Discover Top Benefits of Sourcing from Table Manufacturers (2025)
Introduction: Navigating the Global Market for table manufacturer
In the dynamic landscape of global trade, sourcing the right table manufacturers can present a significant challenge for B2B buyers, especially when considering factors such as quality, cost, and compliance with international standards. Whether you’re seeking elegant conference tables for corporate settings or robust dining tables for hospitality venues, understanding the diverse offerings available in the market is crucial. This guide delves into various types of tables, their applications across different industries, and the critical aspects of supplier vetting to ensure reliability and quality.
International buyers from regions like Africa, South America, the Middle East, and Europe, including countries such as Argentina and Egypt, face unique hurdles when navigating the global market. Language barriers, differing regulations, and varied cultural expectations can complicate purchasing decisions. This comprehensive guide aims to empower you with actionable insights, from evaluating cost structures to understanding logistics and supply chain dynamics. By equipping you with the knowledge needed to make informed decisions, we strive to enhance your sourcing strategies and ultimately contribute to the success of your business operations.
As you explore the intricacies of sourcing table manufacturers, you’ll gain valuable perspectives on market trends, supplier credibility, and negotiation tactics that can lead to better deals and enhanced partnerships. Let’s embark on this journey to transform your procurement process into a streamlined and efficient venture.
Understanding table manufacturer Types and Variations
Type Name | Key Distinguishing Features | Primary B2B Applications | Brief Pros & Cons for Buyers |
---|---|---|---|
Solid Wood Table Manufacturers | Use of high-quality, durable wood; customizable designs | Restaurants, offices, hotels | Pros: Aesthetic appeal, durability. Cons: Higher cost, heavier weight. |
Metal Table Manufacturers | Made from steel or aluminum; often foldable or stackable | Event venues, outdoor settings, factories | Pros: Lightweight, easy to transport. Cons: Less warmth in appearance. |
Plastic Table Manufacturers | Lightweight, weather-resistant materials; often stackable | Schools, outdoor events, casual dining | Pros: Affordable, easy to clean. Cons: Less durable than wood or metal. |
Glass Table Manufacturers | Use of tempered glass; modern designs; often combined with metal frames | Corporate offices, upscale restaurants | Pros: Sleek design, easy maintenance. Cons: Fragile, requires careful handling. |
Specialty Table Manufacturers | Focus on niche markets (e.g., gaming tables, conference tables) | Gaming lounges, conference rooms | Pros: Tailored for specific uses. Cons: Limited versatility, often higher price points. |
What Are the Characteristics of Solid Wood Table Manufacturers?
Solid wood table manufacturers specialize in crafting tables from high-quality hardwoods, such as oak, maple, or walnut. These tables are often customizable, allowing businesses to choose dimensions, finishes, and designs that fit their specific needs. They are particularly well-suited for environments where durability and aesthetics are paramount, such as restaurants and hotels. Buyers should consider the initial investment, as these tables tend to be more expensive but offer long-term value through durability and timeless appeal.
How Do Metal Table Manufacturers Stand Out?
Metal table manufacturers typically produce tables using materials like steel or aluminum, known for their strength and lightweight properties. These tables are popular in settings that require mobility, such as event venues and outdoor environments. The foldable or stackable designs make them ideal for businesses that need to optimize space. Buyers should weigh the benefits of affordability and portability against the less inviting aesthetic compared to wooden tables.
What Advantages Do Plastic Table Manufacturers Offer?
Plastic table manufacturers focus on creating lightweight, weather-resistant tables that are perfect for casual settings like schools and outdoor events. These tables are often stackable for easy storage and transport, making them a practical choice for transient or seasonal businesses. While they are typically more affordable and easier to clean, buyers should consider their lower durability compared to wood or metal options, especially for long-term use.
What Are the Key Features of Glass Table Manufacturers?
Glass table manufacturers create tables using tempered glass, often paired with metal frames for added stability. These tables are favored for their modern, sleek appearance and are commonly found in corporate offices and upscale restaurants. They are easy to maintain but can be fragile, requiring buyers to consider the handling and placement in their intended environment. The investment in glass tables can elevate the overall aesthetic but may necessitate careful consideration of safety and durability.
How Do Specialty Table Manufacturers Cater to Niche Markets?
Specialty table manufacturers focus on creating tables designed for specific applications, such as gaming tables or conference tables. These products are tailored to meet the unique needs of niche markets, making them ideal for businesses like gaming lounges or corporate environments. While they provide targeted functionality, buyers should evaluate the versatility of these tables, as they may not be suitable for other uses and often come at a premium price point.
Related Video: Heat Pump Thermostat O, B, and C Terminal Variations Explained
Key Industrial Applications of table manufacturer
Industry/Sector | Specific Application of Table Manufacturer | Value/Benefit for the Business | Key Sourcing Considerations for this Application |
---|---|---|---|
Hospitality | Restaurant and café furniture, including dining tables | Enhances customer experience and increases table turnover | Durability, ease of cleaning, and aesthetic appeal are essential. |
Education | Classroom and library tables | Facilitates collaborative learning and maximizes space usage | Compliance with safety regulations and ergonomic design are crucial. |
Office and Corporate | Conference and meeting room tables | Supports effective teamwork and decision-making processes | Customization options for branding and modularity are important. |
Healthcare | Patient and examination tables | Improves patient comfort and operational efficiency | Must meet hygiene standards and be easily sanitized. |
Event Management | Tables for banquets and exhibitions | Versatile setups for various events, maximizing space utility | Portability and easy assembly/disassembly are key features. |
How is ‘Table Manufacturer’ Utilized in the Hospitality Sector?
In the hospitality industry, table manufacturers provide a range of dining tables for restaurants, cafés, and hotels. These tables are designed to optimize space and enhance the dining experience, which is crucial for customer satisfaction and repeat business. Buyers from regions like Africa and South America should consider factors such as durability and ease of maintenance, as these tables must withstand high traffic and frequent cleaning. Additionally, aesthetic appeal plays a significant role, as furniture design can influence overall ambiance and customer perceptions.
What Role Do Tables Play in Education?
In educational settings, tables are essential for classrooms and libraries, facilitating various learning activities. Table manufacturers supply desks and collaborative tables that support group work, thereby enhancing educational outcomes. International buyers, particularly from Europe and the Middle East, should prioritize ergonomic designs to promote student comfort and engagement. Compliance with safety standards is also critical, as educational institutions require furniture that minimizes risks and supports diverse learning environments.
Why are Tables Important for Corporate Environments?
In office settings, conference and meeting room tables are vital for fostering collaboration and effective communication. Table manufacturers cater to corporate clients by offering customizable solutions that reflect brand identity and meet specific functional needs. Buyers should focus on the table’s modularity and adaptability, allowing for different configurations based on meeting size and purpose. Additionally, sourcing tables that promote a professional atmosphere can significantly enhance corporate image and employee morale.
How are Tables Used in Healthcare Facilities?
Healthcare facilities utilize specialized tables, such as patient examination tables, which are designed for comfort and functionality. Table manufacturers in this sector must adhere to stringent hygiene standards, ensuring that their products can be easily sanitized. International buyers from regions such as Africa and South America should also consider the ergonomic features of these tables, as they directly impact patient comfort and healthcare provider efficiency. The ability to customize tables for specific medical procedures can be a significant advantage when sourcing.
What are the Applications of Tables in Event Management?
Event management relies heavily on versatile tables for banquets, conferences, and exhibitions. Manufacturers provide foldable and portable tables that can be easily set up and taken down, maximizing space utility. Buyers should consider the weight, ease of transport, and assembly time when sourcing tables for events. Additionally, the ability to customize tables for branding purposes can enhance the overall event experience, making it memorable for attendees and clients alike.
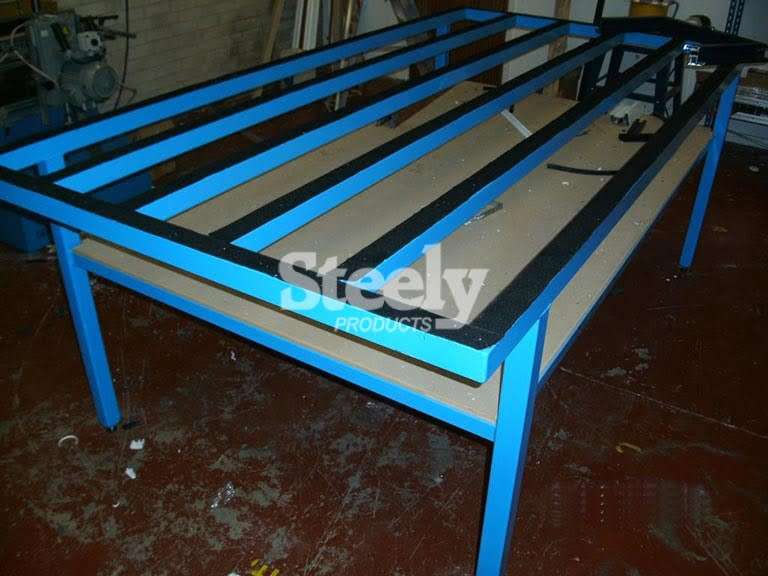
A stock image related to table manufacturer.
Related Video: Sources and Uses Table
3 Common User Pain Points for ‘table manufacturer’ & Their Solutions
Scenario 1: Navigating Supply Chain Disruptions in Table Manufacturing
The Problem:
B2B buyers in regions like Africa and South America often face significant challenges with supply chain disruptions. This may include delays in shipping, lack of reliable suppliers, or inconsistent quality of materials. For instance, a furniture retailer in Egypt might place a large order for tables, only to find that the manufacturer is unable to meet the delivery deadline due to logistical issues. Such disruptions can lead to lost sales, dissatisfied customers, and ultimately harm the buyer’s reputation in the market.
The Solution:
To mitigate these challenges, B2B buyers should establish a diversified supplier network. This means sourcing from multiple manufacturers across different regions to ensure that if one supplier encounters issues, others can fulfill the order. Buyers should also engage in thorough due diligence when selecting suppliers; this includes checking their production capabilities, logistics, and past performance. Regular communication with manufacturers can help buyers stay informed about any potential delays or issues. Additionally, utilizing technology platforms that allow for real-time tracking of orders can help in managing expectations and coordinating logistics more effectively.
Scenario 2: Ensuring Quality Control of Tables from Manufacturers
The Problem:
Quality assurance is a critical concern for B2B buyers, particularly when sourcing tables for commercial use. For example, a hotel chain in Europe may face issues when tables delivered from a manufacturer do not meet their durability standards, resulting in damages and replacements that incur additional costs. Such problems can disrupt operations and lead to dissatisfaction among clients.
The Solution:
To ensure consistent quality, B2B buyers should implement a rigorous quality control process. This could involve setting clear specifications and standards that manufacturers must meet before delivery. Buyers should consider conducting regular factory visits or using third-party inspection services to assess the quality of tables during production. Additionally, establishing a clear return policy for defective products can safeguard the buyer’s interests. Building a strong relationship with manufacturers that emphasizes quality assurance can also lead to better results. Regular feedback and collaboration can improve the manufacturing process and ensure that the products delivered align with the buyer’s expectations.
Scenario 3: Customization Challenges in Table Designs
The Problem:
Customization is increasingly becoming a demand in the B2B furniture market, as businesses seek unique designs that reflect their brand identity. However, a buyer from South America may encounter issues when trying to get customized tables from a manufacturer, such as limited design options or excessive lead times. These challenges can hinder a buyer’s ability to meet their customers’ needs and differentiate themselves in a competitive market.
The Solution:
To navigate customization challenges, B2B buyers should look for manufacturers that specialize in bespoke solutions. It is essential to communicate specific design requirements clearly and early in the negotiation process. Buyers can benefit from providing sketches or design inspirations to help manufacturers understand their vision. Engaging in collaborative design processes, such as using 3D modeling software, can also facilitate better communication and reduce misunderstandings. Furthermore, buyers should inquire about the manufacturer’s capabilities regarding customization and lead times to set realistic expectations. Building a long-term partnership with manufacturers that excel in custom projects can lead to more efficient processes and innovative solutions tailored to the buyer’s needs.
Strategic Material Selection Guide for table manufacturer
When selecting materials for table manufacturing, international B2B buyers must consider various factors, including the properties, advantages, and limitations of each material. This section analyzes four common materials used in table manufacturing: wood, metal, plastic, and glass. Each material has unique characteristics that can significantly impact product performance and suitability for different applications.
What Are the Key Properties of Wood in Table Manufacturing?
Wood is a traditional material known for its aesthetic appeal and versatility. It offers excellent strength-to-weight ratios and is relatively easy to work with. Key properties of wood include its natural insulation against temperature changes and its ability to absorb moisture, which can affect durability. However, wood is susceptible to warping and insect damage, which can compromise its longevity.
Pros: Wood is durable, offers a warm aesthetic, and can be easily customized. It is also relatively cost-effective compared to other materials.
Cons: The main limitations include susceptibility to moisture and pests, which may require additional treatments. Additionally, wood can be more expensive in regions where it is not locally sourced.
How Does Metal Perform as a Material for Tables?
Metal, particularly steel and aluminum, is increasingly popular in table manufacturing due to its strength and durability. Metals are resistant to wear and tear, making them suitable for high-traffic environments. Key properties include high corrosion resistance (especially stainless steel) and the ability to withstand high temperatures and pressures.
Pros: Metal tables are highly durable, easy to clean, and can support heavier loads. They are also resistant to fire and pests.
Cons: The primary disadvantages include higher manufacturing complexity and costs, especially for intricate designs. Additionally, metal can be prone to scratching and may not provide the same aesthetic warmth as wood.
What Are the Benefits of Using Plastic in Table Manufacturing?
Plastic is a lightweight and versatile material that is gaining traction in the table manufacturing industry. It is resistant to moisture, making it ideal for outdoor use. Key properties include a wide range of colors and finishes, along with the ability to mold into various shapes.
Pros: Plastic tables are cost-effective, lightweight, and resistant to weather conditions. They are also easy to maintain and clean.
Cons: However, plastic may not offer the same level of durability as wood or metal and can be prone to fading and scratching over time. It may also not be suitable for high-end applications where aesthetics are paramount.
Why Is Glass Considered a Premium Material for Tables?
Glass is often used in high-end table designs due to its sleek appearance and modern appeal. It is non-porous, making it resistant to stains and easy to clean. Key properties include high transparency and the ability to create an illusion of space.
Pros: Glass tables provide a sophisticated aesthetic and are easy to maintain. They can also be combined with other materials, such as metal or wood, for enhanced design.
Cons: The main limitations of glass include its fragility, which can lead to breakage, and the potential for higher costs. Additionally, glass can be heavy and may require special handling during manufacturing and transport.
Summary of Material Selection for Table Manufacturing
Material | Typical Use Case for table manufacturer | Key Advantage | Key Disadvantage/Limitation | Relative Cost (Low/Med/High) |
---|---|---|---|---|
Wood | Residential and commercial tables | Aesthetic appeal and ease of customization | Susceptible to moisture and pests | Medium |
Metal | Industrial and outdoor tables | High durability and resistance to wear | Higher manufacturing complexity and cost | High |
Plastic | Lightweight and portable tables | Cost-effective and weather-resistant | Less durable and prone to fading | Low |
Glass | High-end and modern tables | Sophisticated aesthetic and easy maintenance | Fragile and potentially expensive | High |
This guide provides international B2B buyers with actionable insights into selecting the right materials for table manufacturing, considering factors such as performance, cost, and regional preferences. Understanding these materials can aid in making informed purchasing decisions that align with specific application needs and market standards.
In-depth Look: Manufacturing Processes and Quality Assurance for table manufacturer
What Are the Key Manufacturing Processes for Table Production?
In the competitive landscape of B2B furniture manufacturing, understanding the core stages involved in table production is crucial for buyers seeking quality and efficiency. The manufacturing process typically encompasses several key stages:
-
Material Preparation
The first step in table manufacturing involves selecting and preparing the right materials. Common materials include wood, metal, glass, and composites. For wooden tables, the wood is often sourced from sustainable forests, treated for durability, and cut into specified dimensions. Buyers should inquire about the types of wood used (e.g., hardwood vs. softwood) and verify certifications that ensure sustainability, such as FSC (Forest Stewardship Council). -
Forming Techniques
Once materials are prepared, forming techniques come into play. For wooden tables, this may involve processes like cutting, shaping, and bending. Advanced techniques such as CNC (Computer Numerical Control) machining enable precise cuts and designs, enhancing customization options. Metal tables may undergo welding or stamping, while glass tables require cutting and polishing. Buyers should look for manufacturers utilizing state-of-the-art machinery to ensure accuracy and quality. -
Assembly
The assembly phase is where components come together to form the final product. This stage may involve joining tabletops to legs, attaching hardware, and ensuring structural integrity. Manufacturers often use various joining techniques, including doweling, mortise and tenon, or metal brackets. Buyers should assess the assembly methods used to ensure durability and strength in the final product. -
Finishing Processes
The final stage involves finishing touches such as sanding, staining, and sealing. These processes not only enhance the aesthetic appeal of the tables but also protect them from wear and tear. For instance, applying a polyurethane finish can improve scratch resistance. Buyers should inquire about the finishing techniques and materials used, as these can significantly affect the longevity and maintenance of the tables.
How Do Quality Assurance Practices Impact Table Manufacturing?
Quality assurance (QA) is integral to ensuring that the final product meets the expected standards and specifications. For B2B buyers, understanding the QA processes employed by manufacturers can help mitigate risks associated with product quality.
-
International Standards and Certifications
Many manufacturers adhere to international standards, such as ISO 9001, which provides a framework for quality management systems. Compliance with these standards demonstrates a commitment to quality and continuous improvement. Additionally, industry-specific certifications like CE marking for safety and API standards for specific materials can also be relevant. Buyers should request documentation of these certifications to verify compliance. -
Quality Control Checkpoints
Manufacturers typically implement several quality control checkpoints throughout the production process:
– Incoming Quality Control (IQC): This initial inspection ensures that raw materials meet specified standards before they enter production.
– In-Process Quality Control (IPQC): Inspections during various manufacturing stages help identify defects early, reducing waste and rework.
– Final Quality Control (FQC): The final inspection verifies that the finished product meets all specifications and quality standards before shipment. -
Common Testing Methods
Various testing methods are employed to ensure product quality, including:
– Physical Testing: Assessing the strength and durability of materials through stress tests.
– Chemical Testing: Ensuring that finishes and materials comply with health and safety regulations.
– Visual Inspection: Checking for aesthetic defects such as scratches or blemishes.
What Strategies Can B2B Buyers Use to Verify Supplier Quality Control?
For international B2B buyers, especially those from regions like Africa, South America, the Middle East, and Europe, verifying a supplier’s quality control processes is essential to ensure product reliability.
-
Conducting Supplier Audits
One effective strategy is to conduct on-site audits of potential suppliers. This allows buyers to observe manufacturing practices, quality control measures, and working conditions. Audits can be performed by the buyer or through third-party auditing firms that specialize in quality assessments. -
Requesting Quality Reports
Buyers should ask suppliers for comprehensive quality reports that detail their QA processes, inspection results, and any corrective actions taken in response to defects. These reports provide transparency and insight into the manufacturer’s commitment to quality. -
Utilizing Third-Party Inspections
Engaging third-party inspection services can offer an unbiased evaluation of the manufacturing process and product quality. These services often include pre-shipment inspections and random sampling tests, ensuring that the products meet specified standards before they leave the factory.
What Are the Nuances of Quality Control for International B2B Buyers?
Understanding the nuances of quality control is critical for international B2B buyers. Different regions may have varying standards and regulations that affect manufacturing practices. For example:
-
Regulatory Compliance: Buyers should be aware of the local regulations governing product safety and environmental impact in their respective markets. For instance, European buyers must comply with REACH regulations concerning chemical safety.
-
Cultural Differences: Different regions may have distinct cultural attitudes toward quality and workmanship. Buyers from Europe may prioritize meticulous craftsmanship, while buyers from Africa may focus more on cost-effectiveness. Understanding these differences can help buyers communicate effectively with suppliers.
-
Logistical Considerations: International shipping and logistics can introduce additional quality risks, such as damage during transit. Buyers should discuss packaging standards and shipping methods with suppliers to ensure that products arrive in perfect condition.
In conclusion, a thorough understanding of manufacturing processes and quality assurance practices is essential for B2B buyers in the table manufacturing sector. By focusing on these areas, buyers can make informed decisions that enhance their procurement strategies and ensure the quality of the products they purchase.
Practical Sourcing Guide: A Step-by-Step Checklist for ‘table manufacturer’
In today’s global marketplace, sourcing tables from manufacturers requires careful consideration and strategic planning. This guide provides a comprehensive checklist to help international B2B buyers, especially from Africa, South America, the Middle East, and Europe, navigate the procurement process effectively.
Step 1: Define Your Technical Specifications
Clearly outlining your requirements is crucial for successful sourcing. Identify the materials, dimensions, design styles, and functionalities needed for the tables. This not only helps in communicating your needs to suppliers but also aids in evaluating their capabilities.
- Material Selection: Consider durability and aesthetics; options may include wood, metal, or composite materials.
- Design Requirements: Specify whether you need custom designs or standard models.
Step 2: Conduct Market Research
Understanding the market landscape is essential before reaching out to suppliers. Research potential manufacturers in regions known for quality table production, such as Asia or Eastern Europe.
- Industry Trends: Stay updated on design trends and innovations that could influence your procurement choices.
- Competitor Analysis: Look at what similar companies are sourcing to ensure competitiveness.
Step 3: Evaluate Potential Suppliers
Before committing, it’s crucial to vet suppliers thoroughly. Request company profiles, case studies, and references from buyers in a similar industry or region.
- Quality Assurance: Inquire about the manufacturing processes and quality control measures in place.
- Experience and Reputation: Look for suppliers with a proven track record in delivering quality products on time.
Step 4: Verify Supplier Certifications
Ensure that the suppliers hold relevant certifications that guarantee quality and compliance with international standards. This step protects your investment and ensures product safety.
- ISO Certifications: Look for ISO 9001 for quality management systems.
- Sustainability Certifications: If applicable, check for certifications like FSC for sustainable sourcing.
Step 5: Request Samples
Before finalizing any orders, always request samples. This step allows you to assess the quality of the materials and craftsmanship firsthand.
- Testing for Durability: Ensure that the samples can withstand typical use cases.
- Design Approval: Confirm that the samples meet your aesthetic and functional specifications.
Step 6: Negotiate Terms and Pricing
Once you are satisfied with the samples, move on to negotiations. Discuss pricing, payment terms, and delivery schedules to find a mutually beneficial agreement.
- Volume Discounts: Inquire about pricing for bulk orders, which could lead to significant savings.
- Payment Flexibility: Explore options such as letters of credit or staggered payments to manage cash flow effectively.
Step 7: Establish Clear Communication Channels
Effective communication is key to a successful partnership. Ensure that you have established clear lines of communication with your chosen manufacturer.
- Regular Updates: Agree on a schedule for updates throughout the production process.
- Crisis Management: Discuss how to handle potential issues or delays proactively.
By following this checklist, international B2B buyers can streamline their sourcing process, ensuring they select the right table manufacturer while minimizing risks and maximizing value.
Comprehensive Cost and Pricing Analysis for table manufacturer Sourcing
What Are the Key Cost Components in Table Manufacturing?
When sourcing tables from manufacturers, understanding the cost structure is crucial for international B2B buyers. The primary components include:
-
Materials: The choice of materials—wood, metal, glass, or composites—significantly impacts cost. Premium materials can enhance durability and aesthetics but will raise the price.
-
Labor: Labor costs vary widely based on the manufacturing region. Countries in Africa and South America may have lower labor costs compared to Europe, influencing overall pricing.
-
Manufacturing Overhead: This includes expenses related to utilities, rent, and equipment maintenance. Efficient manufacturers often have lower overhead, allowing them to offer more competitive pricing.
-
Tooling: Initial setup costs for molds and machinery can be substantial, particularly for custom designs. These costs are usually amortized over larger production runs.
-
Quality Control (QC): Investing in QC processes ensures that products meet specifications and regulations, particularly important for international shipping. Higher QC standards may increase costs but can prevent costly returns.
-
Logistics: Transportation costs, including shipping and customs duties, play a significant role in the final price. Buyers should consider the total logistics costs when evaluating suppliers.
-
Margin: Manufacturers typically include a profit margin in their pricing. Understanding the standard margins in different regions can aid in negotiations.
How Do Price Influencers Affect Table Manufacturing Costs?
Several factors can influence the pricing of tables, including:
-
Volume and Minimum Order Quantity (MOQ): Larger orders often result in lower per-unit costs. Negotiating MOQs can lead to significant savings.
-
Specifications and Customization: Customized tables or specific design requirements can increase production costs. Buyers should clearly define their needs to avoid unexpected charges.
-
Materials and Quality Certifications: Higher quality materials and certifications (like ISO or FSC) can add to costs. However, they can also enhance the product’s marketability.
-
Supplier Factors: The reputation and reliability of suppliers can affect pricing. Established manufacturers with a track record may charge more but offer better service and product reliability.
-
Incoterms: Understanding Incoterms (International Commercial Terms) is essential for pricing negotiations. They define who bears the cost and risk at each stage of the shipping process, impacting the overall cost.
What Tips Can Help Buyers Negotiate Better Pricing?
International B2B buyers can employ several strategies to enhance their purchasing experience:
-
Effective Negotiation: Always negotiate pricing, especially for larger orders. Suppliers may have flexibility in their pricing structure.
-
Focus on Cost-Efficiency: Analyze the total cost of ownership (TCO), which includes purchase price, maintenance, and logistics. A slightly higher upfront cost may result in lower overall expenses.
-
Understand Pricing Nuances: Be aware of regional differences in pricing and quality expectations. For instance, buyers from Europe might prioritize certifications more than those from Africa.
-
Leverage Volume Discounts: If possible, consolidate orders to meet MOQ thresholds, which can lead to better pricing.
-
Build Long-Term Relationships: Establishing a strong relationship with suppliers can lead to better terms and pricing over time.
Conclusion: What Should Buyers Remember About Pricing Analysis?
While indicative prices can provide a baseline, they should be treated cautiously. Each factor—from material choice to supplier reliability—can significantly impact the final cost. By understanding the comprehensive cost structure and influencing factors, international buyers can make informed decisions that align with their budgets and quality expectations.
Alternatives Analysis: Comparing table manufacturer With Other Solutions
Introduction: Exploring Alternatives to Table Manufacturers
In the dynamic landscape of B2B operations, selecting the right table manufacturing solution is crucial for international buyers. However, understanding the alternatives available can help businesses make informed decisions tailored to their unique needs. This section will analyze ‘table manufacturers’ against alternative solutions, providing insights that cater specifically to buyers from Africa, South America, the Middle East, and Europe.
Comparison Table
Comparison Aspect | Table Manufacturer | Modular Furniture Systems | Custom Built Solutions |
---|---|---|---|
Performance | High durability and stability | Flexible configurations | Tailored designs for specific needs |
Cost | Moderate to high | Generally lower initial costs | Higher due to custom materials |
Ease of Implementation | Quick setup and installation | Easy to assemble | Requires longer lead time |
Maintenance | Minimal, depends on material | Varies based on material choice | Regular upkeep needed |
Best Use Case | Office environments needing stability | Collaborative spaces, versatile needs | Unique environments or branding |
Detailed Breakdown of Alternatives
What Are Modular Furniture Systems and Their Benefits?
Modular furniture systems provide a flexible solution for businesses that require adaptable workspaces. These systems are designed to be easily assembled and reconfigured, allowing companies to modify their layouts as needed. The major advantage of modular furniture is its cost-effectiveness, particularly for startups or businesses looking to optimize budgets. However, they may lack the high durability and stability found in traditional table manufacturing, making them less suitable for environments with heavy use.
How Do Custom Built Solutions Compare?
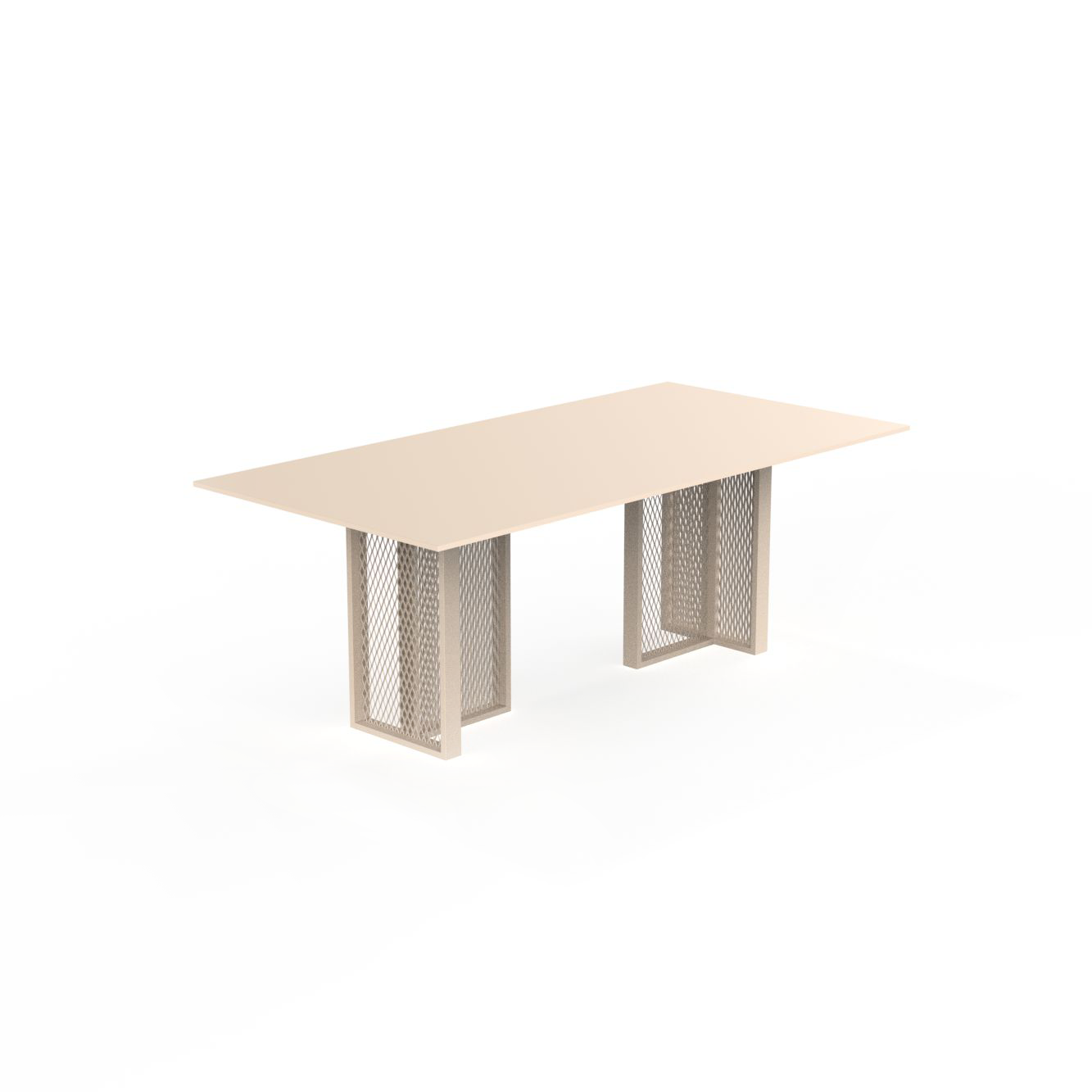
A stock image related to table manufacturer.
Custom built solutions offer a tailored approach, allowing businesses to create furniture that meets specific design and functional requirements. This option is particularly advantageous for companies with unique branding or operational needs, as custom pieces can enhance the aesthetic appeal of a workspace. However, the downside is the higher cost associated with custom materials and longer lead times for production. Regular maintenance is also necessary to ensure longevity, which can add to the overall operational costs.
Conclusion: Choosing the Right Solution for Your Business
When evaluating alternatives to table manufacturers, it’s essential for B2B buyers to assess their specific needs and operational contexts. Buyers should consider factors such as budget constraints, the need for flexibility in design, and the importance of durability in their furniture choices. By carefully weighing the performance, cost, ease of implementation, and maintenance requirements of each option, businesses can select the solution that best aligns with their strategic goals and workplace dynamics.
Essential Technical Properties and Trade Terminology for table manufacturer
What Are the Key Technical Properties for B2B Table Manufacturing?
When sourcing tables for commercial use, understanding the technical properties is crucial for ensuring quality, durability, and suitability for your specific needs. Here are several key specifications:
1. Material Grade: Why Is It Important?
Material grade refers to the quality and type of materials used in table production, such as hardwood, plywood, or metal. For instance, hardwood tables offer durability and aesthetic appeal, making them suitable for high-end markets, while plywood is often used for cost-effective solutions. Selecting the right material grade impacts the table’s longevity, maintenance requirements, and overall cost.
2. Tolerance Levels: What Do They Mean for Quality Control?
Tolerance levels define the allowable variations in dimensions during manufacturing. For tables, this could include the thickness of the tabletop or the height of the legs. Understanding tolerances is essential for ensuring that tables fit well within existing spaces and meet design specifications. Precise tolerances contribute to the overall stability and safety of the tables.
3. Load Capacity: How Does It Affect Your Purchase Decision?
Load capacity indicates the maximum weight a table can support without compromising its structure. This specification is vital for commercial settings like restaurants or conference rooms, where tables may need to support heavy items or equipment. Choosing tables with appropriate load capacities ensures safety and functionality in your workspace.
4. Finish Type: What Are the Options and Their Benefits?
The finish type refers to the surface treatment applied to the table, such as varnish, laminate, or paint. Each finish offers different benefits, including resistance to scratches, ease of cleaning, and aesthetic appeal. Understanding the available finishes helps buyers select tables that align with their maintenance preferences and visual branding.
5. Sustainability Standards: Why Should They Matter to You?
Sustainability standards pertain to the environmental impact of materials and manufacturing processes. Tables made from sustainably sourced wood or recycled materials can enhance a company’s green credentials. For international buyers, being aware of sustainability standards can influence purchasing decisions and corporate social responsibility initiatives.
What Are Common Trade Terminologies in Table Manufacturing?
Familiarity with industry jargon can streamline negotiations and improve communication with manufacturers. Here are some essential terms:
1. OEM (Original Equipment Manufacturer): What Does It Entail?
OEM refers to companies that produce parts or equipment that may be marketed by another manufacturer. In table manufacturing, an OEM might create tables designed to a specific brand’s specifications. Understanding OEM relationships is crucial for maintaining quality and consistency in your product line.
2. MOQ (Minimum Order Quantity): Why Is It Significant?
MOQ represents the smallest quantity of a product that a supplier is willing to sell. For table manufacturers, MOQs can vary significantly based on production capabilities. Knowing the MOQ helps buyers assess their budget and inventory needs, as larger orders may lead to cost savings.
3. RFQ (Request for Quotation): How to Utilize It Effectively?
An RFQ is a document sent to suppliers requesting price quotes for specific products. In table procurement, an RFQ allows buyers to compare prices, specifications, and lead times from different manufacturers. Crafting a detailed RFQ can lead to better pricing and more tailored responses.
4. Incoterms: What Are They and Why Are They Important?
Incoterms (International Commercial Terms) are standardized rules that define the responsibilities of buyers and sellers in international trade. For table manufacturers, understanding Incoterms clarifies shipping, insurance, and delivery responsibilities. This knowledge is vital for avoiding misunderstandings and ensuring smooth transactions.
5. Lead Time: How Does It Impact Your Supply Chain?
Lead time refers to the time taken from placing an order to receiving the goods. In table manufacturing, lead times can affect inventory management and project timelines. Being aware of lead times allows buyers to plan effectively, ensuring they meet customer demand without overstocking.
By grasping these technical properties and trade terminologies, B2B buyers can make informed decisions that align with their operational needs and market expectations.
Navigating Market Dynamics and Sourcing Trends in the table manufacturer Sector
What Are the Key Market Dynamics and Sourcing Trends in the Table Manufacturing Sector?
The table manufacturing sector is witnessing significant transformations driven by globalization, technological advancements, and changing consumer preferences. International B2B buyers, especially in regions such as Africa, South America, the Middle East, and Europe, must stay attuned to these dynamics to optimize their sourcing strategies.
Global Drivers Impacting Table Manufacturing
One of the primary drivers is the increasing demand for customizable furniture solutions. Buyers are looking for manufacturers that can provide tailored designs that cater to specific cultural and functional requirements. Additionally, the rise of e-commerce platforms has changed how manufacturers interact with buyers, creating a need for robust digital catalogs and direct-to-consumer sales strategies.
Emerging B2B Technology Trends
Technological advancements like 3D printing and augmented reality are revolutionizing the table manufacturing process. These technologies allow manufacturers to create prototypes rapidly and enable buyers to visualize products in their intended environments. Moreover, the integration of Artificial Intelligence (AI) in supply chain management helps optimize inventory levels and enhance demand forecasting, which is critical for maintaining competitive pricing and availability.
Sourcing Trends for International Buyers
For international buyers, especially from emerging markets, understanding local manufacturing capabilities is crucial. Many manufacturers are now establishing local partnerships to reduce lead times and shipping costs. This trend also aligns with the growing emphasis on local sourcing, which supports regional economies and ensures more responsive supply chains.
How Important Is Sustainability and Ethical Sourcing in the Table Manufacturing Sector?
The environmental impact of manufacturing processes is increasingly under scrutiny, prompting buyers to prioritize sustainability in their sourcing decisions. The table manufacturing sector is no exception, with many manufacturers adopting eco-friendly practices to minimize waste and reduce carbon footprints.
The Importance of Ethical Supply Chains
International B2B buyers are now placing a strong emphasis on ethical sourcing. This involves ensuring that raw materials are sourced responsibly, labor practices are fair, and that the overall supply chain adheres to ethical standards. Buyers are increasingly demanding transparency, pushing manufacturers to provide documentation and certifications that verify compliance with environmental and social governance (ESG) criteria.
Green Certifications and Materials
To meet these demands, manufacturers are investing in green certifications such as Forest Stewardship Council (FSC) and ISO 14001, which signify compliance with sustainability standards. Buyers should look for products made from reclaimed wood, recycled materials, and non-toxic finishes, which not only reduce environmental impact but can also enhance brand reputation in an increasingly eco-conscious market.
What Is the Evolution of the Table Manufacturing Sector?
The table manufacturing sector has evolved significantly over the decades, influenced by technological advancements and changing consumer preferences. Historically, table production relied heavily on manual craftsmanship, with artisans creating bespoke pieces.
With the advent of industrialization in the 20th century, mass production techniques emerged, enabling manufacturers to produce tables at scale, significantly reducing costs. Today, the sector is experiencing a renaissance as a blend of traditional craftsmanship and modern manufacturing techniques, such as CNC machining, allows for both high-quality and efficient production. This evolution is crucial for B2B buyers to understand, as it informs their sourcing decisions and influences product availability and pricing strategies in the market.
In summary, navigating the table manufacturing landscape requires international B2B buyers to be aware of market dynamics, prioritize sustainability, and understand the historical context of the sector to make informed purchasing decisions.
Frequently Asked Questions (FAQs) for B2B Buyers of table manufacturer
-
How do I identify a reliable table manufacturer for my business needs?
To identify a reliable table manufacturer, start by conducting thorough research online and utilizing B2B platforms like Alibaba, Global Sources, or local directories relevant to your region. Check for verified suppliers, read customer reviews, and request references. Additionally, assess their production capacity, quality certifications, and compliance with international standards. Engaging in direct communication with potential manufacturers can provide insight into their responsiveness and professionalism. -
What factors should I consider when evaluating table manufacturers?
When evaluating table manufacturers, consider their experience in the industry, production capabilities, and quality assurance processes. Look for certifications such as ISO 9001, which indicate adherence to quality management standards. Additionally, assess their ability to customize products to meet your specific requirements and their track record in delivering on time. Don’t overlook their customer service and after-sales support, as these are crucial for long-term partnerships. -
What is the typical minimum order quantity (MOQ) for table manufacturing?
The minimum order quantity (MOQ) for table manufacturers can vary significantly based on the type of table and the supplier’s policies. Generally, MOQs can range from 50 to 500 units for standard designs. For customized tables, MOQs may be higher due to the increased production costs. It’s essential to discuss MOQs upfront with potential suppliers to ensure they align with your business needs and budget. -
What are the common payment terms offered by table manufacturers?
Common payment terms in the table manufacturing industry include a deposit (typically 30%) upon order confirmation, with the balance due before shipment. Some manufacturers may offer more flexible terms, such as payment against documents or letter of credit, particularly for larger orders. It’s advisable to negotiate terms that protect your interests while establishing a trusting relationship with the supplier. -
How can I ensure quality control when sourcing tables from manufacturers?
To ensure quality control when sourcing tables, implement a comprehensive inspection process. This may include requesting samples before full production, conducting on-site inspections, or hiring third-party quality control services. Establish clear quality standards and communicate them with the manufacturer. Additionally, consider including quality assurance clauses in your contract to safeguard against defects and non-compliance. -
What are the logistics considerations when importing tables from manufacturers?
Logistics is crucial when importing tables. Consider shipping methods (sea, air, or land) based on cost and delivery timelines. Factor in customs duties, taxes, and import regulations specific to your country. Collaborate with a reliable freight forwarder to streamline the shipping process and ensure compliance with international trade laws. Understanding the logistics chain will help you anticipate delays and manage inventory effectively. -
Can I customize the design of tables when working with manufacturers?
Yes, many table manufacturers offer customization options to meet specific design requirements. This can include variations in materials, dimensions, colors, and finishes. When discussing your needs, provide detailed specifications and examples of your desired design. Keep in mind that customization may affect the MOQ and lead time, so plan accordingly. -
What is the best way to communicate with international table manufacturers?
Effective communication with international table manufacturers is key to a successful partnership. Utilize clear and professional language, and consider time zone differences when scheduling meetings. Use email for detailed discussions and follow-ups, while instant messaging apps can facilitate quicker responses. Providing visual aids such as sketches or images can enhance understanding, especially when discussing custom designs or specifications.
Important Disclaimer & Terms of Use
⚠️ Important Disclaimer
The information provided in this guide, including content regarding manufacturers, technical specifications, and market analysis, is for informational and educational purposes only. It does not constitute professional procurement advice, financial advice, or legal advice.
While we have made every effort to ensure the accuracy and timeliness of the information, we are not responsible for any errors, omissions, or outdated information. Market conditions, company details, and technical standards are subject to change.
B2B buyers must conduct their own independent and thorough due diligence before making any purchasing decisions. This includes contacting suppliers directly, verifying certifications, requesting samples, and seeking professional consultation. The risk of relying on any information in this guide is borne solely by the reader.
Strategic Sourcing Conclusion and Outlook for table manufacturer
In the evolving landscape of global commerce, strategic sourcing remains a vital component for international B2B buyers seeking high-quality table manufacturing solutions. By prioritizing relationships with reliable suppliers and leveraging data-driven insights, businesses can enhance their procurement processes, reduce costs, and ensure product quality. Buyers from Africa, South America, the Middle East, and Europe, particularly in emerging markets like Argentina and Egypt, must focus on identifying manufacturers that not only meet their specifications but also align with their sustainability goals and ethical standards.
What are the key takeaways for effective strategic sourcing in table manufacturing? First, understanding local market dynamics and supplier capabilities can lead to more informed purchasing decisions. Second, fostering open communication with manufacturers can yield innovative solutions tailored to specific business needs. Lastly, a forward-looking approach that embraces technology and sustainability will be essential for long-term success.
As you navigate your sourcing strategies, consider engaging with diverse suppliers and exploring new markets to expand your options. The future of table manufacturing is bright, and by acting now, you can position your business for growth and success in a competitive environment.