made every effort to ensure the accuracy and timeliness of the information, we are not responsible for any errors, omissions, or outdated information. Market conditions, company details, and technical standards are subject to change.
B2B buyers must conduct their own independent and thorough due diligence before making any purchasing decisions. This includes contacting suppliers directly, verifying certifications, requesting samples, and seeking professional consultation. The risk of relying on any information in this guide is borne solely by the reader.
Strategic Sourcing Conclusion and Outlook for tubing manufacturer
What Are the Key Takeaways for Strategic Sourcing in Tubing Manufacturing?
In summary, strategic sourcing plays a pivotal role in enhancing the competitive edge of B2B buyers in the tubing manufacturing sector. By aligning sourcing strategies with market demands and supplier capabilities, businesses can not only secure high-quality products but also foster sustainable relationships that drive innovation. Key takeaways include the importance of conducting thorough market research, evaluating supplier performance, and leveraging technology for better decision-making.
How Can International Buyers Benefit from Strategic Sourcing?
International buyers from Africa, South America, the Middle East, and Europe—particularly Germany and Spain—should recognize the potential of strategic sourcing to optimize costs and enhance product quality. By understanding regional market dynamics and supplier landscapes, buyers can make informed decisions that mitigate risks associated with supply chain disruptions.
What’s Next for B2B Buyers in Tubing Manufacturing?
Looking ahead, the focus should be on building resilient supply chains that can adapt to changing market conditions. Engaging in continuous supplier development, investing in digital tools, and fostering collaboration will be essential strategies. We encourage international B2B buyers to take proactive steps in refining their sourcing strategies today, ensuring they are well-positioned to seize emerging opportunities in the tubing manufacturing market.